1射出成型机简介解析
射出成型制程简介

剪切率分佈
(a)典型流體的流動狀況 (b)射出成型時融熔塑膠的剪切率分佈狀況
溫度與壓力對黏度的影響
壓力流 Pressure - Driven Flow
壓力流
壓力梯度與融膠速度的關係
射出成型製程簡介
射出成型製程簡介
射出成型機及操作 塑膠成型製程物理
射出成型機系統
鎖模系統
模具系統
充填系統
液壓系統
控制系統
射出成型機規格
一般而言,射出成型機規格指定以鎖模噸 數(Clamping tonnage) 及射料量(shot size)兩者為主。
其他的參數,還包括了射出速率(injection rate),射出壓力( injection pressure), 螺桿規格( screw design),最大模厚 ( mold thickness),以及柱間距( the distance between tie bars )。
射出成型機的液壓系統提供了開閉模,鎖模系 統,螺桿轉動,模具頂出等系統的動力來源。 液壓系統包括了幫浦,油閥,液壓馬達,液壓 配合件,液壓渦輪,以及 油槽等。.
The hydraulic system on the injection molding machine provides the power to open and close the mold, build and hold the clamping tonnage, turn the reciprocating screw, drive the reciprocating screw, and enes. A number of hydraulic components are required to provide this power, which include pumps, valves, hydraulic motors, hydraulic fittings, hydraulic tubing, and hydraulic reservoirs.
塑胶射出成型

收缩下陷 收缩下陷是成型品表面呈现凹陷的现象,主要原因是 熔融材料冷却固化时的体积收缩所致。收缩下陷易发生 于成型品肉厚较厚部位、肋、凸毂的背面、注道的背面 等肉不均的部份。因此为了防止收缩下陷,基本上,成 型品的设计要适切。 收缩下陷是成型品收缩所致,易见于PE、PP、PA等 成型收缩率大于结晶性塑料材料。反之,以玻璃纤维强 化的塑料或充填无机质的塑料材料之成型收缩率甚少, 故其收缩下陷可减至最小。
19
流痕 流痕是熔融材料流动的痕迹,以浇口为中心而呈现的 条纹模样。 流痕是最初流入成型空间(模穴)内的材料冷却过快,而 与其后流入的材料间形成界线所致。
银白纹 银条是在成型品表面或表面附近,沿材料流动方向, 呈现的银白色条纹。
20
烧焦 一般所谓的烧焦,包括成型品表面因材料遇热所致的 变色及成型品的锐角部位或谷部、肋的前端等材料焦黑 的现象。 烧焦是滞留在模穴内的空气,在熔融材料进入时未能 迅速排出,被压缩而显著升温,再将材料烧焦所致。 黑条 黑条是在成型品上有黑色条纹的现象,其发生的原因是 成型材料的热分解所致;常见于热安定性不良的材料。 有效防止黑条发生的对策是防止加热缸内的材料温度过 高,减慢射出速度
13
毛边 熔融材料流入分模面或侧向滑板活动间隙时,会发生毛 边。 发生毛边的原因,基本上除了射出机对成型品的投影 面积无充分的合模(锁模)力之外,大都是模具与成型材料 所致。模具配件发生间隙或配件密着性不良的原因,是模 具设计制作不当或模具配件变形及磨损。模穴的熔融材料 流动性太好时,也会造成毛边,防止的方法是降低模具温 度、材料温度、射出压力及射出速度,但必须配合前项充 填不足问题,否则可能造成解决毛边问题而造成充填不足 的现象发生。
翘曲、扭曲 翘曲、弯曲都是从模具取出的成型品产生之变形,平 行边变形者称为翘曲。对角线方向的变形称为扭曲。 这些变形为成型时的各种内应力所致,原因大别如下: (1)脱摸时的内部应力所致。 (2)模具温度控制不充分或不均匀所致。 (3)材料或填充料的流动配向所致。 (4)成型条件不适当所致。 (5)成型品形状,肉厚等所致。
射出成型简介

射出成型简介1 射出成形之基本知识。
1.1 射出成形的特征以及组成。
射出成形是将溶融的成形材料以高压的方式填充到封闭的模具内,射出成形的模腔内承受的压力约400KGF/CM2,大约为400个大气压,以这样高的压力来制作产品是它的特征,这是它的优点也是它的缺点。
也就是说模具必须制作得相当坚固,因而模具价格也相当昂贵,因此必须大量生产以便与高价的模具费用互相扣抵,例如每批之生产量必须10000PCS以上才合理,换句话说;射出成形的工作必须以大量生产才行。
