我国催化裂化技术
陈俊武:中国炼油催化裂化技术起步的故事

陈俊武:中国炼油催化裂化技术起步的故事作者:徐沛宇来源:《能源》 2016年第8期口述/中国科学院院士陈俊武文/本刊记者徐沛宇陈俊武被誉为我国催化裂化工程技术的奠基人,曾与炼油工业的多项“共和国第一”息息相关。
1948年7月,22岁的陈俊武从北京大学化工系毕业后,几经辗转,于1949年1 2月来到辽宁抚顺矿务局,参加了人造石油工厂修复的工作。
1961年冬天,石油工业部在北京香山召开了炼油科技工作会议,决定开展炼油新技术(即后来被誉为“五朵金花”的流化催化裂化等五项炼油新工艺)技术攻关。
34岁的陈俊武受命担任了我国第一套流化催化裂化装置设计师。
60年代初,古巴革命成功,将国外公司的炼油厂收归国有,陈俊武有机会赴古巴考察流化催化裂化技术,尽力收集了当时国外比较先进炼油技术资料,采用笔记加照相复制的方式,收集了大量资料。
回国后,石油部又组织了专人进一步整理和翻译,极大地提高了我国炼油工业的技术水平。
本期《能源》,记者专访了陈俊武院士,请他回忆了那段中国催化裂化的起步故事。
自主研发超步和国外技术考察60年代初,在前苏联老大哥帮助下建成的兰州炼油厂的催化裂化技术是移动床催化裂化,催化剂仍然是无定型硅铝小球,而西方国家已经有了流化催化裂化技术,催化剂已经是微球分子筛,无论轻油收率还是选择性均比苏联高出一大截。
我们发现,苏联的技术比西方技术落后二十年,相当于美国40年代的水平。
那时候苏联也拿不出更先进的技术,他们的技术还没有跳出美国四十年代的技术水平。
所以,如何赶上六十年代的国际先进技术,是当时国内炼油工业面临的一个大问题。
当时国外的一般技术可以卖给你,但战略性的先进技术绝不卖给我们。
美国对中国实施技术封锁,所以中国只能考虑自主开发,只能靠自己去摸索和创新,这就是石油部1961年12月在北京召开炼油新技术开发科技会议的初衷。
可是,我们在兰州炼油厂做的一些实验都不成功,催化剂的损失太大,非常期望能够到国外去考察先进催化裂化技术。
我国催化裂化工艺技术进展_许友好
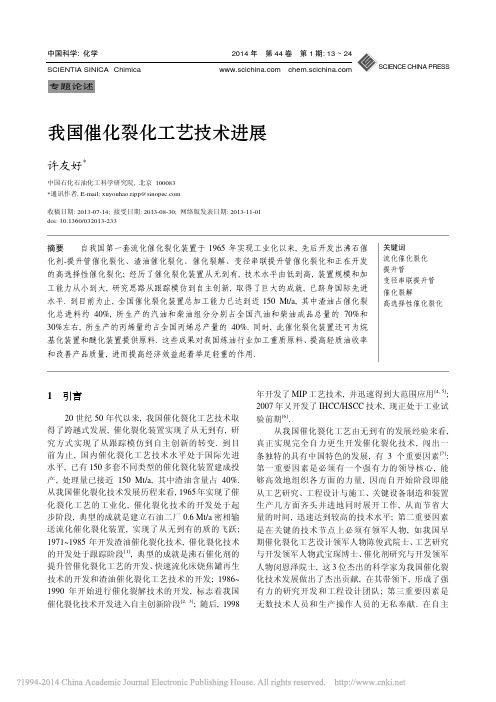
《中国科学》杂志社
SCIENCE CHINA PRESS
我国催化裂化工艺技术进展
许友好*
中国石化石油化工科学研究院, 北京 100083 *通讯作者, E-mail: xuyouhao.ripp@ 收稿日期: 2013-07-14; 接受日期: 2013-08-30; 网络版发表日期: 2013-11-01 doi: 10.1360/032013-233
年开发了 MIP 工艺技术, 并迅速得到大范围应用[4, 5]; 2007 年又开发了 IHCC/HSCC 技术, 现正处于工业试 验前期[6]. 从我国催化裂化工艺由无到有的发展经验来看 , 真正实现完全自力更生开发催化裂化技术 , 闯出一 条独特的具有中国特色的发展 , 有 3 个重要因素 [7]: 第一重要因素是必须有一个强有力的领导核心 , 能 够高效地组织各方面的力量 , 因而自开始阶段即能 从工艺研究、工程设计与施工、关键设备制造和装置 生产几方面齐头并进地同时展开工作 , 从而节省大 量的时间, 迅速达到较高的技术水平; 第二重要因素 是在关键的技术节点上必须有领军人物 , 如我国早 期催化裂化工艺设计领军人物陈俊武院士、 工艺研究 与开发领军人物武宝琛博士、 催化剂研究与开发领军 人物闵恩泽院士, 这 3 位杰出的科学家为我国催化裂 化技术发展做出了杰出贡献, 在其带领下, 形成了强 有力的研究开发和工程设计团队 ; 第三重要因素是 无数技术人员和生产操作人员的无私奉献 . 在自主
产率分布 (%)
汽油性质
烯烃 芳烃 MON
a) 抚顺二厂第一套装置的标定数据; b) 高桥分公司渣油催化裂化装置标定数据
入大气中. 再生器烧焦所用的空气由主风机供给, 大 部分空气分成两路进辅助燃烧室 , 以较高的线速通 过分布板小孔, 进入再生器密相床层, 与催化剂接触 进行烧焦; 少量的空气经增压机增压, 增压后送到密 相提升管, 作提升空气用. 密相流化催化裂化装置加 工大庆蜡油时典型的产物分布和汽油产品性质列于 表 1[7]. 兰州炼油厂于 1965 年 12 月建成了我国第一套 3 kt/a 的微球催化剂生产装置, 生产出合格的微球催 化剂. 随后, 微球催化剂应用于我国第一套催化裂化 装置, 并取得满意的工业应用结果. 随着催化裂化装 置的增多以及加工能力的增加, 1970、1976 和 1978 年 相继在长岭炼油厂、 齐鲁石化公司催化剂厂和石油六 厂建成投产年产分别为 6、4.5 和 2 kt 的微球催化剂 生产装置, 从而形成了我国 4 个裂化催化剂制备基地[9].
催化裂化技术.

