公差分析的方法与比较 实用
第4部分:公差分析
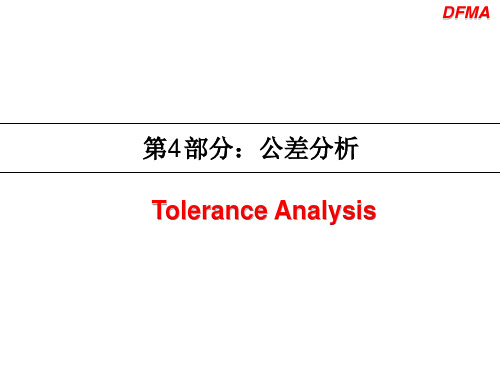
22
四. 公差分析的计算方法
DFMA
4. 极值法与均方根法的区别
当零件尺寸公差都是±0.1时,利用WC和RSS方法的计算结果区别如下: WC方法的累积公差更大,计算结果更大
23
四. 公差分析的计算方法
DFMA
4. 极值法与均方根法的区别
当产品装配公差要求是±0.5时,利用WC和RSS方法,对零件尺寸公差要 求的区别(假设尺寸链中的每个尺寸分配相同的公差)
减少尺寸链的长度,尺寸允许较大的公差
13
二. 公差分析
DFMA
C.使用定位特征
在零件的装配关系中增加可以定位的特征,例如定位柱等,定位特征能 够使得零件准确的装配在产品之中,产品设计只需要对定位特征相关的 尺寸公差进行制程管控,对其他尺寸就可以允许宽松的公差要求
D.使用点或线或小平面与平面配合代替平面与平面配合
DFMA
第4部分:公差分析 Tolerance Analysis
内容:
一.常见的公差分析做法 二.公差分析 三.公差分析的计算步骤 四.公差分析的计算方法 五.公差分析的三大原则 六.产品开发中的公差分析
DFMA
2
一. 常见的公差分析做法
DFMA
1. 产品详细设计完成后,在design review时,针对O-ring的压缩量进行
使用点或线与平面配合的方式代替平面与平面的配合方式,避免平面的 变形或者平面较高的粗糙度阻碍零件的顺利运动,从而可以对零件的平 面度和粗糙度允许宽松的公差
原始的设计
优化的设计
14
二. 公差分析
DFMA
4.公差分析的概念:
公差分析是指在满足产品功能、性能、外观和可装配性等要求的前提下, 合理定义和分配零件和产品的公差,优化产品设计,以最小的成本和最 高的质量制造产品
CAD中的公差分析与调整技巧
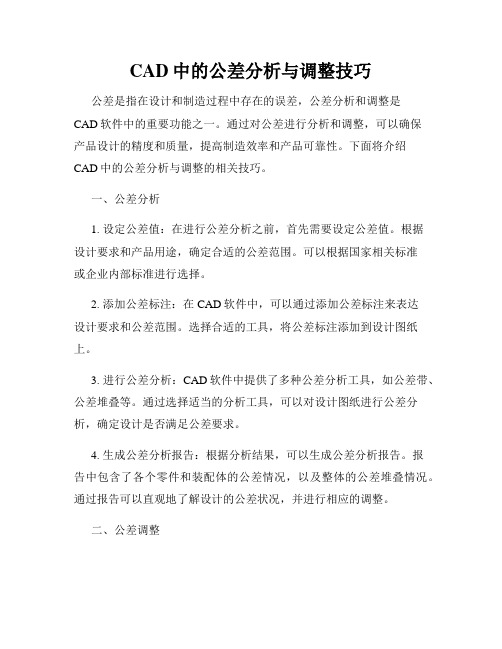
CAD中的公差分析与调整技巧公差是指在设计和制造过程中存在的误差,公差分析和调整是CAD软件中的重要功能之一。
通过对公差进行分析和调整,可以确保产品设计的精度和质量,提高制造效率和产品可靠性。
下面将介绍CAD中的公差分析与调整的相关技巧。
一、公差分析1. 设定公差值:在进行公差分析之前,首先需要设定公差值。
根据设计要求和产品用途,确定合适的公差范围。
可以根据国家相关标准或企业内部标准进行选择。
2. 添加公差标注:在CAD软件中,可以通过添加公差标注来表达设计要求和公差范围。
选择合适的工具,将公差标注添加到设计图纸上。
3. 进行公差分析:CAD软件中提供了多种公差分析工具,如公差带、公差堆叠等。
通过选择适当的分析工具,可以对设计图纸进行公差分析,确定设计是否满足公差要求。
4. 生成公差分析报告:根据分析结果,可以生成公差分析报告。
报告中包含了各个零件和装配体的公差情况,以及整体的公差堆叠情况。
通过报告可以直观地了解设计的公差状况,并进行相应的调整。
二、公差调整1. 修改零件尺寸:如果公差分析结果显示某些零件的尺寸在公差范围之外,可以通过修改零件尺寸来调整公差。
在CAD软件中,选择要修改的零件,通过编辑操作来改变零件的尺寸。
2. 调整装配体尺寸:如果公差分析结果显示整体装配的公差超出了要求,可以通过调整装配体尺寸来达到公差要求。
在CAD软件中,选择装配体,通过编辑操作来改变装配体的尺寸。
3. 调整零件位置:有时候,公差问题可能是由于零件之间的相对位置不当造成的。
在CAD软件中,可以通过移动零件的位置来调整公差。
选择要调整的零件,通过移动操作将其放置在合适的位置。
4. 使用公差配合:在CAD软件中,可以使用公差配合来调整公差。
选择合适的公差配合关系,使得不同零件之间的配合关系满足公差要求。
通过调整公差配合关系,可以减小公差堆叠效应。
总结:公差分析与调整是CAD软件中重要的功能,通过合理使用这些工具和技巧,可以提高设计的精度和质量,避免公差超出要求造成的质量问题。
CAD中的公差分析与调整方法

CAD中的公差分析与调整方法公差分析是CAD设计中至关重要的一步。
它可以帮助工程师确定零件的几何尺寸和公差范围,以确保产品的质量和性能。
在设计过程中,需要考虑材料的变化、加工和装配误差等因素,以及在使用和维修过程中的变形和磨损。
本文将介绍CAD中常用的公差分析方法和调整技巧。
首先,我们需要了解公差的定义。
在CAD中,公差是指工作尺寸和实测尺寸之间的差异。
公差可以分为线性公差和形位公差。
线性公差是指线段、直线和角度的公差,形位公差则是指位置和轮廓的公差。
在CAD软件中进行公差分析的一种常用方法是使用可视化分析工具。
这些工具可以帮助工程师在设计过程中直观地展示零件的公差分布和范围。
例如,在CAD中可以使用箭头、曲线和符号来表示零件的公差。
工程师可以通过调整这些元素的位置和大小来优化零件的设计。
另一种常用的方法是使用数学模型进行公差分析。
在CAD软件中,可以使用几何约束和参数化建模来建立数学模型。
通过模拟零件的装配和运动过程,工程师可以分析和优化公差分布。
例如,可以使用回归分析和优化算法来确定最佳公差范围。
公差的调整需要考虑到产品的功能需求、制造工艺和成本等因素。
在CAD软件中,可以采用以下几种方法来调整公差。
首先,可以通过增加材料的公差容限来调整公差。
公差容限是指在设计和加工过程中允许的误差范围。
通过增加公差容限,可以提高零件的装配和功能性能。
但是需要注意的是,增加公差容限可能会增加生产成本和制造难度。
其次,可以通过调整零件的设计和加工工艺来改善公差。
例如,可以使用更高精度的机床和工艺来加工零件,或者采用更合适的装配工艺来减少公差堆积。
