3DCS公差分析工作规范
基于3DCS的发动机前端轮系装配偏差仿真分析
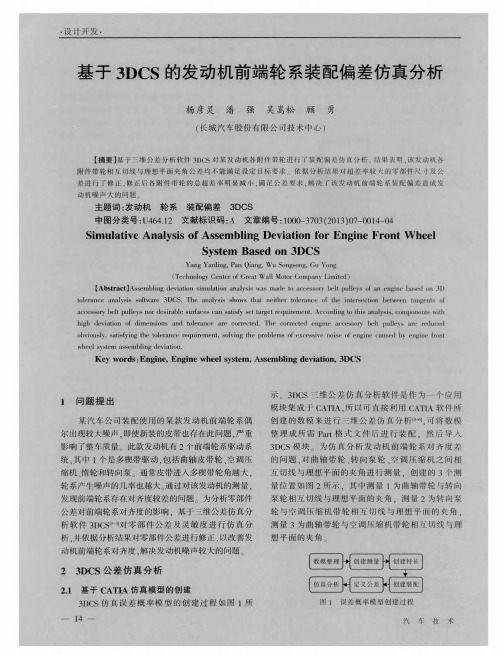
- 0 . 2 6
0. 57
0 . 0 8
-0. 41
0 . 2 0
0. 08
2 7 5
3 08
0 . 2 9
O. 1 8
0 . 2 5
0- 3 8
0 . 3 5
0. 2 6
1 9 4
1 95
4
5
一 O . 1 2
/ ( 。 )
一0 . 11
/ ( 。 )
0. 32
/ mm
-0. 3 பைடு நூலகம்
/ ( 。 )
O. 1 l
/ ( 。 )
2 61
/ ( 。 )
0. 1 7
/ mm
0. 2 8
/ ( 。 )
0 . 23
/ ( 。 )
1 95
2
3
0 . 0 3
5 %的要 求 。
4 对 齐 度 测 量
为验证 公差 修正 后发 动机前 端 轮系对 齐度改 善 情 况 .采 用 F A R O便携 式 C MM 对生 产线 上 的一 台 发动 机机 体进行 测量 . 共测 量 5台套 附件 系统 . 测量 结果 如表 7所列 修正前 发动 机前 端轮 系对齐 度测
表 明公 差 修正 后 发动 机 前端 轮 系 对齐 度 明 显改 善 .
解决 了发 动机 前端 轮 系皮带 进入角 超差 问题
参 考 文 献 1 贾 信朝 . 龚 成云. D C S在 长 安 公 司 的应 用 及 展 望 . 电焊 机 .
2 0 1 0 , 4 0 ( 5 ) : 1 2 4 ~ 1 2 9 .
三坐标操作规范范文
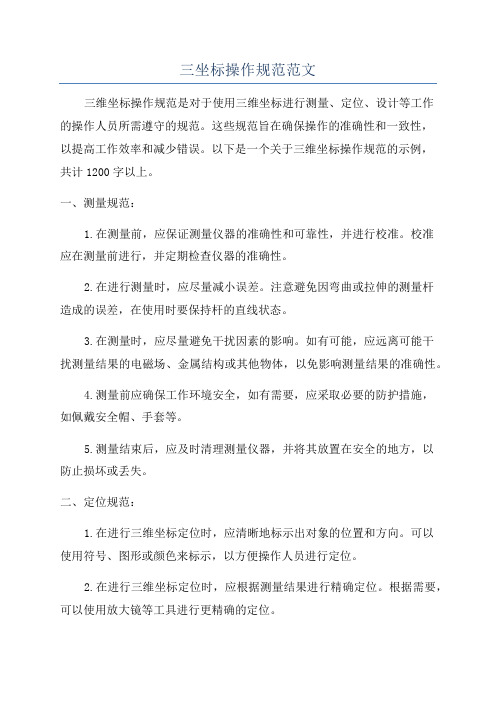
三坐标操作规范范文三维坐标操作规范是对于使用三维坐标进行测量、定位、设计等工作的操作人员所需遵守的规范。
这些规范旨在确保操作的准确性和一致性,以提高工作效率和减少错误。
以下是一个关于三维坐标操作规范的示例,共计1200字以上。
一、测量规范:1.在测量前,应保证测量仪器的准确性和可靠性,并进行校准。
校准应在测量前进行,并定期检查仪器的准确性。
2.在进行测量时,应尽量减小误差。
注意避免因弯曲或拉伸的测量杆造成的误差,在使用时要保持杆的直线状态。
3.在测量时,应尽量避免干扰因素的影响。
如有可能,应远离可能干扰测量结果的电磁场、金属结构或其他物体,以免影响测量结果的准确性。
4.测量前应确保工作环境安全,如有需要,应采取必要的防护措施,如佩戴安全帽、手套等。
5.测量结束后,应及时清理测量仪器,并将其放置在安全的地方,以防止损坏或丢失。
二、定位规范:1.在进行三维坐标定位时,应清晰地标示出对象的位置和方向。
可以使用符号、图形或颜色来标示,以方便操作人员进行定位。
2.在进行三维坐标定位时,应根据测量结果进行精确定位。
根据需要,可以使用放大镜等工具进行更精确的定位。
3.在定位时,应尽量减小误差。
注意避免因位置偏移、旋转不准确等原因造成的误差。
4.定位结束后,应将定位结果记录下来,并标记在相应的位置上。
保留记录以备日后参考。
三、设计规范:1.设计时应遵循客户需求和工程要求,合理确定设计方案。
根据需要,可以使用三维建模软件进行辅助设计。
2.在进行三维建模时,应注意几何关系的准确性和完整性。
确保图形的各个元素之间的关系合理明确,以提高设计的可读性和可操作性。
3.在进行三维建模时,应注意保持设计的一致性。
遵循相同的尺寸单位、比例尺和坐标系,以确保不同部分之间的协调性。
4.设计结束后,应对设计结果进行审查和验证。
根据需要,可以进行仿真和模拟验证,以确保设计的可行性和可靠性。
四、数据处理规范:1.在进行三维坐标数据处理时,应使用专业的软件工具。
基于3DCS的矫直机装配公差仿真及优化

《中国重型装备》CHIPAHEAVYEQUIPMENTNo. 2Aprii 2021厂“ “、♦实验研究♦基于3DCS 的矫直机装配公差仿真及优化韦联(二重(德阳)重型装备有限公司,四川618000)摘要:应用三维公差分析软件3DCS 对某钢厂矫直机下辐座装配过程进行仿真分析,得到辐面间隙值的概 率分布图以及各组成环公差对该间隙值影响的贡献度,按贡献度大小,有针对性的对各组成环公差值进行优 化,再次仿真,最终得到合理的各组成环公差值分配。
关键词:下辐座装配;蒙特卡洛法;3DCS;公差仿真;公差优化中图分类号:TG333.2*3 文献标志码:BTolerance Simuiation and Optimization of Straightener Assembiy Based on 3DCSWei LianAbstraC : Lower roller stand assembly process of the straightener in a certain steel plant has been carried outsimulation analysis by applying 3DCS, a three-dimensionai telerance analysis software, it cencluded probability distribution figuro of roli surface clearance values and contribution deeree of effects of components ring tolerance onthe clearance values. According te conWibuUon degree , taraeted components ring tolerance values have beenoptimized te obtain reasonable components ring tolerance ealues disWiXuUon after simulation.Key wordt : lower roller stand assembly ; Monte optimization辐式矫直机是轧制件连续通过多个交错排列 转动着的矫直辐,在矫直辐压下力作用下,产生弹塑性变形,轧制件经过多个矫直辐的作用后,弯曲 曲率逐步减少,最终达到规定的平面度要求。
