软包锂电池胀气的原因分析
软包装锂离子电池产气机理研究和预测

软包装锂离子电池产气机理研究和预测近年来,随着先进技术在新能源产业发展中的应用,研究者们开始将重点放在软包装锂离子电池上,这种电池拥有海量的能量容量,而且成本低。
但是在实际使用中,由于缺乏充分的安全保护,软包装锂离子电池很容易发生破裂、发气等情况,甚至可能造成火灾爆炸事故。
因此,研究新软包装锂离子电池的产气机理是非常关键的,也将为此类电池的安全预防和应用提供重要参考。
首先要研究的是软包装锂离子电池的结构特性及其对产气的影响。
软包装锂离子电池通常由电极、电解液和膜组成,电极可以将原料供电,膜结构则具有调节电解液移动和离子替代的作用。
当电池进入充电状态时,电极及其间的电解液将发生变化,例如电流密度和电压等,从而导致电极及其间的电解液本身应力增大,从而引发破裂和产气。
为此,研究者们可以计算电极间的电解液流动情况和离子交换,以及电流的流动、电压的变化和发热情况,从而深入研究软包装锂离子电池产气的机理。
另外,研究者们可以通过实验和分析来研究软包装锂离子电池产气的机理。
实验可以采用不同的电极结构、不同的膜材料和不同的电解液,在不同的电流密度和电压下,以及各种温度和湿度的条件下,进行充放电实验,了解软包装锂离子电池的可靠程度,并研究膜在电活性物质的移动和电解介质的变化等情况下的行为,从而解析出电解液流动的机理以及发生破裂、发气的原因。
最后,对于软包装锂离子电池产气的机理,研究者们可以采用数值模拟来预测和分析。
例如,可以采用计算流体力学和热力学模拟技术来模拟软包装锂离子电池内部的机理,用来模拟电解液流动和电流流动,评估电解液对电极的热影响,识别电极发热、破裂、发气及其影响因素,以及在各种温度和湿度条件下,电极间产气的位置、时间及强度等,从而建立完整的模型,来预测不同条件下软包装锂离子电池的产气情况。
综上所述,研究新软包装锂离子电池的产气机理对于该类电池的安全预防和应用来说是非常重要的,以及对于新能源的发展也是非常有必要的。
锂电软包电池气鼓、硬鼓原因!

软包锂电池胀气的原因聚合物锂离子电池芯採用的是铝塑複合膜的包装技术,当电池芯内部由于异常化学反应的发生而产生气体时,Pocket会被充起,电池芯鼓胀(有轻微鼓胀和严重鼓胀两种情况),且不论外观如何,电池芯的使用性能(Capacity、Cycle life、C-rate等)会发生严重的失效,导致电池芯不能使用。
胀气会发生在生产过程中也会在客户甚至最终用户手中。
当然,电池芯在化成启动或Baking过程中会正常的产生一定量(一般很少)的气体,这根据所使用的原材料而异,这种气体在Degassing工序会被抽掉。
目前部分Model(一次封装成型电池芯)通过添加V18溶剂来消除这种SEI层形成、相介面稳定时所产生的气体。
但是由于工序异常所产生的气体在Degassing前表面非常明显或者Degassing后产生不能再消掉或者添加V18也不能消除。
这里简要介绍工序异常产生气体的原因:1.封装不良,由封装不良所引起胀气电池芯的比例已经大大地降低。
前面已经介绍了引起Top sealing、Side sealing和Degassing三边封装不良的原因,任何一边封装不良都会导致电池芯,表现以Top sealing 和Degassing居多,Top sealing主要是Tab位密封不良,Degassing 主要是分层(包括受电解液和凝胶影响导致PP与Al脱离)。
封装不良引起空气中水分进入电池芯内部,引起电解液分解产生气体等。
2.Pocket表面破损,电池芯在流拉过程中,受到异常损坏或人为破环导致Pocket破损(如针孔)而使水分进入电池芯内部。
3.角位破损,由于折边角位铝的特殊变形,气袋晃动会扭曲角位导致Al破损(电池芯越大,气袋越大,越易破损),失去对水的阻隔作用。
可以在角位加皱纹胶或热熔胶缓解。
并且在顶封后的各工序禁止拿气袋移动电池芯,更要注意操作方式防止老化板上电芯池的摆动。
4.电池芯内部水含量超标,前面我们已经介绍过对电池芯内水含量有一定的要求,一旦水含量超标,电解液会失效在化成或Degassing后产生气体。
锂离子电池气胀问题探析

