烧结工艺流程
烧结工艺流程简述
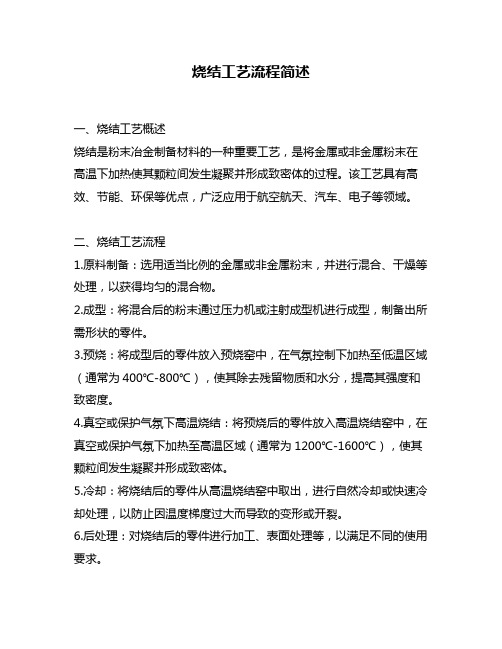
烧结工艺流程简述一、烧结工艺概述烧结是粉末冶金制备材料的一种重要工艺,是将金属或非金属粉末在高温下加热使其颗粒间发生凝聚并形成致密体的过程。
该工艺具有高效、节能、环保等优点,广泛应用于航空航天、汽车、电子等领域。
二、烧结工艺流程1.原料制备:选用适当比例的金属或非金属粉末,并进行混合、干燥等处理,以获得均匀的混合物。
2.成型:将混合后的粉末通过压力机或注射成型机进行成型,制备出所需形状的零件。
3.预烧:将成型后的零件放入预烧窑中,在气氛控制下加热至低温区域(通常为400℃-800℃),使其除去残留物质和水分,提高其强度和致密度。
4.真空或保护气氛下高温烧结:将预烧后的零件放入高温烧结窑中,在真空或保护气氛下加热至高温区域(通常为1200℃-1600℃),使其颗粒间发生凝聚并形成致密体。
5.冷却:将烧结后的零件从高温烧结窑中取出,进行自然冷却或快速冷却处理,以防止因温度梯度过大而导致的变形或开裂。
6.后处理:对烧结后的零件进行加工、表面处理等,以满足不同的使用要求。
三、烧结工艺参数1.预烧温度:预烧温度过低会导致残留物质和水分未完全除去,影响零件强度和致密度;预烧温度过高则会使零件表面氧化、变质等不良反应发生。
2.高温烧结温度:高温烧结温度是影响零件致密度和力学性能的重要参数。
一般情况下,高温烧结温度越高,零件的致密度越大、力学性能越好。
但超过一定范围后,会出现晶粒长大、相变等问题。
3.保护气氛:保护气氛可以有效防止零件表面氧化、变质等问题,提高烧结质量。
常用的保护气氛有氢气、氮气、氩气等。
4.烧结时间:烧结时间是影响零件致密度和力学性能的重要参数。
一般情况下,烧结时间越长,零件的致密度越大、力学性能越好。
但过长的烧结时间会导致晶粒长大、相变等问题。
四、烧结工艺优点1.高效:粉末冶金制备材料的成型和加工过程简单,可实现快速生产。
2.节能:相比于传统工艺,烧结工艺耗能较低。
3.环保:粉末冶金制备材料过程中无废水废气排放,符合环保要求。
烧结生产工艺流程

烧结生产工艺流程烧结是一种重要的金属制造工艺,通过粉末冶金的方式将金属粉末加热到合适的温度,使其粒子间发生扩散和结合,从而形成固态的金属件。
下面将介绍烧结生产工艺流程。
1. 准备原材料:选择合适的金属粉末作为原材料,根据产品要求控制粉末的成分和粒度。
2. 混合:将不同成分的金属粉末按一定比例混合均匀,可以加入一些助剂如润滑剂、增塑剂等,以提高粉末的流动性和可塑性。
3. 成型:将混合好的金属粉末放入模具中,进行成型。
常见的烧结成型方法有压制成型和注射成型两种。
4. 压制成型:将金属粉末放入专用的压制机中,通过给予一定的压力使其成型。
压制成型包括冷压和等静压两种方式,通常需要经过多道工序进行。
5. 注射成型:将金属粉末和一定比例的粘结剂混合后,通过注射成型机将其注入模具中,利用粘结剂的粘合力将粉末粒子黏结在一起。
6. 烧结:将成型好的金属零件置于烧结炉中进行加热处理。
烧结温度通常在金属的熔点以下,但足够高以使粉末颗粒表面形成液相。
烧结过程中,金属粉末的颗粒间发生扩散和结合,形成密实的结构。
7. 冷却:烧结结束后,将待烧结的金属件从烧结炉中取出,进行自然冷却。
