渗碳常见缺陷
渗碳缺陷及质量控制
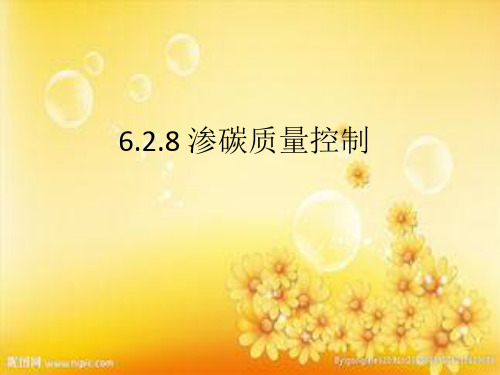
4 过热 渗碳时或渗碳后加热时过热,表现为钢
的晶粒过大。
危害:增加脆性,增加表面碳化物的数量, 并形成粗大碳化物,甚至形成莱氏体,使 零件报废。
消除办法:进行正火后再淬回火。
5 表面氧化和脱碳
原因: 渗碳后期渗碳气氛浓度过低,或渗碳后 冷却及淬火加热时保护不良。
危害:降低了表面硬度和耐磨性,也降低了接触疲 劳强度,淬火时易开裂。
危害:降低表面硬度和接触疲劳、弯曲疲劳 性能,淬火易变形。
消除办法:进行高温回火后,重新加热淬火 或冷处理。
3 黑色组织
所谓黑色组织是指在渗层内的组织中沿晶界出现断续 网状渗碳体及铁素体和黑色的非马氏体组织,其特征颇似 过烧组织。深度约为0.03-0.05毫米左右。 产生原因:出现黑色组织的原因,目前还没有取得一致的看 法。一般认为,可能是由氧化和深层淬透性不足引起的。 危害:降低表面硬度和耐磨性,缩短零件使用寿命。 消除办法:减少氧化性气氛,增加炉子的密封性,排气充分; 同时应加快冷却速度以减少非马氏体体组织的出现。 。
根据分析的数据作出含碳最与离表面距离的分布 曲线,该曲线反映出渗层浓度分布情况。
二、渗碳件常见缺陷
1 渗碳层中有网状或大块状碳化物 2 渗层中有大量的残余奥氏体 3 黑色组织 4 过热 5 表面脱碳 6表面含碳量过低渗层深度不足 7 渗碳层过深 8 渗碳层不均匀 9 表面腐蚀及氧化 10 心部硬度不足 11心部出现过多的铁素体 12反常组织
对严格要求渗层的产品只能报废。
8 渗碳层不均匀
产生原因:零件表面不清洁或积碳,炉温不均,气 氛循环不良或漏气,原材料带状偏析严重。
危害:性能不均,降低使用寿命。 消除办法:补渗 为避免层深增加太多,可适当取低
点的渗碳温度
渗碳
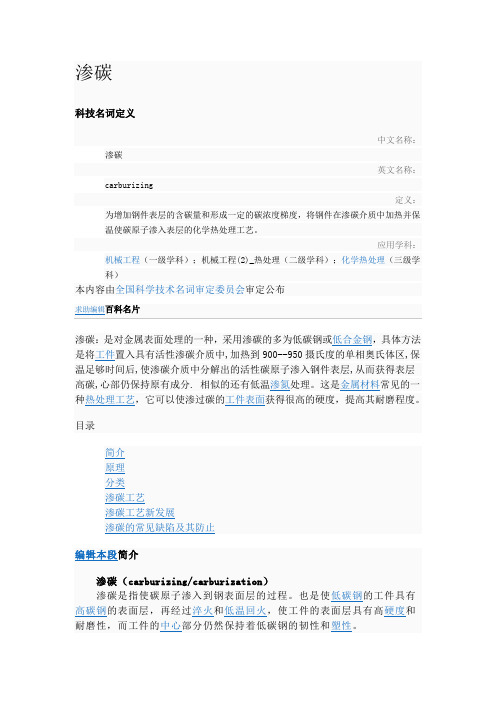
渗碳科技名词定义中文名称:渗碳英文名称:carburizing定义:为增加钢件表层的含碳量和形成一定的碳浓度梯度,将钢件在渗碳介质中加热并保温使碳原子渗入表层的化学热处理工艺。
应用学科:机械工程(一级学科);机械工程(2)_热处理(二级学科);化学热处理(三级学科)本内容由全国科学技术名词审定委员会审定公布编辑本组织及性能特点:不能细化钢的晶粒。
工件淬火变形较大,合金钢渗碳件表面残余奥氏体量较多,表面硬度较低适用范围:操作简单,成本低廉用来处理对变形和承受冲击载荷不大的零件,适用于气体渗碳和液体渗碳工艺。
2 、预冷直接淬火、低温回火,淬火温度800-850℃组织及性能特点:可以减少工件淬火变形,渗层中残余奥氏体量也可稍有降低,表面硬度略有提高,但奥氏体晶粒没有变化。
适用范围:操作简单,工件氧化、脱碳及淬火变形均小,广泛应用于细晶粒钢制造的各种工具。
3、一次加热淬火,低温回火,淬火温度820-850℃或780-810℃组织及性能特点:对心部强度要求较高者,采用820-850℃淬火,心部为低碳M,表面要求硬度高者,采用780-810℃淬火可以细化晶粒。
适用范围:适用于固体渗碳后的碳钢和低合金钢工件、气体、液体渗碳的粗晶粒钢,某些渗碳后不宜直接淬火的工件及渗碳后需机械加工的零件。
4、渗碳高温回火,一次加热淬火,低温回火,淬火温度840-860℃组织及性能特点:高温回火使M和残余A分解,渗层中碳和合金元素以碳化物形式析出,便于切削加工及淬火后残余A减少。
