排气方式和排气槽的设计
模具排气镶件的排气原理

模具排气镶件的排气原理模具排气镶件是一种用于模具中的排气装置,它的设计原理是通过合理的结构和材料选择,使得模具在工作过程中能够有效地排出气体,确保模具的正常运行和产品的质量。
排气是模具注塑过程中非常重要的一个环节,它直接影响到产品的质量和生产效率。
在注塑过程中,由于塑料熔化后会产生气体,如果没有良好的排气装置,这些气体就会被困在模具中,造成气泡、缺陷等问题,甚至会导致模具损坏。
因此,模具排气镶件的作用就是通过设计合理的结构,将这些气体顺利排出,保证模具和产品的质量。
模具排气镶件的排气原理主要包括以下几点:1. 气体的产生:在注塑过程中,由于塑料在加热和熔化的过程中会释放气体,这些气体主要来自于塑料的分解、挥发和反应等过程。
同时,还可能会产生一些溶解在塑料中的气体,如水分、空气等。
2. 气体的运动:在注塑过程中,由于塑料的流动和压缩,气体会被挤压和推动,沿着塑料流动的方向逐渐向模具的出口移动。
同时,由于注塑速度和压力的变化,气体也会产生剧烈的运动和振荡。
3. 排气通道的设计:模具排气镶件通常包括排气孔、排气槽和排气道等部分。
排气孔是指通过模具的壁面或部件上开设的小孔,用于气体的排出。
排气槽是指模具中的一个凹槽,用于收集和导向气体。
排气道是指将排气孔和排气槽连接起来的通道,它可以是直线的,也可以是弯曲的,甚至可以是螺旋状的。
4. 排气效果的评估:模具排气镶件的设计需要考虑气体的排出速度和排气压力等因素。
一方面,如果排气速度过快,会导致塑料流动受阻和产生缺陷;另一方面,如果排气速度过慢,会导致气体无法及时排出,造成气泡和缺陷。
因此,需要通过实验和模拟计算等方法,评估排气效果,确定最佳的排气设计。
模具排气镶件的排气原理是通过合理的结构和通道设计,将注塑过程中产生的气体顺利排出,确保模具和产品的质量。
在实际应用中,我们需要根据具体的注塑工艺和产品要求,选择合适的材料和设计参数,确保排气效果达到最佳状态。
只有这样,才能保证模具的寿命和产品的质量,提高生产效率和经济效益。
住宅厨卫排气道施工工法

住宅厨卫排气道施工工法XX公司XX1、前言随着人民生活水平的不断提高,对居住环境提出了新的要求,小康住宅就是优化其质量与功能,室内环境质量又是其中重要指标之一。
厨房及卫生间是住宅的“心脏”,住宅厨房油烟及卫生间民异味污染困扰着亿万家庭。
其排污长期没有得到彻底解决,使原设计住宅就像一个“先天性心脏病”患者,成为一种病态建筑,给以后的改造带来较大的困难。
排气道成功地解决了一这难题。
排气道是必须按照《住宅设计规范》GB50096-2011生产的,需要满足住宅厨房排油烟及卫生间排异味的要求的同时,又得有防止上下楼层之间互相串烟、串味功能的新型产品,能有效的解决生活气体对居住空间环境的污染问题。
目前,作为住宅厨卫系统中不可缺少的一部分,排气道已经越来越多的被运用到现代住宅的厨卫排气通风当中。
2、工法特点2。
1安装制成的排气道最佳截面尺寸满足了每户厨房排油烟风量大于360Ma/h的要求,提高了排污效率,改善了环境质量。
2。
2该工艺中排气道采用主、支管道构造,对变压板和导向管结构形状进行了优化设计,能自动防止各层厨房之间互相串烟、串味、交叉污染。
2.3该工艺中排气道采用钢丝网水泥砂浆薄壁(15mm)预制工艺,产品使用寿命长、强度高、安装方便。
2。
4该工艺中排气道具有防腐、防燃、防潮和防雨、雪倒灌等特点,广泛适用于各类住宅的厨房、卫生间.3、适用范围其适用范围为:适用于广大的现代住宅建筑的排风系统当中.4、工艺原理排气道的工作原理如下:住宅厨房内的油烟气体或者卫生间内的污浊空气,在排油烟机或者排气扇的机械推动下,通过连接软管送入竖向安装的排气道中,顺着排气道上升送至楼顶,通过出气口排出.在寒冷的冬季,室内烟气的温度较高、密度较小,室外大气的温度较低、密度较大;冷热气流之间的密度差,有利于排气道内的烟气上升,这种现象称为“拔烟”;热烟的温度与冷空气的温度差别越大,“拔烟”效果就越好.当烟气通过机械设备和“拔烟”方式排除之后,必将在厨房或者卫生间内形成一定的负压,在室内外压力差的作用下,新鲜空气被吸入到厨房、卫生间内.一般来说,楼顶的风速比较高,风吹到楼顶上的障碍物(例如:斜屋面、高位水池等)时,就会形成紊乱的气流,甚至发生风吹倒灌的现象,影响排气道的排烟效果。
