CAE 分析报告样板及说明
CAE分析报告样板详解演示文稿

流入量分布图
10.0
26.3
43.3
53.8
65.0
42.7
16.8
13.0
18.1
23.4
28.7 24.2
27.0 24.4 66.3 55.3 41.0 32.8
流入量分布图
流入量说明
现场调试时确保坯料流入量和模拟结果相近(最好小于5mm)是非 常重要的,在试模坯料流入量达到模拟值前,CAE分析报告缺乏参考性。
由于冲床状态,加工精度,钳工研配对拉延筋和压料面间隙影响较 大,CAE分析在准确模拟压边力和拉延筋锁料能力方面存在一定难度, 所以容易发生制件单初时坯料流入量和成型分析结果偏差较大的情况, 这种情况下应先调整压边力,拉延筋强度和压料面间隙使现场流入量和 模拟结果相近。然后再调整分模线以内的补充型面,最后再调整产品型 面。
一般模具设计时加工面边界是在理论坯料边界均匀外扩1020mm,故单初件坯料定位时在理论坯料和加工面边界四周 留均匀的距离可保证定位和CAE分析情况一致
加工面边界
1800
坯料边界
1030
Forming process:The blank gravity (重力状态)
Forming process:The binder closing
现场测量流入量的最好方法就是在确认压边圈闭合状态和模拟情况 一致时(必须先解决板料定位,压边圈行程等问题),在压边圈上用油 笔画出闭合后的板料边界,和板料拉延完毕后的轮廓比较即可得出流料 分布。
(料厚分布图)
蓝色减薄量大,红色减薄量小
从模拟结果上看出:此处最大减 薄22.8, FLD图上此区域为黄色 区域处于破裂临界状态,调试 时注意模面光洁度,示意图见第 六页B图。
cae分析报告

VACUUM VESSEL END FLANGE CAE分析报告产品名称:VACUUM VESSEL END FLANGE分析软件:Autoform4.2分析材质:14301实质材质:304L料厚:3mm成形类型:拉延毛坯尺寸:φ2010产品及工艺补充形状:产品成形性评估分析结果(Draw)板料变薄量图结论:由于现有的材料库没有304L,现用14301进行替代模拟,分析结论本零件拉延基本成功。
THERMAL SHIELD END FLANGE CAE分析报告产品名称:THERMAL SHIELD END FLANGE分析软件:Autoform4.2分析材质:6016 T4实质材质:6061 T6料厚:6.35mm成形类型:拉延毛坯尺寸:φ2124产品及工艺补充形状:产品成形性评估分析结果(Draw)板料变薄量图结论:由于现有的材料库没有6061-T6,现用6016-T4进行替代模拟,分析结论本零件拉延基本成功。
下面是赠送的团队管理名言学习,不需要的朋友可以编辑删除谢谢1、沟通是管理的浓缩。
2、管理被人们称之为是一门综合艺术--“综合”是因为管理涉及基本原理、自我认知、智慧和领导力;“艺术”是因为管理是实践和应用。
3、管理得好的工厂,总是单调乏味,没有任何激动人心的事件发生。
4、管理工作中最重要的是:人正确的事,而不是正确的做事。
5、管理就是沟通、沟通再沟通。
6、管理就是界定企业的使命,并激励和组织人力资源去实现这个使命。
界定使命是企业家的任务,而激励与组织人力资源是领导力的范畴,二者的结合就是管理。
7、管理是一种实践,其本质不在于“知”而在于“行”;其验证不在于逻辑,而在于成果;其唯一权威就是成就。
8、管理者的最基本能力:有效沟通。
9、合作是一切团队繁荣的根本。
10、将合适的人请上车,不合适的人请下车。
11、领导不是某个人坐在马上指挥他的部队,而是通过别人的成功来获得自己的成功。
12、企业的成功靠团队,而不是靠个人。
CAE 分析报告样板详解
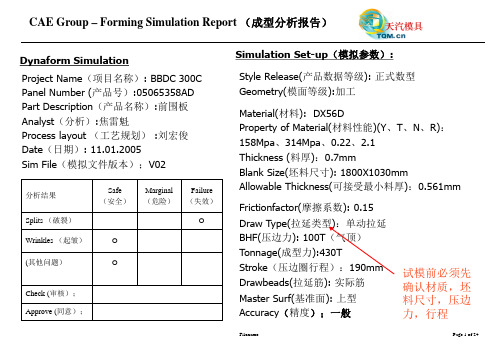
Filename
Page 3 of 24
CAE Group – Forming Simulation Report (成型分析报告)
A图 B图
绿色点为20%安全裕度 地成型极限曲线以下的 安全点
考虑20%安全裕度地成型极限曲线,黄色的点表示该 区域的材料有破裂的危险,这种模拟结果处于临界 状态,必须设法予以改善,如工艺上无法改善,则 应该在分析报告中指明现场解决该问题的方向
粉色为起皱点,但FLD一般不作为起皱判断的依据
Filename
Filename
Page 5 of 24
CAE Group – Forming Simulation Report (成型分析报告)
FLD 成型极限图
理论成型极限曲线,图中的点表示某区 域材料的变形状态,所有在该曲线以上 的点为红色,表示对应区域的材料已经 破裂失效,这种模拟结果不可接受
蓝色为有起皱趋势的点Filen源自mePage 8 of 24
CAE Group – Forming Simulation Report (成型分析报告)
危险状态的模拟结果(Marginal)应该是
材料最大变形点在成型极限曲线以下, -20%安全裕度地成型极限曲线以上,减 薄量>20%,小于30% (不同材质的允许减薄量相差较大,具体材质应具体分析) 外板成型不够充分 考虑到位置以及材料拉应力的和谐变化,在外表面区域内的最小板料厚度减薄 大于2%。小于3% 起皱和波纹(通过成型过程中的板料形状和应力状态来判断) -- 整个变形过程中有皱纹或镦粗,难以判断这些皱纹在下死点时能否出现表 面损伤; -- 补充面或则零件的不可见区域有小皱褶或波纹 ,但不会导致功能故障(非 安装面、法兰或坡口连接处),也不会在模具表面造成损伤。
CAE分析实例

浇口位置如图所示,热流道直径为16mm,浇口尺寸为15*2*2 2.流动情况
