烧结工序节能降耗新技术发展趋势
烧结过程余热利用现状及趋势
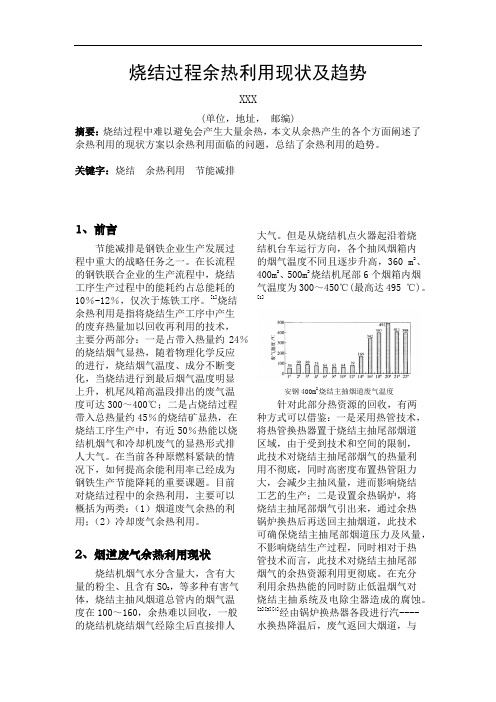
烧结过程余热利用现状及趋势XXX(单位,地址,邮编)摘要:烧结过程中难以避免会产生大量余热,本文从余热产生的各个方面阐述了余热利用的现状方案以余热利用面临的问题,总结了余热利用的趋势。
关键字:烧结余热利用节能减排1、前言节能减排是钢铁企业生产发展过程中重大的战略任务之一。
在长流程的钢铁联合企业的生产流程中,烧结工序生产过程中的能耗约占总能耗的10%-12%,仅次于炼铁工序。
[1]烧结余热利用是指将烧结生产工序中产生的废弃热量加以回收再利用的技术,主要分两部分:一是占带入热量约24%的烧结烟气显热,随着物理化学反应的进行,烧结烟气温度、成分不断变化,当烧结进行到最后烟气温度明显上升,机尾风箱高温段排出的废气温度可达300~400℃;二是占烧结过程带入总热量约45%的烧结矿显热,在烧结工序生产中,有近50%热能以烧结机烟气和冷却机废气的显热形式排人大气。
在当前各种原燃料紧缺的情况下,如何提高余能利用率已经成为钢铁生产节能降耗的重要课题。
目前对烧结过程中的余热利用,主要可以概括为两类:(1)烟道废气余热的利用;(2)冷却废气余热利用。
2、烟道废气余热利用现状烧结机烟气水分含量大,含有大量的粉尘、且含有SO2,等多种有害气体,烧结主抽风烟道总管内的烟气温度在100~160,余热难以回收,一般的烧结机烧结烟气经除尘后直接排人大气。
但是从烧结机点火器起沿着烧结机台车运行方向,各个抽风烟箱内的烟气温度不同且逐步升高,360 m2、400m2、500m2烧结机尾部6个烟箱内烟气温度为300~450℃(最高达495 ℃)。
[1]安钢400m2烧结主抽烟道废气温度针对此部分热资源的回收,有两种方式可以借鉴:一是采用热管技术,将热管换热器置于烧结主抽尾部烟道区域,由于受到技术和空间的限制,此技术对烧结主抽尾部烟气的热量利用不彻底,同时高密度布置热管阻力大,会减少主抽风量,进而影响烧结工艺的生产;二是设置余热锅炉,将烧结主抽尾部烟气引出来,通过余热锅炉换热后再送回主抽烟道,此技术可确保烧结主抽尾部烟道压力及风量,不影响烧结生产过程,同时相对于热管技术而言,此技术对烧结主抽尾部烟气的余热资源利用更彻底。
浅谈降低烧结工序能耗的措施
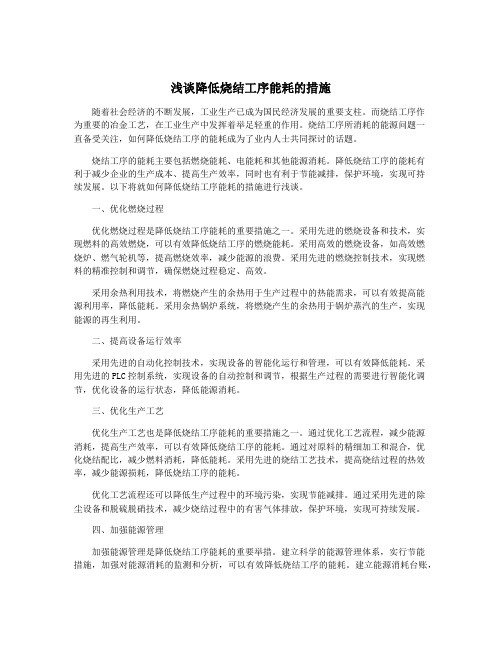
浅谈降低烧结工序能耗的措施随着社会经济的不断发展,工业生产已成为国民经济发展的重要支柱。
而烧结工序作为重要的冶金工艺,在工业生产中发挥着举足轻重的作用。
烧结工序所消耗的能源问题一直备受关注,如何降低烧结工序的能耗成为了业内人士共同探讨的话题。
烧结工序的能耗主要包括燃烧能耗、电能耗和其他能源消耗。
降低烧结工序的能耗有利于减少企业的生产成本、提高生产效率,同时也有利于节能减排,保护环境,实现可持续发展。
以下将就如何降低烧结工序能耗的措施进行浅谈。
一、优化燃烧过程优化燃烧过程是降低烧结工序能耗的重要措施之一。
采用先进的燃烧设备和技术,实现燃料的高效燃烧,可以有效降低烧结工序的燃烧能耗。
采用高效的燃烧设备,如高效燃烧炉、燃气轮机等,提高燃烧效率,减少能源的浪费。
采用先进的燃烧控制技术,实现燃料的精准控制和调节,确保燃烧过程稳定、高效。
采用余热利用技术,将燃烧产生的余热用于生产过程中的热能需求,可以有效提高能源利用率,降低能耗。
采用余热锅炉系统,将燃烧产生的余热用于锅炉蒸汽的生产,实现能源的再生利用。
二、提高设备运行效率采用先进的自动化控制技术,实现设备的智能化运行和管理,可以有效降低能耗。
采用先进的PLC控制系统,实现设备的自动控制和调节,根据生产过程的需要进行智能化调节,优化设备的运行状态,降低能源消耗。
三、优化生产工艺优化生产工艺也是降低烧结工序能耗的重要措施之一。
通过优化工艺流程,减少能源消耗,提高生产效率,可以有效降低烧结工序的能耗。
通过对原料的精细加工和混合,优化烧结配比,减少燃料消耗,降低能耗。
采用先进的烧结工艺技术,提高烧结过程的热效率,减少能源损耗,降低烧结工序的能耗。
优化工艺流程还可以降低生产过程中的环境污染,实现节能减排。
通过采用先进的除尘设备和脱硫脱硝技术,减少烧结过程中的有害气体排放,保护环境,实现可持续发展。
四、加强能源管理加强能源管理是降低烧结工序能耗的重要举措。
建立科学的能源管理体系,实行节能措施,加强对能源消耗的监测和分析,可以有效降低烧结工序的能耗。
烧结行业发展趋势总结

烧结行业发展趋势总结烧结行业发展趋势总结烧结技术是一种重要的冶金制造技术,广泛应用于钢铁、有色金属、建材等行业。
烧结行业在我国经济和工业发展中起着至关重要的作用。
近年来,随着各种新技术的不断涌现,烧结行业发生了许多变化,如何把握烧结行业的发展趋势,对于烧结企业对未来的发展是非常必要的。
本文将从材料、工艺、环保、自动化及数字化等方面来总结烧结行业的发展趋势。
一、材料烧结行业的重要特点之一是材料的使用,因此材料的发展趋势具有非常重要的意义。
未来烧结企业将更加注重材料的多元化和高端化。
这种趋势主要体现在以下几个方面:1. 多元化的原料——烧结原料将更加广泛,以满足未来各行业的需求。
比如在钢铁工业中,烧结原料将更多地涉及废钢、废铁、废渣等。
2. 高端化的合金——烧结合金将更多地涉及多种合金元素混合的高端合金,以广泛满足高精度的行业需求。
3. 新型材料的应用——烧结技术已经开始涉及到新的材料领域,如陶瓷材料、复合材料等,未来,在这些新型材料的应用方面,烧结技术将会有更多的发展。
