BGA、CSP焊点缺陷分析与自动X射线检测(AXI)图像的评估和判断
ICT、AOI、AXI检测知识

AXI(Advanced eXtensible Interface)是一种总线协议,该协议是ARM 公司提出的AMBA(Advanced Microcontroller Bus Architecture)3.0协议中最重要的部分,是一种面向高性能、高带宽、低延迟的片内总线。
它的地址/控制和数据相位是分离的,支持不对齐的数据传输,同时在突发传输中,只需要首地址,同时分离的读写数据通道、并支持显著传输访问和乱序访问,并更加容易就行时序收敛。
AXI(Automated X-Ray Inspection),自动X射线检测,光学检测系统的一种。
AXI测试技术AXI是近几年才兴起的一种新型测试技术。
当组装好的线路板(PCBA)沿导轨进入机器内部后,位于线路板上方有一X-Ray发射管,其发射的X射线穿过线路板后被置于下方的探测器(一般为摄象机)接受,由于焊点中含有可以大量吸收X射线的铅,因此与穿过玻璃纤维、铜、硅等其它材料的X射线相比,照射在焊点上的X射线被大量吸收,而呈黑点产生良好图像,使得对焊点的分析变得相当直观,故简单的图像分析算法便可自动且可靠地检验焊点缺陷。
AXI技术已从以往的2D检验法发展到目前的3D检验法。
前者为透射X 射线检验法,对于单面板上的元件焊点可产生清晰的视像,但对于目前广泛使用的双面贴装线路板,效果就会很差,会使两面焊点的视像重叠而极难分辨。
而3D检验法采用分层技术,即将光束聚焦到任何一层并将相应图像投射到一高速旋转的接受面上,由于接受面高速旋转使位于焦点处的图像非常清晰,而其它层上的图像则被消除,故3D检验法可对线路板两面的焊点独立成像。
3DX-Ray技术除了可以检验双面贴装线路板外,还可对那些不可见焊点如BGA等进行多层图象“切片”检测,即对BGA焊接连接处的顶部、中部和底部进行彻底检验。
同时利用此方法还可测通孔(PTH)焊点,检查通孔中焊料是否充实,从而极大地提高焊点连接质量。
X光机检测BGA 焊球虚焊情况分析-PPT课件

焊球明显偏大
OPEN
一 优良焊接质量BGA的判定方法
图一
图二
图一:运用VIEW-X的2D检测,可以明显看到BGA焊球中间有一圈颜色较深的“Dark Ring”;表明此BGA焊球的焊接质量非常好。 注:图一的“Dark Ring”,即图二黄色虚线与红色虚线二者之间的区域 图二:黄色虚线与红色虚线之间形成的“Dark Ring”区域,是焊锡膏完全熔融后,BGA 焊球与PCB的焊盘焊接良好,且焊锡膏对PCB焊盘有良好的“wetting”即润湿效 果,而形成的图形效果。
三、总结
BGA焊球的虚焊现象,在焊球底部与焊盘之间是非常细微的,所以对比度变 化很细微。目前市场上亦有运用3D 技术的X-RAY,意图是对焊球的虚焊进行直接 目视观察。其工作原理为:将探测器倾斜后围绕BGA焊球进行360度旋转,以创造 直接目视观察焊球底部与焊盘之间的焊接状况的机会。
而由于现代BGA封装技术,对高I/O数的不断要求和发展,也要求BGA焊球之间的 间距向更小间距发展。采用3D技术的检测设备,当其探测器在倾斜到一定角度时,焊球 与焊球之间因互相遮挡,对BGA内部的焊球底部,因“视线遮挡”已经无法直接观测。而 对BGA外部的焊球来说,也可能存在检测限制,即BGA旁边的其他元器件可能对BGA焊 球底部造成的“视线遮挡”,从而可能对3D检测效果产生不利影响。即便BGA旁边无其他 元器件对焊球造成遮挡时,3D检测手段亦只能对BGA焊球的外侧进行局部观察,这仍然 是因为BGA焊球之间因微小间距而造成的“视线遮挡”。所以3D检测虚焊,理论上是以通 过直接的目视观察,以提高“虚焊”检测的直观性,而实际操作中也存在着一定的局限性。 同时,3D检测手段除了上述的检测覆盖范围的局限性外,检测方法与手段太耗时,无法 满足制造厂商日益高密度、高速度的生产需求,也是突出的问题,同时制造厂商还必须 应对设备高投资,高维护成本的风险。
bga焊点的缺陷分析与工艺改进(doc11页)
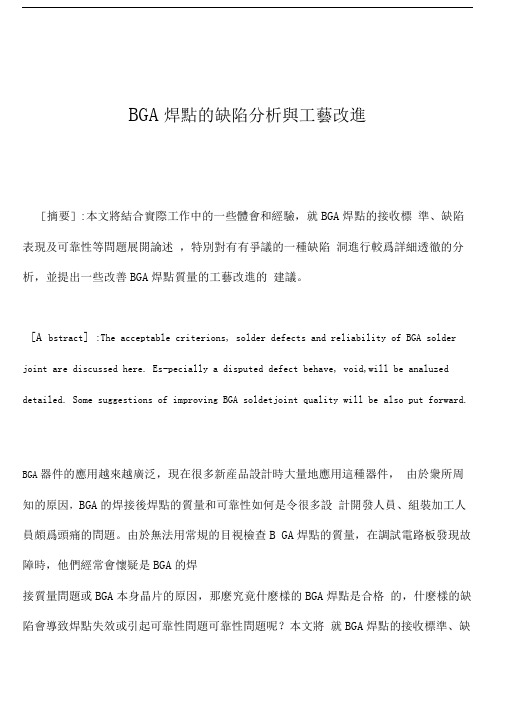
BGA焊點的缺陷分析與工藝改進[摘要]:本文將結合實際工作中的一些體會和經驗,就BGA焊點的接收標準、缺陷表現及可靠性等問題展開論述,特別對有有爭議的一種缺陷洞進行較爲詳細透徹的分析,並提出一些改善BGA焊點質量的工藝改進的建議。
[A bstract] :The acceptable criterions, solder defects and reliability of BGA solder joint are discussed here. Es-pecially a disputed defect behave, void,will be analuzed detailed. Some suggestions of improving BGA soldetjoint quality will be also put forward.BGA器件的應用越來越廣泛,現在很多新産品設計時大量地應用這種器件,由於衆所周知的原因,BGA的焊接後焊點的質量和可靠性如何是令很多設計開發人員、組裝加工人員頗爲頭痛的問題。
由於無法用常規的目視檢查B GA焊點的質量,在調試電路板發現故障時,他們經常會懷疑是BGA的焊接質量問題或BGA本身晶片的原因,那麽究竟什麽樣的BGA焊點是合格的,什麽樣的缺陷會導致焊點失效或引起可靠性問題可靠性問題呢?本文將就BGA焊點的接收標準、缺陷表現及可靠性等問題展開論述,特別對有爭議的一種缺陷空洞進行較爲透徹的分析。
1.BGA簡介BGA是一種球柵陳封裝的器件,它出現於20世紀90年代初,當時由於有引線封裝的器件引腳數越來越多,引線間距越來越小,最小的器件間距已經達到0.3mm(12mil), 這對於組裝來講,無論從可製造性或器件焊接的可靠性都已經達到了極限,出錯的機會也越來越大。
這時一種新型的球柵陣列封裝器件出現了,相對於同樣尺寸的QFP器件,BGA能夠提供多至幾倍的引腳數(對於BGA來講其晶片下面的焊球就相當於引腳)而引腳的間距還比較大,這對於組裝來講是件好事,可以大幅度地提高焊接合格率和一次成功率。
BGACSP焊点缺陷分析与自动X射线检测AXI图像的评估和判断

2D传输影象 局部放大 3D 影象
第14页/共21页
BGA焊球空洞的图像
2D传输影象 局部放大 3D 影象
第15页/共21页
X-ray焊点图像分析需将软件与工艺结合,与IPC-A-610D验收标准相结合。
第5页/共21页
(3)桥接和短路
焊膏量过多或印刷缺陷(焊膏图形粘连)贴片后手工拨正时由于焊膏滑动造成的焊接温度过高,焊料液态时间太长,焊球过度塌陷焊盘设计间距过窄造成的PBGA的塑料基板吸潮,焊接时在高温下水蒸气膨胀引起焊盘起翘,使相邻焊点桥接。
桥接和短路也是不可接受的,主要原因:
第6页/共21页
第11页/共21页
X-ray焊点图像分析
X射线透视图能够定量地显示出焊点厚度、形状及质量的密度分布。根据X射线检测到的厚度、形状及质量的密度分布指标及图像,结合强大的图像分析软件就能够分析和判断焊点的焊接质量
第12页/共21页
均匀一致的合格焊球
2D传输影象 3D 影象
第13页/共21页
(4)冷焊、锡球熔化不完全
焊点扰动是焊点冷却凝固时由于PCB震动,或由于加热过程中PCB膨胀变形,冷却凝固时PCB收缩变形应力造成的,无铅焊点表面粗糙不属于焊点扰动。
(5)焊点扰动
第7页/共21页
(6)移位(焊球与PCB焊盘不对准)
