结晶器铜管镀层参数一览表
连铸结晶器铜管内腔镀硬铬技术解析

连铸结晶器铜管内腔镀硬铬技术解析连铸结晶器铜管加工后,要对内腔进得表面处理,目前国内结晶器铜管的生产厂家已充分认知结晶器铜管R角镀层厚度与质量的重要性,均已不再使用原始的普通镀铬工艺,都是对标准液里加入添加剂后提高镀层质量与速度。
目前国内铜管生产厂家使用较多的有广州维恩;合肥安诚;南京首创;烟台DW-32的添加剂,其添加剂的组成成份前三家都大同小异样,但烟台DW-032对于内R角镀层明显高于其他几家。
在平面镀铬层厚度10丝,角部厚度可达6-8丝,完全能满足结晶器铜管对镀层质量的要求。
但同样优秀的添加剂,同样的工艺,很多的铜管生产厂家镀出的产品质量却有着不同的档次,这关健就在于其镀铬工艺/现场管理/阳极的设计与加工/工装模具的设计/电镀设备等各条件的不一样,下面就结晶器铜管内壁镀硬铬,如何取得最佳效果进行简明的阐述:一、象形阳极。
阳极的加工技术是目前很多结晶器生产厂家没能完全掌握的。
很多的厂家都是使用铅皮包铁芯,这是无法保证电镀质量的。
目前最好的方法是整体浇铸(内置芯材)后防形机械加工出整体的设计尺寸与四尖角,这样能完保保证阳极的尺寸与形位精度,这个防形装置很容易在龙门刨床上设置出来。
如果不能用防形刨,也可以对比标准样板在压力机或自行设计的工装上把弧度压出来。
同时阳极材料在浇铸时必须加点锡,导电部位也要设计合理。
目前大多数结晶器厂家都在使用该方法。
烟台电镀技术研究所结合结晶器铜管的电镀特点,研究新的阳极系统。
新阳极完全打破原来的设计思路,导电均匀,配合DW-32添加剂可以实现R角部镀层厚度同平面镀层厚度一致。
且结合力好。
二、间距结晶器铜管镀硬铬不同于其它工件的电镀,有其形状的特殊性。
其面间距与间距要选择合理合适,目前一般面间距都在15-20之间,不能超过20,否则角部薄相切处比平面厚很多。
三、电流拥有良好的槽液状态和优良的添加剂,正常电流可以开到40-45A/dm2之间,冲击电流可以加大三分之一。
结晶器铜管镀铬添加剂试验总结

结晶器铜管镀铬添加剂试验总结试验添加剂: 维恩,安美特,合肥,南京,南京理工大学,天津镀铬添加剂,亚泰,上海普莱德,Dw-09镀铬添加剂乐思试验单位:济南东方试验目的:综合考察结晶器铜管镀铬添加剂各项性能。
提高结晶器铜管镀铬的各项性能,同时,减少处理镀槽次数。
试验方法:在1000升的小镀铬槽中,电镀结晶器铜管。
实验准备:1,结晶器铜管10件。
150*150*900 R62,铅阳极制作(利用旧阳极)含锡大于10% 独立设计铅阳极。
新阳极设计思路独特,新颖,是结晶器铜管阳极设计的一次革命。
3,槽液准备铬酐250公斤,硫酸,dw-09结晶器铜管耐磨镀铬专用添加剂,20公斤,铬雾抑雾剂。
新配制镀液。
4,吊具制作(利旧),极杠等5,加热管加热玻璃加热管6只,也可用钛加热管但贵些。
2KW也可用蒸汽加热。
6,镀槽设计尺寸1000*1200*1000,,采用厚度16pvc焊制。
或利旧。
7,整流器5000A 高频开关电源8,测试平均厚度,电流效率,硬度,分散能力,深度能力,微裂纹数。
阳极腐蚀程度。
9.槽液变化2月10日开始试验,电镀前分析,电镀后分析,对比。
空白镀液配制,分别加入以上各种添加剂。
(添加剂从市场购买,真伪无法判别)大约电镀10批,10件,每种添加剂一件。
Dw-09结晶器铜管镀铬添加剂简介:通过实验Dw-09结晶器铜管镀铬添加剂为国内最好的添加剂。
可以加入铬雾抑制剂,不起针孔。
参照德国维恩,日本大和,乐思,安美特,南京理工大学,沈阳理工大学,西安理工大学,山东建筑大学及国外专利研制而成。
赫尔槽试验完成。
性能优异。
小槽试验各项性能,优异。
综合性能好,微裂纹900条以上,硬度结晶器铜管平面大于900HV,角部大于1000,同时铬层不发脆。
耐盐雾192小时以上。
电镀2小时,电流2500A,冲击电流5000A,平面厚度大于10丝,角部8丝以上,整个铜管无烧焦现象,电流效率达30%。
以上数据,来自铜管破坏试验。
方坯结晶器铜管电镀Ni-co,cr复合镀层