塑胶模具排气槽的设计探讨
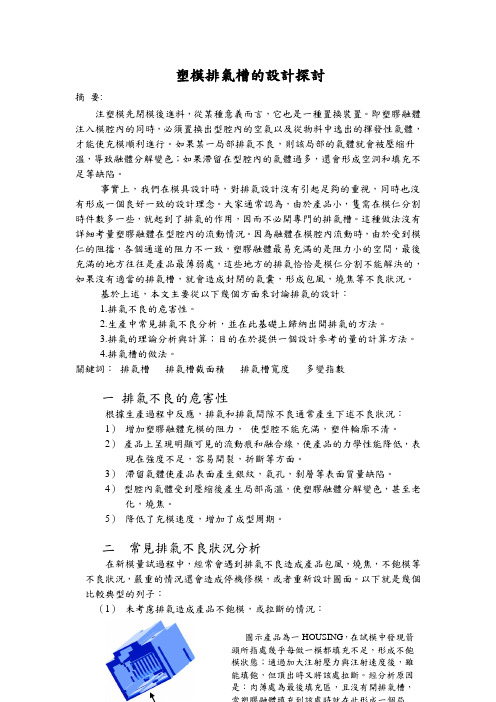
三 排氣槽位置選擇的一般原則
根據典型不良狀況分析,排氣槽位置的選擇,主要考慮以下幾個方面:
(1)產品的薄壁處;這裡通常為塑膠融體最後填充區域。
(2)流程的最終點;PIN多,體長的產品尤其要考慮這一點。
(3)兩股料流的匯合處。
通常取一摩爾理想氣體在00C,標準大氣壓時來計算氣體摩爾常數R(一摩爾氣體在標準狀況時體積為22.4升);由(1)式變換得:
R=P0*V0/n*T0=1.013*105*22.4*10-3/1.0*273.15
= 8.31(N*m/ml*K)
根據V.V.sushkov實驗,型腔內的氣體,可以引用以下的氣體計算公式:
n=Lg(P1/P0)/Lg(V1/V0)
=Lg(20/0.1)/Lg(100/1.0)=1.15
則型腔內氣體最終溫度:
T1=T0*(P1/P0)(1.15-1.0)/1.15= T0*(P1/P0)0.13-----(5)
式中:P0-----型腔內氣體的初始壓力(0.1Mpa)
T0---模具內氣體的初始溫度;T0=20+273=293K
Vmax=1.15*S*P0*(R*T1)-1/2-----(2)
式中:Vmax----氣體排除的最大質量速度(kg/s)
S--------排氣槽截面積(m2)
P0-------型腔內氣體的初始壓力(1.013*105Pa)
R-------摩爾氣體常數(前面已介紹)
T1------型腔內氣體最終溫度(K)
充填不良,成品外觀接合線,燒焦等
不良現象都與排氣不良有關,除了
應做好排氣設置外,其次要依成型
厨房装修中的排气系统设计

厨房装修中的排气系统设计厨房装修中的排气系统设计是一个至关重要的环节,它不仅能够有效排除厨房中产生的油烟和异味,还能够保护家人的健康和延长厨房的使用寿命。
在进行厨房装修时,排气系统设计是必不可少的一部分,下面我们来详细介绍一下在厨房装修中排气系统设计的一些注意事项。
首先,要选择适合的抽油烟机。
抽油烟机是排气系统设计中最重要的设备之一,它能够有效地抽走厨房中产生的油烟和异味。
在选择抽油烟机时,需要考虑到厨房的大小、炉灶的位置以及使用频率等因素。
一般来说,如果厨房比较小,可以选择壁挂式的抽油烟机;如果厨房比较大,可以选择岛式或吸顶式的抽油烟机。
此外,还要注意选择抽油烟机的风量和噪音级别,确保其能够有效地排除油烟和异味的同时,又不会给家庭生活带来太大的噪音。
其次,要合理布置排气管道。
排气管道是连接抽油烟机和排气口的重要组成部分,它的设计和布置直接影响着排气系统的效果。
在布置排气管道时,首先要保证管道的通畅,避免出现死角或弯曲过多的情况,从而影响排气系统的正常运行。
另外,还要避免排气管道通过潮湿的地方或易燃易爆的区域,以免造成安全隐患。
最好将排气管道尽可能地延长到室外,这样能够有效地将油烟和异味排放到室外,不会对室内空气质量造成影响。
再次,要定期清洗和维护排气系统。
排气系统长时间使用后,会积累一定的油垢和灰尘,如果不及时清洗和维护,会导致排气系统的效果下降甚至出现堵塞的情况。
因此,在日常生活中要定期清洗抽油烟机的油网和油杯,清洗排气管道及排气口,以确保排气系统的畅通。
另外,还要定期检查抽油烟机和排气管道是否有损坏或老化的情况,如有需要及时更换和维修,以保证排气系统的正常运行。
最后,要考虑排气系统的附属设备。
除了抽油烟机和排气管道之外,还可以考虑安装一些附属设备来提升排气系统的效果。
比如,可以在厨房墙面或天花板上安装除湿机或净化器,以减少油烟和异味的产生;也可以安装温度探测器或智能开关,实现排气系统的智能化和自动化控制。
压铸模具排气技术之浪板排气法

2.5 最新技术
图1-铝液通过浪板1时 出现了喷溅
图2-同样的铝液,在 浪板2内流动了很短的 距离
Why?
