注塑工艺培训资料
注塑成型工艺培训资料
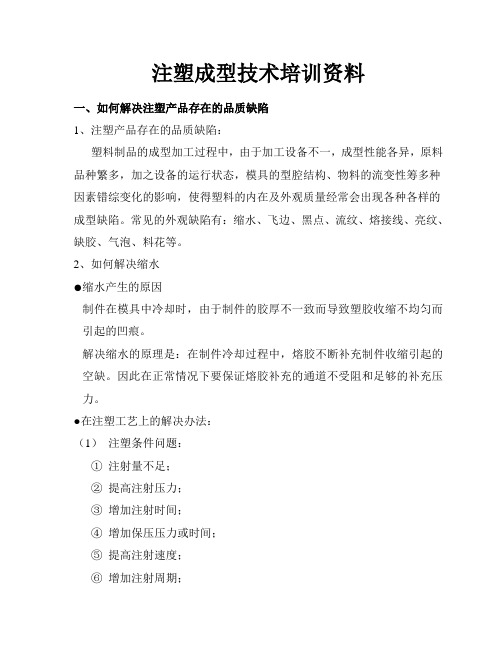
注塑成型技术培训资料一、如何解决注塑产品存在的品质缺陷1、注塑产品存在的品质缺陷:塑料制品的成型加工过程中,由于加工设备不一,成型性能各异,原料品种繁多,加之设备的运行状态,模具的型腔结构、物料的流变性筹多种因素错综变化的影响,使得塑料的内在及外观质量经常会出现各种各样的成型缺陷。
常见的外观缺陷有:缩水、飞边、黑点、流纹、熔接线、亮纹、缺胶、气泡、料花等。
2、如何解决缩水●缩水产生的原因制件在模具中冷却时,由于制件的胶厚不一致而导致塑胶收缩不均匀而引起的凹痕。
解决缩水的原理是:在制件冷却过程中,熔胶不断补充制件收缩引起的空缺。
因此在正常情况下要保证熔胶补充的通道不受阻和足够的补充压力。
●在注塑工艺上的解决办法:(1)注塑条件问题:①注射量不足;②提高注射压力;③增加注射时间;④增加保压压力或时间;⑤提高注射速度;⑥增加注射周期;⑦操作原因造成的注射周期反常。
(2)温度问题:①物料太热造成过量收缩;②物料太冷造成充料压实不足;③模温太高造成模壁处物料不能很快固化;④模温太低造成充模不足;⑤模子有局部过热点;⑥改变冷却方案。
(3)模具问题:①增大浇口;②增大分流道;③增大主流道;④增大喷嘴孔;⑤改进模子排气;⑥平衡充模速率;⑦避免充模料流中断;⑧浇口进料安排在制品厚壁部位;⑨如果有可能,减少制品壁厚差异;⑩模子造成的注射周期反常。
(4)设备问题:①增大注压机的塑化容量;②使注射周期正常;(5)冷却条件问题:①部件在模内冷却过长,避免由外往里收缩,缩短模子冷却时间;②将制件在热水中冷却。
3、如何解决飞边●产生飞边的原因:产品溢边往往由于模子的缺陷造成,其他原因有:注射力大于锁模力、物料温度太高、排气不足、加料过量、模子上沾有异物等。
●如何判断产生飞边的原因:在一般情况下,采用短射的办法。
即在注塑压力速度较低、不用保压的情况下注塑出制件90%的样板,检查样板是否出现飞边,如果出现,则是模具没有配好或注塑机的锁模压力不足,如果没有出现,则是由于注塑条件变化而引起的飞边,比如:保压太大、注射速度太快等。
注塑成型工艺培训资料

保压压力影响
过保压Over packing
保压压力高,浇口附近体积收缩量少 远离浇口处保压压力低且体积收缩量较大 导致产品翘曲变形,产品中央向四周推挤 形成半球形 (Dome Shape)
保压不足Under packing
浇口附近压力低 远离浇口处压力更低 导致产品翘曲变形,产品中央向四周拉扯 形成馬鞍形 Twisted shape
• 也是一般所称的固化时 间(Cure Time)
• 当熔体进入模腔,碰到 金属表面时,熔体冷却 的步骤就己经开始
开始储料了
回目录页
成型过程图解
开模时间
• 整个行程包括公模后移, 模具打开,成品顶出及移 出,模具关闭等(下一次 充填前)。
为下一阶段做好准备了!
回目录页
成型示意模型
產品模穴
模型竖胶道与浇口
塑料件产能测算与注塑成型工艺
目录
• 塑料件产能测算 • 注塑成型工艺
产能测算
• 年度产能测算 • 月度产能测算 • 日产能测算 • 峰值测算(最高峰的日
产能) 注意:注塑机台和模具产
能相匹配
注塑成型工艺
注塑成型过程
注塑成型条件 成型参数设定 成型条件VS产品
常见质量问题分 析及对策
模具结构图
本
回目录页
注射速度的影響
較長的充填時間 較慢的射出速度
較厚的凝固層
較短的充填時間 較快的射出速度
較薄的凝固層
熔体
V1
Melt
V2>V1
V2
回目录页
注塑速度影响
等速推進
根据产品外型 及厚度调整射速
Higher Pressure
Lower Pressure
注塑培训资料
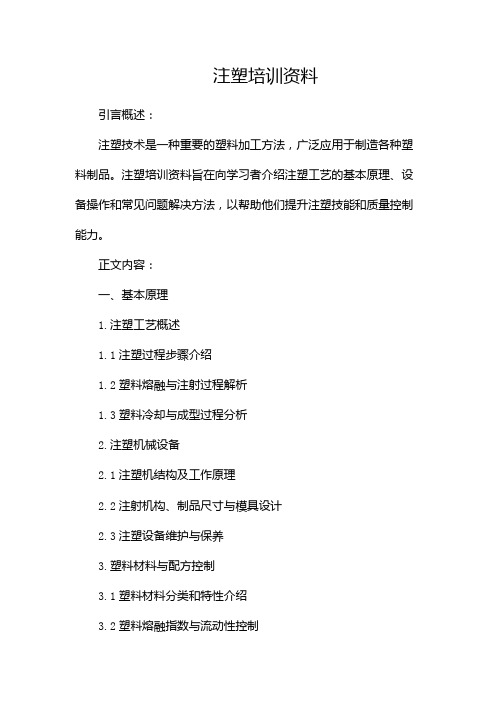
注塑培训资料引言概述:注塑技术是一种重要的塑料加工方法,广泛应用于制造各种塑料制品。
注塑培训资料旨在向学习者介绍注塑工艺的基本原理、设备操作和常见问题解决方法,以帮助他们提升注塑技能和质量控制能力。
正文内容:一、基本原理1.注塑工艺概述1.1注塑过程步骤介绍1.2塑料熔融与注射过程解析1.3塑料冷却与成型过程分析2.注塑机械设备2.1注塑机结构及工作原理2.2注射机构、制品尺寸与模具设计2.3注塑设备维护与保养3.塑料材料与配方控制3.1塑料材料分类和特性介绍3.2塑料熔融指数与流动性控制3.3配方设计及其对制品质量的影响二、设备操作1.注塑模具安装与调试1.1模具安装的步骤和注意事项1.2模具调试的原则和方法2.注塑机操作技巧2.1注塑机开机前的准备工作2.2注塑机操作面板及参数设置2.3操作中的常见问题及解决方法3.温度和压力控制3.1注塑过程中温度的控制与意义3.2注塑过程中流道压力的控制与优化3.3温度和压力异常的判断和处理三、质量控制1.注塑制品缺陷与分析1.1常见的注塑制品缺陷类型1.2缺陷产生的原因与分析方法1.3预防和解决制品缺陷的措施2.注塑制品检测与测试2.1检测设备与方法概述2.2注塑制品物理性能测试2.3检测结果分析及质量控制措施3.注塑工艺参数的优化3.1注塑工艺参数的选择和调整3.2工艺参数优化的试验方法与流程3.3注塑工艺参数优化的实例和经验总结四、安全与环保1.注塑操作的安全措施1.1注塑设备安全使用规范1.2塑料材料储存和处理的安全注意事项1.3紧急事故处理与应急措施2.注塑过程的环保问题2.1废水、废气、废渣的处理与回收利用2.2资源节约和能耗优化措施五、未来发展趋势1.自动化与智能化1.1注塑生产线自动化控制1.2智能注塑机的应用前景2.环保和可持续发展2.1生物降解塑料的应用前景2.2注塑技术对环境的影响与改进方向3.新材料和新工艺3.1高性能塑料的研发和应用3.2先进注塑工艺的研究与实践总结:注塑培训资料涵盖了注塑技术的基本原理、设备操作、质量控制、安全与环保以及未来发展趋势等重要内容。