方坯结晶器铜管电镀Ni- Co+ Cr 复镀层技术(简称复合镀技术)方坯结晶器铜管电镀Ni- Co+ Cr 复镀层技术(简称复合镀技术)为了提高产品的市场竞争力, 各钢铁企业从生产的各个环节进行技术开发、技术改造, 力求在生产的每一个环节上提高设备的工作效率, 降低生产成本, 确保产品的质量,使企业的经济效益最大化。
连铸是炼钢生产的重要环节, 连铸结晶器是连铸机的心脏, 结晶器质量的好坏在相当大的程度上影响着连铸机的生产效率、连铸进程的稳定性和连铸坯质量, 直接关系到炼钢生产和经济效益。
连铸小方坯结晶器铜管是方坯结晶器最重要的组件, 也是经常需要更换的部件。
济南东方结晶器有限公司开发的方坯结晶器铜管电镀N i- Co+ Cr 复镀技术, 能大幅度地提高方坯结晶器铜管的使用寿命, 提高连铸机的作业效率和连铸技术的水平, 推动连铸技术的发展完善; 可以把结晶器铜管在连铸生产中的成本降到1. 0 元之内, 有效地降低连铸生产成本, 提高产品的竞争力。
在连铸生产中, 影响结晶器铜管质量的有以下两个关键指标: 一是铜管内腔锥度曲线, 另一个则是铜管内表面镀层。
目前, 国内普遍采用的是结晶器铜管内表面电镀硬铬, 由于铬和铜的收缩比差别较大, 影响了两者之间的结合力, 也直接制约了结晶器铜管的使用寿命。
因此, 研究开发结晶器铜管新镀层是提高结晶器铜管使用寿命的关键。
N i- Co 合金镀层与铜管有很好的结合力,在较高的温度下有较高的硬度和耐磨性, 表面套镀一层铬, 可以解决镀层脱铬问题及镀铬层的种种影响, 起到抗磨损、保护铜管的作用, 从而大大提高结晶器铜管的使用寿命。
历尽艰辛终结硕果烟台电镀技术服务部同济南东方结晶器有限公司开发结晶器铜管内表面采用电镀Ni- Co+ Cr 复合镀层工艺技术。
从2001 年4 月开始, 他们进行电镀Ni- Co+ Cr 复合镀层的120mm2 方坯结晶器铜管的连铸试验, 先后历时一年时间、分6批进行了电镀工艺试验。
结晶器铜管内壁镀硬铬流镀技术应用

结晶器铜管内壁镀硬铬流镀技术应用摘要:概述了结晶器铜管内壁镀硬铬流镀技术的应用情况,讲述了结晶器铜管内壁镀硬铬流镀技术的基本原理,操作要点。
通过与传统槽式电镀的比较,表明了结晶器铜管硬铬流镀技术的主要效益指标和技术指标有了显著的改善,符合电镀企业推行清洁生产管理的趋势,有显著的环境保护和经济效益方面的优势,具有较高的实用推广价值。
关键词:结晶器铜管;流镀技术;环境保护;经济效益前言当前钢铁连铸结晶器铜管内壁电镀硬铬层的主要方法是传统的槽式电镀方法,就是通过挂具的固定及连接支撑作用将铜管和阳极组合起来,整体挂到镀槽中进行电镀,通常称为槽式镀(浸入式电镀),其主要优点是电镀设备简单,设备主体就是直流电源和镀槽,生产线投资低,易于建设,所以这种电镀方法在过去获得广泛应用,到目前,也有很多企业仍在用。
槽式镀的缺点也非常显著,主要有:①铬酸酐利用率低,一般在30%左右,主要是因为挂具、阳极、工件的带出、槽边排风、镀液寿命短造成。
②电流效率低,一般在15`18%③能耗高,镀层厚度0.1mm,平均每平方分米耗电1.14kwh④劳动强度大⑤环境污染风险大⑥综合成本高,镀层厚度0.1mm,平均每平方分米67元左右。
综合这些优缺点情况,目前各相关企业都在想办法探索新的结晶器铜管电镀硬铬的技术,克服传统槽式镀的缺点。
大山表面处理有限公司,经过多年的探索应用,探索出了在槽外完成结晶器铜管内壁镀铬的装备及工艺,通常称为流镀,在2018年~2022年期间,先后投入800多万,大山表面处理有限公司完成了结晶器铜管内壁镀铬由传统的槽式镀向流镀设备及工艺技术的升级。
1.流镀系统基本原理结晶器铜管内壁镀铬流镀设备及操控原理,如图1所示:图1:结晶器内壁镀硬铬流镀设备原理图如图1所示,流镀设备系统主要有计算机、储液槽、电镀电源、输液泵、气动阀、温控装置、液位监控装置、三价铬电解装置等组成,整个流镀设备系统由计算机进行控制。
1.1温度控制:根据电镀硬铬工艺要求,在计算机上将温度设定在55±2℃,计算机将指令发送到温控系统上(图1中红色矩形区域内),温控系统将执行计算机指令,对镀液进行加温或降温工作。
连铸机最佳结晶器参数

