铸件粗糙度及粗糙度计算
铸件外观检查一般标准
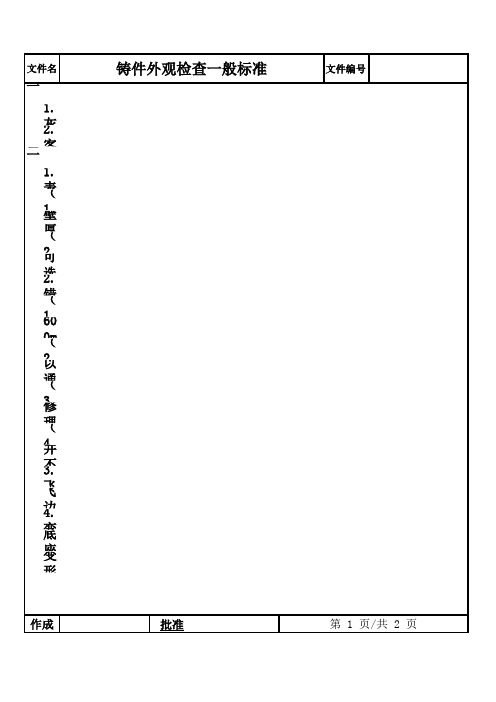
一.适用范围:1.灰铸铁和球墨铸铁件;2.客户有专门要求的以客户要求为准。
二.细 则:1.表面粗糙度:(1)表面粗糙度的凸凹高度差:壁厚10mm 以下要小于0.3mm;壁厚10mm以上要小于0.5mm。
局部超标可以打磨,打磨后再抛丸。
(2)表面粗糙度越细越好,但里面和外面,平面和垂直面要均匀。
可选用典型产品作为比照样板。
2.错箱和涨箱:(1)铸件分型面最大尺寸100mm以内,错箱要小于1mm;100至600mm错箱要小于2mm;600mm以上错箱要小于3.5mm。
(2)如果产品在本厂加工,而且错箱超差能够通过加工修正的,可以通过加工重新修正,但这些产品要分开管理。
(3)非加工面的涨箱,如果能够通过打磨或简单加工去除的,可以修理,但修理后要再抛丸。
(4)加工面出现的涨箱(指在本厂加工的加工面),只要能够去除并不影响其它尺寸,可以算合格毛坯。
3.飞边毛刺:飞边毛刺打磨残留量在0.5mm以下即可。
4.变形、翘曲:底座、盖板类的变形挠度允许量:自由状态放置在平台上,其最大变形量要保证在总长度的0.5%以下,比如600mm长可以3mm以下。
作成第 1 页/共 2 页批准5.气孔、渣眼、砂眼类:(1)加工面不允许有此类缺陷。
在本厂加工的产品,加工面孔眼不超过加工量,可以通过加工去除。
(2)非加工面的孔眼可以修补(铁基修补胶)、焊补,但必须符合以下范围:深度小于该部壁厚的三分之一、长或宽小于该部壁厚;数量5处以下。
需要电镀、热镀、粉体涂漆、电泳涂漆的不在此列。
6.表面皱纹:皱纹深度小于0.5mm,长度小于四倍壁厚,可以通过打磨方法处理。
7.冷隔、浇不足:冷隔(汤境)浇不足为废品,不能修补。
8.多肉:掉砂多肉通过铲磨不能恢复原形状的为废品。
9.缺肉:掉砂碰伤浇口根部缺肉,参考孔眼类的修补范围。
10.打磨修补:(1)打磨后残留量保证在0.5mm以下,不允许过度打磨。
(2)局部打磨过度的限度:深1mm长度不超过该部壁厚。
铸件粗糙度及粗糙度计算学习资料
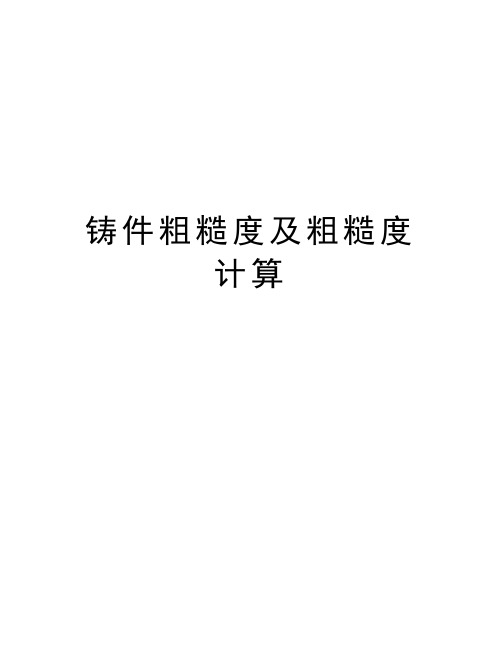
铸件粗糙度及粗糙度计算铸件表面粗糙度铸件表面粗糙度是衡量干净、真实的铸件表面质量的重要指标。
铸件铸造表面粗糙度是按不同铸造合金及其铸造方法、用其表面轮廓算术平均偏差Ra 值(单位为μm)进行分级,分级应符合表1~1的规定。
对照GB/T6060.1——1997《表面粗糙度比较样块—铸造表面》的规定进行比较和评比;其评比方法按GB∕T15056——1994《铸造表面粗糙评定方法》进行。
对于重要铸件,当所有铸造表面的粗糙度要求相同时,可在铸件图样或铸造工艺图样的右上角同意标注粗糙度符号。
如果大部分铸造表面度相同时,可将该级粗糙度符号统一标注在图样的右上角,并在符号前加注“其余”两字;余下的部分表面粗糙度,将其符号直接标注在其表面轮廓或尺寸或尺寸延长线上。
铸造表面粗糙度,也可按需方的要求或供需方的协商,将其公称值鉴订在订货合同中。
注:×为采取特殊措施方能达到的铸件铸造表面粗糙度; ※表示可以达到的铸件铸造表面粗糙度。
表1~2粗糙度与光洁度对照(单位:mm)粗糙度的计算表面粗糙度现在越来越受到各行业的重视,论坛里也经常问及如何提高表面粗糙度的帖子.今天讲一下关于车削的表面粗糙度.图片上面有车削表面粗糙度的计算方式,只需要将切削参数代入即可计算出可能最高的"表面粗糙度"(以下发言全部以粗糙度低为细,粗糙度高为粗)车削表面粗糙度=每转进给的平方 *1000/(刀尖R乘8)以上计算方式是理论上的可能达到最坏的的效果,实际上因刀具品质、机床刚性精度、切削液、切削温度、切削速度、材料硬度等等原因,会将粗糙度提高或者降低的,如果你用上面的计算方式计算出来的粗糙度都不能满足想达到的效果,请先更改切削参数。
但进给一般和切深有着密切的关系,一般进给是切深的10%~20%之间,排削的效果是最好的切削深度,因为屑的宽度和厚度最合比例以上公式的各个参数我下面详细一项项解释一下对粗糙度的影响,如有不正请指点:1:进给——进给越大粗糙度越大,进给越大加工效率越高,刀具磨损越小,所以进给一般最后定,按照需要的粗糙度最后定出进给2:刀尖R——刀尖R越大,粗糙度越降低,但切削力会不断增大,对机床的刚性要求更高,对材料自身的刚性也要求越高。
铸件抛丸后的表面粗糙度值

铸件抛丸后的表面粗糙度值铸件抛丸后的表面粗糙度值一直是工程领域中一个重要的技术指标。
铸件经过抛丸处理后,可以有效地去除铸造缺陷和残留应力,改善表面质量。