冷却过程中需要控制冷却速度,以避免由于温度变化过快引起的应力和变形。
8. 后处理:经过烧结和冷却后的金属件通常需要进行后处理,以提高其性能。
后处理过程包括热处理、表面处理、机械加工等,以获得所需的尺寸、性能和外观。
9. 检验:对烧结成品进行检验,包括尺寸、密度、力学性能等方面的检测,确保产品符合要求。
10. 包装和出货:对合格的烧结件进行包装,并按照订单要求出货。
烧结生产工艺流程是一个相对复杂的过程,需要控制好各个环节的参数和条件,以确保最终产品的质量。
随着科技的进步和生产工艺的发展,烧结技术在各个行业中得到广泛应用,成为一种重要的制造方法。
烧结的工艺流程
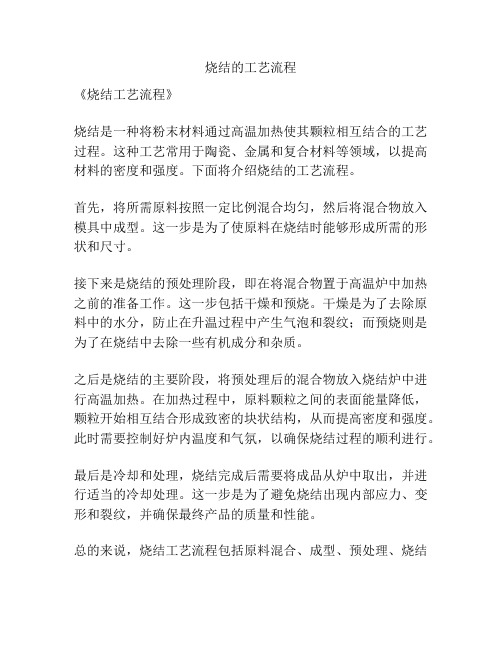
烧结的工艺流程
《烧结工艺流程》
烧结是一种将粉末材料通过高温加热使其颗粒相互结合的工艺过程。
这种工艺常用于陶瓷、金属和复合材料等领域,以提高材料的密度和强度。
下面将介绍烧结的工艺流程。
首先,将所需原料按照一定比例混合均匀,然后将混合物放入模具中成型。
这一步是为了使原料在烧结时能够形成所需的形状和尺寸。
接下来是烧结的预处理阶段,即在将混合物置于高温炉中加热之前的准备工作。
这一步包括干燥和预烧。
干燥是为了去除原料中的水分,防止在升温过程中产生气泡和裂纹;而预烧则是为了在烧结中去除一些有机成分和杂质。
之后是烧结的主要阶段,将预处理后的混合物放入烧结炉中进行高温加热。
在加热过程中,原料颗粒之间的表面能量降低,颗粒开始相互结合形成致密的块状结构,从而提高密度和强度。
此时需要控制好炉内温度和气氛,以确保烧结过程的顺利进行。
最后是冷却和处理,烧结完成后需要将成品从炉中取出,并进行适当的冷却处理。
这一步是为了避免烧结出现内部应力、变形和裂纹,并确保最终产品的质量和性能。
总的来说,烧结工艺流程包括原料混合、成型、预处理、烧结
和冷却处理这几个主要阶段。
通过精确地控制每个环节,可以获得致密、坚固和具有优良性能的烧结制品。
烧结生产工艺流程

烧结工艺1 含铁原料、熔剂和燃料1.1 含铁原料所用含铁原料有精矿、粉矿、除尘灰、轧钢皮等等。
各种含铁原料均在原料场内储存,用装载机输送到烧结系统配料室。
1.2 熔剂烧结机用熔剂为生石灰、石粉和白云石。
合格的生石灰用汽车运至烧结配料室,用压缩空气送至生石灰配料槽。
石粉及白云石用汽车运至烧结配料室料槽。
1.3 燃料1.3.1 固体燃料烧结用固体燃料为焦粉及无烟煤,由汽车运入烧结厂区,于燃料准备间储存和破碎,破碎后粒度3~0mm占80%的合格燃料经转运送至配料室。
1.3.2 气体燃料烧结点火使用热值为3349~4187KJ/m3的高炉煤气2、工艺流程及车间组成烧结机系统工艺流程见图2-1。
烧结机系统工艺车间有:燃料准备间、配料室、一次混合、二次混合、烧结室、带冷机、筛分室、成品矿槽、主抽风机室、主电除尘器、水泵房、转运站及通廊运输系统等。
2.1 燃料准备间烧结生产用燃料为焦粉及无烟煤,入厂粒度40~0mm,由汽车运入厂区,于燃料准备间储存,燃料破碎为2台Φ900×700四辊破碎机。
燃料直接通过大倾角皮带机输入燃料矿仓,先通过滚筛筛除大块粒度燃料,再通过仓下皮带送入四辊破碎机进行细破。
燃料经破碎后,3~0mm部分占80%以上,经皮带转运送至配料室燃料槽。