①.散式流化态: 颗粒均匀地分布在整个流化床内且随着 流速的增加床层均匀膨胀,床内孔隙率均匀 增加,床层上界面平稳,压降稳定、波动很 小。因此,散式流化态是较理想的流化状态。 一般流-固两相密度差较小的体系呈现散式流 态化特征,如液-固流化床。 ②.聚式流化态: 颗粒在床层的分布不均匀,床层呈现两 相结构:一相是颗粒浓度与空隙率分布较为 均匀且接近初始流态化状态的连续相,称为 乳化相;另一相则是以气泡形式夹带少量颗 粒穿过床层向上运动的不连续的气泡相,因 此又称为鼓泡流态化。
四、催化裂化的方法 1、固定床: 反应和再生过程是在同一设备中交替进行, 属于间歇式操作。为了使整个装置能连续生产, 就要用几个反应器轮流的进行反应和再生。因 此这种装置的设备结构复杂,生产能力小,钢 材耗量大,操作麻烦,工业上早已被淘汰。 2、移动床: 移动床催化裂化,使用直径约3mm的小 球催化剂,起初是用机械提升的方法在两器间 运送催化剂,后来改为空气提升,生产能力较 固定床大为提高,产品质量也得到改善。由于 催化剂在反应器和再生器内靠重力向下移动, 速度缓慢,所以对设备磨损较小,不过移动床 的设备结构仍比较复杂,钢材耗量比较大。
催化裂化技术
第一章 概述
一、催化裂化技术 二、催化裂化技术发展状况 三、催化裂化反应类型 四、催化裂化的方法 五、催化裂化的目的及意义
第二章 工艺叙述
一、反应-再生系统 二、分馏系统
三、吸收—稳定系统
四、余热锅炉系统 五、反应系统主要设备
第一章
概述
一、催化裂化技术 催化裂化(Fluid Catalytic Cracking)是石油炼制 过程之一,是在热和催化剂的作用下使重质油发生裂 化反应,转变为裂化气、汽油和柴油等的过程。催化 裂化原料是原油通过原油蒸馏(或其他石油炼制过程) 分馏所得的重质馏分油;或在重质馏分油中掺入少量渣 油,或经溶剂脱沥青后的脱沥青渣油;或全部用常压渣 油或减压渣油。在反应过程中由于不挥发的类碳物质 沉积在催化剂上,缩合为焦炭,使催化剂活性下降, 需要用空气烧去(见催化剂再生),以恢复催化活性, 并提供裂化反应所需热量。催化裂化是石油炼厂从重 质油生产汽油的主要过程之一。所产汽油辛烷值高 (马达法80左右),裂化气(一种炼厂气)含丙烯、 丁烯、异构烃多。
先进炼油化工技术催化裂解技术(DCC)
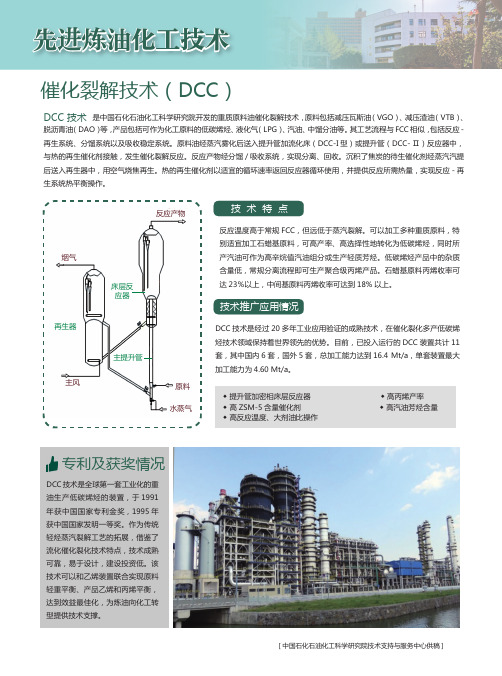
催化裂解技术(DCC)
DCC 技术 是中国石化石油化工科学研究院开发的重质原料油催化裂解技术,原料包括减压瓦斯油(VGO)、减压渣油(VTB)、脱沥青油(DAO)等,产品包括可作为化工原料的低碳烯烃、液化气(LPG)、汽油、中馏分油等。
其工艺流程与FCC 相似,包括反应-再生系统、分馏系统以及吸收稳定系统。
原料油经蒸汽雾化后送入提升管加流化床(DCC-I 型)或提升管(DCC-Ⅱ)反应器中,与热的再生催化剂接触,发生催化裂解反应。
反应产物经分馏/吸收系统,实现分离、回收。
沉积了焦炭的待生催化剂经蒸汽汽提后送入再生器中,用空气烧焦再生。
热的再生催化剂以适宜的循环速率返回反应器循环使用,并提供反应所需热量,实现反应-再生系统热平衡操作。
DCC 油生产低碳烯烃的装置,于[中国石化石油化工科学研究院技术支持与服务中心供稿]反应产物烟气原料
水蒸气主风再生器床层反应器主提升管
先进炼油化工技术。
催化裂化rtc工艺技术

催化裂化rtc工艺技术催化裂化是一种重要的炼油工艺,用于将原油中的重质烃类分解为较轻质的产品。
催化裂化工艺技术(RTC)是催化裂化的一种改进技术,能够提高裂化效率和产品质量。
催化裂化RTC工艺技术主要包括三个方面的改进:催化剂的优化、反应器的改进和生产过程的改进。
首先,催化剂的优化是提高催化裂化效率的关键。
采用高活性和高选择性的催化剂,能够促进裂化反应的进行,同时减少副反应的发生。
通过选择合适的催化剂组分和处理方法,能够提高催化剂的稳定性和寿命,延长其使用寿命。
其次,反应器的改进是提高裂化效率和产品质量的重要手段。
通过优化反应器的结构设计和工艺参数的控制,能够提高裂化反应的效率和产量。
例如,采用多级反应器系统,可以充分利用热量和物料的传递,提高产物的收率和产品质量。
此外,采用先进的控制技术和自动化设备,能够实现反应器系统的精确控制,提高产品的稳定性和一致性。
最后,生产过程的改进是提高催化裂化RTC工艺技术的关键。
通过优化原油的预处理和催化裂化的操作条件,可以提高裂化反应的效率和选择性。
例如,采用适当的预处理方法,如加氢处理和脱盐处理,能够去除原油中的杂质和重金属,减少催化剂中毒和磨损。
此外,通过优化操作参数,如温度、压力和进料比等,能够更好地控制反应的进行,提高产品的质量和产量。
催化裂化RTC工艺技术具有以下优势:一是能够提高炼油厂的利润和竞争力。
采用RTC技术,能够提高裂化产物的收率和产品质量,同时减少能耗和废水废气的排放,降低生产成本。
二是能够提高产品的附加值和市场竞争力。
通过优化裂化产物的组分和品质,能够提高产品的附加值,满足市场需求。
三是对环境保护具有积极作用。
采用RTC技术,能够减少能源消耗和废物排放,降低对环境的污染。
总之,催化裂化RTC工艺技术是一种重要的炼油工艺技术,能够提高裂化效率和产品质量。
通过催化剂的优化、反应器的改进和生产过程的改进,能够实现催化裂化过程的精确控制,提高产品的收率和附加值,同时降低能耗和环境污染。
催化裂化工艺介绍
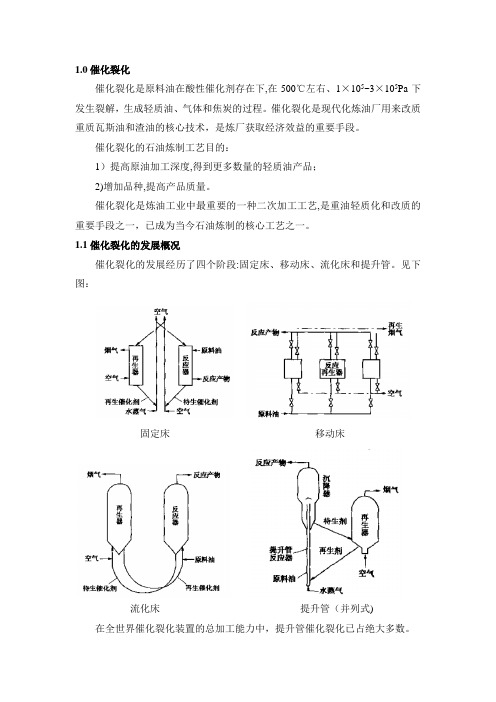
1.0催化裂化催化裂化是原料油在酸性催化剂存在下,在500℃左右、1×105~3×105Pa下发生裂解,生成轻质油、气体和焦炭的过程。
催化裂化是现代化炼油厂用来改质重质瓦斯油和渣油的核心技术,是炼厂获取经济效益的重要手段。
催化裂化的石油炼制工艺目的:1)提高原油加工深度,得到更多数量的轻质油产品;2)增加品种,提高产品质量。
催化裂化是炼油工业中最重要的一种二次加工工艺,是重油轻质化和改质的重要手段之一,已成为当今石油炼制的核心工艺之一。
1.1催化裂化的发展概况催化裂化的发展经历了四个阶段:固定床、移动床、流化床和提升管。
见下图:固定床移动床流化床提升管(并列式) 在全世界催化裂化装置的总加工能力中,提升管催化裂化已占绝大多数。
1。
2催化裂化的原料和产品1。
2.0原料催化裂化的原料范围广泛,可分为馏分油和渣油两大类。
馏分油主要是直馏减压馏分油(VGO),馏程350—500℃,也包括少量的二次加工重馏分油如焦化蜡油等,以此种原料进行催化裂化称为馏分油催化裂化。
渣油主要是减压渣油、脱沥青的减压渣油、加氢处理重油等.渣油都是以一定的比例掺入到减压馏分油中进行加工,其掺入的比例主要受制于原料的金属含量和残炭值。
对于一些金属含量低的石蜡基原有也可以直接用常压重油为原料.当减压馏分油中掺入渣油使通称为RFCC。
以此种原料进行催化裂化称为重油催化裂化。
1。
2。
1产品催化裂化的产品包括气体、液体和焦炭。
1、气体在一般工业条件下,气体产率约为10%—20%,其中含干气和液化气。
2、液体产物1)汽油,汽油产率约为30%-60%;这类汽油安定性较好.2)柴油,柴油产率约为0-40%;因含较多芳烃,所有十六烷值较低,由重油催化裂化得到的柴油的十六烷值更低,这类柴油需经加氢处理.3)重柴油(回炼油),可以返回到反应器内,已提高轻质油收率,不回炼时就以重柴油产品出装置,也可作为商品燃料油的调和组分。
4)油浆,油浆产率约为5%-10%,从催化裂化分馏塔底得到的渣油,含少量催化剂细粉,可以送回反应器回炼以回收催化剂.油浆经沉降出去催化剂粉末后称为澄清油,因多环芳烃的含量较大,所以是制造针焦的好原料,或作为商品燃料油的调和组分,也可作加氢裂化的原料。
催化催化裂化技术

