管道焊接标准(一)
焊接管道的技术标准

焊接管道的技术标准一、焊接材料选择焊接材料的选择应基于管道的材质、规格、使用条件和焊接工艺等因素进行综合考虑。
应选择符合质量要求、焊接性能良好且经济合理的焊接材料。
焊接材料的选用应符合相关标准和规范的要求。
二、焊接工艺评定在焊接管道之前,应对选用的焊接工艺进行评定。
评定的内容包括焊接接头的力学性能、化学成分、金相组织等方面的试验和检测。
通过评定,确定焊接工艺的可行性和合理性,并为焊接接头的质量控制提供依据。
三、焊接接头的质量要求焊接接头应具有足够的强度、致密性和耐腐蚀性。
接头应符合设计要求,并应通过无损检测、压力试验等手段进行检验。
接头的质量应符合相关标准和规范的要求。
四、焊接缺陷的防止和处理焊接过程中可能出现气孔、夹渣、裂纹等缺陷。
为了防止这些缺陷的产生,应采取相应的预防措施,如选择合适的焊接工艺、清理坡口及焊缝等。
若出现焊接缺陷,应及时进行处理,如打磨、补焊等。
五、焊接检验与验收焊接完成后,应对焊接接头进行检验与验收。
检验的内容包括接头的外观质量、尺寸偏差、无损检测结果等。
接头的质量应符合相关标准和设计要求,对于不符合要求的接头,应进行返修或重新焊接。
六、焊接安全要求焊接操作应遵守安全规定,采取安全防护措施。
操作人员应经过培训并取得相应的资格证书。
在焊接过程中,应注意防火、防爆、防电击等安全事项。
七、焊接操作人员资格要求从事管道焊接的操作人员应取得相应的资格证书,并具备相应的技能和经验。
在焊接过程中,操作人员应遵守职业道德和操作规范,确保焊接质量和安全。
八、焊接工艺文件管理管道焊接的工艺文件应包括焊接工艺评定报告、焊接作业指导书、焊接质量检验报告等。
这些文件应完整、准确并易于查阅。
工艺文件的管理应符合档案管理的要求。
管道焊接常用标准【范本模板】
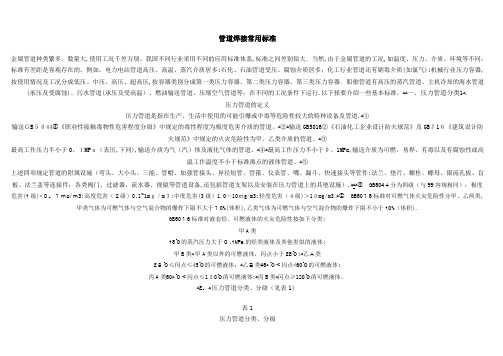
管道焊接常用标准金属管道种类繁多、数量大,使用工况千差万别。
我国不同行业采用不同的应用标准体系,标准之间差别很大.当然,由于金属管道的工况,如温度、压力、介质、环境等不同,标准有差距是客观存在的。
例如,电力电站管道高压、高温、蒸汽介质居多;石化、石油管道受压、腐蚀介质居多;化工行业管道还有剧毒介质(如氯气);机械行业压力容器,按使用情况及工况分成低压、中压、高压、超高压,按容器类别分成第一类压力容器、第二类压力容器、第三类压力容器.船舶管道有高压的蒸汽管道、主机冷却的海水管道(承压及受腐蚀)、污水管道(承压及受高温)、燃油输送管道、压缩空气管道等,在不同的工况条件下运行.以下择要介绍一些基本标准。
ﻫﻫ一、压力管道分类ﻫ1.压力管道的定义压力管道是指在生产、生活中使用的可能引爆或中毒等危险性较大的特种设备及管道.ﻫ①ﻫ输送GB5016②《石油化工企业设计防火规范》及GBJ16《建筑设计防②输送GB5044①《职业性接触毒物性危害程度分级》中规定的毒性程度为极度危害介质的管道。
ﻫ火规范》中规定的火灾危险性为甲、乙类介质的管道。
ﻫ③ﻫ最高工作压力不小于0。
1MPa,输送介质为可燃、易焊、有毒以及有腐蚀性或高④最高工作压力不小于0。
1MPa(表压,下同),输送介质为气(汽)体及液化气体的管道。
ﻫ温工作温度不小于标准沸点的液体管道。
ﻫ⑤上述四项规定管道的附属设施(弯头、大小头、三能、管帽、加强管接头、异径短管、管箍、仪表管、嘴、漏斗、快速接头等管件;法兰、垫片、螺栓、螺母、限流孔板、盲板、法兰盖等连接件;各类阀门、过滤器、流水器、视镜等管道设备,还包括管道支架以及安装在压力管道上的其他设施).ﻫﻫﻫ①GB5044分为四级(与99容规相同):极度危害(1级)<0。
1mg/m3;高度危害(2级)0.1~1mg/m3;中度危害(3级)1.0~10mg/m3;轻度危害(4级)>10mg/m3.ﻫ②GB5016标准对可燃气体火灾危险性分甲、乙两类,甲类气体为可燃气体与空气混合物的爆炸下限不大于10%(体积),乙类气体为可燃气体与空气混合物的爆炸下限不小于10%(体积).GB5016标准对液态烃、可燃液体的火灾危险性按如下分类:甲A类15℃的蒸汽压力大于0.1MPa的烃类液体及其他类似的液体;甲B类ﻫ甲A类以外的可燃液体,闪点小于28℃;ﻫ乙A类45℃<闪点<60℃的可燃液体;28℃≤闪点≤45℃的可燃液体;ﻫ乙B类ﻫ60℃<闪点≤120℃的可燃液体;ﻫ丙B类ﻫ闪点≥120℃的可燃液体。
工艺管道焊接工艺要求(1)
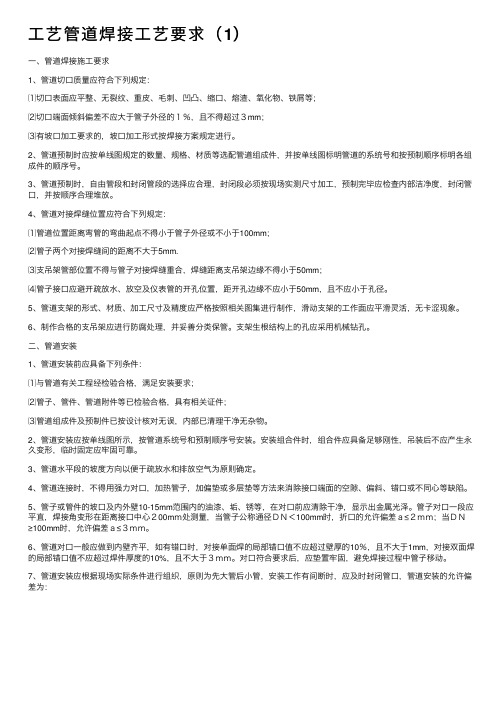
⼯艺管道焊接⼯艺要求(1)⼀、管道焊接施⼯要求1、管道切⼝质量应符合下列规定:⑴切⼝表⾯应平整、⽆裂纹、重⽪、⽑刺、凹凸、缩⼝、熔渣、氧化物、铁屑等;⑵切⼝端⾯倾斜偏差不应⼤于管⼦外径的1%,且不得超过3mm;⑶有坡⼝加⼯要求的,坡⼝加⼯形式按焊接⽅案规定进⾏。