成型过程所说几个步骤:1.1.1关门安全门上才开始成型。
1.1.2 锁模将移动侧的移动板前进,使得模具关闭,模具关闭以后确实地把模具锁紧。
1.1.3 射出(包括保压)螺杆快速地往前推进,把熔融之成形材料注入模腔内填充成形,填充之后压力要必须继续保持,这个动作特别取名为“保压”。
在刚充填时模具承受的压力,一般叫做射出压或者叫做“一次压”。
1.1.4 冷却(以及下个动作的可塑化工程)模腔内之成形材料等待冷却凝固之过程叫“冷却”。
在这时候射出装置也准备下次工作,这个过程叫做“可塑化过程”。
放在料斗里的成形材料,流入加热的料管内加热,是依据螺杆旋转把原料变成熔融状态,螺杆像拨取螺丝的原理一样,一面转一面后退,螺杆前端会储存熔融之成形材料,螺杆旋转时,抵抗螺杆向后退的压力称之为螺杆的“背压”。
1.1.5 打开模具将移动侧的移动板向后退,模具跟着打开。
1.1.6 打开安全门安全门打开,这时成形机处于待机中之状能。
1.1.7 取件将成品取出,然后检视确认模具内未残留任何对象再关门.以上整个成形作业叫做一个CYCLE成型。
成品是由模具的形状成形出来。
模具是由母模及公模块合成,公母模模仁之间留有空隙,材料在此流入压缩形成产品。
成型材料要流入公母模之前的通路有主流道(SPRUE)流道(RUNNER)闸门(GATE)等。
1.2 射出成形机射出成形机以较大项目来区分,可分为两项,锁模装置和射出装置。
射出机介绍

18
六.射出機規格表
t ¨ Î ² O § µ ¶ Ø ¥ ê Â Ò ¼ O ¤ unit ³ Á Û ± ì ± ½ ª | ® mm ù ¬  û ® g ¥ X À £ ¤ O kg/cm2 | ¬ ¥ û ® g ¥ X À £ ¤ O kg/cm2 z ½ ² × ® g ¥ X ® e ¿ n cm3 g g ® X ¥ « q ¶ oz ù  û ¬ g ® X ¥ v ² cm3/sec | ¬ ¥ û ® g ¥ X ² v cm3/sec i ¶ ¥ ì ¤ Æ ¯ à ¤ O kg/hr ³ ± Á Û ± ì ° j Â à ¼ Æ rpm } ¼ ¶ Ò ¦ æ µ { mm W ¤ ¬ º ¶ ¡ ¹ j (H*V) mm Ò ª ¼ O ¤ Ø o ¤ mm Ò « ¼ p d ½ ³ ò mm o £ ª À ¦ « ¼ Ò ¦ æ µ { mm ¹ ® q ð ° ¨ ¹ F (À ° ® ú ) hp q ¼ ¹ ö ® e ¶ q kw ° ® À ú ³ Ì ° ª ¨ Ï ¥ Î À £ ¤ O kg/cm2 ÷ ± ¾ ñ ¤ Ø ¤ o m ÷ ± ¾ ñ « ¶ q ton Ë ½ ¸ c ¤ Ø ¤ o m Ë ½ ¸ c « ¶ q ton HC-250 250
要研究成形技術及其管理,如不能對所謂成形三要素的--原科、成 形及模具加以一番的探討,必難一登殿堂 15
五.射出工程條件控制
影響射出成型品質的射出工程可分為3階段 A.填充:將原料射出/擠壓到模穴內,將之填充。 B.保壓:為彌補模穴內原料冷卻固化(反應固化)所 導致的體積收縮,而保持的壓力。
C.冷卻:模穴內原料進一步冷卻,固化到成型工 件可從模具內取出。
(新)射出成型简介_

射出成型简介1 射出成形之基本知识。
1.1 射出成形的特征以及组成。
射出成形是将溶融的成形材料以高压的方式填充到封闭的模具内,射出成形的模腔内承受的压力约400KGF/CM2,大约为400个大气压,以这样高的压力来制作产品是它的特征,这是它的优点也是它的缺点。
也就是说模具必须制作得相当坚固,因而模具价格也相当昂贵,因此必须大量生产以便与高价的模具费用互相扣抵,例如每批之生产量必须10000PCS以上才合理,换句话说;射出成形的工作必须以大量生产才行。
成型过程所说几个步骤:1.1.1关门安全门上才开始成型。
1.1.2 锁模将移动侧的移动板前进,使得模具关闭,模具关闭以后确实地把模具锁紧。
1.1.3 射出(包括保压)螺杆快速地往前推进,把熔融之成形材料注入模腔内填充成形,填充之后压力要必须继续保持,这个动作特别取名为“保压”。
在刚充填时模具承受的压力,一般叫做射出压或者叫做“一次压”。
1.1.4 冷却(以及下个动作的可塑化工程)模腔内之成形材料等待冷却凝固之过程叫“冷却”。
在这时候射出装置也准备下次工作,这个过程叫做“可塑化过程”。
放在料斗里的成形材料,流入加热的料管内加热,是依据螺杆旋转把原料变成熔融状态,螺杆像拨取螺丝的原理一样,一面转一面后退,螺杆前端会储存熔融之成形材料,螺杆旋转时,抵抗螺杆向后退的压力称之为螺杆的“背压”。
