零缺陷抽样规定
零缺陷抽样标准
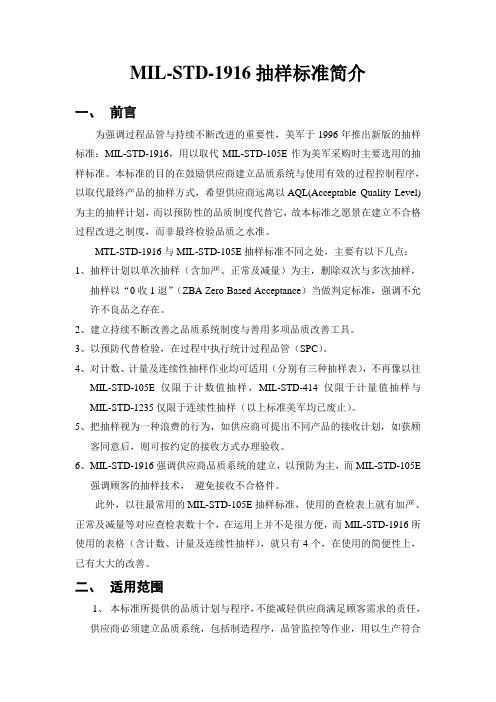
MIL-STD-1916抽样标准简介一、前言为强调过程品管与持续不断改进的重要性,美军于1996年推出新版的抽样标准:MIL-STD-1916,用以取代MIL-STD-105E作为美军采购时主要选用的抽样标准。
本标准的目的在鼓励供应商建立品质系统与使用有效的过程控制程序,以取代最终产品的抽样方式,希望供应商远离以AQL(Acceptable Quality Level)为主的抽样计划,而以预防性的品质制度代替它,故本标准之愿景在建立不合格过程改进之制度,而非最终检验品质之水准。
MTL-STD-1916与MIL-STD-105E抽样标准不同之处,主要有以下几点:1、抽样计划以单次抽样(含加严、正常及减量)为主,删除双次与多次抽样,抽样以“0收1退”(ZBA Zero Based Acceptance)当做判定标准,强调不允许不良品之存在。
2、建立持续不断改善之品质系统制度与善用多项品质改善工具。
3、以预防代替检验,在过程中执行统计过程品管(SPC)。
4、对计数、计量及连续性抽样作业均可适用(分别有三种抽样表),不再像以往MIL-STD-105E仅限于计数值抽样,MIL-STD-414仅限于计量值抽样与MIL-STD-1235仅限于连续性抽样(以上标准美军均已废止)。
5、把抽样视为一种浪费的行为,如供应商可提出不同产品的接收计划,如获顾客同意后,则可按约定的接收方式办理验收。
6、MIL-STD-1916强调供应商品质系统的建立,以预防为主,而MIL-STD-105E强调顾客的抽样技术,避免接收不合格件。
此外,以往最常用的MIL-STD-105E抽样标准,使用的查检表上就有加严、正常及减量等对应查检表数十个,在运用上并不是很方便,而MIL-STD-1916所使用的表格(含计数、计量及连续性抽样),就只有4个,在使用的简便性上,已有大大的改善。
二、适用范围1、本标准所提供的品质计划与程序,不能减轻供应商满足顾客需求的责任,供应商必须建立品质系统,包括制造程序,品管监控等作业,用以生产符合顾客品质要求的产品。
C=0抽样方案
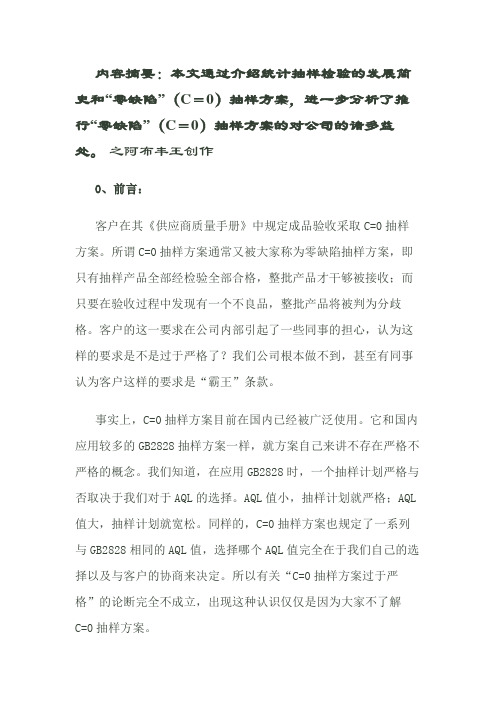
内容摘要:本文通过介绍统计抽样检验的发展简史和“零缺陷”(C=0)抽样方案,进一步分析了推行“零缺陷”(C=0)抽样方案的对公司的诸多益处。
之阿布丰王创作0、前言:客户在其《供应商质量手册》中规定成品验收采取C=0抽样方案。
所谓C=0抽样方案通常又被大家称为零缺陷抽样方案,即只有抽样产品全部经检验全部合格,整批产品才干够被接收;而只要在验收过程中发现有一个不良品,整批产品将被判为分歧格。
客户的这一要求在公司内部引起了一些同事的担心,认为这样的要求是不是过于严格了?我们公司根本做不到,甚至有同事认为客户这样的要求是“霸王”条款。
事实上,C=0抽样方案目前在国内已经被广泛使用。
它和国内应用较多的GB2828抽样方案一样,就方案自己来讲不存在严格不严格的概念。
我们知道,在应用GB2828时,一个抽样计划严格与否取决于我们对于AQL的选择。
AQL值小,抽样计划就严格;AQL 值大,抽样计划就宽松。
同样的,C=0抽样方案也规定了一系列与GB2828相同的AQL值,选择哪个AQL值完全在于我们自己的选择以及与客户的协商来决定。
所以有关“C=0抽样方案过于严格”的论断完全不成立,出现这种认识仅仅是因为大家不了解C=0抽样方案。
需要说明的是,该客户的《供应商质量手册》是根据ISO/TS16949(即GB/T18305)建立的,而ISO/TS16949在7.1.2 条款中明确要求接收水平必须是零缺陷。
(ISO/TS16949 7.1.2接收准则:组织应规定接收准则,要求时,由顾客批准。
对于计数型数据抽样,接收水平应是零缺陷。
)所以,客户的要求是根据的,不存在任何“霸王”要求。
1、抽样检验简介抽样检验又称为统计抽检检验,是指从交验的一批产品中,随机抽取若干单位产品组成样本进行检验,通过对样本的检验结果对整批产品做出质量判定的过程。