T=——————
y1L
或
100(y2-y1)
T=—————
y2L
式中y2—结晶器顶部两相对面间的距离,mm
y1—结晶器底部两相对面间的距离,mm
L—结晶器长度,m
单锥度结晶器常用的锥度为0.6~0.7%/m,140~150mm小方坯采用的最大锥度为0.9%/m
锥度太小容易产生偏离角纵裂,锥度太大会增加拉坯阻力和结晶器磨损。
1vc
(8)负滑动时间tn/s(tn=—cos-1——)
pfpfs
0.12~0.15
(9)结晶器导前/mm
(结晶器导前=ssin(pftn)-vctn)
3~4
(10)水质(即总硬度)/%
<0.0005,管壁上没有沉积物
(11)水缝宽度/mm
3~5
(12)是否测量结晶器内型尺寸变化
是
结晶器锥度T(%/m)为
如果用对高碳钢合适的锥度来浇低碳钢时,低碳钢铸坯就可能粘结在结晶器内,引起横向凹陷和横向裂纹。在浇铸时铸坯颤动,就表明铸坯粘结在结晶器内。
连铸机小方坯最佳结晶器参数
(1)铜的品种
P-Cu,Ag-Cu,Cr-Zr-Cu
(2)锥度
双锥度或多锥度
(3)壁厚/mm
13(100-150mm方),20(200mm方)
(4)内角半径/mm3Fra bibliotek4(5)液面距结晶器上口/mm
100~150
(6)水速/(m·S-1)
>10~11
(7)结晶器铜管支撑
4面或顶底
结晶器铜管镀铬层厚度标准

结晶器铜管镀铬层厚度标准
1. 国家标准和行业标准,不同国家和行业对于镀铬层的厚度标
准可能会有不同的规定,这些标准通常由相关的标准化组织或行业
协会制定,以确保产品质量和安全性。
2. 使用环境和要求,镀铬层的厚度标准通常会根据产品的使用
环境和要求来确定。
例如,对于结晶器铜管这样的产品,如果需要
在潮湿或腐蚀性环境中使用,镀铬层的厚度可能会相对较厚,以增
强产品的耐腐蚀性能。
3. 工艺和成本考虑,制定镀铬层厚度标准时,还需要考虑到镀
铬工艺的可行性和成本因素。
通常会进行工艺优化和成本效益分析,以确定最合适的镀铬层厚度。
总的来说,结晶器铜管镀铬层厚度标准是一个综合考虑产品要求、行业标准、使用环境和成本等因素的结果。
具体的厚度标准需
要根据产品的具体情况和要求来确定,并且需要符合相关的国家标
准和行业规定。
结晶器铜管镀铬阳极种类及形状对镀层及通钢量的影响

结晶器铜管镀铬阳极种类及形状对镀层及通钢量的影响结晶器铜管镀铬时,最早使用纯铅阳极,导电性一般,需经常刷洗才能导电。
之后使用铅锡合金阳极,导电性好些,不用频繁刷洗阳极,阳极溶解物明显减少。
镀铬时使用的阳极材料有DSA钛阳极(贵金属氧化涂层钛阳极)pbsn(铅锡),石墨,钛基二氧化铅电极,这些材料都有能力把铬离子氧化成铬酸离子,而使用不溶性钛阳极时,阳极的氧化过电位比铅电极约低450mv,节约电能消耗.同时钛阳极可以大电流密度运行,使用寿命长,铬镀层与基体结合牢固,表面光亮洁净.涂层钛阳极又称为尺寸稳定性阳极DSA(dimensionally stable anode),DSA通常是在起骨架和导电作用的金属基体上刷涂或者是滚涂一层或者多层的活性涂层氧化物,所以也被称为金属涂层电极[1]。
钌系尺寸稳定阳极析氯催化活性高,被大量的用在氯碱工业和氯酸盐工业中;铱系尺寸稳定阳极具有高活性及阳极耐腐蚀稳定性,常被用于酸性介质中析氧电催化材料[1,2]。
钛基DSA阳极自被发现以来由于其阳极材料环保、尺寸稳定性好、无二次污染、基体可以重复利用、涂层可修复等优点受到人们的广泛关注,随着其不断的发展已经广泛用于电镀工业、废水处理、氯碱工业等多个领域。
钛基IrO2涂层阳极在酸性析氧环境中具有良好的电催化活性和稳定性,而且在电解过程中IrO2的溶解相当小可以忽略,不会对镀液产生污染,寿命长,而且Ti基体可以重复利用,涂层可以修复。
研究发现,IrO2涂层阳极在酸性溶液中表现出优于其他贵金属氧化物涂层的电催化活性和稳定性,但和高电流密度、高温介质条件下其使用寿命并不理想,但若与惰性组元TiO2,SnO2,Ta2O5和Nb2O5组合起来使用则可以有效地增加其使用寿命。
