蜗杆加工方法【干货技巧】
蜗杆加工工艺技术
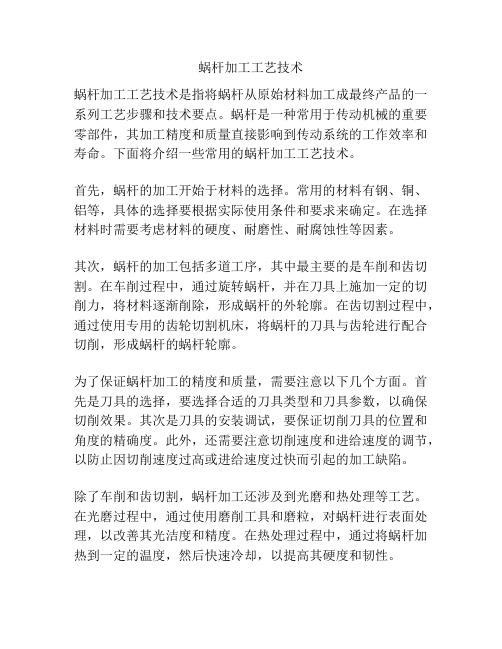
蜗杆加工工艺技术蜗杆加工工艺技术是指将蜗杆从原始材料加工成最终产品的一系列工艺步骤和技术要点。
蜗杆是一种常用于传动机械的重要零部件,其加工精度和质量直接影响到传动系统的工作效率和寿命。
下面将介绍一些常用的蜗杆加工工艺技术。
首先,蜗杆的加工开始于材料的选择。
常用的材料有钢、铜、铝等,具体的选择要根据实际使用条件和要求来确定。
在选择材料时需要考虑材料的硬度、耐磨性、耐腐蚀性等因素。
其次,蜗杆的加工包括多道工序,其中最主要的是车削和齿切割。
在车削过程中,通过旋转蜗杆,并在刀具上施加一定的切削力,将材料逐渐削除,形成蜗杆的外轮廓。
在齿切割过程中,通过使用专用的齿轮切割机床,将蜗杆的刀具与齿轮进行配合切削,形成蜗杆的蜗杆轮廓。
为了保证蜗杆加工的精度和质量,需要注意以下几个方面。
首先是刀具的选择,要选择合适的刀具类型和刀具参数,以确保切削效果。
其次是刀具的安装调试,要保证切削刀具的位置和角度的精确度。
此外,还需要注意切削速度和进给速度的调节,以防止因切削速度过高或进给速度过快而引起的加工缺陷。
除了车削和齿切割,蜗杆加工还涉及到光磨和热处理等工艺。
在光磨过程中,通过使用磨削工具和磨粒,对蜗杆进行表面处理,以改善其光洁度和精度。
在热处理过程中,通过将蜗杆加热到一定的温度,然后快速冷却,以提高其硬度和韧性。
最后,蜗杆加工还需要进行质量检测和表面处理。
通过使用专用的测量工具和设备,对蜗杆的尺寸、形状和表面质量进行检测,以确保其符合设计要求。
在表面处理中,可以进行镀铬、喷涂等处理,以提高蜗杆的耐磨性和耐腐蚀性。
综上所述,蜗杆加工工艺技术包括材料选择、车削、齿切割、光磨、热处理等一系列步骤和技术要点。
通过合理的选择和应用这些技术,可以提高蜗杆的加工精度和质量,从而提高传动系统的工作效率和寿命。
蜗杆加工工艺技术是一项复杂的机械加工工艺,要求加工过程具有高度的精度和稳定性。
下面将继续介绍相关的技术内容。
在蜗杆的加工过程中,车削是一个关键的工艺步骤。
蜗杆加工工艺路线和论证

蜗杆加工工艺路线和论证蜗杆加工工艺路线:1. 材料选择:蜗杆材料通常选择高强度、高硬度的合金钢、不锈钢、铜合金等材料。
2. 切削加工:蜗杆是通过切削工艺来制造的,常见的切削方式有车削、铣削、磨削、拉削等。
3. 热处理:为了提高蜗杆的强度和耐磨性,通常需要对其进行热处理。
常见的热处理工艺有淬火、回火、渗碳等。
4. 精密加工:蜗杆是精密零件,需要进行精密加工处理。
常见的精密加工方式有磨齿、研磨等。
5. 表面处理:蜗杆表面处理通常采用镀铬、喷涂、阳极氧化等方式,提高其表面硬度和耐磨性。
6. 装配和检验:蜗杆制造完成后,需要进行装配和检验,确保其质量符合要求。
论证:蜗杆是机械传动中常用的零件之一,其加工质量的好坏直接影响到机械传动的稳定性和可靠性。
针对蜗杆的加工工艺路线,需要考虑以下几个方面:1. 材料选择的合理性:蜗杆通常承受较大的负荷,因此需要选择高强度、高硬度的材料。
在选择材料时需要综合考虑其成本、可加工性、耐磨性等因素。
2. 切削加工的精度和表面质量:蜗杆是高精度零件,其几何形状和表面粗糙度直接影响到传动的精度和噪声水平。
因此在切削加工时需要考虑刀具的选择、切削参数的控制、加工过程中的冷却和润滑等因素。
3. 热处理的工艺控制:蜗杆的热处理需要精确控制温度、时间和冷却方式,以保证其组织结构和性能指标符合要求。
4. 精密加工的工艺控制:蜗杆的磨齿和研磨加工需要使用高精密度的设备,并严格控制加工过程中的参数和误差,以确保蜗杆的精度和表面质量符合要求。
5. 表面处理的效果评价:蜗杆表面处理需要注意其基材与涂层之间的黏着度和密合性,以及涂层的厚度和硬度等因素。
需要进行表面质量的评价和质量检查,确保蜗杆表面的质量符合要求。
6. 装配和检验的质量控制:在蜗杆的装配和检验过程中,需要严格控制加工误差和装配偏差,保证蜗杆的传动精度和噪声水平符合要求,并进行可靠性测试。
精通双线蜗杆的加工细节,助力工艺完美

精通双线蜗杆的加工细节,助力工艺完美双线蜗杆是数控加工中常见的零件之一。
它通常用于传动机构中,是一种带有歯轮的蜗轮蜗杆传动系统。
由于其结构特殊,制造难度较大。
在制造双线蜗杆的同时,切削工具的选择、加工工艺的合理调配及各个细节的处理都直接关系到双线蜗杆的质量和性能。
本文将从加工工具、数控加工及细节处理等方面进行探讨,以期帮助工程师在加工双线蜗杆的时候能够做到事半功倍、制造高品质的产品。
一、加工工具的选择在加工双线蜗杆的时候,切削工具的选择非常重要。
由于蜗杆的齿廓和蜗轮的齿廓都十分特殊,在加工的时候需要使用高精度的切削工具。
特别是在加工蜗轮的时候,由于蜗轮的齿形偏瘦而且齿根的肉厚不一样,一般需要使用高硬度的切削工具来保证加工的精度和效率。
在选择刀具时应注意选择合适类型的结构和尺寸,来保证切削质量和材料加工精度,满足蜗轮齿形和蜗杆齿形的精度要求。
二、数控加工双线蜗杆是一种高精度的零件,其制造需要高精度的数控加工设备。
由于蜗轮蜗杆的传动比较大,因此需要进行连续加工。
在装夹中心时,应注意蜗轮的齿廓的定位,力求达到最小间隙定位,保证加工的精度和效果。
同时,采用高高速走刀等加工方法,可以大大提高加工效率和精度。
三、细节处理在加工双线蜗杆的时候,由于零件特殊的结构和功能,需要对一些细节进行精细处理。
具体而言如下:1.加工前需要清洗:对于双线蜗杆的表面,应及时清洗干净,以免被切屑污染或残留的油脂影响加工效果。
同时,对钢材的表面也要清洗干净,使得钢材表面光洁度更高。
2.选择合适的润滑油:在数控加工过程中,适当使用一些润滑油可以提高切削效果和延长刀具使用寿命,但应选择合适的量和类型。
3.压力控制:采用高效的压力控制装置,对加工过程中的力量进行控制,避免其对双线蜗杆进行损伤。
