汽车板簧冲压成型生产线中英文对照V0
冲压词汇中英文-最新版本
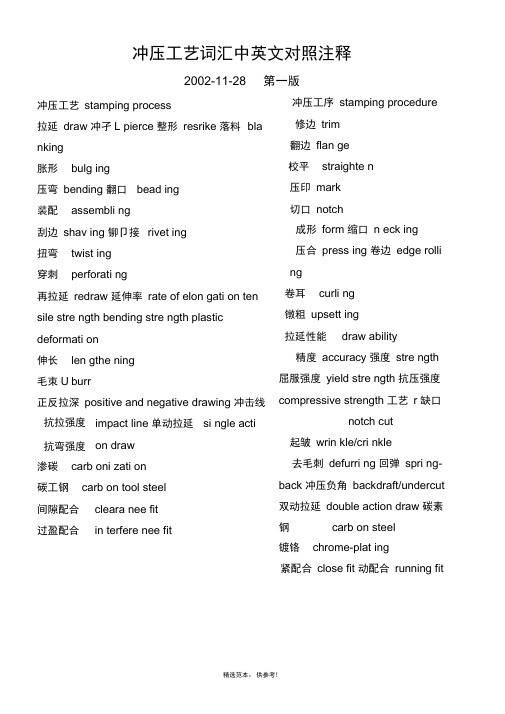
冲压工艺词汇中英文对照注释2002-11-28第一版冲压工艺 stamping process拉延 draw 冲孑L pierce 整形 resrike 落料 blanking胀形 bulg ing压弯 bending 翻口 bead ing 装配 assembli ng刮边 shav ing 铆卩接 rivet ing 扭弯 twist ing 穿刺 perforati ng再拉延 redraw 延伸率 rate of elon gati on tensile stre ngth bending stre ngth plastic deformati on伸长 len gthe ning 毛朿U burr正反拉深 positive and negative drawing 冲击线 impact line 单动拉延 si ngle acti on draw 渗碳 carb oni zati on 碳工钢 carb on tool steel 间隙配合 cleara nee fit 过盈配合 in terfere nee fit抗拉强度 抗弯强度 冲压工序 stamping procedure 修边 trim 翻边 flan ge 校平 straighte n 压印 mark 切口 notch成形 form 缩口 n eck ing 压合 press ing 卷边 edge rolling卷耳 curli ng 镦粗 upsett ing 拉延性能 draw ability 精度 accuracy 强度 stre ngth 屈服强度 yield stre ngth 抗压强度compressive strength 工艺 r 缺口notch cut起皱 wrin kle/cri nkle去毛刺 defurri ng 回弹 spri ng-back 冲压负角 backdraft/undercut双动拉延 double action draw 碳素钢 carb on steel镀铬 chrome-plat ing紧配合 close fit 动配合 running fit系数coefficient 同心度concentricity曲柄crank 筒形件拉延cup drawing开卷机decoiler 深拉延deep drawing变形程度degree of deformation 凹坑凹痕dent模具寿命die life 双排冲double-row layout拉延系数draw rate 凸耳earing弹性回复elastic recovery 疲劳裂纹fatigue crack.> A r r —r. r -疲劳破坏fatigue fracture 成形极限forming limit加热炉furnace 砂轮grinding wheel灰口铁grey cast iron 中性层neutral layern-value n值工艺卡process chart拉毛划痕scoring 无废料排样side-by-side layout 搭边bridge 材料利用率stock utilization 加工硬化strain hardening带钢ribbon steel 轧制方向rolling direction材料利用率material utilization 步距pitch冲压模具词汇中英文对照注释2002-11-28 第一版工程图die layout 工序working procedure冲压方向pressing direction 送料方向feeding direction送料高度loading height 取件高度unloading height毛坯stock blank 调试tryout展开prolongation 条料band排样stock layout 片料sheet凸模轮廓线punch profile/line 凹模入口线die opening line 压料面binder(surface) 拉延槛lock step拉延筋draw bead 拉延深度draw depth拉延力draw tonnage 压边力binder tonnage装配图assembly drawing 零件图detail drawing剖面图section view 局部视图sketch view基准点datum mark 中心线central line制件名称part name 制件号part number零件detail part 工件work piece直径diameter 半径radius制件finished part 备件spare part易损件quick-wear part 模具维修die maintenance调试try-out 废料scrap宽度width 长度length高度height 厚度thickness公差tolerance 尺寸dimension圆孔round hole 长圆孔elongated hole/oblong 方孔square 异形孔irregular hole凸点weld embossment压床press 气垫air cushion滑块ram 闭合高度shut height内滑块inner slide 外滑块outerd slide模柄shank 托杆ejector/cushion pin平衡托杆balancing pin 自动夹紧automatic clamp location 垫板bolster T 型槽T groove材料material 铸铁cast iron铸钢cast steel 铸造镶块cast sectional镶块(钢镶件) insert 镶块(凹模)sectional die工具钢tool steel 合金钢alloy-steel上模upper die 下模lower/bottom die模架die set 模座shoe上底板upper plate/shoe 导柱guide pin下底板lower plate/shoe 导套guide pin bushing凸模punch 导向块guide block凹模die/matrix 导正销pilot压料圈blank holder 间隙clearance顶出器knockout/pad 接缝空刀joint relief定位块locator 挡料销stop pin废料刀scrap cutter 支架bracket缓冲器bumper block 弹簧spring导板wear(guide) plate 自润导板self-lube plate空开面relief/relieve 天窗window plate废料槽chute 废料滑板scrap shedding废料盒storage box 暗键blind key防护板guard 铭牌name plate橡皮rubber 加强筋rib键key 键槽keyway侧销retainer pin 安全侧销safety retainer pin 安全挡板securing plate 顶销pushing-out pin退料板/器stripper 回程return stroke预压弹簧pre-compressed spring 复位弹簧return spring到位标记bottom mark 压印器bottoming marker 压字器emboss button 压字标记marker凸模固定板punch holder/retainer 定位块l o cator反侧块back-up/heel block 侧向力lateral force/thrust观察孔/排水(气)孔vent 切刀深度trim entrance气缸cylinder 氮气缸nitrogen gas cylinder 滚轮滑道roller carrier 橡胶滚轮rubber roller定位板(拉延用)nest guide 定位检测器panel input detector 传感器sensor 行程stroke, travel定位销locating pilot pin 安全凸耳safety lug调整垫块distance plate 平衡块equalizer block铸造倒角cast bevel 铸造凸台cast boss聚胺酯存放限制器合件 urethane stock block sets /storage block 行程限制器 stopblock模具标牌 die information tag 托杆标牌air pin tag送料装置 feeding mechanism 送 料(进料) feed 泡沫模型 foam model 数控加工 nc machining 车削 lathe 数控铣 nc mill 磨削 grind钻孔 drill 耐磨性 wear-resistance 石墨 graphite极进模 progressive die 复合模compound die热处理 heat treatment 淬火quenching/hardenin g火焰淬火flame hardening 局部淬火 local hardening 正火normalizing退火 annealing凹 模 button die 球锁凸模 ball-lock punch 废料弹顶器 Scrap stripper 通过孔 access core 角 钢 angle iron 斜 楔cam 驱动楔 cam driver 斜楔座 cam adapter 咬合(预导向) engagement安全区 safety area 起重棒 lift pin 快换冲头 quick exchanging punch 凸 V 型导板 male v block 螺 钉 bolt 内六角螺钉 sockethead screw 带肩螺钉 sockethead shoulder screw 柱 销 dowel pin带肩凸模 shoulder punch 弹簧定位销 spring guide pin 脱件器shedder pin 减轻孔 Lightening core 双向斜楔 filler slide cam 吊楔 aerial/flying cam 滑 楔 camslide 固定座 die adapter 斜楔导板 cam slide gibC/P 点 coordinate point 铸入式起重棒 cast-in steel lug 压板台fastening slot 凹 V 型导板 female u block 螺 纹 screw 平头十字螺钉 flathead screw 外六角螺钉 hexagon nut 真空吸盘 vacuum【本文档内容可以自由复制内容或自由编辑修改内容期待你的好评和 关注,我们将会做得更好】渗 氮 nitriding硬 度 hardness 布氏硬度Brielle hardness 主模型 master model夹 具 jig调质处理 refining维氏硬度 Vickers hardness 洛氏硬度 Rockwell hardness 检 具checking fixture 加工余量 machine allowance。
STAMPING AND SHEET METAL FORMING——冲压成形和板材冲压【中英文
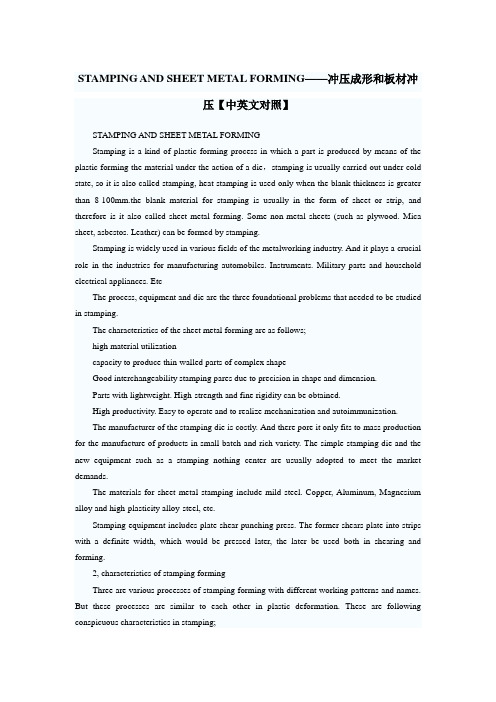
STAMPING AND SHEET METAL FORMING——冲压成形和板材冲压【中英文对照】STAMPING AND SHEET METAL FORMINGStamping is a kind of plastic forming process in which a part is produced by means of the plastic forming the material under the action of a die,stamping is usually carried out under cold state, so it is also called stamping, heat stamping is used only when the blank thickness is greater than 8-100mm.the blank material for stamping is usually in the form of sheet or strip, and therefore is it also called sheet metal forming. Some non-metal sheets (such as plywood. Mica sheet, asbestos. Leather) can be formed by stamping.Stamping is widely used in various fields of the metalworking industry. And it plays a crucial role in the industries for manufacturing automobiles. Instruments. Military parts and household electrical appliances. EtcThe process, equipment and die are the three foundational problems that needed to be studied in stamping.The characteristics of the sheet metal forming are as follows;high material utilizationcapacity to produce thin-walled parts of complex shapeGood interchangeability stamping pares due to precision in shape and dimension.Parts with lightweight. High-strength and fine rigidity can be obtained.High productivity. Easy to operate and to realize mechanization and autoimmunization.The manufacturer of the stamping die is costly. And there pore it only fits to mass production for the manufacture of products in small batch and rich variety. The simple stamping die and the new equipment such as a stamping nothing center are usually adopted to meet the market demands.The materials for sheet metal stamping inc lude mild steel. Copper, Aluminum, Magnesium alloy and high-plasticity alloy-steel, etc.Stamping equipment includes plate shear punching press. The former shears plate into strips with a definite width, which would be pressed later, the later be used both in shearing and forming.2, characteristics of stamping formingThree are various processes of stamping forming with different working patterns and names. But these processes are similar to each other in plastic deformation. These are following conspicuous characteristics in stamping;The force per unit area perpendicular to the blank surface is not large but is enough to causethe material plastic deformation it is much less than the inner stresses on the plate plane directions. In most cases stamping forming can be treated approximately as that of the plane stress state to simplify vastly the theoretical analysis and calculation of process parameters.Due to the small relative thickness, the anti-instability capability of the blank is weak under compressive stress. As a result, the stamping process is difficult to proceed successfully without using the anti-instability device; therefore the varieties of the stamping processes dominated bytensile are more than dominated by compressive stress.During stamping forming the inner stress of the blank is equal toor sometimes less than the yield stress of the material in this point, the stamping is different from the bulk forming, during stamping forming, the influence of the hydrostatic pressure of the stress state in the bulk forming. In some circumstances, such influence may be neglected. Even in the case when this influence should be considered, the treating method is also different from that of bulk forming.In stamping forming. The restrain action of the die blank is not severs as in the case of the bulk forming, in bulk forming. The constraint forming is preceded by the die exactly the same shape of the part. Whereas in stamping. In most cases. The blank has a certain degree of freedom. Only one surface of the blank contacts with the die. In some extra cases, such as the forming of the blank on the deforming zone contact the die.The deformation in these regions is and controlled by the die applying an external force to its adjacent area.Due to the characteristics of stamping deformation and mechanics mentioned stamping technique is different form the bulk metal forming;The importance or the strength and the rigidity of die in stamping forming that in bulk forming because can be formed without applying large area on its surface. Instead. The simple die and the pneumatic forming are developed.Due to the plane stress or simple strain state in comparison with research on deformation or force and power parameters has been done, stamping forming can be performed by more reasonable scientific methods, based on the real time analysis on the sheet metal and stamping parameters by means of modern testing apparatus. Research on the intellectualized control of stamping proceedingIt is shown that there is a close between stamping materials. The research on the properties of the stamping forming, that is, shape stability on the properties of the forming that is, shape stability, has because a key point in stamping technology development, the technique of iron and steel industry, and provides a increasing sheet metal quality.3. CA TEGORIES OF STAMPING FORMINGMany deformation processes can be done by stamping, the basic processes can be dividedinto two kinds, cutting and forming.Cutting is a shearing process that one part of the blank is cut form the other. It mainly includes blanking, punching, trimming, parting and shaving, where punching and blanking are the most widely used. Forming is a process that of the blank has some displacement form the other. It mainly includes deep drawing, bending, local forming, Bulging, flanging necking, sizing and spinning.In substance, stamping forming is such that the plastic deformation occurs in the deformation zone of stamping blank caused by the external force. The stress state and deformation characteristic of the deformation zone are the basic factors to decide the properties of the stamping forming. Based on the stress state and deformation characteristics of the deformation zone, the forming methods 网can divided into several categories with the same forming properties and be studied systematically.The deformation zone in almost all of stamping forming is in the plane stress state. Usually there is no force or only small force applied on the blank surface. When is assumed that the stress perpendicular to the blank surface equals to zero, two principal stresses perpendicular to each other and act on the blank surface, the stress state and the deformation characteristics of the deformation of stamping forming can be denoted by the points in the coordinates of the plane principal stresses and the coordinates of the corresponding plane principal stains4. RA W MA TERIALS FOR STAMPING FORMINGThere are a lot of raw materials used in stamping forming and the properties of these materials may have large difference. The stamping forming can be succeeded only by determining the stamping method, the forming the relationships between the material properties for stamping forming is as follows;Definition of stamping property of the material.Method to judge the stamping property of the material, find parameters to express the definitely material property of the stamping forming. Establish the relationship between the property parameters and the practical stamping forming. And investigate the methods of the property paramters.Establish the materials for stamping forming mainly include various metals and nonmetal plate. Sheet metal includes both ferrous and nonferrous metals. The most widely used materials are steel, stainless steel, aluminum alloy and various composite metal plates5. STAMPING FORMING PROPERTY OF SHEET METAL AND ITS ASSESSING METHODThere are direct and indirect testing methods to assess the stamping property of the sheetmetal.Practicality stamping test the most direct method to assess stamping forming property of the sheet meals. This test is done exactly in the same condition as actual production by using the practical and dies. Surely, this test result is most reliable. But this kind of assessing method is not comprehensively applicable. And cannot be shared as a commonly used standard between factories.The simulation test is a kind of assessing method that after simplifying and summing up actual stamping forming methods, as well as eliminating trivial factors, the stamping properties of the sheet metal are assessed. Based on simplified axial-symmetric forming method under the same deformation and states between the seating plate and actual forming states. In order to guarantee the reliability and generality of simulation results, a lot of factors are regulated in detail. Such as the shape and dimension of tools for test, blank dimension and testing conditions.Indirect testing method is also called testing methods its characteristic is to connect analysis and research on fundamental property and principle of the metal in actual stamping forming. And then to establish forming property. Because the shape and dimension of the specimen/the deformation characteristics and stress form the indirect test are different from those of the actual one. So. The results obtained form the indirect not the stamping forming parameters. But are the fundamental parameters that be used to represent the stamping forming property of the sheet metal。
