化肥厂工艺反应原理简介
某化肥厂工艺流程介绍

某化肥厂工艺流程介绍
本项目造气工段以无烟煤为原料采用固定层间歇法制取半水煤气,采用TSC催化脱硫法脱除半水煤气中的硫化氢,脱硫后的半水煤气经压缩至2.1MPa进变换工段,采用中低低变换工艺、湿法栲胶变脱工艺,以及PSA变压吸附法脱除变换气中的CO2,脱碳后的净化气压缩至15.0MPa采用中压甲醇合成、25.0MPa高压醇烷化工艺,使合成新鲜气得以深度净化,之后在高温、高压和触媒存在的条件下将合格的氮氢混合气在合成塔内进行合成反应,最终生成中间产品液氨。
来自变压吸附脱碳工段的CO2经压缩,与来自氨合成工段的液氨在尿素合成塔内反应,生成熔融尿素,经蒸发、造粒、包装得到最终产品尿素。
小型合成氨厂的基本工艺

二、冷鼓车间
•目的和任务: • 除去焦炉气中残余粉尘 微粒及焦油后,再经煤气鼓 风机升压后送往洗氨脱萘为 后工序提供洁净的焦炉气。
三、压缩工段
目的和任务: 是把气体输送到各工序
并提供过程进行所需要的压力, 以使这些过程按工艺要求得以 顺利进行。
四、变换岗位
合成岗位
目的和任务:
将经甲烷化后送来的氢氮比合格的气体导入 系统,在一定的温度、压力下在氨催化剂的 作用下使氢氮气合成氨,热后经过水冷、氨 冷使混合气中的大部分气氨冷凝成液氨而分 离出来,并送往氨贮槽。分离出液氨的氢氮 混合气经循环机赠压后与补充的新鲜气在一 起送入合成塔内进行反应,如此循环。
小型化肥厂的工艺简介
小型氮肥厂的整体工艺流程
焦化车间
冷鼓车间
原料气压缩工段
变脱工段
PSA一段
碳化车间
氨回收工段
合成车间
合成压缩工段
PSA二段 精脱工段硫 工段甲烷化
CO2压缩
碳化车间 化肥
一、焦化车间
•主要的工作原理及目的 •原理:原煤经过焦化炉高温干熘后, 产出煤气,并留下了其付产品焦Βιβλιοθήκη 炭、焦油等产品。精脱硫岗位
目的与任务: 除和去有变机脱硫后,原保料证气 气中体少中量硫的化H物2S 总含量小于0.1PPm,满足甲烷 化工艺对硫的要求,同时消除 硫化物对管道和设备的腐蚀。
甲烷化岗位
除<1去.0脱%)碳,气在少适量当的的C温O和度C、O压2(共力 下,通过甲烷化催化剂的作用 将成残触余媒的无C害O的和甲CO烷2转,化出为口对气合体 (CO+CO2<20PPm)。
目的和任务: 将压缩工段送来的焦炉气中
的CO加入水蒸气并在催化剂的作 用 后下工转段化提成供较CO合2,格同的时原获料得气H2。,为
化学肥料的生产方法和原理

• 天然矿物
(两大类)
水溶性: 钾长石、光卤石、硝石 水不溶性: 磷灰石、明矾石
水溶性矿物生产化学肥料,加工比较简单,仅 需溶解富集、分离和提纯的过程。
水不溶性矿物生产化学肥料时,首先必须进行 化学加工,使其成为作物所能吸收的水溶性或 微溶性物质,然后经过除去杂质、蒸发、结晶 等工序制成成品。
天然矿物可分为水溶性和水不溶性两大类。钾长石、光卤石、 硝石是水溶性的矿物,磷灰石、明矾石是水不溶性矿物的例 子。用水溶性矿物生产肥料仅是富集、分离和提纯的过程, 加工简单。而水不涪性矿物用来生产肥料时,首先必须进行 化学加工,使其成为作物所能吸收的水涪性或微溶性物质, 然后经过除去杂质、蒸发、结晶等工序3贼成品。
在选矿时,为了将其中的有用成分一一分离, 往往同时采用几种方法。
含钛铁矿、磁铁矿的 浮选法 含P2O5 >30% 重力选
低品位磷矿石
的磷灰石精矿
钛铁矿、磁铁矿 磁选法
含TiO2 48.48%的钛精矿
含铁67.68%的铁精矿
上述各种选矿方法称为物理选矿法 (矿石的化学结构不发生变化) 有些选矿方法是使矿石经过化学变化之后而进行的
各种药剂的用量都很少,浮选每吨矿石,多者只 要数百克,少者仅仅需要数克。有的药剂兼有几种 作用,如硫化钠既是抑制剂,又是PH调节剂。
正浮选 将其中的有用成份浮入泡沫产物中, 而将脉石矿物留在矿浆中
反浮选 将脉石矿物浮入泡沫产物而将 有用矿物留在非泡沫产物中
如矿物中含有两种或两种以上的有用矿物,其浮选方法有两种:
以磷灰石(Ca5F(PO4)3) 生产磷酸为例,既可用硫 酸、硝酸、盐酸等无机酸使之分解,然后利用生成 沉淀(过滤)和溶剂萃取等方法除去CaS04 、 Ca(N03)2和CaCl2而得到磷酸;也可以在电炉中用 焦炭还原先制得黄磷,而后经氧化和水吸收而得磷 酸。得到磷酸以后进一步加工成为肥料时,方法就 更多了。
化肥厂合成氨装置生产原理及工艺流 共78页
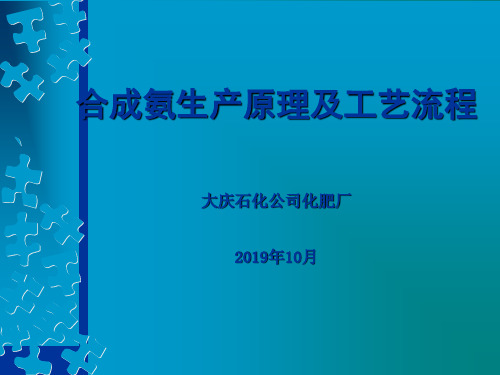
4.4 二段转化反应 二段转化反应是在一个自热式的内衬耐火材料的
圆筒式反应炉内进行的,在此引入空气,空气中的氧 气与一段转化出口气中的氢气发生燃烧,燃烧热用来 进一步转化残余甲烷。控制补入的空气流量,可同时 满足合成氨反应对氮气的需要。 1.氢气与空气中的氧燃烧反应方程式如下:
H2 + 0.5 O2 = H2O + 242 KJ/mol
3.2一段炉炉管透火。 该炉管为2000年更换,使用7年多,10月停车处理
123根泄漏炉管,现在炉顶仍有两处透火,用氮气保护 特护运行,制定事故预案,准备2019年大修更换整炉炉 管。 3.3 二段炉偏烧,出口气体CH4超过设计值,影响装置 能耗,2019年大修检查处理。 3.4 101-CA内漏
4.2 氧化锌脱硫反应 氧化锌脱硫是目前在工业上采用的脱硫效率最高的方
