群钻的特征和使用性能
第十六讲钻削加工二
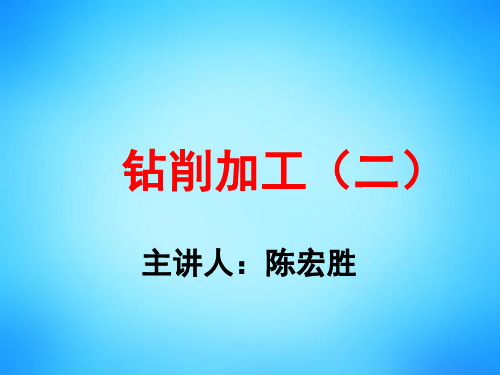
----------------------------------------
2
6.2 钻头的刃磨
修磨部位
修磨月牙 槽
修磨短横 刃
表6.2
标准群钻修磨
图示
修磨效果
在钻头的后刀面上,对称地磨出月牙槽, 它把主切削刃分成三段,即外直刃(图中AB 段)、圆弧刃(图中BC段)、内直刃(图中 CD段),所形成的圆弧刃是群钻最显著的特 点
修磨单边 分屑槽
在一条外刃上磨出凹形分屑槽,有利于排屑和 减少切削力
----------------------------------------
3
6.2 钻头的刃磨
(2)薄板群钻修磨 薄板群钻修磨如表6.3所示。
修磨部位
表6.3 薄板群钻修磨
图示
修磨效果
修磨两主切 削刃磨成圆 弧形切削刃
修磨后,钻尖高度磨低,切削刃 外圆磨成锋利的两个刃尖,与钻 心的高度相差0.5mm~1.5mm, 形成三尖。当钻头钻穿时,两切 削刃已在工件上切削出圆环槽, 加强了定心作用,轴向力不会突 然减小。在两锋利的外尖和圆弧 刃的转动切削下,把薄板孔中间 的圆片切离,孔圆整、光洁,具 有定中心外切圆的良好效果。
1.麻花钻扩孔
用麻花钻扩孔时,由于钻头横刃不参与切削,轴 向力小,进给省力。但因钻头外缘处前角较大,易把钻 头从钻套中拉下来,所以应把麻花钻外缘处的前角修磨 得小一些,并适当控制进给量。
2.扩孔钻扩孔
① 齿数较多(一般3~4个齿),导向性好,切削 平稳。
② 切削刃不必由外缘一直到中心,没有横刃,可避 免横刃对切削的不良影响,如图6.10所示。
由于磨出圆弧刃,增大了靠近钻心处前角 数值,减少挤刮现象,使切削省力,主切削刃 分成几段有利于断屑和排屑。钻孔时圆弧刃在 孔底上切削出一道圆环筋,能稳定钻头的方向 ,限制钻头的摆动,加强定心作用。磨月牙槽 时,降低了钻尖高度,这样可以把槽刃处磨得 较锋利,且不致影响钻尖强度
标准群钻的切削特点和修磨方法
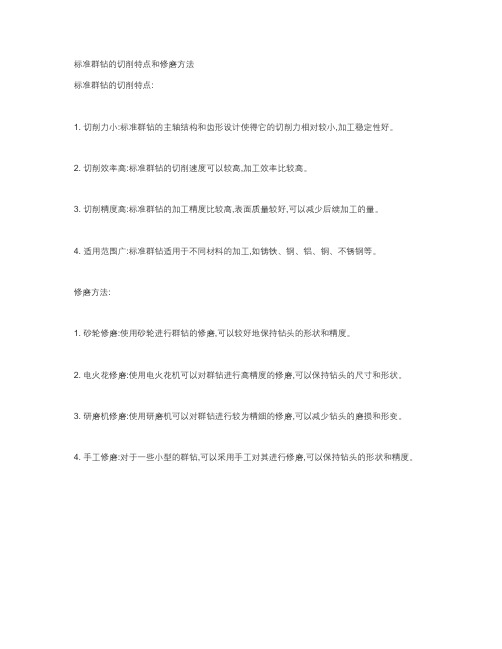
标准群钻的切削特点和修磨方法
标准群钻的切削特点:
1. 切削力小:标准群钻的主轴结构和齿形设计使得它的切削力相对较小,加工稳定性好。
2. 切削效率高:标准群钻的切削速度可以较高,加工效率比较高。
3. 切削精度高:标准群钻的加工精度比较高,表面质量较好,可以减少后续加工的量。
4. 适用范围广:标准群钻适用于不同材料的加工,如铸铁、钢、铝、铜、不锈钢等。
修磨方法:
1. 砂轮修磨:使用砂轮进行群钻的修磨,可以较好地保持钻头的形状和精度。
2. 电火花修磨:使用电火花机可以对群钻进行高精度的修磨,可以保持钻头的尺寸和形状。
3. 研磨机修磨:使用研磨机可以对群钻进行较为精细的修磨,可以减少钻头的磨损和形变。
4. 手工修磨:对于一些小型的群钻,可以采用手工对其进行修磨,可以保持钻头的形状和精度。
刀具群钻将标准麻花钻的切削部分修磨成特殊形状的钻头。群钻是中国
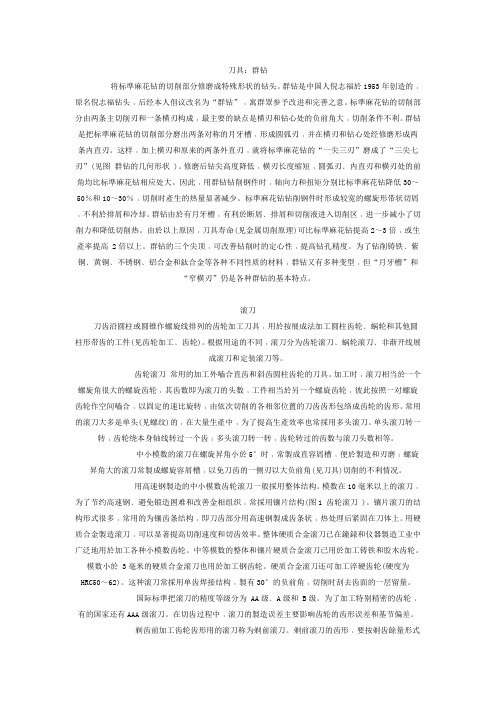
刀具:群钻将标準麻花钻的切削部分修磨成特殊形状的钻头。
群钻是中国人倪志福於1953年创造的﹐原名倪志福钻头﹐后经本人倡议改名为“群钻”﹐寓群眾参予改进和完善之意。
标準麻花钻的切削部分由两条主切削刃和一条横刃构成﹐最主要的缺点是横刃和钻心处的负前角大﹐切削条件不利。
群钻是把标準麻花钻的切削部分磨出两条对称的月牙槽﹐形成圆弧刃﹐并在横刃和钻心处经修磨形成两条内直刃。
这样﹐加上横刃和原来的两条外直刃﹐就将标準麻花钻的“一尖三刃”磨成了“三尖七刃”(见图群钻的几何形状 )。
修磨后钻尖高度降低﹐横刃长度缩短﹐圆弧刃﹑内直刃和横刃处的前角均比标準麻花钻相应处大。
因此﹐用群钻钻削钢件时﹐轴向力和扭矩分别比标準麻花钻降低30~50%和10~30%﹐切削时產生的热量显著减少。
标準麻花钻钻削钢件时形成较宽的螺旋形带状切屑﹐不利於排屑和冷却。
群钻由於有月牙槽﹐有利於断屑﹑排屑和切削液进入切削区﹐进一步减小了切削力和降低切削热。
由於以上原因﹐刀具寿命(见金属切削原理)可比标準麻花钻提高2~3倍﹐或生產率提高 2倍以上。
群钻的三个尖顶﹐可改善钻削时的定心性﹐提高钻孔精度。
为了钻削铸铁﹑紫铜﹑黄铜﹑不锈钢﹑铝合金和鈦合金等各种不同性质的材料﹐群钻又有多种变型﹐但“月牙槽”和“窄横刃”仍是各种群钻的基本特点。
