精馏塔的节能与控制
浅析化工精馏高效节能技术开发及应用
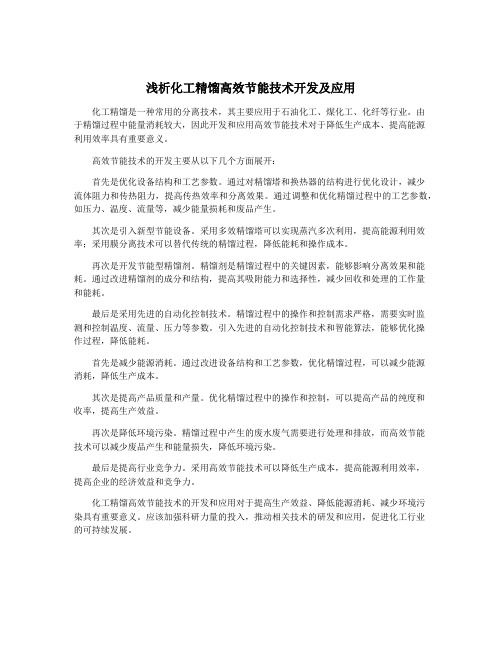
浅析化工精馏高效节能技术开发及应用化工精馏是一种常用的分离技术,其主要应用于石油化工、煤化工、化纤等行业。
由于精馏过程中能量消耗较大,因此开发和应用高效节能技术对于降低生产成本、提高能源利用效率具有重要意义。
高效节能技术的开发主要从以下几个方面展开:首先是优化设备结构和工艺参数。
通过对精馏塔和换热器的结构进行优化设计,减少流体阻力和传热阻力,提高传热效率和分离效果。
通过调整和优化精馏过程中的工艺参数,如压力、温度、流量等,减少能量损耗和废品产生。
其次是引入新型节能设备。
采用多效精馏塔可以实现蒸汽多次利用,提高能源利用效率;采用膜分离技术可以替代传统的精馏过程,降低能耗和操作成本。
再次是开发节能型精馏剂。
精馏剂是精馏过程中的关键因素,能够影响分离效果和能耗。
通过改进精馏剂的成分和结构,提高其吸附能力和选择性,减少回收和处理的工作量和能耗。
最后是采用先进的自动化控制技术。
精馏过程中的操作和控制需求严格,需要实时监测和控制温度、流量、压力等参数。
引入先进的自动化控制技术和智能算法,能够优化操作过程,降低能耗。
首先是减少能源消耗。
通过改进设备结构和工艺参数,优化精馏过程,可以减少能源消耗,降低生产成本。
其次是提高产品质量和产量。
优化精馏过程中的操作和控制,可以提高产品的纯度和收率,提高生产效益。
再次是降低环境污染。
精馏过程中产生的废水废气需要进行处理和排放,而高效节能技术可以减少废品产生和能量损失,降低环境污染。
最后是提高行业竞争力。
采用高效节能技术可以降低生产成本,提高能源利用效率,提高企业的经济效益和竞争力。
化工精馏高效节能技术的开发和应用对于提高生产效益、降低能源消耗、减少环境污染具有重要意义。
应该加强科研力量的投入,推动相关技术的研发和应用,促进化工行业的可持续发展。
精馏塔控制关键因素和节能途径

精馏塔控制关键因素和节能途径摘要:精馏是化工生产中重要的基础操作,由于化工行业能耗非常高,如何实现高效节能已经成为社会及行业广泛关注的课题,化工产品生产组织过程中,精馏塔是主要的设备组成部分,也是节能降耗的重点,对此我们要在强化精馏塔控制的基础上,着力对节能降耗方面进行研究探讨。
关键词:精馏塔;控制;节能;气相流体一、精馏塔控制基本原理蒸馏是化学生产中分离溶液混合物的典型操作.它的本质是多级蒸馏,也就是在一定汽化压力下,采用不同的沸点或溶解液混合物组分的饱和,对低沸点或高蒸汽压力进行汽化,经过反复蒸发并在气态中部分冷凝后逐渐分离。
在此过程中,传热和传质过程同时进行,并受传质过程的控制。
原料从塔中间的合适位置进入塔内,其中塔的上部为不进给蒸馏,而下部为保留部分。
冷凝器提供液体从塔顶的相流入,然后沸腾器提供来自塔深的回流空气。
气相流体回流是精馏的一个重要特性。
总得来看,精馏塔是气体和液体之间提供接触设备,用于实施质量交换过程。
二、精馏塔控制关键因素(一)精馏塔稳定性为了使精馏塔稳定运行,必须保持精馏装置的平衡。
为确定原液中流量,只要给出蒸馏液中挥发性成分系数和蒸汽渣中挥发性成分系数,还可以确定蒸馏液和锅炉渣流量。
同时,压舱物中挥发性组分的分离程度和系数取决于气液与理论板数关系,因此,要根据残留立方体液体中挥发性成分的摩尔系数来确定,从一定程度上说,这种平衡及系数不能随意改变,否则将导致不平衡,最终改变塔的组成,导致功能不平衡。
(二)回流比例控制影响精馏塔分离效率的主要原因是与回流有关。
在操作和生产中,通常通过改变反比来控制产品的质量。
区间工作线的陡度与逆流成正比,该扇区的传递力与逆流成正比。
首先由于精馏塔理论板块数量限制在规定的板材数量范围内,即使回流程度增加到总流量一定限度值,其次根据整个塔架的材料平衡,分辨率极限。
(三)原料输入输出原料输入输出应随实际运行条件改变而改变,精馏塔控制一般设置有多个进给位置,以满足生产过程中的一些突发情况,主要是在精馏塔中准确、合适的位置方面进行精准把握,以保证流量安全。
精馏塔控制和节能优化研究综述

173经济全球一体化以来,人们的生活质量以及生活水平逐渐提升,对石油化等工业需求越来越高,对产品纯度的需求也在逐渐提升,使精馏有了更加广泛的应用。
为了与绿色、节能理念相契合,给精馏过程带来了新的挑战,对精馏过程进行严格的控制以及优化是十分重要的。
但是,在对精馏塔进行控制以及节能优化之前,必须有效确保整个精馏过程中所生产的产品质量,只有产品达到了相关标准,才可以进行装置优化,从而降低能耗、有效提升回收率,做到将成本最大化的转变成经济效益。
1 精馏原理以及操作过程精馏就是将一定浓度的液体输送到精馏装置中,常见的精馏设备就是图1所示的连续精馏装置。
精馏装置主要分为五个大部分:一是精馏塔;二是冷凝器;三是再沸器;四是回流罐;五是回流罐。