2.2 配料室配料室按单列式布置,配料槽内各种原料的贮存时间都在4h以上,满足工艺生产对贮存时间的要求。
原矿采用自卸汽车或装载机向各配料槽给料。
燃料、冷返矿采用固定可逆胶带机向燃料、冷返矿配料槽给料。
熔剂采用汽车运到配料槽。
含铁料、石粉、白云石、返矿采用振动漏斗、圆盘给料机、皮带秤作为给料和配料设备,圆盘给料机变频调速;燃料采用振动漏斗、皮带秤作为给料和配料设备,皮带秤变频调速;生石灰采用细灰闸门、回转给料机、螺旋电子秤、生石灰配消器作为给料、配料和消化设备,回转给料机变频调速。
各种物料可按配料比例定量给出所要求的物料,实现自动配料。
2.3 一次混合设置1台Φ3×9m圆筒混合机,安装角度2°,混合时间为2.19min,填充率为8.99%。
烧结生产工艺
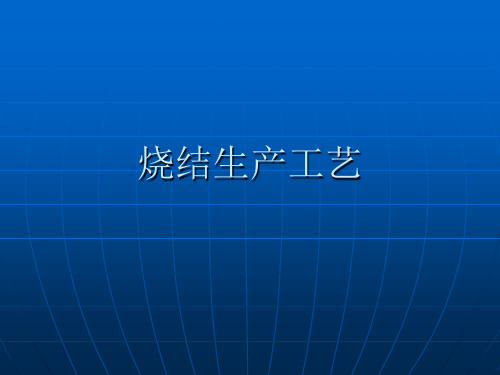
8)、烧结矿整粒
主要设备: 1、一次冷矿筛(椭圆振动筛) 2000×6000、筛孔20mm 2、二次冷矿筛(直线振动筛) 2000×6000、筛孔5mm; 10mm。 整粒分级为: 1、大成品≥20mm; 2、铺底料:10-20mm; 3、小成品:5-10mm; 4、冷返矿:≤5mm。 我厂大小成品分后又混供。
4)、烧结配料
一、主要设备: 1、配料圆盘; 2、拉式皮带机; 3、配消器及湿 式除尘器; 4、配料矿槽; 5、称量设备;
二、配料的目的: 1、使烧结料化学成份和物理性质稳定,符合烧结生 产需要; 2、使烧结料有一定的原始透气性,提高烧结生产率; 3、使烧结料化学成份稳定,符合高炉冶炼需要; 4、实现烧结和炼铁的物料平衡、资源利用和效益最 大化。 三、配料方法: 1、容积配料法; 2、重量配料法;
2、水分的蒸发、冷凝与结晶水分解
一、水的作用: 1、利用水的表面张力,将烧结料制成具有 一定强度的颗粒和小球; 2、在料层自动蓄热过程中将温度压缩在一 个较窄的区间内。 二、蒸发与冷凝: H2O(液)=H2O(气) 三、露点 四:结晶水的分解:
3、碳酸盐的分解和氧化钙的化合
9、烧结矿贮存与转运
1、成品矿槽:360m3×6; 2、SW系列皮带机; 3、S系列皮带机。
10、抽风与除尘
1、主抽风机;额定风量9000m3/min;匹 配电机3200KW;大烟道直径3600mm; 2、机头除尘器:198m2(4电场);多管除尘 器824管; 3、成品电除尘器50m2(3电场);燃料电除 尘器30m2(3电场);1#、2#机尾电除尘器 40m2(3电场);配料电除尘器40m2(3电 场)。
4、铁氧化物分解、氧化和还原
1、铁氧化物主要有三种形态:FeO、Fe2O3、 Fe3O4 2、分解:3Fe2O3=2Fe3O4+1/2O2。 3、氧化和还原: Fe FeO Fe3O4 Fe2O3 从左至右为氧化过程,放热;从右至左为还 原过程,吸热。 4、烧结过程总体上是氧化气氛,局部存在还 原气氛。
烧结工艺流程过程步骤

烧结工艺流程过程步骤烧结工艺流程是一种金属材料的加工方法,通过高温加热和压制,使粉末颗粒之间发生熔结和固化,形成坚固的整体结构。
下面将详细介绍烧结工艺流程的步骤。
一、原料的准备需要准备烧结所需的原料。
原料一般是金属粉末,可以是单一金属或是合金粉末。