滚刀刀齿沿圆柱或圆锥作螺旋线排列的齿轮加工刀具﹐用於按展成法加工圆柱齿轮﹑蜗轮和其他圆柱形带齿的工件(见齿轮加工﹑齿轮)。
根据用途的不同﹐滚刀分为齿轮滚刀﹑蜗轮滚刀﹑非渐开线展成滚刀和定装滚刀等。
齿轮滚刀常用的加工外嚙合直齿和斜齿圆柱齿轮的刀具。
加工时﹐滚刀相当於一个螺旋角很大的螺旋齿轮﹐其齿数即为滚刀的头数﹐工件相当於另一个螺旋齿轮﹐彼此按照一对螺旋齿轮作空间嚙合﹐以固定的速比旋转﹐由依次切削的各相邻位置的刀齿齿形包络成齿轮的齿形。
常用的滚刀大多是单头(见螺纹)的﹐在大量生產中﹐为了提高生產效率也常採用多头滚刀。
单头滚刀转一转﹐齿轮绕本身轴线转过一个齿﹔多头滚刀转一转﹐齿轮转过的齿数与滚刀头数相等。
2024年机修钳工(技师)证考试题库及答案

2024年机修钳工(技师)证考试题库及答案试题11、【单选题】()是指工作对象在装配过程中,有顺序地由一个工人转移到另一个工人。
(B)A、部件装配B、移动式装配C、固定式装配D、总装配2、【单选题】0是指测量器具的内在误差。
(C)A、测量器具误差B、阿贝误差C、测量方法误差D、读数方式误差3、【单选题】0是采用压床、手压床或锤击将零件的长度压缩,增加内、外径尺寸,用来修复有色金属套筒或柱形零件。
(C)A、挤压法B、扩张法C、傲粗法D、拉伸法4、【单选题】()适用于容量不大和不经常启动的直流电动机。
(C)A、直接启动B、减压启动C、在电枢电路中串联启动变阻器D、自耦变压器启动5、【单选题】0适用范围广,不受零件材料和形状轮廓的限制。
(A)A、渗透检测B、超声波检测C、磁粉探伤D、频谱检测6、【单选题1M7120A磨床主轴动平衡时,在右支承架上有放大机构,经机械放大10倍左右后输入至(),传感器即将机械振动量转换成电信号输入微机电测系统。
(B)A、传动机构B、传感器C、放大机构D、输入系统7、【单选题】T68卧式镇床()检验时,精车端面的不平度只允许中凹。
(C)A、尺寸精度B、几何精度C、工作精度D、旋转精度8、【单选题】三相步进电动机的步距角是1.5°,若步进电动机通电频率为2000Hz,则步进电动机的转速为()r/min。
(B)A、3000B、500C、1500D、10009、【单选题】下列叙述中不属于设备修理班组的质量管理活动的内容是0。
(D)A、提出活动课题B、调查现状C、制定方案D、提高劳动生产率10、【单选题】两端中100mm轴颈的径向圆跳动均在()mm以内。
(A)A、0.01B、0.02C、0.03D、0.0411、【单选题】主轴采用()变速时,其滑移齿轮的位移常用液压拨叉和电磁离合器两种方式。
(A)A、齿轮分段B、液压涡轮C、变频器D、齿轮齿条12、【单选题】修复后的零件必须保持足够的(),并不影响使用寿命和性能。
标准群钻的刃磨
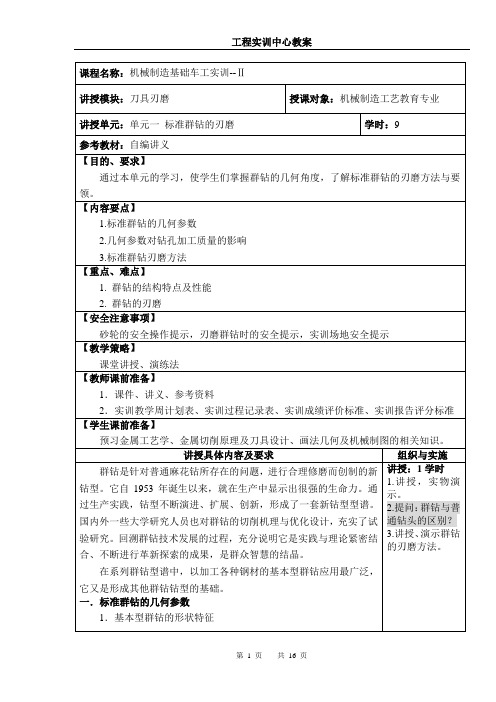
讲授模块:刀具刃磨
授课对象:机械制造工艺教育专业
讲授单元:单元一标准群钻的刃磨
学时:9
参考教材:自编讲义
【目的、要求】
通过本单元的学习,使学生们掌握群钻的几何角度,了解标准群钻的刃磨方法与要领。
【内容要点】
1.标准群钻的几何参数
2.几何参数对钻孔加工质量的影响
3.标准群钻刃磨方法
3、分屑、断屑、排屑得到改善
由于外刃、圆弧刃和内刃交接处有明显的转折点,而且一侧外刃上还开出分屑槽,故能保证良好分屑。切屑变窄后有利于断屑和排屑。在这种情况下,如施加切削液,则切削液较易到达孔底与钻尖,能充分发挥冷却、润滑作用。
4、钻头耐用度提高
切削试验与现场验证表明,“群钻”切削部分的磨损比普通麻花钻明显减缓,耐用度显著提高。一般“群钻”的耐用度可提高2~3倍。
图1普通麻花钻
图2基本型群钻
(a)小型d≤15mm(b)中型d≤40mm(c)大型d>40mm
图3基本型群钻与普通麻花钻比较
下面,就以中等基本型群钻(15<d<40毫米)为例(如图4),详细说明它的特征:
图4中等基本型群钻(Φ15~40mm)
1)主切削刃分成三段,并形成三个尖
(1)外刃——AB段切削刃,是外刃后面1与刃沟螺旋槽的交线。外刃长度l约为钻头直径d的1/5或1/3,即l≈0.2d(不磨分屑槽,d≤15毫米);l≈0.3d(磨分屑槽,d>15毫米)。
3)开始刃磨。主任接触砂轮,一手握住钻头某个固定的部位作定位支点,一手将钻尾上下摆动,同时控制沿砂轮径向的吃刀量,磨出外刃后面,保证外刃结构后角。