我们知道,检验是不发生价值的工作,因此如何更经济、快捷的进行检验就直接关系到生产的成本和效率。
零缺陷(C=0)抽样方案

零缺陷概念的产生:被誉为“全球质量管理大师”、“零缺陷之父”和“伟大的管理思想家”的菲利浦·克劳士比(Philip B. Crosby)在20世纪60年代初提出“零缺陷”思想,并在美国推行零缺陷运动。
后来,零缺陷的思想传至日本,在日本制造业中得到了全面推广,使日本制造业的产品质量得到迅速提高,并且领先于世界水平,继而进一步扩大到工商业所有领域。
零缺陷理论核心是:“第一次就把事情做对”。
所谓"零缺陷"抽样方案,简单的说,就是不管你的批量和样本大小如何,其抽样检验的接收数Ac=0,即"0收1退"。
举例:某客户在其《供应商质量手册》中规定成品验收采用 C=0 抽样方案。
所谓 C=0 抽样方案通常又被大家称为零缺陷抽样方案,即只有抽样产品全部经检验全部合格,整批产品才能够被接收;而只要在验收过程中发现有一个不良品,整批产品将被判为不合格。
客户的这一要求在公司内部引起了一些同事的担心,认为这样的要求是不是过于严格了?公司根本做不到,甚至有同事认为客户这样的要求是“霸王”条款。
事实上,C=0 抽样方案目前在国内已经被广泛使用。
它和我们中国应用较多的GB/T2828.1-2012抽样方案一样,就方案本身来讲不存在严格不严格的概念。
在应用GB/T2828.1-2012时,一个抽样计划严格与否取决于我们对于 AQL 的选择。
AQL 值小,抽样计划就严格;AQL 值大,抽样计划就宽松。
同样的,C=0 抽样方案也规定了一系列与GB/T2828.1-2012 相同的 AQL值,选择哪个AQL 值完全在于我们自己的选择以及与客户的协商来决定。
所以有关“C=0 抽样方案过于严格”的论断完全不成立,出现这种认识仅仅是因为大家不了解C=0 抽样方案。
需要说明的是,该客户的《供应商质量手册》是根据IATF16949:2016 建立的,而IATF16949 :2016标准条款8.6.6中明确要求接收水平必须是零缺陷。
C=0-抽样方案介绍
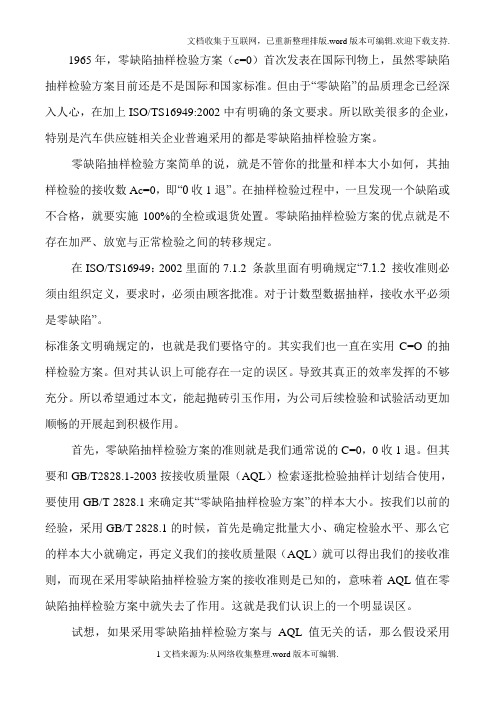
1965年,零缺陷抽样检验方案(c=0)首次发表在国际刊物上,虽然零缺陷抽样检验方案目前还是不是国际和国家标准。
但由于“零缺陷”的品质理念已经深入人心,在加上ISO/TS16949:2002中有明确的条文要求。
所以欧美很多的企业,特别是汽车供应链相关企业普遍采用的都是零缺陷抽样检验方案。
零缺陷抽样检验方案简单的说,就是不管你的批量和样本大小如何,其抽样检验的接收数Ac=0,即“0收1退”。
在抽样检验过程中,一旦发现一个缺陷或不合格,就要实施100%的全检或退货处置。
零缺陷抽样检验方案的优点就是不存在加严、放宽与正常检验之间的转移规定。
在ISO/TS16949:2002里面的7.1.2 条款里面有明确规定“7.1.2 接收准则必须由组织定义,要求时,必须由顾客批准。
对于计数型数据抽样,接收水平必须是零缺陷”。
标准条文明确规定的,也就是我们要恪守的。
其实我们也一直在实用C=O的抽样检验方案。
但对其认识上可能存在一定的误区。
导致其真正的效率发挥的不够充分。
所以希望通过本文,能起抛砖引玉作用,为公司后续检验和试验活动更加顺畅的开展起到积极作用。
首先,零缺陷抽样检验方案的准则就是我们通常说的C=0,0收1退。
但其要和GB/T2828.1-2003按接收质量限(AQL)检索逐批检验抽样计划结合使用,要使用GB/T 2828.1来确定其“零缺陷抽样检验方案”的样本大小。
按我们以前的经验,采用GB/T 2828.1的时候,首先是确定批量大小、确定检验水平、那么它的样本大小就确定,再定义我们的接收质量限(AQL)就可以得出我们的接收准则,而现在采用零缺陷抽样检验方案的接收准则是已知的,意味着AQL值在零缺陷抽样检验方案中就失去了作用。
这就是我们认识上的一个明显误区。
试想,如果采用零缺陷抽样检验方案与AQL值无关的话,那么假设采用GB/T2828.1里面的正常检验一次抽样方案II级检验水平的话,意味着样本量是统一的。
aql c=0抽样标准