注塑技术培训资料
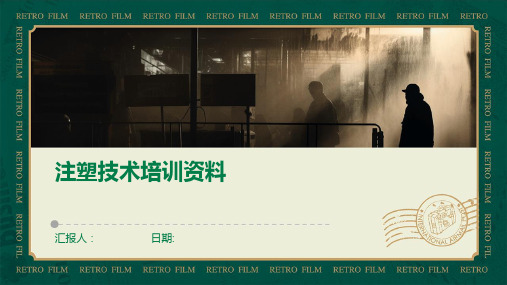
成型过程中的注意事项及维护保养方法
温度控制 压力调整 循环时间控制 维护保养
注塑过程中需严格控制模具和原材料的温度,以获得最佳的成 型效果。同时,定期检查加热元件、冷却系统等是否正常工作
。
根据产品需求和模具结构,合理调整注射压力、保压压力等参 数,以保证注塑件的质量和稳定性。
优化注射、保压、冷却等环节的时间,以提高生产效率。
操作步骤
根据生产计划,准备好原料、模具和 机器,调整注射成型参数,进行生产 。
注射压力、注射速度、保压时间等参数的设置与调整
01
02
03
注射压力
根据产品大小和模具情况 设定适当的注射压力,一 般不超过1500bar。
注射速度
根据产品厚度和模具结构 设定适当的注射速度,一 般不超过150mm/s。
保压时间
定期对注塑机、模具等设备进行保养,包括润滑、清洁、紧固 等措施,以延长设备的使用寿命。
成型后的产品检验及质量评估方法
外观检测
尺寸检测
观察注塑件是否有气孔、缩孔、流痕等缺 陷,以及尺寸是否符合要求。
使用测量工具对注塑件的尺寸进行精确测 量,包括长度、宽度、高度等参数。
性能测试
质量评估
根据产品需求,对注塑件进行相应的性能 测试,如耐温性、耐冲击性、耐磨损性等 。
具有较好的强度和耐冲击 性,适用于机械零件和家 电制品等领域。
塑料的收缩率及影响因素
塑料的收缩率
塑料制品的收缩率是指其尺寸在熔融状态下与冷却后的差异,不同的塑料品种和 加工条件下的收缩率会有所不同。
收缩率的影响因素
塑料的收缩率主要受到其结晶度、分子量、添加剂和加工条件等因素的影响。
选材原则及注意事项
由于冷却不均匀或其他因素,可 能导致成型件变形。解决方法是 优化冷却系统设计和成型条件,
注塑工艺培训资料doc2024

注塑工艺培训资料引言概述:注塑工艺是一种常用的塑料加工方法,通过将熔融状态的塑料材料注入模具中,并在一定的温度和压力下进行冷却和固化,最终形成所需的塑料制品。
注塑工艺具有生产效率高、制品质量好、产品多样化等优点,被广泛应用于各个领域。
本文将对注塑工艺进行详细的介绍和分析。
正文内容:一、注塑工艺基础知识1.注塑工艺的定义和发展历史2.注塑机的组成和工作原理3.塑料材料的选型和性能要求4.模具的设计和制造5.注塑过程中的工艺参数二、注塑机操作与维护1.注塑机的开机、关机和调试2.调节注射速度、温度和压力等参数的方法3.常见注塑机故障及其解决方法4.定期维护与保养措施5.注塑机的能耗管理与环保措施三、注塑工艺优化与改进1.注塑工艺的优化目标和方法2.挤出率和气蚀的控制与改善3.空气泡和热熔背变形的解决方案4.热应力和冷却速度的控制与调整5.模具设计的创新与改进四、注塑制品质量控制1.注塑制品缺陷的分类与原因分析2.缺陷防控措施与改进方法3.模具的维护与修复4.注塑制品的非destruct性检测方法5.注塑制品的可靠性测试与验证五、注塑工艺的发展趋势1.注塑工艺的自动化与智能化2.注塑技术在新材料、新工艺中的应用3.环保要求对注塑工艺的影响与挑战4.注塑工艺在新兴行业中的应用前景5.优化成本和提高效率的新思路和新方法总结:通过本文的阐述,我们对注塑工艺的基础知识、操作维护、优化改进、质量控制和发展趋势都有了深入的了解。
注塑工艺不仅仅是一种加工方法,更是一个综合性的领域,需要了解和掌握不同的技术和知识。
未来,随着科技的进步和市场需求的变化,注塑工艺将继续发展并在更多领域中得到应用。
我们需要不断学习与创新,不断提高自身的专业能力,以适应行业发展的需求。
注塑工艺技术培训教材
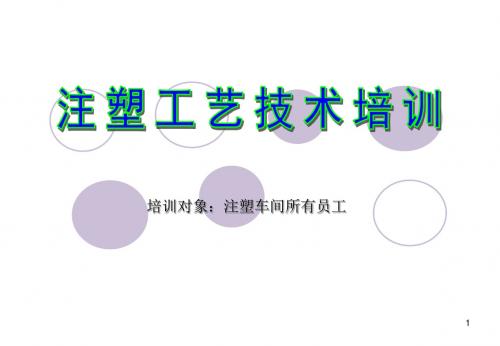
7
步骤10:关闭油泵电动机。 步骤11:拧紧动模板、定模板上的模具压板螺栓, 锁紧动、定模板上的模具。 步骤12:用螺栓、模具压板、压板垫块、平垫圈、 弹簧垫圈等把模具的固定模板部份固定模板上, 此时注塑机不必用很大的锁紧力。注意:螺牙 旋进机床固定板螺孔深度最少应为螺栓直径的 1.5---2倍。
步骤2:开模,使模板开启 步骤3:将注射座向后移动 步骤4:关闭油泵电动机 步骤5:调整顶针的位置与数目,使之与模具相 适合。 步骤6:首先清理模板平面及定位孔,以及模具
表面的脏物、毛刺,再吊起成对的模瓣,放入
模板内(放入时,注意不要让模具拉杆及其他 机器部件相撞),把定位环装入固定模板上的
6
注意! 起吊前,应确定前后模不会分离!!