当和Ta2O5结合使用时,可使得涂层和基体的结合稳定,涂层电解消耗速率减小,而且还可以提高电流密度,即使是在较高的电流密度下也具有较长的使用寿命。
六价铬电镀工艺中通常采用铅锡合金电极进行电镀,在电镀过程中表面发生析氧反应;但在使用中析氧电位高,而且在使用过程容易在阳极表面生成一层导电性很差的铬酸铅膜,使得电镀过程中槽压较高;另外由于膜层和基体间的应力作用以及气体和溶液对阳极表面冲刷作用导致该阳极表面有颗粒进入到镀液中污染镀液并使阳极尺寸发生变化,这无疑增加了成本和能耗。
结晶器铜板各种镀层特性一览表

结晶器铜板各种镀层特性一览表在正常冷却条件下,结晶器内壁工作温度为250~350℃ ,结晶器铜板应具有良好的导热性和抗变形能力,有较高的高温强度、表面精度和耐磨性。
Ag —Cu 和Cr —Zr —Cu 板使用寿命优于脱氧铜和紫铜。
结晶器铜板镀层的作用是:避免结晶器铜板产生星状裂纹;防止铜渗入铸坯;提高润滑性和耐磨性。
目前主要采用Ni+Cr 和Ni-co ,Co-Ni Ni-Co-Fe 系镀层及其他开发的新合金镀层。
镀层种类镀层特性特点主成分名称硬度高温磨损量(Hv )(mg) 电镀Cr 系Cr9002硬度高,耐磨损性强。
E-Cr40015不出现Cr 特有的细裂纹,耐腐蚀性强。
Ni 系Ni200 60耐热、耐腐蚀性强。
可厚电镀(电铸)。
母模的复制性好。
Ni 合金650 18硬度高,耐磨损性强。
Co 系Co-Ni200 13与Ni 、Ni 系合金相比,其高温耐磨损性更优越。
K-2200 13Co-Ni 的延性(耐裂纹性)有改善。
Ni-Co-Fe系镍钴铁合金 700 13硬度高,耐磨损性强。
其高温耐磨损性更优越热喷镀NiCr 系MMS-1650 5耐磨损性超好。
BK-2400 4保持高耐磨损性的同时,耐裂纹性及耐粘钢性得以改善。
几种结晶器镀层的特点及使用情况解析镀铬层硬度较高,化学稳定性好,缺点为:安全厚度受限制,镀层无论厚薄都有裂纹存在;随温度升高硬度迅速降低,与铜结合时,其线膨胀系数、导热率相差太大,镀层容易在高温状态起皮剥落[ 。
因此,镀铬层影响结晶器寿命,其使用受到一定的限制。
镀镍层化学稳定性较好,封闭能力很强,且能镀至3—8 mm。
但其硬度(200 HV左右)经不起连铸钢坯的磨损,因此镀层寿命不高;采用镀厚镍的结晶器,使用寿命相对延长。
在铜板表面先镀l一4 mm的镍,经加工后再镀铬。
镍起中间过渡作用,可提高铬层与基体的结合强度,而外表面硬铬提高其耐磨性。
虽镀层性能。
如硬度和耐磨性可以达到要求,网状裂纹可以消除,结晶器寿命得到延长,但双镀层工艺相对复杂,由于铬与镍的热膨胀系数相差近2倍,使得铬层与镍层间的结合强度仍较低[Bl。
连铸结晶器铜管尺寸规格
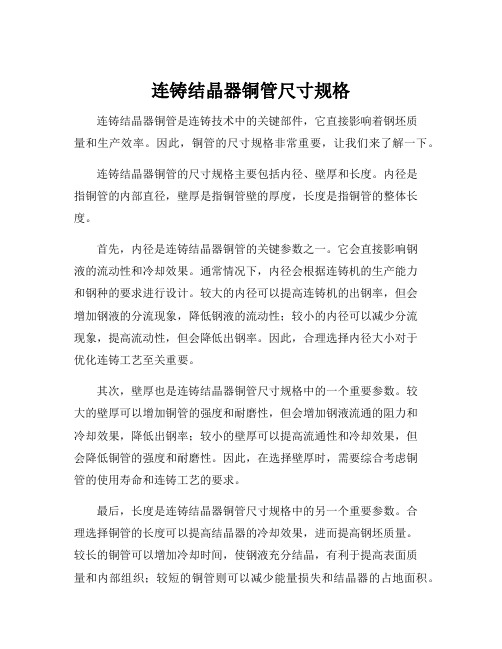
连铸结晶器铜管尺寸规格连铸结晶器铜管是连铸技术中的关键部件,它直接影响着钢坯质量和生产效率。
因此,铜管的尺寸规格非常重要,让我们来了解一下。
连铸结晶器铜管的尺寸规格主要包括内径、壁厚和长度。
内径是指铜管的内部直径,壁厚是指铜管壁的厚度,长度是指铜管的整体长度。
首先,内径是连铸结晶器铜管的关键参数之一。
它会直接影响钢液的流动性和冷却效果。
通常情况下,内径会根据连铸机的生产能力和钢种的要求进行设计。
较大的内径可以提高连铸机的出钢率,但会增加钢液的分流现象,降低钢液的流动性;较小的内径可以减少分流现象,提高流动性,但会降低出钢率。
因此,合理选择内径大小对于优化连铸工艺至关重要。
其次,壁厚也是连铸结晶器铜管尺寸规格中的一个重要参数。
较大的壁厚可以增加铜管的强度和耐磨性,但会增加钢液流通的阻力和冷却效果,降低出钢率;较小的壁厚可以提高流通性和冷却效果,但会降低铜管的强度和耐磨性。
因此,在选择壁厚时,需要综合考虑铜管的使用寿命和连铸工艺的要求。
最后,长度是连铸结晶器铜管尺寸规格中的另一个重要参数。
合理选择铜管的长度可以提高结晶器的冷却效果,进而提高钢坯质量。
较长的铜管可以增加冷却时间,使钢液充分结晶,有利于提高表面质量和内部组织;较短的铜管则可以减少能量损失和结晶器的占地面积。