一种可能是由于贴片偏移过大造成的;另一个原因是焊接温度过低,焊接过程中没有到达使焊球完成二次下沉的温度,没有完成自校准效应就结束焊接。这种情况下,贴片造成的偏移量不能被纠正,因此会造成焊球与PCB焊盘不对准、看上去焊球的形状是扭曲的。
Socket BGA(BGA插座)
Pitch
直径
1.27mm
X射线检测焊缝图像中缺陷的分割与识别的开题报告
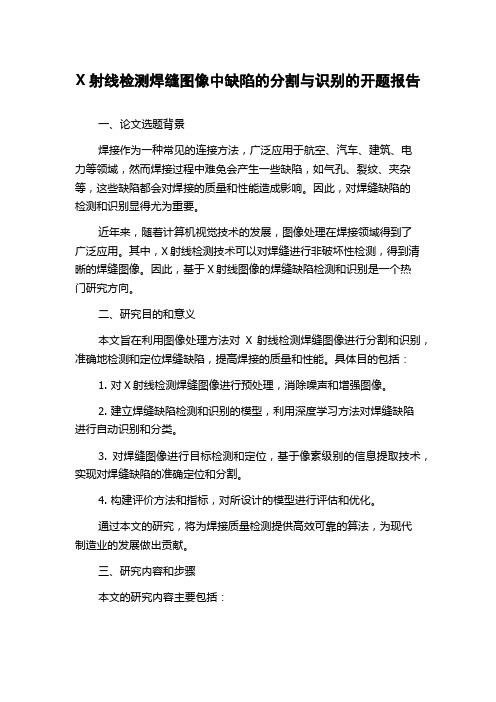
X射线检测焊缝图像中缺陷的分割与识别的开题报告一、论文选题背景焊接作为一种常见的连接方法,广泛应用于航空、汽车、建筑、电力等领域,然而焊接过程中难免会产生一些缺陷,如气孔、裂纹、夹杂等,这些缺陷都会对焊接的质量和性能造成影响。
因此,对焊缝缺陷的检测和识别显得尤为重要。
近年来,随着计算机视觉技术的发展,图像处理在焊接领域得到了广泛应用。
其中,X射线检测技术可以对焊缝进行非破坏性检测,得到清晰的焊缝图像。
因此,基于X射线图像的焊缝缺陷检测和识别是一个热门研究方向。
二、研究目的和意义本文旨在利用图像处理方法对X射线检测焊缝图像进行分割和识别,准确地检测和定位焊缝缺陷,提高焊接的质量和性能。
具体目的包括:1. 对X射线检测焊缝图像进行预处理,消除噪声和增强图像。
2. 建立焊缝缺陷检测和识别的模型,利用深度学习方法对焊缝缺陷进行自动识别和分类。
3. 对焊缝图像进行目标检测和定位,基于像素级别的信息提取技术,实现对焊缝缺陷的准确定位和分割。
4. 构建评价方法和指标,对所设计的模型进行评估和优化。
通过本文的研究,将为焊接质量检测提供高效可靠的算法,为现代制造业的发展做出贡献。
三、研究内容和步骤本文的研究内容主要包括:1. 焊缝图像预处理。
利用均值滤波、中值滤波、高斯滤波等方法对X射线检测焊缝图像进行去噪和增强。
2. 焊缝缺陷识别模型的设计。
提出一种基于深度学习的模型,利用卷积神经网络(CNN)特点对焊缝缺陷进行分类和识别。
3. 焊缝缺陷目标检测和定位。
基于像素级别的信息提取技术,通过对焊缝图像进行分割,实现对焊缝缺陷的准确定位和分析。
4. 评价方法和指标。
设计评价指标,通过对所构建的模型进行评估和验证,优化算法效果。
研究步骤如下:1. 收集X射线检测焊缝图像数据,进行基本的图像处理和预处理,包括去除噪声、增强图像、调整图像大小等操作。
2. 建立焊缝缺陷分类和识别模型,选取合适的卷积神经网络结构,训练并测试模型。
X射线检测焊缝的图像处理与缺陷识别
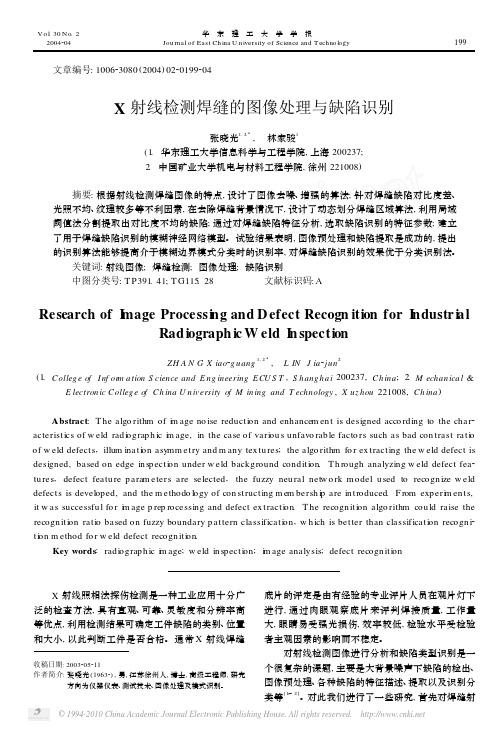
V o l .30N o.22004204华 东 理 工 大 学 学 报 Journal of East Ch ina U niversity of Science and T echno logy 收稿日期:2003205211作者简介:张晓光(19632),男,江苏徐州人,博士,高级工程师,研究方向为仪器仪表、测试技术、图像处理及模式识别。
文章编号:100623080(2004)022*******X 射线检测焊缝的图像处理与缺陷识别张晓光1,23, 林家骏1(1.华东理工大学信息科学与工程学院,上海200237;2.中国矿业大学机电与材料工程学院,徐州221008) 摘要:根据射线检测焊缝图像的特点,设计了图像去噪、增强的算法;针对焊缝缺陷对比度差、光照不均、纹理较多等不利因素,在去除焊缝背景情况下,设计了动态划分焊缝区域算法,利用局域阈值法分割提取出对比度不均的缺陷;通过对焊缝缺陷特征分析,选取缺陷识别的特征参数;建立了用于焊缝缺陷识别的模糊神经网络模型。
试验结果表明,图像预处理和缺陷提取是成功的,提出的识别算法能够提高介于模糊边界模式分类时的识别率,对焊缝缺陷识别的效果优于分类识别法。
关键词:射线图像;焊缝检测;图像处理;缺陷识别中图分类号:T P 391.41;T G 115.28文献标识码:AResearch of I mage Processi ng and D efect Recogn ition for I ndustr i alRad iograph ic W eld I n spectionZH A N G X iao 2g uang1,23, L IN J ia 2jun 2(1.Colleg e of Inf or m a tion S cience and E ng ineering ECU S T ,S hang ha i 200237,Ch ina ;2.M echan ica l &E lectron ic Colleg e of Ch ina U n iversity of M in ing and T echnology ,X uz hou 221008,Ch ina )Abstract :T he algo rithm of i m age no ise reducti on and enhancem en t is designed acco rding to the char 2acteristics of w eld radi ograph ic i m age ,in the case of vari ou s unfavo rab le facto rs such as bad con trast rati o of w eld defects ,illum inati on asymm etry and m any tex tu res ;the algo rithm fo r ex tracting the w eld defect is designed ,based on edge in specti on under w eld background conditi on .T h rough analyzing w eld defect fea 2tu res ,defect featu re param eters are selected ,the fuzzy neu ral netw o rk m odel u sed to recogn ize w eld defects is develop ed ,and the m ethodo logy of con structing m em bersh i p are in troduced .F rom exp eri m en ts ,it w as successfu l fo r i m age p rep rocessing and defect ex tracti on .T he recogn iti on algo rithm cou ld raise the recogn iti on rati o based on fuzzy boundary pattern classificati on ,w h ich is better than classificati on recogn i 2ti on m ethod fo r w eld defect recogn iti on .Key words :radi ograph ic i m age ;w eld in sp ecti on ;i m age analysis ;defect recogn iti on X 射线照相法探伤检测是一种工业应用十分广泛的检查方法,具有直观、可靠、灵敏度和分辨率高等优点,利用检测结果可确定工件缺陷的类别、位置和大小,以此判断工件是否合格。
X射线是如何对焊点和缺陷进行分析的?

