简述熔融沉积成型的成型原理
熔融沉积成型技术的原理
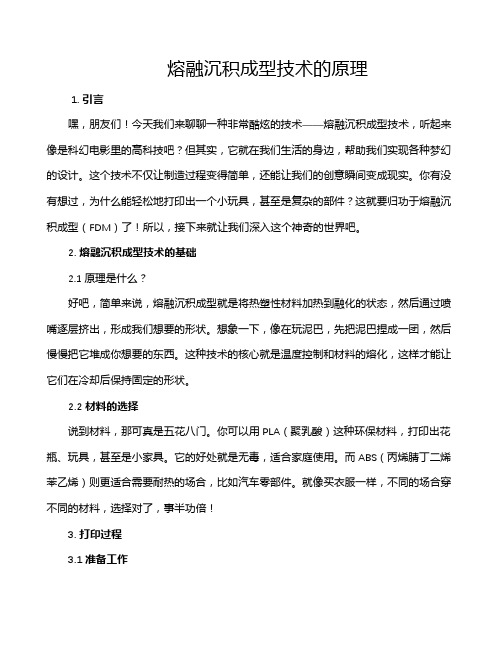
熔融沉积成型技术的原理1. 引言嘿,朋友们!今天我们来聊聊一种非常酷炫的技术——熔融沉积成型技术,听起来像是科幻电影里的高科技吧?但其实,它就在我们生活的身边,帮助我们实现各种梦幻的设计。
这个技术不仅让制造过程变得简单,还能让我们的创意瞬间变成现实。
你有没有想过,为什么能轻松地打印出一个小玩具,甚至是复杂的部件?这就要归功于熔融沉积成型(FDM)了!所以,接下来就让我们深入这个神奇的世界吧。
2. 熔融沉积成型技术的基础2.1 原理是什么?好吧,简单来说,熔融沉积成型就是将热塑性材料加热到融化的状态,然后通过喷嘴逐层挤出,形成我们想要的形状。
想象一下,像在玩泥巴,先把泥巴捏成一团,然后慢慢把它堆成你想要的东西。
这种技术的核心就是温度控制和材料的熔化,这样才能让它们在冷却后保持固定的形状。
2.2 材料的选择说到材料,那可真是五花八门。
你可以用PLA(聚乳酸)这种环保材料,打印出花瓶、玩具,甚至是小家具。
它的好处就是无毒,适合家庭使用。
而ABS(丙烯腈丁二烯苯乙烯)则更适合需要耐热的场合,比如汽车零部件。
就像买衣服一样,不同的场合穿不同的材料,选择对了,事半功倍!3. 打印过程3.1 准备工作在开始打印之前,有几步是必须得做的。
首先,你需要设计一个模型,这可以用软件像Tinkercad、Fusion 360来完成,真的超级简单。
设计好之后,将文件转换成3D打印机能识别的格式,这就像把外语翻译成母语,让机器听懂你的指令。
然后,选择好材料,装载进打印机,就等着它大展身手了。
3.2 实际操作接下来就是最激动人心的部分了!打印机开始工作,喷嘴发出“滋滋”的声音,慢慢地将熔化的塑料层层叠加。
这时候,你可能会想,哇,这么神奇的过程,真是让人目瞪口呆!每一层材料就像是画画,上一层下去,再加一层,最后就能看到你设计的物品慢慢成形。
等到打印结束,打开盖子,取出作品,那种成就感简直无法用言语形容,心里暗想:“这就是我的杰作!”4. 总结总的来说,熔融沉积成型技术真的是一门让人眼前一亮的艺术,兼具科技感与创造力。
熔融沉积成型技术原理

熔融沉积成型技术原理熔融沉积成型技术(Melt Deposition Modeling,MDM)是一种先进的快速成型技术,它利用高能激光束或电子束将金属粉末熔融成型,逐层堆积,最终形成所需的零件。
这种技术在航空航天、汽车制造、医疗器械等领域有着广泛的应用前景。
本文将介绍熔融沉积成型技术的原理及其应用。
首先,熔融沉积成型技术的原理是基于金属粉末的熔融堆积。
在成型过程中,激光束或电子束对金属粉末进行瞬间加热,使其熔化成液态金属,然后在特定的位置上进行凝固,形成一层固态金属。
接着,工作台下降一个层次,再次喷射金属粉末,重复上述过程,直至整个零件成型。
这种逐层堆积的方式使得熔融沉积成型技术能够制造出复杂形状的零件,且具有较高的成型精度。
其次,熔融沉积成型技术的原理还包括材料的选择和热力学特性的控制。
在选择材料时,需要考虑金属粉末的熔点和热导率等因素,以确保在激光束或电子束的作用下能够快速熔化和凝固。
同时,需要控制金属粉末的喷射速度、激光束或电子束的功率和扫描速度等参数,以使得每一层的成型质量得到保障。
最后,熔融沉积成型技术的原理还涉及到成型过程中的温度控制和残余应力的消除。
由于金属粉末的熔化和凝固过程是在极短的时间内完成的,因此需要对成型区域进行精确的温度控制,以避免出现裂纹和变形等缺陷。
同时,还需要对成型后的零件进行热处理等工艺,以消除残余应力,提高零件的稳定性和耐久性。
总之,熔融沉积成型技术的原理是基于金属粉末的熔融堆积,通过控制材料特性、热力学参数和成型过程中的温度和应力等因素,实现对复杂零件的高效成型。
这种技术具有成型速度快、成本低、适用性广等优点,将在未来的制造业中发挥重要作用。
简述熔融沉积成型的成型原理(一)
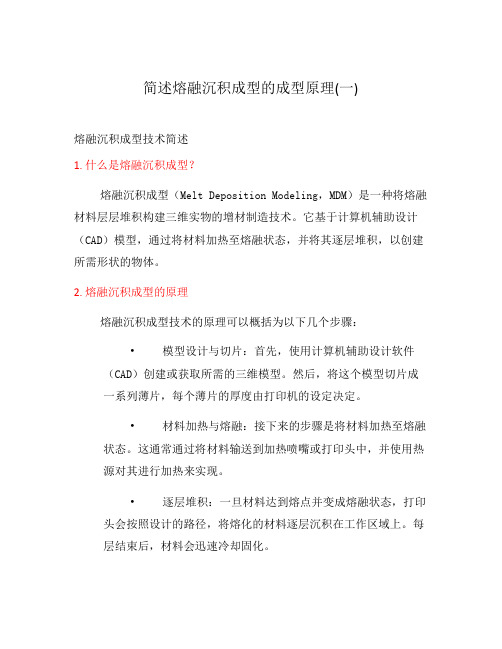
简述熔融沉积成型的成型原理(一)熔融沉积成型技术简述1. 什么是熔融沉积成型?熔融沉积成型(Melt Deposition Modeling,MDM)是一种将熔融材料层层堆积构建三维实物的增材制造技术。
它基于计算机辅助设计(CAD)模型,通过将材料加热至熔融状态,并将其逐层堆积,以创建所需形状的物体。
2. 熔融沉积成型的原理熔融沉积成型技术的原理可以概括为以下几个步骤:•模型设计与切片:首先,使用计算机辅助设计软件(CAD)创建或获取所需的三维模型。
然后,将这个模型切片成一系列薄片,每个薄片的厚度由打印机的设定决定。
•材料加热与熔融:接下来的步骤是将材料加热至熔融状态。
这通常通过将材料输送到加热喷嘴或打印头中,并使用热源对其进行加热来实现。
•逐层堆积:一旦材料达到熔点并变成熔融状态,打印头会按照设计的路径,将熔化的材料逐层沉积在工作区域上。
