磨削平面
简述磨削平面的方法

简述磨削平面的方法磨削平面是机械加工中常用的一种方法,它可以使工件表面光滑、平整、精度高。
下面将详细介绍磨削平面的方法。
一、准备工作在进行磨削平面前,需要做好以下准备工作:1.选择合适的磨削工具和砂轮。
根据被加工材料的硬度和形状,选择合适的砂轮和磨削工具。
2.调整机床。
调整机床的刀架高度和角度,使其与被加工材料表面垂直,并且旋转方向与材料运动方向相反。
3.清洁被加工材料表面。
清除被加工材料表面上的油污和灰尘,以保证磨削效果。
二、粗加工1.粗选合适的砂轮。
根据被加工材料的硬度和形状,选择合适的粗砂轮,并将其安装到机床上。
2.调整刀架高度和角度。
将刀架调整到与被加工材料表面垂直,并且旋转方向与材料运动方向相反。
3.开始粗加工。
打开机床,将砂轮轻轻地接触到被加工材料表面,然后逐渐增加砂轮的压力,直到达到所需的粗磨效果。
4.检查粗加工效果。
停止机床,检查被加工材料表面的平整度和光滑度。
如果需要进一步精加工,则进行下一步操作。
三、精加工1.选择合适的砂轮。
根据被加工材料的硬度和形状,选择合适的细砂轮,并将其安装到机床上。
2.调整刀架高度和角度。
将刀架调整到与被加工材料表面垂直,并且旋转方向与材料运动方向相反。
3.开始精加工。
打开机床,将细砂轮轻轻地接触到被加工材料表面,然后逐渐增加砂轮的压力,直到达到所需的精磨效果。
4.检查精加工效果。
停止机床,检查被加工材料表面的平整度和光滑度。
如果需要进一步提高平整度和光滑度,则进行下一步操作。
四、抛光1.选择合适的抛光材料。
根据被加工材料的硬度和形状,选择合适的抛光材料,如毛毡轮、绒布轮等。
2.调整刀架高度和角度。
将刀架调整到与被加工材料表面垂直,并且旋转方向与材料运动方向相反。
3.开始抛光。
打开机床,将抛光材料轻轻地接触到被加工材料表面,然后逐渐增加压力,直到达到所需的抛光效果。
4.检查抛光效果。
停止机床,检查被加工材料表面的平整度和光滑度。
如果需要进一步提高平整度和光滑度,则进行下一步操作。
简述磨削加工

磨削加工1. 简介磨削加工是一种常见的金属加工方法,通过使用磨料对工件表面进行摩擦磨损,以达到加工的目的。
它可以用于改善工件表面质量、调整尺寸精度和形状精度,以及去除杂质和残余应力等。
磨削加工广泛应用于机械制造、航空航天、汽车制造、模具制造等领域。
2. 磨削原理磨削加工是利用切削性能较差的材料(磨料)对工件进行切削,通过与工件表面的相对运动来实现切削作用。
其主要原理包括以下几个方面:•切削颗粒:磨料是由硬度较高的颗粒组成,通常为氧化铝、碳化硅等材料。
这些颗粒与工件表面摩擦产生很高的切向力,从而实现切削作用。
•切向力:当磨料与工件表面接触时,由于相对运动产生了摩擦力,使得磨料在切向方向上产生了切削力。
这种力对工件表面进行了切削作用。
•磨屑形成:在磨削过程中,磨料与工件表面的摩擦力和切向力使得工件表面的材料被切削下来,形成了磨屑。
这些磨屑会随着磨料的运动带走,并通过冷却液进行排出。
•热效应:由于切削过程中的摩擦力和切向力,会产生较高的温度。
为了避免温度过高引起工件变形或损坏,通常需要使用冷却液进行冷却。
3. 磨削方法根据加工目标和工件材料的不同,磨削加工可以采用多种方法。
下面介绍几种常见的磨削方法:3.1 平面磨削平面磨削是最基本、最常用的磨削方法之一。
它主要用于对平面工件进行加工,如平面零件、平底孔等。
平面磨削通常采用平面砂轮进行加工,通过对工件表面进行连续的摩擦来实现加工效果。
在平面磨削过程中,需要注意保持磨削面与砂轮之间的良好接触,以确保加工质量。
3.2 内圆磨削内圆磨削是用于加工孔内表面的一种方法。
它通常使用内圆砂轮进行加工,通过对孔内表面进行旋转磨削来实现加工效果。
在内圆磨削过程中,需要注意选择合适的砂轮尺寸和形状,并控制好加工参数,以确保加工质量。
3.3 外圆磨削外圆磨削是用于加工轴类零件外表面的一种方法。
它通常使用外圆砂轮进行加工,通过对零件外表面进行旋转磨削来实现加工效果。
在外圆磨削过程中,同样需要注意选择合适的砂轮尺寸和形状,并控制好加工参数。
磨削的加工范围
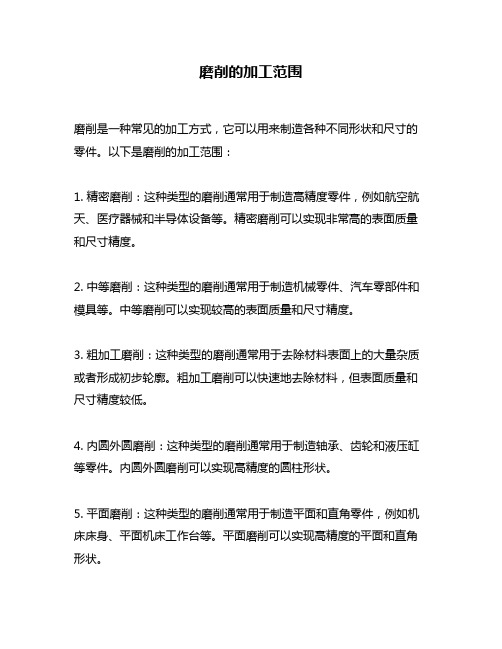
磨削的加工范围
磨削是一种常见的加工方式,它可以用来制造各种不同形状和尺寸的零件。
以下是磨削的加工范围:
1. 精密磨削:这种类型的磨削通常用于制造高精度零件,例如航空航天、医疗器械和半导体设备等。
精密磨削可以实现非常高的表面质量和尺寸精度。