15
显示器为各种参数调整的依据, F1到F8可以显示不同的画面。
16
17
要求保 险杠与 挡块距 离2CM
紧急停止按
钮
18
冷却水系统 外进水,内回 水
19
接班和换模后生产时检查冷却水是否开启
二、注塑安全操作规程
注塑操作工上岗前必须接受以下安全知识培训并严格遵守,确保人身设备的安全。
• • • • • • •
20
二、操作工注塑作业规程
• 确保以上条件都完成后,才能进行下一步的工作。 • 其安全操作规程如下: • 按电动机启动键,启动电动机;观察各种动作和压力是否正常,安全门和急 停开关等安全保护装置是否符合要求; • 按住关模键做关模动作到关模结束,先对空注射,观察料的熔融状况是否正 常; • 按住注射座前进键,使注射座前进,至喷嘴口与模具的注口接触; • 观察模具顶板的复位情况没问题后,按半自动,进入半自动状态; • 关闭保险门,机器开始半自动动作; • 观察制品的状态,直至合格,否则请相关人员及时调整; • 在生产结束时按下列次序操作:a、按加热开关,关闭料筒电热;b、关闭 料斗挡板;c、注射座后退,将料筒内的余料彻底清除,使料筒处在射空状 态;d、在手动状态下合模,合模前,须对型腔型芯部分喷涂防锈剂,使动 定模间隙为1cm左右;e、关油泵马达,关注塑机总电源;f、关闭设备、模 具冷却系统,整理现场卫生
注塑培训资料
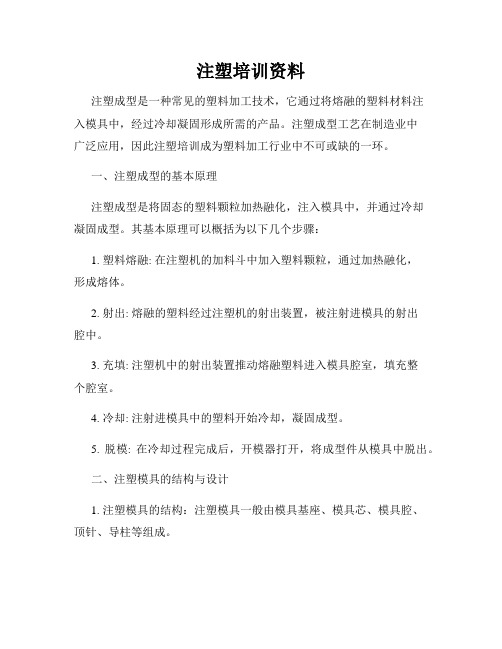
注塑培训资料注塑成型是一种常见的塑料加工技术,它通过将熔融的塑料材料注入模具中,经过冷却凝固形成所需的产品。
注塑成型工艺在制造业中广泛应用,因此注塑培训成为塑料加工行业中不可或缺的一环。
一、注塑成型的基本原理注塑成型是将固态的塑料颗粒加热融化,注入模具中,并通过冷却凝固成型。
其基本原理可以概括为以下几个步骤:1. 塑料熔融: 在注塑机的加料斗中加入塑料颗粒,通过加热融化,形成熔体。
2. 射出: 熔融的塑料经过注塑机的射出装置,被注射进模具的射出腔中。
3. 充填: 注塑机中的射出装置推动熔融塑料进入模具腔室,填充整个腔室。
4. 冷却: 注射进模具中的塑料开始冷却,凝固成型。
5. 脱模: 在冷却过程完成后,开模器打开,将成型件从模具中脱出。
二、注塑模具的结构与设计1. 注塑模具的结构:注塑模具一般由模具基座、模具芯、模具腔、顶针、导柱等组成。
2. 注塑模具的设计:注塑模具设计需要考虑成型件的形状、尺寸、材料流动性等因素,以确保最终产品的质量与精度。
三、注塑设备的选择与操作1. 注塑机的选择:根据生产需求和产品特性选择适合的注塑机型号,考虑射出量、射出压力、射出速度、射出温度控制等因素。
2. 注塑机的操作:注塑机的操作包括设定射出参数、模具安装、开机调试、生产检验等环节,需要熟悉设备的操作界面和控制系统。
四、塑料材料与添加剂的选择1. 塑料材料的选择:根据产品的性能要求,选择合适的塑料材料,如聚丙烯、聚乙烯、聚苯乙烯等。
2. 添加剂的选择:根据塑料的特性,可以添加增强剂、稳定剂、着色剂等,以提升产品的力学性能、稳定性和外观效果。
五、注塑成型的常见问题与解决方法1. 短冲、缺料现象:可能是注塑机射出量不足或模具缺陷导致,需要检查射出参数和模具结构。
2. 热裂纹、气泡:可能是塑料材料选择不当或注射过程中存在气体混入,需要更换合适的塑料材料或调整注射工艺。
3. 凸起、缩水等缺陷:可能是模具设计不合理或模具损耗过大,需要优化模具结构或更换模具。
注塑培训资料
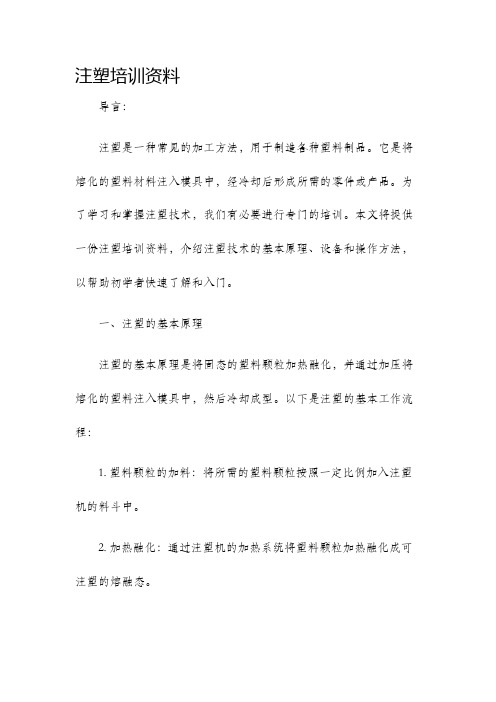
注塑培训资料导言:注塑是一种常见的加工方法,用于制造各种塑料制品。
它是将熔化的塑料材料注入模具中,经冷却后形成所需的零件或产品。
为了学习和掌握注塑技术,我们有必要进行专门的培训。
本文将提供一份注塑培训资料,介绍注塑技术的基本原理、设备和操作方法,以帮助初学者快速了解和入门。
一、注塑的基本原理注塑的基本原理是将固态的塑料颗粒加热融化,并通过加压将熔化的塑料注入模具中,然后冷却成型。
以下是注塑的基本工作流程:1. 塑料颗粒的加料:将所需的塑料颗粒按照一定比例加入注塑机的料斗中。
2. 加热融化:通过注塑机的加热系统将塑料颗粒加热融化成可注塑的熔融态。
3. 注塑过程:将熔融的塑料通过注塑机的螺杆推动器,注入模具中的注射腔。
4. 冷却成型:待塑料在模具中冷却定型后,打开模具取出成品。
5. 循环重复:重复上述步骤进行连续的注塑生产。
二、注塑设备1. 注塑机注塑机是注塑过程中最关键的设备,它包括了控制系统、加热系统、注射系统等。
注塑机的选择应根据生产需求、注塑材料的特性和产品尺寸来进行。
常见的注塑机有垂直注塑机、水平注塑机和全电动注塑机等。
2. 模具模具是用来决定所注塑产品最终形状的关键部件。
它包括注射腔、冷却系统和顶出机构等。
模具材料常用的有钢、铝等。