每层结束后,材料会迅速冷却固化。
•层间附着:固化的每层通过层间粘结力与下一层成为一体,形成一个坚固的整体结构。
•重复堆积与冷却:以上步骤循环迭代,直到最后一层被堆积完成。
在最后一层完成后,整个打印件会继续冷却,以确保结构的稳定性和强度。
3. 熔融沉积成型的应用领域熔融沉积成型具有广泛的应用领域。
以下是一些常见的应用领域示例:•原型制作:熔融沉积成型技术被广泛应用于原型制作领域。
它能够快速制造出高度复杂的原型模型,为设计师和工程师提供了快速验证设计的能力。
•定制产品:熔融沉积成型技术还可以用于制造个性化的定制产品。
通过根据客户的要求进行定制设计和制造,可以满足个人化需求,例如个性化饰品、定制鞋类等。
•检验工具:熔融沉积成型技术可以用于制造各种类型的检验工具和模型,用于质量控制和检验过程中。
4. 常见的熔融沉积成型设备目前市场上有许多不同类型的熔融沉积成型设备。
以下是几种常见的设备类型:•熔融沉积成型机:这种设备通常包含一个加热喷嘴,用于将材料加热至熔点,并通过定位系统逐层堆积材料。
第五章 熔融沉积成型(FDM)
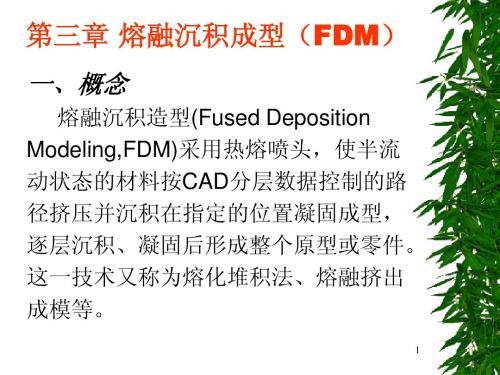
3.软件系统 软件系统包括几何建模和信息处理两部分。 几何建模单元是由设计人员借助AD软件,如 PROE等构造产品的实体模型或内三维测量仪 获取产品的数据重构产品的实体模型。 信息处理单元由STL文件处理、工艺处理数 控、图形显示等模块组成,分别完成STL文件 错误数据检验与修复、层片文件生成、填充线 计算、数控代码生成和对成型机的控制。 4.供料系统 低的凝固收缩率、陡的粘度—温度曲线和一 定的强度、硬度、强韧性。一般的塑料、蜡等 6 热塑性材料经适当改性后都可以使用。
4
三、制造系统的组成
1.机械系统 包括运动、喷头、成型宝、材料室、控制室 和电源室等单元。其机械系统采用模块化设计, 各个单元相互独立。 2.控制系统 基于PC总线的运动控制卡能实现直线、圆弧 插补和多轴联动。PC总线的喷头控制卡用于完 成喷头的出丝控制,具有超前与滞后动作补偿。 喷头控制卡与运动控制卡能够协同丁作。
9
Application Areas
Conceptual modeling Fit, form and functional test Pattern for investment casting The MABS (methy methacrylate ABS) material is particularly suitable for medical applications
8
Disadvantages
Accuracy is relatively low and is difficult to build parts with complicated details Poor strength in vertical direction Slow for building a mass part
简述熔融沉积成型的成型原理

简述熔融沉积成型的成型原理熔融沉积成型是一种先进的制造技术,通过将材料加热至熔点,使其熔化成液态,然后通过喷射或涂覆的方式将熔融材料沉积在基底上,最终形成所需的零件或构件。
这种成型方法具有高效、灵活和精密的特点,被广泛应用于航空航天、汽车制造、医疗器械等领域。
熔融沉积成型的原理是基于材料的熔化和凝固过程。
首先,选择适合的材料并加热至其熔点,使其转变成液态。
然后,通过喷射或涂覆的方式将熔融材料沉积在基底上。
喷射方式通常使用喷嘴将熔融材料喷射到基底上,形成一层薄膜。
涂覆方式则是将熔融材料涂覆在基底上,形成一层均匀的涂层。
最后,熔融材料在基底上冷却凝固,形成所需的零件或构件。
熔融沉积成型的原理可以分为两个主要过程:熔化和凝固。
在熔化过程中,材料被加热至其熔点,形成液态。
这一过程可以通过电弧、激光或电子束等加热源来实现。
加热源的选择取决于材料的性质和所需成型的精度。
在熔化过程中,材料的表面张力会使其形成球形,这种球形的特性有助于喷射或涂覆过程的进行。
在凝固过程中,熔融材料在基底上冷却凝固,形成均匀的涂层或薄膜。
凝固过程中,材料的温度逐渐降低,由液态转变为固态。
在这个过程中,凝固速度对成型的质量和性能起着重要作用。
如果凝固速度过快,可能会导致材料内部产生缺陷,影响成型的质量。
因此,控制凝固速度是熔融沉积成型的关键之一。
熔融沉积成型的原理可以应用于各种材料,包括金属、陶瓷和塑料等。
不同材料的熔化和凝固过程可能存在差异,需要针对不同材料进行调整和优化。
同时,熔融沉积成型还可以实现多材料的复合成型,通过控制不同材料的比例和喷射顺序,可以在基底上形成复合材料结构,提高材料的性能和功能。
熔融沉积成型是一种高效、灵活和精密的制造技术,通过将材料加热至熔点,使其熔化成液态,然后将熔融材料沉积在基底上,最终形成所需的零件或构件。