4)钻尾摆动时不要高出水平面,以防止磨出负后角。
5)当主刃即将磨好成型时,应注意不要由刃瓣尾根向刃口方向进行磨削,以免刃口退火。如图6所示。
多孔钻
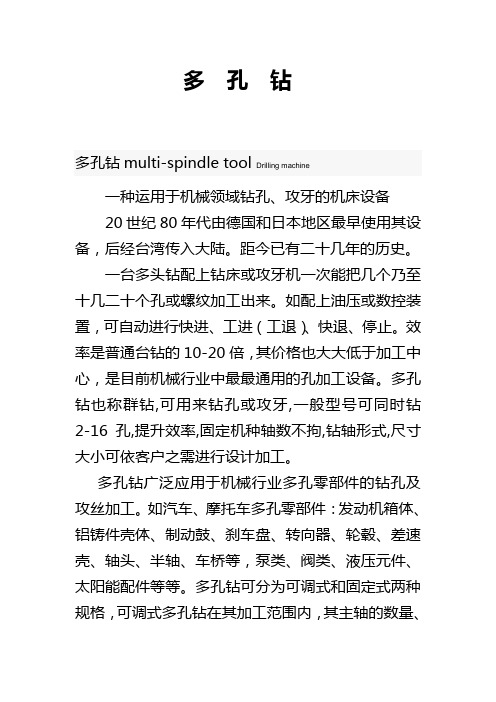
多孔钻多孔钻multi-spindle tool Drilling machine一种运用于机械领域钻孔、攻牙的机床设备20世纪80年代由德国和日本地区最早使用其设备,后经台湾传入大陆。
距今已有二十几年的历史。
一台多头钻配上钻床或攻牙机一次能把几个乃至十几二十个孔或螺纹加工出来。
如配上油压或数控装置,可自动进行快进、工进(工退)、快退、停止。
效率是普通台钻的10-20倍,其价格也大大低于加工中心,是目前机械行业中最最通用的孔加工设备。
多孔钻也称群钻,可用来钻孔或攻牙,一般型号可同时钻2-16孔,提升效率,固定机种轴数不拘,钻轴形式,尺寸大小可依客户之需进行设计加工。
多孔钻广泛应用于机械行业多孔零部件的钻孔及攻丝加工。
如汽车、摩托车多孔零部件:发动机箱体、铝铸件壳体、制动鼓、刹车盘、转向器、轮毂、差速壳、轴头、半轴、车桥等,泵类、阀类、液压元件、太阳能配件等等。
多孔钻可分为可调式和固定式两种规格,可调式多孔钻在其加工范围内,其主轴的数量、主轴间的距离,相对可以任意调整,一次进给同时加工数孔。
在其配合液压机床工作时,可自动进行快进、工进(工退)、快退、停止.同单轴钻(攻丝)比较,工件加工精度高、工效快,可有效的节约投资方的人力、物力、财力。
尤其机床的自动化大大减轻操作者的劳动强度。
固定式多孔钻采用单件(加工件)专机的设计方案,根据其加工件加工频率高、量大之原因,专门量身定制一件一机的设备,在其工作中勿须担心尺寸跑偏而伤脑筋。
除用到常规的产品外,还可根据客户的特殊要求进行专项设计。
多孔钻参数/精度要求Main specification of multi-spindle tool噪声(由分贝仪测定)型号转速(rpm)测点距离(cm)最大噪声值(dB) A型20003088T型20003083U型(8轴以内)最大轴距〈200mm20003085U型(8轴以内)最大轴距≥200mm20003090U型(8轴以上)最大轴距〈200mm20003088U型(8轴以上)最大轴距〈200mm20003093输出轴径向跳动型号距离L(mm)径向跳动ER8400.06ER11400.06两孔间距离L类型距离(mm)加导孔板±0.05不加导孔板±0.1ER16400.06 ER20400.06 C5400.12 C6400.12 C9400.12 C12400.12普通钻床配备多孔钻实例加工件案例:配合液压机床:。
标准群钻的形状特点

标准群钻的形状特点标准群钻是一种常见的工业用钻头,其形状特点对于钻削加工起着至关重要的作用。
标准群钻通常用于金属材料的孔加工,因此其形状特点直接影响着加工效率和加工质量。
下面将详细介绍标准群钻的形状特点。
首先,标准群钻的主要部分是刀头。
刀头的形状对于加工效果有着决定性的影响。
通常情况下,标准群钻的刀头呈现出锥形或者锥度较小的形状,这样可以更好地集中切削力,提高切削效率。
另外,刀头的刃部也需要具备一定的锋利度,这样可以更好地切削金属材料,减少加工过程中的摩擦力,提高加工质量。
其次,标准群钻的刀柄也是其形状特点之一。
刀柄的形状设计需要考虑到钻削加工时的稳定性和刚性。
通常情况下,标准群钻的刀柄呈现出圆柱形或者圆锥形,这样可以更好地与钻孔机床的夹持装置相匹配,提高加工的稳定性。
另外,刀柄的材质和加工工艺也需要保证其具备足够的刚性,这样可以避免在加工过程中出现振动和变形,保证加工质量。
此外,标准群钻的切削边缘也是其形状特点之一。
切削边缘的形状设计需要考虑到切削力的集中和切屑的排出。
通常情况下,标准群钻的切削边缘呈现出螺旋线状或者螺旋槽状的形状,这样可以更好地排出切屑,减少加工过程中的阻力,提高加工效率。
另外,切削边缘的后角和前角的设计也需要符合金属材料的切削特性,这样可以更好地控制切削温度,减少刀具磨损,延长使用寿命。
总的来说,标准群钻的形状特点对于钻削加工起着至关重要的作用。
刀头的形状、刀柄的形状和切削边缘的形状都需要经过精心设计,以满足金属材料的切削特性,提高加工效率和加工质量。
只有充分理解和把握了标准群钻的形状特点,才能更好地进行钻削加工,实现高效、精准的加工目标。
为什么群钻又叫做倪志富钻头?它是什么样的?