模具-冲压及工序英语用语

组装、冲压、喷漆等专业词汇Assembly line组装线Layout布置图Conveyer流水线物料板Rivet table拉钉机Rivet gun拉钉枪Screw driver起子Electric screw driver电动起子Pneumatic screw driver气动起子worktable 工作桌OOBA开箱检查fit together组装在一起fasten锁紧(螺丝)fixture 夹具(治具)pallet栈板barcode条码barcode scanner条码扫描器fuse together熔合fuse machine热熔机repair修理operator作业员QC品管supervisor 课长ME制造工程师MT制造生技cosmetic inspect外观检查inner parts inspect内部检查thumb screw大头螺丝lbs. inch镑、英寸EMI gasket导电条front plate前板rear plate后板chassis基座bezel panel面板power button电源按键reset button重置键Hi-pot test of SPS高源高压测试V oltage switch of SPS电源电压接拉键sheet metal parts 冲件plastic parts塑胶件SOP制造作业程序material check list物料检查表work cell工作间trolley台车carton纸箱sub-line支线left fork叉车personnel resource department人力资源部production department生产部门planning department企划部QC Section品管科stamping factory冲压厂painting factory烤漆厂molding factory成型厂common equipment常用设备uncoiler and straightener整平机punching machine 冲床robot机械手hydraulic machine油压机lathe车床planer |'plein|刨床miller铣床grinder磨床driller??床linear cutting线切割electrical sparkle电火花welder电焊机staker=reviting machine铆合机position职务president董事长general manager总经理special assistant manager特助factory director厂长department director部长deputy manager | =vice manager副理section supervisor课长deputy section supervisor =vice sectionsuperisor副课长group leader/supervisor组长line supervisor线长assistant manager助理to move, to carry, to handle搬运be put in storage入库pack packing包装to apply oil擦油to file burr 锉毛刺final inspection终检to connect material接料to reverse material 翻料wet station沾湿台Tiana天那水cleaning cloth抹布to load material上料to unload material卸料to return material/stock to退料scraped |'skræpid|报废scrape ..v.刮;削deficient purchase来料不良manufacture procedure制程deficient manufacturing procedure制程不良oxidation |' ksi'dein|氧化scratch刮伤dents压痕defective upsiding down抽芽不良defective to staking铆合不良embedded lump镶块feeding is not in place送料不到位stamping-missing漏冲production capacity生产力education and training教育与训练proposal improvement提案改善spare parts=buffer备件forklift叉车trailer=long vehicle拖板车compound die合模die locker锁模器pressure plate=plate pinch压板bolt螺栓name of a department部门名称administration/general affairs dept总务部automatic screwdriver电动启子thickness gauge厚薄规gauge(or jig)治具power wire电源线buzzle蜂鸣器defective product label不良标签identifying sheet list标示单screwdriver holder起子插座pedal踩踏板stopper阻挡器flow board流水板hydraulic handjack油压板车forklift叉车pallet栈板glove(s)手套glove(s) with exposed fingers割手套thumb大拇指forefinger食指midfinger中指ring finger无名指little finger小指band-aid创可贴iudustrial alcohol工业酒精alcohol container沾湿台head of screwdriver起子头sweeper扫把mop拖把vaccum cleaner吸尘器rag 抹布garbage container灰箕garbage can垃圾箱garbage bag垃圾袋chain链条jack升降机production line流水线chain链条槽magnetizer加磁器lamp holder灯架to mop the floor拖地to clean the floor扫地to clean a table擦桌子air pipe 气管packaging tool打包机packaging打包missing part漏件wrong part错件excessive defects过多的缺陷critical defect极严重缺陷major defect主要缺陷minor defect次要缺陷not up to standard不合规格dimension/size is a little bigger尺寸偏大(小)cosmetic defect外观不良slipped screwhead/slippery screw head螺丝滑头slipped screwhead/shippery screwthread滑手speckle斑点mildewed=moldy=mouldy发霉rust生锈deformation变形burr(金属)flash(塑件)毛边poor staking铆合不良excesssive gap间隙过大grease/oil stains油污inclusion杂质painting peel off脏污shrinking/shrinkage缩水mixed color杂色scratch划伤poor processing 制程不良poor incoming part事件不良fold of pakaging belt打包带折皱painting make-up补漆discoloration羿色water spots水渍polishing/surface processing表面处理exposed metal/bare metal金属裸露lack of painting烤漆不到位safety安全quality品质delivery deadline交货期cost成本engineering工程die repair模修enterprise plan = enterprise expansionprojects企划QC品管die worker模工production, to produce生产equipment设备to start a press开机stop/switch off a press关机classification整理regulation整顿cleanness清扫conservation清洁culture教养qualified products, up-to-gradeproducts良品defective products, not up-to-gradeproducts不良品waste废料board看板feeder送料机sliding rack滑料架defective product box不良品箱die change 换模to fix a die装模to take apart a die拆模to repair a die修模packing material包材basket蝴蝶竺plastic basket胶筐isolating plate baffle plate; barricade隔板carton box纸箱to pull and stretch拉深to put material in place, to cut material,to input落料to impose lines压线to compress, compressing压缩character die字模to feed, feeding送料transportation运输(be)qualfied, up to grade合格not up to grade, not qualified不合格material change, stock change材料变更feature change 特性变更evaluation评估prepare for, make preparations for 准备parameters参数rotating speed, revolution转速manufacture management制造管理abnormal handling异常处理production unit生产单位lots of production生产批量steel plate钢板roll material卷料manufacture procedure制程operation procedure作业流程to revise, modify修订to switch over to, switch---to throw--over switching over切换engineering, project difficulty工程瓶颈stage die工程模automation自动化to stake, staking, reviting铆合add lubricating oil加润滑油shut die架模shut height of a die架模高度analog-mode device类模器die lifter举模器argon welding氩焊vocabulary for stamping冲压常词汇stamping, press冲压punch press, dieing out press冲床uncoiler & strainghtener整平机feeder送料机rack, shelf, stack料架cylinder油缸robot机械手taker取料机conveyer belt输送带transmission rack输送架top stop上死点bottom stop下死点one stroke一行程inch寸动to continue, cont.连动to grip(material)吸料location lump, locating piece, blockstop 定位块reset复位smoothly顺利dent压痕scratch刮伤deformation变形filings铁削to draw holes抽孔inquiry, search for查寻to stock, storage, in stock库存receive领取approval examine and verify审核processing, to process加工delivery, to deliver 交货to return delivenry to.to send delinery backto retrn of goods退货registration登记registration card登记卡to control管制to put forward and hand in提报safe stock安全库存acceptance = receive验收to notice通知application form for purchase请购单consume, consumption消耗to fill in填写abrasion磨损reverse angle = chamfer倒角character die字模to collect, to gather收集failure, trouble故障statistics统计demand and supply需求career card履历卡to take apart a die卸下模具to load a die装上模具to tight a bolt拧紧螺栓to looser a bolt拧松螺栓to move away a die plate移走模板easily damaged parts易损件standard parts标准件breaking.(be)broken,(be)cracked 断裂to lubricate润滑common vocabulary for dieengineering模具工程常用词汇die 模具figure file, chart file图档cutting die, blanking die冲裁模progressive die, follow (-on)die连续模compound die复合模punched hole冲孔panel board镶块to cutedges=side cut=side scrap切边to bending折弯to pull, to stretch拉伸Line streching, line pulling线拉伸engraving, to engrave刻印upsiding down edges翻边to stake铆合designing, to design设计design modification设计变化die block模块folded block折弯块sliding block滑块location pin定位销lifting pin顶料销die plate, front board模板padding block垫块stepping bar垫条upper die base上模座lower die base下模座upper supporting blank上承板upper padding plate blank上垫板spare dies模具备品spring 弹簧bolt螺栓document folder文件夹file folder资料夹to put file in order整理资料spare tools location手工备品仓first count初盘人first check初盘复棹人second count 复盘人second check复盘复核人equipment设备waste materials废料work in progress product在制品casing = containerazation装箱quantity of physical invetory second count 复盘点数量quantity of customs count会计师盘,点数量the first page第一联filed by accounting department for reference会计部存查end-user/using unit(department)使用单位summary of year-end physical inventory bills年终盘点截止单据汇总表bill name单据名称This sheet and physical inventory list will be sent to accounting department together (Those of NHK will be sent to financial department)本表请与盘点清册一起送会计部-(NHK厂区送财会部)Application status records of year-end physical inventory List andphysical inventory card 年终盘点卡与清册使用-状况明细表blank and waste sheet NO.空白与作废单号plate电镀mold成型material for engineering mold testing工程试模材料not included in physical inventory不列入盘点sample样品incoming material to be inspected进货待验description品名steel/rolled steel钢材material statistics sheet物料统计明细表meeting minutes会议记录meeting type 会别distribution department分发单位location地点chairman主席present members出席人员subject主题conclusion结论decision items决议事项responsible department负责单位pre-fixed finishing date预定完成日approved by / checked by / prepared by核准/审核/承办PCE assembly production schedulesheetPCE组装厂生产排配表model机锺work order工令revision版次remark备注production control confirmation生产确认checked by初审approved by核准department部门stock age analysis sheet库存货龄分析表on-hand inventory现有库存available material良品可使用obsolete material良品已呆滞to be inspected or reworked待验或重工total合计cause description原因说明part number/ P/N 料号type形态item/group/class类别quality品质prepared by制表notes说明year-end physical inventory differenceanalysis sheet年终盘点差异分析表physical inventory盘点数量physical count quantity帐面数量difference quantity差异量cause analysis原因分析raw materials原料materials物料finished product成品semi-finished product半成品packing materials包材good product/accepted goods/ acceptedparts/good parts良品defective product/non-good parts不良品disposed goods处理品warehouse/hub仓库on way location在途仓oversea location海外仓spare parts physical inventory list备品盘点清单spare molds location模具备品仓skid/pallet栈板tox machine自铆机wire EDM线割EDM放电机coil stock卷料sheet stock片料tolerance工差score=groove压线cam block滑块pilot导正筒trim剪外边pierce剪内边drag form压锻差pocket for the punch head挂钩槽slug hole废料孔feature die公母模expansion dwg展开图radius半径shim(wedge)楔子torch-flame cut火焰切割set screw止付螺丝form block折刀stop pin定位销round pierce punch=die button圆冲子shape punch=die insert异形子stock locater block定位块under cut=scrap chopper清角active plate活动板baffle plate挡块cover plate盖板male die公模female die母模groove punch压线冲子air-cushion eject-rod气垫顶杆spring-box eject-plate弹簧箱顶板bushing block衬套insert 入块club car高尔夫球车capability能力parameter参数factor系数phosphate皮膜化成viscosity涂料粘度alkalidipping脱脂main manifold主集流脉bezel斜视规blanking穿落模dejecting顶固模demagnetization去磁;消磁high-speed transmission高速传递heat dissipation热传rack上料degrease脱脂rinse水洗alkaline etch龄咬desmut剥黑膜D.I. rinse纯水次Chromate铬酸处理Anodize阳性处理seal封孔revision版次part number/P/N料号good products良品scraped products报放心品defective products不良品finished products成品disposed products处理品barcode条码flow chart流程表单assembly组装stamping冲压molding成型spare parts=buffer备品coordinate座标dismantle the die折模auxiliary fuction辅助功能poly-line多义线heater band 加热片thermocouple热电偶sand blasting喷沙grit 砂砾derusting machine除锈机degate打浇口dryer烘干机induction感应induction light感应光response=reaction=interaction感应ram连杆edge finder巡边器concave凸convex凹short射料不足nick缺口speck瑕??shine亮班splay 银纹gas mark焦痕delamination起鳞cold slug冷块blush 导色gouge沟槽;凿槽satin texture段面咬花witness line证示线patent专利grit沙砾granule=peuet=grain细粒grit maker抽粒机cushion缓冲magnalium镁铝合金magnesium镁金metal plate钣金lathe车mill锉plane刨grind磨drill铝boring镗blinster气泡fillet镶;嵌边through-hole form通孔形式voller pin formality滚针形式cam driver铡楔shank摸柄crank shaft曲柄轴augular offset角度偏差velocity速度production tempo生产进度现状torque扭矩spline=the multiple keys花键quenching淬火tempering回火annealing退火carbonization碳化alloy合金tungsten high speed steel钨高速的moly high speed steel钼高速的organic solvent有机溶剂bracket小磁导liaison联络单volatile挥发性resistance电阻ion离子titrator滴定仪beacon警示灯coolant冷却液crusher破碎机模具工程类plain die简易模pierce die冲孔模forming die成型模progressive die连续模gang dies复合模shearing die剪边模riveting die铆合模pierce冲孔forming成型(抽凸,冲凸) draw hole抽孔bending折弯trim切边emboss凸点dome凸圆semi-shearing半剪stamp mark冲记号deburr or coin压毛边punch riveting冲压铆合side stretch侧冲压平reel stretch卷圆压平groove压线blanking下料stamp letter冲字(料号) shearing剪断tick-mark nearside正面压印tick-mark farside反面压印冲压名称类extension dwg展开图procedure dwg工程图die structure dwg模具结构图material材质material thickness料片厚度factor系数upward向上downward向下press specification冲床规格die height range适用模高die height闭模高度burr毛边gap间隙weight重量total wt.总重量punch wt.