4.合理选用渐近圆弧插入:在加工蜗轮的时候,采用渐近圆弧插入方法可以避免拉出大缺口,同时提高铣削质量和切削效率。
精通双线蜗杆的加工细节可以助力工艺完美,制造高品质的产品。
螺纹(蜗杆)的加工方法

1.蜗杆是用来配合蜗轮来传递动力的,常用于减速机构中,以传递两轴在空间90°交错的运动。
常用的蜗杆有米制(齿形角为40°)和英制(齿形角为29°)两种。
我国大多采用米制蜗杆。
如图4.13所示,阿基米德蜗杆是用刀刃角为2a=40°的梯形车刀车削出来的。
图4.13加工时刀刃处于过蜗杆轴线的水平面内,这样车削出的蜗杆轴剖面上的齿形为直线(类似于渐开线齿条)。
b)车削蜗杆的方法蜗杆和大导程螺纹车削的进刀方法有多种,如直进法、左右切削法、斜进法和切槽法等。
在数控车床上车削较大导程的蜗杆、梯形螺纹和锯齿螺纹,由于工件的齿形深,需要切除的毛坯余量多,一般是选择较低的切削速度和高速钢成形刀,使用G32和G76等指令车削,加工精度特别是表面粗糙度很难达到图纸要求,加工难度较大。
c)合理选择车削蜗杆的刀具角度,使刀具的刀尖角小于齿形角车削蜗杆刀具的刀尖角如果等于蜗杆的齿形角。
这种刀具在车削时两侧刀刃与工件侧面容易发生摩擦,甚至三个刀刃同时参加切削,易产生较大的切削力而损坏刀具。
如果选择车刀的刀尖角35 小于蜗杆的齿形角40 ,(如图2)这种车刀在车削时,可防止三个刀刃同时参加切削,减少了摩擦、切削力,能很好地避免“闷车”、“扎刀”和打刀的情况发生。
3 . 实训内容a)如图所示为40的棒料,模数为1.4mm。
齿高计算:h=2.2xm=2.9mmb)参考程序:O0002;左端外圆序号N1 G00 G40 G97 G99 M03 S600 T0101 F0.2;程序初始设置Z2.;X42.; 快进到起刀点G71 U1.5 R0.5;G71 P10 Q20 U0.3; 外圆粗车循环调用N10 G00 X10.;Z0;G01 X15. C1.;Z-27.;X20. C1.;Z-18.;X38. W-3.267;N20 W-60.; 外圆粗车循环结束G00 X100.;Z100.; 返回换刀点G00 M03 S900; 精加工X42. Z2.;G70 P10 Q20 F0.1; 外圆精加工调用G00 X100.;Z100.; 快退至换刀点M05; 主轴停转M30; 程序结束调头加工右端O0003; 程序号序号N1 G00 G40 G97 G99 M03 S600 T0101 F0.2;Z2.;X42.; 快进到起刀点G71 U1.5R0.5;G71 P30 Q40 U0.2; 外圆粗车循环调用G00 X15.;N3G01 Z0;X20. C1.;Z-18.;X38. W-3.267;W-5.; 外圆粗车循环结束N4G00 X100.;Z100.; 快退到换刀点G00 M03 S900; 外圆精加工设置X42.;Z2.; 起刀点G70 P30 Q40 F0.1; 外圆精车调用G00 X100.;Z100.; 快退到换刀点M05; 主轴停转M0; 程序暂停N2 ; 蜗杆加工G00 M03 S300 T0303;X 42.;Z-8.; 起刀点G76 P000030 Q40 R0;G76 X30.2 Z-80. P2900Q300 F4; 螺纹复合循环调用G00 X100.;Z100.; 快退到换刀点M05; 主轴停转M30; 程序结束。
实际操作训练,让你轻松掌握双线蜗杆的加工要点
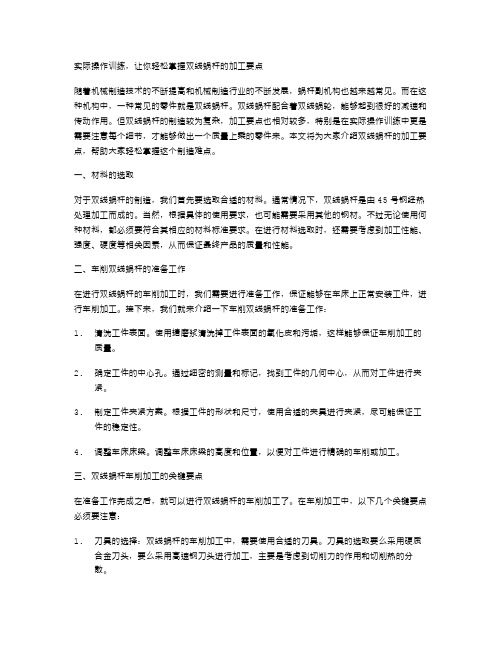
实际操作训练,让你轻松掌握双线蜗杆的加工要点随着机械制造技术的不断提高和机械制造行业的不断发展,蜗杆副机构也越来越常见。
而在这种机构中,一种常见的零件就是双线蜗杆。
双线蜗杆配合着双线蜗轮,能够起到很好的减速和传动作用。
但双线蜗杆的制造较为复杂,加工要点也相对较多,特别是在实际操作训练中更是需要注意每个细节,才能够做出一个质量上乘的零件来。
本文将为大家介绍双线蜗杆的加工要点,帮助大家轻松掌握这个制造难点。
一、材料的选取对于双线蜗杆的制造,我们首先要选取合适的材料。
通常情况下,双线蜗杆是由45号钢经热处理加工而成的。
当然,根据具体的使用要求,也可能需要采用其他的钢材。
不过无论使用何种材料,都必须要符合其相应的材料标准要求。
在进行材料选取时,还需要考虑到加工性能、强度、硬度等相关因素,从而保证最终产品的质量和性能。
二、车削双线蜗杆的准备工作在进行双线蜗杆的车削加工时,我们需要进行准备工作,保证能够在车床上正常安装工件,进行车削加工。
接下来,我们就来介绍一下车削双线蜗杆的准备工作:1.清洗工件表面。
使用搪磨浆清洗掉工件表面的氧化皮和污垢,这样能够保证车削加工的质量。
2.确定工件的中心孔。
通过细密的测量和标记,找到工件的几何中心,从而对工件进行夹紧。
3.制定工件夹紧方案。
根据工件的形状和尺寸,使用合适的夹具进行夹紧,尽可能保证工件的稳定性。
4.调整车床床梁。
调整车床床梁的高度和位置,以便对工件进行精确的车削或加工。
三、双线蜗杆车削加工的关键要点在准备工作完成之后,就可以进行双线蜗杆的车削加工了。
在车削加工中,以下几个关键要点必须要注意:1.刀具的选择:双线蜗杆的车削加工中,需要使用合适的刀具。
刀具的选取要么采用硬质合金刀头,要么采用高速钢刀头进行加工,主要是考虑到切削力的作用和切削热的分散。
2.切削参数的设定:在进行车削加工之前,还需要设定好切削参数。
比如进给速度、主轴转速、切削深度、切削宽度和切削角度等等,这样才能够保证加工质量和效率。
渐开线蜗杆加工方法
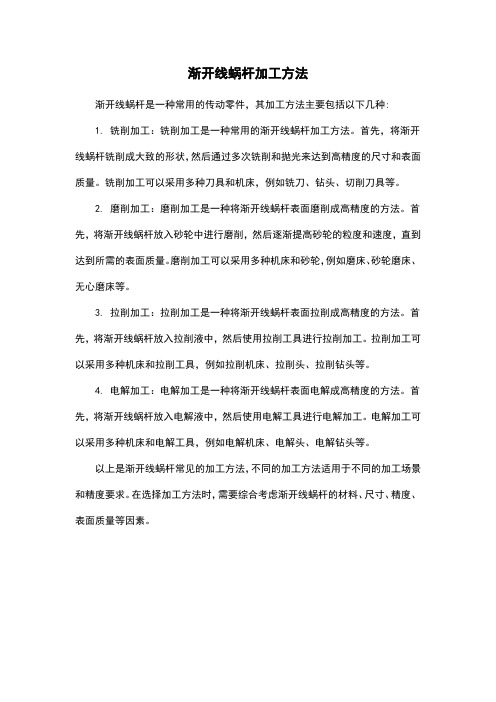
渐开线蜗杆加工方法
渐开线蜗杆是一种常用的传动零件,其加工方法主要包括以下几种:
1. 铣削加工:铣削加工是一种常用的渐开线蜗杆加工方法。