法,它能以极快的速度将H2S和部分有机硫全部“吃掉” ,净化后气体中硫含量可降到0.1ml/m3甚至更低。
合成装置有两台氧化锌反应炉,可以并联、串联,或 任意切除一台,以便正常生产时更换触媒。由于氧化锌实 际参加化学反应,所以其寿命很短,根据油田气含硫量及 生产负荷不同,我厂合成氨装置每年约更换4炉氧化锌触 媒。
4.7 甲烷化反应原理、影响甲烷化反应的因素、甲烷 化催化剂 1.甲烷化反应的化学方程式:
CO + 3 H2 = CH4 + H2O + 206.284KJ/MOL CO2 + 4 H2 = CH4 + 2 H2O + 165.127KJ/MOL 这两个的反应都是强放热反应,造成显著的温升,绝 热温升的数值大体是: 每反应1%CO温升72℃ 每反应1%CO2温升60℃ 甲烷化反应随温度或压力的提高而加速。如果前部反 应不好,会造成甲烷化催化剂超温,烧坏触媒。
复合肥生产工艺介绍

复合肥的生产工艺介绍目前颗粒状复混肥料的生产方法主要有料浆法、固体团粒法、部分料浆法、融熔法等,下面对这几种典型的生产方法作以介绍。
1.料浆法以磷酸、氨为原料,利用中和器、管式反应器将中和料浆,在氨化粒化器中进行涂布造粒,生产过程中添加部分氮素和钾素以及其他物质,再经干燥、筛分、冷却而得到PK复合肥产品,这是国内外各大化肥公司和大规模生产常采用的生产方法。
磷酸可由硫酸分解磷矿制取,有条件时也可直接外购商品磷酸,以减少投资和简化产环节。
该法的优点是:既可生产磷酸铵也可生产NPK复合肥,同时也充分利用了酸、氨的中和热,蒸发物料水份,降低造粒水含量和干燥负荷,减少能耗,生产规模大,生产成本较低,产品质量好,产品强度较高。
由于通常需配套建设磷酸装置及硫酸装置,建设不仅投资大,周期长,而且涉及磷、硫资源的供应和众多的环境保护问题(如磷石膏、氟、酸沫、酸泥等),一般较适用于在磷矿加工基地和较大规模生产、产品品数不多的情况。
如以外购的商品磷酸为原料,则目前稳定的来源和运输问题及价格因素是不得不考虑的,近年来,由于我国磷酸工业技术和装备水平的提高,湿法磷酸作为商品进入市场有了良好的条件,在有资源和条件的地区建立磷酸基地,以商品磷酸满足其它地区发展高浓度磷复肥的需要,正在形成一种新的思路和途径,市场需求必将促进这一行业发展,也必将解决众多地区原料磷酸的需求问题。
拥有该种生产技术的外国公司主要有挪威的norsk hydro、西班牙incro、espindsea、法国的AZF、KT、美国的Davy/TVA等。
国内的主要生产厂家有:中阿化肥有限公司、江西贵溪化肥厂、云南云峰化工公司、南京南化磷肥厂、大连化工厂、金昌化工公司、广西鹿寨磷肥厂等。
拥有相近于该种生产技术的国内企业主要有山东的红日集团、四川成都科技大学、上海化工研究院等。
2.固体团粒法以单体基础肥料如:尿素、硝铵、氯化铵、硫铵、磷铵(磷酸一铵、磷酸二铵、重钙、普钙)、氯化钾(硫酸钾)等为原料,经粉碎至一定细度后,物料在转鼓造粒机(或园盘造粒机)的滚动床内通过增湿、加热进行团聚造粒,在成粒过程中,有条件的还可以在转鼓造粒机加入少量的磷酸和氨,以改善成粒条件。
化肥厂生产过程及工艺流程

化肥厂生产过程及工艺流程煤制合成氨、尿素C+ 0.5 O2 →COC+ O2 →CO2CO + H2O→CO2+ H2H2+N2→NH3CO2 + 2NH3 →CO (NH2)21 全厂流程简介2 过程工艺描述(1)水煤浆气化制合成气装置由水煤浆制备工序来的水煤浆送入煤浆槽储存待用。
浓度约为63%的水煤浆通过煤浆给料泵加压输送到气化炉顶部工艺烧嘴,并与空分装置来的纯氧分别进入气化炉在6.5MPa(G),约1400℃工艺条件下,水煤浆与纯氧进行部分氧化反应,生成粗合成气。
反应后的粗合成气和溶渣进入气化炉下部的激冷室。
在激冷室中,粗合成气经冷却、洗涤,将粗合成气中的大部分碳黑洗去,并和粗渣分开。
出激冷室的粗合成气直接进入文丘里洗涤器和碳洗塔进一步洗涤,除去粗合成气中残留的碳黑,然后将水蒸汽/干气比约1.3~1.5的合成气送至变换工序。
溶渣被激冷室底部通过破渣机进入锁斗,定期排入渣池,渣池设有捞渣机将粗渣捞出,装车运往园区免烧砖项目。
渣池中含细渣的灰水通过渣池泵送至真空闪蒸器。
碳洗塔的液位通过控制进入塔内的灰水量来维持,碳洗塔内的黑水分两股排出,一股黑水去高压闪蒸器;另一股由灰水循环泵送至气化炉也进入高压闪蒸器,黑水经减压,闪蒸出黑水中溶解的气体并通过变换冷凝液加热器回收闪蒸汽的热量,通过高压闪蒸分离器,闪蒸出的气体至变换或火炬,水送入脱氧水槽。
(2)净化装置a. 变换变换工序主要反应式为:COS+H2O——CO2+H2S+QCO+H2O——CO2+H2+Q由气化送来粗煤气经煤气水分离器分离掉少量的冷凝液及灰尘后,经中温换热器温度升高至250℃,进第一中温变换炉。
第一中温变换炉分上、下两段,炉内装有两段三层耐硫变换触媒,层间配有煤气激冷管线调温,出第一中温变换炉变换气CO含量为24%(干),温度为420℃左右。
变换气经中温换热器降温后进淬冷器,用本工段产生的高温冷凝液淬冷至240℃,然后进入第二中温变换炉,炉内装有两段耐硫变换触媒,出口变换气CO浓度为4.0%(干),温度为358℃左右,进入中变废热锅炉,产生1.0MPa(G)的低压蒸汽,使变换气温度降温进入低温变换炉,低温变换炉装两段耐硫变换触媒,出口变换气CO浓度为1.0%(干),温度升至为222℃左右,进入低变废热锅炉,产生0.4MPa(G)的低压蒸汽,变换气温度降至163℃;经第一水分离器分离出冷凝液后的变换气进入锅炉给水加热器,温度降至140℃,然后进入脱盐水加热器温度降至70℃、进变换气水冷器温度降至为40℃,进水洗塔,在塔底进行气液分离后,气体经塔顶40℃洗涤水洗涤除去NH3后送至甲醇洗工段。
