冲压模具设计与制造弯曲模
冲压模具设计与制造

第一章 冲压模具设计与制造基础
内容简介:
本章讲述冲压模具设计与制造的基础知识。 涉及冲压和冲模概念、冲压工序和冲模分类;常见冲压设备及工作原理、选用原则;冲压成形基本原理和规律;冲压成形性能及常见冲压材料;模具材料种类、性能、选用原则及热处理方法;模具制造特点、模具零件加工方法及应用等 。
第一章 冲压模具设计与制造基础
一、冲压与冲模概念
1.基本概念(续)
冲压模具:
在冲压加工中,将材料加工成零件(或半成品)的一种特殊工艺装备,称为冲压模具(俗称冲模)。
第一章 冲压模具设计与制造基础
第一节 冲压成形与模具技术概述 冲压与冲模概念 基本概念(续) 合理的冲压工艺 先进的模具 高效的冲压设备 冲压生产的三要素
第一章 冲压模具设计与制造基础
多工位精密级进模
第一章 冲压模具设计与制造基础
冲压成形产品示例一——日常用品
第一章 冲压模具设计与制造基础
冲压成形产品示例二—— 高科技产品 汽车覆盖件 飞机蒙皮
第一章 冲压模具设计与制造基础
数控高速铣削加工
高效 、高精度 、高的表面质量 、可加工高硬材料
第一章 冲压模具设计与制造基础
五、冲压技术现状与发展方向(续)
第一节 冲压成形与模具技术概述
多品种、少批量,更新换代速度快
计算机技术、制造新技术
第一章 冲压模具设计与制造基础
(1)冲压成形理论及冲压工艺
加强理论研究,开展CAE技术应用。 开发和应用冲压新工艺。
2.冲压技术发展方向
满足产品开发在T(Time)、Q(Quality)、 C(Cost)、S(Service)、E(Environment)的要求。
1.我国冲压技术现状 技术落后、经济效益低。 主要原因:①冲压基础理论与成形工艺落后; ②模具标准化程度低; ③模具设计方法和手段、模具制造工艺及设备落后; ④模具专业化水平低。 所以,结果导致我国模具在寿命、效率、加工精度、生产周期等方面与先进工业发达国家的模具相比差距相当大。
《冲压模具设计与制造》课程教学大纲DOC

《冲压模具基础》课程教学大纲课程编号:课程英文译名:课内总学时:72学时学分:4。
5学分课程类别:必修课开课对象:汽车制造与装配技术专业执笔人:编写日期:一、课程性质、目的和任务《冲压模具设计与制造》是汽车制造及汽车整形专业的一门主干专业技术课,它是一门将冲压成形加工原理、冲压设备、冲压工艺、冲模设计与冲模制造有机融合,综合性和实践性较强的课程。
其目的是使学生了解冲压变形规律,认识冲压成形工艺方法,冲压模具结构,冲压模具制造方法与手段,掌握冲压模具设计与计算方法,掌握冲压工艺与模具设计方法,冲压模具制造工艺方法,能进行中等冲压零件的冲压工艺编制,冲模设计与冲模制造工艺编制,并培养学生发现问题、分析问题和解决问题的能力,培养学生逻辑思维能力,为毕业设计及毕业以后从事专业工作打下必要的基础。
二、教学基本要求本课程是冲压模具设计与计算,冲压模具结构,模具制造工艺方法为重点。
学外本课程应达到以下基本要求:1、能应用冲压变形理论,分析中等复杂冲压件变形特点,制定合理冲压工艺规程的能力。
2、协调冲压设备与模具的关系,选择冲压设备的能力。
3、熟悉掌握冲模设计计算方法,具备中等复杂冲模结构选择和设计的能力,所设计的冲模应工作可行、操作方便、便于加工和装配,技术经济性好。
4、具备正确选择冲压模具加工方法,制定中等复杂冲模制造工艺和装配工艺的能力.5、初步具备进行多工位级进模设计和制造的能力。
6、初步具备进行分析和处理试模过程中产生的有关技术问题的能力。
三、教学内容及要求:第1章冲压模具设计与制造基础1.1 冲压成形与模具技术概述掌握冲压与冲模概念;冲压工序的分类;冲模的分类;冲模设计与制造的要求;了解冲压现状与发展方向。
1.2 冲压设备及选用了解常见冲压设备;掌握冲压设备的选用;模具的安装。
1.3 冲压变形理论基础掌握塑性变形的概念;理解塑性力学基础;掌握金属塑性变形的一些基本规律;冲压材料及其冲压成形性能.1.4 模具材料选用掌握冲压对模具材料的要求;冲模材料的选用原则;冲模常见材料及热处理要求。
模具设计与制造第6章弯曲工艺与模具设计

06
总结与展望
弯曲工艺与模具设计的现状与挑战
现状
随着制造业的快速发展,弯曲工艺与模具设计在产品制造中占据重要地位。目前,弯曲工艺与模具设 计已经取得了长足进步,能够满足多种复杂形状的加工需求。
挑战
然而,在弯曲工艺与模具设计过程中,仍存在一些挑战,如高精度控制、复杂曲面加工、高效自动化 等方面的问题。
未来发展方向与技术前沿
柔性制造技术
