热固性塑料的注塑成型加工知识
注塑成型工艺培训资料
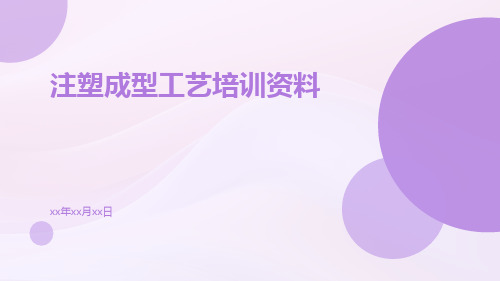
THANKS
谢谢您的观看
注塑成型工艺具有高效率、高精度和高自动化程度等特点, 可适用于各种热塑性和热固性塑料制品的生产。
注塑成型工艺的基本原理和分类
注塑成型工艺的基本原理是利用塑料在高温下具有良好的 流动性和可塑性,将塑料熔体注入模具型腔中,在冷却条 件下固化而形成制品。
注塑成型工艺主要分为热塑性塑料注塑和热固性塑料注塑 两种。热塑性塑料注塑包括单物料注塑、双物料注塑和多 物料注塑等;热固性塑料注塑包括模压成型、传递成型和 挤出成型等。
溢料
可能由于注射压力过大、浇口尺寸过大等原因导 致。排除方法包括减小注射压力、缩小浇口尺寸 等。
表面光泽不良
可能由于模具温度过高、注射速度过慢等原因导 致。排除方法包括降低模具温度、提高注射速度 等。
特殊故障及排除方法
粘模
可能由于模具温度过高、塑料 粘度过大等原因导致。排除方 法包括降低模具温度、更换粘
注塑成型工艺培训资料
xx年xx月xx日
目 录
• 注塑成型工艺简介 • 注塑成型工艺流程 • 注塑成型工艺参数 • 注塑成型工艺故障及排除 • 注塑成型工艺优化 • 注塑成型工艺安全与环保
01
注塑成型工艺简介
注塑成型工艺的定义与特点
注塑成型工艺是指将热塑性塑料或热固性塑料通过塑料注射 机进行熔融、注射、充模、保压、冷却等过程,在模具中快 速冷却固化,从而得到具有一定形状、尺寸和性能的塑料制 品的工艺过程。
。
实例二
引入气辅成型技术,解决某产品 缩痕问题,提高了产品外观质量 和生产效率。
实例三
通过改进模具浇口数量和优化排气 设计,提高某公司模具使用寿命和 降低废品率。
优化后的效果评估与持续改进
效果评估
第6章热固性塑料的主要成型加工技术
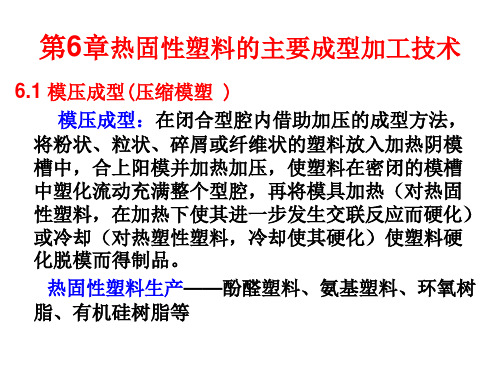
半溢式:有支承面与溢式相似,有装料室,用于小嵌件制品
无支承面与不溢式模具很相似,阴模向外倾斜3°, 阴模阳间有溢料槽
溢式模具
不溢式模具
图6-5 半溢式模具示意图 (a)有支承面 (b)无支承面
6.1.3 模压成型过程及操作
6.1.3.1 模压成型过程
成型物料的准备、成型和制品后处理三个阶段
模压成型原理
(2) 热固性与热塑性塑料注射成型不同点
热固性塑料在料筒内的塑化(料筒温度)
热固性塑料熔体在充模过程的流动(剪切
应力和充模速度)
热固性塑料在模腔内的固化(模具温度)
6.4.2 热固性塑料注射成型机
(1)注射装置
作用:将塑料均匀地塑化成熔融状态,将熔料注射到模腔内
基本形式:螺杆式和柱塞式,主要采用往复式单螺杆注射
机
螺杆——与热塑性塑料注射机区别大 (2) 螺杆驱动装置(低转速大扭矩油马达驱动螺杆旋转)
(3) 合模装置(由模板,拉杆,合模油缸等组成,合模力大)
(4) 控制系统
(5) 特殊注射机
双柱塞式注射机
图6-22 柱塞式聚酯料团注塑机 图6-21 多工位注塑机
6.4.3 热固性塑料注射成型工艺
图6-23 热固性塑料注塑成型工艺过程
C→E,交联,放Q→T物>T模, V↓
E点卸压, P↓常压
F点脱模
模压成型压力-温度-体积关系 ——:无支承面 ------:有支承面
6.1.4 模压成型工艺控制
6.1.4.1 模压压力Pm
指成型时压机对塑 料所施加的压力
pm
D2
4 Am
pg
Pm与塑料种类、模温、 制品形状有关
模压P对流动固化曲线的影响 a-50MPa b-20MPa c-10MPa
塑料成型原理与工艺
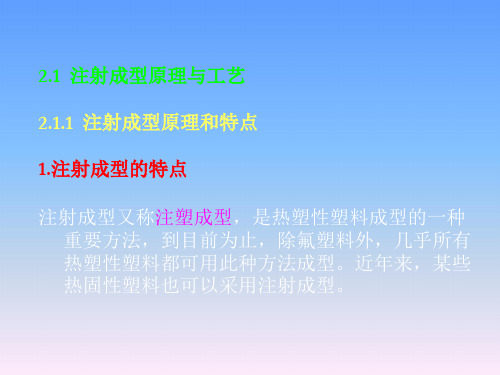
压缩成型与注射成型相比的优点是: (1)无浇注系统,耗料少; (2)设备使用及模具较简单; (3)易于成型流动性较差如以纤维为填料的塑料; (4)制品收缩率小,变形小,各向性能比较均匀; (5)能成型面积大、厚度又比较小的大型扁平制品。
缺点是: (1)生产周期长,效率低; (2)不易成型尺寸精度要求较高、形状复杂、壁厚 相差较大及带有精细易断嵌件的制品; (3)劳动强度大,难以实现自动化,劳动条件较差; (4)模具寿命较短。
2.2.2 压缩成型工艺过程
压缩成型工艺过程主要包括预压、预热和 干燥、嵌件的安放、加料、闭模、排气、固化、 脱模、清理模具、制品后处理等。
但模温也不能过低,过低的模温不仅使 固化速度慢,而且效果差,也会造成制品的 灰暗,甚至表面发生肿胀,这是因为固化不 完全的外层受不住内部挥发物压力作用的结 果。