化肥厂尿素装置生产原理及工艺流程

化肥厂尿素装置生产原理及工艺流程一、引言化肥厂尿素装置是化肥生产过程中的重要设备,用于生产尿素肥料。
本文将介绍尿素装置的生产原理和工艺流程。
二、尿素的生产原理尿素是一种氮肥,具有高氮含量、溶解性好等特点,被广泛应用于农业生产中。
尿素的生产原理主要包括合成部分和后处理部分。
2.1 合成部分尿素的合成是通过将氨气和二氧化碳在一定条件下反应得到的。
具体的反应方程式如下:2NH3 + CO2 -> NH2CONH2 + H2O上述反应是在一定压力和温度下进行的。
通常情况下,尿素的合成压力为100至180巴,温度为130至160摄氏度。
2.2 后处理部分尿素合成反应得到的产物中还包含着一些杂质,需要经过后处理步骤进行处理。
后处理主要包括脱水和浓缩两个步骤。
脱水是指将产物中的水分去除,以提高尿素肥料的含氮量和稳定性。
浓缩则是将产物浓缩,以便进行后续的干燥和颗粒化处理。
三、尿素装置的工艺流程尿素装置的工艺流程主要包括原料准备、合成反应、脱水、浓缩、干燥和颗粒化等步骤。
3.1 原料准备尿素的主要原料为氨气和二氧化碳。
氨气一般通过蒸发液氨或氨气合成装置进行提供,而二氧化碳可通过燃煤锅炉烟气或气化炉烟气提供。
3.2 合成反应合成反应是将氨气和二氧化碳在合成反应器中进行反应。
反应器内通常采用催化剂来加速反应速率,保证反应的高效进行。
3.3 脱水合成反应后得到的产物中含有一定的水分,在脱水塔中通过高温条件蒸发除去水分,以提高尿素肥料的纯度。
3.4 浓缩脱水后的产物含有浓度较低的尿素,为了提高尿素的浓度,需要经过浓缩塔进行浓缩处理。
3.5 干燥浓缩后的产物通过干燥器进行干燥,以去除水分和其他杂质。
干燥后的尿素颗粒具有较高的纯度和稳定性。
3.6 颗粒化干燥后的尿素通过颗粒化机进行颗粒化处理,使其形成均匀的粒状,便于储存和施用。
四、总结尿素装置是化肥厂生产尿素肥料的重要设备,其生产原理主要包括合成和后处理两个部分。
工艺流程包括原料准备、合成反应、脱水、浓缩、干燥和颗粒化等步骤。
化肥厂工艺反应原理简介.

化肥厂生产装置工艺反应原理简介化肥厂技术科2008-12-15第一章合成氨装置工艺原理1、合成氨工艺反应机理化肥厂合成氨装置工艺采用烃类蒸汽转化法。
整套工艺共有七个主反应,按照工艺流程顺序分别为钴钼加氢反应、氧化锌脱硫反应、转化反应(包括一段转化和二段转化反应)、变换反应(包括高温变换和低温变换反应)、脱碳反应、甲烷化反应、合成氨反应。
合成氨装置的原料为油田伴生气、空气和水蒸气,这三种原料经过上述七个主反应最后生成产品氨。
注: ①第三步转化反应分为一段和二段转化反应的原因是:如果要求在一段转化反应就使原料气中的甲烷完全转化为氢气、一氧化碳和二氧化碳,则必须要加大水碳比或者提高温度。
前一种方法必将导致耗用过多的水蒸气,而后一种方法对于采用外加热方式的一段反应炉来说对设备材质的要求也会更高。
因此在自热式的二段转化炉内通过气体自身燃烧放热,只需要在炉内做一层耐火衬里就能既解决高温对设备材料的要求又能增加反应温度,可使原料气中的甲烷完全转化,同时二段转化工段在加入空气助燃的同时又加入了合成氨反应所需的氮气。
②第四步变换反应分为高温变换和低温变换反应的原因是:采用Fe3O4催化剂的高变反应只能使96-98%的一氧化碳转化为二氧化碳,要想使一氧化碳含量降低到0.2-0.5%的指标范围内,只有在单质铜催化剂存在下的低温变换反应才能达到,如果在高温变换反应中应用单质铜催化剂,由于单质铜催化剂较昂贵会增加催化剂的使用成本,而且由于单质铜催化剂的作用温度低将导致废热的利用价值降低。
2、工艺流程简述油田伴生气加压至4.05MPa,经预热升温到371℃在脱硫工序脱硫后与水蒸汽混合,进入一段转化炉进行转化制H2反应,一段转化炉出来的转化气进入二段转化炉,在此引入空气,转化气在二段炉内燃烧掉一部分H2,放出热量以供进一步转化,同时获得N2。
二段转化气经余热回收后,进入变换系统,气体中的CO与水蒸汽反应,生成CO2和H2,从变换系统出来的气体经脱碳、甲烷化后为合成氨提供纯净的氢氮混合气,氢氮混合气经压缩至14.0MPa,送入合成塔进行合成氨反应。
初二物理化肥生产工艺流程分析

初二物理化肥生产工艺流程分析物理化肥是指通过物理方法,将天然气、煤炭、磷矿石等原材料转化为适合农作物生长的肥料。
其生产过程需要经历多个工艺环节,包括原材料处理、反应转化、成品提取和包装等。
本文将对初二物理化肥生产工艺流程进行详细分析。
一、原材料处理物理化肥的主要原材料包括天然气、煤炭、磷矿石和硫磺等。
在生产过程中,首先需要对这些原材料进行处理。
比如,如果使用天然气作为原材料,需要经过脱硫、除尘等工艺步骤,以去除其中的杂质物质,确保生产的物理化肥符合质量标准。
二、反应转化经过原材料处理后,进入反应转化阶段。
不同种类的物理化肥生产有不同的转化反应过程。
以磷矿石为例,其制备过程中最关键的反应是磷酸盐的溶解和磷酸二氢铵的生成。
该反应需在特定的温度和压力条件下进行,以确保高效率的转化率。