模具的设计和制造应考虑产品的结构、尺寸、表面要求等多个因素。
三、注塑操作方法1. 准备工作在进行注塑操作之前,需要对注塑机进行预热、清洁和检查,确保所有零部件正常运行。
同时,准备好所需的塑料颗粒、模具、辅助设备等。
2. 注塑过程(1)设置注塑参数:根据要注塑的塑料类型和产品要求,设置合适的注塑参数,包括注射速度、注射压力、保压时间等。
(2)开模和关模:将模具安装到注塑机上,通过控制系统进行模具的开合操作。
(3)加料和加热:将塑料颗粒加入注塑机的料斗中,并启动加热系统将塑料加热融化。
(4)注塑过程:通过操作注塑机的控制系统,控制螺杆的运转和注塑过程中的温度、压力等参数。
注塑培训资料
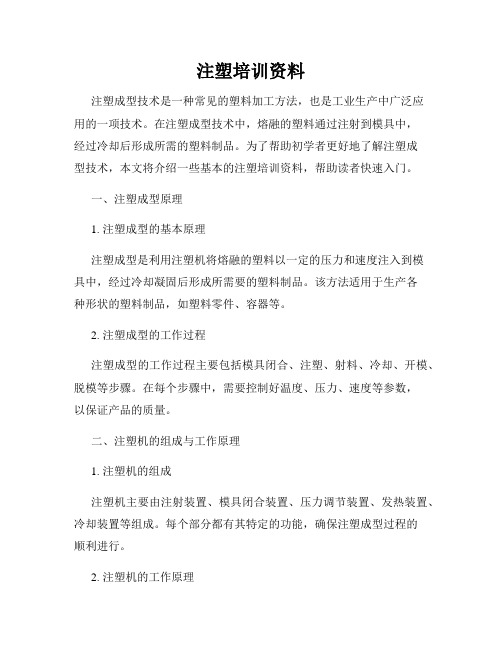
注塑培训资料注塑成型技术是一种常见的塑料加工方法,也是工业生产中广泛应用的一项技术。
在注塑成型技术中,熔融的塑料通过注射到模具中,经过冷却后形成所需的塑料制品。
为了帮助初学者更好地了解注塑成型技术,本文将介绍一些基本的注塑培训资料,帮助读者快速入门。
一、注塑成型原理1. 注塑成型的基本原理注塑成型是利用注塑机将熔融的塑料以一定的压力和速度注入到模具中,经过冷却凝固后形成所需要的塑料制品。
该方法适用于生产各种形状的塑料制品,如塑料零件、容器等。
2. 注塑成型的工作过程注塑成型的工作过程主要包括模具闭合、注塑、射料、冷却、开模、脱模等步骤。
在每个步骤中,需要控制好温度、压力、速度等参数,以保证产品的质量。
二、注塑机的组成与工作原理1. 注塑机的组成注塑机主要由注射装置、模具闭合装置、压力调节装置、发热装置、冷却装置等组成。
每个部分都有其特定的功能,确保注塑成型过程的顺利进行。
2. 注塑机的工作原理注塑机通过螺杆将塑料颗粒加热并熔化,然后将熔融的塑料注射到模具中。
在注射过程中,需要控制好注射速度、压力等参数,以获得所需的产品。
三、模具设计与制造1. 模具设计的基本原则模具设计是注塑成型过程中至关重要的一环。
设计合理的模具可以提高生产效率和产品质量。
模具设计时需要考虑产品的形状、尺寸、材料等因素,同时还要注意模具的结构和材料的选择。
2. 模具的制造过程模具的制造包括模具加工、组装、调试等步骤。
其中,模具加工是模具制造的关键环节,需要使用精密加工设备进行加工,确保模具的精度和质量。
四、塑料材料选择与加工参数调整1. 塑料材料的选择不同的塑料材料具有不同的特性和适用范围。
在进行注塑成型时,需要根据产品的要求选择合适的塑料材料,同时考虑到成本、环保等因素。
2. 加工参数的调整在注塑成型过程中,需要根据具体的产品和塑料材料来调整一些加工参数,如注射压力、注射速度、冷却时间等。
通过合理的参数调整,可以提高产品的质量和产量。
注塑工艺培训资料

注塑工艺培训教程成型参数设定要领与优化注塑成型四大要素1)塑胶原料2)注塑模具3)注塑机4)成型工艺技术成型工艺的五种参数:温度时间压力速度位置切换注射工艺参数◆储料参数;加料量(注射量)、余料量(缓冲垫)、螺杆转速、背压(塑化压力)、倒塑(松退)。
◆注射参数:注射压力、注射速度.保压压力和时间、分段注射与位置◆温度参数:料筒温度、喷嘴温度、模具温度、油液温度。
◆时间参数:注射时间、保压时间、中间停留时间、储料时间、冷却时间。
一、储料工艺参数1)加料量(注射量)2)余料量(缓冲垫)3)螺杆转速4)背压(塑化压力)5)倒塑(松退)1.1加料量的设定螺杆从注射终止位置后退到加料终止位置的距离称为计量行程或储料行程。
因此,螺杆端前面部分的塑料容积就是螺杆后退行程的计量容积(即注射量),所以计量行程办是注射行程。
1.2余料量(缓冲垫)在料量设定时,料筒前端熔料被注射的分量在零位前要预留一段位置作缓冲用,称为“缓冲垫”。
此段位置不少于3mm,通常设定10mm。
1.3余料量的调整作用1)设定缓冲垫可提高注射量的重复精度和稳定塑件成型质量。
2)在保压阶段有一个缓慢推进过程,将剩余的高积存压力继续向模腔及流道传送,使塑件冷却收缩时不断有料补充。
3)可改善塑件密度,使塑件表面光泽度好、颜色均匀、尺寸稳定、内应力小,从而提高塑件的质量。
4)对缓冲垫位置大小的调节.可改普某些工艺上的不足。
5)保护螺杆头如射胶射尽到零位置或预留射终位置过小,在注射惯性或机器控制失准的情况下.容易出现螺杆头卡住料筒头,在预料动作时甚至会拧断螺杆头。
1.4螺杆转速的作用螺杆转速越高.熔料在螺杆中输出能力和剪切效应越好。
调整螺杆转速(n/min)即是调整塑化效果及加料进行时间。
一般情况下加料时间的长短是由螺杆转速与背压所决定:螺杆转速越高,背压压力越小,加料时间越短,反之加料时间越长。
因此螺杆转速是影响塑化能力、塑化质量和储料时间的主要参数。
注塑技术培训资料
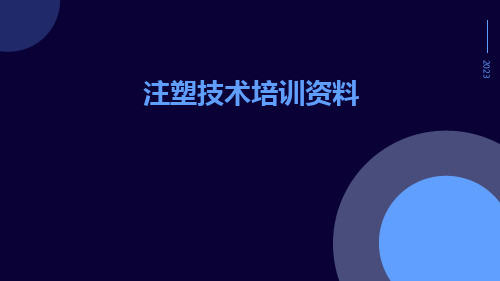