成型厚度较大的制品时,宜采用降低模 具温度,延长成型时间的工艺规程。
3.压缩成型时间
成型时间是指从闭模加压起,物料在模具 内升温到固化脱模为止的这段时间。它直接 影响制品的成型周期和固化度。
1.压缩成型前的准备工作
(1)预压
在压缩成型前,将松散的粉状或纤维状的 热固性塑料在室温下预先用冷压法(即模具不 加热)压成重量一定、形状一致的密实体的过 程称为预压,所得到的物体称为预压物(或压 锭、型坯、压片)。
预压的作用主要有:
(1)加料快而准确。避免加料过多或不足而造成 的残次品。
(2)减小模具的加料室,降低模具制造成本。
(1)加料 (2)塑化 (3)加压注射 (4)保压 (5)冷却定型 (6)脱模
3. 塑件的后处理 塑件经注射成型后,除去浇口凝料,修饰浇口处余料
注塑成型的工作原理

注塑成型的工作原理注塑成型是一种常见的塑料加工技术,通过将熔化的塑料注入模具中,并在固化后得到所需形状的制品。
本文将详细介绍注塑成型的工作原理,并探讨其具体步骤及相关特点。
一、工作原理注塑成型的工作原理基于热塑性塑料的特点,其主要包括以下几个步骤:1. 塑料熔化:首先,将塑料颗粒加入注射机的料斗中。
然后,通过外加热源,调节注射机的温度,使塑料颗粒迅速熔化成为黏稠的熔融塑料。
2. 注射:在塑料熔化的同时,注射机会将熔融塑料注入模具中。
注射机通过螺杆运动,将熔融塑料推动到注射筒前端,并通过喷嘴进入模具的腔体。
3. 塑料充填:一旦熔融塑料进入模具腔体,它会填充整个腔体,包括模具中所定义的产品形状。
在此过程中,注射机保持一定的压力,以确保塑料充分填充模具。
4. 塑料固化:一旦塑料充填完成,它会开始在模具中逐渐冷却,并渐渐固化。
注射机会保持模具一定的冷却时间,以确保塑料完全固化。
5. 产品脱模:当塑料完全固化后,模具会打开并释放成形的产品。
产品的脱模可以通过模具的自动弹出装置或人工操作实现。
释放后,可以开始进行下一次注射循环。
二、特点与优势注塑成型作为一种成熟的塑料加工技术,具有以下特点与优势:1. 精度高:注塑成型产品的尺寸精度高,可以满足不同行业的严格要求,如医疗器械、汽车零部件等。
2. 产品种类多样:注塑成型可以加工各种形状的产品,从小到大,从简单到复杂,包括零件、容器、玩具等。
3. 生产效率高:注塑成型具有高效连续生产的能力,可以快速完成成形循环,满足大批量生产的需求。
4. 自动化程度高:注塑成型设备智能化程度高,可以实现自动化操作,提高生产效率和产品质量。
5. 材料选择广泛:注塑成型可适用于热塑性塑料、热固性塑料和橡胶等材料,具有较广泛的应用范围。
三、应用领域注塑成型技术广泛应用于众多行业,例如:1. 汽车工业:注塑成型可制造汽车内部和外部的零部件,如仪表盘、门把手、保险杠等。
2. 电子电器:注塑成型可制造电子产品的外壳,如手机壳、电视遥控器等。
高分子材料成型加工(注射成型)详解

作用:将注射油缸的压力传给塑料,并使熔体注射 入模具 (4)分流梭
将物料流变成薄层,使塑料产生分流和收敛流动 加快热传递,缩短传热过程,避免物料过热分解 熔体在分流梭表面流速↑,剪切速度↑,产生较大的 摩擦热,使料温↑,有利于塑料的混合与塑化,有效 提高产量和质量
顿流体,通过圆形截面或平板狭缝形浇口。
ηa= Kγn-1 (n<1) 浇口的截面积↑ ,熔体体积流量↑
高分子材料成型加工
4. 熔体在模腔的流动:
4.1 熔体在典型模腔内的流动方式
4.2 熔体在模腔内的流动类型
高分子材料成型加工
三. 增密与保压过程: 1. 增密过程(压实过程) 2. 保压过程
4. 注射模具 成型零部件
凸模、凹模、型芯、 成型杆、镶块、动模、定模
浇注系统
主流道、分流道、浇口、 冷料阱、导向零件、分型 抽芯机构、顶出、加热、冷却、 排气
二. 注射机的工作过程
高分子材料成型加工
高分子材料成型加工
第二节 注射过程原理
一. 塑化过程 对塑料塑化的要求:塑料熔体进入模腔之前要 充分塑化,达到规定的成型温度。 塑化料各处的温度要均匀一致。 热分解物的含量达最小值。
高分子材料成型加工
2. 按注射机外形特征分类
高分子材料成型加工
高分子材料成型加工
3. 按注射机加工能力分类
注射量:注射机在注射螺杆(柱塞)作一次最大注射 行程时,注射装置所能达到的最大注射量
锁模力:注射机合模机构所能产生的最大模具闭紧力
4. 按注射机用途分类
高分子材料成型加工
二.注射机的基本结构
热固性塑料注塑工艺过程