同时,在反应过程中要对温度、压力、反应时间等参数进行严格控制,以保证反应的稳定性和产物质量。
三、成品提取反应转化完成后,需要对产物进行提取。
这一步骤主要包括过滤、结晶、干燥等操作。
过滤是将反应液中的固体磷酸二氢铵分离出来,结晶则是通过控制温度和浓度来使化肥成分逐渐形成晶体。
最后,通过干燥操作将结晶物质中的水分去除,以获得细小颗粒并便于包装和储存。
四、包装经过成品提取后,物理化肥需要进行包装。
包装过程通常包括称量、封装和贴标等环节。
称量是为了确保每包物理化肥的重量标准化,封装则是将化肥装入袋中,并密封保鲜。
最后,贴标环节负责为每个包装袋标识产品的名称、规格、生产日期等重要信息,以方便消费者购买和使用。
综上所述,初二物理化肥生产工艺流程包括原材料处理、反应转化、成品提取和包装等环节。
通过这些工艺步骤的有序进行,我们可以获得高质量的物理化肥产品,以满足农业生产的需求。
随着科技的不断进步,物理化肥的生产工艺也在不断创新和改进,以提高生产效率和产品质量。
相信通过全社会的努力,我们能够不断完善物理化肥生产工艺,为农业发展做出更大贡献。
化肥厂原理

化肥厂原理
化肥厂原理是指利用化学反应制造化肥的一种工艺。
化肥是指用于促进植物生长和提高农作物产量的一种物质。
化肥厂主要通过以下原理实现化肥的制造:
1. 合成气制氨法:该原理是将天然气、石油或煤炭等碳源经过蒸汽重整或气化制取合成气,再将合成气与氮气经过反应,生成氨气。
氨气是制造氮肥的关键原料。
2. 氨的硫酸化:将氨气与硫酸反应生成硫酸铵。
硫酸铵是常见的氮肥之一,含有丰富的氮元素,并且具有较高的溶解度,便于植物吸收。
3. 物理吸附法:该原理是利用吸附材料,如硅胶、活性炭、分子筛等,吸附空气中的氮气,通过压降或冷凝方法分离出氮气和其他杂质,从而制造高纯度的氮肥。
4. 化学反应法:采用化学反应制造氮肥,如尿素的合成。
尿素是一种高氮含量的氮肥,主要用于作物的迅速吸收和利用。
5. 植物养殖废弃物处理和转化:利用植物养殖废弃物的有机成分,通过发酵、厌氧处理等方法,将其转化为有机肥料。
有机肥料可提供植物所需的营养元素,同时改善土壤性质。
化肥厂的原理是基于以上几种方式进行制造,通过不同的反应过程和方法,可以制造出不同种类和用途的化肥,满足不同植物的需求。
化肥的制造需要严格控制反应条件、原料质量,以
及生产过程中的环保措施,以保证化肥质量的稳定和生产的可持续性。
肥料制造中的化学反应与反应机理
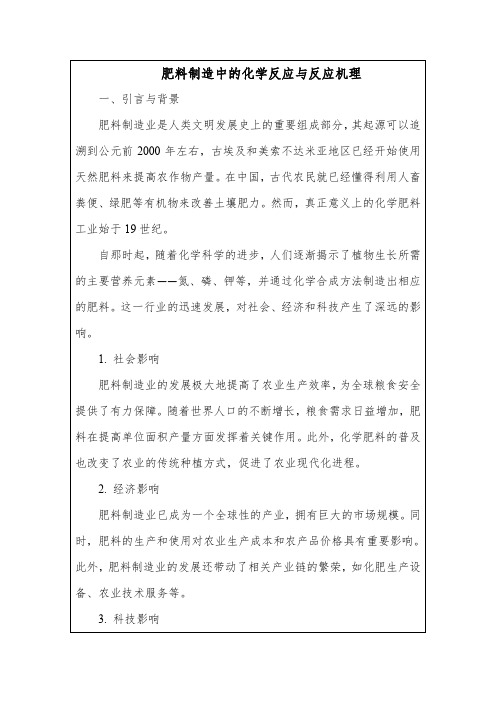
-价格战:虽然价格竞争能短期内提升市场份额,但可能导致利润下降和产品质量降低。
-差异化:通过产品创新、技术优势、品牌建设等手段,形成独特卖点,提高市场竞争力。
-市场集中:企业通过并购、联盟等方式,提高市场集中度,实现规模经济和成本优势。
五、行业挑战与应对策略
1.当前面临的挑战和问题
-技术瓶颈:肥料利用效率、环保性能、新产品研发等方面仍存在技术难题。
-案例二:一家专注于生物肥料的企业,利用基因工程技术研发出具有抗病、抗旱功能的新型微生物肥料,在市场上取得了良好反响。
3.失败案例
-案例一:某企业未经充分市场调研,盲目推出一款高端肥料,由于价格过高,市场接受度低,导致产品积压。
-案例二:一家企业在新产品推广过程中,忽视与农民的沟通,导致农民对新产品的使用方法掌握不足,影响作物产量,使产品信誉受损。
二、行业/领域的核心概念与分类
1.行业/领域核心概念
肥料制造业涉及的核心概念主要包括化学合成、植物营养学、土壤学和环境科学。化学合成是指通过一系列化学反应,将基础化工原料转化为含有植物所需营养元素的肥料产品。植物营养学关注的是植物对营养元素的需求及其在植物体内的循环利用。土壤学则研究肥料施入土壤后的转化、迁移和有效性。环境科学则着重于评估肥料使用对生态环境的影响。
2.行业分类与特征
肥料制造业可细分为氮肥、磷肥、钾肥和复合肥料等几个类别。
-氮肥:以氮元素为主要成分,包括尿素、铵态氮肥等,主要用于促进植物茎叶生长。
-磷肥:以磷元素为主要成分,如过磷酸钙、磷酸二铵等,对植物根系发育和果实成熟至关重要。
-钾肥:以钾元素为主要成分,如氯化钾、硫酸钾等,对提高植物抗病能力和调节水分平衡有显著作用。
-政策倡导重点:推动制定有利于行业可持续发展的政策,如税收优惠、研发补贴等。
化肥厂生产工艺

化肥厂生产工艺
化肥厂生产工艺是指用科学、系统的方法,将原材料经过一系列的物理、化学反应,转化成合格的化肥产品的工艺。
下面以尿素和复合肥为例,介绍一下化肥厂的生产工艺。
尿素的生产工艺一般分为脱气工艺和结晶工艺两个部分。
脱气工艺主要有两种方法,一种是挥发脱气法,一种是溶剂脱气法。
挥发脱气法是将尿素溶液在脱气塔中进行受热脱气,使溶液中的尿素脱水,生成氨基甲酸酯。
溶剂脱气法是在脱气塔中将尿素溶液加入溶剂,通过溶剂的挥发脱气,使尿素分解生成氨基甲酸酯。
结晶工艺是将脱气后的尿素氨基甲酸酯溶液进一步蒸发浓缩,达到结晶的浓度后,通过结晶器中的稀酸或稀碱溶液作用,使尿素结晶。
尿素结晶后经过分离、干燥等工序,最终得到合格的尿素产品。
复合肥的生产工艺主要包括配比、混合、造粒和包衣等工序。
配比是根据不同农作物的需求,确定配方比例,将不同种类的化肥原料按照一定比例混合到一起。
混合工序是通过搅拌设备将化肥原料均匀混合,以保证复合肥的均匀性和一致性。