随着个性化需求的增加,柔性制造技术将成为未 来发展的重点。通过柔性制造技术,可以实现快 速、高效、个性化的产品制造,提高生产效率和 降低成本。
增材制造技术
增材制造技术是一种基于数字模型的快速成型技 术,能够实现复杂形状的高精度加工。未来,增 材制造技术有望在弯曲工艺与模具设计中发挥更 大的作用。
模具材料的选择蚀性等。
常用材料
碳素工具钢、合金工具钢、硬质合金、铸铁等。
材料处理
热处理、表面处理等。
模具设计的流程与方法
设计流程
明确设计任务→收集设计资料→设计 出图→审查→修改。
设计方法
经验设计法、解析设计法、计算机辅 助设计法等。
04
弯曲工艺与模具设计的关系
THANK YOU
模具设计对弯曲工艺的影响
模具结构
模具的结构对弯曲工艺的实施具 有重要影响,合理的模具结构可 以提高弯曲效率并降低不良品率。
模具材料
模具材料的选取直接影响弯曲工艺 的效果,选用高强度、耐磨和耐热 的材料可以提高模具的使用寿命和 弯曲质量。
冷却系统
模具中的冷却系统对于控制弯曲过 程中的温度至关重要,合理的冷却 系统设计可以减少热应力,提高产 品质量。
02
弯曲工艺的基本原理
弯曲变形的过程与特点
冲压模具设计与制作配套案例库:案例09 冲模结构与设计

案例九冲模结构与设计冲模是冲压生产的主要工艺设备,冲模结构设计对冲压件品质、生产率及经济效益影响很大。
因此,了解冲模结构,研究和提高冲模的各项技术指标,对冲模设计和发展冲压技术是十分必要的。
8. 1冲模分类及其特点按不同的特征对冲模进行分类,其分类方法主要有:(1)按冲压工序性质可分为冲裁模、拉深模、翻边模、胀形模、弯曲模……。
习惯上把冲裁模当作所有分离工序模的总称,包括落料模、冲孔模、切断模、切边模、半精冲模、精冲模及整修模等。
(2)按冲压工序的组合方式可分为单工序模、级进模和复合模。
1)单工序模在压力机一次冲压行程内,完成一道冲压工序的模具。
2)级进模在压力机一次冲程内,在模具不同工位上完成多道冲压工序的模具。
3)复合模在压力机一次行程内,在模具一个工位上完成两道以上冲压工序的模具。
(4)按进料、出件及排除废料方式可分为手动模、半自动模、自动模。
(5)按模具零件组合通用程度可分为专用模(包括简易模)和组合冲模。
(6)按凸、凹模材料可分钢模、硬质合金模、钢结硬质合金模、聚氨酯模、低熔点合金模等。
(7)按模具轮廓尺寸可分为大型模、中型模、小型模等。
8.2冲模零部件分类及功能各种类型冲模复杂程度不同,所含零件各有差异,但根据其作用都可归纳为如下五种类型:(1)工作零件工作零件直接使被加工材料变形、分离,而成为工件,如凸模、凹模、凸凹模等。
(2)定位零件定位零件控制条料的送进方向和送料进距,确保条料在冲模中的正确位置,有挡料销、导正销、导尺、定位销、定位板、导料板、侧压板和侧刃等。
(3)压料、卸料与顶料零件压料、卸料与顶料零件包括冲裁模的卸料板、顶出器、废料切刀、拉深模中的压边圈等。
卸料与顶料零件在冲压完毕后,将工件或废料从模具中排出,以使下次冲压工序顺利进行;拉深模中的压边圈的作用是防止板料毛坯发生失稳起皱。
(4)导向零件导向零件的作用是保证上模对下模相对运动精确导向,使凸模与凹模之间保持均匀的间隙,提高冲压件品质。
冲压工艺流程
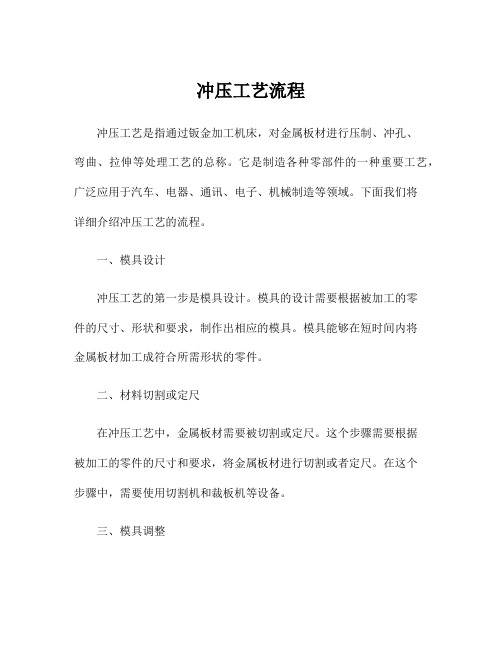
冲压工艺流程冲压工艺是指通过钣金加工机床,对金属板材进行压制、冲孔、弯曲、拉伸等处理工艺的总称。
它是制造各种零部件的一种重要工艺,广泛应用于汽车、电器、通讯、电子、机械制造等领域。
下面我们将详细介绍冲压工艺的流程。
一、模具设计冲压工艺的第一步是模具设计。
模具的设计需要根据被加工的零件的尺寸、形状和要求,制作出相应的模具。
模具能够在短时间内将金属板材加工成符合所需形状的零件。
二、材料切割或定尺在冲压工艺中,金属板材需要被切割或定尺。
这个步骤需要根据被加工的零件的尺寸和要求,将金属板材进行切割或者定尺。
在这个步骤中,需要使用切割机和裁板机等设备。
三、模具调整在模具设计完成之后,需要对模具进行调整。
模具调整时需要将其与机床进行配合,根据加工要求将模具准确、平整地安装在机床上。
四、精确定位精确定位是冲压工艺流程中非常重要的一步。
在精确定位时要保证零件的位置准确无误,这可以通过机床的数控系统进行自动定位。
五、冲压加工在进行冲压加工时,需要将模具配合机床进行操作。
机床会按照加工好的程序进行操作,从而将金属板材加工成符合要求的零部件。
六、去毛刺在冲压加工完成之后,需要对加工出来的零件进行去毛刺处理。
去毛刺需要使用专门的设备,对零件表面进行抛丸或者机械去毛刺处理。
七、品质检测品质检测是冲压工艺中最后一个步骤。