此外,还可以优化零件的形状和结构,以提高公差的分布和范围。
最后,可以使用CAD软件中提供的公差优化工具来调整公差。
这些工具可以根据产品的功能需求和制造工艺要求,自动调整零件的公差范围和分布。
工程师可以通过设置不同的优化目标和约束条件,来获得最佳的公差方案。
综上所述,公差分析和调整在CAD设计中是不可或缺的一步。
CAD软件中的公差与公差分析技巧

CAD软件中的公差与公差分析技巧在CAD软件中,公差是一个非常重要的概念,它对于设计和制造过程都起着至关重要的作用。
公差是指设计中允许的尺寸或形状的变化范围,它可以反映出产品的质量水平和制造的可行性。
在设计过程中,合理的公差设置可以保证产品的相互配合和功能的正常运行。
而在制造过程中,准确的公差控制可以保证产品的质量稳定性和工艺可控性。
首先,让我们来了解一下CAD软件中的公差设置方法。
在大多数CAD软件中,公差可以通过在设计模型中设置尺寸界限来实现。
比如,在3D模型中,可以通过设定最大和最小尺寸值来定义公差范围。
这些尺寸值可以是绝对值,也可以是相对值。
另外,在CAD软件中,还可以通过设置公差带、公差链和公差堆等特定功能来实现更加精细的公差控制。
其次,公差分析是一个重要的工具,可以帮助工程师和设计师评估设计方案的可行性以及产品质量的稳定性。
公差分析可以通过模拟产品在公差条件下的装配和使用情况,来评估其性能和可靠性。
在CAD软件中,常用的公差分析方法包括结构约束分析、位姿公差分析和公差传递分析等。
结构约束分析主要用于评估装配过程中的零部件间的相对位置和约束是否满足设计要求。
通过该分析方法,可以检查设计模型中各个零件之间的配合情况和公差是否合理。
位姿公差分析则主要用于评估产品在使用过程中的运动和位置变化是否满足设计要求。
该方法可以通过模拟产品在不同位置和运动状态下的变形和变化情况,来预测设计的可行性。
公差传递分析则主要用于评估公差在装配过程中的传递路径和效果。
通过该分析方法,可以确定公差来源和主要传递路径,并找出最敏感的公差链。
在进行公差分析时,需要注意一些技巧和要点。
首先,公差分析的准确性和可靠性取决于模型的准确性和复杂程度。
因此,在进行公差分析之前,需要确保模型的几何结构和尺寸是完整和准确的。
其次,为了提高公差分析的效率和精确度,可以使用一些特定的公差分析工具和软件插件。
这些工具和插件可以帮助自动化公差计算和分析过程,并提供更加直观和详细的分析结果。
DFSS及公差设计与分析(2013-6)

Reliability Analysis of Accelerated Life Test Data
对于机构工程师来说,phase 3的 优化设计及公差设计分析乃是DFSS 的核心。
知道Part1、 Part2 、 Part3的公差,如何确认组装之后的总公差? 知道Part1、 Part2 、 Part3、 Part4的公差,如何设定Gap, 并且得知不出现干涉的概率达到预设的σ水平? 反之,如果给定Gap, 如何合理的给各Part分配公差?
DFSS适用于任何行业、任何产品或流程的设计。利用DFSS,产品的设计、生产以及投放市场具有更强的可靠性和更高的性价比。
“DFSS” Vs “早期的6σ方法 ”
DFSS: A Process + Methods & Tools
PROlaunch NPD
1: Gather Voice of Customer (VoC)
4: Identify Potential Risks
7: Determine Tolerances
Statistical Tolerancing / Allocation
Audit / FRACAS
9: Launch Robust Product aligned with VoC
Trade-off Matrix / Pugh Concept
5: Find Critical Parameters and quantify their impact on CTQs via transfer functions
Science / Engineering Equations
二、公差分析的方法(RSS)
定义:对各零件公差的平方求和,再开方。假设各零件的公差都符合正太分布,那么,累积公差也会是正太分布。 RSS的特征: 累积公差的计算: 尺寸链为线性的 各尺寸为正态分布 更适用于尺寸的数量≥4 允许不良率存在,故,比Worst-Case更能符合实际
公差数据处理与分析技巧

公差数据处理与分析技巧公差数据处理与分析技巧公差是指在制造过程中,由于各种原因造成的产品尺寸、形状、位置等方面的偏差。
准确地处理和分析公差数据对于确保产品质量和满足设计要求至关重要。
下面将介绍一些公差数据处理与分析的技巧。
首先,对于公差数据的处理,我们需要进行数据的收集和整理。
在制造过程中,我们需要收集每个产品的测量数据,包括尺寸、形状、位置等方面的数据。
这些数据需要按照一定的规范进行整理和记录,以便后续的分析和处理。
其次,我们需要对公差数据进行统计和分析。
统计分析能够帮助我们了解产品的制造过程中存在的问题,并找到解决问题的方法。
常用的统计分析方法包括均值、标准差、概率分布等。
通过对公差数据的统计分析,我们可以了解产品的尺寸偏差的分布情况,以及存在的异常情况。
此外,我们还需要进行公差数据的可视化处理。
可视化处理可以帮助我们更直观地了解公差数据的分布情况和变化趋势。
常用的可视化处理方法包括绘制直方图、散点图、箱线图等。
通过对公差数据的可视化处理,我们可以更加清楚地了解产品的尺寸偏差的分布情况,以及存在的异常情况。
最后,我们需要对公差数据进行合理的解释和应用。
在处理和分析公差数据的过程中,我们需要根据产品的设计要求和使用环境,对公差数据进行合理的解释。
