烧结矿冷却的目的和意义
烧结生产知识

烧结生产知识一、铁矿石烧结知识(原料条件)1、天然矿粉与烧结1)天然矿粉包括富矿粉和贫矿粉,其中天然矿粉含铁量在45%以上的通常称为富矿粉,含铁量低于45%的通常称为贫矿粉。
45%这个界限随着冶炼技术的发展是会变化的。
2)铁矿粉烧结是重要的造块技术之一。
由于开采时产生大量的铁矿粉,特别是贫铁矿富选促进了铁精矿粉的生产发展,使铁矿粉烧结成为规模最大的造块作业。
烧结矿比天然矿石有许多优点,如含铁量高、气孔率大、易还原、有害杂质少、含碱性熔剂等。
2、铁矿石分类:按照铁矿物不同的存在形态,分为磁铁矿、赤铁矿、褐铁矿、菱铁矿四大类。
1)磁铁矿:磁铁矿化学式为Fe3O4,也可以视为Fe2O3与FeO的固溶体。
比密度为4.9--5.2t/m3,硬度为5.5--6.5,难还原和破碎,有金属光泽,具有磁性。
其理论含铁量为72.4%。
磁铁矿晶体为八面体,组织结构较致密坚硬,一般成块状和粒状,表面颜色由钢灰色到黑色,条痕均是黑色,俗称青矿。
2)赤铁矿:赤铁矿俗称“红矿”,化学式为Fe2O3,其矿物成份是不含结晶水的三氧化二铁,密度为4.8—5.3,硬度不一,结晶完整的赤铁矿硬度为5.5—6.0,理论含铁量70%。
赤铁矿由非常致密的结晶组织到很分散的粒状,结晶的赤铁矿外表颜色为钢灰色和铁黑色,其它为暗红色,但条痕均为暗红色。
3)褐铁矿:褐铁矿石(mFe2O3. nH2O)是一种含结晶水的Fe2O3,按结晶水含量不同,褐铁矿分为五种,其中以2Fe2O3. 3H2O形式存在的较多。
4)菱铁矿:菱铁矿石的化学式为FeCO3,理论含铁量为48.2%。
自然界中常见的是坚硬致密的菱铁矿,外表颜色为灰色和黄褐色,风化后变为深褐色,条痕为灰色或带黄色,由玻璃光泽。
菱铁矿的比重为3.8吨/米3,无磁性。
3、铁矿粉分类:1)精矿粉:也称选粉。
是天然矿石经过破碎、磨碎、选矿等加工处理,除去一部分脉石和杂质,使含铁量提高后的极细的矿粉叫精矿粉。
烧结讲义

前言烧结矿是现代钢铁生产的重要工艺之一。
为了适应天丰钢铁有限公司150m2步进式冷却烧结机的需要,即要说明理论知识,也结合生产实际,介绍工艺设备和操作要点。
从而使我们150m2烧结机,在短时间内让新员工尽快掌握生产操作本领,加速这种类型烧结机为天丰服务,满足整个铁厂在冶金炉料方面需求,从而使烧结的产品——烧结矿,各项冶金性能满足和达到高炉的要求。
一、烧结目的和意义:高炉的冶炼过程中,为了保证料透气性的良好,要求炉料粒度均匀、粉未少、机械强度(冷强度和热强度)高。
为了降低高炉焦比,要求炉料含铁品位高,有害杂质少,且具有自熔性和良好的还原性能,采用现代烧结法,上述目的几乎全部能达到。
二、烧结技术的发展及现状烧结生产起源于英国和德国,大约1870年这些国家开始使用烧结锅。
用来处理矿山开采、冶金工厂、化工厂的废弃物。
1892年美国也出现了烧结锅。
世界第一台带式烧结机,1910年在美国投产,这台烧结机的面积为8.325m3(1.07m×7.78m)。
当时用于处理高炉炉尘,每天生产烧结矿140t,它的出现引起了烧结生产的重大变革,从此带式烧结机,得到了广泛的应用。
自中日甲午战争后,辽东割让于日本。
这里的一切主权全部丧失,日本人在辽东取得了采矿权、筑路权,向满州大量移民。
在慈禧太后去世的1908年,进入辽东半岛的日本资本家、科考队,在鞍山地区发现了大量的铁矿,而且储藏量相当丰富。
于是,在1926后在鞍山相继建成4台21.63m2(1.067m×20.269m)带式烧结机,日产1200t。
1935~1937年,又相继建成4台50m2的烧结机,年产19万吨烧结矿。
1952年,鞍钢从苏联引进75m2烧结设备和技术。
这套当时具有国际先进水平的设备,对新中国的烧结事业起到了示范作用。
这套设备于90年代拆除。
目前,国内已拥有:13m2、18m2、24m2、36m2、50m2、75m2、90m2、130m2、182m2、265m2、450m2等规格的烧结机。
烧结矿竖式冷却工艺的分析与研究
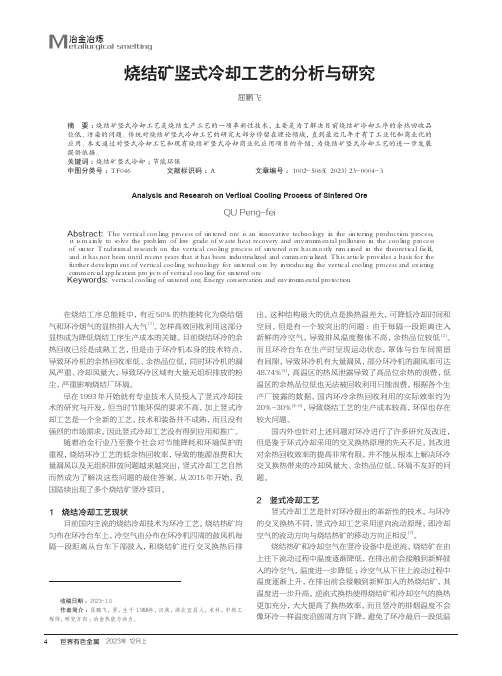
4冶金冶炼M etallurgical smelting烧结矿竖式冷却工艺的分析与研究屈鹏飞[普锐特冶金技术(中国)有限公司,上海 201103]摘 要:烧结矿竖式冷却工艺是烧结生产工艺的一项革新性技术,主要是为了解决目前烧结矿冷却工序的余热回收品位低、污染的问题。
传统对烧结矿竖式冷却工艺的研究大部分停留在理论领域,直到最近几年才有了工业化和商业化的应用。
本文通过对竖式冷却工艺和现有烧结矿竖式冷却商业化应用项目的介绍,为烧结矿竖式冷却工艺的进一步发展提供依据。