B01锂离子电池气胀问题探析许名飞+’1,郭永兴1,李新海1,吴显明2(1中南大学冶金科学与工程学院,长沙410083:2吉首大学化学与化工学院,吉首427000)摘要:随着应用领域不断扩大,锂离子电池发展迅速。
但控制电池气胀问题一直是电池制造的难点。
本史对锂离子电池气胀的原因进行了分析,并对如何解决电池的气胀问题进行了探讨。
关键词:锂离子电池气胀SE[膜目前锂离子电池发展迅速,已成为电池中生力军,但在实际生产中一直存在着气胀问题[1l。
电池气胀不但影响到锂离子电池的外观及其电化学性能,更为严重的是会引发安全性问题。
目前人们对于锂离子电池气胀产生的原因研究较少,至于其解决方法更是鲜见报道12】。
1电池气胀原因分析锂离子电池在初次化成时,由于层间化合物的自身原因,Lr在层问化合物中脱嵌和嵌入的反应速度慢”-』,不能以大电流充电,晟好以小电流(锄|2c)进行化成而且应是采取多次逐步化成。
但锂离子电池在首次化成,即首次充电过程中,电解液中的非质子溶剂会在电极与电解液界面上发生反应,这些反应一方面形成覆盖在电极表面上的钝化薄膜,称为电子绝缘膜或固体电解质相界面膜,即SEl膜,同时会产生如1-12、CH2=CH2、CH4、CO、C02等气体…j。
SEl膜的形成~方面消耗了电流中有限的锂离子,造成不可逆容量损失,同时也增加了电栅电解液界面的电阻,造成一定的电压滞后;而此过程中产生的气体导致电池内压升高,出现气胀问题,严重影响电池的性能(如电池的循环性能和电池的安全性能),同时还影响到电池的外观,特别是采用软包装的聚合物锂离子电池。
另外,锂离子电池在使用过程中,有时由于使用不当还存在过充过放问题,过充过放也可能产生气体,也会导致电池气胀。
所以控制锂离子电池在化成阶段雨】循环过程中气体的产生对电池的性能改善有巨大的作用。
锂离子电池中气体的产生主要集中在首次化成阶段,即SEI膜的形成过程中,在随后的循环过程中产生的气体相对较少,但如果首次充电过程中形成的SEI膜不够稳定,随着循环的进行负极材料可能脱落或变疏松,在电极的表面需重新形成SEl膜,这样便义会产生气体。
电池-软包锂离子电池鼓胀原因超全总结

电池-软包锂离子电池鼓胀原因超全总结电池| 软包锂离子电池鼓胀原因超全总结引起软包锂离子电池鼓胀的原因有很多。
根据实验研发经验,笔者将锂电池鼓胀的原因分为三类,一是电池极片在循环过程中膨胀导致的厚度增加;二是由于电解液氧化分解产气导致的鼓胀。
三是电池封装不严引进水分、角位破损等工艺缺陷引起的鼓胀。
在不同的电池体系中,电池厚度变化的主导因素不同,如在钛酸锂负极体系电池中,鼓胀的主要因素是气鼓;在石墨负极体系中,极片厚度和产气对电池的鼓胀均起到促进作用。
一、电极极片厚度变化石墨负极膨胀影响因素及机理讨论锂离子电池在充电过程中电芯厚度增加主要归结为负极的膨胀,正极膨胀率仅为2~4%,负极通常由石墨、粘接剂、导电碳组成,其中石墨材料本身的膨胀率达到~10%,造成石墨负极膨胀率变化的主要影响因素包括:SEI膜形成、荷电状态(state of charge,SOC)、工艺参数以及其他影响因素。
(1)SEI膜形成锂离子电池首次充放电过程中,电解液在石墨颗粒在固液相界面发生还原反应,形成一层覆盖于电极材料表面的钝化层(SEI 膜),SEI膜的产生使阳极厚度显著增加,而且由于SEI膜产生,导致电芯厚度增加约4%。
从长期循环过程看,根据不同石墨的物理结构和比表面,循环过程会发生SEI的溶解和新SEI生产的动态过程,比如片状石墨较球状石墨有更大的膨胀率。
(2)荷电状态电芯在循环过程中,石墨阳极体积膨胀与电芯SOC呈很好的周期性的函数关系,即随着锂离子在石墨中的不断嵌入(电芯SOC的提高)体积逐渐膨胀,当锂离子从石墨阳极脱出时,电芯SOC 逐渐减小,相应石墨阳极体积逐渐缩小。
(3)工艺参数从工艺参数方面看,压实密度对石墨阳极影响较大,极片冷压过程中,石墨阳极膜层中产生较大的压应力,这种应力在极片后续高温烘烤等工序很难完全释放。
电芯进行循环充放电时,由于锂离子的嵌入和脱出、电解液对粘接剂溶胀等多个因素共同作用,膜片应力在循环过程得到释放,膨胀率增大。
锂聚合物电池鼓包是什么原因导致的?

锂聚合物电池鼓包是什么原因导致的?锂聚合物电池鼓包的主要原因是锂离子电池内部电芯产生气体。
几乎所有锂离子电池在损坏时的第一个表现就是电池单元内部产生气体。
对于真空软包装的聚合物电芯,其表现就是电池膨胀,所以电池的膨胀也是对电芯损坏安全的预警。
既然如此,那锂聚合物电池鼓包是什么原因导致的呢?1、锂聚合物电池过充:如上所述,当电池电压超过4.2V时,会发生一系列化学反应产生气体。
如果电池长时间多次轻微过充,电池内的气体会逐渐聚集,导致电芯膨胀。
2、锂聚合物电池过度放电:当电池过度放电(电压<2.0V)并长期储存时,由于电池内部发生电解反应,阳极集电极的铜发生分解,并且电池内部产生气体。
3、对于锂聚合物电池在正常工作电压范围内产生的气体,在电池刚刚制作成时,我们会进行多次充放电循环,使电极表面形成复合堆积层,为保护极片以后不再参与充放电过程中的反应。
4、当锂聚合物电池包装材料的封口破损时,空气中的水分子会进入电池内部,也会造成电池内部严重膨胀。
5、锂聚合物电池厂商生产制作工艺问题:由于厂家众多,很多厂家为省成本,使得制作环境恶劣,使用将要淘汰设备机器等等,这样一来使得电池的涂层不均匀,电解液内混入了灰尘颗粒等。
这些都有可能使得锂电池包在用户使用时出现鼓包现象,甚至出现更大的危险。
6、锂聚合物电池长期不用且保存不恰当任何一种电池产品如果长期不用的话,原有的性能基本上都会下降,电池长期不使用,然后也没有进行较好的保存处理。
当其长期暴露于空气中不使用,并且电量充满。
由于空气在一定程度上是导电的,放的时间过长就相当于电池的正负极直接接触,进行了慢性的短路,一旦短路就会发热,一些电解质分解甚至气化,从而导致发生鼓包。
以上就是锂聚合物电池出现鼓包原因的介绍。
格瑞普小编在此提醒大家,锂聚合物电池鼓包是大问题的前兆,不建议再继续使用。
继续使用可能会出现短路、发热、冒烟、燃烧等难以想象的后果。
深度剖析锂离子电池鼓胀原因