上模重量五金零件类inner guiding post内导柱inner hexagon screw内六角螺钉dowel pin固定销coil spring弹簧lifter pin顶料销eq-height sleeves=spool等高套筒pin销lifter guide pin浮升导料销guide pin导正销wire spring圆线弹簧outer guiding post外导柱stop screw止付螺丝located pin定位销outer bush外导套模板类top plate上托板(顶板)top block上垫脚punch set上模座punch pad上垫板punch holder上夹板stripper pad脱料背板up stripper上脱料板male die公模(凸模)feature die公母模female die母模(凹模)upper plate上模板lower plate下模板die pad下垫板die holder下夹板die set下模座bottom block下垫脚bottom plate下托板(底板)stripping plate内外打(脱料板)outer stripper外脱料板inner stripper内脱料板lower stripper下脱料板零件类punch冲头insert入块(嵌入件)deburring punch压毛边冲子groove punch压线冲子stamped punch字模冲子round punch圆冲子special shape punch异形冲子bending block折刀roller滚轴baffle plate挡块located block定位块supporting block for location定位支承块air cushion plate气垫板air-cushion eject-rod气垫顶杆trimming punch切边冲子stiffening rib punch = stinger 加强筋冲子ribbon punch压筋冲子reel-stretch punch卷圆压平冲子guide plate定位板sliding block滑块sliding dowel block滑块固定块active plate活动板lower sliding plate下滑块板upper holder block上压块upper mid plate上中间板spring box弹簧箱spring-box eject-rod弹簧箱顶杆spring-box eject-plate弹簧箱顶板bushing bolck衬套cover plate盖板guide pad导料块塑件&模具相关英文compre sion molding压缩成型flash mold溢流式模具plsitive mold挤压式模具split mold分割式模具cavity型控母模core模心公模taper锥拔leather cloak仿皮革shiver饰纹flow mark流痕welding mark溶合痕post screw insert螺纹套筒埋值self tapping screw自攻螺丝striper plate脱料板piston活塞cylinder汽缸套chip细碎物handle mold手持式模具移转成型用模具encapsulation molding低压封装成型射出成型用模具two plate两极式(模具)well type蓄料井insulated runner绝缘浇道方式hot runner热浇道runner plat浇道模块valve gate阀门浇口band heater环带状的电热器spindle阀针spear head刨尖头slag well冷料井cold slag冷料渣air vent排气道h=0.02~0.05mmw=3.2mmL=3~5mm welding line熔合痕eject pin顶出针knock pin顶出销return pin回位销反顶针sleave套筒stripper plate脱料板insert core放置入子runner stripper plate浇道脱料板guide pin导销eject rod (bar)(成型机)顶业捧subzero深冷处理three plate三极式模具runner system浇道系统stress crack应力电裂orientation定向sprue gate射料浇口,直浇口nozzle射嘴sprue lock pin料头钩销(拉料杆)slag well冷料井side gate侧浇口edge gate侧缘浇口tab gate搭接浇口film gate薄膜浇口flash gate闸门浇口slit gate缝隙浇口fan gate扇形浇口dish gate因盘形浇口H=F=1/2t~1/5tT=2.5~3.5mmdiaphragm gate隔膜浇口ring gate环形浇口subarine gate潜入式浇口tunnel gate隧道式浇口pin gate针点浇口Φ0.8~1.0mmRunner less无浇道(sprue less)无射料管方式long nozzle延长喷嘴方式sprue浇口;溶渣品质人员名称类QC quality control 品质管理人员FQC final quality control 终点品质管制人员IPQC in process quality control制程中的品质管制人员OQC output quality control 最终出货品质管制人员IQC incoming quality control 进料品质管制人员TQC total quality control 全面质量管理POC passage quality control 段检人员QA quality assurance 质量保证人员OQA output quality assurance 出货质量保证人员QE quality engineering 品质工程人员品质保证类FAI first article inspection 新品首件检查FAA first article assurance 首件确认TVR tool verification report 模具确认报告3B 3B 模具正式投产前确认CP capability index 能力指数CPK capability index of process 模具制程能力参数SSQA standardized supplier quality合格供应商品质评估OOBA out of box audit 开箱检查QFD quality function deployment品质机能展开FMEA failure model effectivenessanalysis 失效模式分析8 disciplines 8项回复内容FA final audit 最後一次稽核CAR corrective action request 改正行动要求corrective action report 改正行动报告FQC运作类AQL Acceptable Quality Level 运作类允收品质水准S/S Sample size 抽样检验样本大小ACC Accept 允收REE Reject 拒收CR Critical 极严重的MAJ Major 主要的MIN Minor 轻微的AOQ Average Output Quality 平均出厂品质AOQL Average Output Quality Level 平均出厂品质Q/R/S Quality/Reliability/Service 品质/可靠度服务MIL-STD Military-Standard 军用标准S I-S IV Special I-Special IV 特殊抽样水准等级P/N Part Number 料号L/N Lot Number 特采AOD Accept On Deviation 特采UAI Use As It 首件检查报告FPIR First Piece Inspection Report 百万分之一PPM Percent Per Million 批号制程统计品管专类SPC Statistical Process Control 统计制程管制SQC Statistical Quality Control 统计品质管制R Range 全距AR Averary Range 全距平均值UCL Upper Central Limit 管制上限LCL Lower Central Limit 管制下限MAX Maximum 最大值MIN Minimum 最小值GRR Gauge Reproducibility&Repeatability 量具之再制性及重测性判断量可靠与否DIM Dimension 尺寸DIA Diameter 直径FREQ Frequency 频率N Number 样品数其它品质术语类QCC Quality Control Circle 品质圈QIT Quality Improvement Team 品质改善小组PDCA Plan Do Check Action 计划执行检查总结ZD Zero Defect 零缺点QI Quality Improvement 品质改善QP Quality Policy 目标方针TQM Total Quality Management全面品质管理MRB Material Reject Bill 退货单LQL Limiting Quality Level 最低品质水准RMA Return Material Audit 退料认可QAN Quality Amelionrate Notice品质改善活动ADM Absolute DimensionMeasuremat 全尺寸测量QT Quality Target 品质目标7QCTools 7 Quality Controll Tools品管七大手法通用之件类ECN Engineering Change Notes 工程变更通知(供应商)ECO Engineering Change Order 工程改动要求(客户)PCN Process Change Notice 工序改动通知PMP Product Management Plan 生产管制计划SIP Specification In Process 制程检验规格SOP Standard Operation Procedure制造作业规范IS Inspection Specification 成品检验规范BOM Bill Of Material 物料清单PS Package Specification 包装规范SPEC Specification 规格DWG Drawing 图面系统文件类QC Quality System 品质系统ES Engineering Standarization 工程标准CGOO China General PCE龙华厂文件H Huston (美国)休斯敦C Compaq (美国)康伯公司C China 中国大陆A Assembly 组装(厂)S Stamping 冲压(厂)P Painting 烤漆(厂)I Intel 英特尔公司T TAIWAN 台湾IWS International WorkmanStandard 工艺标准ISO International StandardOrganization 国际标准化组织GS General Specification 一般规格CMCS C-China M-ManufactC-Compaq S-Stamping Compaq产品在龙华冲压厂制造作业规范CQCA Q-Quality A-AssemblyCompaq产品在龙华组装厂品管作业规范CQCP P-Painting Compaq产品在龙华烤漆厂品管作业规范部类PMC Production & MaterialControl 生产和物料控制PPC Production Plan Control 生产计划控制MC Material Control 物料控制ME Manafacture Engineering 制造工程部PE Project Engineering 产品工程部A/C Accountant Dept 会计部P/A Personal & Administration 人事行政部DC Document Center 资料中心QE Quality Engineering 品质工程(部)QA Quality Assurance 品质保证(处)QC Quality Control 品质管制(课) PD Product Department 生产部LAB Labratry 实验室IE Industrial Engineering 工业工程R&D Research & Design 设计开发部P Painting 烤漆(厂)A Asssembly 组装(厂)S Stamping 冲压(厂)生产类PCS Pieces 个(根,块等)PRS Pairs 双(对等)CTN Carton 卡通箱PAL Pallet/skid 栈板PO Purchasing Order 采购订单MO Manufacture Order 生产单D/C Date Code 生产日期码ID/C Identification Code (供应商)识别码SWR Special Work Request 特殊工作需求L/N Lot Number 批号P/N Part Number 料号其它OEM Original Equipment Manufacture 原设备制造PCE Personal Computer Enclosure 个人电脑外设PC Personal Computer 个人电脑CPU Central Processing Unit 中央处理器SECC SECC` 电解片SGCC SGCC 热浸镀锌材料NHK North of Hongkong 中国大陆PRC People's Republic of China中国大陆U.S.A the United States of America美国A.S.A.P As Soon As Possible 尽可能快的E-MAIL Electrical-Mail 电子邮件N/A Not Applicable 不适用QTY Quantity 数量VS 以及REV Revision 版本JIT Just In Time 零库存I/O Input/Output 输入/输出OK Ok 好NG Not Good 不行,不合格C=0 Critical=0 极严重不允许ESD Electry-static Discharge 静电排放5S 希腊语整理,整顿,清扫,清洁,教养ATIN Attention 知会CC Carbon Copy 副本复印相关人员APP Approve 核准,认可,承认CHK Check 确认AM Ante Meridian 上午PM Post Meridian 下午CD Compact Disk 光碟CD-ROM Compact Disk Read-OnlyMemory 只读光碟FDD Floppy Disk Drive 软碟机HDD Hard Disk Drive 碟碟机REF Reference 仅供参考CONN Connector 连接器CA V Cavity 模穴CAD Computer Aid Design 计算机辅助设计ASS'Y Assembly 装配,组装MAT'S Material 材料IC Integrated Circuit 集成电路T/P True Position 真位度TYP Type 类型WDR Weekly Delivery Requitement周出货需求C?T Cycle Time 制程周期L/T Lead Time 前置时间(生产前准备时间)S/T Standard Time 标准时间P/M Product Market 产品市场3CComputer,Commumcation,Consumerelectronic's 消费性电子5WIHWhen,Where,Who,What,Why,How to5MMan,Machine,Material,Method,Measurement4MIHMan,Materia,Money,Method,Time人力,物力,财务,技术,时间(资源)SQA Strategy Quality Assurance策略品质保证DQA Desigh Quality Assurance 设计品质保证MQA Manufacture QualityAssurance 制造品质保证SSQA Sales and service QualityAssurance 销售及服务品质保证LRR Lot Rejeet Rate 批退率BS Brain storming 脑力激荡EMI Electronic Magnetion Inspect高磁测试FMI Frequency Modulatim Inspect高频测试B/M Boar/Molding(flat cable)C/P Connector of PCA/P AssemblySPS Switching power supply 电源箱DT Desk Top 卧式(机箱)MT Mini-Tower 立式(机箱)DVD Digital Vedio DiskVCD Vdeio Compact DiskLCD Liquid Crystal DisplayCAD Computer AID DesignCAM Computer AID ManufacturingCAE Computer AID EngineeringABIOS Achanced Basic input/output system 先进的基本输入/输出系统CMOS Complemeruary Metoll Oxide Semiconductor 互补金属氧化物半导体PDA Personal Digital Assistant 个人数字助理IC Integrated Circuit 集成电路ISA Industry Standard Architecture 工业标准体制结构MCA Micro Channel Architecture 微通道结构EISA Extended Industry Standard Architecture 扩充的工业标准结构SIMM Single in-line memory module 单项导通汇流组件DIMM Dual in-line Memory Module 双项导通汇流组件LED Light-Emitting Diode 发光二级管FMEA Failure Mode Effectivenes 失效模式分析W/H Wire Harness 金属线绪束集组件F/C Flat Calle 排线PCB Printed Circuit Board 印刷电路板CAR Correction Action Report 改善报告NG Not Good 不良WPR Weekly Delivery Requirement 周出货要求PPM Parts Per Million 百万分之一TPM Total Production Maintenance全面生产保养MRP Material Requiremcnt Planning物料需计划OC Operation System 作业系统TBA To Be Design 待定,定缺D/C Drawing ChangeP/P Plans & ProceduneEMI Electrical-Music Industry 电子音乐工业RFI Read Frequency Input 读频输入MMC Maximum Material ConditionMMS Maximum Material SizeLMC Least Material ConditionLMS Least Material Size模具技术用语各种模具常用成形方式accurate die casting 精密压铸powder forming 粉末成形calendaring molding 压延成形powder metal forging 粉末锻造cold chamber die casting 冷式压铸precision forging 精密锻造cold forging 冷锻press forging 冲锻compacting molding 粉末压出成形rocking die forging 摇动锻造compound molding 复合成形rotaryforging 回转锻造compression molding 压缩成形rotational molding 离心成形dip mold 浸渍成形rubber molding橡胶成形encapsulation molding 注入成形sand mold casting 砂模铸造extrusion molding 挤出成形shellcasting 壳模铸造foam forming ?泡成形sinter forging烧结锻造forging roll 轧锻six sides forging 六面锻造gravity casting 重力铸造slushmolding 凝塑成形hollow(blow) molding 中空(吹出)成形squeeze casting 高压铸造hot chamber die casting 热室压铸swaging 挤锻hot forging 热锻transfer molding 转送成形injection molding 射出成形warmforging 温锻investment casting 精密铸造matched die method 对模成形法laminating method 被覆淋膜成形low pressure casting 低压铸造lost wax casting 脱蜡铸造matchedmould thermal forming 对模热成形模各式模具分类用语bismuth mold 铋铸模landed plungermold 有肩柱塞式模具burnishing die 挤光模landed positivemold 有肩全压式模具button die 镶入式圆形凹模loadingshoe mold 料套式模具center-gated mold 中心浇口式模具loose detail mold 活零件模具chill mold 冷硬用铸模loose mold活动式模具clod hobbing 冷挤压制模louveringdie 百叶窗冲切模composite dies 复合模具manifolddie 分歧管模具counter punch 反凸模modular mold组合式模具double stack mold 双层模具multi-cavity mold 多模穴模具electroformed mold 电铸成形模multi-gate mold 复式浇口模具expander die 扩径模offswt bendingdie 双折冷弯模具extrusion die 挤出模palletizing die叠层模family mold 反套制品模具plastermold 石膏模blank through dies 漏件式落料模porous mold 通气性模具duplicated cavity plate 复板模positive mold 全压式模具fantail die 扇尾形模具pressure die压紧模fishtail die 鱼尾形模具profile die 轮廓模flash mold 溢料式模具progressive die 顺序模gypsum mold 石膏铸模protable mold 手提式模具hot-runner mold 热流道模具prototype mold 雏形试验模具ingot mold 钢锭模punching die 落料模lancing die 切口模raising(embossing) 压花起伏成形re-entrant mold 倒角式模具sectional die 拼合模runless injection mold 无流道冷料模具sectional die 对合模具segment mold 组合模semi-positive mold 半全压式模具shaper 定型模套single cavity mold 单腔模具solid forging die 整体锻模split forging die 拼合锻模split mold 双并式模具sprueless mold 无注道残料模具squeezing die 挤压模stretch form die 拉伸成形模sweeping mold 平刮铸模swing die 振动模具three plates mold 三片式模具trimming die 切边模unit mold 单元式模具universal mold 通用模具unscrewing mold 退扣式模具yoketype die 轭型模模具厂常用之标准零配件air vent vale 通气阀anchor pin 锚梢angular pin 角梢baffle 调节阻板angular pin 倾斜梢baffle plate 折流档板ball button 球塞套ball plunger 定位球塞ball slider 球塞滑块binder plate 压板blank holder 防皱压板blanking die落料冲头bolster 上下模板bottom board 浇注底板bolster 垫板bottom plate 下固定板bracket 托架bumper block 缓冲块buster 堵口casting ladle 浇注包casting lug 铸耳cavity 模穴(模仁)cavity retainer plate 模穴托板centerpin 中心梢clamping block 锁定块coil spring螺旋弹簧cold punched nut 冷冲螺母coolingspiral 螺旋冷却栓core 心型core pin 心型梢cotter 开口梢cross 十字接头cushion pin 缓冲梢diaphragm gate盘形浇口die approach 模头料道die bed 型底die block 块形模体die body 铸模座die bush 合模衬套die button 冲模母模die clamper 夹模器die fastener 模具固定用零件die holder 母模固定板die lip 模唇die plate 冲模板die set 冲压模座direct gate 直接浇口dog chuck 爪牙夹头dowel 定位梢dowel hole 导套孔dowel pin 合模梢dozzle 辅助浇口dowel pin 定位梢draft 拔模锥度draw bead 张力调整杆drive bearing传动轴承ejection pad 顶出衬垫ejector 脱模器ejector guide pin 顶出导梢ejectorleader busher 顶出导梢衬套ejector pad 顶出垫ejector pin 顶出梢ejector plate 顶出板ejector rod 顶出杆ejector sleeve 顶出衬套ejector valve顶出阀eye bolt 环首螺栓filling core 椿入蕊film gate 薄膜形浇口finger pin 指形梢finish machined plate 角形模板finish machined round plate 圆形模板fixed bolster plate 固定侧模板flanged pin 带凸缘?flash gate 毛边形浇口flask 上箱floating punch 浮动冲头gate 浇口gate land 浇口面gib 凹形拉紧?goose neck 鹅颈管guide bushing 引导衬套guide pin 导梢guide post 引导柱guide plate 导板guide rail 导轨head punch 顶?冲头headless punch直柄冲头heavily tapered solid 整体模蕊盒hose nippler 管接头impact damper 缓冲器injection ram压射柱塞inlay busher 嵌入衬套inner plunger内柱塞inner punch 内冲头insert 嵌件insert pin 嵌件梢king pin 转向梢king pin bush 主梢衬套knockout bar脱模杵land 合模平坦面land area 合模面leader busher 导梢衬套lifting pin 起模顶?lining 内衬locating center punch 定位中心冲头locating pilot pin 定位导梢locatingring 定位环lock block 压块locking block 定位块locking plate 定位板loose bush 活动衬套making die 打印冲子manifold block歧管档块。
毕业设计中英文翻译资料--冲压成形与板材冲压

毕业设计中英文翻译资料--冲压成形与板材冲压Stamping and Sheet Metal Forming1.The article overviewStamping is a kind of plastic forming process in which a part is produced by means of the plastic forming the material under the action of a die. Stamping is usually carried out under cold state, so it is also called stamping. Heat stamping is used only when the blank thickness is greater than 8~100mm. The blank material for stamping is usually in the form of sheet or strip, and therefore it is also called sheet metal forming. Some non-metal sheets (such as plywood, mica sheet, asbestos, leather)can also be formed by stamping.Stamping is widely used in various fields of the metalworking industry, and it plays a crucial role in the industries for manufacturing automobiles, instruments, military parts and household electrical appliances, etc.The process, equipment and die are the three foundational problems that needed to be studied in stamping.The characteristics of the sheet metal forming are as follows:(1)High material utilization(2)Capacity to produce thin-walled parts of complex shape.(3)Good interchangeability between stamping parts due to precision in shape anddimension.(4)Parts with lightweight, high-strength and fine rigidity can be obtained.(5)High productivity, easy to operate and to realize mechanization andautomatization.The manufacture of the stamping die is costly, and therefore it only fits to mass production. For the manufacture of products in small batch and rich variety, the simple stamping die and the new equipment such as a stamping machining center, are usually adopted to meet the market demands.The materials for sheet metal stamping include mild steel, copper, aluminum, magnesium alloy and high-plasticity alloy-steel, etc.Stamping equipment includes plate shear punching press. The former shears plate into strips with a definite width, which would be pressed later. The later can be used both in shearing and forming.2.Characteristics of stamping formingThere are various processes of stamping forming with different working patterns and names. But these processes are similar to each other in plastic deformation. There are following conspicuous characteristics in stamping:(1).The force per unit area perpendicular to the blank surface is not large but is enough to cause the material plastic deformation. It is much less than the inner stresses on the plate plane directions. In most cases stamping forming can be treated approximately as that of the plane stress state to simplify vastly the theoretical analysis and the calculation of the process parameters.