连续精馏装置的工作原理是由进料泵将溶液供给到精馏塔,由于溶液中的液体沸点不同,就会将溶液分为低沸点组和高沸点组,低沸点组也就是易挥发组会因为汽化而向上升腾;高沸点组会因其难挥发而向下流淌,并与向上升腾的蒸汽在塔板之间发生接触,从而实现相际传质[1]。
在相对恒压的条件下,若对单组液体进行持续加热,温度并不会出现变化,但是,在对混合溶液进行沸腾后持续加热,其温度必然会发生变化。
在恒压的条件下,溶液的组分情况会与气相平衡有着密切的联系,其中组分的沸点与浓度成正比,沸点越高浓度就会越高,当然平衡温度也就会更高。
与纯物质相比,混合溶液中液相与气相均处于平衡状态下的温度是不一样的。
当沸点高的液体流到釜液泵后,就会成为塔底产品,而沸点低的液体就会成为塔顶产品,这两段操作的结合,可以将混合溶液中的液体分为两个部分,并进行分离,从而精馏出两种所需纯度的产品。
精馏可以将混合物液体进行分离,主要利用的就是液体的沸点不同,通过汽化以及冷凝的方式,经过精馏装置对其进行反复冷凝以及汽化,从而有效的不同组分的液体完全分离。
所以,整个精馏过程其实就是进行多次汽化、多次冷凝的过程,并且,溶液会在汽化以及冷凝的过程中会吸收和释放大量的热量,因此精馏装置必须具备冷凝器以及再沸器等装置给予辅助,从而实现整个精馏装置的完整运行,从而得到预期塔顶以及塔底的产品[2]。
精馏塔的节能优化综述
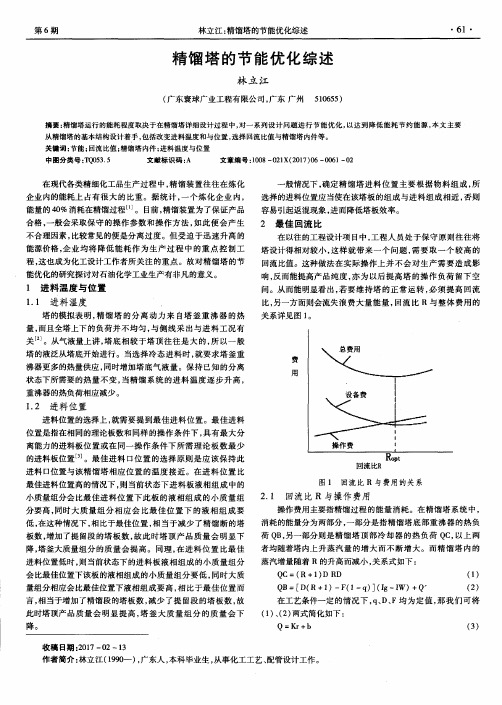
1 进料 温 度与位 置 1 . 1 进 料 温度 .
塔 的模拟表 明 , 精 馏 塔 的分 离 动力 来 自塔 釜 重 沸器 的 热 量, 而且全 塔上下的 负荷并 不均匀 , 与侧线 采 出与进 料 工况 有 关 』 。从气液量上讲 , 塔底 相较 于塔顶 往往 是 大 的, 所 以一 般
程, 这也成为化工设计工作者所关 注 的重 点。故对精 馏塔 的节 能优化 的研究探讨对石油化学工业生 产有 非凡的意义。
容易引起返混现象 , 进 而降低塔板效 率。
2 最 佳 回流 比
在以往的工程设计项 目中, 工 程人员 处于保 守原则 往往将 塔设计得相对较小 , 这样 就带 来一 个 问题 , 需要 取一 个较 高 的 回流 比值。这种做法 在实 际操作 上并 不会对 生 产需 要造 成影
塔 的液泛从塔底开始进行 。当选 择冷态 进料 时 , 就要求 塔釜 重 沸器更多 的热量供应 , 同时增加塔底 气液量 。保 持 已知的分 离
间。从 而能明显看 出, 若要 维持 塔 的正 常运 转 , 必须 提高 回流 比, 另一方面则会流失 浪费 大量 能量 , 回流 比 R与 整体 费用 的
在现代各类精 细化工 品生产 过程 中 , 精馏装 置往往 在炼 化
企业 内的能耗上 占有很 大 的 比重。据统 计 , 一个 炼化 企业 内,
一
般情况下 , 确定 精馏 塔进 料 位置 主要 根据 物料 组成 , 所
选 择的进料位置应当使在该塔板 的组成与 进料组 成相近 , 否则
能量 的 加%消耗在精馏过程 J 。 目前 , 精 馏装 置为了保证产 品 合格 , 一般会 采取保守 的操作 参数 和操 作方 法 , 如此 便会 产 生 不合理 因素 , 比较常见的便是分离 过度 。但受 迫于迅 速升高 的 能源价格 , 企业 均将 降 低能 耗 作为 生产 过 程 中 的重 点控 制 工
精馏过程的节能降耗

精馏过程的节能降耗精馏过程在化工产业中是一项重要的分离技术,但是它也是能耗较高的过程。
为了降低能耗,节能降耗已经成为精馏技术的一个重要研究方向。
本文将介绍几种精馏过程的节能降耗技术。
首先,提高精馏塔的热效率是提高精馏过程的一个关键。
一种常见的做法是引入换热器网络来最大程度地利用出塔冷凝液和进塔蒸汽之间的热量传递。
这种方法可以降低所需的蒸汽量,从而降低了能耗。
此外,还可以使用多效精馏、热泵或采用废热回收技术进一步提高热效率。
其次,提高精馏过程的物质效率也是节能降耗的一个重要途径。
物质效率是指在精馏过程中使用的干燥剂或者吸附剂能够更有效地去除杂质,从而减少能耗。
通过改进精馏塔的操作条件,如温度、压力和液体流速等参数,可以提高物质效率。
同时,使用高效的精馏填料或者塔板也能够提高分离效果,减少杂质的含量。
此外,使用先进的辅助技术可以进一步降低精馏过程的能耗。
例如,在精馏过程中引入膜分离技术可以减少能源消耗。
膜分离技术是一种基于材料表面或孔隙的选择性渗透性原理分离混合物的方法。
与传统的溶剂萃取或者蒸馏技术相比,膜分离技术具有能耗低、操作简单、体积小等优点。
通过将膜分离技术与精馏过程相结合,可以实现更高效的分离效果。
最后,优化精馏过程的操作策略也是节能降耗的一个重要途径。
通过优化参数设定和控制策略,可以使精馏过程更加稳定和高效。