为什么群钻又叫做倪志富钻头?它是什么样的?'倪志福钻头'1953年10月,时为北京永定机械厂的青年钳工倪志福创制了一种新型钻头(见下图),其基本特征为“三尖七刃锐当先,月牙弧槽分两边”,生产效率和使用寿命均大幅提高,被称为“倪志福钻头”。
1964年8月,北京(国际)科学讨论会举办,31岁的倪志福同志登上国际讲坛,宣读了《倪志福钻头》一文。
随后,该文在《机械工人》、《机械工程学报》和《科学通报》上发表。
这三本刊物一本是金属加工生产实践领域影响最大的技术刊物,一本是代表机械工程技术领域最高水准的学术刊物,一本是自然科学基础理论研究领域的权威学术刊物,此举在我国科技领域引起极大的反响。
1965年5月,全国先进工具经验交流会在北京召开,倪志福等一批全国著名劳模在交流会上做了表演。
倪志福表演时,盛利为他调整机床,表演后,苏广铭等老英雄都热烈地向他表示祝贺。
在今天,“倪志福”这个名字所代表的正是那批金属加工技术精湛的老劳模们(见下图,图中右起依次为盛利、金福长、宿天和、朱恒、倪志福、朱兆金),他们为我国机械工业的发展立下了不可磨灭的功绩。
“群钻”:群众智慧的结晶1965年,倪志福同志建议将“倪志福钻头”改名为“群钻”,因为它是群众智慧的结晶,实现了领导、专家和群众的三结合。
倪志福同志担任领导以后,仍一直关心群众技术协作和金属加工技术创新。
1977年10月,北京先进刀具表演大会在北京第一机床厂等四厂同时进行,时任中共北京市委第二书记的倪志福同志前往参观,还亲自进行不锈钢断屑群钻操作表演(见下图)。
《机械工人》一直关注“群钻”技术的发展,从1956年第12期《新型钻头》报道倪志福创制的新型钻头开始,宣传报道了许多倪志福同志和北京永定机械厂群钻小组的实践经验文章。
据我们统计,从1979年第10期到1982年第4期,北京永定机械厂群钻小组就在《机械工人》发表了9篇文章,既包括群钻小组对“群钻”研究和实践的最新进展,如“加工不锈钢和耐酸钢的断屑群钻”、“钴铸帖精孔群钻”、“钴钛合金群钻”等,也包括20世纪80年代改革开放初期,全国各地掀起学习科学技术的高潮,群钻小组撰写的“群钻问答一百例”在《机械工人》1980年第7~12期选登连载,简明概括地介绍了“群钻”的实践与认识的基本内容。
群钻
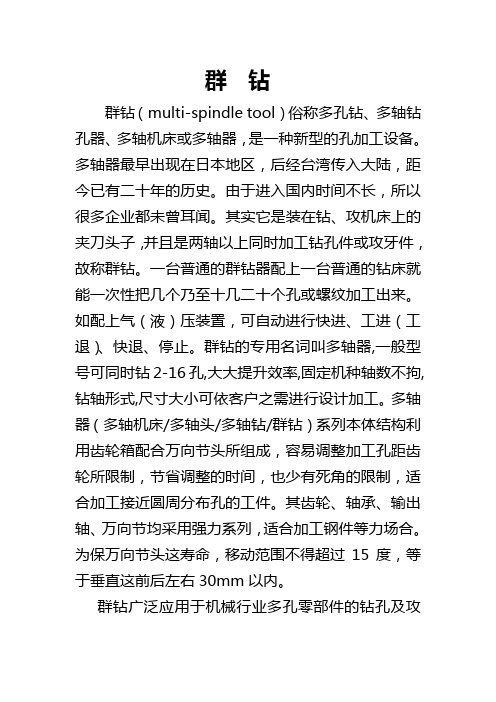
群钻群钻(multi-spindle tool)俗称多孔钻、多轴钻孔器、多轴机床或多轴器,是一种新型的孔加工设备。
多轴器最早出现在日本地区,后经台湾传入大陆,距今已有二十年的历史。
由于进入国内时间不长,所以很多企业都未曾耳闻。
其实它是装在钻、攻机床上的夹刀头子,并且是两轴以上同时加工钻孔件或攻牙件,故称群钻。
一台普通的群钻器配上一台普通的钻床就能一次性把几个乃至十几二十个孔或螺纹加工出来。
如配上气(液)压装置,可自动进行快进、工进(工退)、快退、停止。
群钻的专用名词叫多轴器,一般型号可同时钻2-16孔,大大提升效率,固定机种轴数不拘,钻轴形式,尺寸大小可依客户之需进行设计加工。
多轴器(多轴机床/多轴头/多轴钻/群钻)系列本体结构利用齿轮箱配合万向节头所组成,容易调整加工孔距齿轮所限制,节省调整的时间,也少有死角的限制,适合加工接近圆周分布孔的工件。
其齿轮、轴承、输出轴、万向节均采用强力系列,适合加工钢件等力场合。
为保万向节头这寿命,移动范围不得超过15度,等于垂直这前后左右30mm以内。
群钻广泛应用于机械行业多孔零部件的钻孔及攻丝加工。
如汽车、摩托车多孔零部件:发动机箱体、铝铸件壳体、制动鼓、刹车盘、转向器、轮毂、差速壳、轴头、半轴、车桥等,泵类、阀类、液压元件、太阳能配件等等。
多孔钻在其加工范围内,其主轴的数量、主轴间的距离,可以任意调整,一次进给同时加工数孔。
在其配合液压机床工作时,可自动进行快进、工进(工退)、快退、停止、同单轴钻(攻丝)比较,工件加工精度高、工效快,可有效的节约投资方的人力、物力、财力。
尤其机床的自动化大大减轻操作者的劳动强度。
除用到常规的产品外,还可根据客户的特殊要求进行专项设计。
多轴器参数/精度要求产品名称:可调式U型圆型多轴器常规型号例举型号MU110MU165MU200MU250MU300筒夹规格最大钻孔能力ER8/5 C5/5ER11/7 C6/6ER16/10ER20/13ER8/5 C5/5ER11/7 C6/6ER16/10ER20/13ER8/5 C5/5ER11/7 C6/6ER16/10ER20/13ER8/5 C5/5ER11/7 C6/6ER16/10ER20/13ER8/5 C5/5ER11/7 C6/6ER16/10ER20/13转速比1:11:11:11:11:1最小距离(二轴间)1318262813182628131826281318262813182628最大轴心范围110165200250300轴数2-62-104-124-124-14在普通钻床上安装多轴器:在专用机床上配备:在组合机床上配备:。
群钻的各种钻型
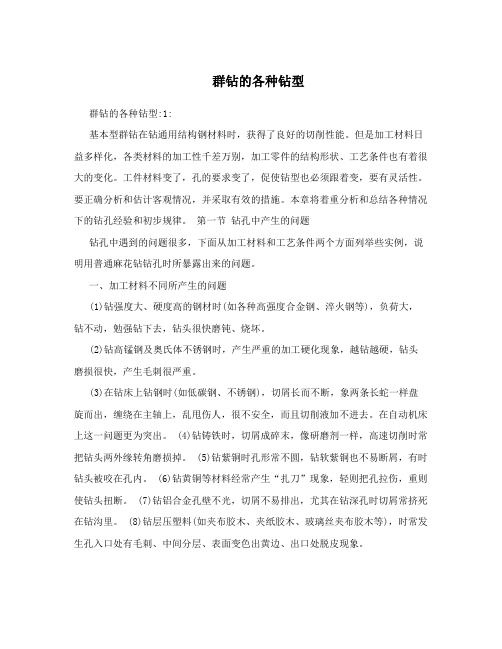
群钻的各种钻型群钻的各种钻型:1:基本型群钻在钻通用结构钢材料时,获得了良好的切削性能。
但是加工材料日益多样化,各类材料的加工性千差万别,加工零件的结构形状、工艺条件也有着很大的变化。
工件材料变了,孔的要求变了,促使钻型也必须跟着变,要有灵活性。
要正确分析和估计客观情况,并采取有效的措施。
本章将着重分析和总结各种情况下的钻孔经验和初步规律。
第一节钻孔中产生的问题钻孔中遇到的问题很多,下面从加工材料和工艺条件两个方面列举些实例,说明用普通麻花钻钻孔时所暴露出来的问题。
一、加工材料不同所产生的问题(1)钻强度大、硬度高的钢材时(如各种高强度合金钢、淬火钢等),负荷大,钻不动,勉强钻下去,钻头很快磨钝、烧坏。
(2)钻高锰钢及奥氏体不锈钢时,产生严重的加工硬化现象,越钻越硬,钻头磨损很快,产生毛刺很严重。