(2).Due to the small relative thickness, the anti-instability capability of the blank is weak under compressive stress. As a result, the stamping process is difficult to proceed successfully without using the anti-instability device (such as blank holder). Therefore the varieties of the stamping processes dominated by tensile stress are more than dominated by compressive stress.(3).During stamping forming, the inner stress of the blank is equal to or sometimes less than the yield stress of the material. In this point, the stamping is different from the bulk forming. During stamping forming, the influence of the hydrostatic pressure of the stress state in the deformation zone to the forming limit and the deformation resistance is not so important as to the bulk forming. In some circumstances, such influence may be neglected. Even in the case when this influence should be considered, the treating method is also different from that of bulk forming.(4).In stamping forming, the restrain action of the die to the blank is not severs as in the case of the bulk forming (such as die forging). In bulk forming, the constraint forming is proceeded by the die with exactly the same shape of the part. Whereas in stamping, inmost cases, the blank has a certain degree of freedom, only one surface of the blank contacts with the die. In some extra cases, such as the forming of the blank on the deforming zone contact with the die. The deformation in these regions are caused and controlled by the die applying an external force to its adjacent area.Due to the characteristics of stamping deformation and mechanics mentioned above, the stamping technique is different form the bulk metal forming:(1).The importance or the strength and rigidity of the die in stamping forming is less than that in bulk forming because the blank can be formed without applying large pressure per unit area on its surface. Instead, the techniques of the simple die and the pneumatic and hydraulic forming are developed.(2).Due to the plane stress or simple strain state in comparison with bulk forming, more research on deformation or force and power parameters has been done. Stamping forming can be performed by more reasonable scientific methods. Based on the real time measurement and analysis on the sheet metal properties and stamping parameters, by means of computer and some modern testing apparatus, research on the intellectualized control of stamping process is also in proceeding.(3).It is shown that there is a close relationship between stamping forming and raw material. The research on the properties of the stamping forming, that is, forming ability and shape stability, has become a key point in stamping technology development, but also enhances the manufacturing technique of iron and steel industry, and provides a reliable foundation for increasing sheet metal quality.3.Categories of stamping formingMany deformation processes can be done by stamping, the basic processes of the stamping can be divided into two kinds: cutting and forming.Cutting is a shearing process that one part of the blank is cut from the other. It mainly includes blanking, punching, trimming, parting and shaving, where punching and blanking are the most widely used. Forming is a process that one part of the blank has some displacement from the other. It mainly includes deep drawing, bending, local forming,bulging, flanging, necking, sizing and spinning.In substance, stamping forming is such that the plastic deformation occurs in the deformation zone of the stamping blank caused by the external force. The stress state and deformation characteristic of the deformation zone are the basic factors to decide the properties of the stamping forming. Based on the stress state and deformation characteristics of the deformation zone, the forming methods can be divided into several categories with the same forming properties and be studied systematically.The deformation zone in almost all types of stamping forming is in the plane stress state. Usually there is no force or only small force applied on the blank surface. When is assumed that the stress perpendicular to the blank surface equals to zero, two principal stresses perpendicular to each other and act on the blank surface produce the plastic deformation of the material. Due to the small thickness of the blank, it is assumed approximately the two principal stresses distribute uniformly along the thickness direction. Based on this analysis, the stress state and the deformation characteristics of the deformation zone in all kinds of stamping forming can be denoted by the points in the coordinates of the plane principal stresses and the coordinates of the corresponding plane principal strains.4.Raw materials for stamping formingThere are a lot of raw materials used in stamping forming, and the properties of these materials may have large difference. The stamping forming can be succeeded only by determining the stamping method, the forming parameters and the die structures according to the properties and characteristics of the raw materials. The deformation of the blank during stamping forming has been investigated quite thoroughly. The relationships between the material properties decided by the chemistry component and structure of the material and the stamping forming has been established clearly. Not only the proper material can be selected based on the working condition and usage demand, but also the new material can be developed according to the demands of the blank properties during processing the stamping part. This is an important domain in stamping formingresearch. The research on the material properties for stamping forming is as follows: (1).Definition of the stamping property of the material.(2).Method to judge the stamping property of the material, find parameters to express the definitely material property of the stamping forming, establish the relationship between the property parameters and the practical stamping forming, and investigate the testing methods of the property parameters.(3).Establish the relationship among the chemical component, structure, manufacturing process and stamping property.The raw materials for stamping forming mainly include various metals and nonmetal plate. Sheet metal includes both ferrous and nonferrous metals. Although a lot of sheet metals are used in stamping forming, the most widely used materials are steel, stainless steel, aluminum alloy and various composite metal plates.5.Stamping forming property of sheet metal and its assessing methodThe stamping forming property of the sheet metal is the adaptation capability of the sheet metal to stamping forming. It has crucial meaning to the investigation of the stamping forming property of the sheet metal. In order to produce stamping forming parts with most scientific, economic and rational stamping forming process and forming parameters, it is necessary to understand clearly the properties of the sheet metal, so as to utilize the potential of the sheet metal fully in the production. On the other hand, to select plate material accurately and rationally in accordance with the characteristics of the shape and dimension of the stamping forming part and its forming technique is also necessary so that a scientific understanding and accurate judgment to the stamping forming properties of the sheet metal may be achieved.There are direct and indirect testing methods to assess the stamping property of the sheet metal.Practicality stamping test is the most direct method to assess stamping forming property of the sheet metal. This test is done exactly in the same condition as actual production by using the practical equipment and dies. Surely, this test result is mostreliable. But this kind of assessing method is not comprehensively applicable, and cannot be shared as a commonly used standard between factories.The simulation test is a kind of assessing method that after simplifying and summing up actual stamping forming methods, as well as eliminating many trivial factors, the stamping properties of the sheet metal are assessed, based on simplified axial-symmetric forming method under the same deformation and stress states between the testing plate and the actual forming states. In order to guarantee the reliability and generality of simulation results, a lot of factors are regulated in detail, such as the shape and dimension of tools for test, blank dimension and testing conditions(stamping velocity, lubrication method and blank holding force, etc).Indirect testing method is also called basic testing method its characteristic is to connect analysis and research on fundamental property and principle of the sheet metal during plastic deformation, and with the plastic deformation parameters of the sheet metal in actual stamping forming, and then to establish the relationship between the indirect testing results(indirect testing value) and the actual stamping forming property (forming parameters). Because the shape and dimension of the specimen and the loading pattern of the indirect testing are different from the actual stamping forming, the deformation characteristics and stress states of the indirect test are different from those of the actual one. So, the results obtained form the indirect test are not the stamping forming parameters, but are the fundamental parameters that can be used to represent the stamping forming property of the sheet metal.冲压成形与板材冲压1.概述通过模具使板材产生塑性变形而获得成品零件的一次成形工艺方法叫做冲压。
(完整版)冲压词汇中英文-1

冲压工艺词汇中英文对照注释2002-11-28 第一版冲压工艺stamping process 冲压工序stamping procedure 拉延draw 修边trim冲孔pierce 翻边flange整形resrike 校平straighten落料blanking 压印mark胀形bulging 切口notch压弯bending 成形form翻口beading 缩口necking装配assembling 压合pressing刮边shaving 卷边edge rolling铆接riveting 卷耳curling扭弯twisting 镦粗upsetting穿刺perforating 拉延性能draw ability再拉延redraw 精度accuracy延伸率rate of elongation 强度strength抗拉强度tensile strength 屈服强度yield strength抗弯强度bending strength 抗压强度compressive strength 塑性变形plastic deformation 工艺r缺口notch cut伸长lengthening 起皱wrinkle/crinkle毛刺burr 去毛刺defurring正反拉深positive and negative drawing 回弹spring-back冲击线impact line 冲压负角backdraft/undercut单动拉延single action draw 双动拉延double action draw渗碳carbonization 碳素钢carbon steel碳工钢carbon tool steel 镀铬chrome-plating间隙配合clearance fit 紧配合close fit过盈配合interference fit 动配合running fit系数coefficient 同心度concentricity曲柄crank 筒形件拉延cup drawing开卷机decoiler 深拉延deep drawing变形程度degree of deformation 凹坑凹痕dent模具寿命die life 双排冲double-row layout拉延系数draw rate 凸耳earing弹性回复elastic recovery 疲劳裂纹fatigue crack疲劳破坏fatigue fracture 成形极限forming limit加热炉furnace 砂轮grinding wheel灰口铁grey cast iron 中性层neutral layern-value n值工艺卡process chart拉毛划痕scoring 无废料排样side-by-side layout 搭边bridge 材料利用率stock utilization 加工硬化strain hardening带钢ribbon steel 轧制方向rolling direction材料利用率material utilization 步距pitch冲压模具词汇中英文对照注释2002-11-28 第一版工程图die layout 工序working procedure冲压方向pressing direction 送料方向feeding direction送料高度loading height 取件高度unloading height毛坯stock blank 调试tryout展开prolongation 条料band排样stock layout 片料sheet凸模轮廓线punch profile/line 凹模入口线die opening line 压料面binder(surface) 拉延槛lock step拉延筋draw bead 拉延深度draw depth拉延力draw tonnage 压边力binder tonnage装配图assembly drawing 零件图detail drawing剖面图section view 局部视图sketch view基准点datum mark 中心线central line制件名称part name 制件号part number零件detail part 工件work piece直径diameter 半径radius制件finished part 备件spare part易损件quick-wear part 模具维修die maintenance调试try-out 废料scrap宽度width 长度length高度height 厚度thickness公差tolerance 尺寸dimension圆孔round hole 长圆孔elongated hole/oblong 方孔square 异形孔irregular hole凸点weld embossment压床press 气垫air cushion滑块ram 闭合高度shut height内滑块inner slide 外滑块outerd slide模柄shank 托杆ejector/cushion pin平衡托杆balancing pin 自动夹紧automatic clamp location 垫板bolster T型槽T groove材料material 铸铁cast iron铸钢cast steel 铸造镶块cast sectional镶块(钢镶件) insert 镶块(凹模)sectional die工具钢tool steel 合金钢alloy-steel上模upper die 下模lower/bottom die模架die set 模座shoe上底板upper plate/shoe 导柱guide pin下底板lower plate/shoe 导套guide pin bushing凸模punch 导向块guide block凹模die/matrix 导正销pilot压料圈blank holder 间隙clearance顶出器knockout/pad 接缝空刀joint relief定位块locator 挡料销stop pin废料刀scrap cutter 支架bracket缓冲器bumper block 弹簧spring导板wear(guide) plate 自润导板self-lube plate空开面relief/relieve 天窗window plate废料槽chute 废料滑板scrap shedding废料盒storage box 暗键blind key防护板guard 铭牌name plate橡皮rubber 加强筋rib键key 键槽keyway侧销retainer pin 安全侧销safety retainer pin 安全挡板securing plate 顶销pushing-out pin退料板/器stripper 回程return stroke预压弹簧pre-compressed spring 复位弹簧return spring到位标记bottom mark 压印器bottoming marker 压字器emboss button 压字标记marker凸模固定板punch holder/retainer 定位块locator反侧块back-up/heel block 侧向力lateral force/thrust观察孔/排水(气)孔vent 切刀深度trim entrance气缸cylinder 氮气缸nitrogen gas cylinder 滚轮滑道roller carrier 橡胶滚轮rubber roller定位板(拉延用)nest guide 定位检测器panel input detector 传感器sensor 行程stroke, travel定位销locating pilot pin 安全凸耳safety lug调整垫块distance plate 平衡块equalizer block铸造倒角cast bevel 铸造凸台cast boss凹模button die 带肩凸模shoulder punch球锁凸模ball-lock punch 弹簧定位销spring guide pin 废料弹顶器Scrap stripper 脱件器shedder pin通过孔access core 减轻孔Lightening core角钢angle iron 双向斜楔filler slide cam斜楔cam 吊楔aerial/flying cam驱动楔cam driver 滑楔cam slide斜楔座cam adapter 固定座die adapter咬合(预导向)engagement 斜楔导板cam slide gib安全区safety area C/P点coordinate point起重棒lift pin 铸入式起重棒cast-in steel lug快换冲头quick exchanging punch 压板台fastening slot凸V型导板male v block 凹V型导板female u block 螺钉bolt 螺纹screw内六角螺钉sockethead screw 平头十字螺钉flathead screw 带肩螺钉socket head shoulder screw 外六角螺钉hexagon nut柱销dowel pin 真空吸盘vacuum聚胺酯存放限制器合件urethane stock block sets /storage block行程限制器stop block模具标牌die information tag 托杆标牌air pin tag送料装置feeding mechanism 送料(进料)feed泡沫模型foam model 数控加工nc machining车削lathe 数控铣nc mill磨削grind 钻孔drill耐磨性wear-resistance 石墨graphite极进模progressive die 复合模compound die热处理heat treatment 淬火quenching/hardening 火焰淬火flame hardening 局部淬火local hardening正火normalizing 退火annealing渗氮nitriding 调质处理refining硬度hardness 维氏硬度Vickers hardness 布氏硬度Brielle hardness 洛氏硬度Rockwell hardness 主模型master model 检具checking fixture夹具jig 加工余量machine allowance。