因此,在选择长度时,需要根据连铸机的生产能力和产品质量要求进行合理的权衡。
综上所述,连铸结晶器铜管的尺寸规格对于连铸工艺至关重要。
合理选择内径、壁厚和长度可以优化工艺,提高钢坯质量和生产效率。
因此,在生产过程中,需要根据实际需求和工艺要求进行精确的设计和选择。
只有这样,才能确保连铸技术的稳定运行和优质产品的生产。
德马克、ROKOP型连铸机结晶器
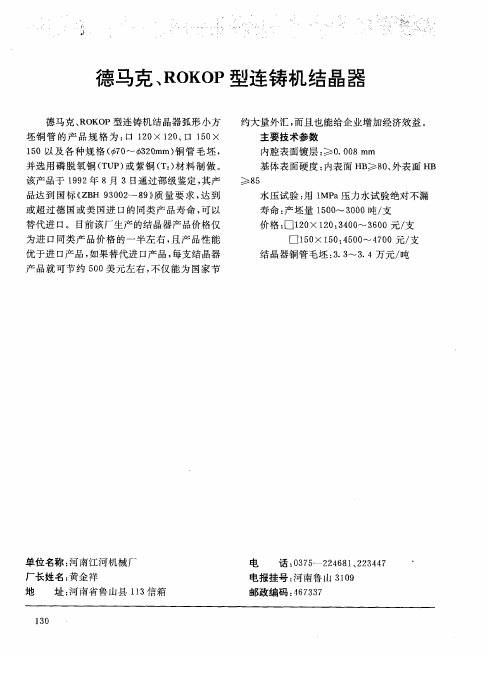
魂 鱿 曦羹
裹 蒸
撇桃篡
、
蓦
ROK OP 型 连 铸 机 结 晶 器
德 马 克
德马 克
150
、
RO K
P o
型 连铸机 结 晶 器弧形 小 方
:
约 大量外 汇 而 且也 能给企业 增 加经济效 益
,
。
坯 铜 管 的产 品 规 格 为
口 1 2 0x
12 0
、
口 150 丫
,
ห้องสมุดไป่ตู้
主 要技术 参数 内腔 表 面 镀 层 妻 0 0 基体 表 面 硬度 内表面 )
单位 名 称 河南 江河机 械 厂 厂长 姓 名 黄金 祥
地
:
:
电
3
话
:
0 3 7 5一 2 2 4 6 8 1
、
223 447
电报挂 号 河 南 鲁 山 信箱 邮政编 码
:
:
31 0 9
址 河南 省鲁 山 县 n
13 0
:
4 67337
元 /支 元 /支
同类 产 品 价格 的 一 半左 右 且 产 品 性 能
口产 品
口
i 50 x
1 5 0 : 4 5 0 0一 4 7 0 0
:
优 于进
如 果替代进
5
口产品
,
,
每支 结 晶器
结 晶器 铜管 毛 坯
3
.
3~ 3
.
4
万元 / 吨
产 品 就 可 节约
0 美元 左 右 不仅 能为 国 家节
85
: :
.
320mm )铜 管 毛 坯 以 及各 种 规 格 师 7 0 一价
结晶器用铜板
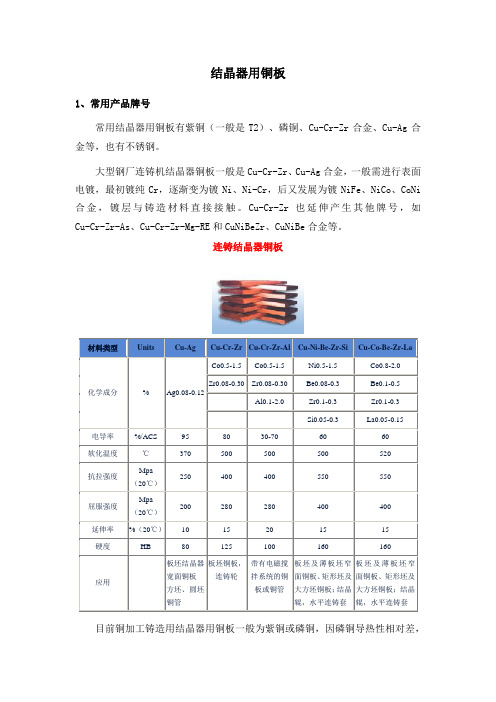
结晶器用铜板1、常用产品牌号常用结晶器用铜板有紫铜(一般是T2)、磷铜、Cu-Cr-Zr合金、Cu-Ag合金等,也有不锈钢。
大型钢厂连铸机结晶器铜板一般是Cu-Cr-Zr、Cu-Ag合金,一般需进行表面电镀,最初镀纯Cr,逐渐变为镀Ni、Ni-Cr,后又发展为镀NiFe、NiCo、CoNi 合金,镀层与铸造材料直接接触。
Cu-Cr-Zr也延伸产生其他牌号,如Cu-Cr-Zr-As、Cu-Cr-Zr-Mg-RE和CuNiBeZr、CuNiBe合金等。
连铸结晶器铜板目前铜加工铸造用结晶器用铜板一般为紫铜或磷铜,因磷铜导热性相对差,价格也高,紫铜更常见。
铜板有电镀和非电镀两种,黄铜等铸造温度相对较低的产品,进行电镀,镀层与铸造材料直接接触,如现有精诚公司立式半连续铸造黄铜等使用的结晶器;紫铜、高铜合金等铸造温度相对较高的产品,铜材一般不与铸造材料直接接触,而是通过石墨结晶器与铸造材料接触,铜板不需要电镀,如精诚公司与鑫科公司水平连铸磷青铜用结晶器铜板和立式半连续铸紫铜铸造等用结晶器。
2、产品规格主要有两种形式。
一种是黄铜等立式半连续铸造结晶器,其材质主要是紫铜,结构是封闭环形式,内腔比铸造材料外形略大,内面进行电镀,最外除了钢衬板外,其余全部是紫铜,厚度约60mm,长度约180~220mm。
一种是铜板形式,其材质包括上述各种牌号。
厚度规格一般约为40mm以下,长度约700~1000mm,宽度根据铸造材料宽度而定。
3、生产工艺结晶器材料应具有高强度,高硬度,耐磨性及导热性好的性能,Cr,Zr,Mg 都是降低铜导热性能较小的元素,且Cr,Zr,Mg均可提高铜的力学性能。
为了保证材料具有良好的综合性能,采用了如下的工艺:熔炼→铸锭→热锻→固溶析出热处理→机械加工→电镀。
熔炼:电解铜板加入坩埚中→加热→加入覆盖剂→熔化→脱氧→加入中间合金→均匀化→出炉(温度控制在≤1250℃)。
铸锭:将熔炼好的合金扒渣→测温→浇注在预热的模型中。
结晶器铜板电镀镀层设计与控制概述

结晶器铜板电镀镀层设计与控制概述一、引言铜镀层是电镀工艺中非常重要的一环,通常用于增加金属表面的导电性、耐腐蚀性以及美观性。
