烧结烟气制酸工艺流程图2008年
烧结(球团)工艺过程氮氧化物产生及控制
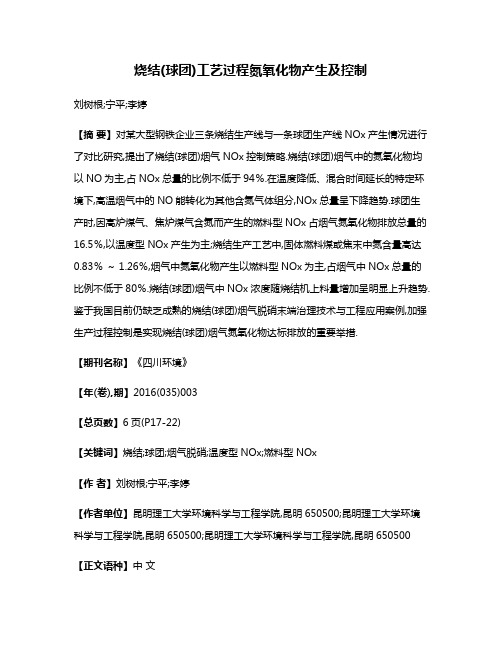
烧结(球团)工艺过程氮氧化物产生及控制刘树根;宁平;李婷【摘要】对某大型钢铁企业三条烧结生产线与一条球团生产线NOx产生情况进行了对比研究,提出了烧结(球团)烟气NOx控制策略.烧结(球团)烟气中的氮氧化物均以NO为主,占NOx总量的比例不低于94%.在温度降低、混合时间延长的特定环境下,高温烟气中的NO能转化为其他含氮气体组分,NOx总量呈下降趋势.球团生产时,因高炉煤气、焦炉煤气含氮而产生的燃料型NOx占烟气氮氧化物排放总量的16.5%,以温度型NOx产生为主;烧结生产工艺中,固体燃料煤或焦末中氮含量高达0.83%~ 1.26%,烟气中氮氧化物产生以燃料型NOx为主,占烟气中NOx总量的比例不低于80%.烧结(球团)烟气中NOx浓度随烧结机上料量增加呈明显上升趋势.鉴于我国目前仍缺乏成熟的烧结(球团)烟气脱硝末端治理技术与工程应用案例,加强生产过程控制是实现烧结(球团)烟气氮氧化物达标排放的重要举措.【期刊名称】《四川环境》【年(卷),期】2016(035)003【总页数】6页(P17-22)【关键词】烧结;球团;烟气脱硝;温度型NOx;燃料型NOx【作者】刘树根;宁平;李婷【作者单位】昆明理工大学环境科学与工程学院,昆明650500;昆明理工大学环境科学与工程学院,昆明650500;昆明理工大学环境科学与工程学院,昆明650500【正文语种】中文【中图分类】X511目前,我国钢铁行业氮氧化物控制面临严峻压力。
一方面,《钢铁烧结、球团工业大气污染物排放标准》(GB28662-2012)规定:自2015年1月1日起,现有及新建钢铁企业烧结(球团)设备执行更严格的氮氧化物排放浓度限值300 mg/m3;另一方面,我国现有钢铁企业虽已基本建成烟气脱硫设施,但烧结(球团)烟气脱硝方面的基础研究及工程应用明显滞后[1~3]。
整体来讲,烟气脱硝技术可分为催化还原法[4~6]、物理吸附法[7~9]、氧化—吸收法[10~13]、循环流化床法[14]、高能电子氧化法等主要类型。
烟气制酸工艺流程
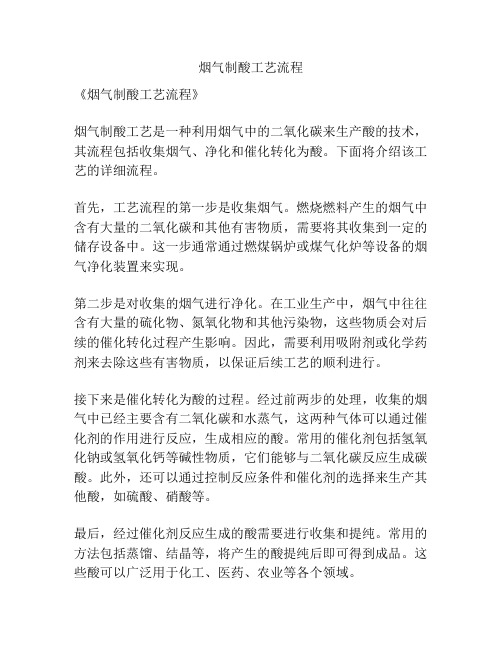
烟气制酸工艺流程
《烟气制酸工艺流程》
烟气制酸工艺是一种利用烟气中的二氧化碳来生产酸的技术,其流程包括收集烟气、净化和催化转化为酸。
下面将介绍该工艺的详细流程。
首先,工艺流程的第一步是收集烟气。
燃烧燃料产生的烟气中含有大量的二氧化碳和其他有害物质,需要将其收集到一定的储存设备中。
这一步通常通过燃煤锅炉或煤气化炉等设备的烟气净化装置来实现。
第二步是对收集的烟气进行净化。
在工业生产中,烟气中往往含有大量的硫化物、氮氧化物和其他污染物,这些物质会对后续的催化转化过程产生影响。
因此,需要利用吸附剂或化学药剂来去除这些有害物质,以保证后续工艺的顺利进行。
接下来是催化转化为酸的过程。
经过前两步的处理,收集的烟气中已经主要含有二氧化碳和水蒸气,这两种气体可以通过催化剂的作用进行反应,生成相应的酸。
常用的催化剂包括氢氧化钠或氢氧化钙等碱性物质,它们能够与二氧化碳反应生成碳酸。
此外,还可以通过控制反应条件和催化剂的选择来生产其他酸,如硫酸、硝酸等。
最后,经过催化剂反应生成的酸需要进行收集和提纯。