这种成型原理可以应用于各种材料,并且可以实现多材料的复合成型。
熔融沉积成型的发展将为制造业带来新的机遇和挑战,推动制造业向数字化、柔性化和智能化方向发展。
熔融沉积成型技术原理

熔融沉积成型技术原理熔融沉积成型技术(Fused Deposition Modeling,FDM)是一种常见的3D打印技术,也被称为熔融沉积制造。
它是一种将熔融的材料通过喷嘴逐层沉积,最终构建出三维实物的方法。
本文将介绍熔融沉积成型技术的原理及其应用。
熔融沉积成型技术的原理主要分为四个步骤:建模、切片、预处理和成型。
建模是指使用计算机辅助设计(CAD)软件创建三维模型。
这个模型可以是从零开始设计,也可以是从现有的物体扫描或下载。
在建模过程中,可以对模型进行编辑、调整和优化,以确保最终打印出来的物体满足需求。
接下来,切片是将三维模型切割成一层层的二维切片,每个切片都代表了打印出来的一层。
切片软件通常会根据所选的打印参数,例如层高、填充密度等,生成适合打印的切片图像。
然后,预处理是指对切片图像进行处理,以便将其转换为打印机可以理解的指令。
这些指令包括控制打印机的运动、温度和材料供给等。
预处理软件会将每个切片图像转换为打印机可以执行的指令序列,这些指令将用于控制打印机的运动和材料的沉积。
成型是指将熔融的材料通过打印头逐层沉积到打印平台上,逐渐构建出最终的三维实物。
打印头通常会加热并将材料推送到沉积区域,使其熔化并与前一层的材料粘合在一起。
随着打印头的运动,材料会逐渐沉积,从而形成一个完整的三维物体。
熔融沉积成型技术具有许多优点,使其在各个领域得到广泛应用。
首先,它可以实现快速、准确和经济高效的原型制作。
相比传统的制造方法,熔融沉积成型技术可以大大缩短产品的开发周期,节省制造成本。
熔融沉积成型技术可以制造复杂的几何形状和内部结构。
由于打印是逐层进行的,因此可以实现更多细节和内部空间,这是传统制造方法无法实现的。
这使得熔融沉积成型技术在医疗、航空航天和汽车等行业中具有广阔的应用前景。
熔融沉积成型技术可以使用多种材料,如塑料、金属和陶瓷等。
这种多材料选择的灵活性使得熔融沉积成型技术在不同行业和应用中具有广泛的适应性。
3d打印熔融沉积成型原理

3d打印熔融沉积成型原理
3D打印熔融沉积成型是一种快速原型制造技术,其原理是将熔化的材料通过打印头喷射到建造平台上逐层堆叠形成物体。
下面将详细介绍3D打印熔融沉积成型的原理以及其工作流程。
原理:
3D打印熔融沉积成型的原理是通过CAD(计算机辅助设计)软件
将三维模型切片成数百或数千层,然后将这些层逐层打印出来。
打印时,打印头将熔化的材料喷射到建造平台上,一层层堆积成所需的
3D模型。
在打印过程中,打印头会按照预设的路径移动,同时喷射材料,形成连续的图层,最终形成一个完整的3D模型。
工作流程:
3D打印熔融沉积成型的工作流程包括以下几个步骤:
1. 设计模型:首先需要使用CAD软件设计所需的3D模型,可以通过手动绘制或扫描现有物体得到。
2. 切片:将设计好的3D模型进行切片处理,将其分成数百或数千个非常薄的水平层。
3. 准备材料:根据所需的3D模型,选择适当的材料,如ABS, PLA, NYLON等。
4. 打印:将所选的材料放入3D打印机中,启动打印程序,打印头将逐层喷射熔化的材料。
5. 完成打印:当所有图层都打印完成后,将建造平台取出,清除支撑结构和残余材料,最终得到一个完整的3D模型。
总结:
3D打印熔融沉积成型是一种快速、灵活、低成本的原型制造技术。
其工作原理和工作流程都相对简单,只需设计好3D模型并选择适当的材料,就可以通过3D打印机将所需物体快速打印出来。
随着3D打印技术的不断发展,它将在许多领域得到广泛应用,如医疗、航空、建筑等。
简述熔融沉积快速成型技术
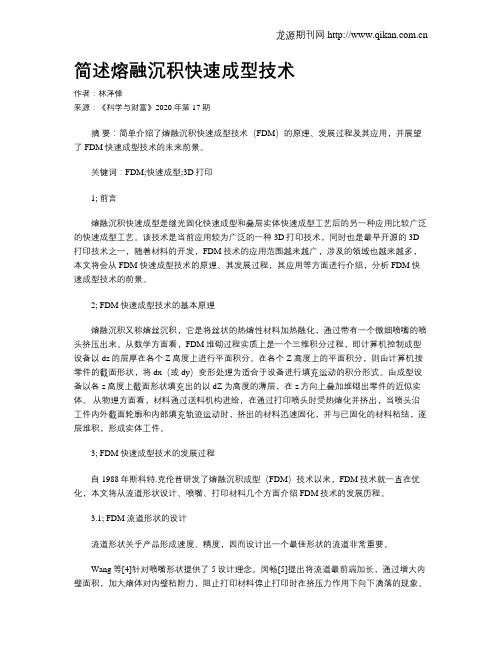
简述熔融沉积快速成型技术作者:林泽锋来源:《科学与财富》2020年第17期摘要:简单介绍了熔融沉积快速成型技术(FDM)的原理、发展过程及其应用,并展望了FDM快速成型技术的未来前景。
关键词:FDM;快速成型;3D打印1; 前言熔融沉积快速成型是继光固化快速成型和叠层实体快速成型工艺后的另一种应用比较广泛的快速成型工艺。
该技术是当前应用较为广泛的一种3D打印技术,同时也是最早开源的3D 打印技术之一,随着材料的开发,FDM技术的应用范围越来越广,涉及的领域也越来越多,本文将会从FDM快速成型技术的原理、其发展过程,其应用等方面进行介绍,分析FDM快速成型技术的前景。
2; FDM快速成型技术的基本原理熔融沉积又称熔丝沉积,它是将丝状的热熔性材料加热融化,通过带有一个微细喷嘴的喷头挤压出来。
从数学方面看,FDM堆砌过程实质上是一个三维积分过程,即计算机控制成型设备以dz的层厚在各个Z高度上进行平面积分。
