蒸发工段生产工艺规程
乙酸乙酯生产线蒸发工段的设

乙酸乙酯生产线蒸发工段的设乙酸乙酯是一种常用的醋酸酯类有机溶剂,广泛应用于化工、制药、涂料等领域。
在乙酸乙酯的生产过程中,蒸发工段是一个关键的环节。
本文将详细介绍乙酸乙酯生产线蒸发工段的工艺流程和设备特点。
一、工艺流程乙酸乙酯生产线的蒸发工段通常采用多效蒸发器。
首先,将乙酸乙酯溶液从前一工段输送至蒸发器中。
蒸发器内部有多个效应器,每个效应器都是一个独立的蒸发单元。
乙酸乙酯溶液经过加热器加热后进入第一个效应器,溶液在效应器内部蒸发,产生蒸汽。
部分蒸汽进入下一个效应器,与乙酸乙酯溶液进行热交换,使得溶液温度升高,蒸发更加充分。
蒸发器内的效应器数目可以根据生产需求进行调整。
通常情况下,乙酸乙酯生产线的蒸发工段会设置三至五效应器,以确保溶液得到充分的蒸发。
经过多效蒸发器处理后的溶液中乙酸乙酯的浓度会大幅提高。
二、设备特点1. 多效蒸发器:多效蒸发器是乙酸乙酯生产线蒸发工段的核心设备。
其采用多个效应器的设计,能够有效提高蒸发效率,降低能耗。
同时,多效蒸发器还具有结构紧凑、占地面积小等特点,适用于大规模生产。
2. 加热器:加热器用于对乙酸乙酯溶液进行加热,提高溶液温度,促进蒸发。
加热器通常采用蒸汽加热或热水加热的方式,能够满足不同生产条件的需求。
3. 蒸汽回收系统:乙酸乙酯生产过程中产生的蒸汽可以通过蒸汽回收系统进行回收利用。
蒸汽回收系统能够提高能源利用效率,减少能耗。
4. 温度控制系统:蒸发工段需要对溶液温度进行精确控制,以确保蒸发过程的稳定性和有效性。
温度控制系统能够通过自动调节加热器的热量,实现对溶液温度的精确控制。
5. 安全设备:乙酸乙酯是一种易燃易爆物质,蒸发工段应配备相应的安全设备,如爆炸防护设备、泄漏报警装置等,以确保生产过程的安全性。
三、总结乙酸乙酯生产线蒸发工段是乙酸乙酯生产过程中的关键环节。
通过多效蒸发器的运用,能够有效提高蒸发效率,降低能耗。
同时,采用适当的设备和安全措施,能够保证生产过程的安全性和稳定性。
蒸发操作规程

蒸发岗位操作规程编写人:审核人:生产部:安环部:设备部:总经理:二〇一一年八月十五日目录第一章岗位任务 ...................................... 错误!未定义书签。
1.蒸发岗位任务....................................... 错误!未定义书签。
2.岗位控制点......................................... 错误!未定义书签。
3.岗位职责.......................................... 错误!未定义书签。
4.巡检.............................................. 错误!未定义书签。
第二章工作原理 ...................................... 错误!未定义书签。
第三章工艺流程 ...................................... 错误!未定义书签。
一、降膜蒸发原理.................................... 错误!未定义书签。
二、工艺流程概述..................................... 错误!未定义书签。
第四章物料特性 ...................................... 错误!未定义书签。
第五章工艺指标 ...................................... 错误!未定义书签。
第六章操作要点 ...................................... 错误!未定义书签。
1.1停车操作要点 ..................................... 错误!未定义书签。
1.2成品碱质量控制操作要点 ........................... 错误!未定义书签。
碱回收蒸发工艺规程
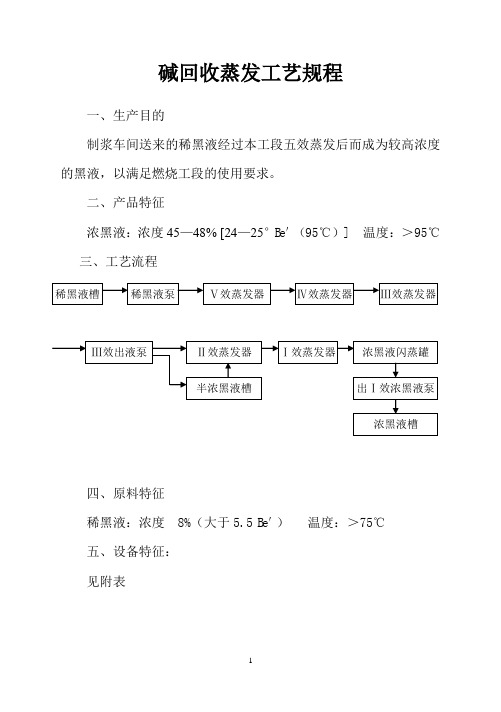
碱回收蒸发工艺规程一、生产目的制浆车间送来的稀黑液经过本工段五效蒸发后而成为较高浓度的黑液,以满足燃烧工段的使用要求。
二、产品特征浓黑液:浓度45—48% [24—25°B e′(95℃)] 温度:>95℃三、工艺流程四、原料特征稀黑液:浓度 8%(大于5.5 B e′)温度:>75℃五、设备特征:见附表附表:六、工艺技术条件1.新蒸汽(进Ⅰ效)压力:0.2—0.24Mpa温度:<138℃进汽量:5—8t/h2.稀黑液浓度:>5.5°B e′(直测)温度:>75℃3.温水(冷却水)温度:40—45℃Ⅰ效蒸发器液室蒸汽温度:116℃Ⅱ效蒸发器液室蒸汽温度:100℃Ⅲ效蒸发器液室蒸汽温度:86℃Ⅳ效蒸发器液室蒸汽温度:72℃Ⅴ效蒸发器液室蒸汽温度:58℃Ⅰ效蒸发器液室蒸汽压力:0.078MpaⅡ效蒸发器液室蒸汽压力:0.03MpaⅢ效蒸发器液室蒸汽压力:-38.6KpaⅣ效蒸发器液室蒸汽压力:-65.3KpaⅤ效蒸发器液室蒸汽压力:-84.44KpaⅠ—Ⅴ效黑液循环泵出口压力:0.12Mpa出Ⅰ效浓黑液泵出口压力:0.25Mpa清凝洁水泵出口总管压力:0.32Mpa送燃烧浓黑液泵出口压力:0.32Mpa出Ⅱ效、Ⅲ效黑液泵出口压力:0.25Mpa半浓黑液泵出口压力:0.2Mpa稀黑液泵出口压力:0.15Mpa污凝洁水泵出口压力:0.21Mpa真空泵抽气压力:-82Kpa温水泵出口压力:0.35Mpa清水进蒸发总管压力:0.25Mpa仪表用压缩空气总管压力:0.7Mpa蒸发工岗位职责1.负责蒸发工艺的全部操作,按操作规程使用和维护各种设备,确保安全生产;2.严格执行工艺规程,完成当班的生产任务,供给燃烧工段合格的浓黑液;3.做好突然停电、停汽、停水的停机安全操作;4.注意水、电、汽的供应情况,发现异常随时与生产调度及有关部门取得联系,以确保正常生产;5.检查制浆车间来的稀黑液质量,如发现不合格应及时通知有关部门;6.注意新蒸汽冷凝水的清洁程度,如发现异常现象,应立即通知碱炉停止供软水,通知化验工取样化验,不得将不合格的冷凝水送往燃烧工段;7.生产中应做到勤检查,认真做好各项记录,注意仪表运转是否正确,经常查看电脑各画面的变化与现场是否一致;8.发现设备、仪表等有故障时,应立即通知检修;9.做好各项生产记录,填写交班记录,并认真做好交接班工作;10.做好本岗位所属设备、管道、仪表的一般保养工作(包括黑液泵、黑液贮槽、黑液管道及其流量计、各种调节阀的清洗工作);11.勤测试黑液的温度、波美度。
蒸发工段工艺操作规程
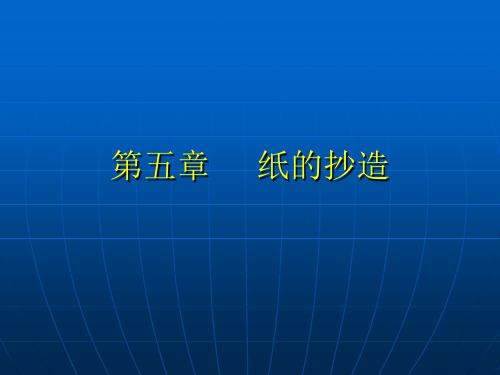
(四)网部主要脱水元件的功能与作用机理
1.纸页的成形脱水段:
(1)案辊的脱水机理:
案辊是一个空心的管辊,外层包胶。
脱水过程、机理、特点 (2)案板的脱水机理:脱水过程、机理、特点 (3)案辊与案板的比较 (4)网案摇振装置 (5)整饰辊的结构及应用 (6)真空案用: ①提供产生与网速相适应的浆速的静压头。 ②通过整流元件对浆料进行整流并产生适当的湍动。 堰池包括:
整流元件
溢流装置 喷水管 封闭式流浆箱还有视孔和照明装置。
纸机车速与堰池静压头的关系
(KcKTV)2 2gμ
2
H=
(米)
H――堰池内纸料的深度 V――纸机的车速 Kc――网速对车速的滞后系数 KT――浆速对网速的滞后系数 G――重力加速度 μ ――出唇系数(浆料湍流的系数)
二、长网成形器的主要部件及纸页成形与脱水
长网部的主要组成就是从胸辊到伏辊之间一张平直、无端的网子所形成 的网案,以及网内装的脱水元件.
