硫回收装置开车方案
脱硫工序开车方案
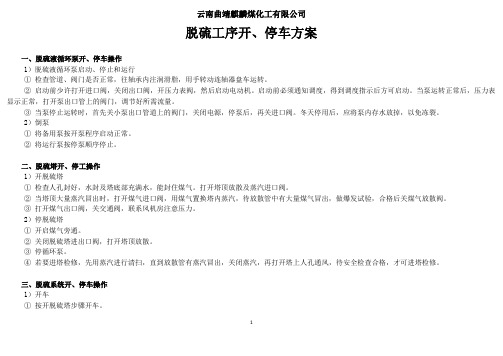
云南曲靖麒麟煤化工有限公司脱硫工序开、停车方案一、脱硫液循环泵开、停车操作1)脱硫液循环泵启动、停止和运行①检查管道、阀门是否正常,往轴承内注润滑脂,用手转动连轴器盘车运转。
②启动前少许打开进口阀,关闭出口阀,开压力表阀,然后启动电动机。
启动前必须通知调度,得到调度指示后方可启动。
当泵运转正常后,压力表显示正常,打开泵出口管上的阀门,调节好所需流量。
③当泵停止运转时,首先关小泵出口管道上的阀门,关闭电源,停泵后,再关进口阀。
冬天停用后,应将泵内存水放掉,以免冻裂。
2)倒泵①将备用泵按开泵程序启动正常。
②将运行泵按停泵顺序停止。
二、脱硫塔开、停工操作1)开脱硫塔①检查人孔封好,水封及塔底部充满水,能封住煤气。
打开塔顶放散及蒸汽进口阀。
②当塔顶大量蒸汽冒出时,打开煤气进口阀,用煤气置换塔内蒸汽,待放散管中有大量煤气冒出,做爆发试验,合格后关煤气放散阀。
③打开煤气出口阀,关交通阀,联系风机房注意压力。
2)停脱硫塔①开启煤气旁通。
②关闭脱硫塔进出口阀,打开塔顶放散。
③停循环泵。
④若要进塔检修,先用蒸汽进行清扫,直到放散管有蒸汽冒出,关闭蒸汽,再打开塔上人孔通风,待安全检查合格,才可进塔检修。
三、脱硫系统开、停车操作1)开车①按开脱硫塔步骤开车。
1②将溶液循环槽内充满脱硫液。
③打开溶液循环槽出口阀。
④开溶液循环泵,同时密切注意溶液循环槽液位,并及时补充溶液。
⑤调节溶液循环量达到工艺指标,当脱硫液返回溶液循环槽后,保持槽内液位在1/2~2/3。
⑥工序正常运转一段时间后,打开压缩空气、泡沫槽及泵、熔硫釜依次开始运行。
2)停车①开启煤气旁通。
②关闭脱硫塔进出口阀,打开塔顶放散。
③停压缩空气。
④停溶液循环泵,关闭泵进出口。
⑤打开再生塔,放空至事故槽。
⑥通蒸汽吹扫,大量蒸汽冒出后,关闭蒸汽。
2脱硫工序工艺流程图3脱硫工序简明工艺流程简明工艺流程:来自粗苯系统的粗煤气串联进入脱硫塔下部与塔顶喷淋下来的脱硫液逆流接触洗涤,吸收煤气中的H2S、HCN等物质,脱除硫化氢、的煤气经净煤气管送到各用户及外供。
脱硫系统开车处置措施方案

脱硫系统开车处置措施方案背景介绍燃煤发电站是我国主要的能源发电方式,但是在燃煤过程中会产生大量的二氧化硫气体,这对环境和人体健康都会造成很大的危害。
为了减少二氧化硫的排放,燃煤发电站通常都会配置脱硫系统,用于将二氧化硫转化为硫酸盐,进而实现减排效果。
但是,当脱硫系统出现异常时,就需要进行开车处置,以保证系统的正常运行。
开车处置措施在脱硫系统出现异常时,需要进行开车处置措施以确保系统的安全运行。
具体的处置措施如下:1. 关闭进料阀门当脱硫系统出现异常时,首先需要关闭进料阀门。
这可以防止原料继续输入,进而防止二氧化硫气体继续产生,从而避免危害环境和人体健康。
2. 停止循环泵在关闭进料阀门之后,需要停止循环泵的运行。
这样可以防止硫酸盐溶液在系统中滞留,进而导致系统堵塞或者出现其他问题。
3. 停止石膏输送泵与停止循环泵类似,停止石膏输送泵的运行也是为了防止石膏溶液在系统中滞留,进而导致系统堵塞或者出现其他问题。
4. 排放管道中的气体在关闭进料阀门、停止循环泵和停止石膏输送泵之后,需要排放管道中的气体。
这可以将残留在管道中的气体完全排出,防止在开车过程中对人员和环境造成危害。
5. 进行系统检查在排放管道中的气体之后,需要进行系统检查。
此时,应该检查系统的阀门、泵、管道等部件是否存在异常,是否需要修理或更换。
只有当系统完全处于正常工作状态时,才能继续投入使用。
结论脱硫系统是燃煤发电站中必不可少的部分,它对减少二氧化硫排放具有重要的作用。
当系统出现异常时,应该立即进行开车处置措施,以确保系统的安全运行。
要想保证开车处置措施的顺利进行,需要提前做好相关的准备工作,保证人员和设备的安全。
脱硫开车方案

某某锅炉厂
脱硫装置开车方案
编制:
审核:
批准:
2013年5月30日
1、目的
为加强腾达锅炉厂脱硫装置开车工作管理,明确开车工作任务和职责,规范开车程序,使脱硫开车工作有组织、有计划、安全、顺利地进行,特制定本方案。
2、脱硫开车领导小组
3、脱硫开车前的准备工作
1、准备好相应的开车器具和材料。
2、石灰石粉仓内有一定料位,便于制浆。
3、各挡板门、电动阀手动实验、电动实验开关灵活。
4、确认各循环水、压缩空气用点流通。
5、各仪表完好备用,CEMS完好备用。
6、转动设备盘车灵活,无卡涩现象。
7、投相关设备启动保护联锁。
8、工艺水具备使用条件。
9、各人员到位,脱硫具备开车条件。
4、脱硫开车步骤。
原始开车方案
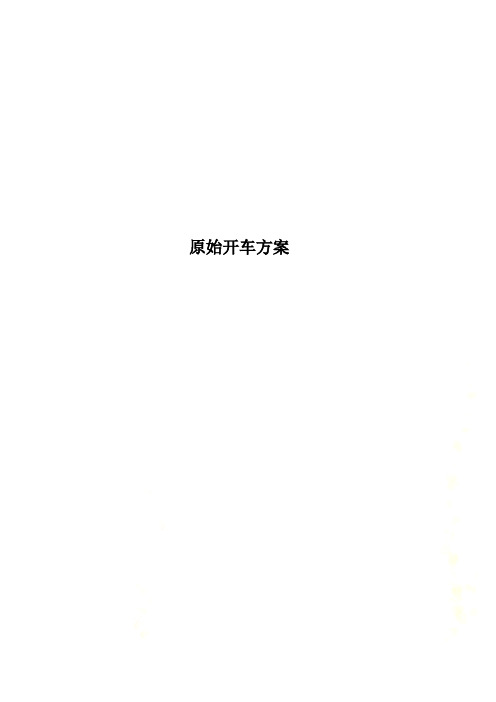
原始开车方案目录目录 1 第一章一次脱硫原始开车方案 7 第一节目标 7 第二节组织机构 7 第三节开车前应具备的条件和准备工作 7一、应具备的条件 7二、准备工作 8 第四节具体操作步骤 8一、系统吹扫清理 8二、系统气密试验 9三、清洗及水联动试车方案 9四、栲胶溶液配制 10五、系统置换 10六、开车步骤 11七、安全注意事项及应急措施 12 第二章变换系统原始开车方案 12 第一节目标 12净化车间原始开车方案2 / 73第二节组织机构 13 第三节开车前应具备的条件和准备工作 13一、应具备的条件 13二、准备工作 14第四节具体操作步骤 14一、变换工艺管线吹扫 14(一)吹除具备条件 14 (二)准备工作 14 (三)吹扫 15二、安全注意事项及应急措施 16 第五节变换系统气密性试验 16一、准备工作及具备条件 16二、气密性试验 17三、安全注意事项及应急措施 17第六节变换系统置换 18一、具备条件 18二、置换步骤 18三、安全注意事项及应急措施 19第七节升温硫化 19一、概述 19净化车间原始开车方案3 / 