注塑生产效率提升策略
06
注塑技术发展趋势与展望
自动化生产
随着工业4.0的发展,自动化生产逐渐成为注塑行业的重要趋势。通过引入机器人、自动化设备等,实现生产过程的智能化和自动化,提高生产效率和质量。
智能化技术
智能化技术如人工智能、大数据分析、物联网等在注塑行业的应用逐渐普及。这些技术能够帮助企业优化生产流程、降低成本、提高产品质量等。
高性能复合材料与多材料成型技术
THANK YOU.
谢谢您的观看Βιβλιοθήκη 注塑生产计划与调度03
04
05
注塑生产成本控制
详细描述
2. 生产过程成本控制
4. 人工成本控制
总结词
1. 原材料成本控制
3. 能源成本控制
01
02
03
04
05
06
4. 加强员工培训
详细描述
提高注塑生产效率主要包括以下策略
2. 自动化与智能化
引入自动化设备和智能化技术,如机械手、智能仓库等,减少人工干预,提高生产效率。
缩痕
由于制品厚度不均或冷却不充分,导致制品表面出现缩痕。解决方案包括调整注射速度或优化冷却系统。
翘曲
由于冷却不均匀或保压时间不足,导致制品形状发生变化。解决方案包括优化冷却系统或增加保压时间。
气泡
由于注射速度过快或气体未被完全排除,导致制品内部产生气泡。解决方案包括降低注射速度、增加排气孔或优化模具设计。
注塑成型常见问题及解决方案
03
注塑模具基础知识
模具通常由动模和定模两个主要部分组成,动模又称凸模,定模又称凹模。
模具的组成
模具是实现塑料成型的重要工具,通过模具成型可得到具有特定形状、尺寸和性能的制品。
注塑工艺培训资料史上最全PPT课件
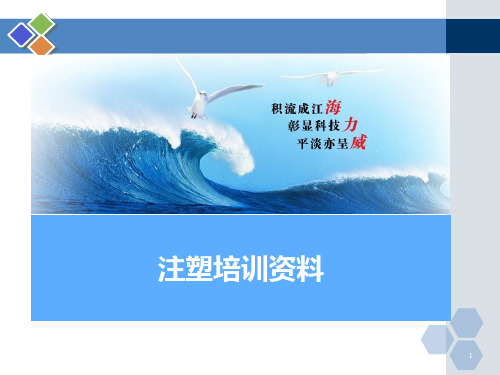
目录
2.成型工艺的设定
13
成型参数的组成
时间 压力 速度 位置 温度
五 因 素 缺 一 不 可
14
五要素解释
时间 压力 速度
材料干燥时间、计量时间、 填充时间、保压时间、冷 却时间、周期
锁模压力、填充压力、保压 压力、计量负荷压力、螺杆 背压力
计量速度(螺杆转速)、射出速度、 开锁模速度、顶出速度、减压速 度
位置
材料放入量、注塑开始位置、注塑最前进 位置、注塑结束位置、计量开始位置、减 压位置、注塑位置
温度
材料干燥、加热筒温度、树脂温度、模具温度、制品 取出温度、室内温度、油温、冷却水温度
15
成型条件设定前确认
01
树脂特性
02
制品大小
03
胶位厚薄
04
模具大小
05
使用机器容模量、射胶量、锁模力等
16
成型准备
8
注塑机的种类---螺杆式注塑机
二、螺杆式注塑系统:螺杆式注塑系统的结构组成:由塑化装置(螺杆,机筒、 射嘴、加热器等)、料斗、计量装置、螺杆传动装置、注塑油缸、注塑座整体移 动油缸等组成。 特点:物料受热均匀,物料受压均匀塑化程度好,物料计量准确。 总结:螺杆式注塑机是现在注塑成型的主流设备,可成型各种通用塑料和工程塑 料,成型过程稳定,生产效率较高。
注塑培训资料1标题添加源自点击此处输入相 关文本内容
标题添加
点击此处输入相 关文本内容
总体概述
点击此处输入 相关文本内容
点击此处输入 相关文本内容
2
目录 1.注塑机讲解 2.成型工艺的设定 3.成型过程中容易出现的不良及解决方法
3
目录
1.注塑机讲解
注塑成型工艺培训资料
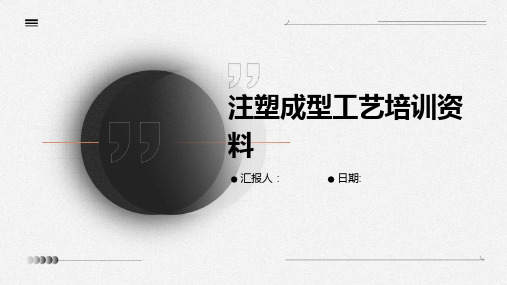
02
注塑成型前的准备
塑料材料的选取与检验
总结词
塑料材料的选取与检验是注塑成型工艺的第一步,对于最终制品的质量、成本 和生产效率具有重要影响。
详细描述
在选取塑料材料时,需要考虑制品的使用场合、受力情况、外观要求以及成本 等因素。同时,需要对塑料材料进行检验,确保其符合相关标准和要求,例如 密度、收缩率、流动性等。
构进行合理设定。
冷却时间
冷却时间对于确保注塑件充分冷却 和减少残余应力至关重要,应根据 产品要求和模具结构进行合理设定 。
周期时间
周期时间是整个注塑成型过程的时 间,需综合考虑注射时间、冷却时 间、取出产品等因素。
04
注塑成型后的处理及检验
塑料件的取出与处理
塑料件的取出
在注塑机完成注塑成型后,应立即将 塑料件从模具中取出,以避免塑料件 在高温下变形或产生水口。
注塑机的选取与调试
总结词
注塑机的选取与调试是注塑成型工艺的 关键环节,对于制品的质量和生产效率 具有重要影响。
VS
详细描述
在选取注塑机时,需要考虑制品的形状、 尺寸、材料特性以及生产效率等因素。同 时,需要对注塑机进行调试,确保其工作 状态良好,例如注射压力、注射速度、模 具温度等参数的调整。此外,还需要对制 品的尺寸和外观进行检测,确保其符合相 关标准和要求。
废弃物回收和处理
对于注塑制品的废弃物,应采取有效的回收和处理措施,以减少对环境的污染。同时,应积极推广可循环利用的 塑料材料,实现资源的有效利用。
感谢观看
THANKS
05
02
加料