深度剖析锂离子电池鼓胀原因锂离子电池由于具有高寿命、高容量被广泛推广使用,但是随着使用时间的延长,其存在鼓胀、安全性能不理想和循环衰减加快的问题也日益严重,引起了锂电界深度的分析和抑制研究。
根据实验研发经验,笔者将锂电池鼓胀的原因分为两类,一是电池极片的厚度变化导致的鼓胀;二是由于电解液氧化分解产气导致的鼓胀。
在不同的电池体系中,电池厚度变化的主导因素不同,如在钛酸锂负极体系电池中,鼓胀的主要因素是气鼓;在石墨负极体系中,极片厚度和产气对电池的鼓胀均起到促进作用。
一、电极极片厚度变化在锂电池使用过程中,电极极片厚度会发生一定的厚度变化,尤其是石墨负极。
据现有数据,锂电池经过高温存储和循环,容易发生鼓胀,厚度增长率约6%——20%,其中正极膨胀率仅为4%,负极膨胀率在20%以上。
锂电池极片厚度变大导致的鼓胀根本原因是受石墨的本质影响,负极石墨在嵌锂时形成LiCx(LiC24、LiC12和LiC6等),晶格间距变化,导致形成微观内应力,使负极产生膨胀。
下图是石墨负极极片在放置、充放电过程中的结构变化示意图。
石墨负极的膨胀主要是嵌锂后产生不可恢复膨胀导致的。
这部分膨胀主要与颗粒尺寸、粘接剂剂及极片的结构有关。
负极的膨胀造成卷芯变形,使电极与隔膜间形成空洞,负极颗粒形成微裂纹,固体电解质相界面(SEI)膜发生破裂与重组,消耗电解液,使循环性能变差。
影响负极极片变厚的因素有很多,粘接剂的性质和极片的结构参数是最重要的两个。
石墨负极常用的粘接剂是SBR,不同的粘接剂弹性模量、机械强度不同,对极片的厚度影响也不同。
极片涂布完成后的轧制力也影响负极极片在电池使用中的厚度。
在相同的应力下,粘接剂弹性模量越大,极片物理搁置反弹越小;充电时,由于Li+嵌入,使石墨晶格膨胀;同时,因负极颗粒及SBR的形变,内应力完全释放,使负极膨胀率急剧升高,SBR处于塑性变形阶段。
这部分膨胀率与SBR的弹性模量和断裂强度有关,导致SBR的弹性模量和断裂强度越大,造成不可逆的膨胀越小。
软包电池胀气原因

软包锂电池胀气的原因聚合物锂离子电池芯採用的是铝塑複合膜的包装技术,当电池芯内部由于异常化学反应的发生而产生气体时,Pocket会被充起,电池芯鼓胀(有轻微鼓胀和严重鼓胀两种情况),且不论外观如何,电池芯的使用性能(Capacity、Cycle life、C-rate等)会发生严重的失效,导致电池芯不能使用。
胀气会发生在生产过程中也会在客户甚至最终用户手中。
当然,电池芯在化成启动或Baking过程中会正常的产生一定量(一般很少)的气体,这根据所使用的原材料而异,这种气体在Degassing工序会被抽掉。
目前部分Model(一次封装成型电池芯)通过添加V18溶剂来消除这种SEI层形成、相介面稳定时所产生的气体。
但是由于工序异常所产生的气体在Degassing前表面非常明显或者Degassing后产生不能再消掉或者添加V18也不能消除。
这里简要介绍工序异常产生气体的原因:1、封装不良:由封装不良所引起胀气电池芯的比例已经大大地降低。
前面已经介绍了引起Top sealing、Side sealing和Degassing三边封装不良的原因,任何一边封装不良都会导致电池芯,表现以Top sealing 和Degassing居多,Top sealing主要是Tab位密封不良,Degassing 主要是分层(包括受电解液和凝胶影响导致PP与Al脱离)。
封装不良引起空气中水分进入电池芯内部,引起电解液分解产生气体等。
2、Pocket表面破损:电池芯在流拉过程中,受到异常损坏或人为破环导致Pocket破损(如针孔)而使水分进入电池芯内部。
3、角位破损:由于折边角位铝的特殊变形,气袋晃动会扭曲角位导致Al破损(电池芯越大,气袋越大,越易破损),失去对水的阻隔作用。
可以在角位加皱纹胶或热熔胶缓解。
并且在顶封后的各工序禁止拿气袋移动电池芯,更要注意操作方式防止老化板上电芯池的摆动。
4、电池芯内部水含量超标:前面我们已经介绍过对电池芯内水含量有一定的要求,一旦水含量超标,电解液会失效在化成或Degassing后产生气体。
软包电芯体积的膨胀行为