在各个Z 高度上的平面积分,则由计算机按零件的截面形状,将dx(或dy)变形处理为适合于设备进行填充运动的积分形式。
由成型设备以各z高度上截面形状填充出的以dZ为高度的薄层,在z方向上叠加堆砌出零件的近似实体。
从物理方面看,材料通过送料机构进给,在通过打印喷头时受热熔化并挤出,当喷头沿工件内外截面轮廓和内部填充轨迹运动时,挤出的材料迅速固化,并与已固化的材料粘结,逐层堆积,形成实体工件。
3; FDM快速成型技术的发展过程自1988年斯科特.克伦普研发了熔融沉积成型(FDM)技术以来,FDM技术就一直在优化,本文将从流道形状设计、喷嘴、打印材料几个方面介绍FDM技术的发展历程。
3.1; FDM流道形状的设计流道形状关乎产品形成速度、精度,因而设计出一个最佳形状的流道非常重要。
Wang等[4]针对喷嘴形状提供了5设计理念。
闵畅[5]提出将流道最前端加长,通过增大内壁面积,加大熔体对内壁粘附力,阻止打印材料停止打印时在挤压力作用下向下滴落的现象。
熔融沉积成型技术(一)
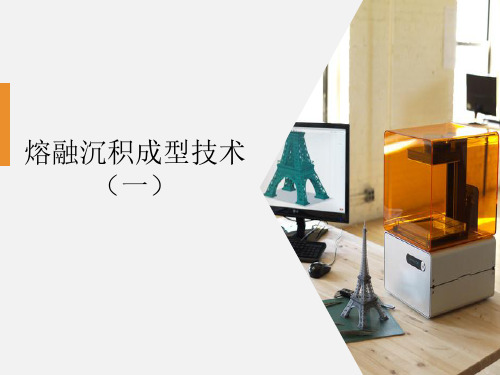
1、 熔融沉积成型技术成型原理
当制件的轮廓变化较大时, 前一层的强度不足以支撑当前层, 需设计适当的支撑,保证模型顺 利成形。
目前,很多工业级FDM设备 采用双喷嘴,一个喷嘴用于填充 成形材料,一个喷嘴用于填充支 撑材料,成形速度为单喷头的5 倍左右。
2. 熔融沉积成型挤出过程
熔融挤出过程如下:通过控制FDM喷头加热器,直接将 丝状或粒状的热熔性材料加热熔化。
在国内,清华大学也较早地进行了FDM工艺 商品化系统的研制工作,并推出熔融挤压制造设备 MEM250。
一、 熔融沉积成型技术成型原理
1、 熔融沉积成型技术成型原理
熔融沉积(简称FDM) 又叫熔丝沉积,采用丝状材料作为加工物质。 成型设备主要由送丝机构、喷头 、工作台、运动机构以及控制系统 组成。
(b)为清华大学开发的弹簧挤压摩擦轮送料装置。该装置采用可调 直流电机来带动摩擦轮,并通过压力弹簧将丝料压紧在两个摩擦轮 之间,两摩擦轮是活动结构,其间距可调,压紧力可通过螺母调节, 这就解决了图(a)喷头结构中进料装置的缺点。该进料装置的优点 是结构简单、轻巧,可实现连续稳定地进料,可靠性高。
1.丝料;2.可调直流电机;3.压力弹簧;4.螺母;5.摩擦轮;6.丝料入口
螺杆式出丝系统工作原理图
二、 熔融沉积成型技术成型特点
1、 熔融沉积成型技术优点
(1)成本低。FDM技术无需激光系统,因而价格低廉。现在市场上 的桌面打印机大多采用FDM技术,最便宜的已经降至1万元以下。
(2)原材料的利用率高。没有废弃的成型材料,支撑材料可以回收。 且没有毒气或化学物质的污染。
(3)设备、材料体积较小,原材料以材料卷的形式提供,易于搬运和 快速更换。
缺点:(1)精度低。(2)强度低。(3)打印时间长。(4)需要支撑 材料。
熔融沉积成型技术原理
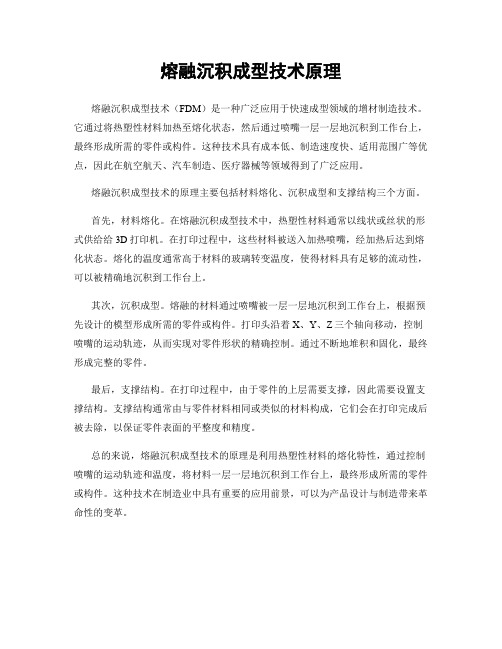
熔融沉积成型技术原理
熔融沉积成型技术(FDM)是一种广泛应用于快速成型领域的增材制造技术。
它通过将热塑性材料加热至熔化状态,然后通过喷嘴一层一层地沉积到工作台上,最终形成所需的零件或构件。
这种技术具有成本低、制造速度快、适用范围广等优点,因此在航空航天、汽车制造、医疗器械等领域得到了广泛应用。
熔融沉积成型技术的原理主要包括材料熔化、沉积成型和支撑结构三个方面。
首先,材料熔化。
在熔融沉积成型技术中,热塑性材料通常以线状或丝状的形式供给给3D打印机。
在打印过程中,这些材料被送入加热喷嘴,经加热后达到熔化状态。
熔化的温度通常高于材料的玻璃转变温度,使得材料具有足够的流动性,可以被精确地沉积到工作台上。
其次,沉积成型。
熔融的材料通过喷嘴被一层一层地沉积到工作台上,根据预先设计的模型形成所需的零件或构件。
打印头沿着X、Y、Z三个轴向移动,控制喷嘴的运动轨迹,从而实现对零件形状的精确控制。
通过不断地堆积和固化,最终形成完整的零件。
最后,支撑结构。
在打印过程中,由于零件的上层需要支撑,因此需要设置支撑结构。
支撑结构通常由与零件材料相同或类似的材料构成,它们会在打印完成后被去除,以保证零件表面的平整度和精度。
总的来说,熔融沉积成型技术的原理是利用热塑性材料的熔化特性,通过控制喷嘴的运动轨迹和温度,将材料一层一层地沉积到工作台上,最终形成所需的零件或构件。
这种技术在制造业中具有重要的应用前景,可以为产品设计与制造带来革命性的变革。
熔融沉积快速成型工艺技术

ξ2 快速成型制造工艺
模具工程技术研究中心 METRC
(二)气压式熔融沉积快速成形系统的特点
成型材料广泛
一般的热塑性材料如塑料、尼龙、橡胶、蜡等,作适当改性后都可用于沉积成 形。
设备成本低、体积小
熔融沉积成形是靠材料熔融时的粘性粘结成形,不象SLA、LOM、SLS等工艺靠 激光的作用来成形,没有激光器及其电源和树脂槽,大大简化了设备,使成本降低。 熔融沉积成形设备运行、维护容易,工作可靠,是桌面化快速成形设备的最佳工艺。