通过合理解释公差数据,我们可以为产品的制造过程提供合理的指导和改进措施。
综上所述,公差数据处理与分析技巧对于确保产品质量和满足设计要求至关重要。
通过对公差数据的收集、整理、统计、分析和可视化处理,我们可以更好地了解产品的尺寸偏差情况,为产品的制造过程提供合理的指导和改进措施。
公差数据处理与分析技巧不仅可以提高产品的质量,还可以提高制造效率,降低成本,提升企业的竞争力。
实用的CAD软件中的尺寸标注与公差分析技巧

实用的CAD软件中的尺寸标注与公差分析技巧CAD(计算机辅助设计)软件是现今工程设计领域中必不可少的工具。
它可以提高设计师的工作效率,减少错误,并且提供更准确的设计结果。
在CAD软件中,尺寸标注与公差分析是设计过程中非常重要的组成部分。
在本文中,我们将探讨一些实用的CAD软件中的尺寸标注与公差分析的技巧。
首先,让我们来看看尺寸标注技巧。
在CAD软件中,准确地标注尺寸是设计的关键之一。
正确标注尺寸可以确保制造过程中的精确度,并且有助于相应部件的装配。
以下是几个实用的尺寸标注技巧:1. 使用符号:在CAD软件中,可以使用不同的符号来表示不同的尺寸类型。
例如,直径可以用一个圆圈表示,而长度可以用一条直线表示。
正确使用这些符号可以有效地传递设计意图。
2. 标注尺寸链:当几个尺寸相互关联时,可以使用尺寸链来标注它们。
这样,设计师和加工人员就能更好地理解它们之间的关系。
3. 使用文字注释:在尺寸标注中,文字注释是非常重要的。
可以使用文字注释来提供更多的说明,例如表面质量要求、公差限制等。
确保文字清晰易懂,并将其正确放置在合适的位置。
接下来,我们将讨论公差分析技巧。
公差分析是确保设计符合制造要求的关键。
以下是几个实用的公差分析技巧:1. 理解公差类型:在CAD软件中,有几种不同类型的公差,如线性公差、角度公差和表面公差等。
了解每种类型的公差以及如何应用它们是非常重要的。
2. 使用公差带:公差带是用于限制尺寸范围的一种工具。
在CAD软件中,可以使用公差带来表示一个特定尺寸的允许偏差范围。
这有助于设计师和制造人员更好地理解尺寸的接受范围。
3. 公差堆叠分析:在复杂的装配设计中,公差堆叠分析非常有用。
它可以帮助预测各个零件之间的偏差对整体装配的影响。
CAD软件提供了一些工具来进行公差堆叠分析,包括Monte Carlo模拟和统计分析等。
综上所述,尺寸标注与公差分析是CAD软件中不可或缺的技巧。
通过准确地标注尺寸和进行合理的公差分析,设计师可以提供更精确、准确的设计结果,并且确保设计符合制造要求。
公差分析培训

公差分析表格
1. 2. 3. 4. 5. 6. 7. 8. 9.
项目名称
公差分析人员及日期
公差分析对象的草图 指定分析零件的图纸号及版本号,将尺寸链做好标签
对应尺寸链标签输入名义尺寸及公差
显示输出结果,包含极值法结果与RSS法结果 得出结论
根据结果需要进一步的工作
如果是一个复杂分析,有多个分析表,最好编辑一个封面
公差分析-概率法
因为公差处理的是变量,很自然的可以想到使用概 率的方法考虑公差分析 这里主要考虑三种概率方法: 均方根法(RSS法) 经典概率法 蒙特卡洛法
11
Amperex Technology Limited
ATL Confidential Surpassing customer’s expectation
公差分析-概率法-RSS法
RSS法使用两个假定:
每个特征变化符合正态分布
特征变化相互独立
那么,总体标准差Байду номын сангаас计算如下
假定公差为3倍标准差,则总体公差
13
Amperex Technology Limited
ATL Confidential Surpassing customer’s expectation
22
Amperex Technology Limited
ATL Confidential Surpassing customer’s expectation
总结
公差分析是产品设计一个关键部分,在设计阶段好的公差 分析能避免一些可能出现的问题及客户的投诉。 概率的方法能提供额外的公差给制造,从而降低成本。但 是必须小心存在的风险 好的分析步骤是成功的重要因素
公差分析的方法与比较

公差分析的方法與比較PSBU-RDD4-MDD 工程師朱誠璞 alex.chu@2002/11/14 PM 04:32 version 1.1A.公差分析的傳統方法( I)----Worst Case 法首先,必須解釋在公差分析時所用的兩種方法: 公差合成與公差分配.而在以下兩個例子中用來運算公差範圍的數學方法為 Worst Case 法,這是傳統的做法 :1.公差的合成(使用Worst Case 法運算)Part A 與 Part B 必須接合在一起,合成後的尺寸與公差範圍會是如何呢?在這個例子中,可以得到一個很直觀的結果------當Part A 與 Part B相接後所得到的 Part A+B 長度和公差範圍都是Part A + Part B 的結果.也就是說:合成後的公差範圍會包括到每個零件的最極端尺寸,無論每個零件的尺寸在其公差範圍內如何變化,都會 100% 落入合成後的公差範圍內.聽起來相當合理,不是嗎?稍後會解釋這樣做的缺點.2.公差的分配(使用Worst Case 法運算)現在 Part A+B 必須放入 Part C 的開口處,而開口的尺寸與公差如圖所示,那麼 Part A 與 B 的分別的公差範圍又應該是多少呢?我們以最簡單的方法 : 平均分配給其中所有的零件,所以 Part A 與 B 各得50 %,當然也可以按照其他的比例來調整,並沒有絕對的優劣之分.B. Worst Case法的問題1.控制公差範圍難以被控制在設計的需求範圍中.