(3)在钻床上钻钢时(如低碳钢、不锈钢),切屑长而不断,象两条长蛇一样盘旋而出,缠绕在主轴上,乱甩伤人,很不安全,而且切削液加不进去。
在自动机床上这一问题更为突出。
(4)钻铸铁时,切屑成碎末,像研磨剂一样,高速切削时常把钻头两外缘转角磨损掉。
(5)钻紫铜时孔形常不圆,钻软紫铜也不易断屑,有时钻头被咬在孔内。
(6)钻黄铜等材料经常产生“扎刀”现象,轻则把孔拉伤,重则使钻头扭断。
(7)钻铝合金孔壁不光,切屑不易排出,尤其在钻深孔时切屑常挤死在钻沟里。
(8)钻层压塑料(如夹布胶木、夹纸胶木、玻璃丝夹布胶木等),时常发生孔入口处有毛刺、中间分层、表面变色出黄边、出口处脱皮现象。
(9)钻有机玻璃时,孔不光亮,发暗(乌),本来是透明净亮的,钻完孔后,孔壁变成乳白色了,更严重时孔壁烧伤,和产生“银斑”状裂纹。
(10)钻橡皮时,孔收缩量很大,易成锥形、上大下小,孔壁毛糙。
二、工艺条件不同产生的问题(1)钻薄板孔,有时工件不便于压紧,人们多采用手扶,但当钻头刚要钻出工件时,手就扶不住工件了,发生抖动,很容易出工伤事故。
中级钳工技术第二章群钻和钻削特殊孔

3.6.3 平面划线
平面画线
3.6.4 立体划线
立体画线
复杂工件的划线
箱体工件的划线: 箱体工件的划线,除按一般划线时选择划线基 准、找正、借料外,还应注意以下几点: 1)划线前必须仔细检查毛坯质量,有严重缺 陷和很大误差的毛坯,就不要勉强去划,避免出 现废品和浪费较多工时。
2)认真掌握技术要求,如对箱体工件的外观 要求、精度要求和形位公差要求;分析箱体的加 工部位与装配工件的相互关系,避免因划线前考 虑不周而影响工件的装配质量。 3)了解零件机械加工工艺路线,知道各加工 部位应划的线与加工工艺的关系,确定划线的次 数和每次要划哪些线,避免因所划的线被加工掉 而重划。
【例3-1】 要在工件的某圆周上划出均匀分 布的10个孔,试求出每划完一个孔的位置 后, 手柄转过的圈数。
解 根据公式 n=40/Z,则n=40/10=4圈。 即每划完一个孔的位置后,手柄应转过四圈再划 另一个孔,以此类推。
【例3-2】 在一圆盘端面上划六边形,求先 划一条线后,手柄应转几圈后再划第二条线? 解 已知 Z =6,则 n=40/Z=40/6 =6(2/3) 若将2/3分子、分母同时扩大10倍,即 2/3×10/10 =20/30,则分度手柄在分度盘中 有30个孔的孔圈上转过六圈后,再转过20个孔 即可。
3.4.2 划线基准的选择
划线基准的选择: 应先分析图样,找出设计基准, 使划线基准与设计基准尽量一致, 能够直接量取划线尺寸,简化换算过程。 划线时,应从划线基准开始。
划线基准一般可根据以下三个原则来选择: (1)以两个互相垂直的平面(或线)为划线基 准。
(2)以两条中心线为划线基准
(1)磨有月牙槽,形成凹形圆弧刃: ①磨出圆弧刃后,主切削刃分成三段,能分屑和断屑, 减小铁屑所占空间,是排屑流畅。 ②圆弧刃上各点前角比原来增大。减小切削阻力,可 提高切削速度。 ③钻尖提高降低,这样可把横刃磨得较为锋利,但不 致影响钻尖强度。 ④在钻孔过程中,圆弧刃在孔底切削出一道圆环筋。 他与钻头棱边共同起着稳定钻头方向的作用,进一步 限制了钻头的摆动,加强了定心作用。有利于提高进 给量和孔的表面质量。 (2)修磨横刃后,内刃前角增大: ①钻孔时轴向阻力减小,使机床负荷减小,钻头和工 件产生的热变形小,提高了孔的质量和钻头寿命。
标准群钻的刃磨

课程名称:机械制造基础车工实训--Ⅱ讲授模块:刀具刃磨授课对象:机械制造工艺教育专业讲授单元:单元一标准群钻的刃磨学时:9参考教材:自编讲义【目的、要求】通过本单元的学习,使学生们掌握群钻的几何角度,了解标准群钻的刃磨方法与要领。
【内容要点】1.标准群钻的几何参数2.几何参数对钻孔加工质量的影响3.标准群钻刃磨方法【重点、难点】1. 群钻的结构特点及性能2. 群钻的刃磨【安全注意事项】砂轮的安全操作提示,刃磨群钻时的安全提示,实训场地安全提示【教学策略】课堂讲授、演练法【教师课前准备】1.课件、讲义、参考资料2.实训教学周计划表、实训过程记录表、实训成绩评价标准、实训报告评分标准【学生课前准备】预习金属工艺学、金属切削原理及刀具设计、画法几何及机械制图的相关知识。
讲授具体内容及要求组织与实施群钻是针对普通麻花钻所存在的问题,进行合理修磨而创制的新钻型。
它自1953年诞生以来,就在生产中显示出很强的生命力。
通过生产实践,钻型不断演进、扩展、创新,形成了一套新钻型型谱。
国内外一些大学研究人员也对群钻的切削机理与优化设计,充实了试验研究。
回溯群钻技术发展的过程,充分说明它是实践与理论紧密结合、不断进行革新探索的成果,是群众智慧的结晶。
在系列群钻型谱中,以加工各种钢材的基本型群钻应用最广泛,它又是形成其他群钻钻型的基础。
一.标准群钻的几何参数1.基本型群钻的形状特征讲授:1学时1.讲授,实物演示。
2.提问:群钻与普通钻头的区别?3.讲授、演示群钻的刃磨方法。
比较图1与图2,对照普通麻花钻与基本型群钻的外观形状。
也可从图3中明显地看出,基本型群钻是在普通麻花钻的钻尖上,磨出两个对称的月牙形圆弧槽,形成钻心尖退缩,两侧尖并立的三尖“w”刃形.再进一步修磨.减窄横刃,形成两条较锋利的内刃。
对于直径较大的钻头,还在一侧外刃上再磨出1~2条分屑槽。
于是,一支基本型群钻就形成了。
图1普通麻花钻图2基本型群钻(a)小型d≤15mm (b)中型d≤40mm (c)大型d>40mm 图3基本型群钻与普通麻花钻比较下面,就以中等基本型群钻(15<d<40毫米)为例(如图4),详细说明它的特征:图4中等基本型群钻(Φ15~40mm)1)主切削刃分成三段,并形成三个尖(1)外刃——AB段切削刃,是外刃后面1与刃沟螺旋槽的交线。
群钻与新型群钻
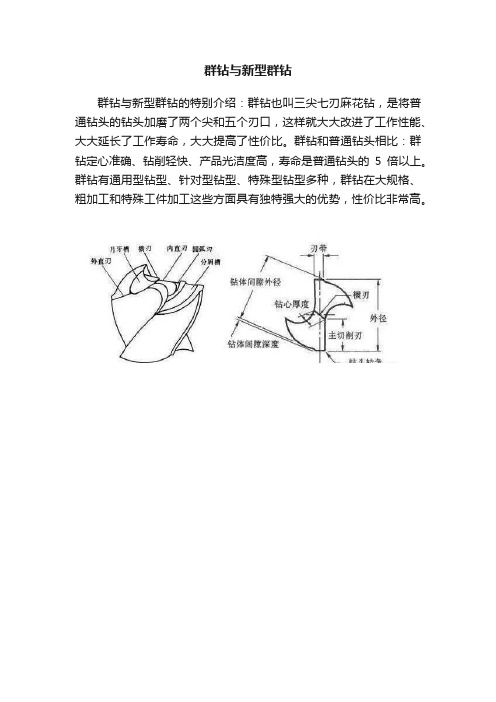
群钻与新型群钻