2、管道预制时应按单线图规定的数量、规格、材质等选配管道组成件,并按单线图标明管道的系统号和按预制顺序标明各组成件的顺序号。
3、管道预制时,⾃由管段和封闭管段的选择应合理,封闭段必须按现场实测尺⼨加⼯,预制完毕应检查内部洁净度,封闭管⼝,并按顺序合理堆放。
4、管道对接焊缝位置应符合下列规定:⑴管道位置距离弯管的弯曲起点不得⼩于管⼦外径或不⼩于100mm;⑵管⼦两个对接焊缝间的距离不⼤于5mm.⑶⽀吊架管部位置不得与管⼦对接焊缝重合,焊缝距离⽀吊架边缘不得⼩于50mm;⑷管⼦接⼝应避开疏放⽔、放空及仪表管的开孔位置,距开孔边缘不应⼩于50mm,且不应⼩于孔径。
5、管道⽀架的形式、材质、加⼯尺⼨及精度应严格按照相关图集进⾏制作,滑动⽀架的⼯作⾯应平滑灵活,⽆卡涩现象。
6、制作合格的⽀吊架应进⾏防腐处理,并妥善分类保管。
⽀架⽣根结构上的孔应采⽤机械钻孔。
⼆、管道安装1、管道安装前应具备下列条件:⑴与管道有关⼯程经检验合格,满⾜安装要求;⑵管⼦、管件、管道附件等已检验合格,具有相关证件;⑶管道组成件及预制件已按设计核对⽆误,内部已清理⼲净⽆杂物。
2、管道安装应按单线图所⽰,按管道系统号和预制顺序号安装。
安装组合件时,组合件应具备⾜够刚性,吊装后不应产⽣永久变形,临时固定应牢固可靠。
3、管道⽔平段的坡度⽅向以便于疏放⽔和排放空⽓为原则确定。
4、管道连接时,不得⽤强⼒对⼝,加热管⼦,加偏垫或多层垫等⽅法来消除接⼝端⾯的空隙、偏斜、错⼝或不同⼼等缺陷。
5、管⼦或管件的坡⼝及内外壁10-15mm范围内的油漆、垢、锈等,在对⼝前应清除⼲净,显⽰出⾦属光泽。
管道焊接规范
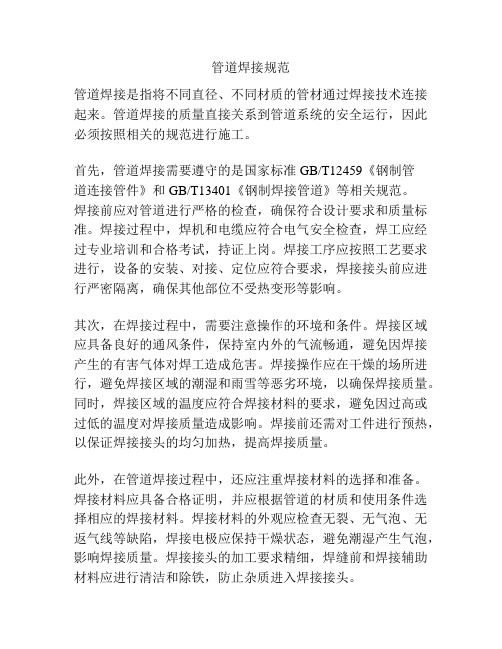
管道焊接规范管道焊接是指将不同直径、不同材质的管材通过焊接技术连接起来。
管道焊接的质量直接关系到管道系统的安全运行,因此必须按照相关的规范进行施工。
首先,管道焊接需要遵守的是国家标准GB/T12459《钢制管道连接管件》和GB/T13401《钢制焊接管道》等相关规范。
焊接前应对管道进行严格的检查,确保符合设计要求和质量标准。
焊接过程中,焊机和电缆应符合电气安全检查,焊工应经过专业培训和合格考试,持证上岗。
焊接工序应按照工艺要求进行,设备的安装、对接、定位应符合要求,焊接接头前应进行严密隔离,确保其他部位不受热变形等影响。
其次,在焊接过程中,需要注意操作的环境和条件。
焊接区域应具备良好的通风条件,保持室内外的气流畅通,避免因焊接产生的有害气体对焊工造成危害。
焊接操作应在干燥的场所进行,避免焊接区域的潮湿和雨雪等恶劣环境,以确保焊接质量。
同时,焊接区域的温度应符合焊接材料的要求,避免因过高或过低的温度对焊接质量造成影响。
焊接前还需对工件进行预热,以保证焊接接头的均匀加热,提高焊接质量。
此外,在管道焊接过程中,还应注重焊接材料的选择和准备。
焊接材料应具备合格证明,并应根据管道的材质和使用条件选择相应的焊接材料。
焊接材料的外观应检查无裂、无气泡、无返气线等缺陷,焊接电极应保持干燥状态,避免潮湿产生气泡,影响焊接质量。
焊接接头的加工要求精细,焊缝前和焊接辅助材料应进行清洁和除铁,防止杂质进入焊接接头。
最后,焊接后应进行必要的检验和测试。
焊接完成后,应对焊接接头进行外观检查和尺寸测量,检查焊缝是否饱满、缺陷是否存在,焊接接头是否符合设计要求。
还应进行无损检测,如超声波检测、射线检测等,以排除焊接区域存在的隐藏缺陷。
若检测结果不合格,应及时进行修补或更换焊接接头,确保焊接质量。
综上所述,管道焊接的规范包括检查准备工作、操作环境和条件、焊接材料的选择和准备、焊接工艺的施工以及焊后的检验和测试等方面。
遵守这些规范能够保证焊接质量,提高管道系统的安全性和稳定性。
管道焊接标准
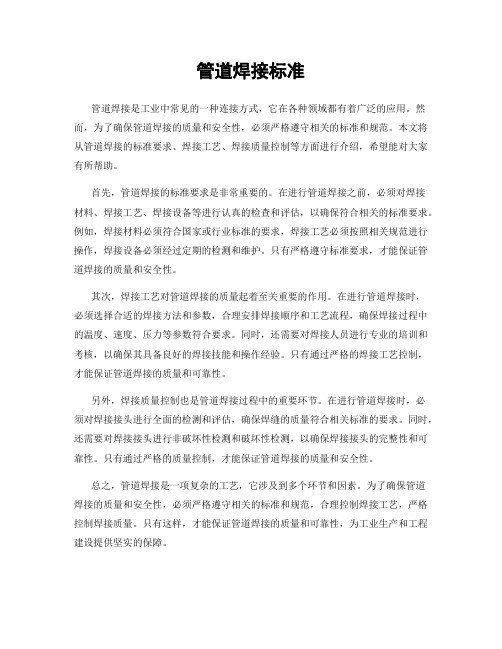
管道焊接标准管道焊接是工业中常见的一种连接方式,它在各种领域都有着广泛的应用。
然而,为了确保管道焊接的质量和安全性,必须严格遵守相关的标准和规范。
本文将从管道焊接的标准要求、焊接工艺、焊接质量控制等方面进行介绍,希望能对大家有所帮助。
首先,管道焊接的标准要求是非常重要的。
在进行管道焊接之前,必须对焊接材料、焊接工艺、焊接设备等进行认真的检查和评估,以确保符合相关的标准要求。
例如,焊接材料必须符合国家或行业标准的要求,焊接工艺必须按照相关规范进行操作,焊接设备必须经过定期的检测和维护。
只有严格遵守标准要求,才能保证管道焊接的质量和安全性。
其次,焊接工艺对管道焊接的质量起着至关重要的作用。
在进行管道焊接时,必须选择合适的焊接方法和参数,合理安排焊接顺序和工艺流程,确保焊接过程中的温度、速度、压力等参数符合要求。
同时,还需要对焊接人员进行专业的培训和考核,以确保其具备良好的焊接技能和操作经验。
只有通过严格的焊接工艺控制,才能保证管道焊接的质量和可靠性。
另外,焊接质量控制也是管道焊接过程中的重要环节。