在品质检测过程中,要对加工好的零件进行检查、测试,以确保其达到设计要求,是否存在问题需要及时进行处理。
总之,冲压工艺是一项非常复杂的加工技术,需要配合各种设备、技术手段和专业知识。
只有经过良好的模具设计、机床操作和后续处理等流程,才能够生产出高质量的零部件,为整个制造业提供优越的材料和零部件。
弯曲模具的基本原理
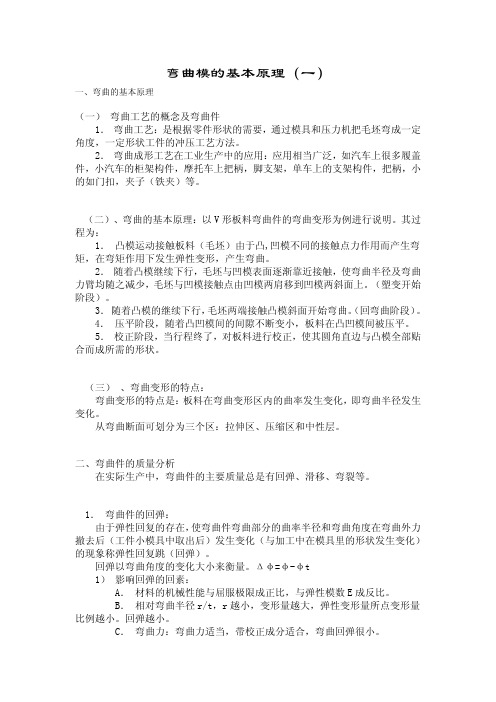
弯曲模的基本原理(一)一、弯曲的基本原理(一) 弯曲工艺的概念及弯曲件1. 弯曲工艺:是根据零件形状的需要,通过模具和压力机把毛坯弯成一定角度,一定形状工件的冲压工艺方法。
2. 弯曲成形工艺在工业生产中的应用:应用相当广泛,如汽车上很多履盖件,小汽车的柜架构件,摩托车上把柄,脚支架,单车上的支架构件,把柄,小的如门扣,夹子(铁夹)等。
(二)、弯曲的基本原理:以V形板料弯曲件的弯曲变形为例进行说明。
其过程为:1. 凸模运动接触板料(毛坯)由于凸,凹模不同的接触点力作用而产生弯矩,在弯矩作用下发生弹性变形,产生弯曲。
2. 随着凸模继续下行,毛坯与凹模表面逐渐靠近接触,使弯曲半径及弯曲力臂均随之减少,毛坯与凹模接触点由凹模两肩移到凹模两斜面上。
(塑变开始阶段)。
3. 随着凸模的继续下行,毛坯两端接触凸模斜面开始弯曲。
(回弯曲阶段)。
4. 压平阶段,随着凸凹模间的间隙不断变小,板料在凸凹模间被压平。
5. 校正阶段,当行程终了,对板料进行校正,使其圆角直边与凸模全部贴合而成所需的形状。
(三) 、弯曲变形的特点:弯曲变形的特点是:板料在弯曲变形区内的曲率发生变化,即弯曲半径发生变化。
从弯曲断面可划分为三个区:拉伸区、压缩区和中性层。
二、弯曲件的质量分析在实际生产中,弯曲件的主要质量总是有回弹、滑移、弯裂等。
1. 弯曲件的回弹:由于弹性回复的存在,使弯曲件弯曲部分的曲率半径和弯曲角度在弯曲外力撤去后(工件小模具中取出后)发生变化(与加工中在模具里的形状发生变化)的现象称弹性回复跳(回弹)。
回弹以弯曲角度的变化大小来衡量。
Δφ=φ-φt1) 影响回弹的回素:A. 材料的机械性能与屈服极限成正比,与弹性模数E成反比。
B. 相对弯曲半径r/t,r越小,变形量越大,弹性变形量所点变形量比例越小。
回弹越小。
C. 弯曲力:弯曲力适当,带校正成分适合,弯曲回弹很小。
D. 磨擦与间隙:磨擦越大,变形区拉应力大,回弹小。
凸、凹模之间隙小,磨擦大,校正力大,回弹小。
冲压模具设计与制造-冲模结构及设计
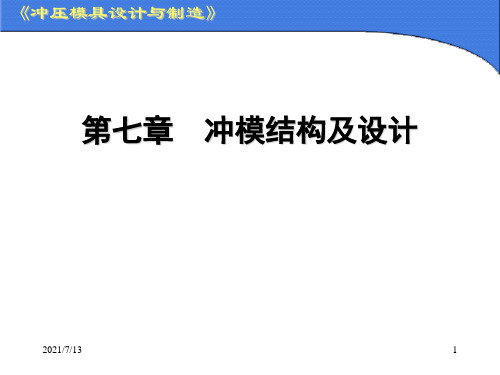
§7.2 冲模主要零件设计
七.连接与固定零件
1.固定板
将凸模或凹模按一定相对位置压 入固定后,作为一个整体安装在上 模座或下模座上。(H7/m6、H7/n6)
2.垫板
直接承受凸模的压力,以降低模 座所受的单位压力,防止模座被局 部压陷,
2021/7/13
37
§7.2 冲模主要零件设计
3.模柄
作为上模与压力机滑块连接的零件。 ① 与压力机滑块上的模柄孔正确配合,安装可靠; ② 与上模正确而可靠连接(H7/m6、H7/h6) 。
2021/7/13Fra bibliotek14§7.2 冲模主要零件设计
2021/7/13
15
§7.2 冲模主要零件设计
(2) 凹模刃口的结构类型
2021/7/13
16
§7.2 冲模主要零件设计
a. 直壁刃口 ① 刃口强度较高,修磨后刃口尺寸不变。 ② 凹模内易积存废料或冲裁件,尤其间隙较小时,刃口直壁
部分磨损较快。 ③ 用于冲裁形状复杂或精度要求较高的零件。
2021/7/13
10
§7.2 冲模主要零件设计
b. 非圆形凸模
a) 台肩固定
b) 铆接固定
2021/7/13
c) 直通式凸模
11
§7.2 冲模主要零件设计
c. 大、中型凸模 镶拼式凸模不但节约贵重的模具钢,而且减少锻造、热处理和 机械加工的困难。
2021/7/13
12
§7.2 冲模主要零件设计
工艺结构部分
定位零件
6.定位销(定位板)
7.侧压板
8.侧刃
9.卸料板
压、卸料及出件零件
10.压料板(压边圈) 11.顶件器
12.推件器
简述冲压弯曲成形的工艺过程及基本特点

1. 设计模具:冲压弯曲成形的第一步是设计模具。
模具根据产品的形状和尺寸要求进行设计,通常包括冲头、模座、导向柱、顶针等部件。
模具的设计要考虑产品的材料特性、成形工艺和使用要求。
2. 材料准备:冲压弯曲成形需要使用金属材料,常见的包括钢板、铝板、铜板等。
在成形之前需要对材料进行切割、整形和表面处理,以保证成形后产品的质量和外观要求。