J引线组件的常见缺陷。几个焊点的X射线图像。对于要求不高的电子产品,也可以忽略PLCC和SOJ的其他缺陷,例 如“锡缺乏”和“锡过量”。遵循的原则与QFP和SOIC相同。 “对齐不良”缺陷。对于J引线组件,很少有单引脚偏离的情况。 “引线 或组件缺失”缺陷实际上是“开放式焊接”的特殊情况。它的X射线图像与QFP&SOIC的“焊接”图像非常相似。因此,很少发生J 引线组件的“空洞”缺陷。
常见的焊接缺陷主要包括以下几种:桥接,开路焊接,锡不足,锡过多,对准不良,空洞,焊珠,缺少的组件或销钉等。 以下我将列出焊点的可能类型X射线焊点图像,并对缺陷焊点的图像进行一些粗略的分析。
1.芯片元件的焊点主要的常见芯片元件是:片状电阻器和片状电容器。这些组件只有两个焊锡末端,并且焊点结构相对简 单。由于各种芯片组件的主体材料不同,因此可以在X射线下完全穿透芯片电阻器。只有两端的铅锡焊点才能阻挡X射线; X 射线无法穿透材料,但是不可能在钽电容器的阴极附近穿上特殊物质,因此可以判断钽电容器的极性是否正确以及是否缺少组 件。
X射 线 是 如 何 对 焊 点 和 缺 陷 进 行 分 析 的 ?
本文转载自日联科技:https:///hangyexinwen/17-1266.html 随着组件包装的飞速发展,电子组装正朝着紧凑,小型化,轻薄化的方向发展。 BGA,Flip,Chip和CSP等高科技封装 技术的出现,使表面贴装电子组件变得越来越复杂。当然,具有挑战性的是,这增加了焊点测试的难度。
X光检测焊点判据

X光检测焊点判据X射线检测BGA、CSP焊点图像的评估和判断及其他应用理想的、合格的BGA的X光图像将清楚地显示BGA焊料球与PCB 焊盘一一对准。
如图(1)所示的焊球图像均匀一致,是理想的回流焊结果。
反之畸形焊球,大致有以下原因造成,回流温度低,PCB翘曲或PBGA的塑料基板变形,还有可能是由于SMT加工印刷缺陷造成的。
X射线检测对简单和明显的缺陷,如桥接、短路、缺球等的定义已经很清楚,但对于虚焊、冷焊等复杂和不明显缺陷没有更多深入的定义。
双面板上密集的组装元件常常导致阴影。
虽然X射线头和被测工件的工作台设计为旋转式,可以从不同角度进行检测,但有时效果不明显。
为了有效地判断复杂和不明显缺陷,有的设备制造商开发了“信号确认”软件。
例如,根据回流焊后X-光图形中焊球的尺寸改变及均匀一致性来评估和判断X-光图像的真正含义。
下面介绍如何根据BGA、CSP回流焊工艺过程中三个阶段焊球直径的变化和X-光图像的均匀性来判断某些焊接缺陷。
(1)63Sn-37Pb焊料回流焊工艺过程中,三个阶段焊球直径的变化A阶段(150℃例热阶段、焊球未熔化),BGA站立高度等于焊球高度。
B阶段(开始塌陷阶段或称一次下沉),当温度上升到183℃时,焊球开始熔化,进入塌陷阶段,此时焊球的站立高度降至初始焊球高度的80%C阶段(最后塌陷阶段或称二次下沉),当温度上升到230℃时,焊球充分熔化,并与焊膏熔在一起,在焊球上、下两个界面形成结合层,此时焊球的站立高度降至初始焊球高度的50%,X光图上球的直径增至17%,导致突出面积增加37%。
(2)X光图像的均匀一致如果所有球的X光图像均匀一致,圆形面积等于球面积或在10%~15%的范围内变化,则这种情况非常好,在回流焊中没有缺陷,称做“均匀一致”,在使用X光检查中,均匀性对于迅速判定BGA焊接质量提供了最首要的特性,从垂直的角度检测,BGA焊球是有规则的黑色圆点。
桥接、不充分焊接或者过度焊接、焊料溅散、没有对正和气泡都能够很快地检查出来。
浅谈X—ray检验设备评判BGA器件焊接质量

浅谈X—ray检验设备评判BGA器件焊接质量作者:李柏东来源:《科技创新与应用》2014年第24期摘要:BGA器件焊接之后,由于其结构的特殊性无法采用常规检验手段对其焊接质量进行检验与评判,X-ray检验技术作为新技术、新手段越来越广泛的应用于电子产品组装检验中。
文章以工艺及质量检验要求为基础,介绍BGA器件焊接后形成不良焊点的原因,指出如何利用X-ray检验设备的检验影像评判BGA器件焊接质量。
关键词:BGA器件;X-ray;检验;质量随着电子产品便携化、小型化的发展要求,越来越多的小型器件应用于电子组装过程中,高密度、高集成的电子装联技术日趋成熟,随之而来的检验手段也日新月异。
作为小型器件典范的BGA器件近些年来在电子产品中应用非常广泛,与QFP封装器件或PLCC封装器件相比,BGA器件具有引脚数目更多、引脚间电感及电容更小、引脚共面性好、电性能及散热性能好等诸多优点。
虽然BGA器件有诸多方面的优点,但仍存在着无法改变的不足之处:即BGA器件在焊接完成之后,由于其焊点全部在器件本体腹底之下,因此既无法采用传统的目测方法观测检验全部焊点的焊接质量,也不能应用AOI(自动光学检验)设备对焊点外观做质量评判,只能采用X-ray检验设备对BGA器件焊点的物理结构进行检验。
X-ray检验设备是基于X射线的影像原理,由X射线发生装置发出X射线,对被检验印制板组及BGA器件进行照射,利用X射线不能穿透锡、铅等密度大且厚的物质,可形成深色影像,而会轻易穿透印制板及塑料封装等密度小且薄的物质,不会形成影像的现象,实现对BGA器件焊接焊点的质量检验,图1所示即是X-ray检验设备的检验原理。
下面就对此种检验的评判要求做些介绍与探讨。
图1 X-ray检验设备的检验原理图1 基本要求在X-ray检验设备的影像区内,BGA器件无明显位置偏移和翘起的现象,BGA焊料球的影像尺寸、形状、颜色和对比度应均匀一致,焊点影像应呈现形状规则的圆形,并且边界光滑,轮廓清晰,无回流焊接不良的迹象。
关于BGA封装器件焊点缺陷X-射线检测法的探讨

关于BGA封装器件焊点缺陷X-射线检测法的探讨摘要:制造者一般都是采用目视观察的方法,观察最外面一圈焊点的塌陷是否一致,再将芯片对着光线观察。
通过试验发现,使用X -射线检测仪检查BGA 封装器件的焊点,可以快速、准确地检测出BGA 封装器件中焊点的桥连、空洞、虚焊等缺陷,在BGA 封装器件焊点的质量检测方面得到广泛应用。
本文所用仪器和检测方法能够自动计算BGA 封装器件贴装焊点的空洞率,对空洞缺陷的快速检测和预防具有实际意义。
关键词:BGA;无损检测;缺陷引言:对于表面组装焊点,常用的无损检测方法有X -射线检测、三维光学摄像检验、激光/红外检测、超声波检测等多种方法。
要想不破坏BGA 封装器件本身的结构、性能等,就可以看出BGA 封装器件内在的缺陷或者是更加准确地检测出焊点的质量,就必须采用其它更为先进、可靠的无损检测方法。
通过对BGA 封装器件可视图像X -射线检测和分析,可以准确地检测出BGA 封装器件贴装焊点的各种缺陷。