原料的选择要根据所需产品的性能要求和工艺要求进行合理搭配,确保烧结后得到的材料具有理想的性能。
二、混合和制备将所需的金属粉末按照一定的比例混合均匀,以保证最终产品的成分均匀性。
混合后的粉末可以通过球磨机等设备进行进一步的细化处理,以提高粉末的活性和流动性。
三、成型成型是烧结工艺流程的重要一步。
常用的成型方法有压制和注塑两种。
压制方法是将混合后的金属粉末放入模具中,施加一定的压力使其成型。
注塑方法则是将混合后的金属粉末与有机物混合后注入注塑机中,通过加热和压力使其成型。
四、烧结经过成型后的产品需要进行烧结处理。
烧结是通过加热和压力使金属粉末颗粒之间发生熔结和固化的过程。
在烧结过程中,需要控制好温度、时间和压力等参数,以确保粉末颗粒能够充分熔结并形成致密的结构。
五、冷却和处理经过烧结后的产品需要进行冷却处理。
冷却过程可以通过自然冷却或使用冷却介质进行加速冷却。
冷却后的产品可以进行进一步的处理,例如去除表面氧化层、进行热处理等,以进一步提高产品的性能。
六、加工和检验经过烧结和处理后的产品可以进行加工,例如切割、磨削、打磨等。
同时,还需要对产品进行严格的检验,以确保产品的质量达到要求。
常用的检验方法包括外观检查、尺寸测量、力学性能测试等。
七、表面处理和包装经过加工和检验的产品需要进行表面处理和包装。
表面处理可以根据产品的用途和需求进行选择,例如镀层、喷漆等。
包装过程则是将产品进行适当的包装,以保护产品不受损坏,并方便运输和储存。
总结:烧结工艺流程包括原料准备、混合和制备、成型、烧结、冷却和处理、加工和检验、表面处理和包装等步骤。
每一步都需要严格控制工艺参数,以确保产品的质量和性能达到要求。
烧结工艺流程

烧结工艺流程烧结是指将粉煤灰、粉煤、石灰石、矿渣等原料通过一定的热处理工艺,使其在高温下结合成块状的固体材料的工艺过程。
烧结工艺是冶金、化工、建材等行业中常见的生产工艺之一,其产品广泛应用于水泥生产、冶金工业、建筑工程等领域。
下面将介绍烧结工艺的流程及其关键步骤。
1. 原料准备。
烧结工艺的第一步是原料的准备。
通常情况下,原料包括粉煤灰、粉煤、石灰石、矿渣等。
这些原料需要经过粉碎、混合等处理,以确保其颗粒大小和化学成分的均匀性,从而保证烧结后的产品质量。
2. 配料混合。
经过原料准备后,需要将各种原料按照一定的配比进行混合。
混合的目的是使各种原料充分混合,确保烧结后产品的化学成分均匀,并且提高烧结料的透气性和流动性。
3. 成型。
混合好的原料需要进行成型,通常采用压制成型或浇铸成型的方式。
压制成型是将原料放入成型机中,通过一定的压力将原料压制成一定形状的块状体。
浇铸成型则是将原料熔化后倒入模具中进行成型。
4. 预烧。
成型后的块状体需要进行预烧处理。
预烧是指将成型体在较低温度下进行热处理,以去除其中的水分和一些有机物,提高其强度和耐火性。
5. 烧结。
经过预烧处理后的块状体需要进行烧结。
烧结是将预烧后的块状体在高温下进行加热,使其在颗粒间发生化学反应,形成坚固的结合。
烧结的温度和时间是影响产品质量的重要因素。
6. 冷却。
烧结后的产品需要进行冷却处理。
冷却是将烧结后的产品缓慢降温,以避免产生内部应力和裂纹,确保产品的完整性和稳定性。
7. 成品。
经过冷却处理后,烧结产品即成为最终的成品。