催化催化裂化技术催化裂化技术是一种重要的炼油工艺,可以将重质石油馏分转化为高附加值的轻质产品。
本文将从催化裂化技术的原理、应用和发展前景等方面进行探讨,以期为读者提供对该技术的全面了解。
一、催化裂化技术的原理催化裂化技术是通过催化剂的作用将重质石油馏分分解为较轻的产品。
其主要原理是在高温和高压的条件下,将原料油与催化剂接触,使其发生裂化反应。
这种反应可以将长链烃分子裂解成短链烃分子,从而提高汽油和燃料油的产率。
催化裂化反应主要分为两个阶段:热裂化和催化裂化。
在热裂化阶段,原料油在高温下分解成烃气和液体烃。
然后,在催化剂的作用下,烃气和液体烃进一步反应,生成较轻的产品,如汽油、液化气和柴油等。
二、催化裂化技术的应用催化裂化技术在炼油行业中具有广泛的应用。
首先,它可以提高汽油的产率。
由于汽车的普及,对汽油的需求量不断增加。
催化裂化技术可以将重质石油馏分转化为轻质的汽油,从而满足市场需求。
催化裂化技术可以生产出高质量的柴油。
在催化裂化过程中,石油馏分中的硫、氮和金属等杂质可以得到有效去除,从而提高柴油的质量。
这对于减少柴油排放的污染物具有重要意义。
催化裂化技术还可以生产出液化气、石脑油和石化原料等产品。
这些产品在化工、冶金和化肥等行业中具有广泛的应用。
三、催化裂化技术的发展前景随着能源需求的增加和石油资源的日益枯竭,催化裂化技术在未来的发展前景十分广阔。
一方面,随着汽车工业的高速发展,对汽油的需求将持续增加,催化裂化技术将成为满足市场需求的重要手段。
另一方面,随着环境保护意识的提高,对燃料油质量的要求也越来越高。
催化裂化技术可以提高燃料油的质量,减少对环境的污染,因此在未来的发展中具有重要的作用。
随着科技的不断进步,催化剂的研发和改进也将推动催化裂化技术的发展。
新型的催化剂可以提高反应的选择性和活性,从而提高产品的产率和质量。
催化裂化技术作为一种重要的炼油工艺,在提高石油产品产率和质量方面具有重要的作用。
催化裂化工艺技术的改进

催化裂化工艺技术的改进催化裂化是一种重要的石油加工技术,主要用于将长链烷烃分子裂解为短链烯烃和芳烃。
以催化裂化技术为核心的石油炼制工艺已经发展了几十年,随着科学技术的不断进步,催化裂化技术也在不断改进和完善。
首先,研究人员通过改进催化剂的性能来提高催化裂化的效率。
催化剂是催化裂化技术的关键,可以促进原料油在裂化过程中的反应速率和选择性。
近年来,人们通过改变催化剂的组成、结构和物理化学性质,成功地实现了催化裂化反应的高效进行。
例如,研究人员发现,采用新型催化剂可以提高芳烃和短链烯烃的产率,同时降低副产物的生成率,从而提高产品的质量。
其次,研究人员改进了催化裂化反应器的结构和运行方式。
催化裂化反应器是催化裂化工艺的核心设备,直接影响到裂化产物的质量和产率。
为了提高催化裂化的效果,人们对反应器进行了各种改进。
例如,引入先进的内径梯度填料,可以增加反应器有效体积,提高催化剂与原料油的接触效率。
此外,还引入了多级反应器和中间分离回收装置,以优化反应条件,增加产品的收率,并减少催化剂的损失。
再次,研究人员改进了催化裂化过程中的催化剂再生技术。
催化剂的失活是催化裂化工艺中的一大难题,因为长期的高温、高压和有毒物质的作用会导致催化剂性能下降。
为了延长催化剂的使用寿命,人们引入了催化剂再生技术。
催化剂再生技术可以通过氧化、还原、酸洗和物理方法等手段,修复催化剂结构和活性,使其恢复到原来的状态,从而延长催化剂的使用寿命。
最后,研究人员还改进了催化裂化工艺中的产品分离和处理技术。
由于催化裂化反应产物的种类繁多、组成复杂,因此需要通过一系列的分离和处理工艺来得到目标产品。
为了提高产品的纯度和收率,人们引入了先进的分离技术,如闪蒸、吸附、蒸馏等。
此外,还研发了高效的处理技术,如催化裂化汽油加氢和重油深度加工等,以进一步提高产品的质量和降低环境污染。
综上所述,催化裂化工艺技术在不断改进和创新中不断提高着效率和产品质量。
通过改进催化剂的性能、反应器的结构、催化剂再生技术和产品分离处理技术,可以提高催化裂化的经济效益和社会效益,为石油加工行业的可持续发展做出贡献。
(完整版)我国催化裂化技术

我国催化裂化技术发展现状及前景左丽华(石油化工科学研究院,北京,100083)概括论述了我国催化裂化发展现状和世界FCC技术的最新发展水平,分析和比较了我国FCC技术与世界先进水平的差距,初步提出我国催化裂化技术的发展前景。
关键词:催化裂化现状最新水平差距前景1 概况流化催化裂化(FCC)是现代化炼油厂用来改质重质瓦斯油和渣油的核心技术,是炼厂获取经济效益的一种重要方法。
据统计,截止到1999年1月1日,全球原油加工能力为 4 015.48 Mt/a,其中催化裂化装置的加工能力为668.37 Mt/a,约占一次加工能力的16.6%,居二次加工能力的首位。
美国原油加工能力为821.13 Mt/a,催化裂化能力为271 Mt/a,居界第一,催化裂化占一次加工能力的比例为33.0%。
我国催化裂化能力达66.08 Mt/a,约占一次加工能力的38.1%,居世界第二位。
我国石油资源中,原油大部分偏重,轻质油品含量低,这就决定了炼油工业必须走深加工的路线。
近十几年来,催化裂化掺炼渣油量在不断上升,已居世界领先地位。
催化剂的制备技术已取得了长足的进步,国产催化剂在渣油裂化能力和抗金属污染等方面均已达到或超过国外的水平。
在减少焦炭、取出多余热量、催化剂再生、能量回收等方面的技术有了较大发展。
2 现代催化裂化技术发展特点及趋势影响FCC未来发展的重要因素将是:原油价格、满足环保要求、新燃料规格、石油化工原料需求和渣油加工。
环保法规已成为FCC技术发展的主要推动力。
FCC已从简单解决诸如汽油、柴油、液化气、抗金属等其中的一、二个问题转向要同时解决多个矛盾的组合。
80年代以来,催化裂化技术的进展主要体现在两个方面:① 开发成功掺炼渣油(常压渣油或减压渣油)的渣油催化裂化技术(称为渣油FCC,简写为RFCC);② 催化裂化家族技术,包括多产低碳烯烃的DCC技术,多产异构烯烃的MIO技术和最大量生产汽油、液化气的MGG技术。
渣油加氢处理-催化裂化双向组合(RICP)技术

