车身材料铆接工艺 SPR FDS
车身异种金属连接SPR连接技术

Tool Changer品牌 Walther,Staubli
如果采取换枪的方式,则在在整个CT里面每次换枪时需要额外4+4=8 秒(放/拿)的时间
SPR Matrix—设备
设备接口标准、公用动力要求: 无特别要求
设备易损件寿命
SPR Matrix—设备
设备维修保养
SPR Matrix—设备
Self Piercing Rivet 自冲铆接
一 工艺 1、定义 2、工艺的优缺点 3、基本的设计标准 4、工艺参数 5、供应商及运用
二 设备 1、工艺运用方式 2、系统构成 3、焊枪种类 4、送钉类型 5、柔性 6、易损件 7、公用动力 8、保养
SPR Matrix—工艺
简介:自冲铆接工艺是一个在铆钉与板料之间形成牢固互锁的冷成型工艺。
3. 不同材质铆接原则: 薄板铆向厚板,硬材质铆向软材质(steel->Al) 底层板材的厚度必须大于铆点总厚度的1/3
SPR Matrix—工艺
工艺要求MR接头设计要求
SPR Matrix—工艺
工艺要求MR铆接翻边设计要求
SPR Matrix—工艺
工艺开发过程优化选择rivet,模具,C-Frame
RSW电阻点焊强度 3. 单步工艺 4. CT时间短 2s (纯铆接时间) 5. 能耗低,绿色工艺 6. 工艺质量可以过程自监控
SPR Matrix—工艺
缺点:SPR工艺的局限性
1. 连接点处需要保留双侧的进枪空间 2. 通常不同的材质、厚度、硬度的接头组合需要不同的铆钉、
冲头冲模 3. 铆钉成本的piece cost 0.08Euro/Rivet 4. 设备系统成本远高于电阻点焊 800K人民币/system 5. 铆接点凸起约2-3mm 6. 只能使用C型铆接枪
焊装结构胶对铝车身连接工艺的影响
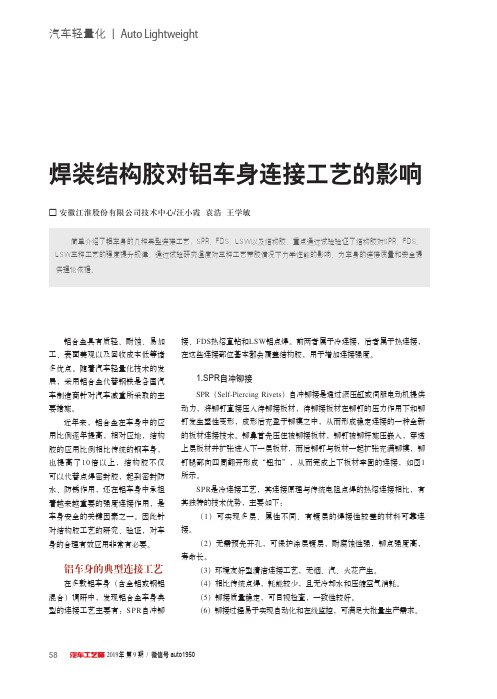
2. FDS热熔直钻FDS(Flow Dirll Screwing)即流钻螺钉,通过高速旋转及轴向下压力使工件发生塑性变形,螺钉穿透工件,形成圆柱形通道,它的工作过程分成6步:将高转速和气缸产生的高气压传导至材料表面使材料产生塑性变形(定位预热过程)→流动钻孔成型(热融穿透过程)→圆柱形通道成型(锥孔成型过程→自攻完全啮合的螺纹(螺纹成型过程)→正常螺钉拧紧(螺钉拧入过程)→拧紧至设定的转矩(紧固落座过程)。
具体如图2所示。
FDS是单面连接工艺,连接设备相对简单,对工件的要求也较为宽松,这种连接工艺主要技术优势如下:(1)单面进入工件,无需前置工作,有无预留孔都可连接。
(2)可连接不同的材料及多于两层板的连接,如型材、铸铝件等多种轻量化材料。
(3)充分利用材料本身,不会像焊接那样引起材料热形变,无公差问题。
(4)高拉出力,高破坏扭矩以及好的抗震能力。
(5)可作为临时连接,易拆除易修复,并且可用为标准螺纹孔。