适用范围:主要用于Cr—Ni合金渗碳工件5、二次淬火低温回火组织及性能特点:第一次淬火(或正火),可以消除渗碳层网状碳化物及细化心部组织(850-870℃),第二次淬火主要改善渗层组织,对心部性能要求不高时可在材料的Ac1—Ac3之间淬火,对心部性能要求高时要在Ac3以上淬火。
适用范围:主要用于对力学性能要求很高的重要渗碳件,特别是对粗晶粒钢。
但在渗碳后需经过两次高温加热,使工件变形和氧化脱碳增加,热处理过程较复杂。
渗碳淬火表面缺陷组织照片

图 A 渗碳淬火齿轮齿根处的晶界内氧化(IGO )。
Motion_0576
图B 齿根处的非马组织
(托氏体为主),高温转变组织。
图 C 渗碳淬火表面硬化层中的贝氏体量(高温转变组织,或中间转变产物ITP )
Motion_0576
Motion_0576
说明:
图A 为晶间内氧化,1%Nital 轻浸蚀。
非常常见,但图中太严重了。
图B 为内氧化造成表面层淬透性降低,产生的淬火非马组织(淬火托氏体为主)。
图示的2张照片都严重不合格。
图C 为渗碳层淬火后在表面层和次表面层形成的高温转变组织(贝氏体为主),如果0.30mm 内超过5%就属于不合格。
图示照片上面一张接近合格,下面严重不合格。
形成的原因RCLbbs 中讨论的很多,讲的都基本到位,我这里就不再赘述了。
渗碳件常见缺陷与对策

渗碳件常见缺陷与对策一、渗碳层出现大块状或网状碳化物缺陷产生原因:1、表面碳浓度过高;2、滴注式渗碳,滴量过大;3、控制气氛渗碳,富化气太多;4、液体渗碳,盐浴氰根含量过高;5、渗碳层出炉空冷,冷速太慢;对策:1、降低表面碳浓度,扩散期内减少滴量和适当提高扩散期湿度,也可适当减少渗碳期滴量;2、减少固体渗碳的催碳剂;3、减少液体渗碳的氰根含量;4、夏天室温太高,渗后空冷件可吹风助冷;5、提高淬火加热温度50~80ºC并适当延长保温时间;6、两次淬火或正火+淬火,也可正火+高温回火,然后淬火回火;二、渗层出现大量残余奥氏体缺陷产生原因:1、奥氏体较稳定,奥氏体中碳及合金元素的含量较高;2、回火不及时,奥氏体热稳定化;3、回火后冷却太慢;对策:1、表面碳浓度不宜太高;2、降低直接淬火或重新加热淬火温度,控制心部铁素体的级别≤3级;3、低温回火后快冷;4、可以重新加热淬火,冷处理,也可高温回火后重新淬火;三、表面脱碳缺陷产生原因:1、气体渗碳后期,炉气碳势低;2、固体渗碳后,冷却速度过慢;3、渗碳后空冷时间过长;4、在冷却井中无保护冷却;5、空气炉加热淬火无保护气体;6、盐浴炉加热淬火,盐浴脱氧不彻底;对策:1、在碳势适宜的介质中补渗;2、淬火后作喷丸处理;3、磨削余量,较大件允许有一定脱碳层(≤0.02mm);四、渗碳层淬火后出现屈氏体组织(黑色组织)缺陷产生原因:渗碳介质中含氧量较高:氧扩散到晶界形成Cr、Mn、Si的氧化物,使合金元素贫化,使淬透性降低。
对策:1、控制炉气介质成分,降低含氧量;2、用喷丸可以进行补救;3、提高淬火介质冷却能力;五、心部铁素体过多,使硬度不足缺陷产生原因:1、淬火温度低;2、重新加热淬火保温时间不足,淬火冷速不够;3、心部有未溶铁素体;4、心部有奥氏体分解产物;对策:1、按正常工艺重新加热淬火;2、适当提高淬火温度延长保温时间;六、渗碳层深度不足缺陷产生原因:1、炉温低、保温时间短;2、渗剂浓度低;3、炉子漏气;4、盐浴渗碳成分不正常;5、装炉量过多;6、工件表面有氧化皮或积炭;对策:1、针对原因,调整渗碳温度、时间、滴量及炉子的密封性;2、加强新盐鉴定及工作状况的检查;3、零件应该清理干净;4、渗层过薄,可以补渗,补渗的速度是正常渗碳的1/2,约为0.1mm/h左右;七、渗层深度不均匀缺陷产生原因:1、炉温不均匀;2、炉内气氛循