梯形螺纹蜗杆6
数控车床上加工梯形螺纹

数控车床上加工梯形螺纹内容摘要:在数控车床上加工梯形螺纹是一个全新的课题,本文通过对梯形螺纹加工的工艺分析和加工方法的研讨,探索出一套可以在数控车床上加工出合格梯形螺纹的方法在普通车床的生产实习过程中,加工梯形螺纹课题是最基本的实习课题,但在数控车床实习过程中,常常由于加工工艺方面的原因,却很少进行梯形螺纹的加工练习,甚至有人提出在数控车床上不能加工梯形螺纹,显然这种提法是错误的.其实,只要工艺分析合理,使用的加工指令得当,完全可以在数控车床上加工出合格的梯形螺纹。
一、梯形螺纹加工的工艺分析1。
梯形螺纹的尺寸计算梯形螺纹的代号梯形螺纹的代号用字母“Tr”及公称直径×螺距表示,单位均为mm。
左旋螺纹需在尺寸规格之后加注“LH”,右旋则不用标注。
例如Tr36×6,Tr44×8LH等.国标规定,公制梯形螺纹的牙型角为30°。
梯形螺纹的牙型如图(1),各基本尺寸计算公式如表1—1。
图1 梯形螺纹的牙型2。
梯形螺纹在数控车床上的加工方法直进法螺纹车刀X向间歇进给至牙深处(如图2a)。
采用此种方法加工梯形螺纹时,螺纹车刀的三面都参加切削,导致加工排屑困难,切削力和切削热增加,刀尖磨损严重。
当进刀量过大时,还可能产生“扎刀”和“爆刀”现象。
这种方法数控车床可采用指令G92来实现,但是很显然,这种方法是不可取的。
斜进法螺纹车刀沿牙型角方向斜向间歇进给至牙深处(如图2b)。
采用此种方法加工梯形螺纹时,螺纹车刀始终只有一个侧刃参加切削,从而使排屑比较顺利,刀尖的受力和受热情况有所改善,在车削中不易引起“扎刀"现象。
该方法在数控车床上可采用G76指令来实现。
交错切削法螺纹车刀沿牙型角方向交错间隙进给至牙深(如图2c)。
该方法类同于斜进法,也可在数控车床上采用G76指令来实现.切槽刀粗切槽法该方法先用切槽刀粗切出螺纹槽((如图2d),再用梯形螺纹车刀加工螺纹两侧面。
这种方法的编程与加工在数控车床上较难实现。
螺纹(丝扣)连接介绍
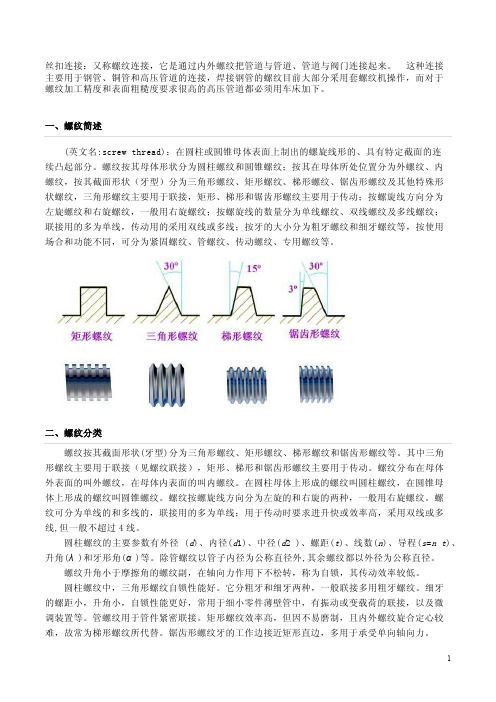
丝扣连接:又称螺纹连接,它是通过内外螺纹把管道与管道、管道与阀门连接起来。
这种连接主要用于钢管、铜管和高压管道的连接,焊接钢管的螺纹目前大部分采用套螺纹机操作,而对于螺纹加工精度和表面粗糙度要求很高的高压管道都必须用车床加下。
一、螺纹简述(英文名:screw thread):在圆柱或圆锥母体表面上制出的螺旋线形的、具有特定截面的连续凸起部分。
螺纹按其母体形状分为圆柱螺纹和圆锥螺纹;按其在母体所处位置分为外螺纹、内螺纹,按其截面形状(牙型)分为三角形螺纹、矩形螺纹、梯形螺纹、锯齿形螺纹及其他特殊形状螺纹,三角形螺纹主要用于联接,矩形、梯形和锯齿形螺纹主要用于传动;按螺旋线方向分为左旋螺纹和右旋螺纹,一般用右旋螺纹;按螺旋线的数量分为单线螺纹、双线螺纹及多线螺纹;联接用的多为单线,传动用的采用双线或多线;按牙的大小分为粗牙螺纹和细牙螺纹等,按使用场合和功能不同,可分为紧固螺纹、管螺纹、传动螺纹、专用螺纹等。
二、螺纹分类螺纹按其截面形状(牙型)分为三角形螺纹、矩形螺纹、梯形螺纹和锯齿形螺纹等。
其中三角形螺纹主要用于联接(见螺纹联接),矩形、梯形和锯齿形螺纹主要用于传动。
螺纹分布在母体外表面的叫外螺纹,在母体内表面的叫内螺纹。
在圆柱母体上形成的螺纹叫圆柱螺纹,在圆锥母体上形成的螺纹叫圆锥螺纹。
螺纹按螺旋线方向分为左旋的和右旋的两种,一般用右旋螺纹。
螺纹可分为单线的和多线的,联接用的多为单线;用于传动时要求进升快或效率高,采用双线或多线,但一般不超过4线。
圆柱螺纹的主要参数有外径 (d)、内径(d1)、中径(d2 )、螺距(t)、线数(n)、导程(s=n t)、升角(λ)和牙形角(α)等。
除管螺纹以管子内径为公称直径外,其余螺纹都以外径为公称直径。
螺纹升角小于摩擦角的螺纹副,在轴向力作用下不松转,称为自锁,其传动效率较低。
圆柱螺纹中,三角形螺纹自锁性能好。
它分粗牙和细牙两种,一般联接多用粗牙螺纹。
细牙的螺距小,升角小,自锁性能更好,常用于细小零件薄壁管中,有振动或变载荷的联接,以及微调装置等。
数控车床中梯形螺纹(蜗杆)加工方法

数控车床中梯形螺纹(蜗杆)加工方法作者:李俊来源:《文理导航》2011年第20期通常车削梯形螺纹时,采用高速钢材料刀具进行低速车削,一般采用图1四种进刀方法:直进法、左右切削法、车直槽法和车阶梯槽法。
直进法适用于车削螺距较小(P4mm)的梯形螺纹常采用左右切削法、车直槽法和车阶梯槽法。
在这四种切削方法中,除直进法外,其他三种车削方法都能不同程度地减轻或避免三刃同时切削,使排屑较顺畅,刀尖受力、受热情况有所改善,从而不易出现振动和扎刀现象,还可提高切削用量,改善螺纹表面质量。