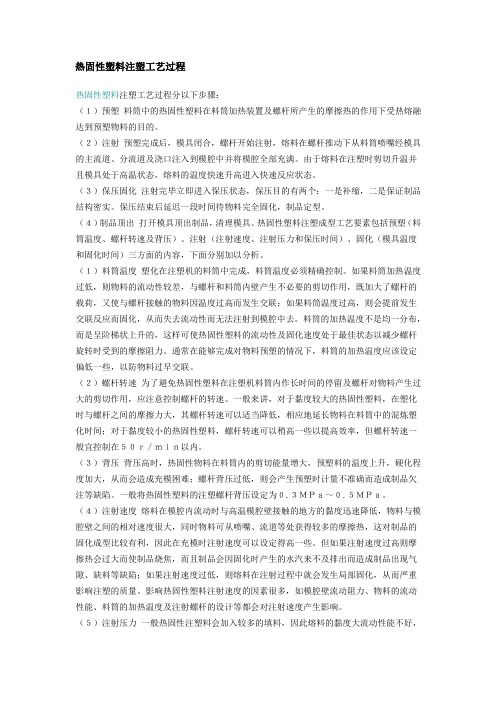
热固性塑料注塑工艺过程热固性塑料注塑工艺过程分以下步骤:(1)预塑料筒中的热固性塑料在料筒加热装置及螺杆所产生的摩擦热的作用下受热熔融达到预塑物料的目的。
(2)注射预塑完成后,模具闭合,螺杆开始注射,熔料在螺杆推动下从料筒喷嘴经模具的主流道、分流道及浇口注入到模腔中并将模腔全部充满。
由于熔料在注塑时剪切升温并且模具处于高温状态,熔料的温度快速升高进入快速反应状态。
(3)保压固化注射完毕立即进入保压状态,保压目的有两个:一是补缩,二是保证制品结构密实。
保压结束后延迟一段时间待物料完全固化,制品定型。
(4)制品顶出打开模具顶出制品,清理模具。
热固性塑料注塑成型工艺要素包括预塑(料筒温度、螺杆转速及背压)、注射(注射速度、注射压力和保压时间)、固化(模具温度和固化时间)三方面的内容,下面分别加以分析。
(1)料筒温度塑化在注塑机的料筒中完成,料筒温度必须精确控制。
如果料筒加热温度过低,则物料的流动性较差,与螺杆和料筒内壁产生不必要的剪切作用,既加大了螺杆的载荷,又使与螺杆接触的物料因温度过高而发生交联;如果料筒温度过高,则会提前发生交联反应而固化,从而失去流动性而无法注射到模腔中去。
料筒的加热温度不是均一分布,而是呈阶梯状上升的,这样可使热固性塑料的流动性及固化速度处于最佳状态以减少螺杆旋转时受到的摩擦阻力。
通常在能够完成对物料预塑的情况下,料筒的加热温度应该设定偏低一些,以防物料过早交联。
(2)螺杆转速为了避免热固性塑料在注塑机料筒内作长时间的停留及螺杆对物料产生过大的剪切作用,应注意控制螺杆的转速。
一般来讲,对于黏度较大的热固性塑料,在塑化时与螺杆之间的摩擦力大,其螺杆转速可以适当降低,相应地延长物料在料筒中的混炼塑化时间;对于黏度较小的热固性塑料,螺杆转速可以稍高一些以提高效率,但螺杆转速一般宜控制在50r/min以内。
(3)背压背压高时,热固性物料在料筒内的剪切能量增大,预塑料的温度上升,硬化程度加大,从而会造成充模困难;螺杆背压过低,则会产生预塑时计量不准确而造成制品欠注等缺陷。
注塑工艺基础知识

Page 7
注塑设备—注塑机的组成结构
一台通用注塑机主要由塑化注射系统、合模机构、液压传动(或气动)装置、电器控制 系统等组成,如图所示:
Page 8
注塑设备—注塑机的组成结构
塑化注射系统 塑化注射系统的主要作用是使塑料加热塑化和熔融, 并能以足够的压力和速度下将一定量的溶料注入模具型腔中。塑化注射系 统主要由塑化部件(螺杆、机筒、喷嘴等组成)、料斗、计量装置、传动 装置、注射油缸、注射座整体移动油缸等组成。
注塑工艺基础知识
提纲
一、注塑工艺简介 二、注塑设备 三、注塑工艺过程 四、注塑制品的设计要点
Page 2
注塑工艺简介
各种各样的塑料制品是怎么制成的呢?塑料的主要成型方法 有挤出成型、注塑成型、吹塑成型、压延成型、浇铸成形等,其 中注射成型因形状适应性广,是热塑性塑料成型主要工艺。
注塑也称注射成型或注射模塑,是用注塑机将塑料粒子或塑 料粉的原料熔融后,施加压力使其注入温度较低的模具内冷却固 化形成与模腔形状一致的塑料制品的加工过程。
Page 6
注塑设备—注塑机分类
近年来注塑机发展很快,类型不断增加,分类的方法也较多。有的按塑料塑化 方式分为柱塞式和螺杆式;有的按锁模装置的传动方式分为液压式、机械式和液压 机械式;也有按机器操作方式分为自动、半自动和手动等,至今尚未完全形成统一 的分灯方法,目前使用较多的分类方法有以下几种:
塑料注塑成型工艺基本知识

塑料制品的尺寸精度影响因素
• 6) 填料影响:塑料材料进行增强或无机填充改性后,可提高塑料制品的尺寸精度 。
五、热塑性塑料注塑成型工艺
• 塑料注塑加工过程流程 :
…成型前的准备 加料 塑化 注射入模 保压冷却 脱模 (修整) (后处理 ) …
• 成型前的准备
• 1、原料或嵌件预处理
(并非所有原料或嵌件都需要进行预处理——干燥、预热,视产品技术要求程度、 原材料品种、气温状况而定,对于金属嵌件,在冬季一般都需要预热处理。)
• 成型前的准备
• 2—料筒清洗注意: • 在改变原料品种,或调换颜色时,必须对料筒进行清洗,清洗后
的料应做好标识。严禁误用!! • 被清洗料为*PC ,不得用ABS或PA ; • 被清洗料为POM ,不得接触PVC ;
• 注塑成型过程(加料 、塑化、注射入模 、保压冷却 、脱模、(修整))
• 关注:
脱模剂 使用应注意!!!