(6)可与胶同用,水、气密性好。
3. LSW铝点焊LSW(AL Spot Welding点焊,即铝合金板材搭接的电阻点焊,通过电极压紧板件,利用电阻热熔化金属,铝合金板材与钢板相比,由于有较高的比热容焊时需要更多的热能进行加热,而其较高的导热性和高导电率,极易导致热量的快速流失,不易产生足够的电阻热来熔化板材,使得铝的电阻点焊比钢的电阻电焊困难。
为了解决铝点焊的上述问题,一般采用中频直流变压器,输出大电流或者增加电极带,提高接触电图1 SPR铆接步骤1.铆模2.板材3.铆杆4.铆鼻5.铆钉图2 FDS铆接步骤(a)不带胶(剪切) (b)带胶(剪切) (c)不带胶(剥离) (d)带胶(剥离) 图3 剪切剥离实验图片(a)各温度下剪切力力值(5组)(b)各温度下拉伸力力值(5组)图4 6111_3+6111_3不同温度下LSW力学性能示意(a)各温度下剪切力力值(5组)(b)各温度下拉伸力力值(5组)图5 E170_0.9+6111_1.5+6111_2不同温度下LSW力学性能示意于30℃,其稳定性和30℃无明显差异。
轻量化车身设计-铝合金车身连接工艺
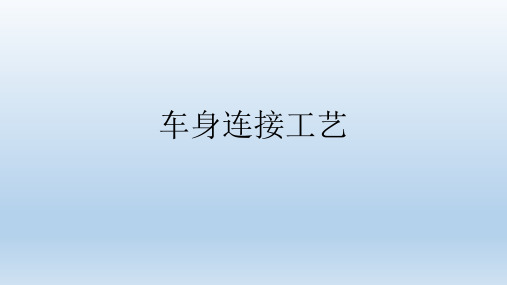
5182
冲压件
M6
1
5182
冲压件
M6
1.2
5182
冲压件
M6
1.4
6005A T6
型材
M6
1.5
5182
冲压件
M6
1.5
6005A T6
型材
M6
2
5182
冲压件
M6
3
6005A T6
型材
M8
1.5
5182
冲压件
M8
2
5182
冲压件
M8
2.3
5182
冲压件
M10
3
6005A T6
型材
/
/
/
/
螺栓
板厚(mm)
材料
种类
备注
M6*16
1.2
5182
冲压件
M8*25
1.2
5182
冲压件
二、铝车身连接工艺:FDS
• 简介:FDS攻丝铆接工艺是通过高速旋转使板料变形后攻丝铆接的冷成型工艺
• 1.高速速(最高可达500转/分钟)和高压(最高可达1500N)的物料将被加热
• 2.推进材料(流动钻成型)
• 3.会形成圆柱形
但会使用特殊类型铆钉,铆接实现困难较大。
工艺过程图解
5、SPR位置要求
• 铆接对板材重合面长度、板材边缘到铆钉距离、翻边到底模距离。为了保证铆接效果,铆接位置 遵守的尺寸要求如下
描述
钉类型 S (板材重合面长度)
Ø RIVET [mm]
5.3 3.35
≥ 18
≥ 16
铆接位置要求
S (板材重合面长度)备注: 针对脆性材料如珠履 ≥ 30
“流钻螺钉”(FDS)工艺
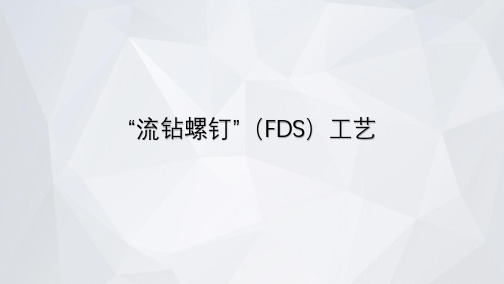
BMW 8 Series Coupe
Jaguar I-PACE
五、 FDS工艺的优、缺点