软包电芯体积的膨胀行为
软包电芯是一种广泛应用于电动汽车、移动电源等领域的重要电池组件,其具有体积小、重量轻、可塑性强等优点。
然而,在充放电过程中,由于电极内部嵌入的锂离子引起了化学反应,会导致电芯体积的膨胀行为。
软包电芯中的正负极电极材料都是由多种化学物质组成的复合材料。
在充放电过程中,锂离子从正极材料向负极材料扩散,同时电池内部化学反应也会产生气体。
这些因素会导致电芯内部的压力增加,从而引起电芯的膨胀。
软包电芯的膨胀程度与电池中的锂离子扩散速率、电解质浓度、电池温度等因素有关。
为了减小软包电芯的膨胀行为对电池组件和设备的影响,研究者们采取了多种措施。
其中一种常见的方法是使用锂离子扩散速率较快、容积膨胀率较小的电极材料;另外,加入抑制气体生成的添加剂、优化电解质组成、控制电池的温度等方法也被广泛应用。
软包电芯的膨胀行为对电池性能和使用寿命具有一定的影响,因此对于电池组件的设计和制造,需要充分考虑和控制电芯的膨胀行为。
同时,加强对软包电芯膨胀行为的研究和探索,可以为电池性能的提升和电池安全的保障提供重要的支持。
1/ 1。
软包装锂离子电池产气机理研究和预测

软包装锂离子电池产气机理研究和预测软包装锂离子电池是近年来发展迅速的新型电池技术,具有质量轻、能量密度高、成本低等突出优势。
然而,由于其中的高温副产物,它也带来了安全隐患。
重要的是,软包装锂离子电池在发生故障时可能会自燃,甚至发生爆炸,这为其产生的有毒气体和易燃物提出了挑战。
因此,深入了解软包装锂离子电池的产气机理,并研发有效的产气预报技术,是消除其存在的安全隐患和提供安全保障的重要手段。
本文在对软包装锂离子电池产气机理进行系统总结和研究的基础上,经过分析,总结出了软包装锂离子电池产气的主要机理。
其中包括外界热激活机理、流动电池机理、原位热反应机理、电池内受损机理、滞后热反应机理和正极材料聚合机理等。
此外,文章还根据软包装锂离子电池的特性,通过模型预测技术,针对软包装锂离子电池的产气行为进行了实验和试验,研究了电池产气的临界温度、可燃温度等参数,为设计新型软包装锂离子电池提供了有效的预测模型。
本文还对控制软包装锂离子电池产气的已有技术方法进行了深入分析。
例如,传统的防火保护技术,如温度感应器、烟雾检测器和阻燃材料,以及近期发展起来的新颖技术,如极化技术、可控发热技术、电解液监测技术、湿度控制技术等,分析了不同技术的有效性和可行性。
最后,本文对当前软包装锂离子电池产气机理研究和预测的发展方向提出了建议。
首先,结合当前电池设计、制造和管理技术,设计出新型软包装锂离子电池,以降低产气风险;其次,开展基于多物理场和多尺度的产气预测模型研究,以提高预测的准确性和可靠性;此外,还应加强技术创新,开发新的产气控制技术,以提高电池的安全性能。
本文从软包装锂离子电池的产气机理研究出发,全面剖析了软包装锂离子电池的安全性能研究,并阐述其中的有效的预测技术,为提高软包装锂离子电池的安全性能提供了有益的建议和指导。
当前,软包装锂离子电池安全性能研究仍然存在一定的局限性,有必要继续加强软包装锂离子电池安全性能研究,以期改善软包装锂离子电池的安全性能。
锂电池发鼓胀气和爆炸原因分析