成品可以根据需要进行包装、储存和运输,以满足不同领域的需求。
总结。
烧结工艺流程包括原料准备、配料混合、成型、预烧、烧结、冷却和成品等关键步骤。
每个步骤都对产品的质量和性能有着重要影响,需要严格控制和管理。
烧结工艺的优化和改进,可以提高产品的品质,降低生产成本,促进工艺的可持续发展。
烧结厂工艺流程
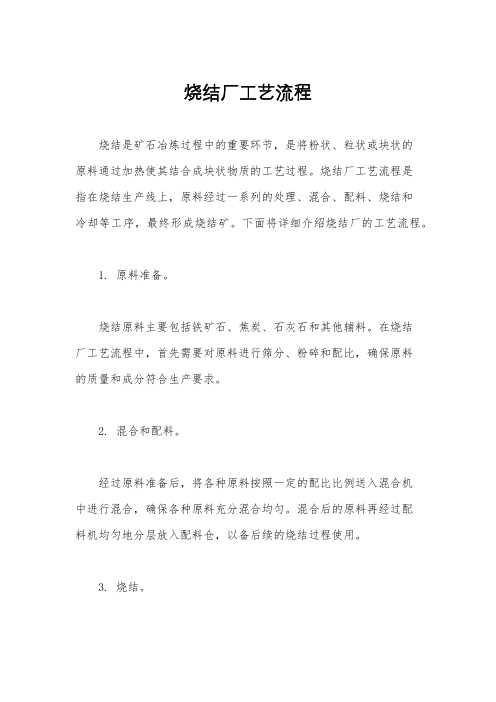
烧结厂工艺流程烧结是矿石冶炼过程中的重要环节,是将粉状、粒状或块状的原料通过加热使其结合成块状物质的工艺过程。
烧结厂工艺流程是指在烧结生产线上,原料经过一系列的处理、混合、配料、烧结和冷却等工序,最终形成烧结矿。
下面将详细介绍烧结厂的工艺流程。
1. 原料准备。
烧结原料主要包括铁矿石、焦炭、石灰石和其他辅料。
在烧结厂工艺流程中,首先需要对原料进行筛分、粉碎和配比,确保原料的质量和成分符合生产要求。
2. 混合和配料。
经过原料准备后,将各种原料按照一定的配比比例送入混合机中进行混合,确保各种原料充分混合均匀。
混合后的原料再经过配料机均匀地分层放入配料仓,以备后续的烧结过程使用。
3. 烧结。
配料完成后,原料通过皮带输送机送入烧结机中进行烧结。
在高温下,原料颗粒之间发生部分熔融和结合,形成初步的烧结块。
在烧结过程中,需要控制烧结温度、气氛和烧结时间,以确保烧结块的质量和强度。
4. 冷却。
烧结完成后的烧结块通过冷却机进行冷却处理,使其温度逐渐降低。
冷却后的烧结块具有一定的强度和耐磨性,可以进入下一道工序进行后续加工或直接用于炼铁生产。
5. 烟气处理。
烧结过程中会产生大量的烟气,为了减少对环境的污染,烧结厂通常会设置烟气处理系统,对烧结烟气进行除尘、脱硫等处理,以达到排放标准。
6. 废渣处理。
烧结过程中产生的废渣需要进行处理和利用。
常见的处理方式包括回炉再烧结、制成矿渣水泥等,以减少对环境的影响。
总结:烧结厂工艺流程是一个复杂的生产过程,需要各个环节紧密配合,确保原料的质量和成分符合要求,烧结过程中的温度、气氛和时间得到有效控制,最终形成具有一定强度和耐磨性的烧结块。
同时,还需要关注烟气和废渣的处理,以减少对环境的影响,实现绿色生产。
希望本文对烧结厂工艺流程有所帮助,谢谢阅读!。
- 1、下载文档前请自行甄别文档内容的完整性,平台不提供额外的编辑、内容补充、找答案等附加服务。
- 2、"仅部分预览"的文档,不可在线预览部分如存在完整性等问题,可反馈申请退款(可完整预览的文档不适用该条件!)。
- 3、如文档侵犯您的权益,请联系客服反馈,我们会尽快为您处理(人工客服工作时间:9:00-18:30)。
烧结工艺流程烧结是钢铁生产工艺中的一个重要环节,它是将铁矿粉、粉(无烟煤)和石灰按一定配比混匀。
经烧结而成的有足够强度和粒度的烧结矿可作为炼铁的熟料。
利用烧结熟料炼铁对于提高高炉利用系数、降低焦比、提高高炉透气性保证高炉运行均有一定意义。
由于烧结技术具体的作用和应用太广泛了, 以下介绍一下烧结生产在钢铁工业粉矿造块的意义和作用我国的铁矿石大部分都是贫矿,贫矿直接入炉炼铁是很不合算b,因此必须将贫矿进行破碎、选出高品位的精矿后,再将精矿粉造块成为人造富矿才能入高炉冶炼。
所以,粉矿造块是充分合理利用贫矿的不可缺少的关控环节。