(1)FDM在日本丰田公司的应用
丰田公司采用FDM工艺制作右侧镜支架和四个门把手的母模,通过快速模具 技术制作产品而取代传统的CNC制模方式,使得2000 Avalon车型的制造成本显 著降低,右侧镜支架模具成本降低20万美元,四个门把手模具成本降低30万美元 。FDM工艺已经为丰田公司在轿车制造方面节省了200万美元。
模具工程技术研究中心 METRC
ξ2 快速成型制造工艺
模具工程技术研究中心 METRC
将实芯丝材原材料缠绕在供料辊上,由电机驱动辊子旋转,辊子和丝材之间的 摩擦力使丝材向喷头的出口送进。在供料辊与喷头之间有一导向套,导向套采用低 摩擦材料制成,以便丝材能顺利、准确地由供料辊送到喷头的内腔(最大送料速度 为10~25mm/s,推荐速度为5~18mm/s)。喷头的前端有电阻丝式加热器,在其 作用下,丝材被加热熔融(熔模铸造蜡丝的熔融温度为74℃,机加工蜡丝的熔融温 度为96℃,聚烯烃树脂丝为106℃,聚酰胺丝为155℃,ABS塑料丝为270℃),然 后通过出口(内径为0.25~1.32mm,随材料的种类和送料速度而定),涂覆至工作 台上,并在冷却后形成界面轮廓。由于受结构的限制,加热器的功率不可能太大, 因此,丝材一般为熔点不太高的热塑性塑料或蜡。丝材熔融沉积的层厚随喷头的运 动速度(最高速度为380mm/s)而变化,通常最大层厚为0.15~0.25mm。
试析国内熔融沉积快速成型技术的发展滞因及未来发展趋势
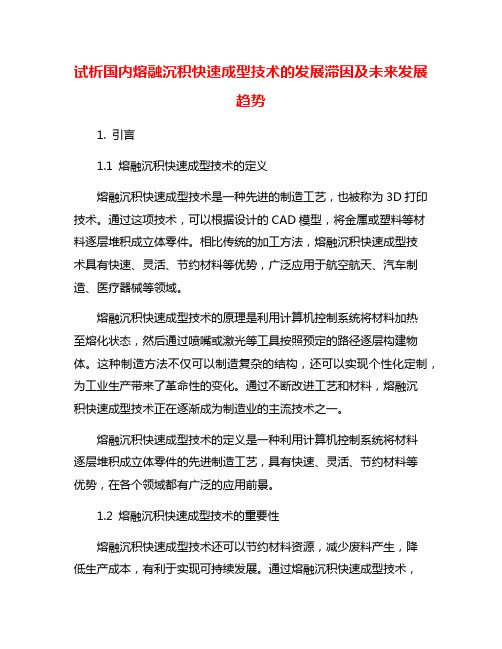
试析国内熔融沉积快速成型技术的发展滞因及未来发展趋势1. 引言1.1 熔融沉积快速成型技术的定义熔融沉积快速成型技术是一种先进的制造工艺,也被称为3D打印技术。
通过这项技术,可以根据设计的CAD模型,将金属或塑料等材料逐层堆积成立体零件。
相比传统的加工方法,熔融沉积快速成型技术具有快速、灵活、节约材料等优势,广泛应用于航空航天、汽车制造、医疗器械等领域。
熔融沉积快速成型技术的原理是利用计算机控制系统将材料加热至熔化状态,然后通过喷嘴或激光等工具按照预定的路径逐层构建物体。
这种制造方法不仅可以制造复杂的结构,还可以实现个性化定制,为工业生产带来了革命性的变化。
通过不断改进工艺和材料,熔融沉积快速成型技术正在逐渐成为制造业的主流技术之一。
熔融沉积快速成型技术的定义是一种利用计算机控制系统将材料逐层堆积成立体零件的先进制造工艺,具有快速、灵活、节约材料等优势,在各个领域都有广泛的应用前景。
1.2 熔融沉积快速成型技术的重要性熔融沉积快速成型技术还可以节约材料资源,减少废料产生,降低生产成本,有利于实现可持续发展。
通过熔融沉积快速成型技术,可以实现轻量化设计,减轻产品重量,提高产品性能,同时还可以实现废旧物资的再利用,实现循环经济的发展。
熔融沉积快速成型技术的重要性体现在提高生产效率、满足个性化需求、节约资源、降低成本、推动可持续发展等方面,对于我国的制造业发展具有重要的意义。
加强熔融沉积快速成型技术的研究和推广是十分必要的。
2. 正文2.1 国内熔融沉积快速成型技术发展的现状熔融沉积快速成型技术是一种先进的制造技术,已经在国内得到了广泛应用和推广。
目前,国内熔融沉积快速成型技术的发展已经取得了一定的成就。
在技术水平方面,国内企业已经能够独立研发和生产出一系列熔融沉积快速成型设备,并且实现了一些技术指标的突破。
在应用领域方面,熔融沉积技术已经被广泛应用于航空航天、汽车制造、医疗器械等领域,为我国制造业发展提供了有力支撑。
熔融沉积快速成型工艺技术

熔融沉积快速成型工艺技术熔融沉积快速成型工艺技术(Rapid Prototyping by Additive Manufacturing)是一种新兴的制造技术,它可以通过将材料一层层地堆积在一起来创建复杂的三维物体。
这种技术已经在许多领域得到了广泛的应用,包括航空航天、医疗、汽车制造等。
熔融沉积快速成型工艺技术的出现,使得制造业在生产效率、成本控制和产品设计方面都取得了重大进展。
熔融沉积快速成型工艺技术的原理是利用计算机辅助设计(CAD)软件将三维模型分解成许多薄层,然后通过一种称为“熔融沉积”的方法,将材料一层层地堆积起来。
这种堆积过程通常是通过喷嘴或激光熔化材料来实现的。
在堆积过程中,每一层的形状都是根据前一层的形状来确定的,这样就可以逐层地构建出复杂的三维结构。
最终,堆积完成后,就可以得到一个与设计模型完全相同的实体物体。
熔融沉积快速成型工艺技术的优势之一是可以快速制造出复杂的结构。
传统的制造方法通常需要制作模具或者进行多道工序的加工,而熔融沉积快速成型工艺技术可以直接根据设计模型来制造物体,大大节省了制造时间。
此外,由于是通过堆积材料来制造物体,因此可以实现对材料的高效利用,减少了浪费。