一.试验材料与仪器(一)试验材料测试工件为采用再流焊焊接的BGA 封装器件,基板材料为FR -4,钎料为A lpha公司生产的Sn62 /Pb36 /Ag2合金焊膏,BGA 焊球的直径为0.7mm,I /O 端子间距为1.27 mm,通过贴片机或贴片装置完成BGA 贴装。
(二)X -射线检测仪实验所用X - 射线检测仪型号为HAWK -160X I型。
X -射线检测仪的工作原理是由在高电压下产生的电子束照射到金属钨表面,产生X 射线,产生的X 束射线倾斜向下照射并高速旋转,同时在下面有一个闪烁器平台也以同样的速度与X射线同步旋转,闪烁器平台实际上是一个对X -射线敏感的接收器。
一般来讲,X -射线不能透过锡、铅等重金属,从而形成深色影像;而一般的物质则被X -射线穿透,不会形成影像。
X -射线在光源与闪烁器平台之间的某一位置上聚焦,出现一个聚焦平面,聚焦平面上的物体或图像会在闪烁器平台上形成一个清晰的图像,不在聚焦平面上的物体或图像在闪烁器平台上则被”虚掉“,只有一个阴影。
X射线探伤中焊缝缺陷的图像处理与自动识别的开题报告
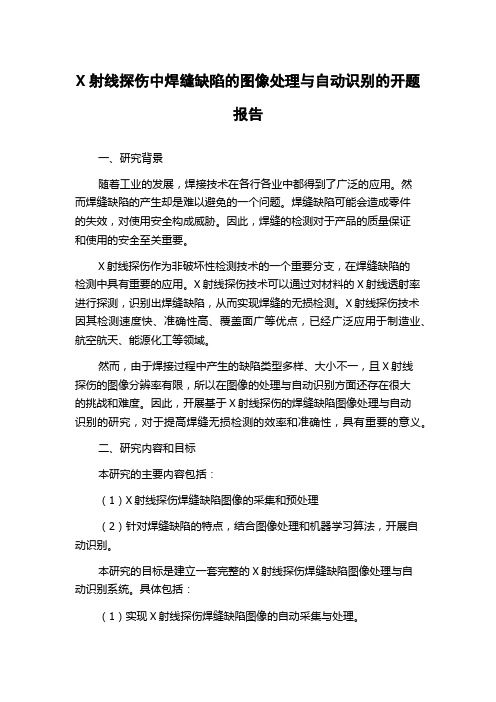
X射线探伤中焊缝缺陷的图像处理与自动识别的开题报告一、研究背景随着工业的发展,焊接技术在各行各业中都得到了广泛的应用。
然而焊缝缺陷的产生却是难以避免的一个问题。
焊缝缺陷可能会造成零件的失效,对使用安全构成威胁。
因此,焊缝的检测对于产品的质量保证和使用的安全至关重要。
X射线探伤作为非破坏性检测技术的一个重要分支,在焊缝缺陷的检测中具有重要的应用。
X射线探伤技术可以通过对材料的X射线透射率进行探测,识别出焊缝缺陷,从而实现焊缝的无损检测。
X射线探伤技术因其检测速度快、准确性高、覆盖面广等优点,已经广泛应用于制造业、航空航天、能源化工等领域。
然而,由于焊接过程中产生的缺陷类型多样、大小不一,且X射线探伤的图像分辨率有限,所以在图像的处理与自动识别方面还存在很大的挑战和难度。
因此,开展基于X射线探伤的焊缝缺陷图像处理与自动识别的研究,对于提高焊缝无损检测的效率和准确性,具有重要的意义。
二、研究内容和目标本研究的主要内容包括:(1)X射线探伤焊缝缺陷图像的采集和预处理(2)针对焊缝缺陷的特点,结合图像处理和机器学习算法,开展自动识别。
本研究的目标是建立一套完整的X射线探伤焊缝缺陷图像处理与自动识别系统。
具体包括:(1)实现X射线探伤焊缝缺陷图像的自动采集与处理。
(2)开展焊缝缺陷图像的特征提取和特征优化。
(3)结合机器学习算法开展焊缝缺陷图像的自动识别。
(4)实现将自动识别的结果与X射线探伤系统实时对接,及时发现和处理焊缝缺陷。
三、研究方法(1)开展X射线探伤焊缝缺陷图像的采集与预处理。
(2)通过图像处理算法提取焊缝缺陷图像的特征,如形状、纹理、边缘等。
(3)结合机器学习算法,训练识别模型,实现自动识别焊缝缺陷。
(4)将识别结果通过X射线探伤系统实时展示,为焊缝的质量控制提供决策支持。
四、研究意义(1)提高焊缝无损检测的效率和准确性,为制造业、航空航天、能源化工等领域的技术进步和质量保障提供支持。
(2)优化X射线探伤焊缝缺陷图像的处理与分析方式,减少人力和时间成本,提高焊缝缺陷的检测效率。
焊缝缺陷检测的X射线图像分析方法

焊缝缺陷检测的X射线图像分析方法焊缝缺陷检测的X射线图像分析方法步骤一:确定焊缝缺陷检测的目的和要求在进行焊缝缺陷检测之前,首先需要明确检测的目的和要求。
这可以包括确定需要检测的焊缝类型、缺陷种类以及对缺陷的灵敏度要求等。
这些信息将有助于确定后续的分析方法和参数设置。
步骤二:准备X射线设备和样品进行焊缝缺陷检测需要使用X射线设备。
确保设备的正常运行,并根据具体情况选择合适的参数设置,如电压、电流和曝光时间等。
同时,准备焊缝样品并进行必要的清洁和表面处理,以确保能够获得清晰的X射线图像。
步骤三:选择合适的成像技术在进行焊缝缺陷检测时,可以采用不同的成像技术,如传统的投影成像、断层成像和CT成像等。
根据具体情况选择合适的成像技术,以获得对焊缝内部缺陷的准确和全面的了解。
步骤四:获取X射线图像通过将焊缝样品放置在X射线设备下,使用合适的曝光时间和参数设置,获取焊缝的X射线图像。
确保图像清晰度和对比度的同时,避免过度曝光或欠曝光情况的发生。
步骤五:对X射线图像进行分析获得X射线图像后,需要对其进行分析以检测焊缝缺陷。
可以使用人工观察的方法,通过仔细查看图像中的缺陷特征和形态来识别缺陷。
同时,也可以借助计算机辅助分析的方法,利用图像处理和模式识别技术对图像进行自动化分析和缺陷检测。
步骤六:评估和分类焊缝缺陷在分析X射线图像时,需要对检测到的焊缝缺陷进行评估和分类。
这可以基于缺陷的形态、大小、位置和严重程度等指标进行。
根据缺陷评估结果,可以确定缺陷的严重程度,并采取相应的修复措施或进一步研究。
步骤七:记录和报告结果最后,将焊缝缺陷检测的结果记录并进行报告。
报告中应包括焊缝样品的信息、检测方法和参数设置、检测结果以及对缺陷的评估和分类等内容。
这有助于将检测结果传达给相关人员,并为后续的修复和质量控制提供参考。
通过以上步骤,可以根据焊缝缺陷检测的X射线图像分析方法,对焊缝进行准确和全面的缺陷检测。
这将有助于提高焊接质量和产品安全性,并为焊接工艺的改进和优化提供参考。
焊点缺陷分析与自动X射线检测AXI图像的评估和判断
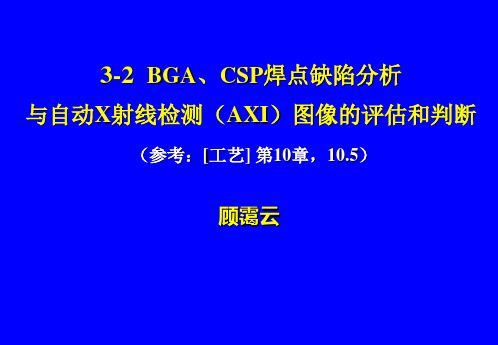
例如:X射线检查焊点虚焊的例子
首先要了解:回流焊工艺过程中,三个阶段焊球直径的变化
• A阶段(150℃, 焊球没有熔化)
• BGA高度等于 焊球直径
• B阶段(183℃,开 始塌陷)
• BGA高度等于焊球 直径的80%;
• C阶段(230℃最 后塌陷阶段)
• BGA高度等于焊球 直径的50%
虚焊的检查是通过一定的原理分析出来的
出现在元件的一侧或者一角。优化温度曲线,充分预 热,减少四个角的ΔT,球窝缺陷明显有了改善。 • 器件或PCB在加热过程中变形 • 目前有的公司针对X射线不能判断那些不明显的焊接 缺陷,采用光学检测(AOI或内窥镜)来弥补X射线 的不足。
三、X射线检测BGA、CSP焊点图像 的评估和判断
X射线图像检测基本原理
X-ray焊点图像分析
• X射线透视图能够定量地显示出焊点厚度、 形状及质量的密度分布。根据X射线检测到 的厚度、形状及质量的密度分布指标及图像, 结合强大的图像分析软件就能够分析和判断 焊点的焊接质量
均匀一致的合格焊球
2D传输影象
3D 影象
BGA焊球桥接的图像