(一)主要部件
胸辊、成形板、案辊、刮水板(案板)、湿真空箱、真空箱、伏辊、其它
(二)纸页的成形和脱水
1.长网部纸页成形脱水的过程 纸料从流浆箱堰板的喷口处喷出,以一定的速度和角 度喷到成形网上,这个成形和脱水的过程大体上可以分为三 个阶段:上网段、成形脱水段、高压差脱水区
2.传统圆网机网槽的典型结构 顺流式网槽、逆流式网槽、侧流式网槽
(二)圆网成形器的纸页成形与脱水过程控制
1.脱水压差和脱水弧长对纸页成形和脱水的影响
dQ Ap dt R 其中:A为脱水面积(A=脱水弧长×网宽) 2.浆速和网速的关系
2.纤维在网上的过滤与浓缩 过滤、浓缩概念; 纤维、细小组分概念:纸料中能通过200目的叫细 小组分。
生产工艺流程控制的规程

生产工艺流程控制的规程(草稿)一、目的为加强企业的生产工艺流程控制,全面提升产品的制作质量,降低生产成本,各相关部门和人员按照优化5M1E(注1)的原则进行生产活动,增强企业的竞争力,特制订本规程。
—-注1:5M1E分别是英文—人员、机器、材料、方法、测量和环境的单词首位字母。
二、使用范围本集团下属各公司的应依据本规程来制订、执改进行、生产工艺流程、对其结果进行考核、奖惩,除另有规定外,均以本规程执行;三、规程的内容:1、工艺流程涉及的部门(体系化)工艺流程涉及的部门有:各公司的技术部、生产部、质检部、和集团采购部.2、管理责任(制度化)(1)各公司技术部责任a,制定合理的工艺流程文件各公司的技术部依据产品任务单,制定生产工艺流程的文件,工艺流程文件的主要是以下三种类:-—工艺过程卡片;-—工序卡片;——操作说明书;工艺流程的卡片和操作说明书中应包含:图纸(加工的工件图纸以及关键步骤和重要环节都有图纸说明)、加工工序、加工方法及对环境的要求、检验及方法、产品的包装、工时定额、材料和物耗定额、使用的设备和工装、加工工具、对特殊工件的吊装位置及方法、包装方法、加工的起始时间、责任者的签名等,总之应当是实际工作中涉及的工序和各个工序中要点(5M1E)都要简约地反映在流程中; -—注2:工时定额和物耗定额:在实际中灵活应用和执行,对于首件和单件生产可以是定性管理;对于3-5件的小批量生产应当是首件完成后,对出其余件进行的半定量管理,就是给个范围值;对于成熟的大批量生产件应当是定量管理,就是应当给出固定的定额;—-注3:可以有空项,按实际生产中需要的项目编写,应当简要全面部不应当有漏项;各个公司在制定工艺流程时,可以是表格式、卡片式、文字表述式,只要能在实际生产中,对生产的产品有以下作用即可-—加工的指导、检验指导、记录完整(可以追溯产品的加工历史);b,根据生产出现的问题,可以用工艺流程附加单的形式进行补充及修改,必要时废除老工艺,重新制定新工艺;c,会同质检部门处理质量异常问题.(2)各公司生产部责任a,生产操作者应当随时自我查对,检查是否符合流程的规定与相关的质量标准,即开展自检工作。
液氯工段

第九章液氯工段第一节工艺流程及主要设备一、本工段任务本工段的主要任务是.将气体氯经低温冷却成液体氯,液氯贮存在贮槽内,经计量包装入钢瓶或槽车。
未液化气体去合成盐酸工段。
氯气液化所需的冷量由气氨压缩冷却液化后节流蒸发过程产生的冷量所提供。
二、工艺流程简述液氯生产工段由冷冻、液化、包装、整瓶四个工序组成(见图9—1)。
来自氯干燥工段合格的干燥氯气进入液化槽的氯冷凝器,与槽内-10~-25℃的氯化钙盐水进行间接换热后冷凝成气、液混合物进入分离器,液氯由底部出口管流出,进入液氯计量槽,没有冷凝下来的含氯尾气送盐酸工段处理。
气氯冷凝的传热过程为:气氯将热量传给氯化钙水溶液,氯化钙水溶液再将热量传给氨,液氨吸热蒸发气化以供给气氯液化时所需的冷量,氯化钙溶液则在氨蒸发器和氯冷凝器之间循环以传递冷量。
液氨蒸发成气氨进集氨器,经过双级压缩到1.5MP,经油分离器,然后进入氨冷凝器冷凝成液氨。
又经分配台节流分配到各液化槽和用冷部门作再次循环。
液氯在汽化器内通过夹套热水加热,使液氯气化产生1.0MPa的压力,将计量槽内的液氯压送到包装岗位,按规定的包装量灌入检验合格的液氯钢瓶内。
计量槽、包装岗位和整瓶的低压、低浓度废气送漂粉精或其它用氯工段处理。
包装后计量槽和汽化器中剩余的氯排入液化槽进口的原氯总管继续液化。
图9-1 液氯工艺流程图1-液化槽;2-液氯气液分离器;3-集氨器;4-低压机;5-中间冷却器;6-高压机;7-氨油分离器;8-冷凝器;9-氨贮槽;10-氨分配台;11-液氯计量槽;12-20t地中衡;13-汽化器;14-热水槽;15-液下泵;16-排水槽;17-钢瓶;18-3t地中衡;19-缓冲器;20-娜氏泵;21-旋风分离器;22-酸沫捕集器;23-浓硫酸高位槽三、主要设备及作用1.氯气液化器(1)箱式液化槽箱式液化槽为长方形碳钢设备(见图9—2),中间有一导流挡板,槽的一边为多组盘管组成的氯气冷凝器,另一边为多组盘管组成的氨蒸发管,并装有立式搅拦器。
蒸发车间操作规程

目录一、车间概述 (1)1.车间主要任务 (1)2.生产原理 (1)3.工艺流程 (1)3.1工艺流程描述 (1)3.2工艺流程简图 (2)4.管式降膜蒸发器原理 (3)二、蒸发车间主要工艺技术指标 (3)三、车间责任制、岗位划分及管辖区域 (4)1.车间责任制 (4)1.1车间主任岗位职责 (4)1.2主任助理岗位职责 (4)1.3设备管理员岗位职责 (5)1.4值班长岗位责任制 (5)1.5班长岗位责任制 (5)2.