造粒工序是将混合后的化肥原料通过造粒机进行造粒,形成颗粒状的复合肥。
最后,通过包衣工序,将复合肥颗粒表面包上滋养剂等物质,以提高肥料的利用率和效果。
此外,化肥厂的生产工艺还包括原材料的贮存和输送、废气的处理等环节。
原材料需要进行贮存和输送,以保证生产的连续性和稳定性。
废气处理是对化肥厂产生的废气进行处理,将其中的有害物质去除,以保护环境。
以上就是化肥厂生产尿素和复合肥的简单工艺流程介绍。
化肥厂的生产过程是一个复杂的系统工程,需要严格按照工艺流程进行操作,以确保生产的产品质量和生产效率。
化肥工艺

化肥工艺流程方框图
造气
半水煤气 湿法脱硫 焦炉气 经除焦油、苯、萘
合成1#、2#低压机
净化新中变
炼焦
合成3#、4#低压机
焦炉气
净化干法脱硫
产品氮气 产品氧压缩 空气 61或115压缩 空分装置
转化
121压缩 SVK压缩
空气
中变
碱洗气
氧化锌
氨合成
高压机
氢氮气 循环机
甲烷化
脱碳
NH3
循环氢 CO2 尿素 CO2压缩 钾碱液再生
3、硫磺回收
3-1、硫磺回收工艺,湿法脱硫氧化槽溢流出的 硫泡沫进入1#泡沫槽,定期排进压力输送槽,用 空气加压将硫泡沫送至2#泡沫槽,通过下料管进 入熔硫釜,在釜的上部被加热至60-90℃,硫泡 沫中的硫颗粒聚集变大沉于下釜,被分离的溶液 上升,从上釜的排液管回到地下池。当釜内的硫 积累超过釜内容积的1/2时,打开放硫阀放硫。 在原料充足的情况下,始终保持连续分离,连续 放硫,制成硫磺。
指标名称 焦炉煤气量 半水煤气量 净化前焦炉煤气含H2S 净化后焦炉煤气含H2S 净化前半水煤气含H2S 净化后半水煤气含H2S 碱耗 再生空气量 溶液温度 溶液循环量 ℃ m3/h ≤45 800 单位 m3/h m3/h g/m3 mg/m3 g/m3 mg/m3 Kg/t 设计值 13000 7000 ≤7 ≤20 ≤1 ≤20 现运行值 12000 11000 3—4 14-18 0.3--0.7 13-15 1.5-1.8 3000-3500 30-45 765
净化车间:主要对原料气(焦炉气、半水煤气) 中含有的甲烷、CO、CO2、及有机硫、无机硫等 有害气体成份进行脱除、变换、转化,以达到获 得质量符合要求的H2和N2,送往氨合成工序。 合成车间:将净化气在适当的温度、一定的压力 和催化剂作用下,合成氨。然后从新产生的气氨 中冷凝分离出来,成为液态氨,供尿素生产。同 时负责将系统贮罐气和吹除气中的氨及氢气进行 有效回收利用。 尿素车间:将前工序送来的CO2和液氨进行加工、 合成,将生成的尿液进行浓缩、造粒;未反应物 进行分解、吸收,达到全循环目的。
化肥生产工作原理

化肥生产工作原理化肥作为农业生产中重要的辅助物资,对提高农产品产量和改善农业生产质量起着至关重要的作用。
化肥的生产工作原理涉及到多个环节,包括原料采购、反应制剂、生产工艺、质量控制等方面。
本文将从这几个方面分析化肥生产的工作原理。
一、原料采购化肥生产的原料主要包括氮、磷、钾等元素的化合物。
这些原料可以从矿石、矿渣、尿素、硝酸铵等来源获取。
原料采购的关键在于确保原料的质量和供应的稳定性。
化肥生产企业需要与供应商建立长期稳定的合作关系,同时对原料进行严格的检验和把关,以确保化肥生产的质量和可持续发展。
二、反应制剂在化肥生产中,原料需要通过反应制剂的作用进行化学反应,生成可溶性的肥料物质。
通常,反应制剂是一种能够促进反应速度和提高反应产率的物质,可以是酸、碱、催化剂等。
反应制剂的选择需要根据原料的特性和生产工艺的要求来确定,以确保反应过程的高效性和产量的稳定性。
三、生产工艺化肥的生产工艺主要包括混合、颗粒化、干燥等环节。
首先,将原料按照一定比例混合,并添加适量的水分,形成均匀的混合物。
然后,将混合后的物料送入颗粒化设备,通过滚筒等方式将其制成一定大小的颗粒。
最后,将颗粒化后的物料进行干燥,以去除多余的水分,增加产品的稳定性和储存寿命。
四、质量控制化肥生产过程中,质量控制是一个关键的环节。
质量控制包括原料的检测、生产过程的监控和成品的质量评估。
化肥生产企业需要建立一套科学合理的质量控制体系,对原料进行全面的检验,对生产过程进行实时监控,并对成品进行严格的质量评估,以确保产品的合格率和质量稳定性。
总结化肥的生产工作原理包括原料采购、反应制剂、生产工艺和质量控制等环节。
通过合理的原料采购、科学的反应制剂配比、精细的生产工艺和严格的质量控制,可以保证化肥生产的质量和效益。
同时,化肥生产企业还需要关注环保问题,采取节能减排措施,致力于推动可持续发展的化肥生产。
希望本文能够对化肥生产工作原理有所了解,并为相关从业人员提供参考和借鉴。
尿素工艺流程和结论

化肥厂尿素生产工艺流程(co2汽提法)•第一步由氨与二氧化碳生成中间产物甲铵,其反应式为:2NH3(液)+CO2(气) NH2COONH4(液)+ 119.2KJ/molA•第二步由甲铵脱水生成尿素,其反应式为(合成尿素过程中的控制反应):NH2COONH4(液) CO(NH2)2(液)+H2O(液)- 15.5KJ/mol B•总的反应方程式:•2NH3(液)+CO2(气) CO(NH2)2(液)+H2O(液)+103.7KJ/mol•从气提塔201C底部出来的液体经减压进入精馏塔顶部,均匀地喷洒在精馏塔的填料层上,然后自上而下和上升的135℃分解气逆流接触,温度上升至120℃左右,尿液从301E底部送到底部和中部、顶部循环加热器,在此分别用高调水和0.6MPa蒸汽将其温度提高到约140℃,使甲铵再次发生分解。