3DCS软件操作书

欢迎使用3DCS Analyst CAA V53DCS软件使用说明书基于CATIA V5的图形公差分析3DCS Analyst, CAA V5 Based 软件由Dimensional Control Systems, Inc.(Dassault Systems公司合作伙伴) 出品。
©1994-2012 Dimensional Control Systems, Inc.版权所有©中文版有ETA编译(2.0版)如有任何建议请联系技术支持目录目录 (2)第一课:3DCS模型概述 (5)1.1启动3DCS Analyst, CAA V5 (9)1.2网格显示菜单(Display Mesh) (10)1.3参数(Preferences) (13)1.4图形分析菜单(Graphical Analysis Menu) (18)1.5统计分析菜单(Statistical Analysis Menu) (20)1.6模型创建菜单(Model Creation Menu ) (25)1.7特征创建浏览(Feature Creation Review) (30)第二课:开始建立新的模型 (34)2.1插入零件 (35)2.2更改零件参数 (36)第三课:测量 (43)3.1 创建上部间隙测量 (43)3.2 创建下部间隙测量值 (51)3.3创建特征之间的间距测量 (52)3.4平移Headlamp和Turnlamp使之与Bracket分离。
(55)第四课创建装配 (58)4.1 特征创建(Feature Creation) (60)4.2创建Slot(槽)功能(Slot Function) (65)4.3创建Turnlamp装配 (67)4.4创建Headlamp装配 (73)第五课:创建公差 (80)5.1 为零件Bracket添加公差 (81)5.2 为Headlamp和Turnlamp添加公差 (85)第六课:模型分析 (89)6.1运行分析 (90)6.2运行GeoFactor (92)第七课:创建夹具 (95)7.1更新模型。
3DCS软件操作书

欢迎使用3DCS Analyst CAA V53DCS软件使用说明书基于CATIA V5的图形公差分析3DCS Analyst, CAA V5 Based 软件由Dimensional Control Systems, Inc.(Dassault Systems公司合作伙伴) 出品。
©1994-2012 Dimensional Control Systems, Inc.版权所有©中文版有ETA编译(2.0版)如有任何建议请联系技术支持目录目录 (2)第一课:3DCS模型概述 (5)1.1启动3DCS Analyst, CAA V5 (9)1.2网格显示菜单(Display Mesh) (10)1.3参数(Preferences) (13)1.4图形分析菜单(Graphical Analysis Menu) (18)1.5统计分析菜单(Statistical Analysis Menu) (20)1.6模型创建菜单(Model Creation Menu ) (25)1.7特征创建浏览(Feature Creation Review) (30)第二课:开始建立新的模型 (34)2.1插入零件 (35)2.2更改零件参数 (36)第三课:测量 (43)3.1 创建上部间隙测量 (43)3.2 创建下部间隙测量值 (51)3.3创建特征之间的间距测量 (52)3.4平移Headlamp和Turnlamp使之与Bracket分离。
(55)第四课创建装配 (58)4.1 特征创建(Feature Creation) (60)4.2创建Slot(槽)功能(Slot Function) (65)4.3创建Turnlamp装配 (67)4.4创建Headlamp装配 (73)第五课:创建公差 (80)5.1 为零件Bracket添加公差 (81)5.2 为Headlamp和Turnlamp添加公差 (85)第六课:模型分析 (89)6.1运行分析 (90)6.2运行GeoFactor (92)第七课:创建夹具 (95)7.1更新模型。
尺寸控制解决方案介绍-3DCS

尺寸控制解决方案介绍
1
DS PLM解决方案的同一平台----V5
2
需求
1、从经验到理论 - 间隙的控制 -拆分公差; -设计工艺评审
2、各个工艺独立设计->协同工艺设计 - 单件公差控制 - 装焊公差控制 -总装公差控制
3、设计部门的数据直接利用 - 3D数模(含定位孔、夹点、焊点等信息) - 2D数模/打印图纸(冲压件关键处、搭接处的公差、大装配
12
4. 几何因子分析
有了上一步灵敏度分析中得到的重要因素后,对这些因素进行分析评价, 得出其几何因子。可以通过改变产品结构、工装卡具等,增强设计的鲁 棒性。
13
5. 装配验证
3DCS可以在CATIA环境中模拟实际的装配过程,检查由公差带来的装配问题。
14
3DCS is the ideal tool for supporting the Dimensional Management Process in CATIA V5
3DCS Analyst
An Advanced tool to meet the needs of Specialists
3DCS Designer
A core solution to meet the needs of Designers & Engineers
基于3DCS的白车身偏差分析
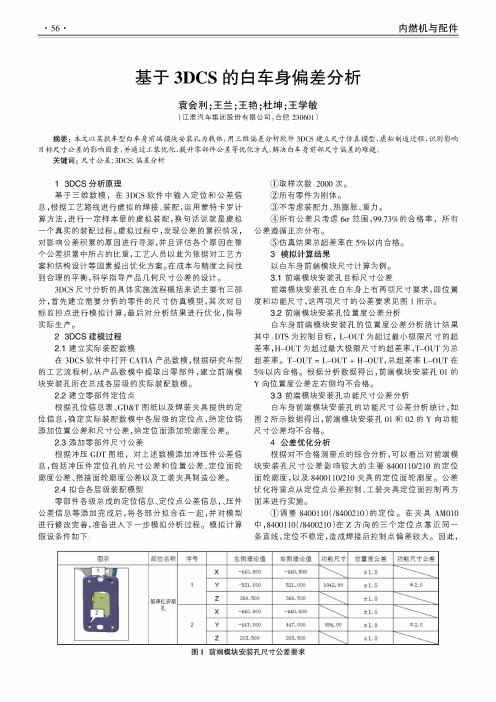