岗位划分及管辖区域 (7)四、交接班制度 (8)五、车间通用技术标准 (11)5.1车间设备完好标准 (11)5.2车间设备点巡检标准 (11)5.3车间作业环境标准 (12)5.4车间设备故障标准 (12)5.5车间设备润滑标准 (13)5.6车间安全标准 (13)六、各岗位作业标准 (14)6.1蒸发站岗位 (14)6.1.1主操岗位职责 (14)6.1.2蒸发站现场操作工岗位职责 (14)6.1.3蒸发站岗位技术指标 (16)6.1.4蒸发站岗位技术操作标准 (16)6.1.4.1开车前的准备工作 (16)6.1.4.2开车步骤 (17)6.1.4.3运行过程的操作事项 (18)6.1.4.4正常停车步骤 (18)6.1.4.5紧急停车步骤 (19)6.1.4.6蒸发站水洗 (19)6.1.5蒸发器事故处理 (20)6.1.6蒸发站岗位设备点检及维护标准 (20)6.1.6.1蒸发器点检、润滑标准 (20)6.1.6.2蒸发器维护保养标准 (20)6.1.6.3真空泵点检标准 (20)6.1.6.4离心泵点检标准 (21)6.1.6.5板式换热器点检标准 (22)6.1.6.6真空泵润滑标准 (22)6.1.6.7离心泵润滑标准 (22)6.1.6.8真空泵维护与保养标准 (22)6.1.6.9离心泵维护与保养标准 (22)6.1.6.10板式维护与保养标准 (23)6.1.7蒸发站岗位安全作业标准 (23)6.1.8蒸发站现场岗位巡检标准 (23)6.1.9点巡检路线图 (24)6.2原液及水洗岗位 (24)6.2.1原液及水洗岗位职责 (24)6.2.2原液及水洗技术指标 (25)6.2.3原液岗位技术操作标准 (25)6.2.3.2开车步骤 (25)6.2.3.3运行过程的操作事项 (25)6.2.3.4正常停车步骤 (26)6.2.4水洗岗位技术操作标准 (26)6.2.4.1开车前的准备工作 (26)6.2.4.2开车步骤 (26)6.2.4.3运行过程的操作事项 (26)6.2.4.4正常停车步骤 (26)6.2.5原液水洗常见故障处理 (26)6.2.6原液及水洗岗位设备点检及维护标准 (27)6.2.6.1离心泵点检标准 (27)6.2.6.2板式换热器点检标准 (27)6.2.6.3离心泵润滑标准 (28)6.2.6.4离心泵维护与保养标准 (28)6.2.6.5板式维护与保养标准 (28)6.2.7原液及水洗岗位安全巡检标准 (28)6.2.8点巡检路线图 (29)6.3循环母液及补碱岗位 (29)6.3.1循环母液岗位职责 (29)6.3.2补碱岗位职责 (29)6.3.3循环母液及补碱岗位技术指标 (30)6.3.4循环母液技术操作标准 (30)6.3.4.1开车前的准备工作 (30)6.3.4.2开车步骤 (30)6.3.4.3运行过程的操作事项 (30)6.3.4.4正常停车步骤 (30)6.3.5补碱岗位技术操作标准 (31)6.3.5.1开车前的准备工作 (31)6.3.5.2开车步骤 (31)6.3.5.4正常停车步骤 (31)6.3.6合格循环母液调配方法 (31)6.3.7常见故障处理 (32)6.3.8循环母液及补碱岗位设备点检及维护标准 (32)6.3.8.1离心泵点检标准 (32)6.3.8.2离心泵润滑标准 (33)6.3.8.3离心泵维护与保养标准 (33)6.3.9循环母液及补碱岗位安全巡检标准 (33)6.3.10点巡检路线图 (34)6.4蒸发酸洗站岗位 (34)6.4.1蒸发酸洗站岗位职责 (34)6.4.2蒸发酸洗站技术指标 (34)6.4.3配酸的操作标准 (35)6.3.4.1配酸前的准备工作 (35)6.3.4.2配酸步骤 (35)6.3.4.3配酸的安全注意事项 (35)6.4.4稀酸配置公式 (35)6.4.5酸泵的操作标准 (36)6.4.5.1开车前的准备工作 (36)6.4.5.2开车步骤 (36)6.4.5.3运行过程的操作事项 (36)6.4.5.4正常停车步骤 (36)6.4.6常见故障处理 (36)6.4.7蒸发酸洗站岗位设备点检及维护标准 (37)6.4.7.1氟塑料离心泵点检标准 (37)6.4.7.2离心泵润滑标准 (37)6.4.7.3氟塑料离心泵维护与保养标准 (37)6.4.8蒸发酸洗站岗位安全巡检标准 (38)6.4.9点巡检路线图 (38)6.5蒸发循环水岗位 (38)6.5.1蒸发循环水岗位职责 (38)6.5.2蒸发循环水岗位技术指标 (39)6.5.3循环水泵操作标准 (39)6.5.3.1开车前的准备工作 (39)6.5.3.2开车步骤 (39)6.5.3.3运行过程的操作事项 (39)6.5.3.4正常停车步骤 (39)6.5.4冷却塔操作标准 (40)6.5.4.1开车前的准备工作 (40)6.5.4.2开车步骤 (40)6.5.4.3运行过程的操作事项 (40)6.5.4.4正常停车步骤 (40)6.5.5常见故障处理 (40)6.5.5.1泵常见故障处理 (40)6.5.5.2冷却塔常见故障处理 (40)6.5.6蒸发循环水岗位设备点检及维护标准 (41)6.5.6.1蒸发循环水岗位点检标准 (41)6.5.6.2蒸发循环水设备润滑标准 (41)6.5.6.3蒸发循环水设备维护与保养标准 (42)6.5.7蒸发循环水岗位安全巡检标准 (42)6.5.8点巡检路线图 (42)七、应急预案 (42)第一节紧急停电处理方案 (42)第二节机封水泵跳停处理方案 (44)第三节蒸发循环水软连接爆管应急预案 (44)附录一:技术术语 (46)附录二:蒸发车间主要计算公式....................................................................... - 71 -6 附录三:蒸发车间设备明细表 (48)一、车间概述1.车间主要任务1.1将分解车间的种分母液进行蒸发浓缩,蒸发出高浓度的蒸发母液,并保证液量顺利通过,同时将合格冷凝水送至各工序的用水点。
蒸发工艺运行规程

蒸发工段一.工艺规程二.安全操作规程编制:审核:批准:20xx 年7月一.工艺规程1生产目的蒸发工段的主要目的是把从蒸煮工段送来的稀黑液蒸发浓缩成供燃烧工段碱炉燃烧用的合格浓黑液。
2原料及能源特征2.1原料特征蒸发工段的原料是制浆送来的黑液。
硫酸盐蒸煮木片所产生的黑液,固形物中无机物约占30-35%,主要为蒸煮废液中残余的化学药品,以及和制浆原料中的有机物化合的金属基、制浆原料本身带来的无机物成分等,是黑液回收过程中再生蒸煮液的主要化学药品的来源;有机物约占65-70%,主要包括制浆原料在蒸煮过程中降解产物、溶出物等,如木素、纤维素、半纤维素、淀粉、树脂、色素及有机酸等,其中木素的燃烧值约为25MJ/Kg,碳水化合物约为12.6MJ/Kg,黑液回收时产生热量的主要来源。
2.2能源特征(低压饱和蒸汽)2.3产品特征超浓黑液(阔叶木):温度120-128℃、流量65(t/h)、固含量71-76%;2.4设备特征2.4.1自流降膜蒸发器蒸发器效室加热单元(膜板)由两块不锈钢板焊接组成。