关键词:烧结矿竖式冷却;节能环保中图分类号:TF046 文献标识码:A 文章编号:1002-5065(2023)23-0004-3Analysis and Research on Vertical Cooling Process of Sintered OreQU Peng-fei[Primet Metallurgical Technology (China) Co., Ltd,Shanghai 201103,China]Abstract: The vertical cooling process of sintered ore is an innovative technology in the sintering production process, it is mainly to solve the problem of low grade of waste heat recovery and environmental pollution in the cooling process of sinter. Traditional research on the vertical cooling process of sintered ore has mostly remained in the theoretical field, and it has not been until recent years that it has been industrialized and commercialized. This article provides a basis for the further development of vertical cooling technology for sintered ore by introducing the vertical cooling process and existing commercial application projects of vertical cooling for sintered ore.Keywords: vertical cooling of sintered ore; Energy conservation and environmental protection收稿日期:2023-10作者简介:屈鹏飞,男,生于1988年,汉族,湖北宜昌人,本科,中级工程师,研究方向:冶金热能与动力。
烧结工艺理论知识(全面)

第一章烧结生产概述§1-1 烧结生产在冶金工业中的地位一、简述烧结工艺的产生和发展烧结方法在冶金生产中的应用,起初是为了处理矿山、冶金、化工厂的废气物(如富矿粉、高炉炉尘、扎钢皮、炉渣等)以便回收利用。
随着钢铁工业的快速发展,矿石的开采量和矿粉的生成量亦大大增加。
据统计,每生产1t生铁需1.7~1.9t铁矿石,若是贫矿,需要的铁矿石则更多。
另外,由于长期的开采和消耗,能直接用来冶炼的富矿愈来愈少,人们不得不大量开采贫矿(含铁25%~30%)。
但贫矿直接入炉冶炼是很不经济的,所以必须经过选矿处理。
选矿后的精矿粉,在含铁品位上是提高了,但其粒度不符合高炉冶炼要求。
因此,对开采出来的粉矿(0~8mm)和精矿粉都必须经过造块后方可用于冶炼。
我国铁矿资源丰富,但贫矿较多,约占80%以上,因此,冶炼前大都需经破碎、筛分、选矿和造块等处理过程。
烧结生产的历史已有一个多世纪。
它起源于资本主义发展较早的英国、瑞典和德国。
大约在1870年前后,这些国家就开始使用烧结锅。
我国在1949年以前,鞍山虽建有10台烧结机,总面积330m2,但工艺设备落后,生产能力很低,最高年产量仅几十万吨。
我国铁矿石烧结领域取得的成就,概括起来包括以下几个方面:(1)烧结工艺:自1978年马钢冷烧技术攻关成功后,一批重点企业和地方骨干企业基本完成了热烧改冷烧工艺。
部分企业建成原料混匀料场,并投入使用,绝大多数钢铁企业实现了自动化配料、混合机强化制粒、偏析布料、冷却筛分、整粒及铺底料技术。
(2)新工艺、新技术开发和应用:如高碱度烧结矿技术、小球烧结技术、低温烧结技术、低硅烧结技术等,在钢铁企业得到推广应用,并取得了显著的效益。
(3)设备大型化和自动化:20世纪50年代,我国最大烧结机75m2,60年代130 m2,80年代265m2,90年代宝钢二、三期和武钢等450m2烧结机相继投产,这些都是我国自行设计、自行制造,并实现自动化生产的。
烧结环冷工技能题库

烧结环冷工技能题库
烧结环冷工是钢铁企业中的一种重要岗位,主要负责烧结矿的冷却工作。
以下是烧结环冷工技能题库,以供参考:
一、选择题
1. 烧结矿为什么要进行冷却?
A. 提高烧结矿的强度
B. 便于运输和储存
C. 回收余热,节约能源
D. 提高烧结矿的还原性
2. 烧结环冷机的冷却效率与什么因素有关?
A. 冷却风量
B. 冷却水温
C. 冷却风压
D. 环冷机转速
3. 烧结环冷机的工作原理是什么?
A. 利用水来冷却烧结矿
B. 利用气体来冷却烧结矿
C. 利用油来冷却烧结矿
D. 利用太阳能来冷却烧结矿
4. 如何提高烧结环冷机的冷却效率?
A. 增加冷却风量
B. 降低冷却水温
C. 降低冷却风压
D. 提高环冷机转速
5. 烧结环冷工的主要职责是什么?
A. 负责烧结矿的配料和混合
B. 负责烧结矿的运输和储存
C. 负责烧结矿的破碎和筛分
D. 负责烧结矿的冷却和输送
二、简答题
1. 简述烧结环冷工的工作流程。
2. 简述烧结环冷机的主要组成部分。
3. 简述烧结环冷机的工作原理。
4. 如何维护和保养烧结环冷机?
5. 简述烧结环冷工的安全操作规程。
熟料为何需急冷,有何作用?

熟料为何需急冷,有何作用?1.熟料冷却过程及目的熟料烧结过程完成之后,C3S 的生成反应结束,熟料从烧成温度开始下降至常温,熔体晶化、凝固,熟料颗粒结构形成,并伴随熟料矿物相变的过程称为熟料的冷却。