常用的方法包括蒸馏、结晶等,将产生的酸提纯后即可得到成品。
这些酸可以广泛用于化工、医药、农业等各个领域。
总的来说,烟气制酸工艺流程是一种有效利用烟气资源的技术,能够减少燃烧过程中产生的有害物质排放,同时生产出具有经济价值的酸产品。
随着环保意识的提高和资源化利用的重要性,该工艺将在未来得到更广泛的应用和发展。
冶炼烟气制酸工艺介绍ppt课件
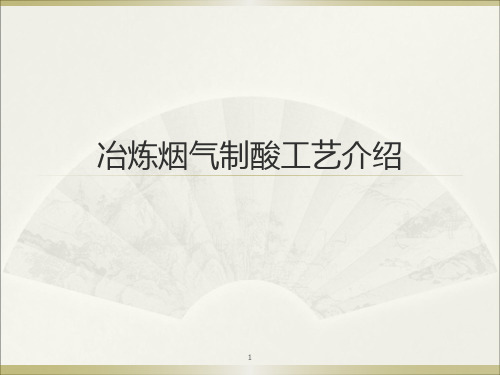
18
上清液储槽
(5)控制要点
1 事故高位槽不能缺水 2 各管道烟气温度要严格控制 3 稀酸洗净化的酸浓要有所控制 4 安全水封不能缺水 5 电除雾器的开启要求
19
4 转化工段
(1)二氧化硫转化的定义 烟气在净化工序除去矿尘、酸雾、砷、氟
等有害杂质后,再通过干吸工序的干燥塔 除去水分,然后进入转化工序,在一定的 温度下,通过触媒的催化,使烟气中的二 氧化硫与氧化合生产三氧化硫,简称二氧 化硫的转化。
尘 等杂质也进一步被清除,净化后的烟气送往干吸工段。
10
11
(4) SO2烟气净化的原理 冶炼烟气来
高位水槽
一级动力波
270~330℃
去气体冷却
塔≤65℃
排 污 管
循环泵
电 除 雾 冲 洗 来
气
冷
稀酸
串 酸
来
12
一级动力波的工作原理: 利用高速气体把从底部射 入的液体冲击成无数细小 液滴,使气液高度湍流混 合,充分接触,强化传质 传热,达到绝热降温和除 尘的目的。
氧化后SO2转化率约为94.9%的SO3气体,经各自对应的换热器
换热后送往第一吸收塔吸收SO3制取硫酸。
第一吸收塔出来的未反应的冷SO2气体,俗称二次气,利用
第Ⅲ热交换器和第Ⅱ热交换被第三段、第二段触媒出来的热气
体加热到430℃,进入转化器四段触媒层进行第二次转化。经催
化转化后,总转化率≥99.75%的SO3气体,经第Ⅳ热交换器换
热后送往第二吸收塔吸收SO3制取硫酸。
在各换热器进行换热时,被加热的SO2气体走各列管热交换
器的管间,而被冷却的SO3气体则走各列管热交换器的管内。为
了控制进第一吸收塔的SO3烟气温度不至于太高,在第Ⅲ热交换
第三章 烟气制酸

第一章概述第一节硫酸工业的发展世界上最早的硫酸,产生于15世纪后半叶,当时的原料为绿矾石[FeSO4·7H2O]。
通过对其加热分解和吸收制出硫酸。
这种方法距今已有500多年的历史了。
到了1746年世界上第一座运用亚硝基法制酸的工厂,铅室法制取硫酸在英国的伯明翰建成并投入生产。
这就是世界上最早的铅室法制酸工厂。
之后在硫酸工业和其它工业的推动下,又出现了塔式法制酸。
尽管如此,到了1940年,染料、化纤、有机合成及石油、化工等工业取得了逢勃发展,它们不仅增加了对硫酸的需求量,特别对硫酸浓度提出了更高的要求(需要发烟硫酸)。
万里铅室法、塔式法成品酸浓度不够(产品酸:65%、76%)从而不能满足上述工业部门的需要。
必需寻求制酸的新方法。
接触法诞生于1831年,用二氧化硫在空气中通过接触铂粉或铂丝并在炽热条件下制取三氧化硫为生产高浓度硫酸创造了条件。
这就是最早的接触法,触媒用昂贵的铂。
此法到了20世纪初得到了迅速的发展。
特别是1913年,前西德BASF AG公司发明出了活性好、不易中毒,而价格又较便宜的钒触媒。
钒触媒取代了铂触媒,从而推动了硫酸工业的快速发展。