所以,左右切削法、车直槽法和车阶梯槽法获得了广泛的应用。
在数控车床上车削三角螺纹时一般可选用标准机夹刀具,利用螺纹循环指令完成加工。
但由于梯形螺纹较之三角螺纹,其螺距和牙型都大,而且精度高,牙型两侧面表面粗糙度值较小,致使梯形螺纹车削时,吃刀深,走刀快,切削余量大,切削抗力大,加之有些数控车床刚性较差,如果在切削过程中参数选择不合理就容易产生“扎刀”和“爆刀”现象。
采用斜进法对标准螺纹来说,由于有固定循环指令,较为方便,但对异型螺纹加工就不太方便。
下面介绍利用宏程序采用“分层法”切削加工梯形螺纹,该方法切削状况好,对刀具要求不高,尺寸由程序中相应数值保证,当牙顶宽和螺纹底径达到尺寸要求时,螺纹中径等其他各项尺寸也相应达到尺寸要求,尺寸精度易于控制,螺纹表面质量好,甚至蜗杆和其它异型螺纹的加工也可套用该方法的编程思路。
这里讲的“分层法”车削梯形螺纹实际上是直进法和左右切削法的综合应用。
在车削较大螺距的梯形螺纹时,“分层法”通常不是一次性就把梯形槽切出来,而是把牙槽分成若干层,每层深度根据实际机床情况可转化成若干个较浅的梯形槽来进行切削。
每一层的切削都采用左右交替车削的方法,背吃刀量很小,刀具只需沿左右牙型线切削,梯形螺纹车刀始终只有一个侧刃参加切削,从而使排屑比较顺利,刀尖的受力和受热情况有所改善,因此能加工出较高质量的梯形螺纹。
螺旋传动与蜗杆传动的异同

螺旋传动与蜗杆传动的异同螺旋传动和蜗杆传动是两种基本的机械传动方式。
螺旋传动主要是内螺纹和外螺纹的配合,而蜗杆传动主要是蜗杆和涡轮的啮合。
这两种机械传动方式具有许多共同点,下文对这两种机械传动方式进行分析,归纳了螺旋传动和蜗杆传动的异同。
一、螺旋传动与蜗杆传动的相同点(一)旋向的判断方法相同螺旋传动和蜗杆传动具有相同的旋向判断方法。
所谓旋向,是指螺纹或者蜗杆,抑或是涡轮螺旋线,它们在圆柱面上的绕向。
无论是内螺纹还是外螺纹,都具有左旋和右旋这两种绕向。
蜗杆和涡轮的绕向也不例外,也是左旋和右旋两种绕向。
在机械传动中,较为常用的是右旋螺纹,还有就是右旋蜗杆和右旋涡轮。
在螺纹中,通常是梯形螺纹用于传动。
蜗杆从本质上来看,也是一种特殊的梯形螺纹,只是它的螺距比较大。
因此,螺旋传动和蜗杆传动具有相同的旋向判断方法。
具体方法是:将右手平伸出去,使手心向上,四指的方向和螺纹、蜗杆的方向保持一致,右手的大拇指的指向如果和螺纹斜向一致,那么该螺纹、蜗杆为右旋螺纹、右旋蜗杆。
如果右手的大拇指的指向如果和螺纹斜向不一致,则该螺纹、蜗杆为左旋螺纹、左旋蜗杆。
(二)螺纹移动方向和涡轮转向的判断方法相同常见的螺旋传动应用形式:(1)螺母是固定的,主要是螺杆旋转,并进行轴向的移动;(2)螺杆是固定的,主要是螺母旋转,并进行轴向的移动;(3)螺杆旋转,而螺母进行轴向的移动。
对于螺杆旋转而螺母轴向移动这种形式中,都是利用左右手螺旋定则,来对螺母移动方向和蜗杆传动中涡轮转向进行判断。
左右手螺旋定则的含义是:左旋用左手半握拳,右旋用右手半握拳,将四指的方向和蜗杆或者螺杆的转向保持一致,通过大拇指指向的反方向来判断涡轮转向或者螺母移动的方向,两者的方向与大拇指的指向相反。
(三)传动条件相同蜗杆涡轮轮齿的大小,以模数来表示,模数的单位是毫米。
模数越大,说明蜗杆涡轮的轮齿也越大,相应的,其承载力也越强。
螺纹牙型的大小用螺距来表示,螺距的单位也是毫米,螺距的大小和螺纹牙型的大小成正比,同样的,螺距越大,其承载力也越强。
蜗轮蜗杆设计参数选择
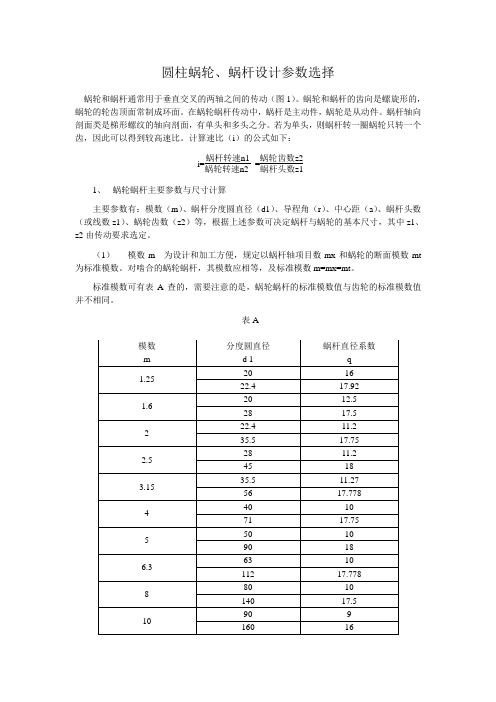
圆柱蜗轮、蜗杆设计参数选择蜗轮和蜗杆通常用于垂直交叉的两轴之间的传动(图1)。
蜗轮和蜗杆的齿向是螺旋形的,蜗轮的轮齿顶面常制成环面。
在蜗轮蜗杆传动中,蜗杆是主动件,蜗轮是从动件。
蜗杆轴向剖面类是梯形螺纹的轴向剖面,有单头和多头之分。
若为单头,则蜗杆转一圈蜗轮只转一个齿,因此可以得到较高速比。
计算速比(i)的公式如下:i=蜗杆转速n1蜗轮转速n2=蜗轮齿数z2蜗杆头数z11、蜗轮蜗杆主要参数与尺寸计算主要参数有:模数(m)、蜗杆分度圆直径(d1)、导程角(r)、中心距(a)、蜗杆头数(或线数z1)、蜗轮齿数(z2)等,根据上述参数可决定蜗杆与蜗轮的基本尺寸,其中z1、z2由传动要求选定。
(1)模数m 为设计和加工方便,规定以蜗杆轴项目数mx和蜗轮的断面模数mt 为标准模数。
对啮合的蜗轮蜗杆,其模数应相等,及标准模数m=mx=mt。
标准模数可有表A查的,需要注意的是,蜗轮蜗杆的标准模数值与齿轮的标准模数值并不相同。
表A图1图2(2)蜗杆分度圆直径d1 再制造蜗轮时,最理想的是用尺寸、形状与蜗杆完全相同的蜗轮滚刀来进行切削加工。
但由于同一模数蜗杆,其直径可以各不相同,这就要求每一种模数对应有相当数量直径不同的滚刀,才能满足蜗轮加工需求。