1.1.5 打开模具将移动侧的移动板向后退,模具跟着打开。
1.1.6 打开安全门安全门打开,这时成形机处于待机中之状能。
1.1.7 取件将成品取出,然后检视确认模具内未残留任何对象再关门.以上整个成形作业叫做一个CYCLE成型。
成品是由模具的形状成形出来。
模具是由母模及公模块合成,公母模模仁之间留有空隙,材料在此流入压缩形成产品。
成型材料要流入公母模之前的通路有主流道(SPRUE)流道(RUNNER)闸门(GATE)等。
1.2 射出成形机射出成形机以较大项目来区分,可分为两项,锁模装置和射出装置。
成型射出的原理
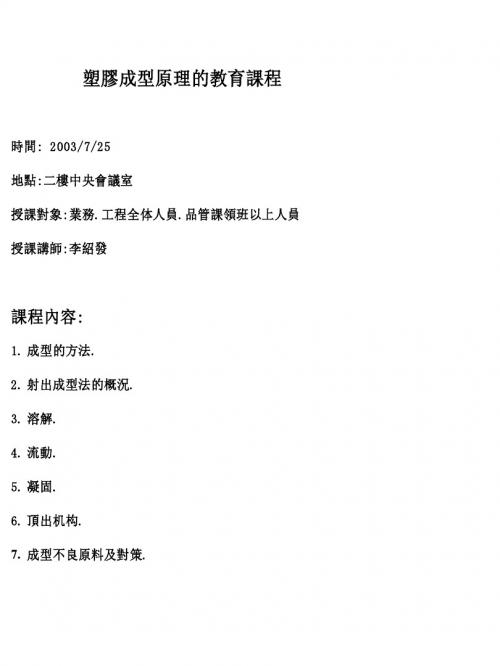
別是透明制品.避免頂出時,產生破裂變形.与脫模板不同的是,不需加多一塊脫模板,直接在公模上鑲一 頂出塊.如 0133 飾板 6. 斜頂. 适用于產品上有卡鉤位,在頂出時,需有一個位移,才不至于使卡鉤拉斷. 7. 中子. 适用于模具結构中有滑塊.或抽芯動作時,其基本原理是關模后,中子進.中子退后.才能開模. 七. 成型不良原因及對策: 1. 短射(填充不足) a. 流動性不良,材質本身流動性不好.溶融塑膠,在尚未流到模具未端已開始產生固化,必然產生填 充不足; 相應對策:增加樹脂的流動性.即提高加熱溫度,或增加背壓.提高模溫,加快射出速度. b. 排气不良,樹脂射入模腔內,會壓縮模腔內的空气,并擠壓至角落.特別是薄肉壁部份和長而深的 击緣未端.這時若提高射速,提高溫度會產生黑線條紋或燒焦.所以根本的對策是改善模具結构. 加排气,使空气逸出. 2. 毛邊: a. 鎖模力不足.由于射出壓力太大,超過設定的鎖模力,將模具可動部分向外頂出,則在合模面上產 生非常小的間隙,成形時在此結合面上產生毛邊.相應對策是提高鎖模力,降低射出壓力. b. 模具密合不良,變形.模具在合模面上密合不良,或者模板本身厚度不足,在射出高壓下,產生變形 而產生毛邊.通常是重新飛模.增強密合度.降低壓力.減少模板變形.若因模具本身設計,結构和老 化的原因.變更成型參數是無法改變的. 3. 縮水 a. 收縮不足,与成型品的肉厚或容積比較起來,如果主澆道,分澆道.進膠口太細小時,注入模腔的樹 脂,很難維持充足的射出壓力,而無法達到保壓的目的.造成增大成型的收縮率.縮水缺陷也隨之 增加.特別是在採用針點澆口,側面澆口,潛入澆口等限制形澆口的情況下,即使延長保壓時間,由 于澆口本身容易固化,模腔內無法保持這個射出壓力,于是產生收縮缺陷.這就是平時稱為:保壓 不足” 對策上:一是提高射出壓力,并降低加熱溫度;二是維持十足的保壓,如果還是無法克服或減輕收 縮缺陷.則只好加大主澆道和進澆口的口徑子. b. 冷即不均.因厚肉部份處冷卻速度將此薄肉部份慢而產生收縮凹陷現象.此缺陷主要是肋骨厚度 不能超過肉厚的 1/2.如果是 BOSS 柱在模面上應設偷膠處.俗稱火山口. 4. 翹曲.扭曲.變形. 射出成型時,在塑流的方向上与其直交方向上的成型收縮率并不相同.在塑流方向上,其收縮率較大, 并与肉厚不同而相异.這种收縮率之差异必然是造成成形品變形的潛在原因.因成形收縮完了后,射出
射出成型的介绍(一)

一、射出成型机的认识介绍
第一章
一、射出成型的特征: 射出成型是把成型材料以主压方式充填到模具腔内,射出
成型的模具腔内承受之压力约400KG.F/CM2大约为400个大气压。 以这样高的压力来制作产品,是射出成型的特征,这是它
的优点,也是它的缺点,也就是部模具必须制作得相当坚固,困而 模具价格也相当昂贵,因此必须多量生产,以便于高价之模具费用, 互相扣抵,换句话说,射出成型之工作,必须大量生产才行。 二、射出成型的过程(一个CYCLE循环)
OFF,ON—OFF……7~8次,听到马达转换为Y之声音后,启动马达之动作,便完成。 12、启动后,让PUMP(泵)空转约3~5分钟后再浪各油路动作。 13、启动后,马达的声需费1小时的时间),成型机才能达
到安定的状态,生产出来的产品品质才会稳定。
整个射出成型的循环中时间内容可分为三大部分: 1、射出时间 2、静止时间 3、开关模时间
第二章 一、塑胶射出成型机的分类:
1、依射出量来区分 2、依锁模力来区分 3、依锁模方式来区分 二、塑胶射出成型机旬部的构造分为: 1、锁模装置单元 2、射出装置单元 3、机座装置单元 三、塑胶射出成型机各部位名称及功能:
1、操作控制箱 功能:是各种开启开关及操作开关。如:装模手动、半自动、全自动、顶
出、射出座前、退油压中子,等开关。 2、成型条件调整控制盘 功能:是调整压力、速度行程、料量、时间等射出成型条件。 3、侦(监)测器 功能:可以由侦监测器查出机器的异常点及高定时间功能。 4、温度高定控制器 功能:是调整料管温度,控制料管温度、各段料管温度、灌嘴(NOZZLE)