由於 Worst Case 法合成時要求100 % 的可以容許單一零件的公差變化,會造成合成後的公差範圍變的較大,對設計者而言,是非常容易造成零件組裝後相互干涉或間隙過大.在以上的例子中,如果要將 Part A+B 放入 Part C 時,會發生過緊干涉的情況,因為 Part C 最窄只有 10.75 mm,但是 Part A+B 卻可能有 11.50 mm的情況則有 0.75 mm 的干涉;另一方面,當 Part C 最寬11.25 mm,而 Part A+B 為10.5 mm 的最小值時,又有 0.75 mm的間隙產生.由此可知公差範圍過大所造成的難以控制的缺點.2.決定公差範圍的過程缺乏客觀及合邏輯的程序以此類方式決定的公差範圍尺寸,必須仰賴設計者的經驗,且必須經過多次的試作才可真正決定;若生產條件改變:如更換生產廠商,模具修改…等,皆有可能使原訂之公差範圍無法達成,而被迫放寬或產生大量不良品的損失.3.公差範圍與產品生產的品質水準無關對生產者而言,公差範圍越大越容易生產,同時品質要求也較低;但對設計者而言,公差範圍給定越大,品質水準低,則越難達成功能上的需求;由於此種矛盾的情況無法以此方式解決,造成設計者與生產者的衝突.C.其他的公差分析方法 ---基礎知識由於上述的缺點,使得Worst Case法只能被視為一種粗略的近似方法;以下將介紹兩種較接近真實世界的公差分析方法,但是,我們必須先有一些基礎知識才能瞭解這些方法的運作方式.1.何謂不可調整的公差範圍?在做任何的公差分析前,必須清楚的定義哪些是可由設計者調整的,而哪些又不是;在這裡,我們認為只有兩種是不可以被更改的:a.機械上的製造公差範圍:例如各種工具機的精度不同,如果以CNC加工的精度來要求鈑金零件,則勢必吃力不討好.b.客戶或規範上要求的公差範圍例如1U rack mount 機殼的高度,ATX主機板的孔位;特別是有相容性問題發生時.2.何謂常態分佈曲線?我們以一個簡單的例子說明:在一群人中身高與人數的分佈情況.簡單的說,就是中等身材的人應該最多,很高或很矮的人很少;在統計學中會利用這條曲線來模擬真實的情況並藉此進行下一步的分析,當我們在對於工廠所生產出來的一批產品,測量相同的一個尺寸,我們也會得到類似的分佈曲線;例如量測1000件長度為10mm的零件,正常狀況下一定會得到長度為10 mm的零件數目最多;而長度是20 mm或 1 mm 的零件出現的機會應該是微乎其微.在數學定義上,只要知道兩個條件就可以畫出這條曲線,如圖所示:在未來的討論中我們會利用下面的兩項特性進行分析:a.中間值 µ :曲線的對稱軸的位置,這決定了整條曲線的位置b.標準差σ :由中間值到曲線的曲率正負號改變點的距離,這決定了曲線的分散或集中程度.這些特性的來源,其實就是在微積分中,以此曲線的方程式求導數為0所得的解(參照附錄A的說明),有興趣的人可以到這個網頁進一步了解: /CE597N/1997F/students/michael.a.kropins ki.1/project/tutorial3.何謂 “6-σ” ?在我們運用常態分佈曲線來模擬並分析真實的情況時,如果我們加入上限及下限,且運用於品質管制的領域時,而被提出的一種品質水準的規範: “在一批生產出來的產品中,如其允收上限與下限的範圍是其常態分佈曲線σ的6倍,則可確保有 99.9999998 % 的產品是合格的.” 此種方式稱為 6-σ的品質水準要求,如下圖,這是一個簡單的表示方法 :D. 傳統的公差分析方法 ( II )---統計公差分析法我們一樣使用合成與分配的兩個例子來解釋:1.合成:我們一樣用前面所提的例子來看,現在實際上我們要做的是如何疊加這兩條曲線:毫無疑問的,疊加以後,我們還是會得到一條類似的曲線,但是疊加後的上下限應該在那裡??由常態分佈曲線的數學特性(參照附錄A的說明),我們有一個很方便的數學式:Tasm = √(T12+ T22+ T32+ T42+…….) T 代表上限或下限的公差, 所以結果是 :Tasm = √( 0.22+0.32) = 0.36055128... ~ 0.361我們可以知道合成後的情況應該是: 11+/- 0.361 mm.2.分配:同樣道理,用於分配時,可以得到的結果之一:Tasm = 0.25 = √(T12+ T22) Æ T1 = T2= 0.176776695…~ 0.177 也就是說: Part A = 5 +/- 0.177Part B =6 +/- 0.177E.比較兩種傳統公差分析的問題與改善方法:首先我們比較 Worst case 與統計公差法所得的結果:第一,我們可以看出公差合成後所得的公差範圍明顯縮小了,對設計者而言,較小的公差範圍意味著較準確的組裝與配合,所以累積下來的誤差也會減少,可以得到較佳的設計.第二,在公差分配的情況時,每個零件所得到的公差範圍變大了,對製造者而言,較大的公差範圍意味著較容易製作及控制生產品質,十分有利於製造者.所以,統計公差法顯然優於 Worst Case 法,但是是否完全解決了問題呢?答案是“ NO “,統計公差仍然會發生相同的問題,由其是在疊加或分析的零件很多時,請參照附錄C所提的例子,我們依舊需要進行Try and Error 的過程,以求得設計和製造上的平衡點;在這篇文章中利用加入 weight factor的方法修改原有公差以其放大或縮小原有公差範圍來達成設計及製造的需求.另一方面,統計公差法,仍然無法與實際生產的品質有任何關聯,所以仍舊會發生,同樣的公差範圍下,甲廠商可以達成,乙廠商卻叫苦連天的情況.F.新的公差分析方法( I )---加入 6-σ概念的統計公差分析法為了修正上一節所提到的問題,我們導入 6-σ品質水準的概念進入公差分析的過程中,這樣可以取得一個在理論(設計者)與實際(生產者)都可接受的一個平衡點.