73二、准备工作及具备条件 19三、硫化原理 20四、升温硫化 21五、升温硫化工艺指标 24六、注意事项及应急措施 24 第八节变换系统开车 25一、开车前准备工作和具备条件 25二、开车步骤 25三、安全注意事项及应急措施 26 第三章二次脱硫系统开车方案 26 第一节目标 26 第二节组织机构 27 第三节开车前准备工作和具备条件 27 第四节工艺管线吹扫 27一、吹除具备条件 27二、准备工作 28三、吹扫步骤 28四、安全注意事项及应急措施 29 第五节二次脱硫系统气密性试验 29一、准备工作及具备条件 29净化车间原始开车方案4 / 73二、气密性试验 30三、安全注意事项 30 第六节二次脱硫系统置换 30一、具备条件 30二、置换步骤 31三、安全注意事项及应急措施 32 第七节清洗、水联动试车 32一、碱洗的目的32二、水联动试车的目的 32三、应具备的条件 32四、制备清洗溶液 33五、循环清洗及水联动试车 33六、安全注意事项及应急措施 34 第八节溶液的制备 34 第九节系统开车 35 第四章变换催化剂等装填方案 35一、装填时所具备的条件 35二、装填的准备工作 36三、装填量 36净化车间原始开车方案5 / 73四、装填操作 37(一)装填方法 37(二)装填的要求 38五、安全注意事项及应急措施 39第五章脱碳开车方案 40第一节组织机构 40第二节脱碳工艺管线吹扫 40一、吹扫的目的 40二、准备工作和具备条件 41三、吹扫程序 41(一)提纯段 41(二)净化段 45四、安全注意事项及应急措施 48第三节脱碳系统气密性试验方案 48一、设备概况 48二、具备条件 49三、净化段试压查漏 49四、提纯段试压查漏 50五、各条管道试验压力 53(一)净化段试验压力 53净化车间原始开车方案6 / 73(二)提纯段试验压力 53六、安全注意事项及应急措施 54 第四节提纯和净化装置的置换 55一、置换用气 55二、置换的目的 55三、具备的条件和准备工作 55四、置换步骤 55(一)提纯吸附塔区、对应管道及其相连缓冲罐的置换 56 (二)净化吸附塔区、对应管道及其相连缓冲罐的置换 57五、置换要求和安全注意事项及应急措施 58 第五节脱碳系统开车 58一、开车前的准备及具备条件 58二、开车步骤 59 第六章吸附塔吸附剂装填方案 60一、工程概况 60二、装填准备工作 60三、装填步骤 61(一)提纯段装填 61 (二)净化段装填 61四、安全注意事项及应急措施 62净化车间原始开车方案7 / 73第七章原始开车安全注意事项 63一、试压 63二、置换 63三、开车 63 附:1、提纯段吸附塔吸附剂装填示意图 652、净化段吸附塔吸附剂装填示意图 663、中温水解剂装填示意图 674、预变炉装填示意图 685、干法脱硫槽装填示意图 696、精脱硫槽装填示意图 707、净化炉装填示意图 718、变换炉催化剂装填示意图 729、变换催化剂升温曲线图 73第一章一次脱硫原始开车方案第一节目标本方案的目标:1、对系统进行全面清洗,去除系统内的杂质,脱除设备及填料安装时带进的油脂,同时对动设备进行带负荷试车,暴露设计和安装中的一些问题。
脱硫工段开车方案
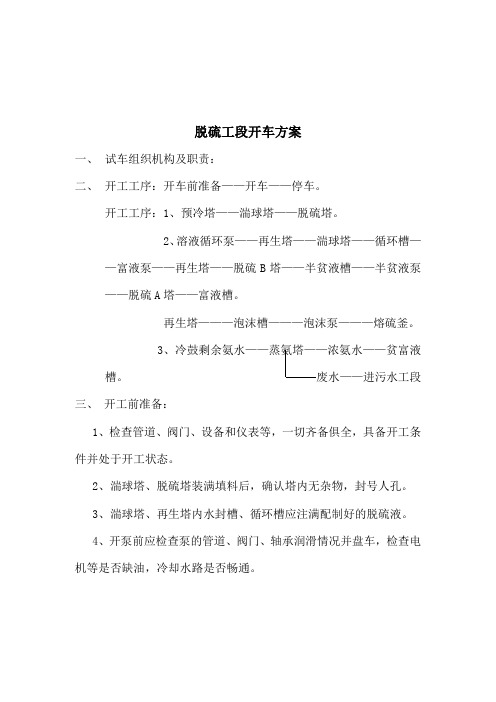
脱硫工段开车方案一、试车组织机构及职责:二、开工工序:开车前准备——开车——停车。
开工工序:1、预冷塔——湍球塔——脱硫塔。
2、溶液循环泵——再生塔——湍球塔——循环槽——富液泵——再生塔——脱硫B塔——半贫液槽——半贫液泵——脱硫A塔——富液槽。
再生塔———泡沫槽———泡沫泵———熔硫釜。
3、冷鼓剩余氨水——蒸氨塔——浓氨水——贫富液槽。
废水——进污水工段三、开工前准备:1、检查管道、阀门、设备和仪表等,一切齐备俱全,具备开工条件并处于开工状态。
2、湍球塔、脱硫塔装满填料后,确认塔内无杂物,封号人孔。
3、湍球塔、再生塔内水封槽、循环槽应注满配制好的脱硫液。
4、开泵前应检查泵的管道、阀门、轴承润滑情况并盘车,检查电机等是否缺油,冷却水路是否畅通。
5、预冷塔冷凝液槽应注满水。
6、检查蒸氨系统管道、设备和泵类完好,蒸汽、碱液和氨水充足。
7、检查并关闭放硫阀门,打开熔硫釜清夜阀,打开泡沫泵进口阀和熔硫釜进料阀。
8、预冷塔、湍球塔、脱硫塔逐个用蒸汽置换空气,煤气置换蒸汽。
9、放散管冒出大量煤气后,做爆发实验合格后关闭各塔放散,逐步关小蒸汽,开打煤气,全开煤气进口阀出口阀,关严蒸汽阀。
最后关闭旁通阀。
10、先开煤气系统,再开溶液系统、蒸氨系统,泡沫槽有大量泡沫产生并至1/2处时,启动泡沫泵熔硫。
开工:1、接到总指挥指令后,首先置换煤气合格,阀门处于正确开闭状态。
2、预冷塔循环水、制冷水运行正常,出口温度控制在规定范围内。
3、开启冷凝液泵,喷洒回流正常。
4、各塔煤气下液管道畅通,水封注满水,防止煤气外泄。
5、启动溶液泵、贫富液泵,逐步加大循环量,调节好再生器液位,直至循环正常。
6、开蒸氨塔底的直接蒸汽,调节好蒸汽量,用循环水控制好塔顶温度和塔底废水含氨量。
7、启动碱液泵,控制好蒸氨废水PH值,NH3-N量。
8、开蒸氨浓氨水的制冷水流量,浓氨水温度合乎技术规范。
9、启动废水泵,通知污水接受蒸氨废水。
10、每班进行一次脱硫液成分化验,保证脱硫效果良好,指标控制在规定范围内。
KCA脱硫系统开车操作规程

KCA脱硫工程开车操作规程一、开车前的必备条件1、全部设备、管道、阀门、仪表安装完毕,而阀门的盘根需全部检查或更换,且开关灵活可靠。
2、水、电、汽供应及照明灯光正常。
3、化工原料备足。
4、记录本及报表、文具及操作工具(如开阀门扳手)备好,消防器材备好。
5、设备内外清扫干净,各塔、槽内壁用水冲洗并排空。
6、室内外场地清理干净。
7、操作人员经培训合格。
二、试压试漏用罗茨机往脱硫塔送空气补压至7KPa,检查脱硫塔及有关管道、阀门有无泄漏,保压一天,观测其气密性如何,直至验收合格为准。