温度分开单独设定,调整、控制。
5、锁模单元: 功能: 将模具关闭、打开的作用。 6、顶出油压单元 功能: 系模具打开后,将产品由模具内顶出来,以利人手去取拿,或自行落下,
注塑培训射出成型机於高分子加工简介.ppt

經換算為射出時間最好在1秒以內。
EX: D=40mm, L=0.6*S=2.4D=96mm, t=1sec,
螺桿速度多段控制的影響—波前速度
螺桿等速度
螺桿速度多段控制
滯流區
螺桿速度多段控制的影響—壓力
螺桿等速度(87.8MPa) 螺桿速度多段控制(57.9MPa)
充填速度適當的調控,將可有效降低射出壓力
螺桿速度多段控制的影響—合模力
88ton
62ton
螺桿等速度
螺桿速度多段控制
充填速度適當的調控,將可有效降低合模力
(2)合模裝置的構造區主要區分為肘節式及直壓式
頂出機構
二、射出成形步驟原理
加熱熔化 加壓流動 壓縮及續壓
塑料
熔膠
成形
冷卻固化 開模頂出 成品
螺桿轉速 料缸溫度 噴嘴溫度 螺桿背壓
充填速度 充填壓力上限 充填時間 進料位置、 充填/保壓轉換位置 殘留量 保壓壓力(二段壓) 保壓時間
模具溫度 冷卻時間 開關模速度 頂出速度 頂出量
各塑膠ρ值、μ值
塑膠名稱 PS PE PP ABS AS
NYLON PC
PMMA H.PVC NORYL PBT POM
ρ值 0.98 0.73 0.75 0.92 0.99 1.01 1.06 1.06 1.00 0.9 1.02 1.17
μ值 92% 95% 95% 88% 90% 90% 85% 86% 83% 85% 90% 88%
发那科注塑机全资料

1. 射出成型机射出成型机是将塑料原料在熔解的状态下高压射入模具,待塑料冷却凝固后再打开模具,将成型品取出的机器。
为了追求塑料制品的高精度、高效率的大量生,目前,以轻薄短小见长的射出成型机在射出成型工业中已逐渐流行起来。
以下,就上述特点和应用围展开论述。
1. 1 全电气式射出成型机的特征1.考虑经济实用的合理设计.低价格:全电气式射出成型机通过软件的改造,能够进行复杂的控制。
.节约能源:运转费用低,与油压机相比,其电力消耗仅占1/3。
.高功能:该机拥有强大的人工智能。
.高信赖性:其控制装置具有很高的可信度,机械构造具有高刚性的特点。
.无污染:无噪音,不使用机油。
2.使用AC伺服马达(数字控制)AC 伺服马达能够精确设定ROBOSHOT 的各轴的速度和位置。
速度控制的最小单位为0.1mm/s,位置控制的最小单位0.01mm。
[用AC伺服马达的控制轴总共有4根轴]:1. 射出轴2. 螺杆回转轴3. 锁模轴4. 顶出轴[使用齿轮马达的控制轴总共有2根轴]:1. 射出座(喷嘴接触)2.模具厚度的调整[成型塑料]塑料可分为热塑性树脂和热固性树脂。
同时,热塑性树脂又可分为结晶性树脂和非结晶性树脂。
使用塑料原料时一定要很好了解树脂生厂家的树脂特性。
1.热塑性树脂:加热以后软化流动,将其冷却后又固化,再次加热又熔化为原来的状态,好象蜡一样,温度一高就熔化,冷却后又恢复还原成原有的状态。
2.热固性树脂:加热以后软化流动,在一定的温度下固化。
它跟鸡蛋一样,在一定的温度下硬化,而再次加热后却不会再软化熔融。
该树脂在加工成制品后失去了成型性,因而不能再生。
[塑料原料的主要用途和种类]1.精密成型品:照相机镜头,精密接插件,CD,精密齿轮,其他。
2.一般成型品:接插件,电子零部件,照相机外壳,家用电器部件及其它。
3.杂物成型品:废纸篓,塑料杯等日常用品,塑料模特儿,其他。
1.聚苯乙烯(PS):非常通用的透明树脂。
用于盒式日常用品。
射出成型机操作知识
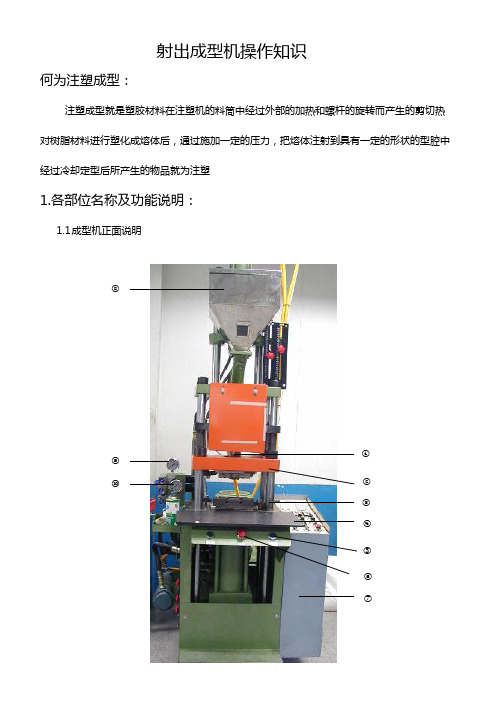
射出成型机操作知识何为注塑成型:注塑成型就是塑胶材料在注塑机的料筒中经过外部的加热和螺杆的旋转而产生的剪切热对树脂材料进行塑化成熔体后,通过施加一定的压力,把熔体注射到具有一定的形状的型腔中经过冷却定型后所产生的物品就为注塑1.各部位名称及功能说明:1.1成型机正面说明料管 上模板●立柱❍工作台⏹自动☐紧急回升☐电箱❑料斗❒油压表♦压力表1.2电控板说明:a.成型计数b.料嘴温度c.射退计时d.松退计时e.电热开关f.开模/关模 g.手动/自动 h.马达激活 i.马达停止 j. 射退/射出k.洗料/螺旋 l.顶针使用 m.松退使用 n.顶针开关 o.电源开关p.冷却计时 q.上节温度表2.模具安装:2.1打开电源,电热开关,调整内模或外模在作业规范中所设定的温度。
2.2待达升至所设定的温度后,按动马达,将总压力调至用手动能开模,关模为合适。
