深孔加工技术改进
利用带状切屑解决深孔内腔平底的加工操作方法

利用带状切屑解决深孔内腔平底的加工操作方法信连志(北方华安工业集团公司,黑龙江齐齐哈尔 161006)摘要:本文真对深孔内腔平底工序车削中存在的主要问题进行深入分析,结合车削实际的加工过程,阐述了刀具的材料,刀具几何参数、切削参数的选择对切屑及刀具破损的影响,优选了刀具材料、优化了刀具几何角度、刀具结构,给出相应的加工切削用量,解决弹体内腔平底加工难题,提出利用带状切屑解决内腔深孔加工的新方法和思路。
对提高产品质量降低废品率。
深孔干式切削也是一种环保的加工新技术。
关键词:干式车削;刀具角度;内腔深孔加工;带状切屑1 引言本文就深孔内腔平底工序加工中,深孔刀杆直径与排屑之间的矛盾,进行认真研究和分析,结合工艺特点及现有工艺装备条件,在原有刀具的基础上进行改进,利用长条可控带状切屑,有效的解决并提高了弹体内腔平底工序加工质量和生产效率。
2内腔平底工序工艺及破损主要问题分析(1)工艺分析:某产品内腔平底工序加工,长径比大于五,属于深孔切削加工。
为避免热处理变形等因素,内腔平底加工余量(双边)留10MM,内腔平底加工装备结构特点是:图1 固定刀台示意图将CW6163A普通车床小托板和刀台卸下,更换成一体固定刀台安装刀杆(图1),前端方孔安装使用焊接刀。
一体刀台安装稳固,为减少切削时的震动,刀杆前方安装固定套,弹体内腔直径为φ90,刀杆直径φ80。
同时也解决了刀体过长,无法在刀台安装的问题(2)刀具破损分析:原加工过程为水质切屑液冷却车削,使用YT5硬质合金焊接整体刀具,产生弧形切屑,主要以冷却液将切屑冲出。
刀具破损的主要原因是由于刀具前方定位套、刀体与弹体内腔间隙过小。
使切屑无法排出,造成切屑与刀具产生冲击,这种机械冲击造成的应力超过了刀具材料许可的强度引起崩刃、剥落或碎断。
刀具使用中基本无正常磨损,由于弹体加工过程中经常发生非正常磨损,硬质合金与弹体发生镶嵌无法修复。
且须多次走刀加工时间较长,因此影响了产品的批量生产。
机械加工过程中的深孔加工技术分析

2 . 高压 内排屑深孔钻钻深孑 L 加工技术
2 . 1 单 刃深孔钻钻深孔加工技术 内排 屑单 刃深 孔钻 的刀片和导 向部分采用 硬质 合金材料 . 其刀尖 偏离 中心 3 m m . 以至于在切 削时工件 中心形成 定心尖 , 并 能够抵消一 部分径 向切 削力 。 主切削刃形成 阶台型 . 能够起到分 屑的作用 。 在操作 时可依据钻孔直径 大小来定其分刃数量 , 保证排屑顺利 。 在深孔加工过程中. 各削刃的后 刀面应和被加工 的孔径错开 . 防止 加工时对孔的表 面造成损伤 而导向垫 的尺寸则要 比刀具刃部 直径尺 寸小 0 . 0 8 — 0 . 1 mm, 以免影响钻孔的直线性 。导 向垫上的倒角设计为 1 × 1 8 。 将有利于吸人切削液从而形成油楔 。这种深孔加工技术主要应用在 求 都可以降低 。因此 , 我们应该尽可能采用较先进的喷吸钻加工。 各种实心铸件的油缸上 . 在实践过程 中发现其效果还是比较好的。 对不 同直径的深孔 , 应选不 同形式的钻头加工 . 这样可以发挥各种 深孔加工时 . 切削 区域 的温度高 , 为保证正常工作 . 冷 却液的温度 一 2 0 小直径深孔时用枪孔钻 ; 加工 巾 4 _ 4 0 一 要控制在一定合适 范围内. 一般规定冷却液 的最 高工作 温度将不超过 钻头的特长。如加工 3 加工 2 0 一 6 5 深孔时 , 用 喷吸钻 或高压 内 4 5 — 5 0 ℃. 如果超过 这一数值 . 就应 立刻采用冷却装 置如水 冷或风冷来 般孔 时可用硬质合金钻 头 ; 排屑深孔钻; 加工 6 5以上的深孔时用机械夹固式不重磨深孔钻 。 降低冷却液 的温度 . 保证正常 的深孔加工 。
◇ 科技论坛◇
科技 嚣向导
2 0 1 3 年第0 9 期
机械加工深孔加工技术

02
深孔加工技术分类
枪钻技术
01
02
03
原理
枪钻是利用后角刀刃和切 削部分同时进行切削,实 现钻孔的加工。
特点பைடு நூலகம்
枪钻的刚性和导向性较好 ,可以加工小直径、深孔 和精密孔。
应用
广泛应用于汽车、航空航 天、机床等领域。
BTA深孔钻技术
原理
BTA深孔钻是利用切削液 通过钻头内部通道从钻头 喷出,将切屑从钻头外部 排出,实现深孔加工。
排屑问题
总结词
深孔加工中的排屑问题通常是由于切削过程中产生的切屑堆积、堵塞或排出不畅所引起的。
详细描述
为了解决排屑问题,可以采取多种措施,如优化刀具形状和切削参数、选择合适的冷却液和润滑剂、 使用振动器或超声波装置等。此外,还可以通过改变加工方式或使用专门的排屑装置来避免切屑堵塞 或排出不畅的问题。
加工要求
高精度、高强度、高耐热性
加工过程
应用效果
使用深孔钻进行粗加工和精加工,保证孔 的直径、圆度和表面粗糙度符合要求,并 进行热处理提高零件强度和耐热性
提高发动机性能和安全性,降低维护成本
案例三:某医疗器械零件深孔加工
零件名称
医疗器械微针头
加工要求
高精度、高表面质量、高一致性,微米级 尺寸
加工过程
应用
广泛应用于机械、航空航天等领域 。
挤压钻技术
原理
挤压钻是利用钻头挤压孔壁,使 材料发生塑性变形,实现深孔加
工。
特点
挤压钻具有加工硬化层浅、工件 表面质量好等优点,但需要较大
压力和较强的刚性支撑。
应用
广泛应用于机械、航空航天等领 域。
03
深孔加工机床与工具
机械加工深孔加工技术研究的论文