为了减少蜗轮滚刀数目,在规定标准模数的同时,对蜗杆分度圆直径亦实行了标准化,且与m 有一定的匹配。
蜗杆分度圆直径d1与轴向模数mx之比为一标准值,称蜗杆的直径系数。
即q=蜗杆分度圆直径模数=d1m d1=mq有关标准模数m 与标准分度圆直径d1的搭配值及对应的蜗杆直径系数参照表A (3) 蜗杆导程角r 当蜗杆的q 和z1选定后,在蜗杆圆柱上的导程角即被确定。
为导程角、导程和分度圆直径的关系。
tan r=导程分度圆周长 = 蜗杆头数x 轴向齿距分度圆周长 =z1px d1π =z1πm πm q =z1q相互啮合的蜗轮蜗杆,其导程角的大小与方向应相同。
(4) 中心距a 蜗轮与蜗杆两轴中心距a 与模数m 、蜗杆直径系数q 以及蜗轮齿数z2间的关系式如下:a=d1+d22 =m q(q+z2)蜗杆各部尺寸如表B蜗轮各部尺寸如表C2、 蜗轮蜗杆的画法(1) 蜗杆的规定画法 参照图1图2 (2)蜗轮的规定画法 参照图1图2 (3)蜗轮蜗杆啮合画法 参照图1图2.。
6-9 蜗杆传动
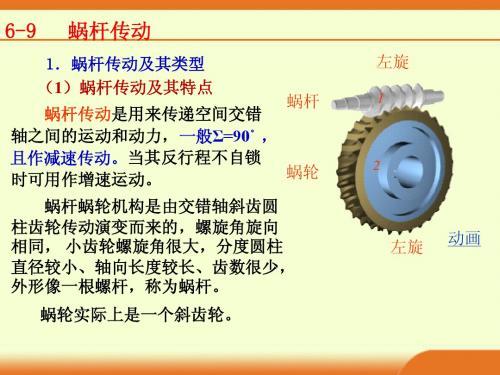
蜗杆
1
2
左旋
动画
蜗杆传动的特点和用途 1)传动比大,结构紧凑。 i=10—40,最大可达80。 若只传递运动,传动比可达1000。 2)传动平稳、振动、冲击噪声小。 3) 可制成具有自锁性的蜗杆。 4) 效率较低。η =0.7—0.8。 5) 轮齿间的相对滑动速度大,传动效 率低,需用减摩耐摩的材料制造蜗轮, 成本高。
整体式蜗轮
齿圈式蜗轮
镶铸式蜗轮
螺栓联接式蜗轮
观看涡轮照片
五 蜗杆传动的效率
1 蜗杆传动效率
h h1 h 2 h 3
h1─计及啮合摩擦损耗的效率; h2─计及轴承摩擦损耗的效率; h3─计及溅油损耗的效率; h1是对总效率影响最大的因素,可由下式确定: tan 式中: -蜗杆的导程角; h1 tan( v ) -当量摩擦角。
平面定轴轮系从动轮的转向,也可以采用画箭头的方法确定。 箭头方向表示齿轮(或构件)最前点的线速度方向。
3)空间定轴轮系传动速比的计算
传动速比的大小仍采用 推广式计算,确定从动轮的 转向,只能采用画箭头的方 法。圆锥齿轮传动,表示齿 轮副转向的箭头同时指向或 同时背离相互啮合处。 蜗杆传动,从动蜗轮转向 判定方法用蜗杆“左、右手 法则” 。
角标a和b分别表示输入和输出 轮系的速比计算,包括计算其速比的大小和确定输出轴 的转动方向两个内容。 最简单的定轴轮系是由一对齿轮所组成的。其传动速比为 i=n1/n2 = ±z2/ z1
一对齿轮的传动比大小为其齿数的反比。若考虑转向关 系,外啮合时,两轮转向相反,传动比取“-”号;内啮合时, 两轮转向相同,传动比取“+”号。
方向判断如图所示
例:如图所示的轮系,已知 z1=24, z2=46, z2’=23, z3=48, z4=35, z4’=
机械设计课后题答案

3-1答:主要类型有:普通螺纹、管螺纹、矩形螺纹、梯形螺纹和锯齿形螺纹五种。
特点及应用:普通螺纹是米制三角螺纹,牙型角 a=60,因牙型角较大,故当量摩擦系数也较大,自锁性能好,主要用于联接。
管螺纹是英制三角螺纹,牙型角 a=55度。
它有圆柱管螺纹和圆锥管螺纹之分,常用圆柱管螺纹。
这种螺纹联接常用于高温、高压及紧密性要求较高的管与管的联接中。
矩形螺纹牙型为正方形,牙型角 a=0度,因牙型角小,当量摩擦系数小,传动效率高,故常用于传动。
梯形螺纹牙型呈梯形,牙型角 a=30度。
因牙型角较小,所以传动效率较高,对中性较好,故为应用较多的传动螺纹。
锯齿形螺纹牙型呈锯齿形,工作面牙侧角。
传动效率高,牙根强度高。
因只有一个工作面,故多用于承受单方向轴向力的场合。
3-2答:螺栓有普通螺栓和铰制孔螺栓两种。
普通螺栓常用于被联接件比较薄,能够放置螺母及需要经常拆卸的场合。
铰制孔螺栓在承受横向载荷或(和)转矩以及需精确固定被联接件的相对位置时常采用铰制孔螺栓。
双头螺柱被联接件之一太厚不宜制成通孔,无法放置螺钉头,材料较软且需经常拆装时宜采用双头螺柱。
螺钉被联接件之一太厚,无法放置螺母,不需经常拆装的场合。
3-3 答:螺纹联接在冲击、振动、变载荷或高温环境下,将使螺旋副的摩擦力减小或瞬间消失,经多次重复后,最终导致联接松脱。
因此,设计时应采取有效的防松措施。
防松方法有摩擦防松、机械防松、铆冲防松等。
3-4 答:为提高联接刚性、紧密性和防松能力以及提高螺栓在变载荷下的疲劳强度,因此大多数螺纹联接都要拧紧。
拧紧力矩要克服螺纹副力矩和螺母底面的摩擦阻力矩。
3-5 答:提高螺栓联接强度的措施有:1 .降低影响螺栓疲劳强度的应力幅;2 .改善螺纹牙上载荷分布不均匀的现象;3 .减小应力集中的影响;4 .避免附加弯曲应力;5 .采用合理的制造工艺方法。