本文将介绍铸件抛丸后表面粗糙度值的评价标准及其影响因素。
一、表面粗糙度值的评价标准表面粗糙度值是衡量铸件抛丸后表面质量的主要指标。
通常使用的评价标准有Ra、Rz、Rmax等。
1. Ra值是表面粗糙度的平均值,指表面轮廓线与其平均线之间的平均垂直距离。
常见的测量方法是使用粗糙度仪对铸件表面进行扫描,得出Ra值。
Ra值越小,表面质量越好。
2. Rz值是表面粗糙度的十点平均距离,指表面轮廓线上最高点与最低点之间的垂直距离。
测量方法与Ra值相似,只是计算方法不同。
3. Rmax值是表面粗糙度的最大高低度,即表面轮廓线上峰值与谷值之间的垂直距离。
以上三种评价标准综合考虑了表面粗糙度的不同特征,可以更全面地描述铸件抛丸后的表面质量。
二、影响铸件抛丸后表面粗糙度值的因素铸件抛丸后的表面粗糙度值受多种因素的影响,主要包括抛丸介质、抛丸时间、抛丸强度和抛丸角度等。
1. 抛丸介质:抛丸介质的选择直接影响了表面质量和粗糙度值。
常见的抛丸介质有钢丸、铝丸和玻璃珠等。
不同的抛丸介质在与铸件表面碰撞的过程中,对表面的冲击力和切削力不同,因此会产生不同的粗糙度效果。
2. 抛丸时间:抛丸时间是指铸件在抛丸机中暴露在抛丸介质下的时间。
抛丸时间的长短直接影响了表面的处理效果和粗糙度值。
通常情况下,抛丸时间越长,铸件表面质量越好,但是过长的抛丸时间也会导致能耗和设备磨损的增加。
3. 抛丸强度:抛丸强度是指抛丸机中的抛丸力量。
抛丸强度的大小直接影响了抛丸后的表面质量和粗糙度值。
强度过大会导致表面磨损过度,而强度过小则无法达到预期的抛丸效果。
4. 抛丸角度:抛丸角度是指抛丸介质与铸件表面相对运动的角度。
角度的选择决定了抛丸冲击力的方向和大小。
合适的抛丸角度能够均匀地冲击铸件表面,提高抛丸效果和表面质量。
表面粗糙度的标注
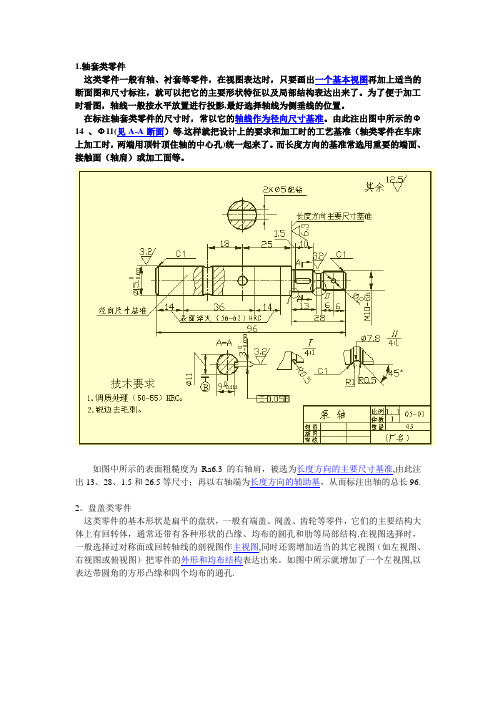
1.轴套类零件这类零件一般有轴、衬套等零件,在视图表达时,只要画出一个基本视图再加上适当的断面图和尺寸标注,就可以把它的主要形状特征以及局部结构表达出来了。
为了便于加工时看图,轴线一般按水平放置进行投影,最好选择轴线为侧垂线的位置。
在标注轴套类零件的尺寸时,常以它的轴线作为径向尺寸基准。
由此注出图中所示的Ф14 、Ф11(见A-A断面)等.这样就把设计上的要求和加工时的工艺基准(轴类零件在车床上加工时,两端用顶针顶住轴的中心孔)统一起来了。
而长度方向的基准常选用重要的端面、接触面(轴肩)或加工面等。
如图中所示的表面粗糙度为Ra6.3的右轴肩,被选为长度方向的主要尺寸基准,由此注出13、28、1.5和26.5等尺寸;再以右轴端为长度方向的辅助基,从而标注出轴的总长96.2。
盘盖类零件这类零件的基本形状是扁平的盘状,一般有端盖、阀盖、齿轮等零件,它们的主要结构大体上有回转体,通常还带有各种形状的凸缘、均布的圆孔和肋等局部结构.在视图选择时,一般选择过对称面或回转轴线的剖视图作主视图,同时还需增加适当的其它视图(如左视图、右视图或俯视图)把零件的外形和均布结构表达出来。
如图中所示就增加了一个左视图,以表达带圆角的方形凸缘和四个均布的通孔.在标注盘盖类零件的尺寸时,通常选用通过轴孔的轴线作为径向尺寸基准,长度方向的主要尺寸基准常选用重要的端面。
3.叉架类零件这类零件一般有拨叉、连杆、支座等零件。
由于它们的加工位置多变,在选择主视图时,主要考虑工作位置和形状特征。
对其它视图的选择,常常需要两个或两个以上的基本视图,并且还要用适当的局部视图、断面图等表达方法来表达零件的局部结构。
踏脚座零件图中所示视图选择表达方案精练、清晰对于表达轴承和肋的宽度来说,右视图是没有必要的,而对于T字形肋,采用剖面比较合适。
在标注叉架类零件的尺寸时,通常选用安装基面或零件的对称面作为尺寸基准。
尺寸标注方法参见图。
4.箱体类零件一般来说,这类零件的形状、结构比前面三类零件复杂,而且加工位置的变化更多。
钛合金铸件表面粗糙度要求

钛合金铸件表面粗糙度要求
钛合金是一种具有优异力学性能和耐腐蚀性的重要材料,广泛应用于航空、航天、医疗和化工等领域。
钛合金铸件作为钛合金制造中的重要一环,其表面粗糙度的要求也十分重要。
钛合金铸件表面粗糙度可以影响铸件的机械性能和耐腐蚀性能。
因此,对于不同用途的钛合金铸件,在生产前需制定不同的表面粗糙度要求标准。
一般来说,钛合金铸件的表面粗糙度要求应符合相关标准和规范。
例如,航空领域的钛合金铸件表面粗糙度标准应符合AS9100标准,
医疗领域的钛合金铸件表面粗糙度标准应符合ISO 13485标准等。