三、脱硫塔及管道中空气的置换可用蒸汽进行置换,但要求填料耐温>130℃,直至脱硫塔及管道中含O2<0.5%为合格。
四、单体试车(可与试漏试压同时进行)1、各泵电机连续空转四小时,看其是否正常。
2、搅拌机空转四小时,看其是否正常。
五、联动试车1、优先把富液槽安装清理完毕,往槽内灌软水~800m3(液位高~6m)。
2、开富液泵往喷射再生槽送液,待贫液槽有半槽液,同时并继续向富液槽酌补软水,再开贫液泵往脱硫塔送液,调节泵流量,使之正常循环,液位稳定,然后对全系统的设备、管道、阀门、仪表及取样点进行全面检查。
如发现缺陷或故障则停车消除,直到完全达到要求为止。
要连续正常运转八小时以上。
查项目包括:(1)各贫、富液泵轮流开动,先各开一台,后各开两台。
看其电机及轴承是否超温,电机及泵是否有异响;大富液泵出口压力~0.55MPa,大贫液泵出口压力~0.36MPa,小富液泵出口压力~0.58MPa,小贫液泵出口压力~0.43MPa时,电流是否超高。
(2)硫泡沫泵及配液泵也按前法试转。
(3)硫泡沫槽灌水2/3槽后开动搅拌机,检查电机及轴承是否超温或有异响,电流是否超高。
(4)根据开贫、富液泵台数调整开喷射器支数(各开一台大泵时开喷射器~16支;各开一大一小泵时,开喷射器~22支)使富液泵出液压力≥0.55MPa。
逐支检查各喷射器抽吸力,看其有无倒喷。
烟气脱硫系统开车、运行方案(简化版)
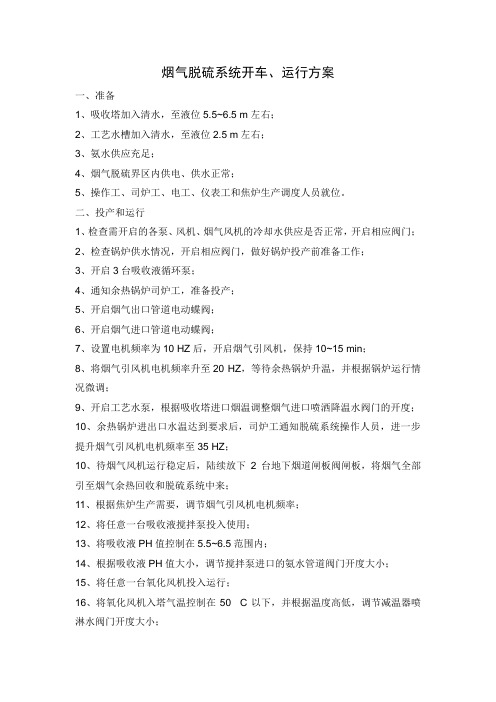
烟气脱硫系统开车、运行方案一、准备1、吸收塔加入清水,至液位5.5~6.5 m左右;2、工艺水槽加入清水,至液位2.5 m左右;3、氨水供应充足;4、烟气脱硫界区内供电、供水正常;5、操作工、司炉工、电工、仪表工和焦炉生产调度人员就位。
二、投产和运行1、检查需开启的各泵、风机、烟气风机的冷却水供应是否正常,开启相应阀门;2、检查锅炉供水情况,开启相应阀门,做好锅炉投产前准备工作;3、开启3台吸收液循环泵;4、通知余热锅炉司炉工,准备投产;5、开启烟气出口管道电动蝶阀;6、开启烟气进口管道电动蝶阀;7、设置电机频率为10 HZ后,开启烟气引风机,保持10~15 min;8、将烟气引风机电机频率升至20 HZ,等待余热锅炉升温,并根据锅炉运行情况微调;9、开启工艺水泵,根据吸收塔进口烟温调整烟气进口喷洒降温水阀门的开度;10、余热锅炉进出口水温达到要求后,司炉工通知脱硫系统操作人员,进一步提升烟气引风机电机频率至35 HZ;10、待烟气风机运行稳定后,陆续放下2台地下烟道闸板阀闸板,将烟气全部引至烟气余热回收和脱硫系统中来;11、根据焦炉生产需要,调节烟气引风机电机频率;12、将任意一台吸收液搅拌泵投入使用;13、将吸收液PH值控制在5.5~6.5范围内;14、根据吸收液PH值大小,调节搅拌泵进口的氨水管道阀门开度大小;15、将任意一台氧化风机投入运行;16、将氧化风机入塔气温控制在50 °C以下,并根据温度高低,调节减温器喷淋水阀门开度大小;17、将吸收液温度控制在55~60 °C以内;18、根据吸收液温度,决定是否将螺旋板换热器投入使用,并依据吸收液温度调整冷却水阀门开度大小;19、注意观察吸收塔液位高度,正常操作时将液位控制在7.5~8.0 m,最大液位为8.5 m,超过8.5 m后,吸收液开始溢流,至地下槽;20、吸收塔液位高时,可将烟气进口喷淋降温水切换为吸收液管线,也可外排部分吸收液;21、吸收塔液位低时,可将烟气进口喷淋降温水切换为工艺水管线,也可开启水洗泵至吸收塔的电动补水阀向吸收塔补水;22、吸收塔顶部除雾层,每班冲洗1~2次,每次每层15秒,每次共冲洗1分钟;23、定期测试吸收液密度,比重超过1.2时即可外排硫酸铵溶液,先通过搅拌泵出口旁路送至硫铵溶液贮槽,再通过硫铵溶液输送泵送至化产硫铵工段。
硫磺回收装置操作手册A
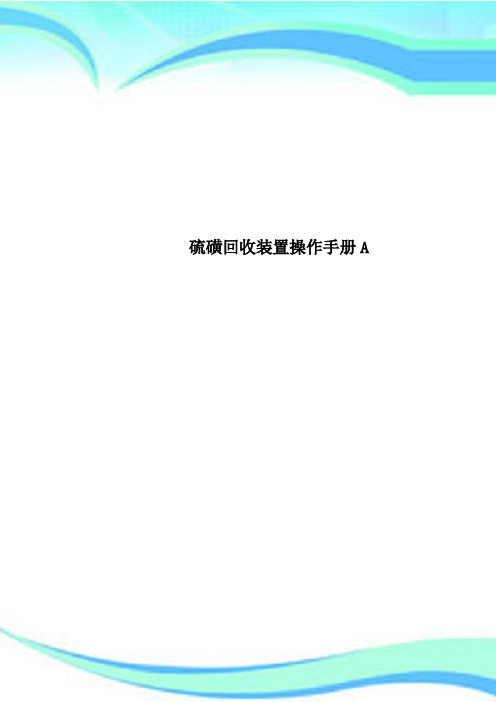
硫磺回收装置操作手册A————————————————————————————————作者: ————————————————————————————————日期:8万吨/年硫磺回收装置工艺手册目录1 前言2 概述2.1 装置组成2.2 设计基础2.3 设备3工艺流程3.1 硫回收部分工艺说明3.2 尾气处理部分工艺说明3.3 胺液再生部分工艺说明3.4 液硫脱气及液硫成型部分工艺说明4 工艺原理及操作条件4.1工艺原理4.2主要操作条件5 装置开工前的准备5.1 系统及设备检查5.2 单机试运行5.3系统清扫5.4 煮炉操作5.5 烘炉和烘器5.6 催化剂装填5.7 水联运5.8 系统吹扫和系统气密6装置开车操作程序6.1系统升温6.2硫回收部分开车6.3尾气净化系统的生产准备6.4尾气加氢催化剂预硫化6.5装置的正常运行7装置停车操作程序7.1装置停工操作7.2制硫部分系统吹扫7.3尾气处理系统吹扫和尾气加氢催化剂钝化7.4急冷水系统和胺液系统的处理8 装置故障停工操作8.1急冷水系统和胺液系统的处理8.2 故障停工操作9 长期停工的维护10安全、环保、健康技术规定1 前言本工艺手册仅适用于海南炼化续建项目8万吨/年硫磺回收装置。
本工艺手册提供了硫磺回收装置总的操作指南。
在本装置工作的所有操作人员和维护人员都要经过良好的培训和熟悉所有的设备,并能熟练地操作和维护、维修。
在装置的实际运行过程中,对于可能出现的各种问题和情况,工艺手册不可能全部预见到并包括进去。
由于原料性质是变化的,操作条件可能相应变化,因此,工艺手册中叙述的所有条款,都要经过试运行和装置实际操作经验加以修正,才能适应生产情况的变化。
2 概述2.1装置组成硫磺回收装置由制硫、尾气处理、液硫脱气、尾气焚烧及液硫成型五部分组成。
2.2设计基础2.2.1装置能力装置能力:硫化氢富气的流量大约为9900Nm3/h;硫磺产量约为79200吨/年。
硫回收操作规程..