蒸汽在单元内冷凝;黑液进入效室底部,由循环泵把黑液从底部循环至顶部均匀分配,并沿膜板外表面流下。
较大的黑液循环量保证了加热表面充分湿润,没有干固现象发生。
效室底部有适量黑液,以保证供给液的变化或其它扰动发生时,系统不会因效室黑液的不足而产生运行的困难。
二次蒸汽从黑液中溢出并上升进入雾沫分离器。
雾沫分离器装有洗涤喷嘴。
两块黑液侧膜板间有约20-30mm的自由空间。
2.4.2表面冷凝器Ⅵ效的二次蒸汽在表面冷凝器中冷凝。
二次蒸汽在膜板内冷凝并把热量传给在外表面流动和冷却水(来自冷却水循环站)。
出口水温45℃左右。
3工艺流程制浆来的黑液16-18%与Ⅱ效黑液混合18%60%添加碱灰64-74% 送碱炉燃烧4工艺过程及原理4.1概述本工段设计蒸发能力240吨水/小时(汽压350KPa)。
固含量16%的稀黑液在六效自流降膜式蒸发器中增浓,最终产品固含量64-74%的浓黑液泵送超浓黑液槽。
浸出车间工艺流程

浸出车间设备操作规程(二)一、浸出工段1、主要设备:进料封闭绞龙(E101)、浸出器(E102)、分料绞龙(102a)、混合油循环泵(103-1-6、E105-1-2)、缓冲罐、旋液分离器(E104a、E104b、E104c)、分水罐(E129)、新鲜溶剂泵(E130)、新鲜溶剂加热器(E140)。
2、工艺流程循环油泵103-1-6入浸料胚螺旋喂料器E101 浸出器E102 混合油泵新鲜溶剂E129分水罐室外罐143-1-2130 分水泵105-1 旋液分离器E104a、E104c 离心油泵E105-2 旋液分离器E104b 节能器E1143、技术要求3、1、1 溶剂比:1︰0.8—1.13、1、2 溶剂温度:50℃—55℃3、1、3 浸出器料封高度为3.8m—5.0m3、1、4 浸出器保持负压状态为10—30㎜H2O3、1、5 混合油温度为:55℃左右3、1、6 粕中残油:1%以下4、浸出开车顺序4·1系统预热及真空预备开启(E161-1-2-3)循环水泵,将安全水供给系统就绪,确认其它设备都处于关闭状态,打开并检查所有自动控制的空气供给情况,关闭DTDC每层卸料门和人孔,启动抽风机(E138),调节风机出口管线上的旁通阀门,调整尾气负压值为30㎜H2O,启动吸收塔(E132)调节矿物油的喷淋量到4-6m3/h。
检查分水罐(E129)中的水位,必要时加水到视镜中可以看到溢流,启动循环分水泵(E130)开启蒸汽阀,并开启下列各设备的蒸汽阀门。
(1)、解吸塔(E133)加热。
(2)、矿物油加热(135)。
(3)、预蒸发器(E119)。
(4)、汽提塔内外加热(E121)。
(5)、DTDC(E109)加热。
(6)、蒸发喷射泵(E117)。
(7)、汽提喷射泵(E127)。
(8)、废水蒸煮罐中白水温达到90℃时,启动热水泵(E113),待浸出器负压值达到10—30㎜H2O时,通知预处理进料。
4·2启动(E106)调节溶剂流量计,按位号依次启动混合油循环油泵(E103-1-6),混合油应在料床上均匀分布,当溶剂达到浸出器第二格的适当高度时,启动(E105-1)循环油泵,将混合油送入旋液分离器(E104)。
硫铵工段技术操作规程
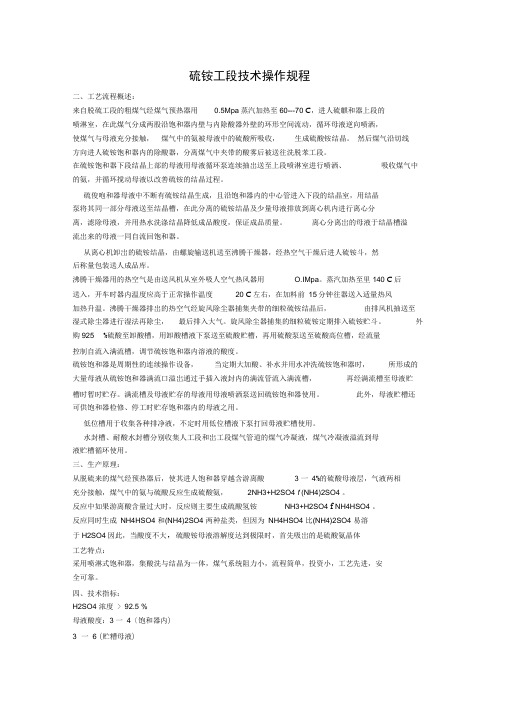
硫铵工段技术操作规程二、工艺流程概述:来自脱硫工段的粗煤气经煤气预热器用0.5Mpa蒸汽加热至60---70 C,进人硫麒和器上段的喷淋室,在此煤气分成两股沿饱和器内壁与内除酸器外壁的环形空间流动,循环母液逆向喷洒,使煤气与母液充分接触,煤气中的氨被母液中的硫酸所吸收,生成硫酸铵结晶。
然后煤气沿切线方向进人硫铵饱和器内的除酸器,分离煤气中夹带的酸雾后被送往洗脱苯工段。
在硫铵饱和器下段结晶上部的母液用母液循环泵连续抽岀送至上段喷淋室进行喷洒、吸收煤气中的氨,并循环搅动母液以改善硫铵的结晶过程。
硫俊咆和器母液中不断有硫铵结晶生成,且沿饱和器内的中心管进入下段的结晶室,用结晶泵将其同一部分母液送至结晶槽,在此分离的硫铵结晶及少量母液排放到离心机内进行离心分离,滤除母液,并用热水洗涤结晶降低成品酸度,保证成品质量。
离心分离岀的母液于结晶槽溢流岀来的母液一同自流回饱和器。
从离心机卸岀的硫铵结晶,由螺旋输送机送至沸腾干燥器,经热空气干燥后进人硫铵斗,然后称量包装送人成品库。
沸腾干燥器用的热空气是由送风机从室外吸人空气热风器用O.IMpa。
蒸汽加热至里140 C后送入,开车时器内温度应高于正常操作温度20 C左右,在加料前15分钟往器送入适量热风加热升温。
沸腾干燥器排岀的热空气经旋风除尘器捕集夹带的细粒硫铵结晶后,由排风机抽送至湿式除尘器进行湿法再除尘,最后排入大气。
旋风除尘器捕集的细粒硫铵定期排入硫铵贮斗。
外购925 %硫酸至卸酸槽,用卸酸槽液下泵送至硫酸贮槽,再用硫酸泵送至硫酸高位槽,经流量控制自流入满流槽,调节硫铵饱和器内溶液的酸度。
硫铵饱和器是周期性的连续操作设备,当定期大加酸、补水并用水冲洗硫铵饱和器时,所形成的大量母液从硫铵饱和器满流口溢岀通过手插入液封内的满流管流入满流槽,再经满流槽至母液贮槽时暂时贮存。
满流槽及母液贮存的母液用母液喷洒泵送回硫铵饱和器使用。
此外,母液贮槽还可供饱和器检修、停工时贮存饱和器内的母液之用。
蒸发岗位操作规程
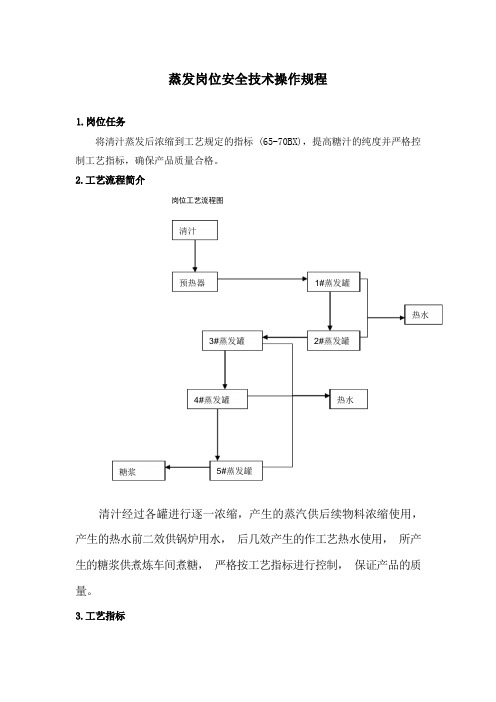
将清汁蒸发后浓缩到工艺规定的指标 (65-70BX),提高糖汁的纯度并严格控 制工艺指标,确保产品质量合格。
岗位工艺流程图清汁经过各罐进行逐一浓缩,产生的蒸汽供后续物料浓缩使用, 产生的热水前二效供锅炉用水, 后几效产生的作工艺热水使用, 所产 生的糖浆供煮炼车间煮糖, 严格按工艺指标进行控制, 保证产品的质 量。
清汁1#蒸发罐热水3#蒸发罐4#蒸发罐5#蒸发罐2#蒸发罐预热器糖浆热水4.1 管辖区域:本岗位管辖范围包括 6 台蒸发罐、 1 台冷凝器、减温减压设备及 所属工艺管道、蒸汽管道、疏水管道、管件、阀门、仪表和建构筑物等。