而结晶器铜板电镀镀层是其中的一种特殊镀层,能够在铜基板上形成致密均匀的结晶形态,具有优异的导电性和耐腐蚀性。
本文将就结晶器铜板电镀镀层的设计与控制进行概述,分析其工艺流程、关键参数及控制要点,以期为相关领域的研究和应用提供参考。
二、工艺流程结晶器铜板电镀镀层工艺流程主要包括表面预处理、电镀和后处理三个主要步骤。
1. 表面预处理:表面预处理是镀层工艺中非常重要的一环,其目的是清理基材表面的杂质和氧化物,以确保镀层与基材之间的粘接力和镀层的致密性。
通常包括去油、酸洗、活化、镍化等步骤。
2. 电镀:电镀是结晶器铜板电镀镀层的核心步骤,直接影响着镀层的质量和性能。
电镀过程中,铜离子在电场的作用下沉积到基材表面上,形成致密的结晶结构。
关键参数包括电镀液的成分、温度、pH值、电流密度、搅拌速度等。
合理控制这些参数可以有效提高镀层的致密性和均匀性。
3. 后处理:后处理是为了提高镀层的表面光洁度和耐腐蚀性而进行的一系列处理步骤,通常包括水洗、干燥、涂漆、包装等。
三、关键参数及控制要点1. 电镀液成分:结晶器铜板电镀镀层的电镀液一般由铜盐、添加剂、酸碱调节剂和助镀剂组成。
其中铜盐的种类和浓度、添加剂的种类和用量、酸碱调节剂的类型和浓度都会直接影响着镀层的结晶性、致密性和导电性。
需要对电镀液的成分进行精确控制,保证电镀液的稳定性和一致性。
2. 温度和pH值:电镀液的温度和pH值是影响镀层质量的重要参数。
一般来说,温度过高易导致镀层内应力过大、结晶不致密;温度过低则易导致镀层内应力过小、导电性不佳。
pH值偏离正常范围,也会使镀层结晶不良、表面粗糙。
因此需要根据具体工艺要求,合理控制电镀液的温度和pH值。
3. 电流密度和搅拌速度:电流密度是电镀过程中控制镀层厚度和结晶度的重要参数,搅拌速度则影响着电镀液的对流速度和溶液的均匀性。
结晶器铜板电镀镀层设计与控制概述

结晶器铜板电镀镀层设计与控制概述随着科技的不断发展,电镀技术在工业生产中发挥着越来越重要的作用。
电镀工艺可以通过在金属表面形成一层均匀、致密、具有良好性能的镀层,从而提高材料的抗腐蚀性、耐磨性和表面光泽度。
在电镀工艺中,结晶器铜板电镀是一种常见的表面处理工艺,特别适用于半导体、电子、通讯等领域。
结晶器铜板电镀是一种通过电化学方法在金属表面镀上一层铜薄膜的工艺。
其原理是在合适的工艺条件下,将含有铜离子的电解液通过阳极和阴极的电流作用下,在金属表面沉积形成一层致密、均匀的铜层。
想要获得理想的铜板电镀镀层,需要严格控制工艺参数,包括电解液成分、电流密度、温度、搅拌速度等。
只有合理设计和严格控制这些参数,才能确保获得高质量的镀层产品。
在结晶器铜板电镀工艺中,镀层的设计和控制是至关重要的。
镀层的设计需要考虑到材料的特性,需要保证镀层的致密性、平整度和良好的导电性。
需要从工艺参数入手,通过调整电解液成分、电流密度、温度等参数,来控制镀层的厚度、结晶度和表面质量。
只有合理设计和控制了这些参数,才能保证获得符合要求的铜板电镀镀层。
在结晶器铜板电镀工艺中,电解液的成分是至关重要的。
电解液中的铜盐对镀层的性能有着直接影响,因此需要合理选择电解液成分,保证镀层的致密性和均匀性。
需要定期检测电解液的成分,确保铜盐浓度、PH值、杂质含量等参数符合要求。
电流密度也是影响镀层质量的重要参数。
过高或过低的电流密度都会导致镀层的质量下降,影响镀层的均匀性和致密性。
在实际生产中,需要根据材料的特性和要求,合理设定电流密度,避免出现镀层过厚或者不足的情况。
温度和搅拌速度也是影响镀层质量的重要因素。
适当的温度和搅拌速度可以提高电镀效率,保证镀层的均匀性和致密性。
在镀层工艺中,需要严格控制温度和搅拌速度,避免出现温差过大或者搅拌不均匀的情况。
在结晶器铜板电镀工艺中,除了上述参数外,还需要考虑到阳极和阴极的设计,以及电镀设备的维护和保养。
结晶器铜板镀镍合金主要工艺参数控制

2 . 2温度