2. 中等磨削:这种类型的磨削通常用于制造机械零件、汽车零部件和模具等。
中等磨削可以实现较高的表面质量和尺寸精度。
3. 粗加工磨削:这种类型的磨削通常用于去除材料表面上的大量杂质或者形成初步轮廓。
粗加工磨削可以快速地去除材料,但表面质量和尺寸精度较低。
4. 内圆外圆磨削:这种类型的磨削通常用于制造轴承、齿轮和液压缸等零件。
内圆外圆磨削可以实现高精度的圆柱形状。
5. 平面磨削:这种类型的磨削通常用于制造平面和直角零件,例如机床床身、平面机床工作台等。
平面磨削可以实现高精度的平面和直角形状。
总之,磨削是一种非常重要的加工方式,可以用于制造各种不同形状和尺寸的零件。
不同类型的磨削适用于不同的加工要求,需要根据具体情况选择合适的磨削方式。
平面磨削中常见缺陷及其原因
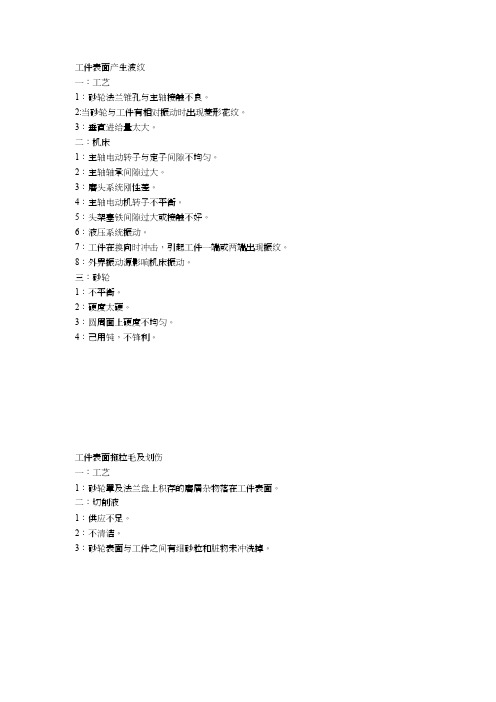
工件表面产生波纹一:工艺1:砂轮法兰锥孔与主轴接触不良。
2:当砂轮与工件有相对振动时出现菱形花纹。
3:垂直进给量太大。
二:机床1:主轴电动转子与定子间隙不均匀。
2:主轴轴承间隙过大。
3:磨头系统刚性差。
4:主轴电动机转子不平衡。
5:头架塞铁间隙过大或接触不好。
6:液压系统振动。
7:工件在换向时冲击,引起工件一端或两端出现振纹。
8:外界振动源影响机床振动。
三:砂轮1:不平衡。
2:硬度太硬。
3:圆周面上硬度不均匀。
4:己用钝,不锋利。
工件表面拖拉毛及划伤一:工艺1:砂轮罩及法兰盘上积存的磨屑杂物落在工件表面。
二:切削液1:供应不足。
2:不清洁。
3:砂轮表面与工件之间有细砂粒和脏物未冲洗掉。
工件表面呈直线痕迹一:工艺1:垂直进给量太大2:横向进给量太大3:金刚石修整器安放位置不对二:机床1:热变形不稳定2:主轴系统刚性差三:砂轮1:己用钝,不锋利工件表面烧伤一:工艺1:工件前进速度太低2:垂直和横向进给量太大二:砂轮1:粒度太细或硬度太硬2:己用钝,不锋利3:修整太细三:切削液1:喷射位置不佳2:压力及流量不够工件两表面平行度或表面平面度超差一:工艺1:夹具基准不平,或有毛刺,脏物2:垂直和横向进给量太大3:用压板压紧工件磨削时,夹紧点不合理,夹紧力过大4;用砂轮端面磨削时,立柱倾斜角位置未调整好二:机床1:热变形太大2:导轨润滑油太多3:导轨润滑油压力差太大4:磨头横向运动精度超差三:砂轮1:选择不当,不锋利四:工件1:基准面平面度超差或有毛刺2:工件太大,变形大3:工件内应力未去除工件塌角或侧面呈喇叭形一:工艺1:换向时越程太大2:进给量太大二:机床1:主轴轴承间隙过大三:砂轮1:选择不当2:不锋利以上为本人这几天发的话题,经管理员思远的要求现重新整理在一块,以后发帖尽量改进。
文案编辑词条B 添加义项?文案,原指放书的桌子,后来指在桌子上写字的人。
现在指的是公司或企业中从事文字工作的职位,就是以文字来表现已经制定的创意策略。
锉削平面的操作方法

锉削平面的操作方法
锉削平面的操作方法如下:
1. 准备工作:先确保锉具的齿面是干净且锋利的。
可以使用刷子或布擦拭锉具的齿面,如果发现锉具齿面钝了,可以使用锉刀磨削工具将其磨削出锋利的齿面。
2. 定位要削平的工件表面:将要削平的工件放在平整的工作台上,通过触摸和视觉定位好要削平的表面。
可以使用工作台上的夹具将工件固定住,以确保工件的稳定性。
3. 初始锉削:首先在要削平的表面上选择一个起始点,通常从一个角开始进行锉削。
将锉刀对准起始点,保持锉刀与工件表面之间约30度的角度,轻轻地推动锉刀沿着一个方向削减表面,注意保持锉刀与工件表面始终保持接触。
轻轻推动锉刀,不要用力过猛,以免过早损坏锉刀齿面。
4. 均匀锉削:在初始锉削的基础上,逐渐将锉刀向其他方向移动,保证锉削的表面均匀。
可以使用锉刀上的齿面来指导锉削的方向,以确保表面的平整和光滑。
5. 交替锉削:为了保持表面的平整,可以使用交替锉削的方法。
即在一个方向上削平后,再在垂直的方向上进行锉削,以全部覆盖表面,并确保削平的均匀性。
6. 注意细节:在进行锉削时,注意细节的处理。
例如,锉削边缘时,应特别小
心,以免过度削减或损坏细小的部件。
还要注意锉削的深度,避免过度削减或不足削减。
7. 定期检查:在锉削过程中,定期检查工件表面的平整度和光滑度。
如发现不平整的地方,可以进一步锉削,直至达到所需的平整度和光滑度。
8. 清洁工作:锉削完毕后,用刷子或布擦拭工件和锉具,将剩余的金属屑清除掉,并确保锉具的齿面干净。
以上是锉削平面的操作方法,希望能对您有所帮助。
磨削加工参数-磨削加工的范围有哪些?