熟料的冷却是熟料烧中一系列物理化学变化过程之一,冷却的目的在于:改善熟料质量与易磨性;降低熟料温度,便于熟料的运输、储存和粉磨;部分回收熟料出窑带走的热量,预热二次、三次空气,从而降低熟料热耗,提高热利用率。
2.熟料冷却速率对熟料质量的影响熟料冷却的速率影响着熟料的矿物组成、结构以及易磨性。
冷却速率不同,所得到的熟料矿物组成与性能也会不同。
当熟料缓慢地冷却时,熟料熔体中的离子扩散足以保证固液相间反应充分进行(即平衡冷却),熟料中的所有成分几乎都形成晶体并促使熟料晶体长大,部分矿物晶体顺利进行相变。
当熟料冷却速率很快(即急冷或称淬冷)时,在高温下形成的熟料熔体来不及结晶而冷却成玻璃相,并且因急冷阻止了晶体的长大与相变。
实验研究表明,当以4~5℃/min的缓慢降温速率对熟料冷却时,熟料中的C3A、C4AF呈结晶态,MgO形成晶体尺寸可达60μm的方镁石。
如果把含1% 30~6060μm方镁石晶体的水泥与含4%5μm方镁石的水泥分别在压蒸釜中试验,可发现它们呈现的膨胀率相近,即方镁石晶体大小影响水泥的安定性。
更为值得注意的是,缓慢冷却条件下,C3S在1250℃以下易分解成C2S和二次游离氧化钙,结果是降低水硬性,当伴随有还原气氛时,上述分解过程加速;而β-C2S也易转化成γ-C2S,最终造成熟料粉化并降低水硬性。
如果以18~20℃/min的急速降温速率对熟料进行冷却,则可以发现上述C3S的分解、C2S的转化、过大的方镁石晶体及全部的C3A和C4AF结晶态不复存在,即急速降温(急冷)优于缓慢冷却(慢冷)。
3.急冷对改善熟料质量的作用①防止或减少C3S的分解当急速冷却时,温度迅速从烧成温度开始下降并越过C3S的分解温度,使C3S来不及分解而呈介稳状态保存下来,避免或减少了因C3S分解成C2S和二次游离CaO而使水硬性降低的可能性。
项目六 烧结矿的处理及质量评价
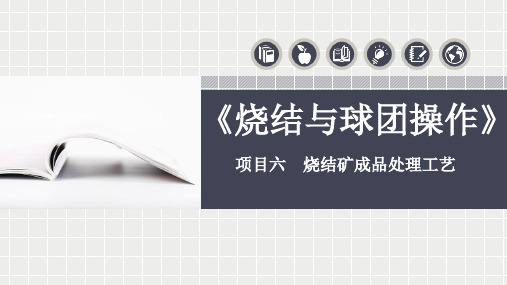
1.学习目标
2.任务描述
3.相关知识
任务二
烧结矿的破碎
4.任务实施
学习目标
任务描述
学习
目标
通过学习,明确剪切式单辊破碎机结构和工作原
理,掌握剪切式单辊破碎机的操作注意事项及事故原
因和处理方法。
剪切式单辊破碎机生产操作方法、事故处理方法。
任务
描述
相关知识
一、剪切式单辊破碎机结构
剪刀式单辊破碎机主要由星辊、轴辊、轴套、水管、固定箅及传动减速机构组成。
箅板是固定的,设在破碎机的下面,星辊在箅条之间的间隙内转动,破碎齿冠由耐热耐
磨材料堆焊或镶块而成。破碎齿形状不一,有三齿的也有四齿的,一般多采用四齿的。
相关知识
二、剪切式单辊破碎机的工作原理
剪切式单辊破碎机是借助转动的星辊与侧下方的箅板形成剪切作用将热烧结矿破碎的。
任务实施
二、热振筛常见故障及处理方法
任务实施
二、热振筛常见故障及处理方法
1.学习目标
2.任务描述
3.相关知识
任务四
烧结矿的冷却
4.任务实施
学习目标
任务描述
学习
目标
通过学习,了解烧结矿冷却的方法及影响冷却效果的因素;
掌握冷却设备的结构及冷却的原理;
能够按照操作规程的要求对冷却设备进行操作;
会处理烧结矿冷却过程中出现的一般事故。
掌握环式冷却机生产过程的操作。
任务
描述
相关知识
一、冷却意义
烧结矿冷却是将机尾卸下的红热烧结矿由卸矿温度强制冷却为100~150℃的冷矿。
1.烧结矿冷却后,便于整粒,出厂成品块度均匀,可以强化高炉冶炼,降低焦比。
烧结矿冷却方式

烧结矿冷却方式及国内生产实践2006-8-14 15:56:37 中国选矿技术网浏览981 次收藏我来说两句(一)烧结矿冷却方式的分类烧结矿的冷却靠介质进行。
冷却介质可以是空气、水或两者联合使用。
因此,国内外曾出现了多种的冷却方法和设备,可分为图1所示的类型。
(二)国内烧结矿冷却的生产实践1.机上冷却工艺机上冷却工艺是在烧结机上完成烧结和冷却过程。
即在烧结终了时,不立即卸下烧结矿,而让其继续停留在烧结机上,与此同时,利用冷却段风机吸入的冷空气使烧结矿冷却。
机上冷却的简图见图2.(1)机上冷却工艺的优缺点机上冷却工艺的优点是单辊破碎机的工作温度低,不需热矿振动筛和单独的冷却机,可以提高设备作业率、降低设备维修费;返矿量少、成品率高、燃料耗量低;简化了设备配置,改善操作环境,减少污染,便于冷却系统和环境除尘。
机上冷却工艺的缺点是冷却产生的废气温度高(可达600℃)、压力损失大(风机压力需8000Pa左右)、需要高温风机、功率消耗大;台车和箅条受热循环作用大;不能利用返矿的废热来预热混合料。
(2)机上冷却工艺的主要影响因素机上冷却工艺的主要影响因素如下:矿石性能对机上冷却工艺的影响较大,见图3.从图3可知,贫铁矿。
特别是褐铁矿烧结,其初始堆积密度低、烧损高,这类矿石烧成的烧结矿所需的冷却时间短,冷烧比小。
如水城烧结厂采用机上冷却工艺,冷烧比为0.77。
富矿中的磁铁矿烧结时,因所得烧结矿堆积密度大、透气性差,以及冷却过程的氧化放热,故其冷却时间长,但由于磁铁矿烧结时间也长,所以对冷烧比影响不大,冷烧比为1.0。
赤-针铁矿烧结所需冷烧比在上述两者之间。
不同矿物原料烧结所需的冷烧比,应通过烧结试验来确定。
烧结矿碱度(m(CaO)/m(SiO2))升高时,所得的烧结饼透气性得到改善,其冷却时间减少,从而减少冷烧比。