2.6 铜,Be-Cu
使用Be-Cu浪板的好处: 1.热传导性是钢的7倍,排气间隙要比 钢大1.4~1.8倍,排气效率是钢的3~8倍。
钢 2.Be-Cu不与材料粘附
3.2 3D浪板材质
Bi-Cu
H13
Ejector Pin
Ejector Pin
3.3 3D浪板规格
3.4 Compared to a normal chill vent
三、浪板的设计
1.设计流程
铸件
2.浪板设计的主要参数
排气渐变位置长度 排气口长度 波浪板长度 排气通道宽度 浪板宽度 排气通道进口厚度 浪板斜面排气间隙 浪板平面排气间隙 浪板波峰间距离 浪板波峰内距离 浪板波峰高度 浪板波峰间角度 30~60度
浪板可以超出模框,但不应过大;过大时,后面需加支撑。
7.3浪板上一般要设计顶出顶针,防止脱模困难。
7.4浪板排气位置的变化。
7.5浪板与排气槽配合设计细节
本设计说明: 1.集中一个浪板设计时, 设计排气槽的原则是尽可能使金属汤同时到达排气口 2.并不是所有溢流井都要开排气槽 3.排气槽可以增加深度方向,但宽度方向不要太大。
3.間隙大小
浪板的间隙大小要认真考量
与下列因素有关 1.铸造合金 2.铸件末端距离排气板距离 3.浪板的材质 4.浪板是否有冷却水路 5.浪板的波浪数
手绘草图
4.浪板的“波浪”形式
Triangular vs Trapezoid
Pressures by Varying Venting Area
模具设计习题与答案

模具设计习题与答案模具设计习题与答案模具是用来成型物品的工具,这种工具由各种零件构成,不同的模具由不同的零件构成。
下面是店铺整理的模具设计习题与答案,欢迎大家参考。
填空1. 分型面的形状有平面、斜面、阶梯面、曲面。
2. 分型面选择时为便于侧分型和抽芯,若塑件有侧孔或侧凹时,宜将侧型芯设置在垂直开模方向上,除液压抽芯机构外,一般应将抽芯或分型距较大的放在开模方向上。
3. 为了保证塑件质量,分型面选择时,对有同轴度要求的塑件,将有同轴度要求的部分设在同一模板内。
4. 为了便于排气,一般选择分型面与熔体流动的末端相重合。
5. 为了便于塑件的脱模,在一般情况下,使塑件在开模时留在动模或下模上。
6. 注射模分流道设计时,从传热面积考虑,热固性塑料宜用梯形截面和半圆形截面分流道;热塑性塑料宜用圆形分流道。
从压力损失考虑,圆形截面分流道最好:从加工方便考虑用梯形、U形或矩形分流道。
7. 在多型腔模具中,型腔和分流道的排列有平衡式和非平衡式两种。
8. 当型腔数较多,爱模具尺寸限制时,通常采用非平衡布置。
由于各分流道长度不同,可采用将浇口设计成不同的截面尺寸来实现均衡进料,这种方法需经多次试模和整修才能实现。
9. 浇口的类型可分点浇口、侧浇口、直接浇口、中心浇口、潜伏式浇口、护耳浇口六类。
10. 浇口截面形状常见的有矩形和圆形。
一般浇口截面积与分流道截面之比为3%~9%,浇口表面粗糙度值不低于为0.4um。
设计时浇口可先选取偏小尺寸,通过试模逐步增大。
11. 注射模的排气方式有开设排气槽排气和利用模具分型面可模具零件的配合间隙自然排气。
排气槽通常开设在型腔最后被填充的部位。
最好开在分型面上,并在凹模一侧,这样即使在排气槽内产生飞边,也容易随塑件脱出。
12. 排气是塑件成型的需要,引气是塑件脱模的需要。
13. 常见的引气方式有镶拼式侧隙引气和气阀式引气两种。
判断1. 侧浇口包括扇形浇口和薄片式浇口,扇形浇口常用来成型宽度较大薄片状塑件;薄片式浇口常用来成型大面积薄板塑件(√)2. 成型零件的磨损是因为塑件与成型零件在脱模过程中的相对摩擦及熔体冲模过程中的冲刷。
7.压铸模溢流槽和排气槽的设计探讨

7. 压铸模溢流槽和排气槽的设计探讨第九届中国国际压铸会议论文集??压铸模溢流槽和排气槽的设计探讨刘遵建旭东压铸(上海)有限公司摘要:这里探讨的压铸模溢流槽、溢流口和排气槽的各种结构模式、形状、尺寸,是自己对平时工作的总结,与大家共享,希望能够对您的压铸模设计和使用有所帮助。