图中红色部分最后充填。
图中所示红线为溶解痕。
4.注射压力
最大注射压力约为55Mpa。
图中红色位置注意设排气。
浇口位置如图所示,热流道直径为16mm,左边浇口尺寸为8*2*2,右边为10*2*2。
2.流动情况
图中红色部分最后充填。
图中所示红线为溶解痕。
4.注射压力
最大注射压力约为47Mpa。
图中红色位置注意设排气。
两个方案比较来看,方案二注射压力较小,估计成型时间为20s,冷却时间为50s;而方案一估计成型时间为20s,冷却时间为53s。
所以,推荐使用方案二。
CAE-分析报告样板详解

A
Page 21 of 24
CAE Group – Forming Simulation Report (成型分析报告)
Forming process:5mm to the draw home
A
Page 22 of 24
CAE Group – Forming Simulation Report (成型分析报告)
Forming process:The binder closing
试模时首先保证重力状态和压边圈闭合 状态和模拟情况一致是非常重要的,复 杂曲面的压边圈和闭合情况对最终的成 型结果影响很大,但复杂压边圈闭合的 精确模拟也是成型模拟的难点之一
A
Page 13 of 24
CAE Group – Forming Simulation Report (成型分析报告)
CAE Group – Forming Simulation Report (成型分析报告)
Dynaform Simulation
Project Name(项目名称): BBDC 300C Panel Number (产品号):05065358AD Part Description(产品名称):前围板 Analyst(分析):焦雷魁 Process layout (工艺规划) :刘宏俊 Date(日期): 11.01.2005 Sim File(模拟文件版本);V02
CAE Group – Forming Simulation Report (成型分析报告)
料厚,减薄量和表示材料变形状态的成形极限图(是衡量材料成型性(破裂) 的3个重要指标
好的模拟结果(Safe)应该是
成型CAE实验报告完整版
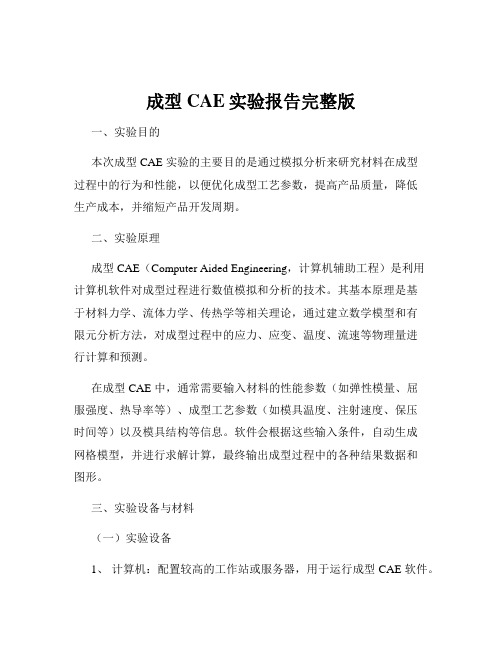
成型CAE实验报告完整版一、实验目的本次成型 CAE 实验的主要目的是通过模拟分析来研究材料在成型过程中的行为和性能,以便优化成型工艺参数,提高产品质量,降低生产成本,并缩短产品开发周期。
二、实验原理成型 CAE(Computer Aided Engineering,计算机辅助工程)是利用计算机软件对成型过程进行数值模拟和分析的技术。
其基本原理是基于材料力学、流体力学、传热学等相关理论,通过建立数学模型和有限元分析方法,对成型过程中的应力、应变、温度、流速等物理量进行计算和预测。
在成型 CAE 中,通常需要输入材料的性能参数(如弹性模量、屈服强度、热导率等)、成型工艺参数(如模具温度、注射速度、保压时间等)以及模具结构等信息。
软件会根据这些输入条件,自动生成网格模型,并进行求解计算,最终输出成型过程中的各种结果数据和图形。
三、实验设备与材料(一)实验设备1、计算机:配置较高的工作站或服务器,用于运行成型 CAE 软件。
2、成型 CAE 软件:选用了市场上较为成熟和广泛应用的_____软件,版本为_____。
(二)实验材料1、选用了_____材料,其主要性能参数如下:密度:_____弹性模量:_____屈服强度:_____热导率:_____四、实验步骤1、建立几何模型使用三维建模软件(如_____)创建成型产品的几何模型,并将其导入到成型 CAE 软件中。
2、划分网格在成型 CAE 软件中,对几何模型进行网格划分。
选择合适的网格类型(如四面体网格、六面体网格等)和网格尺寸,以保证计算精度和效率。
3、定义材料属性根据实验材料的性能参数,在成型 CAE 软件中定义材料的力学、热学等属性。
4、设置成型工艺参数根据实际的成型工艺条件,设置模具温度、注射速度、保压时间、冷却时间等工艺参数。
5、边界条件和加载确定模型的边界条件,如模具的固定约束、流体的入口和出口等,并施加相应的载荷。
6、求解计算运行成型 CAE 软件进行求解计算,等待计算完成。
CAE-分析报告样板详解 PPT

滑移线- 外板在可见区域有滑移线。
危险状态的模拟结果(Marginal)应该是
材料最大变形点在成型极限曲线以下, -20%安全裕度地成型极限曲线以上,减 薄量>20%,小于30% (不同材质的允许减薄量相差较大,具体材质应具体分析)
FLD 成型极限图
理论成型极限曲线,图中的点表示某区 域材料的变形状态,所有在该曲线以上 的点为红色,表示对应区域的材料已经 破裂失效,这种模拟结果不可接受
蓝色为有起皱趋势的点
A图 B图
绿色点为20%安全裕度 地成型极限曲线以下的 安全点
考虑20%安全裕度地成型极限曲线,黄色的点表示该 区域的材料有破裂的危险,这种模拟结果处于临界 状态,必须设法予以改善,如工艺上无法改善,则 应该在分析报告中指明现场解决该问题的方向
从模拟结果 上看出:此处 最大减薄21.9, FLD图上此 区域为黄色
区域处于破 裂临界状态。
从模拟结果上看出:此处最大减薄 20.9, FLD图上此区域为黄色区 域处于破裂临界状态,请在调试 时注意模面光洁度。
从模拟结果上看出:此两处最大减薄27.4, FLD 图上此区域为黄色区域处于破裂临界状态.但是 分析认为此处已经破裂,调试时局部调整此处圆 角, 可解决破裂问题.