•用精馏塔出口调节阀TIC301来调节进入顶部循环加热器的蒸汽压力,在循环分离段中气液相发生分离,气体通过精馏塔填料段进行热质交换后,从精馏塔301E塔顶出口管进入低甲冷,冷凝吸收。
•离开精馏塔分离段的尿液位液位调节阀LV301送至闪蒸槽,闪蒸槽301F真空度由HV701控制,闪蒸使尿液中部分氨、CO2、H2O挥发,尿液由135℃降至90~95℃,浓度增加到约72~74%,流入尿液小槽,闪蒸气相去闪蒸冷凝器冷凝。
•精馏气回流泵来回流液及工艺液在低甲冷进行浸没式冷凝吸收,为了移走冷凝热,低甲冷用低调水进行冷却,现低调水是由化水送来的脱盐水与系统换热后热脱盐水混合后温度控制在50~55℃,一部分热脱盐水送至电厂,出301C的汽液混合物进入低压液位槽进行气液分离,气相及回流冷气相同时进入鼓泡塔,经吸收塔给料泵打来的解吸液吸收后再进入常压吸收塔,液相返回氨水槽,气体至放空总管,循环气相管前设有吹扫蒸汽,以防此管线结晶。
循环系统甲铵液经甲铵泵加压至15MPa送至高压洗涤器作吸收剂。
.精馏塔的精馏过程•高压圈合成的合成液,经气提塔气提后,由气提塔出料调节阀压力由14.6MPa减压至0.25~0.3MPa,使气提液中的部分甲铵分解成为氨和二氧化碳气体。
复合肥的生产工艺介绍

复合肥的生产工艺介绍目前颗粒状复混肥料的生产方法主要有料浆法、固体团粒法、部分料浆法、融熔法等,下面对这几种典型的生产方法作以介绍。
1.料浆法以磷酸、氨为原料,利用中和器、管式反应器将中和料浆,在氨化粒化器中进行涂布造粒,生产过程中添加部分氮素和钾素以及其他物质,再经干燥、筛分、冷却而得到PK复合肥产品,这是国内外各大化肥公司和大规模生产常采用的生产方法。
磷酸可由硫酸分解磷矿制取,有条件时也可直接外购商品磷酸,以减少投资和简化产环节。
该法的优点是:既可生产磷酸铵也可生产NPK复合肥,同时也充分利用了酸、氨的中和热,蒸发物料水份,降低造粒水含量和干燥负荷,减少能耗,生产规模大,生产成本较低,产品质量好,产品强度较高。
由于通常需配套建设磷酸装置及硫酸装置,建设不仅投资大,周期长,而且涉及磷、硫资源的供应和众多的环境保护问题(如磷石膏、氟、酸沫、酸泥等),一般较适用于在磷矿加工基地和较大规模生产、产品品数不多的情况。
如以外购的商品磷酸为原料,则目前稳定的来源和运输问题及价格因素是不得不考虑的,近年来,由于我国磷酸工业技术和装备水平的提高,湿法磷酸作为商品进入市场有了良好的条件,在有资源和条件的地区建立磷酸基地,以商品磷酸满足其它地区发展高浓度磷复肥的需要,正在形成一种新的思路和途径,市场需求必将促进这一行业发展,也必将解决众多地区原料磷酸的需求问题。
拥有该种生产技术的外国公司主要有挪威的norsk hydro、西班牙incro、espindsea、法国的AZF、KT、美国的Davy/TVA等。
国内的主要生产厂家有:中阿化肥有限公司、江西贵溪化肥厂、云南云峰化工公司、南京南化磷肥厂、大连化工厂、金昌化工公司、广西鹿寨磷肥厂等。
拥有相近于该种生产技术的国内企业主要有山东的红日集团、四川成都科技大学、上海化工研究院等。
2.固体团粒法以单体基础肥料如:尿素、硝铵、氯化铵、硫铵、磷铵(磷酸一铵、磷酸二铵、重钙、普钙)、氯化钾(硫酸钾)等为原料,经粉碎至一定细度后,物料在转鼓造粒机(或园盘造粒机)的滚动床内通过增湿、加热进行团聚造粒,在成粒过程中,有条件的还可以在转鼓造粒机加入少量的磷酸和氨,以改善成粒条件。
工业合成氨原理
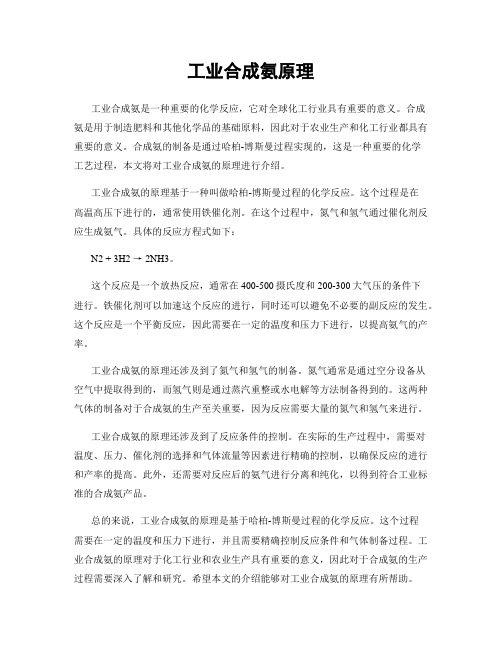
工业合成氨原理工业合成氨是一种重要的化学反应,它对全球化工行业具有重要的意义。
合成氨是用于制造肥料和其他化学品的基础原料,因此对于农业生产和化工行业都具有重要的意义。
合成氨的制备是通过哈柏-博斯曼过程实现的,这是一种重要的化学工艺过程,本文将对工业合成氨的原理进行介绍。
工业合成氨的原理基于一种叫做哈柏-博斯曼过程的化学反应。
这个过程是在高温高压下进行的,通常使用铁催化剂。
在这个过程中,氮气和氢气通过催化剂反应生成氨气。
具体的反应方程式如下:N2 + 3H2 → 2NH3。
这个反应是一个放热反应,通常在400-500摄氏度和200-300大气压的条件下进行。
铁催化剂可以加速这个反应的进行,同时还可以避免不必要的副反应的发生。
这个反应是一个平衡反应,因此需要在一定的温度和压力下进行,以提高氨气的产率。
工业合成氨的原理还涉及到了氮气和氢气的制备。
氮气通常是通过空分设备从空气中提取得到的,而氢气则是通过蒸汽重整或水电解等方法制备得到的。
这两种气体的制备对于合成氨的生产至关重要,因为反应需要大量的氮气和氢气来进行。
工业合成氨的原理还涉及到了反应条件的控制。
在实际的生产过程中,需要对温度、压力、催化剂的选择和气体流量等因素进行精确的控制,以确保反应的进行和产率的提高。
此外,还需要对反应后的氨气进行分离和纯化,以得到符合工业标准的合成氨产品。
总的来说,工业合成氨的原理是基于哈柏-博斯曼过程的化学反应。
这个过程需要在一定的温度和压力下进行,并且需要精确控制反应条件和气体制备过程。
工业合成氨的原理对于化工行业和农业生产具有重要的意义,因此对于合成氨的生产过程需要深入了解和研究。
