渗碳压淬件常见问题及分析共20页
齿轮渗碳加工常见缺陷的原因分析及预防措施
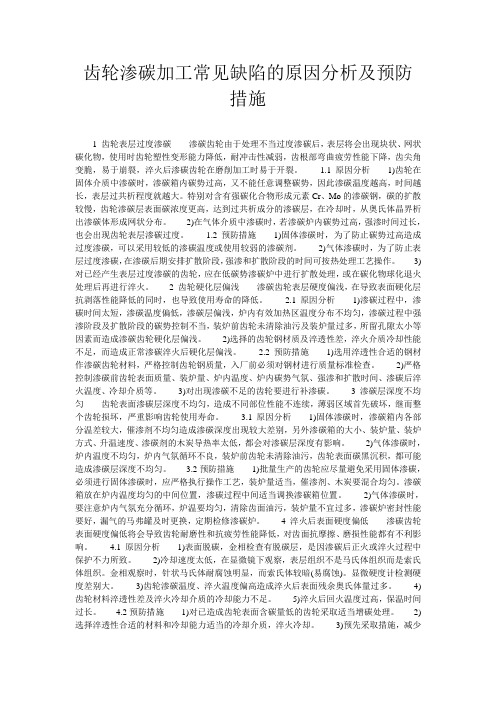
齿轮渗碳加工常见缺陷的原因分析及预防措施1 齿轮表层过度渗碳渗碳齿轮由于处理不当过度渗碳后,表层将会出现块状、网状碳化物,使用时齿轮塑性变形能力降低,耐冲击性减弱,齿根部弯曲疲劳性能下降,齿尖角变脆,易于崩裂,淬火后渗碳齿轮在磨削加工时易于开裂。
1.1原因分析1)齿轮在固体介质中渗碳时,渗碳箱内碳势过高,又不能任意调整碳势,因此渗碳温度越高,时间越长,表层过共析程度就越大。
特别对含有强碳化合物形成元素Cr、Mo的渗碳钢,碳的扩散较慢,齿轮渗碳层表面碳浓度更高,达到过共析成分的渗碳层,在冷却时,从奥氏体晶界析出渗碳体形成网状分布。
2)在气体介质中渗碳时,若渗碳炉内碳势过高,强渗时间过长,也会出现齿轮表层渗碳过度。
1.2预防措施1)固体渗碳时,为了防止碳势过高造成过度渗碳,可以采用较低的渗碳温度或使用较弱的渗碳剂。
2)气体渗碳时,为了防止表层过度渗碳,在渗碳后期安排扩散阶段,强渗和扩散阶段的时间可按热处理工艺操作。
3)对已经产生表层过度渗碳的齿轮,应在低碳势渗碳炉中进行扩散处理,或在碳化物球化退火处理后再进行淬火。
2 齿轮硬化层偏浅渗碳齿轮表层硬度偏浅,在导致表面硬化层抗剥落性能降低的同时,也导致使用寿命的降低。
2.1原因分析1)渗碳过程中,渗碳时间太短,渗碳温度偏低,渗碳层偏浅,炉内有效加热区温度分布不均匀,渗碳过程中强渗阶段及扩散阶段的碳势控制不当,装炉前齿轮未清除油污及装炉量过多,所留孔隙太小等因素而造成渗碳齿轮硬化层偏浅。
2)选择的齿轮钢材质及淬透性差,淬火介质冷却性能不足,而造成正常渗碳淬火后硬化层偏浅。
2.2预防措施1)选用淬透性合适的钢材作渗碳齿轮材料,严格控制齿轮钢质量,入厂前必须对钢材进行质量标准检查。
2)严格控制渗碳前齿轮表面质量、装炉量、炉内温度、炉内碳势气氛、强渗和扩散时间、渗碳后淬火温度、冷却介质等。
3)对出现渗碳不足的齿轮要进行补渗碳。
3 渗碳层深度不均匀齿轮表面渗碳层深度不均匀,造成不同部位性能不连续,薄弱区域首先破坏,继而整个齿轮损坏,严重影响齿轮使用寿命。
渗碳淬火质量缺陷分析

齿轮渗碳后淬火的质量分析摘要:通过对齿轮渗碳淬火后出现质量问题的分析和处理,论述了齿轮淬火产生缺陷的原因,提出了控制淬火过程和合理选用淬火介质应该注意的一些问题。
1 齿轮渗碳淬火常见质量问题(1)淬火后硬度不足、硬度分布不均匀、硬化深度不够;(2)淬火后心部硬度过高;(3)淬火变形超差;(4)淬火开裂;(5)油淬后表面光亮度不够。
这类质量问题的出现往往与齿轮的材质、前处理、淬火加热、渗碳碳势和淬火冷却有关。
在排除材质、前处理和加热渗碳中的问题后,淬火介质及相关技术的作用就特别突出了。
近年来国外对淬火冷却问题的研究证明,它是提高热处理质量最值得注意的问题。
渗碳齿轮淬火常用油作冷却介质。
因此,下面将首先分析齿轮淬火产生质量问题与淬火介质特性和用法的关系,并指出了淬火介质冷却速度的特点。
最后介绍了常用淬火介质的特点和选用时的注意事项。
1.1 硬度不足与硬化层深度不够淬火冷却速度偏低是造成齿轮淬火硬度不足、硬度不均和硬化深度不够的原因,冷却偏低又可以分为高温阶段冷速不足、中低温阶段冷速不足以及低温阶段冷速不足等情况。
如对于中小齿轮,淬火硬度不足往往是中高温阶段冷速不足所致,而模数大的齿轮要求较深淬硬层时,提高低温冷却速度就非常必要了。
对于淬火用油,一般说,油的蒸气膜阶段短、中温冷速快、低温冷却速度快,往往能获得高而且均匀的淬火硬度和足够的淬硬深度。
工件装挂方式对淬火冷却效果也有明显影响。
要使淬火油流动通畅,并配备和使用好搅拌装置,才能得到更好的冷却效果。
提高淬火介质的低温冷却速度,可以增大淬硬层深度。
在渗层碳浓度分布相同的情况下,采用低温冷却速度高的淬火油,往往获得更深的淬火硬化层,因此,采用冷却速度快的淬火油,缩短渗碳时间,也能获得要求的淬硬层深度。
要求的渗碳淬硬层深度越大,这种方法缩短渗碳时间的效果越明显。
1.2 淬火后心部硬度过高这类问题主要与原材料淬透性、所选淬火油冷速过快或其低温冷却速度过高有关。
经验分享:差速器齿轮渗碳淬火缺陷原因分析及对策

差速器齿轮渗碳淬火的质量缺陷大致可分为:外观缺陷(氧化、锈蚀),硬度、有效硬化层不合格(硬度高、硬度低、硬度不均匀,有效硬化层深、有效硬化层浅),金相组织缺陷(马氏体、碳化物、心部组织级别超标、表层非马超标),热处理变形(缩孔、锥度、圆度及畸变),下面就齿轮渗碳淬火生产中常见的质量缺陷,进行影响因素分析及补救对策实施阐述。
一、外观缺陷(1)表面氧化产生原因可能是热处理炉密封差而导致漏气,另外还有可能是渗碳介质纯度不够(含有水分)。
防范措施即为检查炉子密封性和提高渗碳介质纯度。
(2)表面锈蚀、污物、金属瘤产生原因可能是进炉前零件没有彻底清洗干净,热处理前机加工时切削液不合格,没有清洗干净。
零件表面沾有碎切屑,热处理加热过程中熔化粘结于零件表面。
防范措施即为采用弱碱性清洗液对进炉前零件进行认真彻底清洗,确保进炉前零件的清洁度。
二、有效硬化层深度、表面硬度、心部硬度缺陷(1)有效硬化层深度又叫淬硬层深度,一般用显微硬度计检测,从表面一直测至界限硬度处的直线距离;而渗碳层深是指渗碳层的深度,一般用金相法来检测,合金渗碳钢从表面测至过渡区。