• 所选脱模剂品种是否合适。(不能对产品有浸蚀) • 对产品表面要喷油漆的零件,严禁使用脱模剂;
注塑过程(工艺)参数应关注:
工艺参数:
• 注塑量 • 注塑料筒各段温度 • 各级注塑压力、塑化时背压、保压压力 • 各级注塑速度 • 注塑时间、保压时间、冷却时间 • 模具温度 • 使用回头料情况
• 注射成型(或注塑成型或注射模塑):
将粒状或粉状塑料从注射机的料斗送进加热的料筒,经加热熔化呈流动状后,由柱塞或螺杆的 推动而通过料筒端部的喷嘴并注入温度较低的闭合模具中,充满塑模的熔料在受压的情况况下,经 冷却因化后即可保持塑模型腔所赋予的形样。
二、塑料成型方法
• 注射成型(*) • 挤出成型:如管材类产品、型材类产品(建材用)… • 吹塑成型:如油箱、加注管、民用油/水壶… • 热成型(真空吸塑成型) :如轿车塑料地垫、防水帘等 • 浇铸成型:如方向盘、仪表板 • 压延与涂层:如人造革 • 烧结成型:主要PTFE制品 • 搪塑成型:如玩具类产品,车门扶手表皮 • 模压成型:(板材) • ……
热固性塑料的注塑成型有何特点?(杨氏注塑法)
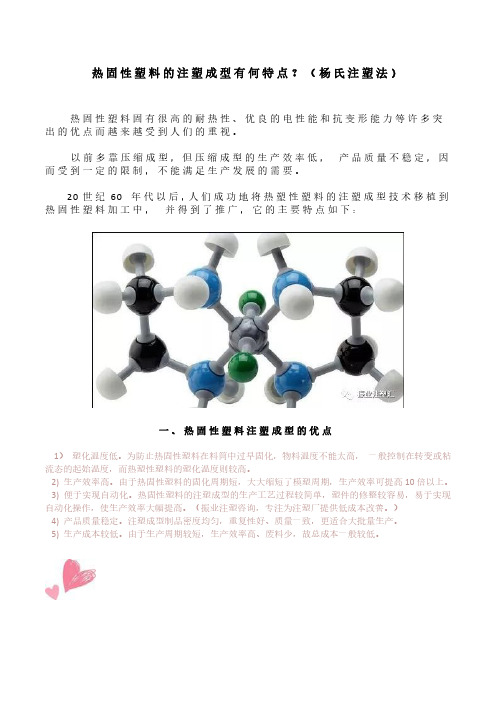
热固性塑料的注塑成型有何特点?(杨氏注塑法)热固性塑料固有很高的耐热性、优良的电性能和抗变形能力等许多突出的优点而越来越受到人们的重视。
以前多靠压缩成型,但压缩成型的生产效率低,产品质量不稳定,因而受到一定的限制,不能满足生产发展的需要。
20世纪60年代以后,人们成功地将热塑性塑料的注塑成型技术移植到热固性塑料加工中,并得到了推广,它的主要特点如下:一、热固性塑料注塑成型的优点1)塑化温度低。
为防止热固性塑料在料筒中过早固化,物料温度不能太高,一般控制在转变或粘流态的起始温度,而热塑性塑料的塑化温度则较高。
2)生产效率高。
由于热固性塑料的固化周期短,大大缩短了模塑周期,生产效率可提高10倍以上。
3)便于实现自动化。
热固性塑料的注塑成型的生产工艺过程较简单,塑件的修整较容易,易于实现自动化操作,使生产效率大幅提高。
(振业注塑咨询,专注为注塑厂提供低成本改善。
)4)产品质量稳定。
注塑成型制品密度均匀,重复性好、质量一致,更适合大批量生产。
5)生产成本较低。
由于生产周期较短,生产效率高、废料少,故总成本一般较低。
二、热固性塑料注塑成型的缺点1)注射压力高。
热固性塑料的塑化温度低,熔料粘度大,为使熔料能完全充满模腔,需要施加较高的注射压力(100~200MPa)。
2)加工工艺较复杂。
热固性塑料是在加热的模具中固化成型的,为此,热固性塑料成型模具需配备加热装置。
(更多请关注:“振业注塑汇”)3)废料不能再利用。
热固性塑料成型后产生的废料,加热时不再软化,只能作废物丢弃。
4)成型温度范围窄。
成型温度的范围不大,温度稍低熔料难以流动,而温度稍高又使其流动性迅速变小甚至硬化,因此对料筒和喷嘴温度的控制精度要求很高,一般在±3℃范围内。
5)成型时产生气体较多。
由于热固性塑料在发生交联反应时会产生气体,它们将对模具设计带来一些难度,因为这些气体若不及时排出,将严重影响产品质量。
注塑工艺知识点总结归纳

注塑工艺知识点总结归纳一、注塑工艺概述注塑是一种常见的塑料成型工艺,通过将熔化的塑料注入模具腔内,经冷却后形成所需的零件。
注塑工艺广泛应用于电子、汽车、家电等行业,其工艺技术和设备不断发展,成为塑料制品生产的重要工艺之一。
在注塑工艺中,主要包括塑料材料、模具设计、注塑机、工艺参数、注塑工艺流程等方面的内容。
下面将分别详细介绍这些知识点。
二、塑料材料1. 塑料材料的分类塑料是一种高分子化合物,按照不同的化学结构和性能特点,可以分为热塑性塑料和热固性塑料两大类。
热塑性塑料在注塑成型过程中可以反复加热和冷却,保持可塑性,常见的有聚丙烯、聚乙烯、ABS等;热固性塑料在注塑成型后会发生化学反应,不可反复加热和冷却,例如酚醛树脂、环氧树脂等。
2. 塑料材料的性能塑料材料具有轻、坚、耐腐蚀、绝缘、隔音、不导电等特点,广泛应用于各种领域。
不同种类的塑料具有不同的物理和化学性能,如强度、耐热性、耐腐蚀性、尺寸稳定性等。
3. 塑料材料的选择在注塑工艺中,选择合适的塑料材料是十分重要的。
需要考虑产品的使用环境、功能要求、成本等因素,选择符合要求的塑料材料进行注塑成型。
三、模具设计1. 模具的类型注塑模具分为冷却型模具和热流道模具两种类型。
冷却型模具是常用的模具类型,通过模具内的冷却系统冷却熔化的塑料,形成成型件。
热流道模具是通过热流道系统将熔化的塑料直接注入模具腔内,具有更高的生产效率和产品质量。