渣油加氢处理-催化裂化双向组合(RICP)技术中国石化石油化工科学硏究院开发的渣油加氢-催化裂化双向组合(RICP)技术是将催化裂化装置中回炼的重循环油(HCO)掺入渣油加氢原料中,作为渣油加氢原料的稀释油,和渣油一起加氢后作为催化裂化原料。
RICP技术对渣油加氢和催化裂化两套装置均有改善效果:对渣油加氢装置,高芳香性的HCO促进了渣油加氢反应;对催化裂化装置,因HCO加氢后再作为催化裂化原料,轻油收率可提高1~3百分点,焦炭收率下降。
本技术已获授权专利13件。
♦RICP技术将传统工艺中RFCC装置原本自身回炼的HCO改为输送到渣油加氢装置,和渣油一起加氢后再作为RFCC原料。
高芳香性的HCO掺入到渣油加氢原料中,促进了渣油加氢反应并抑制了渣油加氢催化剂结焦;加氢后的HCO再回催化裂化装置作为原料,提高了催化裂化处理量和轻油收率。
♦通过改变HCO抽出位置并增设精密过滤器除去HCO中催化剂颗粒,避免了HCO中催化剂颗粒对渣油加氢装置的影响。
♦装置改造费用低,工业上易实施。
氢气减压渣油固定床渣油加氢>350°C加氢渣油渣油催化裂化―干气―液化气―汽油―柴油HCO▲RICP技术工艺流程示意4气体»石脑油»柴油4油浆主要技术指标:♦渣油加氢装置进料中可掺入5%〜30%的HCO作为稀释油,相应可顶替同样比例的直馏蜡油。
♦RICP技术与常规渣油加氢-重油催化裂化组合工艺相比,催化裂化装置处理能力可提高4%〜5%,轻质油收率增加1〜3百分点,油浆产率下降1〜3百分点,焦炭产率降低0.1〜0.5百分点。
▲中国石化齐鲁分公司1.5Mt/a年渣油加氢和0.8Mt/a催化裂化装置与传统的渣油加氢-催化裂化单向组合技术(现有技术)相比,RICP技术的轻油收率高1〜3百分点,催化裂化处理量和掺渣量也有所提高,因此具有更高的经济和社会效益。
RICP技术于2006年5月在中国石化齐鲁分公司1.5Mt/a渣油加氢装置和0.8Mt/a催化裂化装置进行了工业应用试验。
催化裂化mip技术

催化裂化MIP技术引言催化裂化是石油化工领域中一项非常重要的加工技术,通过将重质石油馏分在高温、高压和催化剂作用下分子裂解,生产出更高价值的燃料和化工产品。
在催化裂化过程中,MIP(Microsphere-embedded Insulator)技术作为一种新兴的催化剂承载技术发挥着重要作用。
本文将重点探讨催化裂化MIP技术的原理、应用和未来发展方向。
MIP技术的原理MIP技术是一种将催化剂包裹在微粒子(通常是陶瓷、氧化铝等材料)中的方法,形成高度稳定的催化剂载体。
在催化裂化过程中,MIP技术可以提供更好的热稳定性和化学稳定性,延长催化剂的寿命并提高催化效率。
MIP技术的原理包括以下几个方面:1. 载体选择MIP技术的首要任务是选择合适的载体材料。
通常,陶瓷和氧化铝是常用的载体材料,由于它们具有良好的热稳定性和化学稳定性,在高温和高压条件下不易破裂或变形。
此外,载体材料应具有适当的表面积和孔隙结构,以便催化剂能够均匀地分散在载体中,并提供最大的活性表面积。
2. 催化剂包裹催化剂包裹是指将催化剂均匀地分散在载体中。
这一步骤旨在确保催化剂能够充分接触到反应物,从而提高反应效率。
通常,可以通过浸渍法、沉积法和蒸镀法等方法将催化剂包裹到载体表面。
这些方法可以使催化剂在载体上形成均匀分布的颗粒,并保持良好的催化活性。
3. 表面修饰MIP技术可以通过表面修饰来改变载体和催化剂之间的相互作用。
表面修饰可以通过调整催化剂和载体表面的化学性质,如酸碱性和亲疏水性,来改善催化效果。
此外,表面修饰还可以增加载体与底层催化层之间的附着力,从而提高催化剂的稳定性和寿命。
MIP技术的应用MIP技术在催化裂化领域有着广泛的应用。
以下将重点介绍几个方面的应用。
1. 燃料生产催化裂化是燃料生产的重要环节,MIP技术可以在催化裂化过程中提高燃料产率和质量。
MIP技术可以使催化剂更均匀地分散在载体中,从而提高烟气与催化剂的接触效率。
此外,MIP技术还可以提高催化剂的稳定性,延长催化剂的使用寿命。
催化裂化技术的现状及发展趋势

催化裂化技术的现状及发展趋势
催化裂化技术是最近几年来人们极力推进研究的一个技术,它对于提高生物柴油的性能以及破坏有毒有机物质有显著的改善。
目前,催化裂化技术已经发展迅猛,并在未来的发展中有发挥出巨大的潜力,其中包括其在碳氢化合物低温裂化领域的巨量发展。
首先,催化裂化技术在开发绿色燃料、降低有毒物质的排放方面发挥着重要作用。
它为油脂,烃类,污染物,有毒有机物,废弃物,碳氢化合物等制备生物柴油等清洁能源提供了可能。
其中,碳氢化合物的低温裂烃技术可以提高生物柴油的收率,降低有毒有机物的排放,提高燃料的燃烧能效,为构建低碳的绿色社会奠定基础。
其次,催化裂化技术近年来发展迅猛,包括催化剂的合成,催化裂化反应机理,催化剂和反应条件等。
例如,今年在日本开发出用于催化裂化柴油的新型钴催化剂。
此外,也合成了用于催化裂化石油、烃类和有机废料等材料的新型催化剂,例如以钯和钼为分子基础的纳米微粒等。
另外,催化裂化技术也受到国内外科学家的研究关注,已经取得了显著的进展。
国外的研究主要集中在改进催化加氢裂化反应最前沿的技术和装置技术以及提高反应温度和在碳氢化合物低温裂化方面取得巨大进展。
至于国内,主要工作集中在改进催化剂和催化反应机理以及提高催化裂化反应效率的方面,如金属催化剂和非金属催化剂的研究以及反应温度的改进等,以期在技术发展上取得突破性进展。
总的来说,催化裂化技术的发展取得了显著的成绩,在未来的研究中,将会继续完善并发展其本身的技术,并继续在低温碳氢化合物催化裂烃方面展示出巨大的潜力。
我国催化裂化技术发展现状及前景