• 56•内燃机与配件基于3DCS的白车身偏差分析袁会利;王兰;王艳;杜坤;王学敏(江淮汽车集团股份有限公司,合肥230601)摘要:本文以某款车型白车身前端模块安装孔为载体,用三维偏差分析软件3D C S建立尺寸仿真模型,虚拟制造过程,识别影响目标尺寸公差的影响因素,并通过工装优化、提升零部件公差等优化方式,解决白车身前部尺寸偏差的难题。
关键词:尺寸公差;3DCS;偏差分析13D C S分析原理基于三维数模,在3DCS软件中输入定位和公差信 息,根据工艺路线进行虚拟的焊接、装配,运用蒙特卡罗计 算方法,进行一定样本量的虚拟装配,换句话说就是虚拟 一个真实的装配过程。
虚拟过程中,发现公差的累积情况,对影响公差积累的原因进行寻源,并且评估各个原因在整 个公差积累中所占的比重,工艺人员以此为依据对工艺方 案和结构设计等因素提出优化方案。
在成本与精度之间找 到合理的平衡,科学指导产品几何尺寸公差的设计。
3DCS尺寸分析的具体实施流程概括来说主要有三部 分,首先建立需要分析的零件的尺寸仿真模型,其次对目 标监控点进行模拟计算,最后对分析结果进行优化,指导 实际生产。
2 3D C S建模过程2.1建立实际装配数模在3DCS软件中打开CATIA产品数模,根据研究车型 的工艺流程树,从产品数模中提取出零部件,建立前端模 块安装孔所在总成各层级的实际装配数模。
2.2 建立零部件定位点根据孔位信息表、GD&T图纸以及焊装夹具提供的定 位信息,确定实际装配数模中各层级的定位点,给定位销 添加位置公差和尺寸公差,给定位面添加轮廓度公差。
2.3添加零部件尺寸公差根据冲压GDT图纸,对上述数模添加冲压件公差信 息,包括冲压件定位孔的尺寸公差和位置公差、定位面轮 廓度公差、搭接面轮廓度公差以及工装夹具制造公差。
2.4拟合各层级装配模型零部件各级总成的定位信息、定位点公差信息,、压件 公差信息等添加完成后,将各部分拟合在一起,并对模型 进行修改完善,准备进入下一步模拟分析过程。
汽车尺寸工程中的公差分析技术

各个区域的公差给定(下图 5):
图5 总成的公差源分析(下图 6):
图6
地板宽度方向的尺寸公差计算:
1.42 + 0.52 + 0.52 + 0.52 + 0.52 + 1.42 = 2.22=±1.11
结论,方案二的产品及工艺设计基本符合要求。 ④ 方案三,通过翻边及定位销定位(下图 7):
一、汽车尺寸工程
汽车白车身由几百个薄板冲压件经过焊接而成。主要经历的工艺流程有:薄板冲压-中小分总成 焊接-运输-焊接-车身。从制造过程来看,车身的公差主要由冲压件本身的公差、运输产生的公差、 夹具定位公差、焊接造成的公差等构成。车身公差的情况直接导致车辆品质的好坏,车身公差是汽 车尺寸工程重点解决的问题。
尺寸工程开发流程:贯穿于新车型开发项目全过程中的同步工程分析(SE)、工程化阶段的冲压 CAE 分析、尺寸公差仿真分析,以及在开发及生产制造过程中的全面质量管理。
同步工程分析(SE)是借助于工艺设计人员的经验、企业的工艺标准、工艺能力,重点对汽车产 品的工艺可行性进行分析、优化产品设计。冲压 CAE 分析主要对车身冲压件的成型性、工艺性进行 校核和优化。尺寸公差仿真分析则是借助于三维分析软件对车身尺寸公差链进行计算和验证,验证 及优化产品结构设计、公差设计及工艺设计。同时采用比较完善的生产过程尺寸控制手段(如各种 检具、功能主模型 CUBING、匹配夹具 PCF 等)来监测和指导整改实物零部件尺寸质量,最终保证整 车的制造精度。
3DCS 的核心机理是按照实际生产能力初步给出零部件的公差,然后按照工艺规划的装配顺序, 按照夹持点文件,按加工能力给定工装(夹具)的公差,按实际能力给出焊接变形公差,建立公差 分析模型,根据定位系统及公差进行驱动,在三维空间内进行各个特征的公差叠加计算,根据零部 件的几何形状在其自身公差及工装的定位公差作用下模拟出公差在三维空间中的传递、转换。3DCS 三维公差叠加的原理:所有的特征点公差服从正态分布(及其他分布如平均分布等),按照蒙特卡罗 规则,对所有特征点(零部件孔、面公差,夹具公差,焊接变形公差等)随机给出服从于正态分布 的实际公差,然后按照零部件的装配关系,对所有的几何形状在三维空间中进行叠加计算,计算出 所要关注特征的尺寸公差结果。可以简单的这样理解,在三维环境中,把每个零部件当实物零件看 待,按蒙特卡罗规则给出的每一组公差,代表着实物零部件样本的生产制造实际公差,然后对所有 的零部件按照现实中的工艺流程进行装配焊接,并尽可能真实得考虑到夹具定位、焊接变形带来的 公差。车身公差分析模型构建完成后也就代表着实际生产的白车身,我们可以很容易地对车身上的 每一个功能尺寸进行检测、评估,判断其是否符合设计要求。对车身上每一个零部件特征尺寸按照 正态分布随机给出 2000 组公差,虚拟装配成白车身总成后各个功能尺寸对应有 2000 组公差值,对 这 2000 组公差值进行统计过程控制(SPC),我们可以得到一系列的评价指标及参数:6σ、CPK 等, 根据它们我们可以评估车身尺寸状态。
3DCS公差分析应用介绍-HSY

华盛扬科技
华盛扬科技有限公司
3DCS 公差分析应用指南
底盘悬架案例
+
±0.5度
-注意弄清楚装配基准和检测基准
-最好是GD&T图纸(检测基准和尺寸要素形位公差要求)3、对于图纸不全的或者不明确的,需要明确基础公差或通行公差
PART 文件PART 文件
更新结构数和模型
编辑DCS 点创建DCS 点创建装配MOVE
定义公差3D GD&T 相关定义测量高级功能
DCS点的坐标参数
DCS点的方向矢量参
数
MOVE 的类型
MOVE 的类型有6面、台阶面、3-2-1、Autobend(user-Dll)、两点和三
点)
MOVE 的介绍
两点MOVE:
三点MOVE:
MOVE 的介绍
6面MOVE:
台阶面MOVE: 3-2-1
MOVE 的介绍
Autobend(自动弯曲):
定义每个定位点的
控制方向
定义需要装配的零
件或总成
最常用的是线性:适用于轮廓度
圆形:使用于位置度、垂直度定义方向