在进行管道焊接时,必须对焊接接头进行全面的检测和评估,确保焊缝的质量符合相关标准的要求。
同时,还需要对焊接接头进行非破坏性检测和破坏性检测,以确保焊接接头的完整性和可靠性。
只有通过严格的质量控制,才能保证管道焊接的质量和安全性。
总之,管道焊接是一项复杂的工艺,它涉及到多个环节和因素。
为了确保管道焊接的质量和安全性,必须严格遵守相关的标准和规范,合理控制焊接工艺,严格控制焊接质量。
只有这样,才能保证管道焊接的质量和可靠性,为工业生产和工程建设提供坚实的保障。
希望本文的介绍能够对大家有所帮助,让大家对管道焊接有更深入的了解,从而更好地应用于实际工作中。
同时,也希望大家在进行管道焊接时,能够严格遵守相关的标准和规范,确保焊接质量和安全性,为工程建设和生产运行提供可靠的支持。
管道焊接施工工艺标准

全面讲解管道焊接施工工艺标准1、焊接方法优缺点及主要使用场合2、焊接材料3、手工电弧焊及CO2 气体保护焊3.1 适用范围本焊接方法适用于无缝钢管及焊接钢管的焊接。
3.2 两种工艺的特点3.3.焊接要领(1)二氧化碳气体保护半自动焊焊接示意图如下所示。
(2)焊接燃弧点位置如果燃弧位置过小时,背面成型焊缝有呈漏出现象不是熔合焊缝且成型焊缝两交界有明显的凹痕界线未有过渡熔合。
当间隙过大时,即产生焊瘤,甚至焊穿无法正常成型,所以燃弧点位置掌握非常关健的操作技术,燃弧点每次焊接都要在距底部1~2mm 处进行连续燃弧焊接。
(3)用月牙形横向摆动手法,在两边坡口处稍作停留运条焊接,当装配间隙大于4mm 时,可采用月牙形增大往后回复弧度摆动手法,使背面焊缝能正常成型,可视对背部面焊缝的技术要求而定。
(4)根部击穿小孔在0.5~1mm 范围内击穿小孔是确保背面焊透成型的重要方法,其根部击穿小孔,即可控制背面成型焊缝高度尺寸。
(5)层焊缝接头方法:应在弧坑前2~3mm 处引弧后焊至弧坑前方边界时即把焊枪向下压1~2mm使焊缝增加重力,背面焊缝接头处重新熔出接上,不会产生内凹或脱节现象,也可在弧坑上进斜削打磨,减薄弧坑也可接上。
(6)当管道焊接环形密封接头时,应先在已焊弧坑处用砂轮打磨一个斜度,当焊接此斜度时焊枪向下压1~2mm即可接上背面成型焊缝无内凹和脱节现象。
(7)为使焊接稳定,焊机选用NBK—350 焊机和使用较轻巧的焊枪,操作灵活。
(8)由于在坡口内焊接根部时,焊丝伸出长度会增加,此时焊枪导电与喷嘴内缩为0.5~1mm 以便使焊接过程稳定。
(9)若使用混合气体,Ar+CO2 混合比80%∶20%焊接可使焊接电弧更稳定和飞溅明显减少,且颗粒细小。
(10)由于采用短路过渡小电流低电压,规范焊接其焊机的外部接线必须牢固可靠尤其接工件回路线。
(11)采用反极性接法:即“-”接工件,“+”接焊枪,否则极点压力增大产生严重飞溅。
管道与管道焊接国家标准

管道与管道焊接国家标准管道及管道焊接是工业生产中常见的工艺,其质量直接关系到工程的安全和稳定运行。
为了保障管道及管道焊接的质量,我国制定了一系列的国家标准,对于管道及管道焊接的设计、材料、施工、检验等方面进行了规范。
本文将对管道与管道焊接国家标准进行详细介绍,以便工程技术人员和相关从业人员能够更好地理解和应用这些标准。
首先,国家标准对于管道的设计和选材提出了明确的要求。
在设计方面,标准要求应根据工程需要确定管道的材料、尺寸、压力等级和温度等参数,并且应符合相关的国家标准和规范。
在选材方面,标准规定了各种类型管道应选用的材料,以及材料的化学成分、力学性能、加工工艺等方面的要求,以确保管道材料的质量和可靠性。
其次,国家标准对于管道的施工和焊接工艺也进行了详细的规定。
在施工方面,标准要求施工单位应按照设计要求进行施工,并且应符合相关的施工工艺规范。
在焊接工艺方面,标准规定了各种类型焊接工艺的要求,包括焊接方法、焊接材料、预热温度、焊接层次、焊接工艺评定等内容,以确保焊接接头的牢固性和密封性。
此外,国家标准还对管道的检验和验收提出了严格的要求。
在检验方面,标准规定了对于管道材料、管道焊接接头、管道外观和尺寸等方面的检验方法和标准,以确保管道的质量符合设计要求。
在验收方面,标准要求施工单位应对管道的质量进行全面的验收,并且应出具相应的验收报告,以确保管道的质量符合国家标准和合同要求。
总之,国家标准对管道与管道焊接进行了全面的规范,涵盖了设计、选材、施工、焊接工艺、检验和验收等方面。
遵循国家标准,能够保障管道及管道焊接的质量,提高工程的安全性和可靠性,对于工程技术人员和从业人员来说具有重要的指导意义。
希望相关人员能够深入学习和理解国家标准,严格按照标准要求进行工作,共同为工程质量和安全保驾护航。
管道焊接检验标准

管道焊接检验标准 Revised by Hanlin on 10 January 2021管道焊接对焊接方式和焊接质量,应按设计规定套用相应定额。
如设计无规定时,可参考以下规定套用相应定额项目。