我国催化裂化技术发展现状及前景一、技术水平提升近年来,我国催化裂化技术取得了显著的技术进步,主要体现在以下几个方面:1. 催化剂性能提升:研发新型催化剂,提高催化裂化反应活性和选择性,从而提高产品收率和质量。
2. 反应工艺优化:通过改进反应工艺条件,提高反应转化率和产品收率,同时降低能源消耗和环境污染。
3. 设备更新换代随着技术的不断发展,催化裂化设备也在不断更新换代。
新型催化裂化设备具有更高的传热效率、更低的能源消耗和更好的环保性能。
同时,设备的自动化和智能化水平不断提高,降低了人工成本和操作难度。
二、绿色环保方向随着环保意识的不断提高,绿色环保成为催化裂化技术发展的重要方向。
具体表现在以下几个方面:1. 减少污染物排放:采用新型催化剂和反应工艺,降低催化裂化过程中的污染物排放量,实现清洁生产。
2. 能源高效利用:优化能源利用结构,提高能源利用效率,减少能源浪费和环境污染。
3. 废弃物资源化:对催化裂化过程中的废弃物进行资源化利用,如生产硫酸、水泥等产品,实现废弃物的增值和环保利用。
三、工业互联网融合工业互联网技术的不断发展,为催化裂化技术的数字化转型提供了有力支持。
通过将工业互联网技术与催化裂化技术相结合,可以实现生产过程的全面数字化管理和智能控制,提高生产效率和产品质量。
四、产业链协同发展催化裂化技术作为石油化工产业链中的重要环节,需要与上下游产业协同发展。
通过加强与相关产业的合作,优化原料采购、产品销售等环节,提高产业链的协同效应和整体竞争力。
五、国际化战略布局随着全球化进程的不断深入,我国催化裂化技术也在积极拓展海外市场,进行国际化战略布局。
通过参与国际技术交流与合作,开展国际项目合作等方式,推动我国催化裂化技术的国际化发展。
六、智能化生产应用智能化生产是指通过应用人工智能、大数据、物联网等技术,实现生产过程的自动化、信息化和智能化。
在催化裂化技术领域,智能化生产的应用可以提高生产效率、降低能耗和减少人力成本。
催化裂化、催化裂解、热裂解技术对比

催化裂化、催化裂解、催化重整、加氢精制与裂解、芳烃抽提技术总结
MGG是以减压渣油、掺渣油和常压渣油等为原料的最大量生产富含烯烃的液态烃,同时最大生产高辛烷值汽油的工艺技术,与其他同类工艺的差别在于它在多产液态烃下还能有较高的汽油产率,并且可以用重油作原料(包括常压渣油)。
反应温度在510~540℃时,液化气产率可达25%~35%(摩尔比),汽油产率40%~55%(摩尔比)。
液化气加汽油产率为70%~80%。
汽油RON 一般为91~94,诱导期为500~900 min。
这一技术是以液化气富含烯烃、汽油辛烷值高和安定性好为特点的,现已有多套装置应用。
MIO技术是以掺渣油为原料,较大量地生产异构烯烃和汽油为目的产物的工艺技术。
1995年3-6月在中国兰州炼化总厂实现了工业化。
以石蜡基为原料时,缩短反应时间和采取新的反应系统,异构烯烃的产率高达15%(摩尔比)。
我国催化裂化工艺技术进展

我国催化裂化工艺技术进展催化裂化工艺技术是一种将重质烃类裂解为轻质烃类和汽油等燃料的重要手段。
在我国,随着石油化工行业的快速发展,催化裂化工艺技术也取得了显著的进步。
本文将简要回顾我国催化裂化工艺技术的发展历程,介绍技术创新与应用情况,并展望未来的发展前景。
自20世纪50年代以来,我国催化裂化工艺技术经历了从引进到自主研发的过程。
早期,我国从国外引进了一批先进的催化裂化装置和技术,在消化吸收的基础上,逐渐开始自主创新。
到20世纪80年代,我国已成功开发出具有自主知识产权的催化裂化工艺技术,并在大型工业装置上得到应用。
进入21世纪,我国催化裂化工艺技术水平进一步提升,已成为世界催化裂化工艺技术的重要研发和应用大国。
近年来,我国催化裂化工艺技术在技术创新和应用方面取得了许多重要成果。
在催化剂的种类和性能方面,通过优化制备工艺和组分设计,成功开发出多种高效、环保型催化剂。
这些催化剂在提高产品收率、降低能源消耗、减少污染物排放等方面具有显著优势。
在反应器设计方面,我国已成功开发出多套具有自主知识产权的反应器设计。
这些反应器在提高原料适应性、优化产品分布、降低能源消耗等方面表现出色。
例如,某新型反应器采用独特的结构设计,有效提高了催化剂的利用率和产品的分离效果,降低了装置的运行成本。
展望未来,我国催化裂化工艺技术将继续深入研究和技术创新。
随着环保要求的日益严格,开发高效、环保型催化裂化工艺技术将成为重要方向。
通过优化催化剂和反应器设计,降低污染物排放,提高资源利用率,实现绿色生产。
市场对燃料油和化工产品的需求将持续增长,因此催化裂化工艺技术的研究和应用将更加注重产品结构的优化和多样性的拓展。
例如,通过引入新的反应条件和原料,开发生产高附加值化学品的技术,提高企业的经济效益。
随着智能化和自动化的快速发展,催化裂化工艺技术将更加注重信息技术和自动化技术的应用。
通过建立自动化控制系统和实时监测分析系统,提高装置的运行效率和安全性,实现生产过程的智能化和信息化。
催化裂化mip技术