2D传输影象
局部放大
3D 影象
BGA焊球空洞的图像
X射线倾斜一定角度检查BGA虚焊缺陷
未熔化的焊球
塌陷的焊球
四、大尺寸BGA 的焊盘与模板设计
Pitch 1.27mm 1.0mm 0.8mm 0.5mm
直径 外三圆28mil,其余24mil 外三圆22mil,其余20mil 外二圆17mil,其余15mil 外二圆11.5mil,其余11mil
2D传输影象
局部放大
3D 影象
X-ray焊点图像分析需将软件与工艺结合, 与IPC-A-610D验收标准相结合。
X射线焊缝图像的缺陷检测与识别技术

X射线焊缝图像的缺陷检测与识别技术刘辉;万文;熊震宇【摘要】针对目前无损检测主要采用人工方式存在的主观不一致、检测效率低、操作复杂等问题,设计了一套焊缝缺陷自动检测系统.提出基于Otsu双阈值分割的缺陷区域自动提取、图像的降噪和灰度增强的图像预处理方法;通过SUSAN算法检测焊缝缺陷目标,并结合形态学孔洞填充算法修正缺陷目标;计算焊缝缺陷目标特征参数,并结合所设计的深度为4的二叉树分类识别逻辑流程,实现了较好的焊缝缺陷的检测结果.%Aiming at the problems existing in the nondestructive testing using artificial methods,such as subjective inconsistency,low efficiency and complicated operation,a set of automatic inspection system for weld defects was designed.An image preprocessing method based on Otsu double threshold segmentation for automatic extraction of defective area,image noise reduction and grayscale enhancement was proposed;by SUSAN algorithm for detection of weld defect target,and combined with morphology hole filling algorithm to modify defect targets;through the calculation of the target characteristic parameters of the weld defects,and combined with the design depth of two of the 4 binary tree classification recognition logic process,to achieve a better detection results of the weld defects.【期刊名称】《电焊机》【年(卷),期】2017(047)004【总页数】5页(P89-93)【关键词】焊缝缺陷;图像处理;特征参数【作者】刘辉;万文;熊震宇【作者单位】南昌航空大学,江西南昌330063;南昌航空大学,江西南昌330063;南昌航空大学,江西南昌330063【正文语种】中文【中图分类】TG409针对焊接过程中出现的各种质量问题,对其中的焊接构件进行有效的无损检测。
BGA封装的焊点失效分析
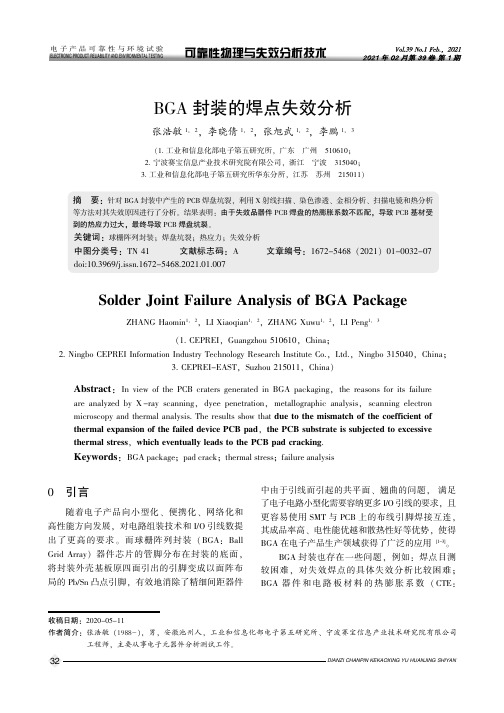
BGA 封装的焊点失效分析张浩敏1,2,李晓倩1,2,张旭武1,2,李鹏1,3(1.工业和信息化部电子第五研究所,广东广州510610;2.宁波赛宝信息产业技术研究院有限公司,浙江宁波315040;3.工业和信息化部电子第五研究所华东分所,江苏苏州215011)摘要:针对BGA 封装中产生的PCB 焊盘坑裂,利用X 射线扫描、染色渗透、金相分析、扫描电镜和热分析等方法对其失效原因进行了分析。
结果表明:由于失效品器件PCB 焊盘的热膨胀系数不匹配,导致PCB 基材受到的热应力过大,最终导致PCB 焊盘坑裂。
关键词:球栅阵列封装;焊盘坑裂;热应力;失效分析中图分类号:TN 41文献标志码:A文章编号:1672-5468(2021)01-0032-07doi:10.3969/j.issn.1672-5468.2021.01.007Solder Joint Failure Analysis of BGA PackageZHANG Haomin 1,2,LI Xiaoqian 1,2,ZHANG Xuwu 1,2,LI Peng 1,3(1.CEPREI ,Guangzhou 510610,China ;2.Ningbo CEPREI Information Industry Technology Research Institute Co.,Ltd.,Ningbo 315040,China ;3.CEPREI-EAST ,Suzhou 215011,China )Abstract :In view of the PCB craters generated in BGA packaging ,the reasons for its failureare analyzed by X -ray scanning ,dyee penetration ,metallographic analysis ,scanning electron microscopy and thermal analysis.The results show that due to the mismatch of the coefficient of thermal expansion of the failed device PCB pad ,the PCB substrate is subjected to excessivethermal stress ,which eventually leads to the PCB pad cracking .Keywords :BGA package ;pad crack ;thermal stress ;failure analysis收稿日期:2020-05-11作者简介:张浩敏(1988-),男,安徽池州人,工业和信息化部电子第五研究所、宁波赛宝信息产业技术研究院有限公司工程师,主要从事电子元器件分析测试工作。
缺陷检测技术图像质量评估与优化研究
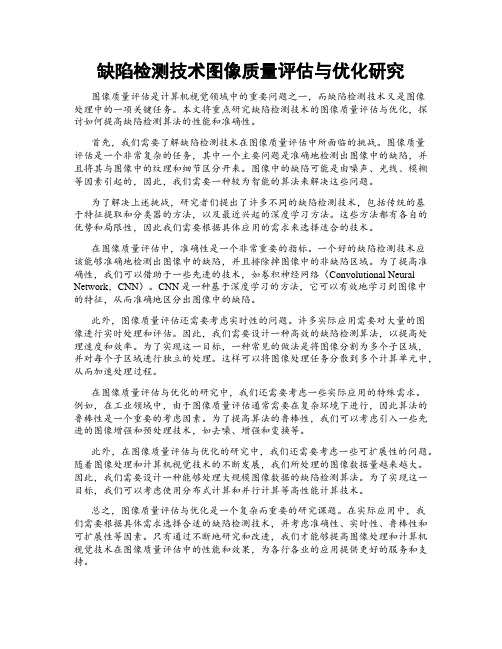