首先,将渐开线蜗杆铣削成大致的形状,然后通过多次铣削和抛光来达到高精度的尺寸和表面质量。
铣削加工可以采用多种刀具和机床,例如铣刀、钻头、切削刀具等。
2. 磨削加工:磨削加工是一种将渐开线蜗杆表面磨削成高精度的方法。
首先,将渐开线蜗杆放入砂轮中进行磨削,然后逐渐提高砂轮的粒度和速度,直到达到所需的表面质量。
磨削加工可以采用多种机床和砂轮,例如磨床、砂轮磨床、无心磨床等。
3. 拉削加工:拉削加工是一种将渐开线蜗杆表面拉削成高精度的方法。
首先,将渐开线蜗杆放入拉削液中,然后使用拉削工具进行拉削加工。
拉削加工可以采用多种机床和拉削工具,例如拉削机床、拉削头、拉削钻头等。
4. 电解加工:电解加工是一种将渐开线蜗杆表面电解成高精度的方法。
首先,将渐开线蜗杆放入电解液中,然后使用电解工具进行电解加工。
电解加工可以采用多种机床和电解工具,例如电解机床、电解头、电解钻头等。
以上是渐开线蜗杆常见的加工方法,不同的加工方法适用于不同的加工场景和精度要求。
在选择加工方法时,需要综合考虑渐开线蜗杆的材料、尺寸、精度、表面质量等因素。
球面蜗杆的加工

冷加工
! " " # 年 第 $ % 期 # !" ! ! !" # $ % & ’ ! ( ) * + , -. / 0 1" 2 ( #
图! %
侧间隙较小,通常需要采用修形来达到这一目的。 ,蜗杆的粗、 由球面蜗杆的成形原理可知( 见图 % )
精切齿加工工艺方案,不能像普通蜗杆那样在车床上加 工,因为车床只能加工圆柱形蜗杆,而球面蜗杆在车床 上是无法加工的。加工球面蜗杆的刀具切削刃必须绕一 个固定圆做圆周运动,并与之相切,目前国内外现有设 备,能实现该功能的只有立式滚齿机。由滚齿机性能可 知正常切削的运动速度非常高,对蜗杆齿形精加工不合 适,尤其是多头蜗杆,因为这种切削速度超过了滚齿机 分度蜗杆,蜗轮之间易产生胶合而损坏机床。因此必须 采用一套降速装置,为提高精切螺纹的生产效率,空行
图! "
%" 精车蜗杆
在同一基面上用高度尺测量刀高和蜗杆 "%#1& (,, 的轴颈与其等高,然后蜗杆即刀架向下降 "%#1& (,, 的 一半。这样保证了蜗杆中心高与车刀切削刃等高。 ( # ) 对刀盒的固定 ! 首先将对刀尺固定在刀盒上, 对刀尺寸厚度为 %-,,。用量块调整修正圆直径达 0 5 (#-& #*,,,对刀尺靠在对刀圆盘上,紧固刀盒。卸下 对刀尺,装好车刀。 ( " ) 精切齿! 用车刀靠近齿面,车刀刀尖达到螺纹 底部紧固刀,用大车转动去两侧余量,至还有 #,, 余 量后,开始精车用慢速精车至图要求。 ( % ) 对称修形 ! 分度交换齿轮齿数比 & 5 (% + $ ,中 心距 增 量 !- 5 #%& %’,,。 修 正 成 形 圆 直 径 0 5 (#-& #*",,。 ( * ) 二次倒坡修形 ! 中心距增大值 1 5 #.& ($,,, 即立柱在原位置上后退 #.& ($,,,入口端倒坡开始点至 喉颈中心距离为 #%$(& *1,, 打出油含点,每侧 $ 个,共 计 #" 个油含点。倒左侧入口油含点,即左齿面时,轴 向相反方向窜动 " 倍加 %& %#,,。最后倒边角,铣齿加 工全部完成。
高效率的蜗杆加工工艺流程【详解】

高效率的蜗杆加工工艺内容来源网络,由“XX机械展〔11万㎡,1100多家展商,超10万观众〕〞收集整理!更多cnc加工中心、车铣磨钻床、线切割、数控刀具工具、工业机器人、非标自动化、数字化无人工厂、精密测量、3D打印、激光切割、钣金冲压折弯、精密零件加工等展示,就在XX机械展.1、蜗杆轴加工的工艺路线实例,图2所示为一蜗杆轴,材料选用40Cr 钢。
产品属于小批量生产。
图2 蜗杆轴该蜗杆轴φ20j6,φ17k5两外圆表面为支撑轴颈;锥体部分是装配离合器的表面;M18 ×1处装配圆螺母来固定轴承的轴向位置。
根据外形结构其毛坯选用φ50mm的圆钢〔棒料〕,在锯床上按240mm长度下料。
1.1基本加工路线外圆加工的方法很多,基本加工路线可归纳为四条。
①粗车—半精车—精车,对于一般常用材料,这是外圆表面加工采用的最主要的工艺路线。
②粗车—半精车—粗磨—精磨,对于黑色金属材料,精度要求高和表面粗糙度值要求较小、零件需要淬硬时,其后续工序只能用磨削而采用的加工路线。
③粗车—半精车—精车—金刚石车,对于有色金属,用磨削加工通常不易得到所要求的表面粗糙度,因为有色金属一般比较软,容易堵塞沙粒间的空隙,因此其最终工序多用精车和金刚石车。
④粗车—半精—粗磨—精磨—光整加工,对于黑色金属材料的淬硬零件,精度要求高和表面粗糙度值要求很小,常用此加工路线。
1.2 典型加工工艺路线蜗杆轴的主要加工表面是外圆表面,也还有常见的特特形表面,因此针对各种精度等级和表面粗糙度要求,按经济精度选择加工方法。
对普通精度的蜗杆轴加工,其典型的工艺路线如下:毛坯与其热处理—预加工—车削外圆—铣键槽—〔花键槽、沟槽〕—热处理—磨削—终检。
1.21 蜗杆轴的预加工轴类零件的预加工是指加工的准备工序,即车削外圆之前的工艺。
校直毛坯在制造、运输和保管过程中,常会发生弯曲变形,为保证加工余量均匀与装夹可靠,一般冷态下在各种压力机或校值机上进行校直。
浅谈普通车床加工蜗杆的车削技巧
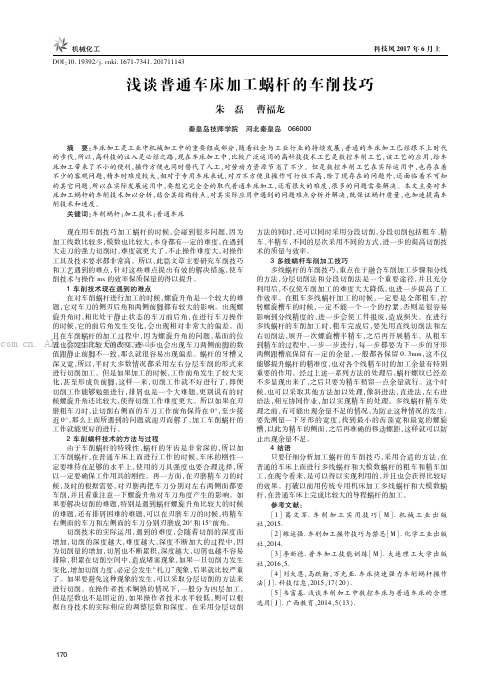
'车削技术现在遇到的难点 在对车削蜗杆进行加工的时候"螺旋升角是一个较大的难 题"它对车刀的侧刃后角和两侧前脚都有较大的影响$ 出现螺 旋升角时"相比处于静止状态的车刀前后角"在进行车刀操作 的时候"它的前后角发生变化"会出现相对非常大的偏差$ 而 且在车削蜗杆的加工过程中"因为螺旋升角的问题"基面的位
蜗杆加工工艺与工装设计

蜗杆加工工艺与工装设计一、蜗杆加工工艺蜗杆是一种常用于传动装置中的零件,具有高精度、高可靠性和高耐磨性等特点。
蜗杆的加工工艺是指对蜗杆进行加工的一系列工艺过程。