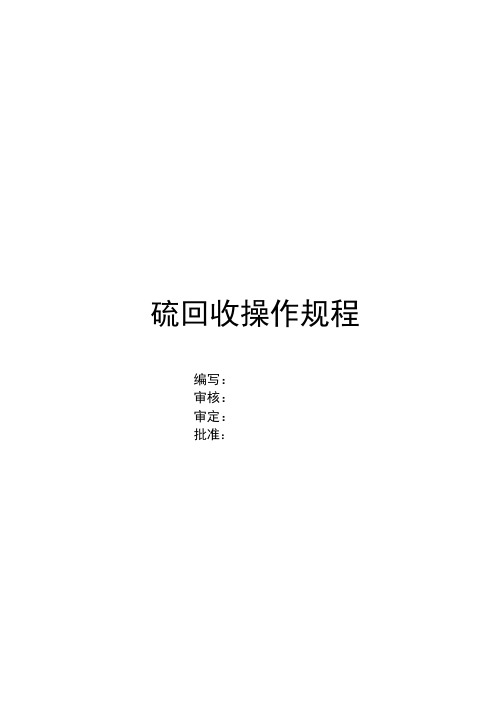
硫回收操作规程编写:审核:审定:批准:目录第一章: 工艺说明 (1)1.岗位任务 (1)2.管辖范围 (1)3.工艺原理 (1)4.工艺流程 (3)5.工艺联锁说明 (7)第二章:岗位操作法 (20)一.开车 (20)二.停车 (55)三.正常操作要点及注意事项 (61)四.硫磺回收装置故障分析 (66)五.紧急情况处理 (68)第三章:转动设备开停车及关键设备维护 (72)1.转动设备的开车 (72)2.转动设备停车 (74)3.关键设备维护 (75)第四章:安全技术要点及保安措施 (79)1.有毒有害气体性质 (79)2.保安措施 (80)第五章:工艺管理制度 (81)1.岗位责任制 (81)2.交接班制度 (82)3.设备维护保养制度 (83)4.巡回检查制度 (83)5.质量检查制度 (84)附表 (86)附表1:1223单元安全阀一览表 (86)附表2:1223单元工艺操作参数一览表(温度) (87)附表3:1223单元工艺操作参数一览表(压力) (90)附表4:1223单元工艺操作参数一览表(液位) (93)附表5:1223单元工艺操作参数一览表(流量) (95)附表6:取样分析一览表 (98)附表7:调节阀一览表 (99)附表8控制按钮、控制器 (101)附表9:1223单元设备一览表 (103)第一章: 工艺说明1.岗位任务本岗位的任务是将低温甲醇洗工序送来的酸性气体,通过燃烧氧化,部分H2S转化成SO2,然后H2S 与SO2经两级常规克劳斯催化反应和一级超优克劳斯催化反应、一级超级克劳斯催化反应,转化成单质硫。
通过硫磺造粒机生产纯度为99.9%(wt)的硫磺颗粒,包装出售;克劳斯尾气再经焚烧炉燃烧,H2S 完全燃烧转化成SO2,焚烧后的尾气经烟囱高空排放,保证排放到大气中的气体指标合格,符合环保要求。
2.管辖范围(1).塔C-2301,共1台(2).废热锅炉、换热器E-2301,E-2308、E-2302/03~E-2307,E-2309~E-2314共12台(3). 槽罐类V-2301~V-2307,共12台(4). 机泵类P-2301A/B~P-2303,K-2301A/B,共7台(5). 炉子F-2301(烧嘴),F-2302(烧嘴),F-2303,F-2304,共4台(6). 反应器R-2301/02/03/04,共1台(7). 其他:J-2301,X-2301,X-2302A/B,X-2303 共5台上述设备及设备的附属管线、阀门及仪表等。
硫回收联动试车方案

硫回收联动试车一、装置原始开车前的准备:原始开车即新装置建好后第一次试运行过程。
1. 系统检查:1)检查工艺管道,确认工艺管道安装是否符合流程和安装图的要求;2)检查公用工程管道,确认公用工程管道安装是否符合流程图和安装图的要求;3)检查伴热管道和夹套管道,确认蒸汽管道安装是否符合安装图和操作使用要求;4)系统检查,确认管道介质流向、阀门和调节阀的安装位置及流向准确无误;确认管道上的温度、压力、流量仪表的安装位置及流向准确无误;确认管道附件如盲板、放空阀、管道支撑、过滤器、消音器、采样器等的安装位置准确无误。
5)液硫封中回装硫磺,并已熔化,所有蒸汽伴热管道已经打通。
2. 设备检查1)工艺设备检查外部检查确认设备的平台、围栏、梯子、保温、涂漆等符合要求;内部检查,必须在该设备外部有专职监护人的情况下进行。
确认设备内件的安装准确无误;设备内没有遗留物;设备内没有机械杂质;外部附件检查,确认安全阀、放空阀、温度仪表、压力仪表、液面仪表及其它外部附件的安装准确无误。
2)机动设备检查整体检查,确认设备基础符合设计要求、地脚螺栓牢固、劳动保护罩完整、铭牌及涂漆完好、附属管道附件安装准确无误,且各运转设备单体试车正常。
润滑系统检查,确认润滑系统安装施工无误;确认润滑油牌号与设备润滑要求一致;确认润滑油的过滤和加注程序符合规定;确认加注的润滑油量和油位符合要求。
3.其它检查1)检查装置区的安全、消防设施,确认完好无损;2)检查装置区内的场地、卫生,确认达到操作条件;3)确认设备、管道试压及化学清洗(煮炉)余热锅炉已经完成;4)确认电路安装、电路保护及继电器预校、电动机与机械的联结和调整已经完成;5)确认仪表安装和试压、仪表调校、控制系统/安全系统/报警系统的调校已经完成;6)确认排水系统畅通无阻;7)确认所有设备的接地系统符合要求;8)已备好开车各类曲线图;9)人员准备:所有操作人员都具有压力容器操作证和安全作业证,完全具备克劳斯硫回收上岗要求。
克劳斯硫回收原始开车方案

原始开车1烘炉1.1 烘炉目的:大修后或新开工的炉子,需脱除耐火衬里的水份和结晶水,使耐火材料达到一定强度,并让炉体各部位在热状态下的设备情况能满足工艺生产要求。
1.2 烘炉步骤:1.2.1 本燃烧炉烘炉曲线规定如下;a)升温到120□,升温速度15□∕h,需用时间8h;b) 120□上保温32h;c) 120口升温至U300口,升温速度10□∕h,需用时间18h;d) 300□上保温32h;e) 300□升温至∣J5OO□,升温速度10口∕h,需用时间20h;f) 500□上保温20h;g) 500□升温至∣J8OO□,升温速度25口∕h,需用时间12h;h)在800□上保温8ho全部烘炉过程累计时间150h,烘炉完成后,应自然冷却。
1.2.2 做好点火准备,按点火规程进行点火。
1.2.3 火点着后,利用燃料气和空气量来调节升温速度;1.2.4 绘制实际升温曲线;3.4.2点火操作燃烧炉系统包括:主风机、燃烧炉、废热锅炉及汽包,点火前必须系统试压、试漏、吹扫、清洗合格后才能点火运行。
3.3.4.2.1 点火前的准备:a)各设备及仪表正常且处于备用状态。
b)开工烟囱畅通,E2301出口阀已关闭。
c)关闭FV2321,将N2引至炉前备用。
d)启动风机,打开FV2315并关闭E2311出口阀将空气炉前放空备用;e)关闭FV2322将燃料气引至炉前(经分析氧含量小于0.5%方合格),并将压力保持在0.2〜0.3MPa;f)对废热锅炉先用低压蒸汽预热,待点火正常约15分钟左右,加水建立废热锅炉液位。