镀液温度会影响对流传质速度, 镀液的黏度 ( 进 而影响 电 迁 移速度) , 影 响电极电位 与表面活性物质的吸脱附性质 ( 进而影 响阴极极化效果) , 影响 允许采用 的阴极电流密度大小、 物质溶解 的好坏、 镀液成分的交互影响。同 时, 氨基磺酸镍 的稳定性差, 在高温下容易发生水解 。因此氨基磺 酸盐 电镀 液的温度不能超过7 O ℃, 一般控制在6 0  ̄ C 以下 。根据生产实际, 镀镍液温度
而且镀镍层的孔隙率是 比较高的, 为 了减少或防止针孔的产生 , 需要 向镀液 中加入少量的润湿剂 。
4杂质控 制 电镀液 中杂质 的来源是多方面的, 其 污染 物主要有 尘埃, 阳极泥渣 , 无 机杂质和有机杂质 。 4 . 1尘埃和 阳极泥渣 空气质量差时,空气 中的尘埃一旦落到镀镍槽 内, 会影 响镀液 的清洁
科 学 发 展
锻 鸯 与赌寓
结晶器铜板镀镍合金主要工艺参数控制
李
摘
尹 Leabharlann ( 马钢表 面工程 技术公司 安徽 马鞍 山 2 4 3 0 0 0 ) 要: 本文 以马钢特种 电镀厂结晶器铜板镀镍钻钨三元合 金为例 , 对其 工艺 条件 , 镀液组分 , 杂质情况, 以及控制方法 进行 分析。 并结合实际操作 经
度, 镀出的镍合金层会 出现粗糙、 毛刺 、 针孔等弊病 。 电镀厂镀槽四周配备 了 侧吸风装置, 能够有效避免灰尘直接落入槽内, 不生产时, 采用槽盖予 以隔
离。
另外, 可溶性阳极内含有大量的碳 、 硫、 锰、 铁等杂质, 组织不均一 , 溶解 性差, 易生成阳极泥渣 。电镀厂在 阳极框外包覆布套 以收集阳极泥渣 , 避免
控 制在5 5 5 ℃左右。 2 . 3 P H值 P H 值对 电镀 质量 影响很大, P H 值 过高和过低 时分 别会产生镀层氢 夹 杂和氢氧化物夹杂, 增 大镀层 内应力和孔隙率 。 要注意 的是, P H 值 ≤3 时, 氨 基磺 酸镍发生水解 , 使 电解液不稳定。因此 , P H / I  ̄ 要严格在一定范围内, 以 3 . 4 0 - ' 3 . 7 0 为宜。 3镀 液组分分析 目 前 结晶器铜板电镀使用 的镍钴钨三元合金 电镀液 , 主要成分包括: 氨 基磺 酸镍 , 氨基磺酸钻 , 钨盐 , 氯化镍 , P H 缓冲剂和润湿剂。 3 . 1 主盐: 氨基磺酸镍 , 氨基磺酸钴, 钨盐 氨基磺酸镍 , 氨基磺酸钴 , 钨盐作为 电镀液 中的主盐 , 是必不可少 的重
结晶器铜管

建设高效率企业
结晶器铜管
肖建平
阳春新钢铁有限责任公司
实施低成本战略
建设高效率企业
• 工艺路线: 工艺路线: • 原料铜锭──加热──挤压──冷拔──矫形 ──成品。 • 作用 作用: • 钢铁公司在炼钢连铸过程中,钢水必须先 按一定速度经过结晶器铜管放热冷却凝固 ,才能从液态变为固态
阳春新钢铁有限责任公司
实施低成本战略
建设高效率企业
• 5 脱方与钢水过热度 • 钢水的过热度越高,脱方的几率越大。过热度高的钢水
热导出量大,易造成铸坯断面上的热流不均,从而导致了 脱方缺陷的形成,钢水过热度大于40℃易出脱方缺陷。
• •
6 二冷水量分布
水条对中不准及水咀堵塞等原因,影响到二冷铸坯的均 匀冷却。脱方是根源于结晶器在二冷段进一步发展的一种 缺陷,二冷水均匀性对脱方有着重要影响。即使出结晶器 时的铸坯形状完好,而二次冷却不均匀,也会形成二冷区 的脱方,这种脱方单纯由二冷水不均引起。
阳春新钢铁有限责任公司
实施低成本战略
建设高效率企业
• 2 脱方与拉速的关系 • 拉速与结晶器热流的关系如图8。
• • • • • • 拉速的变化主要影响 到热流的变化, 对任何一种断面,拉速的 提高都会增加脱方的几率, 而低拉速的状态下往往 会抑制脱方的发展。
阳春新钢铁有限责任公司
实施低成本战略
阳春新钢铁有限责任公司
实施低成本战略
建设高效率企业
• 4 脱方与断面的关系
• 断面对脱方缺陷有不同影响,同是方坯,小断面脱方率 大于大断面,矩形坯脱方率大于方坯。小断面铜管壁厚薄 ,拉速快,导出的瞬间热量大,易造成横断面上热流不均 匀,对控制热流均匀的各种因素要求更加精确,有一些薄 弱之处就会造成热流不均匀而脱方。矩形断面,由于铸坯 宽度的绝对值大,收缩的绝对值也大,又因为宽面窄面的 面积差异大,钢水静压力作用在宽面和窄面的效果也就有 很大的差异, 收缩量极易产生差别。因此,要求铜管的锥 度在不同面有不同的变化,也加大了铜管的技术要求,当 锥度上出现偏差时,容易形成热流不均匀造成脱方。