冲压工艺工序中英文对照(1)
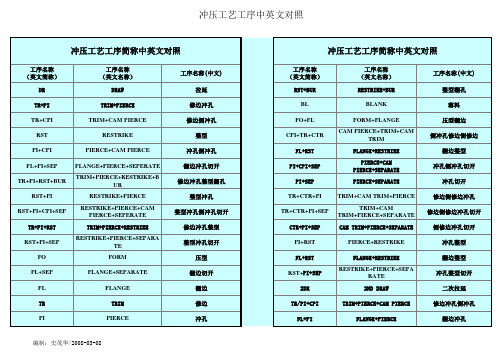
TR+CTR+PI+SEP CTR+PI+SEP PI+RST FL+RST RST+PI+SEP 2DR TR/PI+CPI FL+PI
编制:史茂华/2008-03-08
冲压工艺工序中英文对照
冲压工艺工序简ห้องสมุดไป่ตู้中英文对照
工序名称 (英文简称) DR TR+PI TR+CPI RST PI+CPI FL+PI+SEP TR+PI+RST+BUR RST+PI RST+PI+CPI+SEP TR+PI+RST RST+PI+SEP FO FL+SEP FL TR PI 工序名称 (英文名称) DRAW TRIM+PIERCE TRIM+CAM PIERCE RESTRIKE PIERCE+CAM PIERCE FLANGE+PIERCE+SEPERATE TRIM+PIERCE+RESTRIKE+B UR RESTRIKE+PIERCE RESTRIKE+PIERCE+CAM PIERCE+SEPERATE TRIM+PIERCE+RESTRIKE RESTRIKE+PIERCE+SEPARA TE FORM FLANGE+SEPARATE FLANGE TRIM PIERCE 工序名称(中文) 拉延 修边冲孔 修边侧冲孔 整型 冲孔侧冲孔 翻边冲孔切开 修边冲孔整型翻孔 整型冲孔 整型冲孔侧冲孔切开 修边冲孔整型 整型冲孔切开 压型 翻边切开 翻边 修边 冲孔 工序名称 (英文简称) RST+BUR BL FO+FL CPI+TR+CTR FL+RST PI+CPI+SEP PI+SEP TR+CTR+PI
组装、冲压、喷漆等专业词汇 及英文对照

组装、冲压、喷漆等专业词汇1组装、冲压、喷漆等专业词汇Assembly line组装线Layout布置图Conveyer流水线物料板Rivet table拉钉机Rivet gun拉钉枪Screw driver起子Electric screw driver电动起子Pneumatic screw driver气动起子worktable 工作桌OOBA开箱检查fit together组装在一起fasten锁紧(螺丝)fixture 夹具(治具)pallet栈板barcode条码barcode scanner条码扫描器fuse together熔合fuse machine热熔机repair修理operator作业员QC品管supervisor 课长ME制造工程师MT制造生技cosmetic inspect外观检查inner parts inspect内部检查thumb screw大头螺丝lbs. inch镑、英寸EMI gasket导电条front plate前板rear plate后板chassis基座bezel panel面板 apower button电源按键reset button重置键Hi-pot test of SPS高源高压测试V oltage switch of SPS电源电压接拉键sheet metal parts 冲件plastic parts塑胶件SOP制造作业程序material check list物料检查表work cell工作间trolley台车carton纸箱sub-line支线left fork叉车personnel resource department人力资源部production department生产部门planning department企划部QC Section品管科stamping factory冲压厂painting factory烤漆厂molding factory成型厂common equipment常用设备uncoiler and straightener整平机punching machine 冲床robot机械手hydraulic machine油压机lathe车床planer |'plein|刨床miller铣床grinder磨床driller??床linear cutting线切割electrical sparkle电火花welder电焊机staker=reviting machine铆合机position职务president董事长general manager总经理special assistant manager特助factory director厂长department director部长deputy manager | =vice manager副理section supervisor课长deputy section supervisor =vice sectionsuperisor副课长group leader/supervisor组长line supervisor线长assistant manager助理to move, to carry, to handle搬运be put in storage入库pack packing包装to apply oil擦油to file burr 锉毛刺final inspection终检to connect material接料to reverse material 翻料wet station沾湿台Tiana天那水cleaning cloth抹布to load material上料to unload material卸料to return material/stock to退料scraped |'skræpid|报废scrape ..v.刮;削deficient purchase来料不良manufacture procedure制程deficient manufacturing procedure制程不良oxidation |' ksi'dein|氧化scratch刮伤dents压痕defective upsiding down抽芽不良defective to staking铆合不良embedded lump镶块feeding is not in place送料不到位stamping-missing漏冲production capacity生产力education and training教育与训练proposal improvement提案改善spare parts=buffer备件forklift叉车trailer=long vehicle拖板车compound die合模die locker锁模器pressure plate=plate pinch压板bolt螺栓name of a department部门名称administration/general affairs dept总务部1automatic screwdriver电动启子thickness gauge厚薄规gauge(or jig)治具power wire电源线buzzle蜂鸣器defective product label不良标签identifying sheet list标示单screwdriver holder起子插座pedal踩踏板stopper阻挡器flow board流水板hydraulic handjack油压板车forklift叉车pallet栈板glove(s)手套glove(s) with exposed fingers割手套thumb大拇指forefinger食指midfinger中指ring finger无名指little finger小指band-aid创可贴iudustrial alcohol工业酒精alcohol container沾湿台head of screwdriver起子头sweeper扫把mop拖把vaccum cleaner吸尘器rag 抹布garbage container灰箕garbage can垃圾箱garbage bag垃圾袋chain链条jack升降机production line流水线chain链条槽magnetizer加磁器lamp holder灯架to mop the floor拖地to clean the floor扫地to clean a table擦桌子air pipe 气管packaging tool打包机packaging打包missing part漏件wrong part错件excessive defects过多的缺陷critical defect极严重缺陷major defect主要缺陷minor defect次要缺陷not up to standard不合规格dimension/size is a little bigger尺寸偏大(小)cosmetic defect外观不良slipped screwhead/slippery screw head螺丝滑头slipped screwhead/shippery screw thread滑手speckle斑点mildewed=moldy=mouldy发霉rust生锈deformation变形burr(金属)flash(塑件)毛边poor staking铆合不良excesssive gap间隙过大grease/oil stains油污inclusion杂质painting peel off脏污shrinking/shrinkage缩水mixed color杂色scratch划伤poor processing 制程不良poor incoming part事件不良fold of pakaging belt打包带折皱painting make-up补漆discoloration羿色water spots水渍polishing/surface processing表面处理exposed metal/bare metal金属裸露lack of painting烤漆不到位safety安全quality品质delivery deadline交货期cost成本engineering工程die repair模修enterprise plan = enterprise expansionprojects企划QC品管die worker模工production, to produce生产equipment设备to start a press开机stop/switch off a press关机classification整理regulation整顿cleanness清扫conservation清洁culture教养qualified products, up-to-grade products良品defective products, not up-to-gradeproducts不良品waste废料board看板feeder送料机sliding rack滑料架defective product box不良品箱die change 换模to fix a die装模to take apart a die拆模to repair a die修模packing material包材basket蝴蝶竺plastic basket胶筐isolating plate baffle plate; barricade隔板carton box纸箱to pull and stretch拉深to put material in place, to cut material,to input落料to impose lines压线to compress, compressing压缩character die字模to feed, feeding送料transportation运输(be)qualfied, up to grade合格not up to grade, not qualified不合格1material change, stock change材料变更feature change 特性变更evaluation评估prepare for, make preparations for 准备parameters参数rotating speed, revolution转速manufacture management制造管理abnormal handling异常处理production unit生产单位lots of production生产批量steel plate钢板roll material卷料manufacture procedure制程operation procedure作业流程to revise, modify修订to switch over to, switch---to throw--over switching over切换engineering, project difficulty工程瓶颈stage die工程模automation自动化to stake, staking, reviting铆合add lubricating oil加润滑油shut die架模shut height of a die架模高度analog-mode device类模器die lifter举模器argon welding氩焊vocabulary for stamping冲压常词汇stamping, press冲压punch press, dieing out press冲床uncoiler & strainghtener整平机feeder送料机rack, shelf, stack料架cylinder油缸robot机械手taker取料机conveyer belt输送带transmission rack输送架top stop上死点bottom stop下死点one stroke一行程inch寸动to continue, cont.连动to grip(material)吸料location lump, locating piece, block stop定位块reset复位smoothly顺利dent压痕scratch刮伤deformation变形filings铁削to draw holes抽孔inquiry, search for查寻to stock, storage, in stock库存receive领取approval examine and verify审核processing, to process加工delivery, to deliver 交货to return delivenry to.to send delinery backto retrn of goods退货registration登记registration card登记卡to control管制to put forward and hand in提报safe stock安全库存acceptance = receive验收to notice通知application form for purchase请购单consume, consumption消耗to fill in填写abrasion磨损reverse angle = chamfer倒角character die字模to collect, to gather收集failure, trouble故障statistics统计demand and supply需求career card履历卡to take apart a die卸下模具to load a die装上模具to tight a bolt拧紧螺栓to looser a bolt拧松螺栓to move away a die plate移走模板easily damaged parts易损件standard parts标准件breaking.(be)broken,(be)cracked 断裂to lubricate润滑common vocabulary for die engineering模具工程常用词汇die 模具figure file, chart file图档cutting die, blanking die冲裁模progressive die, follow (-on)die连续模compound die复合模punched hole冲孔panel board镶块to cutedges=side cut=side scrap切边to bending折弯to pull, to stretch拉伸Line streching, line pulling线拉伸engraving, to engrave刻印upsiding down edges翻边to stake铆合designing, to design设计design modification设计变化die block模块folded block折弯块sliding block滑块location pin定位销lifting pin顶料销die plate, front board模板padding block垫块stepping bar垫条upper die base上模座lower die base下模座upper supporting blank上承板upper padding plate blank上垫板spare dies模具备品spring 弹簧bolt螺栓document folder文件夹file folder资料夹to put file in order整理资料2spare tools location手工备品仓first count初盘人first check初盘复棹人second count 复盘人second check复盘复核人equipment设备waste materials废料work in progress product在制品casing = containerazation装箱quantity of physical invetory second count 复盘点数量quantity of customs count会计师盘,点数量the first page第一联filed by accounting department for reference会计部存查end-user/using unit(department)使用单位summary of year-end physical inventory bills年终盘点截止单据汇总表bill name单据名称This sheet and physical inventory list will be sent to accountingdepartment together (Those of NHK will be sent to financialdepartment)本表请与盘点清册一起送会计部-(NHK厂区送财会部)Application status records of year-end physical inventory List andphysical inventory card 年终盘点卡与清册使用-状况明细表blank and waste sheet NO.空白与作废单号plate电镀mold成型material for engineering mold testing工程试模材料not included in physical inventory不列入盘点sample样品incoming material to be inspected进货待验description品名steel/rolled steel钢材material statistics sheet物料统计明细表meeting minutes会议记录meeting type 会别distribution department分发单位location地点chairman主席present members出席人员subject主题conclusion结论decision items决议事项responsible department负责单位pre-fixed finishing date预定完成日approved by / checked by / prepared by核准/审核/承办PCE assembly production schedule sheetPCE组装厂生产排配表model机锺work order工令revision版次remark备注production control confirmation生产确认checked by初审approved by核准department部门stock age analysis sheet库存货龄分析表on-hand inventory现有库存available material良品可使用obsolete material良品已呆滞to be inspected or reworked待验或重工total合计cause description原因说明part number/ P/N 料号type形态item/group/class类别quality品质prepared by制表notes说明year-end physical inventory differenceanalysis sheet年终盘点差异分析表physical inventory盘点数量physical count quantity帐面数量difference quantity差异量cause analysis原因分析raw materials原料materials物料finished product成品semi-finished product半成品packing materials包材good product/accepted goods/ acceptedparts/good parts良品defective product/non-good parts不良品disposed goods处理品warehouse/hub仓库on way location在途仓oversea location海外仓spare parts physical inventory list备品盘点清单spare molds location模具备品仓skid/pallet栈板tox machine自铆机wire EDM线割EDM放电机coil stock卷料sheet stock片料tolerance工差score=groove压线cam block滑块pilot导正筒trim剪外边pierce剪内边drag form压锻差pocket for the punch head挂钩槽slug hole废料孔feature die公母模expansion dwg展开图radius半径shim(wedge)楔子3torch-flame cut火焰切割set screw止付螺丝form block折刀stop pin定位销round pierce punch=die button圆冲子shape punch=die insert异形子stock locater block定位块under cut=scrap chopper清角active plate活动板baffle plate挡块cover plate盖板male die公模female die母模groove punch压线冲子air-cushion eject-rod气垫顶杆spring-box eject-plate弹簧箱顶板bushing block衬套insert 入块club car高尔夫球车capability能力parameter参数factor系数phosphate皮膜化成viscosity涂料粘度alkalidipping脱脂main manifold主集流脉bezel斜视规blanking穿落模dejecting顶固模demagnetization去磁;消磁high-speed transmission高速传递heat dissipation热传rack上料degrease脱脂rinse水洗alkaline etch龄咬desmut剥黑膜D.I. rinse纯水次Chromate铬酸处理Anodize阳性处理seal封孔revision版次part number/P/N料号good products良品scraped products报放心品defective products不良品finished products成品disposed products处理品barcode条码flow chart流程表单assembly组装stamping冲压molding成型spare parts=buffer备品coordinate座标dismantle the die折模auxiliary fuction辅助功能poly-line多义线heater band 加热片thermocouple热电偶sand blasting喷沙grit 砂砾derusting machine除锈机degate打浇口dryer烘干机induction感应induction light感应光response=reaction=interaction感应ram连杆edge finder巡边器concave凸convex凹short射料不足nick缺口speck瑕??shine亮班splay 银纹gas mark焦痕delamination起鳞cold slug冷块blush 导色gouge沟槽;凿槽satin texture段面咬花witness line证示线patent专利grit沙砾granule=peuet=grain细粒grit maker抽粒机cushion缓冲magnalium镁铝合金magnesium镁金metal plate钣金lathe车mill锉plane刨grind磨drill铝boring镗blinster气泡fillet镶;嵌边through-hole form通孔形式voller pin formality滚针形式cam driver铡楔shank摸柄crank shaft曲柄轴augular offset角度偏差velocity速度production tempo生产进度现状torque扭矩spline=the multiple keys花键quenching淬火tempering回火annealing退火carbonization碳化alloy合金tungsten high speed steel钨高速的moly high speed steel钼高速的organic solvent有机溶剂bracket小磁导liaison联络单volatile挥发性resistance电阻ion离子titrator滴定仪beacon警示灯coolant冷却液crusher破碎机模具工程类4plain die简易模pierce die冲孔模forming die成型模progressive die连续模gang dies复合模shearing die剪边模riveting die铆合模pierce冲孔forming成型(抽凸,冲凸) draw hole抽孔bending折弯trim切边emboss凸点dome凸圆semi-shearing半剪stamp mark冲记号deburr or coin压毛边punch riveting冲压铆合side stretch侧冲压平reel stretch卷圆压平groove压线blanking下料stamp letter冲字(料号) shearing剪断tick-mark nearside正面压印tick-mark farside反面压印冲压名称类extension dwg展开图procedure dwg工程图die structure dwg模具结构图material材质material thickness料片厚度factor系数upward向上downward向下press specification冲床规格die height range适用模高die height闭模高度burr毛边gap间隙weight重量total wt.总重量punch wt.