然后打开V2305放空阀,关闭PV2326;g)打开FV2321,用N2置换炉内至CO+H2<0.5%; h)打开系统伴热蒸汽,并排放冷凝水;D打开点火所需电磁阀。
3.3.4.2.2 点火燃烧炉点火操作通常在就地点火控制柜(见YKGR-K01)上进行:3.3.4.2.2.1 开点火控制柜电源按钮(36),电源指示灯(37)亮;3.3.4.2.2.2 燃烧炉在其各个参数检测正常后,检测风门控制挡板位置,处于关闭位置时,可启动风机;3.3.4.223 启动后,柜上启动联锁灯(35)亮;3.3.422.4 操作点火开关(38)到扫风位置,吹扫中灯(23)亮;3.3.422.5 五分钟后,吹扫完成,吹扫中灯(23)灭;3.3.422.6 燃烧炉点火灯(25)亮;3.3.422.7 操作点火开关(38)1切到点火位置;3.3.422.8 点火燃料气切断阀开灯(26)亮;3.3.422.9 火焰正常灯,(31)亮;3.3.422.10 燃料气调节阀最小位置灯(32)亮;3.3.422.11 11燃料气切断阀开灯(29)亮;3.3.422.12 操作点火开关(38)切到运行位置,点火燃料气切断阀关灯(27)亮。
能源公司甲醇部硫回收尾气增压机操作规程

能源公司甲醇部硫回收尾气增压机操作规程1.开车前准备1.1.检查压缩机原始记录1.2.了解压缩机运转情况,确认压缩机正常完好时方可进行开车准备。
1.3.检查机身油池和注油器油位,向润滑部位注油4.机身油池和注油器油位应处在最高油位处,启动辅助油泵和注油器,向运动机构和气缸填料部位注入润滑油,并观察油压、油温及油流动是否畅通。
1.5.开启冷却水进出口总管及各支管阀门使冷却系统通水1.6.通过各回水管视水窥镜,观察水流动情况,检查冷却系统中的水压、水温是否符合规定要求。
1.7.检查气管路中阀门及气量调节装置的开闭情况1.8.将负荷调节器手柄扳至空负荷位置,使全部吸气阀片压开。
按规定要求开启气路中的各类阀门,使用权压缩机处于空载状态下启动。
1.9.盘车:手动盘车2~3圈,各运动机构应轻巧无阻。
2.正常操作2.1.启动时,应注意倾听机器的声音和振动有无异常,空载运行5~10min后一切正常即可进入负荷运转,此时,将负荷控制阀手柄扳至100%负荷位置,使气阀进入工作状态,然后按操作程序缓慢关闭全部各类阀门,使压缩机进入额定工况下的正常运转。
2.2..油水排放压缩机工作期间,如无自动排放装置时,应定期将分离器、冷却器中的冷凝液进行排放。
2.3.监听机器的响声随时倾听压缩机各部位的响声是否正常,如电机的动转声、气阀启闭声、运动机构撞击声等,以便积累经验,对异常响声做出及时准确判断,及早发现事故隐患。
2.4.巡视检查及记录压缩机运行数据定期巡视压缩机运转数据是否在正常范围内,如各级吸排气压力、温度、油压、油温、水压、水温、电机电流值、主轴承电机轴承温度等,每隔1小时记录一次,以便对照检查。
3.紧急事故处理当出现下列情况时,必须紧急停车:(1)突然停水、断油;(2)有严重的不正常响声和异常严重振动,或发现机身接筒气缸处有裂纹等异党情况;(3)压缩机某部位冒烟、着火或任一部位温度不断升高;(4)出现其它危及机器和人身安全时;停车要求4.正常停车4.1.接到停车信号后,应先压开各级吸气阀或开启旁通回路使压缩机处于空载状态;4.2.停主电机并切断电源;4.3.关闭末级出口和I级进口阀门;4.4.开启辅机上的排污阀放掉冷凝液,卸载后关闭;4.5.停止润滑系统油泵和注油器工作;4.6.关闭冷却水进出总管阀门;4.7.当停车时间较长或环境温度较低时,应将冷却系统中的存水全部放净;5.非正常情况5.1.当发现意外事故将要发生或已经发生,要立即切断主电机电源,停止电动机工作;5.2.压开各级吸气阀或开启旁回路,5.3. 以下程序同正常停车中的第(3)~(9)项。
硫磺回收装置试车方案

文件编号 JSHH-YT-LH ———————————————硫磺回收装置试车方案江苏汉皇安装工程有限公司二0一四年试车方案编审表编制:审核:审批:目录第1章开车准备 (2)第2章装置的清洗、吹扫、贯通 (6)第3章装置气密 (8)第4章装置水联运 (13)第5章装置烘炉、系统烘干 (15)第6章催化剂及填料装填 (19)第7章投料试车方案 (22)第1章开车(试车)准备硫磺回收装置包过:溶剂再生装置、酸性气提装置、硫磺回收装置。
生产装置安装完毕后,按设计工艺流程对装置内的管线、附塔管线,装置内的塔、各类机泵、风机、冷换设备、容器贮罐、电器、仪表、安全附件及其它附属设备及系统进行全面详细检查并作好记录,填写以下内容:检查时间;检查项目;检查结果及发现的问题;整改及复查结果,执行人/监护人签署。
1.1 系统检查1)检查公用工程管道,确认公用工程管道安装符合设计流程和安装图的要求。
2)检查伴热管道和夹套管道,确认蒸汽管道安装符合安装图和操作使用要求。
3)检查各类管道隔热、防腐涂漆,确认管道隔热和涂漆符合设计规范要求。
4)系统检查,确认管道介质流向、阀门和调节阀的安装位置及流向准确无误;5)检查所安装的工艺管线,应符合设计规范要求和生产需要,支架牢固,介质流向标识正确,确认管道附件放空阀、排凝阀、管道支撑、补偿器、过滤器、消音器、采样器等的安装位置是否准确无误、灵活好用。
6)检查热力管线的补偿结构、垫片、螺栓、法兰符合标准。
7)检查各管线上的阀门、温度计、热电偶管、压力表、管嘴、流量仪表等安装位置及流向是否正确、齐全、规格化、符合设计和满足生产需求。
8)检查各管线的试压盲板是否拆除,各管线的油漆、保温等是否符合要求。
9)框架、管廊、设备裙座防火按设计要求施工完毕,防火等级达到要求。
1.2 工艺设备各设备必须无杂物,设备资料及动改资料齐全,安全阀必须有定压记录,设备必须有试压记录。
外部检查确认设备的平台、围栏、梯子、保温、涂漆等符合要求。
脱硫工段联动开车方案

脱硫工段联动开车方案脱硫工段联动试车(假生产)及开工投运总方案根据实际工程进展,决定脱硫工段联动试车假生产阶段开始,假生产期间煤气不经过脱硫塔,其余设施全面进行负荷试车。
以检验和发现设计、施工、设备管线、电器、仪表的运行状况和操练岗位职工,并对发现的问题进行彻底处理。
在全面假生产发现的问题处理完毕后,再决定正式投运脱硫工段设施的时间(本方案已经包括投产阶段的内容)。