研究背景与意义
研究内容
本文主要研究了深孔加工技术的现状、发展趋势和存在的问题,重点探讨了深孔加工的关键技术、加工参数优化、加工质量与效率提升等方面的内容。
研究方法
本文采用文献综述、理论分析和实验研究相结合的方法,对深孔加工技术进行了全面的研究和分析。首先,通过对国内外相关文献的梳理和评价,掌握了深孔加工技术的研究现状和发展趋势。其次,结合理论分析,对深孔加工过程中的切削力、切削温度、刀具磨损等关键因素进行了深入研究。最后,通过实验研究,对深孔加工参数进行了优化,并验证了所提方法的可行性和有效性。
研究不足与展望
虽然本文研究的深孔加工技术在某些方面取得了进展,但仍存在一些问题需要进一步研究和改进。
未来可以进一步优化深孔加工技术的工艺参数,提高加工效率和质量。
针对不同类型的材料和产品,需要研究更加适应的深孔加工技术,以满足不断变化的市场需求。
07
参考文献
总结词
详细描述
总结词
参考文献
感谢观看
机械加工深孔加工技术研究的论文
2023-10-30
CATALOGUE
目录
引言机械加工深孔加工技术概述机械加工深孔加工技术研究现状机械加工深孔加工技术改进与创新机械加工深孔加工技术实际应用案例分析结论与展望参考文献
01
引言
深孔加工技术是机械加工中的重要组成部分,广泛应用于航空、航天、汽车等领域。
THANKS
模具钢材料深孔加工
模具型腔深孔加工
深孔加工技术在模具制造业的应用案例
06
结论与展望
研究结论
本文研究的深孔加工技术在实际生产中得到了广泛应用,并取得了良好的效果。
加工深孔螺旋油槽

1 支 承块 .
2 .刀具
3 杆 4 2一 .镗 . M6螺钉
5 件 .工
加工 时 ,为 了防 止 切 屑 卡 入 支 承 块 表 面 ,利 用
了小 型空气 压 缩 机 把 气 管 固定 在 刀 架 上 对 准 工 件 内
孑 进行 气 压 冲 孔 ,使 切 屑 始 终 在 刀 具 的 前 方 掉 落 , L
图 1 .T件 2 示表 .指 3 3 镗杆 . 4 .垫 刀片
块 R 4圆弧 即可保 证 两轴线 一致 。 2 为了保 证镗 杆 在 支 承块 之 上 自由移 动 ,镗 杆 燕
找正后 ,采 用 专 用 套 筒 可 调 刀 具 在 车 床 上 直 接
镗出支 承块 圆弧 R 4 m。镗支 承块 R 4 2m 2 mm 圆弧方 法
有效 地防 止 了切 屑卡 人支 承块 之 间 。
为 了保 证改 进后 的 镗杆 圆弧 R 4 2 mm轴 线 与 工件 内孑 轴 线一 致 ,在 支 承 块 中 间处 加 工 4 . rm孔 与 L ,5 8 a 沉孔 41 m '6 m,用 M8螺 钉 把 支 承块 与 镗杆 固定 ,校 正 镗杆 轴线 ,采用 专用 套 筒刀 具 在 车 床 上 镗 出支 承
)
2 0 02
‘一
‘一
2 0 02
‘一
利用 车床 中滑 板 与 溜 板 燕 尾 连 接 ,刀 具 可 以径 向移 动 的原 理 ,把普 通 的镗 杆 前端 处 铣 出一 段燕 尾
6 ( O
图
1
凹槽 ,采 用 一 块 HT 2材 料 铣 出燕 尾 凸槽 作 支 承 块 6
加 工 精 度 亦 得 到 可 靠 保
证
3 调 节螺钉 .
深孔加工技术改进

径大小不一 ,都偏大 ,最 小为 6 5 . 2 0 mm,最大为
6 6 . 2 0 mm。 经 分 析 认 为 ,钻 头 的 损 坏 是 钻 头 导 向 块 未起 到 导 向支 承 作用 ,且 与 切 削前 速 度 低 、进 给
量小而导致钻削时失稳 、钻杆颤动有关。
于 是 ,在 原 有 工艺 装 备 基 础 上 进行 了 改进 ,具 体做法如下 : 针 对 已经加 工 出的 8 0 0 mm深 的 孔 ,在车 床 上 用
( 2 )切削热不 易传散 ,须采 取强制有效的冷
却 方式 。
( 3 )切屑不易排 出 ,需要控 制切屑长短和形
状 ,并进 行 强行 排 屑 。
( 4 )工艺 系统 刚性差 ,由于孔的长径之 比较
大 ,钻杆 细 而长 , 因而 支承导 向极 为 重要 。
( 4 ) 问题 :刚开 始钻 孔时 还 比较 顺 利 ,待
体如 下 :
头 ,如 图2 所示 。然后 用过渡 接
头把钻头和钻杆联接在一起。
( 3 )原 始 加 工 方 法 :最 初
图 2 内 排屑 式
合 金钻头
( 1 )不能直 接观察到 刀具切 削情况 ,只能凭
经验 、听声音 、看切屑、观察机床负荷和压力表 、
触摸 振 动等 来 判 断切 削 过程 是 否正 常 。
实 体 棒 料 经 调 质 处理 至硬 度2 2 0 ~2 5 5 HB W 后 制 作
ቤተ መጻሕፍቲ ባይዱ
的迅速发展、新型材料 的出现、加工精度要求越来 越高 ,孔加工难 度越 来越大 ,深孔加 工往往 成为
而成。加 工前 的毛坯 尺寸为 l 5 0 mm×3 0 1 0 mm,
高精度深长孔加工方法