磨削加工参数-磨削加工的范围有哪些?磨削加工参数磨削加工是一种常用的精密加工方法,其加工参数对加工效果有着至关重要的影响。
以下是常用的磨削加工参数及其单位:1.磨削要素磨削速度v:砂轮旋转运动的线速度,单位为m/s。
工件速度vw:工件运动的线速度,单位为m/min。
轴向进给量fa:对平面磨削而言,指工作台每单行程或双行程后砂轮轴向移动量,单位为mm/单行程或mm/双行程,本“推荐表”采用mm/双行程为单位。
对外圆、内圆磨削而言,指工件每相对于砂轮的轴向移动量,单位为mm/r。
径向进给量fr:砂轮径向切入工件的深度,单位为mm。
Ra:以轮廓算术平均偏差评定的表面粗糙度参数,单位为μm。
B:砂轮宽度,单位为mm。
2.平面磨削平面磨削是一种常见的磨削加工方法。
下表列出了三种不同硬度的钢材在淬火状态下的平面磨削参数:XXX淬火状态(硬度:40~45HRC)类别 Ra fr(mm) fa(mm/双行程) v(m/s) vw(m/min)砂轮粗磨 1.6 0.02~0.04 0.3B 25~30 15~25WA46K 精磨 0.8 0.01~0.015 0.1B 20~25 10~15WA60KGCr15钢淬火状态(硬度:61~65HRC)类别 Ra fr(mm) fa(mm/双行程) v(m/s) vw(m/min)砂轮粗磨 1.6 0.015~0.03 0.3B 15~20 15~25WA46K 精磨 0.8 0.005~0.01 0.1B 15~20 15~25WA60KT10钢淬火状态(硬度:58~64HRC)类别 Ra fr(mm) fa(mm/双行程) v(m/s) vw(m/min)砂轮粗磨 1.6 0.02~0.03 0.3B 25~30 15~25WA46K 精磨 0.8 0.005~0.01 0.1B 20~25 10~15WA60K3.外圆磨削外圆磨削是一种将工件放置于旋转的工作台上,通过砂轮的切削作用来加工工件外圆的方法。
磨削加工的范围

磨削加工的范围磨削加工是一种常见的金属加工方式,它通过使用磨料和磨削工具来去除金属表面的材料,从而达到精密加工的目的。
在现代制造业中,磨削加工已经成为了不可或缺的一部分。
本文将介绍磨削加工的范围,包括其应用领域、加工对象、加工形式等方面。
一、应用领域1. 机械制造业机械制造业是磨削加工最广泛应用的领域之一。
在机械制造过程中,许多零部件需要进行精密加工,例如轴承、齿轮、凸轮等等。
这些零部件需要高精度和高表面质量,因此需要采用磨削加工来达到要求。
2. 航空航天业航空航天业是另一个重要的应用领域。
在这个行业中,许多关键零部件需要进行高精度和高表面质量的精密加工。
例如飞机发动机叶片、涡轮叶片等等。
这些零部件需要经过多道复杂的磨削程序才能满足要求。
3. 模具制造业模具制造业是另一个重要的应用领域。
在这个行业中,许多零部件需要进行高精度和高表面质量的加工,例如注塑模具、压铸模具等等。
这些零部件需要采用磨削加工来达到要求。
4. 其他行业除了上述三个领域,磨削加工还广泛应用于其他行业中。
例如汽车制造、医疗器械制造、电子产品制造等等。
在这些行业中,许多零部件需要进行高精度和高表面质量的加工,因此需要采用磨削加工来达到要求。
二、加工对象1. 金属材料磨削加工最常见的对象是金属材料。
在机械制造、航空航天、模具制造等领域中,许多零部件都是由金属材料制成的。
因此,磨削加工对于金属材料的精密加工至关重要。
2. 非金属材料除了金属材料之外,磨削加工还可以应用于一些非金属材料。
例如陶瓷材料、玻璃材料、塑料材料等等。
这些材料需要进行高精度和高表面质量的加工,因此磨削加工也可以为它们提供有效的加工解决方案。
三、加工形式1. 平面磨削平面磨削是最常见的一种磨削形式。
在这种磨削方式中,磨削工具被用来去除金属表面的材料,从而达到平滑表面和高精度的要求。
平面磨削可以应用于许多不同的零部件上,例如轴承、齿轮、凸轮等等。
2. 内圆磨削内圆磨削是一种专门用于加工内孔的磨削方式。
平面磨削

平面磨削机械零件除了带有圆柱、圆锥表面外,还有若干平面组成,如零件底平面,零件上相互平行、垂直或成一定角度的平面。
这些平面所要求达到的技术要求主要是平面的平面度,平面之间的平行度、垂直度、倾斜度以及平面与其他要素之间的位置度,还有平面的表面粗糙度。
平面磨削就是在平面磨床上对这些平面进行加工,达到一定的要求,小型的平面工件也可在工具磨床上进行加工。
平面磨削后的表面精度一般可达IT7一IT6级,表面粗糙度达Ra0.63~0.16um,平行度误差在1000mm长度内为0.01mm。
任务一机床原理项目1平面磨床的结构M7130G/F型平面磨床是在M7130A型基础上经过改进的卧轴矩台平面磨床,也是较为常用的一种平面磨床之一(见图)。
下面就以M7130G/F为例介绍平面磨床的基本操作。
一、M7130G/F型平面磨床各部件名称和作用(一)床身床身1为箱型铸件,上面有V型导轨及水平导轨;工作台2安装在导轨上。
床身前侧的液压操纵箱上安装有垂直进给机构、液压操纵板等,用以控制机床的机械与液压转动。
电器按钮板上有电器控制按钮。