3. 冲裁:冲裁是冲压成形的第一步,通过模具的冲头和模座对材料进行切割,得到所需的基本形状。
4. 弯曲:在冲裁完成后,需要对材料进行弯曲成形,通过模具的顶针和模具座将材料弯曲成产品需要的形状。
5. 尾料处理:在冲压弯曲成形之后,通常会有一些尾料产生,需要对这些尾料进行处理,包括回收利用和废弃处理等。
6. 检验和调整:需要对冲压弯曲成形的产品进行检验,确保产品的质量和尺寸达到要求。
同时也需要对模具和成形工艺进行调整,以满足产品的生产要求。
1. 高效率:冲压弯曲成形是一种批量生产的工艺,可以快速地完成产品的成形,提高生产效率。
2. 精度高:冲压弯曲成形可以保证产品的尺寸和形状精度,有利于产品的装配和使用。
3. 适用范围广:冲压弯曲成形可以适用于各种金属材料,成形的产品形状也可以多样化,适用范围广泛。
4. 成本低:相比其他成形工艺,冲压弯曲成形的模具制造成本低,适合批量生产和大规模生产。
5. 自动化程度高:冲压弯曲成形可以实现自动化生产,降低劳动强度,提高生产效率和一致性。
6. 适应性强:冲压弯曲成形可以适应各种复杂的产品形状和结构要求,满足不同行业的生产需求。
通过以上内容的介绍,我们可以了解到冲压弯曲成形工艺的基本过程和特点。
这种成形工艺在工业生产中有着广泛的应用,能够满足各种产品的生产需求,并且具有高效率、高精度、低成本和高自动化程度的特点。
随着科技的不断发展,冲压弯曲成形工艺将会在未来的生产中发挥越来越重要的作用。
冲压弯曲成形是金属加工中常用的一种技术,在各行业都有着广泛的应用。
冲压模具设计开题报告

毕业设计开题报告题目:冲压工艺分析与弯曲冲孔模具的设计院系:三峡大学机械与材料学院专业:机械设计制造及其自动化学生:学号:指导老师:三峡大学机械与材料学院冲压工艺分析与弯曲冲孔模具的设计开题报告一、课题的来源课题来源于生产实际,探讨冲压加工中较常见零件的工艺方法和结构设计。
课题涉及知识面较广,且设计要求较高,对学生的设计能力,特别是思考能力是一个很好的锻炼。
课题研究内容包括机械工程学科的力学,材料学,机械原理,机械设计,公差与互换性,机械制造工艺等知识,特别锻炼学生规范性设计的能力。
使学生能得到全面的锻炼。
课题要求学生具备较强的机构设计能力和创新能力,对学生是一个挑战。
课题为典型的机械设计类课题,涉及机械知识全面,与工程机械专业方向结合紧密。
二、选题的现实意义和理论意义冲压加工是现代机械制造业中先进高效的加工方法之一。
它是利用安装在压力机上的模具,在常温或加热的条件下对板材施加压力使其变形和分解,从而获得一定形状、尺寸的零件的加工方法。
因为它主要用于加工板料零件,所以又称板料冲压。
冲压加工的特点如下:(1). 借助压力机的压力,利用模具能获得壁薄、质量轻、刚性好、形状复杂的零件,这些零件用其他的方法难以加工甚至无法加工;(2). 冲压加工的零件精度高、尺寸稳定,具有良好的互换性;(3).冲压加工是少、无切削加工的一种,部分零件冲压直接成形,大部分无需任何再加工,材料利用率高,达85%以上;(5.)操作简单,便于组织生产和管理。
冲压加工的缺点是模具制造的周期长,制造成本高,不适于单件小批量生产;其次,冲压加工多用机械压力机,由于滑块往复运动快,大量手工操作,劳动强度较大,易发生事故,安全生产与管理要求高,须采用必要的安全技术措施来保证。
冲压加工的应用十分广泛,不仅可以加工金属材料,而且可以加工非金属材料。
在现代制造业,比如汽车、拖拉机、农业机械、电机、电器、仪表、化工容器、玩具以及日常生活用品的生产方面,都占有十分重要的地位。
模具设计第3章弯曲工艺与弯曲模课件

b/t<3窄板弯曲,断面产生了 畸变 ,外窄内宽
3.1.4 弯曲件的结构工艺性
弯曲件的结构工艺性是指弯曲零件的形状、 尺寸、精度、材料以及技术要求等是否符合弯 曲加工的工艺要求。具有良好工艺性的弯曲件, 能简化弯曲的工艺过程及模具结构,提高工件 的质量。
1. 弯曲件的形状 弯曲件形状对称,对应r 相等
播放动画
1-顶杆 2-定位钉 3-模柄 4-凸模 5-凹模 6-下模座
3. L形件弯曲 适用于两直边长度相差较大的单角弯曲件
a)竖边无校正
b)竖边可校正
L形件弯曲
4.复杂零件 多次V形弯曲制造复杂零件举例
3.2.2 U形件弯曲模
1.U形件弯曲模的一般结构形式
U 形 件 弯 曲 模
1.凸模 2.凹模 3.弹簧 4.凸模活动镶块 5.凹模活动镶块 6.定位销 7.转轴 8.顶板 9.凹模活动镶块
弯曲半径r>0.5t: 按中性层不变原理,坯料总长度应等于弯曲 件直线部分和圆弧段长度之和,即:
提问:下面的弯曲件展开长度如何计算?