由于冲床状态,加工精度,钳工研配对拉延筋和压料面间隙影响较 大,CAE分析在准确模拟压边力和拉延筋锁料能力方面存在一定难度, 所以容易发生制件单初时坯料流入量和成型分析结果偏差较大的情况, 这种情况下应先调整压边力,拉延筋强度和压料面间隙使现场流入量和 模拟结果相近。然后再调整分模线以内的补充型面,最后再调整产品型 面。
CAE分析报告样板及说明

CAE分析报告样板及说明报告标题:CAE分析报告报告日期:xxxx年xx月xx日1.引言在本节中,将介绍报告的目的、范围和CAE分析的背景信息。
还将提供有关分析所使用的软件和工具的说明。
2.分析目标本节将说明CAE分析的目标和预期结果。
这里可以列出分析所要解决的问题和需要回答的关键问题。
3.模型建立详细介绍了模型的建立过程,包括从CAD数据导入到CAE软件中,并生成适合进行分析的几何体和网格。
此外,还包括了模型各部分的材料属性定义和约束条件的设定。
4.材料特性在这一节中,将详细描述被分析物体的材料特性。
这包括材料的密度、弹性模量、屈服强度等信息。
如果存在多种材料,还需进一步对不同材料进行区分。
5.边界条件在这一节中,将描述和讨论在CAE分析中使用的边界条件。
这包括施加在模型上的载荷和约束,如外力、约束、初始条件等。
边界条件的选择对分析结果有着重要的影响。
6.并行化与计算资源需求在本节中,将介绍使用的计算机系统的配置和相关软件的设置。
这包括计算资源的使用情况,例如并行计算所使用的CPU核数和内存的使用情况。
还将讨论计算模型的网格划分和适应性分析的结果。
7.分析结果在这一节中,将给出对于分析所关心的参数的具体计算结果。
根据分析目标,可能需要计算应力、应变、位移等参数,并进行相应的结果分析和解释。
这里可以使用图表、表格等形式展示结果。
8.结果讨论在本节中,将对分析结果进行进一步的讨论和解释。
这可能涉及到对模型行为的理解,对结果的合理性的验证以及和实验结果的对比等。
此外,还可以对分析结果与设计准则进行比较,以评估模型的可行性和改进性。
9.结论在这一节中,将总结整个CAE分析的主要结果和发现,并提供建议和改进的方向。
如果有关未来工作的计划,也可以在此进行说明。
列出本CAE分析报告所参考的文献和资料。
引用的方法应符合指定的引用格式。
附录:模型几何图、网格划分图、原始数据、CAE软件输入文件等附件的相关信息。
CAE分析报告

Fቤተ መጻሕፍቲ ባይዱrming process:The blank gravity(重力状态)
10
The binder closing(压边圈闭合)
11
85mm to the draw home
75mm to the draw home
12
65mm to the draw home
55mm to the draw home
17
附页
供应商可自行填入其他重要内容,包括结论以及改 进方案等
18
5
Thinning Ratio Analysis(坯料减薄率分布图) 注:破裂起皱区域要显示出来
零件最大减薄率(或 则最大厚度)云图分 级显示
零件增厚率(或则最小厚度)
6
Wrinkle Analysis : Mean stress (平均应力分布图:起皱判断) 注:仅对DYNAFORM
最大值为材料屈服强度
云图8级显示, 红色表示起皱风 险极高,黄色表 示有一定风险。
最小值为负的材料抗拉强度 7
Wrinkling Criterion Plot(起皱趋势) 注:仅对AUTOFORM
8
Forming Limit Diagram 成型极限图( 必须显示出零件有起皱和破裂的区域)
FLD0:0.35
FLD图必须显示清晰,且对 于DYNAFORM,必须在此页 注明FLD0值。FLD安全裕度 推荐10%-20%
SIMULATION PACKAGE
DYNAFORM () AF SHELL ()
PAMSTAMP () AF MEMBRANCE ( )
Project (项目名称) Part No. (零件号) Part Name (零件名称) Analyst (分析员): Date (日期) SIM Version (模拟文件版本)
某汽车公司CAE分析报告
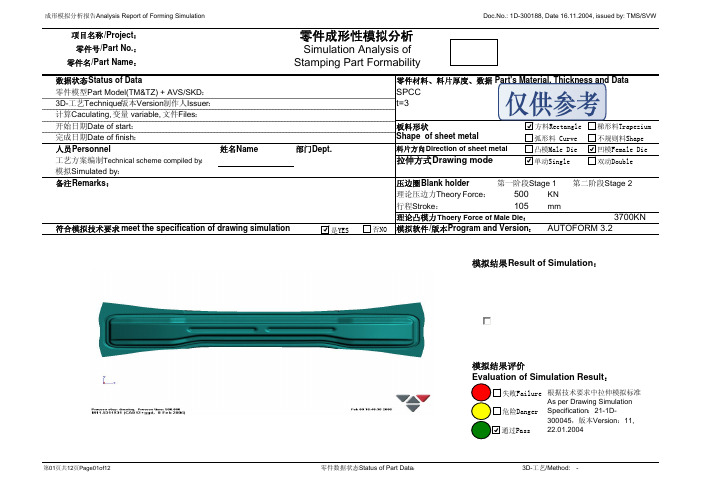
成形模拟分析报告Analysis Report of Forming Simulation Doc.No.: 1D-300188, Date 16.11.2004, issued by: TMS/SVWStamping Part Formability零件成形性模拟分析Simulation Analysis of 模拟结果评价:模拟结果Result of Simulation :根据技术要求中拉伸模拟标准As per Drawing SimulationSpecification :21-1D-300045,版本Version :11,22.01.2004零件名/Part Name :项目名称/Project :零件号/Part No.:失败Failure 危险Danger项目名称/Project:零件号/Part No.:零件名/Part Name:模拟结果评价一览Summary of simulation Result根据技术要求中深拉伸模拟标准As per Drawing零件号/Part