例如,采用先进的控制算法,如模型预测控制或者模糊控制算法,可以实现对精馏过程的快速响应和精确控制,从而降低了能耗和运行成本。
总的来说,精馏过程的节能降耗是一个涉及多个方面的工程问题。
通过提高热效率、物质效率,使用先进的辅助技术和优化操作策略,可以有效地降低精馏过程的能耗。
这些节能降耗技术不仅可以减少环境污染,还可以提高精馏过程的经济效益。
因此,精馏过程的节能降耗在工业应用中具有重要的意义。
精馏节能技术

热泵精馏工艺分析化工行业就是能耗大户,其中精馏又就是能耗极高的单元操作,而传统的精馏方式热力学效率很低,能量浪费很大。
如何降低精馏塔的能耗,充分利用低温热源,已成为人们普遍关注的问题。
对此人们提出了许多节能措施,通过大量的理论分析、实验研究以及工业应用表明其中节能效果比较显著的就是热泵精馏技术。
热泵精馏就是把精馏塔塔顶蒸汽加压升温,使其用作塔底再沸器的热源,回收塔顶蒸汽的冷凝潜热。
热泵精馏在下述场合应用,有望取得良好效果:(1)塔顶与塔底温差较小,因为压缩机的功耗主要取决于温差,温差越大,压缩机的功耗越大。
据国外文献报导,只要塔顶与塔底温差小于36℃,就可以获得较好的经济效果。
(2)沸点相近组分的分离,按常规方法,蒸馏塔需要较多的塔盘及较大的回流比,才能得到合格的产品,而且加热用的蒸汽或冷却用的循环水都比较多。
若采用热泵技术一般可取得较明显的经济效益。
(3)工厂蒸汽供应不足或价格偏高,有必要减少蒸汽用量或取消再沸器时。
(4)冷却水不足或者冷却水温偏高、价格偏贵,需要采用制冷技术或其她方法解决冷却问题时。
(5)一般蒸馏塔塔顶温度在38~138℃之间,如果用热泵流程对缩短投资回收期有利就可以采用,但就是如果有较便宜的低压蒸汽与冷却介质来源,用热泵流程就不一定有利。
(6)蒸馏塔底再沸器温度在300℃以上,采用热泵流程往往就是不合适的。
以上只就是对一般情况而言,对于某个具体工艺过程,还要进行全面的经济技术评定之后才能确定。
根据热泵所消耗的外界能量不同,热泵精馏可分为蒸汽加压方式与吸收式两种类型1、蒸汽加压方式蒸汽加压方式热泵精馏有两种:蒸汽压缩机方式与蒸汽喷射式。
1、1蒸汽压缩机方式蒸汽压缩机方式又可分为间接式、塔顶气体直接压缩式、分割式与塔釜液体闪蒸再沸式流程。
1、1、1间接式当塔顶气体具有腐蚀性或塔顶气体为热敏性产品或塔顶产品不宜压缩时,可以采用间接式热泵精馏,见图1。
图1 间接式热泵精馏流程图它主要由精馏塔、压缩机、蒸发器、冷凝器及节流阀等组成。
化工生产中热泵精馏工艺流程分析及节能措施
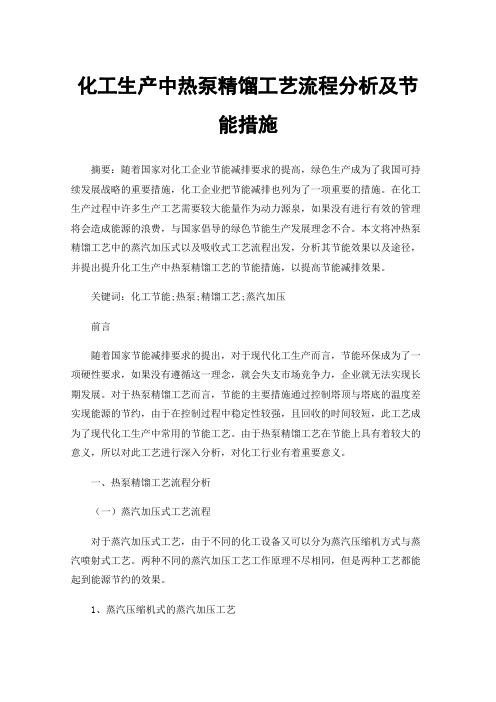
化工生产中热泵精馏工艺流程分析及节能措施摘要:随着国家对化工企业节能减排要求的提高,绿色生产成为了我国可持续发展战略的重要措施,化工企业把节能减排也列为了一项重要的措施。
在化工生产过程中许多生产工艺需要较大能量作为动力源泉,如果没有进行有效的管理将会造成能源的浪费,与国家倡导的绿色节能生产发展理念不合。
本文将冲热泵精馏工艺中的蒸汽加压式以及吸收式工艺流程出发,分析其节能效果以及途径,并提出提升化工生产中热泵精馏工艺的节能措施,以提高节能减排效果。
关键词:化工节能;热泵;精馏工艺;蒸汽加压前言随着国家节能减排要求的提出,对于现代化工生产而言,节能环保成为了一项硬性要求,如果没有遵循这一理念,就会失支市场竞争力,企业就无法实现长期发展。
对于热泵精馏工艺而言,节能的主要措施通过控制塔顶与塔底的温度差实现能源的节约,由于在控制过程中稳定性较强,且回收的时间较短,此工艺成为了现代化工生产中常用的节能工艺。
由于热泵精馏工艺在节能上具有着较大的意义,所以对此工艺进行深入分析,对化工行业有着重要意义。
一、热泵精馏工艺流程分析(一)蒸汽加压式工艺流程对于蒸汽加压式工艺,由于不同的化工设备又可以分为蒸汽压缩机方式与蒸汽喷射式工艺。
两种不同的蒸汽加压工艺工作原理不尽相同,但是两种工艺都能起到能源节约的效果。
1、蒸汽压缩机式的蒸汽加压工艺对于热泵精馏工艺流程而言,蒸汽加压方式应用中,压缩机发挥着重要作用。
压缩机式蒸汽加压,顾名思义,就是以压缩机为核心,通过压缩机与其他设备进行相互配合实现蒸汽的加压,从而达到节能效果。
在此过程中,化工设备的完整性是基础,需要的主要化工设备有精馏塔、蒸发器、压缩机、冷凝器、节流阀等,确保这些设备运行的性能下,采用封闭式的循环作业法,通过物理方法,控制温度,是院士的反应物料保持为气体的状态,在压缩机的作业下,实现气体运输到塔釜并实现气体的压缩。
在许多化工企业在应用热泵精馏工艺过程中,由于压缩机式的作业方式,操作较为简单,设计过程简易,控制效果好,逐渐成为了主要的热泵精馏工艺。
MTO级甲醇精馏产品质量控制与节能
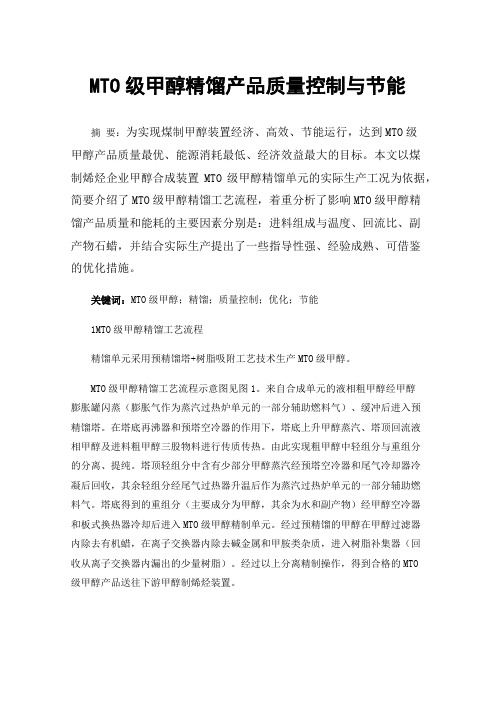