混合料的均匀性、料层高度与烧结负压、冷却负压等操作条件,都会影响机上冷却的冷却时间和冷却效果。
冷却时间在很大程度上取决于冷却风量和冷却负压。
基于烧结矿冷却过程余热利用分析

基于烧结矿冷却过程余热利用分析利用烧结矿冷却过程中的余热是一种节能、环保和经济效益的有效途径。
本文主要从烧结矿的生成过程以及冷却过程中余热的利用等方面进行分析,探讨余热利用的可行性和应用前景。
一、烧结矿的生成过程烧结矿是利用铁矿石、焦炭、石灰石等原料,在高温条件下进行反应,形成的一种铁矿石材料。
在这个过程中,需要将原料进行混合后送入耐火材料制成的烧结机中进行烧结,通过高温烧结生成烧结矿。
二、烧结矿的冷却过程烧结矿的高温状态需要冷却后才能使用,一般冷却的方式包括自然风冷和水冷两种形式。
自然风冷需要将烧结矿放置在风中进行自然冷却,这种方式的冷却时间较长,一般需要5-7天。
水冷则是利用冷水进行冷却,冷却时间相对较短,但是需要耗费大量的水资源和能源。
三、利用烧结矿冷却过程余热的可行性分析烧结矿冷却过程中产生的热量并不是无法利用的,通过合适的技术手段,可以将烧结矿冷却的热量转化为有用的能源。
目前,使用烧结矿冷却过程余热的方式主要有以下几种:1、余热回收发电利用余热回收发电是一种成熟、稳定的技术。
通过在冷却过程中设置余热回收装置,将热量转化为能电,减少对外界能源的依赖,达到节能的目的。
2、余热回收制氢烧结矿冷却过程中余热的温度较高,可用于制氢过程中的蒸汽重整反应中,这也是目前较为普遍的一种利用方式。
通过利用余热,可以使制氢过程中的成本降低,提高废气的利用率。
3、余热回收供暖冬季供暖是一项大消耗能源的工作,利用烧结矿冷却过程中的余热为供暖提供能源,可以有效地降低供暖成本,同时减少对环境的影响。
四、总结烧结矿冷却过程中的余热利用的可行性已经得到了很好的论证,不论是经济效益还是社会效益,都是非常可观的。
不同的利用方式可以根据实际情况的不同,进行灵活的应用。
我们相信,在不断推进科技进步的同时,利用余热也将越来越被人们所重视、关注、和采用。
钢厂烧结工艺流程

钢厂烧结工艺流程一、烧结工艺概述烧结是钢铁冶炼过程中的一项重要工艺,通过将细粉状的铁矿石和焦炭等物料加热,使其部分熔化并粘结成为直径一定大小的烧结矿,为后续的铁水冶炼提供原料。
钢厂烧结工艺流程主要包括原料配比、矿石破碎、混合、烧结、冷却、筛分等环节。
二、原料配比钢厂烧结工艺的首要任务是确定合理的原料配比比例。
根据矿石的化学成分和质量要求,钢厂技术人员会制定烧结矿的配比方案。
一般来说,烧结矿的主要成分包括铁矿石、焦炭、石灰石和其他添加剂。
这些原料按一定比例混合后,形成矿料堆积。
三、矿石破碎矿石破碎是将原料中的铁矿石进行粉碎的过程。
首先,将原料送入破碎机中,经过粉碎机的破碎作用,将矿石破碎成一定粒度的颗粒。
矿石破碎的目的是为了增大表面积,提高矿石的反应性,有利于后续的烧结过程。
四、混合矿石破碎后的铁矿石与焦炭、石灰石等原料按照一定比例混合。
混合的目的是确保各种原料在烧结过程中能够充分反应,形成均匀的矿料堆积。
混合通常采用混料机进行,通过机械搅拌使各种原料充分混合。
五、烧结烧结是将混合后的矿料进行加热处理的过程。
在烧结机中,矿料堆积被加热至一定温度,使其部分熔化并形成烧结矿。
烧结过程中,焦炭在高温下发生氧化反应,产生一定量的热量,使矿料熔化并粘结在一起。
同时,石灰石中的CaO也发生反应,形成熔融的CaO-SiO2-Al2O3-Fe2O3等化合物,进一步增强矿料的粘结性。
六、冷却烧结完成后,烧结矿需要进行冷却处理。
冷却的目的是使烧结矿迅速降温,并保持其结构和硬度。
通常采用冷却机进行冷却,通过强风将烧结矿表面的热量带走,使其迅速冷却。
七、筛分经过冷却后的烧结矿需要进行筛分,将不符合规格要求的颗粒进行分离。
筛分的目的是获得符合要求的烧结矿颗粒,以供后续的冶炼使用。
通常采用筛分机进行筛分,根据烧结矿的粒度要求,将不同大小的颗粒进行分离。
八、成品矿料经过上述工艺流程,最终得到的是符合钢厂要求的成品矿料。
这些成品矿料具有一定的强度和耐高温性能,适合用于钢铁冶炼的高炉和转炉炼钢过程。
烧结矿的冷却与整粒

烧结矿的冷却与整粒一、烧结矿冷却的目的和意义烧结矿在烧结机上烧成后从机尾卸下时其温度大约在600 ~1000 ℃,对这样的赤热烧结矿,在现代化得烧结厂中,一般却要将其冷却到150℃以下,这是因为以下几个原因:1、保护运输设备,使厂区配置紧凑。
如果烧结矿不冷却,运送赤热得烧结矿就需要使用较多得专用矿车来装载,当烧结配比不当、残碳较多时,烧结矿还会在专用得矿车中继续燃烧,致使矿车烧坏变形,而且使用矿车时还要有较长的铁路运输线,会使烧结厂与炼铁厂在配置上不得不拉得很远。
若将烧结矿冷却就可采用胶带机运输,使厂区配置紧凑,少占农田用地。
2、护高炉炉顶设备及高炉矿槽。
结矿如不冷却贮存在高炉矿槽之中,保烧会很快损坏高炉矿槽,致使有时要停止生产修补矿槽,影响作业率,降低产量。
使用不经过冷却得烧结矿,高炉炉顶温度高,为了保护炉顶设备,一般炉顶压力不敢提高。
而使用冷烧结矿,可以提高炉顶压力,对强化高炉冶炼、提高产质量有利,高炉的上料系统及炉顶设备不易损坏,使用寿命也大大提高了。
3、改善高炉、烧结厂的劳动条件。