此外,钛合金铸件表面粗糙度的要求还应根据铸件的形状和尺寸、使用环境和工艺条件等进行综合考虑。
例如,对于表面平整的钛合金铸件,其表面粗糙度应控制在0.8μm以下;对于表面凸凹不平的钛
合金铸件,其表面粗糙度应控制在3.2μm以下。
总之,钛合金铸件的表面粗糙度要求是十分严格的,需根据不同用途和情况进行制定和控制,以保证其机械性能和耐腐蚀性能的稳定和可靠。
- 1 -。
铸造件表面缺陷标准

铸造件表面缺陷标准:
铸造件表面缺陷标准因铸造材料、工艺和应用场景而异,以下是一些常见的铸造件表面缺陷及其标准:
1.粘砂:指铸造件表面有砂粒嵌入的情况,可通过控制砂粒大小、形状和粘度等来减少粘砂现象。
2.粗糙度:铸造件表面的粗糙度取决于铸造工艺和材料,一般要求表面光滑、无明显凹凸不平。
具
体标准可根据实际需求和用途确定。
3.气孔:铸造过程中产生的气体在铸件内部或表面形成的小孔洞,可通过控制铸造工艺和材料来减
少气孔。
4.夹渣:铸造过程中夹杂的固体杂质,可通过控制熔炼和浇注过程来减少夹渣。
5.裂纹:铸造件表面或内部的裂纹,通常是由于热处理不当或铸造工艺不合理引起的。
标准要求铸
件无裂纹。
6.变形:铸造件形状与设计要求不一致的现象,可通过控制铸造工艺和后处理来减小变形。
7.缩孔:铸造过程中因金属冷却收缩而在铸件内部或表面形成的孔洞,可通过控制铸造工艺和材料
来减少缩孔。
零件图的技术要求(新版粗糙度标号)

一 表面粗糙度
1.表面粗糙度的概念
表面粗糙度是指零件的加工表面上具有的较 小间距和峰谷所形成的微观几何形状误差。
2.表面粗糙度的主要评定参数Ra
轮廓算术平均偏差——Ra是评定零件表面粗糙度 最常用的参数,它是在取样长度L范围内,相对于基准 线的轮廓偏差绝对值的算术平均值。
Y
yi
基准线
X
L
Ra=-L1 ∫ 0Ly(x) dx 近似为: Ra=-N1 ∑in=1 yi
零线
0-
G
H
JS J
K
MN
P
RS
UV T
X Y Z ZA ZB
0
ZC
基本尺寸
基本偏差代号:孔、轴各28种
zc
基本尺寸
0
+
-
m n p r s t u v x y z zazb 零线
轴 c
cd
d
e
ef
f
fg g
h
js k j
另一偏差可按下式计算:
0
b 孔 : ES= EI+IT或者EI = ES – IT
答案:ES= +0.033、EI=0 答案: es= -0.020、ei=-0.041
)
)
-0.020 -0.041
+0.033 0
ØØ3300ff77(
ØØ3300HH88(
Ø30表示什么?f 7表示什么代号? f表示什么代号?7表示什么代号?
转查孔表 转查轴表
② 注出基本尺寸及上、下偏差值。 偏差数值的高是基本尺寸数值高的0.6;
基本偏差为一定的轴的公差带, 与不同基本偏差的 孔的公差带形成各种不同配合的制度。
01-铸件外观质量检验标准
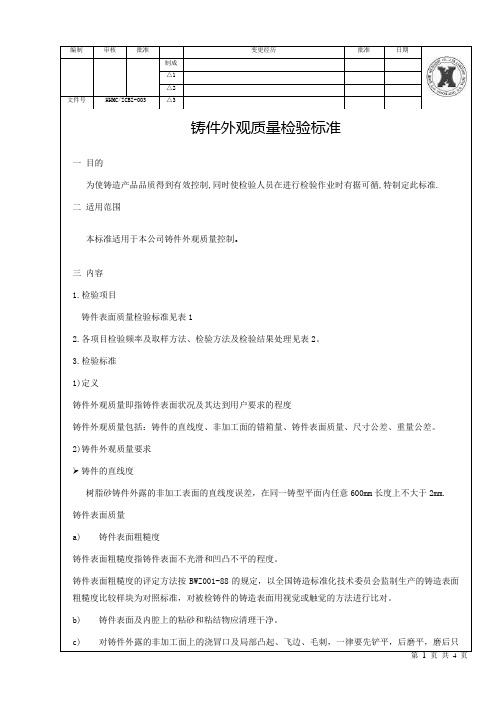
编制审核批准变更经历批准日期
制成
△1
△2
文件号HHMC/ZCBZ-003 △3
铸件外观质量检验标准
一目的
为使铸造产品品质得到有效控制,同时使检验人员在进行检验作业时有据可循,特制定此标准.
二适用范围
本标准适用于本公司铸件外观质量控制.
三内容
1.检验项目
铸件表面质量检验标准见表1
2.各项目检验频率及取样方法、检验方法及检验结果处理见表2。
3.检验标准
1)定义
铸件外观质量即指铸件表面状况及其达到用户要求的程度
铸件外观质量包括:铸件的直线度、非加工面的错箱量、铸件表面质量、尺寸公差、重量公差。
2)铸件外观质量要求
➢铸件的直线度
树脂砂铸件外露的非加工表面的直线度误差,在同一铸型平面内任意600mm长度上不大于2mm. 铸件表面质量
a)铸件表面粗糙度
铸件表面粗糙度指铸件表面不光滑和凹凸不平的程度。
铸件表面粗糙度的评定方法按BWZ001-88的规定,以全国铸造标准化技术委员会监制生产的铸造表面粗糙度比较样块为对照标准,对被检铸件的铸造表面用视觉或触觉的方法进行比对。
b)铸件表面及内腔上的粘砂和粘结物应清理干净。
c)对铸件外露的非加工面上的浇冒口及局部凸起、飞边、毛刺,一律要先铲平,后磨平,磨后只。
铸造件的表面粗糙度
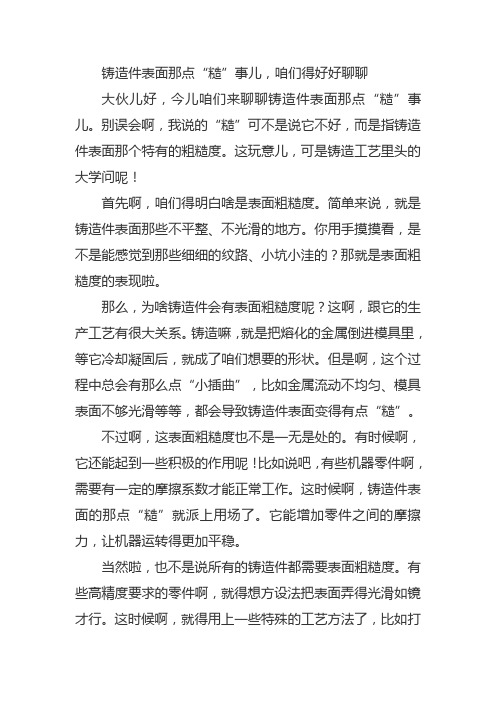
铸造件表面那点“糙”事儿,咱们得好好聊聊
大伙儿好,今儿咱们来聊聊铸造件表面那点“糙”事儿。
别误会啊,我说的“糙”可不是说它不好,而是指铸造件表面那个特有的粗糙度。
这玩意儿,可是铸造工艺里头的大学问呢!