L
l1
l2
l3
π α1 180
(r1
xt
)
π α2 180
S / E 越大,回弹越大。
E1>E2
1 2
.
1 2
图a)
E3=E4
3 4
3 4
图b)
材料的力学性能对回弹值的影响 1、3-退火软钢 2-软锰黄铜 4-经冷变形硬化的软钢
应尽量选择屈服极限小、n值小的材料以获得 形状规则、尺寸精确的弯曲件。
(2)相对弯曲半径r/t r/t越小,变形程度越大,回弹量减小。
例:1mm厚铝板、65Mn板,弯曲时易裂,退火后 再弯,则弯曲正常。
弯曲与弯曲模具设计

二、弯曲件的工艺计算
2.弯曲力的计算
(1)自由弯曲力对于V形件,有
F自
0.6kbt 2 b
rt
对于U形件,有
F自
0.7kbt 2 b
rt
(2)校正弯曲力如果弯曲件在冲压行程结束时受到模具的校正
(见图3-27)
上一页 下一页
第四节 弯曲件的工艺特性及工艺计 算
二、弯曲件的工艺计算
(3)顶件力或压料力
上一页 下一页
第四节 弯曲件的工艺特性及工艺计 算
一、弯曲件的工艺性
(6)增添连接带和定位工艺孔 如图3-22所示。 (7尺寸标注 尺寸标注对弯曲件的工艺性有很大的影响。 如图3-23所示。
上一页 下一页
第四节 弯曲件的工艺特性及工艺计 算
二、弯曲件的工艺计算
1.弯曲件展开长度的确定
第三章 弯曲与弯曲模具设计
第一节 弯曲技术概述 第二节 弯曲变形过程分析 第三节 弯曲件坯料尺寸的计算 第四节 弯曲件的工艺特性及工艺计算 第五节 弯曲件的工序安排 第六节 弯曲模典型结构及结构设计
第一节 弯曲技术概述
弯曲是利用压力使金属板料、管料、棒料或型材在模具中弯 成一定曲率、一定角度和形状的变形工序。弯曲工艺在冲压 生产中占有很大的比例,应用相当广泛,如汽车纵梁、电器 仪表壳体、支架、铰链等,都是用弯曲方法成型的。
所示为V形件弯曲的变形过程。 2.弯曲变形特点 为了分析板料弯曲变形的规律,将试验用的长方形板料的 侧面画成正方形网格,如图3-4(a)所示,然后弯曲,观察其
变形特点,弯曲后情况如图3-4(b)所示。
下一页
第二节 弯曲变形过程分析
一、弯曲的变形特点
(1)变形区主要在弯曲件的圆角部分,圆角区内的正方形网 格变成厂扇形。
冲压模具设计与制造-弯曲工艺与模具设计
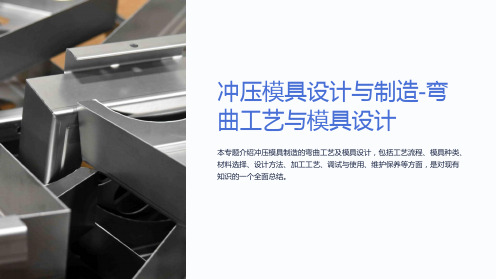
应用场景
广泛应用于手机、汽车、电视机、 计算机等产品的制造中
弯曲工艺的应用场景
个人消费品
行李车、儿童座椅、自行车座等
建筑领域
门窗、钢结构等
工业制造
吊车臂、桥架、挖掘机臂等
汽车领域
汽车车身、排气管、离合器等
弯曲工艺的优缺点
优点
• 工艺简单 • 生产效率高 • 生产成本低 • 形状可变
缺点
• 成型重量限制 • 无法实现非线性弯曲 • 弯曲角度存在最小值 • 弯曲半径限制较大
3 材料
应选择强度和韧性都较高的材料,同时应考 虑在操作过程中的磨耗性和修复性
4 可维修性
模具设计应考虑寿命和易损件,易于维修和 更换
弯曲模具的分类
按形式分类
• 单工位模 • 连续模 • 中空模 • 异形模
按应用分类
• 汽车工业专用模 • 造船业用弯管模 • 机床上安装的弯管模 • 家电制造业弯头型号模
Hale Waihona Puke 弯曲模具的设计方法常见方法
手工模拟、数值模拟、经验规律法、模拟仿真
设计步骤
1. 确定工件的几何形状 2. 计算弯曲力矩和弯曲角度 3. 准备模具的设计图纸 4. 优化模具的几何尺寸
弯曲模具对模具的要求
1 强度
模具应具有足够的强度来承受弯曲力矩和弯 曲压力的作用
2 精度
模具必须保证成型精度的要求,例如加工定 位孔及精度要求达到零误差
弯曲工艺的材料选择
常见材料
铝合金、钢材、不锈钢、镁合金 等
制造工艺
冷拔可广泛应用,热轧用于钢材 弯曲时的复合成型
板厚选择
在保证预算的前提下,尽量选择 薄板
弯曲模具的构造和原理
1
弯曲模具课程设计
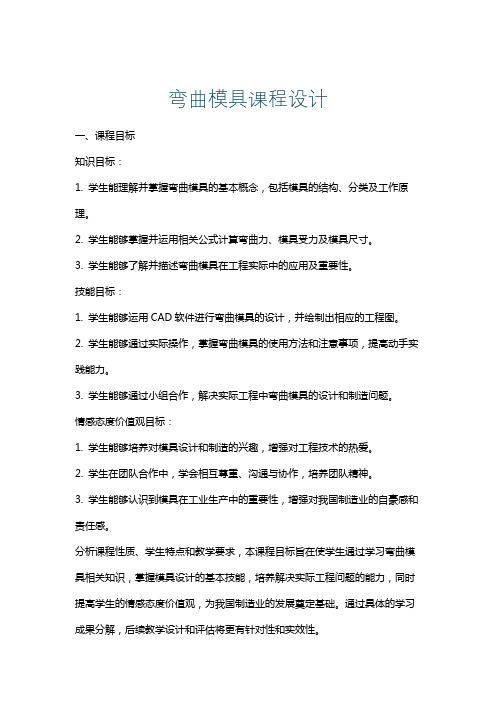
弯曲模具课程设计一、课程目标知识目标:1. 学生能理解并掌握弯曲模具的基本概念,包括模具的结构、分类及工作原理。
2. 学生能够掌握并运用相关公式计算弯曲力、模具受力及模具尺寸。
3. 学生能够了解并描述弯曲模具在工程实际中的应用及重要性。
技能目标:1. 学生能够运用CAD软件进行弯曲模具的设计,并绘制出相应的工程图。
2. 学生能够通过实际操作,掌握弯曲模具的使用方法和注意事项,提高动手实践能力。
3. 学生能够通过小组合作,解决实际工程中弯曲模具的设计和制造问题。