一、试车指挥机构及职责:试车指挥组成员:试车技术总负责:操作范围:脱硫工段内的所有设备、阀门、管线、电器仪表1、要求在试车前对所有设备编号,按照设计图纸的编号和名称制作铁牌,悬挂或固定在设备设施上的醒目处---------负责2、对现场进行清扫,对设备进行擦抹,要求窗门卫生干净,地面无杂物,设备光亮,阀门加油,备好记录本、笔、办公桌椅。
---------负责3、水泵、电机的开车准备工作--------含加油、转向检查、电器开关对应设备的编号、冷却设施及其他所有相关检查---------组织,现场操作工配合。
4、仪表就为---------------督促安装单位在10日下午6点全部就位,派人检查并初步验收确认可以使用。
操作工检点。
5、现场照明-------------负责检点。
6、在上述工作结束后,由一厂操作工给事故槽和溶液循环槽加水至4/5处。
--------负责7、购置开工及一个半月到两个月的药剂和原料------经理负责。
(暂购置0.5吨催化剂,150~200吨碳酸钠)8、协调生产中的水、电、气、汽的使用------负责9、保驾护航,处理试车运行过程中的安装问题-------协调。
二、假生产注意事项:1、首先按照正常开车先开启空压机,将空气送入再生塔,约20分钟到半个小时后,再按照正常开车开启循环泵(开机前一定要确认将空气系统溶液系统所有要开车的阀门开关好),循环泵开启后,加量一定要慢,不能过猛,应留有余地的慢慢调节流量直至正常循环。
硫酸装置开车方案
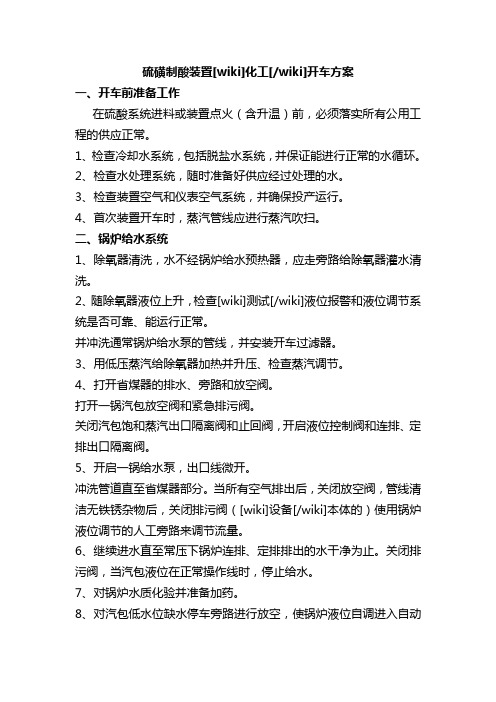
硫磺制酸装臵[wiki]化工[/wiki]开车方案一、开车前准备工作在硫酸系统进料或装臵点火(含升温)前,必须落实所有公用工程的供应正常。
1、检查冷却水系统,包括脱盐水系统,并保证能进行正常的水循环。
2、检查水处理系统,随时准备好供应经过处理的水。
3、检查装臵空气和仪表空气系统,并确保投产运行。
4、首次装臵开车时,蒸汽管线应进行蒸汽吹扫。
二、锅炉给水系统1、除氧器清洗,水不经锅炉给水预热器,应走旁路给除氧器灌水清洗。
2、随除氧器液位上升,检查[wiki]测试[/wiki]液位报警和液位调节系统是否可靠、能运行正常。
并冲洗通常锅炉给水泵的管线,并安装开车过滤器。
3、用低压蒸汽给除氧器加热并升压、检查蒸汽调节。
4、打开省煤器的排水、旁路和放空阀。
打开一锅汽包放空阀和紧急排污阀。
关闭汽包饱和蒸汽出口隔离阀和止回阀,开启液位控制阀和连排、定排出口隔离阀。
5、开启一锅给水泵,出口线微开。
冲洗管道直至省煤器部分。
当所有空气排出后,关闭放空阀,管线清洁无铁锈杂物后,关闭排污阀([wiki]设备[/wiki]本体的)使用锅炉液位调节的人工旁路来调节流量。
6、继续进水直至常压下锅炉连排、定排排出的水干净为止。
关闭排污阀,当汽包液位在正常操作线时,停止给水。
7、对锅炉水质化验并准备加药。
8、对汽包低水位缺水停车旁路进行放空,使锅炉液位自调进入自动状态,并设定正常操作水位调节。
将连排器的液水调节设臵在自动位臵。
三、硫酸系统开车1、准备工作向酸系统进酸前,务必落实完成以下全部操作:1.1、所有塔,槽,交换器和管线经过清理没有杂物。
1.2、管线在施工时已经按要求进行过水压试验。
将所有盲板去掉,将水从系统中排掉。
1.3、检查所有排污阀的运行情况。
将容器中的水放掉。
1.4、检查所有进酸系统的管线和阀件。
1.5、所有仪表均处于运行状态。
酸浓度分析仪进口的[wiki]阀门[/wiki]应关闭。
1.6、开车时须准备好足够的98[wiki]%[/wiki]浓硫酸供应。
硫磺制酸开车方案
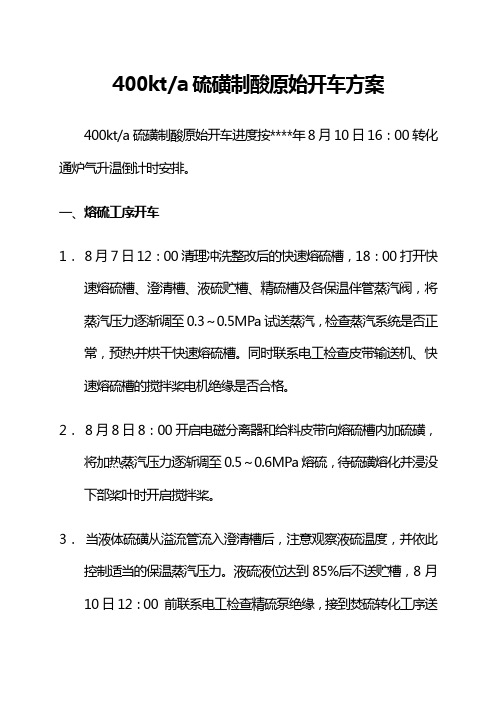
400kt/a硫磺制酸原始开车方案400kt/a硫磺制酸原始开车进度按****年8月10日16:00转化通炉气升温倒计时安排。
一、熔硫工序开车1. 8月7日12:00清理冲洗整改后的快速熔硫槽,18:00打开快速熔硫槽、澄清槽、液硫贮槽、精硫槽及各保温伴管蒸汽阀,将蒸汽压力逐渐调至0.3~0.5MPa试送蒸汽,检查蒸汽系统是否正常,预热并烘干快速熔硫槽。
同时联系电工检查皮带输送机、快速熔硫槽的搅拌桨电机绝缘是否合格。
2. 8月8日8:00开启电磁分离器和给料皮带向熔硫槽内加硫磺,将加热蒸汽压力逐渐调至0.5~0.6MPa熔硫,待硫磺熔化并浸没下部桨叶时开启搅拌桨。
3.当液体硫磺从溢流管流入澄清槽后,注意观察液硫温度,并依此控制适当的保温蒸汽压力。
液硫液位达到85%后不送贮槽,8月10日12:00 前联系电工检查精硫泵绝缘,接到焚硫转化工序送液硫通知后直接由澄清槽排放至精硫槽启动精硫泵送液硫。
4. 在向焚硫转化正常供液硫后,快速熔硫槽生产的液硫超过焚硫用量的部分经澄清后再送液硫贮槽。
当液硫贮槽液位>15%后,具备向精硫槽供液硫条件。
二、焚硫转化工序升温1.8月7日抽硫磺制酸预热管线至转化一段盲板,插矿制酸预热管线盲板,以避免两系统相互串气。
2. 8月8日18:00前安排好焚硫转化升温所需0#轻质材油40t。
3. 8月8日中班需做好以下工作:a 关闭干燥塔出口至焚硫炉主管线上阀门,关闭焚硫炉助燃风阀、二次风阀和稀释阀。
打开干燥塔出口至预热系统阀门,打开预热器出口至转化器一段阀门。
b 关闭气体过滤器出口至转化器一段阀门、关闭高温过热器炉气出口阀门。
打开转化器一段出口至二段旁路阀(TV1308),并将转化系统切为一转一吸。
c 准备好预热器点火用工具。
4.热空气升温4.1 转化热空气升温a 8月9日0:00 按空气风机操作规程启动空气风机,用进口阀调节风量。
1:00启动预热炉抽风机,一次风机、油泵,点燃预热炉,开始触媒热空气升温,控制转化一段进口升温速率为15℃/h。
罗寻硫酸开车方案
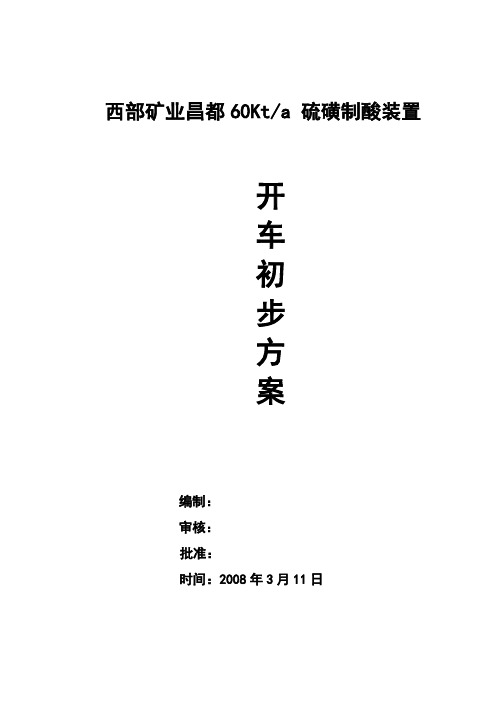
西部矿业昌都60Kt/a 硫磺制酸装置开车初步方案编制:审核:批准:时间:2008年3月11日前言鉴于该装置是西藏地区第一套硫酸装置,西藏昌都地处海拔4500多米的高原地区,氧含量低,对于新建的硫磺制酸装置的原始开车,存在一定的风险和难度。
为保证开车过程安全、环保和一次开车成功,由于没有看到本套硫酸制酸装置的工艺和设备配置,在此只能制定开车初步方案。