aql c=0抽样标准AQL C=0抽样标准。
AQL(Acceptable Quality Level)是指可接受质量水平,是一种用于产品质量抽样检验的标准。
在AQL C=0抽样标准下,接受质量水平为0,即不允许有任何缺陷品存在。
这种抽样标准通常应用于对产品质量要求非常高的行业,如医疗器械、航空航天等领域。
本文将介绍AQL C=0抽样标准的相关内容,以便读者更好地了解和应用这一标准。
首先,AQL C=0抽样标准的核心是零缺陷。
在实际抽样检验中,抽样数量和接受数都为0,即对每批产品进行全数检验,确保产品的质量达到最高标准。
这种严格的抽样标准要求生产企业在生产过程中严格控制每一个环节,确保产品的质量不容忽视。
其次,AQL C=0抽样标准的实施需要依靠科学的抽样方法和严格的质量管理体系。
在抽样过程中,需要根据产品的特性和生产批次确定合适的抽样数量和抽样方法,确保抽样的代表性和可靠性。
同时,企业需要建立健全的质量管理体系,包括从原材料采购到生产制造再到产品出厂的全过程质量控制,确保产品质量的稳定和可靠。
此外,AQL C=0抽样标准的实施还需要依靠先进的检测设备和技术手段。
企业需要投入大量的人力、物力和财力,引进先进的检测设备和技术手段,确保对产品质量的全面检测和监控。
只有通过科学、准确的检测手段,才能有效地保证产品质量的稳定和可靠。
最后,AQL C=0抽样标准的实施对企业来说既是一种挑战,也是一种机遇。
挑战在于企业需要投入更多的资源和精力来保证产品质量的全面可靠,这对企业的生产制造和管理水平提出了更高的要求。
但与此同时,AQL C=0抽样标准也为企业提供了一个展示自身实力和竞争优势的机会,通过不断提升产品质量,企业可以赢得消费者的信任和市场的认可。
总之,AQL C=0抽样标准是一种对产品质量要求极高的抽样标准,其核心是零缺陷。
企业在实施AQL C=0抽样标准时需要依靠科学的抽样方法、严格的质量管理体系和先进的检测设备和技术手段,以确保产品质量的稳定和可靠。
零缺陷抽样规定
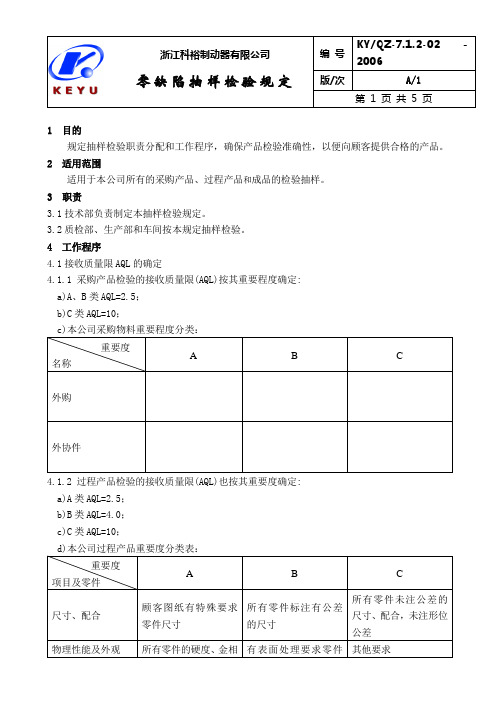
1 目的规定抽样检验职责分配和工作程序,确保产品检验准确性,以便向顾客提供合格的产品。
2 适用范围适用于本公司所有的采购产品、过程产品和成品的检验抽样。
3职责3.1技术部负责制定本抽样检验规定。
3.2质检部、生产部和车间按本规定抽样检验。
4 工作程序4.1接收质量限AQL的确定4.1.1 采购产品检验的接收质量限(AQL)按其重要程度确定:a)A、B类AQL=2.5;b)C类AQL=10;4.1.2 过程产品检验的接收质量限(AQL)也按其重要度确定:a)A类AQL=2.5;b)B类AQL=4.0;c)C类AQL=10;4.2检验分类4.2.1采购产品(包括外协件)的检验采用计数抽样正常检查一次抽样方案。
本公司不允许二次抽样。
接收准则必须满足零缺陷,不合格则退货或100%全检。
4.2.2过程产品检验:采用首检和巡检相结合方式。
每班开始生产时操作者自检合格后再由检验员按相应规定检验,记录检验结果;若不合格应要求返工或重新生产,直至检验员确认首检合格方能批量生产;检验员按生产控制计划对过程产品进行巡检,一旦发现不合格,应立即停止生产,查找原因,并对已加工的产品进行全检。
重新开机后应连续抽检不少于3只工件,全部合格后方可继续生产。
4.2.3成品检验:a)汽车制动钳按QC/T592-1999规定进行试验、检验,接收准则为零缺陷。
b)其它采用计数抽样正常检验一次抽样方案,接收准则为零缺陷。
4.5具体检测项目,技术要求和检验方法执行相应的检验规程、控制计划。
4.6合格判定4.6.1若样本中不合格品数C=0(即AC = 0) , 则判批合格;4.6.2若样本中不合格品数C≥1(即AC≥1) , 则判批不合格。
注: 交验批必须是在同一条件下制造出来的产品。
4.7其他4.7.1 凡属A、B类的原材料、外购件、外协件都必须附有质保单,其化学成份及力学性能应符合有关国家标准或图纸要求。
4.7.2若顾客有要求时,按顾客要求执行。
什么是“零缺陷”抽样?与正常抽样有何不同?