富矿的开采过程中要产生粉矿,为了满足高炉的粒度要兔在整较过程中也会产生粉矿,粉矿直接入炉会51起高炉不顺。
恶化高炉技术经济指标,因此粉矿也必须经过造块才能入炉。
粉矿经过迭决后,可以进一步控制相改善合铁原料的性肠获得气孔串高、还原性好、强度合适、软熔温度较高、成份稳定的优质冶金原料,有助于炉况的稳定和技术经济指标的改善。
粒矿造块过程中,还可以除去部份有害杂质,如硫、氟、砷、锌等,有利于提高生铁的质量。
因为人造富矿比天然富矿更具有优越性,成为了现代商炉原料的主要来源。
粉矿迭块还可综合利用含铁、合被、台钙的粉状工业废料,如高炉炉尘、钢迢、轧钢皮、均热炉渣、硫酸渣、染料铁红、电厂烟尘灰笔适当配入可以成为廉价的高炉好原料,又可以减少环境污染,取得良好的经济效益和社会效益。
粉矿造铁是现代高炉冶炼并获得优质高产的基础,对于高炉冶炼有君十分重要的意义,是钢铁工业生产必不可少的重要工序,对钢铁生产的发展起着重要作用。
1.2 粉矿造块的方法粉矿造块方法很多,主要是烧结矿和球团矿。
此外,还有压制方团矿、辊压团矿、蒸养球团t碳酸化球团,其成球方式和固结方法与球团矿不同,还有小球烧结,国外称为HPs球团化挠结矿,界于球团和烧结之间;还有铁焦生产,是炼焦和粉矿造块相结合。
球团矿的焙烧方法主要乞竖队带式焙烷仇链蓖机—回转窃。
目前地方小铁厂还有平地堆烷的。
烧结方法主要有吹风烧结法和抽风烧结法两大类。
吹风烧结有平地堆挠、饶结识、挠结盘,抽风烧结有路式侥结、艰面步进式烧绍机、带式烧结机、环形挠结机电即日本矢作式)。
国内外苫遍采用的是常式抽风烧结机,在我国地方小铁广还有相当一部分用平地吹风堆烧和箱式抽风烧结。
比外,还有回转窑浇结法、悬浮烧结法。
所谓“烧结”就是指粉状物料加热到熔点以下而粘结成固体的现象.烧结过程简单来说,就是把品位满足要求,但粒度却不满足的精矿与其他辅助原料混合后在烧结机上点火燃烧,重新造块,以满足高炉的要求。
点火器就是使混合料在烧结机上燃烧的关键设备,控制好点火器的温度、负压等,混合料才能成为合格的烧结成品矿。
烧结的主要体系是,配料,混料,看火等。
看火的经验:看火主要控制的三点温度是;点火温度,终点温度,和总管废气温度。
一般来说把终点温度控制在倒数第2号风箱的温度。
铁矿粉造块铁矿粉造块目前主要有两种方法:烧结法和球团法。
两种方法所获得的块矿分别为烧结矿和球团矿。
铁矿粉造块的目的:◆综合利用资源,扩大炼铁用的原料种类。
◆去除有害杂质,回收有益元素,保护环境。
◆改善矿石的冶金性能,适应高炉冶炼对铁矿石的质量要求。
一、铁矿粉烧结生产1.烧结的概念将各种粉状含铁原料,配入适量的燃料和熔剂,加入适量的水,经混合和造球后在烧结设备上使物料发生一系列物理化学变化,将矿粉颗粒黏结成块的过程。
2. 烧结生产的工艺流程目前生产上广泛采用带式抽风烧结机生产烧结矿。
烧结生产的工艺流程如图2—4所示。
主要包括烧结料的准备,配料与混合,烧结和产品处理等工序。
图2-4 抽风烧结工艺流程◆烧结原料的准备①含铁原料含铁量较高、粒度<5mm的矿粉,铁精矿,高炉炉尘,轧钢皮,钢渣等。
一般要求含铁原料品位高,成分稳定,杂质少。
②熔剂要求熔剂中有效CaO含量高,杂质少,成分稳定,含水3%左右,粒度小于3mm的占90%以上。
在烧结料中加入一定量的白云石,使烧结矿含有适当的MgO,对烧结过程有良好的作用,可以提高烧结矿的质量。