优点: 1、可连接的材料种类多,包括超高强钢、铝镁合金、复合材料在内 的异种材料; 2、单面操作,可用于封闭型腔结构、壁厚大或封闭腔体,无法使用 SPR或Clinching; 3、板件被加热,板件与螺钉接触好,连接强度大。 4、 螺钉可拆卸,回收方便,可使用公制螺栓进行返修。 5、工作环境清洁,无火花、碎屑,几乎无噪声。 缺点 1、设备系统成本远高于电阻点焊,铆钉成本高(单价 0.15 欧元) ; 2、单面施力,连接时需要高强度刚性支撑; 3、工艺完成后材料正反面均有较大凸起,同时大量使用会增加车身 自重(M5单个螺钉重4~5g,而SPR铆钉约0.3~0.8g) 4、CT时间长,约为2~6S(部分设备优化可达到1.5~3S,取决于板材 厚度)
六、FDS常见缺陷:
Hale Waihona Puke 缺失/位置错误螺栓断裂/破损
边距过小
头部间隙
FDS返修方法: 在缺陷螺钉附近重新打一个螺钉。
七、设备系统组成:
4.
2.
FDS两种标准枪
Standard Length
Reduced Length
二、 FDS工艺历史
FDS发明于1990年,1996年首次应用于莲花轿车车身框架的连接。由于当时采用的主 要是手持夹具进行装夹,整个装配过程的时间和精度不好控制,使得该工艺使用受到限 制。 20世纪90年代末,巍博(Weber)为EJOT公司开发了RSF20S螺钉驱动系统,此系 统的问世实现了FDS工艺的自动化生产,并可以增大连接的板材总厚度,于2000年首次 应用在奥迪A4后轮罩的连接上。
三、 FDS工艺的过程
FDS连接工艺过程包括六个阶段:旋转(加热)→穿透→通孔→攻螺纹→拧螺纹→紧固。
浅析钢铝车身先进连接工艺

浅析钢铝车身先进连接工艺发布时间:2022-06-29T08:26:05.299Z 来源:《中国科技信息》2022年5期作者:苏华,安珂,李金山[导读] 汽车车身的连接设计与制造是汽车生产中的重要环节,也是汽车生产新技术研究的主要内容。
文章主要阐述了汽车车身相关连接设计方法及过程中的讲解应用。
苏华,安珂,李金山(奇瑞用车(安徽)有限公司,安徽芜湖 241000)摘要:汽车车身的连接设计与制造是汽车生产中的重要环节,也是汽车生产新技术研究的主要内容。
文章主要阐述了汽车车身相关连接设计方法及过程中的讲解应用。
关键词:车身;连接设计;新技术前言:低碳环保、安全节能、智能化、轻量化是汽车行业发展趋势,车身连接设计开发与制造是整车开发重要组成部分。
随着中国汽车保有量的不断增加,汽车增速逐渐放缓,更新换代周期越来越短,汽车市场的竞争也越来越激烈,如何提高车身的连接设计及制造水平,提升产品竞争力是当前研究的热点。
1、汽车车身连接设计技术为保证整车结构刚度及安全性能要求,采用了以轻质铝合金材料为主,超高强度钢板为辅的钢铝混合车身结构。
整车铝合金比例达到88%。
在钢铝混合车身结构连接设计时,大量使用了钢铝混合车身连接工艺:自冲铆接(SPR)、自攻螺接(FDS)、螺栓连接、压铆、拉铆等冷连接工艺以及铝点焊、激光焊、铝弧焊、铝螺柱焊等热连接工艺。