因零件的渗碳层深仅指对合金钢渗入碳的深度,是齿轮热处理生产中的一个过程指标,不能很好地反映齿轮的热处理最终结果,故正规的技术文件,大多以有效硬化层深度作为零件热处理后的检测、考核指标。
有效硬化层深度缺陷又分以下两种情况:第一种是有效硬化层深度浅,产生的原因可能是:原材料的淬透性差、端淬值低;淬火冷却介质的冷却能力差;渗碳保温时间短、强渗及扩散期的碳浓度低,导致渗碳层深度不够;渗碳炉的有效加热区的温度分布不均匀,导致不同区域零件渗碳层深度不够。
相应防范措施为:调换淬透性好、端淬值高的原材料;调换冷却能力好的淬火冷却介质或加大淬火冷却介质容量,增加搅拌功能;延长渗碳保温时间,提高强渗及扩散期的碳浓度,使渗碳层深度合格;检测渗碳炉有效加热区的温度均匀性,使各零件的渗碳层深度稳定、统一,达到技术要求。
渗碳件常见缺陷与对策之欧阳文创编

渗碳件常见缺陷与对策一、渗碳层出现大块状或网状碳化物缺陷产生原因:1、表面碳浓度过高;2、滴注式渗碳,滴量过大;3、控制气氛渗碳,富化气太多;4、液体渗碳,盐浴氰根含量过高;5、渗碳层出炉空冷,冷速太慢;对策:1、降低表面碳浓度,扩散期内减少滴量和适当提高扩散期湿度,也可适当减少渗碳期滴量;2、减少固体渗碳的催碳剂;3、减少液体渗碳的氰根含量;4、夏天室温太高,渗后空冷件可吹风助冷;5、提高淬火加热温度50~80ºC并适当延长保温时间;6、两次淬火或正火+淬火,也可正火+高温回火,然后淬火回火;二、渗层出现大量残余奥氏体缺陷产生原因:1、奥氏体较稳定,奥氏体中碳及合金元素的含量较高;2、回火不及时,奥氏体热稳定化;3、回火后冷却太慢;对策:1、表面碳浓度不宜太高;2、降低直接淬火或重新加热淬火温度,控制心部铁素体的级别≤3级;3、低温回火后快冷;4、可以重新加热淬火,冷处理,也可高温回火后重新淬火;三、表面脱碳缺陷产生原因:1、气体渗碳后期,炉气碳势低;2、固体渗碳后,冷却速度过慢;3、渗碳后空冷时间过长;4、在冷却井中无保护冷却;5、空气炉加热淬火无保护气体;6、盐浴炉加热淬火,盐浴脱氧不彻底;对策:1、在碳势适宜的介质中补渗;2、淬火后作喷丸处理;3、磨削余量,较大件允许有一定脱碳层(≤0.02mm);四、渗碳层淬火后出现屈氏体组织(黑色组织)缺陷产生原因:渗碳介质中含氧量较高:氧扩散到晶界形成Cr、Mn、Si的氧化物,使合金元素贫化,使淬透性降低。
对策:1、控制炉气介质成分,降低含氧量;2、用喷丸可以进行补救;3、提高淬火介质冷却能力;五、心部铁素体过多,使硬度不足缺陷产生原因:1、淬火温度低;2、重新加热淬火保温时间不足,淬火冷速不够;3、心部有未溶铁素体;4、心部有奥氏体分解产物;对策:1、按正常工艺重新加热淬火;2、适当提高淬火温度延长保温时间;六、渗碳层深度不足缺陷产生原因:1、炉温低、保温时间短;2、渗剂浓度低;3、炉子漏气;4、盐浴渗碳成分不正常;5、装炉量过多;6、工件表面有氧化皮或积炭;对策:1、针对原因,调整渗碳温度、时间、滴量及炉子的密封性;2、加强新盐鉴定及工作状况的检查;3、零件应该清理干净;4、渗层过薄,可以补渗,补渗的速度是正常渗碳的1/2,约为0.1mm/h左右;七、渗层深度不均匀缺陷产生原因:1、炉温不均匀;2、炉内气氛循环不良;3、炭黑在表面沉积;4、固体渗碳箱内温差大及催渗剂不均匀;5、零件表面有锈斑、油污等;6、零件表面粗糙度不一致;7、零件吊挂疏密不均;8、原材料有带状组织;对策:1、渗碳前严格清洗零件;2、清理炉内积炭;3、零件装夹时应均匀分布间隙大小相等;4、经常检查炉温均匀性;5、原材料不得有带状组织;6、经常检查炉温、炉气及装炉情况;八、表面硬度低缺陷产生原因:1、表面碳浓度低;2、表面残余奥氏体多;3、表面形成屈氏体组织;4、淬火温度高,溶入奥氏体碳量多,淬火后形成大量残余奥氏体;5、淬火加热温度低,溶入奥氏体的碳量不够,淬火马氏体含碳低;6、回火温度过高;对策:1、碳浓度低,可以补渗;2、残余奥氏体多,可高温回火后再加热淬火;3、有托氏体组织,可以重新加热淬火;4、严格热处理工艺纪律;九、表面腐蚀和氧化缺陷产生原因:1、渗剂不纯有水、硫和硫酸盐;2、气体渗碳炉漏气固体渗碳时催渗剂在工件表面融化,液体渗碳后,工件表面粘有残盐;3、高温出炉,空冷保护不够;4、盐炉校正不彻底,空气炉无保护气氛加热,淬火后不及时清洗;5、零件表面不清洁;对策:1、严格控制渗碳剂及盐浴成分;2、经常检查设备密封情况;3、对零件表面及时清理和清洗;4、严格执行工艺纪律;十、渗碳件开裂缺陷产生原因:1、冷却速度过慢,组织转变不均匀;2、合金钢渗后空冷,在表层托氏体下面保留一层未转变奥氏体在随后冷却或室温放置时,转变成马氏体,比容加大,出现拉应力;3、第一次淬火时,冷却速度太快或工件形状复杂;4、材质含提高淬透性的微量元素(Mo、B)太多等;对策:1、渗后减慢冷却速度,使渗层在冷却过程中完全共析转变;2、渗后加快冷却速度,得到马氏体+残余奥氏体。
渗碳件常见缺陷与对策之欧阳与创编