锂电池发鼓胀气和爆炸原因分析standalone; self-contained; independent; self-governed;autocephalous; indie; absolute; unattached; substantive一、锂离子电池特性锂是化学周期表上直径最小也最活泼的金属。
体积小所以容量密度高,广受消费者与工程师欢迎。
但是,化学特性太活泼,则带来了极高的危险性。
锂金属暴露在空气中时,会与氧气产生激烈的氧化反应而爆炸。
为了提升安全性及电压,科学家们发明了用石墨及钴酸锂等材料来储存锂原子。
这些材料的分子结构,形成了奈米等级的细小储存格子,可用来储存锂原子。
这样一来,即使是电池外壳破裂,氧气进入,也会因氧分子太大,进不了这些细小的储存格,使得锂原子不会与氧气接触而避免爆炸。
锂离子电池的这种原理,使得人们在获得它高容量密度的同时,也达到安全的目的。
锂离子电池充电时,正极的锂原子会丧失电子,氧化为锂离子。
锂离子经由电解液游到负极去,进入负极的储存格,并获得一个电子,还原为锂原子。
放电时,整个程序倒过来。
为了防止电池的正负极直接碰触而短路,电池内会再加上一种拥有众多细孔的隔膜纸,来防止短路。
好的隔膜纸还可以在电池温度过高时,自动关闭细孔,让锂离子无法穿越,以自废武功,防止危险发生。
保护措施:锂电池电芯过充到电压高于后,会开始产生副作用。
过充电压愈高,危险性也跟着愈高。
锂电芯电压高于后,正极材料内剩下的锂原子数量不到一半,此时储存格常会垮掉,让电池容量产生永久性的下降。
如果继续充电,由于负极的储存格已经装满了锂原子,后续的锂金属会堆积于负极材料表面。
这些锂原子会由负极表面往锂离子来的方向长出树枝状结晶。
这些锂金属结晶会穿过隔膜纸,使正负极短路。
有时在短路发生前电池就先爆炸,这是因为在过充过程,电解液等材料会裂解产生气体,使得电池外壳或压力阀鼓涨破裂,让氧气进去与堆积在负极表面的锂原子反应,进而爆炸。
锂电池发鼓胀气和爆炸原因分析详细版
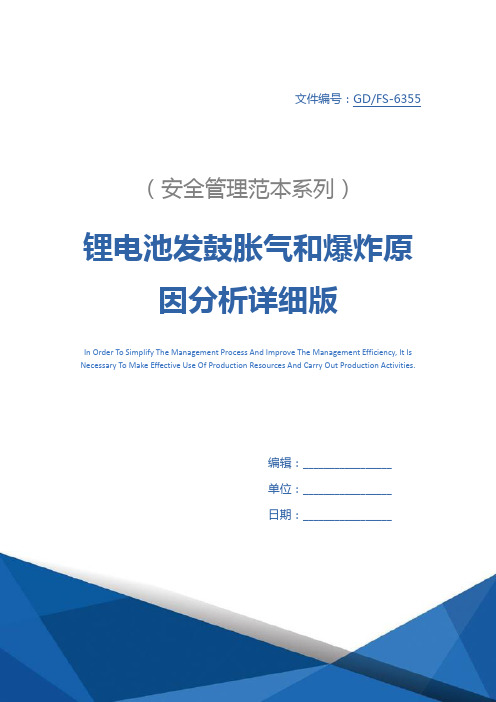
文件编号:GD/FS-6355(安全管理范本系列)锂电池发鼓胀气和爆炸原因分析详细版In Order To Simplify The Management Process And Improve The Management Efficiency, It Is Necessary To Make Effective Use Of Production Resources And Carry Out Production Activities.编辑:_________________单位:_________________日期:_________________锂电池发鼓胀气和爆炸原因分析详细版提示语:本安全管理文件适合使用于平时合理组织的生产过程中,有效利用生产资源,经济合理地进行生产活动,以达到实现简化管理过程,提高管理效率,实现预期的生产目标。
,文档所展示内容即为所得,可在下载完成后直接进行编辑。
一、锂离子电池特性锂是化学周期表上直径最小也最活泼的金属。
体积小所以容量密度高,广受消费者与工程师欢迎。
但是,化学特性太活泼,则带来了极高的危险性。
锂金属暴露在空气中时,会与氧气产生激烈的氧化反应而爆炸。
为了提升安全性及电压,科学家们发明了用石墨及钴酸锂等材料来储存锂原子。
这些材料的分子结构,形成了奈米等级的细小储存格子,可用来储存锂原子。
这样一来,即使是电池外壳破裂,氧气进入,也会因氧分子太大,进不了这些细小的储存格,使得锂原子不会与氧气接触而避免爆炸。
锂离子电池的这种原理,使得人们在获得它高容量密度的同时,也达到安全的目的。
锂离子电池充电时,正极的锂原子会丧失电子,氧化为锂离子。
锂离子经由电解液游到负极去,进入负极的储存格,并获得一个电子,还原为锂原子。
放电时,整个程序倒过来。
为了防止电池的正负极直接碰触而短路,电池内会再加上一种拥有众多细孔的隔膜纸,来防止短路。
好的隔膜纸还可以在电池温度过高时,自动关闭细孔,让锂离子无法穿越,以自废武功,防止危险发生。
电池 - 软包锂离子电池鼓胀原因超全总结

电池| 软包锂离子电池鼓胀原因超全总结引起软包锂离子电池鼓胀的原因有很多。
根据实验研发经验,笔者将锂电池鼓胀的原因分为三类,一是电池极片在循环过程中膨胀导致的厚度增加;二是由于电解液氧化分解产气导致的鼓胀。
三是电池封装不严引进水分、角位破损等工艺缺陷引起的鼓胀。
在不同的电池体系中,电池厚度变化的主导因素不同,如在钛酸锂负极体系电池中,鼓胀的主要因素是气鼓;在石墨负极体系中,极片厚度和产气对电池的鼓胀均起到促进作用。
一、电极极片厚度变化石墨负极膨胀影响因素及机理讨论锂离子电池在充电过程中电芯厚度增加主要归结为负极的膨胀,正极膨胀率仅为2~4%,负极通常由石墨、粘接剂、导电碳组成,其中石墨材料本身的膨胀率达到~10%,造成石墨负极膨胀率变化的主要影响因素包括:SEI膜形成、荷电状态(state of charge,SOC)、工艺参数以及其他影响因素。
(1)SEI膜形成锂离子电池首次充放电过程中,电解液在石墨颗粒在固液相界面发生还原反应,形成一层覆盖于电极材料表面的钝化层(SEI膜),SEI膜的产生使阳极厚度显著增加,而且由于SEI膜产生,导致电芯厚度增加约4%。
从长期循环过程看,根据不同石墨的物理结构和比表面,循环过程会发生SEI的溶解和新SEI生产的动态过程,比如片状石墨较球状石墨有更大的膨胀率。
(2)荷电状态电芯在循环过程中,石墨阳极体积膨胀与电芯SOC呈很好的周期性的函数关系,即随着锂离子在石墨中的不断嵌入(电芯SOC的提高)体积逐渐膨胀,当锂离子从石墨阳极脱出时,电芯SOC逐渐减小,相应石墨阳极体积逐渐缩小。
(3)工艺参数从工艺参数方面看,压实密度对石墨阳极影响较大,极片冷压过程中,石墨阳极膜层中产生较大的压应力,这种应力在极片后续高温烘烤等工序很难完全释放。
电芯进行循环充放电时,由于锂离子的嵌入和脱出、电解液对粘接剂溶胀等多个因素共同作用,膜片应力在循环过程得到释放,膨胀率增大。
另一方面,压实密度大小决定了阳极膜层空。
干货丨锂离子电池鼓胀分析