结晶器铜管技术参数

结晶器铜管技术参数嘿,朋友们!今天咱们来唠唠结晶器铜管这个超酷的东西。
你可别小看它,它就像是钢铁世界里的超级模具大师。
这结晶器铜管的长度啊,就像是模特的大长腿,不过不是用来走T台的,而是精确控制着钢水变身的旅程。
有的铜管长那么恰到好处,就像厨师手中那把刚好能切出完美食材的刀。
再说说它的内径,那可真是个讲究的尺寸。
如果把它比作一个隧道,这个隧道既不能太宽敞让钢水肆意乱流,就像不能让一群调皮的孩子在马路上乱跑一样;也不能太狭窄把钢水挤得难受,就像给一个大胖子穿小一号的衣服。
还有铜管的壁厚,这就像战士的铠甲厚度。
厚了呢,显得笨重,成本还高,就像给小蚂蚁穿上大象的盔甲;薄了又不够结实,容易在钢水的强大冲击下“受伤”,就像纸糊的盾牌面对汹涌的波涛。
它的锥度啊,简直是个神奇的魔法数字。
这个锥度就像是给钢水定制的滑梯坡度,太陡了钢水滑得太快,容易失控,就像坐过山车脱轨了一样;太缓了钢水又懒得动,就像冬天早上赖床的我们。
表面粗糙度那也是个有趣的点。
如果表面粗糙得像砂纸,那钢水在里面流动就像开着破车在坑洼路上颠,钢坯的质量肯定好不了。
要是光滑得像溜冰场,那钢水就像滑冰选手一样顺畅地变身。
它的材质就像武林高手的内功,要是材质不好,就像武林新手,在钢水这个大反派面前很快就会败下阵来。
好的材质就像绝世高手,稳稳地掌控着局面。
冷却水槽在铜管上的分布,就像精心设计的灌溉系统。
分布得合理,就能像雨露均匀地滋润大地一样,让铜管均匀冷却;要是分布乱了,那就像有的地儿旱死,有的地儿涝死,铜管可就出大问题啦。
这结晶器铜管的热传导性能,就像超级快递员,要快速把热量传递出去。
要是传得慢,就像蜗牛送信,那钢水凝固得不好,整个生产就乱套喽。
总之,结晶器铜管的每一个技术参数都像是拼图的一块,少了哪一块或者哪一块不合适,都没法拼出完美的钢铁画卷呢!哈哈。
结晶器铜板电镀镍钴铁工艺研究

结晶器铜板电镀镍钴铁工艺研究摘要:Ni-Cr, Ni—Fe。
Ni-Co Ni-Co- Fe镀层在结晶器铜板上的开发应用,详细阐述以上四种镀层的优劣,同时对结晶器铜板电镀镍钴铁的优越性进行了详细的阐述。
引言:结晶器铜板在工作过程中由于长时间经受高温铁水的冲刷,存在较严重的摩擦和磨损,其损坏的主要形式是产生热裂纹、磨损和腐蚀;表面的局部损坏又往往造成整个部件失效,最终导致设备报废。
据统计,一套结晶器的价格在7—120万元,我国冶会企业每年铜结晶器的消耗在2o亿元以上,是除了轧辊之外的第二大冶金耗材;而且铜及铜合金的资源紧缺,近期来价格又有不断上涨的趋势;因此提高结晶器铜板表面的耐磨性和耐热性是提高经济效益和生产效率的根本措施,具有很好的科学研究意义和实际应用价值。
1,结晶器铜板的表面处理表面处理技术,即利用各种物理的、化学的或机械的工艺方,法使材料表面获得特殊的成分、组织结构与性能,以提高其耐磨抗蚀性能,延长其使用寿命的技术,也可称为表面加工等。
常用的表面技术有:堆焊技术、熔结技术、电镀、电刷镀及化学镀技术、非金属镀技术、热喷涂技术、物理与化学气相沉积、化学热处理、激光表面处理、电子束技术相变硬化、离子注入等。
其中,利用电镀、热喷涂技术、化学热处理强化结晶器铜板在国内或国外已经有所应用。
(1)电镀在表面处理技术中,电镀是最有效的方法之一。
电镀是指在含有欲镀金属的盐类溶液中,在直流电的作用下,以被镀基体金属为阴极,以欲镀金属或其它惰性导体为阳极,通过电解作用,在基体表面上获得结合牢固的金属膜的表面工程技术。
目前,利用电镀强化的结晶器有单镀层铜板和复合镀层铜板。
单一镀层主要用铬或镍;现已开发结晶器复合镀层铜板,如Ni—cr,Ni-Fe,Ni—Fe—w,Ni—Fe—co,Ni co,Ni—w 等效果很好。
此外,还有Ni—w—P镀层等另外,为降低生产成本,优化我国冶金技术设备,国内已有人进行电镀镍及其合金的研究,其中,以铜铬锆为材质的结晶器电镀镍铁,镍钴,钴镍镀层已经在板坯连铸机获得应用。