定义类型定义公差带和中值
几何因子排序
尺寸链链环数量:取决于产品结构设计、工艺流程、工
艺方案、定位基准等
END
华盛扬科技。
3DCS公差分析应用介绍-HSY

调整数模结构
2、明确装配工艺流程
建立DCS点
+ + +
建立MOVE
定义公差 3、明确分析项目和目标公差 分析前轮外倾角和后倾角,目标公差为±0.5度 分析和编制报告
定义测量
华盛扬科技
HSY HI-TEC
北京华盛扬科技有限公司 Beijing Huashengyang Hi-tech Co., Ltd. +86-10-82022908 hsy@ Page 11
HSY HI-TEC
北京华盛扬科技有限公司 Beijing Huashengyang Hi-tech Co., Ltd. +86-10-82022908 hsy@ Page 8
3DCS公差分析流程 3DCS Tolerance Analysis Workflow
数据准备
GD&T准备
调整数模结构
1、按照装配工艺流程调整数模结构数 2、如果有必要,建立虚拟零部件(如虚 拟夹具、虚拟工装、虚拟零部件)
建立DCS点
建立MOVE
定义公差
定义测量
分析和编制报告
华盛扬科技
HSY HI-TEC
北京华盛扬科技有限公司 Beijing Huashengyang Hi-tech Co., Ltd. +86-10-82022908 hsy@ Page 5
数据准备
GD&T准备
调整数模结构
建立DCS点
1、常用的MOVE有6面、台阶面、3-2-1、 AUTOBEND、2点和3点 2、MOVE是对零部件实现虚拟装配的过程 ,MOVE类型的选择必须基于真实的装 配定位
建立MOVE
定义公差
定义测量
3DCS公差分析操作步骤
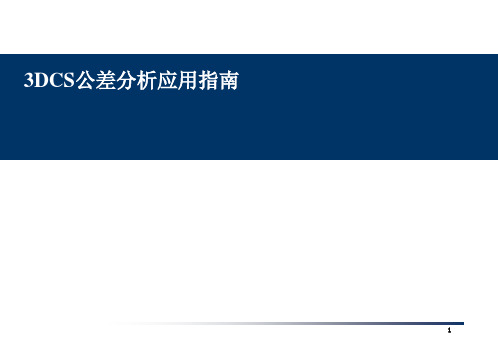
分析 Analysis
编制报告 Reporting
Update Model Update Model
Nominal Build Nominal Build
分析 Analysis
3DCS公差分析流程 3DCS Tolerance Analysis Workflow
CAD 数据 CAD data
工艺流程图 Flow Chart
MLP表 MLP Forms
技术要求 Major Technical Specifications
产品质量基准 GD&T Drawing
3DCS公差分析流程 3DCS Tolerance Analysis Workflow
数据准备 Data Preparation
定义Measurement Creating Measurement
分析 Analysis
编制报告 Reporting
定义焊点位置零件的Tolerance Creating Part Pro at Weld Point Position
定义焊点位置另外一个焊装零件的的Tolerance Creating Weld-to Part Pro at Weld Point Position
定义零件焊点的DCS Point Creating DCS Weld Points on Part
复制零件焊点的DCS Point到焊装的另外一个零件 Coping DCS Points from Part to Weld-to Part
定义Move Creating Move
3DCS公差分析流程 3DCS Tolerance Analysis Workflow
基于3DCS的白车身子基准的公差设计
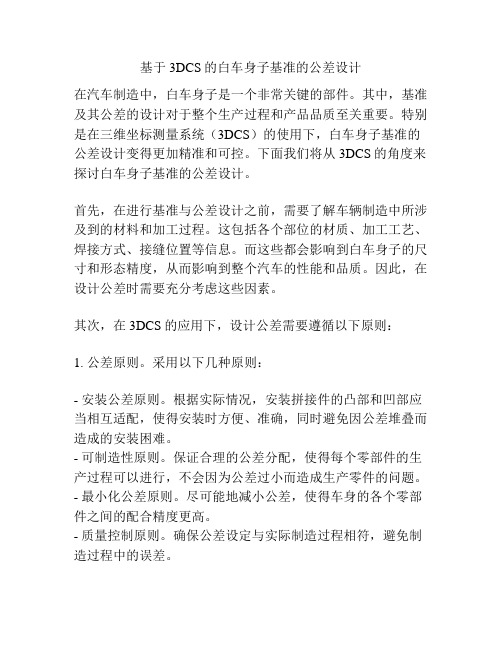
基于3DCS的白车身子基准的公差设计在汽车制造中,白车身子是一个非常关键的部件。
其中,基准及其公差的设计对于整个生产过程和产品品质至关重要。
特别是在三维坐标测量系统(3DCS)的使用下,白车身子基准的公差设计变得更加精准和可控。
下面我们将从3DCS的角度来探讨白车身子基准的公差设计。
首先,在进行基准与公差设计之前,需要了解车辆制造中所涉及到的材料和加工过程。
这包括各个部位的材质、加工工艺、焊接方式、接缝位置等信息。
而这些都会影响到白车身子的尺寸和形态精度,从而影响到整个汽车的性能和品质。
因此,在设计公差时需要充分考虑这些因素。
其次,在3DCS的应用下,设计公差需要遵循以下原则:1. 公差原则。
采用以下几种原则:- 安装公差原则。
根据实际情况,安装拼接件的凸部和凹部应当相互适配,使得安装时方便、准确,同时避免因公差堆叠而造成的安装困难。
- 可制造性原则。
保证合理的公差分配,使得每个零部件的生产过程可以进行,不会因为公差过小而造成生产零件的问题。
- 最小化公差原则。
尽可能地减小公差,使得车身的各个零部件之间的配合精度更高。
- 质量控制原则。
确保公差设定与实际制造过程相符,避免制造过程中的误差。
2. 公差分配。
通过3DCS软件的模拟,在结果可信的范围内,将公差分配到不同零部件上,尽可能降低总体公差值。
同时需要考虑到车身的各个部分的功能,和公差对功能带来的影响。
3. 公差分析。
使用3DCS软件,针对各个零部件的尺寸及位置测量数据进行分析和模拟,确定公差的分配和调整,分析结果是对公差分配的校验和指导。
总之,在白车身子基准的公差设计中,3DCS能够提供精准的测量和模拟分析工具,根据实际情况进行公差设计,并且通过模拟并校验公差设置的准确性,有效地提高了制造质量和效率。
除此之外,3DCS还可以通过对数据的收集、分析和处理来获取更多的信息,例如设计的改良、增加制造过程的控制、验证设计等。
同时,它可以让生产商在成本控制和品质保证之间求得平衡,并可以识别和纠正生产流程中任何不规则或缺陷。
3DCS公差分析操作步骤
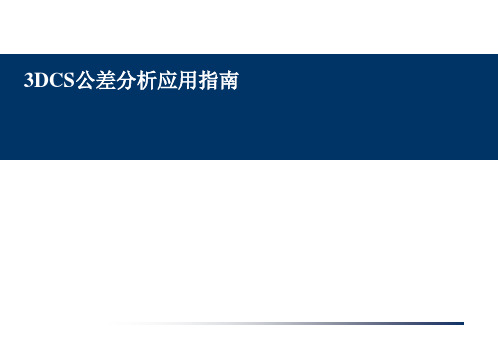