MTO级甲醇精馏产品质量控制与节能摘要:为实现煤制甲醇装置经济、高效、节能运行,达到MTO级甲醇产品质量最优、能源消耗最低、经济效益最大的目标。
本文以煤制烯烃企业甲醇合成装置MTO级甲醇精馏单元的实际生产工况为依据,简要介绍了MTO级甲醇精馏工艺流程,着重分析了影响MTO级甲醇精馏产品质量和能耗的主要因素分别是:进料组成与温度、回流比、副产物石蜡,并结合实际生产提出了一些指导性强、经验成熟、可借鉴的优化措施。
关键词:MTO级甲醇;精馏;质量控制;优化;节能1MTO级甲醇精馏工艺流程精馏单元采用预精馏塔+树脂吸附工艺技术生产MTO级甲醇。
MTO级甲醇精馏工艺流程示意图见图1。
来自合成单元的液相粗甲醇经甲醇膨胀罐闪蒸(膨胀气作为蒸汽过热炉单元的一部分辅助燃料气)、缓冲后进入预精馏塔。
在塔底再沸器和预塔空冷器的作用下,塔底上升甲醇蒸汽、塔顶回流液相甲醇及进料粗甲醇三股物料进行传质传热。
由此实现粗甲醇中轻组分与重组分的分离、提纯。
塔顶轻组分中含有少部分甲醇蒸汽经预塔空冷器和尾气冷却器冷凝后回收,其余轻组分经尾气过热器升温后作为蒸汽过热炉单元的一部分辅助燃料气。
塔底得到的重组分(主要成分为甲醇,其余为水和副产物)经甲醇空冷器和板式换热器冷却后进入MTO级甲醇精制单元。
经过预精馏的甲醇在甲醇过滤器内除去有机蜡,在离子交换器内除去碱金属和甲胺类杂质,进入树脂补集器(回收从离子交换器内漏出的少量树脂)。
经过以上分离精制操作,得到合格的MTO级甲醇产品送往下游甲醇制烯烃装置。
图1 MTO级甲醇精馏工艺流程示意图2影响MTO级甲醇精馏产品质量与能耗的因素2.1进料组成与温度的影响MTO级甲醇精馏的进塔物料为合成单元所产的粗甲醇,主要是由甲醇、水、有机杂质和少部分不凝气(CO2、CO、H2、CH4、N2)等组成的混合物。
通常以常温、常压下甲醇的沸点64.7℃为分界线,将沸点低于甲醇沸点的有机杂质称为轻组分,将沸点高于甲醇沸点的有机杂质称为重组分[1]。
精馏塔的原理及控制要求
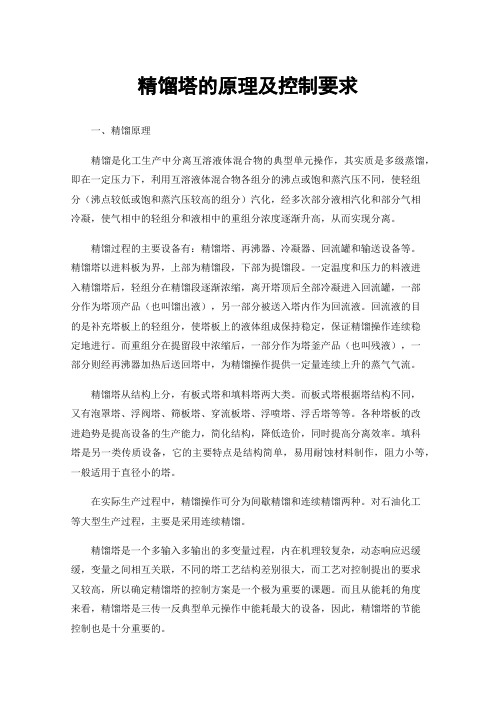
精馏塔的原理及控制要求一、精馏原理精馏是化工生产中分离互溶液体混合物的典型单元操作,其实质是多级蒸馏,即在一定压力下,利用互溶液体混合物各组分的沸点或饱和蒸汽压不同,使轻组分(沸点较低或饱和蒸汽压较高的组分)汽化,经多次部分液相汽化和部分气相冷凝,使气相中的轻组分和液相中的重组分浓度逐渐升高,从而实现分离。
精馏过程的主要设备有:精馏塔、再沸器、冷凝器、回流罐和输送设备等。
精馏塔以进料板为界,上部为精馏段,下部为提馏段。
一定温度和压力的料液进入精馏塔后,轻组分在精馏段逐渐浓缩,离开塔顶后全部冷凝进入回流罐,一部分作为塔顶产品(也叫馏出液),另一部分被送入塔内作为回流液。
回流液的目的是补充塔板上的轻组分,使塔板上的液体组成保持稳定,保证精馏操作连续稳定地进行。
而重组分在提留段中浓缩后,一部分作为塔釜产品(也叫残液),一部分则经再沸器加热后送回塔中,为精馏操作提供一定量连续上升的蒸气气流。
精馏塔从结构上分,有板式塔和填料塔两大类。
而板式塔根据塔结构不同,又有泡罩塔、浮阀塔、筛板塔、穿流板塔、浮喷塔、浮舌塔等等。
各种塔板的改进趋势是提高设备的生产能力,简化结构,降低造价,同时提高分离效率。
填科塔是另一类传质设备,它的主要特点是结构简单,易用耐蚀材料制作,阻力小等,一般适用于直径小的塔。
在实际生产过程中,精馏操作可分为间歇精馏和连续精馏两种。
对石油化工等大型生产过程,主要是采用连续精馏。
精馏塔是一个多输入多输出的多变量过程,内在机理较复杂,动态响应迟缓缓,变量之间相互关联,不同的塔工艺结构差别很大,而工艺对控制提出的要求又较高,所以确定精馏塔的控制方案是一个极为重要的课题。
而且从能耗的角度来看,精馏塔是三传一反典型单元操作中能耗最大的设备,因此,精馏塔的节能控制也是十分重要的。
二、精馏塔的主要干扰因素精馏塔的主要干扰因素为进料状态,即进料流量F、进料组分zf ,进料温度Tf或热焓FE.此外,冷剂与加热剂的压力和温度及环境温度等因素也会影响精馏塔的平衡操作。
浅谈精馏操作的节能优化措施

浅谈精馏操作的节能优化措施摘要:石油化工是我国经济发展中的一个重要产业,数据显示,石油化工能耗约占全国工业总能耗的15%。
在能源消耗领域,分离工序占能源消耗的41%至71%,而蒸馏工序占能源消费的96%。
在热力学上,蒸馏是一种非常低效的能耗操作,具有很强的热力学不可逆性。
因此,作为蒸馏操作中的中间操作,蒸馏塔系统的整个操作过程都以产品质量合格和能耗最低为标准。
然而,优化蒸馏操作需要许多因素。
本文从以下几个方面分析了精馏操作的节能措施。
关键词:蒸馏;节能;发展趋势;技术分析前言蒸馏操作是化工生产中的一个重要操作单元,因其能耗高、节能效果好而备受关注。