2. 模具设计要点模具设计要考虑产品的结构、尺寸、成型特点等因素,以确保最终产品的质量。
具体包括模具结构设计、成型件的放料方式、冷却系统设计、射嘴和排气系统设计等。
3. 模具材料选择模具的材料选择直接关系到模具的使用寿命和成型精度。
常见的模具材料有P20、718、H13等,需要根据产品的材料和加工要求选择合适的模具材料。
四、注塑机1. 注塑机的结构注塑机主要由注射系统、压力系统、锁模系统、电气控制系统等部分组成。
其中注射系统用于将熔化的塑料注入模具腔内,压力系统用于提供成型时所需的压力,锁模系统用于锁模和开模操作,电气控制系统用于控制注塑机的运行。
热固性塑料注塑成型基础知识

一、热固性塑料注塑成型技术简介热固性塑料指在加热、加压下或在固化剂、紫外光作用下,进行化学反应,交联固化成为不熔物质的一大类合成树脂。
这种树脂在固化前一般为分子量不高的固体或粘稠液体;在成型过程中能软化或流动,具有可塑性,可制成一定形状,同时又发生化学反应而交联固化,有时释放出一些副产物,如水等。
热固性塑料的树脂固化前是线型或带支链的,固化后分子链之间形成化学键,成为三维的网状结构,不仅不能再熔融,在溶剂中也不能溶解。
酚醛、三聚氧胺甲醛、环氧、不饱和聚酯以及有机硅等塑料,都是热固性塑料。
热固性塑料第一次加热时可以软化流动,加热到一定温度,产生化学反应,交链固化而变硬,这种变化是不可逆的,此后,再次加热时,已不能再变软流动了。
正是借助这种特性进行成型加工,利用第一次加热时的塑化流动,在压力下充满型腔,进而固化成为确定形状和尺寸的制品。
热固性塑料注塑利用螺杆或柱塞把聚合物送入注塑机机筒,聚合物经机筒加热粘度会降低,注塑机把粘度降低的聚合物注射进加热过的模具中。
物料充满模具,即对其保压。
此时产生化学交联,使聚合物变硬。
硬的(即固化的)制品趁热即可自模具中顶出,固化后的塑料不能再成型或再熔融。
最早应用于热固性塑料成型的工艺方法是压塑法(ComPreSSionmou1ding)和压铸法(transferMoU1ding)与它们相比,注塑法(InjeCtionMou1ding)的优缺点如下:注塑法比压塑法、压铸法优越处是:较快的成型周期(2〜3倍),过程自动化;制品生产稳定性较好;较低的人工费;高的生产能力。
注塑法相对于压塑法、压铸法的缺点是:较高的设备和模具投资;压塑法可以得到较高的制品强度和较好的表面光洁度。
二、热固性塑料注塑成型工艺过程1、热固性塑料注塑工艺步骤热塑性塑料和热固性塑料在加热时都将降低粘度。
然而,热固性塑料的粘度却随时间和温度而增加,这是因为发生了化学交联反应。
这些作用的综合结果是粘度随时间和温度而呈U型曲线。
注塑成型培训资料

在满足使用和加工要求的前提下,选择价格适宜、资源丰富的材料。
塑料材料的性能及测试方法
密度
通过比重杯或浮力法测量塑料颗粒的密度 。
冲击强度
通过摆锤冲击试验测量塑料条的冲击强度 。
收缩率
通过测量注塑件尺寸变化计算收缩率。
弯曲强度
通过三点弯曲试验测量塑料条的弯曲强度 。
拉伸强度
通过万能材料试验机测量塑料条的拉伸强 度。
成型尺寸
按照图纸要求,检查成品的尺寸是 否符合标准。
表面质量
检查成品表面是否光滑、无明显缺 陷。
力学性能
对成品进行力学性能测试,如拉伸 强度、弯曲强度、冲击强度等。
耐久性测试
对成品进行耐久性测试,如老化试 验、疲劳试验等。
05
注塑成型安全生产及环保要求
注塑成型安全生产要求
确保工作场所安全
注塑成型车间应保持整洁,无杂物堆放,确保通 道畅通。
03
数据分析和结论
通过对实验数据的分析,得出该材料的最佳成型条件,为实际生产提
供指导。
案例三:某工艺参数优化实践操作
工艺参数介绍
介绍注塑成型过程中的关键工艺参数,如注射压力、注射速度 、模具温度等。
实验设计
以某一种工艺参数为例,设计一组实验,以探究其对产品性能 的影响。
数据分析和结论
通过对实验数据的分析,得出该工艺参数对产品性能的影响规 律,为实际生产提供指导。
解决方法
针对上述问题,提出了相应的解决方法,包括优化模具设计、调整成型工艺参数等,以改 善产品的质量和生产效率。
案例二:某材料注塑成型实践操作
01
材料选择
介绍某一种适合注塑成型的材料,包括其物理性质、化学性质及加工
热塑性塑料(注塑成型)的工艺性能、 热固性塑塑料工艺性能-课件
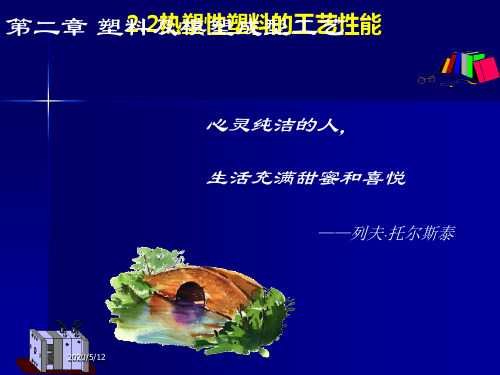
拉伸取向—由拉应力引起,取向方向与拉伸方向一致; 由拉应力引起,取向方向与拉伸方向一致; 流动取向—在切应力作用下沿着熔体流动方向形成的. 在切应力作用下沿着熔体流动方向形成的.