希望本文的介绍能够对工业合成氨的原理有所帮助。
化肥工艺技术
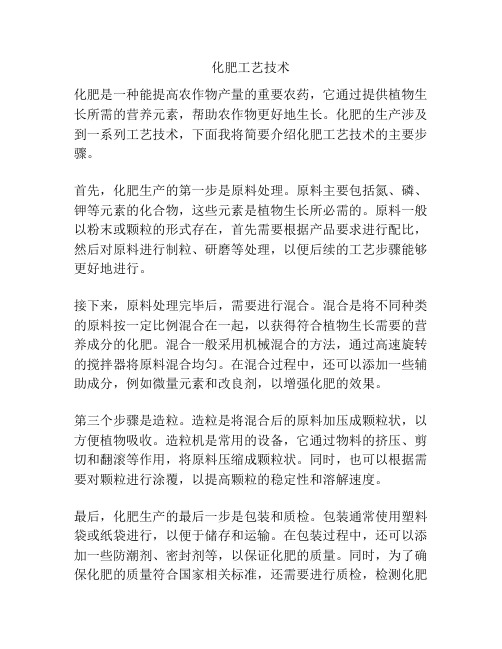
化肥工艺技术化肥是一种能提高农作物产量的重要农药,它通过提供植物生长所需的营养元素,帮助农作物更好地生长。
化肥的生产涉及到一系列工艺技术,下面我将简要介绍化肥工艺技术的主要步骤。
首先,化肥生产的第一步是原料处理。
原料主要包括氮、磷、钾等元素的化合物,这些元素是植物生长所必需的。
原料一般以粉末或颗粒的形式存在,首先需要根据产品要求进行配比,然后对原料进行制粒、研磨等处理,以便后续的工艺步骤能够更好地进行。
接下来,原料处理完毕后,需要进行混合。
混合是将不同种类的原料按一定比例混合在一起,以获得符合植物生长需要的营养成分的化肥。
混合一般采用机械混合的方法,通过高速旋转的搅拌器将原料混合均匀。
在混合过程中,还可以添加一些辅助成分,例如微量元素和改良剂,以增强化肥的效果。
第三个步骤是造粒。
造粒是将混合后的原料加压成颗粒状,以方便植物吸收。
造粒机是常用的设备,它通过物料的挤压、剪切和翻滚等作用,将原料压缩成颗粒状。
同时,也可以根据需要对颗粒进行涂覆,以提高颗粒的稳定性和溶解速度。
最后,化肥生产的最后一步是包装和质检。
包装通常使用塑料袋或纸袋进行,以便于储存和运输。
在包装过程中,还可以添加一些防潮剂、密封剂等,以保证化肥的质量。
同时,为了确保化肥的质量符合国家相关标准,还需要进行质检,检测化肥的主要成分、含量和纯度等。
总的来说,化肥工艺技术是一个复杂的过程,需要经过多个步骤才能最终制成优质的化肥产品。
每个步骤都需要严格控制,以确保化肥的成分、含量和质量符合要求。
随着农作物需求的增加,化肥工艺技术也在不断创新发展,以提高化肥的效果和减少对环境的影响。
希望通过不断研究和改进,能够生产出更高效、环保的化肥产品,为农业生产做出更大的贡献。
- 1、下载文档前请自行甄别文档内容的完整性,平台不提供额外的编辑、内容补充、找答案等附加服务。
- 2、"仅部分预览"的文档,不可在线预览部分如存在完整性等问题,可反馈申请退款(可完整预览的文档不适用该条件!)。
- 3、如文档侵犯您的权益,请联系客服反馈,我们会尽快为您处理(人工客服工作时间:9:00-18:30)。
化肥厂生产装置工艺反应原理简介
化肥厂技术科
2008-12-15
第一章合成氨装置工艺原理
1、合成氨工艺反应机理
化肥厂合成氨装置工艺采用烃类蒸汽转化法。
整套工艺共有七个主反应,按照工艺流程顺序分别为钴钼加氢反应、氧化锌脱硫反应、转化反应(包括一段转化和二段转化反应)、变换反应(包括高温变换和低温变换反应)、脱碳反应、甲烷化反应、合成氨反应。
合成氨装置的原料为油田伴生气、空气和水蒸气,这三种原料经过上述七个主反应最后生成产品氨。
合成氨工艺主反应汇总表(按反应发生的前后顺序排列)
注: ①第三步转化反应分为一段和二段转化反应的原因是:如果要求在一段转化反应就使原料气中的甲烷完全转化为氢气、一氧化碳和二氧化碳,则必须要加大水碳比或者提高温度。
前一种方法必将导致耗用过多的水蒸气,而后一种方法对于采用外加热方式的一段反应炉来说对设备材质的要求也会更高。
因此在自热式的二段转化炉内通过气体自身燃烧放热,只需要在炉内做一层耐火衬里就能既解决高温对设备材料的要求又能增加反应温度,可使原
料气中的甲烷完全转化,同时二段转化工段在加入空气助燃的同时又加入了合成氨反应所需的氮气。
②第四步变换反应分为高温变换和低温变换反应的原因是:采用Fe3O4催化剂的高变反应只能使96-98%的一氧化碳转化为二氧化碳,要想使一氧化碳含量降低到的指标范围内,只有在单质铜催化剂存在下的低温变换反应才能达到,如果在高温变换反应中应用单质铜催化剂,由于单质铜催化剂较昂贵会增加催化剂的使用成本,而且由于单质铜催化剂的作用温度低将导致废热的利用价值降低。
2、工艺流程简述
油田伴生气加压至,经预热升温到371℃在脱硫工序脱硫后与水蒸汽混合,进入一段转化炉进行转化制H2反应,一段转化炉出来的转化气进入二段转化炉,在此引入空气,转化气在二段炉内燃烧掉一部分H2,放出热量以供进一步转化,同时获得N2。
二段转化气经余热回收后,进入变换系统,气体中的CO与水蒸汽反应,生成CO2和H2,从变换系统出来的气体经脱碳、甲烷化后为合成氨提供纯净的氢氮混合气,氢氮混合气经压缩至,送入合成塔进行合成氨反应。
油田气
脱硫
二段转化
一段转化
高变 低变
去高变
产品氨
甲烷化
氨合
成
来自二段转化
合成氨装置工艺流程简图
CoMo
ZnO
ZnO
一段炉
二段炉
吸收
再
生
甲烷化
高温变
低温变
原料气压缩机
加氢
氨分
离
合成氨 产品CO
蒸气 空气
脱碳
第二章尿素装置工艺原理
1、尿素工艺反应机理
化肥厂尿素装置采用二氧化碳汽提工艺生产尿素产品。
尿素装置的原料为合成氨装置的产品液氨和二氧化碳。
整套尿素工艺共有二个主反应,即液态NH3和CO2气生成氨基甲酸铵反应和氨基甲酸铵脱水生成尿素反应。
原料氨和二氧化碳经过上述两个主反应后生成尿素装置产品尿素。
尿素工艺主反应汇总表(按反应顺序排列)
2、二氧化碳汽提工艺原理
二氧化碳汽提法分离未反应物,是将合成反应液(包括尿素、氨基甲酸铵、氨和水)在与尿素合成过程相同的压力及较高的温度下与汽提气CO2逆流接触,将氨基甲酸铵分解成NH3和CO2并从合成液中分离出来。