渗碳件常见缺陷与对策一、渗碳层出现大块状或网状碳化物缺陷产生原因:1、表面碳浓度过高;2、滴注式渗碳,滴量过大;3、控制气氛渗碳,富化气太多;4、液体渗碳,盐浴氰根含量过高;5、渗碳层出炉空冷,冷速太慢;对策:1、降低表面碳浓度,扩散期内减少滴量和适当提高扩散期湿度,也可适当减少渗碳期滴量;2、减少固体渗碳的催碳剂;3、减少液体渗碳的氰根含量;4、夏天室温太高,渗后空冷件可吹风助冷;5、提高淬火加热温度50~80ºC并适当延长保温时间;6、两次淬火或正火+淬火,也可正火+高温回火,然后淬火回火;二、渗层出现大量残余奥氏体缺陷产生原因:1、奥氏体较稳定,奥氏体中碳及合金元素的含量较高;2、回火不及时,奥氏体热稳定化;3、回火后冷却太慢;对策:1、表面碳浓度不宜太高;2、降低直接淬火或重新加热淬火温度,控制心部铁素体的级别≤3级;3、低温回火后快冷;4、可以重新加热淬火,冷处理,也可高温回火后重新淬火;三、表面脱碳缺陷产生原因:1、气体渗碳后期,炉气碳势低;2、固体渗碳后,冷却速度过慢;3、渗碳后空冷时间过长;4、在冷却井中无保护冷却;5、空气炉加热淬火无保护气体;6、盐浴炉加热淬火,盐浴脱氧不彻底;对策:1、在碳势适宜的介质中补渗;2、淬火后作喷丸处理;3、磨削余量,较大件允许有一定脱碳层(≤0.02mm);四、渗碳层淬火后出现屈氏体组织(黑色组织)缺陷产生原因:渗碳介质中含氧量较高:氧扩散到晶界形成Cr、Mn、Si的氧化物,使合金元素贫化,使淬透性降低。
对策:1、控制炉气介质成分,降低含氧量;2、用喷丸可以进行补救;3、提高淬火介质冷却能力;五、心部铁素体过多,使硬度不足缺陷产生原因:1、淬火温度低;2、重新加热淬火保温时间不足,淬火冷速不够;3、心部有未溶铁素体;4、心部有奥氏体分解产物;对策:1、按正常工艺重新加热淬火;2、适当提高淬火温度延长保温时间;六、渗碳层深度不足缺陷产生原因:1、炉温低、保温时间短;2、渗剂浓度低;3、炉子漏气;4、盐浴渗碳成分不正常;5、装炉量过多;6、工件表面有氧化皮或积炭;对策:1、针对原因,调整渗碳温度、时间、滴量及炉子的密封性;2、加强新盐鉴定及工作状况的检查;3、零件应该清理干净;4、渗层过薄,可以补渗,补渗的速度是正常渗碳的1/2,约为0.1mm/h左右;七、渗层深度不均匀缺陷产生原因:1、炉温不均匀;2、炉内气氛循环不良;3、炭黑在表面沉积;4、固体渗碳箱内温差大及催渗剂不均匀;5、零件表面有锈斑、油污等;6、零件表面粗糙度不一致;7、零件吊挂疏密不均;8、原材料有带状组织;对策:1、渗碳前严格清洗零件;2、清理炉内积炭;3、零件装夹时应均匀分布间隙大小相等;4、经常检查炉温均匀性;5、原材料不得有带状组织;6、经常检查炉温、炉气及装炉情况;八、表面硬度低缺陷产生原因:1、表面碳浓度低;2、表面残余奥氏体多;3、表面形成屈氏体组织;4、淬火温度高,溶入奥氏体碳量多,淬火后形成大量残余奥氏体;5、淬火加热温度低,溶入奥氏体的碳量不够,淬火马氏体含碳低;6、回火温度过高;对策:1、碳浓度低,可以补渗;2、残余奥氏体多,可高温回火后再加热淬火;3、有托氏体组织,可以重新加热淬火;4、严格热处理工艺纪律;九、表面腐蚀和氧化缺陷产生原因:1、渗剂不纯有水、硫和硫酸盐;2、气体渗碳炉漏气固体渗碳时催渗剂在工件表面融化,液体渗碳后,工件表面粘有残盐;3、高温出炉,空冷保护不够;4、盐炉校正不彻底,空气炉无保护气氛加热,淬火后不及时清洗;5、零件表面不清洁;对策:1、严格控制渗碳剂及盐浴成分;2、经常检查设备密封情况;3、对零件表面及时清理和清洗;4、严格执行工艺纪律;十、渗碳件开裂缺陷产生原因:1、冷却速度过慢,组织转变不均匀;2、合金钢渗后空冷,在表层托氏体下面保留一层未转变奥氏体在随后冷却或室温放置时,转变成马氏体,比容加大,出现拉应力;3、第一次淬火时,冷却速度太快或工件形状复杂;4、材质含提高淬透性的微量元素(Mo、B)太多等;对策:1、渗后减慢冷却速度,使渗层在冷却过程中完全共析转变;2、渗后加快冷却速度,得到马氏体+残余奥氏体。
渗碳热处理缺陷分析

第 卷第期 年月
哈尔 滨轴 承
渗碳热处理缺 陷分析
张润慧 ,张延成 ,宋立波
哈尔滨轴承集团公 司 热处理分厂 ,黑龙江 哈尔滨 巧
摘 要 详细分析渗碳热处理过程 中的各种缺陷 ,指 出产生缺陷的原 因 ,提 出了预防措施 ,在生产过程 中取得 良好 效果 。
林
竹
二
一林 ,
彻
一二 。
各标称尺寸量块 的合成标准不确定度和有效
自由度见表 。
表 合成标准不确定度和有效 自由度一览表
标称尺寸
合成标准不确定度
自由度
从动林
扩展不确定度 妹 的计算
取置信概率
,查分布表得到
环 凡·
联叼 · 由。
对于
的环规 ,彻 司 ,取置信概率
,查 表可得 杨 场
杨 ·喊 由
林“
对于
的环规 , , 护
哈尔滨轴承
第卷
灵敏系数 。 必 。
标准不确定度汇总表
量输人量 的标准不确定度汇总于表
。一
环规的标准不确定度见表 。
合成标准不确定度 动
由上 文知
对于
石 砌, 环规 ,
丫啪 合成标 准不确定度 计算
,“
林。
有效 自由度 , , 的
卜
。气
艺引一
司
边因 里晒 城城
对于
环规 ,
动一 ·‘“林‘,
艺一 气 林 肛
渗碳 件淬火 后表 面硬度低
渗碳件淬火后 , 要求工件表面硬度必须达到
渗碳淬火的问题和对策

渗碳淬火的问题和对策作者:孙亮来源:《经济技术协作信息》 2018年第5期大型铸锻件在渗碳淬火时经常会因工件材质、操作方法、淬火介质等很多复杂因素导致出现淬火裂纹,充分认识各种裂纹形成的原因,并针对问题提前做出有效措施进行预防,对大型铸锻件的渗碳淬火成功率会有很大的提高。
一、硬度不良渗碳淬火的目的是为了提高钢制零件的表面硬度,所以硬度不足就满足不了使用要求。
渗碳淬火硬度不足的原因,可以认为是渗碳不足;淬火时脱碳;淬火温度过低;冷却速度太慢等。
同时也不要忽略表面层内存在的残余奥氏体,以及晶界氧化对硬度的影响。