其中大多数内容是许多压铸工程师经常使用的一些方法,有些观点是我个人的认识,不一定成熟,如果有不确之处,请大家批评指正,共同提高。
关键词:压铸模具溢流槽;溢流口;排气槽;排气块;真空阀;压铸工艺?在压铸模型腔适当的位置,布置容量大小合适的溢流槽和排气槽,能够改善填充条件,提高铸件质量。
而合适的溢流槽和排气槽结构形式,不仅可以提高排液和排气的效率,还能使溢流槽和排气槽处不出现飞边、飞料,使压铸生产得以顺利进行。
这里介绍了溢流槽、溢流口、排气槽的深度、宽度大小,探讨了溢流槽、溢流口和排气槽的各种结构模式。
其中的每种结构模式都可以单独使用,也可以组合使用,都能够起到较好的排液、排气和防止飞边的效果。
图1、图2是一些常见的溢流槽和排气槽的结构图片。
图1 溢流槽和排气槽的照片-1图2 溢流槽和排气槽的照片-21??第九届中国国际压铸会议论文集??压铸模的溢流排气系统,是浇注系统不可缺少的帮手,是一颗大树的树干与绿叶的关系。
设计好的溢流排气系统,不仅能够促使压铸出质量良好的铸件,还能解决影响压铸生产顺利进行的飞边问题。
从模具需要长久生产、顺利的使用来看,在溢流排气部位产生的飞边缺陷(见图3、图4),是影响压铸顺利进行的主要原因。
压铸出现的飞边,不仅仅是模具的制造问题,也不仅是压射速度和压射压力的问题,重要的一点是压铸模的溢流排气系统结构设计的问题,要从溢流槽和排气槽的结构上,达到有效的排液、排气,防止飞边、飞料,让操作压铸的工人师傅少一点辛苦,多一些安全。
图3??模具分型面的飞边?A BC图4 排气块部位的飞边A、B排气块分型面密封不严密有飞边,C 排气块的齿形侧面面密封不严密有飞边 1 型腔在定模一侧的溢流口和溢流槽的结构形式(1)平直连接的溢流口(见图5),内浇口连接在铸件的侧面。
《塑料注塑模结构设计》7成型零部件设计7
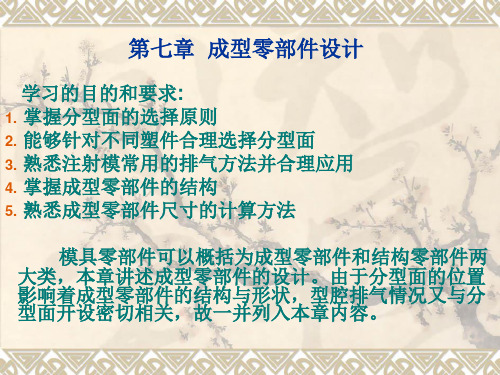
5 瓣合式凹模(镶拼式凹模) 镶拼式凹模)
组成凹模的每一个镶块都是活动的, 组成凹模的每一个镶块都是活动的,它们被模套或其他锁合装置 箍合在一起 适用: 适用:有侧凹或侧孔的制品 当瓣合模块数量等于2时 可将他们组成的凹模成为哈夫凹模。 当瓣合模块数量等于 时,可将他们组成的凹模成为哈夫凹模。
瓣合式凹模结构示意图
二 设计要点
排气槽(或孔 位置和大小的选定 主要依靠经验, 排气槽 或孔)位置和大小的选定,主要依靠经验,经过试模 或孔 位置和大小的选定, 后再修改或增加。 后再修改或增加。 基本的设计要点可归纳如下: 基本的设计要点可归纳如下: 1.排气要保证迅速、完全,排气速度要与充模速度相适应; .排气要保证迅速、完全,排气速度要与充模速度相适应; 2.排气槽(孔)尽量设在塑件较厚的成型部位 2.排气槽(孔)尽量设在塑件较厚的成型部位; 尽量设在塑件较厚的成型部位; 3.排气槽应尽量设在分型面上,但排气槽溢料产生的毛边应不 .排气槽应尽量设在分型面上, 妨碍塑件脱模; 妨碍塑件脱模; 4.排气槽应尽量设在料流的终点,如流道、冷料井的尽端; .排气槽应尽量设在料流的终点,如流道、冷料井的尽端; 5.为了模具制造和清模的方便,排气槽应尽量设在凹模的一面; .为了模具制造和清模的方便,排气槽应尽量设在凹模的一面; 6.排气槽排气方向不应朝向操作面,防止注射时漏料烫伤人; .排气槽排气方向不应朝向操作面,防止注射时漏料烫伤人; 7.排气槽 孔)不应有死角,防止积存冷料; 不应有死角, .排气槽(孔 不应有死角 防止积存冷料;
一 凹模结构设计
凹模是成型塑件外表面的成型零件。 凹模是成型塑件外表面的成型零件。 凹模的基本结构:整体式、整体嵌入式和组合式、镶拼式。 凹模的基本结构:整体式、整体嵌入式和组合式、镶拼式。
塑料注射成型模具排气槽的设计

消除制品的各种缺陷, 减少模具污染等。那么, 模腔 的排气怎样才算充分 呢?一般来说 , 以最高的注 若
射速率注射熔料, 在制品上却未留下焦斑, 就可以认 为模 腔 内的排气 是充 分 的。
1 2 排气 方式 .