干货丨锂离子电池鼓胀分析来源:《电源技术》杂志锂离子电池具有能量密度高,体积小的优点[1],近年来,随着4G 的普及,5G的到来,对于锂离子电池的要求更加苛刻,锂离子电池朝着更高能量密度、更快的充电速度发展。
然而能量越高,其危险性就越大,近年来社会上发生的锂电池安全事故越来越多,2018年~2019年上半年一共发生了60多起纯电动汽车起火事故,导致16万辆纯电动汽车召回[2],手机鼓胀、起火、爆炸的事故更是频发。
本文以一款客户投诉电池(简称客诉电池)的分析为切入点,研究该电池的起鼓原因,并实验模拟手机日常使用中可能存在的失效情况,并分析其机理。
实验1.1 客诉电池分析对客诉电池进行电压内阻测试,根据电池编码进行系统查询,判断其出厂是否合格;对其进行充放电测试,判定是否可以正常进行充放电,判断电性能是否正常;测试气体成分,拆解进行电感耦合等离子体光谱分析法(ICP)、扫描电子显微镜法(SEM)测试,分析其失效原因。
1.2 过放模拟实验采用6组电池,每组3只,以0.5 C、0.1 C、0.01 C、0.001 C分别将电池放电至3、2、1、0.5、0.2、0 V,放电后休眠1 h,再继续进行后续放电,观察是否鼓胀产气,拆解进行SEM、ICP分析;对放电至3与2.5 V的电池进行长期存储,观察其是否产气,测试其低压下长期存储电压内阻的变化情况。
1.3 高温浮充模拟实验采用4组电池,每组3只,分别进行45、60、70 ℃浮充,60 ℃ (4.2~4.4 V)循环充电,测试其厚度变化,观察鼓胀产气情况,测试气体成分,拆解进行SEM、ICP分析。
1.4 设备与仪器充放电设备采用ARBIN;电压内阻测试设备采用BK-300内阻测试仪;气体成分采用津岛质联用仪GCMS-2010测试;形貌采用扫描电子显微镜JSM-6510测试;微量金属元素含量采用电感藕合等离子体发射光谱仪 Optima 8000DV测试。
结果与分析2.1 客诉电池分析检测客诉电池六面外观(图1),未发现存在破损、腐蚀现象,排除封装破损导致电池起鼓。
软包锂电池胀气的原因

软包锂电池胀气的原因聚合物锂离子电池芯采用的是铝塑複合膜的包装技术,当电池芯内部由于异常化学反应的发生而产生气体时,Pocket会被充起,电池芯鼓胀(有轻微鼓胀和严重鼓胀两种情况),且不论外观如何,电池芯的使用性能(Capacity、Cycle life、C-rate等)会发生严重的失效,导致电池芯不能使用。
胀气会发生在生产过程中也会在客户甚至最终用户手中。
当然,电池芯在化成启动或Baking过程中会正常的产生一定量(一般很少)的气体,这根据所使用的原材料而异,这种气体在Degassing工序会被抽掉。
目前部分Model(一次封装成型电池芯)通过添加V18溶剂来消除这种SEI层形成、相介面稳定时所产生的气体。
但是由于工序异常所产生的气体在Degassing前表面非常明显或者Degassing后产生不能再消掉或者添加V18也不能消除。
这里简要介绍工序异常产生气体的原因:1.封装不良,由封装不良所引起胀气电池芯的比例已经大大地降低。
前面已经介绍了引起Top sealing、Side sealing和Degassing三边封装不良的原因,任何一边封装不良都会导致电池芯,表现以Top sealing 和Degassing居多,Top sealing 主要是Tab位密封不良,Degassing主要是分层(包括受电解液和凝胶影响导致PP与Al脱离)。
封装不良引起空气中水分进入电池芯内部,引起电解液分解产生气体等。
2.Pocket表面破损,电池芯在流拉过程中,受到异常损坏或人为破环导致Pocket 破损(如针孔)而使水分进入电池芯内部。
3.角位破损,由于折边角位铝的特殊变形,气袋晃动会扭曲角位导致Al破损(电池芯越大,气袋越大,越易破损),失去对水的阻隔作用。
可以在角位加皱纹胶或热熔胶缓解。
并且在顶封后的各工序禁止拿气袋移动电池芯,更要注意操作方式防止老化板上电芯池的摆动。
4.电池芯内部水含量超标,前面我们已经介绍过对电池芯内水含量有一定的要求,一旦水含量超标,电解液会失效在化成或Degassing后产生气体。
锂离子软包电池鼓气分析