1.Ⅰ、Ⅱ级焊缝以及管内壁清洁度要求严格,且焊后不易清理的管道(如透平机入口管、锅炉给水管、机组的循环油、控制油、密封油管道等)单面焊缝、宜采用氩电联焊。
合金钢管焊缝采用氩弧焊打底时,焊缝内侧宜充氩气保护。
2.奥氏体不锈钢管单面焊的焊缝,宜采用手工钨极氩弧焊打底,手工电弧焊填充盖面(氩电联焊)。
公称直径在50毫米以下的采用氩弧焊。
3.Ⅲ级以下焊缝碳钢管,公称直径在50毫米以下的(壁厚在3.5毫米以下)采用氧炔焊。
4.管道分类见表1表1注:⑴剧毒介质的管道按Ⅰ类管道。
⑵有毒介质,甲、乙类火灾危险物质的管道均升一类。
⑶“工作压力”项内任意为不分压力均为一级管道。
5.管口焊前预热和焊后热处理要求见表2。
表2注:⑴当焊接环境温度低于零度时,除规定壁厚必须作预热要求的金属外,其余金属壁厚也均应作适当的预热,使被焊接母材有手温感。
规定必须作预热要求的金属,定额项目内的预热消耗已考虑了温度变化因素,故不再增加预热。
⑵有应力腐蚀的碳素钢、合金钢,不论其壁厚条件,均应进行焊后热处理。
6.管口焊缝无损探伤计算规定数据:(1)管口焊接含量取定见表3。
表3(2)每个管口焊缝X光拍片张数,如无规定者可按表4计算。
表4注:⑴公称直径80毫米以下的管道焊缝X光透视检查拍片,一个焊口要求至少拍两张片。
定额中采用的胶片为85×300毫米的,实际上可用85×150毫米的胶片,执行定额时,人工和机械使用费壁变,材料费乘0.5系数。
⑵片子有效长度按片长减去搭接每边25毫米计算。
⑶管道焊口透视拍片的张数=管道等级规定的探伤百分比×焊口数量×张数(见表4)(3)管道各级焊缝射线探伤数量,应按设计规定计算。
如设计无规定时,按表5规定计算。
管道焊接检验标准

管道焊接对焊接方式和焊接质量,应按设计规定套用相应定额。
如设计无规定时,可参考以下规定套用相应定额项目。
1.Ⅰ、Ⅱ级焊缝以及管内壁清洁度要求严格,且焊后不易清理的管道(如透平机入口管、锅炉给水管、机组的循环油、控制油、密封油管道等)单面焊缝、宜采用氩电联焊。
合金钢管焊缝采用氩弧焊打底时,焊缝内侧宜充氩气保护。
2.奥氏体不锈钢管单面焊的焊缝,宜采用手工钨极氩弧焊打底,手工电弧焊填充盖面(氩电联焊)。
公称直径在50毫米以下的采用氩弧焊。
3.Ⅲ级以下焊缝碳钢管,公称直径在50毫米以下的(壁厚在3.5毫米以下)采用氧炔焊。
4.管道分类见表1注:⑴剧毒介质的管道按Ⅰ类管道。
⑵有毒介质,甲、乙类火灾危险物质的管道均升一类。
⑶“工作压力”项内任意为不分压力均为一级管道。
5.管口焊前预热和焊后热处理要求见表2。
注:⑴当焊接环境温度低于零度时,除规定壁厚必须作预热要求的金属外,其余金属壁厚也均应作适当的预热,使被焊接母材有手温感。
规定必须作预热要求的金属,定额项目内的预热消耗已考虑了温度变化因素,故不再增加预热。
⑵有应力腐蚀的碳素钢、合金钢,不论其壁厚条件,均应进行焊后热处理。
6.管口焊缝无损探伤计算规定数据:(1)管口焊接含量取定见表3。
表3(2)每个管口焊缝X光拍片张数,如无规定者可按表4计算。
表4注:⑴公称直径80毫米以下的管道焊缝X光透视检查拍片,一个焊口要求至少拍两张片。
定额中采用的胶片为85×300毫米的,实际上可用85×150毫米的胶片,执行定额时,人工和机械使用费壁变,材料费乘0.5系数。
⑵片子有效长度按片长减去搭接每边25毫米计算。
⑶管道焊口透视拍片的张数=管道等级规定的探伤百分比×焊口数量×张数(见表4)(3)管道各级焊缝射线探伤数量,应按设计规定计算。
如设计无规定时,按表5规定计算。
注:每条管线上最低探伤不得少于一个焊口。
不锈钢管道焊接标准

不锈钢管道焊接标准不锈钢管道在工业生产和生活中有着广泛的应用,其焊接质量直接影响着管道的使用效果和安全性。
因此,制定和严格执行不锈钢管道焊接标准显得尤为重要。
下面将就不锈钢管道焊接标准进行详细介绍。
首先,不锈钢管道焊接的材料选择非常重要。
在进行不锈钢管道的焊接时,应选择符合要求的不锈钢焊接材料,以确保焊接接头的质量和稳定性。
同时,还应注意对材料进行质量检测,确保其符合相关的标准要求。
其次,焊接工艺是影响不锈钢管道焊接质量的关键因素之一。
在进行焊接时,应根据管道的具体情况选择合适的焊接工艺,包括焊接方法、焊接参数等。
同时,焊接过程中应严格控制焊接温度和速度,避免产生焊接缺陷,确保焊接接头的牢固性和密封性。
另外,焊接人员的技术水平和操作规范也对不锈钢管道焊接质量有着直接影响。
焊接人员应具备专业的焊接技能和丰富的实践经验,严格按照相关的焊接标准和规范进行操作,确保焊接质量达到要求。
此外,不锈钢管道焊接接头的质量检测也是非常重要的一环。
在完成焊接后,应对焊接接头进行全面的质量检测,包括外观检查、尺寸测量、无损检测等,以确保焊接接头的质量符合标准要求。
最后,对不锈钢管道焊接接头的防护和维护同样至关重要。
在使用过程中,应加强对焊接接头的保护,避免受到外部环境的腐蚀和损坏。