什么是“零缺陷”抽样?与正常抽样有何不同?所谓“零缺陷”抽样方案,简单的说,就是不管你的批量和样本大小如何,其抽样检验的接收数Ac=0,即“0收1退”。
很多人会有疑问,这样会不会太理想、太严格了,供应商根本不可能做到?本文将通过对正常抽样和“零缺陷”抽样的介绍和比较为你详解“零缺陷”抽样的理念与做法。
抽样检验概述抽样检验是指从交验的一批产品中,随机抽取若干单位产品组成样本进行检验,通过对样本的检验结果对整批产品做出质量判定的过程。
抽样检验又分为统计抽检检验和非统计抽样检验。
非统计抽样(已淘汰):按照固定的百分比例来抽样。
存在两个方面的问题:大批宽、小批严;总体数量多的时候,抽样数很大,不具经济性。
统计抽样:是美国贝尔实验室的道奇和罗米格于1929年创立的,它和1924年休哈特提出的统计过程控制(SPC)一起被视为质量管理从质量检验阶段进入统计质量控制阶段的两个标志性成果。
其标准在美国是MIL-STD-105E(已被MIL-STD-1916取代),国标是GB2828。
第一部分:正常抽样正常抽样的标准1,检验水平的选择原则1)没有特殊规定时,首先采取一般检验水平II2)比较检查费用,若每个样品的检查费用为a,处理一个判批不合格样品的费用为b,检查水平应遵循:a) a>b,选择检验水平Ib) a<b,选择检验水平III3)另外4 个特殊检验水平S-1、S-2、S-3 和S-4,可用于样本量必须相对地小而且能容许较大抽样风险的情形,例如检验费用极高或者破坏性检验的情形。
4)辨别能力:Ⅰ<Ⅱ<Ⅲ;S-1<S-2<S-3<S42,确定抽样方案根据此前已确定的检验水平与AQL水准制定抽样方案。
在了解如何确定AQL水准之前,需要知道抽样风险的概念。
采用抽样检验时,生产方和使用方都要冒一定的风险。
因为抽样检验是按照一定的抽样方案从批中抽取样本进行检验,根据检验结果及接收准则来判断该批是否接收。
由于样本的随机性,同时它仅是批的一部分,通常还是很少的一部分,所以有可能做出错的判断。
零缺陷抽样方案
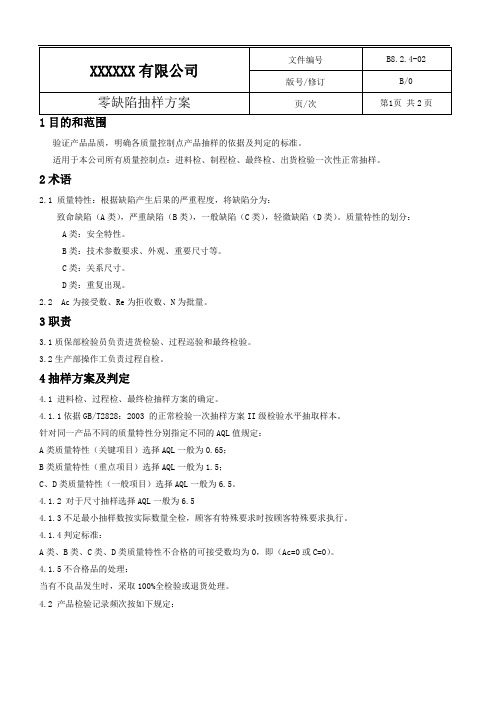
验证产品品质,明确各质量控制点产品抽样的依据及判定的标准。
适用于本公司所有质量控制点:进料检、制程检、最终检、出货检验一次性正常抽样。
2术语2.1 质量特性:根据缺陷产生后果的严重程度,将缺陷分为:致命缺陷(A类),严重缺陷(B类),一般缺陷(C类),轻微缺陷(D类)。
质量特性的划分:A类:安全特性。
B类:技术参数要求、外观、重要尺寸等。
C类:关系尺寸。
D类:重复出现。
2.2 Ac为接受数、Re为拒收数、N为批量。
3职责3.1质保部检验员负责进货检验、过程巡验和最终检验。
3.2生产部操作工负责过程自检。
4抽样方案及判定4.1 进料检、过程检、最终检抽样方案的确定。
4.1.1依据GB/T2828:2003 的正常检验一次抽样方案II级检验水平抽取样本。
针对同一产品不同的质量特性分别指定不同的AQL值规定:A类质量特性(关键项目)选择AQL一般为0.65;B类质量特性(重点项目)选择AQL一般为1.5;C、D类质量特性(一般项目)选择AQL一般为6.5。
4.1.2 对于尺寸抽样选择AQL一般为6.54.1.3不足最小抽样数按实际数量全检,顾客有特殊要求时按顾客特殊要求执行。
4.1.4判定标准:A类、B类、C类、D类质量特性不合格的可接受数均为0,即(Ac=0或C=0)。
4.1.5不合格品的处理:当有不良品发生时,采取100%全检验或退货处理。
4.2 产品检验记录频次按如下规定:控制程序》处理。
4.3质量记录抽样结果记录5个数据:最大值 1个、最小值1个、中间值 3个5相关文件5.1 A8.3-01 不合格品控制程序6相关质量记录6.1 JL8.2.4-02 产品检验记录表6.2 JL8.2.4-07 进货检验记录6.3 JL8.2.4-13 终检检验记录表7本程序更改记录。
浅谈“零缺陷”(C=0)抽样方案
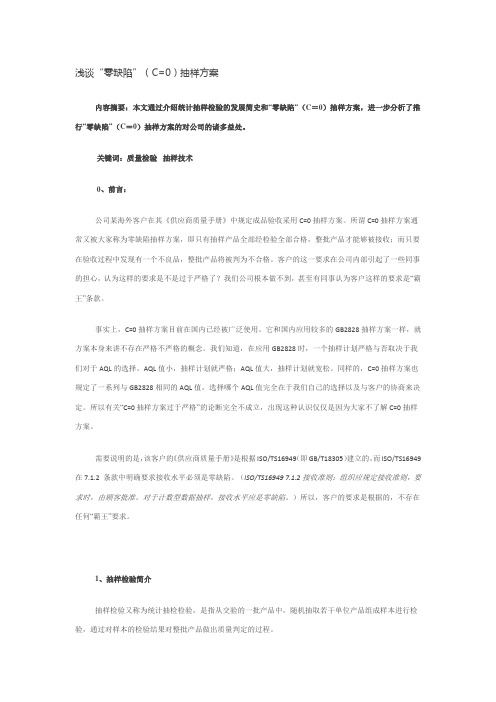
浅谈“零缺陷”(C=0)抽样方案内容摘要:本文通过介绍统计抽样检验的发展简史和“零缺陷”(C=0)抽样方案,进一步分析了推行“零缺陷”(C=0)抽样方案的对公司的诸多益处。