汽车在使用钢铝混合车身。
2、钢铝车身连接方式分:焊接:CMT(冷金属过渡电弧工艺)、?Deltaspot 电极带式电阻点焊铆接:SPR、FDS、压力铆3、CMT(冷金属过渡电弧工艺)CMT定义及工艺流程CMT冷金属过渡技术是在短路过渡基础上开发的,但同普通GMAW不同的是,送丝不是一成不变的往前送,焊丝不仅会向前送丝,而且还有往回抽的动作。
其焊接过程是:电弧燃烧,加热工件和熔化焊丝,同时焊丝往前送,直到形成的熔滴同工件接触,在这一刻,焊机将焊接电流降至几乎为零,同时枪头处的伺服马达倒转,焊丝往回抽,通过机械方式将熔滴从焊丝端分离,实现熔滴向焊缝处过渡。
新能源铝制车身SPS铆接设备技术要求
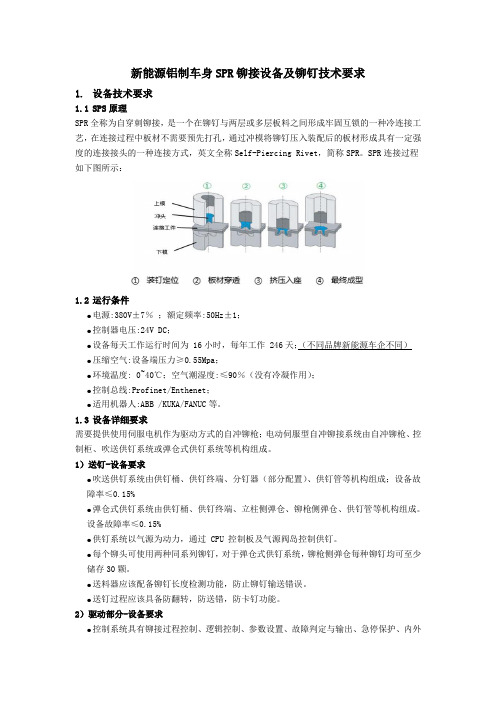
新能源铝制车身SPR铆接设备及铆钉技术要求1.设备技术要求1.1SPS原理SPR全称为自穿刺铆接,是一个在铆钉与两层或多层板料之间形成牢固互锁的一种冷连接工艺,在连接过程中板材不需要预先打孔,通过冲模将铆钉压入装配后的板材形成具有一定强度的连接接头的一种连接方式,英文全称Self-Piercing Rivet,简称SPR。
SPR连接过程如下图所示:1.2运行条件●电源:380V±7%;额定频率:50Hz±1;●控制器电压:24V DC;●设备每天工作运行时间为 16小时,每年工作 246天;(不同品牌新能源车企不同)●压缩空气:设备端压力≥0.55Mpa;●环境温度: 0~40℃;空气潮湿度:≤90%(没有冷凝作用);●控制总线:Profinet/Enthenet;●适用机器人:ABB /KUKA/FANUC等。
1.3设备详细要求需要提供使用伺服电机作为驱动方式的自冲铆枪;电动伺服型自冲铆接系统由自冲铆枪、控制柜、吹送供钉系统或弹仓式供钉系统等机构组成。
1)送钉-设备要求●吹送供钉系统由供钉桶、供钉终端、分钉器(部分配置)、供钉管等机构组成;设备故障率≤0.15%●弹仓式供钉系统由供钉桶、供钉终端、立柱侧弹仓、铆枪侧弹仓、供钉管等机构组成。
设备故障率≤0.15%●供钉系统以气源为动力,通过 CPU 控制板及气源阀岛控制供钉。
●每个铆头可使用两种同系列铆钉,对于弹仓式供钉系统,铆枪侧弹仓每种铆钉均可至少储存30颗。
●送料器应该配备铆钉长度检测功能,防止铆钉输送错误。
●送钉过程应该具备防翻转,防送错,防卡钉功能。
2)驱动部分-设备要求●控制系统具有铆接过程控制、逻辑控制、参数设置、故障判定与输出、急停保护、内外部系统通信等功能。
●铆接速度≥200mm/s,铆接压力需≥80KN,具有连续可调、稳定性高等特点,最小调整精度 1mm/s。
压力精度±0.1KN,位移精度 0.01mm。
铝车身连接工艺方法大全
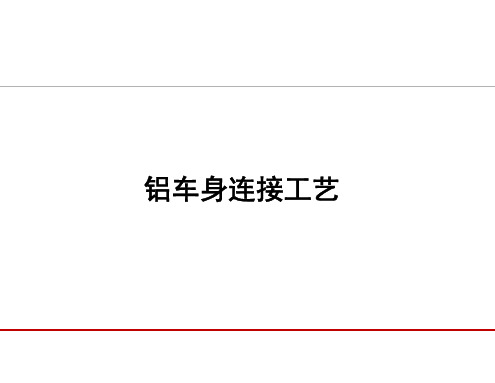