催化裂化mip技术催化裂化MIP技术是一种利用分子印迹聚合物(MIP)作为固定相,结合催化裂化技术进行有机物分离和纯化的新型技术。
该技术具有高选择性、高灵敏度、高稳定性等优点,在石油化工、环境监测等领域具有广泛应用前景。
催化裂化是一种重要的石油加工技术,通过在高温下将重质烃分子分解成轻质烃分子,以达到提高汽油、柴油等产品产率的目的。
然而,在催化裂化过程中,会产生大量的副产物和杂质,如苯、甲苯、二甲苯等有机物,这些有机物对环境和人体健康都有一定危害。
因此,对这些有机物进行有效的分离和纯化就显得尤为重要。
传统的分离和纯化方法包括蒸馏、吸附、萃取等,但这些方法存在着效率低、成本高、操作复杂等问题。
而MIP技术则通过特定模板分子与单体发生作用形成聚合物,并将模板分子从聚合物中去除,从而形成具有特定识别能力的固定相。
这种固定相可以选择性地吸附目标分子,实现分离和纯化。
MIP技术具有高选择性、高灵敏度、高稳定性等优点,可以用于有机物的分离和纯化。
在催化裂化MIP技术中,MIP作为固定相与催化剂一起放置在反应器中,通过对反应产物进行选择性吸附和分离,实现对目标有机物的高效纯化。
该技术不仅可以提高产品的质量和产率,还可以减少环境污染和资源浪费。
催化裂化MIP技术的关键是制备具有高选择性、高稳定性的MIP材料。
制备MIP材料需要选择合适的单体、交联剂、模板分子等原料,并进行聚合反应、去模板等步骤。
此外,还需要考虑到反应条件、聚合时间等因素对材料性能的影响。
近年来,研究人员已经成功地将催化裂化MIP技术应用于苯乙烯生产过程中对苄基氢氧化铵(BHA)进行了有效地分离和纯化,并取得了良好的效果。
此外,该技术还可以用于环境监测、食品安全等领域。
总之,催化裂化MIP技术是一种具有广泛应用前景的新型分离和纯化技术。
通过制备具有特定识别能力的MIP材料,实现对目标有机物的高效选择性吸附和分离,为提高产品质量和产率、减少环境污染和资源浪费等方面提供了新的解决方案。
浅析我国炼油催化裂化的发展技术
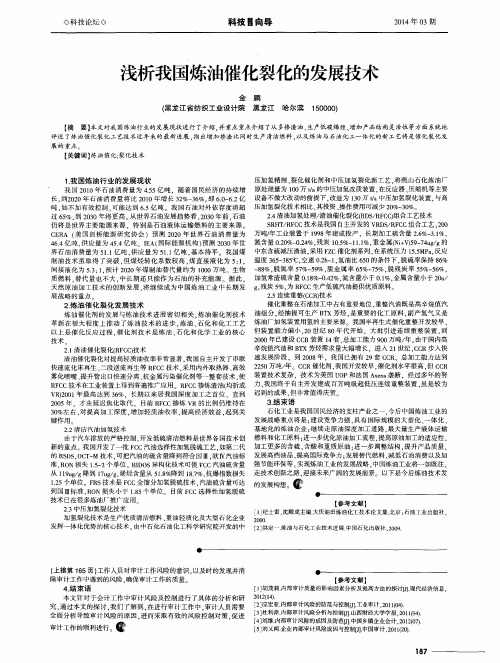
评述 了炼油催化 裂化 工艺技 术近年 来的最新进展 , 指 出增加掺 渣比 同时生产清 洁燃料 , 以及 炼油与石油化工一体化 的新工艺将是催化裂化发
展 的重点。
【 关键 词】 炼油催 化; 裂化技术
1 . 我 国炼 油 行 业 的 发 展 现 状
我国2 0 1 0年石油 消费量 为 4 . 5 5 亿 吨 .随着 国 民经 济 的持续增 长. 到2 0 2 0 年石 油消费 量将 比 2 0 1 0年增长 3 2 %一 3 6 %. 即6 . 0 — 6 . 2 亿 吨. 如不加有 效控制 . 可能达 到 6 . 5 亿 吨 我 国石油对外 依存度 将超 过6 5 %. 到2 0 3 0 年将 更高 。 从 世界石 油发展趋势 看 , 2 0 3 0 年前 . 石油 仍 将是世 界主要 能源来 源 .特 别是石 油液体 运输燃 料的 主要来 源 C E R A( 美 国剑桥 能源 研究 协会 )预测 2 0 2 0年 世界 石 油消 费量 为 4 6 . 4亿 吨. 供应量 为 4 5 . 4 亿 吨 I E A ( 国际能源机构 ) 预测 2 0 3 0年世 界 石油 消费量 为 5 1 . 1 亿吨. 供应 量为 5 1 . 1 亿吨. 基 本持平 我 国煤 制 油技术 虽取 得 了突破 . 但煤 烃转 化系数 较高 , 煤 直接液 化为 5 : 1 , 间接液化 为 5 . 3 : 1 . 预计 2 0 2 0年煤制油替代 量约为 1 0 0 0万吨 。生物 质 燃料 . 替代量 也不大 . 中长期 还 只能作为 石油 的补充能 源 据 此 , 天 然原油 加工技 术 的创新 发展 . 将继 续成为 中 国炼 油工业 中长期 发 展 战略 的重点
◇ 科技论坛◇
科技 嚣向导
我国催化裂化工艺技术进展

我国催化裂化工艺技术进展一、本文概述催化裂化(FCC)作为一种重要的石油加工技术,在我国石油工业中占据着举足轻重的地位。
随着科技的不断进步和环保要求的日益严格,我国催化裂化工艺技术也在持续发展和创新。
本文旨在全面概述我国催化裂化工艺技术的最新进展,包括技术原理、工艺流程、催化剂研发、设备改进以及环保措施等方面的内容。
通过对这些方面的深入探讨,本文旨在展示我国催化裂化工艺技术在提高石油资源利用效率、促进石油工业可持续发展以及减少环境污染等方面的积极贡献。
本文还将对催化裂化工艺技术的发展趋势进行展望,以期为相关领域的科研人员和企业提供有益的参考和借鉴。
二、催化裂化工艺技术的基本原理催化裂化(Catalytic Cracking)是一种重要的石油加工过程,主要目的是将重质烃类转化为更有价值的轻质产品,如汽油、煤油和柴油等。
其基本原理是利用催化剂加速烃类分子在高温高压环境下的热裂解反应,使长链烃类断裂成较短的链烃,从而改善产品的品质和产量。
催化裂化工艺主要包括热裂化和催化裂化两个阶段。
热裂化是在没有催化剂的情况下,通过高温使烃类分子发生热裂解,生成较小的烃分子。
然而,这个过程的选择性较差,会产生大量的裂化气和焦炭,导致产品收率较低。
催化裂化则是在热裂化的基础上引入催化剂,通过催化剂的选择性吸附和表面酸性,使得烃类分子在较低的温度下就能发生裂解,同时提高裂解的选择性和产品的收率。
催化剂的活性、选择性和稳定性对催化裂化过程的影响至关重要。
在催化裂化过程中,烃类分子首先被催化剂表面的酸性位点吸附,然后在催化剂的作用下发生裂解反应。
生成的较小烃分子随后从催化剂表面脱附,进入气相,最后通过冷凝和分离得到所需的产品。
随着科技的不断进步,我国的催化裂化工艺技术也在不断发展。
新型的催化剂、反应器和工艺条件的优化等技术的发展,使得催化裂化过程的效率和选择性得到了显著提高,为我国石油工业的发展做出了重要贡献。
三、我国催化裂化工艺技术的现状我国催化裂化工艺技术自上世纪五十年代引进至今,经历了从引进消化到自主创新的发展历程,目前已经形成了具有自主知识产权的催化裂化工艺技术体系。
催化催化裂化技术
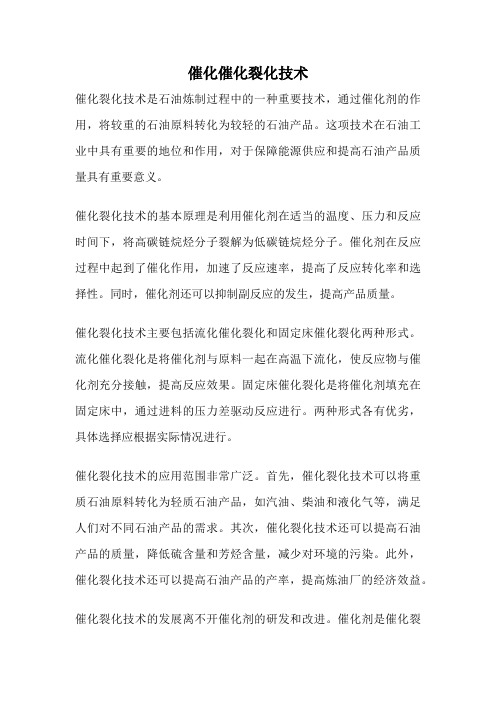
催化催化裂化技术催化裂化技术是石油炼制过程中的一种重要技术,通过催化剂的作用,将较重的石油原料转化为较轻的石油产品。
这项技术在石油工业中具有重要的地位和作用,对于保障能源供应和提高石油产品质量具有重要意义。
催化裂化技术的基本原理是利用催化剂在适当的温度、压力和反应时间下,将高碳链烷烃分子裂解为低碳链烷烃分子。
催化剂在反应过程中起到了催化作用,加速了反应速率,提高了反应转化率和选择性。
同时,催化剂还可以抑制副反应的发生,提高产品质量。
催化裂化技术主要包括流化催化裂化和固定床催化裂化两种形式。
流化催化裂化是将催化剂与原料一起在高温下流化,使反应物与催化剂充分接触,提高反应效果。
固定床催化裂化是将催化剂填充在固定床中,通过进料的压力差驱动反应进行。
两种形式各有优劣,具体选择应根据实际情况进行。
催化裂化技术的应用范围非常广泛。
首先,催化裂化技术可以将重质石油原料转化为轻质石油产品,如汽油、柴油和液化气等,满足人们对不同石油产品的需求。
其次,催化裂化技术还可以提高石油产品的质量,降低硫含量和芳烃含量,减少对环境的污染。
此外,催化裂化技术还可以提高石油产品的产率,提高炼油厂的经济效益。
催化裂化技术的发展离不开催化剂的研发和改进。
催化剂是催化裂化反应的核心,直接影响着反应的效果和产品的质量。
目前,石油工业中主要采用的催化剂是沸石型催化剂和金属催化剂。
沸石型催化剂具有较高的活性和选择性,能够有效地促进裂化反应的进行。
金属催化剂具有良好的抗中毒性能和稳定性,能够提高催化剂的使用寿命。
催化裂化技术的研究和应用还存在一些挑战和问题。
首先,催化剂的选择和制备是关键问题,需要探索新的催化剂材料和合成方法。
其次,催化剂的失活和再生问题也需要解决,以延长催化剂的使用寿命和降低生产成本。
此外,催化裂化技术的节能、环保和安全性问题也需要重视和解决。
催化裂化技术是石油工业中一项重要的技术,对于提高石油产品质量、增加产能和保障能源供应具有重要意义。
国内外催化裂化技术的新进展 文献综述