4.2 主要设备(见下表)5.1 准备工作a) 为确保开机生产安全, 各效罐在启用前应给汽鼓、汽室试水压, 确认无漏才干投入使用;b) 所有安全阀、 压力表、 真空表和温度计等测量仪表必须经过校 准后才干使用;c) 检查各效罐 的玻璃视镜,如有破裂应即将更换;d) 开启废汽管疏水阀;e) 检查各效罐 的糖汁、蒸汽和水等管道、阀门开关是否灵便, 调节好启用罐阀门;f) 待供废汽后,即可对列管式蒸发罐进行暖罐;序 设备位号 设备名称 规格及型号 单 数 备注 号 位 量 1 2 3 4 6备 注根据不同的生产情况,严格按照技术员要求进行控制,严格执行 技术员的指令工艺控制指标 末效真空度 1#罐进汽温度1#罐进汽压力 糖浆锤度数 据g) 上述工作做好后,即可通知供水部门开始供给冷凝器用水,并检查真空管路,无异常情况即可准备开机。
5.3 开机操作关闭被暖蒸发罐的蒸汽阀,并调节好相应阀门;待糖汁达到末效蒸发罐后,即通知加热岗位可抽取汁汽,开启糖浆排出阀,通知水泵工开启粗糖浆泵抽取糖浆,将糖浆送至下一工序;调节各效罐液面至正常状况,调节各效氨管,保持各效罐有一定压力(温度)差,逐渐转入正常蒸发操作。
5.4 正常操作蒸发罐按低液面五定操作原则,进行正常均衡生产。
即:a)保持各效力(真空度)稳定;b) 保持各效液面稳定,列管式蒸发罐应按低液位(糖汁沸腾时液面刚好盖过汽鼓管板);c) 保持各效各种阀门稳定;d) 保持进汽稳定;e) 保持各效抽汁汽稳定。
碱炉工艺
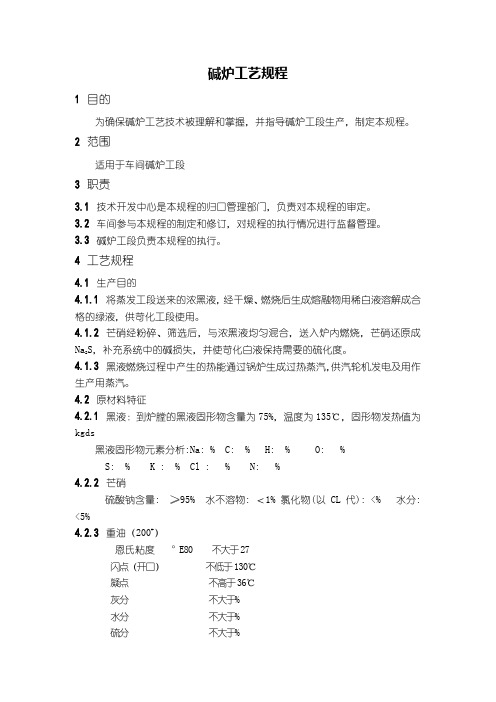
碱炉工艺规程1 目的为确保碱炉工艺技术被理解和掌握,并指导碱炉工段生产,制定本规程。
2 范围适用于车间碱炉工段3 职责3.1 技术开发中心是本规程的归口管理部门,负责对本规程的审定。
3.2 车间参与本规程的制定和修订,对规程的执行情况进行监督管理。
3.3 碱炉工段负责本规程的执行。
4 工艺规程4.1 生产目的4.1.1 将蒸发工段送来的浓黑液,经干燥、燃烧后生成熔融物用稀白液溶解成合格的绿液,供苛化工段使用。
4.1.2 芒硝经粉碎、筛选后,与浓黑液均匀混合,送入炉内燃烧,芒硝还原成S,补充系统中的碱损失,并使苛化白液保持需要的硫化度。
Na24.1.3 黑液燃烧过程中产生的热能通过锅炉生成过热蒸汽,供汽轮机发电及用作生产用蒸汽。
4.2 原材料特征4.2.1 黑液:到炉膛的黑液固形物含量为75%,温度为135℃,固形物发热值为kgds黑液固形物元素分析:Na: % C: % H: % O: %S: % K : % Cl : % N: %4.2.2 芒硝硫酸钠含量: ≥95% 水不溶物: <1% 氯化物(以CL代): <% 水分: <5%4.2.3 重油(200#)恩氏粘度°E80 不大于27闪点(开口)不低于130℃凝点不高于36℃灰分不大于%水分不大于%硫分不大于%机械杂质不大于%最小净发热值 41MJ/Kg 4.3 产品特征4.3.1 绿液O计)浓度:128-133g/L (以Na2硫化度:35%芒硝还原率:>90%4.3.2 过热蒸汽含Na+: kg含SiO2: kg温度: 480℃压力: 68bar4.4 工艺流程方框图4.4.1 汽水流程回收冷凝水、软化水主蒸汽去汽轮机4.4.2 供风、烟气流程顶部取风气烟囱4.4.3 黑液流程蒸发来浓黑液入炉膛燃烧4.4.4 重油流程入炉膛燃烧4.4.5 芒硝、灰流程芒硝锅炉管束、Ⅰ、Ⅱ级省煤器灰斗静电除尘器4.4.6 绿液流程熔融物苛化工段排汽管排空4.4.7 溜槽冷却水流程软化水4.5 主要工艺技术参数1) 处理黑液干固物能力: 1204tds/d2) 过热器出口蒸汽温度: 480℃3) 主蒸汽阀处的蒸汽压力 68bar4) 设计压力87bar5) 省煤器前给水温度 120℃6) 干固物总发热量(不含芒硝) kgdS7) 蒸发来黑液温度 135℃8) 干固物含量 75%9) 省煤器出口烟气温度 170℃10) 燃烧空气温度11) 补充芒硝 20kg/kgdS4.5.1 蒸汽和给水(燃烧负荷1204tds/d)4.5.1.1 蒸汽1) 产生蒸汽(净) kgdS2) 吹灰蒸汽 kg/kgdS3) 蒸汽流量 s4) S HⅢ出口蒸汽温度 480℃5) S HⅡ出口蒸汽温度 425℃6) S HⅠ出口蒸汽温度 395℃7) S HⅠ进口蒸汽温度 294℃8) 过热器出口压力 68bar9) 汽包压力 76bar4.5.1.2 给水10) 给水流量 s11) 省煤器进口水温 120℃12) 省煤器出口水温 225℃13) 省煤器压降 2 bar4.5.2 黑液14) 到混合槽干固物含量 66%15) 到炉膛干固物含量 76%16) 黑液喷枪黑液流量(燃烧) s17) 进喷枪黑液温度 135℃18) 喷枪黑液压力(估计) —4.5.3 燃烧空气19) 炉膛总空气流量 s20) 空气温度 30℃21) 入炉空气温度22) 一次风 150℃23) 二次风 150℃24) 三次风 80℃4.5.4 烟气25) 锅炉烟气流量(O2=%) m3n/s(0℃)26) 过热器烟温℃ 92027) 锅炉管束前烟温℃ 55028) 省煤器前烟温℃ 43029) 省煤器出口烟温℃ 1704.6 工艺流程描述4.6.1 给水(图1)在正常运行期间,给水加入除氧器/贮水箱经低压蒸汽喷淋后,去除给水中的氧气和二氧化碳,并将给水加热到120℃,经除氧和加热后的给水由给水泵送往锅炉。
三效蒸发器操作规程(新编版)
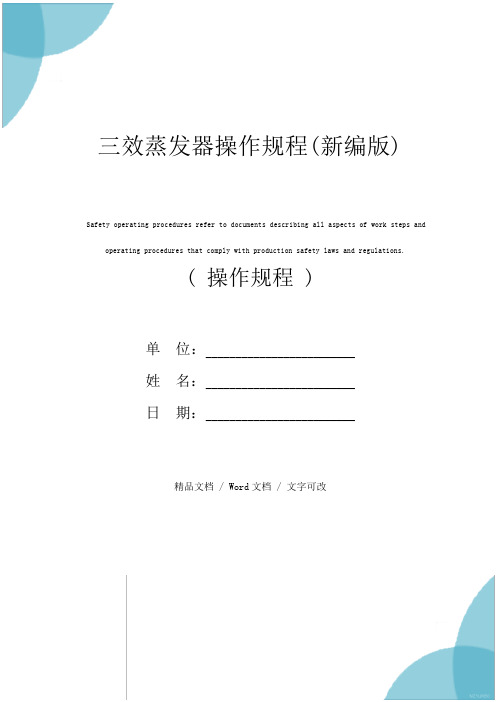
( 操作规程 )单 位:_________________________姓 名:_________________________日 期:_________________________精品文档 / Word文档 / 文字可改三效蒸发器操作规程(新编版)Safety operating procedures refer to documents describing all aspects of work steps and operating procedures that comply with production safety laws and regulations.三效蒸发器操作规程(新编版)备注:安全操作规程表达的是根据物料性质、工艺流程、利用设备或者工具进行生产工作时,就如何使用和材料准备,环境安全,质量保证等方面的工作步骤进行描述的文件和符合安全生产法律法规的操作程序。