图M7130G/F平面磨床1—床身;2一工作台;3一磨头;4一滑板;5一立柱:6一电器箱;7一电磁吸盘;8一电钮板;9一液压操纵箱(二)工作台工作台2是一盆形铸件,上部有长方型台面,下部有凸出的导轨。
工作台上部台面经过磨削,并有一条T形槽,用以固定工作物和电磁吸盘。
在台面四周装有防护罩,以防止切削液飞溅。
(三)磨头磨头3在壳体前部,装有两套短三块油膜滑动轴承和控制轴向窜动的两套球面止推轴承,主轴尾部装有电动机转子,电动机定子固定在壳体上。
磨头3在水平有两种进给形式:一种是断续进给,即工作抬换向一次,砂轮磨头横向作一次断续进给,进给量1~12mm;另一种是连续进给,磨头在水平面燕尾导轨上往复连续移动,连续移动速度为0.3~3m/min,由进给选择旋钮控制。
磨头除了可液压传动外,还可作手动进给。
(四)滑板滑板4有两组相互垂直的导轨,一组为垂直矩形导轨,用以沿立柱作垂直移动;另一组为水平燕尾导轨,用以作磨头横向移动。
不同类型平面磨床的区别及磨削操作特点

不同类型平面磨床的区别及磨削操作特点不同类型平面磨床的区别及磨削操作特点一、平面磨削的方式按照平面磨床和工作台的结构特点和配置形式,可将平面磨床分为五种类型,即卧轴矩台平面磨床、卧轴圆台平面磨床、立轴矩台平面磨床、立轴圆台平面磨床及双端面磨床等。
1、平面磨床的类型简介(1)卧轴矩台平面磨床砂轮的主轴轴线与工作台台面平行,工件安装在矩形电磁吸盘上,并随工作台作纵向往复直线运动。
砂轮在高速旋转的同时作间歇的横向移动,在工件表面磨去一层后,砂轮反向移动,同时作一次垂向进给,直至将工件磨削到所需的尺寸。
(2)卧轴圆台平面磨床砂轮的主轴是卧式的,工作台是圆形电磁吸盘,用砂轮的圆周面磨削平面。
磨削时,圆形电磁吸盘将工件吸在一起作单向匀速旋转,砂轮除高速旋转外,还在圆台外缘和中心之间作往复运动,以完成磨削进给,每往复一次或每次换向后,砂轮向工件垂直进给,直至将工件磨削到所需要的尺寸。
由于工作台是连续旋转的,所以磨削效率高,但不能磨削台阶面等复杂的平面。
(3)立轴柜台平面磨床砂轮的主轴与工作台垂直,工作台是矩形电磁吸盘,用砂轮的端面磨削平面。
这类磨床只能磨简单的平面零件。
由于砂轮的直径大于工作台的宽度,砂轮不需要作横向进给运动,故磨削效率较高。
(4)立轴圆台平面磨床砂轮的主轴与工作台垂直,工作台是圆形电磁吸盘,用砂轮的端面磨削平面。
磨削时,圆工作台匀速旋转,砂轮除作高速旋转外,定时作垂向进给。
(5)双端面磨床该磨床能同时磨削工件两个平行面,磨削时工件可连续送料,常用于自动生产线等场合。
2、平面磨削的形式以砂轮工作表面的不同,平面磨削可分为周边磨削、端面磨削以及周边一端面磨削三种方式。
①周边磨削:又称圆周磨削,是用砂轮的圆周面进行磨削。
卧轴的平面磨床属于这种形式。
②端面磨削:用砂轮的端面进行磨削。
立轴的平面磨床均属于这种形式。
③周边一端面磨削:同时用砂轮的圆周面和端面进行磨削。
磨削台阶面时,若台阶不深,可在卧轴矩台平面磨床上,用砂轮进行周边一端面磨削。
平磨磨削知识

平面磨削余量的选择 对于我们的立磨,一般磨削长度1570mm,加工宽度200mm,对于粗加工(零件在装置中未经校准)加工余量选择0.6,公差0.15左右相 对合适;对于精加工(零件在装置中经校准)加工余量选择0.4,公差0.15左右相对合适.实用加工工艺手册(陈宏钧)-按照P1211表11184-187 总结经验: 说明:数值为单面加工余量;热处理零件余量乘以1.2修正系数。 一、往复式平面磨ap(圆周磨削、单行程mm,工作台往复行程切削深度乘2) 粗磨切削深度 影响因素:砂轮宽度、纵向进给量、工件速度、工件材料、砂轮直径、工作台充满系数 最大极限深度,不准超过0.066*1.6*1.17=0.12(条件最为宽松时,指铸铁、砂轮窄32直径大600、工件速度低6m/min,纵向进给量比 小0.5、工作台充满系数低0.2) 最小极限深度,不得低于0.0059*0.7*0.71=0.003(条件最为苛刻时,指耐热铁、砂轮宽100直径小320、工件速度高20m/min,纵向进 给量比大0.8、工作台充满系数高1.0) 我们“一般情况切削深度选择0.017左右”(材料淬火或非淬火钢、砂轮处于bs=40-60宽直径450、工件速度12m/min,纵向进给量比大 0.6、工作台充满系数高0.5) 精磨切削深度 影响因素:砂轮宽度、纵向进给量、工件速度、工件材料、砂轮直径、工作台充满系数、加工精度及余量。 最大极限深度,不准超过0.086*2.5*1.75*1.6=0.602(条件最为宽松时,指铸铁、砂轮窄32直径大600、工件速度低5m/min,纵向进给 量小8m/min、工作台充满系数低0.2、加工精度0.08、加工余量0.7) 最小极限深度,不得低于0.0035*0.4*0.56*0.71=0.0006(条件最为苛刻时,指耐热铁、砂轮宽100直径小320、工件速度高20m/min, 纵向进给量比大0.8、工作台充满系数高1.0、、加工精度0.02、加工余量0.12)
不锈钢的平面磨床磨削方法
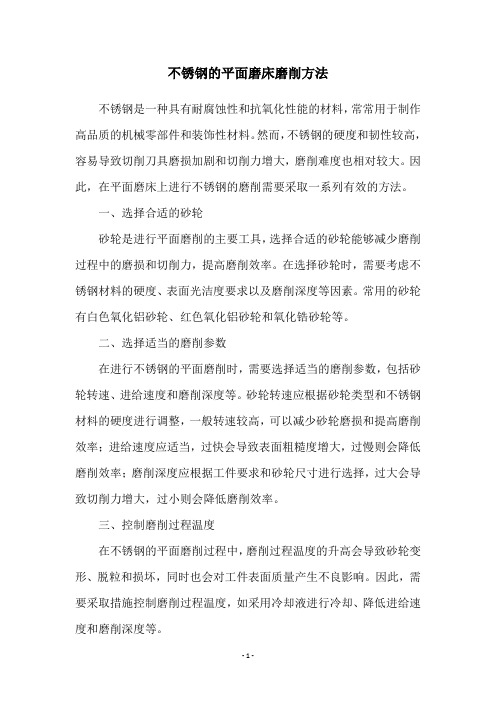
不锈钢的平面磨床磨削方法
不锈钢是一种具有耐腐蚀性和抗氧化性能的材料,常常用于制作高品质的机械零部件和装饰性材料。