No.:零件名/Part Name:开裂Crack, FLD项目名称/Project:料片图、拉延筋以及拉伸后料片轮廓Blank, Drawbead & Post-draw-blank项目名称/Project :零件号/Part No.:零件名/Part Name :000轧制方向Rolling direction of sheet meta材料流动方向Flowing direction of sheet metal项目名称/Project:零件号/Part No.:零件名/Part Name:最小材料变薄Min.Thinning ofsheet metal thickness项目名称/Project:零件号/Part No.:零件名/Part Name:材料变薄率分析Thinning Ratio Analysis ofSheet Metal Thickness项目名称/Project:成形性能分析零件号/Part No.:Formability Analysis零件名/Part Name:项目名称/Project:零件号/Part No.:零件名/Part Name:最小材料变薄Min.Thinning ofsheet metal thickness距下死点50mm 距下死点30mm项目名称/Project :零件号/Part No.:零件名/Part Name :起皱分析(总体)Wrinkle Analysis(General)成形模拟分析报告Analysis Report of Forming Simulation Doc.No.: 1D-300188, Date 16.11.2004, issued by: TMS/SVW项目名称/Project:滑移线分析零件号/Part No.:Skid Line Analysis零件名/Part Name:压变圈闭合距下死点105mm压变圈闭合距下死点60mm 压变圈闭合距下死点30mm 压变圈闭合距下死点20mm 压变圈闭合距下死点10mm 压变圈闭合距下死点1mm 零件名/Part Name :零件号/Part No.:起皱分析(局部)Wrinkle Analysis(Local)项目名称/Project :零件号/Part No.:备注,协商, …Remarks, negotiation,...项目名称/Project:零件名/Part Name:。
××车型白车身模态CAE分析报告模板

项目名称
××
数据版本
M0/2012.02.25
1/3
文件编号
项目 -CAE-NVH-
分析内容
所属部门
××车型白车身模态CAE分析报告模板
CAE部
1、分析目的 对× × 车型白车身模态进行校核。 2、使用软件 ① 前处理:HyperMesh v10.0 ② 求解器 NASTRAN2010 ③ 后处理:Hypermesh 10.0
3、模型及边界条件
图1:白车身有限元模型
3.1模型说明—白车身NVH焊接模型
3.2 车身材料说明
部件
钣金件 减震胶
材料
steel glue
弹性模量 泊松比 密度
210000 10
0.3 7.89E-9 0.49 1.10E-9
分析版次
REV1秘密级别源自绝密秘密对外保密
原件保管部门
资料室
审核
校对
制作
朱志峰 年-月-日
3.3工况说明—自由状态 , 频率范围 0----200Hz 4、计算结果—模态阵型云图
2 /3
3 /3
5、分析结论—分析结果是否满足设计要求 XX白车身模态频率是否满足设计要求。
6、优化方向—如分析结果不满足设计要求,对优化方案提供方向性建议
备注:
NVH仿真分析输入规范
●分析所需完整3D数模,含各部件数据,各总成焊点,螺栓连接,粘胶以及装配关系等; ●分析所需完整BOM表,含各部件材料料厚信息; ●如分析为非典型工况,则需提供分析所需载荷及边界条件。
××车型白车身刚度CAE分析报告模板

图3 考核点分布图
4.2绘制白车身弯曲刚度变形曲线(见下图):
3 /3
图4 白车身弯曲刚度曲线
4.3刚度计算公式K=F/δ(F为加载力,δ为位移) 4.4刚度云图
图5 白车身弯曲刚度云图
5、分析结论—分析结果是否满足设计要求 XX车型白车身弯曲刚度是否满足目标要求。
6、优化方向—如分析结果不满足设计要求,对优化方案提供方向性建议
项目名称
××
数据版本
M0/2012.02.25
分析内容
××车型白车身刚度CAE分析报告模板
1、分析目的 对× × 车型白车身弯曲刚度进行校核。 2、使用软件 ① 前处理:HyperMesh v10.0 ② 求解器 NASTRAN2010 ③ 后处理:Hypermesh 10.0
1/3
文件编号
项目 -CAE-NVH-
审核
校对
制作
朱志峰 年-月-日
3.3工况说明—
2 /3
约束条件:在前、后悬架与车身连接处,约束X、Y、Z移动自由度;(见图2) 加载条件:在前排左右座椅质心处各施加1000N的垂向力,后排座椅质心处施加 2000N的垂向力
4、计算结果
图2 白车身弯曲刚度加载工况
4.1分析数据处理 在车身纵梁下部和门槛梁下部分布了一系列考核点,通过考核点的X坐标值和ቤተ መጻሕፍቲ ባይዱ向变形 量绘制弯曲刚度曲线(见下图)。
所属部门
CAE部
3、模型及边界条件
图1:白车身有限元模型
3.1模型说明—白车身NVH焊接模型
3.2 车身材料说明
部件
钣金件 减震胶
材料