按流动性质不同,取向结构可分为: 按流动性质不同,取向结构可分为:
单轴取向—结构单元均沿着一个流动方向有序排列(取向); 单轴取向—结构单元均沿着一个流动方向有序排列(取向); 多轴取向—结构单元可沿两个或两个以上流动方向有序排列; 多轴取向—结构单元可沿两个或两个以上流动方向有序排列; 按结晶与非结晶聚合物分为: 按结晶与非结晶聚合物分为: 结晶取向 / 非结晶取向
a—中心层定向 最小 ; 中心层定向 b—内层定向较大; 内层定向较大; 内层定向较大 c—外层定向最大; 外层定向最大; 外层定向最大 d—表层未定向。 表层未定向。 表层未定向
20122012-2-23
定向原因: 定向原因:
2.2热塑性塑料的工艺性能 2.2热塑性塑料的工艺性能
d—未取向区 c—高度取向区 b—中等取向区 a—轻度取向区
2.2热塑性塑料的工艺性能 2.2热塑性塑料的工艺性能
定向:
在成型加工中聚合物在 某方向的压力作用下, 某方向的压力作用下,由于 剪应力造成的速度梯度的诱 导,聚合物分子在很大程度 上会顺着流动的方向整齐地 作平行的排列, 作平行的排列,这就是分子 取向的一种情况。 取向的一种情况。
d—未取向区 c—高度取向区 b—中等取向区 a—轻度取向区
2.2热塑性塑料的工艺性能 2.2热塑性塑料的工艺性能 第二章 塑料及模塑成型工艺
心灵纯洁的人, 生活充满甜蜜和喜悦
——列夫·托尔斯泰
20122012-2-23
2.2热塑性塑料的工艺性能 2.2热塑性塑料的工艺性能 2.2热塑性塑料的工艺性能
塑料的成型原理

塑料的成型原理
塑料的成型原理是通过热塑性塑料或热固性塑料在一定温度下加热融化后,注入到模具中,经过冷却固化形成所需的产品形状。
具体的成型原理包括以下几个步骤:
1. 塑料材料制备:选取适当的塑料原料,如聚乙烯(PE)、
聚丙烯(PP)、聚氯乙烯(PVC)等,然后进行预处理,如
研磨、干燥等,以确保原料质量。
2. 加热与融化:将塑料原料放入注塑机的加料口中,经过传热系统加热,使其在一定温度下融化成为可流动的熔体。
3. 注射与压力:将热融化的塑料熔体通过螺杆推进器送入模具的射嘴,随后利用注塑机的压力系统施加一定的压力,推动熔体充满整个模具腔道。
4. 冷却与固化:熔体注入模具后,通过模具内部的冷却系统,将熔体迅速冷却,使其在模具内部形成所需产品的形状。
5. 开模与取出:冷却固化后,注塑机分离模具,开启模具,取出成型好的塑料制品。
如果有多腔模具,则会重复进行上述步骤,以获得更多产品。
值得注意的是,不同的塑料成型方法(如注塑、吹塑、挤塑等)在成型原理上会有所区别,但大致遵循上述基本原理。
此外,塑料的成型过程还需要考虑到模具的设计和制造、熔体流动性、冷却方式等因素,以确保最终产品的质量和形状的精准度。
注塑成型技术简介

3.3熔接痕
3.3.1物料温度或模具温度低 对策:提高物料温度或模具温度,加快注 射速度,在材料未降温的状态下迅 速熔合。 3.3.2排气不良 原因:熔接痕处有气体存在,熔料不易 熔合 对策:开排气槽或采用其它排气方式
3.3熔接痕 3.3.3脱模剂的影响 原因:当模具表面涂有脱模剂时,一旦接 合处的熔料沾有脱模剂,会因二者 相互不熔合而造成熔接痕加深、强 度降低。 对策:少使用脱模剂或不用
3.1材料不足(欠注、缺料、短射)
3.1.4排气不良 原因:型腔内空气不能有效排出,残留的空气受 材料挤压产生压力抵抗,材料不能将模腔 完全充满。 对策:⑴模具上开设适当的排气槽; ⑵降低注射速度; ⑶降低合模力; ⑷确认原料干燥程度、降低料温
3.1材料不足(欠注、缺料、短射)
3.1.5熔体压力损失大 原因:浇口或流道尺寸偏小,导致熔体流 动阻力大,不能将模腔充满。 对策:将浇口或流道尺寸扩大,或流道缩短。 3.1.6冷料堵塞浇口或浇道 原因:在材料充满模腔之前,浇口或浇道 已封闭,材料不能继续注入。 对策:扩大冷料井尺寸,提高射出速度或压力
2.2双分型面注塑模
2.3侧抽芯注塑模
3.成型技术
• 注塑工艺过程是从锁模、射出、保压、
冷却(塑化)、开模、到制品脱模,然 后再锁模射出的一个循环过程。 • 在原料、成型机、模具等因素确定之后, 对注塑工艺过程有显著影响的主要有以 下几个因素:熔体温度、模具温度、射 出速度、射出压力、保压压力及各阶段 的作用时间等。
1.2合模系统
• 合模系统是保证成型模具可靠地开闭,在注射
(保压)时能保持足够锁紧力的机构。 • 合模机构 基本要求:⑴有足够大的锁模力,保证成型过 程中不出现溢料;⑵开合模速度应可以调节, 为防止损坏模具和产品,避免机器的强烈震动, 合模时应设置为先快后慢,开模时应设置为先 慢、后快、再慢。
BMC注塑工艺及注塑机操作培训
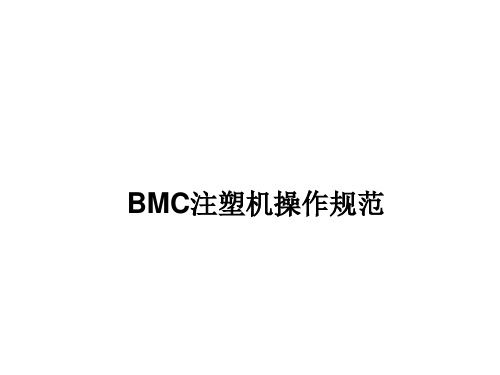
1.塑化装置
• 塑化装置主要由螺杆、机筒等组成,如下图所示 • (1)螺杆。热固性注塑机的螺杆主要用于对物料的塑化、混炼和将其注入模
腔中。 (2) BMC材料是一种热固性塑料,一般要求在15℃以上温度使用,否则其粘 度大,成型所需压力大,但是到60℃以上会发生交联固化反应,因此机筒的 温度必须严格控制。机筒的温度控制一般采用恒温控制的水加热系统,结构 示意如下右图所示。进行温度控制时,温水经充水阀、滤清器、水泵输送到
• (3)后抽胶:注射完成后,注座后退,喷嘴离开模具然后熔胶抽胶,熔胶抽 胶完注座前进。该动作适用于加工成型温度特别窄的塑料,由于喷嘴与模具 接触时间短,避免了热量的流失,也避免了熔料在喷嘴孔内的凝固。
• 抽胶就是防延,就是防止喷嘴处溢料。 • 练习题:前面射胶第一段位置为15mm,则在熔胶的图面中,熔胶位置一应设
所有近接开关 与碰块之间 距离为2-3mm
开模完近接开 关
开模完后高度
锁模慢近接开 关
锁模完上20mm
锁模完近接开 关
锁紧模具的位 置
开锁模调节
• 第二题:近接开关与碰块之间的距离为多少