群钻与新型群钻的特别介绍:群钻也叫三尖七刃麻花钻,是将普通钻头的钻头加磨了两个尖和五个刃口,这样就大大改进了工作性能、大大延长了工作寿命,大大提高了性价比。群钻和普通钻头相比:群钻定心准确、钻削轻快、产品光洁度高,寿命是普通钻头的5倍以上。群钻有通用型钻型、针对型钻型、特殊型钻型多种,群钻在大规格、粗加工和特殊工件加工这些方面具有独特强大的优势,性价比非常高。
群钻的特征和使用性能

群钻的特征和使用性能
于启勋
【期刊名称】《机械工人:冷加工》
【年(卷),期】1999(000)005
【摘要】“群钻”是我国工人阶级和科技人员的重大创造。
它已经走过了46年的历程。
为使广大从事机械制造工作的生产、研究人员了解“群钻”产生的历史背景、特征及其使用性能,特撰写和发表此文。
1.标准麻花钻的缺陷及其改善途径孔加工是机械制造中的重要加工工种,钻头则是用得最广泛的切削刀具之一。
19世纪中叶以前,
【总页数】2页(P13-14)
【作者】于启勋
【作者单位】北京理工大学
【正文语种】中文
【中图分类】TG713.1
【相关文献】
1.井温对螺杆钻具使用性能的影响 [J], 王春阳;李连强;李良君;马峰;景文清;宋烨
2.群钻钻削力研究(IV):群钻钻削力预测模型 [J], 胡仲勋;蔡逸玲
3.群钻钻削力研究:群钻钻削的流屑角模型(I) [J], 蔡逸玲;温松明
4.群钻钻削力研究(Ⅲ):群钻钻削能的理论计算 [J], 胡思节;温松明
5.群钻钻削力研究:群钻钻削的流屑角模型的试验验证(Ⅱ) [J], 温松明;蔡逸玲
因版权原因,仅展示原文概要,查看原文内容请购买。
从倪志福钻到群钻
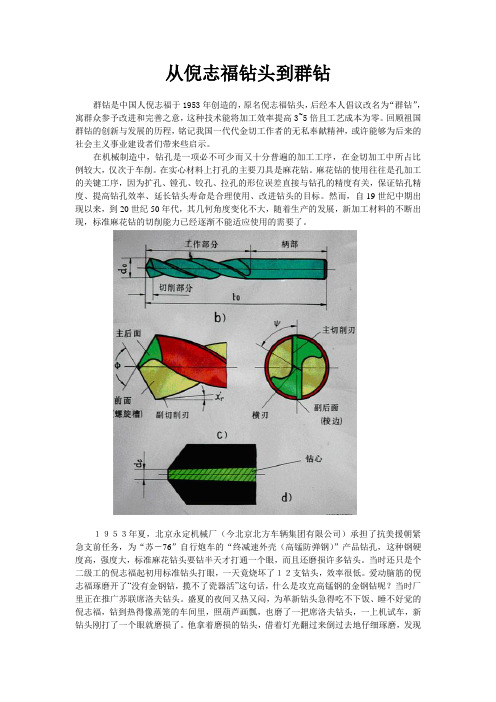
从倪志福钻头到群钻群钻是中国人倪志福于1953年创造的,原名倪志福钻头,后经本人倡议改名为“群钻”,寓群众参予改进和完善之意,这种技术能将加工效率提高3~5倍且工艺成本为零。
回顾祖国群钻的创新与发展的历程,铭记我国一代代金切工作者的无私奉献精神,或许能够为后来的社会主义事业建设者们带来些启示。
在机械制造中,钻孔是一项必不可少而又十分普遍的加工工序,在金切加工中所占比例较大,仅次于车削。
在实心材料上打孔的主要刀具是麻花钻。
麻花钻的使用往往是孔加工的关键工序,因为扩孔、镗孔、铰孔、拉孔的形位误差直接与钻孔的精度有关,保证钻孔精度、提高钻孔效率、延长钻头寿命是合理使用、改进钻头的目标。
然而,自19世纪中期出现以来,到20世纪50年代,其几何角度变化不大,随着生产的发展,新加工材料的不断出现,标准麻花钻的切削能力已经逐渐不能适应使用的需要了。
1953年夏,北京永定机械厂(今北京北方车辆集团有限公司)承担了抗美援朝紧急支前任务,为“苏-76”自行炮车的“终减速外壳(高锰防弹钢)”产品钻孔,这种钢硬度高,强度大,标准麻花钻头要钻半天才打通一个眼,而且还磨损许多钻头。
当时还只是个二级工的倪志福起初用标准钻头打眼,一天竟烧坏了12支钻头,效率很低。
爱动脑筋的倪志福琢磨开了“没有金钢钻,揽不了瓷器活”这句话,什么是攻克高锰钢的金钢钻呢?当时厂里正在推广苏联席洛夫钻头。
盛夏的夜间又热又闷,为革新钻头急得吃不下饭、睡不好觉的倪志福,钻到热得像蒸笼的车间里,照葫芦画瓢,也磨了一把席洛夫钻头,一上机试车,新钻头刚打了一个眼就磨损了。
他拿着磨损的钻头,借着灯光翻过来倒过去地仔细琢磨,发现每个用过的钻头的钻心部分外缘转角处都烧坏了。
一个大胆的设想诞生了,磨损和烧坏的部分不正是钻头的薄弱环节吗?如果把钻头的薄弱点攻下来,它不就成了一把无坚不摧的“金钢钻”了吗?倪志福兴奋了,赶紧拿起一个磨损的钻头,用砂轮把磨损的部位磨成三个尖、七个刃的形状,他用这把钻头连夜干了起来,奇迹发生了,效率提高了,新钻头获得了成功。
GQ10型钻机概述

一、GQ-10型钻机概述GQ-10型钻机是我公司为适应不断发展的基础桩孔工程施工而研制的大口径轻型工程钻机。
该工程钻机采用立轴式岩芯钻机的结构形式,结构紧凑体积小,施工过程稳定可靠。
该钻机适用于高层建筑、堤坝、港口码头、桥梁工程等大口径基础桩孔的施工钻进。
该钻机具有结构合理、装机功率大、性能广泛、重量轻、通用性强等特点,兼之产品质量优良、售后服务周到,广受水电工程、建筑工程等施工部门所欢迎。
二、GQ-10型钻机的主要特点1.钻机具有较多的转速级数和合理的转速范围。
可配Y225M-6、Y225S-4电动机或R4105G54、R4105ZG53柴油机,特别适用于大口径基础桩工程施工。
2.钻机具有一挡反转速度,便于处理孔内事故。
3.钻机的装机功率大,钻进能力强,可钻直径1000 mm以内的桩孔。
4.钻机立轴通径大,给进行程长,钻进工艺适应性强,钻进效率高。
5.钻机常闭式液压卡盘设计合理、夹持力大、夹持稳定、可靠。
6.钻机卷扬机提升能力强,单绳最大提升力可达39.6 k N·m。
7.钻机重心低,移车平稳且距离长,并带有自动伸缩的孔口板,使孔口操作更方便。
8.钻机采用双联油泵供油,功率消耗少,液压系统油温较低。
钻压表与液压系统压力表合二为一,并采用了充油防震结构,钻压值刻度简单、指示准确,仪表使用寿命长。
9.钻机的结构先进,布局合理,便于维护、保养和维修。
10.钻机体积小,重量轻,可拆性好。
其不含动力机的重量约为2430 kg。
它可分解成八个部件搬运,最大部件重量为350kg,搬迁运输方便。
特别说明:本钻机在一定时期后,由于产品结构的不断改进,此说明书的所述内容可能与实际产品有所出入,尚希用户注意。