关键词:质量检验抽样技术0、前言:公司某海外客户在其《供应商质量手册》中规定成品验收采用C=0抽样方案。
所谓C=0抽样方案通常又被大家称为零缺陷抽样方案,即只有抽样产品全部经检验全部合格,整批产品才能够被接收;而只要在验收过程中发现有一个不良品,整批产品将被判为不合格。
客户的这一要求在公司内部引起了一些同事的担心,认为这样的要求是不是过于严格了?我们公司根本做不到,甚至有同事认为客户这样的要求是“霸王”条款。
事实上,C=0抽样方案目前在国内已经被广泛使用。
它和国内应用较多的GB2828抽样方案一样,就方案本身来讲不存在严格不严格的概念。
我们知道,在应用GB2828时,一个抽样计划严格与否取决于我们对于AQL的选择。
AQL值小,抽样计划就严格;AQL值大,抽样计划就宽松。
同样的,C=0抽样方案也规定了一系列与GB2828相同的AQL值,选择哪个AQL值完全在于我们自己的选择以及与客户的协商来决定。
所以有关“C=0抽样方案过于严格”的论断完全不成立,出现这种认识仅仅是因为大家不了解C=0抽样方案。
需要说明的是,该客户的《供应商质量手册》是根据ISO/TS16949(即GB/T18305)建立的,而ISO/TS16949在7.1.2条款中明确要求接收水平必须是零缺陷。
(ISO/TS16949 7.1.2接收准则:组织应规定接收准则,要求时,由顾客批准。
对于计数型数据抽样,接收水平应是零缺陷。
)所以,客户的要求是根据的,不存在任何“霸王”要求。
1、抽样检验简介抽样检验又称为统计抽检检验,是指从交验的一批产品中,随机抽取若干单位产品组成样本进行检验,通过对样本的检验结果对整批产品做出质量判定的过程。
我们知道,检验是不产生价值的工作,因此如何更经济、快捷的进行检验就直接关系到生产的成本和效率。
零缺陷抽样规定

零缺陷抽样规定文件编号:QD8.9.1-2016
版本:C/0 页次:1/1 1. 目的
为明确本公司外购产品、自制零部件及成品的验收抽样方案及允收标准,特制定本规定。
2. 范围
本文件适用于本公司外购产品、自制零部件及成品的逐批检验。
3. 接收准则
本公司所有产品数据的接收准则为零缺陷。
4. 抽样计划
4.1 如本公司企业标准或其它三级文件未明确规定其抽样要求的,则其抽样计划按附录规定执行,其样本级别的确定原则如下:
原料入厂检验、工序巡检样本级别:10.0
成品抽样样本级别:4.0
4.2 产品抽样采取一次抽样方案,随机抽取样本,尽量在不同的包装中抽取。
4.3 根据抽取样本的检查结果,如果发现的不合格品数为Ac≤0,则判该批产品为合格批;如果发现的不合格品数Re≥1,则应有相关人员进行再次进行抽检,如果再次检验仍发现不合格品数Re≥1,则应由检验员进行100%检验,或做退货、返工、返修、换货处理。
编制/日期:
审核/日期:
批准/日期:。
零缺陷抽样方案QS/TS

QS9000、ISO/TS16949的要求-零缺陷(A C=0或c=0)抽样检验方案3。
1 企业引进零缺陷抽样方案的必要性在全面介绍零缺陷抽样检验方案前,请先看一看QS9000之4.10.1.1条款(计数特性的接收准则)的要求。
4.10.1.1 计数特性的接收准则计数数据接收抽样计划的接收准则必须是零缺陷。
所有其他情况(如:目视标灌)的接收准则必须由供方形成文件并由顾客批准。
从这一条款不难看出,QS9000标准要求所有计数抽样方案都为零缺陷,也即抽样验收的合格判定数为零,即“0收1不收”。
这一条款对企业来说,是一很大挑战。
在满足这一条款时,很多企业缺乏科学的抽样表,往往使用GB2828(或MIL-SrD-105E)正常检查一次抽样方案中的样本大小(n)作为零缺陷抽样检验方案的样本大小(n)。
这一作法无论从理论上抑或从实践上都是很不经济的(表3-2显示GB2828之样本数量大大地超过了零缺陷抽样方案对样本数量的要求),为此企业有必要引进零缺陷的抽样方案。
3.2 零缺陷(c=0)抽样方案之发展历史1965年,c=0抽样方案首次发表于国际刊物,1969年首次出书,1981年再版,1983年发行第三版。
零缺陷(c=0)抽样方案目前还不是国际或国家标准,但由于“零缺陷”的品质观念已通行全球,因此欧美很多企业都广泛采用零缺陷(c=0)抽样方案。
从使用者报告中犟示,当抽样方案由MIL-STD-105E改变为c=0的抽样方案时,可节省8%-30%的成本。