定义工装定位块和定位销的Tolerance Creating Fixture Pad/Pin Tolerance 定义焊装过程的Move Creating Weld Move 定义焊点位置零件的Tolerance Creating Part Tolerance at Weld Point Position 定义Measurement Creating Measurement 分析 Analysis 编制报告 Reporting
1. 数据准备 Data Preparation
Step1:根据MLP表,装配流程表等规划 公差分析的Move。
Tips for define Moves The Primary plane is largest plane to create point1, 2, 3 The Secondary plane is second largest plane to create point 4, 5 The Tertiary plane is smallest plane to create point6
定义焊装过程的Move Creating Weld Move 定义焊点位置零件的Tolerance Creating Part Tolerance at Weld Point Position 定义Measurement Creating Measurement 分析 Analysis 编制报告 Reporting
数据准备 Data Preparation 定义零件到工装的Move Creating Part-to-Fixture Move
定义工装定位块和定位销的Tolerance Creating Fixture Pad/Pin Tolerance 定义焊装过程的Move Creating Weld Move 定义焊点位置零件的Tolerance Creating Part Tolerance at Weld Point Positieasurement 分析 Analysis 编制报告 Reporting Update Model Update Model Nominal Build Nominal Build 分析 Analysis
3dcs公差分析应用介绍 hsy

3DCS公差分析应用介绍什么是3DCS公差分析?3DCS(Dimensional Control Systems)是一种用于模拟和评估产品装配过程中的公差累积和影响的软件工具。
通过3DCS公差分析,可以发现并解决产品装配中可能出现的问题,确保产品的质量和性能。
公差是指由于制造过程中的不精确性而导致的产品尺寸、形状和位置的变化。
在许多行业,如汽车、航空航天和电子设备制造等,产品的尺寸和形状非常重要,公差问题可能导致产品的不合适装配、性能下降甚至不能正常工作。
3DCS公差分析可模拟产品装配过程中的公差累积情况,并预测产品装配后的质量和性能。
这使得制造商能够及早发现并解决潜在的公差问题,使产品达到设计要求。
3DCS公差分析的应用1.公差累积分析:通过对每个零部件的公差进行分析,可以确定整个产品装配过程中的公差累积情况。
这有助于评估产品的装配要求和可能的公差敏感区域。
2.公差优化:通过对不同公差方案的模拟和比较,可以找到最佳的公差方案,以减小公差累积和改善装配质量。
3.工艺改进:公差分析可以帮助制造商了解哪些工艺参数对装配过程的公差累积有重要影响。
这有助于改进生产工艺,减小公差,提高产品的质量和性能。
4.设计验证:在产品设计阶段,通过3DCS公差分析,可以预测产品装配后的质量和性能。
这有助于验证设计的可行性以及改进设计以满足装配要求。
5.故障解决:当产品在装配过程中出现问题时,通过从装配数据和公差分析结果中提取关键信息,可以帮助解决装配问题,找到解决方案。
3DCS公差分析的优势1.全面性:3DCS公差分析可以对产品的每个零部件和装配过程进行细致的模拟和分析,包括各种公差特性如平面度、直线度、圆度、位置偏移等。
2.可视化:通过3DCS公差分析,可以生成3D模型,直观地展示公差累积情况和装配结果。
这有助于更好地理解产品装配过程中的公差问题和潜在风险。
3.高度准确性:3DCS公差分析基于先进的数学模型和统计方法,能够高度准确地预测产品的装配质量和性能。
3DCS软件公差分析培训资料
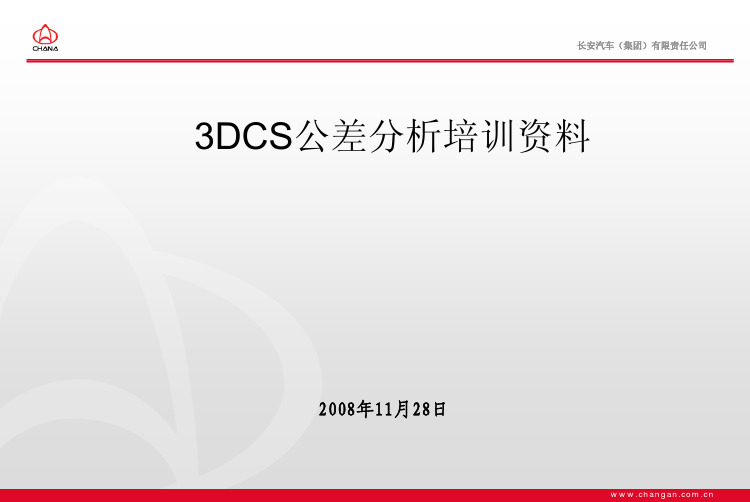
3DCS公差分析培训资料2008年11月28日报告题名前排座椅安装孔区域公差计算分析报告车型/机种报告版本适应标准报告分类分析类型01 3维仿真分析验证分析软件版本3DCS总页数模型文件相关零件XXX前一版本号协作单位/人员报告完成人员报告完成日期DCS公差分析假设条件1、零件公差的设定应遵循如下的流程:1.1 装配顺序(流程)严格服从于产品及工艺设计;1.2 定位系统严格服从于定位设计及工装设计;1.3 各种公差设定严格服从于现有制造水平2、除非特别指出,零件的公差均服从正态分布;3、所有的零部件均被认为是刚体,不存在变形(特殊零件除外);4、除非特别指出,中立的影响不考虑在内;5、单件在总成装配中的磨损不考虑在内;6、装配夹具和检具的变形不考虑在内;7、夹具和检具的热变形记热膨胀不考虑在内;8、CAD模型的尺寸是名义尺寸。
9、仿真计算的次数(样本数)为5000(虚拟制造的台数)。
分析项目:¾按照产品数模、工艺设计(焊接工艺流程)等输入,根据现有制造能力,分析计算前排座椅A、B、C、D四个安装孔位置度公差、安装面轮廓度公差及各个安装孔间的距离公差。