3-6 由上图可知,在螺母下加弹性元件将使螺栓刚度由C b1 减小到C b2 ,可使螺栓承载截面的应力幅值减小,所以螺栓的疲劳强度提高。
梯形螺纹的测量

梯形螺纹的测量
图3 量针直径的选择 a)最大量针直径 b)最佳量针直径 c)最小量针直径
梯形螺纹的测量
三针测量实例
用三针测量Tr36X6-7e梯形螺纹中径, 求千分尺读数M值。 解:根据表中的计算式: 量针直径:dD=0.518P=0.518X6=3.1mm。 螺纹中径:d2=d-0.5P=36-0.5x6=33mm。 查表2和表3得中径尺寸充许偏差为:
P(mm)
梯形螺纹的测量
表3 梯形外螺纹中径公差Td2
公称直径d(mm) 螺距 P(mm) > < 5.6 11.2 1.5 2 3 2 3 4 公 差 等 级 6 132 150 170 160 180 212 7 170 190 212 200 224 265 8 212 236 265 259 280 335 9 265 300 335 315 355 425
梯形螺纹的测量
图2
三针测量法
梯形螺纹的测量
量针的选择 • 三针测量的量针直径(dD)不能太大, d1为蜗杆分度圆直径 (mm),Mx为轴向模数。否则测量针的横截面与螺纹牙侧不相切 (见图3-a),无法量得中径的实际尺寸。也不能太小,不然测量针陷 入牙槽中,其顶点低于螺纹牙顶而无法测量(见图3-c)。量针直径 最大值、最佳值和最小值可在表中查出。选用量针时,应尽量接近 最佳值,以便获得较高的测量精度。
• 工作量规分螺纹塞规和螺纹环规两种,每种又各分有通规与止规之 分。综合测量外螺纹方法如下:
梯形螺纹的测量
图1
用环规检测外螺纹
梯形螺纹的测量
检验外螺纹则需用通端和止端螺纹塞规,如图1,其中通端螺纹环规用 以控制外螺纹的中径和大径的实际尺寸分别不大于最大实体牙型的中径 和大径,即控制d2≤d2max和d1≤d2min;止端螺纹塞规用以控制内螺纹 的实际尺寸中径不小于最小实体螺纹牙型中径,即控制d2a≥d2min。
机械设计基础习题含答案讲解

机械设计基础课程》习题第 1 章机械设计基础概论1- 1 试举例说明机器、机构和机械有何不同?1- 2 试举例说明何谓零件、部件及标准件?1- 3 机械设计过程通常分为几个阶段?各阶段的主要内容是什么?1- 4 常见的零件失效形式有哪些?1- 5 什么是疲劳点蚀?影响疲劳强度的主要因素有哪些?1- 6 什么是磨损?分为哪些类型?1-7 什么是零件的工作能力?零件的计算准则是如何得出的?1-8 选择零件材料时,应考虑那些原则?1-9 指出下列材料牌号的含义及主要用途: Q275 、 40Mn 、40Cr 、 45 、ZG310 - 570 、 QT600 -3。
第 2 章现代设计方法简介2- 1 简述三维CAD 系统的特点。
2- 2 试写出优化设计数学模型的一般表达式并说明其含义。
2- 3 简述求解优化问题的数值迭代法的基本思想。
2- 4 优化设计的一般过程是什么?2- 5 机械设计中常用的优化方法有哪些?2- 6 常规设计方法与可靠性设计方法有何不同?2-7 常用的可靠性尺度有那些?2-8 简述有限元法的基本原理。
2-9 机械创新设计的特点是什么?2-10 简述机械创新设计与常规设计的关系。
第 3 章平面机构的组成和运动简图3- 1 举实例说明零件与构件之间的区别和联系。
3- 2 平面机构具有确定运动的条件是什么?3- 3 运动副分为哪几类?它在机构中起何作用?3- 4 计算自由度时需注意那些事项?3- 5 机构运动简图有何用途?怎样绘制机构运动简图?3- 6 绘制图示提升式水泵机构的运动简图,并计算机构的自由度。
3-7 试绘制图示缝纫机引线机构的运动简图,并计算机构的自由度。
3-8 试绘制图示冲床刀架机构的运动简图,并计算机构的自由度。
3-9 试判断图a、b、c 所示各构件系统是否为机构。
若是,判定它们的运动是否确定(图中标有箭头的构件为原动件)3-10 计算图 a、b、c、d、e、f 所示各机构的自由度,如有复合铰链、局部自由度、或虚约束请指出。
车工技术教程-车削梯形螺纹

车削梯形螺纹学习目标1.了解梯形螺纹车刀的形状,掌握梯形螺纹车刀的刃磨和检测方法。
2.掌握外梯形螺纹的尺寸计算、车削和检测方法。
梯形螺纹相关知识一、梯形螺纹牙型及相关参数计算牙型如图图图梯形螺纹计算公式如表表梯形螺纹各参数及计算公式名称代号计算公式牙型角αα=30°螺距P 由螺纹标准确定牙顶间隙a cP(mm) 1.5~5 6~12 14~44 ac(mm)0.25 0.5 1外螺纹大径 d 公称直径中径d2d2=d-0.5P 小径d3d3=d-2h3 牙高h3h3=0.5P+ ac内螺纹大径D4D4=d+2ac中径D2D2= d2小径D1D1=d-P牙高H4H4= h3牙顶宽f,f= f’=0.366P牙槽底宽W,W’W=W’=0.336P-0.536a c轴向齿厚Sx Sx=0.5P法向尺厚Sn Sn==0.5Pcos二、梯形螺纹基本标注1.外螺纹2.内螺纹三、螺纹车刀梯形螺纹车刀分为硬质合金和高速钢两种。