• 锁模过程分为三段,大体是快-----慢-----高压;开模分为三段,大体是慢----快-----慢。
• 锁模力,一般按2ton/in2 , 1in2 =6.45cm2 , 或者F=(nA+B)*Pc/(0.6-0.8) • n:型腔数 • F:锁模力(kg) • B:流道和浇口在分型面的投影面积(cm2 ) • A :产品在分型面的投影面积(cm2 ) • Pc:型腔内塑胶熔体的压力(本厂使用的BMC一般为10-20MPa) • 锁模力太大或太小都不好,太小易跑披锋,太大易损坏模具,损坏设
热固性塑料注塑成型的分析

热固性塑料注塑成型的特点热塑性聚合物在成型中基本上是一种形态转化的物理过程。
而热固性聚合物在成型中不仅有物理状态的变化,还有化学变化,并且是不可逆的。
热固性聚合物在未交联前与热塑性聚合物相似,都是线型聚合物。
但热固性聚合物在分子链中带有反应基团或反应活点,成型时分子链通过自带的反应基团的作用或反应活点与交联剂(硬化剂)的作用而发生交联,使线型变成体型结构。
对于热固性聚合物的这种交联反应,粘度反映了它的固化程度。
粘度一.影响粘度的因素1.热固性塑料的粘度与热固化时间的关系:热固化时间在极值之前的一段时间内,聚合物的热固化反应不占优势,由松驰的结晶,粘度随时间的增加而减小。
在极值之后,优势,聚合物相对分子量增大很快,而使粘度增大。
2.热固性塑料的粘度对成型温度的关系:当成型温度在极值之前时,粘度主要取决于材料的物理变化,即随着温度的升高而减小,在极值之后,粘度因交联固化反应占优势而快速升高。
对于热固性塑料的注射正是利用这一点:在低于极值点的温度下,材料在注射机料筒内达到流动态(粘度低),以便注模;在大于极值点的温度下,材料可在模腔内固化成型。
3.随着剪切速率的增加,物料的粘度会降低,但由于物料的磨擦生热而使交联反应的活化能降低,从而加速了交联固化反应速率,又使物料的粘度迅速增加。
二.成型工艺1.温度塑料从料斗进入料筒后,一定要逐步受热塑化,温度分布不宜过分激烈。
因为温度的突变,会引起熔料粘度的变化。
见图所示热固性塑料在注塑过程中温度对粘度的变化。
注射时,塑料在喷嘴处流速很高,这样因磨擦生热而使塑料温升很快。
对射击熔料的温度最好控制在120~130℃,因为这时熔料呈现出最好的流动性,并接近于硬化的“临界塑性”的状态。
所以,各段温度的分布见表:2.压力一般情况下,注射压力应高一些,压力越高,收缩率越小,其制品的机械强度和电性能都较好。
压力越高,流速就越快,产生的磨擦热越多,固化时间就可缩短。
但是,注射压力高会引起制品内应力的增加,飞边增多和脱模困难。
常用热固性塑料的注塑成型工艺条件

常用热固性塑料的注塑成型工艺条件是什么?(1) 酚醛塑料注塑成型工艺条件酚醛塑料是热固性塑料中应用最多的一种注塑材料,一般多用木粉或纤维素做填充料。
酚醛熔体流动性好,加热时间范围也较宽。
酚醛塑料品牌种类比较多,能用于注塑成型的酚醛粉料及其工艺性能参数见表1。
表1 酚醛注塑粉的工艺性能和注塑成型工艺参数 牌号 流动性/mm 收缩率/% 体积系数≤ 模具温度/℃ 保压时间/S定模 动模 PF2A 2-151J 130~180 0.60~1.00 3PF2A 2-161J 130~1800.50~0.90 3 165~175 170~18020~30PF2A 4-151J ― ― ― PF2A 4-161J ― ― ― PF2A 4-160IJ 130~180 0.60~1.00 3 175~185 180~190 30~40 PF2C 3-431J 130~160 0.40~0.90 3 165~175 170~180 25~35 SP2201J130~1800.70~1.20―160~170170~18025~35(2) 氨基塑料注塑成型工艺条件氨基塑料中主要有脲甲醛、三聚氰胺甲醛和三聚氰胺酚醛,可用于注塑成型制品。
这种原料要求塑化时加热时间短,塑化时加热时间短,所以应采用较高的注射速度。
所以应采用较高的注射速度。
所以应采用较高的注射速度。
但高速注射成型又会引起制品有残留应力,但高速注射成型又会引起制品有残留应力,但高速注射成型又会引起制品有残留应力,使制品使制品容易产生裂纹。
这种原料的熔体固化条件要求较高,所以对机筒温度和成型模具温度范围应严格控制。
脲甲醛和三聚氰胺甲醛塑料的注塑成型工艺参数见表3。
(3) 不饱和聚酯塑料注塑成型工艺条件不饱和聚酯塑料用于注塑成型的品种有SMC 和UP 。
这种原料的成型性及工艺性良好。
这种原料的成型性及工艺性良好。
具体注塑具体注塑成型工艺参数见表3。
(4) 环氧树脂注塑料注塑成型工艺条件环氧树脂熔料注射后在5〜180°C 范围内迅速或缓慢固化,这与选用的固化剂和环氧体系有关。
- 1、下载文档前请自行甄别文档内容的完整性,平台不提供额外的编辑、内容补充、找答案等附加服务。
- 2、"仅部分预览"的文档,不可在线预览部分如存在完整性等问题,可反馈申请退款(可完整预览的文档不适用该条件!)。
- 3、如文档侵犯您的权益,请联系客服反馈,我们会尽快为您处理(人工客服工作时间:9:00-18:30)。
为改进制品的质量和重现性采用了许多不 同的和专门的技术。鉴于有一些热固性聚合物在 加热时产生气体,在模具被部分充满后往往有一 个放气操作。在这一步骤中,模具微微开启,以 便让气体逸出,然后迅即关闭,把余下物料再注 人。
注压模塑提供了较高的强度、较好的尺寸控 制,并改进了表面状态(外观),这是因为采用 了带有伸缩式膜腔与膜芯的模具而得到的,注射 过程中模具可以开启 1/8—l/2in,并随后迅速 压紧,似模具关闭那样。
注射模塑工艺过程利用一螺杆使物料流经 加热过的机筒,机筒则以水或油循环于机筒四周 的夹套中。螺杆可按每种材料的不同类型加以设 计,稍加压缩以脱除空气并加热物料获得低粘 度。大多数热固性物料在此处的流动都是相当好 的。