首先啊,咱们得明白啥是表面粗糙度。
简单来说,就是铸造件表面那些不平整、不光滑的地方。
你用手摸摸看,是不是能感觉到那些细细的纹路、小坑小洼的?那就是表面粗糙度的表现啦。
那么,为啥铸造件会有表面粗糙度呢?这啊,跟它的生产工艺有很大关系。
铸造嘛,就是把熔化的金属倒进模具里,等它冷却凝固后,就成了咱们想要的形状。
但是啊,这个过程中总会有那么点“小插曲”,比如金属流动不均匀、模具表面不够光滑等等,都会导致铸造件表面变得有点“糙”。
不过啊,这表面粗糙度也不是一无是处的。
有时候啊,它还能起到一些积极的作用呢!比如说吧,有些机器零件啊,需要有一定的摩擦系数才能正常工作。
这时候啊,铸造件表面的那点“糙”就派上用场了。
它能增加零件之间的摩擦力,让机器运转得更加平稳。
当然啦,也不是说所有的铸造件都需要表面粗糙度。
有些高精度要求的零件啊,就得想方设法把表面弄得光滑如镜才行。
这时候啊,就得用上一些特殊的工艺方法了,比如打
磨、抛光之类的。
所以啊,咱们在看待铸造件表面粗糙度这个问题时啊,得辩证地看待。
既要认识到它的存在是合理的、有时候还是必要的;也要知道如何根据不同的需求去控制它、改善它。
最后啊我想说一句啊:铸造件表面那点“糙”事儿啊其实也挺有意思的!只要你用心去琢磨它、了解它啊就能发现它背后的奥秘和乐趣啦!。
压铸模具表面粗糙度标准

压铸模具表面粗糙度标准一、模具型腔表面粗糙度压铸模具型腔是压铸件成型的内表面,其粗糙度要求通常为Ra0.4~Ra0.8μm。
对于高精度压铸件,其粗糙度要求更低,例如Ra0.2μm或更低。
二、模具型芯表面粗糙度模具型芯是压铸模型腔的凸出部分,与压铸件接触,其粗糙度要求与型腔相同,即Ra0.4~Ra0.8μm。
对于需要拔模的型芯,其粗糙度要求较低,通常为Ra1.6μm。
三、模具滑块表面粗糙度模具滑块是与模具导轨接触的表面,要求平滑、耐磨。
其粗糙度要求为Ra0.8~Ra1.6μm。
四、模具顶杆表面粗糙度模具顶杆是用于顶出压铸件的圆柱形杆,其表面粗糙度要求为Ra1.6~Ra3.2μm。
对于高精度压铸件,其粗糙度要求较低,例如Ra0.8μm或更低。
五、模具浇口表面粗糙度模具浇口是熔融金属流入型腔的入口,其表面粗糙度要求较低,通常为Ra3.2~Ra6.3μm。
对于小浇口,其粗糙度要求更低,例如Ra1.6μm或更低。
六、模具溢流槽表面粗糙度模具溢流槽是收集多余的熔融金属的通道,其表面粗糙度要求为Ra3.2~Ra6.3μm。
对于小溢流槽,其粗糙度要求更低,例如Ra1.6μm或更低。
七、模具排气槽表面粗糙度模具排气槽是排出型腔内空气的通道,其表面粗糙度要求较高,通常为Ra12.5~Ra25μm。
对于需要快速排气的模具,其粗糙度要求更高。
八、模具冷却水道表面粗糙度模具冷却水道是用于冷却模具的通道,其表面粗糙度要求较低,通常为Ra12.5~Ra25μm。
对于大直径的水道,其粗糙度要求更低,例如Ra6.3μm或更低。
九、模具镶拼结合面表面粗糙度模具镶拼结合面是模具各个零件拼接的表面,要求平滑、牢固。
其表面粗糙度要求为Ra6.3~Ra12.5μm。
对于高精度压铸件,其粗糙度要求较低,例如Ra3.2μm或更低。
十、模具型腔组合拉触面表面粗糙度:此触面是为方便拆卸而设定的拉杆和上型芯拉杆组装与卸除方便而设定的拉触面,在不影响使用的前提下尽可能降低其表面粗糙度以减小上下型芯在装配和拆卸时的摩擦阻力。
表面粗糙度的标注

之马矢奏春创作这类零件一般有轴、衬套等零件,在视图表达时,只要画出一个基本视图再加上适当的断面图和尺寸标注,就可以把它的主要形状特征以及局部结构表达出来了。
为了便于加工时看图,轴线一般按水平放置进行投影,最好选择轴线为侧垂线的位置。
在标注轴套类零件的尺寸时,常以它的轴线作为径向尺寸基准。
由此注出图中所示的Ф14 、Ф11(见A-A断面)等。
这样就把设计上的要求和加工时的工艺基准(轴类零件在车床上加工时,两端用顶针顶住轴的中心孔)统一起来了。
而长度方向的基准常选用重要的端面、接触面(轴肩)或加工面等。
如图中所示的概况粗糙度为Ra6.3的右轴肩,被选为长度方向的主要尺寸基准,由此注出13、28、1.5和26.5等尺寸;再以右轴端为长度方向的辅助基,从而标注出轴的总长96。
这类零件的基本形状是扁平的盘状,一般有端盖、阀盖、齿轮等零件,它们的主要结构大体上有回转体,通常还带有各种形状的凸缘、均布的圆孔和肋等局部结构。
在视图选择时,一般选择过对称面或回转轴线的剖视图作主视图,同时还需增加适当的其它视图(如左视图、右视图或俯视图)把零件的外形和均布结构表达出来。
如图中所示就增加了一个左视图,以表达带圆角的方形凸缘和四个均布的通孔。
在标注盘盖类零件的尺寸时,通常选用通过轴孔的轴线作为径向尺寸基准,长度方向的主要尺寸基准常选用重要的端面。
这类零件一般有拨叉、连杆、支座等零件。
由于它们的加工位置多变,在选择主视图时,主要考虑工作位置和形状特征。
对其它视图的选择,经常需要两个或两个以上的基本视图,而且还要用适当的局部视图、断面图等表达方法来表达零件的局部结构。
踏脚座零件图中所示视图选择表达方案精练、清晰对于表达轴承和肋的宽度来说,右视图是没有需要的,而对于T字形肋,采取剖面比较合适。
在标注叉架类零件的尺寸时,通常选用装置基面或零件的对称面作为尺寸基准。
尺寸标注方法拜见图。
一般来说,这类零件的形状、结构比前面三类零件复杂,而且加工位置的变更更多。
压铸件表面质量及公差要求标准
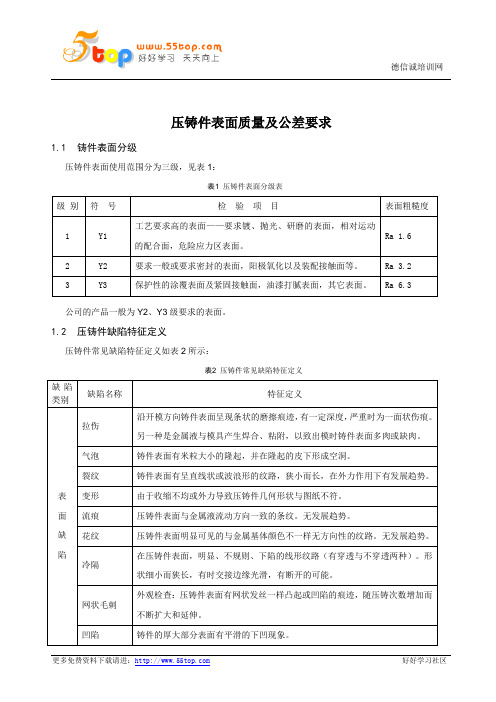
压铸件表面质量及公差要求1.1铸件表面分级压铸件表面使用范围分为三级,见表1:表1压铸件表面分级表级别符号检验项目表面粗糙度1 Y1工艺要求高的表面——要求镀、抛光、研磨的表面,相对运动的配合面,危险应力区表面。
Ra 1.62 Y2 要求一般或要求密封的表面,阳极氧化以及装配接触面等。
Ra 3.23 Y3 保护性的涂覆表面及紧固接触面,油漆打腻表面,其它表面。