缺陷检测技术图像质量评估与优化研究图像质量评估是计算机视觉领域中的重要问题之一,而缺陷检测技术又是图像处理中的一项关键任务。
本文将重点研究缺陷检测技术的图像质量评估与优化,探讨如何提高缺陷检测算法的性能和准确性。
首先,我们需要了解缺陷检测技术在图像质量评估中所面临的挑战。
图像质量评估是一个非常复杂的任务,其中一个主要问题是准确地检测出图像中的缺陷,并且将其与图像中的纹理和细节区分开来。
图像中的缺陷可能是由噪声、光线、模糊等因素引起的,因此,我们需要一种较为智能的算法来解决这些问题。
为了解决上述挑战,研究者们提出了许多不同的缺陷检测技术,包括传统的基于特征提取和分类器的方法,以及最近兴起的深度学习方法。
这些方法都有各自的优势和局限性,因此我们需要根据具体应用的需求来选择适合的技术。
在图像质量评估中,准确性是一个非常重要的指标。
一个好的缺陷检测技术应该能够准确地检测出图像中的缺陷,并且排除掉图像中的非缺陷区域。
为了提高准确性,我们可以借助于一些先进的技术,如卷积神经网络(Convolutional Neural Network,CNN)。
CNN是一种基于深度学习的方法,它可以有效地学习到图像中的特征,从而准确地区分出图像中的缺陷。
此外,图像质量评估还需要考虑实时性的问题。
许多实际应用需要对大量的图像进行实时处理和评估。
因此,我们需要设计一种高效的缺陷检测算法,以提高处理速度和效率。
为了实现这一目标,一种常见的做法是将图像分割为多个子区域,并对每个子区域进行独立的处理。
这样可以将图像处理任务分散到多个计算单元中,从而加速处理过程。
在图像质量评估与优化的研究中,我们还需要考虑一些实际应用的特殊需求。
例如,在工业领域中,由于图像质量评估通常需要在复杂环境下进行,因此算法的鲁棒性是一个重要的考虑因素。
为了提高算法的鲁棒性,我们可以考虑引入一些先进的图像增强和预处理技术,如去噪、增强和变换等。
此外,在图像质量评估与优化的研究中,我们还需要考虑一些可扩展性的问题。
BGA、QFN、CSP器件焊点空洞分析

BGA、QFN、CSP器件焊点空洞分析计景春、伏政(广东技术师范学院工业实训中心SMT培训)0 前言在SMT生产中,BGA、QFN、CSP等无引脚的元器件,在进行焊接时,无论是回流焊接还是波峰焊接,无论是有铅制程还是无铅制程,冷却之后都难免会出現一些在所难免的空洞(气泡)现象的产生。
焊点內部发生空洞的主要成因是FLUX中的有机物经过高溫裂解后产生的气泡无法及时逸出。
在回流区FLUX已经被消耗殆尽,锡膏的粘度发生了较大的变化,此时锡膏之中的FLUX发生裂解,导致高溫裂解后的气泡无法及时的逸出,被包围在锡球中,冷却后就形成空洞現象。
目前,一般使用X-Ray设备进行检查空洞的面积,通过X-Ray都可以看到焊球的空洞分布狀況。
只要有些器件空洞所占面积的比例不是很大,常常认为是符合接受标准标准(如IPC-A-610D 8.2.12.4),因此在检验时沒有引起足够的重视。
在众多的空洞现象中发现,产生空洞现象与焊料本身的表面张力有着直接的联系。
锡膏的表面张力越大,高温裂解的气泡越难逸出焊料球,气泡被团团包围在锡球之中(无铅焊料的表面张力达到4.60×10-3 N/260 ℃),表面张力越小,高温裂解后的气泡就很容易逃出焊料球,被锡球团团包围的机率就相当小(有铅焊料的表面张力达到3。
80×10-3 N / 260 ℃,Sn63-Pb37,m.p为183 ℃)。
已经陷入高温裂解的气泡,在有铅焊料密度较大(约8.44 g/cm3)的情况之下,焊料中的合金在相互挤压下,有机物就会向外面逃脱,所以有机物残留在焊点中的机率是相当小的,但是无铅就完全不一样了。
比重不但比有铅小,而且无铅的表面张力又比有铅高出很多,同时熔点又比有铅高出34 ℃之多(Sn63-Pb37,熔点为183 ℃,SAC305熔点约为217 ℃),在种种环境不利的情况下,无铅焊料中的有机物就很难从焊球中分解出来,有机物常常被包围在焊球中,冷却后就会形成空洞现象。
X射线实时成像技术在BGA器件焊点的失效判定研究

X射线实时成像技术在BGA器件焊点的失效判定研究摘要:随着计算机技术及软件技术的日益发展,X射线中广泛应用的胶片技术照相法逐步被X射线实时成像替代。
X射线实时成像系统主要包括X射线探伤机、高分辨率图像采集单元、计算机图像处理单元、机械传动及电气控制单元、射线防护单元五个单元组成。
其原理与传统X射线类似,主要利用X射线穿过不同密度、厚度的物体后,得到不同灰度显示图像的特性,对物体内部进行无损评价,是产品的筛选、失效分析、质量评价、改进工艺等工作的有效手段。
对于电子元器件的失效分析,X射线实时成像系统更是不可替代的重要工具。
本文首先对X射线实时成像的原理及功能进行介绍,对BGA电路中焊点的锡溅,冷焊,气泡,裂纹,锡球损伤等具有代表的失效模式进行研究。
该研究取得的成果已用于实际生产,极大地提高了失效分析的成功率,对后续的电子元器件失效分析及质量控制工作有一定的借鉴意义。
关键词:X射线实时成像系统 BGA器件缺点定位一、引言BGA器件有焊点较多,焊球密集,焊球无法直观检查等特点,电性能测试不能检测由焊接工艺造成的缺陷,利用X射线检测系统,可以检测出由焊接工艺造成硬件上的失效,如锡溅,冷焊,气孔,裂纹,锡球损伤,且利用X射线检测系统可以确认失效点的具体位置。
二、X射线原理及功能X射线是电子波形态的能量,是光的一种,与可见光差别是每个光子含的能量不一样,X射线光子含的能量是普通光光子能量的5000倍,X射线有着光子的能量高,能够穿透物体的特点。
X射线的产生过程为:1.灯丝发热,像灯泡一样本身加热到高温,在高温下组成灯丝的钨原子内部电子逸出,在高温灯丝周围会形成电子云。
2.电子云在阳极和阴极之间的电压差的作用下,从灯丝向靶运动,并且速度越来越快。
3.在这个过程中,电子云被聚焦线圈聚焦,形成电子束。
4.电子束通过高电压区,获得能量及速度。
5.电子轰击靶(重金属如钨),电子能量超过98%能量转为热和能量转化为热量并通过阳极发散,小于2%的能量转化为X射线。
X射线焊缝图像的缺陷检测与识别技术研究
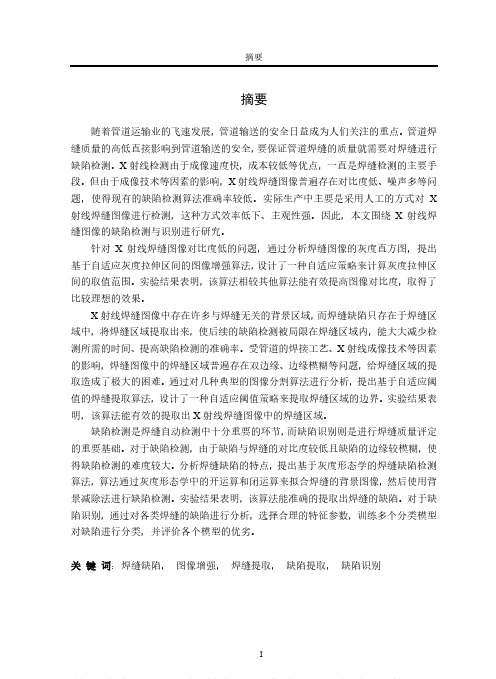
摘要摘要随着管道运输业的飞速发展,管道输送的安全日益成为人们关注的重点。
管道焊缝质量的高低直接影响到管道输送的安全,要保证管道焊缝的质量就需要对焊缝进行缺陷检测。
X射线检测由于成像速度快,成本较低等优点,一直是焊缝检测的主要手段。
但由于成像技术等因素的影响,X射线焊缝图像普遍存在对比度低、噪声多等问题,使得现有的缺陷检测算法准确率较低。