学院: 机械工程学院专业班级: 学号: 姓名:高精度深长孔的精密加工一、历史背景枪钻与内排屑深孔钻两种加工孔的刀具分别出现于20世纪30年代初和40年代初的欧洲兵工厂,这并非历史的偶然。
其主要历史背景是:一次世界大战(1914〜1918年)首次使战争扩大到世界规模。
帝国主义列强为瓜分殖民地而需要大量现代化的枪炮(特别是枪械和小口径火炮的需求量极大)。
而继续使用传统的扁钻、麻花钻、单刃炮钻,已经完全不能满足大量生产新式武器的要求,迫切需要进行根本性的技术更新。
于是高精度深长孔的制造就成为了一个摆在制造者面前的一个首要问题,并且一直延续到了现今。
第一次世界大战中的火炮二、传统加工工艺及存在的问题在现代机械加工中,也经常会遇到一些深孔的加工,例如长径比(L/D)≥10,精度要求高,内孔粗糙度一般为Ra0.4~0.8的典型深孔零件,过去我们采用的传统工艺路线一般是:钻孔(加长标准麻花钻)→扩孔(双刃镗扩孔刀)→铰孔(标准六刃铰刀)→研磨此工艺虽可达到精度要求,但也存在诸多缺点,特别是在最初工序采用加长麻花钻钻孔时,切削刃越靠近中心,前脚就越大。
若钻头刚性差,则震动更大,表面形状误差难以控制,加工后孔的直线度误差,钻头易产生不均匀的磨损等现象,生产效率和产品合格率低,而且研磨抛光时,工作环境比较脏,由于钻孔工序的缺点,而带来的影响难以在后面的工序中克服,形状误差不能得以修正,因此加工质量差。
传统深孔的加工流程三、工艺路线与刀具的改进本着提高生产效率提高产品合格率的原则,结合深孔加工的一些特性,对加工工艺及刀具进行了改进,改进后的工艺路线是:钻孔(BTA钻)→扩孔(BTA扩)→铰孔(单刃铰刀)→研磨1、钻孔与扩孔刀具及工艺的改进单管内排屑深孔钻的由来单管内排屑深孔钻产生于枪钻之后。
其历史背景是:枪钻的发明,使小深孔加工中自动冷却润滑排屑和自导向问题获得了满意的解决,但由于存在钻头与钻杆难于快速拆装更换和钻杆刚性不足、进给量受到严格限制等先天缺陷,而不适用于较大直径深孔的加工。
机械加工中深孔加工技术的研究

机械加工中深孔加工技术的研究摘要:在机械工程行业壮大发展的背景下,机械化工艺水平,深加工技术在现实生产活动中得到了广泛应用,该项技术虽然能创造出较好的效益,但是客观上讲技术应用中还滞留着一些问题。
本文简单分析了深孔加工技术应用的重点与难点,包括技术操作难度较高、钻孔操作有应局限性、碎屑外排环节有问题等,简单分析以上状况的成因,以促进深加工技术有效应用为目标,总结技术要点及应用策略,希望能给同行实践过程带来些许帮助。
关键词:机械化加工;深加工;难点分析;技术应用引言机械加工制造是我国的传统行业之一,其直接关系着国民经济的整体发展水平。
机械化加工生产中可供选择的技术方法有很多,深加工就是其一,其在促进我国机械加工水平全面提升方面表现出良好效能。
深孔通常是孔长度和直径比大于5~10的孔。
通常而言,在机械化加工生产中,深孔的实际加工数量在总量内占比约50%。
综合以上数据,能够认识到做好深孔加工工作的必要性。
为了能全面提升深孔加工效率与质量,应积极研发适宜且高效化的深孔加工技术,并结合实际情况持续完善技术应用过程,彰显新技术的优势,促进我国机械行业获得更大的发展进步。
1深孔加工技术的重点和难点1.1技术应用难度较高主要体现在如下几个方面[1]:一是基本上是孔径小,孔深大的条件下进行生产,受限于设备或刀具因素的制约,加工时出口位置容易产生偏差。
二是由于孔深大,切削过程中切屑不能及时有效地排出孔,以致加工时容易发生金属屑堵塞造成孔壁局部的不良状况,甚至刀具断裂的情况。
三是配备的钻头及定位夹具均会对深孔加工技术应用效果产生较大的影响。
长时间进行深孔加工作业会导致定位导向件发生不同程度的磨损问题,以致深孔半径、深度等指标和设计要求之间出现很大的出入,不仅影响加工的精准度,还弱化深孔加工技术的价值。
四是造成钻头及加工夹具发生磨损情况的因素不唯一,而加工部位的冷却效果差、温度较高等被认定是引起磨损问题的两大主因。
1.2深孔钻加工有一定局限性钻孔作业过程中,加工零件的材质可切削性,被加工的孔深与孔径比例也局限于加工条件,钻孔的刀具刚性和排屑效果也会限制深孔的加工质量。
深孔加工常见问题解决方法

深孔加工常见问题解决方法【德州三嘉机器】在深孔加工过程中,经常出现被加工件尺寸精度、表面质量以及刀具的寿命等问题,如何减少甚至避免这些问题的产生,是我们目前亟待解决的问题。
德州三嘉机器制造有限公司拥有先进的深孔加工技术,拥有一支精益求精、不懈创新的科研团队。
下面德州三嘉为我们介绍一下深孔加工常见问题解决办法~#详情查看#【德州三嘉机器:深孔加工】难切削材料的深孔加工、深孔钻削孔轴线偏斜和深孔加工表面出现螺旋沟都是深孔加工中难以解决的问题,直接影响深孔加工质量和加工效率。
因此,研究难切削材料的深孔加工技术、控制深孔钻削孔轴线偏斜技术和抑制深孔加工表面出现螺旋沟技术,成为深孔加工中最为关注的问题。
【深孔加工常见问题解决方法】1、难切削材料的深孔加工难加工材料一般是指不锈钢类、钛合金类、高温合金类材料,这些材料的共同点是韧性强,断屑困难,导热性差,容易产生加工硬化,应采取相应工艺措施:1.1、选择合适的刀具材料,因为加工材料中有的元素与刀具材料有一定的亲和力,会产生严重的粘刀现象,刀具磨损严重。
1.2、选择合适的切削用量:一般选用V≤20m/min,f=0.01-0.07mm/r。
1.3、选择合适的刀具角度:选择大前角,使切削轻快省力。
1.4、选择合适的排屑方式:由于难加工材料不容易断屑,如果采取低转速,较深断屑台的方式都不能很好断屑的话,最好采用不断屑的相反措施,即减小进给量,适当提高转速,切出薄薄的切屑,使切屑绵长不断并顺利排出,切削十分平稳。
2、深孔钻削孔轴线偏斜深孔钻削孔轴线偏斜问题是目前存在的一个技术难题。
当钻孔长径比大于50时,孔轴线的偏斜一般无法预测和控制。
孔轴线偏斜到一定程度后,就开始急剧变化,此时,孔轴线大大超差,钻头甚至从工件中间穿出,造成工件报废,钻头损坏,损失较大。
针对以上问题可采取以下措施:1、选择最佳切削方式,尽量选择工件旋转+刀具旋转,条件允许的情况下,工件应旋转。
2、合理选择刀具几何参数。
深孔加工技术