三、GQ-10型钻机的主要技术参数1、基本参数:钻孔直径:1000 mm钻机外形尺寸(长×宽×高): 电动机 3160×1250×1935mm柴油机3472×1250×1935mm 钻机重量(不含动力机): 2430 kg2、立轴及回转器:钻机转速:Y225M-6电动机: 47.6; 80; 134; 224; 355; 383 ;反转: 53 r/min Y225S-4电动机: 72; 120; 201; 336; 533; 575 ;反转: 80 r/min 最大输出扭矩: 6000 N·m / 4980 Nm立轴行程: 600mm 立轴通孔直径: 96 mm立轴最大起重力/最大加压力:100 kN / 75 kN3、卷扬机:卷筒直径:285 mm 抱闸直径:500 mm一速单绳(第二层)提升力:35 k N钢丝绳直径:18.5mm (170kg/cm2)单绳第二层提升速度:(Y225M-6 电机)0.665;1.12; 1.87 m/s(Y225S - 4 电机)0.98;1.65;2.78 m/s4、变速箱、离合器:东风DF6S650系列汽车变速箱和离合器5、机架:带有可自动伸缩的孔口板,让开孔口距离:530 mm,可提1000mm钻具6、液压系统:双联齿轮泵:(32+12) L/min 系统压力:8 MPa7、动力机:(选配)电动机:Y 225M-6 30 kW 980 r/minY 225S-4 37 kW 1480 r/min柴油机:R4105G54 42 Kw 1500 r/minR4105ZG53 56 Kw 1500 r/min五、GQ-10型钻机的使用及维护1、钻机的安装:钻机底座应用地脚螺栓紧固在机台木上,机木安装应平整,各机台木之间的连接应牢固可靠。
- 1、下载文档前请自行甄别文档内容的完整性,平台不提供额外的编辑、内容补充、找答案等附加服务。
- 2、"仅部分预览"的文档,不可在线预览部分如存在完整性等问题,可反馈申请退款(可完整预览的文档不适用该条件!)。
- 3、如文档侵犯您的权益,请联系客服反馈,我们会尽快为您处理(人工客服工作时间:9:00-18:30)。
群钻的特征和使用性能普通麻花钻受其固有结构的限制,其几何形状存在着某些缺陷。
通过对其切削部分的修磨,可以得到一定改善。
“群钻”就是一种行之有效的修磨形式。
如果采用比普通高速钢性能更好的新型刀具材料,或变革麻花钻的结构,在此基础上再将钻头切削部分修磨成“群钻”钻型,则钻孔效果将进一步提高。
近年来,新刀具材料的研制技术和刀具的制造技术有了很大的发展,故使变革麻花钻的材料和结构成为可能。
此外,随着被钻孔材料和钻孔条件日益多样化,“群钻”的钻型也有了很多发展,形成了一个系列。
由于“群钻”的几何形状比较复杂,对其刃磨技术的进展也作相应报道。
1.新材料的“群钻”过去普通麻花钻一般用普通高速钢W6Mo5Cr4V2或W18Cr4V制造。
他们的硬度为62~64HRC磨成“群钻”后,切削性能的提高受到刀具材料的限制。
超硬高速钢的出现,使刀具切削性能出现了一个飞跃。
国外多用高钴超硬高速钢,美国的M42(110W1.5Mo9.5Cr4VCo8)和瑞典的HSP―15(W9Mo3Cr4V3Co10)是其中的佼佼者。
但它们的含钴量多,达8%~10%,价格昂贵。
国内多用少钴或无钴超硬高速钢,如501(W6Mo5Cr4V2AL)、(Co5Si(W12Mo3Cr4V3Co5Si)、V3N(W12Mo3Cr4V3N)等。
超硬高速钢的常温硬度达67~69HRC,比普通高速钢高出5HRC,高温硬度亦显著提高。
实践证明,用超硬高速钢制成麻花钻,再修磨成“群钻”形式,与普通高速钢“群钻”相比,钻孔效率可提高一倍以上。
目前,国内一些工具厂可根据用户需求,提供超硬高速钢麻花钻。
上述所有的高速钢都是用熔炼方法制造的。
有用粉末冶金工艺制造的高速钢,其性能优于熔炼高速钢。
如用粉末冶金高速钢制成麻花钻,再磨成“群钻”,其钻孔效率可成倍提高。
在高速钢钻头磨成“群钻”后,如在其工作部分表面上用PVD(物理气相沉积)法涂覆TiN薄层可使其切削性能大幅度提高。
但这样做,除增加了修磨工时外还将加上涂层费用,而重磨后将失去后刀面的涂层,因此涂层“群钻”难以推广。
硬质合金是一种更为先进的刀具材料,其硬度和耐磨性比高速钢高得多。
但是,硬质合金的韧性较差,钻头容易折断,它的可加工性也不太好,故过去很少用硬质合金制造麻花钻。
近年,随着化学成分和制造方法的改进,硬质合金的韧性有了改进,中小尺寸的整体硬质合金麻花钻已得到广泛应用。
在硬材料上钻孔,效果很好。
制造麻花钻,必须选用韧性和抗弯强度较高的硬质合金,例如钻钢材时可用YS25、YT798等,钻铸铁及淬硬钢时可用YS8、YSl0、YG813等,有时亦可采用YT5、YT14、YG6X、YG8等牌号。
作者曾用YG6X整体硬质合金麻花钻(直径10mm)在KmT-BCr20Mo2高铬冷硬铸铁(60HRC)上钻孔,在修磨成“群钻”形式前后进行切削对比。
“群钻”形式的使用寿命约提高了3倍以上。
由于硬质合金较脆,对切削部分应予以加强,“群钻”形状见图1钻高铬冷硬铸铁的整体硬质合金“群钻”图1,几何参数数值见表1。
切削用量:转速n=600r/min,每转进给量ƒ=0.13mm/r。
整体硬质合金2.“群钻”的几何形状早在1953年,北京永定机械厂青年钳工倪志福,用标准麻花钻在装甲钢钢板上钻孔,遇到了困难。
他凭经验,对标准麻花钻切削部分进行了修磨,即在两条直线主切削刃上各磨出了一个圆弧刃,形成了三个钻尖,中心钻尖比原钻尖降低。
修磨过的钻头好用,很快地完成了生产任务。
当时称这种钻型为“倪志福钻头”,即53型“群钻’’(60年代倪志福钻头被正式定名为“群钻”。
)(图2a)。
在1953年以后的十余年中,倪志福和研究小组在实践中逐步总结改进,对53型“群钻”进行过多次修改,几何参数逐步演变,形成了56型、58型、58A型、64型、67型(图2)。
67型是经过多次演进而后定型的“群钻”基本钻型。
图3为中等直径67基本型群钻的切削部分几何参数。
图中:l为外直线切削刃AB的长度,l2为AB刃上分屑槽的宽度,l1为AB刃上分屑槽距外缘点的距离,R为圆弧切削刃BC的圆弧半径,CD为内切削刃,近似为一条直线,h为尖高,即中心尖尖点,0c与侧刃尖尖点B在钻头轴线方向的距离,bΨ为横刃长度,C为AB刃上分屑槽的深度,2φ为外刃锋角,2φτ为内刃锋角,τ为内刃斜角,Ψ为横刃斜角,γτc、αc、αfc、αRc、ατc分别为有关切削刃上的前角、后角。
这些几何参数决定着钻头各部分的强度、锋利程度和分屑、断屑性能,从而影响了钻头工作时的磨损与耐用度。
可以用四句话来总结和概括67基本型“群钻”几何形状的特征:三尖七刃锐当先,月牙弧槽分两边,一侧外刃再开槽,横刃磨低窄又尖。