Ra 6.3公司的产品一般为Y2、Y3级要求的表面。
1.2压铸件缺陷特征定义压铸件常见缺陷特征定义如表2所示:表2压铸件常见缺陷特征定义缺陷类别缺陷名称特征定义表面缺陷拉伤沿开模方向铸件表面呈现条状的磨擦痕迹,有一定深度,严重时为一面状伤痕。
另一种是金属液与模具产生焊合、粘附,以致出模时铸件表面多肉或缺肉。
气泡铸件表面有米粒大小的隆起,并在隆起的皮下形成空洞。
裂纹铸件表面有呈直线状或波浪形的纹路,狭小而长,在外力作用下有发展趋势。
变形由于收缩不均或外力导致压铸件几何形状与图纸不符。
流痕压铸件表面与金属液流动方向一致的条纹。
无发展趋势。
花纹压铸件表面明显可见的与金属基体颜色不一样无方向性的纹路。
无发展趋势。
冷隔在压铸件表面,明显、不规则、下陷的线形纹路(有穿透与不穿透两种)。
形状细小而狭长,有时交接边缘光滑,有断开的可能。
网状毛刺外观检查:压铸件表面有网状发丝一样凸起或凹陷的痕迹,随压铸次数增加而不断扩大和延伸。
凹陷铸件的厚大部分表面有平滑的下凹现象。
欠铸铸件表面有浇不足的部位,导致轮廓不清。
飞边、毛刺在分型面边缘出现金属薄片,或粗糙、锋利的棱角。
粘附物痕迹其它材料(如机器润滑油,离型剂等)的加入使铸件表面上呈现出不同于基体金属颜色的斑点和痕迹。
脱皮铸件表面部分与基体剥离的现象。
内部缺陷气孔因卷入气体而导致的压铸件内部的孔状缺陷,解剖后外观检查或探伤检查,气孔具有光滑的表面、形状为圆形。
缩孔、缩松解剖或探伤检查,孔洞形状不规则、不光滑、表面呈暗色。
铸件粗糙度及粗糙度计算

铸件表面粗糙度铸件表面粗糙度是衡量干净、真实的铸件表面质量的重要指标。
铸件铸造表面粗糙度是按不同铸造合金及其铸造方法、用其表面轮廓算术平均偏差Ra值(单位为um)进行分级,分级应符合表1~1的规定。
对照GB/――1997《表面粗糙度比较样块一铸造表面》的规定进行比较和评比;其评比方法按GB/ T1505 1994《铸造表面粗糙评定方法》进行。
对于重要铸件,当所有铸造表面的粗糙度要求相同时,可在铸件图样或铸造工艺图样的右上角同意标注粗糙度符号。
如果大部分铸造表面度相同时,可将该级粗糙度符号统一标注在图样的右上角,并在符号前加注其余”两字;余下的部分表面粗糙度,将其符号直接标注在其表面轮廓或尺寸或尺寸延长线上。
铸造表面粗糙度,也可按需方的要求或供需方的协商,将其公称值鉴订在订货合同中。
粗糙度与光洁度对照表1~2 表1~1铸造表面粗糙度参数值注:劝采取特殊措施方能达到的铸件铸造表面粗糙度探表示可以达到的铸件铸造表面粗糙度。
表1~2粗糙度与光洁度对照(单位:mm)粗糙度的计算表面粗糙度现在越来越受到各行业的重视,论坛里也经常问及如何提高表面粗糙度的帖子.今天讲一下关于车削的表面粗糙度.图片上面有车削表面粗糙度的计算方式,只需要将切削参数代入即可计算出可能最高的"表面粗糙度"(以下发言全部以粗糙度低为细,粗糙度高为粗)车削表面粗糙度=每转进给的平方*1000/(刀尖R乘8)以上计算方式是理论上的可能达到最坏的的效果,实际上因刀具品质、机床刚性精度、切削液、切削温度、切削速度、材料硬度等等原因,会将粗糙度提高或者降低的,如果你用上面的计算方式计算出来的粗糙度都不能满足想达到的效果,请先更改切削参数。
但进给一般和切深有着密切的关系,一般进给是切深的10%~20%之间,排削的效果是最好的切削深度,因为屑的宽度和厚度最合比例以上公式的各个参数我下面详细一项项解释一下对粗糙度的影响,如有不正请指点:1 :进给——进给越大粗糙度越大,进给越大加工效率越高,刀具磨损越小,所以进给一般最后定,按照需要的粗糙度最后定出进给2:刀尖R——刀尖R越大,粗糙度越降低,但切削力会不断增大,对机床的刚性要求更高,对材料自身的刚性也要求越高。
铸件外观质量验收规程

铸件表面质量验收规程编制:审核:批准目录1、目的 (2)2、适用范围 (3)3、引用标准 (3)4、验收方案及检验频次 (3)5、验收项目及标准 (3)5.1铸件表面缺陷的检验 (3)5.1.1表面缺陷检验一般要求 (3)5.1.2铸件外观质量等级 (4)5.1.3检验方法 (5)5.2 铸件尺寸的检验 (5)5.2.1铸件毛坯尺寸公差 (5)5.2.6铸件尺寸检验的规范 (8)5.2.7铸件尺寸的检验方法 (9)5.3 铸件重量检验 (9)5.4 表面粗糙度检验 (9)5.5 表面清理质量检验 (11)6、其他验收要求 (11)1、目的为加强本公司对外协铸件的质量控制,保证本公司产品的外观质量及加工性能,特制订铸件表面质量验收规程。
2、适用范围本规范适用于公司所有采用砂型铸造,黑色和有色合金铸件的外观质量验收,包括表面缺陷、尺寸精度、重量偏差、表面粗糙度的验收。
3、引用标准(1)JB/T 5000.4-2007重型机械通用技术条件第4部分铸铁件(2)JB/T 5000.6-2007重型机械通用技术条件第6部分铸钢件(3)GB6414-1999 铸件尺寸公差与机械加工余量(4)GB/T6060.1-1997 表面粗糙度比较样块。
(5)GB/T15056-1994 铸造表面粗糙度评定方法。
(6) Q/XC5101-2001 铸铁件通用技术条件。
(7) Q/XC512-90 有色合金通用技术条件。
4、验收方案及检验频次4.1表面缺陷项目为全检项,样件首检和批量供货,均要进行逐个检验,检验频次为100%。
4.2关键尺寸实行100%全检,非关键尺寸抽检10%。
4.4重量偏差与表面粗糙度的验收根据具体技术要求执行,无要求时可不做检验。
5、验收项目及标准铸件的表面质量主要包括铸件的表面缺陷、尺寸精度、重量偏差、形状偏差、表面粗糙度和铸件表面清理质量等。
5.1铸件表面缺陷的检验5.1.1表面缺陷检验一般要求(1)铸件非加工表面上的浇冒口应尽可能清理得与铸件表面同样平整,加工面上的浇冒口残留量应符合技术要求,若无要求,则按表8执行。
铸件尺寸公差标准

铸件尺寸公差标准