下面将从材料选择、车削加工、热处理和磨削加工等方面介绍蜗杆的加工工艺。
1.材料选择:蜗杆通常选择高强度、高耐磨性和高韧性的材料,如45号钢、40Cr、42CrMo等。
材料的硬度要保证达到一定的标准,以保证蜗杆的传动性能。
2.车削加工:蜗杆的加工一般采用车削加工的方法。
在车削前,需要根据蜗杆的尺寸要求制定相应的车削工艺,并选择适当的车削刀具和车削参数。
蜗杆的车削一般需要进行多道次的切削,以保证蜗杆的精度和表面质量。
3.热处理:蜗杆在车削加工完成后需要进行热处理,以提高其硬度和耐磨性。
热处理一般包括淬火和回火两个步骤。
淬火后蜗杆的硬度会大幅提高,但其脆性也会增加,因此需进行回火处理以降低其脆性,提高其韧性。
4.磨削加工:磨削是蜗杆加工的最后一个步骤。
蜗杆磨削主要是为了提高其精度和表面质量。
常用的磨削方法有外圆磨削、蜗杆磨削和蜗轮磨削等。
磨削加工时需要选择合适的砂轮和磨削工艺参数,并对蜗杆进行适当的冷却,以避免高温对蜗杆的影响。
二、蜗杆工装设计蜗杆工装设计是指为了保证蜗杆加工质量和效率,设计和制造相应的工装装置。
下面将从工装的结构设计、定位与夹紧和装置制造等方面介绍蜗杆工装设计的重点。
1.结构设计:蜗杆工装的结构设计应根据蜗杆的尺寸和加工工艺要求进行设计。
工装一般由基座、定位夹具、夹紧装置和切削刀具等组成。
基座需要具备足够的刚性和稳定性,以保证工装的稳定性。
夹具和夹紧装置需要根据蜗杆的形状和尺寸进行设计,以确保其在加工过程中的固定和夹紧。
2.定位与夹紧:蜗杆在加工过程中需要进行定位和夹紧。
定位主要是确定蜗杆的加工位置和方向,通常使用定位销、定位块等来实现。
夹紧则是将蜗杆固定在工装上,通常使用夹紧器、夹爪等来实现。
定位和夹紧应根据蜗杆的加工需求和加工精度进行设计和选型。
蜗杆轴零件的加工工艺

蜗杆轴零件的加工工艺1. 简介蜗杆轴是一种常见的传动装置,在机械设备中用于实现传动和变速功能。
蜗杆轴零件的加工工艺对于其质量和性能起着决定性的作用。
本文将介绍蜗杆轴零件的加工工艺流程以及相关注意事项。
2. 加工工艺流程2.1 材料准备蜗杆轴常用的材料有钢、铸铁等,选择合适的材料对于提高蜗杆轴的耐磨性和强度非常重要。
在加工工艺中,需要根据设计要求选择相应的材料,并进行材料预处理。
2.2 切削加工蜗杆轴的加工通常包括车削、铣削、钻削等切削加工过程。
在切削加工中,需要根据蜗杆轴的尺寸和形状要求,采用适当的切削工艺和工具进行加工。
切削加工时,需确保加工精度和表面质量,避免产生划痕和变形等缺陷。
2.3 热处理蜗杆轴常常需要进行热处理,以提高其硬度和耐磨性。
常用的热处理方法包括淬火、回火和表面渗碳等。
在热处理中,需要控制好加热温度和保温时间,以及冷却速度,以确保蜗杆轴在热处理后具有良好的性能。
2.4 修磨和校验蜗杆轴的表面精度和几何形状对于传动的性能有很大影响。
因此,在加工过程中,需要进行修磨和校验工序。
修磨过程中使用砂轮或砂带进行研磨,校验过程中则使用测量工具如千分尺、游标卡尺等对蜗杆轴进行检测和校正。
2.5 表面处理为了提高蜗杆轴的耐腐蚀性和摩擦性能,常常需要对其进行表面处理。
常见的表面处理方法有镀铬、电镀、喷涂、氮化等。
选择合适的表面处理方法,可以大幅度提高蜗杆轴的使用寿命和传动效率。
3. 注意事项在蜗杆轴零件的加工过程中,还需要注意以下几点:3.1 安全操作加工过程中,需要严格遵守安全操作规程,使用合适的防护设备,避免事故发生。
同时,要保证加工环境良好,防止灰尘、杂质等对加工质量的影响。
3.2 加工精度蜗杆轴是一种高精度零件,加工过程中需严格控制尺寸公差和表面粗糙度。
需要使用合适的切削工具和设备,保证加工精度符合设计要求。
3.3 耐磨性和润滑性蜗杆轴在工作过程中承受较大的摩擦和磨损,因此在加工过程中要注意提高其耐磨性和润滑性。
数控加工车削蜗杆方法及误差分析

数控加工车削蜗杆方法及误差分析在机械制造行业中蜗杆传动是啮合传动的一种重要形式,大多采用的是韶圆柱蜗杆。
我们知道,蜗杆的精度将会直接影响到传动质量,所以对车床的要求也越来越高,普通车床的加工随着数控技术发展正在逐步被数控车床所取代。
虽然数控车床有数控车床比普通车床有很多优势,但有一些加工内容,如大模数蜗杆。
因为这类零件螺旋槽加工深度大,每刀切削厚度难以掌握,所以很容易会出现扎刀把工件破损,对此要予以重视。
一、数控车床加工蜗杆及加工方法一般的圆柱蜗杆的齿面都可以看成由一条切于导圆柱(半径为r )并与端面夹a角的发生线,绕着蜗杆轴线作螺旋造动而形成。
蜗杆的加工方法是在车床上采用车削的方法进行加工,在普通的卧式车床上的切削方法有左右切削法。
但是在有数控技术的车床上,上述切削方法不适宜的,是因为:如果用车直槽或阶梯槽方法要多安装一把切槽刀,每次切槽刀切削后,蜗杆车刀的定位是很难确定的,再者每车一刀都要重新定位一次,程序的段数将相当多。
对于简单的模数=3的蜗杆,其程序的段数就要达几十甚至上百段。
1、粗车和精车所谓的粗车就是用三角螺纹车刀在工件外圆的背部吃刀0.05—0.01mm 处划出痕迹线,如图2所示,再依次沿轴向方向分别移动一个齿距p划线2、3,然后移动一个齿顶s =0.843/Z +0.6mm,图中标出来的,标注划线为第4头,再分别沿轴向方向移动一个齿距划出第5、6头。
划出的齿槽线后将各槽粗车出。
所谓的精车就是在确定某齿厚有0.3mm余量,并将该齿左侧设为1,该齿厚控制在0.15mm之内,以侧面为为基准精车侧面2,控制分度圆直径直到完成槽1车削。
然后完成精车齿侧3,其后各头齿厚及齿槽宽就这样依次车削下去即可。
2、蜗杆的加工方法加工蜗杆的方法常用的有左右切削法、直进法、单刃调头切削法、斜进法等。
左右切削法,加工蜗杆时属于单刃切削,加工中能较好地控制扎刀现象,可以完成蜗杆的粗车和精车,但是过程复杂,效率稍低。
高效加工蜗杆的数控车削方法,超有用!