二、工艺工艺是烧结行业中的重要环节,随着科技的进步和市场要求的提高,工艺的发展也逐渐成为了烧结行业关注的重点。
未来,烧结企业将以更高的标准要求自己,更高效的工艺将是烧结企业不断追求的目标。
主要体现在以下几方面:1. 烧结过程的精细化——未来,烧结企业将会更加注重烧结工艺的精细化,并加强烧结过程中的监控与控制,以保证产品的质量和性能。
2. 绿色的烧结工艺——未来,烧结企业将会更加注重绿色工艺的开发与应用,减少废气、废水、废渣等污染物的排放,减少环境污染,提高企业的可持续性发展。
3. 节能的烧结工艺——未来,烧结企业将会更加注重节能技术的应用,采用高效的能源回收设备,以降低生产成本,提高经济效益。
三、环保随着环保意识的不断提高,烧结企业未来将更加注重环保问题的解决。
环保问题的解决一方面可以促进企业的可持续性发展,另一方面可以增强企业的社会责任感。
降低烧结法氧化铝生产工艺能耗新技术
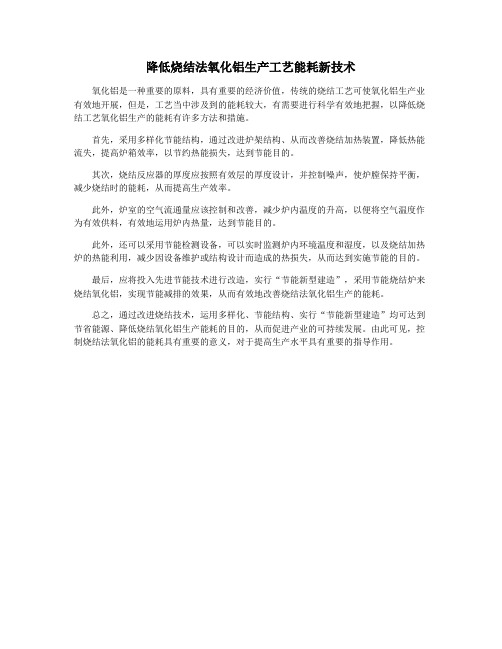
降低烧结法氧化铝生产工艺能耗新技术
氧化铝是一种重要的原料,具有重要的经济价值,传统的烧结工艺可使氧化铝生产业有效地开展,但是,工艺当中涉及到的能耗较大,有需要进行科学有效地把握,以降低烧结工艺氧化铝生产的能耗有许多方法和措施。
首先,采用多样化节能结构,通过改进炉架结构、从而改善烧结加热装置,降低热能流失,提高炉箱效率,以节约热能损失,达到节能目的。
其次,烧结反应器的厚度应按照有效层的厚度设计,并控制噪声,使炉膛保持平衡,减少烧结时的能耗,从而提高生产效率。
此外,炉室的空气流通量应该控制和改善,减少炉内温度的升高,以便将空气温度作为有效供料,有效地运用炉内热量,达到节能目的。
此外,还可以采用节能检测设备,可以实时监测炉内环境温度和湿度,以及烧结加热炉的热能利用,减少因设备维护或结构设计而造成的热损失,从而达到实施节能的目的。
最后,应将投入先进节能技术进行改造,实行“节能新型建造”,采用节能烧结炉来烧结氧化铝,实现节能减排的效果,从而有效地改善烧结法氧化铝生产的能耗。
总之,通过改进烧结技术,运用多样化、节能结构、实行“节能新型建造”均可达到节省能源、降低烧结氧化铝生产能耗的目的,从而促进产业的可持续发展。
由此可见,控制烧结法氧化铝的能耗具有重要的意义,对于提高生产水平具有重要的指导作用。
浅谈烧结节能降耗的技术途径和措施
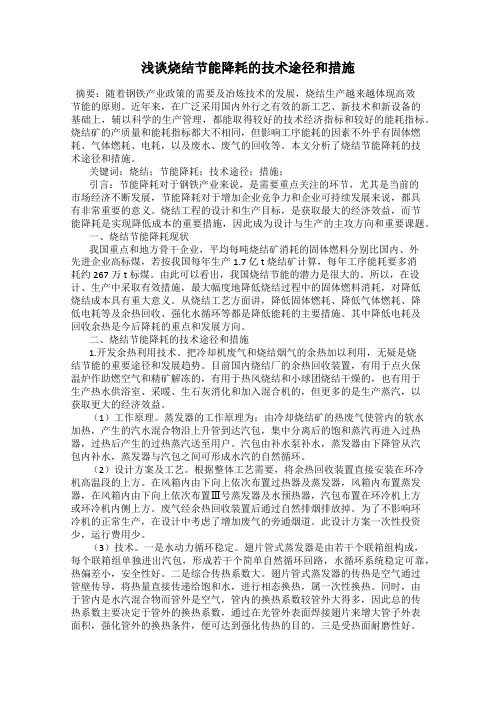
浅谈烧结节能降耗的技术途径和措施摘要:随着钢铁产业政策的需要及冶炼技术的发展,烧结生产越来越体现高效节能的原则。
近年来,在广泛采用国内外行之有效的新工艺、新技术和新设备的基础上,辅以科学的生产管理,都能取得较好的技术经济指标和较好的能耗指标。
烧结矿的产质量和能耗指标都大不相同,但影响工序能耗的因素不外乎有固体燃耗、气体燃耗、电耗,以及废水、废气的回收等。
本文分析了烧结节能降耗的技术途径和措施。
关键词:烧结;节能降耗;技术途径;措施;引言:节能降耗对于钢铁产业来说,是需要重点关注的环节,尤其是当前的市场经济不断发展,节能降耗对于增加企业竞争力和企业可持续发展来说,都具有非常重要的意义。
烧结工程的设计和生产目标,是获取最大的经济效益,而节能降耗是实现降低成本的重要措施,因此成为设计与生产的主攻方向和重要课题。
一、烧结节能降耗现状我国重点和地方骨干企业,平均每吨烧结矿消耗的固体燃料分别比国内、外先进企业高标煤,若按我国每年生产1.7亿t烧结矿计算,每年工序能耗要多消耗约267万t标煤。
由此可以看出,我国烧结节能的潜力是很大的。
所以,在设计、生产中采取有效措施,最大幅度地降低烧结过程中的固体燃料消耗,对降低烧结成本具有重大意义。
从烧结工艺方面讲,降低固体燃耗、降低气体燃耗、降低电耗等及余热回收、强化水循环等都是降低能耗的主要措施。
其中降低电耗及回收余热是今后降耗的重点和发展方向。
二、烧结节能降耗的技术途径和措施1.开发余热利用技术。
把冷却机废气和烧结烟气的余热加以利用,无疑是烧结节能的重要途径和发展趋势。
目前国内烧结厂的余热回收装置,有用于点火保温炉作助燃空气和精矿解冻的,有用于热风烧结和小球团烧结干燥的,也有用于生产热水供浴室、采暖、生石灰消化和加入混合机的,但更多的是生产蒸汽,以获取更大的经济效益。
(1)工作原理。
蒸发器的工作原理为:由冷却烧结矿的热废气使管内的软水加热,产生的汽水混合物沿上升管到达汽包,集中分离后的饱和蒸汽再进入过热器,过热后产生的过热蒸汽送至用户。
试析烧结工序节能降耗新技术发展趋势

试析烧结工序节能降耗新技术发展趋势摘要:钢铁企业长期的艰巨的任务是节能降耗,而具有极大节能潜力的是烧结工序节。
因此,在设计该工序时,节能降耗应放在首位,通过落后设备的改进和节能新技术以及新工艺的充分应用,以达到充分发挥出单体设备的节能效果,将整个系统的节能效果调配到最佳状态,以期提高生产能力的同时能源消耗得以降低,最终能够实现整个烧结工序节能降耗。
关键词:钢铁企业;烧结工序;节能降耗;新技术前言增加对用能的管理就是节能降耗,通过使用相应的措施(如:可行的技术、合理的费用和能被环境和社会接受的措施),将消耗和损失降低以及排放的污染物减少,促进能源从生产到消费的每个环节都能做到有效合理的使用。
我国可持续发展的经济、技术的提升、自然资源和环境的保护都受到节能降耗战略意义的影响。
作为能源消耗大户的钢铁企业仅烧结一项能耗就占10%-15%,因此,烧结过程中尽可能采取有效的方式降低能源消耗的意义是非常重大的。