从理论上来说,批量及AQL值愈大,节省成本愈多。
3.3 c=0抽样方案的特点任何批量检验的产品,c=0抽样方案均可应用,特别适合孤立批的检验(如从临时供应商处采购)。
c=0抽样方案无加严、放宽转移的规定。
3.4 c=0抽样方案的—些概念(1) 暂扣批(withhold the lot)暂扣批是一个特别的概念,它并不意味着“拒收”,在“零缺陷抽样方案中”,只有抽检样本中“不合格”(nonconformity)为零时才接收(即A c=0)。
零缺陷抽样规定

1 目的规定抽样检验职责分配和工作程序,确保产品检验准确性,以便向顾客提供合格的产品。
2 适用范围适用于本公司所有的采购产品、过程产品和成品的检验抽样。
3职责3.1技术部负责制定本抽样检验规定。
3.2质检部、生产部和车间按本规定抽样检验。
4 工作程序4.1接收质量限AQL的确定4.1.1 采购产品检验的接收质量限(AQL)按其重要程度确定:a)A、B类AQL=2.5;b)C类AQL=10;4.1.2 过程产品检验的接收质量限(AQL)也按其重要度确定:a)A类AQL=2.5;b)B类AQL=4.0;c)C类AQL=10;4.2检验分类4.2.1采购产品(包括外协件)的检验采用计数抽样正常检查一次抽样方案。
本公司不允许二次抽样。
接收准则必须满足零缺陷,不合格则退货或100%全检。
4.2.2过程产品检验:采用首检和巡检相结合方式。
每班开始生产时操作者自检合格后再由检验员按相应规定检验,记录检验结果;若不合格应要求返工或重新生产,直至检验员确认首检合格方能批量生产;检验员按生产控制计划对过程产品进行巡检,一旦发现不合格,应立即停止生产,查找原因,并对已加工的产品进行全检。
重新开机后应连续抽检不少于3只工件,全部合格后方可继续生产。
4.2.3成品检验:a)汽车制动钳按QC/T592-1999规定进行试验、检验,接收准则为零缺陷。
b)其它采用计数抽样正常检验一次抽样方案,接收准则为零缺陷。
4.5具体检测项目,技术要求和检验方法执行相应的检验规程、控制计划。
4.6合格判定4.6.1若样本中不合格品数C=0(即AC = 0) , 则判批合格;4.6.2若样本中不合格品数C≥1(即AC≥1) , 则判批不合格。
注: 交验批必须是在同一条件下制造出来的产品。
4.7其他4.7.1 凡属A、B类的原材料、外购件、外协件都必须附有质保单,其化学成份及力学性能应符合有关国家标准或图纸要求。
4.7.2若顾客有要求时,按顾客要求执行。
C=0-抽样方案介绍

C=0-抽样方案介绍
C=0-抽样方案介绍
C=0-抽样方案介绍
1965年,零缺陷抽样检验方案(c=0)首次发表在国际刊物上,虽然零缺陷抽样检验方案目前还是不是国际和国家标准。
但由于“零缺陷”的品质理念已经深入人心,在加上ISO/TS16949:2002中有明确的条文要求。
所以欧美很多的企业,特别是汽车供应链相关企业普遍采用的都是零缺陷抽样检验方案。
零缺陷抽样检验方案简单的说,就是不管你的批量和样本大小如何,其抽样检验的接收数Ac=0,即“0收1退”。
在抽样检验过程中,一旦发现一个缺陷或不合格,就要实施100%的全检或退货处置。
零缺陷抽样检验方案的优点就是不存在加严、放宽与正常检验之间的转移规定。
在ISO/TS16949:2002里面的7.1.2条款里面有明确规定“7.1.2接收准则必须由组织定义,要求时,必须由顾客批准。
对于计数型数据抽样,接收水平必须是零缺陷”。
标准条文明确规定的,也就是我们要恪守的。
其实我们也一直在实用C=O的抽样检验方案。
但对其认识上可能存在一定的误区。
导致其真正的效率发挥的不够充分。
所以希望通过本文,能起抛砖引玉作用,为公司后续检验和试验活动更加顺畅的开展起到积极作用。
C=0抽样方案
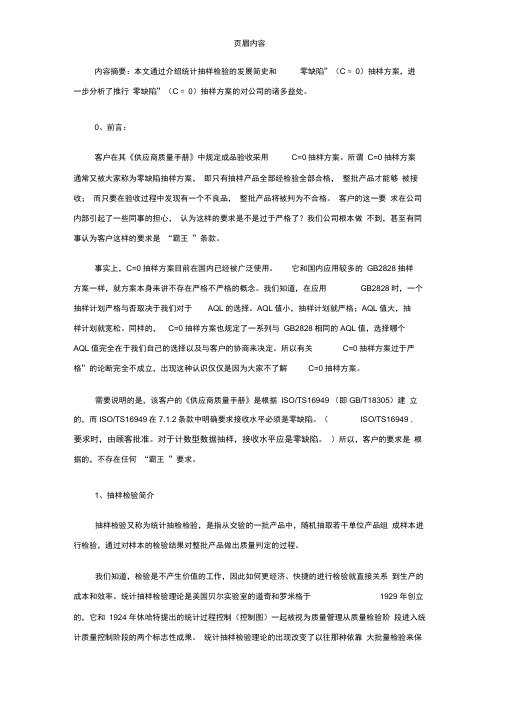
内容摘要:本文通过介绍统计抽样检验的发展简史和零缺陷”(C = 0)抽样方案,进一步分析了推行零缺陷”(C = 0)抽样方案的对公司的诸多益处。
0、前言:客户在其《供应商质量手册》中规定成品验收采用C=0抽样方案。
所谓C=0抽样方案通常又被大家称为零缺陷抽样方案,即只有抽样产品全部经检验全部合格,整批产品才能够被接收;而只要在验收过程中发现有一个不良品,整批产品将被判为不合格。