世界上接触法硫酸生产装置始建于19世纪末和20世纪初,并采用了钒催化剂,到20世纪60年代,钒催化剂得到了广泛应用。
50年代初,前联邦德国和美国同时开发了硫铁矿沸腾焙烧技术。
1964年前联邦德国的一家公司开始应用两次转化工艺,70年代初又建成年产500KT硫磺制酸装置和年产360KT硫铁矿制酸装置。
90年代初,加拿大的一家公司采用美国孟山都环境化学公司技术,建成年产2900KT冶炼烟气制酸装置。
近年来,国外还出现了三转三吸工艺和加压法转化流程。
催化剂开发方面力求活性高、起燃温度低、抗毒性能好、寿命长。
在低位热能回收利用、低浓度SO2烟气回收等方面也有很大进步。
我国于1934年建成第一座接触法硫酸装置,但当时硫酸工业基础相当薄弱。
1949年以后,我国硫酸工业发生巨大的变化,不仅产量增加,生产技术也有很大的提高。
烧结烟气循环设计工艺流程

烧结烟气循环设计工艺流程1一般规定1.1 烧结烟气循环技术的实施,总体原则是在烧结矿产量、质量指标以及烧结矿硫含量不受明显影响的前提下,提高烧结清洁生产的水平。
烧结烟气循环进入料面的气体,相比常规烧结的空气,其氧含量降低,温度提高,二氧化碳、一氧化碳、水蒸气含量增加。
氧含量降低会对烧结指标产生不利影响,但温度、一氧化碳含量的提高,以及含有适量的二氧化碳、水蒸气,可以削弱因氧含量下降而引起的负面影响。
合理的气流介质条件是确保烧结指标不受影响的关键。
氧气的影响:烧结气流介质中的氧气含量降低至一定程度时,因影响到燃料的充分燃烧,烧结矿的质量会急剧变差,此氧含量为烧结指标明显受到影响的临界点。
因此烧结气流介质中的氧气含量不宜低于此临界值。
相关研究表明,赤铁矿为主、磁铁矿为主、褐铁矿为主的烧结过程需氧量不同,磁铁矿氧化需要额外消耗氧量,褐铁矿因燃料用量高而氧消耗量大,采用烟气循环时,其氧含量的临界值更高,三种原料体系的氧含量临界值分别为15%、17%、18%。
因此,氧含量18%为普遍适用的临界值。
一般而言,烧结烟气中氧气含量约为12%~16%,为了保证循环至台车面的气流介质中的氧气含量大于临界值,通常在烧结烟气中配加富氧气体,富氧气体可为空气、冷却废气或纯氧。
二氧化硫的影响:烧结气流介质中含有少量的二氧化硫对烧结矿的产品质量指标影响不大,而当烧结气流介质中二氧化硫的含量大于700mg/Nm3时,硫在成品烧结矿中会发生明显的富集。
因此规定烧结气流介质中二氧化硫含量最好不超过700mg/Nm3。
水蒸气的影响:烧结气流介质中水蒸气在高温下会与燃料发生水煤气反应而起促燃作用,可以一定程度减轻氧含量下降对燃料燃烧的不利影响,因此少量的水蒸气对烧结过程有促进作用。
但水蒸气含量过高,会增加烧结过程料层的过湿,对各项烧结指标不利,所以水蒸气含量有临界值。
赤铁矿为主、磁铁矿为主、褐铁矿为主的原料,各自的水蒸气含量临界值不同。
烟气制酸工艺流程
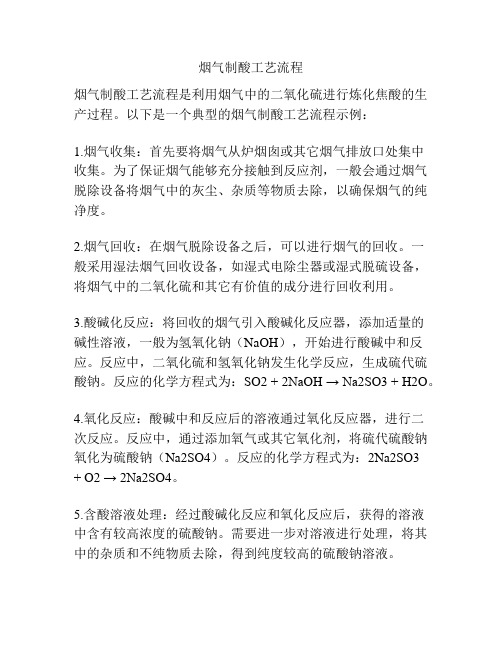
烟气制酸工艺流程烟气制酸工艺流程是利用烟气中的二氧化硫进行炼化焦酸的生产过程。
以下是一个典型的烟气制酸工艺流程示例:1.烟气收集:首先要将烟气从炉烟囱或其它烟气排放口处集中收集。
为了保证烟气能够充分接触到反应剂,一般会通过烟气脱除设备将烟气中的灰尘、杂质等物质去除,以确保烟气的纯净度。
2.烟气回收:在烟气脱除设备之后,可以进行烟气的回收。