使物料进入模具的操作是中止螺杆转动和 用液压把螺杆高速推向前,使被塑化的低粘度物 料压入模具中。这种快速流动要求在 0.5 秒的 时间里填满模腔,压力需达到 193MPa。一旦填满 膜腔时物料的高速流动产生更大的摩察热以加
热固性塑料注塑利用一螺杆或一柱塞把聚 合物经一加热过的机筒(120~260F)以降低粘 度,随后注入一加热过的模具中(300—450F)。 一旦物料充满模具,即对其保压。此时产生化学 交联,使聚合物变硬。硬的(即固化的)制品趁 热即可自模具中顶出,它不能再成型或再熔融。
注塑成型设备有带一用以闭合模具的液压 驱动合模装置和一能输送物料的注射装置。多数 热固性塑料都是在颗粒态或片状下使用的,可由 重力料斗送入螺杆注射装置。当加工聚酯整体模 塑料(BMC)时,它有如“面包团”,采用一供料
为加工设备所克服。
菜呢!他满口答应着。结果程
热塑性塑料和热固性塑料在加热时都将降 低粘度。然而,热固性塑料的粘度却随时间和温 度而增加,这是因为发生了化学交联反应。这些 作用的综合结果是粘度随时间和温度而呈 U 型曲 线。在最低粘度区域完成充填模具的操作这是热 固性注射模塑的目的,因为此时物料成型为模具 形状所需压力是最低的。这也有助于对聚合物中 的纤维损害最低。
一般情况下,设备的能力按该设备所能生产
菜呢!他满口答应着。结果第二天又是睡到上班时间快到了才起
的制品体积的 85%确定。当设备以聚苯乙烯生产 能力来标志时,在确定制件重量计之生产能力时 必须考虑到它和热固性塑料密度上的差异。
目前流行的控制系统是计算机控制,可选择 注射速度、合模装置的负荷。工艺操作的程序、 侧模芯至移入模具中的运动、顶出装置的工作周 期以及机筒和模具温度的控制。一个特定模具和 特定原料依次加料的调定和记录的方法是极有 价值的。因为在工艺过程中有大量的变量。
机筒温度的控制是通过流经包覆机筒之夹
套的热水进行的。模具温度控制最普遍的是利用 插入式加热器进行,但也可以采用蒸汽或循环热 油进行。
高度可控的模具温度是获取均匀制品最重 要的。
常用设备的选择包括:整体模塑料所用的供 料器、快速更换模具系统、为快速注射用的液压 流体储料缸、模具滑动用的连接于液压系统上的 侧模芯、机械手式取件系统以及空气喷气装置 (去除每成型周期中产生的溢料)。
菜呢!他满口答应着。结果第二天又是睡到上班时间快到了才起
由玻璃纤维、填充料和聚酯不饱和树脂制成 的整体模塑料可以在机器上装上另外的专门设 备来完成注射模塑。将一活塞式供料机连接于机 筒上,以强制供料,随后可以用两种不同的方式 进行作业。一种带有传统的往复式螺杆,螺杆将 物料推向前方,同时混炼和加热。这需要螺杆末 端有一止过阀。防止物料返流回螺杆螺纹上,因 为物料的粘度很低。另外一种方式是利用柱塞或 活塞将物料压入模具模腔中,柱塞往往用于含玻 璃纤维重量超过 22%的物料,因为这对纤维的损 害较小,亦可得到较高的强度。
最早应用于热固性塑料成型的另一种工艺 方法是压塑法(pressionmoulding)和压铸法 (transferMoulding)与它 们相比, 注塑法 (InjectionMoulding)的优缺点如下:
注塑法比压塑法优越处是:较快的成型周期 (2~3 倍)过程自动化;制品变化较少;较低的 人工费;高的生产能力。
数常见设备在 100~600t 之间。钢板的厚度和机 器的刚性至为重要。使注料时尽可能少产生弯曲 变形,导致溢料去除困难。
机器的注射能力,需要根据充填模具所需最 大注射压力和模腔与流道体系内物料体积进行 分析。所需注射压力由聚酯整体模塑料所需的 96.5MPa 直到一些特种酚醛塑料所需的 207MPa。 机器的注射能力往往是以理论体积量来标志(螺 杆或活塞注射的面积乘以其冲程)。
注塑法相对于压塑法的缺点是:较高的设备 和模具投资;压塑法可以得到较高的制品强度和 较好的表面光洁度。
菜呢!他满口答应着。结果第二天又是睡到上班时间快到了才起
压铸法的优点一般介于注塑法和压塑法之 间。
设备
选择热固性塑料注塑用设备的重要因素包 括:合模装置能力和注塑能力;控制系统和机筒 温度。
闭合压力以吨计的合模装置,其选择应根据 制品和流道的确定投影成型面积。所需吨位可由 1.5~5t/in2,这取决于模塑制品的复杂程度和 所用的原材料。设备大小在 30~3000t 间,大多
汽车工业:发动机部件、头灯反射镜和制动 用制品。
电气工业:断路器、开关壳体和线圈架。 家用电器:面包烘箱板、煮咖啡器的底座、 电动机整流子、电动机外壳和垃圾处理机外壳。 其它:电动工具壳、灯具外壳、气体流量计 和餐具。
1cv0f3c9a 易博
菜呢!他满口答应着。结果第二天又是睡到上班时间快到了才起
由于聚合物的低粘度,它流入分模线上形成 一层薄的膜状物,因此,热固性塑料成品常常需 修整去除飞边。模塑制品的飞边去除往往是通过 将制品进行滚光或将它们通过一台设备,在这台 设备中,高速状态的塑料粒敲掉了脆的飞边层。
应用
注射模塑法生产出的热固性材料的主要市 场包括:
活塞将物料压入螺纹槽中。
采用这种工艺方法的加工聚合物是(依其用 量大小排列);酚醛塑料、聚酯整体模塑料、三 聚氰胺、环氧树脂、脲醛塑料、乙烯基酯聚合物 和邻苯二甲酸二烯丙酯(DAP)。
多数热固性塑料都含有大量的填充剂(达 70%重量份),以降低成本或提高其低收缩性能, 增加强度或特殊性能。常用填充剂包括玻璃纤 维、矿物纤维、陶土、木纤维和炭黑。这些填充 物可能十分有磨损性,并产生高粘度,它们必须
菜呢!他满口答应着。结果第二天又是睡到上班时间快到了才起
速化学反应。模腔一旦被填满,注射压力就将降 到保压压力 34.5—68.9MPa。这种保压压力维持 在物料上 5—10 秒,随后卸压,然后开始下一个 周期塑化阶段。
这种物料被保持在热的模具中,直至变硬, 然后打开合模装置,顶出制品。制品刚顶出时可 以是轻度未固化和有点柔软,在取出后 1 分钟或 2 分钟内利用制品内部保留的热量完成最终固 化。热固性制品的整个生产周期为 10—120 秒钟, 这取决于制品厚度和原材料的类别。