高效加工蜗杆的数控车削方法,超有用!随着当今时代电子信息技术的突飞猛进,现代机械设备不断向自动化、数控化方向发展。
数控机床是现代制造业的基础技术,是提高产品质量和劳动生产率必不可少的手段,数控技术的发展和应用水平也是一个国家综合国力的标志,普通车床的加工也逐步被数控车床所取代。
对于蜗杆的加工,因螺距大,牙型深,加工余量大,再因其牙型特点,车削时刀刃与工件接触面大,容易发生振动,加工途中极易因工件与刀具间切屑的挤压造成刃具损坏,产生“扎刀”现象,造成蜗杆报废,而且加工时间周期长。
本文结合具体的生产实际,从刀具、车削方法和切削参数等方面对现有的加工进行改进,改善了刀具受力情况、提高了加工质量和切削效率;因数控程序简单,操作性强,为此类零件的加工提供了一定的借鉴、参考。
一、蜗杆的特性及参数的计算1.蜗杆的特性常用的蜗杆有公制(齿形角为40o)和英制(齿形角为29o)两种。
我国大多数采用公制蜗杆。
而最常用的是阿基米德蜗杆(即轴向直轮廓蜗杆)它的齿面为阿基米德螺旋面,端面是阿基米德螺旋线,如图1所示。
轴向齿廓(A-A截面)是直线,而法面(N-N截面)的齿形则为曲线,如图2所示。
2.蜗杆的结构及参数根据生产的要求,所要加工的蜗杆为公制蜗杆,模数Mx=3,齿形角为40o,材料45号钢,具体参数如表1所示。
蜗杆的结构和尺寸要求如图3所示。
如图所示,该蜗杆的尺寸精度和形位公差要求高,加工难度大,为了保证其精度要求,应尽量采用高精度的设备。
另外,公司产品以多品种小批量为主,采用专用铣削机床投入成本高,如果使用普通车床加工,对人员的要求很高,而且加工成本很高,效率太低,产品质量难以保证。
因公司的机床设备多样化,数控加工机床占生产设备70%左右,所以本次加工蜗杆决定采用高精度的数控车床HARDINgE (Quest 8/51),该数控车床为斜床身,12位刀塔,定位精度0.00mm ,重复定位精度0.005mm,Fanuc series 21i-T操作系统,最高转速3 500r/min,最低加工转速50r/min,最大加工直径400mm。
蜗杆加工方法
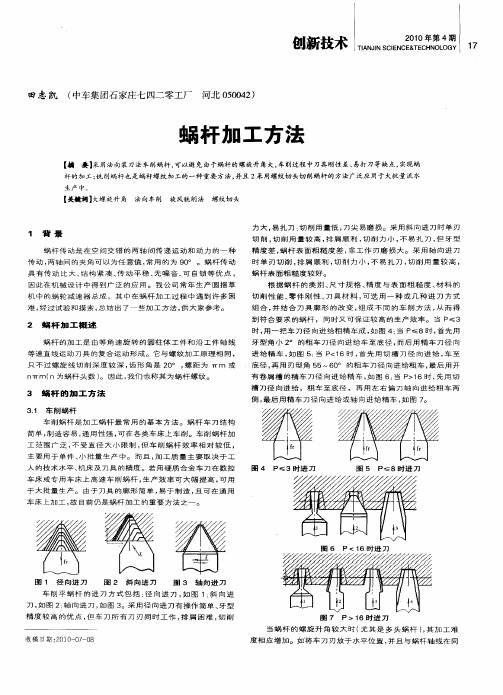
当 蜗 杆 的螺 旋 升 角 较 大 时 ( 其 是 多 头 蜗 杆 ) 其 加 工 难 尤 ,
收稿 日期 :0 0 0 — 8 2 1 - 7 0
度 相 应 增 加 。如 将 车 刀 刃 放 于水 平 位 置 , 并且 与蜗 杆 轴 线 在 同
1 8
21 0 0年第 4期
T AN I I J N SCl C E TE EN & CHNO L OG Y
力 大 , 扎 刀 : 削 用 量 低 , 尖 易 磨 损 。 采 用 斜 向 进 刀 时 单 刃 易 切 刀 切 削 , 削 用 量 较 高 , 屑 顺 利 , 削 力 小 , 易 扎 刀 , 牙 型 切 排 切 不 但 精 度 差 , 杆 表 面 粗 糙 度 差 , 工 作 刃 磨 损 大 。 采 用 轴 向 进 刀 蜗 非
杆 的加工 ; 削蜗杆也是蜗杆螺纹加 工的一种 重要 方法 , 铣 并且 2 用螺纹切 头切 削蜗杆的方法广泛应用 于大批量流 水 采
生 产 中。
【 关奠词 】 大螺旋升 角 法 向车削 旋风铣 削法 螺纹切 头
1 背 景
蜗 杆 传 动 是 在 空 间 交 错 的 两 轴 间传 递 运 动 和 动 力 的 一 种 传 动 , 轴 间 的 夹 角 可 以 为 任 意 值 , 用 的 为 9 。 。 蜗 t- 动 两 常 0 T -传
图 1 径 向进 刀
图 2 斜 向进 刀
图 3 轴 向进 刀
车 削 平 蜗 杆 的 进 刀 方 式 包 括 : 向 进 刀 , 图 1: 向 进 径 如 斜
刀 , 图 2: 向 进 刀 , 图 3 如 轴 如 。采 用 径 向 进 刀 有 操 作 简 单 、 型 牙 精 度 较 高 的 优 点 , 车 刀 所 有 刀 刃 同 时工 作 , 屑 困难 , 削 但 排 切 图 7 P> 1 时 进 刀 6
四头蜗杆的加工工艺

四头蜗杆的加工工艺蜗杆是一种常见的机械传动零件,具有重要的传动功能。
四头蜗杆作为蜗杆的一种特殊类型,其加工工艺相对较为复杂。
本文将从蜗杆的加工原理、工艺流程、加工设备以及质量控制等方面进行详细阐述。
首先,蜗杆的加工原理是基于蜗杆的螺旋曲面特性,通过切削加工将蜗杆母体材料削去一部分,从而形成蜗杆的螺旋丝。
在加工过程中,需要准确控制螺旋丝的螺距、螺旋角等参数,以保证蜗杆的传动效果和使用寿命。
其次,四头蜗杆的加工工艺流程通常包括以下几个步骤:原料准备、车削成型、铣削精加工、热处理、磨削以及质量检验。
首先是原料准备,选择优质的蜗杆母体材料,通常为优质的合金钢或不锈钢材料。
然后进行车削成型,根据蜗杆的设计图纸,通过车床等设备对蜗杆母体进行初步成型。
接着是铣削精加工,利用铣床等设备对螺旋丝的螺距、螺旋角等进行精密加工,以保证蜗杆的传动效果。
之后进行热处理,通过淬火、回火等热处理工艺,提高蜗杆的硬度和强度。
然后是磨削,利用磨床等设备对蜗杆进行表面精密磨削,提高蜗杆的光洁度和精度。
最后进行质量检验,对蜗杆的外观质量、尺寸精度、硬度等进行全面检测,确保蜗杆达到标准要求。
再者,四头蜗杆的加工设备主要包括车床、铣床、磨床、热处理设备以及质量检测设备等。
其中,车床用于蜗杆的初步成型和粗加工,铣床用于螺旋丝的精密加工,磨床用于蜗杆的表面磨削,热处理设备用于提高蜗杆的硬度和强度,质量检测设备用于检验蜗杆的各项质量指标。