首先我們必須加入一個條件: 就是生產者的品質水準是滿足 6-σ的要求.(如果不滿足就不行嗎?當然不是,我們會在後面再檢討這個條件.)1.合成:仍舊是最早的例子,但是現在應該是這樣的分佈狀況,以滿足剛剛的加入條件:由上圖,可以得知 : T1= 0.2 = 6σ1 Æσ1 =0.2/6 =0.03333…~0.03333T2=0.3 =6σ2 Æσ2 = 0.3/6 = 0.05為什麼要求個別零件的σ值呢? 因為對於一個疊加後的常態分佈曲線而言,它的σ值與個別零件的σ值正好有以下的關係(參照附錄A的說明):σasm = √(σ12+σ22+σ32+σ42+….)所以我們可以得到合成後的σ值:σasm =√( 0.033332 + 0.052) = 0.06007….~0.06007請注意,合成後的依然要遵守6-σ品質水準的概念,所以:Tasm = 6σasm = 6 x 0.06007 = 0.36042合成後的情況應該是: 11+/- 0.36042 mm.2.分配:同樣的方法,公差分配時,得到的結果:Tasm = 0.25 = 6σasmσasm =0.041666~0.04167 =√(σ12+σ22) Æσ1 =σ2= 0.02946… ~ 0.0295T1=T2= 6 x 0.0295 = 0.177也就是說: Part A = 5 +/- 0.177Part B =6 +/- 0.177G..兩種統計公差方法的比較:我們會馬上發現兩種方法的結果是完全相同的!也就是說在使用統計方式計算的公差範圍是事實上,就是完全要求生產者的品質水準是符合 6-σ的結果,那麼使用新方法又有什麼優點呢?其實在工廠端要求的品質水準並非完全都是要到 6-σ如此之高的地步,以Sun Microsystem 為例,在模具驗收時,成品的製程水準至少需要Cpk = 1.33,也就是說大約是 4-σ ,( 我們會在下一節中解釋 Cpk的意義,以及對我們的影響)而使用新方法,設計者可以自由的調整所需要的品質水準,並且反映到公差範圍之中,而達到一個生產者與設計者都可以接受的平衡點,以下就是調整過的例子:生產 part A 的廠商有 4-σ的品質水準,所以:T1= 0.2 = 4σ1 Æσ1 =0.2/4 =0.05生產 part B 的廠商仍為 6-σ的品質水準,所以:T2=0.3 =6σ2 Æσ2 = 0.3/6 = 0.05所以我們可以得到合成後的σ值:σasm =√( 0.052 + 0.052) = 0.0707…~0.0707組裝時的品質水準要達到 6-σ :Tasm = 6σasm = 6 x 0.0707= 0.4242所以合成後的設計尺寸與公差應為: 11 +/- 0.4242在這裡隱藏了一個很重要的觀念: 以統計和 6-σ的方法應用於公差範圍的決定,可使設計者( RD ) 與品管 (QC) 使用相同的標準與語言去解決生產的問題,以上面的例子而言,當生產 part A 的廠商只有4-σ的生產水準時, σ值會變大則組裝後的公差範圍就應隨之變大;反過來說,當廠商生產品質高時, σ值會變小,我們就會獲得組裝後較小的公差變化範圍,這與品管人員的努力方向是一致的,且設計者也可以確知自己的設計是否會過嚴苛或過於寬鬆.此外使用此種方式具有相當大的彈性,可以針對不同的品質要求,而有不同的結果,而且一切都有理可循,不必完全倚靠經驗.H.新的公差分析方法( I )---完整的 6-σ公差分析法在前面所舉的例子中,我們所用的都是完美的常態分佈曲線,但是實際生產時我們所面對的卻不見得是如此理想的狀況:也就是說,分佈曲線的中心與設計者所定的中心存在一個偏移量 K,在這種狀況下我們要計算σ值,就必須藉由 Cp 和 Cpk (製程能力指標)來做轉換:Cp的定義:Cpk的定義:一般實務上,品管人員都會掌握Cp或 Cpk 值的變化,藉以評估生產的品質差異,所以在取得實際生產的品質資料時,得到Cp和 Cpk 值的機會較大且符合真正的情況.在這裡留個小小的問題: Cpk = 1.33 ,K=0時, part A 的σ值為何?而其餘的運算皆與上一節所提的相同,在這裡不再重覆計算.I.理論與實務----ADCATS Tolerance Spreadsheets以上所提到的理論基礎,全部來自於這個網頁: /home.html 這是美國猶他州( Utah ) Brigham Young University 機械工程學系的Dr. Ken Chase 所建立的,他發表過許多以電腦輔助做公差分析的論文, PTC( 參數科技)的 CE/Tol,是目前少數能做 3D公差分析的軟體,就是由這位教授的學生開發完成的,CE/Tol訓練教材的分析範例就是來自 Chase 教授的論文.在網頁中提供了一個 excel sheet, 就是實際運用上述理論的產物,請到這裡下載: CATS 1D Tolerance Stack-up :/WWW/ADCATS/software/實際上我們已運用於 Sun Microsystem 的 project 中,在機殼設計所碰到的問題中,1D的分析就幾乎可以含蓋全部的狀況;此外使用它的優點在於此 sheet並非由我們發展,而由客觀的第三者提供,我們不必花費太多精力與客戶溝通分析進行的理論,再者此sheet 免費,也無需軟體購買成本.J.附錄.A. 這些理論都應該在此附上證明,這部份將於最近完成.B. CATS 1D 的power point file.C. “Tolerance Allocation Methods for Designers” ADCATS Report No.99-6 Dr.Kenneth W. Chase 1999。
第4部分:公差分析指南

22
DFMA
谢 谢 !