2、普通铝点焊 只能焊接铝+铝 薄板, 不能焊接铝+钢;
2、铝点焊相比其它几种铝连接方法,焊接效率高,成本低,无需增加铆钉或焊丝 等填充材料。
铝车身连接工艺— 5、DeltaSpot电阻焊
1、 DeltaSpot电阻焊焊接形式
3、 DeltaSpot电阻焊焊接对钣件要求
焊接形式与普通点焊相同,焊接空间与普通点焊相同,焊接翻边宽度比普 通点焊略宽
通用CT6铝车身 FDS 钢+铝连接 奥迪铝车身 FDS应用
铝车身连接工艺— 3、冷金属过渡CMT焊接
1、冷金属过渡CMT焊接形式
CMT焊 接过程
3、冷金属过渡CMT焊接对钣件要求
CMT焊接方式同MIG焊(熔化极电弧焊),都属于弧焊,CMT焊接过程电流控 制更好,飞溅小,更容易焊接薄铝板,对钣件间装配间隙要求更低,焊接质量更 好。
板料B,被铆钉部分刺穿
2、自穿铆接SPR设备
与普通点 焊类似
送料机 控制器 铆接枪
SPR机器人系统 SPR自动化线
4、SPR特点及优点
1、可铆接多层铝板,板材总厚度:1.5mm~16mm,底层板材延展率:大于12% 2、自冲铆接头的疲劳寿命远高于点焊接头; 3、可实现钢+铝的连接,板材硬度:不大于14MPA UHSS 4、每一个连接点需要消耗一颗铆钉(增加车身重量)
AL板
铝+铝 CMT焊
Fe板
铝+铝 CMT焊
铝车身连接工艺— 3、冷金属过渡CMT焊接
5、冷金属过渡CMT焊接应用示例
特斯拉 铝车身CMT焊接(侧围)
通用CT6铝车身CMT焊 奥迪A8铝车身CMT焊
铝车身连接工艺— 4、普通铝点焊
1、普通铝点焊焊接形式
白车身FDS连接技术浅谈
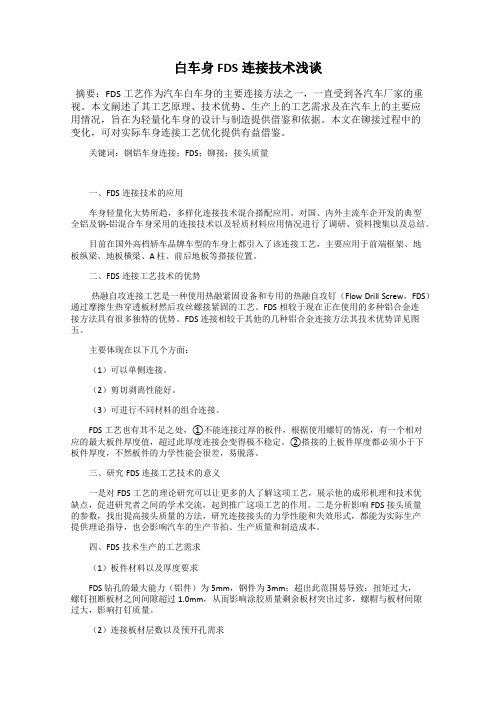
白车身FDS连接技术浅谈摘要:FDS工艺作为汽车白车身的主要连接方法之一,一直受到各汽车厂家的重视。
本文阐述了其工艺原理、技术优势、生产上的工艺需求及在汽车上的主要应用情况,旨在为轻量化车身的设计与制造提供借鉴和依据。
本文在铆接过程中的变化,可对实际车身连接工艺优化提供有益借鉴。
关键词:钢铝车身连接;FDS;铆接;接头质量一、FDS连接技术的应用车身轻量化大势所趋,多样化连接技术混合搭配应用。
对国、内外主流车企开发的典型全铝及钢-铝混合车身采用的连接技术以及轻质材料应用情况进行了调研、资料搜集以及总结。
目前在国外高档轿车品牌车型的车身上都引入了该连接工艺,主要应用于前端框架、地板纵梁、地板横梁、A 柱、前后地板等搭接位置。
二、FDS连接工艺技术的优势热融自攻连接工艺是一种使用热融紧固设备和专用的热融自攻钉(Flow Drill Screw,FDS)通过摩擦生热穿透板材然后攻丝螺接紧固的工艺。
FDS相较于现在正在使用的多种铝合金连接方法具有很多独特的优势。
FDS连接相较于其他的几种铝合金连接方法其技术优势详见图五。
主要体现在以下几个方面:(1)可以单侧连接。