当塑料熔体填充型腔时 , 必须按顺序排出型腔
及 浇注 系统 内的空气及 塑料受 热或凝 固产 生 的低 分
维普资讯
第 7卷 第 8期 20 0 7年 4月 17 ・89 20 ) 814 - 6 11 1 (07 0 .4 60 - - 5
科
学
技
术
与
工
程
V 1 7 N . Ap . 0 7 o. o 8 r2 0
S i n e T c n lg n n i e r g c e c e h oo y a d E g n e i n
@ 16. on。 2 ci
图 1 利用模具零件 的配合 间隙和分型面排气
( ) 分型 面上开设 排气 槽排气 。 2在 ( ) 用排气 塞排 气 。如 果 型腔 最后 充 填 的部 3利
通讯作者简介 : 进 (9 5 , , 周 16 一) 女 湖南南县人 , 副教授, 研究 方向: 计算机应用 与机 电工程。
一
一 (
\ V
。
^ ^
() a
016 ) 6) 2 和湖南铁道职业技术学院科研规划项 目 编号 K 0 ̄1 ) 0 ( 20 8 第一作者 简介 : 熊建武(9 4 ) 男 , 16 一 , 湖南安化 县人, 学硕士 , 工 副 教授、 高级工程师 , 研究方 向: 机电工程。E— a : og aw 2 0 m i x nj n u 06 li i
/一 。
排气槽的设计

在注射成型时,如果型腔内的气体不能在无模时顺利诽至模外.将会亦制品[:形成气孔、接缝、表面轮廓不治等缺陷。
右时封闭在如料焙体内的气体因爪缩所产生的高温会使制品局部烧焦,而且压缩气体所产生的压力还会降低充模速度.闽此在设计模具成型部件时必须考虑排气的问题。
在许多情况下,可利用模只的分型山之间的间隙白然排气。
例如小型制品的排气量不大,如果排气点正好公分型曲上,AVX钽电容就可利用分型面间的微小间隙排飞,M术必再开设专门的排气槽。
止因为大多数模具可从分型面处白然徘气.因此排气问题往往被设11人员所忽视。
屿制品采用特别会产生气体的塑料熔体时,或成型具有部分薄壁的制nDn以及采用快速注射丁艺时.必须妥善地处理排气问题。
徘气槽的位片及大小丰要依靠经验选定,通过试模修改,其基本设汁原则归纳如卜;(1)排气要迅速、充今,排气槽的排气速度要与充模速度相适应。
(2)排气楷应尽量开设在制nDn较厚的成型部位。
(3)徘气槽应尽坦开设人分型团上,但排气槽油料产生的毛边应不妨碍制从脱模。
(4)排气槽应尽量八设在刷腔中最后被充满的部位。
(;)为了制造模义和清模的方便,排气槽应尽量开设在凹模的一侧。
(6)排气槽徘气方向不应朝向下人操作而.以防注射成型时漏料伤人。
(7)排气槽深度一般不超过o.05mm,宽度一般不超过3mm,排气槽如图6 1所尔。
(8),IJ以利用推杆和推杆孔的Dd合间隙排气,也可以利用活动型芯7L的配合间隙排气,如图6—2所示。
峭诽气槽既大法设在分型面上,附近又入供排气的报杆或活动型芯时,可利用布型腔广镶嵌的烧结金属块排气,如图6—3所小G以球粒状原料制成的烧结金届块均具有良好的排气作用,烧结金属块下方的通气孔直径o不宜大大,否则烧站金属块受力后会变形。
wxq$#。
注射成型模具排气槽的设计

*该 课 题 由 2 0 0 6年 度 湖 南 省 高 等 学 校 科 学 研 究 项 目( 号 编
0 D 6 ) 湖 南 铁 道 职 业 技 术 学 院 科 研 规 划 项 目 ( 号 6 02和 编 K20 0 8 资 助 。 061)
加热 过程 中产生 的各种 气体 。越 是薄 壁制 品 , 越
Ke o d : lsis n e t n mo li g li g o le h u tn — lt d sg y w r s p a tc ijci udn o s d n to ; x a si g so ; ei n mo
塑料 注射 成 型模 具 的排 气方 式 和排 气 槽 结
是 远 离 浇 口 的部 位 , 气 槽 的开 设 就 显 得 越 重 排
要 。另外 对 于小 型 件 或精 密 零 件 也要 重 视 排 气
槽 的开设 , 因为它 除 了能避 免制 品表 面灼伤 和注
射 量 不足 外 , 可 以 消除 制 品 的各 种缺 陷 , 少 还 减
模具 污染 等 。一般 来说 , 以最高 的注射 速率 注 若 射熔 料 , 在制 品上未 留下 焦斑 , 可 以认 为模 腔 就
The wa fe ha s i — l ,he d sgn ng e pe i n e, r c i a y a t u t r fe ha s — y o x u tng sot t e i i — x re c p a tc lwa nd s r c u e o x u t i g s o r n r duc d n — l twe e i t o e.