国内外催化裂化技术的新进展1、国内催化剂技术进展随着我国炼油工业的发展,对催化裂化催化剂的要求也不短变化。
本文介绍一下能进一步提高重油的裂化能力,满足催化裂化原料重质的需求的重油催化剂。
由于我国催化裂化装置重油掺炼水平较高,进而促进了重油催化裂化催化剂的发展。
我国重油催化剂的主要突出表现在:很强的重油裂化能力、良好的抗重金属污染能力、较低的干气和焦化产率以及较低的催化剂单耗。
催化裂化催化剂性能必须满足催化裂化的不同要求,如原料、装置工艺、产物分布、油品质量、环保法规等。
炼厂增效和装置运行需求决定了催化裂化催化剂的性能要求,近年来除了对催化剂的常规要求如满足抗磨损、低价格、目的产品收率高、汽油辛烷值较高等方面的要求外,催化剂在适合加工重油原料、改善油品质量(如汽油烯烃、硫含量)、满足特殊的产品分布需求(如多产柴油、低碳烯烃等)、满足转化和产品需要的催化裂化新工艺相匹配的催化剂以及适应环境保护的需要等方面做了许多工作。
国内石科院、等单位在催化材料的研究以及与催化剂有关的分子筛、基质等材料的开发方面取得了较大的进展。
在渣油FCC催化剂方面注重原位合成分子筛技术、分子筛超稳化改性技术、基质抗重金属技术以及基质孔结构和酸性控制技术等;在降烯烃催化剂方面多采用REUSY沸石或复合沸石作为降烯烃催化剂的活性组分,如RIPP开发了特殊氧化物改进性分子筛表面技术,兰州石化研究院开发了HRSY系列以高稀土超稳Y沸石和超稳稀土Y沸石为主的多元活性组分以及多元活性组分的符合改进性技术;在多产烯烃催化剂方面,注重择形分子筛ZSM—5及其改性技术。
重质原油/含酸原油的加工、向石油化工延伸增加炼油装置效益以及因环保要求提高燃料油产品质量和限制装置污染物排放是今后工作的重点,新的FCC工艺技术的开发主要围绕这些主题进行。
同时一些新的设备,如新型喷嘴、快分、终端设备、气提装置和再生器等都有已经成功地在工业FCC装置使用。
FCC装置是的大型化使得干气的利用具有经济性,而FCC装置加工含氧化物也是一些炼油企业提高效益的有效途径。
- 1、下载文档前请自行甄别文档内容的完整性,平台不提供额外的编辑、内容补充、找答案等附加服务。
- 2、"仅部分预览"的文档,不可在线预览部分如存在完整性等问题,可反馈申请退款(可完整预览的文档不适用该条件!)。
- 3、如文档侵犯您的权益,请联系客服反馈,我们会尽快为您处理(人工客服工作时间:9:00-18:30)。
我国催化裂化技术发展现状及前景左丽华(石油化工科学研究院,北京,100083)概括论述了我国催化裂化发展现状和世界FCC技术的最新发展水平,分析和比较了我国FCC技术与世界先进水平的差距,初步提出我国催化裂化技术的发展前景。
关键词:催化裂化现状最新水平差距前景1 概况流化催化裂化(FCC)是现代化炼油厂用来改质重质瓦斯油和渣油的核心技术,是炼厂获取经济效益的一种重要方法。
据统计,截止到1999年1月1日,全球原油加工能力为015.48 Mt/a,其中催化裂化装置的加工能力为668.37 Mt/a,约占一次加工能力的16.6%,居二次加工能力的首位。
美国原油加工能力为821.13 Mt/a,催化裂化能力为271 Mt/a,居界第一,催化裂化占一次加工能力的比例为33.0%。
我国催化裂化能力达66.08 Mt/a,约占一次加工能力的38.1%,居世界第二位。
我国石油资源中,原油大部分偏重,轻质油品含量低,这就决定了炼油工业必须走深加工的路线。
近十几年来,催化裂化掺炼渣油量在不断上升,已居世界领先地位。
催化剂的制备技术已取得了长足的进步,国产催化剂在渣油裂化能力和抗金属污染等方面均已达到或超过国外的水平。
在减少焦炭、取出多余热量、催化剂再生、能量回收等方面的技术有了较大发展。
2 现代催化裂化技术发展特点及趋势影响FCC未来发展的重要因素将是:原油价格、满足环保要求、新燃料规格、石油化工原料需求和渣油加工。
环保法规已成为FCC技术发展的主要推动力。
FCC已从简单解决诸如汽油、柴油、液化气、抗金属等其中的一、二个问题转向要同时解决多个矛盾的组合。
80年代以来,催化裂化技术的进展主要体现在两个方面:① 开发成功掺炼渣油(常压渣油或减压渣油)的渣油催化裂化技术(称为渣油FCC,简写为RFCC);② 催化裂化家族技术,包括多产低碳烯烃的DCC技术,多产异构烯烃的MIO技术和最大量生产汽油、液化气的MGG技术。
2.1 RFCC工艺技术1980年世界上专门设计用于RFCC的生产能力几乎为零,而到1996年其生产能力已达100.5 Mt/a,约占催化裂化总能力(约650 Mt/a)的16%,进入90年代,RFCC的势头有增无减,特别是亚太地区更显得强劲。
如1993-1995年计划进行新建和改建的装置就有42套,其中新建17套。
新建装置中RFCC占大多数,共有12套,除一套为Shell石油公司在美国路易斯安那州的Narco炼油厂外,其余的大都建在东亚地区的中国、日本、韩国、新加坡和泰国。
未来世界FCC装置的能力将继续以1%的速度增长,其中RFCC生产能力也将随之增长。
2.1.1 RFCC原料特征世界RFCC装置原料中渣油的平均量为15%~20%。
从国外各大公司对原料的要求来看,残炭与金属两个指标已分别达到8%和20 μg/g。
而国内渣油催化裂化原料的残炭一般达到6%,金属15 μg/g,与国外水平相比,尚有潜力。
中国石化集团公司FCC装置中约80%都掺炼不同比例的渣油,平均掺渣比约为26%,1989-1997年,掺炼重质油的比例从18.52%增至43.64%。
我国大庆石蜡基原油具有残炭低、金属含量低的特点,其减压渣油的残炭为8.95%,金属为7 μg/g,所以大庆减压渣油可以直接进行催化裂化。
前郭炼油厂已进行了大庆全减压渣油催化裂化的尝试,但未见国外全减压渣油催化裂化的报道。
2.1.2 RFCC工艺技术及硬件设备目前世界上RFCC的主要工艺有Kellogg公司的HOC、UOP公司的RCC、S&W公司的RFCC、Shell公司的RFCC、IFP/Total公司的R2R和Exxon公司的Flexicracking等。
各种工艺特点见表1。
这些工艺虽各有特点,但在解决RFCC问题的技术措施上却大致相近。
总体而言,重油FCC关键设备和工艺的主要改进情况列于表2。
表1 国外几家公司RFCC技术特征表2 重油FCC关键设备和工艺的改进新开发的RFCC技术和装置包括:两段渣油改质技术-移动床+流化床、毫秒催化裂化(MSCC)工艺、下流式反应器与上流式再生器组合构型和NEXCC新型催化裂化装置、双提升管加工高康氏残炭的重量油FCC和FCC短接触时间的改进。