然而,不锈钢的硬度和韧性较高,容易导致切削刀具磨损加剧和切削力增大,磨削难度也相对较大。
因此,在平面磨床上进行不锈钢的磨削需要采取一系列有效的方法。
一、选择合适的砂轮
砂轮是进行平面磨削的主要工具,选择合适的砂轮能够减少磨削过程中的磨损和切削力,提高磨削效率。
在选择砂轮时,需要考虑不锈钢材料的硬度、表面光洁度要求以及磨削深度等因素。
常用的砂轮有白色氧化铝砂轮、红色氧化铝砂轮和氧化锆砂轮等。
二、选择适当的磨削参数
在进行不锈钢的平面磨削时,需要选择适当的磨削参数,包括砂轮转速、进给速度和磨削深度等。
砂轮转速应根据砂轮类型和不锈钢材料的硬度进行调整,一般转速较高,可以减少砂轮磨损和提高磨削效率;进给速度应适当,过快会导致表面粗糙度增大,过慢则会降低磨削效率;磨削深度应根据工件要求和砂轮尺寸进行选择,过大会导致切削力增大,过小则会降低磨削效率。
三、控制磨削过程温度
在不锈钢的平面磨削过程中,磨削过程温度的升高会导致砂轮变形、脱粒和损坏,同时也会对工件表面质量产生不良影响。
因此,需要采取措施控制磨削过程温度,如采用冷却液进行冷却、降低进给速度和磨削深度等。
四、定期更换砂轮
砂轮的磨损程度会影响磨削效率和工件表面质量,因此需要定期更换砂轮,以保证磨削效率和磨削质量。
同时,在更换砂轮时也需要注意选择合适的砂轮规格和类型。
不锈钢的平面磨床磨削方法需要综合考虑多种因素,采取有效的措施进行控制和调整,方可达到理想的磨削效果和工件表面质量。
平面磨床磨削时的三个阶段
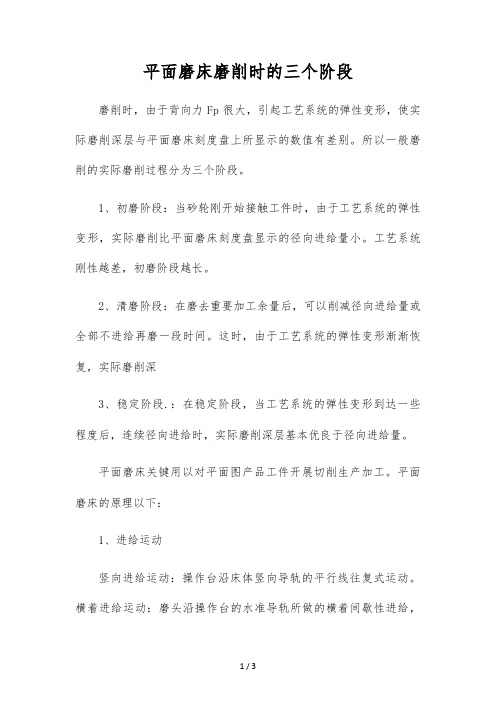
平面磨床磨削时的三个阶段磨削时,由于背向力Fp很大,引起工艺系统的弹性变形,使实际磨削深层与平面磨床刻度盘上所显示的数值有差别。
所以一般磨削的实际磨削过程分为三个阶段。
1、初磨阶段:当砂轮刚开始接触工件时,由于工艺系统的弹性变形,实际磨削比平面磨床刻度盘显示的径向进给量小。
工艺系统刚性越差,初磨阶段越长。
2、清磨阶段:在磨去重要加工余量后,可以削减径向进给量或全部不进给再磨一段时间。
这时,由于工艺系统的弹性变形渐渐恢复,实际磨削深3、稳定阶段.:在稳定阶段,当工艺系统的弹性变形到达一些程度后,连续径向进给时,实际磨削深层基本优良于径向进给量。
平面磨床关键用以对平面图产品工件开展切削生产加工。
平面磨床的原理以下:1、进给运动竖向进给运动:操作台沿床体竖向导轨的平行线往复式运动。
横着进给运动:磨头沿操作台的水准导轨所做的横着间歇性进给,在操作台往复式行程布置结束时开展。
2、数控车床的主运动:切削砂轮由同是安裝在磨头外壳内的电动机立刻推动转动,它是工具磨床的行为主体运动。
3、竖直进给运动由磨头双翘板沿数控车床立杆的竖直导轨挪动,用于调整磨头的多少部位,操纵切削深层进给。
数控车床的各类运动除主轴的转动运动外,别的进给运动均由液压传动系统系统软件来完成,与此同时还可以手动式开展。
实际操作注意事项,精准定位数控车床应在大运动室内空间外再预埋300mm之上,各个支脚螺钉告急,台眼前后及上下水准在0.04/1000mm之内。
(安裝变频调速器的规定需高些)每三个月检查,调整工作中橱柜台面水准,告急各个支脚螺钉。
导致平面磨床主轴轴向颤抖超差的关键原因有:1、主轴撞击或者承受力形变。
2、主轴的适用轴瓦的内孔同心度超差。
磨头主轴能够沿双翘板的水准导轨可作横着进给运动,该双翘板还能够沿立杆的导轨做竖直挪动,用于调整磨头的竖直部位及进行竖直进给运动。
在工具磨床的工作中台子上一般安裝电磁铁吸盘用以上卡具备铁磁性材料的零件,还可以拆卸电磁铁吸盘,改装别的工装夹具或在工作中台子上立刻上卡待生产加工的产品工件。
平面磨削方法

2).用圆柱角尺找正垂直面
把圆柱角尺和工件都放在平板上,使其靠近, 观察间隙,然后在工件下面垫纸,使间隙均匀.再 磨削上平面.
圆 柱 角 尺
工件 垫纸 平板
3).用专用百分表座找正垂直面
1.先把圆柱角尺和百分表座放在平板上,让百分表 座定位点顶住工件下部最大外圆处,表头接触工 件的上部,调到零. 2.圆柱角尺移走,把工件放到原位置,看百分表上的 读数. 3.然后在工件下面垫纸 ,使百分表上读数几乎接近 零.然后再磨削上平面.
作业:
第129页:1.2.3.题
百分表
工件 圆柱角尺
垫纸
百分表座定位点
注意事项:
1.用阶台砂轮磨削法时机床的刚性必须符合要求. 2.用精密平口钳,精密角铁,导磁直角铁.精密V型架之前先了解一 下夹具的精度,磨削之前找正夹具侧面要与工作台纵向方向平行, 然后再找正工件的位置. 3.用垫纸法时,要用很薄的油光纸.
三、平面磨削方法的应用
2.用精密角铁装夹
特点:精密角铁具有两个互相垂直的工作平面,它的垂直 度为0.005毫米,可达到较高的加工精度. 适用:适合装夹大小重量都比角铁小的导磁或非磁性垂 直面工件.
3.导磁直角铁装夹
特点:导磁角铁有四个面互相垂直,黄铜把纯铁隔开,距离与 电磁吸盘一样,磁力线可以延伸到上面. 适用:磨削不易找正的小零件,或比较光滑的工件.
砂轮
工件
2.切入磨削法 定义:磨削时,砂轮不作横向进给, 工作台在纵向行程的终了 砂轮垂直进给一次.把所有的余量磨完. 特点:生产效率低,表面质量差. 适用:适合磨削比较狭窄的工件.