¾公差设定:车身冲压件基准孔尺寸公差:R0-10mm: 0 to +0.1mmR10-20mm: 0 to +0.15mmR20-40mm: 0 to +0.2mm基准孔位置度公差:-0.1 to +0.1mm重要孔位置度公差: -0.5 to +0.5mm(看起来有点大,暂设定)重要面轮廓度公差: -0.7 to +0.7mm焊接夹具定位销尺寸公差:-0.1 to -0.15mm定位销位置度公差:-0.1 to +0.1mm定位块轮廓度公差:-0.2 to +0.2mm焊接工艺流程(装配关系及装配顺序):制定初步公差目标:前地板焊接总成定位基准:定位面:A1,A2,A3主定位孔:B次定位孔:C目标公差(相对于前地板焊接总成定位基准):前排座椅安装孔A/B位置度公差是φ1.5(±0.75),对应安装面轮廓公差是2(±1);前排座椅安装孔C/D位置度公差是φ1.5(±0.75),对应安装面轮廓公差是2(±1);前排座椅安装孔A与D的距离公差是±1.0(未在左边GD&T图中表示出);前排座椅安装孔B与C的距离公差是±1.0(未在左边GD&T图中表示出);前排座椅安装孔C与D的距离公差是±1.0(未在左边GD&T图中表示出).B11-5101583定位方案(GD&T图纸):夹具定位夹持点布置(MCP)B11-5101583GD&T(几何尺寸公差图),A1,A2,A3,E1,B是实际的定位面和定位孔B11-5101585定位方案(GD&T图纸):夹具定位夹持点布置(MCP)B11-5101585GD&T(几何尺寸公差图),A1,A2,A3,E1,B是实际的定位面和定位孔B11-5101581定位方案(GD&T图纸):夹具定位夹持点布置(MCP)B11-5101581GD&T(几何尺寸公差图),A1,A2,A3,B,C是实际的定位面和定位孔。
3DCS三维偏差分析软件分析汽车柔性零件的应用
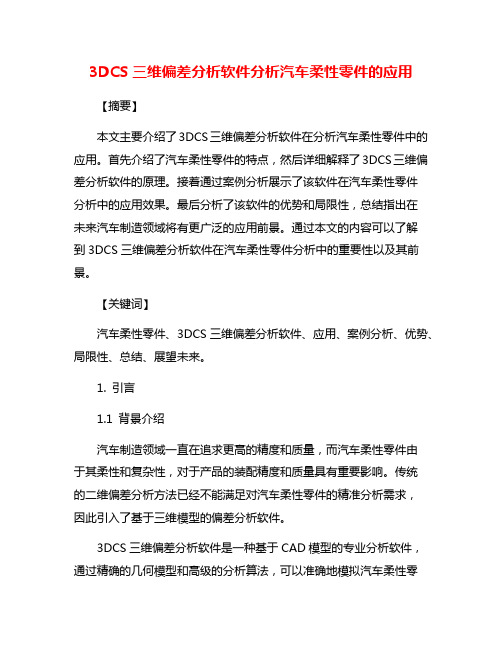
3DCS三维偏差分析软件分析汽车柔性零件的应用【摘要】本文主要介绍了3DCS三维偏差分析软件在分析汽车柔性零件中的应用。
首先介绍了汽车柔性零件的特点,然后详细解释了3DCS三维偏差分析软件的原理。
接着通过案例分析展示了该软件在汽车柔性零件分析中的应用效果。
最后分析了该软件的优势和局限性,总结指出在未来汽车制造领域将有更广泛的应用前景。
通过本文的内容可以了解到3DCS三维偏差分析软件在汽车柔性零件分析中的重要性以及其前景。
【关键词】汽车柔性零件、3DCS三维偏差分析软件、应用、案例分析、优势、局限性、总结、展望未来。
1. 引言1.1 背景介绍汽车制造领域一直在追求更高的精度和质量,而汽车柔性零件由于其柔性和复杂性,对于产品的装配精度和质量具有重要影响。
传统的二维偏差分析方法已经不能满足对汽车柔性零件的精准分析需求,因此引入了基于三维模型的偏差分析软件。
3DCS三维偏差分析软件是一种基于CAD模型的专业分析软件,通过精确的几何模型和高级的分析算法,可以准确地模拟汽车柔性零件的装配过程,帮助汽车制造商预测和分析零件装配时可能出现的偏差和误差。
对于保证产品装配质量和工艺的稳定性具有重要意义。
本文将结合汽车柔性零件的特点和3DCS三维偏差分析软件的原理,探讨该软件在分析汽车柔性零件中的应用,并通过案例分析验证其有效性。
分析其优势和局限性,总结分析目前的研究成果,并展望未来在汽车制造领域的发展前景。
1.2 研究意义汽车行业的发展日新月异,市场竞争日益激烈,对汽车柔性零件的质量和性能要求也越来越高。
柔性零件是指那些在使用过程中可能受到力学变形或损伤的零部件,比如密封件、软管、橡胶制品等。
这些柔性零件在汽车整车设计中起着非常重要的作用,直接影响到汽车的安全性、舒适性和可靠性。
在汽车制造领域,如何准确地分析柔性零件在装配过程中可能出现的偏差,以提前发现和解决问题,一直是汽车制造厂商和设计师们所面临的挑战之一。
而3DCS三维偏差分析软件则是一种通过数字化建模和仿真技术来帮助用户快速准确地评估和优化柔性零件在装配过程中可能出现的偏差的工具。
三维精度分析软件安全操作及保养规程

三维精度分析软件安全操作及保养规程随着科技的不断发展,三维精度分析软件的应用范围越来越广泛,但同时也要求我们在使用这些软件的过程中保证其安全性和稳定性。
本文将介绍三维精度分析软件的安全操作和保养规程,以保证软件的正常工作和延长其使用寿命。
一、安全操作规程1.1 确认软件版本在使用三维精度分析软件之前,务必确认软件版本是否正确。
如果您使用的是过期的版本或不兼容的版本,可能会导致软件出现异常或功能不完整的情况。
1.2 确认计算机配置三维精度分析软件对计算机的配置要求较高,在使用软件之前,应确认计算机的配置是否满足最低要求。
不合适的计算机配置会对软件的性能产生负面影响。
1.3 固定计算机设备在使用三维精度分析软件时,应固定计算机设备,以防止移动时产生的物理损坏和数据丢失等问题。
如果需要移动计算机设备,应该在计算机关闭之后进行,避免发生数据丢失的情况。
1.4 防止病毒入侵在使用三维精度分析软件时,应注意防止病毒入侵。
可以通过安装杀毒软件来防止病毒入侵。
另外,还应定期对计算机进行杀毒扫描,以确保计算机和软件的安全。
1.5 合理使用软件功能在使用三维精度分析软件时,应合理使用各项功能,不得随意更改或删除软件的内部设置文件。
否则,可能会影响软件的运行效果和计算结果的精确度。
1.6 避免操作失误在使用三维精度分析软件时,应避免因为操作失误导致软件出现异常或数据丢失等问题。
应该在使用软件之前仔细阅读软件说明书或教程,熟悉软件的使用方法和注意事项。
1.7 适时备份数据在使用三维精度分析软件时,应定期备份数据,以防止因为计算机故障或意外事件导致数据丢失而造成不必要的损失。
备份数据的频率可以根据实际情况而定,建议至少每周备份一次。
二、保养规程2.1 定期清理计算机三维精度分析软件的使用会产生大量的中间结果和缓存文件,这些文件会占用计算机硬盘空间,同时还会对计算机性能产生影响。
因此,应定期清理计算机,清理临时文件、日志文件和浏览器缓存等。
3DCS公差分析工作规范
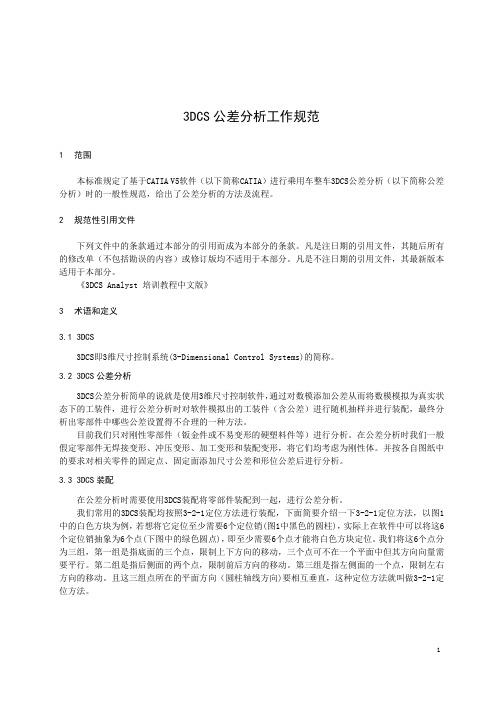
3DCS公差分析工作规范1范围本标准规定了基于CATIA V5软件(以下简称CATIA)进行乘用车整车3DCS公差分析(以下简称公差分析)时的一般性规范,给出了公差分析的方法及流程。
2规范性引用文件下列文件中的条款通过本部分的引用而成为本部分的条款。