steel glue
弹性模量 泊松比 密度
210000 10
cae分析报告

cae分析报告CAE分析报告是一种基于数值模拟、力学分析和材料力学等方法,对于产品的性能进行评估和优化的工程分析方法。
本报告将对某个产品的CAE分析结果进行详细介绍和分析。
经过CAE分析,建议在产品的设计和制造过程中采用合适的材料和结构,以确保产品的性能和质量。
首先,对于材料的选择,通过CAE分析发现,目前使用的材料具有较高的强度和刚度,能够满足应力和振动的要求,但是存在一定的开裂和断裂的风险。
因此,建议在材料选择时,考虑使用更具韧性的材料,以增加产品的抗拉伸能力和耐磨性,同时降低开裂和断裂的风险。
其次,在产品设计和制造过程中,需要考虑到产品的结构强度和刚度。
通过CAE分析,发现当前产品在受力部位存在一定的应力集中,可能导致局部的破坏和失效。
因此,建议在产品的设计过程中,增加受力部位的支撑和加强结构,以分散应力和提高产品的强度。
另外,还可以考虑使用增加刚度的结构设计,以降低振动和共振的影响,提高产品的稳定性和寿命。
此外,在产品的制造过程中,需要注意制造工艺和表面处理的影响。
通过CAE分析,发现产品的表面粗糙度对于摩擦和磨损的影响较大。
因此,建议在制造过程中,采用适当的加工工艺,以提高表面的光洁度和平整度,降低表面粗糙度,从而减少摩擦和磨损。
最后,在产品的使用和维护过程中,需要进行适当的检测和修复。
通过CAE分析,发现产品的应力和变形会随着使用时间的增加而逐渐积累,可能导致材料疲劳和失效。
因此,建议在产品的使用过程中,定期进行检测和维修,以及时发现和修复产品的疲劳和损伤。
综上所述,CAE分析报告提供了一种全面的工程分析方法,可以评估产品的性能和质量,并提供优化的建议。
通过合理选择材料和结构设计,控制制造工艺和维护过程,可以提高产品的性能和寿命,降低故障和失效的风险。
因此,在产品的设计和制造过程中,需要充分应用CAE分析方法,以确保产品的安全性和可靠性。
CAE 分析报告样板及说明

FLD 成型极限图
蓝色为有起皱趋势的点 A图 B图
绿色点为20%安全裕度 地成型极限曲线以下的 安全点 粉色为起皱点,但FLD一般不作为起皱判断的依据
Filename
考虑20%安全裕度地成型极限曲线,黄色的点表示该 区域的材料有破裂的危险,这种模拟结果处于临界 状态,必须设法予以改善,如工艺上无法改善,则 应该在分析报告中指明现场解决该问题的方向
CAE Group – Forming Simulation Report (成型分析报告)
Dynaform Simulation Project Name(项目名称): BBDC 300C Panel Number (产品号):05065358AD Part Description(产品名称):前围板 Analyst(分析):焦雷魁 Process layout (工艺规划) :刘宏俊 Date(日期): 11.01.2005 Sim File(模拟文件版本);V02
A
B
蓝色为拉应力区域, 无皱褶
从模拟结果上可以看出:在产品上没有褶皱产生.但在AB 区域有可能出现轻微波纹
Filename Page 10 of 24
CAE Group – Forming Simulation Report (成型分析报告)
一般模具设计时加工面边界是在理论坯料边界均匀外扩1020mm,故单初件坯料定位时在理论坯料和加工面边界四周 留均匀的距离可保证定位和CAE分析情况一致
Filename Page 4 of 24
CAE Group – Forming Simulation Report (成型分析报告)
减薄量是客户比较关心的指标之一,一般客户会要求减薄 量在20%以内,这也是好的模拟结果的标准之一,但复杂 零件从模拟和现场调试的结果来看都非常难达到这个标准, 图示蓝色为减薄量大,红色减薄量小甚至增厚
CAE分析的开题报告模板

南京工程学院毕业设计开题报告课题名称:基于MPI的载重汽车发动机冷却液水箱顶盖注射工艺优化学生姓名:指导教师:庄卫国所在系部:材料工程学院专业名称:材料成型及控制工程(模具设计)南京工程学院2014年3 月日说明1.根据教育部对毕业设计(论文)的评估标准,学生必须撰写《毕业设计(论文)开题报告》,由指导教师签署意见、教研室审查,系教学主任批准后实施。
2.开题报告是毕业设计(论文)答辩委员会对学生答辩资格审查的依据材料之一。
学生应当在毕业设计(论文)工作前期内完成,开题报告不合格者不得参加答辩。
3.毕业设计开题报告各项内容要实事求是,逐条认真填写。
其中的文字表达要明确、严谨,语言通顺,外来语要同时用原文和中文表达。
第一次出现缩写词,须注出全称。
4.本报告中,由学生本人撰写的对课题和研究工作的分析及描述,应不少于2000字,没有经过整理归纳,缺乏个人见解仅仅从网上下载材料拼凑而成的开题报告按不合格论。
5.开题报告检查原则上在第4周完成,各系完成毕业设计开题检查后,应写一份开题情况总结报告。
学士学位毕业设计(论文)开题报告学生姓名学号专业材料成型及控制工程(模具设计)指导教师姓名庄卫国职称讲师所在系部材料工程学院课题来源企、事业单位委托课题课题类型工程设计课题名称基于MPI的载重汽车发动机冷却液水箱顶盖注塑工艺优化毕业设计的内容和意义1.主要内容(1)对制品结构工艺性和成型工艺性分析;(2)网格划分及修补;(3)更改参数分析出不同结果;(4)选取最优方案;(5)完成毕业设计;(6)翻译一篇相关的外文资料。