环不良;3、炭黑在表面沉积;4、固体渗碳箱内温差大及催渗剂不均匀;5、零件表面有锈斑、油污等;6、零件表面粗糙度不一致;7、零件吊挂疏密不均;8、原材料有带状组织;对策:1、渗碳前严格清洗零件;2、清理炉内积炭;3、零件装夹时应均匀分布间隙大小相等;4、经常检查炉温均匀性;5、原材料不得有带状组织;6、经常检查炉温、炉气及装炉情况;八、表面硬度低缺陷产生原因:1、表面碳浓度低;2、表面残余奥氏体多;3、表面形成屈氏体组织;4、淬火温度高,溶入奥氏体碳量多,淬火后形成大量残余奥氏体;5、淬火加热温度低,溶入奥氏体的碳量不够,淬火马氏体含碳低;6、回火温度过高;对策:1、碳浓度低,可以补渗;2、残余奥氏体多,可高温回火后再加热淬火;3、有托氏体组织,可以重新加热淬火;4、严格热处理工艺纪律;九、表面腐蚀和氧化缺陷产生原因:1、渗剂不纯有水、硫和硫酸盐;2、气体渗碳炉漏气固体渗碳时催渗剂在工件表面融化,液体渗碳后,工件表面粘有残盐;3、高温出炉,空冷保护不够;4、盐炉校正不彻底,空气炉无保护气氛加热,淬火后不及时清洗;5、零件表面不清洁;对策:1、严格控制渗碳剂及盐浴成分;2、经常检查设备密封情况;3、对零件表面及时清理和清洗;4、严格执行工艺纪律;十、渗碳件开裂缺陷产生原因:1、冷却速度过慢,组织转变不均匀;2、合金钢渗后空冷,在表层托氏体下面保留一层未转变奥氏体在随后冷却或室温放置时,转变成马氏体,比容加大,出现拉应力;3、第一次淬火时,冷却速度太快或工件形状复杂;4、材质含提高淬透性的微量元素(Mo、B)太多等;对策:1、渗后减慢冷却速度,使渗层在冷却过程中完全共析转变;2、渗后加快冷却速度,得到马氏体+残余奥氏体。
渗碳常见的五种缺陷和相应的防止方法

书山有路勤为径,学海无涯苦作舟
渗碳常见的五种缺陷和相应的防止方法
一、碳浓度过高
1、产生原因及危害:假如渗碳时急剧加热,温度又过高或固体渗碳时用全新渗碳剂,或用强烈的催渗剂过多都会引起渗碳浓度过高的现象。
随着碳浓度过高,工件表面出现块状粗大的碳化物或网状碳化物。
由于这种硬脆组织产生,使渗碳层的韧性急剧下降。
并且淬火时形成高碳马氏体,在磨削时容易出现磨削裂纹。
⒉防止的方法
①不能急剧加热,需采用适当的加热温度,不使钢的晶粒长大为好。
假如渗碳时晶粒粗大,则应在渗碳后正火或两次淬火处理来细化晶粒。
②严格控制炉温均匀性,不能波动过大,在反射炉中固体渗碳时需特别注意。
③固体渗碳时,渗碳剂要新、旧配比使用。
催渗剂最好采用47%的BaCO3,不使用Na2CO3 作催渗剂。
二、碳浓度过低
⒈产生的原因及危害:温度波动很大或催渗剂过少都会引起表面的碳浓度不足。
最理想的碳浓度为0.91.0%之间,低于0.8%C,零件容易磨损。
⒉防止的方法:
①渗碳温度通常采用920940℃,渗碳温度过低就会引起碳浓度过低,且延长渗碳时间;渗碳温度过高会引起晶粒粗大。
②催渗剂(BaCO3)的用量不应低于4%。
三、渗碳后表面局部贫碳:。
渗碳齿轮热处理常见缺陷及预防措施
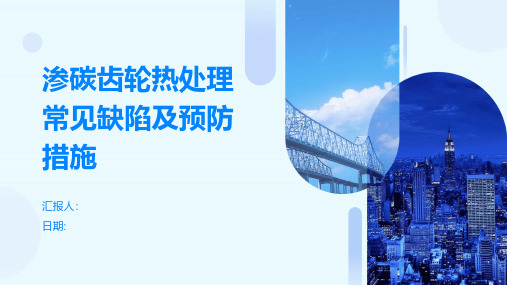
渗碳齿轮热处理常见缺陷及预防措施汇报人:日期:•渗碳齿轮热处理简介•渗碳齿轮热处理常见缺陷•缺陷产生原因分析目•预防措施与建议•结论与展望录渗碳齿轮热处理简介01CATALOGUE渗碳齿轮热处理定义•渗碳齿轮热处理是一种通过向齿轮表面渗入碳元素,然后进行淬火和回火的热处理工艺。
目的是提高齿轮表面的硬度和耐磨性,以满足齿轮传动系统的高强度和高耐久度要求。
5. 后处理清洗、检查、包装等。