将塑料原料加入注塑机中,经过加热熔融后 形成熔体。
04
保压
在注射后,对模具进行保压,以防止 制品产生收缩和变形。
注塑工艺培训资料
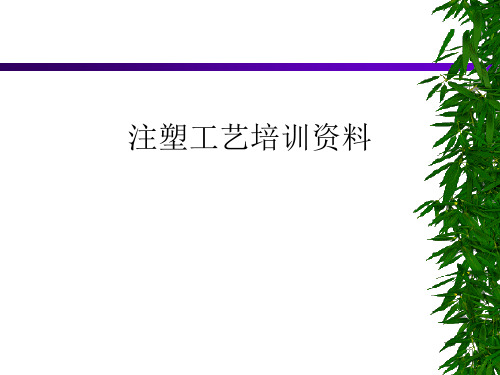
3、PP: 成型温度 170 ℃ -220℃ 烘料温度 70℃-90 ℃ 模具温度 50 ℃-70 ℃ 烘料时间 1-2H
4、PC: 成型温度 240 ℃ -300℃ 烘料温度 100℃-140 ℃ 模具温度 70 ℃-110 ℃ 烘料时间 4-10H
5、PA6: 成型温度 220 ℃ -300℃ 烘料温度 90℃-110 ℃ 模具温度 40 ℃-60 ℃ 烘料时间 4-6H
凸起。 4、气雾:制件表面不光泽成雾状。 5、流痕:制件表面有线状(类似于水花)。 6、熔接线:制件水口或分型面位置有线状。 7、拉伤:制件加强筋或某个部位有伤痕。 8、烧焦:制件分型面或者边缘成黑色现象。
模具:多个制件在同一个部不变化
9、划伤:
人为:制件在不同地方
以上不良现象具体以实物为准
6、PA66: 成型温度 250 ℃ -300℃ 烘料温度 90℃-140 ℃ 模具温度 60 ℃-110 ℃ 烘料时间 4-6H
注塑工艺参数
注塑工艺参数主要可分为: 1、射出压力 2、射出速度 冷却
3、时
间 射胶
保压
4、位
储料
置
射出 保压
模
5、温 度 具
螺 杆
6、背 压 料
注塑参数的作用; 1、射出压力 其作用是克服塑料从料筒流向型腔的阻力,给予熔体充模的
速率以及对熔体进行压实,确保制件成型。
2、射出速度 其作用是确保制件表面光泽对辅助制件成型。
3、保压时间 其作用是确保制件最后成型。 冷却时间 其作用是使制件塑化成型冷。 射胶时间 其作用是螺杆对模具型腔填充及螺杆后退。
4、背 压 其作用是螺杆顶部熔体在螺杆转动后退时所受到的压力。
5、螺杆温度 其作用是材料在料筒进入螺杆后熔化。 模具温度 其作用是防止制件后收缩使产品表面更光泽。 料筒温度 其作用是确保材料在其所需的温度下成型防止水份。
注塑工艺培训资料
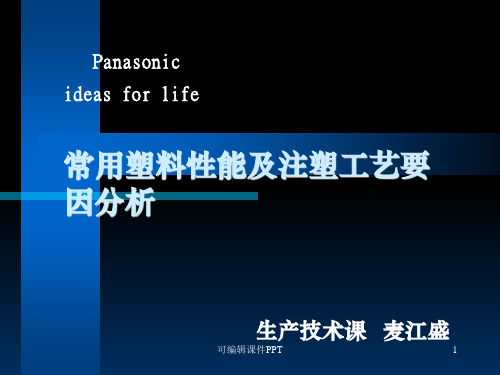
聚碳酸酯(PC)性能表
项目 密度 拉伸强度 断裂伸长率 弯曲强度 冲击强度(缺口) 布氏硬度 热变形温度(1.81MPa) 成型收缩率
单位 g/cm3 MPa
℃
MPa kJ/m2
R ℃ %
数值 1.05 63
180~260 97 6.0 121 89
0.5~0.8
❖ 聚酰胺 (PA)
聚酰胺俗称尼龙,是不会霉烂的淡黄色至琥 珀色透明或半透明的固体物,现有品种很多, 并有很好的综合性能:耐磨、坚韧、轻量、耐 化学药品、耐热、耐寒、易成型、自润滑、无 毒、易染色。多数聚酰胺有自熄性,但也有可 燃的,燃烧缓慢,且火焰传播速度慢,离火后 慢慢熄灭。
是淡黄色非晶态树脂,不透明,密度在
1.05g/cm3左右。 可编辑课件PPT
10
无定形材料,其品种牌号很多,各品种的机电性能, 及成形特性边各有差异,应按品种确定成形方法及 成形条件。
吸湿性强,含水量应小于0.3%必须充分干燥,要求表 面光泽的塑件应要求长时间预热干燥。
流动性中等,溢边值0.04毫米左右(流动性比聚苯乙 烯,AS差,但比聚碳酸脂,聚氯乙烯好)。
❖ 丙烯腈-丁二烯-苯乙烯树脂 (ABS)
ABS树脂是丙烯腈、丁二烯、苯乙烯三元共聚 物,A代表丙烯腈,B代表丁二烯,S代表苯乙 烯,故ABS能表现三种组分的协同性能:丙烯
腈使聚合物有良好的刚性、硬度、耐油耐腐、
良好的着色性和电镀性;丁二烯使聚合物有良
好的韧性、耐寒性;苯乙烯赋予材料刚性、硬 度、光泽性和良好的加工流动性。ABS外观上
- 1、下载文档前请自行甄别文档内容的完整性,平台不提供额外的编辑、内容补充、找答案等附加服务。
- 2、"仅部分预览"的文档,不可在线预览部分如存在完整性等问题,可反馈申请退款(可完整预览的文档不适用该条件!)。
- 3、如文档侵犯您的权益,请联系客服反馈,我们会尽快为您处理(人工客服工作时间:9:00-18:30)。
注塑工艺培训资料 注塑工艺培训教程 成型参数设定要领与优化 注塑成型四大要素1)塑胶原料2)注塑模具3)注塑机4)成型工艺技术 成型工艺的五种参数: 温度时间压力速度位置切换 注射工艺参数 储料参数;加料量(注射量)、余料量(缓冲垫)、螺杆转速、背压(塑化压力)、倒塑 (松退)。
注射参数:注射压力、注射速度.保压压力和时间、分段注射与位置温度参数:料筒温度、喷嘴温度、模具温度、油液温度。
时间参数:注射时间、保压时间、中间停留时间、储料时间、冷却时间。
一、储料工艺参数1)加料量(注射量) 2)余料量(缓冲垫) 3)螺杆转速 4)背压(塑化压力) 5)倒塑(松退) 加料量的设定 螺杆从注射终止位置后退到加料终止位置的距离称为计量行程或储料行程。