降低市场产品生产过程中的生产能耗是降低成本、提高市场竞争力的关键,而蒸馏操作过程具有节能效果。
一、蒸馏的工作原理蒸馏是化学生产中分离不混溶液体混合物的典型单元操作。
其本质是多级蒸馏,利用不混溶液体混合物中每种成分在一定压力下的不同沸点或饱和蒸气压来蒸发轻组分(沸点较低或蒸气压较高的组分)。
经过多次部分液相蒸发和部分气相冷凝,气相中轻组分和液相中重组分的浓度逐渐增加,从而实现分离。
在此过程中,传热和传质过程同时进行,属于传质过程控制。
原料从塔中间合适的位置送入塔中,塔分为两段。
上段是没有进料的蒸馏段,下段包含作为保留段的进料板。
冷凝器从塔顶提供液相回流,再沸器从塔底提供气相回流。
气相和液相的回流是蒸馏的一个重要特征。
蒸馏塔是一种提供混合物气相和液相之间接触条件并实现传质过程的设备。
该设备可分为两类:一类是板式蒸馏塔,另一类是填料蒸馏塔。
二、精馏塔影响的因素1.回流比的影响影响蒸馏塔分离效果的主要原因是回流比,在实际操作和生产中通常通过改变回流比来控制回流比,以控制产品质量。
蒸馏段中操作线的斜率(蒸馏段中下降液体的摩尔流速与上升蒸汽的摩尔流速的比率)与回流比成正比,该段中的传质驱动力也与回流比直接成正比。
具体来说,在确定回收率的条件下,如果用增加回流比来提高分离度,则应满足以下要求:首先,由于蒸馏塔理论塔板数的限制,在规定的塔板数范围内,即使回流比增加到无穷大(总回流),分离度总是存在一个极限最大值;其次,由于整个塔中物料平衡的限制,分离极限为FxF/Dx (F为原料液中挥发性成分的摩尔分数)。
精馏塔的浮压控制与节能

第3 0卷第 3期
2O O 2年 6月
江 苏 化 工
Ja gu C  ̄ne n u ty in s . i Id sr h al
V0 . 0 No. J3 3
Jn.0 2 u 2 O
技 与 装 釜
精 馏 塔 的 浮 压 控 制 与 节 能
维普资讯
第3 0卷第 3期
张大年 : 精馏塔 的浮压控制与节 能
4 5
温度 将 降 低 到 热 负 荷 和 冷 却 剂 温 度 许 可 达 到 的 程 度 。对 大 多数 混 合 物来 说 , 对 挥 发 度 随 温 度 和 压 相 力 的 降低 而 改善 , 而 达 到 同样 的分 离 度 所 需 的能 因 量 较少 。冷 却剂 温 度 每降 低 06K所 节 省 的能 量 约 . 为 1 , % 这对 于 采用 空 冷 器 的 塔 更 为 可取 , 因为 空 冷 器 的冷 却 效 果 易 受 环 境 条 件 变 化 的影 响 。 当然 , 在 操 作压 力 变 化后 , 须 对 塔 的供 热 或 回 流 作 相 应 的 必
塔压 控制技术 的节能效果 和经济效益 。
关键 词 : 馏塔 ; 精 相对挥发度 ; 浮压 操作 ; 浮压控制
中图分类号 :B 5 . T 67 6 文献标识码 : A 文章编号 :02—1 1(02 0 O 4 10 16 20 )3一 04—0 4
在 大多 数 化 工 厂 和 所 有 的炼 油 厂 中 , 馏 塔 总 精 是 必 不可 少 的 , 而且 精 馏所 消耗 的能 量也 是 很 大 的 。 因此 , 研究 精 馏过 程 节 能 问题 的论 著 也层 出不穷 , 并 提 出 了一 系列 的 新 型 的控 制 系统 和控 制 方 法 , 浮 如 压 操作 、 门位置 调 节 器 、 汽 压缩 系 统 以及 能 量 的 阀 蒸 合理 分 配 等 _ J l 。通 过 这 些 系 统 和 方 法 , 量 节 省 尽
精馏操作中的工艺指标调节与控制
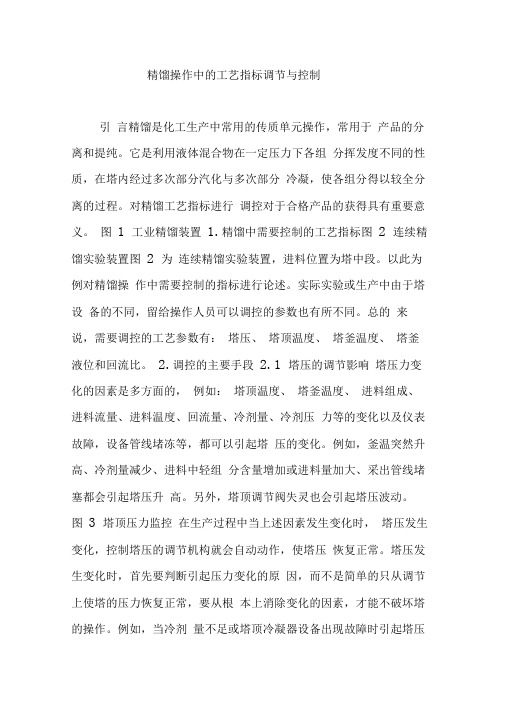
精馏操作中的工艺指标调节与控制引言精馏是化工生产中常用的传质单元操作,常用于产品的分离和提纯。
它是利用液体混合物在一定压力下各组分挥发度不同的性质,在塔内经过多次部分汽化与多次部分冷凝,使各组分得以较全分离的过程。
对精馏工艺指标进行调控对于合格产品的获得具有重要意义。
图1 工业精馏装置1.精馏中需要控制的工艺指标图2 连续精馏实验装置图2 为连续精馏实验装置,进料位置为塔中段。
以此为例对精馏操作中需要控制的指标进行论述。
实际实验或生产中由于塔设备的不同,留给操作人员可以调控的参数也有所不同。
总的来说,需要调控的工艺参数有:塔压、塔顶温度、塔釜温度、塔釜液位和回流比。
2.调控的主要手段2.1 塔压的调节影响塔压力变化的因素是多方面的,例如:塔顶温度、塔釜温度、进料组成、进料流量、进料温度、回流量、冷剂量、冷剂压力等的变化以及仪表故障,设备管线堵冻等,都可以引起塔压的变化。
例如,釜温突然升高、冷剂量减少、进料中轻组分含量增加或进料量加大、采出管线堵塞都会引起塔压升高。
另外,塔顶调节阀失灵也会引起塔压波动。
图3 塔顶压力监控在生产过程中当上述因素发生变化时,塔压发生变化,控制塔压的调节机构就会自动动作,使塔压恢复正常。