2.毕业设计在四年中的意义毕业设计是带有研究性质的专题研究分析、设计报告、是培养合格人才的一个重要实践性教学环节。
通过毕业设计,旨在使我们对所学过的基础理论和专业知识进行一次全面、系统地回顾和总结,通过对具体题目的分析,使理论与实践相结合,巩固和发展所学理论知识,掌握正确的思维方法和基本技能,提高学生独立思考能力和团结协作的工作作风,提高学生利用计算机解决实际问题的能力及计算机实际操作水平,促进学生建立严谨的科学态度和工作作风。
CAE分析结果报告模板

表 1 成型工艺参数表
参数设定
设定值
熔体温度(℃)
240
模具温度(℃)
60
保压切换点(%)
99
保压压力(MPa)
42.11
充填时间(sec)
7
保压时间(sec)
7
冷却时间(sec)
Hale Waihona Puke 40体积(cm3)
314.75
流道体积(cm3)
22.69
4
參、 设计/分析案例
1. 流动波前图(Melt-front advancement(S)):图(1)~图(7)
图(13)为公模的温度分布,图(14)为母模的温度分布图,不均匀的模具温
5
度将形成不均匀的热残留应力因而造成翘曲的问题。本产品公模温度范围在 71~160 ℃左右,而在母模温度范围在 66~103℃左右。
7. 公母模温差分布图(Temperature difference):图(15)
本图表示为公母模温差分布,温差分布约为 2~72℃左右,而温差最大区域分 布在产品中间嵌入物四周。较好的设计方案,应增加此区的散热效果,如增加此区 冷却水管设计;或此区冷却水管独立设计,并改用较低冷却液;或将此区模具材料 改为热传导系数较高钢材如铜合金或铍铜等,以降低此区模温差,以避免温差过大 所造成的问题。此图可作为帮助判断翘曲原因的标准,温差愈大造成翘曲的因素愈 大。而公母模温差的理想值应小于 10℃。
2
壹、 前言
计算机辅助工程(Computer Aided Engineer CAE)可加强工程师全方位处理 塑料注射成型,同时可提高生产力、产品质量、降低成本。
无 CAE 分析,工程师只能仰赖先前的经验、直觉、原型、或试模中得到的 信息来设计模具,例如熔体充填模式、缝合线和气孔(包风)位置,所需的射 出压力和锁模力,纤维配向,成型周期,最终成品外观和变形。若无 CAE 分析, 即使一个配备完整的模具也很难得到下列重要的设计数据,如压力、温度、剪 切速率、剪应力、和速度等的分布。用 CAE 预测的充填模式可以协助有经验的 工程师找出可能被忽略的的因素,利用 CAE 分析重复计算,评估其它形式的设 计和不同材料,成本效益高且能迅速建立设计准则。
CAE模流分析报告
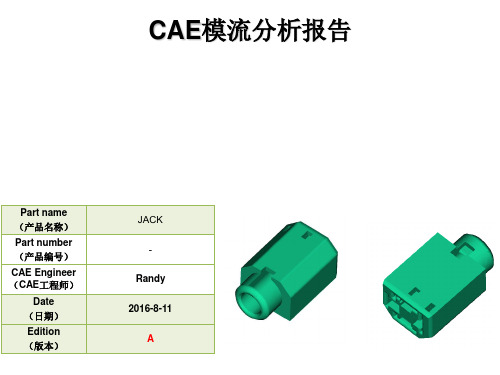
方案1
方案2
Y方向主要表现为收缩
2020/6/5
Deflection All effects: Z deflection
Page - 19
The Z deflection result shows the deflection at each node of the part ( Warp analysis) in deflection of Z . Z向变形结果表明的是产品上每一个点在Z方向的变形结果(翘曲分析).
方案2
Page - 16
加强排气
彩色圆圈所示区域即为可能产生困气的区域。
2020/6/5
Deflection All effects: X deflection
Page - 17
The X deflection result shows the deflection at each node of the part ( Warp analysis) in deflection of X . X向变形结果表明的是产品上每一个点在X方向的变形结果(翘曲分析).
100
℃
04. Melt temperature(熔体温度)
350
℃
05. Absolute max.melt temperature
(裂解温度)
400
℃
06. Ejection temperature(顶出温 度)
250
℃
07.Viscocity Index(粘度指数)
VI(240)0255
08. Min. mold temperature(最小模具温 度) 09. Max. mold temperature(最大模具温 度) 10. Min. melt temperature(最小熔体温 度) 11. Max. melt temperature(最达熔体温 度)
材料加工实验报告(注塑成型CAE分析实验)标准范本
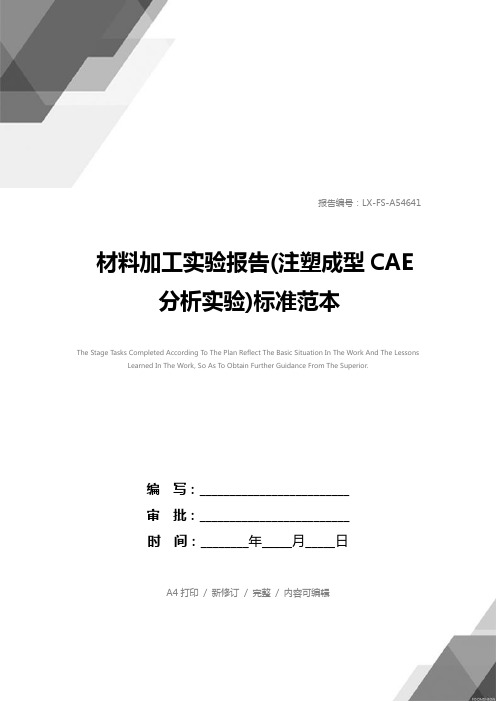
报告编号:LX-FS-A54641材料加工实验报告(注塑成型CAE分析实验)标准范本The Stage T asks Completed According T o The Plan Reflect The Basic Situation In The Work And The Lessons Learned In The Work, So As T o Obtain Further Guidance From The Superior.编写:_________________________审批:_________________________时间:________年_____月_____日A4打印/ 新修订/ 完整/ 内容可编辑材料加工实验报告(注塑成型CAE分析实验)标准范本使用说明:本报告资料适用于按计划完成的阶段任务而进行的,反映工作中的基本情况、工作中取得的经验教训、存在的问题以及今后工作设想的汇报,以取得上级的进一步指导作用。