维普资讯
现
代
塑
料
加
工
应
用
20 0 7年 6月
模具设计—排气系统
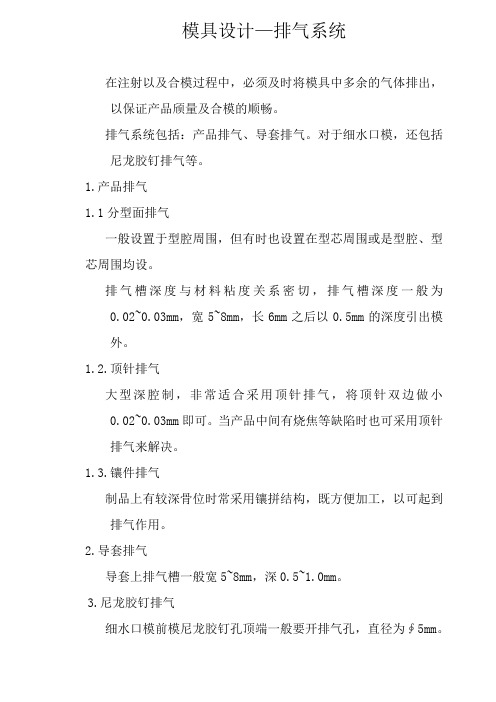
模具设计—排气系统
在注射以及合模过程中,必须及时将模具中多余的气体排出,以保证产品颀量及合模的顺畅。
排气系统包括:产品排气、导套排气。
对于细水口模,还包括尼龙胶钉排气等。
1.产品排气
1.1分型面排气
一般设置于型腔周围,但有时也设置在型芯周围或是型腔、型芯周围均设。
排气槽深度与材料粘度关系密切,排气槽深度一般为
0.02~0.03mm,宽5~8mm,长6mm之后以0.5mm的深度引出模
外。
1.2.顶针排气
大型深腔制,非常适合采用顶针排气,将顶针双边做小
0.02~0.03mm即可。
当产品中间有烧焦等缺陷时也可采用顶针
排气来解决。
1.3.镶件排气
制品上有较深骨位时常采用镶拼结构,既方便加工,以可起到排气作用。
2.导套排气
导套上排气槽一般宽5~8mm,深0.5~1.0mm。
3.尼龙胶钉排气
细水口模前模尼龙胶钉孔顶端一般要开排气孔,直径为∮5mm。
发泡模具排气装置设计

2.3 排气孔排气
排气孔形状:排 气孔设计形式多 种多样,但既要 有利于排气,又 要便于清理气孔, 常见的排气孔有 如下三种结构, 其中结构C最理 想。
2.2 排气槽排气
注射模具的排气槽应设置在塑料流动 的末端,一般常开设在分型面型腔一 侧,排气槽深可取,宽,以塑料不进 入排气槽为宜,其出口不要对着操作 工人,以防熔融塑料喷出造成事故, 有的厂推荐将分型面上的排气槽做成 弯形且逐步增宽,以降低塑料溢出的 可能。小型制件的排气量不大,如排 气点正好在分型面上,一般可以利用 分型面闭合时的微小间隙排气。
CLICK HERE TO ADD A TITLE
泡模具排气系统设计
此处添加副标题
冯
加
和
2
0
16Biblioteka 0913
1、概述
1、概述
在设计发泡成型模具时必须考虑排气问题。如果模具型腔内的气体不能 顺利排出,将造成制品的气泡、疏松、冲模不满、焊接不牢、制件表面 发乌或者在注射时由于气体被压缩所产生的高温制品底部碳化、烧焦, 而且型腔内气体被压缩产生的反压力会降低冲模速度,影响注射周期和 产品质量。
PM-35排气钢是一种优质透气性钢材,内部由微细的小孔相连构成,使空气 或任何气体能顺利渗透及穿过。因此,于注塑模具之适当位置镶上PM-35 排气钢,由气体所形成的注塑问题,可以完全清除,使成型加工更加完美。
2.3 排气钢排气
特性:1.降低注射压力,减少成型和保压时间。2.降低和消除成型件的内应力, 防止产品的变形和曲翘。3.表面皮纹的塑料零件,由于高温高压产生的亮光 皮纹,能解决要求亚光的表面。4.由于模具分型面的紧密配合,可以解决开模 困难等情况。解决通常利用顶针、镶件等无法提供足够表面区域以容纳可 能产生的大量气体等诸多问题,避免了利用分型面或其他排气系统而产生的 飞边及其他瑕疵。5.可使由于浇口偏位、壁厚不匀、壁薄产品等较难成型问 题得到解决和缓解。6.由于成型材料高温产生的气体和模具腔内快速聚压产 生的烧焦、流痕、缺料、吸气造成的零件变形等缺陷能得到充分解决。7.提 高成型生产效率,节约生产成本。
塑料模具与设计复习题及答案

一、填空1.制备合成树脂的方法有加聚反应和缩聚反应两种。
2.塑料制件生产的完整工序顺序为干燥、塑化、成型、冷却、脱模等,这一顺序不容颠倒。
3.塑料成型方法的种类很多,有压缩成型、压注成型、注射成型等。
4.分子定向会导致塑件力学性能的各向异性,顺着分子定向的方向上的机械强度总是大于与其垂直方向上的强度。
5.塑料一般是由高分子合成树脂和添加剂组成。
6.根据塑料的成份不同可以分为热塑性和热固性塑料。
7.塑料的主要成份有树脂、填充剂、增塑剂、稳定剂、润滑剂和着色剂等。
8.塑料的填充剂有机填料和无机填料。
其形状有粉状、纤维状和片状等。
9.塑料中的添加剂之一的稳定剂按其作用分为热稳定剂、光稳定剂和抗氧化剂。