23
3.当公差分析的结果不满足要求时:
DFMA
减少尺寸链的长度; A为54.00±0.20,C为25.00±0.15,D为28.50±0.15
优化的设计
18
四. 公差分析指南
3.当公差分析的结果不满足要求时:
DFMA
使用定位特征; 好处:
定位特征可以提供较精密的尺寸公差 定位特征的尺寸可以放置于比较容易进行尺寸管控的区域 使用定位特征时可以减少和避免对其他尺寸的公差要求,只需严格管控定 位特征的相关尺寸,就可以满足产品设计要求 因为定位特征精度高,使用定位特征有利于减少零件之间的尺寸公差累积
DFMA
制造工艺能力决定了公差分析中公差的设定; 二维图纸中公差标注与公差分析中的公差一致; 对公差分析中的尺寸需要进行制程管控;
制造工艺 能力
公差分析中 公差的设定
二维图样零 件公差标注
零件尺寸 制程管控
15
四. 公差分析指南
3.当公差分析的结果不满足要求时: 不推荐的做法:
DFMA
调整尺寸链中的尺寸公差大小; 降低目标尺寸判断标准;
100±0.20
3
一. 公差分析的介绍
2.公差的本质:
DFMA
公差是产品设计和产品制造的桥梁和纽带,是保证产品以优异的质量、 优良的性能和较低的成本进行制造的关键。
设计 功能 性能 外观 可装配性 设计限制 稳健性设计 设计意图 产品质量 客户满意
公差
制造 制造费用 装配费用 制造方法选择 机器 夹具 检验 不良率 返工率
推荐的做法:
减少尺寸链的长度; 使用定位特征;
公差分析常用方法

公差分析常用方法
公差分析是一种用于研究产品或系统各种要素之间相互连锁关系的方法。
它可用于确定导致产品或系统性能差异的主要因素,并寻找改进的机会。
下面是一些常用的公差分析方法:
1. 传递函数法:传递函数法是一种将产品或系统的总体公差在各个部件或要素上分配的方法。
通过将总体公差按照一定的比例分配给各个部件,以满足产品或系统性能的需求。
2. 采用最小二乘法(Least Square Method):最小二乘法是一种通过最小化观测值和理论值之间的差异平方和,来确定最接近真实值的方法。
在公差分析中,可以使用最小二乘法来评估产品或系统的总体公差和各个部件之间的关系。
3. 驱动因子公差分析(Driver Factor Analysis):驱动因子公差分析是一种通过识别产品或系统的主要性能驱动因子,来优化公差分配的方法。
通过将更多的公差分配给主要驱动因子,可以显著改善产品或系统的性能。
4. 公差优化:公差优化是一种通过最小化总体公差,以满足产品或系统性能要求的方法。
通过分析各个部件之间的相互关系,可以确定最佳的公差分配方案。
5. 敏感度分析:敏感度分析是一种评估产品或系统对公差变化的敏感程度的方法。
通过分析不同参数的变化对产品或系统性能的影响,可以确定哪些部件或要
素对总体公差的变化最为敏感。
以上是常用的公差分析方法,具体选择哪种方法取决于产品或系统的特点和分析目的。
公差分析
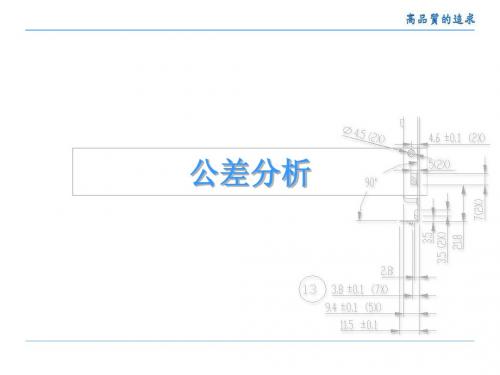
☆.产品设计变更的可行性评估. 产品设计变更的可行性评估.
设计变更后的组装性的检查,看部件的配合性. 设计变更后的组装性的检查,看部件的配合性.
BACK
公差分析--公差分析---做公差分析和方法和步骤 ★. 做公差分析方法和步骤
☆. 原始数据的收集. 原始数据的收集.
(规格,实际量测数据) 规格,实际量测数据)
BACK
公差分析--公差分析---为什么要做公差分析 ★.为什么要做公差分析
☆.组装性的检验
产品在设计阶段互换性的检验, 产品在设计阶段互换性的检验, 产品在设计阶段组装性的验证. 产品在设计阶段组装性的验证. 不同供应商制程的评估,A, 两家供应商分别搭配C家供应商的part. 不同供应商制程的评估,A,B两家供应商分别搭配C家供应商的part.
☆. 从设计上看其公差设计的合理性. 从设计上看其公差设计的合理性.
(剖面上进行上分析) 剖面上进行上分析)
☆. 实际量测数据上看,其进行验证 实际量测数据上看, (供应商实际制程能力的分析,Ca,Cpk.) 供应商实际制程能力的分析,Ca,Cpk.
BACK
公差分析--公差分析---实例说明 ★.公差分析实例说明
☆.Shielding Frame折弯角度从90设计变更性99的评估. Frame折弯角度从90设计变更性99的评估.
此设计变更的可行性评估,折弯角度变更后shielding Frame内空间能否容纳高度增加后的电容,干涉 此设计变更的可行性评估,折弯角度变更后shielding Frame内空间能否容纳高度增加后的电容,干涉 性的检查.
☆.互换性的作用: 互换性的作用:
互换性在机械或仪器制造中的作用是很大的. 从使用方面看,如人们经常使用的自行车和手表的零件,当它们损坏以后,修理人员很快就可以用同样规格的零件换上,恢复自 行车,手表和设备的功能. 从制造方面来看,装配时,不需辅助加工和修配,故能减轻装配工人的劳动强度,缩短装配周期,并且可使装配工人按流水作业 方式进行工作,以致进行自动装配,加工时,由於规定有公差,同一部机器上的各种零可以同时加工.用量大的标准件还可以由专门 车间基工厂单独生产.这样就可以采用高效率的专用设备,这样产量和质量必然会得到提高,成本也会显著降低. 从设计方面看,由於采用互换原则设计和生产标准零碎,部件,可以简化绘图,计算等工作,缩短设计周期.