由于烧结矿冷却后可以筛除粉末,冷烧结矿在由烧结厂到高炉矿槽以及高炉上料系统的一系列装卸运输运转过程所产生的污染环境的灰尘比热烧结矿大大减少,从而改善了劳动条件和环境卫生。
4、为烧结矿的整粒及分出铺底料创造了条件。
烧结矿不经过冷却,由于温度高,很难进行较彻底的破碎筛分以及分出烧结厂需要的铺底料。
烧结矿冷却到150 ℃以下,就可使用在常温下工作的破碎机,筛子及胶带运输机进行冷破碎,以及多次的筛分运输作业,较彻底地筛除粉末(5 ~0mm)分出,铺底料(10~20 mm)。
5、为实现高炉生产技术现代化创造条件。
现代化的高炉生产技术已发展到超高压炉顶操作,无料钟炉顶,胶带机炉顶上料,外燃式热风炉,炉内料位控制等等,所有这些都必须建立在烧结矿冷却及整粒分级的基础上,因而烧结矿如不冷却也无法实现高炉技术现代化。
二、烧结矿的冷却方法烧结矿的冷却方法很多,从方法上来分,有自然冷却和强制通风冷却两类;从冷却的地点和设备来分,有烧结机外冷却和烧结机上冷却两种。
烧结矿冷却过程实验与数值模拟研究的开题报告
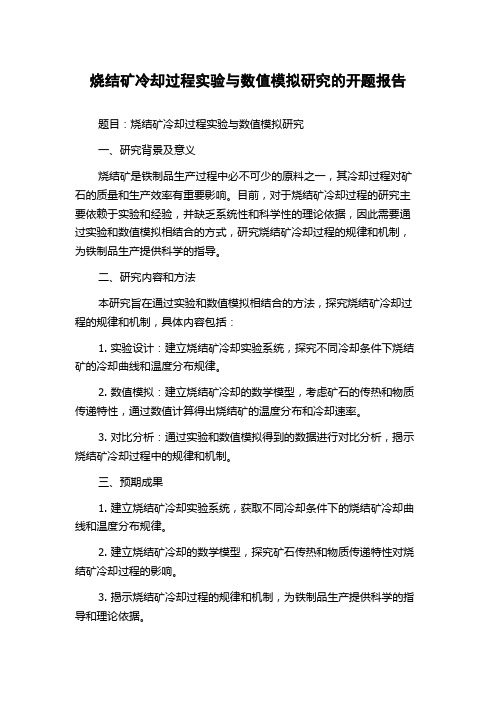
烧结矿冷却过程实验与数值模拟研究的开题报告题目:烧结矿冷却过程实验与数值模拟研究一、研究背景及意义烧结矿是铁制品生产过程中必不可少的原料之一,其冷却过程对矿石的质量和生产效率有重要影响。
目前,对于烧结矿冷却过程的研究主要依赖于实验和经验,并缺乏系统性和科学性的理论依据,因此需要通过实验和数值模拟相结合的方式,研究烧结矿冷却过程的规律和机制,为铁制品生产提供科学的指导。
二、研究内容和方法本研究旨在通过实验和数值模拟相结合的方法,探究烧结矿冷却过程的规律和机制,具体内容包括:1. 实验设计:建立烧结矿冷却实验系统,探究不同冷却条件下烧结矿的冷却曲线和温度分布规律。
2. 数值模拟:建立烧结矿冷却的数学模型,考虑矿石的传热和物质传递特性,通过数值计算得出烧结矿的温度分布和冷却速率。
3. 对比分析:通过实验和数值模拟得到的数据进行对比分析,揭示烧结矿冷却过程中的规律和机制。
三、预期成果1. 建立烧结矿冷却实验系统,获取不同冷却条件下的烧结矿冷却曲线和温度分布规律。
2. 建立烧结矿冷却的数学模型,探究矿石传热和物质传递特性对烧结矿冷却过程的影响。
3. 揭示烧结矿冷却过程的规律和机制,为铁制品生产提供科学的指导和理论依据。
四、拟定工作计划1. 文献调研和理论学习:对烧结矿冷却过程的相关文献进行调研和阅读,学习烧结矿冷却的基本理论和数值计算方法。
2. 实验设计和数据分析:搭建烧结矿冷却实验系统,获取实验数据,对实验数据进行处理和分析。
3. 模型建立和数值计算:建立烧结矿冷却的数学模型,进行数值计算和分析。
4. 对比分析和成果总结:对实验和数值模拟得到的数据进行对比分析,总结烧结矿冷却过程的规律和机制,并撰写毕业论文。
五、预期困难和解决办法1. 实验的可控性和精度问题:初步预计,实验中可能出现温度监测不准确等问题,需要加强实验平台的可控性和精度,以确保可靠的实验结果。
解决办法:增加实验测量点,同时采用多种不同测量方法进行监控和校准,提高实验数据的精度和可靠性。
烧结矿

摘要通过建立烧结矿冷却实验台,对换热本体冷却风出口温度与烧结矿粒径、料层厚度、冷却风温度等变量之间的关系进行分析,主要研究烧结矿粒径、料层厚度、冷却风温度及冷却风速度等因素对烧结矿冷却风速和热废气流量及温度的影响规律及单位烧结矿可利用的换热量。
关键词:冷却;余热;换热。
1. 实验目的建立烧结矿冷却实验台通过改变粒径,冷却风温度,料层厚度等变量测得冷却风出口风温的变化,一方面揭示烧结矿温度、粒径、料层厚度、烧结矿粒度分布特性等因素对烧结矿冷却速度和热废气流量、温度的影响规律并通过正交实验的方法优化出最佳控制工况。
另一方为研发烧结余热高效应用产业链配套工艺技术和装备奠定了理论基础。
2. 实验原理烧结环冷机内换热过程为交叉流移动床气固换热,实验台设计成固定气固填充床。
环冷机冷却过程是一个连续操作过程,实际工况中环冷机运转速度约为1.5m/min,速度比较低,在实验过程中可以用冷却时间来模拟环冷机不同位置上的物料的冷却情况。
3. 实验装置实验台主要由烧结矿换热系统、热泵机组余热利用系统和实验监测及控制系统三部分构成。
烧结矿换热系统由矿石加热炉、天车、变频风机、空气加热器、烧结矿换热本体、换热器及连接管路组成;热泵机组余热利用系统由热泵机组、循环加热器、换热器、管道泵、混合水箱、PE管地埋管路及连接管路组成;实验监测及控制系统由计算机、控制柜、红外热像仪、涡轮流量计、涡街流量计、热电偶、热电阻、压力变送器及相关通信电缆组成。