图6 微型深孔枪钻数控机 床(2轴或4轴可选)
.
16
枪钻机床
✓钻削范围:6mm - 50mm ✓转速:0 – 4500RPM ✓进给速度:0 - 4000mm/min ✓快进速度:12m/min
图7 深孔钻削单元:X、Y、Z、
W、B、C-6轴控. 制
17
BTA系统
2.3 BTA系统及其配置
由于枪钻的一些缺陷,1943年Beisner发明了一种内排屑 深孔钻,由于该种结构于1945年得到欧洲“钻孔与套料协 会(Boring and Trepanning Association,缩写为BTA)”的确 认和推广,通称为BTA钻。由此产生了BTA钻削系统,如 图8所示; 经BTA推荐的深孔刀具共有三种:用于实体材料钻深孔 的BTA钻,扩钻和套料钻。扩钻用于对已钻孔的进一步扩 大和对毛坯粗孔的加工,特别用于以较小尺寸规格的深孔 机床钻较大的孔。套料钻用于从实体上取出大直径或贵重 金属料芯,其所需机床功率也小得多。在三种钻头中,以 BTA(实体)钻应用最广,对深孔钻发展的影响也最深远。
.
3
引言
深孔加工技术,通常指的就是深孔钻削技术,它和车削、 铣削等加工方法不同,其刀具本身进入工件,并在封闭的条 件下进行切削,因而受到较多的限制。其特点有: (1)、在工作过程中,无法直接观察刀具的工作情况,目前 只能凭经验通过不断观察铁屑形状和手摸钻杆等手段来判断 刀具的工作情况; (2)、不可能制成具有足够的刚度与足够牢靠的刀具和夹具, 如钻杆细而长,钻出的孔不可避免地会产生某些偏差。如走 偏,孔中心线弯曲等。 (3)、钻头工作条件恶劣;切屑是在不能保证其正常形成的 不良条件下产生的:整个切削刃全部参加工作,切屑宽度大, 易产生振动;切削刃上各点的切削速度不同等。 (4)、断屑与排屑困难,在孔内钻头钻杆要占据很大一部分 空间,排屑空间受到限制,而且切屑难以自动排出。 (5)、刀具的散热冷却条件不好。
机械加工深孔加工技术研究的论文

机械加工深孔加工技术研究的论文摘要:随着工业的不断发展,对于深孔加工技术的需求也越来越大。
深孔加工是指在工件中加工出较大长度宽径比的孔。
本文通过分析机械加工深孔加工技术的研究现状和存在的问题,提出了一种改进的深孔加工技术,并进行了实验验证。
实验结果表明,改进的深孔加工技术能够提高加工效率和质量,具有较好的应用前景。
关键词:机械加工;深孔加工;技术;研究1.引言深孔加工技术作为一种重要的加工工艺,在航空航天、汽车制造、兵器制造等领域中有着广泛的应用。
随着工业的快速发展,对于深孔加工技术的需求也越来越大。
然而,由于深孔加工存在加工难度大、加工效率低以及加工质量不稳定等问题,限制了其进一步的应用和发展。
2.研究现状深孔加工技术的研究主要集中在以下几个方面:材料选型、切削力分析、润滑冷却技术、切削参数优化等。
其中,材料选型是深孔加工中一个重要的环节,需要选择适合的刀具和工件材料组合,以提高加工效果和延长刀具寿命。
切削力分析能够帮助工程师更好地理解深孔加工过程中力的变化规律,从而指导实际生产中的操作。
润滑冷却技术是深孔加工中的一个关键技术,可以降低加工温度、减少刀具磨损和延长刀具寿命。
切削参数优化能够通过分析加工条件和材料特性,提高加工效率和质量。
3.存在问题虽然深孔加工技术已经有了一定的研究成果,但仍然存在一些问题。
首先,深孔加工过程中的切削力和切削温度较大,容易导致刀具的磨损和加工质量的下降。
其次,传统的润滑冷却技术对于深孔加工来说效果不佳,需要进一步改进。
最后,深孔加工技术的加工效率较低,需要采取一些措施来提高效率。
4.改进技术针对深孔加工技术存在的问题,本文提出了一种改进的深孔加工技术。
首先,在材料选型方面,选择了适合的刀具和工件材料组合,以提高加工效果和延长刀具寿命。
其次,在切削力和切削温度方面,采用了刀具涂层和冷却剂的方式来降低切削力和切削温度,减少刀具磨损和提高加工质量。
最后,在加工效率方面,通过优化切削参数,提高加工效率和质量。
细长深孔加工的几种方案

Hale Waihona Puke 1 设 计和改 善 。 并在 实际
f
易被抱死 或折断的原因 , 认为主要有 以下几种 : 笔者
:
I
: 、 决 方 案 解
1 改制小 扁钻 、
利 用 废 旧 的 小
l 由于钻头直径小 , 、 钻头剐度差 、 强度差 、 抗扭
拒能力差 , 同时 螺 旋 槽 比较 窄 , 屑 易将 螺 旋 槽 堵 铁
的直径 为 2 3 - mm, 速 可 在 1 0 — 0 0转 / 范 转 5020 分 围 ; 当加 工 孔 径 小 于 l a mv,转 速 可 调 至 2 0 ~ 00 30 0 0转 / 分 此 种 情 况 下 ,空 转 时 间短 于 切 削 时
( ) 先 在 钻 轴 的 环 套 上 固定 一 个 螺 栓 , 其 1首 在
上 方套 装 一 个 弹 簧 , 后 装 上 轴 套 , 弹 簧 长 度 高 然 使
于 轴套 5 a , 限动 垫圈 和两 个螺 母 预 紧 。使 主轴 n a用 n 受 到 一个 向 上 的拉力 , 当钻 头跳 动 时有 一 个缓 冲范 围 。同时可 在 小 孔 即将 钻 通时 ( 削力 为零 ) 感 觉 切 ,
液 的进 入 , 降低 了 内孔 表面粗糙 度 。刀 具 主要参数 :
锋 角 :0= 1。 12 前角 : 0 后 角 := 5~0 2 l0~ 1。 = 。 a 1。2。 同时修磨倒 锥约为 O 2 m( . m 以减 小磨 擦 ) 0 。
2 限动 、 调装 置 c 图 2 、 微 如 ) 该 装 置 既 可 解 决 进 给 量 不 均 匀 的 问 题 , 时 同 也 可 解 决 小 孔 在 即 将 钻 通 瞬 间 钻 头 易 折 断 的 问
断屑式深孔加工循环的改进