凡是注日期的引用文件,其随后所有的修改单(不包括勘误的内容)或修订版均不适用于本部分。
凡是不注日期的引用文件,其最新版本适用于本部分。
《3DCS Analyst 培训教程中文版》3术语和定义3.13DCS3DCS即3维尺寸控制系统(3-Dimensional Control Systems)的简称。
3.23DCS公差分析3DCS公差分析简单的说就是使用3维尺寸控制软件,通过对数模添加公差从而将数模模拟为真实状态下的工装件,进行公差分析时对软件模拟出的工装件(含公差)进行随机抽样并进行装配,最终分析出零部件中哪些公差设置得不合理的一种方法。
目前我们只对刚性零部件(钣金件或不易变形的硬塑料件等)进行分析。
在公差分析时我们一般假定零部件无焊接变形、冲压变形、加工变形和装配变形,将它们均考虑为刚性体。
并按各自图纸中的要求对相关零件的固定点、固定面添加尺寸公差和形位公差后进行分析。
3.33DCS装配在公差分析时需要使用3DCS装配将零部件装配到一起,进行公差分析。
我们常用的3DCS装配均按照3-2-1定位方法进行装配,下面简要介绍一下3-2-1定位方法,以图1中的白色方块为例,若想将它定位至少需要6个定位销(图1中黑色的圆柱),实际上在软件中可以将这6个定位销抽象为6个点(下图中的绿色圆点),即至少需要6个点才能将白色方块定位。
我们将这6个点分为三组,第一组是指底面的三个点,限制上下方向的移动,三个点可不在一个平面中但其方向向量需要平行。
第二组是指后侧面的两个点,限制前后方向的移动。
第三组是指左侧面的一个点,限制左右方向的移动。
且这三组点所在的平面方向(圆柱轴线方向)要相互垂直,这种定位方法就叫做3-2-1定位方法。
- 1、下载文档前请自行甄别文档内容的完整性,平台不提供额外的编辑、内容补充、找答案等附加服务。
- 2、"仅部分预览"的文档,不可在线预览部分如存在完整性等问题,可反馈申请退款(可完整预览的文档不适用该条件!)。
- 3、如文档侵犯您的权益,请联系客服反馈,我们会尽快为您处理(人工客服工作时间:9:00-18:30)。
3DCS公差分析工作规范1范围本标准规定了基于CATIA V5软件(以下简称CATIA)进行乘用车整车3DCS公差分析(以下简称公差分析)时的一般性规范,给出了公差分析的方法及流程。
2规范性引用文件下列文件中的条款通过本部分的引用而成为本部分的条款。
凡是注日期的引用文件,其随后所有的修改单(不包括勘误的内容)或修订版均不适用于本部分。
凡是不注日期的引用文件,其最新版本适用于本部分。
《3DCS Analyst 培训教程中文版》3术语和定义3.13DCS3DCS即3维尺寸控制系统(3-Dimensional Control Systems)的简称。
3.23DCS公差分析3DCS公差分析简单的说就是使用3维尺寸控制软件,通过对数模添加公差从而将数模模拟为真实状态下的工装件,进行公差分析时对软件模拟出的工装件(含公差)进行随机抽样并进行装配,最终分析出零部件中哪些公差设置得不合理的一种方法。
目前我们只对刚性零部件(钣金件或不易变形的硬塑料件等)进行分析。
在公差分析时我们一般假定零部件无焊接变形、冲压变形、加工变形和装配变形,将它们均考虑为刚性体。
并按各自图纸中的要求对相关零件的固定点、固定面添加尺寸公差和形位公差后进行分析。
3.33DCS装配在公差分析时需要使用3DCS装配将零部件装配到一起,进行公差分析。
我们常用的3DCS装配均按照3-2-1定位方法进行装配,下面简要介绍一下3-2-1定位方法,以图1中的白色方块为例,若想将它定位至少需要6个定位销(图1中黑色的圆柱),实际上在软件中可以将这6个定位销抽象为6个点(下图中的绿色圆点),即至少需要6个点才能将白色方块定位。
我们将这6个点分为三组,第一组是指底面的三个点,限制上下方向的移动,三个点可不在一个平面中但其方向向量需要平行。
第二组是指后侧面的两个点,限制前后方向的移动。
第三组是指左侧面的一个点,限制左右方向的移动。
且这三组点所在的平面方向(圆柱轴线方向)要相互垂直,这种定位方法就叫做3-2-1定位方法。
图13.4添加公差进行公差分析时需要在软件中给零部件相应的部位添加公差,公差分析的结果受某些因素的影响较大,主要包括以下几种因素:1、每个零部件与装配相关的全部尺寸公差、形位公差信息。
2、每个零部件生产商的公差分布信息(如标准正态分布、偏正态分布等)。
3、检具的全部公差信息与其生产商的公差分布信息。
4、夹具的全部公差信息与其生产商的公差分布信息。
5、车辆运行中极限工况导致的变形。
在实际分析时一般不能充分获得上述信息,为了使分析结果贴近实际情况我们一般将相关公差设置为正态分布。
若能够充分获得上述信息,则可根据实际公差分布情况设置公差。
3.53DCS测量目前公差分析可对风险间隙相关的问题进行分析,并找出设置不合理的公差,减少由于公差设置不合理所导致的间隙不匹配问题。
在进行风险间隙公差分析时需要对重点关注的部位建立3DCS测量(如零部件间隙),以便软件能分析出哪些零部件的公差对测量结果有影响。
3.6公差分析计算在公差分析时软件将每个零部件都模拟成实际生产出的工装件(含有公差,一般选择公差服从正态分布)。
为了使分析结果贴近实际装车情况,软件在分析时从这些模拟出的工装件库中随机抽取零部件进行装配。
为了在保证计算精度的前提下提高计算速度,我们一般使用2000次抽样装配。
3.7公差分析结论公差分析结束后软件会给出公差分析的结论,根据计算结果可以快速分析出所关注的3DCS测量(如零部件间隙)是否满足我们的要求,同时可以分析出哪些公差对所关注部位(如零部件间隙)有较大影响。
由于每个实际零部件的尺寸都与理论数据存在一定的偏差,因此将这些含有公差的零部件装配到一起时零件的间隙会与理论间隙存在一定的偏差。
如果模拟后的最小间隙满足我们的设计要求说明这些零部件的公差设置的比较合理。
反之,零部件公差设置的不合理。