常用的是高速钢材料的车刀。
1.高速钢梯形外螺纹车刀(1)粗车刀刀尖宽度要小于齿根槽宽,径向前角为10°~15°,两侧后角进刀方向为(3°~5°)+φ,背进刀方向为(3°~5°)-φ。
如图图高速钢梯形外螺纹粗车刀(2)精车刀精车径向前角为0°,两侧后角进刀方向为(5°~8°)+φ,背进刀方向为(5°~8°)-φ进刀,可适当磨出卷些槽,增大前角。
如图图高速钢梯形外螺纹精车刀2.硬质合金梯形螺纹车刀适合于车削一般精度的梯形螺纹,效率提高。
几何角度如图图硬质合金梯形外螺纹车刀3.梯形内螺纹车刀几何角度如图图梯形内螺纹车刀四、梯形螺纹车刀的刃磨方法和检测(1)刃磨步骤:①粗磨两侧后面,刃磨出两侧后角、刀尖角。
②精磨两侧后面,控制好刀头宽度,使其小于牙槽底宽0.5mm左右。
③粗磨前刀面,刃磨出径向前角。
蜗杆参数计算公式,很多人都在找

蜗杆参数计算公式,很多⼈都在找蜗轮和蜗杆通常⽤于垂直交叉的两轴之间的传动。
蜗轮和蜗杆的齿向是螺旋形的,蜗轮的轮齿顶⾯常制成环⾯。
在蜗轮蜗杆传动中,蜗杆是主动件,蜗轮是从动件。
蜗杆轴向剖⾯类是梯形螺纹的轴向剖⾯,有单头和多头之分。
若为单头,则蜗杆转⼀圈蜗轮只转⼀个齿,因此可以得到较⾼速⽐。
今天介绍⼀下蜗杆参数计算公式。
加⼯导程=6.3×3.1416=19.79mm 模数*派蜗轮、蜗杆的计算公式:1、传动⽐=蜗轮齿数÷蜗杆头数2、中⼼距=(蜗轮节径+蜗杆节径)÷23、蜗轮吼径=(齿数+2)×模数4、蜗轮节径=模数×齿数5、蜗杆节径=蜗杆外径-2×模数6、蜗杆导程=π×模数×头数7、螺旋⾓(导程⾓)tgB=(模数×头数)÷蜗杆节径蜗杆导程=π×模数×头数模数=分度圆直径/齿数头数是说螺杆上螺旋线的条数;模数是指螺杆上螺旋线的⼤⼩,也就是模数越⼤螺杆上的螺旋线就越“柱装”(东北话,就是⽐较⼤,⽐较结实)直径系数是指螺杆的粗细。
模数:齿轮的分度圆是设计、计算齿轮各部分尺⼨的基准,⽽齿轮分度圆的周长=πd=z p,于是得分度圆的直径d=z p/π由于在上式中π为⼀⽆理数,不便于作为基准的分度圆的定位。
为了便于计算,制造和检验,现将⽐值p/π⼈为地规定为⼀些简单的数值,并把这个⽐值叫做模数(module),以m表⽰。
模数m是决定齿轮尺⼨的⼀个基本参数。
齿数相同的齿轮模数⼤,则其尺⼨也⼤。
为了便于制造,检验和互换使⽤,齿轮的模数值已经标准化了。
建筑模数建筑模数指建筑设计中选定的标准尺⼨单位。
它是建筑设计、建筑施⼯、建筑材料与制品、建筑设备、建筑组合件等各部门进⾏尺度协调的基础。
就象随便来个尺⼨,建筑构件就⽆法标准化了,难统⼀。
基本模数的数值规定为100mm,以M表⽰,即1M= 100mm。
导出模数分为扩⼤模数和分模数,扩⼤模数的基数为3M,6M,12M,15M,30M,60M共6个;分模数的基数为1/10M,1/5M,1/2M共3个。
常用标准螺纹螺距对照表
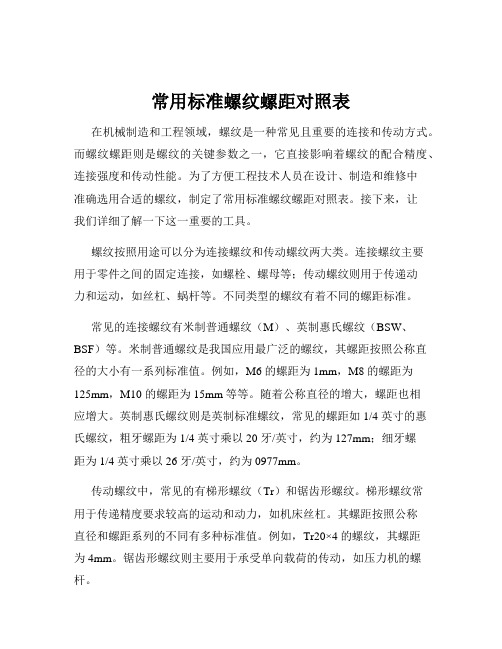
常用标准螺纹螺距对照表在机械制造和工程领域,螺纹是一种常见且重要的连接和传动方式。
而螺纹螺距则是螺纹的关键参数之一,它直接影响着螺纹的配合精度、连接强度和传动性能。
为了方便工程技术人员在设计、制造和维修中准确选用合适的螺纹,制定了常用标准螺纹螺距对照表。
接下来,让我们详细了解一下这一重要的工具。
螺纹按照用途可以分为连接螺纹和传动螺纹两大类。
连接螺纹主要用于零件之间的固定连接,如螺栓、螺母等;传动螺纹则用于传递动力和运动,如丝杠、蜗杆等。
不同类型的螺纹有着不同的螺距标准。
常见的连接螺纹有米制普通螺纹(M)、英制惠氏螺纹(BSW、BSF)等。
米制普通螺纹是我国应用最广泛的螺纹,其螺距按照公称直径的大小有一系列标准值。
例如,M6 的螺距为 1mm,M8 的螺距为125mm,M10 的螺距为 15mm 等等。
随着公称直径的增大,螺距也相应增大。
英制惠氏螺纹则是英制标准螺纹,常见的螺距如 1/4 英寸的惠氏螺纹,粗牙螺距为 1/4 英寸乘以 20 牙/英寸,约为 127mm;细牙螺距为 1/4 英寸乘以 26 牙/英寸,约为 0977mm。
传动螺纹中,常见的有梯形螺纹(Tr)和锯齿形螺纹。
梯形螺纹常用于传递精度要求较高的运动和动力,如机床丝杠。
其螺距按照公称直径和螺距系列的不同有多种标准值。
例如,Tr20×4 的螺纹,其螺距为 4mm。
锯齿形螺纹则主要用于承受单向载荷的传动,如压力机的螺杆。