1国内烧结工序节能技术现状1.1余热回收技术烧结烟气的余热和烧结矿显热的回收利用就是余热回收(如:余热发电、预热的混合料、预热空气点火和烧结废气循环等)。
烧结矿显热是早期余热回收研究和利用的重点(如:早期的民用热水、早期的冬季供暖和早期的试验研究等)。
同时,部分区段的热烟气在20世纪90年代左右被武钢和马钢烧结厂尝试着再次引入烧结循环过程中,这个尝试促进了利用烧结烟气余热的开启。
此外,烧结工序能耗和烟气余热回收问题在迈入新世纪后随着绿色环保理念的不断深化发展已成为“节能减排”发展中的重中之重。
国内钢铁企业采用了许多有效的措施(如:烟气循环、助燃空气预热点火、回收蒸汽利用余热和余热发电等),促使余热回收效率大大提高。
1.2厚料层烧结技术根据厚料层自身蓄热理论烧结实验发现烧结燃烧层一般情况下所需要的40%的热量就可以通过自蓄热作用提供,这种低碳操可以促进低价氧化铁氧化反应的增多,可以促进高价铁氧化物分解热耗的降低,从而实现固体燃料消耗的减少。
浅谈降低烧结工序能耗的措施

浅谈降低烧结工序能耗的措施1. 引言1.1 烧结工序对能源消耗的重要性烧结工序是冶金工业重要的炼铁生产工序之一,其能源消耗对整个生产过程的能耗影响极为重要。
烧结工序主要是通过将铁矿石等原料在高温下加热,使其在烧结炉中发生一系列物理化学反应,最终形成高强度的铁制品。
烧结工序的能源消耗占据了整个冶金生产的重要比重,对于企业的生产成本和环境影响都具有重要的意义。
烧结工序所需能源包括燃料能源和电力能源,其中以燃料消耗较大。
在烧结工序中,煤炭、焦炭等燃料被用来提供高温热能,使原料得以烧结。
传统的烧结工序存在能源利用率低、排放浪费等问题,导致能源消耗较高。
降低烧结工序的能源消耗具有重要意义。
通过优化烧结工艺参数、采用先进的设备和技术、加强热能回收利用、提高烧结燃料的利用率以及应用节能技术等措施,可以有效降低烧结工序的能源消耗,提高生产效率,减少生产成本,实现可持续发展。
节能减排也是当前社会发展的重要趋势,降低烧结工序的能源消耗,不仅符合环保要求,也能提升企业的竞争力。
2. 正文2.1 优化烧结工艺参数优化烧结工艺参数是降低烧结工序能耗的重要措施之一。
通过调整烧结工艺中的各项参数,可以实现更高效的烧结过程,减少能源的消耗。
优化烧结工艺参数可以提高烧结的热效率。
合理调节烧结温度、烧结时间等参数,可以使烧结过程中的热能更加充分利用,减少能源的浪费。
优化参数还可以提高烧结矿的燃烧效率,减少燃料的使用量,降低能耗。
优化烧结工艺参数还可以改善产品质量。
通过精确控制烧结过程中的各项参数,可以确保产品的成分和性能达到要求,避免因为工艺参数不合理导致的质量问题,减少了产品的废品率,提高了资源利用率。
优化烧结工艺参数还可以减少设备运行时的能耗。
通过合理设置烧结设备的工作参数,有效控制能源的消耗,延长设备的使用寿命,减少了能源的浪费,降低了生产成本。
优化烧结工艺参数是降低烧结工序能耗的有效途径之一,可以提高烧结热效率,改善产品质量,减少设备能耗,从而实现节能减排的目标。
烧结技术的发展

烧结新技术的发展高炉炼铁所使用的主要含铁原料是烧结矿。
近几年,我国生铁产量不断上升,烧结矿用量大幅度增加,提高烧结矿的质量、降低消耗、节约能源、保护环境在烧结生产中显得越来越重要,也是烧结生产工艺技术发展的永恒的课题和方向。
近几年烧结新技术从以下几方面在发展。
一、采取措施减少焦粉中过细粒级和过粗粒级减少焦粉中过细粒级和过粗粒级,可降低固体燃料消耗、提高燃料利用率和改善布料时燃料的偏析条件。
如增加破碎前的小焦粉筛分工艺、使用棒磨机破碎、分级筛分和破碎等。
二、实施超高料层操作提高烧结料层高度,可充分利用厚料层的“自动蓄热作用”,节约固体燃料,提高烧结矿的产质量。
目前,我国厚料层烧结已达到国际先进水平。
烧结机布料厚度已达到750~800mm,居国际领先水平,生产的烧结矿质量、品位、强度达到国际同行业领先水平。
加强混合造球,改善混合料的粒度组成,提高混合料的透气性,采用高效的混匀与造球设备,延长混合和造球时间达5min以上,添加生石灰,使生石灰消化为消石灰,提高混合料的成球性能,烧结混合料运输系统尽量减少落差,减少混合料种的小球运输过程中的粉碎,混合机大型化、降低混合机的填充率等。
提高混合料的料温。
混合料的料温达65摄氏度以上,消除烧结过程中的“过湿现象”,改善烧结料层的透气性。
措施有:在烧结混合料中加入热返矿;加生石灰,全部或部分代替石灰石;蒸汽预热混合料,一是将蒸汽采用强力蒸汽喷头喷入烧结机头的混合料仓内,此方法是蒸汽最大限度的和混合料接触,蒸汽热能利用效率高,但此方法加热的混合料温度不太均匀。
在没有热返矿的烧结厂,一般此两种方法同时使用,可保证温度达到要求和混合料温度的均匀性。
从节能的观点出发,预热混合料的蒸汽最好利用。
三、生石灰分加和燃料分加技术该技术过程是将铁矿物、返矿、添加剂、部分生石灰和固体燃料在一次或二次加水混合造球后,在二次或三次混合造球前加入部分的燃料和生石灰,再进行混匀和造球,使小球表层外裹一定比例的生石灰和固体燃料,然后进行烧结。
烧结余热利用现状和趋势
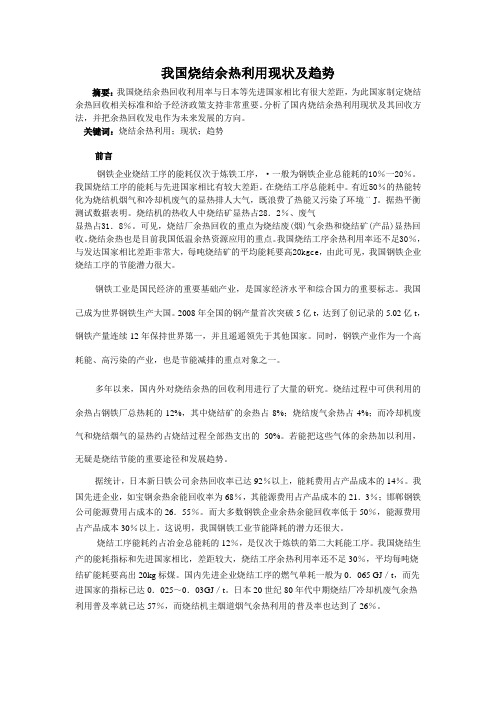
我国烧结余热利用现状及趋势摘要:我国烧结余热回收利用率与日本等先进国家相比有很大差距,为此国家制定烧结余热回收相关标准和给予经济政策支持非常重要。
分析了国内烧结余热利用现状及其回收方法,并把余热回收发电作为未来发展的方向。