4. 回火处理将淬火后的齿轮加热至一定温度,然后缓慢冷却,消除内部应力,提高韧性。
3. 淬火处理将渗碳后的齿轮迅速冷却,提高硬度。
1. 预处理齿轮清洗、除油,确保表面干净。
2. 渗碳处理在一定温度下,将齿轮置于含碳气氛中,使碳元素渗入齿轮表面。
提高齿轮表面硬度:通过渗碳热处理,齿轮表面硬度可大幅提高,从而提高其耐磨性和抗疲劳性能。
延长使用寿命:经过渗碳热处理的齿轮,在承受高负荷和冲击时,不易磨损和断裂,从而延长了齿轮的使用寿命。
请注意,这里只提供了关于渗碳齿轮热处理的简介部分。
如果需要关于其常见缺陷及预防措施的内容,请进一步指明,我会继续为您扩展相应部分。
优化组织结构:通过淬火和回火处理,可以改善齿轮钢的组织结构,使其更加致密,进一步提高其力学性能。
渗碳齿轮热处理常见缺陷02CATALOGUE渗碳过程中温度、时间控制不当,碳浓度不足,导致硬度不达标。
原因影响预防措施硬度不足将降低齿轮的耐磨性和抗疲劳性能,缩短使用寿命。
严格控制渗碳温度、时间和碳浓度,确保渗碳层深度和硬度符合要求。
030201硬度不足淬火过程中温度变化过快,导致内应力过大,产生裂纹。
原因淬火裂纹严重影响齿轮的强度和韧性,增加齿轮断裂风险。
影响优化淬火工艺,控制淬火温度和冷却速度,降低内应力;采用适当的淬火介质,保证齿轮均匀冷却。
预防措施淬火裂纹影响热处理变形会影响齿轮的传动精度和啮合性能,降低齿轮传动效率。
原因热处理过程中温度分布不均,导致齿轮各部分热胀冷缩程度不同,产生变形。
渗碳件的缺陷有哪些及防止措施

渗碳件的缺陷有哪些?如何防止渗碳缺陷?(1)渗碳层中网状或大块花碳化物产生的原因是渗碳碳势太高,使表面渗层含碳量太高合渗碳后冷却速度过慢。
网状碳化物增加了表面脆性,渗层容易剥落,降低使用寿命,容易使零件表面在淬火或磨削加工中产生裂纹。
消除的办法是进行Acm以上的高温淬火或正火。
预防办法是减低炉内碳势,延长扩散时间。
(2)渗碳层中大量残余奥氏体产生的原因是渗碳剂浓度太高使表面含碳量过高、淬火温度太高。
消除的办法是进行高温回火后重新加热淬火+回火或冷处理+回火。
预防措施:降低炉内碳势,选择较低的淬火温度。
淬火剂温度偏高也是原因之一。
淬火剂的温度越低,淬火冷却的终止温度距离马氏体转变终止点Mf也就越近,马氏体转变进行越充分,残余奥氏体就越少。
反之,淬火剂温度高了,则残余奥氏体量也就多了。
(3)反常组织一般在含氧量较高的钢(如沸腾钢)固体渗碳时出现,其特征是网状碳化物和珠光体之间被一层铁素体所分离。
这种组织淬火后易出现软点。
消除的办法是适当提高淬火温度或适当延长淬火加热的保温时间,以便使组织均匀化,并选用更为剧烈的冷却剂淬火。
(4)渗碳零件中形成魏氏组织在高温下进行长时间渗碳后,奥氏体晶粒会急剧长大,碳浓度也大大增加,在随后的缓慢冷却中,二次渗碳体很易于沿奥氏体晶粒的一定晶面析出,形成穿插在晶粒内部的白亮色的粗针,这种组织称为过共析魏氏组织。
产生的原因是长时间过热渗碳和渗碳后冷却太缓慢。
这种组织可通过渗碳后的两次家人淬火予以改善或完全消除。
在渗碳件的心部出现魏氏组织,这种魏氏组织的针状物是先共析铁素体。
形成的原因是:①原材料为本质粗晶粒钢或原始组织中已有魏氏体组织,通过高温长时间渗碳,晶粒会更加粗大,在随后的缓慢冷却中,先共析铁素体以针状自晶界向晶内析出或在晶粒内部单独呈针状析出而形成白亮针状的魏氏组织。
②渗碳工艺不当。
渗碳温度过高,保温时间太长,奥氏体晶粒特别粗大,导致冷却后出现魏氏组织,这种组织具有明显的过热特征。
渗碳齿轮热处理常见缺陷及预防措施