一、开车前准备工作1、按人员组织机构设置,配备相应的人员,把人员招聘到位,进行工艺技术培训15天,设备技术培训5天,安全操作技术培训3天。
管理人员、技术人员、操作人员经过培训,熟练掌握操作技术规程、试车方案,并经过考试取得上岗证、安全作业证。
2、进行开车前的“三查四定”,组织相关技术人员和设备供应厂家进行设备单体试车、联动试车和化工试车,并处理试车过程中出现的问题。
3、组织生产所需的各种原、辅材料供应到位,如硫磺、柴油、木材等。
4、组织相关的安全防护用品和消防设施到位并完好,制定相关安全事故应急方案,确保开车安全。
5、准备开车焚硫炉和转化器升温所需0#轻质柴油40吨。
6、准备开车用98%母酸800t。
7、联动试车已经完成,试车过程中发现的问题已全部整改合格,满足投料试车要求。
8、投料试车所需原料、辅助材料、备品备件、安全防护器材等已准备齐全。
9、参加试车的各级小组、管理人员、操作人员、维修人员、安全、消防、防护人员均已到位。
10、各岗位操作记录报表、交接班日志已准备齐全,发到各岗位。
11、仪表、阀门调校完毕,各设备单体及联动试车合格。
12、焚硫炉、气体过滤器、转化器烘烤合格,锅炉烘炉、煮锅合格。
13、气体管线吹扫干净,触媒按要求装进转化器,各人门封闭完毕。
14、磺枪已拆出,磺枪孔用盲板封闭。
15、油枪装配到位,具备使用条件。
二、开车方法1、严格按烘炉曲线,进行焚硫炉升温烘炉。
2、严格按锅炉升压曲线,对锅炉进行煮炉和升温。
3、用低压蒸气熔化固体硫磺,精制硫磺。
硫回收模拟开车方案表
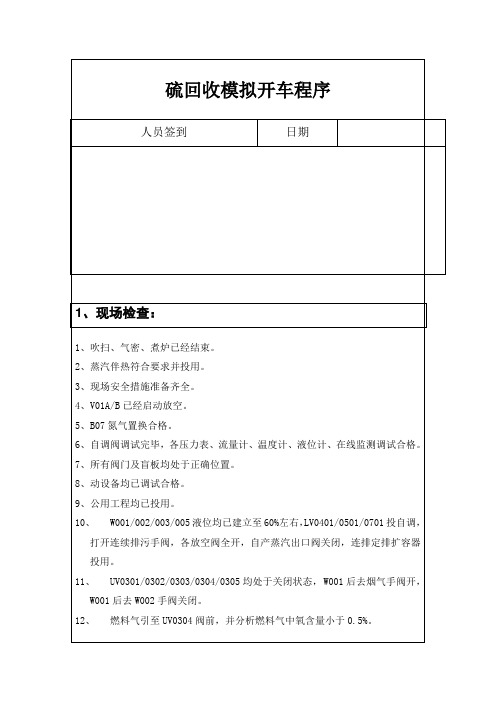
硫回收模拟开车程序人员签到日期1、现场检查:1、吹扫、气密、煮炉已经结束。
2、蒸汽伴热符合要求并投用。
3、现场安全措施准备齐全。
4、V01A/B已经启动放空。
5、B07氮气置换合格。
6、自调阀调试完毕,各压力表、流量计、温度计、液位计、在线监测调试合格。
7、所有阀门及盲板均处于正确位置。
8、动设备均已调试合格。
9、公用工程均已投用。
10、W001/002/003/005液位均已建立至60%左右,LV0401/0501/0701投自调,打开连续排污手阀,各放空阀全开,自产蒸汽出口阀关闭,连排定排扩容器投用。
11、UV0301/0302/0303/0304/0305均处于关闭状态, W001后去烟气手阀开,W001后去W002手阀关闭。
12、燃料气引至UV0304阀前,并分析燃料气中氧含量小于0.5%。
13、高温搀和阀低锅水(大于200Kg/h)及蒸汽已投。
14、在线分析入口阀关(联系仪表)。
15、F01三个热电偶已经换为临时热电偶。
二、烘F01反应炉及烘C01/02反应器步骤1、使用制硫炉顺控点火系统进行点火。
2、点火成功后,各视镜保护氮气投用,派专人观察炉内火焰。
3、拆除主燃料气线上的盲板,按点主火嘴按钮,用点火枪火焰点燃主燃料气火嘴进行升温。
4、按照升温曲线,F01升至900℃时开USV1302(手动控制其开度,控制系统压力约为0.05MPa)、开W001后去W002手阀、关W001后去烟气手阀,给两个反应器升温,根据进C01温度调整高温掺和阀开度使其升至350℃,调节TV0602A/B 使C02升温至250℃,反应器恒温24小时后催化剂升温结束。
5、按照升温曲线,燃烧炉炉膛温度升至1400℃,恒温24小时,烘炉结束。
6、根据风量需求启闭FV0302,完毕后调整FV0304、FV0303开度,使F01炉膛温度降至 1000℃以上,C01温度降至280℃以上,C02温度降至220℃以上,具备接气条件。
净化车间脱硫工段开停车方案

脱硫工段操作规程第一章岗位任务NHD脱硫的主要任务是脱除焦炉气中的硫(包括无机硫和有机硫),使其硫含量达到10PPM以内,能够作为合成工段的新鲜气,并将脱硫回收的酸性气体送到焦化进行硫回收。
第二章工艺原理2.1根据广义酸碱理论,在聚乙二醇二甲醚分子结构中,醚基团内的氧为硬碱性中心,而CH3-和-CH2-CH2-基团则为软酸部分,因此,NHD溶剂对硬酸性气体(如H2S、CO2)和软碱性气体(COS)均有较强的溶解吸收能力,从而达到脱除酸性气体的目的。
2.2NHD溶液吸收H2S是一种物理吸收。
主要原理是NHD在常温下可选择性吸收H2S气体。
吸收了H2S气体的NHD富液减压、加热后可使溶液溶解于其中的气体全部解析出来,使溶液再生得以循环利用。
NHD脱硫装置主要设备有脱硫塔、气提塔和再生塔。
三塔全部是填料塔。
第三章装置流程简述来自转化工段的转化气(40℃,3.0MPaA)经进塔器气离器(V3001)分离掉夹带的水后,进入脱硫塔(T3001)下部,在塔内与自上而下喷淋下来的NHD贫液逆流接触,NHD吸收了转化气中大部分的H2S气体,同时也带走部分CO2、COS、H2等气体。
除去H2S的转化气称之为脱硫气,经出塔气分离器(V3002)分离掉夹带的NHD溶液后去压缩工段。
脱硫塔(T3001)底排出的约25℃的NHD富液由富液泵(P3003A,B)提压后,分别经贫富液换热器Ⅲ(E3003)及贫富液换热器Ⅰ(E3001)换热,被NHD 贫液加热到100℃左右,进入气提塔(T3002)。
采用来自甲醇合成工段的甲醇驰放气(40℃,4.6MPa(A))作为气提气进入气提塔下部,塔顶出来的气提闪蒸气中主要是CO2、H2及少量H2S、COS等气体,该气体经气提气水冷器(E3005)冷却至40℃后经气提气分离器(V3003)并分离掉冷却下来的水后,返回进工段转化气以回收气提气中的H2及CO2气体。
从气提塔底出来的NHD富液由脱硫水力透平(HT3001)回收能量,经贫富液换热器Ⅱ(E3002)换热,被NHD贫液加热至135℃,进入再生塔(T3003)。
- 1、下载文档前请自行甄别文档内容的完整性,平台不提供额外的编辑、内容补充、找答案等附加服务。
- 2、"仅部分预览"的文档,不可在线预览部分如存在完整性等问题,可反馈申请退款(可完整预览的文档不适用该条件!)。
- 3、如文档侵犯您的权益,请联系客服反馈,我们会尽快为您处理(人工客服工作时间:9:00-18:30)。
硫回收装置开车方案
1、开车前具备的条件
(1)维修工作完成或安装结束并且装置正式交给生产分厂,各单位签署开车确认单。