1-矿石加热炉;2-红外热像仪;3-烧结矿换热本体;4-换热器;5-阀门;6-循环加热器;7-管道泵;8-热泵机组;9-混合水箱;10-PE管地埋管路;11-空气加热器;12-变频风机图1 实验装置示意图实验台主要装置具体情况如下:矿石加热炉:沈阳通用电炉制造有限公司,型号RT3-45-10(料斗尺寸Φ900×615mm,电压380V,相数3,额定功率45KW,额定温度1000℃);风机:蚌埠市华力风机有限公司,型号7-19No.5.6A(全压6160Pa,流量2653m3/h,电压380V,额定功率5.5KW);空气加热器:宝应县东洋电器有限公司,(电压380V,额定功率36KW);烧结矿换热本体(定制):河北理工大学机械实习工厂(进出口管路Φ159,内胆材料2520不锈钢,外部敷设保温层);换热器:吉林四平维克斯换热设备有限公司,型号VKJ-38(空气流量1000m3/h,水流量6m3/h,风压500Pa,换热面积38m2);循环加热器:宝应县东洋电器有限公司,(电压380V,额定功率45KW);管道泵:唐山市路南信诚水泵电机销售处,(流量6m3/h,扬程20m,电压380V,额定功率0.75KW)热泵机组:江苏汇能新能源科技有限公司,型号RZX-23(电压380V,额定制冷量23KW,额定功率0.3KW)4. 数据处理4.1 数据筛选通过观察分析10月07日的数据,T11~T17为换热过程中烧结矿的温度,我们可以通过不同时间T11~T17温度的显示绘出烧结矿在换热过程中的温度变化绘画出烧结矿温度变化曲线图(图2)。
烧结工艺流程介绍

烧结工艺流程介绍为了保证供给高炉的铁矿石中铁含量均匀,并且保证高炉的透气性,需要把选矿工艺产出的铁精矿制成10-25mm的块状原料。
铁矿粉造块目前主要有两种方法:烧结法和球团法。
两种方法所获得的块矿分别为烧结矿和球团矿。
本专题将详细介绍烧结生产的工艺流程,主要工艺设备的工作原理以及控制要求等信息,其次,我们将简要介绍球团法生产的工艺流程,主要工艺设备的工作原理以及控制要求等信息。
铁矿粉造块的目的:◆综合利用资源,扩大炼铁用的原料种类。
◆去除有害杂质,回收有益元素,保护环境。
◆改善矿石的冶金性能,适应高炉冶炼对铁矿石的质量要求。
铁矿粉造块的方法:烧结法和球团法。
铁矿粉造块后的产品:分别为烧结矿和球团矿。
(供高炉炼铁生产的主要原料)一、烧结生产的工艺流程介绍:专题:烧结工艺流程介绍[工艺流程] 铁矿粉烧结生产工艺流程[工艺流程] 球团矿生产工艺流程[工艺流程] 烧结工艺流程图专题:烧结工艺的主要设备及其工作原理[烧结设备] 烧结机布料器简介[烧结设备] 带式烧结机[烧结设备] 单辊破碎机[烧结工艺] 烧结基础知识[烧结工艺] 烧结原料的准备及加工处理[烧结工艺] 配料工艺及计算[烧结工艺] 混合与制粒[烧结工艺] 烧结机布料与点火制度[烧结工艺] 烧结矿的冷却与整粒[烧结设备] 除尘器简介[烧结设备] 配料计量秤[烧结设备] 鼓风环式冷却机简介[烧结设备] 振动筛简介[烧结设备] 静电除尘器简介[烧结设备] 圆盘造球机工作原理铁矿粉烧结生产工艺流程1.烧结的概念将各种粉状含铁原料,配入适量的燃料和熔剂,加入适量的水,经混合和造球后在烧结设备上使物料发生一系列物理化学变化,将矿粉颗粒黏结成块的过程。
2. 烧结生产的工艺流程目前生产上广泛采用带式抽风烧结机生产烧结矿。
烧结生产的工艺流程如图2—4所示。
主要包括烧结料的准备,配料与混合,烧结和产品处理等工序。
图2-4 抽风烧结工艺流程◆烧结原料的准备①含铁原料含铁量较高、粒度<5mm的矿粉,铁精矿,高炉炉尘,轧钢皮,钢渣等。
烧结机机尾烧结矿的温度
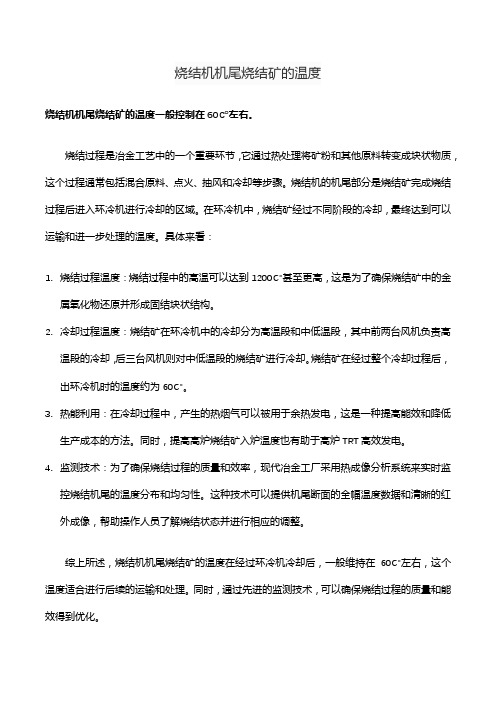
烧结机机尾烧结矿的温度
烧结机机尾烧结矿的温度一般控制在60℃左右。
烧结过程是冶金工艺中的一个重要环节,它通过热处理将矿粉和其他原料转变成块状物质,这个过程通常包括混合原料、点火、抽风和冷却等步骤。
烧结机的机尾部分是烧结矿完成烧结过程后进入环冷机进行冷却的区域。
在环冷机中,烧结矿经过不同阶段的冷却,最终达到可以运输和进一步处理的温度。
具体来看:
1.烧结过程温度:烧结过程中的高温可以达到1200℃甚至更高,这是为了确保烧结矿中的金
属氧化物还原并形成固结块状结构。
2.冷却过程温度:烧结矿在环冷机中的冷却分为高温段和中低温段,其中前两台风机负责高
温段的冷却,后三台风机则对中低温段的烧结矿进行冷却。
烧结矿在经过整个冷却过程后,出环冷机时的温度约为60℃。
3.热能利用:在冷却过程中,产生的热烟气可以被用于余热发电,这是一种提高能效和降低
生产成本的方法。
同时,提高高炉烧结矿入炉温度也有助于高炉TRT高效发电。
4.监测技术:为了确保烧结过程的质量和效率,现代冶金工厂采用热成像分析系统来实时监
控烧结机尾的温度分布和均匀性。
这种技术可以提供机尾断面的全幅温度数据和清晰的红外成像,帮助操作人员了解烧结状态并进行相应的调整。
综上所述,烧结机机尾烧结矿的温度在经过环冷机冷却后,一般维持在60℃左右,这个温度适合进行后续的运输和处理。
同时,通过先进的监测技术,可以确保烧结过程的质量和能效得到优化。
烧结矿冷却的目的和意义
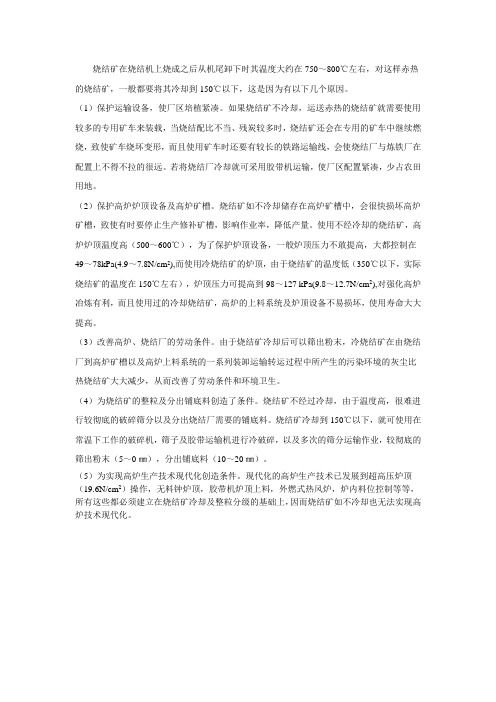
烧结矿在烧结机上烧成之后从机尾卸下时其温度大约在750~800℃左右,对这样赤热的烧结矿,一般都要将其冷却到150℃以下,这是因为有以下几个原因。
(1)保护运输设备,使厂区培植紧凑。
如果烧结矿不冷却,运送赤热的烧结矿就需要使用较多的专用矿车来装载,当烧结配比不当、残炭较多时,烧结矿还会在专用的矿车中继续燃烧,致使矿车烧坏变形,而且使用矿车时还要有较长的铁路运输线,会使烧结厂与炼铁厂在配置上不得不拉的很远。
若将烧结厂冷却就可采用胶带机运输,使厂区配置紧凑,少占农田用地。
(2)保护高炉炉顶设备及高炉矿槽。