理想的渗碳含碳量是共析渗碳量的0.8%~0.9%。
如果含碳量高于0.8%~0.9%,将出现网状渗碳体而变脆,这是令人讨厌的,这种现象称为过渗碳。
出现过渗碳时,最好进行球化处理,渗碳至含碳量为1.1%~1.2%,使其像工具钢那样进行球化的工艺方法称为TSP(tool steel process)法,即工具钢法,这个方法用于需要耐磨性的零件,它比渗碳不足所造成的硬度不良要强些。
渗碳不足是由渗碳气体的渗碳能力过低,渗碳温度和渗碳时间不足引起的,必须注意。
但是,即使顺利地渗了碳,渗碳后的淬火没做好也得不到好结果,渗碳后的淬火有一次淬火(未渗碳的心部细化)和二次淬火(表面硬化),此淬火温度过低和冷却速度过慢自然会引起硬化不良,不过最近为了节省能源,一般是渗碳后直接淬火,因此不存在这个问题。
渗碳层的硬度不足,是残余奥氏体和晶界氧化造成的,渗碳层的含碳量多及为减少淬火变形使用油淬,会使渗碳层的残余奥氏体多,在这种情形下最好进行冷处理,还有,晶界氧化是渗碳气体中少量的氧与钢中的铬和锰化合,在晶界上生成氧化物,使晶界的淬透性降低以致难以淬硬。
因此,最好在渗碳气体中掺入少量的氮气或提高淬火速度,以补充淬透性的不足。
不过,晶界氧化层在表面下只有数微米到数十微米厚,因此可以用磨削除掉。
二、软点有时在渗碳淬火的表面产生淬火软点,渗碳后淬火时如果冷却不均匀往往产生软点。
曲轴渗碳淬火后的缺陷分析及工艺改进

2018年 第7期 热加工H热处理eatTreatment64为了提高曲轴的使用寿命,某些生产厂家曲轴材质选用渗碳钢,并对曲轴进行渗碳淬火处理。
本文涉及的曲轴技术要求如下:曲轴采用模锻成形,材质20C r ,渗碳层深度1~1.5m m ,表面碳浓度0.8%~0.9%,渗碳淬火后硬度55~60HRC 。
曲轴如图1所示,图中红色区域为工作面(该表面需进行渗碳淬火处理)。
原工艺采用渗碳后直接降温淬火。
检验过程中发现硬度在45~50HRC ,未达到要求。
在喷砂处理过程中,发现渗碳层局部剥落,表面存在裂纹等现象,如图2所示。
为查找曲轴硬度不足、渗碳层局部剥落、产生裂纹的原因,对其进行了金相组织观察,对渗碳淬火工艺进行了改进。
1. 曲轴渗碳淬火缺陷分析在渗碳层局部剥落位置取样(横截面),进行宏观形貌观察,发现局部几乎完全剥落的剥离裂纹,裂纹产生在渗碳层与基体过渡区域,如图3所示。
对曲轴进行金相组织观察,以判定裂纹产生的原因。
发现表面及近表面位置晶粒粗大,并存在大量残留奥氏体(见图4),这是曲轴硬度低以及产生裂纹的图1 曲轴示意图2 曲轴渗碳淬火后局部剥落图3渗碳层局部剥落(b )400×图4 粗大马氏体+残留奥氏体(a )100×曲轴渗碳淬火后的缺陷分析及工艺改进■ 张晓阳,齐永丰摘要:介绍了一种锻造镁合金轮毂机加工后热处理工艺。
该热处理工艺主要包括高低温交变热处理过程,采用该工艺可以有效地消除锻造镁合金轮毂机加工后的残余应力,防止因残余应力导致轮毂变形。
通过疲劳、材料试验数据,验证了采用该热处理工艺生产的镁合金轮毂满足可靠性要求。
关键词:镁合金轮毂;锻造;机加工;热处理扫码了解更多2018年 第7期热加工H热处理eatTreatment65主要原因之一。
渗碳后直接淬火不能细化钢的晶粒,表面残留奥氏体较多,硬度较低,表面应力较大,容易在喷砂后产生裂纹。
检测随炉渗碳试样金相组织,表面碳浓度达到1%~1.2%,超出标准范围。
渗碳件常见缺陷与对策之欧阳美创编

渗碳件常见缺陷与对策一、渗碳层出现大块状或网状碳化物缺陷产生原因:1、表面碳浓度过高;2、滴注式渗碳,滴量过大;3、控制气氛渗碳,富化气太多;4、液体渗碳,盐浴氰根含量过高;5、渗碳层出炉空冷,冷速太慢;对策:1、降低表面碳浓度,扩散期内减少滴量和适当提高扩散期湿度,也可适当减少渗碳期滴量;2、减少固体渗碳的催碳剂;3、减少液体渗碳的氰根含量;4、夏天室温太高,渗后空冷件可吹风助冷;5、提高淬火加热温度50~80ºC并适当延长保温时间;6、两次淬火或正火+淬火,也可正火+高温回火,然后淬火回火;二、渗层出现大量残余奥氏体缺陷产生原因:1、奥氏体较稳定,奥氏体中碳及合金元素的含量较高;2、回火不及时,奥氏体热稳定化;3、回火后冷却太慢;对策:1、表面碳浓度不宜太高;2、降低直接淬火或重新加热淬火温度,控制心部铁素体的级别≤3级;3、低温回火后快冷;4、可以重新加热淬火,冷处理,也可高温回火后重新淬火;三、表面脱碳缺陷产生原因:1、气体渗碳后期,炉气碳势低;2、固体渗碳后,冷却速度过慢;3、渗碳后空冷时间过长;4、在冷却井中无保护冷却;5、空气炉加热淬火无保护气体;6、盐浴炉加热淬火,盐浴脱氧不彻底;对策:1、在碳势适宜的介质中补渗;2、淬火后作喷丸处理;3、磨削余量,较大件允许有一定脱碳层(≤0.02mm);四、渗碳层淬火后出现屈氏体组织(黑色组织)缺陷产生原因:渗碳介质中含氧量较高:氧扩散到晶界形成Cr、Mn、Si的氧化物,使合金元素贫化,使淬透性降低。