实际生产中主要是采用人工的方式对X 射线焊缝图像进行检测,这种方式效率低下、主观性强。
因此,本文围绕X射线焊缝图像的缺陷检测与识别进行研究。
针对X射线焊缝图像对比度低的问题,通过分析焊缝图像的灰度直方图,提出基于自适应灰度拉伸区间的图像增强算法,设计了一种自适应策略来计算灰度拉伸区间的取值范围。
实验结果表明,该算法相较其他算法能有效提高图像对比度,取得了比较理想的效果。
X射线焊缝图像中存在许多与焊缝无关的背景区域,而焊缝缺陷只存在于焊缝区域中,将焊缝区域提取出来,使后续的缺陷检测被局限在焊缝区域内,能大大减少检测所需的时间、提高缺陷检测的准确率。
受管道的焊接工艺、X射线成像技术等因素的影响,焊缝图像中的焊缝区域普遍存在双边缘、边缘模糊等问题,给焊缝区域的提取造成了极大的困难。
通过对几种典型的图像分割算法进行分析,提出基于自适应阈值的焊缝提取算法,设计了一种自适应阈值策略来提取焊缝区域的边界。
实验结果表明,该算法能有效的提取出X射线焊缝图像中的焊缝区域。
缺陷检测是焊缝自动检测中十分重要的环节,而缺陷识别则是进行焊缝质量评定的重要基础。
对于缺陷检测,由于缺陷与焊缝的对比度较低且缺陷的边缘较模糊,使得缺陷检测的难度较大。
分析焊缝缺陷的特点,提出基于灰度形态学的焊缝缺陷检测算法,算法通过灰度形态学中的开运算和闭运算来拟合焊缝的背景图像,然后使用背景减除法进行缺陷检测。
实验结果表明,该算法能准确的提取出焊缝的缺陷。
对于缺陷识别,通过对各类焊缝的缺陷进行分析,选择合理的特征参数,训练多个分类模型对缺陷进行分类,并评价各个模型的优劣。
基于2D投影的BGA焊点X射线检测缺陷图像处理方法
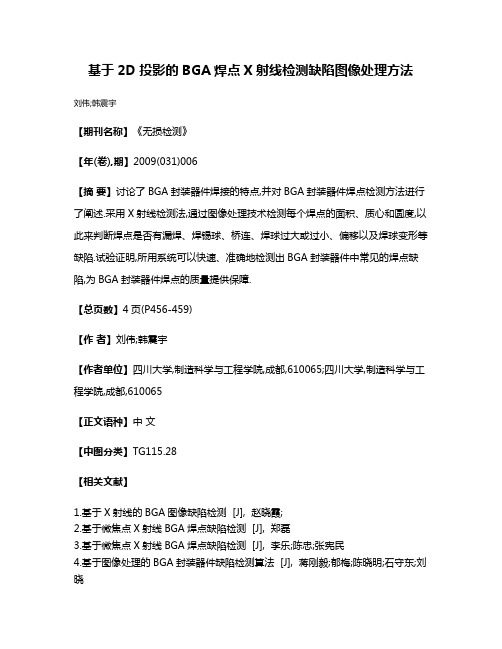
基于2D投影的BGA焊点X射线检测缺陷图像处理方法刘伟;韩震宇
【期刊名称】《无损检测》
【年(卷),期】2009(031)006
【摘要】讨论了BGA封装器件焊接的特点,并对BGA封装器件焊点检测方法进行了阐述.采用X射线检测法,通过图像处理技术检测每个焊点的面积、质心和圆度,以此来判断焊点是否有漏焊、焊锡球、桥连、焊球过大或过小、偏移以及焊球变形等缺陷.试验证明,所用系统可以快速、准确地检测出BGA封装器件中常见的焊点缺陷,为BGA封装器件焊点的质量提供保障.
【总页数】4页(P456-459)
【作者】刘伟;韩震宇
【作者单位】四川大学,制造科学与工程学院,成都,610065;四川大学,制造科学与工程学院,成都,610065
【正文语种】中文
【中图分类】TG115.28
【相关文献】
1.基于X射线的BGA图像缺陷检测 [J], 赵晓霞;
2.基于微焦点X射线BGA焊点缺陷检测 [J], 郑磊
3.基于微焦点X射线BGA焊点缺陷检测 [J], 李乐;陈忠;张宪民
4.基于图像处理的BGA封装器件缺陷检测算法 [J], 蒋刚毅;郁梅;陈晓明;石守东;刘晓
5.BGA焊点气泡缺陷X射线图像的动态阈值分割方法 [J], 张俊生;王明泉;郭晋秦;楼国红
因版权原因,仅展示原文概要,查看原文内容请购买。
- 1、下载文档前请自行甄别文档内容的完整性,平台不提供额外的编辑、内容补充、找答案等附加服务。
- 2、"仅部分预览"的文档,不可在线预览部分如存在完整性等问题,可反馈申请退款(可完整预览的文档不适用该条件!)。
- 3、如文档侵犯您的权益,请联系客服反馈,我们会尽快为您处理(人工客服工作时间:9:00-18:30)。
均匀一致的合格焊球
2D传输影象 2D传输影象
3D 影象
BGA焊球桥接的图像 BGA焊球桥接的图像
2D传输影象 2D传输影象
局部放大
3D 影象
BGA焊球空洞的图像 BGA焊球空洞的图像
2D传输影象 2D传输影象
局部放大
Байду номын сангаас
3D 影象
X-ray焊点图像分析需将软件与工艺结合, ray焊点图像分析需将软件与工艺结合 焊点图像分析需将软件与工艺结合, IPC- 610D验收标准相结合 验收标准相结合。 与IPC-A-610D验收标准相结合。
3-2 BGA、CSP焊点缺陷分析 BGA、CSP焊点缺陷分析
与自动X射线检测(AXI)图像的评估和判断 自动X射线检测(AXI)
(参考:[工艺] 第10章,10.5) 参考: 工艺] 10章 10.5)
顾霭云
如何正确评估和判断BGA焊接缺陷 如何正确评估和判断BGA焊接缺陷
• 了解BGA、CSP的主要焊接缺陷 了解BGA CSP的主要焊接缺陷 BGA、 • 了解缺陷的产生原因 • 了解BGA、CSP的焊点检测标准 了解BGA CSP的焊点检测标准 BGA、 • 正确使用自动X射线的图形分析软件 正确使用自动X
例如: 例如:X射线检查焊点虚焊的例子
首先要了解:回流焊工艺过程中,三个阶段焊球直径的变化 首先要了解:回流焊工艺过程中,
• A阶段(150℃, 阶段(150℃, 焊球没有熔化) 焊球没有熔化) • BGA高度等于 BGA高度等于 焊球直径
• B阶段(183℃,开 阶段(183℃, 始塌陷) 始塌陷) • BGA高度等于焊球 BGA高度等于焊球 直径的80% 80%; 直径的80%;
三、X射线检测BGA、CSP焊点图像 射线检测BGA、CSP焊点图像
的评估和判断
X射线图像检测基本原理
•
X射线由一个微焦点X射线管产生,穿过管壳内的一个铍 射线由一个微焦点X射线管产生, 窗,并投射到测试样品上,穿过样品的X射线轰击到X射 并投射到测试样品上,穿过样品的X射线轰击到X 线敏感板上的磷涂层,并激出发光子, 线敏感板上的磷涂层,并激出发光子,这些光子随后被 摄像机探测到
(7)球窝缺陷
• 焊膏印刷的厚度不够或者焊膏量不足 • BGA共面性差 BGA共面性差 • 温差引起球窝缺陷。据统计,大约有95%以上的球窝 温差引起球窝缺陷。据统计,大约有95%以上的球窝 出现在元件的一侧或者一角。优化温度曲线, 出现在元件的一侧或者一角。优化温度曲线,充分预 热,减少四个角的∆T,球窝缺陷明显有了改善。 减少四个角的∆ 球窝缺陷明显有了改善。 • 器件或PCB在加热过程中变形 器件或PCB在加热过程中变形 • 目前有的公司针对X射线不能判断那些不明显的焊接 目前有的公司针对X 缺陷,采用光学检测(AOI或内窥镜 来弥补X 或内窥镜) 缺陷,采用光学检测(AOI或内窥镜)来弥补X射线 的不足。 的不足。
X射线倾斜一定角度检查BGA虚焊缺陷 射线倾斜一定角度检查BGA虚焊缺陷 倾斜一定角度检查BGA
未熔化的焊球
塌陷的焊球
四、大尺寸BGA 的焊盘与模板设计 大尺寸BGA