一般采用湿法烟气回收设备,如湿式电除尘器或湿式脱硫设备,将烟气中的二氧化硫和其它有价值的成分进行回收利用。
3.酸碱化反应:将回收的烟气引入酸碱化反应器,添加适量的碱性溶液,一般为氢氧化钠(NaOH),开始进行酸碱中和反应。
反应中,二氧化硫和氢氧化钠发生化学反应,生成硫代硫酸钠。
反应的化学方程式为:SO2 + 2NaOH → Na2SO3 + H2O。
4.氧化反应:酸碱中和反应后的溶液通过氧化反应器,进行二次反应。
反应中,通过添加氧气或其它氧化剂,将硫代硫酸钠氧化为硫酸钠(Na2SO4)。
反应的化学方程式为:2Na2SO3+ O2 → 2Na2SO4。
5.含酸溶液处理:经过酸碱化反应和氧化反应后,获得的溶液中含有较高浓度的硫酸钠。
需要进一步对溶液进行处理,将其中的杂质和不纯物质去除,得到纯度较高的硫酸钠溶液。
6.酸的提取:通过浓缩和蒸发等工艺,将得到的硫酸钠溶液进一步处理,使其浓缩至一定的程度,从而获得硫酸。
7.产品处理:将浓缩后的硫酸进行过滤、冷却、结晶等处理工艺,得到纯度高的炼化焦酸作为最终产品。
8.废水处理:在整个烟气制酸过程中,会产生大量废水。
为了保护环境,需要对废水进行处理,去除其中的有毒有害物质,以达到排放标准要求。
以上是一个简要的烟气制酸工艺流程示例。
实际生产中,可能会根据不同的工艺和设备配置有所差异。
总的来说,烟气制酸工艺是一项复杂的过程,需要综合考虑烟气的收集、处理、反应和产品的提取等环节,以确保生产过程的高效稳定和产品的优质符合要求。
烧结机工艺流程图
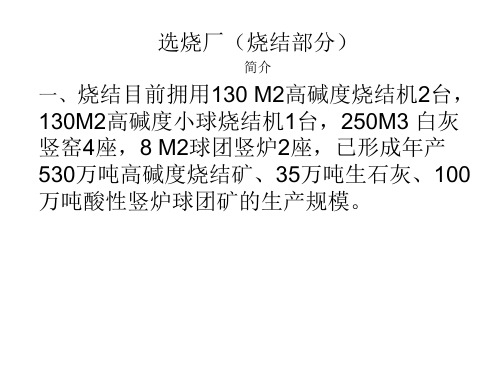
• 生球筛分:为了剔除在造球机排出的生球中 不合格小球、超粒级生球和粉料,避免把大 量的粉末和超粒级生球带入焙烧设备,使生 球粒度均匀,以改善料层或料柱的透气性, 提高焙烧机和成品球团矿的产量和质量。生 球筛分主要利用圆辊筛将生球中小于8mm和 大于18mm的生球绝大部分清除掉,改善竖炉 料柱的透气性,有利于竖炉的正常焙烧 。 • 竖炉焙烧系统:经过干燥、预热、焙烧、均 热、冷却五个阶段 • 焙烧后的球团矿从竖炉底部振动排料机均匀 连续的排出,在竖炉操作过程中要求排球量
• 成品处理系统:从烧结台车上卸下的烧结矿饼块度很大, 温度高达700~800℃ ,不利于运输和高炉冶炼,因此要 对热烧结矿进行破碎、筛分、冷却等处理。 • 破碎:机尾的齿辊式破碎机进行热破碎。 • 一次筛分:偏心热振动筛进行筛分,筛下为热返矿,由热 返矿圆盘给料机给到混合料皮带。 • 冷却:筛上热烧结矿进入环式冷却机冷却。 • 二次筛分:冷却后的烧结矿再经固定筛和冷矿振动筛筛分 后,分别产生>20mm的烧结矿供给高炉,10—20mm烧结矿 一部分作为铺底料送至烧结机,另一部分运往高炉,5— 10mm为小成品送往高炉,<5mm部分作为返矿与混合料进 入一次混合机。
选烧厂(烧结部分)
简介
一、烧结目前拥用130 M2高碱度烧结机2台,
130M2高碱度小球烧结机1台,250M3 白灰 竖窑4座,8 M2球团竖炉2座,已形成年产 530万吨高碱度烧结矿、35万吨生石灰、100 万吨酸性竖炉球团矿的生产规模。
烧结机工艺流程图:
铁料 燃料 熔剂
配料系统
混合造球系统
烧结系统
•