在实际应用中,选择合适的螺纹螺距需要综合考虑多个因素。
首先是载荷的大小和性质。
如果载荷较大,通常需要选择较大螺距的螺纹以提高连接强度和传动能力;反之,如果载荷较小,可以选择较小螺距的螺纹以满足精度要求。
其次是装配和拆卸的便利性。
螺距过大可能导致装配困难,过小则可能使拆卸不便。
此外,还需要考虑成本和制造工艺的可行性。
为了更直观地了解常用标准螺纹螺距,以下为您提供一份较为常见的螺纹螺距对照表:|螺纹类型|公称直径(mm)|螺距(mm)||||||米制普通螺纹(M)|6|1||米制普通螺纹(M)|8|125||米制普通螺纹(M)|10|15||米制普通螺纹(M)|12|175||米制普通螺纹(M)|14|2||米制普通螺纹(M)|16|2||米制普通螺纹(M)|18|25||米制普通螺纹(M)|20|25||米制普通螺纹(M)|22|25||米制普通螺纹(M)|24|3||米制普通螺纹(M)|27|3||米制普通螺纹(M)|30|35||米制普通螺纹(M)|33|35||米制普通螺纹(M)|36|4||米制普通螺纹(M)|39|4||米制普通螺纹(M)|42|45||米制普通螺纹(M)|45|45||米制普通螺纹(M)|48|5||米制普通螺纹(M)|52|5||米制普通螺纹(M)|56|55||米制普通螺纹(M)|60|55||米制普通螺纹(M)|64|6||米制普通螺纹(M)|68|6||梯形螺纹(Tr)|20|4||梯形螺纹(Tr)|24|5||梯形螺纹(Tr)|28|5||梯形螺纹(Tr)|32|6||梯形螺纹(Tr)|36|6||梯形螺纹(Tr)|40|7||梯形螺纹(Tr)|44|8||梯形螺纹(Tr)|50|8|需要注意的是,这只是一份简略的对照表,实际的螺纹标准和螺距规格更加丰富和复杂。
蜗轮蜗杆(常见普通)地规格与尺寸

常见普通蜗轮蜗杆的规格及尺寸例:蜗杆传动,已知模数m=4. 蜗杆头数 z1=1 ,蜗轮齿数 z2=50, 特性系数 q=10 。
求传动中心距a=?变位系数 0 时:中心距a= (蜗杆分度圆 + 蜗轮分度圆) /2=( 特性系数q* 模数m+ 蜗轮齿数Z2* 模数m)/2=(10*4+50*4)/2=120特性系数 :蜗杆的分度圆直径与模数的比值称为蜗杆特性系数。
加工蜗轮时,因为是直径和形状与蜗杆相同的滚刀来切制,由上式可看出,在同一模数下由于Z1 和λ0 的变化,将有很多不同的蜗杆直径,也就是说需要配备很多加工蜗轮的滚刀。
为了减少滚刀的数目,便于刀具标准化,不但要规定标准模数,同时还必须规定对应于一定模数的Z1/tg λ0值,这个值用 q 表示,称之为蜗杆特性系数。
圆柱蜗轮、蜗杆设计参数选择蜗轮和蜗杆通常用于垂直交叉的两轴之间的传动(图1)。
蜗轮和蜗杆的齿向是螺旋形的,蜗轮的轮齿顶面常制成环面。
在蜗轮蜗杆传动中,蜗杆是主动件,蜗轮是从动件。
蜗杆轴向剖面类是梯形螺纹的轴向剖面,有单头和多头之分。
若为单头,则蜗杆转一圈蜗轮只转一个齿,因此可以得到较高速比。
计算速比(i)的公式如下:蜗杆转速i=蜗轮转速n1n2蜗轮齿数=蜗杆头数z2z11、蜗轮蜗杆主要参数与尺寸计算主要参数有:模数( m)、蜗杆分度圆直径( d1)、导程角(蜗轮齿数( z2)等,根据上述参数可决定蜗杆与蜗轮的基本尺寸,其中r )、中心距( a)、蜗杆头数(或线数z1、 z2 由传动要求选定。
z1)、( 1)模数m为设计和加工方便,规定以蜗杆轴项目数mx 和蜗轮的断面模数mt为标准模数。
对啮合的蜗轮蜗杆,其模数应相等,及标准模数m=mx=mt 。
标准模数可有表 A 查的,需要注意的是,蜗轮蜗杆的标准模数值与齿轮的标准模数值并不相同。
表 A模数分度圆直径蜗杆直径系数m d 1q1.252016 22.417.921.62012.5 2817.5222.411.2 35.517.752.52811.2 45183.1535.511.27 5617.77844010 7117.7555010 90186.36310 11217.77888010 14017.510909 16016图 1图 2( 2) 蜗杆分度圆直径 d1 再制造蜗轮时,最理想的是用尺寸、形状与蜗杆完全相同的蜗轮滚刀来进行切削加工。
梯形螺纹加工常用的加工方法

梯形螺纹加工常用的加工方法摘要:梯形螺纹的车削在生产实践中非常重要。
本文就梯形螺纹车削过程中车刀的刃磨要求、梯形螺纹的加工方面保证粗加工余量的快速去除和精加工余量的有效预留,从而达到高效、稳定地车削梯形螺纹,一直采用传统的高速钢车刀左右车削法或斜进法加工,不但效率低、刀具易磨损,还经常由于尺寸控制不准,使精加工余量不够出现废品。
本文介绍几种实践中摸索出来的简单实用、效率高的梯形螺纹车削方法,可以提高生产效率,缩短加工时间,保证粗加工余量的快速去除和精加工余量的有效预留,从而达到高效、稳定地车削梯形螺纹。