情感态度价值观目标:1. 学生能够培养对模具设计和制造的兴趣,增强对工程技术的热爱。
2. 学生在团队合作中,学会相互尊重、沟通与协作,培养团队精神。
3. 学生能够认识到模具在工业生产中的重要性,增强对我国制造业的自豪感和责任感。
分析课程性质、学生特点和教学要求,本课程目标旨在使学生通过学习弯曲模具相关知识,掌握模具设计的基本技能,培养解决实际工程问题的能力,同时提高学生的情感态度价值观,为我国制造业的发展奠定基础。
通过具体的学习成果分解,后续教学设计和评估将更有针对性和实效性。
二、教学内容1. 弯曲模具基本概念:包括模具的定义、结构、分类及工作原理,对应教材第一章内容。
- 模具的结构与分类- 模具工作原理及力学分析2. 弯曲模具设计计算:涉及弯曲力、模具受力及模具尺寸的计算,对应教材第二章内容。
- 弯曲力的计算方法- 模具受力的分析- 模具尺寸的确定3. 弯曲模具设计实践:运用CAD软件进行模具设计,对应教材第三章内容。
- CAD软件的基本操作- 弯曲模具设计流程及技巧- 工程图的绘制方法4. 弯曲模具应用与制造:介绍弯曲模具在工程实际中的应用及制造过程,对应教材第四章内容。
- 模具在工业生产中的应用案例- 模具制造工艺及注意事项- 模具的安装与调试5. 小组合作与展示:学生分组进行弯曲模具设计和制造,展示成果,对应教材第五章内容。
- 团队合作与分工- 设计与制造过程记录- 成果展示与评价根据以上教学内容,制定详细的教学大纲,明确教学内容的安排和进度,确保教学活动的科学性和系统性。
冲压工艺及模具设计(3篇)

第1篇一、引言冲压工艺是一种常见的金属成形工艺,广泛应用于汽车、家电、电子、航空等行业。
冲压工艺具有生产效率高、成本低、精度高、尺寸稳定性好等优点。
模具是冲压工艺中的关键设备,其设计质量直接影响到冲压产品的质量和生产效率。
本文将对冲压工艺及模具设计进行简要介绍。
二、冲压工艺概述1. 冲压工艺原理冲压工艺是利用模具对金属板材施加压力,使其产生塑性变形,从而获得所需形状、尺寸和性能的零件。
冲压工艺的基本原理是金属的塑性变形,即金属在受到外力作用时,产生塑性变形而不破坏其连续性的过程。
2. 冲压工艺分类(1)拉深:将平板金属沿模具凹模形状变形,形成空心或实心零件的过程。
(2)成形:将平板金属沿模具凸模形状变形,形成具有一定形状的零件的过程。
(3)剪切:将平板金属沿剪切线剪切成一定形状和尺寸的零件的过程。
(4)弯曲:将平板金属沿模具凸模形状弯曲,形成具有一定角度的零件的过程。
三、模具设计概述1. 模具设计原则(1)满足产品精度和尺寸要求:模具设计应保证冲压产品具有高精度和尺寸稳定性。
(2)提高生产效率:模具设计应优化工艺流程,减少不必要的加工步骤,提高生产效率。
(3)降低生产成本:模具设计应选用合适的材料,降低模具成本。
(4)确保模具寿命:模具设计应考虑模具的耐磨性、耐腐蚀性等性能,延长模具使用寿命。
2. 模具设计步骤(1)产品分析:分析产品的形状、尺寸、材料等,确定模具设计的基本要求。
(2)工艺分析:根据产品形状和尺寸,确定冲压工艺类型,如拉深、成形、剪切、弯曲等。
(3)模具结构设计:根据工艺要求,设计模具结构,包括凸模、凹模、导向装置、压边装置等。
(4)模具零件设计:根据模具结构,设计模具零件,如凸模、凹模、导向装置、压边装置等。
(5)模具加工:根据模具零件设计,进行模具加工。
(6)模具调试:完成模具加工后,进行模具调试,确保模具性能符合要求。
四、冲压工艺及模具设计要点1. 冲压工艺要点(1)合理选择材料:根据产品形状、尺寸、性能要求,选择合适的金属材料。
- 1、下载文档前请自行甄别文档内容的完整性,平台不提供额外的编辑、内容补充、找答案等附加服务。
- 2、"仅部分预览"的文档,不可在线预览部分如存在完整性等问题,可反馈申请退款(可完整预览的文档不适用该条件!)。
- 3、如文档侵犯您的权益,请联系客服反馈,我们会尽快为您处理(人工客服工作时间:9:00-18:30)。
121
图 3.1.2弯曲件的弯曲方法
1-下模板 2、5-圆柱销 3-弯曲凹模 4-弯曲凸模 6-模柄 7-顶杆 8、9-螺钉 10-定位板 图 3.1.3V形件弯曲模
V形弯曲是最基本的弯曲变形,任何复杂弯曲都可看成是由多个 V形弯曲组成。所以我们以 V形弯曲为代表分析弯曲变形过程。
弯曲回弹的表现形式有两个方面(图 3.3.1):
130
1.曲率减小
图 3.3.1 弯曲后的回弹
2.弯曲中心角减小
1、3-退火软钢 2-软锰黄铜 4-经冷变形硬化的软钢 图 3.3.2 材料的力学性能对回弹值的影响
131