对策:1、控制炉气介质成分,降低含氧量;2、用喷丸可以进行补救;3、提高淬火介质冷却能力;五、心部铁素体过多,使硬度不足缺陷产生原因:1、淬火温度低;2、重新加热淬火保温时间不足,淬火冷速不够;3、心部有未溶铁素体;4、心部有奥氏体分解产物;对策:1、按正常工艺重新加热淬火;2、适当提高淬火温度延长保温时间;六、渗碳层深度不足缺陷产生原因:1、炉温低、保温时间短;2、渗剂浓度低;3、炉子漏气;4、盐浴渗碳成分不正常;5、装炉量过多;6、工件表面有氧化皮或积炭;对策:1、针对原因,调整渗碳温度、时间、滴量及炉子的密封性;2、加强新盐鉴定及工作状况的检查;3、零件应该清理干净;4、渗层过薄,可以补渗,补渗的速度是正常渗碳的1/2,约为0.1mm/h左右;七、渗层深度不均匀缺陷产生原因:1、炉温不均匀;2、炉内气氛循环不良;3、炭黑在表面沉积;4、固体渗碳箱内温差大及催渗剂不均匀;5、零件表面有锈斑、油污等;6、零件表面粗糙度不一致;7、零件吊挂疏密不均;8、原材料有带状组织;对策:1、渗碳前严格清洗零件;2、清理炉内积炭;3、零件装夹时应均匀分布间隙大小相等;4、经常检查炉温均匀性;5、原材料不得有带状组织;6、经常检查炉温、炉气及装炉情况;八、表面硬度低缺陷产生原因:1、表面碳浓度低;2、表面残余奥氏体多;3、表面形成屈氏体组织;4、淬火温度高,溶入奥氏体碳量多,淬火后形成大量残余奥氏体;5、淬火加热温度低,溶入奥氏体的碳量不够,淬火马氏体含碳低;6、回火温度过高;对策:1、碳浓度低,可以补渗;2、残余奥氏体多,可高温回火后再加热淬火;3、有托氏体组织,可以重新加热淬火;4、严格热处理工艺纪律;九、表面腐蚀和氧化缺陷产生原因:1、渗剂不纯有水、硫和硫酸盐;2、气体渗碳炉漏气固体渗碳时催渗剂在工件表面融化,液体渗碳后,工件表面粘有残盐;3、高温出炉,空冷保护不够;4、盐炉校正不彻底,空气炉无保护气氛加热,淬火后不及时清洗;5、零件表面不清洁;对策:1、严格控制渗碳剂及盐浴成分;2、经常检查设备密封情况;3、对零件表面及时清理和清洗;4、严格执行工艺纪律;十、渗碳件开裂缺陷产生原因:1、冷却速度过慢,组织转变不均匀;2、合金钢渗后空冷,在表层托氏体下面保留一层未转变奥氏体在随后冷却或室温放置时,转变成马氏体,比容加大,出现拉应力;3、第一次淬火时,冷却速度太快或工件形状复杂;4、材质含提高淬透性的微量元素(Mo、B)太多等;对策:1、渗后减慢冷却速度,使渗层在冷却过程中完全共析转变;2、渗后加快冷却速度,得到马氏体+残余奥氏体。
渗碳件常见缺陷与对策之欧阳引擎创编

渗碳件常见缺陷与对策欧阳引擎(2021.01.01)一、渗碳层出现大块状或网状碳化物缺陷产生原因:1、表面碳浓度过高;2、滴注式渗碳,滴量过大;3、控制气氛渗碳,富化气太多;4、液体渗碳,盐浴氰根含量过高;5、渗碳层出炉空冷,冷速太慢;对策:1、降低表面碳浓度,扩散期内减少滴量和适当提高扩散期湿度,也可适当减少渗碳期滴量;2、减少固体渗碳的催碳剂;3、减少液体渗碳的氰根含量;4、夏天室温太高,渗后空冷件可吹风助冷;5、提高淬火加热温度50~80ºC并适当延长保温时间;6、两次淬火或正火+淬火,也可正火+高温回火,然后淬火回火;二、渗层出现大量残余奥氏体缺陷产生原因:1、奥氏体较稳定,奥氏体中碳及合金元素的含量较高;2、回火不及时,奥氏体热稳定化;3、回火后冷却太慢;对策:1、表面碳浓度不宜太高;2、降低直接淬火或重新加热淬火温度,控制心部铁素体的级别≤3级;3、低温回火后快冷;4、可以重新加热淬火,冷处理,也可高温回火后重新淬火;三、表面脱碳缺陷产生原因:1、气体渗碳后期,炉气碳势低;2、固体渗碳后,冷却速度过慢;3、渗碳后空冷时间过长;4、在冷却井中无保护冷却;5、空气炉加热淬火无保护气体;6、盐浴炉加热淬火,盐浴脱氧不彻底;对策:1、在碳势适宜的介质中补渗;2、淬火后作喷丸处理;3、磨削余量,较大件允许有一定脱碳层(≤0.02mm);四、渗碳层淬火后出现屈氏体组织(黑色组织)缺陷产生原因:渗碳介质中含氧量较高:氧扩散到晶界形成Cr、Mn、Si的氧化物,使合金元素贫化,使淬透性降低。
对策:1、控制炉气介质成分,降低含氧量;2、用喷丸可以进行补救;3、提高淬火介质冷却能力;五、心部铁素体过多,使硬度不足缺陷产生原因:1、淬火温度低;2、重新加热淬火保温时间不足,淬火冷速不够;3、心部有未溶铁素体;4、心部有奥氏体分解产物;对策:1、按正常工艺重新加热淬火;2、适当提高淬火温度延长保温时间;六、渗碳层深度不足缺陷产生原因:1、炉温低、保温时间短;2、渗剂浓度低;3、炉子漏气;4、盐浴渗碳成分不正常;5、装炉量过多;6、工件表面有氧化皮或积炭;对策:1、针对原因,调整渗碳温度、时间、滴量及炉子的密封性;2、加强新盐鉴定及工作状况的检查;3、零件应该清理干净;4、渗层过薄,可以补渗,补渗的速度是正常渗碳的1/2,约为0.1mm/h左右;七、渗层深度不均匀缺陷产生原因:1、炉温不均匀;2、炉内气氛循环不良;3、炭黑在表面沉积;4、固体渗碳箱内温差大及催渗剂不均匀;5、零件表面有锈斑、油污等;6、零件表面粗糙度不一致;7、零件吊挂疏密不均;8、原材料有带状组织;对策:1、渗碳前严格清洗零件;2、清理炉内积炭;3、零件装夹时应均匀分布间隙大小相等;4、经常检查炉温均匀性;5、原材料不得有带状组织;6、经常检查炉温、炉气及装炉情况;八、表面硬度低缺陷产生原因:1、表面碳浓度低;2、表面残余奥氏体多;3、表面形成屈氏体组织;4、淬火温度高,溶入奥氏体碳量多,淬火后形成大量残余奥氏体;5、淬火加热温度低,溶入奥氏体的碳量不够,淬火马氏体含碳低;6、回火温度过高;对策:1、碳浓度低,可以补渗;2、残余奥氏体多,可高温回火后再加热淬火;3、有托氏体组织,可以重新加热淬火;4、严格热处理工艺纪律;九、表面腐蚀和氧化缺陷产生原因:1、渗剂不纯有水、硫和硫酸盐;2、气体渗碳炉漏气固体渗碳时催渗剂在工件表面融化,液体渗碳后,工件表面粘有残盐;3、高温出炉,空冷保护不够;4、盐炉校正不彻底,空气炉无保护气氛加热,淬火后不及时清洗;5、零件表面不清洁;对策:1、严格控制渗碳剂及盐浴成分;2、经常检查设备密封情况;3、对零件表面及时清理和清洗;4、严格执行工艺纪律;十、渗碳件开裂缺陷产生原因:1、冷却速度过慢,组织转变不均匀;2、合金钢渗后空冷,在表层托氏体下面保留一层未转变奥氏体在随后冷却或室温放置时,转变成马氏体,比容加大,出现拉应力;3、第一次淬火时,冷却速度太快或工件形状复杂;4、材质含提高淬透性的微量元素(Mo、B)太多等;对策:1、渗后减慢冷却速度,使渗层在冷却过程中完全共析转变;2、渗后加快冷却速度,得到马氏体+残余奥氏体。