最后,四头蜗杆的加工质量控制是非常重要的。
在加工过程中,需要严格控制加工参数,确保蜗杆的尺寸精度和表面质量。
特别是在螺旋丝的加工过程中,需要保证螺距、螺旋角等参数的精确度。
此外,热处理工艺也是影响蜗杆质量的关键环节,需要根据材料的不同选择合适的热处理工艺,以保证蜗杆的硬度和强度达到要求。
综上所述,四头蜗杆的加工工艺涉及到多个环节和工艺步骤,需要严格控制加工参数和质量要求,确保蜗杆的传动效果和使用寿命。
只有具备高精度加工设备和严格的质量控制体系,才能生产出高质量的四头蜗杆产品。
蜗杆加工方法【干货技巧】
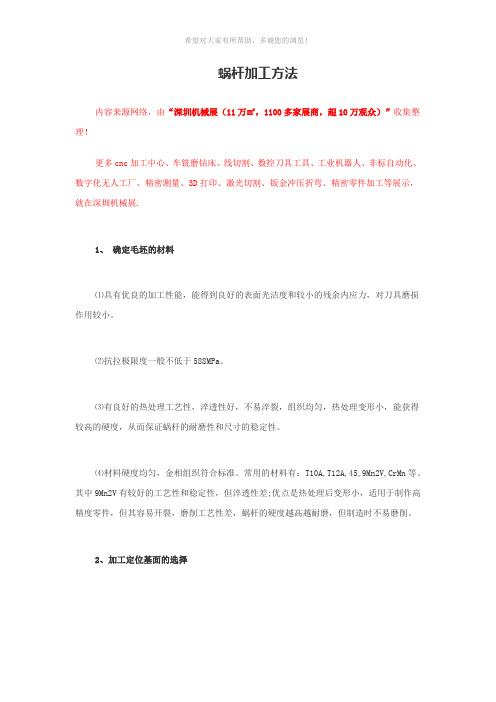
蜗杆加工方法内容来源网络,由“深圳机械展(11万㎡,1100多家展商,超10万观众)”收集整理!更多cnc加工中心、车铣磨钻床、线切割、数控刀具工具、工业机器人、非标自动化、数字化无人工厂、精密测量、3D打印、激光切割、钣金冲压折弯、精密零件加工等展示,就在深圳机械展.1、确定毛坯的材料⑴具有优良的加工性能,能得到良好的表面光洁度和较小的残余内应力,对刀具磨损作用较小。
⑵抗拉极限度一般不低于588MPa。
⑶有良好的热处理工艺性,淬透性好,不易淬裂,组织均匀,热处理变形小,能获得较高的硬度,从而保证蜗杆的耐磨性和尺寸的稳定性。
⑷材料硬度均匀,金相组织符合标准。
常用的材料有:T10A,T12A,45,9Mn2V,CrMn等。
其中9Mn2V有较好的工艺性和稳定性,但淬透性差;优点是热处理后变形小,适用于制作高精度零件,但其容易开裂,磨削工艺性差,蜗杆的硬度越高越耐磨,但制造时不易磨削。
2、加工定位基面的选择蜗杆定位基面:从结构上分,蜗杆有两种形式,套装蜗杆,整体蜗杆。
套装蜗杆以内孔加工基面,因此应先精加工内孔,然后以内孔为基面加工外圆及支承轴颈,螺纹的加工同样以内孔为基面,因此需要心轴。
一般精密分度蜗杆的内孔精度要求是很高的,有的需要进行研磨老保证精度。
一般精度分度蜗杆内孔应不低于1级精度,表面粗糙度不低于0.12,内孔的端面振摆应不小于0.005mm。
蜗杆装在心轴上加工时,应首先检查两端轴肩的径向跳动是否在规定允差之内,以后每道工序均应校验,在蜗杆装配时,同样要校验两端轴肩的径向跳动,心轴精度必须等于或高于与套装蜗杆相配的轴精度。
整体蜗杆以中心孔为加工基面,对中心孔的要求很高,应该有保锥,保证光洁度和接触面积,每道工序前要检查和修正中心孔,对支承轴颈应保证与中心孔同轴度和本身的几何精度,在半精加工和精加工工序前,都应检查支承轴颈的径向,跳径和端面的轴向振摆是否在公差以内。
选择粗基准时,考虑的重点是如何保证各加工面有足够的余量,使不加工基面与加工表面间的尺寸,位子符合图纸要求。
蜗杆加工工艺流程
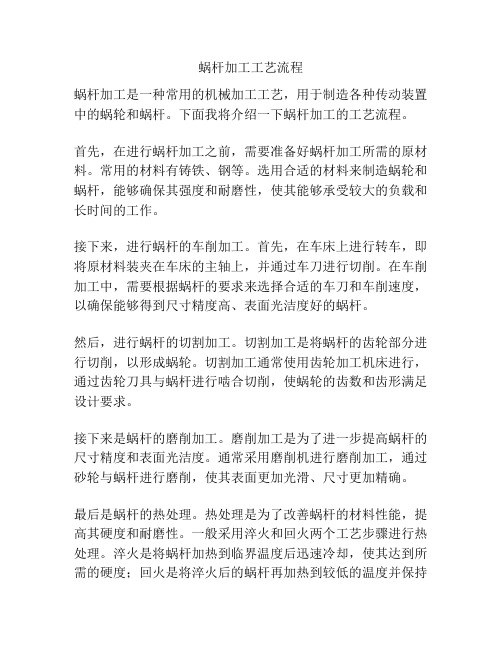
蜗杆加工工艺流程蜗杆加工是一种常用的机械加工工艺,用于制造各种传动装置中的蜗轮和蜗杆。
下面我将介绍一下蜗杆加工的工艺流程。
首先,在进行蜗杆加工之前,需要准备好蜗杆加工所需的原材料。
常用的材料有铸铁、钢等。
选用合适的材料来制造蜗轮和蜗杆,能够确保其强度和耐磨性,使其能够承受较大的负载和长时间的工作。
接下来,进行蜗杆的车削加工。
首先,在车床上进行转车,即将原材料装夹在车床的主轴上,并通过车刀进行切削。
在车削加工中,需要根据蜗杆的要求来选择合适的车刀和车削速度,以确保能够得到尺寸精度高、表面光洁度好的蜗杆。
然后,进行蜗杆的切割加工。
切割加工是将蜗杆的齿轮部分进行切削,以形成蜗轮。
切割加工通常使用齿轮加工机床进行,通过齿轮刀具与蜗杆进行啮合切削,使蜗轮的齿数和齿形满足设计要求。
接下来是蜗杆的磨削加工。
磨削加工是为了进一步提高蜗杆的尺寸精度和表面光洁度。
通常采用磨削机进行磨削加工,通过砂轮与蜗杆进行磨削,使其表面更加光滑、尺寸更加精确。
最后是蜗杆的热处理。
热处理是为了改善蜗杆的材料性能,提高其硬度和耐磨性。
一般采用淬火和回火两个工艺步骤进行热处理。
淬火是将蜗杆加热到临界温度后迅速冷却,使其达到所需的硬度;回火是将淬火后的蜗杆再加热到较低的温度并保持一定时间后冷却,以减轻淬火带来的脆性和应力。
综上所述,蜗杆加工工艺流程包括原材料准备、车削加工、切割加工、磨削加工和热处理。
每个工艺步骤都需要合理选择加工设备和工艺参数,才能够得到质量满足要求的蜗轮和蜗杆。
蜗杆加工工艺流程的优化和改进,能够提高蜗杆的加工效率和质量,满足各种传动装置的使用要求。
圆弧齿蜗杆加工工艺流程

圆弧齿蜗杆加工工艺流程一、加工前的准备。
二、毛坯制造。
接下来就是毛坯制造啦。
这毛坯的制造方式有不少呢。
要是用锻造的方法,就像是把一块铁疙瘩打造成型一样,能让材料的内部结构更紧密,强度更高。
铸造也是一种办法,不过铸造出来的毛坯可能需要更多的后续处理。
在制造毛坯的时候呀,尺寸的控制可重要了,不能偏差太大,不然后续加工就麻烦喽。
就像盖房子打地基,地基要是歪了,房子肯定盖不好呀。
三、粗加工。
粗加工的时候呢,那就是大刀阔斧地干啦。
先把大概的形状给弄出来。
在车床上把蜗杆的外圆、长度这些大的尺寸给加工出来。
这时候可不能太讲究精度,只要把多余的材料去掉就行。
就像画画先画个大概的轮廓一样。
不过呢,也不能太随意,毕竟粗加工要是偏差太大,精加工的时候就有的头疼了。
这就好比是盖房子先把框架搭起来,虽然不用太精致,但也得稳稳当当的。
四、半精加工。
半精加工就有点讲究了。
这时候要把精度提高一些啦。
对圆弧齿的形状开始慢慢雕琢。