另外,熔融沉积快速成型工艺技术还可以实现个性化定制,因为可以根据客户的需求来制造不同的产品。
在航空航天领域,熔融沉积快速成型工艺技术已经得到了广泛的应用。
航空航天零部件通常需要具有复杂的结构和高强度,而传统的制造方法往往难以满足这些要求。
熔融沉积快速成型工艺技术可以根据设计模型直接制造出具有复杂结构的零部件,而且可以使用各种先进的材料,如钛合金、高温合金等,来满足航空航天领域对材料性能的要求。
此外,熔融沉积快速成型工艺技术还可以实现对零部件的修复和更新,大大延长了零部件的使用寿命。
在医疗领域,熔融沉积快速成型工艺技术也发挥着重要作用。
医疗器械和假体通常需要根据患者的个体特征来定制,而传统的制造方法往往难以满足这些要求。
熔融沉积制模过程及原理资料讲解

熔融沉积制模过程及原理快速成型原理及误差分析1 熔融沉积制模过程及原理熔丝堆积成形,FDM,Fused Deposition Modeling。
也叫熔融沉积。
是一种基于数字成像技术的三维实体模型制造,它无需激光系统。
将丝状热熔性材料加热熔化,然后通过带有一个微细喷嘴的喷头挤喷出来。
喷头可沿X轴方向移动,而工作台则沿Y方向移动。
如果热熔性材料的温度始终稍高于固化温度,而成型部分的温度稍低于固化温度,就能保证热熔性材料挤喷出喷嘴后与前面一层熔结在一起。
一个层面沉积完成后,工作台按预定的增量下降一个层的厚度,再继续熔喷沉积,直到完成整个实体造型。
在制造前先要进行以下步骤的前处理:(1)CAD三维造型。
三维造型是CAD模型的最好表达,也是快速原型制作必须的原始数据。
三维造型可以在UG、Pro/E、Catie等大型商业软件上进行。
(2)数据转换。
数据转换是对产品CAD模型的近似处理,主要是生成STL格式的数据文件。
注意控制STL文件生成的精度。
通用CAD软件都有STL数据输出。
(3)确定摆放位置。
摆放位置不但影响着制作时间和效率,更影响这后续支撑的施加以及原型制造的表面质量等。
从缩短原型制作的时间来看,应选尺寸最小的方向作为叠层方向;为了提高原型质量和提高关键尺寸和形状的精度,又需选尺寸最大的方向作为叠层方向;为减少支撑、节省材料、便于后处理,常倾斜摆放。
(4)施加支撑。
对于结构复杂的数据模型,支撑的施加是费时而精细的。
比较先进的支撑类型为点支撑,即在支撑和需要支撑的模型面是点接触的。
(5)切片分层。
根据设备系统的分层厚度沿高度方向进行切片,生成系统需求的层片数据文件。
Creo模型导入STL生成软件Cura对模型添加支承和进行切片处理其中设计软件和打印机之间协作的标准文件格式是STL文件格式。
一个STL文件使用三角面来近似模拟物体的表面。
三角面越小其生成的表面分辨率越高。
打印机通过读取文件中的横截面信息,用液体状材料将这些截面逐层地打印出来,再将各层截面以各种方式粘合起来从而制造出一个实体。
熔融沉积快速成型工艺技术

模具工程技术研究中心 METRC
ξ2 快速成型制造工艺
模具工程技术研究中心 METRC
二、熔融沉积工艺的特点
优点
系统构造原理和操作简单,维护成本低,系统运行安全。 可以使用无毒的原材料,设备系统可在办公环境中安装使用。 用蜡成形的零件原型,可以直接用于失蜡铸造。 可以成型任意复杂程度的零件,常用于成型具有很复杂的内腔、孔等零件。 原材料在成型过程中无化学变化,制件的翘曲变形小。 原材料利用率高,且材料寿命长。 支撑去除简单,无需化学清洗,分离容易。
AJS系统主要由控制、加热与冷却、挤压、喷头机构、可升降工作台及 支架机构6部分组成。其中控制用计算机配置有CAD模型切片软件和加支撑软 件,对三维模型进行切片和诊断,并在零件的高度方向,模拟显示出每隔一 定时间的一系列横截面的轮廓,加支撑软件对零件进行自动加支撑处理。数 据处理完毕后,混合均匀的材料按一定比例人工送入加热室。加热室由电阻 丝加热,经热电阻测温并由温度控制器使其温度恒定,使材料处于良好的熔 融挤压状态,后经压力传感器测压后进行挤压,制造原型零件。控制系统能 使整个AJS系统实现自动控制,其中包括气路的通断、喷头的喷射速度以及 喷射量与原型零件整体制造速度的匹配等。
无污染
熔融沉积成形所用的材料为无毒、无味的热塑性材料,并且废弃的材料还可以回 收利用,因此材料对周围环境不会造成污染。
ξ2 快速成型制造工艺
模具工程技术研究中之处
① FDM工艺一般采用低熔点丝状材料,如蜡丝或ABS塑料丝,如果采用高熔点 的热塑性复合材料,或对于一些不易加工成丝材的材料,如EVA材料等,就会相 当困难。该系统无需再采用专门的挤压成丝设备来制造丝材,工作时只需将热塑 性材料直接倒入喷头的腔体内,依靠加热装置将其加热到熔融挤压状态,不但避 免了必须采用丝材材料这一限制,而且节省了一道工序,提高了生产效率。
简述熔融沉积成型的成型原理

简述熔融沉积成型的成型原理
熔融沉积成型(Fused Deposition Modeling,简称FDM)是一