关键词:烧结余热利用;现状;趋势前言钢铁企业烧结工序的能耗仅次于炼铁工序,·一般为钢铁企业总能耗的10%一20%。
我国烧结工序的能耗与先进国家相比有较大差距。
在烧结工序总能耗中。
有近50%的热能转化为烧结机烟气和冷却机废气的显热排人大气,既浪费了热能又污染了环境¨J。
据热平衡测试数据表明。
烧结机的热收人中烧结矿显热占28.2%、废气显热占31.8%。
可见,烧结厂余热回收的重点为烧结废(烟)气余热和烧结矿(产品)显热回收。
烧结余热也是目前我国低温余热资源应用的重点。
我国烧结工序余热利用率还不足30%,与发达国家相比差距非常大,每吨烧结矿的平均能耗要高20kgce,由此可见,我国钢铁企业烧结工序的节能潜力很大。
钢铁工业是国民经济的重要基础产业,是国家经济水平和综合国力的重要标志。
我国己成为世界钢铁生产大国。
2008年全国的钢产量首次突破5亿t,达到了创记录的5.02亿t,钢铁产量连续12年保持世界第一,并且遥遥领先于其他国家。
同时,钢铁产业作为一个高耗能、高污染的产业,也是节能减排的重点对象之一。
多年以来,国内外对烧结余热的回收利用进行了大量的研究。
烧结过程中可供利用的余热占钢铁厂总热耗的12%,其中烧结矿的余热占8%;烧结废气余热占4%;而冷却机废气和烧结烟气的显热约占烧结过程全部热支出的50%。
若能把这些气体的余热加以利用,无疑是烧结节能的重要途径和发展趋势。
据统计,日本新日铁公司余热回收率已达92%以上,能耗费用占产品成本的14%。
我国先进企业,如宝钢余热余能回收率为68%,其能源费用占产品成本的21.3%;邯郸钢铁公司能源费用占成本的26.55%。
而大多数钢铁企业余热余能回收率低于50%,能源费用占产品成本30%以上。
烧结新技术及发展方向
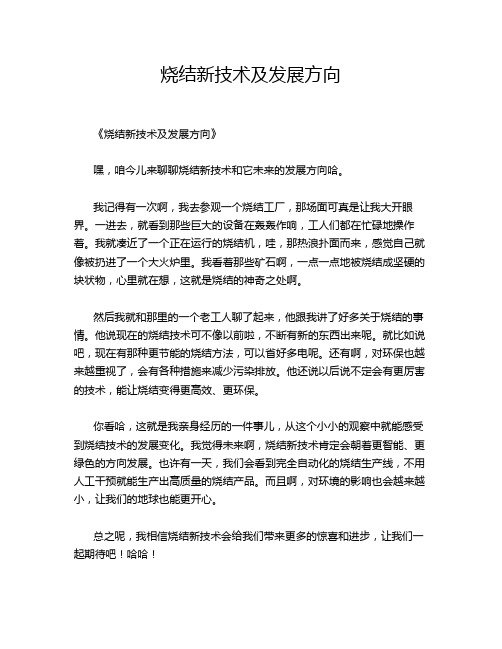
烧结新技术及发展方向
《烧结新技术及发展方向》
嘿,咱今儿来聊聊烧结新技术和它未来的发展方向哈。
我记得有一次啊,我去参观一个烧结工厂,那场面可真是让我大开眼界。
一进去,就看到那些巨大的设备在轰轰作响,工人们都在忙碌地操作着。
我就凑近了一个正在运行的烧结机,哇,那热浪扑面而来,感觉自己就像被扔进了一个大火炉里。
我看着那些矿石啊,一点一点地被烧结成坚硬的块状物,心里就在想,这就是烧结的神奇之处啊。
然后我就和那里的一个老工人聊了起来,他跟我讲了好多关于烧结的事情。
他说现在的烧结技术可不像以前啦,不断有新的东西出来呢。
就比如说吧,现在有那种更节能的烧结方法,可以省好多电呢。
还有啊,对环保也越来越重视了,会有各种措施来减少污染排放。
他还说以后说不定会有更厉害的技术,能让烧结变得更高效、更环保。
你看哈,这就是我亲身经历的一件事儿,从这个小小的观察中就能感受到烧结技术的发展变化。
我觉得未来啊,烧结新技术肯定会朝着更智能、更绿色的方向发展。
也许有一天,我们会看到完全自动化的烧结生产线,不用人工干预就能生产出高质量的烧结产品。
而且啊,对环境的影响也会越来越小,让我们的地球也能更开心。
总之呢,我相信烧结新技术会给我们带来更多的惊喜和进步,让我们一起期待吧!哈哈!。
浅谈降低烧结工序能耗的措施
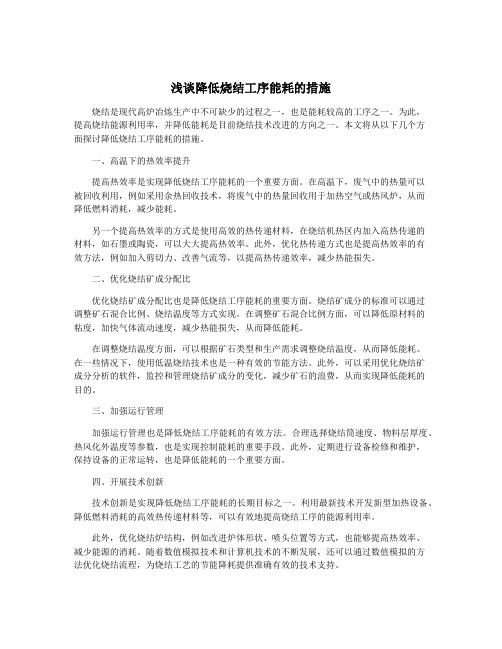
浅谈降低烧结工序能耗的措施烧结是现代高炉冶炼生产中不可缺少的过程之一,也是能耗较高的工序之一。
为此,提高烧结能源利用率,并降低能耗是目前烧结技术改进的方向之一。
本文将从以下几个方面探讨降低烧结工序能耗的措施。
一、高温下的热效率提升提高热效率是实现降低烧结工序能耗的一个重要方面。
在高温下,废气中的热量可以被回收利用,例如采用余热回收技术,将废气中的热量回收用于加热空气或热风炉,从而降低燃料消耗,减少能耗。
另一个提高热效率的方式是使用高效的热传递材料,在烧结机热区内加入高热传递的材料,如石墨或陶瓷,可以大大提高热效率。
此外,优化热传递方式也是提高热效率的有效方法,例如加入剪切力、改善气流等,以提高热传递效率,减少热能损失。
二、优化烧结矿成分配比优化烧结矿成分配比也是降低烧结工序能耗的重要方面。
烧结矿成分的标准可以通过调整矿石混合比例、烧结温度等方式实现。
在调整矿石混合比例方面,可以降低原材料的粘度,加快气体流动速度,减少热能损失,从而降低能耗。
在调整烧结温度方面,可以根据矿石类型和生产需求调整烧结温度,从而降低能耗。
在一些情况下,使用低温烧结技术也是一种有效的节能方法。
此外,可以采用优化烧结矿成分分析的软件,监控和管理烧结矿成分的变化,减少矿石的浪费,从而实现降低能耗的目的。
三、加强运行管理加强运行管理也是降低烧结工序能耗的有效方法。
合理选择烧结筒速度、物料层厚度、热风化外温度等参数,也是实现控制能耗的重要手段。
此外,定期进行设备检修和维护,保持设备的正常运转,也是降低能耗的一个重要方面。
四、开展技术创新技术创新是实现降低烧结工序能耗的长期目标之一。
利用最新技术开发新型加热设备、降低燃料消耗的高效热传递材料等,可以有效地提高烧结工序的能源利用率。
此外,优化烧结炉结构,例如改进炉体形状、喷头位置等方式,也能够提高热效率、减少能源的消耗。
随着数值模拟技术和计算机技术的不断发展,还可以通过数值模拟的方法优化烧结流程,为烧结工艺的节能降耗提供准确有效的技术支持。
浅谈降低烧结工序能耗的措施
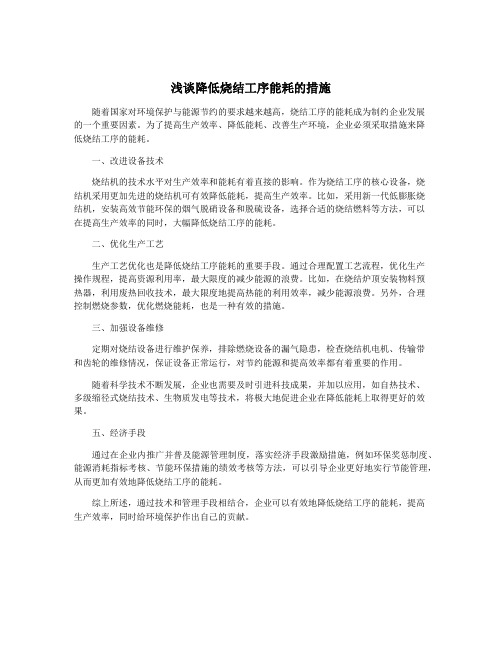
浅谈降低烧结工序能耗的措施随着国家对环境保护与能源节约的要求越来越高,烧结工序的能耗成为制约企业发展的一个重要因素。