润磨处理系统:为了得到良好的造球原料, 现代的球团矿生产工艺一般都采用润磨工艺来 解决,通过对膨润土和铁精矿配合料的润磨, 使其比表面积提高,细度增加,颗粒形状组成 得到改善,激活物料表面能量,进一步混合物 料,提高混合料的成球性能和生球强度,降低 膨润土配用量,降低竖炉烟气含尘量,改善生 产环境。 • 造球系统 :造球是将细磨物料由料仓经皮带 给到造球盘,通过加水喷头精矿被水湿润,借 助造球盘旋转产生的机械力作用而滚动成球的 过程。由于圆盘造球机以一定的倾角和转速进 行运转,在运转过程当中使物料做有规律的圆 周运动,母球、成长球和合格生球分别沿着各 自不同的轨迹运动,因而产生了自动分级的作 用,将合格的生球自盘内排出 。
烟气制酸工艺流程

烟气制酸工艺流程烟气制酸工艺是一种利用烟气中的二氧化碳和其他气体制取酸的工艺方法。
它可以实现废气的资源化利用,减少环境污染,同时也可以生产出有用的化学产品。
下面将介绍烟气制酸的工艺流程。
首先,烟气制酸工艺需要收集烟气。
在工业生产过程中,烟气中会含有大量的二氧化碳、氮氧化物和硫化物等气体,这些气体可以被利用来制取酸。
因此,首先需要将工厂排放的烟气进行收集和处理,以便后续的酸的制取工艺。
接下来,收集到的烟气需要进行净化处理。
这是因为烟气中可能含有大量的杂质和有害物质,这些物质会影响后续酸的制取过程,甚至损坏设备。
因此,需要通过吸附、洗涤、脱硫等方法对烟气进行净化处理,确保烟气中的二氧化碳和其他气体的纯度。
然后,净化后的烟气被输送到制酸设备中。
在制酸设备中,烟气会与酸性溶液进行接触,从而使二氧化碳和其他气体溶解到溶液中。
这个过程通常需要在一定的温度和压力下进行,以便提高溶解度和反应速率。
随后,溶解了二氧化碳和其他气体的酸性溶液被送到分离设备中。
在分离设备中,通过调节温度和压力,可以使溶液中的二氧化碳和其他气体重新释放出来,从而得到纯净的酸。
这个过程通常需要进行多级分离,以确保酸的纯度。
最后,得到的酸可以进行包装和储存,以便后续的销售和使用。
同时,分离出的二氧化碳和其他气体也可以被回收利用,从而实现资源的循环利用。
总的来说,烟气制酸工艺是一种利用工业废气制取酸的环保工艺。
通过收集、净化、溶解和分离等步骤,可以将烟气中的二氧化碳和其他气体转化为有用的化学产品,同时减少对环境的污染。
这种工艺不仅有利于工厂的环保和节能,也为酸的生产提供了一种新的途径。
冶炼烟气制酸工艺操作规程

冶炼烟气制酸工艺操作规程南丹县南方有色冶炼有限责任公司NDNF/JS—SC19,2010 控制状态: 发放编号:编制: 梁世心审核: 刘旭升曹晓星批准:2010年7月20日发布 2010年8月1日实施南丹县南方有色冶炼有限责任公司发布南丹县南方有色冶炼有限责任公司烟气制酸(一系统)工艺操作规程文件编号:NDNF/JS—SC19,20101 范围本规程包括锌精矿焙烧烟气制取工业硫酸的工艺流程、基本原理、原材料及质量要求、工艺操作条件、岗位操作法、产品及质量要求、主要技术经济指标以及主要设备。
2 工艺流程(见附图)3 基本原理将焙烧来的高温含尘、酸雾、水分、砷、氟等杂质的炉气进行净化和降温,使炉气达到净化指标要求,以利后面工序的操作和设备正常运转。
3.1 净化原理经绝热蒸发降温除尘、稀酸洗涤冷却后,烟气在电场力作用下将酸雾除去。
3.2 干吸原理3.2.1 干燥原理利用浓硫酸具有强吸水性而干燥烟气。