FCC与加氢技术相结合也是一种发展方向。
渣油两段改质技术,用于多产汽油、柴油和喷气燃料。
其优点是液体产物增加,而气体和/或焦炭产率减少。
第一段降低渣油的康氏残炭和金属含量,第二段进行FCC反应。
移动床的改质是在气相短时间的热转化条件下进行。
MSCC反应器的进料垂直注射于由催化剂向下流动所形成的帘子,实现了毫秒接触,反应产物与催化剂水平沿着反应区穿过,实现剂气快速分离。
快速的剂气分离和小空间的反应区,减少了非理想的二次反应,提高目的产物的选择性,汽油和烯烃产率增加、焦炭产率减少,能更好地加工重质原料,Ni和V对催化剂的影响减轻,投资费用较低。
目前MSCC的应用情况:150 kt/a验证装置于1993年运行。
第一套工业装置(2800 kt/a),位于美国新泽西州,将Coast Eagle Point Oil Co(ECPOC)传统的FCC装置改造成MSCC设计。
1994年11月开始运转,到1998年1月已运转37个月,开工率达98.2%。
第二套工业装置(设计能力5000 kt/a)建在路易斯安那州的Trans American公司的炼油厂中,1999年开工。
国外在80年代初就有下流式反应器的专利及设计构思,如美国Mobil公司在1983年5月31日发布的专利-带有下流式反应器提升管的FCC反应器;美国Texaco公司1985年4月30日通过公告的专利-催化裂化系统(即下流式弹射反应器和分散相提升管再生器);Kellogg 公司催化裂化专家撰文中设想的未来型FCC/HOC装置。
UOP公司发表的最新专利,提出了下流式反应器与上流式再生器的组合构型。
下流式反应器与常规上流式反应器相比的优点是:由于催化剂在反应器内依靠重力下行,没有催化剂最小提升速度的问题,因而无返混、无偏流,油剂接触均匀、混合迅速、易于实现高温、短接触时间裂化以改善产品分布。
原料适应性强,操作上有更大灵活性。
在采用多个小直径下流式反应器时,不仅能保证固体催化剂分布好,也能对不同质量的进料分别进行裂化。
由于避免了催化剂返混,减少了油气的再裂化,因而能减轻催化剂受金属中毒的不良影响。
可提高装置中催化剂的利用率,从而增加汽油选种性,提高汽油辛烷值并使催化剂系统藏量减少1/5~1/10。
由于不用高速气化喷嘴,可显著减少对催化剂和设备的磨耗和磨损。
可改进装置中催化焦的选种性,从而相对降低焦炭的生成量。
能使催化剂迅速从下流式反应器中完成反应的油料中分离出来,并用最少的汽提量完全脱除可汽提烃。
该专利发明的优势在于:FCC反应将重质烃在催化剂存在下裂化成低沸点产物;FCC反应器--再生器构型安排合理,减少了大型反应器和再生器;改善了进料和催化剂的接触,也改善了产物与催化剂的分离。
NEXCC被称为下一代的催化裂化装置,将由位于芬兰Porvoo的Neste OY公司实现工业化。
与常规FCC装置相比,具有费用低、性能优良的特点。
而且汽油加轻质烯烃的转化率可达85%~90%(常规FCC装置转化率只有70%~75%)。
NEXCC工艺采用两台组合在一起的循环裂化床反应器,其中一台为反应器,另一台为催化剂再生器。
在同一受压壳体内,反应器在再生器内。
此外采用多入口旋风分离器取代了常规的旋风分离器。
进料油、催化剂和输送气体从NEXCC装置的下部进入裂化反应器。
在环形反应器中,催化剂裂化油料。
待生剂送到装置的下部进再生器,待生剂烧焦再生,同时使催化剂升温,并借助燃烧用的空气将催化剂提升到再生器的顶部。
据称,该新装置操作较容易、灵活,也易改换催化剂和原料油。
NEXCC采用较苛刻的条件,以超过常规FCC的产物产率。
如催化剂循环量比常规FCC 多2~3 倍、反应温度600~650℃(常规FCC为530~550℃)、剂油接触时间只有1~2 s (常规5~7 s)。
在这样的条件下操作才能允许有利的反应进行。
在催化裂化装置部分结构的革新方面涉及:多点进料改进产品性质,再生剂与待生剂预混合系统,用下流式反应器加工高碱原料,侧向安装的FCC二段汽提器,FCC待生催化剂分布管。
2.2 催化裂化家族技术80年代末我国进行了多种低碳烯烃技术的开发,目前开发成功并实现工业应用的技术有:DCC、MGG、MIO技术。
这些新工艺的出现为炼油和石化相结合以及生产清洁燃料开辟了经济可行的途径。
DCC技术以重质烃为原料,如VGO、VGO掺脱沥青、VGO掺焦化蜡油及VGO掺渣油等。
以流化催化裂化为基础进行延伸,在工艺、工程和催化剂配方上进行革新,以多产丙烯为目的的DCC-Ⅰ型,采用石蜡基原料时,丙烯产率可达23%;而以多产异构烯烃为目的的DCC-Ⅱ型,在用石蜡基原料时,异丁烯加异戊烯产率接近13%,同时得到14%丙烯。
目前已有多套工业装置在中国国内投产,国内尚有几套FCC装置正准备改造为DCC装置。
泰国也已建成700 kt/a催化裂化装置,并顺利投产。
MGG是以减压渣油、掺渣油和常压渣油等为原料的最大量生产富含烯烃的液态烃,同时最大生产高辛烷值汽油的工艺技术,与其他同类工艺的差别在于它在多产液态烃下还能有较高的汽油产率,并且可以用重油作原料(包括常压渣油)。
反应温度在510~540℃时,液化气产率可达25%~35%(摩尔比),汽油产率40%~55%(摩尔比)。
液化气加汽油产率为70%~80%。
汽油RON一般为91~94,诱导期为500~900 min。
这一技术是以液化气富含烯烃、汽油辛烷值高和安定性好为特点的,现已有多套装置应用。
MIO技术是以掺渣油为原料,较大量地生产异构烯烃和汽油为目的产物的工艺技术。
1995年3-6月在中国兰州炼化总厂实现了工业化。
以石蜡基为原料时,缩短反应时间和采取新的反应系统,异构烯烃的产率高达15%(摩尔比)。
催化裂化家族技术的发展与建设将为下游化工装置提供宝贵的化工原料。
近来,国外在这一领域的研究也相当活跃,预计在21世纪这类技术会得到广泛应用。
2.3现代FCC催化剂技术水平及发展趋势FCC催化剂的技术进步转向开发新沸石及沸石的改性、特定性质的基质及新的制备技术。
FCC催化剂的活性组分已由单组元转向双多沸石复合组元,FCC催化剂技术已从传统的化学制备转变为现代的多种功能组件的物理组装。
由于原油的日益重质化和劣质化,金属污染物、高分子的沥青和胶质以及硫、氮等杂原子化合物的总量有明显增加的趋势,给渣油裂化带来了一系列困难,特别是对裂化催化剂性能的要求越来越高。
因此加快改进和研制开发更高性能的渣油裂化催化剂是摆在炼油界面前的重大课题之一。