(2)剪切剥离性能好。
(3)可进行不同材料的组合连接。
FDS工艺也有其不足之处,①不能连接过厚的板件,根据使用螺钉的情况,有一个相对应的最大板件厚度值,超过此厚度连接会变得极不稳定。
②搭接的上板件厚度都必须小于下板件厚度,不然板件的力学性能会很差,易脱落。
三、研究FDS连接工艺技术的意义一是对FDS工艺的理论研究可以让更多的人了解这项工艺,展示他的成形机理和技术优缺点,促进研究者之间的学术交流,起到推广这项工艺的作用。
二是分析影响FDS接头质量的参数,找出提高接头质量的方法,研究连接接头的力学性能和失效形式,都能为实际生产提供理论指导,也会影响汽车的生产节拍、生产质量和制造成本。
四、FDS技术生产的工艺需求(1)板件材料以及厚度要求FDS 钻孔的最大能力(铝件)为5mm,钢件为3mm;超出此范围易导致:扭矩过大,螺钉扭断板材之间间隙超过1.0mm,从而影响涂胶质量剩余板材突出过多,螺帽与板材间隙过大,影响打钉质量。
汽车铝合金焊接新技术

汽车铝合金焊接新技术摘要:铝合金具有密度低、比强度高、耐腐蚀等综合性能,使得铝合金成为航空、铁路运输、建筑等许多制造行业的一种重要金属材料。
并且,随着我国汽车产业的发展,无论是安全性能还是节能减排,可提高汽车整体强度,使得铝合金成为汽车轻量化的重要材料之一。
因此,铝合金焊接技术已成为汽车制造业的基本工艺之一,本文主要对汽车铝合金车身焊接新工艺和新方法进行了探讨和分析研究。
关键词:汽车;铝合金;焊接技术引言近年来,由于节能环保的要求日益严格,汽车轻量化便已成为世界汽车发展的必然趋势。
对于燃油车辆,车身质量每下降10%,燃料效率就可以提高6%-8%;对于纯电动车辆,车身质量减轻100公斤,汽车续航可提高10%。
车身质量约占汽车总质量的40%,车身轻量化最重要的是使用铝合金材料。
铝密度仅为钢密度的1/3,具有良好的塑性和可回收性,是汽车轻量化的理想材料之一。
铝合金车身比钢制车身具有更高的连接技术要求和更高的技术难度,而铝合金点焊(RSW)、自冲铆接(SPR)、自攻热铆接(FDS)、激光焊接(LW)等技术在连接过程中是铝合金车身常用的连接方法,与其他几种连接方法相比,铝点焊具有设备投资低、无需使用辅助材料、适配板的柔性厚度以及连接后板材表面没有较高的间隙等优点,正被越来越多的汽车厂家所使用。
1汽车制造中铝合金焊接技术概述一方面,由于全球能源紧张等因素,汽车燃料消费受到越来越多的关注,因此,汽车轻量化已成为大型汽车企业产品设计的重点。
作为轻型发展系统的一部分,轻型金属,如中高端钢结构、铝和铝合金结构、镁和镁合金结构,将逐步取代在轻型汽车车身系统中广泛使用传统钢结构,这是因为铝的重量比钢结构少60%,相较于传统的钢结构,车身实际上可以减少45%以上的总重量,而且铝和铝合金在承受同样的冲击强度时可以吸收更高的冲击能量。
另一方面,基于节能环保的发展理念,铝合金是符合节能降耗要求的更加环保的应用材料,铝合金零部件回收率较高。