同时,定期对管道进行检测和维护,确保其安全可靠地运行。
总的来说,不锈钢管道焊接标准的执行对于保障管道的使用效果和安全性具有重要意义。
只有严格按照相关标准要求进行材料选择、焊接工艺控制、人员操作、质量检测和防护维护,才能确保不锈钢管道焊接质量达到标准要求,为工业生产和生活提供更加可靠和安全的管道设备。
钢管焊接规范

钢管焊接规范篇一:钢管的焊接管道焊接技术交底依据标准:《现场设备、工业管道焊接工程施工及验收规范》GB 50236-98《工业设备管道安装规范》GB 50235-97一、施工准备1.1 材料要求1.1.1 钢管无锈蚀,管材不得有弯曲、锈蚀重皮及凹凸不平等现象。
管件无偏扣、乱扣、丝扣不全或角度不准现象。
管材及管件均应有出厂合格证及其他相应质量证明材料。
1.1.2 焊接钢管做防腐用的防锈漆、调和漆必须有出厂合格证。
1.2 主要机具1.2.1 机具:电焊机、套丝机、电钻、电锤、砂轮机、试压泵等。
1.2.2 工具:手锤、压力案、管钳等。
1.2.3 其它:钢直尺、水平尺、角尺、小线等。
1.3 作业条件1.3.1 明装托、吊干管安装必须在安装层的结构顶板完成后进行。
沿管线安装位置的模板及杂物清理干净,托吊卡件均已安装牢固,位置正确。
1.3.2 立管安装应在主体结构完成后进行。
每层均应有明确的标高线。
二、工艺流程安装准备→孔洞预留→预制加工→卡架安装→管道安装→试压→防腐三、操作工艺3.1 预制加工按设计图纸画出管道分路、管径、变径、预留管口,阀门位置等草图,在实际安装的结构位置做上标记,按标记分段量出实际安装的准确尺寸,记录在施工草图上,然后按草图测得的尺寸预制加工,使用专用工具垂直切割管材,切口应平滑,无毛刺;清洁管材与管件的连接部位,避免沙子、灰尘等损害接头的质量。
3.2 焊接连接3.2.1 焊接工艺应遵照已批准的焊接工艺规程(转载于: 小龙文档网:钢管焊接规范)执行。
3.2.2 采暖管道采用焊接钢管焊接,焊接时应有防风、雨措施;一般管道的焊接为对口型式及组对,电焊应符合表3-1规定注:δ≥5㎜的管子对接如能保证焊透可不开坡口。
3.2.3 管材与法兰应先将管材插入法兰盘内,先点焊2~3点再用角尺找正找平后方可焊接。
如图3-1图3-13.2.4 厚壁大管径管口的焊接应采用多层多道焊,多层多道焊缝时,应逐层进行检查合格后方可焊接次层,直至完成。
管道焊接、安装技术标准
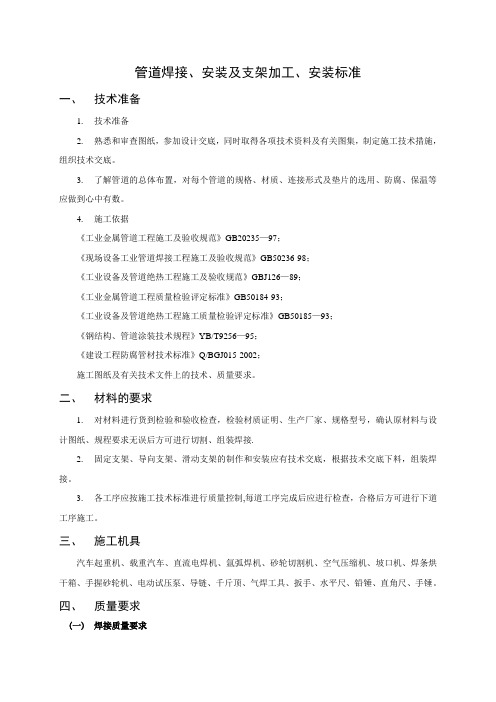
管道焊接、安装及支架加工、安装标准一、技术准备1.技术准备2.熟悉和审查图纸,参加设计交底,同时取得各项技术资料及有关图集,制定施工技术措施,组织技术交底。
3.了解管道的总体布置,对每个管道的规格、材质、连接形式及垫片的选用、防腐、保温等应做到心中有数。
4.施工依据《工业金属管道工程施工及验收规范》GB20235—97;《现场设备工业管道焊接工程施工及验收规范》GB50236-98;《工业设备及管道绝热工程施工及验收规范》GBJ126—89;《工业金属管道工程质量检验评定标准》GB50184-93;《工业设备及管道绝热工程施工质量检验评定标准》GB50185—93;《钢结构、管道涂装技术规程》YB/T9256—95;《建设工程防腐管材技术标准》Q/BGJ015-2002;施工图纸及有关技术文件上的技术、质量要求。
二、材料的要求1.对材料进行货到检验和验收检查,检验材质证明、生产厂家、规格型号,确认原材料与设计图纸、规程要求无误后方可进行切割、组装焊接.2.固定支架、导向支架、滑动支架的制作和安装应有技术交底,根据技术交底下料,组装焊接。
3.各工序应按施工技术标准进行质量控制,每道工序完成后应进行检查,合格后方可进行下道工序施工。
三、施工机具汽车起重机、载重汽车、直流电焊机、氩弧焊机、砂轮切割机、空气压缩机、坡口机、焊条烘干箱、手握砂轮机、电动试压泵、导链、千斤顶、气焊工具、扳手、水平尺、铅锤、直角尺、手锤。
四、质量要求(一)焊接质量要求1.在施工过程中,焊接质量检验应按下列次序进行:(1)对口质量检验;(2)表面质量检验;(3)无损探伤检验;(4)强度和严密性试验;2.对口质量应检验坡口质量、对口间隙、错边量、纵焊缝位置,检验标准应符合表3-2和3-3的规定。
3.焊缝表面质量检验应符合下列规定:(1)检查前,应将焊缝表面熔渣清理干净;(2)焊缝尺寸应符合设计要求,焊缝表面应完整,高度不应低于母材表面,并与母材圆滑过度;(3)不得有表面裂纹、气孔、夹渣及融合性飞溅物等缺陷;(4)咬边深度应小于0.5mm,且每道焊缝的咬边长度不得大于该焊缝总长度的10%;(5)表面加强面的高度不得大于该管道壁厚度的30%,且小于或等于5mm,焊缝加强面宽度应焊出坡口边缘2—3mm。
化工管道焊接技术标准
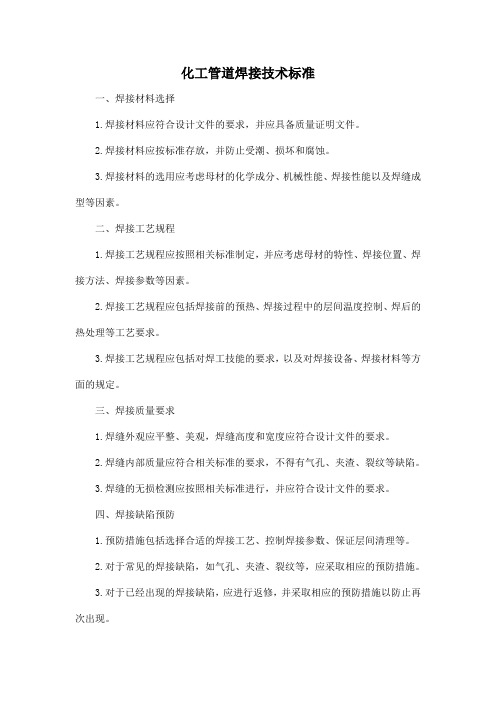