保持热处理过程中温度和冷却速度的稳定性、加强齿轮结构 设计等。
02
预防措施
选用高质量渗碳剂
确保渗碳剂质量
选用由正规厂家生产、质量稳定的渗 碳剂,避免因渗碳剂质量问题导致热 处理缺陷。
查验成分含量
避免混用不同牌号渗碳剂
不同牌号的渗碳剂成分和性能有所差 异,避免混用以免影响热处理效果。
对渗碳剂的成分含量进行严格检验, 确保其符合工艺要求。
渗碳剂的选用和调整
选用
根据齿轮的材质和热处理需求,选择合适的渗碳剂。
调整
根据实际操作情况,对渗碳剂的成分和比例进行适当调整,以确保齿轮能够获得理想的 渗碳效果。
渗碳过程的控制
温度控制
保持渗碳炉内的温度稳定 ,以避免齿轮在渗碳过程 中出现不均匀的温度分布 。
时间控制
渗碳过程应控制在适当的 温度和时间下进行,以确 保齿轮能够充分吸收碳元 素。
淬火过程的控制
温度控制
保持淬火炉内的温度稳定,以避 免齿轮在淬火过程中出现不均匀 的温度分布。
时间控制
淬火过程应控制在适当的温度和 时间下进行,以确保齿轮能够获 得理想的硬度和耐磨性。
冷却控制
淬火后的冷却过程也需严格控制 ,以避免齿轮出现裂纹或其他淬 火缺陷。
04
渗碳齿轮热处理质量检测方法
渗碳层深度检测
预防措施
提高渗碳温度、延长渗碳时间、优化 炉内气氛等。
渗碳层碳浓度不均匀
原因
渗碳层碳浓度不均匀可能是由于渗碳过程中温度波动大、炉内气氛不稳定、渗碳剂分布不均匀等原因引起的。
预防措施
保持渗碳过程中温度稳定、优化炉内气氛、均匀分布渗碳剂等。
齿轮表面粗糙
原因
齿轮表面粗糙可能是由于渗碳后表面残渣未清理干净、热处理过程中氧化脱碳严重等原因引起的。
渗碳淬火的缺陷

渗碳淬火常见缺陷本文是多年从事渗碳淬火的一线工艺人员讲解:工艺流程,渗碳淬火常见缺陷,到积碳如何燃烧,如何定碳,以及炉子的日常保养等。
在热处理实际生产中,往往由于细节的忽略经常导致不良品的出现。
因此热处理工作中要认真负责,将不良品岀现的几率降到最低。
实际生产中的热处理流程如下:来料检验(有无磕碰伤,铁屑,漏工序)一备料(热处理工艺卡,可以拼炉的产品)一一装料(选择正确的装料方式,主要是从变形方而考虑)——淸洗(需要刷涂料的刷涂料防渗,需要螺纹防渗的螺纹防渗)——预氧化(主要是为了使工件表而活化,提髙渗碳速度)——进加热炉(工艺一左要选择正确)一后淸洗——低温回火。
当然随炉试样也要有的。
渗碳淬火常见工艺缺陷:内氧化(IGO),碳化物超标(游离状碳化物,网状碳化物),残余奥氏体超标,渗碳淬硬层中贝氏体数量(NMTP)超标,晶粒粗大,渗碳层淬火后微裂纹, 心部硬度和渗碳深度出现偏差。
内氧化:可控气氛渗破是建立在水煤气反应之上的,CO+H20一CO2+H2,英中C02, H20是有害气体,在高温下极易引起某些以固溶形式存在的合金元素的氧化,在氧化过程中,氧吸附于金属表面然后沿奥氏体晶界向内部扩散,引起晶界合金元素的氧化。
形成内氧化的合金元素是从奥氏体化的固溶体中获得,英结果是靠近氧化物微粒的奥氏体基体中该合金元素减少,造成淬火后内氧化处形成非马组织,降低了工件表面的残余压应力,因此在生产中要避免内氧化的产生。
1. 工件进炉前不能有油,水,锈斑。
2. 合理装炉,保证炉温恢复快,炉气恢复要快,减轻升温阶段内氧化的产生。
3. 严格控制渗碳辅料的质量。
4. 提高淬火温度和淬火冷却介质冷速减轻非马的产生。
5. 渗碳淬火前10-30min通入5-10%NH3也可减缓非马的产生碳化物:碳化物产生主要是由于渗碳碳势高,扩散不好,降温淬火时,在尖角和齿顶部位容易析岀网状和断续网状磯化物。
一旦析出网状碳化物返工也很难消除,因此工艺上一泄要引起注意。