2.3把模具放至机台,用手动关模,射料,检查机器料管射料口是否对正模具进料口。
2.4手动关模,锁紧上下模板。
2.5装模完成。
2.6待机器调整程序完成后方可自动作业。
注意:在安装模具时要特别注意安全,非熟练装模人员或技术人员不得擅自安装。
3.调整机器3.1模具装好后,不能立即转自动操作,须调整机器的各个控制动作开关。
3.2调整总压,一次压,二次压设定适当的压力。
3.3调整开模慢速控制轮,强力锁模控制轮,开模停止控制轮。
特别注意,开模慢速控制一定要调至适当的位置,如关模无慢速,自动操作时易把模具压裂。
3.4根据内、外模穴的大小,调整加料停止控制轮与射二次压控制轮。
3.5调整射出速度与背压至合适为止。
3.6以上工序完成后,进入操作阶段。
注意:调整机器由专业技术人员调整,其它不熟练的人员不得自行调整,操作员若发现有不良现象立即停机,请专业人员调整之。
4.操作方法:4.1将手动/自动开关转为手动,开始旋料(加料)至自动停止为止。
4.2再把开关转为自动,进行试模。
4.3试机二,三模后,准备作业。
射出成形基础(1)

塑料的流动黏度
有一个理论说塑料的黏度决定 于分子链的纠缠程度,纠缠的 程度越少,黏度就越低,反之 亦然;而塑料本身的分子量大 小,分子结构以及外在的加工 温度,流动切断力(使分子链 配向)和受压缩的程度等都会 影响它的纠缠,此既影响塑料 黏度之因素。
充填三阶段: 1.射出相→熔融的塑料 被快速射入模腔,刚
是自注道至成形品之通路,通常设在合模线两侧,浇道的剖面通常是圆形。多模 穴模具的成形品与浇道配置很重要,应使流进各模穴的成形材料同步而均匀。
冷料井(cold slug well)
射出成形机的喷嘴前端在射出后仍有少量熔融材料残留,此残留材料在下次射 出前凝固,若直接进入成形品中会造成制品外观不良,为了防止如此设计冷料井, 使射出 材料前端的凝块积滞此处。
射出成形之重点
工 流 重 点 §心层不会立即冷却,模具的每一角落都有高压力。 射出 §需要保压,成形品的尺寸和凹塌决定于这时段。 后期 §射出压、保压是关键(瞬间施高压,立即降压保 (填充 持)。 及 §模具温度很重要(应高一点)。 保压) §模具内树脂压力的实际变化很重要(需测定)。 §为使心层冷却固化,要冷却模具。 冷 §对模具高速循环冷却水。 §关键是冷却水、速度、温度。 却 §模具温度偏差应尽量少(需测定)。 §由树脂来的热移动很重要。 程
7
开关模
5
向后松退,避免塑料从喷嘴漏出。 塑件冷却定形,同时注射螺杆完成射料
6
6 冷却时间
准备。
滑动模板后退,两半边模打开。退件机 构将塑件顶出。
5 4
7
清除塑件,喷脱模剂,安装嵌件、插针
等。模具重新闭合,下一循环开始。
8
结晶性材料 成型收缩率 较大 。
非结晶性材 料成型收缩 率较小。
射出成形工艺简介

射出成形机 ——射出成形的主要控制参数
4/4Байду номын сангаас
7、射出和保压压力 射出压力的上限是射出机的容量、锁模力和模具的结构。通常,射出压力和 保压压力设定为不会造成短射的最低压力。射出压力和保压压力应该足够高, 维持足够久,以便在塑件的收缩阶段继续填注塑料,将收缩量最小化。然而, 太高的射出压力会造成塑件潜在的应力。两段式加压可以应用在一些制程,第 一阶段的高压进行充填,第二段则以较低压力进行保压。 8、保压时间 完成充填模穴后,射出机仍然施加压力在模具的时间称为保压时间,保压的 目的在维持组件的尺寸精度。 9、剩余冷却时间 解除压力到开模之间的时间称为剩余冷却时间,目的是让塑件足够硬化以便 顶出。假如在塑件尚未完全冷却硬化之前就顶出,会造成塑件翘曲变形。 10、开模时间(mold-opening time,也称为dead time) 开模时间包括打开模具、顶出塑件和关闭模具的时间。开模时间和射出机之 操作效率、成品取出的难易度、使用脱模剂与否都有关系,以人工安置镶埋件 (insert)的模具会更降低操作效率。在射出机运转过程维持最少的人力介入是 开模时间最佳化的方向。
锁模系统
射出成形机 ——塑料射出成形过程
塑料射出成形加工是一种适合高速量产精密组件的加工法,它将粒状塑料于 料筒内融化、混合、移动,再于模穴内流动、充填、凝固。其动作可以区分为 塑料之塑化、充填、保压、冷却、顶出等阶段的循环制程。 塑料射出成形的基本操作动作如下: 1、关闭模具,以便螺杆开始向前推进
进料区
压缩区 计量区
螺杆
料筒
射出成形机 ——射出系统
4/4
4、喷嘴 喷嘴连接料筒和竖浇道衬套(sprue bushing)。当料筒移到最前端的成形位 置,其喷嘴外径必须包覆在竖浇道定位环内,构成密封。喷嘴的温度应该 设定在材料供货商建议之塑料熔化温度,或是略低于温度。如此,清理料筒 时,只要将料筒后退远离竖浇道,清除的塑料可以从喷嘴自由落下。