砂轮
工件
3.阶台砂轮磨削法
定义:是按工件余量的大小,将砂轮修
整成阶梯形,大大提高垂直进给量 . 特点:效率高,磨削效果好.
凸轮磨削产生小平面问题分析及处理
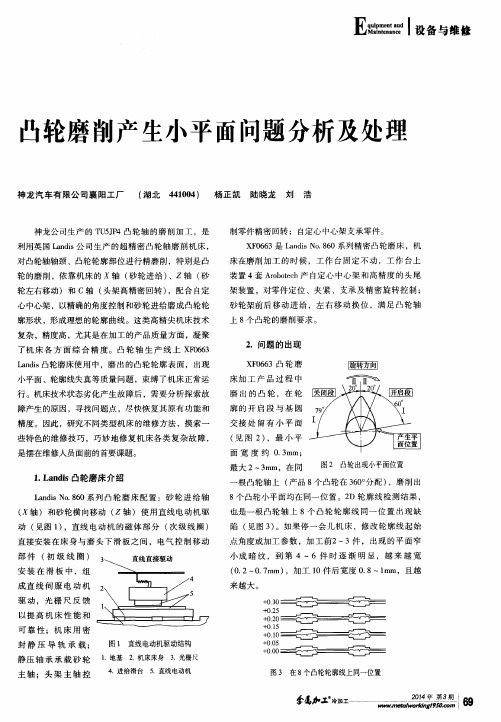
来越大。
以提 高 机 床 性 能 和 可 靠 性 ;机 床 用 密 封静压 导轨 承载;
图 1 直线 电动机驱动结构
+ o 2 0 = 兰三 二;车 = = = :—: = 三三兰宅 二 =
了机 床 各 方 面 综 合 精 度 。凸 轮 轴 生 产 线 上 X F 0 6 6 3
X F 0 6 6 3 是L a n d i s N o . 8 6 0系列 精密 凸轮磨 床 ,机 床 在磨 削加 工 的 时候 ,工 作 台固 定 不 动 ,工 作 台上
装 置 4套 A r o b o t e c h产 自定 心 中心架 和 高 精度 的头 尾
q u i p me n t a n d
I 设 备 与 维 修
凸轮磨削产生小平面问题分析及处理
神龙汽车有 限公司襄 阳工厂 ( 湖北 4 4 1 0 0 4 ) 杨正 凯 陆晓龙 刘 浩
神龙公 司生 产 的 T U 5 J P 4凸轮 轴 的磨 削 加 工 ,是
制 零件 精密 回转 ; 自定 心 中心架支 承零 件 。
L a n d i s 凸轮磨床 使用 中,磨 出的 凸轮 轮廓 表 面 ,出现 小平面 、轮廓线失 真等 质量 问题 ,束缚 了机床 正常 运 行 。机 床技术状态 劣化 产生 故 障后 , 需 要 分析 探索 故
障产生 的原 因 ,寻找 问题 点 ,尽快 恢 复其 原有 功能 和
廓的开启 段 与基 圆 交 接 处 留 有 小 平 面
( 见 图 2) ,最 小 平 面宽 度 约 0 . 3 m m; 最大 2~3 mm,在 同 图2 凸轮出现小平面位置
第3章 常见表面加工方法-3平面加工

a) 图5-8 研磨用的平板 a)带槽平板
b)
b)光滑平板
研磨剂由磨料和研磨液调合而成。 磨料起切削作用,常用磨料有刚玉类和碳化硅类。 根据工件所要求的表面粗糙度选择不同粒度的磨料。 研磨液用来调合磨料,使磨粒均匀分布在研具表面, 也有冷却润滑的作用。常用研磨液有煤油、汽油和机油。 在研磨液中常加入硬质酸、油酸等化学活性物质,使工 件表面产生一层极薄、较软的氧化膜,从而加速研磨过 程,提高研磨质量。
4、各种导向平面,常采用粗刨—精刨—宽刃精刨(或刮研)。
5、单件小批量生产加工内平面(如方孔或花键孔),常采用粗插—精 插。粗插前须钻孔。 6、大批量生产中,加工技术要求较高的、面积不大的平面或内平面, 常采用拉削,以提高生产率。 7、有色金属零件刨削时容易扎刀,磨削时又易堵塞砂轮,均难以保证 质量,宜采用粗铣—精铣—高速精铣,有较高的生产率。
精刨 IT10~IT8 Ra=6.3~1.6
粗磨 IT10~IT8 Ra=6.3~1.6
宽刃精刨 IT7 Ra=1.6~0.4
刮研 IT7~IT6 Ra=0.8~0.4 研磨 IT5~IT3 Ra=0.1~0.008
精磨 IT6~ITT7~IT6 Ra=0.8~0.4
粗刨 IT13~IT11 Ra=50~12.5 粗车 IT13~IT11 Ra=50~12.5 半精车 IT10~IT8 Ra=6.3~1.6 初磨 IT11 Ra=12.5 粗铣 IT13~IT11 Ra=50~12.5 精铣 IT10~IT8 Ra=6.3~1.6 粗插 IT13~IT11 Ra=50~12.5 精插 IT10~IT8 Ra=6.3~3.2
七、研磨平面
研磨也是平面的光整加工方法之一,平面研磨能获 得和高的精度和很小的表面粗糙度。研磨后两平面间的 尺 寸 精 度 可 达 IT5~IT3 , 表 面 粗 糙 度 Ra 值 可 达 0.1~0.008μ m,平面度和直线度也有所提高。
平面磨削

平面磨削机械零件除了带有圆柱、圆锥表面外,还有若干平面组成,如零件底平面,零件上相互平行、垂直或成一定角度的平面。
这些平面所要求达到的技术要求主要是平面的平面度,平面之间的平行度、垂直度、倾斜度以及平面与其他要素之间的位置度,还有平面的表面粗糙度。
平面磨削就是在平面磨床上对这些平面进行加工,达到一定的要求,小型的平面工件也可在工具磨床上进行加工。
平面磨削后的表面精度一般可达IT7一IT6级,表面粗糙度达Ra0.63~0.16um,平行度误差在1000mm长度内为0.01mm。
任务一机床原理项目1平面磨床的结构M7130G/F型平面磨床是在M7130A型基础上经过改进的卧轴矩台平面磨床,也是较为常用的一种平面磨床之一(见图)。
下面就以M7130G/F为例介绍平面磨床的基本操作。
一、M7130G/F型平面磨床各部件名称和作用(一)床身床身1为箱型铸件,上面有V型导轨及水平导轨;工作台2安装在导轨上。
床身前侧的液压操纵箱上安装有垂直进给机构、液压操纵板等,用以控制机床的机械与液压转动。
电器按钮板上有电器控制按钮。
图M7130G/F平面磨床1—床身;2一工作台;3一磨头;4一滑板;5一立柱:6一电器箱;7一电磁吸盘;8一电钮板;9一液压操纵箱(二)工作台工作台2是一盆形铸件,上部有长方型台面,下部有凸出的导轨。
工作台上部台面经过磨削,并有一条T形槽,用以固定工作物和电磁吸盘。
在台面四周装有防护罩,以防止切削液飞溅。
(三)磨头磨头3在壳体前部,装有两套短三块油膜滑动轴承和控制轴向窜动的两套球面止推轴承,主轴尾部装有电动机转子,电动机定子固定在壳体上。