11种渗碳件常见缺陷及防止措施
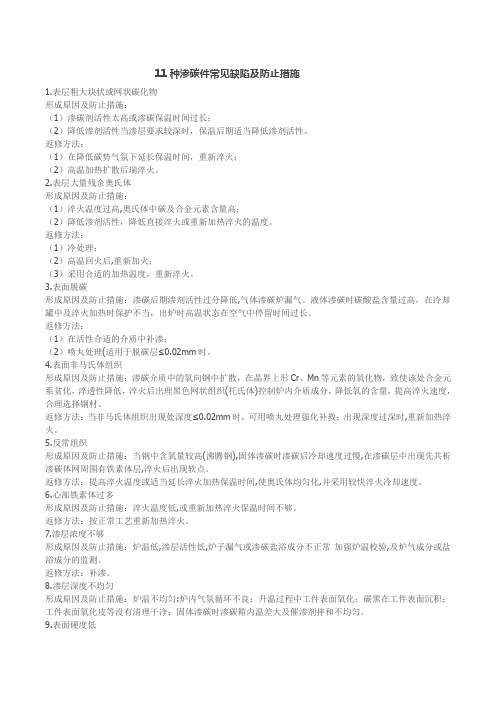
11种渗碳件常见缺陷及防止措施1.表层粗大块状或网状碳化物形成原因及防止措施:(1)渗碳剂活性太高或渗碳保温时间过长;(2)降低渗剂活性当渗层要求较深时,保温后期适当降低渗剂活性。
返修方法:(1)在降低碳势气氛下延长保温时间,重新淬火;(2)高温加热扩散后瑞淬火。
2.表层大量残余奥氏体形成原因及防止措施:(1)淬火温度过高,奥氏体中碳及合金元素含量高;(2)降低渗剂活性,降低直接淬火或重新加热淬火的温度。
返修方法:(1)冷处理;(2)高温回火后,重新加火;(3)采用合适的加热温度,重新淬火。
3.表面脱碳形成原因及防止措施:渗碳后期渗剂活性过分降低,气体渗碳炉漏气。
液体渗碳时碳酸盐含量过高,在冷却罐中及淬火加热时保护不当,出炉时高温状态在空气中停留时间过长。
返修方法:(1)在活性合适的介质中补渗;(2)喷丸处理(适用于脱碳层≤0.02mm时。
4.表面非马氏体组织形成原因及防止措施:渗碳介质中的氧向钢中扩散,在晶界上形Cr、Mn等元素的氧化物,致使该处合金元系贫化,淬透性降低,淬火后出理黑色网状组织(托氏体)控制炉内介质成分,降低氧的含量,提高淬火速度,合理选择钢材。
返修方法:当非马氏体组织出现处深度≤0.02mm时,可用喷丸处理强化补救;出现深度过深时,重新加热淬火。
5.反常组织形成原因及防止措施:当钢中含氧量较高(沸腾钢),固体渗碳时渗碳后冷却速度过慢,在渗碳层中出现先共析渗碳体网周围有铁素体层,淬火后出现软点。
返修方法:提高淬火温度或适当延长淬火加热保温时间,使奥氏体均匀化,并采用较快淬火冷却速度。
6.心部铁素体过多形成原因及防止措施:淬火温度低,或重新加热淬火保温时间不够。
返修方法:按正常工艺重新加热淬火。
7.渗层浓度不够形成原因及防止措施:炉温低,渗层活性低,炉子漏气或渗碳盐浴成分不正常加强炉温校验,及炉气成分或盐浴成分的监测。
返修方法:补渗。
8.渗层深度不均匀形成原因及防止措施:炉温不均匀:炉内气氛循环不良;升温过程中工件表面氧化;碳黑在工件表面沉积;工件表面氧化皮等没有清理干净;固体渗碳时渗碳箱内温差大及催渗剂拌和不均匀。
气体渗碳的常见缺陷和预防措施

櫡櫡櫡櫡櫡櫡櫡櫡~现场经验櫡櫡櫡櫡櫡櫡櫡櫡~收稿日期:2020 01 14作者简介:赵步青(1943—),男,江苏阜宁人,高级工程师,研究方向为工模具热处理工艺,已发表论文和实用性文章共270余篇,出版热处理专著5部,协编图书两部。
联系电话:15067596339;E mail:zsg4272@163.com气体渗碳的常见缺陷和预防措施赵步青,朱 敏,高旭华,徐利建(浙江省金华市华南汽配有限公司,浙江金华321000)中图分类号:TG157 文献标志码:B 文章编号:1008 1690(2020)02 0048 03CommonDefectsforGasCarburizingandPreventiveMeasuresZHAOBuqing,ZHUMin,GAOXuhua,XULijian(ZhejiangJinhuaHuananAutomobiveFittingsCo.,Ltd.,Jinhua321000,ZhejiangChina)0 引言气体渗碳是制造业应用最广泛的化学热处理工艺。
渗碳并淬火和低温回火的低碳钢工件表面硬度和疲劳强度高、耐磨性好,且心部具有足够的强度和韧性。
华南汽配公司是生产汽车防滑链的民营企业,大部分产品都要进行气体渗碳。
渗碳炉有网带炉、井式炉和滚筒炉,产品质量稳定。