渗碳淬火常见缺陷及对策

渗碳淬火常见缺陷及对策渗碳层出现大块状或网状碳化物缺陷产生原因:表面碳浓度过高1.滴注式渗碳,滴量过大2.控制气氛渗碳,富化气太多3.液体渗碳,盐浴氰根含量过高4.渗碳层出炉空冷,冷速太慢对策:1.降低表面碳浓度,扩散期内减少滴量和适当提高扩散期湿度,也可适当减少渗碳期滴量2.减少固体渗碳的催碳剂3.减少液体渗碳的氰根含量4.夏天室温太高,渗后空冷件可吹风助冷5.提高淬火加热温度50~80ºC并适当延长保温时间6.两次淬火或正火+淬火,也可正火+高温回火,然后淬火回火渗层出现大量残余奥氏体缺陷产生原因:1.奥氏体较稳定,奥氏体中碳及合金元素的含量较高2.回火不及时,奥氏体热稳定化3.回火后冷却太慢对策:1.表面碳浓度不宜太高2.降低直接淬火或重新加热淬火温度,控制心部铁素体的级别≤3级3.低温回火后快冷4.可以重新加热淬火,冷处理,也可高温回火后重新淬火表面脱碳缺陷产生原因:1.气体渗碳后期,炉气碳势低2.固体渗碳后,冷却速度过慢3.渗碳后空冷时间过长4.在冷却井中无保护冷却5.空气炉加热淬火无保护气体6.盐浴炉加热淬火,盐浴脱氧不彻底对策:1.在碳势适宜的介质中补渗2.淬火后作喷丸处理3.磨削余量,较大件允许有一定脱碳层(≤0.02mm)渗碳层淬火后出现屈氏体组织(黑色组织)缺陷产生原因:渗碳介质中含氧量较高:氧扩散到晶界形成Cr、Mn、Si的氧化物,使合金元素贫化,使淬透性降低对策:1.控制炉气介质成分,降低含氧量2.用喷丸可以进行补救3.提高淬火介质冷却能力心部铁素体过多,使硬度不足缺陷产生原因:1.淬火温度低2.重新加热淬火保温时间不足,淬火冷速不够3.心部有未溶铁素体4.心部有奥氏体分解产物对策:1.按正常工艺重新加热淬火2.适当提高淬火温度延长保温时间渗碳层深度不足缺陷产生原因:1.炉温低、保温时间短2.渗剂浓度低3.炉子漏气4.盐浴渗碳成分不正常5.装炉量过多6.工件表面有氧化皮或积炭对策:1.针对原因,调整渗碳温度、时间、滴量及炉子的密封性2.加强新盐鉴定及工作状况的检查3.零件应该清理干净4.渗层过薄,可以补渗,补渗的速度是正常渗碳的1/2,约为0.1mm/h左右渗层深度不均匀缺陷产生原因:1.炉温不均匀2.炉内气氛循环不良3.炭黑在表面沉积4.固体渗碳箱内温差大及催渗剂不均匀5.零件表面有锈斑、油污等6.零件表面粗糙度不一致7.零件吊挂疏密不均8.原材料有带状组织对策:1.渗碳前严格清洗零件2.清理炉内积炭3.零件装夹时应均匀分布间隙大小相等4.经常检查炉温均匀性5.原材料不得有带状组织6.经常检查炉温、炉气及装炉情况表面硬度低缺陷产生原因:1.表面碳浓度低2.表面残余奥氏体多3.表面形成屈氏体组织4.淬火温度高,溶入奥氏体碳量多,淬火后形成大量残余奥氏体5.淬火加热温度低,溶入奥氏体的碳量不够,淬火马氏体含碳低6.回火温度过高对策:1.碳浓度低,可以补渗2.残余奥氏体多,可高温回火后再加热淬火3.有托氏体组织,可以重新加热淬火4.严格热处理工艺纪律表面腐蚀和氧化缺陷产生原因:1.渗剂不纯有水、硫和硫酸盐2.气体渗碳炉漏气固体渗碳时催渗剂在工件表面融化,液体渗碳后,工件表面粘有残盐3.高温出炉,空冷保护不够4.盐炉校正不彻底,空气炉无保护气氛加热,淬火后不及时清洗5.零件表面不清洁对策:1.严格控制渗碳剂及盐浴成分2.经常检查设备密封情况3.对零件表面及时清理和清洗4.严格执行工艺纪律渗碳件开裂缺陷产生原因:1.冷却速度过慢,组织转变不均匀2.合金钢渗后空冷,在表层托氏体下面保留一层未转变奥氏体在随后冷却或室温放置时,转变成马氏体,比容加大,出现拉应力3.第一次淬火时,冷却速度太快或工件形状复杂]4.材质含提高淬透性的微量元素(Mo、B)太多等对策:1.渗后减慢冷却速度,使渗层在冷却过程中完全共析转变2.渗后加快冷却速度,得到马氏体+残余奥氏体。
渗碳件的常见缺陷及预防措施

一
测 试与 分析 一
渗 碳 件 的 常 见 缺 陷 及 预 防 措 施
于娜红 , 余 成 龙
( 中国第一汽车股份有 限公 司无锡 油泵油嘴研 究所, 江 苏 无锡 2 1 4 0 6 3 )
摘
要 :渗碳 零件 的 常见缺 陷有 黑 色组 织、 渗层 大块 状或 网状碳 化 合物 、 渗层 不 均 匀和 畸 变过 大 等 。这 些缺 陷 的产生 与渗碳 气氛 的成分 和均 匀性 、 渗碳 操 作 、 工件 的装 炉 方式 、 渗碳 后 的淬 火工 艺和操 作 等 多 种 因素 中的一种 或 几种 有关 。采取 某 些相应 的措 施 可 以预 防这 些缺 陷的产 生。