公差分析及实际案例分享
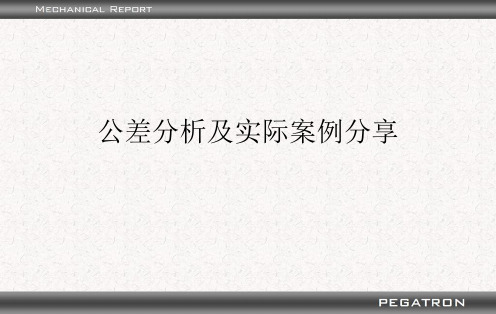
三. 公差分析目的、步骤、计算模型
1.目的: 1) 合理设定零件的公差以减少零件的制造成本。 2) 判断零件的可装配性,判断零件是否在装配过程中发生干涉。 3) 判断零件装配后产品关键尺寸是否满足外观、质量以及功能等要求。 4) 优化产品的设计,这是公差分析非常重要的一个目的。当通过公差分析发现产品设计
公差分析及实际案例分享
目录 一. 公差的定义和分类 二. 尺寸链 三. 公差分析目的、步骤、计算模型 四. 公差分析的工具 五. 案例
一. 公差的定义和分类
1. 公差定义: 零件的尺寸、形状以及其它参数都处在零件设计所规定的范围之内。这个范围通常称 为“公差”。就是实际参数值允许的最大变动量。 例如:10+/-0.5 mm, 公差:(+0.5)-(-0.5)=1mm
三. 公差分析目的、步骤、计算模型
2. 公差分析具体的步骤包括: 1) 定义公差分析的目标尺寸和判断标准。 2) 定义尺寸链。 3) 判断尺寸的正负。 4) 将非双向对称公差转化为双向对称公差。 5) 公差分析的计算。 6) 判断和优化。
3. 计算模型 常用的公差分析的计算模型有两种,一是极值法(WC),二是均方根法(RSS)。 1)极值法
不满足要求时,一般有两种方法来解决问题。其一是通过精密的零件公差来达到要求,但 这会增加零件的制造成本;好的方法,也是公差分析的意义所在。
5) 公差分析除了用于产品设计中,还可用于产品装配完成后,当产品的装配尺寸不符合 要求时,可以通过公差分析来分析制造和装配过程中出现的问题,寻找问题的根本原因。
极值法是考虑零件尺寸最不利的情况,通过尺寸链中尺寸的最大值或最小值来计算目标尺 寸的值。
2)均方根法 均方根法是统计分析法的一种,顾名思义,均方根法是把尺寸链中的各个尺寸公差的平方 之和再开根即得到目标尺寸的公差。
公差分析方法

Modified Root Sum Squares (MRSS)
普通的RSS仍然忽略了一個條件, 即廠商的制程能力可以達到的水準. 單方 面的從設計的角度來定義公差, 脫離了實際制程方面的限定. 所以為了解決這個問題, 我們引入 MRSS的概念. 我們假設廠商可以達到6sigma的制程能力.
公差分析方法
Chaos
分析方法分類
一般來講, 我們常用的公差定義與分析方法可 以分為以下幾種:
1. Worst case 2. RSS 3. MRSS 4. 6 σ
Worst case
此為最傳統的公差分析法. 其中涉及到兩個概念, 公差的合成與公差的分配. 公差的合成說明如下:
Worst case
我们假设组装的制程为6 σ, Part A的廠商只能達到4 σ, Part B的廠商可以達 到6 σ; 亦即 σ1 = 1.5σ2 那么分解之后 對于Part A來講, T=4 σ1=0.208, 對于Part B來講, T=6 σ2=0.204, 由此可見, 制程能力較低的廠商需要更加嚴格的管制其尺寸.
Root Sum Squares (RSS)
通過兩種方法的介紹, 我們可以看出來兩種方法的優缺點:
1.對于公差帶合成, 我們使用RSS方法合成時候的公差要比WC的時候要小. 這樣就意味著有較準確的組裝與配合.
2.對于公差的分解, 我們使用RSS方法, 分解出來的零件公差要比WC法要大. 這樣既意味著, 對于制造者來說, 零件可以變動的范圍大, 更有利于生產.
2. 公差定義過于理論化, 缺乏客觀實際的程序.
以此類方式決定的公差範圍尺寸,必須仰賴設計者的經驗,且必須經過多次的試作 才可真正決定;若生產條件改變:如更換生產廠商,模具修改…等,皆有可能使原訂之公差範 圍無法達成,而被迫放寬或產生大量不良品的損失.
公差分析

公差分析公差分析是一种在制造工程中广泛应用的质量管理方法,用于评估和控制制造过程中的偏差。
通过对产品尺寸、形状和位置的精确测量和分析,可以确定公差限度,以确保产品符合设计要求,并满足客户的期望。
公差分析的目标是确保产品的质量并提高制造过程的效率。
它通过确定关键尺寸和公差限度来控制制造过程中的变异性。
通过合理地设置公差,可以控制产品的尺寸、形状和功能,以便在设计要求范围内实现一致性和可靠性。
公差分析的基本原理是测量和分析产品的功能和特征,并将其与设计要求进行比较。
通过收集和分析数据,可以确定制造过程中的变异性,并采取适当的控制措施来减少这种变异性。
公差分析不仅关注产品的几何形状,还关注产品的功能特性,如运动性能、耐用性和可靠性。
在公差分析中,常用的工具是公差堆积分析。
公差堆积分析是一种确定不同部件公差对整个装配体的影响的方法。
它通过在CAD软件中建立装配模型,然后进行虚拟装配和公差仿真来模拟装配过程中的公差堆积。
通过分析装配体的公差堆积情况,可以确定适当的公差限度,以确保装配体的功能和性能。
公差堆积分析还可以帮助设计人员优化产品设计,以减少公差堆积对产品功能和性能的影响。
通过合理地设计产品尺寸和公差分配方案,可以最大程度地减少装配过程中的公差堆积效应。
除了公差堆积分析,公差分析还可以使用其他工具和方法来评估制造过程中的公差。
例如,公差链分析是一种用于确定不同生产过程对产品公差的贡献的方法。
通过分析制造过程中不同环节的公差,可以了解每个环节对最终产品质量的影响,并采取相应的改进措施。
公差分析在实际制造中发挥着重要作用。
它可以帮助制造商减少产品缺陷和不合格品的数量,提高产品质量和客户满意度。
公差分析还可以帮助制造商优化生产过程,减少生产成本并提高生产效率。
总之,公差分析是一种基于测量和分析的质量管理方法,用于评估和控制制造过程中的偏差。