由于实际装车中冲压变形、焊接变形、注塑变形和装配变形等是无法避免的,因此将这些零件视为刚性体分析出的装配结果可能会与实际装配结果有一定偏差,但分析出的不合理尺寸及公差与实际情况的趋势是一致的,具有一定的指导和参考意义。
4软件设计环境配置在进行整车3DCS公差分析前需要对CATIA软件中的一些参数进行设置,以满足公差分析的要求,使计算机能够更快速有效的进行相关分析计算。
4.1CATIA软件设计设置说明在CATIA中进入“开始→AnalysisSimulation→DCS Tolerance Analysis 7.2.0.0”(如图2),点选图标后弹出参数设置对话框(如图3)进行参数设置,一般采用默认设置即可。
图2图35公差分析整车3DCS公差分析是结合整车数字模型,使用CATIA软件提供的相关功能,对数字模型进行公差分析,从而将现实零部件存在的公差设置不合理问题直观的反映在软件中,以帮助设计师进行零部件设计及调整。
公差分析若想得出与实际情况相近的结果需要搜集不同零部件的公差分布、生产线夹具的数模及其公差分布等信息。
因目前客观条件所限,无法搜信夹具的信息,因此在进行公差分析时只能做总装领域无夹具零部件的装配结果分析,又由于无法搜集零部件公差分布的信息,进行公差分析时可认为零部件公差满足正态分布,这样分析出的结果与实际情况可能有些差别,但具有一定的指导意义。
公差分析完成后可编制公差分析检查报告(见附录A)。
因条件所限目前我们只能做刚性零部件的公差分析。
5.1公差分析应用命令1.创建特征点(Feature Point):根据需求创建公差分析时所用的特征点。
2.定义/编辑移动(Define/Edit Move):根据实际情况实现对公差分析零部件的装配。
3.定义/编辑公差(Define/Edit Tolerance):根据实际情况在待分析零部件上添加公差。
4.定义/编辑测量(Define/Edit Measurement):测量两个零部件间的相对距离。
5.装配(Nominal Build):将待分析零部件装配到一起。
6.运行分析(Run Analysis):公差分析软件开始进行分析计算。
5.2公差分析流程公差分析流程如图4:图45.3 公差分析过程我们以前车灯简易模型的分析为例对整个公差分析的过程进行介绍5.3.1 打开前车灯简易模型的数模打开数模后要将数模激活为设计状态(如图5),进入3DCS模块后点击刷新命令,系统会自动生成3DCS结构树(如图6)。
图5图65.3.2 创建装配所用的点1.使用(Feature Point)命令创建前灯3DCS装配所用的点(如图7)。
按照3-2-1定位法我们需要创建6个点限制前灯的6个自由度。
实际上我们用其中的一个点(H_YZ点)限制2个自由度时可以少创建一个点。
图7中H_X1、H_X2、H_X3三点限制X向的位移和Y、Z向的旋转,H_YZ、H_Z两点限制Z向的位移和X向的旋转,H_YZ点限制Y向的位移。
图72. 使用(Feature Point)命令并选择支架与前灯对应的固定孔,创建3DCS装配所用的5个点点(如图8),创建这5个点时要保证其与前灯的5个点一一对应。
图85.3.3 创建3DCS装配使用Move命令,选择上面创建的装配点将前灯装配到支架上,如图9、图10。
图9图105.3.4 给零部件添加公差使用添加公差命令并点击装配所用点为其添加公差,公差分布使用默认值即可,默认公差分布为正态分布(Normal),并设置公差值,如图11中所示的公差值为±0.5,其中Range表示公差带的范围,Offset表示公差带的中心。
图115.3.5 建立所关注部位的测量如图12所示,使用测量命令建立两灯之间间隙的测量,并设置我们能接受的间隙值范围(即设计要求),如图13,在本例中我们将间隙值上限设置为7.5mm,下限设置为4.5mm。
建立测量后在进行计算时软件会给添加公差的固定点赋予公差值,这样将带公差的零部件装配后会引起零部件位置的变化,最终导致测量值(即间隙值)的变化,计算完成后我们考查测量值(即两灯之间的间隙值)的变化范围是否满足设计要求(4.5mm~7.5mm),如不满足要求则需要对某些公差值进行调整重新计算直至满足设计要求值为止。
图12图135.3.5 公差分析计算点击命令进行计算,一般使用默认计算次数(2000次)即可,这样可以使软件在保证分析精度的前提下高效的进行分析计算,点击Start开始计算(如图14)。
图145.3.6 公差分析结论3DCS公差分析采用蒙特卡罗法进行计算。
蒙特卡罗方法是一种随机模拟方法,以概率和统计理论方法为基础的一种计算方法,是使用随机数(或更常见的伪随机数)来解决很多计算问题的方法。
蒙特卡罗方法将所求解的问题同一定的概率模型相联系,用电子计算机实现统计模拟或抽样,以获得问题的近似解。
我们可以这样理解软件的分析过程:软件分别模拟了前照灯、转向灯和支架的供应商所生产的零件,且这些零件固定点的公差满足我们给出的正态布要求,然后采用随机抽样的方法分别在每家供应商的零件库中抽出一个零件,然后将它们组装到一起,一共进行了2000次这样的操作,并最终组装成了2000个样品。
因固定点均添加了公差,几乎每个组装后的零件与其理论位置都会有一定的偏差,这时测量两灯的间隙,如果2000个样品均满足设计要求说明这些固定点的公差设置的比较合理。
本例的分析结论见图15。
图15中横坐标为间隙值,纵坐标为横坐标对应的值在2000个样品中出现的频次,中间的两条线LSL与USL分别是我们给出的间隙值下限(4.5mm)与上限(7.5mm),图中满足设计要求的部分为绿色,红色为不满足设计要求的部分。
在图的下方有一个列表,分别列出了不同固定点的公差值对分析结果的影响程度(用百分比表示,按照影响力由大到小进行排名)。
如图所示前4项的公差对分析结果产生了决定性的影响,因此需要根据实际情况分析(综合考虑加工工艺水平、成本因素、装配条件等等)这4项的公差有哪些能够修改。
公差修改完成后重新进行计算直至满足设计要求为止。
图15。