③燃料主要为焦粉和无烟煤。
对燃料的要求是固定碳含量高,灰分低,挥发分低,含硫低,成分稳定,含水小于10%,粒度小于3mm的占95%以上。
对入厂烧结原料的一般要求见表2—2。
表2-2入厂烧结原料一般要求◆配料与混合①配料配料目的:获得化学成分和物理性质稳定的烧结矿,满足高炉冶炼的要求。
常用的配料方法:容积配料法和质量配料法。
容积配料法是基于物料堆积密度不变,原料的质量与体积成比例这一条件进行的。
准确性较差。
质量配料法是按原料的质量配料。
比容积法准确,便于实现自动化。
②混合混合目的:使烧结料的成分均匀,水分合适,易于造球,从而获得粒度组成良好的烧结混合料,以保证烧结矿的质量和提高产量。
混合作业:加水润湿、混匀和造球。
根据原料性质不同,可采用一次混合或二次混合两种流程。
一次混合的目的:润湿与混匀,当加热返矿时还可使物料预热。
二次混合的目的:继续混匀,造球,以改善烧结料层透气性。
用粒度10~Omm的富矿粉烧结时,因其粒度已经达到造球需要,采用一次混合,混合时间约50s。
使用细磨精矿粉烧结时,因粒度过细,料层透气性差,为改善透气性,必须在混合过程中造球,所以采用二次混合,混合时间一般不少于2.5~3min。
我国烧结厂大多采用二次混合。
◆烧结生产烧结作业是烧结生产的中心环节,它包括布料、点火、烧结等主要工序。
①布料将铺底料、混合料铺在烧结机台车上的作业。
当采用铺底料工艺时,在布混合料之前,先铺一层粒度为10~25mm,厚度为20~25mm的小块烧结矿作为铺底料,其目的是保护炉箅,降低除尘负荷,延长风机转子寿命,减少或消除炉箅粘料。
铺完底料后,随之进行布料。
布料时要求混合料的粒度和化学成分等沿台车纵横方向均匀分布,并且有一定的松散性,表面平整。
目前采用较多的是圆辊布料机布料。
②点火点火操作是对台车上的料层表面进行点燃,并使之燃烧。
点火要求有足够的点火温度,适宜的高温保持时间,沿台车宽度点火均匀。
点火温度取决于烧结生成物的熔化温度。
常控制在1250±50℃。
点火时间通常40~60s。
点火真空度4~6kPa。
点火深度为10~20mm。
③烧结准确控制烧结的风量、真空度、料层厚度、机速和烧结终点。
烧结风量:平均每吨烧结矿需风量为3200m3,按烧结面积计算为(70~90)m3/(cm2.min)。
真空度:决定于风机能力、抽风系统阻力、料层透气性和漏风损失情况。
料层厚度:合适的料层厚度应将高产和优质结合起来考虑。
国内一般采用料层厚度为250~500mm。
机速:合适的机速应保证烧结料在预定的烧结终点烧透烧好。
实际生产中,机速一般控制在1.5~4m/min为宜。
烧结终点的判断与控制:控制烧结终点,即控制烧结过程全部完成时台车所处的位置。
中小型烧结机终点一般控制在倒数第二个风箱处,大型烧结机控制在倒数第三个风箱处。
带式烧结机抽风烧结过程是自上而下进行的,沿其料层高度温度变化的情况一般可分为5层,各层中的反应变化情况如图2—5所示。
点火开始以后,依次出现烧结矿层,燃烧层,预热层,干燥层和过湿层。
然后后四层又相继消失,最终只剩烧结矿层。
图2-5烧结过程各层反应示意图①烧结矿层经高温点火后,烧结料中燃料燃烧放出大量热量,使料层中矿物产生熔融,随着燃烧层下移和冷空气的通过,生成的熔融液相被冷却而再结晶(1000—1100℃)凝固成网孔结构的烧结矿。