Pitch 1.27mm 1.0mm 0.8mm 0.5mm 直径 外三圆28mil,其余24mil 外三圆28mil,其余24mil 28mil,其余 外三圆22mil,其余20mil 外三圆22mil,其余20mil 22mil,其余 外二圆17mil,其余15mil 外二圆17mil,其余15mil 17mil,其余 外二圆11.5mil,其余11mil 外二圆11.5mil,其余11mil 11.5mil,其余 Socket BGA(BGA插座) BGA(BGA插座 插座) Pitch 1.27mm 1.0mm 直径 外五点32mil,其余24mil 外五点32mil,其余24mil 32mil,其余 外五点24mil,其余20mil 外五点24mil,其余20mil 24mil,其余
(4)冷焊、锡球熔化不完全 冷焊、
• 冷焊、锡球熔化不完全是由于焊接温度过低造成的, 冷焊、锡球熔化不完全是由于焊接温度过低造成的, 也是不可接受的。 也是不可接受的。
(5)焊点扰动
• 焊点扰动是焊点冷却凝固时由于PCB震动,或由于加 焊点扰动是焊点冷却凝固时由于PCB震动, 震动 热过程中PCB膨胀变形,冷却凝固时PCB收缩变形应 热过程中PCB膨胀变形,冷却凝固时PCB收缩变形应 膨胀变形 力造成的,无铅焊点表面粗糙不属于焊点扰动。 力造成的,无铅焊点表面粗糙不属于焊点扰动。
(6)移位(焊球与PCB焊盘不对准) 移位(焊球与PCB焊盘不对准 焊盘不对准)
• 一种可能是由于贴片偏移过大造成的; 一种可能是由于贴片偏移过大造成的; • 另一个原因是焊接温度过低,焊接过程中没有到达 另一个原因是焊接温度过低, 使焊球完成二次下沉的温度, 使焊球完成二次下沉的温度,没有完成自校准效应 就结束焊接。这种情况下,贴片造成的偏移量不能 就结束焊接。这种情况下, 被纠正,因此会造成焊球与PCB焊盘不对准 焊盘不对准、 被纠正,因此会造成焊球与PCB焊盘不对准、看上 去焊球的形状是扭曲的。 去焊球的形状是扭曲的。
二、BGA主要焊接缺陷的原因分析 BGA主要焊接缺陷的原因分析
(1)空洞
• 焊接空洞是由于在BGA加热期间焊料中的助焊剂、 焊接空洞是由于在BGA加热期间焊料中的助焊剂 加热期间焊料中的助焊剂、 活化剂与金属表面氧化物反应时产生的气体和气体 在加热过程中膨胀所导致的( 包括受潮)。 在加热过程中膨胀所导致的( 包括受潮)。 • IPC-A-610D验收标准为,焊球中的空洞不应该超 IPC- 610D验收标准为 验收标准为, 过焊料球直径的25%, 过焊料球直径的25%,并且没有单个空洞出现在焊 接点外表。如果多个空洞出现在焊球内部,空洞的 接点外表。如果多个空洞出现在焊球内部, 总和不应该超过焊料球直径的25%。 总和不应该超过焊料球直径的25%。
PCB中间形变较大, PCB中间形变较大,但拼板时可能每块小板边缘的形变比较大 中间形变较大
(3)桥接和短路
桥接和短路也是不可接受的,主要原因: 桥接和短路也是不可接受的,主要原因: • 焊膏量过多或印刷缺陷(焊膏图形粘连) 焊膏量过多或印刷缺陷(焊膏图形粘连) • 贴片后手工拨正时由于焊膏滑动造成的 • 焊接温度过高,焊料液态时间太长,焊球过度塌陷 焊接温度过高,焊料液态时间太长, • 焊盘设计间距过窄造成的 • PBGA的塑料基板吸潮,焊接时在高温下水蒸气膨 PBGA的塑料基板吸潮, 的塑料基板吸潮 胀引起焊盘起翘,使相邻焊点桥接。 胀引起焊盘起翘,使相邻焊点桥接。
• C阶段(230℃最 阶段(230℃最 后塌陷阶段) 后塌陷阶段) • BGA高度等于焊球 BGA高度等于焊球 直径的50% 直径的50%
虚焊的检查是通过一定的原理分析出来的
• 当X射线倾斜一定角度观察BGA时,焊接良好的焊 射线倾斜一定角度观察BGA时 倾斜一定角度观察BGA 球由于会发生二次坍塌而不再是一个球形的投影, 球由于会发生二次坍塌而不再是一个球形的投影, 而是一个拖尾的形状 • 如果焊接后BGA焊球的X射线投影仍然是一个圆形的 如果焊接后BGA焊球的X BGA焊球的 话,说明这个焊球根本没有发生焊接而坍塌,这样 说明这个焊球根本没有发生焊接而坍塌, 就可以推定该焊点是虚的,或是开路的结构。所以, 就可以推定该焊点是虚的,或是开路的结构。所以, 使用好X 使用好X光透视技术还需要有相关的知识和实践经 验。
如何正确评估和判断焊接缺陷 • 首先要了解BGA、CSP的工艺 首先要了解BGA CSP的工艺 BGA、 • 了解BGA、CSP的主要焊接缺陷 了解BGA CSP的主要焊接缺陷 BGA、 • 了解各种缺陷的产生原因 • 了解BGA、CSP的焊点检测标准 了解BGA CSP的焊点检测标准 BGA、 • 还要正确使用自动X-Ray的图形分析软件。 还要正确使用自动X Ray的图形分析软件。 的图形分析软件
(2)脱焊(裂纹或“枕状效应”) 脱焊(裂纹或“枕状效应”
脱焊是不可接受的,主要原因: 脱焊是不可接受的,主要原因: • 温度过低或温度过高 • 较薄的板或拼板 PCB翘曲,或PBGA的塑料(BT树 PCB翘曲 翘曲, PBGA的塑料 BT树 的塑料( 脂)基板变形 • 焊球表面氧化物和污染物 • 焊盘设计金属化孔加工在焊盘上,焊料从孔中流出; 焊盘设计金属化孔加工在焊盘上,焊料从孔中流出; • 印刷缺陷(漏印或少印)造成的 印刷缺陷(漏印或少印)
四角外圈五点的球大于内侧
一、BGA的主要焊接缺陷与验收标准 BGA的主要焊接缺陷与验收标准
• BGA的主要焊接缺陷: BGA的主要焊接缺陷: 的主要焊接缺陷 空洞、脱焊(开路)、桥接(短路)、焊球内部裂 空洞、脱焊(开路)、桥接(短路)、焊球内部裂 )、桥接 )、 纹、焊接界面的裂纹、焊点扰动、冷焊、锡球熔化 焊接界面的裂纹、焊点扰动、冷焊、 不完全、移位(焊球与PCB焊盘不对准)、球窝等 PCB焊盘不对准)、 不完全、移位(焊球与PCB焊盘不对准)、球窝等 缺陷。 缺陷。 • 目前,验收标准大多采用美国电子装联业协会制定 目前, 的IPC-A-610D, IPC- 610D,
• 然后对信号进行处理放大,由计算机进一步分析或观察 然后对信号进行处理放大, • 根据不同材料对x射线的不透明度系数的差异,利用图像 根据不同材料对x射线的不透明度系数的差异, 分析软件来分析和判断焊点质量。 分析软件来分析和判断焊点质量。
X-ray焊点图像分析 ray焊点图像分析
• X射线透视图能够定量地显示出焊点厚度、 射线透视图能够定量地显示出焊点厚度、 形状及质量的密度分布。根据X 形状及质量的密度分布。根据X射线检测到 的厚度、形状及质量的密度分布指标及图像, 的厚度、形状及质量的密度分布指标及图像, 结合强大的图像分析软件就能够分析和判断 焊点的焊接质量