3.弯曲中心角 a a越大,变形区的长度越长,回弹积累值也越大,故回弹角 越大。 4.弯曲方式及弯曲模 在无底凹模内作自由弯曲时(图 3.3.4),回弹最大。在有底凹模内作校正弯曲时(图 3.1.3), 回弹较小。其原因之一是:从坯料直边部分的回弹来看,由于凹模 V形面对坯料限制作用,当 坯料与凸模三点接触后,随凸模的继续下压,坯料的直边部分则向与以前相反的方向变形,弯 曲终了时可以使产生了一定曲率的直边重新压平并与凸模完全贴合。卸载后弯曲件直边部分的 回弹方向是朝向 V形闭合方向(负回弹)。而圆角部分的回弹方向是朝向 V形张开方向(正回 弹),两者回弹方向相反。原因之二是:从圆角部分的回弹来看,由于板料受凸、凹模压缩的 作用,不仅弯曲变形外区的拉应力有所减小,而且在外区中性层附近还出现和内区同号的压缩 应力,随着校正力的增加,压应力区向板材的外表面逐步扩展,致使板料的全部或大部分断面 均出现压缩应力,于是圆角部分的内、外区回弹方向一致,故校正弯曲圆角部分的回弹比自由 弯曲时大为减小。综上所述,校正弯曲时圆角部分的较小正回弹与直边部分负回弹的抵销 ,回 弹可能出现正、零或是负三种情况。 在弯曲 U形件时,凸、凹模之间的间隙对回弹有较大的影响。间隙越大,回弹角也就越大, 如图 3.3.5所示。
(4)对于 U形件弯曲,减小回弹常用的方法还有:当相对弯曲半径较小时可采取增加背压 的方法(图 3.3.12b);当相对弯曲半径较大时,可采取将凸模端面和顶板表面作成一定曲率的 弧形(图 3.3.13a)。这两种方法的实质都是使底部产生的负回弹和角部产生的正回弹互相补偿。 另一种克服回弹的有效方法是采用摆动式凹模,而凸模侧壁应有补偿回弹角 (图 3.3.13b), 当材料厚度负偏差较大时,可设计成凸、凹模间隙可调的弯曲模(图 3.3.13c)。
图 3.2.6 坯料弯曲变形区内切向应为的分布
126
1.中性层的内移
图 3.2.7 弯曲后的翘曲
图 3.2.8 型材、管材弯曲后的剖面畸变
127
1.影响最小弯曲半径的因素 (1)材料的力学性能 材料的塑性越好,塑性变形的稳定性越强(均匀伸长率 越大),许可的最小弯曲半径就 越小。 (2)材料表面和侧面的质量 板料表面和侧面(剪切断面)的质量差时,容易造成应力集中并降低塑性变形的稳定性, 使材料过早地破坏。对于冲裁或剪裁坯料,若未经退火,由于切断的面存在冷变形硬化层,就 会使材料塑性降低。在上述的情况下应选用较大的最小弯曲半径。 (3)弯曲线的方向
图 3.2.1为 V形弯曲时板材的受力情况。在板材 A处,凸模 1施加外力 2F,在凹模 2支承 点 B处,则产生反力并与这外力构成了弯曲力矩 M=F*L,该弯曲力矩使板材产生—凹模 图 3.2.1V形弯曲板材受力情况
图 3.2.2 弯曲过程
a)弯曲前 b)弯曲后
3.2.3 弯曲前坐标网格的变化
弯曲是将板料、型材、管材或棒料等按设计要求弯成一定的角度和一定的曲率,形成所需 形状零件的冲压工序。它属于成形工序,是冲压基本工序之一,在冲压零件生产中应用较普遍, 图 3.1.1是用弯曲方法加工一些典型零件。
图 3.1.1弯曲成形典型零件 根据所使用的工具与设备的不同,弯曲方法可分为在压力机上利用模具进行的压弯以及在 专用弯曲设备上进行的折弯、滚弯、拉弯等,如图 3.1.2所示。各种弯曲方法尽管所用设备与 工具不同,但其变形过程及特点有共同规律。本章将主要介绍在生产中应用最多的压弯工艺与 弯曲模设计。 弯曲所使用的模具叫弯曲模,它是弯曲过程必不可少的工艺装备。图 3.1.3是一副常见的 V形件弯曲模。弯曲开始前,先将平板毛坯放入定位板 10中定位,然后凸模 4下行,凸模与顶 杆 7将板材压住(可防止板材在弯曲过程中发生偏移),实施弯曲,直至板材与凸模、凹模 3 完全贴紧,最后开模,V形件被顶杆顶出。
(2)对冷作硬化的材料须先退火,使其屈服点 降低。对回弹较大的材料,必要时可采用加热 弯曲。 (3)弯曲相对弯曲半径很大的弯曲件时,由于变形程度很小,变形区横截面大部分或全部处于 弹性变形状态,回弹很大,甚至根本无法成形,这时可采用拉弯工艺。拉弯用模具如图 3.3.9 所示。拉弯特点是在弯曲之前先使坯料承受一定的拉伸应力,其数值使坯料截面内的应力稍大 于材料的屈服强度。随后在拉力作用的同时进行弯曲。图 3.3.10所示为工件在拉弯曲中沿截面 高度的应变分布。图 3.3.10a为拉伸时的应变;图 3.3.10b为普通弯曲时的应变;图 3.3.10c 为拉弯总的合成应变;图 3.3.10d为卸载时的应变;图 3.3.10e为最后永久变形。从图 3.3.10d 可看出,拉弯卸载时坯料内、外区弹复方向一致,故大大减小工件的回弹。所以拉弯主要用于 长度和曲率半径都比较大的零件。