为了提高生产效率、降低能耗、改善生产环境,企业必须采取措施来降低烧结工序的能耗。
一、改进设备技术烧结机的技术水平对生产效率和能耗有着直接的影响。
作为烧结工序的核心设备,烧结机采用更加先进的烧结机可有效降低能耗,提高生产效率。
比如,采用新一代低膨胀烧结机,安装高效节能环保的烟气脱硝设备和脱硫设备,选择合适的烧结燃料等方法,可以在提高生产效率的同时,大幅降低烧结工序的能耗。
二、优化生产工艺生产工艺优化也是降低烧结工序能耗的重要手段。
通过合理配置工艺流程,优化生产操作规程,提高资源利用率,最大限度的减少能源的浪费。
比如,在烧结炉顶安装物料预热器,利用废热回收技术,最大限度地提高热能的利用效率,减少能源浪费。
另外,合理控制燃烧参数,优化燃烧能耗,也是一种有效的措施。
三、加强设备维修定期对烧结设备进行维护保养,排除燃烧设备的漏气隐患,检查烧结机电机、传输带和齿轮的维修情况,保证设备正常运行,对节约能源和提高效率都有着重要的作用。
随着科学技术不断发展,企业也需要及时引进科技成果,并加以应用,如自热技术、多级缩径式烧结技术、生物质发电等技术,将极大地促进企业在降低能耗上取得更好的效果。
五、经济手段通过在企业内推广并普及能源管理制度,落实经济手段激励措施,例如环保奖惩制度、能源消耗指标考核、节能环保措施的绩效考核等方法,可以引导企业更好地实行节能管理,从而更加有效地降低烧结工序的能耗。
综上所述,通过技术和管理手段相结合,企业可以有效地降低烧结工序的能耗,提高生产效率,同时给环境保护作出自己的贡献。
烧结技术国内外现状及发展趋势分解

2010 年 5 月
汇报内容
· 我国烧结技术近年来取得的进步 · 与国外技术的比较 · 烧结技术发展趋势
一、我国烧结技术近年来取得的进步
■ 改革开放以来,我国工程技术人员走出了一条“引进消化-吸收-改进-创新”的道路,在开拓创新新工艺、新 设备、新技术方面相当活跃,硕果累累,经验极其丰富, 堪为世界之最。
烟气循环烧结富集脱硫系统工艺示意图
三三.发发展展趋趋势势
3)烧结机大型化。因为建设一台大型烧结机与建设多台 小型机相比,具有很多明显的优点,其烧结矿质量好 生产管理方便,劳动生产率高,易于环保治理和实现 自动化。特别是燃耗低,因为大烧结机易于实现超厚 料层烧结,蓄热性好,热量散失少。 我国目前还有大约300台小型机在生产,该淘汰的应坚 决淘汰,有些则应改为大中型烧结机。
■ 烧结机漏风率低 烧结机主要漏风点为头尾风箱与台车底部接触处和两侧。 70年代初烧结漏风率高达60%以上,新建烧结漏风率普 遍下降。
2、主要设备方面
■ 新型鼓风环式冷却机 最近中冶长天国际工程有限责任公司开发了一种液密封 鼓风环式冷却机,其漏风率可低到5%。
■ 新型节能点火保温炉 双斜带式点火保温炉采用直接点火,高效低耗,点火质 量好,炉子寿命长,烧嘴不易堵塞,作业率高,在国内 得到普遍使用。最近在鞍钢一些企业有的采用二次连续 低温点火技术,但应在点火前预热烧结机上的混合料。
二 . 与国外技术比较
表1 大中型烧结机主要设备对比或差距表
序 主要设 号 备名称
国内技术水平
国外技术水平
对比或 差距
1 混合与 采用大型圆筒混合 采用大型圆筒混合机和圆 我国尚
制粒设 机和圆筒制粒机, 筒制粒机,日本个别细粒 未使用
降低烧结法氧化铝生产工艺能耗新技术

降低烧结法氧化铝生产工艺能耗新技术
降低烧结法氧化铝生产工艺能耗的新技术是指针对传统工艺存在的高能耗、低效率等问题,提出的一系列新型工艺、设备、材料等创新解决方案,旨在优化生产流程、提高生产效率、降低能耗,从而达到节能减排的目的。
其中,新型燃烧技术是当前主要的研究方向之一。
其原理是利用新型燃烧器实现氧化铝生产过程中的燃料自燃,并通过调节燃烧器结构和参数,达到控制燃烧
反应的目的,从而降低热能损失,提高热能利用率,实现能耗降低。
另外,新型材料的研究也是降低氧化铝生产能耗的重要途径之一。
例如,采用新型耐火材料可以降低炉膛温度,从而减少能耗损失。
同时,还可以通过改进材料的物理性质,提高其热稳定性和抗磨损性能,从而延长使用寿命,减少维修次数,降低维修成本。
除此之外,新型设备的应用也是实现能耗降低的有效手段之一。
例如,采用新型过滤器可以有效降低生产过程中的粉尘排放,从而减少环境污染,降低治理成本。
同时,通过改进设备结构和参数,还可以提高设备的效率,降低能耗,进一步降
低生产成本。
总之,降低烧结法氧化铝生产工艺能耗的新技术是一个综合性的问题,需要多种技术手段的综合应用。
只有在不断探索、创新和实践的基础上,才能实现氧化铝生产过程中的节能减排目标,推动工业可持续发展。
烧结新技术及其发展状况
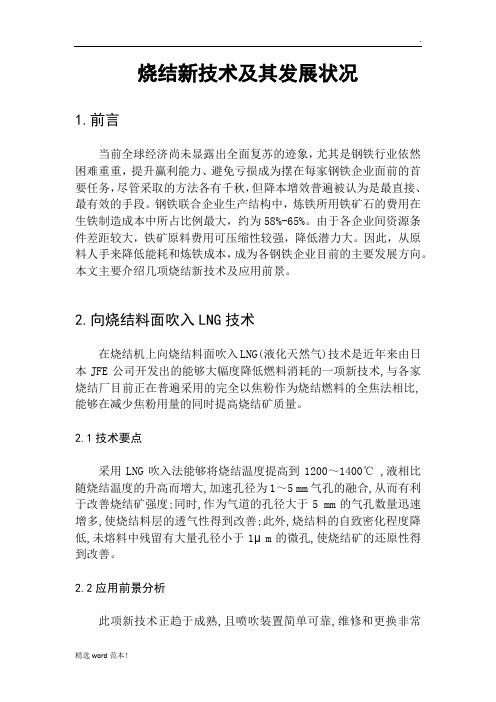
烧结新技术及其发展状况1.前言当前全球经济尚未显露出全面复苏的迹象,尤其是钢铁行业依然困难重重,提升赢利能力、避免亏损成为摆在每家钢铁企业面前的首要任务,尽管采取的方法各有千秋,但降本增效普遍被认为是最直接、最有效的手段。
钢铁联合企业生产结构中,炼铁所用铁矿石的费用在生铁制造成本中所占比例最大,约为58%-65%。
由于各企业间资源条件差距较大,铁矿原料费用可压缩性较强,降低潜力大。
因此,从原料人手来降低能耗和炼铁成本,成为各钢铁企业目前的主要发展方向。
本文主要介绍几项烧结新技术及应用前景。