客户的这一要求在公司内部引起了一些同事的担心,认为这样的要求是不是过于严格了?我们公司根本做不到,甚至有同事认为客户这样的要求是“霸王”条款。
事实上,C=0抽样方案目前在国内已经被广泛使用。
它和国内应用较多的GB2828抽样方案一样,就方案本身来讲不存在严格不严格的概念。
我们知道,在应用GB2828时,一个抽样计划严格与否取决于我们对于AQL的选择。
AQL值小,抽样计划就严格;AQL值大,抽样计划就宽松。
同样的,C=0抽样方案也规定了一系列与GB2828相同的AQL值,选择哪个AQL值完全在于我们自己的选择以及与客户的协商来决定。
所以有关C=0抽样方案过于严格”的论断完全不成立,出现这种认识仅仅是因为大家不了解C=0抽样方案。
需要说明的是,该客户的《供应商质量手册》是根据ISO/TS16949 (即GB/T18305)建立的,而ISO/TS16949在7.1.2条款中明确要求接收水平必须是零缺陷。
(ISO/TS16949 , 要求时,由顾客批准。
对于计数型数据抽样,接收水平应是零缺陷。
)所以,客户的要求是根据的,不存在任何“霸王”要求。
1、抽样检验简介抽样检验又称为统计抽检检验,是指从交验的一批产品中,随机抽取若干单位产品组成样本进行检验,通过对样本的检验结果对整批产品做出质量判定的过程。
我们知道,检验是不产生价值的工作,因此如何更经济、快捷的进行检验就直接关系到生产的成本和效率。
统计抽样检验理论是美国贝尔实验室的道奇和罗米格于1929 年创立的,它和1924 年休哈特提出的统计过程控制(控制图)一起被视为质量管理从质量检验阶段进入统计质量控制阶段的两个标志性成果。
GB2828中的零缺陷抽样方案

GB2828中的零缺陷抽样方案GB2828是中国标准化组织发布的《统一接受质量级别和缺陷限值(AQL)的抽样程序和表》的标准,用于进行零缺陷抽样方案的制定。
这个标准主要用于质量控制,通过抽样的方式来确定产品质量的合格情况。
下面将对GB2828中的零缺陷抽样方案进行详细介绍。
GB2828中的零缺陷抽样方案是在一定的容量或批量情况下,通过少于等于两个样品的检测结果来判断整个批次产品是否合格。
在这个方案中,按照质量级别划分为I级(高)、II级(中)、III级(低)三个级别,不同级别对应不同的采样方案和接收标准。
在GB2828中,主要有两个重要的表格:抽样应接受数表和抽样计划表。
抽样应接受数表是根据质量级别、容量或批量大小和抽样水平来给出的接受和拒收的样本数量。
抽样计划表是根据抽样方案的设计参数,提供具体的抽样计划和样本数量。
这两个表格是制定零缺陷抽样方案的重要参考依据。
在制定零缺陷抽样方案时,首先需要确定产品的质量级别。
质量级别的划分主要基于产品对质量的要求和客户的需求,不同的质量级别对应不同的接受和拒收标准。
其次,需要确定产品的容量或批量大小。
容量或批量大小是指产品的数量,也是抽样方案的重要参数之一,根据不同的容量或批量大小,可以确定不同的抽样水平和样本数量。
最后,需要选择合适的抽样水平。
抽样水平是指在整个容量或批量范围内抽取样本的比例,常用的抽样水平有Ⅰ类水平、Ⅱ类水平和Ⅲ类水平。
不同抽样水平对应的接受和拒收标准不同,可以根据实际情况选择合适的抽样水平。
通过以上步骤确定了质量级别、容量或批量大小和抽样水平后,可以根据GB2828中的抽样应接受数表和抽样计划表得出具体的抽样方案和样本数量。
抽样应接受数表中给出的是在给定的容量或批量大小和抽样水平下,接受和拒收的样本数量。
抽样计划表则给出了具体的抽样方案和样本数量,根据容量或批量大小、抽样水平和质量级别可以找到对应的抽样计划。
制定零缺陷抽样方案的过程主要包括确定质量级别、容量或批量大小、抽样水平和选择相应的抽样计划。
零缺陷抽样标准

MIL-STD-1916抽样标准简介一、前言为强调过程品管与持续不断改进的重要性,美军于1996年推出新版的抽样标准:MIL-STD-1916,用以取代MIL-STD-105E作为美军采购时主要选用的抽样标准。
本标准的目的在鼓励供应商建立品质系统与使用有效的过程控制程序,以取代最终产品的抽样方式,希望供应商远离以AQL(Acceptable Quality Level)为主的抽样计划,而以预防性的品质制度代替它,故本标准之愿景在建立不合格过程改进之制度,而非最终检验品质之水准。