断屑式深孔加工循环的改进随着机械制品高功能化的发展势头,零件逐步趋向细小化和精密化。
由于数控系统功能的限制,程序编制中有时会因为相应循环功能指令不完备或不符合加工要求而使程序的编制变得烦琐,影响加工效率。
利用宏程序,我们可以编制所需要的程序来弥补数控系统本身的功能不足,改善加工状况,提高产品的加工精度和生产效率。
本文以FANUC Oi系统为例,讨论通过用户宏程序改进断屑式深孔加工循环指令的具体过程。
一、循环路径的规划设计孔是零件上最常见的结构,所以孔的加工也较为普遍。
在孔系加工中,随着孔深度的增加,加工难度也随之加大,FANUC系统提供了两种深孔加工循环指令:G83和G73。
两种循环每次切深都是固定的。
随着孔的深度增加,排屑愈加困难。
如果是固定切深,开始时适合,待到孔底时就不一定适合了,若按孔底设定切深,势必影响效率。
所以,我们采用可变切深,控制每次的钻孔深度按一定的要求逐渐减小,来改善加工条件,使加工的高效率与加工的安全性同时得到满足,从而实现可变切深断屑式深孔加工循环功能。
每次钻孔深度的变化按等比级数实现,即每次减少的比例相等。
为保证加工效率,当钻孔深度减小到设定的最小值时,将不再减小(实际使用可以修改)。
1.概述如图1所示,Qn=Qn-1*#19,直到Qn=#1最小钻孔深度。
2.变量设置D(#7变量),每次提刀高度;F(#9变量),切削进给速度;Q(#17变量),初次钻孔深度;R(# 18变量),参考平面高度;S(#19变量),每次递减比例;T(#20变量),最小钻深比例;Z(#26变量),孔底深度。
3.宏程序流程图宏程序流程图如图2所示。
4.程序设计O0910;IF [#18EQ#0] GOTO6;深孔未赋值报警IF [#26EQ#0] GOTO6;R点未赋值报警IF [#17EQ#0] GOTO6;初次钻孔深度(Q)未赋值报警IF [#19EQ#0] GOTO6;每次递减比例(S)未赋值报警IF [#20EQ#0] GOTO6;最小钻深比例(T)未赋值报警IF [#4113EN3] GOTO6;主轴未转报警IF [#9NE#0 ] GOTO1;#9=#4109; F点未赋值取前面的F值N1 #30=#5003;保存初始平面(Z)值#31=#4003; 保存03组G代码(G90或G91)G00 Z#18; 快速趋近R点#27=#18-#26; 确定总深IF[#4003EQ91] THEN #27=-#26;#16=#17; 第一次钻孔深度#1=#20*#17; 确定最小钻深#27=#27-#16 第一次钻孔后剩余深度WHILE [#27GT0] DO1; 钻孔循环G91 G01 Z-#16 F#9; 变量钻孔G00 Z#7; 提刀IF [#16LE#1] GOTO2; 修正每次钻孔深度#16=#16*#19;IF [#16GE#1] GOTO 3;N2 #16=#1;N3 #27=#27-#16; 钻孔后剩余深度G01 Z-#7; 向下钻孔(一个提刀量)END1;#16=#16+#27; 恢复剩余量G01 Z-#16; 加工最后一段孔IF[#31EQ91] GOTO 4;G00 G90 Z#18; 绝对值方式返回R平面GOTO 5;N4 G00 Z-#26; 增量值方式返回R平面N5 IF[#4010EQ99] GOTO 7; 判断执行G98还是G99G90 G00 Z#30 返回初始平面GOTO 7;N6 #3000=10(ARGUMENT IS NOT ASSIGNED);NO.510报警,报警信息为自变量未赋值N7 M99;二、程序的固化与调用当程序调试准确无误后,取消系统参数保护,将程序存入O9000以后的程序下,恢复参数保护后固化成功。
机件加工中深孔的铰削工艺及技术分析