化工管道焊接技术标准一、焊接材料选择1.焊接材料应符合设计文件的要求,并应具备质量证明文件。
2.焊接材料应按标准存放,并防止受潮、损坏和腐蚀。
3.焊接材料的选用应考虑母材的化学成分、机械性能、焊接性能以及焊缝成型等因素。
二、焊接工艺规程1.焊接工艺规程应按照相关标准制定,并应考虑母材的特性、焊接位置、焊接方法、焊接参数等因素。
2.焊接工艺规程应包括焊接前的预热、焊接过程中的层间温度控制、焊后的热处理等工艺要求。
3.焊接工艺规程应包括对焊工技能的要求,以及对焊接设备、焊接材料等方面的规定。
三、焊接质量要求1.焊缝外观应平整、美观,焊缝高度和宽度应符合设计文件的要求。
2.焊缝内部质量应符合相关标准的要求,不得有气孔、夹渣、裂纹等缺陷。
3.焊缝的无损检测应按照相关标准进行,并应符合设计文件的要求。
四、焊接缺陷预防1.预防措施包括选择合适的焊接工艺、控制焊接参数、保证层间清理等。
2.对于常见的焊接缺陷,如气孔、夹渣、裂纹等,应采取相应的预防措施。
3.对于已经出现的焊接缺陷,应进行返修,并采取相应的预防措施以防止再次出现。
五、焊接变形控制1.焊接变形应通过合理的焊接顺序和焊接参数进行控制。
2.对于大型工件或结构,应采用反变形法或刚性固定法等措施来减小焊接变形。
3.对于已经出现的焊接变形,应进行矫正,并采取相应的预防措施以防止再次出现。
六、焊后热处理1.焊后热处理应按照相关标准进行,并应考虑母材的特性、厚度、接头形式等因素。
2.焊后热处理可改善焊缝组织和性能,提高接头的使用性能和寿命。
3.对于某些特殊材料或工艺,如不锈钢、铸铁等,焊后热处理的要求可能会有所不同。
七、焊接检验与验收1.焊接检验包括焊前检验、焊接过程中检验和焊后检验。
焊前检验包括对焊接材料、焊接设备、坡口制备等方面的检查;焊接过程中检验包括对焊工操作技能、焊接参数等的监督和检查;焊后检验包括对焊缝外观、尺寸以及无损检测报告等的审查。
2.验收应按照相关标准和设计文件的要求进行,对于不符合要求的焊缝应进行返修或重新焊接。
GB50236-98_焊接要求规范[1]
![GB50236-98_焊接要求规范[1]](https://img.taocdn.com/s3/m/aebcca830722192e4436f655.png)
现场设备、工业管道焊接工程施工及验收规GBJ236-82目录第一章总则第一节概述第二节一般规定第二章碳素钢及合金钢的焊接第一节材料第二节焊前准备第三节焊接工艺要求第四节焊前预热及焊后热处理第三章铝及铝合金的焊接第一节材料第二节焊前准备第三节焊接工艺要求第四章铜及铜合金的焊接第一节材料第二节焊前准备第三节焊接工艺要求第五章焊接工艺试验第一节试验原则第二节试验要求第三节试验评定第六章焊工考试第一节一般规定第二节焊工操作技能考试第三节附则第七章焊接检验第一节焊接前检查第二节焊接中间检查第三节焊接后检查第四节焊接工程交工验收附录附表1附表1-1附表1-2附表2附表3附表4附表5附表6附表7附表8附表9附表10附表11附表12附表13附表14附表15编制说明主编部门:化学工业部批准部门:国家基本建设委员会实行日期:1982年8月1日国家基本建设委员会文件(82)建发施字25号关于颁发《现场设备、工业管道焊接工程施工及验收规》的通知国务院有关部、总局,各省、市、自治区建委,基建工程兵:由我委委托化学工业部负责组织有关单位编写的《现场设备、工业管道焊接工程施工及验收规》,经有关部门会审,现批准为国家标准施工及验收规,编号为GBJ236—82,自一九八二年八月一日起实行。
本规由化学工业部基建局管理和解释。
一九八二年一月二十日第一章总则第一节概述第1.1.1条为指导设备和工业管道的焊接工程特制定本规。
它适用于石油、化工、电力、冶金、机械和轻纺等行业工程建设的施工现场。
第1.1.2条本规适用于碳素钢(含碳量小于或等于0.3%)、合金钢(普通低合金结构钢、低温用钢、耐热钢及奥氏体不锈钢)、铝及铝合金(工业纯铝及防锈铝合金)、铜及铜合金(紫铜及黄铜)的手工电弧焊、氩弧焊、埋弧焊、二氧化碳气体保护焊和氧-乙炔焊。
第1.1.3条用于现场焊接作业的其他标准和设计文件中的技术要求和规定,不得低于本规。
第1.1.4条焊接作业的安全技术、劳动保护等应按现行有关规定执行。
GB50236-98_焊接规范[1]
![GB50236-98_焊接规范[1]](https://img.taocdn.com/s3/m/cb7ee8e4102de2bd96058851.png)