资料内容可按真实状况进行条款调整,套用时请仔细阅读。
一、实验目的1、掌握注塑成型工艺中各参数如塑件材料、成型压力、温度、注射速度、浇注系统等因素对其成型质量的影响大小。
2、了解塑件各种成型缺陷的形成机理,以及各工艺参数对各种缺陷形成的影响大小。
3、初步了解注塑成型分析软件Moldflow的各项功能及基本操作。
4、初步了解UG软件三维建模功能。
5、初步了解UG软件三维模具设计功能。
二、实验原理1、Moldflow注塑成型分析软件的功能十分齐全,具有完整的分析模块,可以分析出注塑成型工艺中各个参数如塑件材料、成型压力、温度、注射速度、浇注系统等因素对成型质量的影响,还可以模拟出成型缺陷的形成,以及如何改进等等,还可以预测每次成型后的结果。
2、注射成型充填过程属于非牛顿体、非等温、非稳态的流动与传热过程,满足黏性流体力学和基本方程,但方程过于复杂所以引入了层流假设和未压缩流体假设等。
#CAE分析的开题评测报告模板
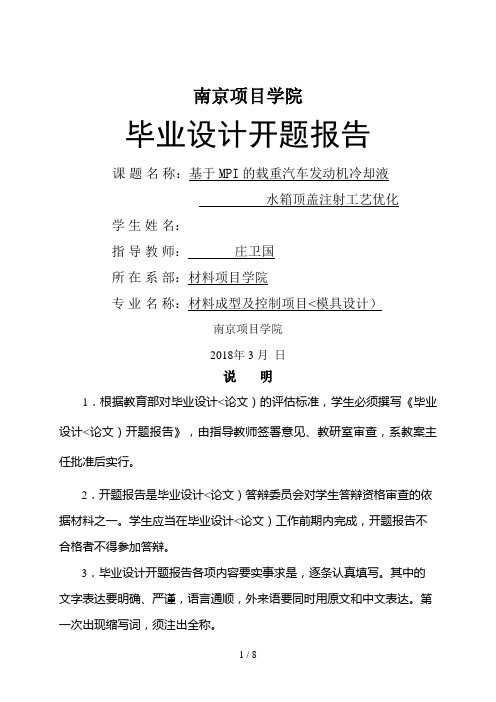
南京项目学院
毕业设计开题报告
课题名称:基于MPI的载重汽车发动机冷却液
水箱顶盖注射工艺优化学生姓名:
指导教师:庄卫国
所在系部:材料项目学院
专业名称:材料成型及控制项目<模具设计)
南京项目学院
2018年 3 月日
说明
1.根据教育部对毕业设计<论文)的评估标准,学生必须撰写《毕业设计<论文)开题报告》,由指导教师签署意见、教研室审查,系教案主任批准后实行。
2.开题报告是毕业设计<论文)答辩委员会对学生答辩资格审查的依据材料之一。
学生应当在毕业设计<论文)工作前期内完成,开题报告不合格者不得参加答辩。
3.毕业设计开题报告各项内容要实事求是,逐条认真填写。
其中的文字表达要明确、严谨,语言通顺,外来语要同时用原文和中文表达。
第一次出现缩写词,须注出全称。
4.本报告中,由学生本人撰写的对课题和研究工作的分析及描述,
应不少于2000字,没有经过整理归纳,缺乏个人见解仅仅从网上下载材料拼凑而成的开题报告按不合格论。
5.开题报告检查原则上在第4周完成,各系完成毕业设计开题检查后,应写一份开题情况总结报告。
学士学位毕业设计(论文>开题报告。
- 1、下载文档前请自行甄别文档内容的完整性,平台不提供额外的编辑、内容补充、找答案等附加服务。
- 2、"仅部分预览"的文档,不可在线预览部分如存在完整性等问题,可反馈申请退款(可完整预览的文档不适用该条件!)。
- 3、如文档侵犯您的权益,请联系客服反馈,我们会尽快为您处理(人工客服工作时间:9:00-18:30)。
18.1
23.4 28.7 27.0 24.2
24.4
66.3
55.3
41.0
32.8
Filename Page 2 of 24
CAE Group – Forming Simulation Report (成型分析报告)
流入量分布图
流入量说明 现场调试时确保坯料流入量和模拟结果相近(最好小于5mm)是非 常重要的,在试模坯料流入量达到模拟值前,CAE分析报告缺乏参考性。 由于冲床状态,加工精度,钳工研配对拉延筋和压料面间隙影响较 大,CAE分析在准确模拟压边力和拉延筋锁料能力方面存在一定难度, 所以容易发生制件单初时坯料流入量和成型分析结果偏差较大的情况, 这种情况下应先调整压边力,拉延筋强度和压料面间隙使现场流入量和 模拟结果相近。然后再调整分模线以内的补充型面,最后再调整产品型 面。 现场测量流入量的最好方法就是在确认压边圈闭合状态和模拟情况 一致时(必须先解决板料定位,压边圈行程等问题),在压边圈上用油 笔画出闭合后的板料边界,和板料拉延完毕后的轮廓比较即可得出流料 分布。
加工面边界 1800 坯料边界
The Blank Size (坯料形状及定位)
1030
Filename
Page 11 of 24
CAE Group – Forming Simulation Report (成型分析报告)
Forming process:The blank gravity (重力状态)
Forming process:50mm to the draw home
Filename
Page 18 of 24
CAE Group – Forming Simulation Report (成型分析报告)
Forming process:40mm to the draw home
Filename
从模拟结果 上看出:此处 最大减薄21.9, FLD图上此 区域为黄色 区域处于破 裂临界状态。
从模拟结果上看出:此处最大减薄 20.9, FLD图上此区域为黄色区 域处于破裂临界状态,请在调试 时注意模面光洁度。
从模拟结果上看出:此两处最大减薄27.4, FLD 图上此区域为黄色区域处于破裂临界状态.但是 分析认为此处已经破裂,调试时局部调整此处圆 角, 可解决破裂问题.