本文为生产实践经验的总结,介绍30多年来遇到的以及同行提供的常见的12种气体渗碳缺陷,供参考。
1 粗大针状马氏体通常,设计人员对渗碳件淬火后渗层的马氏体都会提出级别要求。
对于汽车防滑链,要求其渗碳层马氏体针≤4级。
图1为由于渗碳温度过高和炉气氛碳势较高造成的渗层粗大马氏体组织。
为了防止产生这种缺陷,必须调整渗碳气氛的碳势,降低渗碳温度,加强炉前的抽样检查。
2 网状碳化物根据经验,碳化物的形态、数量、大小及分布对渗碳件的性能有很大影响。
图2为渗碳层中严重的网状碳化物。
其产生的原因有3点:①滴注式渗碳时,煤油或其他渗剂滴量太大;②控制气氛渗碳的富化气用量太大;③渗碳后直接淬火的温度过高且冷却较慢。
渗碳件的常见缺陷及预防措施

一
测 试与 分析 一
渗 碳 件 的 常 见 缺 陷 及 预 防 措 施
于娜红 , 余 成 龙
( 中国第一汽车股份有 限公 司无锡 油泵油嘴研 究所, 江 苏 无锡 2 1 4 0 6 3 )
摘
要 :渗碳 零件 的 常见缺 陷有 黑 色组 织、 渗层 大块 状或 网状碳 化 合物 、 渗层 不 均 匀和 畸 变过 大 等 。这 些缺 陷 的产生 与渗碳 气氛 的成分 和均 匀性 、 渗碳 操 作 、 工件 的装 炉 方式 、 渗碳 后 的淬 火工 艺和操 作 等 多 种 因素 中的一种 或 几种 有关 。采取 某 些相应 的措 施 可 以预 防这 些缺 陷的产 生。
f a c t o r s wh i c h i n c l u de c o mp o s i t i o n a n d u n i f o r mi t y o f e a r b u r l z i n g a t mo s p he r e, o p e r a t i o n o f c a r bu r i z i n g, c ha r g i冷时 , 表层为过共析
层, 是细 密珠 光体加 颗 粒状 均匀 分布碳 化 物 ; 次 表层 为共 析层 , 属 细密珠光体组织 ; 内层 为 亚 共 析 过 渡
气 中的氧发 生 内氧化 。炉 气 中氧原 子吸 入钢 中 向内 扩散 , 在 晶界形 成 C r 、 Mn 、 T i 、 S i 等 的氧 化物 , 造 成 晶 界处 合金元 素 贫乏 , 此处 淬透 性低 , 渗碳 时表层 形成
YU Na h o n g .YU C h e n g l o n g
渗碳件常见的缺陷及防止和补救措施
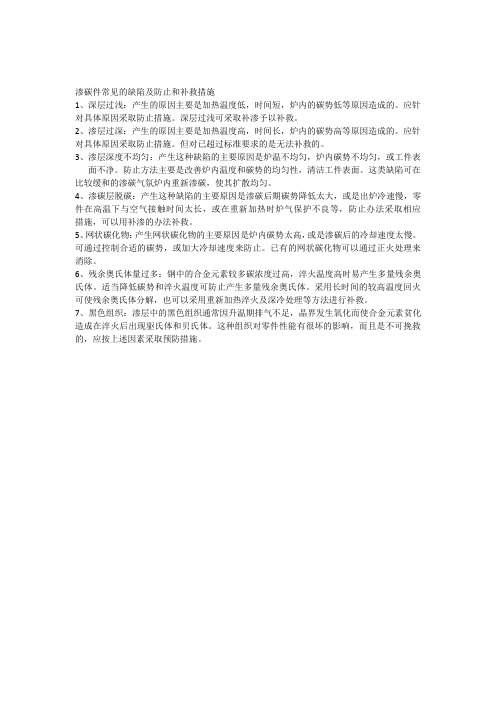
渗碳件常见的缺陷及防止和补救措施
1、深层过浅:产生的原因主要是加热温度低,时间短,炉内的碳势低等原因造成的。
应针对具体原因采取防止措施。
深层过浅可采取补渗予以补救。
2、渗层过深:产生的原因主要是加热温度高,时间长,炉内的碳势高等原因造成的。
应针对具体原因采取防止措施。
但对已超过标准要求的是无法补救的。
3、渗层深度不均匀:产生这种缺陷的主要原因是炉温不均匀,炉内碳势不均匀,或工件表面不净。
防止方法主要是改善炉内温度和碳势的均匀性,清洁工件表面。
这类缺陷可在
比较缓和的渗碳气氛炉内重新渗碳,使其扩散均匀。
4、渗碳层脱碳:产生这种缺陷的主要原因是渗碳后期碳势降低太大,或是出炉冷速慢,零件在高温下与空气接触时间太长,或在重新加热时炉气保护不良等,防止办法采取相应措施,可以用补渗的办法补救。
5、网状碳化物:产生网状碳化物的主要原因是炉内碳势太高,或是渗碳后的冷却速度太慢。
可通过控制合适的碳势,或加大冷却速度来防止。