通过合理地设置公差限度,可以确保产品符合设计要求,并满足客户的期望。
第4部分:公差分析
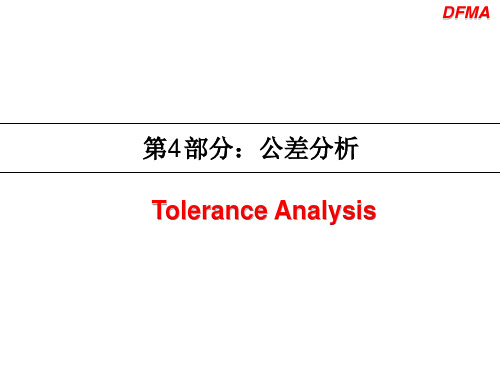
五. 公差分析的三大原则
3.当公差分析的结果不满足要求时: 不推荐的做法:
调整尺寸链中的尺寸公差大小; 增加关键尺寸的公差;
推荐的做法:
调整尺寸链中的尺寸大小 减少尺寸链的长度; 使用定位特征;
DFMA
28
五. 公差分析的三大原则
3.当公差分析的结果不满足要求时:
调整尺寸链中的尺寸大小;
?????合理设定零件的公差以减少零件的制造成本判断零件的可装配性判断零件是否在装配过程中发生干涉判断零件装配后产品关键尺寸是否满足外观质量以及功能等要求预测产品不良率当产品的装配尺寸不符合要求时可以通过公差分析来分析制造和装配过程中出现的问题寻找问题的根本原因优化产品的设计这是公差分析非常重要的一个目的22?三
15
三. 公差分析的步骤
1.定义公差分析的关键尺寸及其公差:
零件的装配间隙 外观零件的配合间隙 零件之间的功能、性能和可靠性等配合尺寸
DFMA
16
三. 公差分析的步骤
DFMA
2.定义尺寸链:
尺寸链,是指在产品的装配关系中,由互相联系的尺寸按一定顺序首尾 相接排列而成的封闭尺寸组
尺寸链两大特点:一是封闭性,尺寸链是由多个尺寸首尾相连;二是关 联性,组成尺寸链的每个尺寸都与关键尺寸有关联性,尺寸链中每个尺 寸的精度会影响到关键尺寸的精度
使用点或线与平面配合的方式代替平面与平面的配合方式,避免平面的 变形或者平面较高的粗糙度阻碍零件的顺利运动,从而可以对零件的平 面度和粗糙度允许宽松的公差
原始的设计
优化的设计
14
二. 公差分析
DFMA
4.公差分析的概念:
公差分析是指在满足产品功能、性能、外观和可装配性等要求的前提下, 合理定义和分配零件和产品的公差,优化产品设计,以最小的成本和最 高的质量制造产品
第4部分:公差分析指南

计算: 计算X的名义值:(方法与极值法相同) DX = 0.50 毫米 计算X的公差
2 TX = TA2 + TB2 + TC2 + TD + TE2
= 0.20 2 + 0.10 2 + 0.10 2 + 0.15 2 + 0.10 2 = 0.04 + 0.01 + 0.01 + 0.0225 + 0.01 = 0.0925 = 0.30
X=0.5±0.30
13
四. 公差分析指南
1.公差分析应当从哪里开始?
定义产品规格 概念设计 材料和工艺选择 成本分析 DFMA设计 DFMA讨论 样品制作 产品制造 DFMA
DFMA
公差分析应当 从概念设计阶段开始
产品装配 测试 小批量试产 量产
14
四. 公差分析指南
2.公差的一致性
推荐的做法:
减少尺寸链的长度; 使用定位特征;
16
四. 公差分析指南
3.当公差分析的结果不满足要求时:
DFMA
减少尺寸链的长度; A为54.00±0.20,B为12.00±0.10,C为13.00±0.10,D为 16.00±0.15,E为12.50±0.10
原始的设计
17
四. 公差分析指南
DFMA
极值法:极值法是考虑零件尺寸最不利的情况,通过尺寸链中尺寸的最大值 或最小值来计算目标尺寸的值 均方根法:均方根法是统计分析法的一种,是把尺寸链中的各个尺寸公差的 平方之和再开根即得到目标尺寸的公差
10
三. 公差分析的计算方法
1.计算方法:
计算方法 计算公式 1. 不可能性;
公差分析方法范文
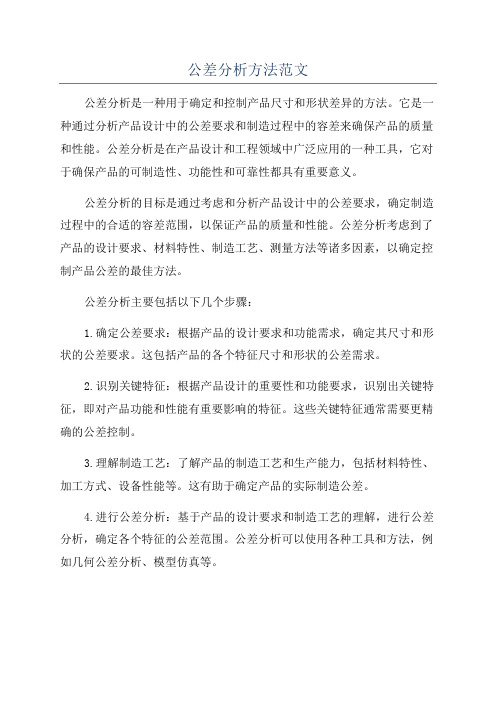
公差分析方法范文公差分析是一种用于确定和控制产品尺寸和形状差异的方法。
它是一种通过分析产品设计中的公差要求和制造过程中的容差来确保产品的质量和性能。
公差分析是在产品设计和工程领域中广泛应用的一种工具,它对于确保产品的可制造性、功能性和可靠性都具有重要意义。
公差分析的目标是通过考虑和分析产品设计中的公差要求,确定制造过程中的合适的容差范围,以保证产品的质量和性能。
公差分析考虑到了产品的设计要求、材料特性、制造工艺、测量方法等诸多因素,以确定控制产品公差的最佳方法。
公差分析主要包括以下几个步骤:1.确定公差要求:根据产品的设计要求和功能需求,确定其尺寸和形状的公差要求。
这包括产品的各个特征尺寸和形状的公差需求。
2.识别关键特征:根据产品设计的重要性和功能要求,识别出关键特征,即对产品功能和性能有重要影响的特征。
这些关键特征通常需要更精确的公差控制。
3.理解制造工艺:了解产品的制造工艺和生产能力,包括材料特性、加工方式、设备性能等。
这有助于确定产品的实际制造公差。
4.进行公差分析:基于产品的设计要求和制造工艺的理解,进行公差分析,确定各个特征的公差范围。
公差分析可以使用各种工具和方法,例如几何公差分析、模型仿真等。
5.优化设计方案:通过公差分析,确定产品的公差控制方案,并优化设计,以提高产品的可制造性和性能。
这可能需要权衡各种设计要求和制造约束。
6.公差管理和控制:制定公差管理和控制计划,确保产品在制造过程中能够控制公差在要求范围内。
这包括对制造过程中各个环节的控制和监测。
公差分析的优势在于它能够帮助设计人员和工程师在产品设计过程中充分考虑到公差要求和制造工艺的限制,以确保产品的一致性和可靠性。
通过合理的公差分析,可以减少产品的尺寸和形状差异,提高产品的质量,降低制造成本。
然而,公差分析也存在一些挑战和限制。
首先,公差分析需要准确的产品设计和制造数据,以及对制造工艺和测量方法的全面了解。
其次,公差分析涉及到多个不确定因素,如材料和设备性能的变化,这可能导致公差分析的结果不准确。