烧结矿如不冷却储存在高炉矿槽中,会很快损坏高炉矿槽,致使有时要停止生产修补矿槽,影响作业率,降低产量。
使用不经冷却的烧结矿,高炉炉顶温度高(500~600℃),为了保护炉顶设备,一般炉顶压力不敢提高,大都控制在49~78kPa(4.9~7.8N/cm2),而使用冷烧结矿的炉顶,由于烧结矿的温度低(350℃以下,实际烧结矿的温度在150℃左右),炉顶压力可提高到98~127 kPa(9.8~12.7N/cm2),对强化高炉冶炼有利,而且使用过的冷却烧结矿,高炉的上料系统及炉顶设备不易损坏,使用寿命大大提高。
(3)改善高炉、烧结厂的劳动条件。
由于烧结矿冷却后可以筛出粉末,冷烧结矿在由烧结厂到高炉矿槽以及高炉上料系统的一系列装卸运输转运过程中所产生的污染环境的灰尘比热烧结矿大大减少,从而改善了劳动条件和环境卫生。
(4)为烧结矿的整粒及分出铺底料创造了条件。
烧结矿不经过冷却,由于温度高,很难进行较彻底的破碎筛分以及分出烧结厂需要的铺底料。
烧结矿冷却到150℃以下,就可使用在常温下工作的破碎机,筛子及胶带运输机进行冷破碎,以及多次的筛分运输作业,较彻底的筛出粉末(5~0㎜),分出铺底料(10~20㎜)。
(5)为实现高炉生产技术现代化创造条件。
现代化的高炉生产技术已发展到超高压炉顶(19.6N/cm2)操作,无料钟炉顶,胶带机炉顶上料,外燃式热风炉,炉内料位控制等等,所有这些都必须建立在烧结矿冷却及整粒分级的基础上,因而烧结矿如不冷却也无法实现高炉技术现代化。
工艺流程中冷却的作用
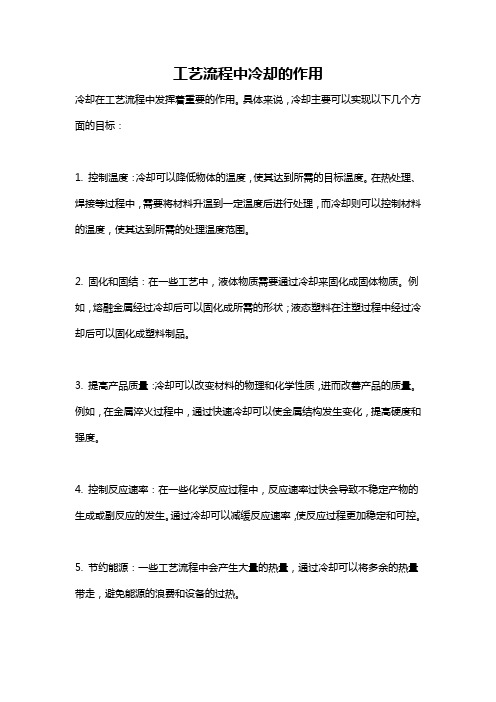
工艺流程中冷却的作用
冷却在工艺流程中发挥着重要的作用。
具体来说,冷却主要可以实现以下几个方面的目标:
1. 控制温度:冷却可以降低物体的温度,使其达到所需的目标温度。
在热处理、焊接等过程中,需要将材料升温到一定温度后进行处理,而冷却则可以控制材料的温度,使其达到所需的处理温度范围。
2. 固化和固结:在一些工艺中,液体物质需要通过冷却来固化成固体物质。
例如,熔融金属经过冷却后可以固化成所需的形状;液态塑料在注塑过程中经过冷却后可以固化成塑料制品。
3. 提高产品质量:冷却可以改变材料的物理和化学性质,进而改善产品的质量。
例如,在金属淬火过程中,通过快速冷却可以使金属结构发生变化,提高硬度和强度。
4. 控制反应速率:在一些化学反应过程中,反应速率过快会导致不稳定产物的生成或副反应的发生。
通过冷却可以减缓反应速率,使反应过程更加稳定和可控。
5. 节约能源:一些工艺流程中会产生大量的热量,通过冷却可以将多余的热量带走,避免能源的浪费和设备的过热。
总之,冷却在工艺流程中起到了温度控制、物质固化、产品质量改善、反应速率调节和能源节约等方面的作用。
出窑熟料快速冷却有何作用

出窑熟料快速冷却有何作用出窑熟料快速冷却有何作用一般所说的熟料冷却过程是指液相凝固以后(< 1300 ℃)熟料的继续冷却。
但是严格地讲,当熟料过了最高煅烧温度后,就算进入了冷却阶段。
熟料的冷却并不单纯是温度的降低,而是伴随着一系列的内在的物理化学变化,同时进行液相的凝固和相变两个过程。
熟料快速冷却有以下作用:1)提高熟料的质量熟料冷却时,形成的矿物要进行相变,如慢冷时β- C2S在500 ℃左右转化为γ- C2S,同时体积膨胀约10%,使熟料“粉化”。
因γ- C2S几乎无水硬性,会使熟料质量下降。
如采用快速冷却越过相变温度区域,并固溶一些杂质离子,可以避免β型C2S向γ型C2S转化,从而获得较高的水硬性。
硅酸三钙在1250 ℃以下不稳定,会缓慢分解为硅酸二钙与二次游离氧化钙,使水硬性降低。
所以提高冷却速度可防止硅酸三钙的分解。
水泥的安定性受方镁石晶体尺寸的影响较大,晶体愈大影响愈严重。
如快速冷却,可使MgO来不及结晶而存在于玻璃体中,或使晶体细小而分散,减少其危害性。
熟料快冷能增强水泥的抗硫酸盐性。
因为熟料快冷时,C3A主要呈玻璃体,因而其抗硫酸盐溶液腐蚀的能力较强。
2)改善熟料的易磨性急冷熟料的玻璃体含量较高,脆性较高;同时急冷造成熟料产生内应力,容易在外力作用下碎裂,而且熟料矿物晶体较小,所里快冷可显著地改善熟料的易磨性。
3)回收余热熟料从1300 ℃冷却,进入冷却机时尚处于1100 ℃以上的高温如把它冷却到室温,则尚有约837 kJ/kg的熟料热量可用二次空气来回收,此举有利于窑内燃料的燃烧,提高窑的热效率。
4)有利于熟料的输送、储存和粉磨为确保输送设备的安全运转,要使熟料温度低于100 ℃。
储存熟料的钢筋混凝土圆库如温度较高,容易出现裂纹;为防止水泥粉磨时磨内温度过高而造成水泥的“假凝”现象,以及磨内温度过高,产生包球,降低磨机产量,必须将熟料快速冷却到较低的温度。
烧结矿竖炉式冷却技术
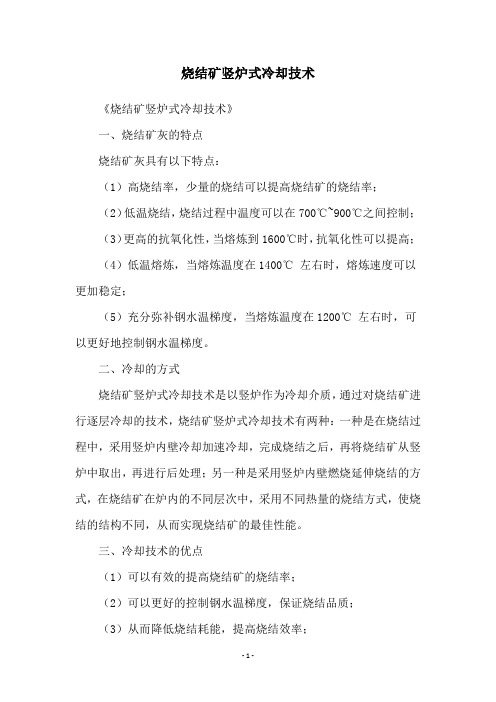
烧结矿竖炉式冷却技术
《烧结矿竖炉式冷却技术》
一、烧结矿灰的特点
烧结矿灰具有以下特点:
(1)高烧结率,少量的烧结可以提高烧结矿的烧结率;
(2)低温烧结,烧结过程中温度可以在700℃~900℃之间控制;
(3)更高的抗氧化性,当熔炼到1600℃时,抗氧化性可以提高;
(4)低温熔炼,当熔炼温度在1400℃左右时,熔炼速度可以更加稳定;