128
图 3.2.9 纤维方向对 的影响
图 3.2.10 开槽后进行弯曲
注: 1.当弯曲线与纤维方向成一定角度时,可采用垂直和平行纤维方向二者的中间值。 2.在冲裁或剪切后没有退火的毛坯弯曲时,应作为硬化的金属选用。 3.弯曲时应使有毛刺的一边处于弯角的内侧。 4.表中 t为板料厚度。
129
与所有塑性变形一样,塑性弯曲时伴随有弹性变形,当外载荷去除后,塑性变形保留下来,而弹性变形 会完全消失,使弯曲件的形状和尺寸发生变化而与模具尺寸不一致,这种现象叫回弹。由于弯曲时内、 外区切向应力方向不一致,因而弹性回复方向也相反,即外区弹性缩短而内区弹性伸长,这种反向的弹 性回复加剧了工件形状和尺寸的改变。所以与其它变形工序相比,弯曲过程的回弹现象是一个影响弯曲 件精度的重要问题,弯曲工艺与弯曲模设计时应认真考虑。
图 3.4.1 中性层位置
1.圆角半径 r>0.5t的弯曲件
2.圆角半径 r<0.5t的弯曲件 对于 r<0.5t的弯曲件,由于弯曲变形时不仅制件的圆角变形区产生严重变薄,而且与其相邻的直边 部分也产生变薄,故应按变形前后体积不变条件确定坯料长度。通常采用表 3.4.2所列经验公式计算。
图 3.4.2 r>0.5t的弯曲
135
图 3.3.11 克服回弹措施Ⅰ
图 3.3.12 克服回弹措施Ⅱ
图 3.3.13 克服回弹措施Ⅲ
(5)在弯曲件直边端部纵向加压,使弯曲变形的内、外区都成为压应力而减少回弹,可得 到精确的弯边高度(图 3.3.14)。
(6)用橡胶或聚氨酯代替刚性金属凹模能减小回弹。通过调节凸模压入橡胶或聚氨酯凹模 的深度,控制弯曲力的大小,以获得满足精度要求的弯曲件(图 3.3.15)。
1.应变状态
a)窄板(B/t3)b)宽板(B/t3) 图 3.2.4 弯曲变形区的横截面变化情况
从应力状态来看,窄板弯曲时的应力状态是平面的,宽板则是立体的。 综上所述,将板料弯曲时的应力应变状态归纳于表 3.2.1。
124
125
a)弹性弯曲 b)弹-塑性弯曲 c)纯塑性弯曲
图 3.2.5 弯曲半径和弯曲中心角
图 3.3.3 变形程度对弹性恢复值的影响 图 3.3.4 无底凹模内的自由弯曲
132
图 3.3.5 间隙对回弹的影响 5.工件的形状 一般而言,弯曲件越复杂,一次弯曲成形角的数量越多,则弯曲时各部分互相牵制作用越 大,弯曲中拉伸变形的成分越大,故回弹量就越小。例如一次弯曲成形时, 形件的回弹量较 U 形件小,U形件又较 V形件为小。
从弯曲变形区的横截面变化来看,变形有两种情况:窄板(B/t3)弯曲时,内区宽度增加, 外区宽度减小,原矩形截面变成了扇形(图 3.2.4a);宽板(B/t3)弯曲时,横截面几乎不变, 仍为矩形(图 3.2.4b)。
123
由此可见,板料在塑性弯曲时,随相对宽度 B/t的不同,其应力、应变的性质也不同,分 析如下:
3.合理设计弯曲模 (1)对于较硬材料(如 45、50、Q275和 H62(硬)等),可根据回弹值对模具工作部分的形 状和尺寸进行修正。
图 3.3.9 拉弯用模具
图 3.3.10 拉弯时断面内切向应变的分析
(2)对于软材料(如 Q215、Q235、10、20和 H62(软)等),其回弹角小于 5°时,可在 模具上作出补偿角并取较小的凸、凹模间隙(图 3.3.11)。
137
3.铰链式弯曲件 图 3.4.3
138
例 3.4.1 计算图 3.4.4所示弯曲件的坯料展开长度。
图 3.4.4 V形支架
139
弯曲件的工艺性是指弯曲零件的形状、尺寸、精度、材料以及技术要求等是否符合弯曲加工 的工艺要求。具有良好工艺性的弯曲件,能简化弯曲的工艺过程及模具结构,提高工件的质量。
133
3.校正弯曲时的回弹值 校正弯曲的回弹可用试验所得的公式计算,公式见表 3.3.2,符号如图 3.3.7所示。
134
在实际生产中,由于材料的力学性能和厚度的波动等,要完全消除弯曲件的回弹是不可能 的。但可以采取一些措施来减小或补偿回弹所产生的误差,以提高弯曲件的精度。
1.改进弯曲件的设计
2.采取适当的弯曲工艺 (1)采用校正弯曲代替自由弯曲。
1.弯曲半径 弯曲件的弯曲半径不宜小于最小弯曲半径,否则,要多次弯曲,增加工序数;也不宜过大, 因为过大时,受到回弹的影响,弯曲角度与弯曲半径的精度都不易保证。 2.弯曲件的形状 一般要求弯曲件形状对称,弯曲半径左右一致,则弯曲时坯料受力平衡而无滑动(图 3.6.1a)。如果弯曲件不对称,由于摩擦阻力不均匀,坯料在弯曲过程中会产生滑动,造成偏 移(图 3.6.1b)。