f a c t o r s wh i c h i n c l u de c o mp o s i t i o n a n d u n i f o r mi t y o f e a r b u r l z i n g a t mo s p he r e, o p e r a t i o n o f c a r bu r i z i n g, c ha r g i冷时 , 表层为过共析
层, 是细 密珠 光体加 颗 粒状 均匀 分布碳 化 物 ; 次 表层 为共 析层 , 属 细密珠光体组织 ; 内层 为 亚 共 析 过 渡
气 中的氧发 生 内氧化 。炉 气 中氧原 子吸 入钢 中 向内 扩散 , 在 晶界形 成 C r 、 Mn 、 T i 、 S i 等 的氧 化物 , 造 成 晶 界处 合金元 素 贫乏 , 此处 淬透 性低 , 渗碳 时表层 形成
YU Na h o n g .YU C h e n g l o n g
渗碳件常见缺陷与对策之欧阳光明创编

渗碳件常见缺陷与对策欧阳光明(2021.03.07)一、渗碳层出现大块状或网状碳化物缺陷产生原因:1、表面碳浓度过高;2、滴注式渗碳,滴量过大;3、控制气氛渗碳,富化气太多;4、液体渗碳,盐浴氰根含量过高;5、渗碳层出炉空冷,冷速太慢;对策:1、降低表面碳浓度,扩散期内减少滴量和适当提高扩散期湿度,也可适当减少渗碳期滴量;2、减少固体渗碳的催碳剂;3、减少液体渗碳的氰根含量;4、夏天室温太高,渗后空冷件可吹风助冷;5、提高淬火加热温度50~80ºC并适当延长保温时间;6、两次淬火或正火+淬火,也可正火+高温回火,然后淬火回火;二、渗层出现大量残余奥氏体缺陷产生原因:1、奥氏体较稳定,奥氏体中碳及合金元素的含量较高;2、回火不及时,奥氏体热稳定化;3、回火后冷却太慢;对策:1、表面碳浓度不宜太高;2、降低直接淬火或重新加热淬火温度,控制心部铁素体的级别≤3级;3、低温回火后快冷;4、可以重新加热淬火,冷处理,也可高温回火后重新淬火;三、表面脱碳缺陷产生原因:1、气体渗碳后期,炉气碳势低;2、固体渗碳后,冷却速度过慢;3、渗碳后空冷时间过长;4、在冷却井中无保护冷却;5、空气炉加热淬火无保护气体;6、盐浴炉加热淬火,盐浴脱氧不彻底;对策:1、在碳势适宜的介质中补渗;2、淬火后作喷丸处理;3、磨削余量,较大件允许有一定脱碳层(≤0.02mm);四、渗碳层淬火后出现屈氏体组织(黑色组织)缺陷产生原因:渗碳介质中含氧量较高:氧扩散到晶界形成Cr、Mn、Si的氧化物,使合金元素贫化,使淬透性降低。
对策:1、控制炉气介质成分,降低含氧量;2、用喷丸可以进行补救;3、提高淬火介质冷却能力;五、心部铁素体过多,使硬度不足缺陷产生原因:1、淬火温度低;2、重新加热淬火保温时间不足,淬火冷速不够;3、心部有未溶铁素体;4、心部有奥氏体分解产物;对策:1、按正常工艺重新加热淬火;2、适当提高淬火温度延长保温时间;六、渗碳层深度不足缺陷产生原因:1、炉温低、保温时间短;2、渗剂浓度低;3、炉子漏气;4、盐浴渗碳成分不正常;5、装炉量过多;6、工件表面有氧化皮或积炭;对策:1、针对原因,调整渗碳温度、时间、滴量及炉子的密封性;2、加强新盐鉴定及工作状况的检查;3、零件应该清理干净;4、渗层过薄,可以补渗,补渗的速度是正常渗碳的1/2,约为0.1mm/h左右;七、渗层深度不均匀缺陷产生原因:1、炉温不均匀;2、炉内气氛循环不良;3、炭黑在表面沉积;4、固体渗碳箱内温差大及催渗剂不均匀;5、零件表面有锈斑、油污等;6、零件表面粗糙度不一致;7、零件吊挂疏密不均;8、原材料有带状组织;对策:1、渗碳前严格清洗零件;2、清理炉内积炭;3、零件装夹时应均匀分布间隙大小相等;4、经常检查炉温均匀性;5、原材料不得有带状组织;6、经常检查炉温、炉气及装炉情况;八、表面硬度低缺陷产生原因:1、表面碳浓度低;2、表面残余奥氏体多;3、表面形成屈氏体组织;4、淬火温度高,溶入奥氏体碳量多,淬火后形成大量残余奥氏体;5、淬火加热温度低,溶入奥氏体的碳量不够,淬火马氏体含碳低;6、回火温度过高;对策:1、碳浓度低,可以补渗;2、残余奥氏体多,可高温回火后再加热淬火;3、有托氏体组织,可以重新加热淬火;4、严格热处理工艺纪律;九、表面腐蚀和氧化缺陷产生原因:1、渗剂不纯有水、硫和硫酸盐;2、气体渗碳炉漏气固体渗碳时催渗剂在工件表面融化,液体渗碳后,工件表面粘有残盐;3、高温出炉,空冷保护不够;4、盐炉校正不彻底,空气炉无保护气氛加热,淬火后不及时清洗;5、零件表面不清洁;对策:1、严格控制渗碳剂及盐浴成分;2、经常检查设备密封情况;3、对零件表面及时清理和清洗;4、严格执行工艺纪律;十、渗碳件开裂缺陷产生原因:1、冷却速度过慢,组织转变不均匀;2、合金钢渗后空冷,在表层托氏体下面保留一层未转变奥氏体在随后冷却或室温放置时,转变成马氏体,比容加大,出现拉应力;3、第一次淬火时,冷却速度太快或工件形状复杂;4、材质含提高淬透性的微量元素(Mo、B)太多等;对策:1、渗后减慢冷却速度,使渗层在冷却过程中完全共析转变;2、渗后加快冷却速度,得到马氏体+残余奥氏体。
渗碳压淬件常见问题及分析
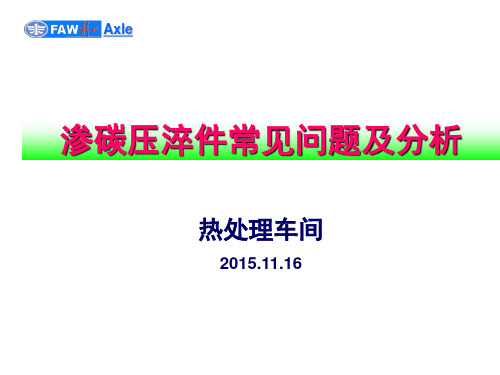
2015.11.13
Axle
二、汽车后桥从动椎齿轮变形的技术要求
(一)Φ300系列:平面度内≤0.10mm,外≤0.06mm;椭圆 度≤0.08mm
(二)Φ390系列:平面度内、外≤0.10mm;椭圆度 ≤0.08mm
(三)Φ420系列:平面度内、外≤0.10mm;椭圆度 ≤0.08mm (四)Φ457系列:平面度内、外≤0.10mm;椭圆度 ≤0.08mm