3.2.2 吸收原理当含有SO的烟气与浓硫酸接触时,SO选择性地溶解在浓硫酸中,该过程的化学反应33) 如式(1SO + HO HSO + Q ……………………(1) 32243.3 转化原理二氧化硫烟气在钒催化剂触媒的作用下氧化为三氧化硫,化学反应如式(2) SO + 1/2O SO +Q…………………………(2) 2234 原材料及质量要求4.1 锌焙烧烟气化学成分333 SO4-8% O 8.15% As?200mg/m F?100mg/m 含尘?500mg/m224.2 钒催化剂(触媒)4.2.1 S101型钒催化剂应符合HG2086的规定。
其中化学性质:五氧化二钒(VO)% 7.5,8.5 硫酸钾(KSO)% 18.3,23 2524二氧化硅(SiO)% 65,75 活性率(耐热后SO转化率)% ?81.0 22物理性质:形状圆柱形条状颜色深黄或红棕色直径mm 4.5,5.5 长度mm 5,15 堆密度?/L 0.6,0.7 4.2.2 S107型钒催化剂应符合HG2088的规定。
烧结生产工艺流程图

烧结工艺流程一、我厂烧结机概况:我厂90M2带式抽风机是有冶金设计研究总院设计。
设计利用系数为1.57t/m·h。
(设备能力为2.0 t/m·h)作业率90.4%,年产烧结矿224万吨。
产品为冷烧结矿;温度小于120℃;粒度5—150mm;0—5mm粉末含量小于5%;TFe55%;FeO小于10%;碱度2.0倍。
配料采用自动重量配料强化制粒烧结工艺。
厚料层烧结、环式鼓风冷却机冷却烧结矿。
冷烧结矿经整粒筛分;分出冷返矿及烧结机铺底料和成品烧结矿。
选用了高效主抽风机等节能设备,电器控制及自动化达到国同类厂先进水平,采用以PLC为核心的EIC控制系统,构成仪电合一的计算机控制系统。
仪表选用性能良好的电动单元组合仪表智能型数字显示仪表等,对生产过程的参数进行指示;记录;控制;自动调节,对原料成品及能源进行计量,在环境保护方面采用静电除尘器,排放浓度小于100mg/m3,生产水循环使用,实现全厂污水零排放。
采取多项措施对薄弱环节设备采用加强型及便于检修的设备,关键部位设电动桥式吊车,有储存时间8小时的成品矿槽以提高烧结机作业率,使烧结和高炉生产互不影响。
二、什么叫烧结工艺:烧结工艺就是按高炉冶炼的要求把准备好的铁矿粉、熔剂、燃料及代用品,按一定比例经配料、混料、加水润滑湿。
再制粒、布料点火、借助风机的作用,使铁矿粉在一定的高温作用下,部分颗粒表面发生软化和熔化,产生一定的液相,并与其他末熔矿石颗粒作用,冷却后,液相将矿粉颗粒粘成块这个过程为烧结工艺。
三.烧结的方法按照烧结设备和供风方式的不同烧结方法可分为:1)鼓风烧结如:烧结锅、平地吹;2)抽风烧结:①连续式如带式烧结机和环式烧结机等;②间歇式如固定式烧结机有盘式烧结机和箱式烧结机,移动式烧结机有步进式烧结机;3)在烟气中烧结如回转窑烧结和悬浮烧结。
四.烧结矿的种类:CaO/SiO2小于1为非自熔性烧结矿;碱度为1-1.5是自熔性烧结.矿碱度为1.5~2.5是高碱度烧结矿;大于2.5是超高或熔剂性烧结矿。
第三章 烟气制酸

第一章概述第一节硫酸工业的发展世界上最早的硫酸,产生于15世纪后半叶,当时的原料为绿矾石[FeSO4·7H2O]。
通过对其加热分解和吸收制出硫酸。
这种方法距今已有500多年的历史了。
到了1746年世界上第一座运用亚硝基法制酸的工厂,铅室法制取硫酸在英国的伯明翰建成并投入生产。
这就是世界上最早的铅室法制酸工厂。