2 不 锈 钢 铰 削 加 工
采用 高速钢 时 . 切削速度 控制在 2 . 5 m r r d m i n : 硬质合 金则 尽量控 制在 1 0 . 5 m m / m i n .该公 司使用 的是 1 C r 1 8 N i 9 T i 材料 ;进给量控 制在 0 . 1 一O . 3 mm / r内: 切削深度为 0 . 1 5 mm ④铰削过程的控制 为保证铰削 的均匀 性 , 对刀齿 的跳 动量加 以严格控制 ; 同时仔 细 观察切屑形状 . 若 呈条状 . 意味着铰 削余量 过大 : 呈块状 , 意味着不 均 匀: 呈卷状 . 说明铰削余量较小。 此外 , 还做好 了切屑堵塞的预防工作 。 ⑤切削液和冷却方式 切屑容易粘 附不锈 钢 . 为解决此 问题 . 该公 司使用 硫化油作 为切 削液 . 为使表 面粗糙度进一步 降低 . 可在其 中适 量掺加 C C 1 4 或煤油 , 因前者对人体有害 , 选用后者。同时 , 采用 内冷却方式进行冷却 。
S c i e n c e& Te c h no l o g y Vi s i o n
科 技 视 界
科技・ 探索・ 争鸣
机件加工中深孔的铰削工艺及技术分析
解 贝 ( 扬 州大 学 , 江 苏 扬州 2 2 5 0 0 0 )
【 摘 要】 本 文首先 对深孔铰 削技 术及影响 因素做 了简单介 绍 , 分析 了其在机件加 工中的重要 意义 , 继而以不锈钢铰 削加工和 深孔振 动铰
定 的难 度 2 . 2 改进
1 深孑 L 铰削技术在 机件 加工 中的应用
铰削属于切削加工的一种 , 在钻孔、 镗孔 之后 , 通常会借助 铰刀将 孔壁的薄层金属切除 . 减少粗糙度 , 提 高孔径 的精确性 , 以获得想 要的 形状 。铰刀刃长齿多 . 刃齿同时工作 . 前端主要 负责切 削, 后端起 防震 校准作 。在机件 制造加工时 , 零件孔加 工以磨 、 钻、 铰、 拉、 镗、 扩为 主. 在尺 寸较小 的孔 精加工 中, 铰孔起 着重要作用 , 属 于二次精加 工 , 在批量零件生产 中很是适用 , 可用于铸铁 、 钢、 非铁金 属诸多材料 , 具 体 又可分 为 :①精 铰 加 工精 度可 达 I T 8 —6 ,可将 粗糙 度控 制 在 R M. 2 —0 . 0 8 1  ̄ m. 切 削深度为 O . O 6 —O . 3 a r m: ②粗 铰 。加 工精度 可达 I T 1 o . . 9 . 可将 粗糙度 控制在 R a 1 O 一1 . 2 m, 切削 深度 为 0 . 3 —0 . 8 m m 。 加上其生产效率较高 . 因此越来越受重视 影响铰孔质量的因素主要 有两个 : ① 铰刀。其质量及 表明精 度直 接影 响着铰孔质 量 . 所以在深孔铰 削过程 中. 首先要 合理选择铰 刀的 几何参数 , 包括其直径 、 齿数 、 刃带宽 、 前后角等 ; ② 铰削用 量。直接关 系着摩擦切 削力 . 进 而影响到加工精度 . 在铰削时 , 首先 , 铰削余 量要 适 中, 过 多或 过少都对铰孑 L 质量不利 ; 其次 , 要注 意切 削速度 , 根 据实 际要求加 以调整 : 此外 . 还有进给量 , 要综合前两者及其他要求确定 。
深孔加工技术
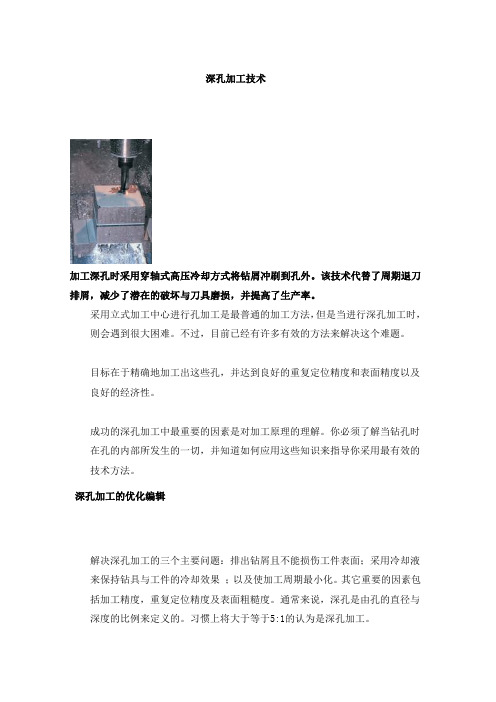
深孔加工技术加工深孔时采用穿轴式高压冷却方式将钻屑冲刷到孔外。
该技术代替了周期退刀排屑,减少了潜在的破坏与刀具磨损,并提高了生产率。
采用立式加工中心进行孔加工是最普通的加工方法,但是当进行深孔加工时,则会遇到很大困难。
不过,目前已经有许多有效的方法来解决这个难题。
目标在于精确地加工出这些孔,并达到良好的重复定位精度和表面精度以及良好的经济性。
成功的深孔加工中最重要的因素是对加工原理的理解。
你必须了解当钻孔时在孔的内部所发生的一切,并知道如何应用这些知识来指导你采用最有效的技术方法。
深孔加工的优化编辑解决深孔加工的三个主要问题:排出钻屑且不能损伤工件表面;采用冷却液来保持钻具与工件的冷却效果;以及使加工周期最小化。
其它重要的因素包括加工精度,重复定位精度及表面粗糙度。
通常来说,深孔是由孔的直径与深度的比例来定义的。
习惯上将大于等于5:1的认为是深孔加工。
钻屑必须足够小才能从钻槽中排出。
长的带状钻屑可以破坏表面精度并造成过早的刀具磨损与断裂。
冷却液必须到达刀具的顶端来保持钻具与工件的冷却,以及迫使钻屑从孔内排出。
稳固的设备结构与良好的减震性能以及很小的轴向跳动是获取加工精度,重复定位精度及表面粗糙度所必需的。
当然,合适的钻头几何形状可以使深孔加工更加高效。
控制钻屑的尺寸和形状一些材料形成了细小的钻屑,且能够通过钻槽容易地排出。
有些材料却形成长的带状钻屑。
一种控制钻屑尺寸和形状的方法是采用特殊的加工周期。
深孔加工与退刀相结合可以破碎钻屑,令其小的足以从钻槽排出,并且不会造成表面的损伤,可避免钻具的过早磨损。
一般来说,有两种深孔加工方法。
一种采用均分退刀深度来达到最终的深度。
另一种是不同的退刀深度,每次的深度逐步递减。
当冷却液不能到达深孔的底部时,切屑很可能堵塞了钻槽,使热量聚集而损坏钻具与工件。
大多数加工设备的控制系统提供了深孔加工的钻削加工,控制钻具钻入材料特定的距离后,从孔内完全退出,然后再钻入孔中。
15-5ph不锈钢深孔加工的改进