比如说齿形的初步成型,得让它有点样子了。
尺寸的精度也要比粗加工的时候提高不少。
这就像画画开始上底色了,虽然还不是最后的成品,但已经能看出个大概模样了。
而且在这个过程中,要时刻关注加工的情况,有没有异常的声音呀,刀具磨损得厉不厉害呀,就像照顾一个小宝贝一样,得时刻留意着。
五、精加工。
精加工那可就是细活了。
这时候就是要把圆弧齿蜗杆加工到最后的精度要求。
齿形要精确,尺寸要精准。
就像雕刻大师在雕刻一件艺术品一样,一点点地修,一点点地磨。
在精加工的时候,切削的参数都要精心调整,速度呀、进给量呀都得恰到好处。
这时候对机床的稳定性要求也很高,可不能有一点晃动,不然就前功尽弃了。
而且精加工的时候要特别小心刀具的磨损,一旦刀具磨损了,那加工出来的东西可就不达标了。
六、检验。
加工完了可不能就完事儿了,还得检验呢。
就像做完一道菜得尝尝味道对不对一样。
用之前准备好的量具来量一量尺寸是不是符合要求,齿形是不是精准。
外观也得看看,有没有划伤之类的。
如何在数控车床上加工蜗杆
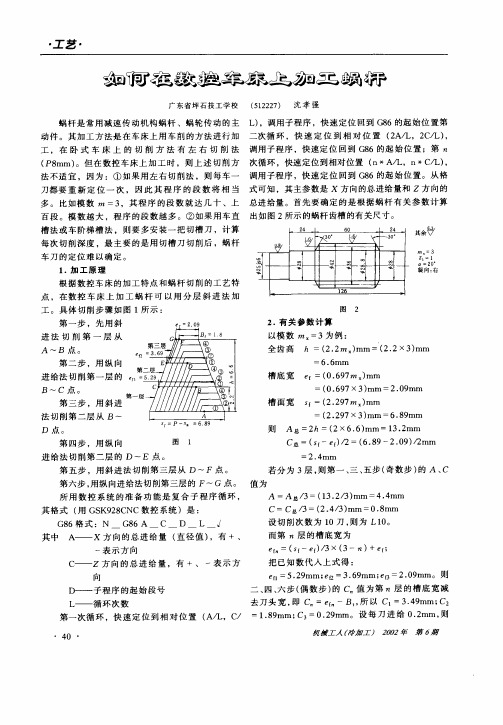
4 ・ 0
机 械1 人 ( 龆 I ) 2 0 冷 02年
第 6 期
・
I 艺・
切 削次数 分别 为 L1 、 0和 L 。如图 1 8 L1 2 所示 。
3 .编 程
( ) 由于 G 3在 y 方 向偏 移 了一 定 的距 离 , 2 3 所 以最 开 始 的定 位 位 置 是 蜗 杆 大 径 加 上 X 的 偏 移
一
C
—
D
—
L
√
设 切 削次数 为 1 0刀 , 为 L1 。 则 0
其中 A —— X 方 向 的总进 给 量 ( 径 值 ) 直 ,有 +、
一
而第 层 的槽 底宽 为
e = (f f/ × ( ) f f 5—e) 3 3一 +e;
表 示 方 向
C — Z方 向 的 总进 给 量 ,有 +、 一表示 方 —
=
A总=2 h= ( ×6 6 mm 1 .mm 2 .) 32 C总= ( f f/ 5—e)2=( .9 6 8 —2 0 ) mm .9 / 2
= 2. m m 4
第 四步 ,用 纵 向
图 1
进 给法 切削 第 二层 的 D~E 点 。 第 五步 ,用斜进 法 切削第 三层 从 D~F 点 。 所 用 数 控 系 统 的准 备 功 能是 复 合 子 程序 循 环 , 其 格式 ( GS 9 8 NC数控 系统 )是 : 用 K 2C
现加工 如 图 2所 示 蜗 杆 。根 据 以上 计 算 结 果 , 量 ,而 Z方 向要 大 于 蜗 杆 的右 端位 置 加 工 A 点 至 以  ̄ 8 m 左端 面为坐标原点 ,编制加 工程序如下 : F 点在 z方 向 的偏 移 量 ,即 C总。 2m
蜗杆怎么加工-蜗杆的加工工艺

蜗杆怎么加工| 蜗杆的加工工艺内容来源网络,由“深圳机械展(11万㎡,1100多家展商,超10万观众)”收集整理!更多cnc加工中心、车铣磨钻床、线切割、数控刀具工具、工业机器人、非标自动化、数字化无人工厂、精密测量、3D打印、激光切割、钣金冲压折弯、精密零件加工等展示,就在深圳机械展.在经济全球化的格局下,我国制造业发展越来越迅速,齿轮的使用范围也越来越广泛,齿轮中的蜗轮蜗杆对其传递与转换的作用也是别的齿轮无法代替的。
那么蜗杆是怎么加工?它的加工工艺又是什么?本文,贤集网小编主要就是讲的这些内容!蜗杆的加工工艺1、确定毛坯的材料⑴具有优良的加工性能,能得到良好的表面光洁度和较小的残余内应力,对刀具磨损作用较小。
⑵抗拉极限度一般不低于588MPa。
⑶有良好的热处理工艺性,淬透性好,不易淬裂,组织均匀,热处理变形小,能获得较高的硬度,从而保证蜗杆的耐磨性和尺寸的稳定性。
⑷材料硬度均匀,金相组织符合标准。
常用的材料有:T10A,T12A,45,9Mn2V,CrMn 等。
其中9Mn2V有较好的工艺性和稳定性,但淬透性差;优点是热处理后变形小,适用于制作高精度零件,但其容易开裂,磨削工艺性差,蜗杆的硬度越高越耐磨,但制造时不易磨削。
2、加工定位基面的选择蜗杆定位基面:从结构上分,蜗杆有两种形式,套装蜗杆,整体蜗杆。
套装蜗杆以内孔加工基面,因此应先精加工内孔,然后以内孔为基面加工外圆及支承轴颈,螺纹的加工同样以内孔为基面,因此需要心轴。
一般精密分度蜗杆的内孔精度要求是很高的,有的需要进行研磨老保证精度。
一般精度分度蜗杆内孔应不低于1级精度,表面粗糙度不低于0.12,内孔的端面振摆应不小于0.005mm。
蜗杆装在心轴上加工时,应首先检查两端轴肩的径向跳动是否在规定允差之内,以后每道工序均应校验,在蜗杆装配时,同样要校验两端轴肩的径向跳动,心轴精度必须等于或高于与套装蜗杆相配的轴精度。
整体蜗杆以中心孔为加工基面,对中心孔的要求很高,应该有保锥,保证光洁度和接触面积,每道工序前要检查和修正中心孔,对支承轴颈应保证与中心孔同轴度和本身的几何精度,在半精加工和精加工工序前,都应检查支承轴颈的径向,跳径和端面的轴向振摆是否在公差以内。
- 1、下载文档前请自行甄别文档内容的完整性,平台不提供额外的编辑、内容补充、找答案等附加服务。
- 2、"仅部分预览"的文档,不可在线预览部分如存在完整性等问题,可反馈申请退款(可完整预览的文档不适用该条件!)。
- 3、如文档侵犯您的权益,请联系客服反馈,我们会尽快为您处理(人工客服工作时间:9:00-18:30)。
蜗杆加工方法
内容来源网络,由“深圳机械展(11万㎡,1100多家展商,超10万观众)”收集整理!