塔压发生变化时,首先要判断引起压力变化的原因,而不是简单的只从调节上使塔的压力恢复正常,要从根本上消除变化的因素,才能不破坏塔的操作。
例如,当冷剂量不足或塔顶冷凝器设备出现故障时引起塔压升高时,若不提高冷剂量,而只是加大塔顶采出量来恢复正常的塔压,就有可能使重组份带到精馏段,造成塔顶产品质量不合格;又如,釜温过低引起塔压下降,若不提釜温,而是单靠通过减少塔顶采出量来恢复正常塔压,将造成釜液中轻组分大量增加,使塔底产品不合格。
当釜温突然升高,引起塔压上升时,重要的是恢复塔釜正常的温度,而不是单靠增加冷剂量和加大塔顶采出量来降低塔压;否则将容易产生液泛,破坏塔的正常操作。
精馏操作中,要针对引起塔压变化的原因相应的进行调节,常用的方法有三种。
精馏塔节能降耗项目
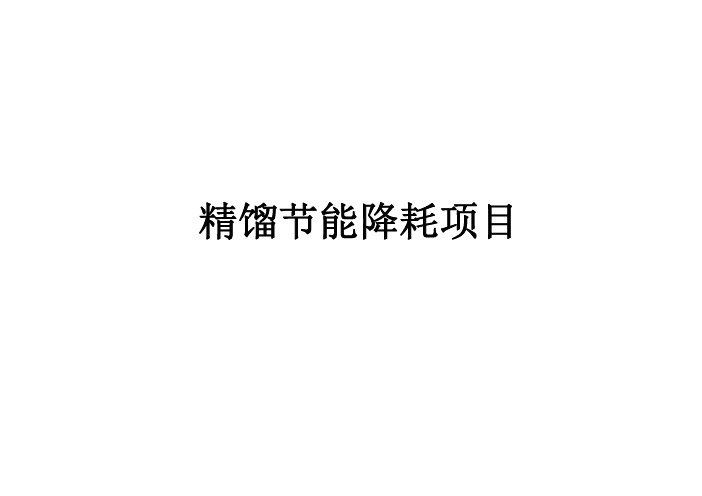
SIPOC 价值流图
项目管理 变革管理
项目输出
项目选题理由 项目指标及其定
义 项目目标 项目团队 项目立项书
完成项目立项书
项目立项书
D1 项目背景
1.战略之声 : 正确认识经济危机对企业所带来的影响,提高产品质量,降低成本,增强企 业的核心竞争力是未来发展之本; 2.客户之声 : 目前,天然气资源缺乏,燃料费用不断增加;我们必须把节约燃料作为节能 降耗的首要任务。
结论: 左图为DCS报表样本,所收集数据来源于 DCS报表,数据真实准确!因此在这个项目中 ,关键输出的测量系统是合格的,我们进行下 一步研究是有意义的。
M3 对AMS塔再沸器热油流量(Y1)现状的分析
AMS塔再沸器热油流量(Y1)从09年8月11日至09年11月9日的控制趋 势如下图:
Y1测量阶段数据
从图中可以看出目前AMS塔再沸器供油温度(Y2)的控制比较稳定,均值是 308.65℃。此温度的控制指标是307-310℃。下面我们对AMS塔再沸器供油温 度(Y2)的过程能力进行分析。
M5 对AMS塔再沸器供油温度(Y2)现状的分析
精馏塔控制方案

精馏塔控制方案引言精馏塔是一种常用的化工设备,广泛应用于石油、化工、制药等行业。
精馏塔的控制是保证塔内蒸汽、冷凝液、流体等流动的关键,能够有效地提高产品纯度和产量。
本文将介绍一种精馏塔控制方案,以提高塔的稳定性和效率。
1. 控制策略1.1 温度控制精馏塔的温度控制是塔内液体和蒸汽相平衡的关键。
通过控制塔顶和塔底的温度,可以调节塔内液位和物料的分离。
常见的控制策略有:•温度比例控制:根据塔顶温度的偏差与目标温度之间的比例关系,调整塔底的回流液流量。
•迭代控制:根据塔底液位的变化,通过反馈调整塔顶温度控制器的参数,以逐步达到温度的稳定。
1.2 压力控制精馏塔的压力控制主要是为了控制蒸汽流量和流体的分布。
压力控制可以通过以下策略实现:•PID控制:利用压力变送器测量塔内压力,并通过PID控制器调节废气量或提升风扇的转速,以保持塔内压力稳定。
•模型预测控制:利用塔内流体的数学模型,预测下一时刻的压力,然后通过调节控制器输出,实现精确的压力控制。
1.3 液位控制精馏塔的液位控制是控制塔内液体高度的重要环节,液位控制的好坏影响着塔内液体的扩散和分离效果。
常见的控制策略有:•PID控制:通过测量塔内液位高度,并根据设定的目标值进行反馈调节,保持液位稳定。
•前馈控制:通过预先计算液位的变化趋势,利用前馈信号及时调整液位,以提高液位的控制精度。
2. 性能评估为了评估控制方案的有效性和稳定性,需要对精馏塔的控制系统进行性能评估。
常用的评估指标有:•稳态误差:指控制系统在稳定状态下与目标值之间的偏差,稳态误差越小,说明控制系统越稳定。
•动态响应:指控制系统对于输入信号的响应速度和抑制扰动的能力。
动态响应越快,说明控制系统的响应速度越高。
•系统稳定性:通过计算系统的闭环传递函数,判断系统是否稳定。
如果传递函数的特征根都具有负实部,说明系统稳定。
3. 控制优化为了进一步提高精馏塔的控制效果,可以采用控制优化的方法。
常见的控制优化技术有:•模型预测控制:利用精馏塔的数学模型,预测未来一段时间内的塔内流体状态,并根据预测结果进行控制器的调整。
精馏塔控制和节能优化分析
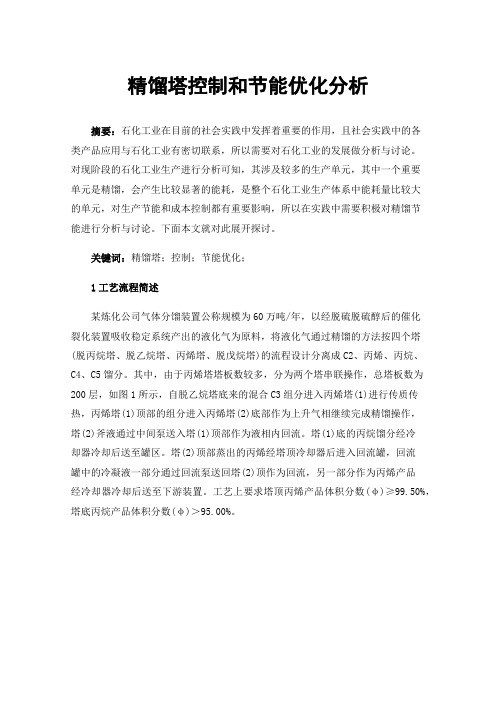
精馏塔控制和节能优化分析摘要:石化工业在目前的社会实践中发挥着重要的作用,且社会实践中的各类产品应用与石化工业有密切联系,所以需要对石化工业的发展做分析与讨论。
对现阶段的石化工业生产进行分析可知,其涉及较多的生产单元,其中一个重要单元是精馏,会产生比较显著的能耗,是整个石化工业生产体系中能耗量比较大的单元,对生产节能和成本控制都有重要影响,所以在实践中需要积极对精馏节能进行分析与讨论。
下面本文就对此展开探讨。