上模重量五金零件类inner guiding post内导柱inner hexagon screw内六角螺钉dowel pin固定销coil spring弹簧lifter pin顶料销eq-height sleeves=spool等高套筒pin销lifter guide pin浮升导料销guide pin导正销wire spring圆线弹簧outer guiding post外导柱stop screw止付螺丝located pin定位销outer bush外导套模板类top plate上托板(顶板)top block上垫脚punch set上模座punch pad上垫板punch holder上夹板stripper pad脱料背板up stripper上脱料板male die公模(凸模)feature die公母模female die母模(凹模)upper plate上模板lower plate下模板die pad下垫板die holder下夹板die set下模座bottom block下垫脚bottom plate下托板(底板)stripping plate内外打(脱料板)outer stripper外脱料板inner stripper内脱料板lower stripper下脱料板零件类punch冲头insert入块(嵌入件)deburring punch压毛边冲子groove punch压线冲子stamped punch字模冲子round punch圆冲子special shape punch异形冲子bending block折刀roller滚轴baffle plate挡块located block定位块supporting block for location定位支承块air cushion plate气垫板air-cushion eject-rod气垫顶杆trimming punch切边冲子stiffening rib punch = stinger 加强筋冲子ribbon punch压筋冲子reel-stretch punch卷圆压平冲子guide plate定位板sliding block滑块sliding dowel block滑块固定块active plate活动板lower sliding plate下滑块板upper holder block上压块upper mid plate上中间板spring box弹簧箱spring-box eject-rod弹簧箱顶杆spring-box eject-plate弹簧箱顶板bushing bolck衬套cover plate盖板guide pad导料块塑件&模具相关英文compre sion molding压缩成型flash mold溢流式模具plsitive mold挤压式模具split mold分割式模具cavity型控母模core模心公模taper锥拔leather cloak仿皮革shiver饰纹flow mark流痕welding mark溶合痕post screw insert螺纹套筒埋值self tapping screw自攻螺丝5striper plate脱料板piston活塞cylinder汽缸套chip细碎物handle mold手持式模具移转成型用模具encapsulation molding低压封装成型射出成型用模具two plate两极式(模具)well type蓄料井insulated runner绝缘浇道方式hot runner热浇道runner plat浇道模块valve gate阀门浇口band heater环带状的电热器spindle阀针spear head刨尖头slag well冷料井cold slag冷料渣air vent排气道h=0.02~0.05mmw=3.2mmL=3~5mmwelding line熔合痕eject pin顶出针knock pin顶出销return pin回位销反顶针sleave套筒stripper plate脱料板insert core放置入子runner stripper plate浇道脱料板guide pin导销eject rod (bar)(成型机)顶业捧subzero深冷处理three plate三极式模具runner system浇道系统stress crack应力电裂orientation定向sprue gate射料浇口,直浇口nozzle射嘴sprue lock pin料头钩销(拉料杆)slag well冷料井side gate侧浇口edge gate侧缘浇口tab gate搭接浇口film gate薄膜浇口flash gate闸门浇口slit gate缝隙浇口fan gate扇形浇口dish gate因盘形浇口H=F=1/2t~1/5tT=2.5~3.5mmdiaphragm gate隔膜浇口ring gate环形浇口subarine gate潜入式浇口tunnel gate隧道式浇口pin gate针点浇口Φ0.8~1.0mmRunner less无浇道(sprue less)无射料管方式long nozzle延长喷嘴方式sprue浇口;溶渣品质人员名称类QC quality control 品质管理人员FQC final quality control 终点品质管制人员IPQC in process quality control 制程中的品质管制人员OQC output quality control 最终出货品质管制人员IQC incoming quality control 进料品质管制人员TQC total quality control 全面质量管理POC passage quality control 段检人员QA quality assurance 质量保证人员OQA output quality assurance 出货质量保证人员QE quality engineering 品质工程人员品质保证类FAI first article inspection 新品首件检查FAA first article assurance 首件确认TVR tool verification report 模具确认报告3B 3B 模具正式投产前确认CP capability index 能力指数CPK capability index of process 模具制程能力参数SSQA standardized supplier quality合格供应商品质评估OOBA out of box audit 开箱检查QFD quality function deployment 品质机能展开FMEA failure model effectivenessanalysis 失效模式分析8 disciplines 8项回复内容FA final audit 最後一次稽核CAR corrective action request 改正行动要求corrective action report 改正行动报告FQC运作类AQL Acceptable Quality Level 运作类允收品质水准S/S Sample size 抽样检验样本大小ACC Accept 允收REE Reject 拒收CR Critical 极严重的MAJ Major 主要的MIN Minor 轻微的AOQ A verage Output Quality 平均出厂品质AOQL A verage Output Quality Level平均出厂品质Q/R/S Quality/Reliability/Service 品质/可靠度服务MIL-STD Military-Standard 军用标准S I-S IV Special I-Special IV 特殊抽样水准等级P/N Part Number 料号L/N Lot Number 特采AOD Accept On Deviation 特采UAI Use As It 首件检查报告6FPIR First Piece Inspection Report 百万分之一PPM Percent Per Million 批号制程统计品管专类SPC Statistical Process Control 统计制程管制SQC Statistical Quality Control 统计品质管制R Range 全距AR A verary Range 全距平均值UCL Upper Central Limit 管制上限LCL Lower Central Limit 管制下限MAX Maximum 最大值MIN Minimum 最小值GRR Gauge Reproducibility&Repeatability 量具之再制性及重测性判断量可靠与否DIM Dimension 尺寸DIA Diameter 直径FREQ Frequency 频率N Number 样品数其它品质术语类QCC Quality Control Circle 品质圈QIT Quality Improvement Team 品质改善小组PDCA Plan Do Check Action 计划执行检查总结ZD Zero Defect 零缺点QI Quality Improvement 品质改善QP Quality Policy 目标方针TQM Total Quality Management 全面品质管理MRB Material Reject Bill 退货单LQL Limiting Quality Level 最低品质水准RMA Return Material Audit 退料认可QAN Quality Amelionrate Notice 品质改善活动ADM Absolute DimensionMeasuremat 全尺寸测量QT Quality Target 品质目标7QCTools 7 Quality Controll Tools品管七大手法通用之件类ECN Engineering Change Notes 工程变更通知(供应商)ECO Engineering Change Order 工程改动要求(客户)PCN Process Change Notice 工序改动通知PMP Product Management Plan 生产管制计划SIP Specification In Process 制程检验规格SOP Standard Operation Procedure制造作业规范IS Inspection Specification 成品检验规范BOM Bill Of Material 物料清单PS Package Specification 包装规范SPEC Specification 规格DWG Drawing 图面系统文件类QC Quality System 品质系统ES Engineering Standarization 工程标准CGOO China General PCE龙华厂文件H Huston (美国)休斯敦C Compaq (美国)康伯公司C China 中国大陆A Assembly 组装(厂)S Stamping 冲压(厂)P Painting 烤漆(厂)I Intel 英特尔公司T TAIW AN 台湾IWS International Workman Standard工艺标准ISO International StandardOrganization 国际标准化组织GS General Specification 一般规格CMCS C-China M-ManufactC-Compaq S-Stamping Compaq产品在龙华冲压厂制造作业规范CQCA Q-Quality A-AssemblyCompaq产品在龙华组装厂品管作业规范CQCP P-Painting Compaq产品在龙华烤漆厂品管作业规范部类PMC Production & Material Control生产和物料控制PPC Production Plan Control 生产计划控制MC Material Control 物料控制ME Manafacture Engineering 制造工程部PE Project Engineering 产品工程部A/C Accountant Dept 会计部P/A Personal & Administration 人事行政部DC Document Center 资料中心QE Quality Engineering 品质工程(部)QA Quality Assurance 品质保证(处)QC Quality Control 品质管制(课)PD Product Department 生产部LAB Labratry 实验室IE Industrial Engineering 工业工程R&D Research & Design 设计开发部P Painting 烤漆(厂)A Asssembly 组装(厂)S Stamping 冲压(厂)生产类PCS Pieces 个(根,块等)PRS Pairs 双(对等)CTN Carton 卡通箱PAL Pallet/skid 栈板PO Purchasing Order 采购订单MO Manufacture Order 生产单D/C Date Code 生产日期码ID/C Identification Code (供应商)识别码SWR Special Work Request 特殊工作需求L/N Lot Number 批号7P/N Part Number 料号其它OEM Original Equipment Manufacture 原设备制造PCE Personal Computer Enclosure 个人电脑外设PC Personal Computer 个人电脑CPU Central Processing Unit 中央处理器SECC SECC` 电解片SGCC SGCC 热浸镀锌材料NHK North of Hongkong 中国大陆PRC People's Republic of China 中国大陆U.S.A the United States of America 美国A.S.A.P As Soon As Possible 尽可能快的E-MAIL Electrical-Mail 电子邮件N/A Not Applicable 不适用QTY Quantity 数量VS 以及REV Revision 版本JIT Just In Time 零库存I/O Input/Output 输入/输出OK Ok 好NG Not Good 不行,不合格C=0 Critical=0 极严重不允许ESD Electry-static Discharge 静电排放5S 希腊语整理,整顿,清扫,清洁,教养A TIN Attention 知会CC Carbon Copy 副本复印相关人员APP Approve 核准,认可,承认CHK Check 确认AM Ante Meridian 上午PM Post Meridian 下午CD Compact Disk 光碟CD-ROM Compact Disk Read-OnlyMemory 只读光碟FDD Floppy Disk Drive 软碟机HDD Hard Disk Drive 碟碟机REF Reference 仅供参考CONN Connector 连接器CA V Cavity 模穴CAD Computer Aid Design 计算机辅助设计ASS'Y Assembly 装配,组装MA T'S Material 材料IC Integrated Circuit 集成电路T/P True Position 真位度TYP Type 类型WDR Weekly Delivery Requitement周出货需求C?T Cycle Time 制程周期L/T Lead Time 前置时间(生产前准备时间)S/T Standard Time 标准时间P/M Product Market 产品市场3CComputer,Commumcation,Consumerelectronic's 消费性电子5WIHWhen,Where,Who,What,Why,How to5MMan,Machine,Material,Method,Measurement4MIHMan,Materia,Money,Method,Time 人力,物力,财务,技术,时间(资源)SQA Strategy Quality Assurance 策略品质保证DQA Desigh Quality Assurance 设计品质保证MQA Manufacture Quality Assurance制造品质保证SSQA Sales and service QualityAssurance 销售及服务品质保证LRR Lot Rejeet Rate 批退率BS Brain storming 脑力激荡EMI Electronic Magnetion Inspect高磁测试FMI Frequency Modulatim Inspect高频测试B/M Boar/Molding(flat cable)C/P Connector of PCA/P AssemblySPS Switching power supply 电源箱DT Desk Top 卧式(机箱)MT Mini-Tower 立式(机箱)DVD Digital V edio DiskVCD Vdeio Compact DiskLCD Liquid Crystal DisplayCAD Computer AID DesignCAM Computer AID ManufacturingCAE Computer AID EngineeringABIOS Achanced Basic in put/outputsystem 先进的基本输入/输出系统CMOS Complemeruary Metoll OxideSemiconductor 互补金属氧化物半导体PDA Personal Digital Assistant 个人数字助理IC Integrated Circuit 集成电路ISA Industry Standard Architecture工业标准体制结构MCA Micro Channel Architecture微通道结构EISA Extended Industry StandardArchitecture 扩充的工业标准结构SIMM Single in-line memory module单项导通汇流组件DIMM Dual in-line Memory Module双项导通汇流组件LED Light-Emitting Diode 发光二级管FMEA Failure Mode Effectivenes 失效模式分析W/H Wire Harness 金属线绪束集组件F/C Flat Calle 排线PCB Printed Circuit Board 印刷电路板CAR Correction Action Report 改善报告NG Not Good 不良8WPR Weekly Delivery Requirement 周出货要求PPM Parts Per Million 百万分之一TPM Total Production Maintenance 全面生产保养MRP Material Requiremcnt Planning 物料需计划OC Operation System 作业系统TBA To Be Design 待定,定缺D/C Drawing ChangeP/P Plans & ProceduneEMI Electrical-Music Industry 电子音乐工业RFI Read Frequency Input 读频输入MMC Maximum Material Condition MMS Maximum Material SizeLMC Least Material ConditionLMS Least Material Size模具技术用语各种模具常用成形方式accurate die casting 精密压铸powder forming 粉末成形calendaring molding 压延成形powder metal forging 粉末锻造cold chamber die casting 冷式压铸precision forging 精密锻造cold forging 冷锻press forging 冲锻compacting molding 粉末压出成形rocking die forging 摇动锻造compound molding 复合成形rotary forging 回转锻造compression molding 压缩成形rotational molding 离心成形dip mold 浸渍成形rubber molding 橡胶成形encapsulation molding 注入成形sandmold casting 砂模铸造extrusion molding 挤出成形shellcasting 壳模铸造foam forming ?泡成形sinter forging烧结锻造forging roll 轧锻six sides forging 六面锻造gravity casting 重力铸造slush molding凝塑成形hollow(blow) molding 中空(吹出)成形squeeze casting 高压铸造hot chamber die casting 热室压铸swaging 挤锻hot forging 热锻transfer molding 转送成形injection molding 射出成形warmforging 温锻investment casting 精密铸造matcheddie method 对模成形法laminating method 被覆淋膜成形lowpressure casting 低压铸造lost wax casting 脱蜡铸造matchedmould thermal forming 对模热成形模各式模具分类用语bismuth mold 铋铸模landed plungermold 有肩柱塞式模具burnishing die 挤光模landed positivemold 有肩全压式模具button die 镶入式圆形凹模loadingshoe mold 料套式模具center-gated mold 中心浇口式模具loose detail mold 活零件模具chill mold 冷硬用铸模loose mold 活动式模具clod hobbing 冷挤压制模louvering die百叶窗冲切模composite dies 复合模具manifold die分歧管模具counter punch 反凸模modular mold组合式模具double stack mold 双层模具multi-cavity mold 多模穴模具electroformed mold 电铸成形模multi-gate mold 复式浇口模具expander die 扩径模offswt bendingdie 双折冷弯模具extrusion die 挤出模palletizing die 叠层模family mold 反套制品模具plastermold 石膏模blank through dies 漏件式落料模porous mold 通气性模具duplicated cavity plate 复板模positivemold 全压式模具fantail die 扇尾形模具pressure die 压紧模fishtail die 鱼尾形模具profile die 轮廓模flash mold 溢料式模具progressive die顺序模gypsum mold 石膏铸模protable mold手提式模具hot-runner mold 热流道模具prototypemold 雏形试验模具ingot mold 钢锭模punching die 落料模lancing die 切口模raising(embossing)压花起伏成形re-entrant mold 倒角式模具sectionaldie 拼合模runless injection mold 无流道冷料模具sectional die 对合模具segment mold 组合模semi-positivemold 半全压式模具shaper 定型模套single cavity mold 单腔模具solid forging die 整体锻模split forgingdie 拼合锻模split mold 双并式模具sprueless mold无注道残料模具squeezing die 挤压模stretch form die拉伸成形模sweeping mold 平刮铸模swing die 振动模具three plates mold 三片式模具trimming die 切边模unit mold 单元式模具universal mold通用模具unscrewing mold 退扣式模具yoke9type die 轭型模模具厂常用之标准零配件air vent vale 通气阀anchor pin 锚梢angular pin 角梢baffle 调节阻板angular pin 倾斜梢baffle plate 折流档板ball button 球塞套ball plunger 定位球塞ball slider 球塞滑块binder plate 压板blank holder 防皱压板blanking die 落料冲头bolster 上下模板bottom board 浇注底板bolster 垫板bottom plate 下固定板bracket 托架bumper block 缓冲块buster 堵口casting ladle 浇注包casting lug 铸耳cavity 模穴(模仁) cavity retainer plate 模穴托板center pin 中心梢clamping block 锁定块coil spring 螺旋弹簧cold punched nut 冷冲螺母cooling spiral 螺旋冷却栓core 心型core pin 心型梢cotter 开口梢cross 十字接头cushion pin 缓冲梢diaphragm gate 盘形浇口die approach 模头料道die bed 型底die block 块形模体die body 铸模座die bush 合模衬套die button 冲模母模die clamper 夹模器die fastener 模具固定用零件die holder 母模固定板die lip 模唇die plate 冲模板die set 冲压模座direct gate 直接浇口dog chuck 爪牙夹头dowel 定位梢dowel hole 导套孔dowel pin 合模梢dozzle 辅助浇口dowel pin 定位梢draft 拔模锥度draw bead 张力调整杆drive bearing传动轴承ejection pad 顶出衬垫ejector 脱模器ejector guide pin 顶出导梢ejectorleader busher 顶出导梢衬套ejector pad 顶出垫ejector pin 顶出梢ejector plate 顶出板ejector rod 顶出杆ejector sleeve 顶出衬套ejector valve顶出阀eye bolt 环首螺栓filling core 椿入蕊film gate 薄膜形浇口finger pin 指形梢finish machined plate 角形模板finishmachined round plate 圆形模板fixed bolster plate 固定侧模板flangedpin 带凸缘?flash gate 毛边形浇口flask 上箱floating punch 浮动冲头gate 浇口gate land 浇口面gib 凹形拉紧?goose neck 鹅颈管guide bushing 引导衬套guide pin 导梢guide post 引导柱guide plate 导板guide rail 导轨head punch 顶?冲头headless punch直柄冲头heavily tapered solid 整体模蕊盒hosenippler 管接头impact damper 缓冲器injection ram压射柱塞inlay busher 嵌入衬套inner plunger内柱塞inner punch 内冲头insert 嵌件insert pin 嵌件梢king pin 转向梢king pin bush 主梢衬套knockout bar脱模杵land 合模平坦面land area 合模面leader busher 导梢衬套lifting pin 起模顶?lining 内衬locating center punch 定位中心冲头locating pilot pin 定位导梢locatingring 定位环lock block 压块locking block 定位块locking plate 定位板loose bush 活动衬套making die 打印冲子manifold block歧管档块master plate 靠模样板match plate 分型板mold base 塑胶模座mold clamp 铸模紧固夹mold platen 模用板moving bolster 换模保持装置moving bolster plate 可动侧模板onepiece casting 整体铸件parallel block 平行垫块paring line 分模线parting lock set 合模定位器pass guide穴型导板peened head punch 镶入式冲头pilotpin 导?pin gate 针尖浇口plate 衬板pre extrusion punch 顶挤冲头punch冲头puncher 推杆pusher pin 衬套梢rack 机架rapping rod 起模杆re-entrant mold 凹入模retainer pin 嵌件梢retainer plate 托料板return pin 回位梢riding stripper 浮动脱模器ring gate环型浇口roller 滚筒runner 流道runner ejector set 流道顶出器runnerlock pin 流道拉梢screw plug 头塞set screw 固定螺丝shedder 脱模装置shim 分隔片shoe 模座之上下模板shoot 流道shoulder bolt 肩部螺丝skeleton 骨架slag riser 冒渣口slide(slide core) 滑块slip joint 滑配接头spacer block 间隔块spacer ring 间隔环spider 模蕊支架spindle 主轴sprue 注道sprue bushing 注道衬套sprue bushingguide 注道导套10。
汽车钢板弹簧中英对照

因为在弹簧这个行业中工作时间尚短,而平时也主要是一些资料翻译的工作,所以这里我仅对弹簧相关的翻译做了一个小结,希望能和大家一起分享,大家可以一起讨论下。
行业专业术语问题刚开始工作的时候觉得很困难,因为学校学的东西似乎都没有什么用,因为需要翻译的都是一些非常专业的行业术语。
根本不知道该用哪些词来表达这些术语,感觉很无助。
建议方法:1.还是那句话,该背的单词一定要背。
但是如果你日常翻译的工作量比较大,那么你就不用刻意的去背,因为你使用这些词语的频率很高,这样你在使用的时候慢慢就熟练了。
2.不知道大家有没有注意到一些行业的标准,其实每个行业里有很多国外的标准,而这些标准大家平时有时间是一定要看的,因为标准里的翻译都是很专业,很正规的。
甚至有时候你会发现你要翻译的那句话标准里有原句,呵呵。
我就碰到过这种情况。
而且多看看标准对提高自己的英语水平很有帮助,有时候你会发现英语没那么难的。
3.其实有的行业之间的英语是相通的,比如弹簧的好多词汇是可以用在别的机械产品中的,所以平时注意总结相关通用的词汇也是一个学习词汇的方法。
日常翻译问题1.相信大家平常翻译最多的就是电子邮件了吧,信件的翻译还是比较容易的,一般不会出现太深的词汇。
翻译的时候个人觉得只要能把自己的意思准确表达出来就可以了,没有必要使用一些很难很复杂的词语。
商务信件其实最重要的是做到及时回信,不要让你的客户等太久,让机会溜走。
如果回信晚了记得要向对方说声sorry,如果有原因的话就把原因写上,这样是对对方的一种尊重。
2.对于一些专业资料的翻译,上面提到的行业标准是一定要看的。
而且要注意英语版本里常用到的一些词组,其实好多词组是非常实用的,我平时碰到一些常用的词组会用本子记下来,这样当自己翻译的时候可以拿来借鉴一下。
小结其实说到底,学习英语是没有捷径的,只有多用、多看、多记才是最好的办法。
当然要注意学习的方法,我觉得最好的方法就是从身边的东西开始学习,随时注意身边的英语。