更多cnc加工中心、车铣磨钻床、线切割、数控刀具工具、工业机器人、非标自动化、数字化无人工厂、精密测量、3D打印、激光切割、钣金冲压折弯、精密零件加工等展示,就在深圳机械展.
1、确定毛坯的材料
⑴具有优良的加工性能,能得到良好的表面光洁度和较小的残余内应力,对刀具磨损作用较小。
⑵抗拉极限度一般不低于588MPa。
⑶有良好的热处理工艺性,淬透性好,不易淬裂,组织均匀,热处理变形小,能获得较高的硬度,从而保证蜗杆的耐磨性和尺寸的稳定性。
⑷材料硬度均匀,金相组织符合标准。
常用的材料有:T10A,T12A,45,9Mn2V,CrMn 等。
其中9Mn2V有较好的工艺性和稳定性,但淬透性差;优点是热处理后变形小,适用于制作高精度零件,但其容易开裂,磨削工艺性差,蜗杆的硬度越高越耐磨,但制造时不易磨削。
2、加工定位基面的选择
蜗杆定位基面:从结构上分,蜗杆有两种形式,套装蜗杆,整体蜗杆。
套装蜗杆以内孔加工基面,因此应先精加工内孔,然后以内孔为基面加工外圆及支承轴颈,螺纹的加工同样以内孔为基面,因此需要心轴。
一般精密分度蜗杆的内孔精度要求是很高的,有的需要进行研磨老保证精度。
一般精度分度蜗杆内孔应不低于1级精度,表面粗糙度不低于0.12,内孔的端面振摆应不小于0.005mm。
蜗杆装在心轴上加工时,应首先检查两端轴肩的径向跳动是否在规定允差之内,以后每道工序均应校验,在蜗杆装配时,同样要校验两端轴肩的径向跳动,心轴精度必须等于或高于与套装蜗杆相配的轴精度。
整体蜗杆以中心孔为加工基面,对中心孔的要求很高,应该有保锥,保证光洁度和接触面积,每道工序前要检查和修正中心孔,对支承轴颈应保证与中心孔同轴度和本身的几何精度,在半精加工和精加工工序前,都应检查支承轴颈的径向,跳径和端面的轴向振摆是否在公差以内。
选择粗基准时,考虑的重点是如何保证各加工面有足够的余量,使不加工基面与加工表面间的尺寸,位子符合图纸要求。
粗基准选择应当满足以下要求:
⑴粗基准的选择应以加工表面为粗基准。
这是为了保证加工面与不加工面的相互位置关系精度,如果工件上表面上有好几个不需要加工的表面,则应选择其中与加工表面的相互位置精度要求较高的表面作为粗基准。
以求壁厚均匀,外形对称,少装夹等。
⑵选择加工余量要求均匀的重要表面作为粗基准。
⑶应选择加工余量最小的表面作为粗基准。
这样可以保证该表面有足够的加工余量。
⑷应尽可能选择平整,光洁,面积足够大的表面作为粗精准,以保证定位准确夹紧可靠。
有浇口,冒口,飞边,毛刺的表面不宜选作粗基准,必要时需经初加工。
⑸粗基准应避免重复使用,因为粗基准的表面大多数是粗糙不规则的,多次使用难以保证外表面间的位置精度。
按照粗基准的选择原则,夹住外圆在一次装夹中把大部分表面加工出来,能保证外圆与内孔同轴度以及端面与轴线的垂直度。
蜗杆加工工艺路线
⑴不淬硬套装蜗杆
备料——正火——粗车——(调制)——半精车外圆,粗车螺旋面——人工时效——精车(精磨)内孔端面——插键槽——半精车螺旋面——钳(休整不完全齿)——半精磨外圆——精磨螺旋面——低温时效——研中心孔——精磨外圆——精磨螺旋面
⑵渗碳淬火整体蜗杆
锻造——退火——粗车——正火——半精车外圆及螺旋面——钳(休整不完全齿)——渗碳——精车外圆(去不需渗碳部分)——淬火回火——研磨中心孔——车紧固螺纹——铣槽——半精磨外圆——半精磨螺旋面——低温时效——研磨中心孔——精磨外圈及端面——精磨螺旋面
下料:按正规定要求坯料要经过锻打处理,为获取良好的金属纤维状。
粗车:要保证同轴度,留适当的精加工量。
热处理调质处理HRC28-32、半精车,各部半精车留0.5mm的精车量,车蜗杆部分及两端退刀槽车至要求,挑蜗杆、粗挑,不论用分层法切入法等都可。
在中经处测量留量,半精挑留量为精光留好较好的基础。
低速精光三面至要求,刀具一定要锋利,刃口粗糙度一定要好,一面一面的光。
精车各部至要求保证同轴度。
普通圆柱蜗杆若用直线切削刃在车床上加工,按刀具安装位置不同,切出的蜗杆又可分为阿基米德蜗杆(ZA)、渐开线蜗杆(ZI)和法向直廓蜗杆(ZN)等。
ZA阿基米德蜗杆车刀刀刃平面通过蜗杆轴线,车刀切削刃夹角2α=40°切出的蜗杆,在轴平面上具有直线齿廓,法向剖面齿廓为外凸曲线。
而端面上的齿廓曲线为阿基米德螺旋线,故称为阿基米德蜗杆。
这种蜗杆加工和测量都比较方便,故应用广泛。
但导程角γ过大时加工困难。
难以用砂轮磨削出精确齿形,故传动精度和传动效率较低。
ZI渐开线蜗杆车刀切削刃平面与蜗杆的基圆柱相切,被切出的蜗杆在轴平面上具有凸廓曲线,而在垂直于轴线的端面上的齿廓为渐开线,故称为渐开线蜗杆。
这种蜗杆可以磨削,故传动精度和传动效率较高,适用于成批生产和大功率、高速精密传动。
ZN法向直廓蜗杆当蜗杆导程角γ较大时,为了使车刀获得合理的前角和后角,车制时车刀刀刃平面放在蜗杆螺旋线的法平面上,这样切出的蜗杆,在法向剖面上齿廓为直线,故称为法向直廓蜗杆。
而在垂直于轴线的端面上的齿廓曲线为延伸渐开线,因而又称为延伸渐开线蜗杆。
这种蜗杆切削性能较好,有利于加工多头蜗杆,且可用砂轮磨齿,常用于机床的多头精密蜗杆传动。
随着技术和产品要求的进步,需要切削速度进一步提高,车削法产生了瓶颈,于是出现了旋风铣。
即用旋转的刀具来提高切削线速度(可达每分钟400米),工件则无须高速旋转。
蜗杆的旋风铣加工方法分两种,内旋风whirling和外旋风milling。
内旋风:工件圆周与刀牙圆周内切(蜗杆在刀盘内部)精度可达DIN7 Ra0.8
外旋风:工件圆周与刀牙圆周外切(蜗杆在刀盘外部)精度可达DIN6 Ra0.4
内容来源网络,由“深圳机械展(11万㎡,1100多家展商,超10万观众)”收集整理!更多cnc加工中心、车铣磨钻床、线切割、数控刀具工具、工业机器人、非标自动化、数字化无人工厂、精密测量、3D打印、激光切割、钣金冲压折弯、精密零件加工等展示,就在深圳机械展.。