Filename
Page 8 of 24
CAE Group – Forming Simulation Report (成型分析报告)
危险状态的模拟结果(Marginal)应该是
材料最大变形点在成型极限曲线以下, -20%安全裕度地成型极限曲线以上,减 薄量>20%,小于30% (不同材质的允许减薄量相差较大,具体材质应具体分析) 外板成型不够充分
FLD 成型极限图
蓝色为有起皱趋势的点 A图 B图
绿色点为20%安全裕度 地成型极限曲线以下的 安全点 粉色为起皱点,但FLD一般不作为起皱判断的依据
Filename
考虑20%安全裕度地成型极限曲线,黄色的点表示该 区域的材料有破裂的危险,这种模拟结果处于临界 状态,必须设法予以改善,如工艺上无法改善,则 应该在分析报告中指明现场解决该问题的方向
CAE Group – Forming Simulation Report (成型分析报告)
Forming process: Home
Filename
Page 23 of 24
(坯料减薄率分布图)
27.4%
18%
21.7%
修边线
不同的材料允许最大减薄量不一样,一般从FLC曲线 衍生得到的TLC曲线
Filename Page 5 of 24
CAE Group – Forming Simulation Report (成型分析报告)
理论成型极限曲线,图中的点表示某区 域材料的变形状态,所有在该曲线以上 的点为红色,表示对应区域的材料已经 破裂失效,这种模拟结果不可接受
滑移线- 外板在可见区域无滑移线。
Filename
Page 7 of 24
CAE Group – Forming Simulation Report (成型分析报告)
差的模拟结果(Failure)应该是
破裂和失效,材料最大变形点在成型极限曲线以上,板材的最大减薄率大于30% 外板成型不充分, 考虑到位置以及材料拉应力的和谐变化,在外表面区域内的最小板料厚度减薄 <2%。 起皱和波纹(通过成型过程中的板料形状和应力状态来判断) - 整个变形过程中有皱纹或镦粗,且在外板可见区域,有表面损伤; 在可见区域以外,有装配和使用功能故障(皱纹位于安装面、法兰或坡口连接 处)。; 滑移线- 外板在可见区域有滑移线。
Forming process:10mm to the draw home
Filename
Page 21 of 24
CAE Group – Forming Simulation Report (成型分析报告)
Forming process:5mm to the draw home
Filename
Page 22 of 24
Filename
Check (审核); Approve (同意);
试模前必须先 确认材质,坯 料尺寸,压边 力,行程
Page 1 of 24
CAE Group – Forming Simulation Report (成型分析报告)
流入量分布图
10.0 16.8
26.3
43.3
53.8
65.0
42.7 13.0
Page 16 of 24
CAE Group – Forming Simulation Report (成型分析报告)
Forming process:60mm to the draw home
Filename
Page 17 of 24
CAE Group – Forming Simulation Report (成型分析报告)
-成型充分,考虑到位置以及材料拉应力的和谐变化,在外表面区域内的最小板 料厚度减薄≥3%。
无起皱和波纹(通过成型过程中的板料形状和应力状态来判断) - 外板在整个变形过程中无临界皱纹产生
- 内板在整个变形过程中有皱纹或镦粗,但最终产品无皱纹,不会造成模具表面
损伤,因为这些皱纹在模具到达下死点时可以被拉平;
Filename
Page 3 of 24
CAE Group – Forming Simulation Report (成型分析报告)
蓝色减薄量大,红色减薄量小
(料厚分布图)
从模拟结果上看出:此处最大减 薄22.8, FLD图上此区域为黄色 区域处于破裂临界状态,调试 时注意模面光洁度,示意图见第 六页B图。
A
B
蓝色为拉应力区域, 无皱褶
从模拟结果上可以看出:在产品上没有褶皱产生.但在AB 区域有可能出现轻微波纹
Filename Page 10 of 24
CAE Group – Forming Simulation Report (成型分析报告)
一般模具设计时加工面边界是在理论坯料边界均匀外扩1020mm,故单初件坯料定位时在理论坯料和加工面边界四周 留均匀的距离可保证定位和CAE分析情况一致
Page 6 of 24
CAE Group – Forming Simulation Report (成型分析报告)
料厚,减薄量和表示材料变形状态的成形极限图(是衡量材料成型性(破裂) 的3个重要指标
好的模拟结果(Safe)应该是
无破裂和失效点,材料最大变形点在-20%安全裕度地成型极限曲线以下,板材 的最大减薄率在20%以内,但高强钢板等成型性能极差的材质最大的允许减薄率 可能还不到20%,这时的破裂判断准则以FLC为准
Forming process:90mm to the draw home
Filename
Page 15 of 24
CAE Group – Forming Simulation Report (成型分析报告)
Forming process:70mm to the draw home
Filename
Filename
Page 9 of 24
CAE Group – Forming Simulation t (成型分析报告)
平均应力分布图 (起皱判断)
红色区域为材料处于压应力状态且接近屈服应力,起皱。黄 色和橙色处于临界状态,难以判断,一般认为细微波纹或者 表面质量不好,不影响使用功能,内板可以接受
Page 19 of 24
CAE Group – Forming Simulation Report (成型分析报告)
Forming process:20mm to the draw home
Filename
Page 20 of 24
CAE Group – Forming Simulation Report (成型分析报告)
分析结果 Splits (破裂) Wrinkles (起皱) (其他问题) O O Safe (安全) Marginal (危险) Failure (失效) O
Simulation Set-up(模拟参数): Style Release(产品数据等级): 正式数型 Geometry(模面等级):加工 Material(材料): DX56D Property of Material(材料性能)(Y、T、N、R): 158Mpa、314Mpa、0.22、2.1 Thickness (料厚):0.7mm Blank Size(坯料尺寸): 1800X1030mm Allowable Thickness(可接受最小料厚):0.561mm Frictionfactor(摩擦系数): 0.15 Draw Type(拉延类型):单动拉延 BHF(压边力): 100T(气顶) Tonnage(成型力):430T Stroke(压边圈行程):190mm Drawbeads(拉延筋): 实际筋 Master Surf(基准面): 上型 Accuracy(精度);一般