3.“群钻”的切削效果与修磨前的普通麻花钻相比,“群钻”有前角比较合理、钻削力降低、耐用度提高、钻孔质量改善等优点;而且,分屑、断屑、排屑性能亦较好。
(1)前角分布较为合理基本型“群钻”与普通麻花钻各段切削刃上前角的数值由下表可见。
除外刃(AB段)前角基本未变外,其余各段切削刃上前角均有所加大。
圆弧刃(BC段)上前角加大10゚~14゚,内刃(CD段)上加大15゚~20゚,横刃上约加大5゚。
加大前角,可减小切屑变形,降低切削力及切削温度。
(2)钻削力和钻削扭矩得到降低切削试验表明,在碳素结构钢上钻孔时,“群钻”的轴向力比普通麻花钻约降低35%~47%,扭矩约减小10%~30%;在钻削灰铸铁时,“群钻”的轴向力约降低35%~50%,而扭矩仅加大2%~8%;在钻削有色金属时,“群钻”的轴向力和扭矩分别降低25%~40%和15%~19%。
钻削力和钻削扭矩降低后,有利于降低切削温度及提高钻孔质量。
(3)分屑、断屑、排屑得到改善由于外刃、圆弧刃和内刃交接处有明显的转折点,而且一侧外刃上还开出分屑槽,故能保证良好分屑。
切屑变窄后有利于断屑和排屑。
在这种情况下,如施加切削液,则切削液较易到达孔底与钻尖,能充分发挥冷却、润滑作用。
(4)钻头耐用度提高切削试验与现场验证表明,“群钻”切削部分的磨损比普通麻花钻明显减缓,耐用度显著提高。
一般“群钻”的耐用度可提高2~3倍。
(5)钻孔质量提高由于横刃磨窄,定心作用好;两个侧刃尖和圆弧刃对钻头均有稳定、定向作用;且轴向力显著减小,故“群钻”钻孔时不易走偏,提高了钻孔精度。
钻削过程平稳,切屑变形减小,也有利于提高钻孔表面质量。
由于“群钻”具有以上优点,40余年来驰名中外,得到了广泛的应用。
群钻的各种钻型(1)基本型群钻在钻通用结构钢材料时,获得了良好的切削性能。
但是加工材料日益多样化,各类材料的加工性千差万别,加工零件的结构形状、工艺条件也有着很大的变化。
工件材料变了,孔的要求变了,促使钻型也必须跟着变,要有灵活性。
要正确分析和估计客观情况,并采取有效的措施。
本章将着重分析和总结各种情况下的钻孔经验和初步规律。
第一节钻孔中产生的问题钻孔中遇到的问题很多,下面从加工材料和工艺条件两个方面列举些实例,说明用普通麻花钻钻孔时所暴露出来的问题。
一、加工材料不同所产生的问题(1)钻强度大、硬度高的钢材时(如各种高强度合金钢、淬火钢等),负荷大,钻不动,勉强钻下去,钻头很快磨钝、烧坏。
(2)钻高锰钢及奥氏体不锈钢时,产生严重的加工硬化现象,越钻越硬,钻头磨损很快,产生毛刺很严重。
(3)在钻床上钻钢时(如低碳钢、不锈钢),切屑长而不断,象两条长蛇一样盘旋而出,缠绕在主轴上,乱甩伤人,很不安全,而且切削液加不进去。
在自动机床上这一问题更为突出。
(4)钻铸铁时,切屑成碎末,像研磨剂一样,高速切削时常把钻头两外缘转角磨损掉。
(5)钻紫铜时孔形常不圆,钻软紫铜也不易断屑,有时钻头被咬在孔内。
(6)钻黄铜等材料经常产生“扎刀”现象,轻则把孔拉伤,重则使钻头扭断。
(7)钻铝合金孔壁不光,切屑不易排出,尤其在钻深孔时切屑常挤死在钻沟里。
(8)钻层压塑料(如夹布胶木、夹纸胶木、玻璃丝夹布胶木等),时常发生孔入口处有毛刺、中间分层、表面变色出黄边、出口处脱皮现象。
(9)钻有机玻璃时,孔不光亮,发暗(乌),本来是透明净亮的,钻完孔后,孔壁变成乳白色了,更严重时孔壁烧伤,和产生“银斑”状裂纹。
(10)钻橡皮时,孔收缩量很大,易成锥形、上大下小,孔壁毛糙。
二、工艺条件不同产生的问题(1)钻薄板孔,有时工件不便于压紧,人们多采用手扶,但当钻头刚要钻出工件时,手就扶不住工件了,发生抖动,很容易出工伤事故。
另外,孔易产生多角形、毛刺和变形。
(2)钻深孔时,切屑难排出,常常要在中途多次退出钻头才能钻完一孔,人们称之为“啄木鸟式”的钻削方式;钻直径大的孔(如在钢上钻直径大于35毫米的孔),直接用普通麻花钻钻出就比较困难,负荷大,钻头和机床都承受不了,常发生“闷车”,此时要先钻出小孔,再用大钻头扩孔。
如果,硬要一次钻出,进给量必定选得很小,这样生产效率就很低。
(3)当工件上已有毛坯孔再扩孔时,由于加工余量不均匀,表面有硬皮,因此钻头常会歪斜,刃口也容易崩坏。
(4)在倾斜表面或曲面上钻孔时,钻头往往定不住中心,发生偏斜,常不得不先将工件表面锪平,然后才能钻孔。
(5)由于小量生产的需要,为了节省非标准尺寸的专用铰刀,希望用钻头钻出精孔。
这也是我们常遇到的难题。
(6)小量生产采用划线钻孔时,钻头不易找正,当孔窝划得浅时,孔偏不容易发现;划深时,看出孔偏再找正也就费劲了。
(7)用钻头进行扩孔,也容易产生“扎刀”;有时孔壁出现大螺旋沟,甚至用铰刀铰孔后也不能除掉。
(8)用钻头锪倒角,容易发生抖动,出现多角形,或产生严重的毛刺。
第二节工件材料的钻削加工性一、概述在钻头与工件的矛盾统一体中,一般来说,钻头是矛盾的主要方面,但也常常会发生转化。
因此研究钻孔过程,既要研究刀具一方,又要研究矛盾的另一方――工件材料。
在这里,着重需要研究的是工件材料的钻削加工性。
工件材料的钻削加工性(或称可钻削性)是指材料由毛坯通过钻削过程,得到所要求孔形难易程度的工艺特性。
显然,钻削加工性是一个综合性指标。
这是由于钻孔中的各种问题:生产效率、切削力、耐用度、加工质量等交织综合在一起,切屑变形与摩擦运动决定着钻削力和切削热;钻削热影响着钻削温度和冷硬层;而积屑瘤与钻削温度密切相关;积屑瘤、振动和切屑的挤刮则限制着表面光洁度的提高;孔要求越精越光,则又限制着钻头耐用度和生产效率的提高,……。
还应指出,由于各种材料在钻孔中的具体要求不同,其钻削加工性的指标也不同。
影响材料钻削加工性的因素很多,有物理一力学性能、化学成分、材料制造和热处理方法等。
化学成分和材料制造状态如金相组织是决定物理一力学性能的根据,然而直接起作用的却还是物理一力学性能,它包括强度(或硬度)、塑性(或韧性)、导热率和线膨胀系数以及弹性系数等,这些因素直接影响到钻孔效率的高低。