1.工艺要求1.1产出合格的水;1.2达到废液浓缩要求;1.3做好液体平衡工作,控制处理量、接收量、排放量平衡;2.岗位任务接收精冶工段、化验室废水,利用炉前岗位蒸汽热能,通过本岗位设备,将废液中水利用蒸发冷凝分离出回用,浓缩后废液再处理的工艺。
3.开、停车程序及注意事项3.1开车前准备3.1.1确认在试水过程中浮现问题的设备均已检修完毕,通知公用工程准备开车;检查所有放空、放净、取样、冲洗阀门均处于关闭状态。
3.1.2.协调前工段操作人员准备向本工段进料。
3.1.3.检查一次水已经供至车间,各用水点排气完毕,水质无明显的铁锈及杂物。
3.1.4.打开各泵的机械密封冷却水的阀门,机械密封不能在无冷却液的情况下运转。
3.1.5.检查循环冷却水供水压力(0.4MPaG),打开间接冷凝器(E05)进口管线CWS01阀门和出口管线CWR01阀门,并调整阀门开度,检查循环冷却水上水压力(PG05)、温度(TG05)及回水温度(TG06)仪表示参数是否准确。
蒸发岗位操作规程

尿素蒸发操作规程目录第一章工段简介及工作任务 (3)第一节岗位工作简介 (3)第二节蒸发岗位任务 (3)第三节岗位责任分工 (3)第二章尿素主厂房主要反应及生产特点 (4)第一节尿素系统主要反应 (4)第二节尿素溶液蒸发的特性 (4)第三节生产特点 (6)第三章工艺流程及说明 (7)第一节尿素工艺流程方块图 (7)第二节工艺流程文字说明 (8)第四章尿素主厂房安全操作规程 (9)第五章蒸发岗位安全技术说明 (10)第一节工艺介质说明 (10)第二节安全、消防器材使用 (12)第六章蒸发岗位工艺指标 (13)第七章蒸发岗位巡检制度及路线 (13)第八章蒸发岗位开停车操作规程 (14)第一节原始开车程序 (14)第二节正常开车规程 (14)第三节停车规程 (15)第四节紧急断电停车规程 (15)第六节倒熔融泵规程 (16)第八节蒸发岗位操作要点 (17)第九节尿素深度水解系统原始开车: (18)第九章蒸发岗位日常管理制度 (19)第一节生产岗位交接班制度 (19)第二节产品质量控制细则 (20)第三节成品尿素分堆程序 (21)第四节成品尿素粒度对比程序 (22)第十章蒸发岗位操作常见知识问答 (22)第十一章设备工艺参数 (31)第一章工段简介及工作任务第一节岗位工作简介蒸发岗位,有四个班组。
其中每个班设岗位班长一名、室内操作一名、室外操作一名,3人组成;四个班共12人;第二节蒸发岗位任务1、本岗位负责由尿素合成反应物经过中低压分解和闪蒸之后,从降膜闪蒸器得到约90℃、71%的尿液,送至一二段蒸发系统,经过蒸发后浓度至99.5%-99.7%的熔融尿素,用尿素熔融泵送至旋转造粒喷头喷洒造粒,在塔底得到颗粒大而均匀的尿素。
2、负责蒸发和水解解吸的的开停车,正常生产的工艺操作和异常问题的处理,确保系统稳定。
3. 保证制得优质合格的颗粒尿素和废液的达标排放。
第三节岗位责任分工一、班长职责1、负责本班的安全生产全面工作,特别是要注意制止违章作业。
蒸发操作
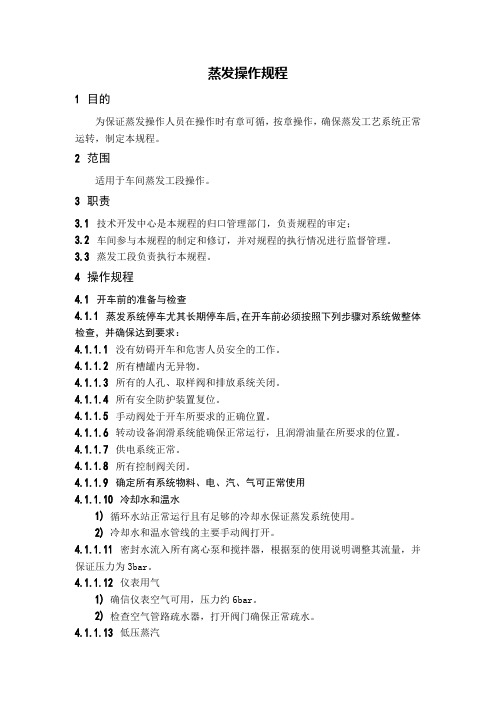
蒸发操作规程1 目的为保证蒸发操作人员在操作时有章可循,按章操作,确保蒸发工艺系统正常运转,制定本规程。
2 范围适用于车间蒸发工段操作。
3 职责3.1 技术开发中心是本规程的归口管理部门,负责规程的审定;3.2 车间参与本规程的制定和修订,并对规程的执行情况进行监督管理。
3.3 蒸发工段负责执行本规程。
4 操作规程4.1 开车前的准备与检查4.1.1 蒸发系统停车尤其长期停车后,在开车前必须按照下列步骤对系统做整体检查,并确保达到要求:4.1.1.1 没有妨碍开车和危害人员安全的工作。
4.1.1.2 所有槽罐内无异物。
4.1.1.3 所有的人孔、取样阀和排放系统关闭。
4.1.1.4 所有安全防护装置复位。
4.1.1.5 手动阀处于开车所要求的正确位置。
4.1.1.6 转动设备润滑系统能确保正常运行,且润滑油量在所要求的位置。
4.1.1.7 供电系统正常。
4.1.1.8 所有控制阀关闭。
4.1.1.9 确定所有系统物料、电、汽、气可正常使用4.1.1.10 冷却水和温水1) 循环水站正常运行且有足够的冷却水保证蒸发系统使用。
2) 冷却水和温水管线的主要手动阀打开。
4.1.1.11 密封水流入所有离心泵和搅拌器,根据泵的使用说明调整其流量,并保证压力为3bar。
4.1.1.12 仪表用气1) 确信仪表空气可用,压力约6bar。
2) 检查空气管路疏水器,打开阀门确保正常疏水。
4.1.1.13 低压蒸汽3) 小心打开低压蒸汽主管线上的手动阀。
4) 确保蒸汽疏水器正常运行,缓慢打开蒸汽疏水器旁通阀。
4.1.1.14 检查液位变送器的清洗水流量应在30-50l/s左右4.2 蒸发站的开车4.2.1 蒸发器空载或长期停车(各效体已排空)的情况下的开车系统的正常开车将按以下顺序执行:稀黑液装效启动真空系统供给系统低压蒸汽给系统正常供给黑液结晶效ⅠA 运行4.2.1.1 稀黑液装效5) 打开手动阀V1709或V1710,选择稀黑液槽1或26) 选择稀黑液泵41-P-033或41-P-034,打开稀黑液泵入口侧的手动阀7) 启动稀黑液泵41-P-033或41-P-0348) 手动稍稍打开给料稀黑液控制阀FV-450直到有黑液开始流入。
土壤调理剂工艺操作规程
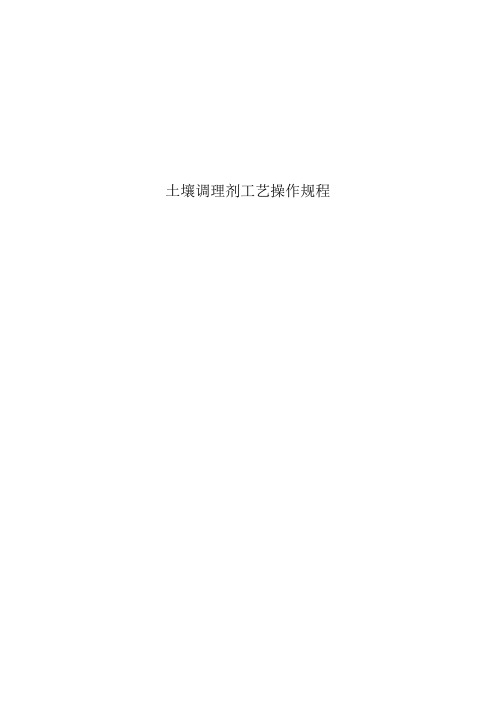
土壤调理剂工艺操作规程1目的为加强肥料车间土壤调理剂生产过程的控制,使操作管理制度化、规范化,有效控制工艺参数,提高设备运行效率,做到节能降耗,保证产品质量,特制定工艺操作规程。
2适用范围本工艺操作规程适用于肥料车间土壤调理剂全体生产操作人员。
3职责3.1本工艺操作规程由肥料车间组织制定,土壤调理剂生产工段负责执行。
3.2工序操作人员按照指导书要求执行并作记录。
3.3工段长、值长负责对作业过程、记录进行监督、审核。
4造粒工艺操作规程4.2蒸发浓缩操作规程蒸发器工作原理:在负压状态下,通过蒸汽加热使料水分离从而达到浓缩的目的。