瓣塑姐.15-5PH不锈钢深孔加工的改进侯朋(中国一航导弹院,河南洛阳471009):一“j+j‘j j”|。
j j|”j|’。
‘”j j j:j j‘j j‘|。
j|1。
j’j’一j?’/隋耍]高速钢刀具在15-5PH不锈钢材料进行深孔加工时效率很低,通过工艺改进,选用硬质合金钻头。
优北切Sq参数,加工效率明显j、改善。
同时用硬厦舍金钻头加工孔的K',J-、形往公差和粗糙度迪敷高速钢刀具加工有辛交大改现,可以减少工步垂£量。
j p搠]15—5pH;硬质合金;切削参数15—5P H不锈钢属于沉淀硬化不锈钢,具有优异的力学性能,时效后抗拉强度1300M Pa。
在485时效后硬度提高到H R C40-47,同时变形非常小,除极少量高精尺寸外,都可在热处理之前加工到最终尺寸。
因此15—5PH不锈钢在我单位的产品中得到了广泛的应用。
某零件材质为15—5P H不锈钢,硬度H R C30-38,,零件上面两个巾5.1孔,深度34m m,长径比L/D约为7(>5属于深孔),孔径公差为+0.2m m,位置度要求0.1m m,孔壁相糙度Ral.6um。
该两孔加工效率很低,成为制约生产的瓶颈。
1材糊特性分析1)加工硬化严重。
与45挣钢相比,15—5P H不锈钢其相对/J O T 性约为03~050特别是热处理时效后,材料强度和硬度都较高,特别是深孔加工中.由于在切削条件不好,材料加工硬化,硬化层的出现会加剧刀具的磨损。
2)切削温度高。
切削15—5P H不锈钢时,其切削温度比45群钢约高200~30a℃。
主要原因:一是由于材料强度高,切削抗力大,消耗功率多;二是导热率低,只有45样钢的1/3;三是深孔加工时冷却和润滑不好,导致切削热导出较慢使切削区和刀面的温度升高。
刀具温度高,寿命就会变短。
3)容易产粘刀和生成积屑瘤。
因为15—5PH不锈钢的塑性好,粘附性强,容易使刀尖产生积屑瘤和后刀面产生附着物,影响已加工表面质量,难以得到光洁的表面。
深孔加工过程中振刀现象对零件加工的影响与对策
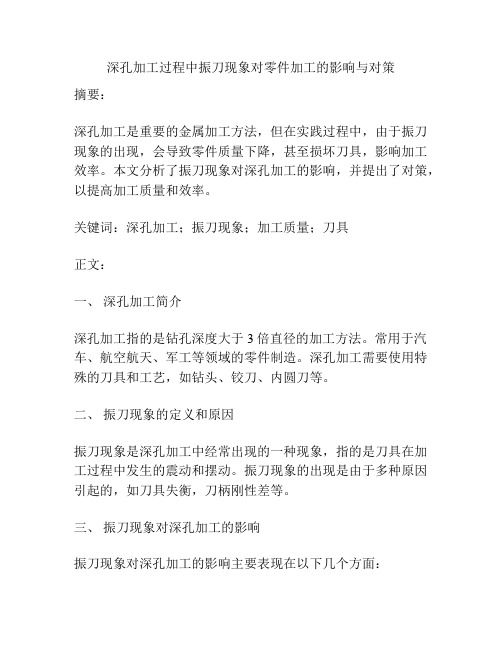
深孔加工过程中振刀现象对零件加工的影响与对策摘要:深孔加工是重要的金属加工方法,但在实践过程中,由于振刀现象的出现,会导致零件质量下降,甚至损坏刀具,影响加工效率。
本文分析了振刀现象对深孔加工的影响,并提出了对策,以提高加工质量和效率。
关键词:深孔加工;振刀现象;加工质量;刀具正文:一、深孔加工简介深孔加工指的是钻孔深度大于3倍直径的加工方法。
常用于汽车、航空航天、军工等领域的零件制造。
深孔加工需要使用特殊的刀具和工艺,如钻头、铰刀、内圆刀等。
二、振刀现象的定义和原因振刀现象是深孔加工中经常出现的一种现象,指的是刀具在加工过程中发生的震动和摆动。
振刀现象的出现是由于多种原因引起的,如刀具失衡,刀柄刚性差等。
三、振刀现象对深孔加工的影响振刀现象对深孔加工的影响主要表现在以下几个方面:1.加工质量下降振刀现象会导致加工精度下降,尤其是加工内表面时,会产生明显的划痕和毛刺,影响零件的装配和使用。
2. 刀具寿命短振刀现象会使刀具受到额外的力和压力,导致其寿命缩短,降低工具的经济效益。
3. 加工效率低振刀现象会使加工后表面质量不良,需要进行二次加工或修整,导致加工效率低下。
四、振刀现象的对策为了避免振刀现象对深孔加工带来的不良影响,可以采取以下对策:1. 选择质量好的刀具和机床选用结构更加稳定的刀柄和导杆,提高机床的刚性和稳定性。
2. 刀具动平衡在安装刀具之前进行动平衡,以使刀具更加平衡稳定。
3. 调整切削参数对切削参数进行优化和调整,减少切削压力和摩擦力。
4. 合理的切削液选择合适的切削液和加工液,降低运转温度,减少振动和摩擦力。
五、总结振刀现象是深孔加工过程中常见的问题。
采取上述对策可以有效减少振刀现象的发生,提高零件的加工质量和效率。
因此,在深孔加工中要重视振刀现象,采取措施避免其对加工过程的干扰。
六、深孔加工工艺优化除了对策外,深孔加工的工艺优化也是避免振刀现象的重要手段。
具体优化措施包括:1. 合理选择刀具和加工设备深孔加工的刀具和加工设备的质量对于减少振刀现象和提高加工效率起着至关重要的作用。
深孔加工走偏的测量与修复
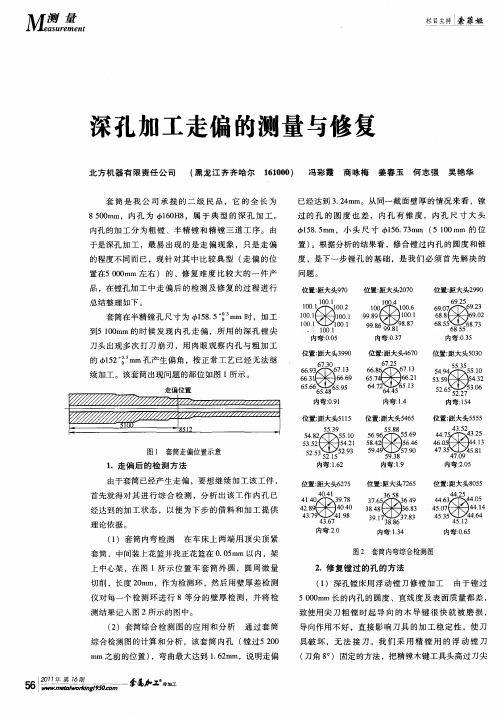
床 的借料后 ,即兼 顾 两 段 内孔 的 弯 曲 ( 内孔 的 弯 使 曲减 小到 可 以达 到进 行 下 道 工 序 的要 求 ) 又 保 证 了
接 合 部 位 的准 确 性 ,大 大 增 加 了 修 复 加 工 的 成 功 率。
5 .镗 孔 修 复 的实 现 过 程
内弯: 20
锥 度 ,经过 多 次空 上 刀 悬 臂 镗 进 行 修 正 ,但 接 合 的
部 位最 后 有 让 刀 台 ,尺 寸 口部 加 工 到 +18 3 m 5 . m,
内孔 已经镗 圆 。
3 9 24 3 8 34
.
3 2.
内弯: 7 20
内弯 :. 21 9
( ) 精镗修 复 过 程 由 于此 套 筒 的 内 弯还 不 是 2
( ) 套筒 综合 检 测 图 的应 用 和 分 析 通 过 套 筒 2 综 合检测 图 的计算 和 分 析 ,该 套 筒 内孔 ( 过520 镗 0 m 之前 的位置 ) m ,弯 曲最 大达 到 16r .2 m,说 明走偏 a
5i 薹 6
j l
参 . ’ ’蜘 『. 属工 工 一 1 。 栉
这样 可保 证 加 工 的表 面 粗 糙 度 。刀 具 本 身 耐磨 ,但 它 的弊端 是 容 易 让 刀 内孔 出 稍 。我 们 利 用 高 速 钢 刀
修镗一段 ( 大概 50 m长 ) 0m ,就换 浮动镗刀对高速
钢 刀 镗过 的孔 进 行 修 镗 ,已纠 正 内孔 的直 线 度 ,改 善 内孔 的表面粗 糙 度 。通过 利 用 高速 钢 刀 和合 金 刀 、 低 速 和高 速 镗 削 相 结 合 的 方 法 ,反 复 修 镗 ,最 终 使
内弯 : 6 5 1 0 位置 : 头 5 1 距大 l5 刀 具 : 刀 板
- 1、下载文档前请自行甄别文档内容的完整性,平台不提供额外的编辑、内容补充、找答案等附加服务。