现场设备、工业管道焊接工程施工及验收规范GBJ236-82目录第一章总则第一节概述第二节一般规定第二章碳素钢及合金钢的焊接第一节材料第二节焊前准备第三节焊接工艺要求第四节焊前预热及焊后热处理第三章铝及铝合金的焊接第一节材料第二节焊前准备第三节焊接工艺要求第四章铜及铜合金的焊接第一节材料第二节焊前准备第三节焊接工艺要求第五章焊接工艺试验第一节试验原则第二节试验要求第三节试验评定第六章焊工考试第一节一般规定第二节焊工操作技能考试第三节附则第七章焊接检验第一节焊接前检查第二节焊接中间检查第三节焊接后检查第四节焊接工程交工验收附录附表1附表1-1附表1-2附表2附表3附表4附表5附表6附表7附表8附表9附表10附表11附表12附表13附表14附表15编制说明主编部门:化学工业部批准部门:国家基本建设委员会实行日期:1982年8月1日国家基本建设委员会文件(82)建发施字25号关于颁发《现场设备、工业管道焊接工程施工及验收规范》的通知国务院有关部、总局,各省、市、自治区建委,基建工程兵:由我委委托化学工业部负责组织有关单位编写的《现场设备、工业管道焊接工程施工及验收规范》,经有关部门会审,现批准为国家标准施工及验收规范,编号为GBJ236—82,自一九八二年八月一日起实行。
本规范由化学工业部基建局管理和解释。
一九八二年一月二十日第一章总则第一节概述第 1.1.1条为指导设备和工业管道的焊接工程特制定本规范。
它适用于石油、化工、电力、冶金、机械和轻纺等行业工程建设的施工现场。
第1.1.2条本规范适用于碳素钢(含碳量小于或等于0.3%)、合金钢(普通低合金结构钢、低温用钢、耐热钢及奥氏体不锈钢)、铝及铝合金(工业纯铝及防锈铝合金)、铜及铜合金(紫铜及黄铜)的手工电弧焊、氩弧焊、埋弧焊、二氧化碳气体保护焊和氧-乙炔焊。
第1.1.3条用于现场焊接作业的其他标准和设计文件中的技术要求和规定,不得低于本规范。
第1.1.4条焊接作业的安全技术、劳动保护等应按现行有关规定执行。
焊接管道标准(标准)

本文由BAOYUJIANSHE贡献 doc文档可能在WAP端浏览体验不佳。
建议您优先选择TXT,或下载源文件到本机查看。
管道焊接技术标准 金属管道种类繁多、数量大,使用工况千差万别。
我国不同行业采用不同的应用标准体系,标准之间 差别很大。
当然,由于金属管道的工况,如温度、压力、介质、环境等不同,标准有差距是客观存在的。
例如,电力电站管道高压、高温、蒸汽介质居多;石化、石油管道受压、腐蚀介质居多;化工行业管道还 有剧毒介质(如氯气);机械行业压力容器,按使用情况及工况分成低压、中压、高压、超高压,按容器 类别分成第一类压力容器、第二类压力容器、第三类压力容器。
船舶管道有高压的蒸汽管道、主机冷却的 海水管道(承压及受腐蚀)、污水管道(承压及受高温)、燃油输送管道、压缩空气管道等,在不同的工 况条件下运行。
以下择要介绍一些基本标准。
一、压力管道分类 1. 压力管道的定义压力管道是指在生产、 生活中使用的可能引爆或中毒等危险性较大的特种设备及管道。
① 输送 GB5044①《职业性接触毒物 性危害程度分级》中规定的毒性程度为极度危害介质的管道。
② 输送 GB5016②《石油化工企业设计 防火规范》及 GBJ16《建筑设计防火规范》中规定的火灾危险性为甲、乙类介质的管道。
③ 最高工作 压力不小于 0.1MPa(表压,下同),输送介质为气(汽)体及液化气体的管道。
④ 最高工作压力不 小于 0.1MPa,输送介质为可燃、易焊、有毒以及有腐蚀性或高温工作温度不小于标准沸点的液体管道。
⑤ 上述四项规定管道的附属设施(弯头、大小头、三能、管帽、加强管接头、异径短管、管箍、仪表 管、嘴、漏斗、快速接头等管件;法兰、垫片、螺栓、螺母、限流孔板、盲板、法兰盖等连接件;各类阀 门、 过滤器、 流水器、 视镜等管道设备, 还包括管道支架以及安装在压力管道上的其他设施) 。
① GB5044 分为四级(与 99 容规相同):极度危害(1 级)<0.1mg/m3;高度危害(2 级)0.1~1mg/ m3;中度危害(3 级)1.0~10mg/m3;轻度危害(4 级)>10mg/m3。
管道焊接三级探伤标准(一)
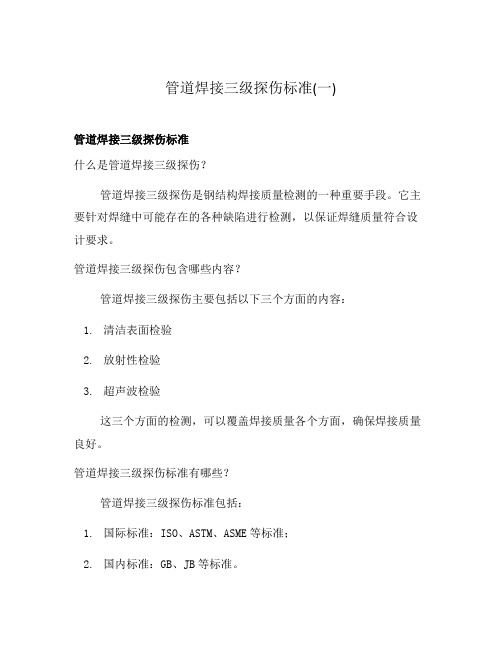
管道焊接三级探伤标准(一)管道焊接三级探伤标准什么是管道焊接三级探伤?管道焊接三级探伤是钢结构焊接质量检测的一种重要手段。
它主要针对焊缝中可能存在的各种缺陷进行检测,以保证焊缝质量符合设计要求。
管道焊接三级探伤包含哪些内容?管道焊接三级探伤主要包括以下三个方面的内容:1.清洁表面检验2.放射性检验3.超声波检验这三个方面的检测,可以覆盖焊接质量各个方面,确保焊接质量良好。
管道焊接三级探伤标准有哪些?管道焊接三级探伤标准包括:1.国际标准:ISO、ASTM、ASME等标准;2.国内标准:GB、JB等标准。
在选择标准时,应根据实际需要进行选择,并且应严格按照标准要求进行操作。
管道焊接三级探伤的重要性管道焊接三级探伤对于保障工程建设的安全和质量具有非常重要的意义。
一方面,能够及早发现存在的问题,及时采取措施进行处理,提高工程建设的质量和效益;另一方面,也能确保施工过程中的安全,降低安全事故的发生概率。
结语管道焊接三级探伤是重要的检测手段,能够确保焊接质量符合要求,保障工程建设的安全和质量。