已有的网状碳化物可以通过正火处理来消除。
6、残余奥氏体量过多:钢中的合金元素较多碳浓度过高,淬火温度高时易产生多量残余奥氏体。
适当降低碳势和淬火温度可防止产生多量残余奥氏体。
采用长时间的较高温度回火可使残余奥氏体分解,也可以采用重新加热淬火及深冷处理等方法进行补救。
7、黑色组织:渗层中的黑色组织通常因升温期排气不足,晶界发生氧化而使合金元素贫化造成在淬火后出现驱氏体和贝氏体。
这种组织对零件性能有很坏的影响,而且是不可挽救的,应按上述因素采取预防措施。
- 1、下载文档前请自行甄别文档内容的完整性,平台不提供额外的编辑、内容补充、找答案等附加服务。
- 2、"仅部分预览"的文档,不可在线预览部分如存在完整性等问题,可反馈申请退款(可完整预览的文档不适用该条件!)。
- 3、如文档侵犯您的权益,请联系客服反馈,我们会尽快为您处理(人工客服工作时间:9:00-18:30)。
渗碳后期渗剂活性过分降低,气体渗碳 炉漏气。液体渗碳时碳酸盐含量过高。 在冷却罐中及淬火加热时保护不当,出 炉时高温状态在空气中停留时间过长。 渗碳介质中的氧向钢中扩散,在晶界上 形成cr,mn等元素的氧化物,致使该处合 金元素贫化,淬透性降低,淬火后出现 黑色网状组织(托氏体) 控制炉内介质成分,降低氧的含量,提 高淬火冷却速度,合理选择钢材。 当钢中含氧量较高(沸腾钢),固体渗 碳时渗碳后冷却速度过慢,在渗碳层中 出现先共析渗碳体网周围有铁素体层, 淬火后出现软体 淬火温度低,或重新加热淬火保温时间 不够 炉温低,渗层活性低,炉子漏气或渗碳 盐浴成分不正常加强炉温校验,及炉气 成分或盐浴成分的监测 炉温不均匀;炉内气氛循环不良;升温 过程中工件表面氧化;碳黑在工件表面 沉积;工件表面氧化皮等没有清理干净 ;固体渗碳时渗碳箱内温差大及催渗剂 拌和不均匀 表面碳浓度低或表面脱碳;残余奥氏体 量过多,或表面形成托氏体网
渗碳件常
缺陷形式
表层粗大块状或网 状碳化物
表层大量残余奥氏 体
形成原因及防止措施
渗碳剂活性太高或渗碳保温时间过长 降低渗剂活性当渗层耍求较深时,保温 后期适当降低渗剂活性
淬火温度过高,奥氏体中碳及合金元素 含量较高。降低渗剂活性,降低直接淬 火或重新加热淬火的温度
表面脱碳 表面非马氏体组织
反常组织 心部铁素体过多 渗层深度不够 渗层深度不均匀
提高淬火温度或适当延长淬火 加热保温时间,使奥氏体均匀 化,并采用较快淬火冷却速度
按正常工艺重新加热淬火
补渗
1,表面碳浓度低者可进行补渗 2,残余奥氏体多者可采用高温 回火或淬火后补一次冷处理消 除残余奥氏体 3,表面有托氏体者可重新加热 置时产生 表面裂纹
渗剂中含有硫或硫酸盐,催渗剂在工作 表面熔化;液体渗碳后工作表面粘有残 有氧化皮工件涂硼砂重新加热淬火等 均引起腐蚀 工件高温出炉保护不当均引起氧化 应仔细控制渗剂及盐浴成分,对工作 表面及清理及清洗
渗碳后慢冷时组织转变不均匀所致,如 18crmnmo钢渗碳后空冷时,在表面托氏 体下面保留了一层未转变的奥氏体,后 者在随后的冷却过程中或室温停留过程 中转变为马氏体,使表面产生拉应力而 出现裂纹 减慢冷却速度,使渗层完成共析转变, 或加快冷却速度,使渗层全部转变为 马氏体加残余奥氏体
返修方法
1,在降低碳势气氛下延长保 温时间重新淬火 2,高温加热扩散后再淬火 1,冷处理 2,高温回火后,重新加热淬火 3,采用合适的加热温度,重 新淬火 1,在活性合适的介质中补渗 2,喷丸处理(适用于脱碳层 〈=0.02mm时
当非马氏体组织出现处深度 〈=0.02mm时,可用喷丸处理 强化补救 出现深度过深时,重新加热 淬火