射出成型介绍

固化
模具传导热的作用,将树脂冷却付型 固化过程中,热收缩和结晶收缩同时进行 冷却不均,收缩时间不同,储存残余应力
注射成型知识
成型品各部位名称及作用
成品
分流道
进胶口闸门主流道Fra bibliotek冷料井
副流道
进胶方式
薄膜进胶
扇形进胶
进胶方式
潜伏进胶
牛角进胶
进胶方式
针点进胶
搭接进胶
进胶方式
直接进胶
侧边进胶
何谓成型工艺
锁模力
就是 阻止模腔内熔融树脂的压力将模具撑开
成型品末端压力 合模压力
流道压力
模具
螺杆 注射压力
射嘴压力(压力降)
温
料管温度 1.电加热 2.摩擦热 3.剪切热 4.压缩热
度
模具温度 1.传导热 2.对流热 3.辐射热 4.循环热
注射速度
注射速度就是螺杆前进的速度。同注射压力 都是成型条件中重要项目之一
塑胶的分类
物理性质
一般塑胶 工程塑胶
高工程塑胶
化学性质
热塑性塑胶
热固性塑胶
结晶性塑胶 非结晶性塑胶
注塑的原理
将熔融的原料以高压的方式快速充填到模腔 内经过冷却固化后得到所需要的成型品。
构成优良成型品主要因素
模具(60%)
注塑工艺(20%)
成型机(15%) 其他(5%)
成型过程
高压锁模 保压 加料计量
光泽度不均
成品表面亮度或颜色不均匀
对策:
调整料温 提高模温 清洗料管 提高背压 模具抛光
拉伤
成品分模线或滑块合模出处出现损伤
对策:
降低射出压力速度 加大脱模角 改善模具开启方式 改善顶出方式 模具加强抛光 避免成品取出使碰伤
射出成形机概说(中日双语+图示)
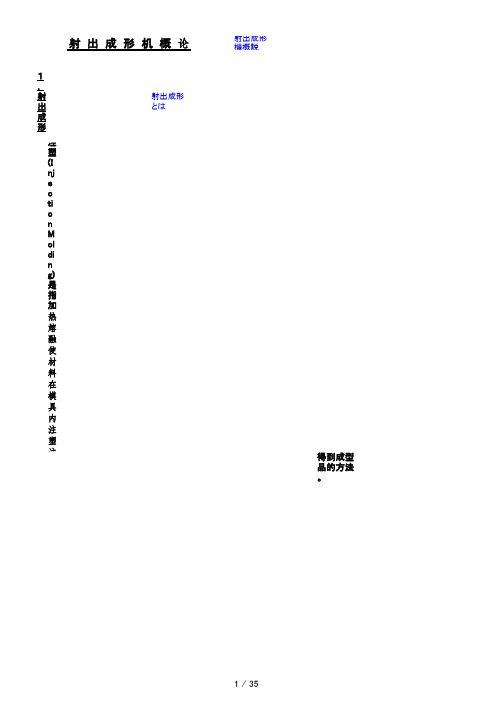
射出成形機概説1.射出成形射出成形とは注塑(Injection Molding)是指加热熔融使材料在模具内注塑注入,经过冷却,固话得到成型品的方法。
射出成形(Injection Molding)とは、加熱溶融させた材料を金型内に射出注入し、冷却・固化させることによって、成形品を得る方法です。
适合复杂形状的产品大量生产成形加工的一大块领域複雑な形状の製品を大量に生産するのに適し、成形加工の一大分野なしています。
注塑工艺大致分为,6个射出成形の工程は大きく分けて、6つあります。
1)合模型締め2)射出射出3)保压保圧4)冷却冷却5)开模型開き6)产品取出製品取り出し用这个顺序进行,周期的循环反复,连续生产产品。
この順序で行なわれ、このサイクルの繰り返しで、製品を連続的に生産します。
2.射出成形机射出成形機射出成形机是由合模单元和射出单元分成射出成形機は型締めユニットと射出ユニットに分かれています。
合模机体开关模具,突出(喷射器)进行型締めユニットは金型の開閉、製品の突き出し(ejector)を行います。
有使用液压缸直接开关模具的"直接式"和有使用联动装置进行开关的,开关"Toggle 式"的种类有2种。
油圧シリンダーで直接金型を開閉する『直接式』とリンク機構を使用して開閉する『トグル(Toggle)式』の2種類があります。
射出机体是让树脂加热熔融,在模具内注射射出ユニットは樹脂を加熱溶融させ、金型内へ射出します。
使螺杆旋转,从加料斗投入树脂,会在螺杆前部积存スクリューを回転させ、ホッパーから投入した樹脂をスクリュー前部へ溜めます。
必要的树脂量里相当的行程蓄力后(叫做计量)射出。
必要な樹脂量に相当するストロークを溜めた後(計量と呼びます)、射出します。
树脂在模具内流动的时候,控制螺杆的移动速度(射出速度)。
樹脂が金型内を流動している時は、スクリューの移動速度(射出速度)を制御します。
1射出成型机简介
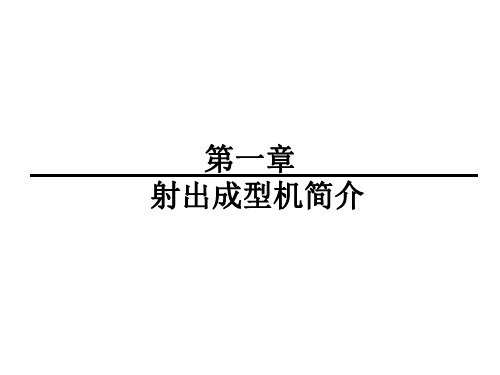
加热缸与喷嘴
(1)加热缸内装螺杆,外围由数组带式加热器直接将内部材料加热。 带式加热器一般分为3~4组,各组有独立的温控,并藉热电偶保 持适合的温度设定 (2)喷嘴是连接模具与加热缸的接合部,通常喷嘴部份也装置独立的 带式加热器;直接控制射出材料的熔融温度,必要时也附加各种装 置用以遮断熔融材料的流动,以防止熔融材料在开模或机座后退 时从加热缸泄漏,如针阀喷嘴及闭锁喷嘴 (3)喷嘴的球状外轮廓的曲率半径(欧规10,15,20,35mm)需小于模具 入口的曲率半径,喷嘴出口半径应小于模具的入口半径 (4)喷嘴可分开口式喷嘴及遮闭式喷嘴,下图为针状遮闭式喷嘴,因 弹簧作用而封闭,可避免漏料,射出时当射压高过弹簧作用力时 即开启,熔胶通过喷嘴射入模穴
直式
肘節直壓式
顶出机构
机械式顶出装置,如下图所示,在合模滑块与可动 盘的接合部之空间部份设置有数支顶出杆,藉顶出杆的 动作,使模具的顶出板前进而将成形品顶出。