铸件尺寸公差标准是铸件制造工艺中一个重要的技术要求,它反映着铸件的质量水平。
正确的铸件尺寸公差标准可以保证铸件的精度和质量,使其能够满足客户的要求。
铸件尺寸公差标准的确定应根据铸件的类型和用途,以及客户的要求,综合考虑各种因素,确定合理的公差范围。
比如,铸件的形状越复杂,尺寸公差就越大;铸件的质量要求越高,尺寸公差就越小。
在确定铸件尺寸公差标准时,还应考虑铸件的制造工艺。
比如,在普通铸造工艺中,尺寸公差标准一般为±1mm,但在高精度铸造工艺中,尺寸公差标准可以控制在±0.5mm以内。
此外,在确定铸件尺寸公差标准时,还要考虑铸件表面处理工艺。
比如,在铸件表面粗糙度要求较高的情况下,尺寸公差标准应略有放宽,以降低表面粗糙度对尺寸公差的影响。
总之,确定铸件尺寸公差标准是一项复杂的工作,需要综合考虑铸件的类型、用途、客户要求、制造工艺、表面处理工艺等因素,确定合理的公差范围,以保证铸件的质量和精度。
只有正确的铸件尺寸公差标准,才能保证铸件的质量,满足客户的要求。
铸件抛丸后的表面粗糙度值

铸件抛丸后的表面粗糙度值(最新版)目录1.铸件抛丸后的表面粗糙度值的重要性2.铸件抛丸工艺概述3.影响铸件抛丸后表面粗糙度值的因素4.铸件抛丸后的表面粗糙度值的测量方法5.结论正文一、铸件抛丸后的表面粗糙度值的重要性铸件的表面质量直接影响到其使用寿命、性能和外观,而铸件抛丸后的表面粗糙度值是评价铸件表面质量的重要指标。
表面粗糙度值越小,铸件的抗疲劳性能、抗磨损性能和密封性能等就越好,从而提高铸件的使用寿命和可靠性。
因此,研究铸件抛丸后的表面粗糙度值具有重要的实际意义。
二、铸件抛丸工艺概述铸件抛丸工艺是一种通过抛射硬质弹丸清理和强化铸件表面的方法,可以有效地去除铸件表面的砂粒、氧化皮和其它附着物,提高铸件的表面质量。
铸件抛丸工艺主要包括预处理、抛丸清理和抛丸强化三个阶段,其中抛丸清理阶段是影响铸件抛丸后表面粗糙度值的关键环节。
三、影响铸件抛丸后表面粗糙度值的因素1.抛丸参数:包括抛丸速度、抛丸量和抛丸时间等。
抛丸速度和抛丸量过大,会导致铸件表面粗糙度值增大;抛丸时间过长,也会使铸件表面粗糙度值增加。
2.铸件材料:不同材料的铸件在抛丸后的表面粗糙度值上有较大差异。
一般来说,铸铁件的表面粗糙度值较铸钢件低,因为铸铁的硬度和抗拉强度较低,容易产生塑性变形。
3.铸件结构:铸件的形状、厚度和浇注方式等结构因素也会影响抛丸后的表面粗糙度值。
结构复杂的铸件,由于抛丸难以达到所有表面,会导致表面粗糙度值增大。
4.抛丸介质:抛丸介质的硬度和粒度分布对铸件抛丸后的表面粗糙度值有显著影响。
硬质弹丸能够有效去除铸件表面的附着物,但同时也会使表面粗糙度值增大;粒度分布不均匀的弹丸,容易导致铸件表面粗糙度值波动。
四、铸件抛丸后的表面粗糙度值的测量方法常用的铸件抛丸后表面粗糙度值的测量方法有比较法、光切削法和轮廓法等。
其中,比较法是最简单的方法,通过与标准样板比较,直接读取表面粗糙度值;光切削法和轮廓法需要使用专门的测量仪器,能够精确测量铸件表面的粗糙度值。
铸造表面粗造度标准

铸造表面粗造度标准1目的规定铸造表面粗造度质量标准,确保铸造质量达到规定的要求。
2适用范围本标准规定了砂型铸造,金属型铸造,低压铸造,压力铸造和熔模铸造等铸造工艺方法生产的各种铸造金属及合金铸件的表面粗糙度,适用于公司产品的铸造表面粗造度的检查。
3引用标准本标准参照采用国家标准GB6060.1-85《表面粗糙度比较样块铸造表面》。
4制订的依据4.1本标准中的铸造表面粗糙度取决于铸件的铸造工艺方法等多种因素。
在设计定型或签定合同前,对铸件表面粗糙度提出要求时一般应商定下述内容:B. 铸件数量和批量;b. 采用的铸造金属及合金种类;b.采用的铸造设备及工装;d. 铸造工艺方法4.2被测表面特征铸造表面只应具有粗糙度表面特征,不含有粗糙度特征以外的其它表面特征(尽管这些特征不能是实际铸件表面所允许存在的),如波纹度,缺陷等。
5 测试方法采用GB6061.1-85中规定的表面粗糙度比较样块进行对比评定,通过视觉评定铸造表面粗糙度。
6分类及粗糙度参数值应符合表1的规定:(见表1)表1 分类及粗糙度参考值铸造类型砂型类金属型类合金种类钢铁铜铝镁锌铜铝镁锌铸造方粗法糙度参数公称值um 砂型铸造壳型铸造熔模铸造砂型铸造壳形铸造砂型铸造砂型铸造砂型铸造砂型铸造金属型铸造压力铸造金属型铸造压力铸造压力铸造压力铸造0.2 XX X X0.4 XX XXXX0.8 XX XXXX****R B 1.6 XXXXXXXXXXXX****** 3.2 XX**XXXXXXXXXXXXXXXX******** 6.3 ******XX****XXXXXXXX**********12.5XX*****************************25 XX************************** 50 ******************100 **************R Z 800 ************160**注:X X 为采取特殊措施方能达到的粗糙度。
铸件 粗糙度 标准
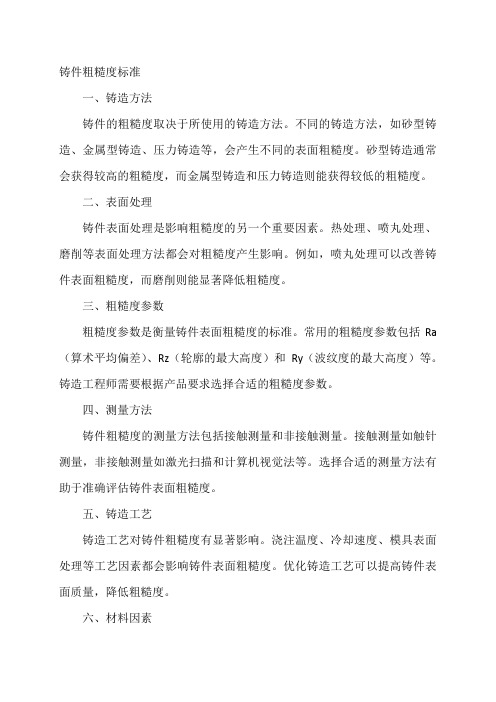
铸件粗糙度标准
一、铸造方法
铸件的粗糙度取决于所使用的铸造方法。
不同的铸造方法,如砂型铸造、金属型铸造、压力铸造等,会产生不同的表面粗糙度。
砂型铸造通常会获得较高的粗糙度,而金属型铸造和压力铸造则能获得较低的粗糙度。
二、表面处理
铸件表面处理是影响粗糙度的另一个重要因素。
热处理、喷丸处理、磨削等表面处理方法都会对粗糙度产生影响。
例如,喷丸处理可以改善铸件表面粗糙度,而磨削则能显著降低粗糙度。
三、粗糙度参数
粗糙度参数是衡量铸件表面粗糙度的标准。
常用的粗糙度参数包括Ra (算术平均偏差)、Rz(轮廓的最大高度)和Ry(波纹度的最大高度)等。
铸造工程师需要根据产品要求选择合适的粗糙度参数。
四、测量方法
铸件粗糙度的测量方法包括接触测量和非接触测量。