冲压机械及周边关连用语中英文对照
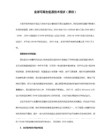
中国矿山机械设备网 冲压机械及周边关连用语中英文对照
back shaft 支撑轴 blank determination 胚料展开
bottom slide press 下传动式压力机 board drop hammer 板落锤
brake 煞车 buckle 剥砂面
core compound 砂心黏结剂 counter blow hammer 对击锻锤
cradle 送料架 crank 曲柄轴
crankless 无曲柄式 cross crank 横向曲轴
cushion 缓冲 depression 外缩凹孔
dial feed 分度送料 die approach 模口角度
中国矿山机械设备网
camlachie cramp 铸包 casting on flat ?合
chamotte sand 烧磨砂 charging hopper 加料漏斗
clearance 间隙 closed-die forging 合模锻造
clump 夹紧 clutch 离合器
die assembly 合模 die cushion 模具缓冲垫
die height 冲压闭合高度 die life 模具寿命
die opening 母模逃孔 die spotting press 调整冲模用压力机
double crank press 双曲柄轴冲床 draght angle 逃料倾斜角
clutch brake 离合器制动器 clutch boss 离合器轮壳
Hale Waihona Puke clutch lining 离合器覆盖 coil car 带卷升降运输机
coil cradle 卷材进料装置 coil reel stand 钢材卷料架
冲压件中英文对照

地板通道前上加强板 REINF - TUNNEL UPR FRONT 转向管柱上支架 BRKT - UPR STRG COLUMN 转向管柱下支架 BRKT - LWR STEERING COLUMN 前地板 PANEL - FRONT FLOOR 地板右侧纵梁 LONGITUDINAL - FLOOR CENTER RH SIDE 地板左侧纵梁 LONGITUDINAL - FLOOR CENTER LH SIDE 地板右侧围板 PANEL - FLOOR SIDE RH 地板左侧围板 PANEL - FLOOR SIDE LH 地板通道上加强件 REINF - TUNNEL UPR REAR 前座椅前横梁 C/MBR - FRONT SEAT FRONT 右前座椅后横梁 C/MBR - FRONT SEAT REAR RH 左前座椅后横梁 C/MBR - FRONT SEAT REAR LH 前座椅后安装点内加强板 REINF - INR. RR C/MBR FR SEAT SUPPORT 右前座椅后横梁外加强板 REINF - OTR. RR C/MBR FR SEAT SUPPORT RH 左前座椅后横梁外加强板 REINF - OTR. RR C/MBR FR SEAT SUPPORT LH 座椅安全带固定支座加强板 REINF- SEAT BELT ANCHOR 中地板 PANEL - REAR FLOOR FRONT 后地板 PANEL - REAR FLOOR REAR 后地板前横梁 C/MBR - REAR FLOOR CENTER 中地板前横梁 C/MBR - REAR FLOOR FRONT
A 柱上加强板 REINF - FRONT PILLAR UPR RH A 柱上加强板 REINF - FRONT PILLAR UPR LH 右前门上铰链加强板 REINF - FRT DOOR HINGE UPPER RH 左前门上铰链加强板 REINF - FRT DOOR HINGE UPPER LH 右前门下铰链加强板 REINF - FR DOOR HINGE LOWER RH 左前门下铰链加强板 REINF - FR DOOR HINGE LOWER LH 顶盖右侧纵梁 RAIL - ROOF SIDE RH 顶盖左侧纵梁 RAIL - ROOF SIDE LH 右B 柱内板 PANEL - "B" PILLAR INNER RH 左B 柱内板 PANEL - "B" PILLAR INNER LH 右侧门铰链和座椅安全带加强板 REINF - SEAT BELT AND DR HINGE RH 左侧门铰链和座椅安全带加强板 REINF - SEAT BELT AND DR HINGE LH 右侧门槛加强板 REINF - ROCKER RH 左侧门槛加强板 REINF - ROCKER LH
冲压英汉对照

序号工序名称缩写英文全称1 剪断SH Shear2 落料BL Blank3 切割CUT Cut4 冲缺NOT Notch5 冲孔PI或PRC Piercing6 剪边TR Trimming7 分割SEP Separating8 修边SHV Shaving9 引伸DR Draw10 再引伸RDR Redraw11 成形FO From12 辗制成形RO-FO Roll-from13 伸展抽制成形SDF Stretch-draw froming14 整形RST Restricting15 压印EMB Emboss16 叠接JOG Joggle17 弯边FL Flange18 密闭弯曲HEM Hemming19 翻孔BUR Burring20 卷边CRL Curling21 凸胀BLG Bulge22 缩紧NEK Necking23 弯曲BE Bend24 侧冲孔CAMPI或CAMPRC25 包边HEM Hemming26 弯曲整形FL RST Flange And Restricting27 落料.冲孔BL+PRC Blank And Piercing28 剪边.冲孔TR+PRC Trimming And Piercing plain die简易模pierce die冲孔模forming die成型模progressive die连续模gang dies复合模shearing die剪边模riveting die铆合模pierce冲孔forming成型(抽凸,冲凸) draw hole抽孔bending折弯trim切边emboss凸点dome凸圆semi-shearing半剪stamp mark冲记号deburr or coin压毛边punch riveting冲压铆合side stretch侧冲压平reel stretch卷圆压平groove压线blanking下料stamp letter冲字(料号) shearing剪断tick-mark nearside正面压印tick-mark farside反面压印extension dwg展开图procedure dwg工程图die structure dwg模具结构图material材质material thickness料片厚度factor系数upward向上downward向下press specification冲床规格die height range适用模高die height闭模高度burr毛边gap间隙weight重量total wt.总重量punch wt.上模重量。
冲压模具中英文对照

冲压模具中英文对照Stamping die is a key component in the stamping process, and it plays a crucial role in shaping metal sheets into desired forms. 冲压模具是冲压工艺中的关键组件,它在将金属板材成形为所需形状中发挥着至关重要的作用。
Stamping die is commonly used in various industries such as automotive, aerospace, electronics, and construction. 冲压模具通常被广泛应用于汽车、航空航天、电子和建筑等各个行业。
The design and manufacturing of stamping die require high precisionand expertise. 冲压模具的设计和制造需要高度的精密度和专业知识。
The quality of stamping die directly affects the quality and efficiency of the stamping process. 冲压模具的质量直接影响了冲压过程的质量和效率。
Therefore, it is important to understand the characteristics and functions of stamping die in order to produce high-quality products. 因此,了解冲压模具的特点和功能对于生产高质量产品是非常重要的。
Stamping die can be classified into various types based on their functions, such as blanking die, piercing die, bending die, and progressive die. 根据其功能,冲压模具可以被分类为各种类型,如剪床模、冲孔模、弯曲模和级进模。
冲压机械关连用语英汉对照

back shaft ⽀撑轴 blank determination 胚料展开bottom slide press 下传动式压⼒机 board drop hammer 板落锤brake 煞车 buckle 剥砂⾯camlachie cramp 铸包chamotte sand 烧磨砂 charging hopper 加料漏⽃clearance 间隙 closed-die forging 合模锻造clump 夹紧 clutch 离合器clutch brake 离合器制动器 clutch boss 离合器轮壳clutch lining 离合器覆盖 coil car 带卷升降运输机coil cradle 卷材进料装置 coil reel stand 钢材卷料架column 圆柱 connection screw 连杆调节螺钉core compound 砂⼼黏结剂 counter blow hammer 对击锻锤cradle 送料架 crank 曲柄轴crankless ⽆曲柄式 cross crank 横向曲轴cushion 缓冲 depression 外缩凹孔dial feed 分度送料 die approach 模⼝⾓度die assembly 合模 die cushion 模具缓冲垫die height 冲压闭合⾼度 die life 模具寿命die opening 母模逃孔 die spotting press 调整冲模⽤压⼒机double crank press 双曲柄轴冲床 draght angle 逃料倾斜⾓edging 边锻伸 embedded core 加装砂⼼feed length 送料长度 feed level 送料⾼度filling core 埋⼊砂⼼ filling in 填砂film play 液⾯花纹 fine blanking press 精密下料冲床forging roll 辊锻机 finishing slag 炼后熔渣fly wheel 飞轮 fly wheel brake 飞轮制动器foot press 脚踏冲床 formboard 进模⼝板frame 床⾝机架 friction 摩擦friction brake 摩擦煞车 gap shear 凹⼝剪床gear 齿轮 gib 滑块引导部gripper 夹具 gripper feed 夹持进料gripper feeder 夹紧传送装置 hammer 槌机hand press ⼿动冲床 hand rack pinion press ⼿动齿轮齿条式冲床hand screw press ⼿动螺旋式冲床 hopper feed 料⽃送料idle stage 空站 inching 微调尺⼨isothermal forging 恒温锻造 key clutch 键槽离合器knockout 脱模装置 knuckle mechanic 转向机构land 模具直线⼑⾯部 level ⽔平loader 供料器 unloader 卸料机loop controller 闭回路控制器 lower die 下模micro inching device 微⼨动装置 microinching equipment 微动装置motor 马达 moving bolster 活动⼯作台notching press 冲缺⼝压⼒机 opening 排料逃孔overload protection device 防超载装置 pinch roll 导正滚轮pinion ⼩齿轮 pitch 节距pressfit 压⼊ progressive 连续送料pusher feed 推杆式送料 pusher feeder 料⽚押⽚装置quick die change system 快速换模系统 regrinding 再次研磨releasing 松释动作 reversed blanking 反转下料robot 机器⼈ roll forming machine 辊轧成形roll forming machine 辊轧成形机 roll release 脱辊roller feed 辊式送料 roller leveler 辊式矫直机rotary bender 卷弯成形机 safety guard 安全保护装置scrap cutter 废料切⼑ scrap press 废料冲床seamless forging ⽆缝锻造 separate 分离shave 崩砂 shear angle 剪⾓sheet loader 薄板装料机 shot 单⾏程⼯作shrinkage fit 收缩配合 shut height 闭合⾼度sieve mesh 筛孔 sintering of sand 铸砂烧贴slide balancer 滑动平衡器 slug hole 逃料孔spin forming machine 旋压成形机 spotting 合模stack feeder 堆叠拨送料机 stickness 黏模性straight side frame 冲床侧板 stretcher leveler 拉伸矫直机strip feeder 料材送料装置 stripping pressure 弹出压⼒stroke 冲程 take out device 取料装置toggle press 肘杆式压⼒机 transfer 传送transfer feed 连续⾃动送料装置 turrent punch press 转塔冲床two speed clutch 双速离合器 uncoiler 闭卷送料机unloader 卸载机 vibration feeder 振动送料机wiring press 嵌线卷边机。
汽车冲压件中英文名称对照表
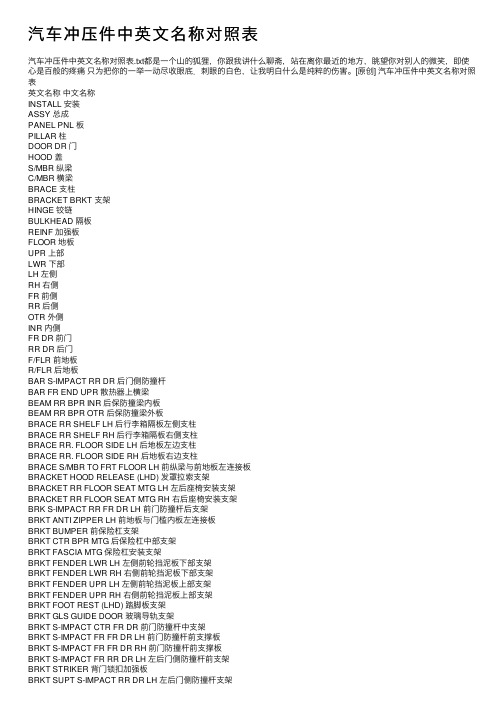
汽车冲压件中英⽂名称对照表汽车冲压件中英⽂名称对照表.txt都是⼀个⼭的狐狸,你跟我讲什么聊斋,站在离你最近的地⽅,眺望你对别⼈的微笑,即使⼼是百般的疼痛只为把你的⼀举⼀动尽收眼底.刺眼的⽩⾊,让我明⽩什么是纯粹的伤害。
[原创] 汽车冲压件中英⽂名称对照表英⽂名称中⽂名称INSTALL 安装ASSY 总成PANEL PNL 板PILLAR 柱DOOR DR 门HOOD 盖S/MBR 纵梁C/MBR 横梁BRACE ⽀柱BRACKET BRKT ⽀架HINGE 铰链BULKHEAD 隔板REINF 加强板FLOOR 地板UPR 上部LWR 下部LH 左侧RH 右侧FR 前侧RR 后侧OTR 外侧INR 内侧FR DR 前门RR DR 后门F/FLR 前地板R/FLR 后地板BAR S-IMPACT RR DR 后门侧防撞杆BAR FR END UPR 散热器上横梁BEAM RR BPR INR 后保防撞梁内板BEAM RR BPR OTR 后保防撞梁外板BRACE RR SHELF LH 后⾏李箱隔板左侧⽀柱BRACE RR SHELF RH 后⾏李箱隔板右侧⽀柱BRACE RR. FLOOR SIDE LH 后地板左边⽀柱BRACE RR. FLOOR SIDE RH 后地板右边⽀柱BRACE S/MBR TO FRT FLOOR LH 前纵梁与前地板左连接板BRACKET HOOD RELEASE (LHD) 发罩拉索⽀架BRACKET RR FLOOR SEAT MTG LH 左后座椅安装⽀架BRACKET RR FLOOR SEAT MTG RH 右后座椅安装⽀架BRK S-IMPACT RR FR DR LH 前门防撞杆后⽀架BRKT ANTI ZIPPER LH 前地板与门槛内板左连接板BRKT BUMPER 前保险杠⽀架BRKT CTR BPR MTG 后保险杠中部⽀架BRKT FASCIA MTG 保险杠安装⽀架BRKT FENDER LWR LH 左侧前轮挡泥板下部⽀架BRKT FENDER LWR RH 右侧前轮挡泥板下部⽀架BRKT FENDER UPR LH 左侧前轮挡泥板上部⽀架BRKT FENDER UPR RH 右侧前轮挡泥板上部⽀架BRKT FOOT REST (LHD) 踏脚板⽀架BRKT GLS GUIDE DOOR 玻璃导轨⽀架BRKT S-IMPACT CTR FR DR 前门防撞杆中⽀架BRKT S-IMPACT FR FR DR LH 前门防撞杆前⽀撑板BRKT S-IMPACT FR FR DR RH 前门防撞杆前⽀撑板BRKT S-IMPACT FR RR DR LH 左后门侧防撞杆前⽀架BRKT STRIKER 背门锁扣加强板BRKT SUPT S-IMPACT RR DR LH 左后门侧防撞杆⽀架BRKT SUPT S-IMPACT RR DR RH 右后门侧防撞杆⽀架BRKT UPR BUMPER MTG 保险杠安装上⽀架BRKT ENG MOUNT 发动机悬置⽀架BRKT SPRING HOUSE RH 右前悬挂上⽀座BRKT FUEL TANK COMMON 油箱安装左后⽀架BRKT TRAILING ARM INR LH 左后悬挂纵臂安装内⽀架BRKT TRAILING ARM INR RH 右后悬挂纵臂安装内⽀架BRKT TRAILING ARM OTR LH 左后悬挂纵臂外⽀架BRKT TRAILING ARM OTR RH 右后悬挂纵臂外⽀架BULKHEAD HINGE FRT LWR LH 左侧前门下部铰链加强板隔板BULKHEAD HINGE FRT LWR RH 右侧前门下部铰链加强板隔板BULKHEAD R/FLR S/MBR LH 后地板左纵梁隔板BULKHEAD R/FLR S/MBR RH 后地板右纵梁隔板BULKHEAD SILL 门槛隔板C/MBR BACKBONE 中央通道横梁C/MBR FR END OTR 散热器下横梁外板C/MBR R/FLR 后地板中横梁C/MBR R/SEAT 后地板前横梁下板C/MBR F/FLR LH 前地板左前横梁C/MBR F/FLR RH 前地板右前横梁C/MBR F/FLR RR LH 前地板左后横梁C/MBR FR END, INR CTR 散热器下横梁中内板C/MBR FR END, INR LH 散热器下横梁左内板CHNL GLS GUIDE FR FR DR LH 左前门玻璃导轨CHNL GLS GUIDE FR FR DR RH 右前门玻璃导轨CHNL GLS GUIDE FR RR DR LH 左后门玻璃导轨CHNL GLS GUIDE FR RR DR RH 右后门玻璃导轨CHNL GLS GUIDE RR FR DR RH 右前门后玻璃导轨CHNL GLS GUIDE UPR RR DR LH 左后门上玻璃导轨CHNL GLS GUIDE UPR RR DR RH 右后门上玻璃导轨EXT DASH PANEL LH 前围挡板左下板EXT DASH PANEL RH 前围挡板右下板EXT C/MBR R/FLR LH 后地板中横梁与纵梁左连接板FRAME FR UPR INR LH 左翼⼦板加强梁内板FRAME FR UPR INR RH 右翼⼦板加强梁内板FRAME FR UPR OTR LH 左侧翼⼦板上部边梁外板FRAME FR UPR OTR RH 右侧翼⼦板上部边梁外板FRONT S/MBR REAR LH 左前纵梁与地板纵梁连接板FRONT, S/MBR REAR RH 右前纵梁与地板纵梁连接板HINGE FUEL FILLER DR 加油⼝盖铰链HOOK, MUFFLER B/BONE 中央通道消⾳器挂钩PANEL A PILLAR LWR LH 左A柱下板PANEL A PILLAR LWR RH 右A柱下板PANEL AIR EXTRACTION BOX OTR LH 左侧排⽓盒外板PANEL AIR EXTRACTION BOX OTR RH 右侧排⽓盒外板PANEL B PILLAR INNER LH 左侧B柱盖板PANEL B PILLAR INNER LH 左侧B柱内板PANEL B PILLAR INNER RH 右侧B柱盖板PANEL B PILLAR INNER RH 右侧B柱内板PANEL BODY SIDE OTR LH 左侧围外板PANEL BODY SIDE OTR RH 右侧围外板PANEL CANTRAIL INNER LH 左侧上边梁内板PANEL CANTRAIL INNER RH 右侧上边梁内板PANEL COWL TOP INR (LHD) 空⽓盒内板PANEL EXT REAR FLR FRT 后地板前连接板PANEL EXT REAR FLR RR 后地板后加强板PANEL FRONT FENDER LH 左前翼⼦板PANEL FRONT FENDER RH 右前翼⼦板PANEL FRT HEADER LWR 顶盖前横梁下部板PANEL PILLAR FR INR LH 左A柱内板PANEL PILLAR FR INR LH 左侧A柱内板PANEL PILLAR FR INR RH 右A柱内板PANEL PILLAR FR INR RH 右侧A柱内板PANEL REAR FLOOR 后地板PANEL REAR SHELF⾏李架隔板PANEL REINF FRT HINGE A PILLAR LH 左侧A柱铰链加强板PANEL REINF FRT HINGE A PILLAR RH 右侧A柱铰链加强板PANEL ROOF 顶盖PANEL ROOF BOW 顶盖中横梁PANEL RR END INR 后围内板PANEL RR END OTR 后围横梁外板PANEL RR HEADER UPR 顶盖后横梁上板PANEL RR QTR INR LWR LH 左后轮罩外板下段PANEL RR QTR INR LWR RH 右后轮罩外板下段PANEL RR QTR INR UPR LH 左后轮罩外板上段PANEL RR QTR INR UPR RH 右后轮罩外板上段PANEL RR. W/HSE INR LH 左轮罩内板PANEL RR. W/HSE INR RH 右轮罩内板PANEL SILL INR LH 前地板左门槛内板PANEL SILL INR LH 左门槛内板PANEL SILL INR RH 前地板右门槛内板PANEL SILL INR RH 右门槛内板PANEL SPRING HOUSE LH 左前悬挂⽀座下板PANEL SPRING HOUSE RH 右前悬挂⽀座下板PANEL COWL TOP OTR 空⽓盒外板PANEL DASH (LHD) 前围挡板PNL FR DR INR LH 左前门内板PNL FR DR INR RH 右前门内板PNL FR DR OTR LH 左前门外板PNL FR DR OTR RH 右前门外板PNL FUEL FILLER DR 加油⼝盖外板PNL HOOD INR 发罩内板PNL HOOD OTR 发罩外板PNL RR DR INR LH 左后门内板PNL RR DR INR RH 右后门内板PNL RR DR OTR LH 左后门外板PNL RR DR OTR RH 右后门外板PNL T-GATE INR 后背门内板PNL T-GATE OTR 后背门外板PNL TRUNK LID INR ⾏李箱盖内板PNL TRUNK LID OTR ⾏李箱盖外板PNL SPRING HOUSE LH 左后悬挂⽀座下板PNL SPRING HOUSE RH 右后悬挂⽀座下板REINF A PILLAR UPR LH 左侧A柱上部加强板REINF A PILLAR UPR RH 右侧A柱上部加强板REINF B PILLAR CTR LH 左B柱中加强板REINF B PILLAR CTR RH 右B柱中加强板REINF B PILLAR DOUBLER LH 左侧B柱铰链加强板REINF B PILLAR DOUBLER RH 右侧B柱铰链加强板REINF B PILLAR LH 左侧B柱加强板REINF B PILLAR RH 右侧B柱加强板REINF B PILLAR UPR LH 左侧B柱加强上段REINF B PILLAR UPR RH 右侧B柱加强上段REINF BRACE REAR SHELF LH ⾏李箱隔板左托架⽀柱REINF BUMP STOP RH 右侧缓冲器加强板REINF BUMPER STAY LH 后保险杠左缓冲⽀柱加强板REINF BUMPER STAY RH 后保险杠右缓冲⽀柱加强板REINF COWL TOP INR (LHD) 转向柱加强板REINF DASH PANEL CTR 前围挡板下加强板REINF DOOR CHECK LH 左侧前门限位器加强板REINF FR END C/MBR SIDE LH 散热器下横梁左侧加强板REINF FRAME UPR FR DR LH 左前门窗框加强板REINF FRAME UPR FR DR RH 右后门窗框加强板REINF FRAME UPR FR DR RH 右前门窗框加强板REINF FRAME UPR RR DR LH 左后门窗框加强板REINF FUEL FILLER DR 加油⼝盖加强板REINF HINGE FRT UPR LH 左侧前门上部铰链加强板REINF HINGE FRT UPR RH 右侧前门上部铰链加强板REINF HINGE RR DR LH 左后门铰链加强板REINF HINGE RR DR RH 右后门铰链加强板REINF HINGE T-LID LH ⾏李箱盖铰链左加强板REINF HINGE T-LID RH ⾏李箱盖铰链右加强板REINF HOOD HINGE LH 发动机罩左侧铰链加强板REINF LATCH FR DR LH 左前门锁加强板REINF LATCH FR DR RH 右前门锁加强板REINF LATCH RR DR RH 右后门锁加强板REINF REAR SHELF FRONT ⾏李架前加强板REINF SBELT SIDE LH 左前座安全带左下加强板REINF SBELT SIDE RH 左前座安全带左下加强板REINF SILL LH 左侧门槛加强板REINF SILL RH 右侧门槛加强板REINF STG COL BRKT (LHD) 转向柱⽀架REINF WAIST OTR RR DR RH 右后门窗沿外加强板REINF BACKBONE 中央通道加强板REINF ENG MOUNT 发动机悬置加强板REINF FR END C/MBR 散热器下横梁加强板REINF FR S/MBR INR, FR LH 左前纵梁内板前加强板REINF FR S/MBR INR, FR RH 右前纵梁内板前加强板REINF FR S/MBR INR, RR LH 左前纵梁内板后加强板REINF FR S/MBR OTR LH 左前纵梁外板加强板REINF FR S/MBR OTR REAR LH 左前纵梁外板后加强板REINF FR S/MBR OTR REAR RH 右前纵梁外板后加强板REINF FRT S/MBR, REAR LH 左前纵梁地板纵梁加强板REINF T/M MOUNT 变速箱悬置加强板REINF DASH PANEL (LHD) 前围挡板内加强板REINF R/FLR LH 后地板左加强板REINF R/FLR RH 后地板右加强板REINF C/MBR UPR LH 后地板前横梁下板左加强板REINF C/MBR UPR RH 后地板前横梁下板右加强板REINF R/FLR S/MBR FR LH 后地板左纵梁加强板REINF R/FLR S/MBR FR RH 后地板右纵梁加强板REINF R/FLR S/MBR LH 后地板左纵梁侧加强板REINF R/FLR S/MBR RH 后地板右纵梁侧加强板REINF S/BELT R/FLR 后座椅安全带内加强板S/MBR FR FLR LH 前地板左纵梁S/MBR FR FLR RH 前地板右纵梁S/MBR FR INR LH 左前纵梁内板S/MBR FR INR RH 右前纵梁内板S/MBR FR OTR LH 左前纵梁外板S/MBR FR OTR RH 右前纵梁外板SHIELD FR FENDER LH 左前挡泥板SHIELD FR FENDER RH 右前挡泥板SMBR RR FLR LH 后地板左纵梁SMBR RR FLR RH 后地板右纵梁SUPT R/FLR S/MBR LH 后地板左纵梁⽀架。
模具-冲压及工序英语用语之令狐文艳创作
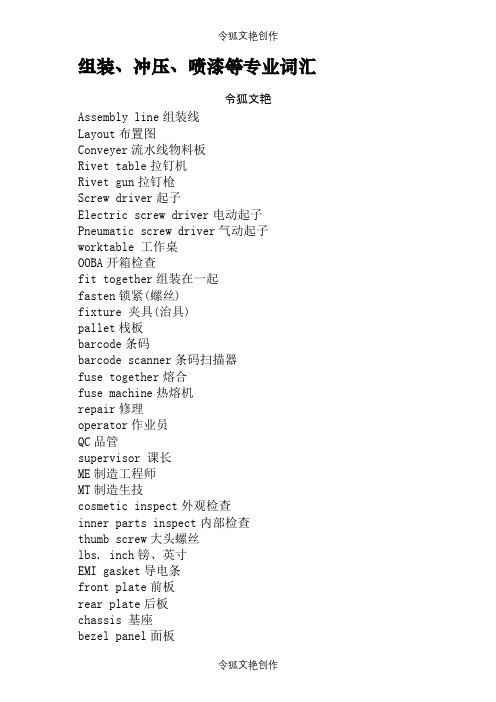