甲铵分解反应式:
NH2COONH4 (液)= 2NH3 (气)+ CO2(气)
由反应方程式可以看出当用纯CO2气进行汽提时,气相NH3的浓度几乎等于零,所以在任何压力下甲铵都能够完全分解。
这也是为什么汽提分解甲铵可
以在与合成尿素压力相同的条件下进行的原因。
3、工艺流程简述
尿素生产所需的原料液氨和CO2均来自化肥厂合成氨装置,两股物料经加压后送高压系统反应生成尿素溶液,然后尿素溶液经过中压精馏、低压精馏以及蒸发系统提浓后送往造粒塔顶部的造粒喷头进行喷淋造粒,在造粒塔底部形成尿素颗粒,最后送往成品装置进行包装成为成品尿素出厂。
尿素工艺流程简图
二氧化碳
CO2
气
提
塔高
压
甲
铵
冷
凝
低
压
系
闪
蒸
尿液槽
蒸
发
系
统
合
成
塔
吸
收
洗
涤
造
粒
塔
液氨
中
压
系
统氨泵
二氧化碳压缩
产品尿素放空
4 、长效尿素所用SOD M添加剂的作用机理
SOD M是模拟SOD酶的简称,是由高纯氨基酸为原料合成。
1)产品物性:
PH值:呈中性至微碱性;
热稳定性:≥250℃;在250℃以下不挥发、不分解;
平均分子量:M:7000-8000;
SOD M产品在室温下溶于水,与纯水制成浓度为30%的制剂;SOD M产品添加进尿素后,尿素的颜色变为淡黄色;SOD M产品在尿素装置生产情况下对生产设备不具备腐蚀作用。
在尿素产品的生产过程中,添加SOD M 制剂能够增加农作物产量,改进农作物产品质量,提高农作物抗逆性,减少尿素的使用量。
2)SOD M加入的工艺流程
在配药槽内添加30%浓度的成品SOD M制剂,使其充分溶解混合均匀,然后用计量泵经过流量计计量、手动调节后送入303-F储槽中,经过303-J尿液泵送入蒸发系统造粒。
第三章水汽装置工艺原理
水气装置有四个部分组成,即预处理装置、脱盐装置、循环水装置、快锅装置。
下面分别对这四个装置的工艺原理进行阐述。
1、预处理装置
预处理装置采用石灰软化法对升压站来水进行处理,所加药剂有三种,按加药顺序为氯气、硫酸亚铁和石灰,加药剂地点为澄清池,源水经过预处理装置后OH- 指标为~l,浊度≤12mg/l。
下面以表格的形式对加药的目的和反应机理进行阐述。
2、脱盐装置
脱盐装置采用的是化学除盐,它主要是靠阴阳离子交换剂,除去水中的盐份。
目前脱盐装置有三个系列,每个系列均由阳床、阴床和混床组成。
脱盐装置的源水主要是合成工艺冷凝液、尿素蒸汽冷凝液和尿素水解水,源水经过脱盐装置后生产出较纯的脱盐水。
下面以表格的方式阐述其工艺原理。
脱盐装置反应机理汇总表
3、循环水装置
循环水装置主要是对合成、尿素和橡胶装置的循环水进行冷却、过滤和稳定处理,然后把处理后的循环水送回合成、尿素和橡胶装置循环使用。
循环水装置工艺较为简单,在循环水处理过程中需要在水质稳定处理部分加入两种药剂,即阻垢-缓蚀剂和杀菌剂。
下面就这两种药剂的作用机理进行阐述。
①阻垢-缓蚀剂
循环水装置使用的阻垢-缓蚀剂HC-565A为有机磷配方,它可以提高结垢物质微粒表面电荷密度,增大排斥力,降低结晶速度,使结晶体结构畸变而失去矫健作用,从而不致结垢,还可以和沉淀在管壁上的胶体结合或与Ca2+、Fe2+等形成络合物,然后把已结成的水垢分散到水中,另外,药剂含Zn2+,能与金属表面形成保护膜,起控制腐蚀的作用。
②杀菌剂
循环水装置的杀菌剂有氧化性和非氧化性杀菌剂两种,其中氯和优氯净属于氧化性杀菌剂,HC-902和GSP-222属于非氧化性杀菌剂。
反应机理
氯进入水中,水解生成盐酸和次氯酸,次氯酸在水中发生电离,生成H+和OCl-两种离子。
次氯酸是一种强氧化剂。
反应方程式如下:
Cl2+H2O → HClO+HCl
HClO → H++OCl-
氯不但有杀菌效果,还是一种强氧化剂,可以与水中的氨反应,减少氨转化为亚硝酸根。
方应方程式如下:
NH3+ HClO → NH2Cl+ H2O (PH:>)
NH3+ 2HClO → NHCl2+ 2H2O (PH: 5~)
NH3+ 3HClO → NCl3+ 3H2O (PH: <)
4、快锅装置
快锅装置主要是给生产装置提供动力蒸气,为了保证锅炉不结垢需要在锅炉中投加药剂以去除水中的钙离子和调整PH值,所用药剂为磷酸三钠。
反应机理
水中加入磷酸三钠,使炉水中维持一定量的磷酸根,由于锅炉处于沸腾状态,且碱性较强, Ca2+与磷酸根会发生如下反应:
10 Ca2+ + 6PO43- + 2OH- = Ca10OH2(PO4)6
第四章供水装置
供水装置共有八个部分组成,分别为升压站、热水站、换热站、生活水场、空压站、外网、污水泵房、返洗排泥水回收装置。
除生活水场外其它部分工艺简单,因此本章仅对生活水场工艺原理进行阐述。
生活水场将红旗泡水库送来的源水进行处理,为化肥厂和卧里屯居民提供优质的生活用水。
整套给水处理装置由常规处理和深度处理两部分工艺系统组成。
(1)常规处理
常规处理工艺包括加药、混凝、沉淀、气浮、过滤和消毒。
(2)深度处理
深度处理包括臭氧氧化、活性炭过滤和后砂过滤三部分。
生活水场所用药剂有聚合铝、氯气、活性炭和滤料。
注:如果需要进一步了解有关化肥厂生产装置工艺的知识,合成氨工艺知识可以查询大连工学院袁一、曾宪龙编写的《大型氨厂合成氨生产工艺》一书;尿素工艺知识可以查询化学工业出版社出版的《氮肥工艺设计手册(尿素)》一书。
(技术科可以提供这两本教材)。