这层的主要变化是熔融物的凝固,伴随着结晶和析出新矿物,还有吸入的冷空气被预热,同时烧结矿被冷却,和空气接触时低价氧化物可能被再氧化。
②燃烧层燃料在该层燃烧,温度高达1350~1600℃,使矿物软化熔融黏结成块。
该层除燃烧反应外,还发生固体物料的熔化、还原、氧化以及石灰石和硫化物的分解等反应。
③预热层由燃烧层下来的高温废气,把下部混合料很快预热到着火温度,一般为400~800℃。
此层内开始进行固相反应,结晶水及部分碳酸盐、硫酸盐分解,磁铁矿局部被氧化。
④干燥层干燥层受预热层下来的废气加热,温度很快上升到100℃以上,混合料中的游离水大量蒸发,此层厚度一般为l0~30mm。
实际上干燥层与预热层难以截然分开,可以统称为干燥预热层。
该层中料球被急剧加热,迅速干燥,易被破坏,恶化料层透气性。
⑤过湿层从干燥层下来的热废气含有大量水分,料温低于水蒸气的露点温度时,废气中的水蒸气会重新凝结,使混合料中水分大量增加而形成过湿层。
此层水分过多,使料层透气性变坏,降低烧结速度。
烧结过程中的基本化学反应①固体碳的燃烧反应固体碳燃烧反应为:反应后生成C0和C02,还有部分剩余氧气,为其他反应提供了氧化还原气体和热量。
燃烧产生的废气成分取决于烧结的原料条件、燃料用量、还原和氧化反应的发展程度、以及抽过燃烧层的气体成分等因素。
②碳酸盐的分解和矿化作用烧结料中的碳酸盐有CaC03、MgC03、FeC03、MnC03等,其中以CaC03为主。
在烧结条件下,CaC03在720℃左右开始分解,880℃时开始化学沸腾,其他碳酸盐相应的分解温度较低些。
碳酸钙分解产物Ca0能与烧结料中的其他矿物发生反应,生成新的化合物,这就是矿化作用。
反应式为:CaCO3+SiO2=CaSiO3+CO2CaCO3+Fe2O3=CaO ·Fe2O3+ CO2如果矿化作用不完全,将有残留的自由Ca0存在,在存放过程中,它将同大气中的水分进行消化作用:CaO+H2O=Ca(OH)2使烧结矿的体积膨胀而粉化。
③铁和锰氧化物的分解、还原和氧化铁的氧化物在烧结条件下,温度高于l300℃时,Fe203可以分解:Fe304在烧结条件下分解压很小,但在有Si02存在、温度大于1300℃时,也可能分解:二、球团矿生产1.球团矿的概念把细磨铁精矿粉或其他含铁粉料添加少量添加剂混合后,在加水润湿的条件下,通过造球机滚动成球,再经过干燥焙烧,固结成为具有一定强度和冶金性能的球型含铁原料。
2.球团矿生产迅速发展的原因:◆天然富矿日趋减少,大量贫矿被采用。
铁矿石经细磨、选矿后的精矿粉,品位易于提高。
过细精矿粉用于烧结生产会影响透气性,降低产量和质量。
细磨精矿粉易于造球,粒度越细,成球率越高,球团矿强度也越高。
◆球团法生产工艺的成熟。
从单一处理铁精矿粉扩展到多种含铁原料。
生产规模和操作也向大型化、机械化、自动化方向发展。
技术经济指标显著提高。
球团产品也已用于炼钢和直接还原炼铁等。
◆球团矿具有良好的冶金性能:粒度均匀、微气孔多、还原性好、强度高,有利于强化高炉冶炼。
3.球团矿生产的工艺流程一般包括原料准备、配料、混合、造球、干燥和焙烧、冷却、成品和返矿处理等工序,如图2-6所示。
图2-6球团矿生产的工艺流程。