关键词:梯形螺纹强力切削螺旋升角一、梯形螺纹的相关知识梯形螺纹是利用很广泛的传动螺纹,分为米制和英制两种。
英制梯形螺纹的牙型角为29°,我国常见的是米制梯形螺纹,其牙型角为30°。
1.梯形螺纹标记梯形螺纹的标记由螺纹代号、公差代号及旋合长度代号组成,彼此间用“―”离开。
根据国标规定,梯形螺纹代号由种类代号Tr和螺纹“公称直径×导程”表示,由于标准对内螺纹小径D1和外螺纹大径只规定了一种公差带(4H、4h),规定外螺纹小径d的公差地位永远为h的基础偏差为零。
公差等级与中径公差等级数雷同,而对内螺纹大径D4,标准只规定下偏差(即基础偏差)为零,而对上偏差不作规定,因此梯形螺纹仅标记中径公差带,并代表梯形螺纹公差(由表现公差带等级的数字及表现公差带地位的字母组成)螺纹的旋合长度分为三组,分辨称为短旋合长度(S)、中旋合长度(N)和长旋合长度(L)。
在一般情形下,中等旋合长度(N)用得较多,可以不标注。
梯形螺纹副的公差代号分辨注出内、外螺纹的公差带代号,前面是内螺纹公差带代号,后面是外螺纹公差带代号,中间用斜线分隔。
2.标记示例螺纹代号:单线螺纹:Tr40×6-6h-L;Tr:螺纹种类代号(梯形螺纹);40:公称直径;6:导程(对于单线螺纹而言,导程即为螺距);6h:内螺纹公差代号;L:旋合长度代号。
蜗轮蜗杆设计参数

圆柱蜗轮、蜗杆设计参数选择蜗轮和蜗杆通常用于垂直交叉的两轴之间的传动(图1)。
蜗轮和蜗杆的齿向是螺旋形的,蜗轮的轮齿顶面常制成环面。
在蜗轮蜗杆传动中,蜗杆是主动件,蜗轮是从动件。
蜗杆轴向剖面类是梯形螺纹的轴向剖面,有单头和多头之分。
若为单头,则蜗杆转一圈蜗轮只转一个齿,因此可以得到较高速比。
计算速比(i)的公式如下:蜗杆转速n1 —蜗轮齿数z2,=蜗轮转速n2 =蜗杆头数z11、蜗轮蜗杆主要参数与尺寸计算主要参数有:模数(m)、蜗杆分度圆直径(di)、导程角(r)、中心距(a)、蜗杆头数(或线数z1)、蜗轮齿数(z2)等,根据上述参数可决定蜗杆与蜗轮的基本尺寸,其中z1、z2由传动要求选定。
(1)模数m 为设计和加工方便,规定以蜗杆轴项目数mx和蜗轮的断面模数mt为标准模数。
对啮合的蜗轮蜗杆,其模数应相等,及标准模数m=mx=mt。
标准模数可有表A查的,需要注意的是,蜗轮蜗杆的标准模数值与齿轮的标准模数值并不相同。
图1(2) 蜗杆分度圆直径di再制造蜗轮时,最理想的是用尺寸、形状与蜗杆完全相同的蜗轮滚刀来进行切削加工。
但由于同一模数蜗杆,其直径可以各不相同,这就要求每一种模数对应有相当数量直径不同的滚刀,才能满足蜗轮加工需求。
为了减少蜗轮滚刀数目,在规定标准模数的同时,对蜗杆分度圆直径亦实行了标准化,且与m 有一定的匹配。
蜗杆分度圆直径di与轴向模数mx之比为一标准值,称蜗杆的直径系数。
即d 仁mq有关标准模数m 与标准分度圆直径 di 的搭配值及对应的蜗杆直径系数参照表 A(3)蜗杆导程角r 当蜗杆的q 和z1选定后,在蜗杆圆柱上的导程角即被确定。
为导程角、导程和分度圆直径的关系。
_ 导程 _蜗杆头数x 轴向齿距 zipx _z1 n m _z1 tan r=分度圆周长=分度圆周长=dT 7 = v mq - =q相互啮合的蜗轮蜗杆,其导程角的大小与方向应相同。
(4)中心距a 蜗轮与蜗杆两轴中心距 a 与模数m 、蜗杆直径系数 q 以及蜗轮齿数 z2 间的关系式如下:d1+d2 m a= 2(q+z2)(1) 蜗杆的规定画法 参照图1图2 (2) 蜗轮的规定画法 参照图1图2 (3)蜗轮蜗杆啮合画法 参照图1图2.蜗杆分度圆直径q = 模数—dim蜗杆各部尺寸如表 B 蜗轮各部尺寸如表 C 2、 蜗轮蜗杆的画法。
1:4分层法车梯形螺纹

1:4分层法车梯形螺纹摘要:初学左右切削法车梯形螺纹时,借刀量不易控制,容易产生“扎刀”等问题,“1:4分层法”将借刀量量化,有效解决了初学者盲目借刀的问题,还可大大地提高车削效率,实践证明是有效可行的。
关键词:1:4分层法、梯形螺纹、中滑板、小滑板、借刀在《车工生产实习》教材上,车削梯形螺纹的方法主要有左右切削法和斜进法。
在教学中发现:如果简单地运用这两种加工,对于初学者往往不能很快地接受并掌握,车削过程中还易出现“扎刀”等不良现象,而且完成一次练习所需要的时间也较多。
原因是上述两种方法在运用过程中,中、小滑板的进给量和借刀量没有予以量化,学生练习时找不到感觉,盲目借刀,很容易造成“扎刀”等问题,从而制约了训练效果的提高。
根据这种情况,从实践中总结得出了“1:4分层法车梯形螺纹”的方法,经实践证明是有效可行的。
1:4分层法的原理是:梯形螺纹的牙形半角为15°,其正切值为:0.2679,近似于1:4。