(5)充分弥补钢水温梯度,当熔炼温度在1200℃左右时,可以更好地控制钢水温梯度。
二、冷却的方式
烧结矿竖炉式冷却技术是以竖炉作为冷却介质,通过对烧结矿进行逐层冷却的技术,烧结矿竖炉式冷却技术有两种:一种是在烧结过程中,采用竖炉内壁冷却加速冷却,完成烧结之后,再将烧结矿从竖炉中取出,再进行后处理;另一种是采用竖炉内壁燃烧延伸烧结的方式,在烧结矿在炉内的不同层次中,采用不同热量的烧结方式,使烧结的结构不同,从而实现烧结矿的最佳性能。
三、冷却技术的优点
(1)可以有效的提高烧结矿的烧结率;
(2)可以更好的控制钢水温梯度,保证烧结品质;
(3)从而降低烧结耗能,提高烧结效率;
(4)节约传统烧结的大量的热量,减少污染;
(5)可以实现烧结矿的高烧结率和高品质,从而提高产品的质量,降低生产成本。
钢厂烧结机原理

钢厂烧结机原理一、概述钢厂烧结机是钢铁行业中一种重要设备,用于将粉状或颗粒状的铁矿石和其他添加剂进行烧结,制成高强度的烧结矿。
烧结矿是高炉冶炼的主要原料之一,具有良好的还原性和透气性,能够稳定高炉冶炼过程,提高冶炼效率和产品质量。
二、烧结机工作原理钢厂烧结机主要由烧结机筒体、烧结机炉排、热风炉、烟气处理设备等组成。
其工作原理可以分为下列几个步骤:1. 堆料铁矿石和其他添加剂通过皮带输送机等设备,被均匀地堆放在烧结机筒体上。
矿石中的硅、锰、磷等杂质会影响烧结矿的质量,因此在堆料时需要根据原料的成分进行合理的配比。
2. 预热热风炉产生的高温热风通过风管送入烧结机筒体,对堆料进行预热。
预热的目的是提高矿石颗粒间的结合力,促进烧结反应的进行。
3. 烧结反应在预热后,矿石中的铁矿物开始发生烧结反应。
烧结反应是一种高温下的固相反应,铁矿石的颗粒通过扩散、熔融、结合等过程,形成新的矿石颗粒。
烧结反应需要一定的时间和温度,因此烧结机筒体通常会有多个炉排,以确保矿石在烧结过程中能够充分反应。
4. 冷却烧结完成后的烧结矿需要进行冷却,以防止热矿在运输过程中发生结块。
冷却一般使用冷风进行,冷风通过风管进入烧结机筒体,对烧结矿进行快速冷却。
5. 矿石分选冷却后的烧结矿需要进行分选,将不同粒度的矿石分离出来。
矿石分选可以采用振动筛分机等设备进行,将烧结矿按照不同粒度进行分类,以满足不同冶炼工艺的需要。
三、烧结机的优点和应用钢厂烧结机具有以下优点:1. 提高矿石利用率:烧结机可以将粉状或颗粒状的铁矿石进行烧结,将废弃物料转化为有价值的烧结矿,提高矿石的利用率。
2. 增加高炉产能:烧结矿具有良好的还原性和透气性,可以提高高炉的冶炼效率和产能。
3. 改善高炉冶炼条件:烧结矿中的铁矿物质经过烧结反应后,形成了新的矿石颗粒,具有更好的还原性和流动性,可以改善高炉的冶炼条件,减少结焦和堵塞现象。
钢厂烧结机广泛应用于钢铁行业,特别是高炉冶炼过程中。
- 1、下载文档前请自行甄别文档内容的完整性,平台不提供额外的编辑、内容补充、找答案等附加服务。
- 2、"仅部分预览"的文档,不可在线预览部分如存在完整性等问题,可反馈申请退款(可完整预览的文档不适用该条件!)。
- 3、如文档侵犯您的权益,请联系客服反馈,我们会尽快为您处理(人工客服工作时间:9:00-18:30)。
烧结矿在烧结机上烧成之后从机尾卸下时其温度大约在750~800℃左右,对这样赤热的烧结矿,一般都要将其冷却到150℃以下,这是因为有以下几个原因。
(1)保护运输设备,使厂区培植紧凑。
如果烧结矿不冷却,运送赤热的烧结矿就需要使用较多的专用矿车来装载,当烧结配比不当、残炭较多时,烧结矿还会在专用的矿车中继续燃烧,致使矿车烧坏变形,而且使用矿车时还要有较长的铁路运输线,会使烧结厂与炼铁厂在配置上不得不拉的很远。
若将烧结厂冷却就可采用胶带机运输,使厂区配置紧凑,少占农田用地。
(2)保护高炉炉顶设备及高炉矿槽。
烧结矿如不冷却储存在高炉矿槽中,会很快损坏高炉矿槽,致使有时要停止生产修补矿槽,影响作业率,降低产量。
使用不经冷却的烧结矿,高炉炉顶温度高(500
~600℃),为了保护炉顶设备,一般炉顶压力不敢提高,大都控制
在49~78kPa(4.9~7.8N/cm2),而使用冷烧结矿的炉顶,由于烧结矿的温度低(350℃以下,实际烧结矿的温度在150℃左右),炉顶压力可提高到98~127 kPa(9.8~12.7N/cm2),对强化高炉冶炼有利,而且使用过的冷却烧结矿,高炉的上料系统及炉顶设备不易损坏,使用寿命大大提高。
(3)改善高炉、烧结厂的劳动条件。
由于烧结矿冷却后可以筛出粉末,冷烧结矿在由烧结厂到高炉矿槽以及高炉上料系统的一系列装卸运输转运过程中所产生的污染环境的灰尘比热烧结矿大大减少,从而改善了劳动条件和环境卫生。
(4)为烧结矿的整粒及分出铺底料创造了条件。
烧结矿不经过冷却,由于温度高,很难进行较彻底的破碎筛分以及分出烧结厂需要的铺底料。
烧结矿冷却到150℃以下,就可使用在常温下工作的破碎机,筛子及胶带运输机进行冷破碎,以及多次的筛分运输作业,较彻底的筛出粉末(5~0㎜),分出铺底料(10~20㎜)。
(5)为实现高炉生产技术现代化创造条件。
现代化的高炉生产技术已发展到超高压炉顶(19.6N/cm2)操作,无料钟炉顶,胶带机炉顶上料,外燃式热风炉,炉内料位控制等等,所有这些都必须建立在烧结矿冷却及整粒分级的基础上,因而烧结矿如不冷却也无法实现高炉技术现
代化。