(2)做好系统气密性试验,检查各复位后连接法兰是否漏气。
(3)联系调度,确认变换中压蒸汽具备使用条件,气化低压蒸汽具备使用条件。
(4)联系调度,确认空分装置低压氮气具备使用条件,低温甲醇洗工段CO2气体具备使用条件。
(5)打开仪表空气界区阀,确认调节阀处有仪表空气,电动阀有电源,调节阀具备使用条件。
(6)所有阀柄,扳手配备齐全,打开所有压力表、液位计、安全阀根部阀。
(7)中控操作人员确认DCS上所有监测点调试正常、准确。
(8)所有分析取样点投用正常,具备分析取样条件。
(9)一次水供水正常,具备使用条件。
(10)单机设备(空压机,鼓风机,洗涤液泵)正常,具备使用条件。
(11)硫分离器(V-2103)底部排污管接上收硫槽。
(12)有害气体防护设备配备齐全。
2、阀门开关状态确认
(1)打开中压蒸汽管线上进界区前两道阀门(分别在变换工段现场和气化管廊上),确认进装置界区阀关闭。
(2)打开低压蒸汽管线上进界区前两道阀门(分别在气化高闪放空管线和气化管廊上),确认进装置界区阀关闭。
(3)打开硫冷凝器上水管线上进界区前两道阀门(分别在变换工段现场和气化管廊上),确认进装置界区阀关闭。
(4)打开汽包上水管线上进界区前两道阀门(分别在变换工段现场和气化管廊上),确认进装置界区阀关闭。
(5)打开酸性气入界区管线上截止阀,确认低温甲醇洗工段酸性气出界区调节阀关闭。
(6)打开CO2管线入界区前两道阀门(分别在低温甲醇洗现场管廊上和气化管
廊上),确认进装置界区阀关闭。
(7)硫分离器(V-2103)出口进硫液封槽(V-2107)管线上阀门关闭。
(8)确认以下调节阀关闭:
酸性气去火炬放空阀(MV-2100)、酸性气流量调节阀(MV-2101)、
酸性气去高处放空阀(MV-2102)、汽包压力调节阀(PV-2101)、
硫冷凝器压力调节阀(PV-2102)、循环气压力调节阀(PV-2105)、
空气流量调节阀(FV-2102)、酸性气温度调节阀(TV-2101)、
空气温度调节阀(TV-2102)、汽包液位调节阀(LV-2101)、
硫冷凝器液位调节阀(LV-2102)、酸性气分离器液位调节阀(LV-2105)。
(9)关闭所有取样阀根部阀。
3、系统氮气置换
(1)打开循环气压力调节阀(PV-2105)及前后截止阀。
(2)打开酸性气流量调节阀(MV-2101)。
(3)联系调度确认氮气是否可投用。
(4)打开低压氮气入硫回收工段总阀。
(5)缓慢打开氮气入酸性气分离器(V-2101)管线上的截止阀。
(6)低压氮气经酸性气分离器(V-2101)、酸性气预热器(E-2101)、反应器(R-2101)、硫冷凝器(E-2103)、硫分离器(V-2103)、洗涤塔(T-2101)、水沉淀槽(V-2106)后排入放空装置。
(7)打开酸性气分离器液位调节阀(LV-2105)及其前后切断阀、付线阀,洗涤塔底部至洗涤液泵进口管线上的导淋阀,各工艺气管线上的导淋阀进行排放。
(8)联系化验室,在反应器出口取样点(A-2105)处、洗涤塔出口取样点(A-2106)处取样分析,当系统中的氧含量≤0.5%时,整个系统置换合格。
(9)关闭循环气压力调节阀(PV-2105)及氮气入酸性气分离器管线上的切断阀,保持系统为微正压。
4、系统上水
(1)打开硫冷凝器上水阀给硫冷凝器上水(50%),上水前打开上部放空阀排气,上水完成后关闭。
(2)打开汽包上水阀给硫冷凝器上水(50%),上水前打开上部放空阀排气,上
水完成后关闭。
5、建立伴热系统
(1)打开气化进系统低压蒸汽阀。
(2)打开酸性气分离器(V-2101)伴热管线进出口阀。
(3)打开硫冷凝器(E-2103)出口液硫管线伴热管线进出口阀。
(4)打开硫分离器(V-2103)夹套伴热管线进出口阀。
6、催化剂升温、汽包升压
(1)打开中压蒸汽进界区截止阀。
(2)打开中压蒸汽进反应器盘管截止阀,催化剂升温、汽包升压完毕后关闭(此时反应器内温度不小于223℃,汽包压力2.5MPa左右,升温速度小于每小时50℃,升压速率小于0.1Mpa每分钟)。
7、洗涤水循环系统的建立
(1)打开一次水进系统总阀及造粒机回水阀,一次水经过造粒机进入水沉淀槽(V-2106),水沉淀槽(V-2106)液位满后关闭造粒机回水阀。
(2)打开水冷却器(E-2104)进出循环水管线上阀门。
(3)打开水沉淀槽(V-2106)出口进洗涤液泵(P-2101)管线上阀门。
(4)打开洗涤液泵(P-2101)。
(5)通过洗涤液泵把水引入洗涤塔(T-2101),打开洗涤塔出口进水沉淀槽(V-2106)管线上阀门。
8、酸性气的引入
(1)打开循环气压力调节阀(PV-2105)及前后截止阀。
(2)打开CO2气体进系统阀门。
(3)打开酸性气进系统阀门。
(4)打开空气流量调节阀(FV-2102)及前后截止阀,和空气进酸性气管线上所有截止阀,打开空气压缩机(C-2102)循环水系统后启动压缩机引入空气至酸性气中。
(5)打开酸性气预热器(E-2101)蒸汽管线上所有截止阀及酸性气温度调节阀(TV-2101),引入中压蒸汽至预热器。
(6)打开空气预热器(E-2102)蒸汽管线上截止阀及空气温度调节阀(TV-2102),
引入中压蒸汽至预热器。
(7)在酸性气成分取样点(A-2103)处分析混合气中H2S气体的浓度,根据分析计算调节酸性气和CO2气量,使混合气中H2S浓度在3%左右。
9、循环气系统的建立
(1)打开循环气鼓风机,循环气压力调节阀(PV-2105)投自动,设定在一个恒定值维持系统压力恒定(具体参数根据进系统酸性气压力确定),关闭CO2管线上阀门。
(2)根据酸性气中H2S含量计算出所需空气的量,并进行配比流量的初步调节,在混合气成分取样点(A-2104)处分析反应气中H2S和O2含量,对酸性气和空气流量进行细微调节。
(3)当汽包和硫冷凝器产生蒸汽后,逐步打开汽包压力调节阀(PV-2101)、硫冷凝器压力调节阀(PV-2102)的副线阀及蒸汽放空阀,同时打开硫冷凝器压力调节阀(PV-2102)及其前截止阀,后截止阀关闭,对硫冷凝器压力调节阀(PV-2102)设定一定值,逐渐关闭来自气化低压蒸汽,稳定伴热系统压力在一个恒定值。
至此,系统开车完毕,进入正常操作阶段。