射出成形的循环周期
(1)螺杆旋转将塑料输入料缸,并加热塑化。 (2)可动侧模盘前进将模具闭合。 (3)螺杆前进将熔胶射入模穴直至填满。 (4)进行压缩使模穴内的熔胶密度升高,避免冷却收缩。 (5)持续续压动作,直到浇口处不发生流动。 (6)模穴继续进行冷却,螺杆旋转进行下一周期之进料塑化 动作,并逐渐后退至进料行程设定位置为止。 (7)模穴继续进行冷却直到冷却时间结束。 (8)可动侧模盘后退将模具打开。 (9)顶出机构前进将成品顶出。 (10)取出成品,进行必要动作如喷脱模济、安置内插物等。 再重新执行步骤(1)。
2.1:1
2.2:1 2.4:1 2.5:1 2.5:1 3:1(max)
0.15
0.15 0.2 0.2 0.25 0.25 最大表面粗糙度2~4μm 2. R2=5mm(直径30~60mm) R2=10mm(直 径 约 牙部宽度0.1D 7. 最大进料行程4D
射出成型机结构
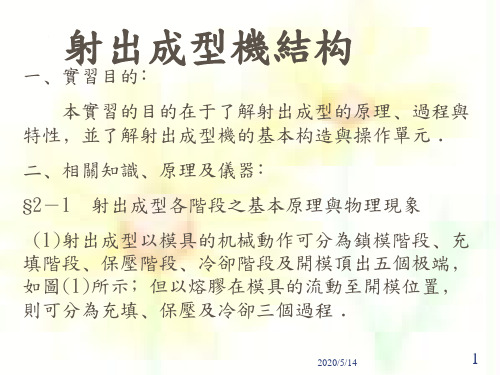
17
直壓式合模裝置又可分為升壓滑塊式、輔助缸式及增壓缸式‧
2016/11/3
18
2. 肘節式鎖模裝置 肘節式合模裝置是以肘節接頭將油壓缸或電動機產生 的力放大,使合模力增大‧在肘節機構中,力的放大 率與速度因連桿位置而大有變化,在閉模的最初階段, 力的放大率小而速度快,接進閉模行程終了時,力的 放大率大而速度慢‧在肘節連接桿將進完全伸直前產 生很大的鎖模力‧
2016/11/3
5
同理靠近模穴處溫度較低而肉厚中央熔膠仍 然保持高溫,优勢由于黏度生熱(Viscous Heating) 的效應(與射速有關)在較近模穴的地方會產生高 溫,這種現象在澆口尤其顯著.由于熔膠是非牛頓 流体,黏度呈現剪薄(Shear Thinning)效應隨著溫 度﹑剪切率而改變﹐因此在充填過程中﹐壓力﹑ 速度﹑溫度﹐以及伴隨的黏度﹑剪切率在流動方 嚮以及肉厚方嚮有很大的變化對于成型及成品品 質會有很大的影響﹒
3. 預備可塑化式設出裝置
預備可塑化式裝置是將預塑加熱缸 ( 將成形材 料加熱熔融 ) 和射出加熱缸 ( 將熔融材料射出 ) 相結 合,依照加熱缸之形式大概分為下列兩種: a.柱塞預備可塑化式(圖(8)) 塑料在預塑加熱缸中加熱,使塑料達到可塑化熔 融,再由柱塞推送至射出加熱缸中,此時送入塑料壓 力使射出柱塞後退,調節此後退量以決定一次的射 出量,在達到所定之射出量時,柱塞再推進將熔融塑 料射入模穴內成形.
一﹑實習目的﹕
射出成型機結构
本實習的目的在于了解射出成型的原理﹑過程與 特性﹐並了解射出成型機的基本构造與操作單元﹒ 二﹑相關知識﹑原理及儀器﹕ §2-1 射出成型各階段之基本原理與物理現象 (1)射出成型以模具的机械動作可分為鎖模階段﹑充 填階段﹑保壓階段﹑冷卻階段及開模頂出五個极端﹐ 如圖(1)所示﹔但以熔膠在模具的流動至開模位置﹐ 則可分為充填﹑保壓及冷卻三個過程﹒
- 1、下载文档前请自行甄别文档内容的完整性,平台不提供额外的编辑、内容补充、找答案等附加服务。
- 2、"仅部分预览"的文档,不可在线预览部分如存在完整性等问题,可反馈申请退款(可完整预览的文档不适用该条件!)。
- 3、如文档侵犯您的权益,请联系客服反馈,我们会尽快为您处理(人工客服工作时间:9:00-18:30)。
标准型螺杆构造
(c) 熔融传送区(melt conveying zone):又称计量区 (metering zone),主要功能是促进熔融物的混合及增压效 果。熔胶在此区域的流动主要包括螺杆旋转所产生的拖曳流 及螺杆前端压力所产生的逆向流,此两种流动方向相反,因 此具有混合功能。当转速增加时会因拖曳流的增加而使熔胶 流速增快,但固体塑料若来不及在熔化区结束时完全熔化, 因而进入计量区将使计量区的混合效果降低,且易造成塑化 不均的现象。同时,在转速增加时塑料的剪切效果提高,亦 有可能导致温度过热或剪应力超过临界值。 (d) 螺旋沟槽的深度比(hm/hf)称为压缩比,通常为 2~3,螺杆全长与螺杆外径比L/D常用20。熔融材料从喷嘴射 出时,由于施加于材料的射出压力之反作用力,材料的一部 份经螺旋沟槽逆流到后方,为了防止逆流,可用逆流防止阀。
第一章 射出成型机简介
内容
射出成形机介绍 射出成形机构造 射出成形机的性能介绍
射出成形机构造
主要單元 主要元件 螺桿、料缸、噴嘴、螺桿旋轉驅動馬達、進料漏斗、 加熱器 可動側模盤﹑固定側模盤﹑繫桿趕﹑頂出機構﹑合模 機構﹑合模油壓缸﹑模具厚度調整機構﹑安全裝置
射出單元
挾模單元
油壓驅動控制 油壓汞、控制閥、濾油器、冷卻器、油箱、油壓缸 單元
2.1:1