10.根据塑料成型需要,工业上用于成型的塑料有粉料、粒料、溶液、和分散体等物料。
11.塑料按合成树脂的分子结构及热性能可分为热塑性塑料和热固性塑料两种。
12.塑料按性能及用途可分为通用塑料、特殊塑料、工程塑料。
13.塑料的性能包括使用性能和工艺性能,使用性能体现塑料的使用价值,工艺性能体现了塑料的成型特性。
14.塑料的使用性能包括:密度小、比强度和比刚度高、化学稳定性好、粘结性好、成型和着色性好等。
15.热固性塑料的工艺性能有:收缩性、流动性、比体积与压缩率、水分及挥发物含量、固化特性。
16.挤出成型时,在挤出过程中,塑料加压方式有连续加压和间断加压两种,因此,挤出成型工艺可分为连续和间间歇两种。
17.在挤出模塑中,塑件的形状和尺寸基本上取决于挤出机头和定型模。
18.中空吹塑根据成型方法可分为挤出吹塑中空成型、注射吹塑中空成型、注射延伸吹塑中空成型、多层吹塑中空成型、片材吹塑中空成型等五种。
19.泡沬塑料制件的成型方式有压制成型和低压发泡注射成型两种,生产泡沬塑料的方法可分为:机械法、物力法和化学法,按气孔结构不同泡沬塑料可分为开孔和闭孔,按塑料软硬程度不同可分为软质泡沫塑料和硬质泡沬塑料。
20.注射模塑工艺包括成型前的准备、注射过程、制品的后处理等工作。
注塑模具排气槽开的标准
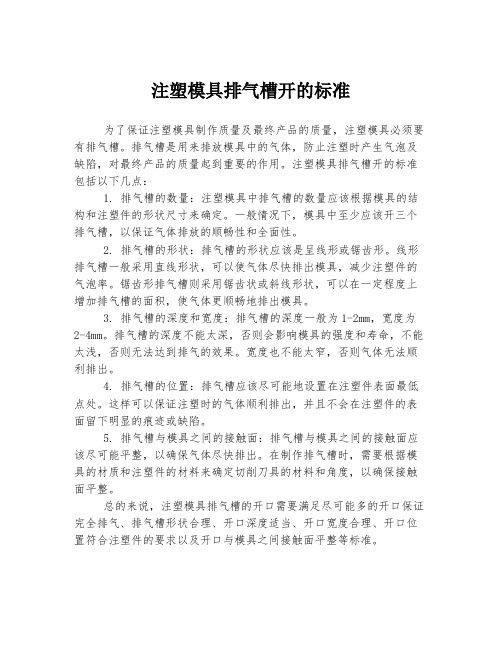
注塑模具排气槽开的标准
为了保证注塑模具制作质量及最终产品的质量,注塑模具必须要有排气槽。
排气槽是用来排放模具中的气体,防止注塑时产生气泡及缺陷,对最终产品的质量起到重要的作用。
注塑模具排气槽开的标准包括以下几点:
1. 排气槽的数量:注塑模具中排气槽的数量应该根据模具的结构和注塑件的形状尺寸来确定。
一般情况下,模具中至少应该开三个排气槽,以保证气体排放的顺畅性和全面性。
2. 排气槽的形状:排气槽的形状应该是呈线形或锯齿形。
线形排气槽一般采用直线形状,可以使气体尽快排出模具,减少注塑件的气泡率。
锯齿形排气槽则采用锯齿状或斜线形状,可以在一定程度上增加排气槽的面积,使气体更顺畅地排出模具。
3. 排气槽的深度和宽度:排气槽的深度一般为1-2mm,宽度为2-4mm。
排气槽的深度不能太深,否则会影响模具的强度和寿命,不能太浅,否则无法达到排气的效果。
宽度也不能太窄,否则气体无法顺利排出。
4. 排气槽的位置:排气槽应该尽可能地设置在注塑件表面最低点处。
这样可以保证注塑时的气体顺利排出,并且不会在注塑件的表面留下明显的痕迹或缺陷。
5. 排气槽与模具之间的接触面:排气槽与模具之间的接触面应该尽可能平整,以确保气体尽快排出。
在制作排气槽时,需要根据模具的材质和注塑件的材料来确定切削刀具的材料和角度,以确保接触面平整。
总的来说,注塑模具排气槽的开口需要满足尽可能多的开口保证完全排气、排气槽形状合理、开口深度适当、开口宽度合理、开口位置符合注塑件的要求以及开口与模具之间接触面平整等标准。
排气槽的合理设计及排气方法

适当地开设排气槽可以大大降低注射压力、注射时间、保压时间以及锁模压力,使塑件成型由困难变为容易,从而提高生产效率,降低生产成本,降低机器的能量消耗。
本标准生效日期为:2004年5月18日
在模具试模和生产中常会出现填充不足、压缩空气灼伤、制品内部很高的内应力、表面流线和熔合线等现象。对于这些现象除了应首先调整注塑工艺外,还要考虑模具浇口是否合理。当注塑工艺和浇口这两个问题都排除以后,那么模具的排气就是主要的问题了,解决这一问题的主要手段是开设排气槽。
排气槽的主要作用:
1、是在模具注胶时,排除模腔内的空气。
2、是排除胶料在加热过程中产生的各种气体。
一、排气槽的尺寸:
开排气槽时应注意两点:
1、排气槽在排气的同时,其尺寸设计应能防止物料溢进槽内。
2、防止排气槽堵塞。
排气槽宽度尺寸:
应根据模具大小取4-10mm之间,见图一
排气槽前端深度尺寸A:
要小于胶料益边值,排气槽前端长度取3-6mm,见表一
排气槽后端深度尺寸:
在封闭气体的部位,设置排气杆。此法排气效果好但会在塑件上留下杆件痕迹,故排气杆应设在塑件的隐蔽处。
三、排气设计时应注意的事项:
1、当排气极困难时采用镶拼结构,如果有些模具的死角不易开排气槽,首先应在不影响产品外观及精度的情况下适当把模具改为镶拼加工,这样不仅有利于加工排气还可以改善原有的加工难度和便于维修。
应根据模具大小取0.3-0.6mm之间,见图一
※排气影响分型面接触面积的大小所以排气槽数量太多是有害的。
二、注塑模具排气方法:
对于模腔模芯有以下几种排气方法:
1、水口排气:
2、分型面排气:
3、镶件和镶针排气:
对于镶拼式的型腔或型芯,可利用其拼合的缝隙排气。
- 1、下载文档前请自行甄别文档内容的完整性,平台不提供额外的编辑、内容补充、找答案等附加服务。
- 2、"仅部分预览"的文档,不可在线预览部分如存在完整性等问题,可反馈申请退款(可完整预览的文档不适用该条件!)。
- 3、如文档侵犯您的权益,请联系客服反馈,我们会尽快为您处理(人工客服工作时间:9:00-18:30)。
排气方式和排气槽的设计
1 .排气系统的作用
在塑料熔体向注射模型腔充满的过程中,熔体取代了型腔中的气体,在此过程中,如果气体不能及时排除,将会引起物料注射压力过大.熔体充填型腔困难。
同时,部分气体还会在压力作用下渗进塑料中去,使塑件产生气泡及组织疏松等缺陷,熔合不良而引起强度下降。
更有甚者,由于气体受到压缩,温度急剧上升,进而引起周围熔体烧灼,使塑件局部碳化和烧焦。
这种现象主要出现在两股料流结合处、死角以及与浇口相对的凸缘处。
烧灼的结果,使塑件表面产生焦斑,成为废品。
因此,在设计型腔结构与浇注系统时,必须考虑排气,这点对大型塑件、高速注射成型和热固性塑料成型尤为重要。
2 .排气结构设计
排气的方式有开设排气槽排气和利用模具零件配合间隙自然排气,所有排气的手段都将在塑件上留下痕迹,这点在设计时应该考虑.
l )排气指的开设位盆及形式
( l )排气槽的开设位置。
塑件的形状及其在模具中的位置、浇口的形状和位置对模具的排气具有很大的影响。
通常排气槽最好加工成弯曲状,其截面由细到粗逐渐加大,这样可降低塑料熔体从排气槽滋出的动能,同时还可降低塑料熔体世出流速,以防发生工伤事故。
选择排气槽的开设位里时,应遵循以下原则.
① 排气槽的排气口不能正对操作工人,以防熔料喷出而发生工伤事故。
② 排气梢最好开设在分型面上,因为在分型面上如果因设排气槽而产生飞边,易随塑件脱出。
通常,排气槽设在分型面凹模一侧,以便于模具加工及清模。
③ 排气槽应尽量开设在型腔最后被充满处,如流道和冷料穴的终端。
在确定浇口的位置时,还要考虑排气槽的开设是否方便.
④ 排气槽最好设在靠近嵌件和塑件壁最薄处,因为,这样的部位最容易形成熔接痕,宜排出气体.并排出部分冷料。
⑤ 若型腔最后充满部位不在分型面上,其附近又无可供排气的推杆或活动型芯时,可在型腔相应部位镶嵌烧结的多孔金属块,以供排气。
⑥ 在高速注射薄壁型制品时,排气槽设在浇口附近,可使气体连续排出而不产生明显的升压。
( 2 )排气槽的形式如表4 一15 所示。
2 )排气抽的尺寸
排气槽的宽度可取为1.5~ 6mm ,深度以塑料不滋进排气槽产生飞边为限,其大小与塑料熔体猫度有关,一般可在0.02 ~ 0.05mm 之间选择,可参考表4 一16 进行设计。
3) 间碑排气
在大多数情况下可利用模具分型面或模具零件间的配合间隙自然排气,可不另设排气槽,特别是对于中小型模具。
表4 一17 列出利用成型零件分型面配合间隙排气的几种形式,间隙值的大小和排气槽一样,以不产生溢料为限,其数据应根据塑料熔体流动性而定,与猫度有关,通常,可在0 . 02~ 0 . 05 mm 范围内选择。
若型腔最后充满部分不在分型面上,其附近又无可供排气的推杆或活动型芯时,可在型腔相应部位镶嵌烧结的多孔金属块以供排气。
作者:汽车模具 。