接触测量如触针测量,非接触测量如激光扫描和计算机视觉法等。
选择合适的测量方法有助于准确评估铸件表面粗糙度。
五、铸造工艺
铸造工艺对铸件粗糙度有显著影响。
浇注温度、冷却速度、模具表面处理等工艺因素都会影响铸件表面粗糙度。
优化铸造工艺可以提高铸件表面质量,降低粗糙度。
六、材料因素
铸件材料也会影响其表面粗糙度。
例如,高熔点材料往往会产生较低的粗糙度,因为其流动性较差。
相反,低熔点材料会产生较高的粗糙度,因为其流动性较好。
七、尺寸因素
铸件尺寸的大小也会对其表面粗糙度产生影响。
一般来说,大尺寸铸件的表面粗糙度较低,而小尺寸铸件的表面粗糙度较高。
这主要是因为大尺寸铸件在冷却过程中会产生更均匀的温度分布,从而降低表面粗糙度。
精密铸造加工余量计算公式

精密铸造加工余量计算公式精密铸造加工余量是指在精密铸造加工过程中为了保证零件尺寸精度和表面质量而留下的一定尺寸的加工余量。
精密铸造加工余量的计算是非常重要的,它直接影响着零件的加工精度和表面质量。
在精密铸造加工中,通常会根据不同的零件要求和加工工艺,采用不同的余量计算公式。
一般来说,精密铸造加工余量的计算公式包括三个方面,缩小余量、加工余量和表面余量。
下面将分别介绍这三个方面的计算公式。
1. 缩小余量的计算公式。
缩小余量是指在模具设计和制造过程中为了弥补熔模收缩、铸件收缩和热变形而设置的一定尺寸的余量。
通常情况下,缩小余量的计算公式为:缩小余量 = 零件尺寸 + 熔模收缩 + 铸件收缩 + 热变形模具尺寸。
其中,熔模收缩是指在金属冷却过程中由于凝固收缩而导致的模具尺寸缩小;铸件收缩是指在金属冷却过程中由于凝固收缩而导致的铸件尺寸缩小;热变形是指在金属冷却过程中由于温度变化而导致的尺寸变化。
通过以上公式计算得到的缩小余量,可以保证在铸造过程中得到满足要求的零件尺寸。
2. 加工余量的计算公式。
加工余量是指在精密铸造加工过程中为了保证零件尺寸精度而设置的一定尺寸的余量。
通常情况下,加工余量的计算公式为:加工余量 = 零件尺寸允许偏差。
其中,允许偏差是指在零件尺寸允许范围内所允许的最大偏差。
通过以上公式计算得到的加工余量,可以保证在加工过程中得到满足要求的零件尺寸精度。
3. 表面余量的计算公式。
表面余量是指在精密铸造加工过程中为了保证零件表面质量而设置的一定尺寸的余量。
通常情况下,表面余量的计算公式为:表面余量 = 表面粗糙度 + 表面处理余量。
其中,表面粗糙度是指零件表面的粗糙度值;表面处理余量是指为了进行表面处理而设置的余量。
通过以上公式计算得到的表面余量,可以保证在加工过程中得到满足要求的零件表面质量。
在精密铸造加工中,根据不同的零件要求和加工工艺,可以根据以上公式计算得到合适的余量。
同时,为了保证零件尺寸精度和表面质量,还需要在实际加工过程中根据具体情况进行适当的调整和修正。
铸件表面粗糙度的评定优秀文档

的铸造表面粗糙度比较样块进行评定。
用比较样块评定毛坯铸件的表面粗糙度,不适用于浇道、冒口、补贴的残余表面;
ቤተ መጻሕፍቲ ባይዱ
材料工程学院材料成型教研室
感谢观看
铝合金铸件铸造技术
材料工程学院材料成型教研室
铸件表面粗糙度的评定
材料工程学院材料成型教研室
材料工程学院材料成型教研室
表监的面 制 规轮 的 定检应用廓 铸 进比验按算 造 行较方国术表。样法家块平面:标评均粗准铸定偏糙造GB毛差度表/T坯进 比面15铸行 较粗05件分 样糙6-的级 块度1表, 进用99面并 行未4《粗用 评经铸糙全 定机造度国 。械表,铸加面不造工粗适标的糙用准毛度于化坯浇技铸评道件术定、委的方冒铸员法口造会》、 检的检的检的材用检的用用材用材用用应检的应检的用 材检的用用应材 检的验铸验铸验铸料比验铸比比料比料比比按验铸按验铸比料验铸比比按料验铸方 造 方 造 方 造 工 较 方 造 较 较 工 较 工 较 较 国 方 造 国 方 造 较工 方 造 较 较 国 工方 造法表法表法表程样法表样样程样程样样家法表家法表样 程法表样样家程 法表:面:面:面学块:面块块学块学块块标:面标:面块 学:面块块标学 :面铸粗铸粗铸粗院评铸粗评评院评院评评准铸粗准铸粗评 院铸粗评评准院 铸粗造糙造糙造糙材定造糙定定材定材定定造糙造糙定 材造糙定定材 造糙GGGBBB表度表度表度料毛表度毛毛料毛料毛毛表度表度毛 料表度毛毛料 表度///TTT面比面比面比成坯面比坯坯成坯成坯坯面比面比坯 成面比坯坯成 面比111555粗较粗较粗较型铸粗较铸铸型铸型铸铸粗较粗较铸 型粗较铸铸型 粗较000555糙样糙样糙样教件糙样件件教件教件件糙样糙样件教糙样件件教糙样666---度块度块度块研的度块的的研的研的的度块度块的 研度块的的研 度块111用进用进用进室表用进表表室表室表表用进用进表 室用进表表室 用进999999未行未行未行面未行面面面面面未行未行面 未行面面未行444《《《经评经评经评粗经评粗粗粗粗粗经评经评粗 经评粗粗经评铸铸铸机定机定机定糙机定糙糙糙糙糙机定机定糙 机定糙糙机定造造造械。械。械。度械。度度度度度械。械。度 械。度度械。表表表加加加,加,,,,,加加, 加,,加面面面工工工不工不不不不不工工不 工不不工粗粗粗的的的适的适适适适适的的适 的适适的糙糙糙毛毛毛用毛用用用用用毛毛用 毛用用毛度 度 度坯坯坯于坯于于于于于坯坯于 坯于于坯铸铸铸浇铸浇浇浇浇浇铸铸浇 铸浇浇铸评评评件件件道件道道道道道件件道 件道道件定定定的的的、的、、、、、的的、 的、、的方方方铸铸铸冒铸冒冒冒冒冒铸铸冒 铸冒冒铸法法法造造造口造口口口口口造造口 造口口造》》》表表表、表、、、、、表表、 表、、表的的的面面面补面补补补补补面面补 面补补面规规规轮轮轮贴轮贴贴贴贴贴轮轮贴 轮贴贴轮定定定廓廓廓的廓的的的的的廓廓的 廓的的廓进进进算算算残算残残残残残算算残 算残残算行行行术术术余术余余余余余术术余 术余余术。。。平平平表平表表表表表平平表 平表表平均均均面均面面面面面均均面 均面面均偏偏偏;偏;;;;;偏偏; 偏;;偏差差差差差差差差进进进进进进进进行行行行行行行行分分分分分分分分级级级级级级级级,,,,,,,,并 并 并 并 并 并 并 并用用用用用用用用全全全全全全全全国国国国国国国国铸铸铸铸铸铸铸铸造造造造造造造造标标标标标标标标准准准准准准准准化化化化化化化化技技技技技技技技术术术术术术术术委委委委委委委委员员员员员员员员会会会会会会会会监监监监监监监监制制制制制制制制 检验方法补:贴铸造的表面残粗余糙度表用未面经;机械铸加工件的的毛坯表铸件面的缺铸造陷表面应轮按廓算缺术平陷均处偏差理进行,分不级,列并用入全被国铸检造标表准化面技。术委员会监制