磨头3在水平有两种进给形式:一种是断续进给,即工作抬换向一次,砂轮磨头横向作一次断续进给,进给量1~12mm;另一种是连续进给,磨头在水平面燕尾导轨上往复连续移动,连续移动速度为0.3~3m/min,由进给选择旋钮控制。
磨头除了可液压传动外,还可作手动进给。
(四)滑板滑板4有两组相互垂直的导轨,一组为垂直矩形导轨,用以沿立柱作垂直移动;另一组为水平燕尾导轨,用以作磨头横向移动。
平磨磨削知识

我们“一般情况切削深度选择0.014左右”(材料淬火或非淬火钢、砂轮处于50-60宽直径450左右、工件速度10m/min,纵向进给量 20mm/st、工作台充满系数0.4、加工精度0.03、加工余量0.25) 二、回转式平面磨ap(端面磨削、单行程mm,工作台进给mm/r) 粗磨切削深度 影响因素:砂轮宽度、纵向进给量、工件速度、工件材料、砂轮直径、工作台充满系数。 最大极限深度,不准超过0.049*1.17*1.4=0.08(条件最为宽松时,指铸铁、砂轮窄32直径大600、工件速度低8m/min,纵向进给量比 小0.5、工作台充满系数低0.25) 最小极限深度,不得低于0.0039*0.7*0.71=0.002(条件最为苛刻时,指耐热铁、砂轮宽100直径小320、工件速度高30m/min,纵向进 给量比大0.8、工作台充满系数高1.0) 我们“一般情况切削深度选择0.021左右”(材料淬火或非淬火钢、砂轮处于50-60宽直径450左右、工件速度10m/min,纵向进给量 20mm/st、工作台充满系数高0.4、加工精度0.03、加工余量0.25),最合理的磨挺柱顶面粗磨计算为0.018,可以理解为粗磨余量0.6,在 30-35圈完成粗磨,粗磨旋转速度24r/min,单盘节拍实动时间应该为1.5分钟左右. 精磨切削深度 影响因素:砂轮宽度、纵向进给量、工件速度、工件材料、砂轮直径、工作台充满系数、加工精度及余量。 最大极限深度,不准超过0.067*2.5*1.75*1.6=0.47(条件最为宽松时,指铸铁、砂轮窄32直径大600、工件速度低5m/min,纵向进给 量小8m/min、工作台充满系数低0.2、加工精度0.08、加工余量0.7) 最小极限深度,不得低于0.0025*0.32*0.56*0.71=0.0003(条件最为苛刻时,指耐热铁、砂轮宽100直径小320、工件速度高40m/min, 纵向进给量大50、工作台充满系数高1.0、加工精度0.02、加工余量0.08) 我们“一般情况切削深度选择0.012左右”(材料淬火或非淬火钢、砂轮处于50-60宽直径450左右、工件速度15m/min,纵向进给量 20mm/st、工作台充满系数0.4、加工精度0.03、加工余量0.25),最合理的磨挺柱顶面计算为0.015,标准理解到加工余量0.4,在26圈完成 粗磨,粗磨旋转速度24r/min,单盘节拍实动时间应该为1分钟左右.
外圆和平面磨削时磨削力的计算公式

外圆和平面磨削时磨削力的计算公式磨削过程中的磨削力是指砂轮与工件之间的相互作用力,它是砂轮将工件材料去除的力量。
在外圆和平面磨削中,磨削力的计算涉及到很多因素,如切削速度、进给速度、切削深度、切削宽度、砂轮特性等,因此并没有一种普适的公式可以适用于所有情况。
下面将针对外圆和平面磨削中常见的一些情况进行力的计算和估算。
1.外圆内径磨削在外圆磨削中,砂轮与工件接触的长度为πd,其中d为工件直径。
当切削深度为a时,可将磨削力分解为切向力和径向力两个方向。
切向力的计算可以使用下面的公式:Ft = Kt ×ae × ν其中Kt为切向力系数,ae为切向力系数的修正值,ν为切削速度。
对于径向力的计算可以使用下面的公式:Fr = Kr × ae × ae × ν其中Kr为径向力系数,ae为于径向力系数的修正值,ν为切削速度。
2.平面磨削在平面磨削中,工件的尺寸通常为L×W×H,L和W分别为工件的长度和宽度,H为磨削后的高度。
切削深度为a时,磨削力可以分解为切向力和径向力两个方向。
切向力的计算可以使用下面的公式:Ft=Kt×a×W×ν其中Kt为切向力系数,a为切削深度,W为工件的宽度,ν为切削速度。
对于径向力的计算可以使用下面的公式:Fr=Kr×a×L×ν其中Kr为径向力系数,a为切削深度,L为工件的长度,ν为切削速度。
需要注意的是,上述公式中的切削力系数Kt和Kr以及修正值ae的具体数值需要根据具体的工艺条件和机械设备来确定,一般需要通过试验和经验来进行估算和调整。
此外,还有一些其他因素也会对磨削力产生影响,比如刃口形状、切削液的使用以及砂轮磨损等。
因此,在实际应用中,还需要综合考虑这些因素来准确计算磨削力。
- 1、下载文档前请自行甄别文档内容的完整性,平台不提供额外的编辑、内容补充、找答案等附加服务。
- 2、"仅部分预览"的文档,不可在线预览部分如存在完整性等问题,可反馈申请退款(可完整预览的文档不适用该条件!)。
- 3、如文档侵犯您的权益,请联系客服反馈,我们会尽快为您处理(人工客服工作时间:9:00-18:30)。
湖南省娄底技师学院
实习教学教案
教师姓名:刘联盟
一、任务引入
机器零件除了圆柱、圆锥表面外,还经常由各种平面图组成。
例如V型铁的两侧面,如图1所示:
钳工加工小型工件之前,有时需要用V型块侧面作靠山来划线。
该侧面必须要有一定的表面粗
糙度要求和平面度要
求,如果表面粗糙度和
平面度不符合要求,则
会影响工件已加工表