2EC+ 2Li+ + 2e− → (CH2OCO2Li)2↓+ C2H4↑ EC+ 2Li+ + 2e− → Li2CO3↓+ C2H4↑ EC+ Li+ + e− → CH3OCO2Li↓+ •CH3 •CH3 +•CH3 → C2H6↑
PC+ 2Li+ + 2e− → Li2CO3↓+ C3H6↑
Journal of Energy Storage 2020, 32, 101791
极片类型影响
不同类型负电极体积变化
1. 形成电池前的负极片不与电解液反应产气 2. 产气必须有电解液参与 3. 产气与负极反应有关 4. 0% SOC NCM负极不与电解液反应产气 5. LFP电池产气与负极电压状态有关
电池鼓气原因及机理分析
背景
0%SOC保存电池容易鼓气失效
0%SOC&100%SOC LFP电池55°C存储7天
现象: 0% SOC:电压、电阻和厚度均↑ 100% SOC:电压↓,电阻和厚度↑
? 鼓胀率: 0% SOC> 100% SOC 与理论相悖,进行验证
电压:电池极化 电阻和厚度:电池在储存过程中的副反应
负极电压影响
三电极电压 A:LFP battery ,B: NCM battery
电池类型 LFP
NCM
SOC 0% 0% 过放
电池电压 负极电压
2V
1.4V
3V
0.25V
2V
1.2V
材料表征
55℃储存前后材料表征
ROCO2Li
Li2CO3
SEI中不稳定的烷基碳酸锂会分解为稳定的Li2CO3。 SEI会在储存中分解和再生
锂离子电池气胀原因探讨
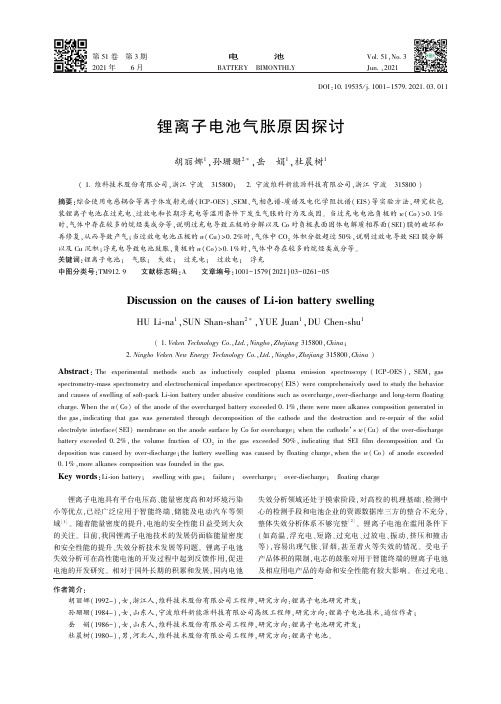
2 结果与讨论
2. 1 过充电产气测试及机理分析
所制备的锂离子电池在过充电测试时,电压和表面温度
随时间的变化曲线见图 1。
6 μm 厚的铜箔( 苏州产,99. 8%) 表面,涂覆速度为( 15 ± 2)
m / min,温度 75 ~ 92 ℃ ,辊压至 132 μm 厚,再进行分切和制
charge. When the w( Co) of the anode of the overcharged battery exceeded 0. 1%,there were more alkanes composition generated in
the gas, indicating that gas was generated through decomposition of the cathode and the destruction and re-repair of the solid
域
[1]
的关注。 目前,我国锂离子电池技术的发展仍面临能量密度
失效分析可在高性能电池的开发过程中起到反馈作用,促进
电池的开发研究。 相对于国外长期的积累和发展,国内电池
( 如高温、浮充电、短路、过充电、过放电、振动、挤压和撞击
产品体积的制,电芯的鼓胀对用于智能终端的锂离子电池
及相应用电产品的寿命和安全性能有较大影响。 在过充电、
关键词:锂离子电池; 气胀; 失效; 过充电; 过放电; 浮充
中图分类号:TM912. 9 文献标志码:A 文章编号:1001-1579(2021)03-0261-05
Discussion on the causes of Li-ion battery swelling
HU Li-na1 ,SUN Shan-shan2∗ ,YUE Juan1 ,DU Chen-shu1
锂电池循环膨胀
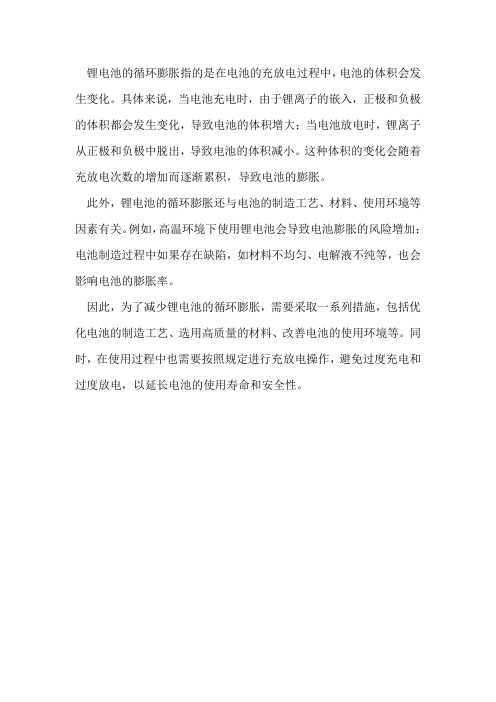
锂电池的循环膨胀指的是在电池的充放电过程中,电池的体积会发生变化。
具体来说,当电池充电时,由于锂离子的嵌入,正极和负极的体积都会发生变化,导致电池的体积增大;当电池放电时,锂离子从正极和负极中脱出,导致电池的体积减小。
这种体积的变化会随着充放电次数的增加而逐渐累积,导致电池的膨胀。
此外,锂电池的循环膨胀还与电池的制造工艺、材料、使用环境等因素有关。
例如,高温环境下使用锂电池会导致电池膨胀的风险增加;电池制造过程中如果存在缺陷,如材料不均匀、电解液不纯等,也会影响电池的膨胀率。
因此,为了减少锂电池的循环膨胀,需要采取一系列措施,包括优化电池的制造工艺、选用高质量的材料、改善电池的使用环境等。
同时,在使用过程中也需要按照规定进行充放电操作,避免过度充电和过度放电,以延长电池的使用寿命和安全性。
重点讲解石墨电极的锂化与膨胀过程