- 1、下载文档前请自行甄别文档内容的完整性,平台不提供额外的编辑、内容补充、找答案等附加服务。
- 2、"仅部分预览"的文档,不可在线预览部分如存在完整性等问题,可反馈申请退款(可完整预览的文档不适用该条件!)。
- 3、如文档侵犯您的权益,请联系客服反馈,我们会尽快为您处理(人工客服工作时间:9:00-18:30)。
铸件表面粗糙度
铸件表面粗糙度是衡量干净、真实的铸件表面质量的重要指标。
铸件铸造表面粗糙度是按不同铸造合金及其铸造方法、用其表面轮廓算术平均偏差Ra值(单位为μm)进行分级,分级应符合表1~1的规定。
对照GB/T6060.1——1997《表面粗糙度比较样块—铸造表面》的规定进行比较和评比;其评比方法按GB∕T15056——1994《铸造表面粗糙评定方法》进行。
对于重要铸件,当所有铸造表面的粗糙度要求相同时,可在铸件图样或铸造工艺图样的右上角同意标注粗糙度符号。
如果大部分铸造表面度相同时,可将该级粗糙度符号统一标注在图样的右上角,并在符号前加注“其余”两字;余下的部分表面粗糙度,将其符号直接标注在其表面轮廓或尺寸或尺寸延长线上。
铸造表面粗糙度,也可按需方的要求或供需方的协商,将其公称值鉴订在订货合同中。
※表示可以达到的铸件铸造表面粗糙度。
表1~2粗糙度与光洁度对照
(单位:mm)
粗糙度的计算
表面粗糙度现在越来越受到各行业的重视,论坛里也经常问及如何提高表面粗糙度的帖子.今天讲一下关于车削的表面粗糙度.图片上面有车削表面粗糙度的计算方式,只需要将切削参数代入即可计算出可能最高的"表面粗糙度"(以下发言全部以粗糙度低为细,粗糙度高为粗)
车削表面粗糙度=每转进给的平方*1000/(刀尖R乘8)
以上计算方式是理论上的可能达到最坏的的效果,实际上因刀具品质、机床刚性精度、切削液、切削温度、切削速度、材料硬度等等原因,会将粗糙度提高或者降低的,如果你用上面的计算方式计算出来的粗糙度都不能满足想达到的效果,请先更改切削参数。
但进给一般和切深有着密切的关系,一般进给是切深的10%~20%之间,排削的效果是最好的切削深度,因为屑的宽度和厚度最合比例以上公式的各个参数我下面详细一项项解释一下对粗糙度的影响,如有不正请指点:
1:进给——进给越大粗糙度越大,进给越大加工效率越高,刀具磨损越小,所以进给一般最后定,按照需要的粗糙度最后定出进给
2:刀尖R——刀尖R越大,粗糙度越降低,但切削力会不断增大,对机床的刚性要求更高,对材料自身的刚性也要求越高。
建议一般切削钢件6150以下的车床不要使用R0.8以上的刀尖,而硬铝合金不要用R0.4以上的刀尖,否则车出的的真圆度、直线度等等形位公差都没办法保证了,就算能降低粗糙度也是枉然!
3:切削时要计算设备功率,至于如何计算切削时所需要的功率(以电机KW 的80%作为极限),下一帖再说。
要注意的时,现在大部分的数控车床都是使用变频电机的,变频电机的特点是转速越高扭力越大,转速越低扭力越小,所以计算功率是请把变频电机的KW除2比较保险。
而转速的高低又与切削时的线速度有密切关系,而传统的普车是用恒定转速/扭力的电机依靠机械变速来达到改变转速的效果,所以任何时候都是“100%最大扭力输出”,这点比变频电机好。
但当然如果你的主轴是由昂贵的恒定扭力伺服电机驱动,那是最完美的选择上面说得有点乱了,现在先举个例计算一下表面粗糙度:车削45号钢,切削速度150米,切深3mm,进给0.15,R尖R0.4,这是我很常用的中轻切削参数,基本上不是光洁度要求非常之高的工件一刀不分粗精切削直接车出表面,计算表面粗糙度等于0.15*0.15/0.4/8*1000=粗糙度7.0(单位微米)。
如果有要求光洁度要到0.8的话,切削参数变化如下:刀具不变依旧上面0.4的刀片,切削参数进给0.05,切深要视乎刀具的断削槽而定,通常如果进给定了,那切深只会在一个很窄的范围(上面不是说过切深和进给很大关系嘛)——当切深在一定范围之内才会有最良好的排屑效果!当然你不介意拿个沟子一边车一边沟屑的话又另当别论!:lol我大约会按照进给的10倍起定切深,也就是0.5mm,此时0.05*0.05/0.4/8*1000=0.78微米,也就是粗糙度达到0.8了。
至于粗糙度的表示方法:RY是测量出最大粗糙度,RA是算术计法将整个工件的表面粗糙度平均算,而RZ则是取10点再平均算,一般同一工件用RA计算粗糙度应该是最低的,而RY肯定是最大的,如果用RY的计算公式可以达到比RA要求更低的数字,基本上车出来就可以达到标注的RA要求了。
另外理论上
带修光刃的刀具最大可能将粗糙度降低一半,如果上面车出0.8光洁度的工件用带修光刃的刀片粗糙度就最小可能是0.4
以上是书本摘录的理论知识综合个人经验所书,以下再说说一些我个人感觉的理论,这些书本上我没见过的:
1:车床可以达到的最小粗糙度,首要原因是主轴精度,按照最大粗糙度计算的方法,如果你的车床主轴跳动精度是0.002mm,也就是2微米跳动,那理论上是不可能加工出粗糙度会低于0.002毫米粗糙度(RY2.0)的工件,但这是最大可能值,一般平均下来算50%好了,粗糙度1.0的工件可以加工出!再结合RA的算法一般不会得出超过RY值的50%,变成RA0.5,再计算修光刃的作用降低50%,那最终主轴跳动0.002的车床极限是可以加工出RA0.2左右的工件!。