我们采用的是四效降膜式蒸发器,每效由加热器、分离器和预热器三部分组成,在蒸发使用过程中影响蒸发性能的因素较多,主要由加热介质、换热面积、真空冷凝系统、设备是否进行保温处理等方面。
4.2.1开车D盘车:检查各循环泵、真空泵、冷凝水泵等的油位是否合适,手动盘车运转设备,应无卡阻现象。
2)检查各效蒸发器及各循环管道有无漏点。
通常关闭各进出阀门,开启蒸汽试压,至一效温度升至100℃,关闭汽阀。
逐一排查有无漏点,保证蒸发效率各效之间以及各配料罐之间阀门的开关情况,打开各泵的冷却水阀门。
3)查量:检查原液罐及成品罐的储存量。
4)开启冷却水泵,使冷却水循环向各用水系统供水。
5)开启真空泵待真空度达到-0.07MPa以上,联系热电开车。
6)进料:开启进料泵,使料液自配料罐进入四效分离器,由四效出料泵依次进入预热器1—►预热器2——A预热器3—►一效蒸发器一►二效蒸发器一►三效蒸发器。
7)一、二、三、四效的液位控制以蒸发器视镜一半内有比较稳定的可视液位为准。
8)缓慢开启蒸汽阀门,使料液有一个稳定的预热过程,蒸汽阀门的开启幅度在蒸汽压力表上反映不超过0.O1MPa09)调节阀门控制各参数:一效:85-93℃;二效:78-88℃;三效:64-78℃;四效:45-60℃。
一效加热器真空度0-—0.045MPa;分离器真空度-0.015——0.050MPao二效加热器真空度-0.021——0.053MPa;分离器真空度-0.025——0.054MPa。
- 1、下载文档前请自行甄别文档内容的完整性,平台不提供额外的编辑、内容补充、找答案等附加服务。
- 2、"仅部分预览"的文档,不可在线预览部分如存在完整性等问题,可反馈申请退款(可完整预览的文档不适用该条件!)。
- 3、如文档侵犯您的权益,请联系客服反馈,我们会尽快为您处理(人工客服工作时间:9:00-18:30)。
QB***企业标准S/LZDH—2005 氯碱分厂蒸发工段生产工艺规程2005-04-01发布2005-05-01实施*** 发布蒸发工段工艺规程1范围本标准介绍了30%烧碱的物理化学性质和生产原理,规定了30%烧碱生产过程的实际生产条件、操作方法和安全注意事项。
本标准适用于氯碱分厂蒸发工段生产岗位的操作。
2产品说明2.1产品名称本产品名称为氢氧化钠,俗名烧碱,分子式为NaOH,分子量为39.997。
2.2氢氧化钠的物理性质2.2.1比重2.13克/厘米32.2.2无水的纯氢氧化钠溶点为318℃。
2.2.5氢氧化钠是最强的碱类之一,用以中和酸时生成钠盐。
2.2.6氢氧化钠的化学性很强,能与许多有机,无机化合物起化学反应,在工业上用途很广泛。
如中和、水化、浓缩、皂化、置换原子团,醇化反应等。
2.2.7氢氧化钠有极强腐蚀性,处理时必须带好防护用品,以免灼伤身体。
2.3产品质量标准产品符合隔膜法国家二级标准NaOH≥30% Na2CO3≤0.8% NaCl≤5.0% Fe2O3≤0.01%2.4产品包装和贮运因为产品是液态,产品包装贮存均在浓碱槽,产品则用带槽罐的汽车或火车运输,小批量用户则用桶装汽车运输。
2.5产品用途烧碱在国民经济中占重要地位,是主要的化工原料,它广泛地应用在各个工业部门中,如造纸工业,纺织工业,轻工工业,冶金工业,化学医药工业,气象等部门。
3原材料的规格蒸发工段所需原材料和动力有电解液、生蒸汽、冷却水和动力电等。
原材料及动力要求规格如下表:4生产基本原理和化学反应过程液碱生产是在蒸发器中进行的,电解液在蒸发器中利用蒸汽间接加热,使电解液浓缩,逐步蒸发水分。
同时,不断分离析出结晶盐。
蒸发整个生产过程是一个物理过程,无化学反应。
蒸发生产的过程可分为三部分。
a) 电解液通过加热浓缩除去大部份水份并分离出大部份结晶盐。
b) 冷却澄清浓碱液并分离出来的结晶盐,才能达到产国家标准,供商品出售。
c) 将蒸发和浓碱冷却分离出来的结晶盐通过离心机分离后化成盐水送盐水工段使用。
母液送回蒸发器,进行再蒸发。
电解液蒸发生产所涉及的一些基本原理。
4.1电解液进蒸发器前需预热的原理。
增加预热段,以提高电解液的进料温度,这样可保证物料进入蒸发器有一个较高的温差,提高蒸发效率,在降低成本方面具体表现为:A能回收蒸汽冷凝水低品质热量。
B可减少传热面积,提高设备生产能力。
C节省加热生蒸汽热耗。
碱液的预热程度在特定的预热器中,决定于碱液物性及冷凝水温度。
电解液温度低时,预热后料液温度就低,所以输送碱液系统和贮存系统必须加强保温,预热温度的理想状态是沸点进料,一般预热温度在110~140℃之间。
4.2电解液在蒸发过程中结晶析出的原理。
溶液溶质结晶的手段有三种:一是冷却,二是蒸发浓缩,第三种是绝热蒸发,即在真空条件下使高温溶液闪蒸,溶剂蒸发时也同时带出潜热,因而蒸发器内的溶液温度下降,它兼有蒸发与冷却的双重效应。
液碱蒸发环境也是一个逐级减压降低的过程,所以在这个过程的结晶手段属后两者的组合。
液碱中NaCl在蒸发过程中结晶经过如图三个区域阶段:NaCl1曲线1:溶溶解度曲线曲线2:解过饱和度曲线度温度溶液的饱和与过饱和溶解曲线图稳定区:碱液NaCl没达到过饱和度,无结晶过程可能。
介稳区:NaCl晶核在杂质作用下能大量生成,但成长速度较慢,所以生成晶体较细小。
不稳区:NaCl晶核成长速度比生成速度快,结晶体较大。
电解液相对NaCl来说是接近饱和的水溶液,在Ⅰ效蒸发器,尽管经过一定的浓缩,但电解液温度升高,NaCl溶解度增大,故Ⅰ效NaCl仍处于接近饱和状态,处于稳定区内,无结晶析出。
影响结晶大小的主要因素:①NaOH浓度:浓度越大,结晶颗粒越小。
②结晶成长时间:时间越长,晶粒越大。
③冷却时温差:温差愈大,温度变化愈大,析出的晶核愈多,结晶颗粒愈小。
④搅拌强度:在一定范围内搅拌强度越大,结晶颗粒越大,但超过这范围,则因二次成核因素而反使颗粒细小。
4.3蒸发水分的原理碱液是由水、碱和盐组成的混合物。
根据低沸点物质先挥发的原理,对碱液进行加热蒸发,即可先赶除低沸点的水,因为在碱液中,水的沸点最低(常压下,水的沸点为100℃,碱的沸点为1390℃,盐的沸点1439℃)。
在蒸发的压力条件下,水的沸点会有所不同,压力越低,水的沸点就越低,蒸发去除水份就越容易。
所以碱液蒸发必须采用真空蒸发工艺。