种常用的增材制造工艺,其成型原理如下:
1. 建模设计:首先,使用计算机辅助设计(CAD)软件创建
三维模型。
设计师可以根据需要调整模型的大小和形状。
2. 打印设置:在打印前,需要进行打印设置,包括选择打印材料(通常是热塑性聚合物),设置打印温度和打印速度等参数。
3. 切片处理:将三维模型切片,将其分解为一系列二维层次切片。
每个层次切片都包含了实际打印时需要的精确信息。
4. 加热和挤出:加热打印头中的塑料材料到其熔点以上的温度。
然后,通过打印头的挤出机构将熔化的塑料材料从针尖喷出,以一定的速度形成连续的熔融线。
5. 堆叠层叠:打印头在打印平台上移动,按照切片的路径逐层堆叠熔融线。
温度较高的熔融线会粘合到下一层,并随着打印头的移动逐渐冷却和凝固。
6. 完成成品:一旦打印完成,待打印对象从打印平台上取下。
可以进行后续的处理,如去除支撑结构、打磨等。
总结起来,熔融沉积成型的成型原理是通过加热和挤出的过程,将熔化的材料堆叠成固定形状的三维对象。
通过逐层堆叠和粘合,最终得到一个完整的成品。
熔融沉积原理
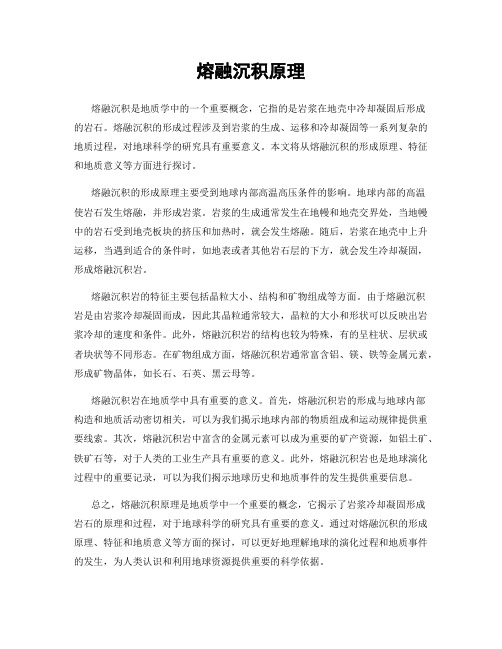
熔融沉积原理熔融沉积是地质学中的一个重要概念,它指的是岩浆在地壳中冷却凝固后形成的岩石。
熔融沉积的形成过程涉及到岩浆的生成、运移和冷却凝固等一系列复杂的地质过程,对地球科学的研究具有重要意义。
本文将从熔融沉积的形成原理、特征和地质意义等方面进行探讨。
熔融沉积的形成原理主要受到地球内部高温高压条件的影响。
地球内部的高温使岩石发生熔融,并形成岩浆。
岩浆的生成通常发生在地幔和地壳交界处,当地幔中的岩石受到地壳板块的挤压和加热时,就会发生熔融。
随后,岩浆在地壳中上升运移,当遇到适合的条件时,如地表或者其他岩石层的下方,就会发生冷却凝固,形成熔融沉积岩。
熔融沉积岩的特征主要包括晶粒大小、结构和矿物组成等方面。
由于熔融沉积岩是由岩浆冷却凝固而成,因此其晶粒通常较大,晶粒的大小和形状可以反映出岩浆冷却的速度和条件。
此外,熔融沉积岩的结构也较为特殊,有的呈柱状、层状或者块状等不同形态。
在矿物组成方面,熔融沉积岩通常富含铝、镁、铁等金属元素,形成矿物晶体,如长石、石英、黑云母等。
熔融沉积岩在地质学中具有重要的意义。
首先,熔融沉积岩的形成与地球内部构造和地质活动密切相关,可以为我们揭示地球内部的物质组成和运动规律提供重要线索。
其次,熔融沉积岩中富含的金属元素可以成为重要的矿产资源,如铝土矿、铁矿石等,对于人类的工业生产具有重要的意义。
此外,熔融沉积岩也是地球演化过程中的重要记录,可以为我们揭示地球历史和地质事件的发生提供重要信息。
总之,熔融沉积原理是地质学中一个重要的概念,它揭示了岩浆冷却凝固形成岩石的原理和过程,对于地球科学的研究具有重要的意义。
通过对熔融沉积的形成原理、特征和地质意义等方面的探讨,可以更好地理解地球的演化过程和地质事件的发生,为人类认识和利用地球资源提供重要的科学依据。
熔融沉积快速成型工艺的原理及过程

熔融沉积快速成型工艺的原理及过程赵萍;蒋华;周芝庭【摘要】快速成型技术中的熔融沉积造型(FDM)工艺由于设备费用较低、材料利用率较高而在实际生产中得到广泛的应用.介绍了FDM的工艺原理和工艺过程,并指出该工艺的特点及应用范围.【期刊名称】《机械制造与自动化》【年(卷),期】2003(000)005【总页数】3页(P17-18,23)【关键词】快速成型;熔融沉积造型(FDM);CAD;工艺原理【作者】赵萍;蒋华;周芝庭【作者单位】东南大学工业发展与培训中心,江苏,南京,210096;东南大学工业发展与培训中心,江苏,南京,210096;东南大学工业发展与培训中心,江苏,南京,210096【正文语种】中文【中图分类】工业技术·机械制造与研究赵萍等,熔融沉积快速成型工艺的原理及过程熔融沉积快速成型工艺的原理及过程赵萍,蒋华,周芝庭 (东南大学工业发展与培训中心,江苏南京 210096)摘要:快速成型技术中的熔融沉积造型(FDM) 工艺由于设备费用较低、材料利用率较高而在实际生产中得到广泛的应用。
介绍了FDM 的工艺原理和工艺过程,并指出该工艺的特点及应用范围。