2.2:1 2.4:1 2.5:1 2.5:1 3:1(max)
0.15
0.15 0.2 0.2 0.25 0.25 最大表面粗糙度2~4μm 2. R2=5mm(直径30~60mm) R2=10mm(直 径 约 牙部宽度0.1D 7. 最大进料行程4D
排气式螺杆的示意图
剪切环设计尺寸
排气式螺杆的特点
加热缸与喷嘴
(1)加热缸内装螺杆,外围由数组带式加热器直接将内部材料加热。 带式加热器一般分为3~4组,各组有独立的温控,并藉热电偶保 持适合的温度设定 (2)喷嘴是连接模具与加热缸的接合部,通常喷嘴部份也装置独立的 带式加热器;直接控制射出材料的熔融温度,必要时也附加各种装 置用以遮断熔融材料的流动,以防止熔融材料在开模或机座后退 时从加热缸泄漏,如针阀喷嘴及闭锁喷嘴 (3)喷嘴的球状外轮廓的曲率半径(欧规10,15,20,35mm)需小于模具 入口的曲率半径,喷嘴出口半径应小于模具的入口半径 (4)喷嘴可分开口式喷嘴及遮闭式喷嘴,下图为针状遮闭式喷嘴,因 弹簧作用而封闭,可避免漏料,射出时当射压高过弹簧作用力时 即开启,熔胶通过喷嘴射入模穴
一般热塑性塑料的螺杆设计尺寸
直径 (mm) 30 进料段沟深 hf(mm) 4.3 计量段沟深 hM(mm) 2.1 压缩比 hf/hM 2:1 径向牙部间隙 (mm) 0.13 其他
40
60 80 100 120 >120
5.4
7.5 9.1 10.7 12 14(max)
2.6
3.4 3.8 4.3 4.8 5.6(max)
(3)柱塞射出,计量准确
螺杆式的特色: (1) 进料时,螺杆旋 转且后退,摩擦生热, 塑化效果佳 (2)射出时,螺杆不 旋转且直接向前,熔 胶高压射出,但会因 逆流而使计量不准
预备可塑化射出成形机
特色: (1)以螺杆塑化胶料 达到塑化均匀的目标
(2)以柱塞进行射出 达到精确计量的目标
不同射出单元的比较
塑化装置与射出装置分别由不同射出机担任
螺杆式
预备可塑化
塑料塑化的关键--螺杆
计量区 熔化区 进料区
螺杆前端构造
止逆阀的作用
进料时止逆阀上的滑动环向前,熔胶由滑动环内 侧流经沟槽,蓄积在螺杆前端,射出时螺杆向前,螺 杆前端压力剧增,滑动环向后抵住环座,产生止逆作 用,防止熔胶逆流。
标准型螺杆构造
電器控制單元 動作控制系統、溫度控制系統、動力控制系統
機架及床台
射出成形机的构造
射出单元功能
(a)将塑料输入料缸,并加热塑化高,并且持续续压动作,直 到浇口处不发生流动,避免冷却收缩
柱塞式的特色: (1)外部加热,塑化效果不佳 (2)藉鱼雷使塑料流经间隙而受 热
种类 柱塞式 特色 加热缸内置鱼雷,材料通过加热缸内面与鱼雷构成的狭小通路,在此充 分加热,成为熔融状态,热源由加热器提供,而后藉柱塞将熔融的材料加压 射出,塑化均质性差。 使用螺杆进料并输送熔胶,进料时螺杆旋转将塑料输送至前端,因熔胶 压力而使螺杆后退。射出时螺杆不旋转,由油压作动以类似柱塞之方式将螺 杆往前推动。热源由加热器(30%)及塑料流动所引起的摩擦热(70%)提供,塑化 混炼效果佳。 其优点如下: (1)藉螺杆的混炼作用,使材料内部也发热,因此可塑化效果较均匀且塑 化能力大。 (2)由于加热缸内的压力损失少,可使用较低的射出压力亦能成形。 (3)加热缸内的材料滞留处少,热安定性差的材料也很少因滞留而分解。 (4)材料更换、换色操作容易。 (5)可直接以色母加入母料着色。 其缺点如下: (1)在射出时,熔融材料易顺着螺旋沟槽逆流。
(a) 固体输送区(solid conveying zone): 固体输送区(又称进料 区)的功能是将藉由重力落入此一区域的塑料颗粒挤压成成固体床并以 塞状向前移动,其主要的驱动力是塑料与套筒内侧表面的摩擦力(F1)及 塑料与螺杆表面的摩擦力(F2)之差(即F1-F2),当F1愈大于F2,则输送 能力就愈高。若固体塑料的孔隙度较大,则整体密度(Bulk density)较 低,因此在进料区必须有较深的螺杆沟深,以利吃料并维持输送量的稳 定。 (b) 熔化区(melting zone):从熔融池的出现到固体床完全熔化, 此段区域称为熔化区,其功能主要是藉由摩擦热及套筒加热将固体塑料 熔化。凡举螺杆熔化速率、背压高低及熔化是否完全,在此段均受到决 定性的影响。当固体塑料熔化时,由于孔隙度消失体积会缩小,因此必 须缩小螺杆与套筒之间的流道断面以维持塑料的压缩效果,通常可由沟 深缩小或导程(pitch)缩小来达到目的。熔化区的长度取决于塑料熔化 的速度,例如结晶性材料(如尼龙)熔化速度快,熔化区的长度较短,非 结晶性材料(如PVC)熔化速度慢,熔化区的长度较长。不过一般而言, 较长的熔化区有较佳的排气及混炼效果。