因此,螺杆端前面部分的塑料容积就是螺杆后退行程的计量容积(即注射量),所以计量行程办是注射行程。
余料量(缓冲垫) 在料量设定时,料筒前端熔料被注射的分量在零位前要预留一段位置作缓冲用,称为“缓冲垫”。
此段位置不少于3mm,通常设定10mm。
余料量的调整作用 1)设定缓冲垫可提高注射量的重复精度和稳定塑件成型质量。
2)在保压阶段有一个缓慢推进过程,将剩余的高积存压力继续向模腔及流道传送,使塑件冷却收缩时不断有料补充。
3)可改善塑件密度,使塑件表面光泽度好、颜色均匀、尺寸稳定、内应力小,从而提高塑件的质量。
4)对缓冲垫位置大小的调节.可改普某些工艺上的不足。
5)保护螺杆头如射胶射尽到零位置或预留射终位置过小,在注射惯性或机器控制失准的情况下.容易出现螺杆头卡住料筒头,在预料动作时甚至会拧断螺杆头。
螺杆转速的作用 螺杆转速越高.熔料在螺杆中输出能力和剪切效应越好。
调整螺杆转速(n/min)即是调整塑化效果及加料进行时间。
一般情况下加料时间的长短是螺杆转速与背压所决定:螺杆转速越高,背压压力越小,加料时间越短,反之加料时间越长。
因此螺杆转速是影响塑化能力、塑化质量和储料时间的主要参数。
1. 螺杆转速的控制要领 调整螺杆转速和背压的参数时,要控制加料时间短于冷却时问。
为了达到料筒温度的准确控制,通常最佳的做法是调整螺杆的旋转速度使加料时间在许可范围内尽量长(相比冷却时间略短1~2s),这样可减少因螺杆旋转磨擦而产生的热量,避免了熔料温度过高。
2. 多段储料的作用 于螺杆在储料阶段会向后退,即表示塑料从料口处输送到螺杆端部的有效长度并不样,螺杆作用在塑料上剪切力能量也不一样。
储料行程越长.塑化作用的有效长度变化越长.产生的不稳定作用亦越大。
为了抵消螺杆塑化有效长度的变化和螺杆越位现象,在不同的螺杆后退位置使用逐渐递增背压和逐渐递减螺杆转速,可达到塑化质量稳定和均一的作用。
3. 多段储料的设定准则 储料开始阶段以合适的背压和螺杆转速完成行程的60%~80%,其后将背后提高和速度减半到储料完成,最后将螺杆后退4~5mm后卸压。
4. 背压的作用 背压对熔体温度的影响是非常明显的,因为背压增加了熔体的内压力,加强了剪切效果,形成剪切热.使大分子热能增加.物料的受热时间增加,从而提高了熔体的温度,塑化质量也得到改善。
5. 背压的产生 在熔料过程中,因螺杆的后退,射胶液压缸内的压力油要排回油箱。
若利用液压阀调节液压油的排放量时,射胶液压缸内的压力便会因螺杆后退而上升,背压便是指这时射胶液压缸内的压力.即背压是用来限制螺杆后退速度而增加塑料在熔胶过程中所受的压力,又称为塑化压力。
6. 背压的用途 1)可解决塑件混色不良。
增加背压后塑料要经过较多次的搅拌才会被推送到螺杆前端,因此颜色的混和会比没有加背压时更好。
2)可解决塑件气纹及气泡。
增加背压后,熔化的塑料因压力的上升令密度增加.使塑料含有空气的机会降低,避免了气纹及气泡的产生。
3)可稳定塑件成型质量。
增加背压能改善塑化效果.增加熔料的单位密度,避免了因塑料塑化不良而导致塑件在重量及尺寸上的不稳定。
4)可助快速转换塑料或颜色。
增加背压令附于螺杆上的塑料所受压力上升,塑料在承受一定压力搅拌时.附于螺杆表面上的旧料或颜色比较容易地被带走及射出,达到快速转换塑料的目的。
倒塑(松退)定义 当螺杆计量(预塑)到位后,再后退一段距离,使计量室中熔体的比容增加,内压下降,防止熔体通过喷嘴或间隙从计量室向外流出,这个后退动作称为倒塑.又叫松退或防涎量.后退的距离称倒塑量或倒塑行程。
倒塑的作用1)防喷嘴流涎。
2)在固定加料时,可降低从喷嘴到流道系统的压力.减少内应力并在开模时容易抽出料杆。
3)稳定计量精度。
倒塑设定准则 螺杆后退速度通常选取最快速度的20%~35%为宜。
因为螺杆以较慢的速度向后退.可使螺杆前端的止逆环可以在每一注塑循环回复到同一位置上.减少了螺杆垫料量的变化。
螺杆后退位置设定必须根据螺杆的直径和止逆环的实际移动范围为目标.典型的数值是4~10mm。
如螺杆后退位置过大,则会形成吸气现象.使塑件产生表面性缺陷。
注射工艺参数 1)注射压力 2)注射速度 3)保压压力与时间 4)分段注射注射压力的定义 在注射过程中为了克服烙料流经喷嘴、流道和模腔等各处的流动阻力,注射螺杆将 料筒内的熔融塑料在设定的时间内完全并持续充满温度较低的模腔,就需要有足够的推进力.当推进力达到某个峰值,就称之为注射压力。
影响注射压力的因素 影响所需注射压力的因素有很多,主要有如下三个方面: 1)塑料流动性因素(塑化粘度、注射速度、模具温度)。
2)塑料流动阻力因素(喷嘴形式和射孔尺寸、模具流道系统尺寸、塑件的形状和尺寸)。
3)塑件尺寸精度或其它品质要求。
注射压力的设定准则 在不会造成塑件粘模及飞边的限度内以稍高的压力注射可使模内熔融体在完全冷凝前始终获得充分的压力和质量补充。