在进行管道焊接工作时,必须严格遵守相关标准和规范,并加强质量管理,才能确保施工质量。
管道焊接三级探伤的操作步骤以下是管道焊接三级探伤的常规操作步骤:1.清洁表面检验:首先对焊缝进行清洁,去除表面的油污、灰尘等杂质,以利于后续检测工作的进行。
2.放射性检验:对焊缝进行X射线检测,来发现焊缝中可能存在的各种缺陷,比如气孔、夹杂、裂纹等。
3.超声波检验:通过超声波探伤来检测焊缝中的各种缺陷,比如缺陷深度、面积等。
进行完整的三级探伤后,根据检测结果,可以对焊缝进行进一步的处理和修整,以确保其质量符合要求。
管道焊接三级探伤的应用领域管道焊接三级探伤主要应用于石化、化工、船舶、核工业等领域。
在这些领域,焊接的质量要求相对较高,一旦出现质量问题,可能会给工程带来极大的安全隐患和经济损失。
总结管道焊接三级探伤作为重要的检测手段,在工程建设中具有非常重要的意义。
- 1、下载文档前请自行甄别文档内容的完整性,平台不提供额外的编辑、内容补充、找答案等附加服务。
- 2、"仅部分预览"的文档,不可在线预览部分如存在完整性等问题,可反馈申请退款(可完整预览的文档不适用该条件!)。
- 3、如文档侵犯您的权益,请联系客服反馈,我们会尽快为您处理(人工客服工作时间:9:00-18:30)。
管道焊接标准(一)
金属管道种类繁多、数量大,使用工况千差万别。
我国不同行业采用不同的应用标准体系,标准之间差别很大。
当然,由于金属管道的工况,如温度、压力、介质、环境等不同,标准有差距是客观存在的。
例如,电力电站管道高压、高温、蒸汽介质居多;石化、石油管道受压、腐蚀介质居多;化工行业管道还有剧毒介质(如氯气);机械行业压力容器,按使用情况及工况分成低压、中压、高压、超高压,按容器类别分成第一类压力容器、第二类压力容器、第三类压力容器。
船舶管道有高压的蒸汽管道、主机冷却的海水管道(承压及受腐蚀)、污水管道(承压及受高温)、燃油输送管道、压缩空气管道等,在不同的工况条件下运行。
以下择要介绍一些基本标准。
一、压力管道分类 1.压力管道的定义压力管道是指在生产、生活中使用的可能引爆或中毒等危险性较大的特种设备及管道。
①输送GB5044①《职业性接触毒物性危害程度分级》中规定的毒性程度为极度危害介质的管道。
②输送GB5016②《石油化工企业设计防火规范》及GBJ16《建筑设计防火规范》中规定的火灾危险性为甲、乙类介质的管道。
③最高工作压力不小于0.1MPa(表压,下同),输送介质为气(汽)体及液化气体的管道。
④最高工作压力不小于0.1MPa,输送介质为可燃、易焊、有毒以及有腐蚀性或高温工作温度不小于标准沸点的液体管道。
⑤上述四项规定管道的附属设施(弯头、大小头、三能、管帽、加强管接头、异径短管、管箍、仪表管、嘴、漏斗、快速接头等管件;法兰、垫片、
螺栓、螺母、限流孔板、盲板、法兰盖等连接件;各类阀门、过滤器、流水器、视镜等管道设备,还包括管道支架以及安装在压力管道上的其他设施)。
①GB5044分为四级(与99容规相同):极度危害(1级)<0.1mg/m3;高度危害(2级)0.1~1mg/m3;中度危害(3级)1.0~10mg/m3;轻度危害(4级)>10mg/m3。
②GB5016标准对可燃气体火灾危险性分甲、乙两类,甲类气体为可燃气体与空气混合物的爆炸下限不大于10%(体积),乙类气体为可燃气体与空气混合物的爆炸下限不小于10%(体积)。
GB5016标准对液态烃、可燃液体的火灾危险性按如下分类:甲A类15℃的蒸汽压力大于0.1MPa的烃类液体及其他类似的液体;甲B类甲A类以外的可燃液体,闪点小于28℃;乙A 类28℃≤闪点≤45℃的可燃液体;乙B类45℃<闪点<60℃的可燃液体;丙A类60℃<闪点≤120℃的可燃液体;丙B类闪点≥120℃的可燃液体。
2.压力管道分类、分级(见表1)表1压力管道分类、分级名称类别级别工况和参数长输管道GAGA1⑴介质:有毒、可燃易爆气体,P>1.6MPa 的管道⑵介质:有毒、可燃易爆气体,DN≥300mm,输送距离≥200km 的管道⑶介质:浆体中,DN≥150mm,输送距离≥50km的管道GA2⑴介质:有毒、可燃易爆气体,P≤1.6MPa的管道⑵GA1(2)范围以外的长输管道⑶GA1(3)范围以外的长输管道公用管道GBGB1燃气管道GB2热力管道工业管道GCGC1⑴GB5044标准中,毒性程度为极度危害介质的管道⑵GB50160、GBJ16标准中规定的火灾危险性为甲、乙类可燃气体或甲类可燃气体介质,且P≥4.0MPa的管道⑶输送流体介质,且P≥10.0MPa
的管道GC2⑴输送GB50160、GBJ160标准中规定的火灾危险性为甲、乙类可燃气体或甲类可燃气体介质,且P<0.4MPa的管道⑵流体介质:可燃、有毒,P<4.0MPa,t≥400℃的管道⑶流体介质:不可燃、无毒,P<10MPa,t≥400℃的管道⑷流体介质:P<10.0MPa,t<400℃的管道注:表中P为设计压力;t为工作温度;DN为公称直径。