组装、冲压、喷漆等专业词汇令狐文艳Assembly line组装线Layout布置图Conveyer流水线物料板Rivet table拉钉机Rivet gun拉钉枪Screw driver起子Electric screw driver电动起子Pneumatic screw driver气动起子worktable 工作桌OOBA开箱检查fit together组装在一起fasten锁紧(螺丝)fixture 夹具(治具)pallet栈板barcode条码barcode scanner条码扫描器fuse together熔合fuse machine热熔机repair修理operator作业员QC品管supervisor 课长ME制造工程师MT制造生技cosmetic inspect外观检查inner parts inspect内部检查thumb screw大头螺丝lbs. inch镑、英寸EMI gasket导电条front plate前板rear plate后板chassis 基座bezel panel面板power button电源按键reset button重置键Hi-pot test of SPS高源高压测试Voltage switch of SPS电源电压接拉键sheet metal parts 冲件plastic parts塑胶件SOP制造作业程序material check list物料检查表work cell工作间trolley台车carton纸箱sub-line支线left fork叉车personnel resource department 人力资源部production department生产部门planning department企划部QC Section品管科stamping factory冲压厂painting factory烤漆厂molding factory成型厂common equipment常用设备uncoiler and straightener整平机punching machine 冲床robot机械手hydraulic machine油压机lathe车床planer |'plein|刨床miller铣床grinder磨床driller??床linear cutting线切割electrical sparkle电火花welder电焊机staker=reviting machine铆合机position职务president董事长general manager总经理special assistant manager特助factory director厂长department director部长deputy manager | =vice manager副理section supervisor课长deputy section supervisor =vice section superisor副课长group leader/supervisor组长line supervisor线长assistant manager助理to move, to carry, to handle搬运be put in storage入库pack packing包装to apply oil擦油to file burr 锉毛刺final inspection终检to connect material接料to reverse material 翻料wet station沾湿台Tiana天那水cleaning cloth抹布to load material上料to unload material卸料to return material/stock to退料scraped |'skræpid|报废scrape ..v.刮;削deficient purchase来料不良manufacture procedure制程deficient manufacturing procedure制程不良oxidation |' ksi'dein|氧化scratch刮伤dents压痕defective upsiding down抽芽不良defective to staking铆合不良embedded lump镶块feeding is not in place送料不到位stamping-missing漏冲production capacity生产力education and training教育与训练proposal improvement提案改善spare parts=buffer备件forklift叉车trailer=long vehicle拖板车compound die合模die locker锁模器pressure plate=plate pinch压板bolt螺栓name of a department部门名称administration/general affairs dept总务部automatic screwdriver电动启子thickness gauge厚薄规gauge(or jig)治具power wire电源线buzzle蜂鸣器defective product label不良标签identifying sheet list标示单screwdriver holder起子插座pedal踩踏板stopper阻挡器flow board流水板hydraulic handjack油压板车forklift叉车pallet栈板glove(s)手套glove(s) with exposed fingers割手套thumb大拇指forefinger食指midfinger中指ring finger无名指little finger小指band-aid创可贴iudustrial alcohol工业酒精alcohol container沾湿台head of screwdriver起子头sweeper扫把mop拖把vaccum cleaner吸尘器rag 抹布garbage container灰箕garbage can垃圾箱garbage bag垃圾袋chain链条jack升降机production line流水线chain链条槽magnetizer加磁器lamp holder灯架to mop the floor拖地to clean the floor扫地to clean a table擦桌子air pipe 气管packaging tool打包机packaging打包missing part漏件wrong part错件excessive defects过多的缺陷critical defect极严重缺陷major defect主要缺陷minor defect次要缺陷not up to standard不合规格dimension/size is a little bigger尺寸偏大(小) cosmetic defect外观不良slipped screwhead/slippery screw head螺丝滑头slipped screwhead/shippery screw thread滑手speckle斑点mildewed=moldy=mouldy发霉rust生锈deformation变形burr(金属)flash(塑件)毛边poor staking铆合不良excesssive gap间隙过大grease/oil stains油污inclusion杂质painting peel off脏污shrinking/shrinkage缩水mixed color杂色scratch划伤poor processing 制程不良poor incoming part事件不良fold of pakaging belt打包带折皱painting make-up补漆discoloration羿色water spots水渍polishing/surface processing表面处理exposed metal/bare metal金属裸露lack of painting烤漆不到位safety安全quality品质delivery deadline交货期cost成本engineering工程die repair模修enterprise plan = enterprise expansion projects企划QC品管die worker模工production, to produce生产equipment设备to start a press开机stop/switch off a press关机classification整理regulation整顿cleanness清扫conservation清洁culture教养qualified products, up-to-grade products良品defective products, not up-to-grade products不良品waste废料board看板feeder送料机sliding rack滑料架defective product box不良品箱die change 换模to fix a die装模to take apart a die拆模to repair a die修模packing material包材basket蝴蝶竺plastic basket胶筐isolating plate baffle plate; barricade隔板carton box纸箱to pull and stretch拉深to put material in place, to cut material, to input落料to impose lines压线to compress, compressing压缩character die字模to feed, feeding送料transportation运输(be)qualfied, up to grade合格not up to grade, not qualified不合格material change, stock change材料变更feature change 特性变更evaluation评估prepare for, make preparations for 准备parameters参数rotating speed, revolution转速manufacture management制造管理abnormal handling异常处理production unit生产单位lots of production生产批量steel plate钢板roll material卷料manufacture procedure制程operation procedure作业流程to revise, modify修订to switch over to, switch---to throw--over switching over切换engineering, project difficulty工程瓶颈stage die工程模automation自动化to stake, staking, reviting铆合add lubricating oil加润滑油shut die架模shut height of a die架模高度analog-mode device类模器die lifter举模器argon welding氩焊vocabulary for stamping冲压常词汇stamping, press冲压punch press, dieing out press冲床uncoiler & strainghtener整平机feeder送料机rack, shelf, stack料架cylinder油缸robot机械手taker取料机conveyer belt输送带transmission rack输送架top stop上死点bottom stop下死点one stroke一行程inch寸动to continue, cont.连动to grip(material)吸料location lump, locating piece, block stop 定位块reset复位smoothly顺利dent压痕scratch刮伤deformation变形filings铁削to draw holes抽孔inquiry, search for查寻to stock, storage, in stock库存receive领取approval examine and verify审核processing, to process加工delivery, to deliver 交货to return delivenry to.to send delinery backto retrn of goods退货registration登记registration card登记卡to control管制to put forward and hand in提报safe stock安全库存acceptance = receive验收to notice通知application form for purchase请购单consume, consumption消耗to fill in填写abrasion磨损reverse angle = chamfer倒角character die字模to collect, to gather收集failure, trouble故障statistics统计demand and supply需求career card履历卡to take apart a die卸下模具to load a die装上模具to tight a bolt拧紧螺栓to looser a bolt拧松螺栓to move away a die plate移走模板easily damaged parts易损件standard parts标准件breaking.(be)broken,(be)cracked 断裂to lubricate润滑common vocabulary for die engineering 模具工程常用词汇die 模具figure file, chart file图档cutting die, blanking die冲裁模progressive die, follow (-on)die连续模compound die复合模punched hole冲孔panel board镶块to cutedges=side cut=side scrap切边to bending折弯to pull, to stretch拉伸Line streching, line pulling线拉伸engraving, to engrave刻印upsiding down edges翻边to stake铆合designing, to design设计design modification设计变化die block模块folded block折弯块sliding block滑块location pin定位销lifting pin顶料销die plate, front board模板padding block垫块stepping bar垫条upper die base上模座lower die base下模座upper supporting blank上承板upper padding plate blank上垫板spare dies模具备品spring 弹簧bolt螺栓document folder文件夹file folder资料夹to put file in order整理资料spare tools location手工备品仓first count初盘人first check初盘复棹人second count 复盘人second check复盘复核人equipment设备waste materials废料work in progress product在制品casing = containerazation装箱quantity of physical invetory second count 复盘点数量quantity of customs count会计师盘,点数量the first page第一联filed by accounting department for reference会计部存查end-user/using unit(department)使用单位summary of year-end physical inventory bills年终盘点截止单据汇总表bill name单据名称This sheet and physical inventory list will be sent to accountingdepartment together (Those of NHK will be sent to financialdepartment)本表请与盘点清册一起送会计部-(NHK厂区送财会部) Application status records of year-end physical inventory List andphysical inventory card 年终盘点卡与清册使用-状况明细表blank and waste sheet NO.空白与作废单号plate电镀mold成型material for engineering mold testing工程试模材料not included in physical inventory不列入盘点sample样品incoming material to be inspected进货待验description品名steel/rolled steel钢材material statistics sheet物料统计明细表meeting minutes会议记录meeting type 会别distribution department分发单位location地点chairman主席present members出席人员subject主题conclusion结论decision items决议事项responsible department负责单位pre-fixed finishing date预定完成日approved by / checked by / prepared by核准/审核/承办PCE assembly production schedule sheetPCE组装厂生产排配表model机锺work order工令revision版次remark备注production control confirmation生产确认checked by初审approved by核准department部门stock age analysis sheet库存货龄分析表on-hand inventory现有库存available material良品可使用obsolete material良品已呆滞to be inspected or reworked待验或重工total合计cause description原因说明part number/ P/N 料号type形态item/group/class类别quality品质prepared by制表notes说明year-end physical inventory difference analysis sheet 年终盘点差异分析表physical inventory盘点数量physical count quantity帐面数量difference quantity差异量cause analysis原因分析raw materials原料materials物料finished product成品semi-finished product半成品packing materials包材good product/accepted goods/ accepted parts/good parts 良品defective product/non-good parts不良品disposed goods处理品warehouse/hub仓库on way location在途仓oversea location海外仓spare parts physical inventory list备品盘点清单spare molds location模具备品仓skid/pallet栈板tox machine自铆机wire EDM线割EDM放电机coil stock卷料sheet stock片料tolerance工差score=groove压线cam block滑块pilot导正筒trim剪外边pierce剪内边drag form压锻差pocket for the punch head挂钩槽slug hole废料孔feature die公母模expansion dwg展开图radius半径shim(wedge)楔子torch-flame cut火焰切割set screw止付螺丝form block折刀stop pin定位销round pierce punch=die button圆冲子shape punch=die insert异形子stock locater block定位块under cut=scrap chopper清角active plate活动板baffle plate挡块cover plate盖板male die公模female die母模groove punch压线冲子air-cushion eject-rod气垫顶杆spring-box eject-plate弹簧箱顶板bushing block衬套insert 入块club car高尔夫球车capability能力parameter参数factor系数。
- 1、下载文档前请自行甄别文档内容的完整性,平台不提供额外的编辑、内容补充、找答案等附加服务。
- 2、"仅部分预览"的文档,不可在线预览部分如存在完整性等问题,可反馈申请退款(可完整预览的文档不适用该条件!)。
- 3、如文档侵犯您的权益,请联系客服反馈,我们会尽快为您处理(人工客服工作时间:9:00-18:30)。
美国DELTA 控制器用于板簧冲孔成型设备改造北京市思路盛自动化系统集成有限公司 孙涛 slsheng@Joining workcells together and streamlining output from one stage to the next, if done correctly, is a surefire way to boost metalforming productivity. One company proving this out, Dayton Parts, Harrisburg, PA, manufactures for the vehicle aftermarket. Part of a manufacturing operation that dates to the 1920s, the company’s leaf-spring production process was upgraded this past year to automate and connect the leaf punching and forming processes into a smooth flow (Fig. 1).将不同加工单元重新组合形成一条连续生产的设备一定会大大提高生产效率。
美国Dayton Parts ,Harrisburg ,PA 一家做车辆配件设备的公司对此进行了成功的实践。
这台设备1920年就投入使用了。
最近这家公司将生产板簧的冲压和成型工序组合在一起形成了协调地连续作业。
Dayton Parts’ leaf springs,made from 1⁄2- to 1-5⁄8-in.-thick 6150-grade high-carbon bar stock, must beheated to 1800 F in bothpunching and formingproduction steps. Beforethe streamlining upgrade,this meant heating thesprings twice. Now, withthe new closely coupledarrangement, the leafsprings need only oneheating prior to punchingand forming, saving energyand time, and as much asdoubling processthroughput. Dayton 配件生产的板簧规格从1/2英寸(26.2 mm )到1-5/8英寸厚(41.275mm ) 6150级高碳棒料材料,有冲孔和成型工序。
在冲孔和成型工序前分别需要将零件加热到982摄氏温度。
在改造前加工板簧需要两次加热。
改造后重新组合加工工序,只要加热一次就可以完成冲孔和成型,既节能省时还能成倍提高产量。
The integrated Dayton Parts workcell has proven the advantage of close coupling and networking of processing stages. The updated line has reduced reheat and changeover downtime to a minimum, while achieving cycle times as short as 17 sec. per part. Fig. 1—This CAD rendering shows the forming station (right) and the punch press (left), with the furnace in the middle. Leaf-spring material moves right-to-left from the furnace to the punch press, and then left-to-right to the forming station. 这个CAD 图形中右边边是成型设备左边是冲孔设备加热炉在中间。
板簧片由加热炉出来后移至左边完成冲孔再移至右边成型。
“We’re seeing 95 percent combined uptime for the machines,” says Joseph Garcia,project manager for Dayton Parts, “and the material handling and energy savings for the company were sufficiently large to pay for this project in one year.”组合在一起的加工工序充分展示了工序衔接距离短,每个工序衔接及时的好处。
经过改造后的生产线避免了重复加热,衔接时间短到17秒。
Dayton 配件的项目经理Joseph Garica 总结说:“改造后设备提升了95%的生产效率。
材料消耗和能源的节省是如此大,我们一年就可以收回这个项目的投资。
Motion Controllers Ke y to Combined Processes运动控制器是实现组合工序的关键 Achieving rapid cycle times forthe combined machine requiresprecise control and closecommunication between the motion operations performed inthe process stages. Supervisorycontrol is performed by aprogrammable logic controller(PLC), but to control theindividual motion axes, PLCswith special capabilities formultiaxis coordination arerequired. At therecommendation of localdistributor Penn-Air & Hydraulics of York, PA, Dayton Parts’engineers chose the RMC150and RMC75 motion controllers from Delta Computer Systems, Inc., Battle Ground, WA. 实现组合工序的高速生产要求在生产的每个环节都有精密控制和快速通讯交换数据。
整个设备的整体控制可以通过PLC 来完成,但是各个定位轴的控制需要有多轴控制能力的PLC 来完成。
在当地分销商 Penn-Air & Hydraulics 的推荐下Dayton 配件的工程师选择了美国DELTA 计算机系统有限公司的RMC150和RMC75运动控制器。
The hot punch for the leaf-spring process is powered by six motion axes (Fig. 2) under control of the RMC150—no problem, as a single RMC150 can control and coordinate the motion of as many as eight axes simultaneously. A pusher axis advances the part against an end gauge, which is positioned by another motion actuator to oppose the pusher in order to set the length between the end of the plate and the center hole to be punched. Two centering jaws along the width of the plate activate to center the hole accurately along that width. The pusher and end-gauge axes travel via position control, Fig. 2—A detailed rendering of the hot punch shows the six motion-control axes used in its operation.详细结构图展示冲孔设备六个轴的作用while the centering jaws use position and force control. One jaw moves to a target position and the other jaw uses force control to clamp the part.板簧热冲孔工序由六个运动轴通过RMC150来控制。
RMC150最多可以同时控制8个轴。
一个推动机构将零件推到末端调整机构,这个机构由另外一个轴定位以保证两个定位板的中心点正好是中心冲孔的位置。
推动机构轴和端部调整机构轴都是位置控制。
还有两个轴用来定位零件两侧,使零件在横向也在中间位置。
两侧轴一个是位置控制另外一个是力控制来夹紧零件。
“The ability tocombine differenttypes of axis controlin one system wasvery helpful,” saysGreg Shortridge,Dayton Partselectrical engineer.“Using position andforce control, wecan ensure that theparts are securelyheld, at the sametime avoiding therisk of damage dueto clamping themtoo tightly. Dayton 配件的工程师 Greg Shortridge 说:“在一个控制系统中有位控和力控的轴对我们很有帮助,这样能准确定位,又能稳稳的保持在定位位置上,还不会因为力过大而夹坏零件。
“And we had never used force control before,” he adds. “But performing pressure/force control was simple using the Delta controllers.”他还说:我们是第一次用力控制方式,没想到的是用DELTA 控制器做力控制很方便。