2.向烧结料面吹入LNG技术在烧结机上向烧结料面吹入LNG(液化天然气)技术是近年来由日本JFE公司开发出的能够大幅度降低燃料消耗的一项新技术,与各家烧结厂目前正在普遍采用的完全以焦粉作为烧结燃料的全焦法相比,能够在减少焦粉用量的同时提高烧结矿质量。
2.1技术要点采用LNG吹入法能够将烧结温度提高到1200~1400℃ ,液相比随烧结温度的升高而增大,加速孔径为1~5 mm气孔的融合,从而有利于改善烧结矿强度;同时,作为气道的孔径大于5 mm的气孔数量迅速增多,使烧结料层的透气性得到改善;此外,烧结料的自致密化程度降低,未熔料中残留有大量孔径小于1μm的微孔,使烧结矿的还原性得到改善。
2.2应用前景分析此项新技术正趋于成熟,且喷吹装置简单可靠,维修和更换非常方便,只要准确控制好LNG喷吹浓度和喷吹速度,就能够生产出高强度、高还原性的烧结矿。
如果从经济性方面考虑,应用LNG吹入法确实需要投入一定的费用,但能够换来减少焦粉用量和提高烧结矿质量的好处,特别是还能够实现CO2的大幅度减排,烧结矿产能越大,效果越明显。
综合多方面因素分析,LNG吹入法烧结具有广阔的应用前景,适用于采用厚料层烧结技术的大型烧结机生产。
3.富氧烧结技术富氧烧结技术是2010年由韩国浦项开发出的能够改善烧结料层中热量分布的新技术。
现有的烧结工艺只单纯依靠焦粉燃烧为烧结料供热,其缺点是容易造成料层中热量分布不均(这是影响烧结矿质量的重要因素),上部料层温度低、下部料层温度高,上部烧结饼质量较差。
节能降耗技术的最新发展
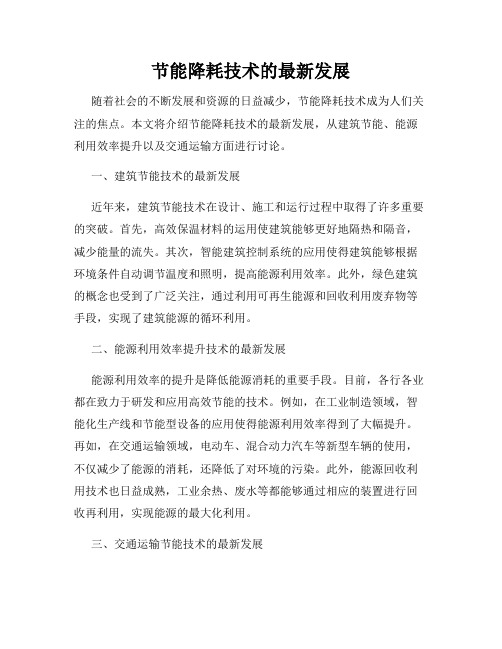
节能降耗技术的最新发展随着社会的不断发展和资源的日益减少,节能降耗技术成为人们关注的焦点。
本文将介绍节能降耗技术的最新发展,从建筑节能、能源利用效率提升以及交通运输方面进行讨论。
一、建筑节能技术的最新发展近年来,建筑节能技术在设计、施工和运行过程中取得了许多重要的突破。
首先,高效保温材料的运用使建筑能够更好地隔热和隔音,减少能量的流失。
其次,智能建筑控制系统的应用使得建筑能够根据环境条件自动调节温度和照明,提高能源利用效率。
此外,绿色建筑的概念也受到了广泛关注,通过利用可再生能源和回收利用废弃物等手段,实现了建筑能源的循环利用。
二、能源利用效率提升技术的最新发展能源利用效率的提升是降低能源消耗的重要手段。
目前,各行各业都在致力于研发和应用高效节能的技术。
例如,在工业制造领域,智能化生产线和节能型设备的应用使得能源利用效率得到了大幅提升。
再如,在交通运输领域,电动车、混合动力汽车等新型车辆的使用,不仅减少了能源的消耗,还降低了对环境的污染。
此外,能源回收利用技术也日益成熟,工业余热、废水等都能够通过相应的装置进行回收再利用,实现能源的最大化利用。
三、交通运输节能技术的最新发展交通运输是耗能量最大的领域之一,因此交通运输节能技术的发展具有重要的意义。
最新的交通运输节能技术主要集中在以下几个方面:一是研发高效低耗的动力系统,例如燃料电池技术和氢能源技术的应用,使得汽车的能源利用效率得到了显著提升。
二是推广公共交通和共享交通模式,减少私家车的使用,以减少能源浪费。
三是优化交通系统,通过交通管制和路面改善等措施,提高交通流通效率,减少堵车和车辆的能源消耗。
这些创新的交通运输节能技术在减少交通能源消耗的同时,也有助于缓解交通拥堵和改善空气质量。
总结起来,随着科技的不断进步,节能降耗技术也在不断发展和创新。
从建筑节能到能源利用效率提升再到交通运输节能,各个领域都在努力寻找适应当下社会需求的节能降耗技术。
通过应用这些最新的技术,不仅可以减少能源的消耗,保护环境,还能够为人们提供更为舒适和宜居的生活空间。
中国钢铁企业烧结工序节能减排技术发展

中国钢铁企业烧结工序节能减排技术发展钢铁是全球经济的基础产品。
作为国民经济的支柱,钢铁工业为中国的快速增长做出了积极的贡献。
自2000年以来,中国的铁产量增长了408%,2016年已达7亿吨。
全球钢铁产量自二十一世纪以来也有所增加,但国外钢铁总产量仍维持在4.5亿吨左右。
中国钢铁产量的增长速率在2005年达到最高,2008年以后钢铁产量占全球产量的一半以上。
在钢铁行业淘汰落后产能以及价格因素的背景下,2014年中国的钢铁产量开始下降,2015年钢铁产量年增长率为负。
钢产量增长的同时,含铁炉料的产量和质量得到了快速发展。
2015年烧结矿产量达到10.08亿吨。
铁矿石烧结是一种典型的高耗能、高耗材且高污染的工业过程。
据报道,铁矿石烧结的能耗约占钢铁企业总能耗的6~10%。
烧结矿是高炉主要的含铁炉料之一,占高炉炉料结构的75%左右。
烧结工序总能耗的75~80%是矿物燃料,如焦粉和无烟煤。
矿物燃料的使用会产生大量温室气体,如CO,SOx,NOx和二噁英,它们是2钢铁工业主要的空气污染源。
因此,降低烧结能耗、减少环境污染、缓解能源短缺的问题变得突出。
图1二十一世纪全球和中国的铁和烧结矿产量:(a)全球和中国铁产量的变化;(b)中国在世界铁产量中的份额演变和中国铁产量的增长率;(c)中国烧结矿产量;(d)中国烧结工艺能耗。
图2中国烧结工艺能源结构长期以来,专家们一直致力于烧结工艺节能减排技术的研发并积累了大量的研究成果。
在过去的十年里,中国在烧结工序节能减排方面取得了实质性进展。
烧结过程的能耗从70 kgce/吨降至50 kgce/吨。
根据以往的研究成果,烧结工艺的节能技术主要集中在以下几个方面。
首先,使用更清洁和更高效的能源(例如半焦,生物质和天然气)来代替焦粉和煤,以此优化烧结燃料结构。
第二,在烧结过程中回收利用余热。