之后在硫酸工业和其它工业的推动下,又出现了塔式法制酸。
尽管如此,到了1940年,染料、化纤、有机合成及石油、化工等工业取得了逢勃发展,它们不仅增加了对硫酸的需求量,特别对硫酸浓度提出了更高的要求(需要发烟硫酸)。
万里铅室法、塔式法成品酸浓度不够(产品酸:65%、76%)从而不能满足上述工业部门的需要。
必需寻求制酸的新方法。
接触法诞生于1831年,用二氧化硫在空气中通过接触铂粉或铂丝并在炽热条件下制取三氧化硫为生产高浓度硫酸创造了条件。
这就是最早的接触法,触媒用昂贵的铂。
此法到了20世纪初得到了迅速的发展。
特别是1913年,前西德BASF AG公司发明出了活性好、不易中毒,而价格又较便宜的钒触媒。
钒触媒取代了铂触媒,从而推动了硫酸工业的快速发展。
世界上接触法硫酸生产装置始建于19世纪末和20世纪初,并采用了钒催化剂,到20世纪60年代,钒催化剂得到了广泛应用。
50年代初,前联邦德国和美国同时开发了硫铁矿沸腾焙烧技术。
1964年前联邦德国的一家公司开始应用两次转化工艺,70年代初又建成年产500KT硫磺制酸装置和年产360KT硫铁矿制酸装置。
90年代初,加拿大的一家公司采用美国孟山都环境化学公司技术,建成年产2900KT冶炼烟气制酸装置。
近年来,国外还出现了三转三吸工艺和加压法转化流程。
催化剂开发方面力求活性高、起燃温度低、抗毒性能好、寿命长。
在低位热能回收利用、低浓度SO2烟气回收等方面也有很大进步。
我国于1934年建成第一座接触法硫酸装置,但当时硫酸工业基础相当薄弱。
1949年以后,我国硫酸工业发生巨大的变化,不仅产量增加,生产技术也有很大的提高。
烟气制酸工艺流程

烟气制酸工艺流程烟气制酸是一种将工业废气中的二氧化硫通过吸收转化为酸的工艺,主要用于环保和资源化利用的目的。
下面是一个简单的烟气制酸工艺流程的描述。
1.烟气收集:从工业生产设备排放出的废气首先通过烟道被收集起来,集中到一个烟气处理装置。
2.烟气预处理:在烟气处理装置内,烟气经过过滤、脱水等预处理步骤,去除其中的颗粒物、水蒸气等杂质,使烟气清洁后进一步处理。
3.二氧化硫吸收:烟气中的二氧化硫被导入酸液中进行吸收。
酸液可采用硫酸、硝酸等,但硫酸是常用的吸收剂。
在吸收剂中,二氧化硫发生化学反应转化为二硫化碳:SO2+H2O→H2SO3→H2CO3其中,二氧化硫(SO2)先与水(H2O)反应生成亚硫酸(H2SO3),随后亚硫酸会进一步自动分解为碳酸(H2CO3)。
4.二氧化硫转化:二氧化硫转化为二硫化碳后,酸液中的溶质浓度会逐渐上升。
当溶液浓度达到一定程度时,会形成含有二硫化碳的酸性溶液。
5.融合过程:融合是指将含有二硫化碳的酸性溶液进行升温处理,使其中的其他成分反应使得酸性溶液中的二硫化碳被转化为二氧化碳和硫酸。
H2CO3→CO2↑+H2O2H2SO3→2SO2↑+O2↑通过这个过程,二硫化碳转化为二氧化碳和硫酸,进一步提高了酸性溶液中的溶质浓度。
6.辅助处理:在上述过程中,还可能需要对反应物质进行补充、循环或排除。
例如,为了提高酸性溶液中溶质的浓度,可以在融合过程中持续添加酸性溶液。
同时,通过监测酸性溶液中的pH值和溶液浓度,对溶液进行调控以获得所需的反应结果。
7.结果产物回收:经过融合和辅助处理后,得到的酸性溶液中含有较高的浓度的硫酸。
这个酸性溶液可以进一步用于其他工业生产或者回收处理。