面质量和划线精度。
所
以,为了加工出合格的
零件,须理解平面磨削
的形式、特点;通过实践操作要掌握平面磨削的操作步骤、工件的装夹方法、平面精度的检验以及工件的常见缺陷形式。
本次课题的任务是磨削加工矩形工件的二面,如图2
二、任务分析
图2为垫铁工件,材料45钢,经淬火硬度40—45HRC,厚度10mm,需要磨削表面的平面图度为0.015mm,表面粗糙度为Ra0.8um。
平面加工的方法比较多,常见的平面图铣削加工。
对于淬硬材料用铣削方式加工不合适,是由于刀具材料的硬度比加工材料的硬度低;所以常用磨削的加工方法,而且经磨削
过的工件表面质量比铣削加工质量高。
三、相关知识
1、平面磨削的形式圆周磨和端面磨
1)圆周磨:利用砂轮的圆周面进行磨削。
工件与砂轮的接触
面积小,发热少,排屑与
冷却情况好,因此加工精
度高,但生产率低,在单
件小批生产中应用较广。
2)端面磨:利用砂轮的端面进行磨削。
1)砂轮轴立式安装,刚性好,可采用较大的切削用量,而且砂轮与工件的接触面积大,故生产率高。
2)但精度较周磨差,磨削热较大,切削液进入磨削区较困难,易使工件受热变形,且砂轮磨损不均匀,影响加工精度。
平面磨削常作为刨削或铣削后的精加工,特别是用于磨削淬硬工件,以及具有平行表面的零件(如滚动轴承环、活塞环等)。
经磨削两平面间的尺寸公差等级可达IT6~IT5级,表面粗糙度R a值为
0.8~0.2μm。
2、平面磨床的磨削方法
在平面磨床上磨削平面有圆周磨削(图1—14a,c)和端面磨削(图1—14b,d)两种形式。
卧轴矩台或圆台平面磨床的磨削属圆周磨削,砂轮与工件的接触面积小,生产效率低,但磨削区散热、排屑条件好,因此磨削精度高。
卧轴矩台平面磨床磨削平面的主要方法如下:
1).横向磨削法(图1—16)
每当工作台纵向行程终了时,砂轮主轴作一次横向进给,待工件表面上第一层金属磨去后,砂轮再按预选磨削深度作一次垂直进给,以后按上述过程逐层磨削,直至切除全部磨削余量。
横向磨削法是最常用的磨削方法,适于磨削长而宽的平面,也适于相
同小件按序排列,作集合磨削。
2).深度磨削法(图1—17)
先粗磨将余量一次磨去,粗磨时的纵向移动速度很慢,横向进给量很大,约为(3/4—4/5)T(T为砂轮厚度)。
然后再用横向磨削法精磨。
深度磨削法垂直进给次数少,生产效率高,但磨削抗力大,仅适于在刚性好、动力大的磨床上磨削平面尺寸较大的工件。
3).阶梯磨削法(图1—18)
将砂轮厚度的前一半修成几个阶台,粗磨余量由这些阶台分别磨除,砂轮厚度的后一半用于精磨。
这种磨削方法生产效率高,但磨削时横向进给量不能过大;由于磨削余量被分配在砂轮的各个阶台圆周面上,磨削负荷及磨损由各段圆周表面分担,故能充分发挥砂轮的磨削性能。
由于砂轮修整麻烦,其应用受到一定限制。
图1-16 横向磨削法磨平面图1-17 深度磨削法磨平面
图1-18 阶梯磨削法磨平面
3、工件的装夹
平面磨削的装夹方法应根据工件的形状、尺寸和材料而定,可用电磁吸盘装夹、相邻面夹持及粘附装夹。
4、平面磨削的特点
砂轮在磨削时具有极高的圆周速度,一般为35m/s左右,高速磨削时可达50~85m/s。
砂轮与工件的接触面较小,磨削时的冷却和排屑条件较好,产生的磨削力和磨削热也较小,因此,有利于提高工件的磨削精度。
这种磨削方法适用于精磨各种平面零件。
但因磨削时要间断的横向进给来完成整个工作表面的磨削,所以生产效率低。
在磨削时除了对工件表面有切削作用外,还有强烈的摩擦,磨削区域的温度可高达400—1000℃,容易引起工件表面退火或烧伤。
5、电磁吸盘及其使用
电磁吸盘是最常用的夹具之一,凡是由钢、铸铁等材料制成的有平面的工件,都可用它装夹。
1)电磁吸盘的结构原理电磁吸盘是根据电的磁效应原理制成的。
在由硅钢片叠成的铁心上绕有线圈,当电流通过线圈,铁心即被磁化,成为带磁性的电磁铁,这时若把铁块引向铁心,立即会被铁心吸住。
当切断电流时,铁心磁性中断,铁块就不再被吸住。
电磁吸盘的外形有矩形和圆形两种,分别用于矩形工作台平面磨床和圆形工作台平面磨床
2)使用电磁吸盘装夹工件有以下特点
①工件装卸迅速方便,并可以同时装夹多个工件。
②工件的定位基准被均匀地吸紧在台面上,能很好地保证平行平面的平行度
公差。
③装夹稳固可靠。
3)使用电磁吸盘时的注意事项
①关掉电磁吸盘的电源后,有时工件不容易取下,这是因为工件和电磁吸盘上仍会保留一部分磁性(剩磁),这时需将开关转到退磁位置,多次改变线圈中的电流方向,把剩磁去掉,工件就容易去下。
②从电磁盘上取底面积较大的工件时,由于剩磁以及光滑表面间粘附力较大,不容易取下,这时可根据工件形状用木棒或铜棒将工件板松后再取下,切不可用力硬拖工件,以防工作台面与工件表面拉毛损伤。
③装夹工件时,工件定位表面盖住绝缘磁层条数应尽可能多,以便充分利用磁性吸力。
小而薄的工件应放在绝缘层中间,并在其左右放置挡板,以防止工件松动。
装夹高度较高而定位面积较小的工件时,应在工件四周上靠上面积较大的挡板,其高度略低于工件,这样可避免因吸力不够而造成工件翻倒。
④电磁吸盘的台阶要经常保持光洁,如果台面上出现拉毛,可用三角油石或细砂纸抛光。
如果台面使用时间长,表面上划纹和细麻点较多,或者有某些变形时,可以对电磁吸盘台面作一次修磨。
修磨时电磁吸盘应接通电源,使它处于工作状态。
磨削量和进给量要小,冷却要充分,待磨光至无火花出现即可,应尽可能减少修磨次数,以延长其使用寿命。
⑤工作结束后,应将吸盘台面擦净。
四、操作实习。