关键词:精馏塔;控制;节能优化;1工艺流程简述某炼化公司气体分馏装置公称规模为60万吨/年,以经脱硫脱硫醇后的催化裂化装置吸收稳定系统产出的液化气为原料,将液化气通过精馏的方法按四个塔(脱丙烷塔、脱乙烷塔、丙烯塔、脱戊烷塔)的流程设计分离成C2、丙烯、丙烷、C4、C5馏分。
其中,由于丙烯塔塔板数较多,分为两个塔串联操作,总塔板数为200层,如图1所示,自脱乙烷塔底来的混合C3组分进入丙烯塔(1)进行传质传热,丙烯塔(1)顶部的组分进入丙烯塔(2)底部作为上升气相继续完成精馏操作,塔(2)斧液通过中间泵送入塔(1)顶部作为液相内回流。
塔(1)底的丙烷馏分经冷却器冷却后送至罐区。
塔(2)顶部蒸出的丙烯经塔顶冷却器后进入回流罐,回流罐中的冷凝液一部分通过回流泵送回塔(2)顶作为回流,另一部分作为丙烯产品经冷却器冷却后送至下游装置。
工艺上要求塔顶丙烯产品体积分数(φ)≥99.50%,塔底丙烷产品体积分数(φ)>95.00%。
图 1 气体分馏装置丙烯塔工艺流程示意2分离序列的选择在精馏的过程中需要强调如下内容:(1)在产品分离的过程中需要按照塔顶产品的挥发度依次递减的顺序进行逐个回收;(2)通过实验对最难分离的组分进行确定,并在精馏的过程中将其放在最末端进行分离;(3)进料按照塔顶和塔底各占50%的分馏比例进行安排;(4)如果是纯度要求比较高的产品,可以放在最后进行分离;(5)如果组分当中有容易造成系统结焦或者腐蚀的,需要在提高后续设备材质要求之后再强调稳定的操作;(6)如果混合物当中的组分存在沸点相差比较大的情况,而且有的组分需要在冷冻的条件下才能够进行分离,应当使进入到冷冻系统或者是冷冻等级更高的系统当中的组分尽可能减少,这样,最终的分离效果会更加理想。
精馏塔控制和节能优化研究综述

精馏塔控制和节能优化研究综述摘要:精馏过程是一个复杂的传质传热过程,表现为过程变量多,被控变量多,可操纵的变量也多,过程动态和机理复杂。
作为化工生产中应用最广的分离过程,精馏也是耗能较大的一种化工单元操作。
但在实际生产中,为了保证产品合格,精馏装置操作往往偏于保守,操作方法以及操作参数设置往往欠合理,过分离普遍存在。
精馏过程消耗的能量绝大部分并非用于组分分离,而是被冷却水或分离组分带走。
因此,精馏过程的节能潜力很大,收效也极为明显。
本文简单介绍了精馏原理,针对精馏塔控制和节能优化展开了深入的研究分析,结合本次研究,发表了一些自己的建议看法,希望可以对精馏塔控制以及节能优化起到一定的参考和帮助,提高精馏塔控制和节能优化有效性。
关键词:精馏塔;控制;节能优化前言:通过对精馏塔的研究过程中发现,在精馏的过程中,会消耗较多的能源,热力学的效率也会出现很大程度的降低,因此,对于化工行业来说,当前困扰着我国化工行业很多专家的一个难题。
在一般的情况下,精馏塔的设计会很大程度上的影响着资源的消耗情况,好的精馏塔结构将为化工省下大量资源,有效提高行业经济效益,降低精馏成本,由此可见,对精馏塔的研究和分析具有非常积极的意义。
1、精馏原理介绍精馏操作属于化工生产行业中较为常见的处理流程之一,其需要将混合物体内部液体部分、气体部分进行接触操作,使相关物质在固定条件下进行反应。
常规状态中,物质会在逆向流动、全面接触前提下逐渐开始反应流程,使液相内部轻组分快速进入气相内部,气相完成重组分操作,最终进入液相内部。
精馏本质属于传质活动,会导致热量不断传导,最终达成反应目标。
在压力恒定环境下,独立组分液体沸腾会持续产生加热效果,但温度却始终维持原有状态。
多组分液体会同样会在沸腾阶段持续加热,但温度会发生对应变化。
恒定压力会使溶液气相平衡与组分存在产生相对联系,组分沸腾温度点越高、浓度级别越高、平衡状态所需温度级别也会越高。
因此,相对于物质气液相平衡状态,溶液气液进入平衡具有独特表现,即气相、液相平衡浓度存在差异。
精馏塔控制和节能优化路径探析
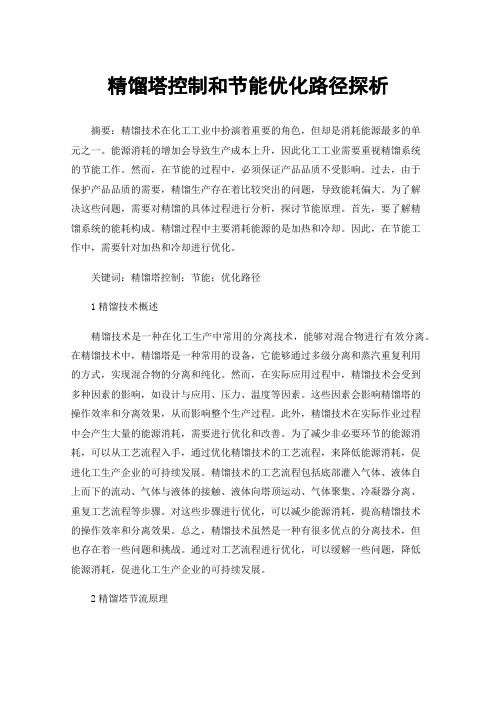
精馏塔控制和节能优化路径探析摘要:精馏技术在化工工业中扮演着重要的角色,但却是消耗能源最多的单元之一。
能源消耗的增加会导致生产成本上升,因此化工工业需要重视精馏系统的节能工作。
然而,在节能的过程中,必须保证产品品质不受影响。
过去,由于保护产品品质的需要,精馏生产存在着比较突出的问题,导致能耗偏大。
为了解决这些问题,需要对精馏的具体过程进行分析,探讨节能原理。
首先,要了解精馏系统的能耗构成。
精馏过程中主要消耗能源的是加热和冷却。
因此,在节能工作中,需要针对加热和冷却进行优化。
关键词:精馏塔控制;节能;优化路径1精馏技术概述精馏技术是一种在化工生产中常用的分离技术,能够对混合物进行有效分离。
在精馏技术中,精馏塔是一种常用的设备,它能够通过多级分离和蒸汽重复利用的方式,实现混合物的分离和纯化。
然而,在实际应用过程中,精馏技术会受到多种因素的影响,如设计与应用、压力、温度等因素。
这些因素会影响精馏塔的操作效率和分离效果,从而影响整个生产过程。