整个烟气制酸工艺流程主要是通过二氧化硫的吸收转化来完成的,既达到了环保要求,又实现了废气资源化利用的目的。
然而,这个工艺流程只是一个简单的描述,实际应用中还需要根据具体情况进行更详细的设计和调整。
二氧化硫烟气制酸

二氧化硫烟气制酸前言:硫酸是工业上一种重要的化学品,它用途十分广泛,如制造肥料、非碱性清洁剂、护肤品、以及油漆添加剂与炸药等。
在冶金工业中,大部分的冶炼原料均为金属硫化物,如硫化锌、硫化铜等,在冶炼中会产生大量的二氧化硫烟气,对环境的污染比较严重,而当烟气中的SO2浓度达到一定程度时,则可采用冶炼烟气制酸的方法,将其变废为宝,既生产出硫酸,又达到了污染物减排、废气综合利用的目的。
在我国,有色金属冶炼烟气以低浓度二氧化硫烟气居多,但随着富氧冶炼技术的发展,也出现了一批高浓度SO2制酸企业。
1.低浓度SO 2烟气制酸低浓度S02烟气制硫酸有两种类型:一种是间接制酸工艺,即先通过物理或化学吸收或吸附的方法将低浓度S02烟气转化为高浓度甚至纯SO2气体,再利用这些气体生产硫酸;另一种是直接制酸工艺,即直接利用低浓度SO2烟气生产硫酸。
1.1间接制酸工艺间接制酸工艺的关键是采用合适的脱硫技术生产高浓度SO2气体,其后续工艺与传统硫酸工艺并无差异。
目前在国内使用较多的间接制酸法包括CANSOLV工艺、离子液循环吸收法。
1.1.1CANSOLV再生胺工艺CANSOLV可再生胺法由原联合碳化物公司(现为陶氏化学公司的子公司)开发,并于2001年实现工业化,目前已成功应用于石油和天然气处理、有色金属冶炼和电厂烟气脱硫【1】。
该技术采用可再生的有机胺溶液作为SO2吸收剂,其优点是吸收剂可循环利用、脱硫效率高(98%以上)、处理气体流量及浓度范围大[流量为(0.5—95.0)×104 m3/h,φ(S02)为0.08%一ll%]、副产S02浓度高[φ(SO2)>99%];其缺点是低压蒸汽和电耗较高,并且处理冶炼烟气时需对烟气进行预净化处理。
CANSOLV工艺可与克劳斯装置或硫酸装置整合生产硫磺或硫酸,也可将高浓度SO2气体压缩为液体SO2产品。
2006年以来CANSOLV可再生胺法在我国推广取得突破性进展,现已用于阳谷祥光铜业200 kt∕a铜冶炼精炼炉烟气、云南红河恒昊矿业镍冶炼烟气、贵铝热电厂二期燃煤锅炉烟气的脱硫,在建的云南锡业100 kt∕a铅冶炼制酸尾气脱硫也将采用该工艺。
- 1、下载文档前请自行甄别文档内容的完整性,平台不提供额外的编辑、内容补充、找答案等附加服务。
- 2、"仅部分预览"的文档,不可在线预览部分如存在完整性等问题,可反馈申请退款(可完整预览的文档不适用该条件!)。
- 3、如文档侵犯您的权益,请联系客服反馈,我们会尽快为您处理(人工客服工作时间:9:00-18:30)。
烟气 取样 冷却塔 填料塔 一间冷器 一电雾器 二间冷器 二电雾器 取样 干燥塔 干燥酸冷器 水 干燥酸循环槽 吸收酸循环槽 吸收酸冷器 吸收塔 ※ 取样 93%酸罐 98%酸罐 外卖 外卖
注:关键工序:※ 为气体路线, 取样点: 为液体路线 为固体路线
取样 沉降槽 冷却循环槽 洗涤循环槽 间冷循环槽 污酸 水 水
转化器※ 取样 主风机 换热器
中和池 取样
纯 碱
压滤 滤 渣 取样 取样 烧结配料 滤 液 烧结配料 (或调运) 鼓风炉硫酸尾气吸收塔 取样 尾气放空(合格排放)