据统计,烧结过程的余热总量达50%,理论二次发电量为1.62 GJ/吨。
可以看出,烧结烟气余热和烧结矿显热的二次能源利用是烧结过程节能减排的重要方向。
- 1、下载文档前请自行甄别文档内容的完整性,平台不提供额外的编辑、内容补充、找答案等附加服务。
- 2、"仅部分预览"的文档,不可在线预览部分如存在完整性等问题,可反馈申请退款(可完整预览的文档不适用该条件!)。
- 3、如文档侵犯您的权益,请联系客服反馈,我们会尽快为您处理(人工客服工作时间:9:00-18:30)。
烧结工序节能降耗新技术发展趋势王 梁(中钢设备有限公司烧结部,北京100080)摘 要:通过分析节能降耗的意义和国内烧结能耗现状,从改善原料条件、回收利用及降低电耗方面总结了国内外常用烧结节能降耗的技术措施,并阐述了部分技术措施的实际运行效果;结合设计经验及考察部分烧结厂实际运行情况,通过分析部分设计和生产参数,探讨了近几年国内采用的烧结节能降耗技术及实际运行效果,提出了烧结节能降耗技术未来发展的建议。
关键词:烧结;节能;降耗文献标志码:A 文章编号:1006-9356(2015)12-0064-04Development tendency of new energy saving andconsumption reducing technology during sintering processWANG Liang(Sintering Engineering Department,Sinosteel Equipment and Engineering Co.,Ltd.,Beijing 100080,China)Abstract:Through the analysis of the significance of energy saving and consumption reducing as well as the presentsituation of sintering energy consumption in our country,sintering energy saving and consumption reducing technol-ogies commonly used at home and abroad are summarized from improving the raw material conditions,recycling andreducing power consumption,and the actual operating effect of some technical measures is expounded.Combinedwith the individual design experience and actual running condition in some sintering plants,the sintering energy sav-ing technologies used in our country in recent years and the actual operating effect are discussed by analyzing the de-sign of the plant and the production parameters.Moreover,some suggestions for the future development of the sin-tering energy consumption technology are put forward.Key words:sintering;energy saving;consumption reducing作者简介:王 梁(1979—),男,硕士,工程师; E-mail:254849151@qq.com; 收稿日期:2014-12-12 节能降耗是指加强用能管理,采取技术上可行、经济上合理以及环境和社会可以承受的措施,从能源生产到消费的各个环节,降低消耗,减少损失和污染物排放,有效、合理地利用能源。
节能降耗对国民经济的持续发展、技术的进步、保护自然资源和环境都具有深远的战略意义。
钢铁企业是能源消耗的大户,其中烧结能耗占10%~15%,采取有效措施最大幅度地降低烧结过程中的能源消耗具有重大意义。
1 国内烧结能耗现状中国在2010年公布的《钢铁企业节能设计规范》中明确说明烧结工序能耗设计指标应符合以下标准:电按当量值算时不小于300m2的大型烧结机,其能耗应不高于53kg/t(矿);180~300m2的中型烧结机不高于55kg/t(矿),但在实际生产时,由于能源条件、装备水平、自动化水平、操作水平等各种条件的限制其能耗会高于国家标准能耗参数。
所以在设计、生产中采取各种有效措施,最大幅度地降低烧结过程中的能耗指标对节能降耗有重大意义。
2 已成熟推广的节能降耗技术2.1 改善原料及混合料的条件2.1.1 强化原料及烧结混合料的混匀效果对于烧结而言,原料混匀能够使矿种结构稳定、粒度均匀,对于一些矿种较多,原料化学成分、粒度等波动较大的企业来说,原料混匀就显得尤为重要;在烧结的配料工艺中要配入燃料、熔剂、返矿等物料,将这些物料混匀能使烧结过程稳定进行、减少波动。
所以强化原料及烧结混合料的混匀效果能够使烧结过程便于控制、烧结矿成分稳定、有利于烧结能耗的降低[1-2]。
2.1.2 完善燃料破碎系统燃料破碎工艺设计中要确定正确的燃料使用制度和改善其粒度组成。