关键词:快速成型;熔融沉积造型( FDM) ; CAD ;工艺原理中图分类号:TP391.72;TP391.73文献标识码: A文章编号:1671-5276(2003)05-0017-02 TheTechnologyTheory and Processfor FusedDepositionModeling RapidPrototyping ZHAO Ping,JIANGHua,ZHOUZhi-ting Centerfor Integrated Engineering, SoutheastUniversity,JS Nanjing 210096, China) Abstract:FusedDepositionModeling(FDM) in rapid prototypingtechnologyiswidelyapplied in industrybe- cause of its lowerexpenseof equipmentandlowerconsumptionof materials. In this paper, the theoryand processof FDMareintroduced. In addition, the characteristicandapplication fieldsof FDMareproposed.Keywords:rapidprototyping;fused depositionmodeling(FDM);C,AD;technologytheory O 前言快速成型技术( RapidPrototyping) 是 20 世纪80年代中后期发展起来的一项新型的造型技术。
熔融沉积原理

熔融沉积原理
熔融沉积原理是指在地质作用过程中,由于高温熔融物质的运动和沉积而形成的地质现象。
熔融沉积是地质学中一个重要的研究领域,它对于理解地球内部构造和地质演化具有重要意义。
熔融沉积的形成主要有两种方式,一种是火山喷发,另一种是岩浆侵入。
火山喷发是指地下岩浆喷发到地表形成火山岩,这些火山岩在喷发过程中会与地表的岩石和土壤发生接触和混合,最终形成熔融沉积。
岩浆侵入是指岩浆从地下向地表或地下岩层侵入并冷却凝固形成岩体,这些岩体在地下和地表都会与周围的岩石相互作用,产生熔融沉积。
熔融沉积的特点是具有高温、高压和高粘度,它在地质作用过程中对周围的岩石和矿物产生了显著的影响。
首先,熔融沉积会改变周围岩石的结构和性质,使其发生变质或变形。
其次,熔融沉积中富含的矿物和矿石对地质资源的形成和分布具有重要影响,例如金属矿床和石油气田的形成与熔融沉积密切相关。
最后,熔融沉积的形成也对地质构造和地貌地貌产生了重要影响,例如火山口、火山岩台地等地质地貌特征都是熔融沉积的产物。
熔融沉积原理的研究对于地质学、矿产资源学和环境地质学等领域具有重要意义。
通过对熔融沉积的研究,可以深入理解地球内部的构造和演化过程,为矿产资源的勘探和开发提供重要依据,同时也有助于认识地球环境的演变和地质灾害的预测与防范。
总之,熔融沉积原理是地质学中一个重要的研究领域,它对于理解地球内部构造和地质演化、矿产资源的形成和环境地质学等方面具有重要意义。
通过深入研究熔融沉积原理,可以更好地认识地球的演化过程,为人类社会的可持续发展提供重要科学依据。
- 1、下载文档前请自行甄别文档内容的完整性,平台不提供额外的编辑、内容补充、找答案等附加服务。
- 2、"仅部分预览"的文档,不可在线预览部分如存在完整性等问题,可反馈申请退款(可完整预览的文档不适用该条件!)。
- 3、如文档侵犯您的权益,请联系客服反馈,我们会尽快为您处理(人工客服工作时间:9:00-18:30)。
简述熔融沉积成型的成型原理
熔融沉积成型是一种高效、精确的制造技术,可以实现复杂零件的快速制造。
其成型原理主要基于熔融金属的沉积和凝固过程。
在熔融沉积成型过程中,金属材料首先被加热至其熔点以上,使其变为熔融状态。
然后,通过控制加热源的移动和喷射速度,将熔融金属喷射到工件的特定位置上。
在喷射过程中,熔融金属与已有的材料层发生热交换,迅速冷却并凝固。
随着喷射的持续进行,熔融金属逐渐沉积在工件上,形成所需的形状和结构。
熔融沉积成型的成型原理可以分为以下几个关键步骤:
1. 材料预处理:在熔融沉积成型之前,需要对金属材料进行预处理。
这包括去除表面的氧化物和杂质,以确保沉积的金属材料具有良好的质量和精度。
2. 加热和熔化:通过引入高温能源,如激光束或电弧,将金属材料加热至其熔点以上,使其变为熔融状态。
在熔化过程中,金属材料的颗粒逐渐熔化并形成液态金属。
3. 喷射和沉积:通过控制加热源的移动和喷射速度,将熔融金属喷射到工件的特定位置上。
喷射过程中,熔融金属与已有的材料层发生热交换,迅速冷却并凝固。
随着喷射的持续进行,熔融金属逐渐沉积在工件上,形成所需的形状和结构。
4. 层与层的连接:在沉积过程中,各层之间需要保持良好的连接。
这可以通过控制喷射参数、调整喷射路径和优化沉积策略来实现。
确保各层之间的连接性对于最终工件的性能和质量非常重要。
5. 结构调整和后处理:在完成沉积过程后,可能需要对工件进行结构调整和后处理。
这包括去除不需要的材料、表面光洁处理、热处理等。
这些步骤可以进一步提高工件的质量和性能。
熔融沉积成型技术的成型原理基于金属材料的熔化和凝固过程,通过控制喷射参数和沉积策略,可以实现复杂零件的高精度制造。
与传统的制造方法相比,熔融沉积成型具有快速、灵活和可定制性强的优势,被广泛应用于航空航天、汽车制造、医疗器械等领域。
随着材料科学和制造技术的不断发展,熔融沉积成型技术将进一步推动制造业的创新和进步。