这一关系正好反映出小滑板的借刀量与中滑板的进给量之间的比例关系,从而为实现进给量与借刀量的量化提供了依据,亦即小滑板每借过一个单位,则中滑板应相应进给四个单位。
以车削螺距P=6的梯形螺纹为例说明“1:4分层法”的具体应用:螺距P=6的梯形螺纹,其牙顶宽f=0.366P=0.366×6≈2.2㎜,牙槽底宽w=0.366P-0.536a c=0.366×6-0.536×0.5≈1.93㎜,牙型高度h3=0.5P+a c=0.5×6+0.5=3.5㎜。
粗车时,粗车刀的刀头宽按“w-(0.3~0.4)”确定,可取为1.5㎜,牙顶宽留精车余量单边为0.2㎜左右,则粗车时牙槽口宽为:6-2.2-0.2×2=3.4㎜,故在牙顶部位小滑板的最大借刀量为:3.4-1.5=1.9㎜,粗车时总切削深度应略小于牙型高度h3,可取为:3.4㎜。
因此,在C6140车床上(中滑板刻度示值0.05mm/小滑板刻度示值0.05mm/格),小滑板的最大借刀范围为3.4/0.05=38格,中滑板共应进给3.4/0.05=68格,于是可按下表进行车削:(注:车削前,中、小滑板刻度应对零)从上表可看出:小滑板每向左或右借1格(0.05㎜),则中滑板相应进给4格(0.2㎜)为1:4的关系,而且每两刀为一层,因此本方法可称作“1:4分层法”。
蜗轮蜗杆常见普通的规格及尺寸
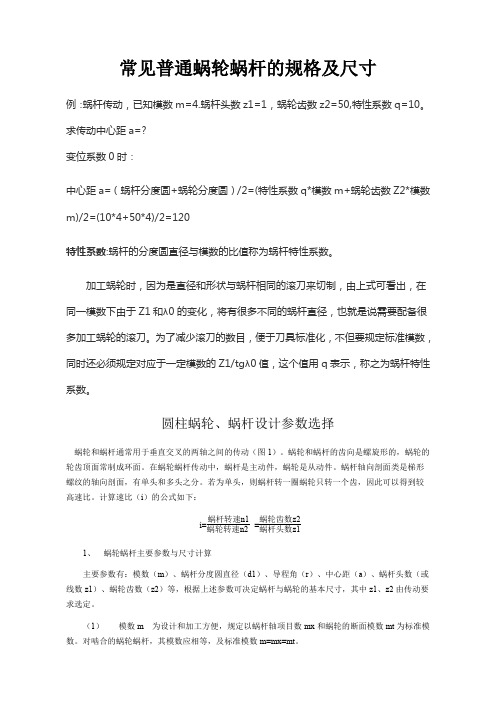
常见普通蜗轮蜗杆的规格及尺寸例:蜗杆传动,已知模数m=4.蜗杆头数z1=1,蜗轮齿数z2=50,特性系数q=10。
求传动中心距a=?变位系数0时:中心距a=(蜗杆分度圆+蜗轮分度圆)/2=(特性系数q*模数m+蜗轮齿数Z2*模数m)/2=(10*4+50*4)/2=120特性系数:蜗杆的分度圆直径与模数的比值称为蜗杆特性系数。
加工蜗轮时,因为是直径和形状与蜗杆相同的滚刀来切制,由上式可看出,在同一模数下由于Z1和λ0的变化,将有很多不同的蜗杆直径,也就是说需要配备很多加工蜗轮的滚刀。
为了减少滚刀的数目,便于刀具标准化,不但要规定标准模数,同时还必须规定对应于一定模数的Z1/tgλ0值,这个值用q表示,称之为蜗杆特性系数。
圆柱蜗轮、蜗杆设计参数选择蜗轮和蜗杆通常用于垂直交叉的两轴之间的传动(图1)。
蜗轮和蜗杆的齿向是螺旋形的,蜗轮的轮齿顶面常制成环面。
在蜗轮蜗杆传动中,蜗杆是主动件,蜗轮是从动件。
蜗杆轴向剖面类是梯形螺纹的轴向剖面,有单头和多头之分。
若为单头,则蜗杆转一圈蜗轮只转一个齿,因此可以得到较高速比。
计算速比(i)的公式如下:i=蜗杆转速n1蜗轮转速n2=蜗轮齿数z2蜗杆头数z11、蜗轮蜗杆主要参数与尺寸计算主要参数有:模数(m)、蜗杆分度圆直径(d1)、导程角(r)、中心距(a)、蜗杆头数(或线数z1)、蜗轮齿数(z2)等,根据上述参数可决定蜗杆与蜗轮的基本尺寸,其中z1、z2由传动要求选定。
(1)模数m 为设计和加工方便,规定以蜗杆轴项目数mx和蜗轮的断面模数mt为标准模数。
对啮合的蜗轮蜗杆,其模数应相等,及标准模数m=mx=mt。
标准模数可有表A查的,需要注意的是,蜗轮蜗杆的标准模数值与齿轮的标准模数值并不相同。
表A图1图2(2)蜗杆分度圆直径d1 再制造蜗轮时,最理想的是用尺寸、形状与蜗杆完全相同的蜗轮滚刀来进行切削加工。
但由于同一模数蜗杆,其直径可以各不相同,这就要求每一种模数对应有相当数量直径不同的滚刀,才能满足蜗轮加工需求。
- 1、下载文档前请自行甄别文档内容的完整性,平台不提供额外的编辑、内容补充、找答案等附加服务。
- 2、"仅部分预览"的文档,不可在线预览部分如存在完整性等问题,可反馈申请退款(可完整预览的文档不适用该条件!)。
- 3、如文档侵犯您的权益,请联系客服反馈,我们会尽快为您处理(人工客服工作时间:9:00-18:30)。
数控编程与操作
教学模式改革-理实一体化授课教案
模块一数控车床的编程与操作
数车基本模块FANUC系统数控车床编程及操作课题十三梯形螺纹、蜗杆加工(G76的应用)
图1 梯形螺纹零件图
图2螺纹切削多次循环与进刀法
⑧K:螺纹牙高(用半径值指令在X轴方向的距离);
⑨△d:第一次的切入量(用半径指定);
图3 K的计算机示意图
、蜗杆与梯形螺纹在程序上区别甚小,只需将N21程序段改为N21 G76 P011040 Q200 R200;N23程序段中根据蜗杆的模数等参数作调整即可。
导学材料
必学部分:教材:《数控车削编程与加工》G76及梯形螺纹与蜗杆的加工部分
选学部分:数控机床加工工艺、《数控铣削编程与加工》G76指令部分
教学后记:今天主要讲了G76,强调其应用方式,作业为做M36×的螺纹,并要求学生尽快补上前几次因打球而欠下的作业。
两小时做仿真包括讲课每次时间偏紧,待检查完成作业往往拖堂半小时。
且此法仿真与实操作脱节。