因为燃料过细使得烧结速度加快导致料层透气性下降;燃料过粗在布料过程中容易造成偏析,烧结时局部过熔而导致料层透气性变差。
所以减少小于0.5mm的过粉碎量和大于3mm的粗粒级以改善燃料在烧结料层的燃烧条件,对节能降耗有明显的效果。
另外有些企业利用燃料分加技术改变部分燃料在混料过程中的赋存形式,提高固体燃料的利用率[3]。
2.1.3 强化制粒强化制粒机的制粒效果,减少混合料中小于3mm粒级的含量,增加大于3mm粒级的含量,改善混合料的粒度组成,使混合料粒度趋于均匀,可明显改善烧结料层的透气性,增高料层,改善烧结矿强度,降低能耗。
表1是某厂将制粒机加长并将其角度适当调整后经制粒机后混合料粒级变化及固体燃料消耗变化3个月生产数据平均值与制粒机未改造前后3个月生产数据平均值对比。
表1 某厂制粒机改造前后混合料粒级变化及固体燃料消耗Table 1 Mixture gradation change and solid fuelconsumption before and after reforming pelletizer阶段粒度组成/%>1mm>3mm固体燃料消耗/(kg·t-1)改造前55 42 54.2改造后92 80 51.8 采用小球烧结工艺能改善烧结过程中料层的透气性且有利于厚料层烧结。
可以在二混中加入污泥水,强化制粒效果。
小球烧结工艺能改善燃料的赋存状态、减少残碳有利于燃烧反应的充分进行,能够提高烧结过程的热利用率和烧结矿的质量,减少固体燃料的消耗。
2.1.4 采用铺底料及厚料层烧结工艺烧结时在台车上铺一层经由成品整粒分级筛出的10~20mm粒度的烧结矿作为铺底料,厚度基本控制在40mm,这样可以提高料层在烧结过程中的透气性,减少烧结烟气的含尘量,同时提高台车以及篦条使用寿命。
某厂报表显示在采用铺底料之后固体燃料消耗比采用铺底料之前固体燃料消耗节省0.5%~1%。
厚料层烧结工艺是目前普遍采用的提高能耗利用率的节能措施。
当料层的厚度增加后烧结料层的蓄热能力提高,利用厚料层烧结中“自动蓄热”的作用,降低了配碳量,氧化物氧化放热的效果得到增强,使烧结料层从上到下保持稳定的高温,延长高温烧结时间,改善了烧结的条件。
同时在烧结过程中下层烧结矿可以获得更高的烧结温度,有利于更多液相的生成,可以有效提高烧结矿的强度,有利于烧结矿成品率的提高[4-7]。
另外厚料层烧结工艺可以结合偏析布料的方法,偏析布料可以很好地解决由于厚料层烧结时自动蓄热而造成的上下热量分布不均现象,可以使料层下部透气性好,上层透气性差,提高料层的整体透气性;有利于提高料层表面的烧结矿强度。
2.1.5 混合料预热工艺目前常见的混合料预热有在配料时加入生石灰、圆筒混合机和烧结机头混合料矿槽中通入蒸汽、利用热返矿等工艺。
预热混合料使混合料温提高,此部分显热可部分替代固体燃料的燃烧热;另外部分混合料预热工艺能够减少烧结过程中过湿层的影响,有利于改善料层的透气性。
表2是某厂混合料中配加石灰石时固体燃料消耗3个月生产数据平均值与混合料中配加生石灰前后3个月生产数据平均值对比,从表中及对该厂生产数据报表分析表明,配加生石灰后由于混合料料温提高且成品率提高,可使固体燃耗显著下降。
表3是某厂在二混和机头混合料矿槽增加蒸汽预热固体燃料消耗前后3个月生产数据平均值。
该厂为尽量防止料层过湿现象将混合料料温控制在70℃以上。
从表可以看出,在尽量避免料层过湿情况下预热混合料可显著降低固体燃料消耗。
表2 某厂混合料配加石灰石与生石灰固体燃料消耗Table 2 Solid fuel consumption before and afteradding limestone into mixture kg/t 烧结混合料配加生石灰前配加生石灰后固体燃料消耗55.3 51.8表3 某厂混合料增加蒸汽预热前后固体燃料消耗Table 3 Solid fuel consumption before and after usingvapor reheating mixture kg/t 烧结混合料加蒸汽前加蒸汽后固体燃料消耗54.3 50.82.1.6 控制混合料成分在烧结过程中配加部分一定量的添加剂,干预烧结过程,通过配料组份抑制或促使烧结过程中某些物化反应的进行。
改变混合料的化学成分。
添加含硼的物料,在烧结矿结晶时能与正硅酸钙形成固溶体,在冷却过程中不容易发生相变,可以降低烧结矿的粉化率。
完善低硅烧结工艺,低硅烧结能够改善烧结矿的冶金性能,降低高炉渣比。
多加入烧结时放热的物料,少加入烧结时耗热的物料,如由于碳酸盐加热时分解耗热,所以配料时可以配加生石灰等物料以取代碳酸盐熔剂。
加入助燃剂改善燃料的燃烧条件,提高燃料的燃尽率,降低烧结料的熔点。
加入增加烧结矿液相的的增强剂,抑制烧结矿的粉化现象,提高烧结矿强度降低返矿率。
2.2 回收利用2.2.1 余热回收利用烧结余热主要是指烧结烟气余热和烧结矿冷却机带出的烧结矿显热两部分,其排放的热量占能耗的40%左右。
充分利用好这部分热量将使烧结工序能耗明显降低。
目前这部分热量主要用于以下方面:预热混合料、余热发电、利用余热锅炉产生蒸汽或提供热水、预热点火炉助燃空气、预热点火炉用煤气、点火炉保温段及烧结矿保温、热风烧结、小球团烧结干燥、精矿解冻等。
目前运用最多的余热回收是烧结矿冷却机带出的烧结矿显热产生蒸汽。
从考察搜集的数据分析,每吨烧结矿产生的蒸汽量在90~160kg左右。
2.2.2 资源回收利用钢铁企业存在大量的含碳、铁、镍、铬等工业废料,在烧结矿中合理地配入这些物料不仅可以达到节能降耗的目的,还回收了资源,减少了污染物的排放保护环境。