任何塑料所需的注射压力是以塑件刚好欠注,再补充一定的注射压力使产品达到质量要求为准则。
注射速度的定义 注射速度是指螺杆在注射动作时移动的速度,通常用cm/s表示。
影响塑料充模流动性的因素 1)原料的流动性(因塑料品级和规格而异)。
2)模腔内料流通道变化大(因塑件结构而异)。
3)充模温差(模具温度与原料塑化温度、模腔各处的温度、型芯与型腔的温度)。
4)充模时差(注射开始到注射结束的时间)。
注射速度与充模流体速度 注射速度是调节充模熔料的流动速率和决定充模时间的必要条件。
若想获得质量满意的塑件,所设置的注射速度必须使熔料在充模过程中得到最佳的连贯性流动要求。
注射速度与残余应力 熔体经喷嘴射出的速度对最终的塑胶产品分子排列及残余应力有很大的影响。
于充模阶段注射速度影响剪切力和剪切速率进而影响产品成型质量。
保压压力的定义 塑件的密度主要决定于封闭浇口时施加压力的大小,而与充模压力无关。
当模腔充满塑料后.还需继续加一定的补充压力,直至浇口完全冷却封闭为止的一段时间,该 注塑工艺培训教程 成型参数设定要领与优化 注塑成型四大要素1)塑胶原料2)注塑模具3)注塑机4)成型工艺技术 成型工艺的五种参数: 温度时间压力速度位置切换 注射工艺参数 储料参数;加料量(注射量)、余料量(缓冲垫)、螺杆转速、背压(塑化压力)、倒塑 (松退)。
注射参数:注射压力、注射速度.保压压力和时间、分段注射与位置温度参数:料筒温度、喷嘴温度、模具温度、油液温度。
时间参数:注射时间、保压时间、中间停留时间、储料时间、冷却时间。
一、储料工艺参数1)加料量(注射量) 2)余料量(缓冲垫) 3)螺杆转速 4)背压(塑化压力) 5)倒塑(松退) 加料量的设定 螺杆从注射终止位置后退到加料终止位置的距离称为计量行程或储料行程。
因此,螺杆端前面部分的塑料容积就是螺杆后退行程的计量容积(即注射量),所以计量行程办是注射行程。
余料量(缓冲垫) 在料量设定时,料筒前端熔料被注射的分量在零位前要预留一段位置作缓冲用,称为“缓冲垫”。
此段位置不少于3mm,通常设定10mm。
余料量的调整作用 1)设定缓冲垫可提高注射量的重复精度和稳定塑件成型质量。
2)在保压阶段有一个缓慢推进过程,将剩余的高积存压力继续向模腔及流道传送,使塑件冷却收缩时不断有料补充。
3)可改善塑件密度,使塑件表面光泽度好、颜色均匀、尺寸稳定、内应力小,从而提高塑件的质量。
4)对缓冲垫位置大小的调节.可改普某些工艺上的不足。
5)保护螺杆头如射胶射尽到零位置或预留射终位置过小,在注射惯性或机器控制失准的情况下.容易出现螺杆头卡住料筒头,在预料动作时甚至会拧断螺杆头。
螺杆转速的作用 螺杆转速越高.熔料在螺杆中输出能力和剪切效应越好。
调整螺杆转速(n/min)即是调整塑化效果及加料进行时间。
一般情况下加料时间的长短是螺杆转速与背压所决定:螺杆转速越高,背压压力越小,加料时间越短,反之加料时间越长。
因此螺杆转速是影响塑化能力、塑化质量和储料时间的主要参数。
1. 螺杆转速的控制要领 调整螺杆转速和背压的参数时,要控制加料时间短于冷却时问。
为了达到料筒温度的准确控制,通常最佳的做法是调整螺杆的旋转速度使加料时间在许可范围内尽量长(相比冷却时间略短1~2s),这样可减少因螺杆旋转磨擦而产生的热量,避免了熔料温度过高。
2. 多段储料的作用 于螺杆在储料阶段会向后退,即表示塑料从料口处输送到螺杆端部的有效长度并不样,螺杆作用在塑料上剪切力能量也不一样。
储料行程越长.塑化作用的有效长度变化越长.产生的不稳定作用亦越大。
为了抵消螺杆塑化有效长度的变化和螺杆越位现象,在不同的螺杆后退位置使用逐渐递增背压和逐渐递减螺杆转速,可达到塑化质量稳定和均一的作用。
3. 多段储料的设定准则 储料开始阶段以合适的背压和螺杆转速完成行程的60%~80%,其后将背后提高和速度减半到储料完成,最后将螺杆后退4~5mm后卸压。
4. 背压的作用 背压对熔体温度的影响是非常明显的,因为背压增加了熔体的内压力,加强了剪切效果,形成剪切热.使大分子热能增加.物料的受热时间增加,从而提高了熔体的温度,塑化质量也得到改善。
5. 背压的产生 在熔料过程中,因螺杆的后退,射胶液压缸内的压力油要排回油箱。
若利用液压阀调节液压油的排放量时,射胶液压缸内的压力便会因螺杆后退而上升,背压便是指这时射胶液压缸内的压力.即背压是用来限制螺杆后退速度而增加塑料在熔胶过程中所受的压力,又称为塑化压力。
6. 背压的用途 1)可解决塑件混色不良。
增加背压后塑料要经过较多次的搅拌才会被推送到螺杆前端,因此颜色的混和会比没有加背压时更好。
2)可解决塑件气纹及气泡。
增加背压后,熔化的塑料因压力的上升令密度增加.使塑料含有空气的机会降低,避免了气纹及气泡的产生。
3)可稳定塑件成型质量。
增加背压能改善塑化效果.增加熔料的单位密度,避免了因塑料塑化不良而导致塑件在重量及尺寸上的不稳定。