此外,精馏技术在实际作业过程中会产生大量的能源消耗,需要进行优化和改善。
为了减少非必要环节的能源消耗,可以从工艺流程入手,通过优化精馏技术的工艺流程,来降低能源消耗,促进化工生产企业的可持续发展。
精馏技术的工艺流程包括底部灌入气体、液体自上而下的流动、气体与液体的接触、液体向塔顶运动、气体聚集、冷凝器分离、重复工艺流程等步骤。
对这些步骤进行优化,可以减少能源消耗,提高精馏技术的操作效率和分离效果。
总之,精馏技术虽然是一种有很多优点的分离技术,但也存在着一些问题和挑战。
通过对工艺流程进行优化,可以缓解一些问题,降低能源消耗,促进化工生产企业的可持续发展。
2精馏塔节流原理精馏塔是一种用于精馏的设备,在化工行业中广泛应用。
为了提高精馏塔的效率和节约能源,需要对其运行过程进行分析和明确节能的地方。
精馏过程实际上就是将物流有效能转化为扩散有效能,通过这种方式可以降低能量损失。
甲醇精馏提质节能合同能源管理
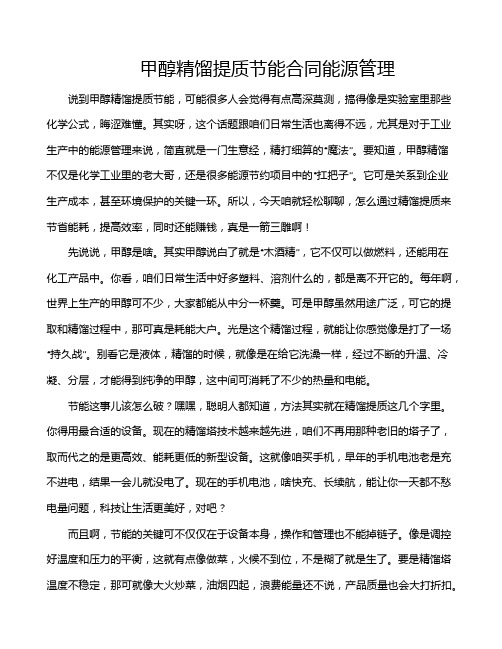
甲醇精馏提质节能合同能源管理说到甲醇精馏提质节能,可能很多人会觉得有点高深莫测,搞得像是实验室里那些化学公式,晦涩难懂。
其实呀,这个话题跟咱们日常生活也离得不远,尤其是对于工业生产中的能源管理来说,简直就是一门生意经,精打细算的“魔法”。
要知道,甲醇精馏不仅是化学工业里的老大哥,还是很多能源节约项目中的“扛把子”。
它可是关系到企业生产成本,甚至环境保护的关键一环。
所以,今天咱就轻松聊聊,怎么通过精馏提质来节省能耗,提高效率,同时还能赚钱,真是一箭三雕啊!先说说,甲醇是啥。
其实甲醇说白了就是“木酒精”,它不仅可以做燃料,还能用在化工产品中。
你看,咱们日常生活中好多塑料、溶剂什么的,都是离不开它的。
每年啊,世界上生产的甲醇可不少,大家都能从中分一杯羹。
可是甲醇虽然用途广泛,可它的提取和精馏过程中,那可真是耗能大户。
光是这个精馏过程,就能让你感觉像是打了一场“持久战”。
别看它是液体,精馏的时候,就像是在给它洗澡一样,经过不断的升温、冷凝、分层,才能得到纯净的甲醇,这中间可消耗了不少的热量和电能。
节能这事儿该怎么破?嘿嘿,聪明人都知道,方法其实就在精馏提质这几个字里。
你得用最合适的设备。
现在的精馏塔技术越来越先进,咱们不再用那种老旧的塔子了,取而代之的是更高效、能耗更低的新型设备。
这就像咱买手机,早年的手机电池老是充不进电,结果一会儿就没电了。
现在的手机电池,啥快充、长续航,能让你一天都不愁电量问题,科技让生活更美好,对吧?而且啊,节能的关键可不仅仅在于设备本身,操作和管理也不能掉链子。
像是调控好温度和压力的平衡,这就有点像做菜,火候不到位,不是糊了就是生了。
要是精馏塔温度不稳定,那可就像大火炒菜,油烟四起,浪费能量还不说,产品质量也会大打折扣。
节能的核心就是用更少的能量,达到更好的分离效果。
所以啊,精馏过程中一旦温度和压力被精准控制,就能降低能耗,实现“事半功倍”的效果。
再有一点,不得不提的就是合同能源管理。
精馏塔的自动控制

第三节 精馏塔的自动控制
• 二、精馏塔的干扰因素
1.进料流量F的波动(*) 2.进料成分ZF的变化(*) 3.进料温度TF的变化 4.再沸器加热剂(如蒸汽)加入热量 的变化 5.冷却剂在冷凝器内除去热量的变化 6.环境温度的变化
图10-41 精馏塔的物料 流程图
第4页41/共13页
第三节 精馏塔的自动控制
• 三、精馏塔的控制方案
1.精馏塔的提馏段温控 以提馏段温度作为衡量产品质量的间接指标,而以改变再
沸器加热量作为控制手段的方案,就称为提馏段温控。
图10-42 提馏段温控的控制方案示意图
第5页42/共13页
第三节 精馏塔的自动控制 提馏段温控的主要特点与使用场合: (1)采用了提馏段温度作为间接质量指标,因 此它能较直接地反映提馏段产品情况。将提馏段 温度恒定后,就能较好地保证塔底产品的质量达 到规定值。 (2)当干扰首先进入提馏段时(液相进料), 用提馏段温控就比较及时,动态过程也比较快。
第6页43/共13页
第三节 精馏塔的自动控制 2.精馏塔的精馏段温控 以精馏段温度作为衡量产品质量的间接指标,而以改变 回流量作为控制手段的方案,就称为精馏段温控。
图10-43 精馏段温控的控制方案示意图
第7页44/共13页
第三节 精馏塔的自动控制 精馏段温控的主要特点与使用场合: ① 采用了精馏段温度作为间接质量指标,因此它能较 直接地反映精馏段的产品情况。当塔顶产品纯度要求 比塔底严格时,一般宜采用精馏段温控方案。 ② 如果干扰首先进入精馏段(气相进料),采用精馏 段温控就比较及时。
第9页46/共13页
第三节 精馏塔的自动控制
3.精馏塔的温差控制及双温差控制
采用温差作为衡量质量指标的间接变量,是为了消除 塔压波动对产品质量的影响。