4.4各效蒸发压力及液温调节原理各效蒸发压力及液温的调节,在设备装置运行过程中,能根据外界的影响而建立起自身的平衡,即随着操作条件的变化而自行调节。
如某效因为加热管结垢或加热室中不凝气排放不完全,而造成传热状况恶化,该效热阻增大,它给操作人员一个指示――排除某效故障,以恢复各效的正常运行状态。
该原理可用于洗效的有效指示:如果:①碱液经过加热管的温升从3℃升至6℃或更高。
②Ⅰ效生蒸汽压力升高(排除锅炉升压和真空下降因素)③前效压力升高④循环泵电机电流逐渐升高这四种现象的出现,都意味着蒸发系统正常工作状态的改变,有需要洗效的可能,需洗效,效体为故障出现效或压力升高的下一效。
4.5离心机分离原理任何物体作圆周运动时,都会产生离心力作用,盐泥是一种固液混合物。
盐泥中的碱液和结晶盐在离心机的转鼓内随转鼓作高速圆周运动,都会受离心力作用。
由于转鼓内筛网的作用,促使盐碱得到分离。
5生产工序和生产流程叙述5.1生产流程叙述5.1.1三效生产流程的叙述来自电解工段的电解液进入电解液贮槽,用加料泵送入螺旋预热器,预热至100℃以上,加入Ⅰ效蒸发器,浓缩后进入Ⅱ效蒸发器,再浓缩后进入Ⅲ效蒸发器,Ⅲ效蒸发器出来的30%的成品碱,送入浓碱接收槽,以经螺旋冷却器冷却沉清后,利用液位差将碱液送至液碱站贮槽,在配碱槽配至合格浓度,即可装车出售。
Ⅲ效蒸发器采出的盐浆经旋液分离器增稠后送入高位槽,清液器流到Ⅲ效蒸发器,或出料至浓碱接收槽(当浓度达到30%时)。
料液Ⅰ效过Ⅱ效,Ⅱ效过Ⅲ效均采用压差自动过料工艺。
浓碱接收槽内浓碱经冷却沉清后采出的盐泥与Ⅲ效蒸发器采出的盐泥通过盐泥高位槽一起输入离心机分离。
离心机分离所得碱液及洗涤液流入母液槽,用母液泵打到母液中间槽,然后送入Ⅲ效蒸发器再蒸发。
离心机分离出来的盐泥加水化成盐水用盐水泵送回盐水工段。
由锅炉房来的生蒸汽送入Ⅰ效蒸发器加热室间接加热碱液。
其冷凝水流经螺旋预热器后流到蒸汽冷凝液贮槽,锅炉来的蒸汽压力为0.6~0.8MPa。
Ⅰ效蒸发器的二次蒸汽通入Ⅱ效蒸发器加热室,加热碱液,同样,其冷凝水流送至蒸汽冷凝液贮槽,冷凝液贮槽的热水用热水泵打至盐水工段化盐,本工段洗效、或供离心机岗位使用。
Ⅱ效的二次蒸汽通入Ⅲ效加热室加热碱液。
其冷凝水排入地沟或供化盐使用。
Ⅲ效蒸发器的二次蒸汽经旋流板除沫器分离夹带碱后,由大气冷凝器用水冲洗后一并排入下水池,并借此地Ⅲ效蒸发器内形成真空。
5.1.2双效生产流程简述二效生产流程与三效生产流程主要差别在于减少一台蒸发器,工艺控制指标的改变,其它部份流程与三效一样。
具体流程的改变就是减少三效中一、二效的其中一效,将另一效与末效构成双效生产流程。
5.2带控制点工艺流程图见附录A 6主要工艺指标和生产控制一览表7原材料及动力消耗定额8副产品本工段副产品回收盐水,含盐240~280克/升,含氢氧化钠4克/升以下,送本分厂盐水工段回收使用。
9主要设备一览表10蒸发岗位操作法10.1开车前准备工作10.1.1检查蒸发器内有无杂物和存水,检查压力表、真空表、温度计、油压系统、自动化仪表是否完好。
10.1.2检查加料管、蒸汽管、过料管、回流管、不凝性气体排出管、出料管、疏水管的所有阀门是否畅通好用,设备、管道、法兰、垫子等是否有泄漏现象。
10.1.3打开各蒸发器不凝性气体排气阀,关好Ⅲ效蒸发器取样阀门。
10.1.4打开各效疏水器进水、出水、平衡管阀门。
10.1.5合上自动控制系统电源。
起动油泵,检查各油压阀启闭是否灵活,并调整各油压阀处于关闭状态,然后将各蒸发器过料管、回流管的手动阀打开。
10.1.6检查加料泵、采盐泵、强制循环泵、输送冷凝水泵、管道泵是否完好。
10.1.7检查完毕,向调度汇报,由调度与动力分厂联系,通知其送水并准备送汽。
10.1.8开启水力喷射冷凝器真空上水管道泵,并检查真空度是否达到工艺指标。
10.2开车步骤10.2.1打开电解液贮槽出口阀,启动电解液加料泵,经进料油压阀向Ⅰ效蒸发器进料,达到规定液面。
10.2.2打开Ⅰ效蒸发器过料阀,过料给Ⅱ效蒸发器,达到规定液面。
10.2.3启动Ⅱ效采盐泵,关采盐器底阀和出料阀,开过料阀,过料给Ⅲ效蒸发器,达到规定液面后,停过料阀,开电解液回流阀。
10.2.4启动Ⅲ效采盐泵,关采盐器底阀和出料阀,开回流阀。
10.2.5启动Ⅱ效、Ⅲ效强制循环泵,观察运行是否正常。
10.2.6通知调度送汽,开启Ⅰ效主加热室加热蒸汽进汽阀,刚开汽时蒸汽进口压力不能超过0.1MPa,开汽后,待二楼蒸汽管排水阀排出的汽不带水后关闭排水阀,各效加热室不凝性气体不带水后关闭其排汽阀。
10.2.7待Ⅰ效蒸发器内物料沸腾后,可将蒸汽压力逐步提高到正常操作指标,进行正常操作。
在蒸汽压力逐步提高过程中要平稳地进行,严防振动。
10.2.8开启Ⅰ效副加热室加热蒸汽进汽阀,刚开汽时蒸汽进口压力不能超过0.1MPa,待关闭不凝汽排放阀后再调节开度,注意应保持副加热室温度始终低于主加热室温度。
10.3正常运行操作与控制10.3.1手动操作10.3.1.1保持各效蒸发器液面至规定指标。
10.3.1.2Ⅰ效沸腾后Ⅱ、Ⅲ效开始采盐,视碱液含盐多少(固液比约70~80%,呈乳白色)控制采盐器阀门开启度,清液送回Ⅱ效或Ⅲ效蒸发器。
10.3.1.3经常分析Ⅲ效碱液浓度,不断补充各效料液,保持液面稳定,当Ⅲ效碱液浓度达到415~420g/l时出料。
10.3.1.4出料时间以6分钟左右为佳,每次出料5m3,出料时不关采盐器底阀,打开Ⅲ效出料油压阀,关闭回流阀。
待出料完毕后,打开回流阀、关闭出料阀。
出料时要控制好各效的汽压。
若Ⅲ效蒸发器加热室压力过高,超过0.15Mpa时,暂时打开不凝性气体排汽阀,直到Ⅲ效蒸发器加料到规定位置,沸腾为止。
10.3.1.5Ⅱ、Ⅲ效采盐泵常开,旋液分离器出来的盐泥进盐泥高位槽,视碱液含盐多少控制旋液分离器出口阀开启度大小,清液分别送回Ⅱ、Ⅲ效蒸发器内。
10.3.1.6操作时要勤加料、过料,发现过料管、蒸发器锥底堵塞时,关闭需进料效加料阀,打开需压碱效阀门,然后关闭加料泵出口回流阀及进Ⅰ效加料阀。
发现需压碱效液面升高时,即证明已压通,打开加料泵出口回流阀,关闭压碱阀。
10.3.1.7操作中思想要高度集中,密切注意各工艺条件和控制点的变化,经常巡回检查各操作点和密封点,消除跑、冒、滴、漏。