石墨电极的锂化与膨胀过程锂离子电池鼓胀是一个常见的问题,特别是大的铝壳和软包电池,锂电池鼓胀的原因分为两类,一是电池极片的厚度变化导致的鼓胀;二是由于电解液氧化分解产气导致的鼓胀。
电池鼓胀,一方面电池厚度和应力的改变可能引起电池性能的变化,对电池的寿命和可靠性造成不利的影响。
另一方面也制约了电池的成组设计。
电池内部产气是导致电池鼓胀的一个重要原因,无论是电池在常温循环、高温循环、高温搁置时,其均会产生不同程度的鼓胀产气。
据目前研究结果显示,引起电芯胀气的本质是电解液发生分解所致。
电解液分解有两种情况,一个是电解液有杂质,比如水分和金属杂质使电解液分解产气,另一个是电解液的电化学窗口太低,造成了充电过程中的分解,电解液中的EC、DEC等溶剂在得到电子后,均会产生自由基,自由基反应的直接后果就是产生低沸点的烃类、酯类、醚类和CO2等。
电池极片的厚度变化又存在以下几种情况:(1)极片辊压后,搁置时厚度的反弹,压实密度越大反弹越大;在相同的应力下,粘接剂弹性模量越大,极片搁置反弹越小,干燥也会导致极片反弹。
(2)极片吸收电解液溶胀,极片厚度增加。
(3)充放电过程中,锂嵌入导致晶格参数变化引起的电极膨胀。
本文主要介绍锂离子电池石墨负极锂化以及极片膨胀过程。
石墨纽扣半电池锂化以及极片膨胀过程如图1所示,第一次放电锂化时,随着锂离子嵌入石墨层间,电极电势逐渐降低,而极片厚度膨胀率逐渐增加。
整个过程可以分为a~e 多个阶段,随着石墨层间嵌入的锂含量增加(x逐渐增加),LixC6存在几种不同的相,表1列出了这几种相的特征,x表示化合物LixC6中锂的摩尔含量,d是晶格参数石墨层间距,随着锂嵌入量增加,石墨从2H相依次转变,SOC50%时,转变为LiC12,完全锂化后变为LiC6,理论容量为372mAh/g。
这个转变过程中,层间距d逐步增加,从而导致极片厚度增加。
图1所示中,各个阶段锂化和膨胀过程如下:(1)f+e区间:石墨首次锂化时,在800mV-200mV电压区间,主要是SEI膜形成过程、极片中的颗粒重排过程,以及2H =>1L的过程,总体极片膨胀率大概1.5%。
- 1、下载文档前请自行甄别文档内容的完整性,平台不提供额外的编辑、内容补充、找答案等附加服务。
- 2、"仅部分预览"的文档,不可在线预览部分如存在完整性等问题,可反馈申请退款(可完整预览的文档不适用该条件!)。
- 3、如文档侵犯您的权益,请联系客服反馈,我们会尽快为您处理(人工客服工作时间:9:00-18:30)。
软包锂电池胀气的原因
聚合物锂离子电池芯採用的是铝塑複合膜的包装技术,当电池芯内部由于异常化学反应的发生而产生气体时,Pocket 会被充起,电池芯鼓胀(有轻微鼓胀和严重鼓胀两种情况),且不论外观如何,电池芯的使用性能(Capacity、Cycle life、C-rate等)会发生严重的失效,导致电池芯不能使用。
胀气会发生在生产过程中也会在客户甚至最终用户手中。
当然,电池芯在化成启动或Baking过程中会正常的产生一定量(一般很少)的气体,这根据所使用的原材料而异,这种气体在Degassing工序会被抽掉。
目前部分Model(一次封装成型电池芯)通过添加V18溶剂来消除这种SEI层形成、相介面稳定时所产生的气体。
但是由于工序异常所产生的气体在Degassing前表面非常明显或者Degassing后产生不能再消掉或者添加V18也不能消除。
这里简要介绍工序异常产生气体的原因:
1、封装不良:由封装不良所引起胀气电池芯的比例已经大大地降低。
前面已经介绍了引起Top sealing、Side sealing和Degassing三边封装不良的原因,任何一边封装不良都会导致电池芯,表现以Top sealing 和Degassing居多,Top sealing主要是Tab位密封不良,Degassing主要是分层(包括受电解液和凝胶影响导致PP与Al脱离)。
封装不良引起空气中水分进入电池芯内部,引起电解液分解产生气体等。
2、Pocket表面破损:电池芯在流拉过程中,受到异常损坏或人为破环导致Pocket破损(如针孔)而使水分进入电池芯内部。
3、角位破损:由于折边角位铝的特殊变形,气袋晃动会扭曲角位导致Al破损(电池芯越大,气袋越大,越易破损),失去对水的阻隔作用。
可以在角位加皱纹胶或热熔胶缓解。
并且在顶封后的各工序禁止拿气袋移动电池芯,更要注意操作方式防止老化板上电芯池的摆动。
4、电池芯内部水含量超标:前面我们已经介绍过对电池芯内水含量有一定的要求,一旦水含量超标,电解液会失效在化成或Degassing后产生气体。
造成电池内部水含量超标的原因主要有:电解液水含量超标,Baking后裸电芯水含量超标,乾燥房湿度超标。
若怀疑水含量超标导致胀气,可进行工序的追溯检查。
5、化成流程异常:错误的化成流程会导致电池芯发生胀气。
6、SEI膜不稳定:电池芯在容量测试充放电过程中发射功能轻微胀气。
7、过充、过放:由于流程或机器或保护板的异常,使电池芯被过充或过度放电,电池芯会发生严重鼓气。
8、短路:由于操作失误导致带电电芯两Tab接触发生短路,电池芯会发生鼓气同时电压迅速下降,Tab会被烧黑。
9、内部短路:电池芯内部阴阳极短路导致电芯迅速放电发热同时严重鼓气。
内部短路的原因有很多种:设计问题;隔离膜收缩、捲曲、破损;Bi-cell错位;毛刺刺穿隔离膜;夹具压力过大;烫边机过度挤压等。
例如曾经由于宽度不足,烫边机过度挤压电芯实体导致阴阳极短路胀气。
10、腐蚀:电池芯发生腐蚀,铝层被反应消耗,失去对水的阻隔作用,发生胀气。
11、真空抽气异常:系统或机器的原因导致真空度异常Degassing抽气不彻底;Vacuum Sealing(真空密封)的热辐射区过大,导致Degassing抽气刺刀不能有效地刺破Pocket袋而导致抽气不乾淨。