MTL-STD-1916与MIL-STD-105E抽样标准不同之处,主要有以下几点:1、抽样计划以单次抽样(含加严、正常及减量)为主,删除双次与多次抽样,抽样以“0收1退”(ZBA Zero Based Acceptance)当做判定标准,强调不允许不良品之存在。
2、建立持续不断改善之品质系统制度与善用多项品质改善工具。
3、以预防代替检验,在过程中执行统计过程品管(SPC)。
4、对计数、计量及连续性抽样作业均可适用(分别有三种抽样表),不再像以往MIL-STD-105E仅限于计数值抽样,MIL-STD-414仅限于计量值抽样与MIL-STD-1235仅限于连续性抽样(以上标准美军均已废止)。
5、把抽样视为一种浪费的行为,如供应商可提出不同产品的接收计划,如获顾客同意后,则可按约定的接收方式办理验收。
6、MIL-STD-1916强调供应商品质系统的建立,以预防为主,而MIL-STD-105E强调顾客的抽样技术,避免接收不合格件。
此外,以往最常用的MIL-STD-105E抽样标准,使用的查检表上就有加严、正常及减量等对应查检表数十个,在运用上并不是很方便,而MIL-STD-1916所使用的表格(含计数、计量及连续性抽样),就只有4个,在使用的简便性上,已有大大的改善。
二、适用范围1、本标准所提供的品质计划与程序,不能减轻供应商满足顾客需求的责任,供应商必须建立品质系统,包括制造程序,品管监控等作业,用以生产符合顾客品质要求的产品。
- 1、下载文档前请自行甄别文档内容的完整性,平台不提供额外的编辑、内容补充、找答案等附加服务。
- 2、"仅部分预览"的文档,不可在线预览部分如存在完整性等问题,可反馈申请退款(可完整预览的文档不适用该条件!)。
- 3、如文档侵犯您的权益,请联系客服反馈,我们会尽快为您处理(人工客服工作时间:9:00-18:30)。
1 目的
规定抽样检验职责分配和工作程序,确保产品检验准确性,以便向顾客提供合格的产品。
2 适用范围
适用于本公司所有的采购产品、过程产品和成品的检验抽样。
3职责
3.1技术部负责制定本抽样检验规定。
3.2质检部、生产部和车间按本规定抽样检验。
4 工作程序
4.1接收质量限AQL的确定
4.1.1 采购产品检验的接收质量限(AQL)按其重要程度确定:
a)A、B类AQL=2.5;
b)C类AQL=10;
4.1.2 过程产品检验的接收质量限(AQL)也按其重要度确定:
a)A类AQL=2.5;
b)B类AQL=4.0;
c)C类AQL=10;
4.2检验分类
4.2.1采购产品(包括外协件)的检验采用计数抽样正常检查一次抽样方案。
本公司不允许二次抽样。
接收准则必须满足零缺陷,不合格则退货或100%全检。
4.2.2过程产品检验:采用首检和巡检相结合方式。
每班开始生产时操作者自检合格后再由检验员按相应规定检验,记录检验结果;若不合格应要求返工或重新生产,直至检验员确认首检合格方能批量生产;检验员按生产控制计划对过程产品进行巡检,一旦发现不合格,应立即停止生产,查找原因,并对已加工的产品进行全检。
重新开机后应连续抽检不少于3只工件,全部合格后方可继续生产。
4.2.3成品检验:
a)汽车制动钳按QC/T592-1999规定进行试验、检验,接收准则为零缺陷。
b)其它采用计数抽样正常检验一次抽样方案,接收准则为零缺陷。
4.5具体检测项目,技术要求和检验方法执行相应的检验规程、控制计划。
4.6合格判定
4.6.1若样本中不合格品数C=0(即AC = 0) , 则判批合格;
4.6.2若样本中不合格品数C≥1(即AC≥1) , 则判批不合格。
注: 交验批必须是在同一条件下制造出来的产品。
4.7其他
4.7.1 凡属A、B类的原材料、外购件、外协件都必须附有质保单,其化学成份及力学性能应符合有关国家标准或图纸要求。
4.7.2若顾客有要求时,按顾客要求执行。
附表1:零缺陷(C=0)抽样检查表
附表2:零缺陷(C=0)抽样方案与GB/T 2828.1正常检验一次抽样方案之样本量比较
编制/日期:审批/日期:
附表1 零缺陷(C=0)抽样检查表
附表2 零缺陷(C=0)抽样方案与GB/T 2828.1正常检验一次抽样方案之样本量比较。