2015.11.13
Axle
八、影响零件压淬变形的因素 6、零件原材料的影响
零件原材料的化学成分、非金属 夹杂、含氧量、淬透性大小、晶 粒度、带状组织、正火后的硬度、 正火后金相组织级别等因素都对 零件压淬后的变形有很大的影响。
2015.11.13
Axle
一汽解放车轴齿中心毛坯供货技术要求
1、 范围 本要求规定了 20CrMnTiH 渗碳钢基本的技术要求。 本要求适用于一汽解放车桥分公司生产的轻型车 V 平台系列桥的齿轮用钢。 2、 引用标准 GB/T225-2006 钢的淬透性末端淬火试ห้องสมุดไป่ตู้方法 GB/T6394-2002 金属平均晶粒度测定方法 GB/T13320-2007 钢质模锻件金相组织平级图及评定方法 GB/T1979-2001 结构钢低倍组织缺陷评级图 GB 10561-1989 钢中非金属夹杂物显微评定方法 GB/T3077-1999 合金结构钢技术条件 Q/CAM-10.1-10.2-2010 结构钢组织偏析评定 Q/CAM-11.1~11.5-2010 渗碳钢技术条件 3、 技术条件 3.1 钢材氧含量≤20ppm。 3.2 化学成分见下表:
淬火压床
2015.11.13
Axle
八、影响零件压淬变形的因素
渗碳件常见缺陷与对策之欧阳理创编

渗碳件常见缺陷与对策一、渗碳层出现大块状或网状碳化物缺陷产生原因:1、表面碳浓度过高;2、滴注式渗碳,滴量过大;3、控制气氛渗碳,富化气太多;4、液体渗碳,盐浴氰根含量过高;5、渗碳层出炉空冷,冷速太慢;对策:1、降低表面碳浓度,扩散期内减少滴量和适当提高扩散期湿度,也可适当减少渗碳期滴量;2、减少固体渗碳的催碳剂;3、减少液体渗碳的氰根含量;4、夏天室温太高,渗后空冷件可吹风助冷;5、提高淬火加热温度50~80ºC并适当延长保温时间;6、两次淬火或正火+淬火,也可正火+高温回火,然后淬火回火;二、渗层出现大量残余奥氏体缺陷产生原因:1、奥氏体较稳定,奥氏体中碳及合金元素的含量较高;2、回火不及时,奥氏体热稳定化;3、回火后冷却太慢;对策:1、表面碳浓度不宜太高;2、降低直接淬火或重新加热淬火温度,控制心部铁素体的级别≤3级;3、低温回火后快冷;4、可以重新加热淬火,冷处理,也可高温回火后重新淬火;三、表面脱碳缺陷产生原因:1、气体渗碳后期,炉气碳势低;2、固体渗碳后,冷却速度过慢;3、渗碳后空冷时间过长;4、在冷却井中无保护冷却;5、空气炉加热淬火无保护气体;6、盐浴炉加热淬火,盐浴脱氧不彻底;对策:1、在碳势适宜的介质中补渗;2、淬火后作喷丸处理;3、磨削余量,较大件允许有一定脱碳层(≤0.02mm);四、渗碳层淬火后出现屈氏体组织(黑色组织)缺陷产生原因:渗碳介质中含氧量较高:氧扩散到晶界形成Cr、Mn、Si 的氧化物,使合金元素贫化,使淬透性降低。
对策:1、控制炉气介质成分,降低含氧量;2、用喷丸可以进行补救;3、提高淬火介质冷却能力;五、心部铁素体过多,使硬度不足缺陷产生原因:1、淬火温度低;2、重新加热淬火保温时间不足,淬火冷速不够;3、心部有未溶铁素体;4、心部有奥氏体分解产物;对策:1、按正常工艺重新加热淬火;2、适当提高淬火温度延长保温时间;六、渗碳层深度不足缺陷产生原因:1、炉温低、保温时间短;2、渗剂浓度低;3、炉子漏气;4、盐浴渗碳成分不正常;5、装炉量过多;6、工件表面有氧化皮或积炭;对策:1、针对原因,调整渗碳温度、时间、滴量及炉子的密封性;2、加强新盐鉴定及工作状况的检查;3、零件应该清理干净;4、渗层过薄,可以补渗,补渗的速度是正常渗碳的1/2,约为0.1mm/h左右;七、渗层深度不均匀缺陷产生原因:1、炉温不均匀;2、炉内气氛循环不良;3、炭黑在表面沉积;4、固体渗碳箱内温差大及催渗剂不均匀;5、零件表面有锈斑、油污等;6、零件表面粗糙度不一致;7、零件吊挂疏密不均;8、原材料有带状组织;对策:1、渗碳前严格清洗零件;2、清理炉内积炭;3、零件装夹时应均匀分布间隙大小相等;4、经常检查炉温均匀性;5、原材料不得有带状组织;6、经常检查炉温、炉气及装炉情况;八、表面硬度低缺陷产生原因:1、表面碳浓度低;2、表面残余奥氏体多;3、表面形成屈氏体组织;4、淬火温度高,溶入奥氏体碳量多,淬火后形成大量残余奥氏体;5、淬火加热温度低,溶入奥氏体的碳量不够,淬火马氏体含碳低;6、回火温度过高;对策:1、碳浓度低,可以补渗;2、残余奥氏体多,可高温回火后再加热淬火;3、有托氏体组织,可以重新加热淬火;4、严格热处理工艺纪律;九、表面腐蚀和氧化缺陷产生原因:1、渗剂不纯有水、硫和硫酸盐;2、气体渗碳炉漏气固体渗碳时催渗剂在工件表面融化,液体渗碳后,工件表面粘有残盐;3、高温出炉,空冷保护不够;4、盐炉校正不彻底,空气炉无保护气氛加热,淬火后不及时清洗;5、零件表面不清洁;对策:1、严格控制渗碳剂及盐浴成分;2、经常检查设备密封情况;3、对零件表面及时清理和清洗;4、严格执行工艺纪律;十、渗碳件开裂缺陷产生原因:1、冷却速度过慢,组织转变不均匀;2、合金钢渗后空冷,在表层托氏体下面保留一层未转变奥氏体在随后冷却或室温放置时,转变成马氏体,比容加大,出现拉应力;3、第一次淬火时,冷却速度太快或工件形状复杂;4、材质含提高淬透性的微量元素(Mo、B)太多等;对策:1、渗后减慢冷却速度,使渗层在冷却过程中完全共析转变;2、渗后加快冷却速度,得到马氏体+残余奥氏体。