- 2、"仅部分预览"的文档,不可在线预览部分如存在完整性等问题,可反馈申请退款(可完整预览的文档不适用该条件!)。
- 3、如文档侵犯您的权益,请联系客服反馈,我们会尽快为您处理(人工客服工作时间:9:00-18:30)。
2. 活塞杆的深孔加工
( 1 )加工零件特点 图 1 所示零件为某型天
是又连续换了一只高速钢钻头,又导致切削部位过 热烧蚀、退火。此时,已钻到800mm深处,就再也 无法进行下去了。 该工件完工日期迫在眉睫,即使花上几千元联 系外协加工,也没有哪个单位愿意承接。我们冷静 下来查找原因,现场分析,提出以下导致钻头损坏 的原因: 一是内排屑油压过小,钻杆排屑孔小且不圆,
T工 艺
echnique
栏目主持 赵宇龙
深孔加工技术改进
中国船舶重工集团公司第722研究所 (湖北武汉 430079) 杨德群 徐家品
孔的加工是机械加工中最常见的加工形式。当 长径之比大于 5 时,则为深孔加工。随着机械工业 的迅速发展、新型材料的出现、加工精度要求越来 越高,孔加工难度越来越大,深孔加工往往成为 “卡脖子”工序。因而充分了解和认识深孔加工的 原理及特点,对提高深孔加工的效率,保证产品质 量都是十件采用 45 钢 实体棒料经调质处理至硬度 220 ~ 255H B W 后制作 而成。加工前的毛坯尺寸为 150mm × 3 010mm , 要求在毛坯上加工一深盲孔,孔径为 65m m 、深 2 800mm,长径之比达43倍。 (2)原始工艺装备:最初 所采用的工艺装备:一是 55mm 钻 杆 , 其 内 孔 为 2 8 m m ; 二 是
64.95m m ,小于所钻出的孔径尺寸,硬质合
金导向起不到支承导向的作用,其间隙过大, 钻杆颤动,钻头的硬质合金撞击工件内壁,导 致硬质合金头崩刃或撞掉。
3. 加工改进措施
( 1 )工艺装备改进:在对已加工的孔进行了 认真的测量后,证明已钻的 800m m 深的孔及其孔 径大小不一,都偏大,最小为 65.20m m ,最大为
5. 结语
在科技高度发展的今天,新的材料,新的刀
图3 导向支承联接套
具,新的加工方法越来越多,应用越来越广,在满 足产品质量的前提下,如何运用合理的加工方法, 最大限度地提高生产效率将是我们永不改变的目 标。 (收稿日期:20121201)
( 2 )切削参数调整:在改进了工艺装备基础 上,又对切削参数进行了调整,即:提高主轴转 速、钻杆箱转速、加工切削速度,加大进给量,具 体调整值如附表所示。
65m m内排屑式镶硬质合金钻
头,如图 2 所示。然后用过渡接 头把钻头和钻杆联接在一起。 (3)原始加工方法:最初
图2 内排屑式 合金钻头
所采用的加工方法是:首先在卧式车床加工引孔
65.16mm × 190mm ,然后上深孔钻镗床,进行钻
孔。加工时,主轴箱主轴转速为112r/min,钻杆箱 转速为81r/min,工件与钻头相对转速为193r/min, 切削速度为 39.4m/m i n ;进给量为 13.51m m/m i n , 内排屑冷却油压为0.3MPa。 (4)问题:刚开始钻孔时还比较顺利,待 钻头在钻入 600m m 深后,钻杆发生颤抖;再钻到 740mm深时,钻头硬质合金镶块挤掉或崩刃。后来 连续换了两个钻头,也将硬质合金挤掉或崩刃。于
65.10mm。活塞杆内孔孔径检验合格。
4. 经验与体会
通过以上深孔加工中的成功实践我们总结出以 下几点经验和体会: ( 1 )进行深孔加工,关键是引孔的加工,引 孔的尺寸应比钻头大 0.01 ~ 0.03m m ,表面粗糙度 值为Ra=3.2μm。 ( 2 )导向套的木质导向键最好比钻头的实际 尺寸大 0.20m m ,可减少摩擦力,又可真正起到支 承导向的作用。 (3)为了使排屑顺畅,油压选0.4~0.6MPa为 宜。 ( 4 )切削速度为 60 ~ 85m/m i n ,给进量应为 0.009 ~ 0.15m m/r 。这条经验在加工过程中体会最 深,当切削速度和给进量增加到以上范围时,反而 切削平稳,加工十分顺畅。 通过对工件特性的分析,正确选取合适的装夹 方法、刀具材料、主要几何参数及切削用量,可以 很好地解决深孔加工中由于切削力和切削热的影 响,并且在保证工件加工质量的前提下,提高生产 效率。
图1 活塞杆
2013年 第7期
使排屑困难,切屑滞流在钻头切削部位,导致硬质
32
冷加工
T工 艺
echnique
合金钻头切削部位挤掉或挤裂。 二是钻头的硬质合金导向部分尺寸为
切削参数调整表
主轴转速 钻杆箱转速 相对转速 切削速度 进给速度 油压 /r·min-1 /r·min-1 /r·min-1 /m·min-1 /mm·min-1 /MPa 原始 状态 改进后 状态 112 140 81 170 193 310 39.4 63 13.51 32 0.3 0.4
1. 深孔加工的特点
由于深孔加工是在封闭状态下进行的,加工过 程中无法观察其切削状态,故有其独特的特点,具 体如下: ( 1 )不能直接观察到刀具切削情况,只能凭 经验、听声音、看切屑、观察机床负荷和压力表、 触摸振动等来判断切削过程是否正常。 ( 2 )切削热不易传散,须采取强制有效的冷 却方式。 ( 3 )切屑不易排出,需要控制切屑长短和形 状,并进行强行排屑。 ( 4 )工艺系统刚性差,由于孔的长径之比较 大,钻杆细而长,因而支承导向极为重要。
( 3 )改进后加工:在加工过程中钻杆振动较 大,是因为木键太紧,与孔壁摩擦力较大引起的, 但切屑排出较为流畅,切屑为“马蹄状”,剩下 的2m长的深孔仅用了70min就完成了。当退出钻头 时,钻头完好无损,测量退出后的导向木键尺寸为
66.20m m 。经分析认为,钻头的损坏是钻头导向
块未起到导向支承作用,且与切削前速度低、进给 量小而导致钻削时失稳、钻杆颤动有关。 于是,在原有工艺装备基础上进行了改进,具 体做法如下: 针对已经加工出的800mm深的孔,在车床上用 木键支承的方式,将其扩镗至 65.6mm,使孔径差 异减小,从而使其导向键真正起到支承导向的作 用。 用调质处理后的45钢制作一个导向支承联接套 (见图 3 ),并采用桦木材料做导向键。木键的导 向支承直径为 65.9mm,使其能紧贴管壁,经浸油 膨胀后,更能起到支承导向作用。