铝车身连接工艺介绍、铝连接技术介绍
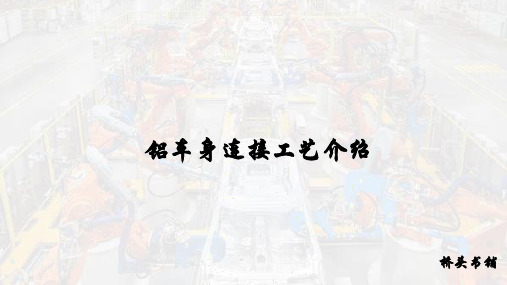
铝车身的连接方法— (2)流钻工艺FDS
19
铝车身的连接方法— (2)流钻工艺FDS
20
1.FDS工艺形式:
热熔自攻丝FDS 过程示意
FDS剖切图
(无预转孔连接)
“流钻螺钉”工艺,(别称:热熔自攻丝/热熔紧固系统), 英文有两种翻译:Flow drill screws(FDS) Flow Form screws(FFS)
30
4. Clinch/TOX连接特点:
优点:
1、可不同板材连接 2、无耗材 3、对产品连接表面没有特殊要求 4、不会损伤产品表面镀层 5、几乎无噪音、无火花碎屑等污染;
缺点:
1、设备成本较高 2、TOX连接强度较弱,车身上主要应用 在门盖内外板连接,以及压铆部分螺母 3、空间需求较大 4、凹凸面明显
螺接、涂 胶、激光
焊等
图示实 例
工艺特点
应用 案例
备注
属于弧焊(MIG焊),焊接温度较低, 接头变形小,结构强度低。
通用CT6, 奥迪,前 保险杠。
CMT焊机属于瑞典福尼斯专利设 备
焊接形式同钢板点焊;焊接电流超大 30~50KA;只能焊接厚度小于2mm 通用CT6 铝点焊应用较少 的薄铝板,效率高,无耗材,成本低。
TOX铆接机器人系统
TOX铆枪
铝车身的连接方法— (3)Clinch/TOX连接
29
3. Clinch/TOX对钣件要求:
1. 铆接处不能含脆性材料(如玻 璃、脆性塑料)
2. 两层板连接 3. 薄板连接
连接点一般在平板搭接处,夹具设计及钣件设计需考虑TOX铆枪空 间。
铝车身的连接方法— (3)Clinch/TOX连接
铝车身的连接方法— (2)流钻工艺FDS
SPR-工艺介绍

Rivets are made from heat-treated carbon steel, with a complex mechanically applied alloy coating to prevent corrosion when used in Al structure.
特殊热处理碳钢材质, 应用到Al连接结构时 其表面有复杂的机械 合金涂层处理(防止 Al-Steel电化学腐蚀)
Self Piercing Rivet 自冲铆接
简介:自冲铆接工艺是一个在铆钉与板料之间形成牢固互锁的冷成型工艺。
Cycle Initiation
Nose Contact
Rivet Inserting Setting Flush
Tool Retract
铆钉:车身通常的铆钉有3mm,5mm两个系列
ห้องสมุดไป่ตู้
Manual System 自动送钉,必须保 证枪体垂直,通常 要求工件旋转
设备应用柔性、互换性
同一系列(同直径)不同长度铆钉可以用一把枪铆接 使用不同送钉器
不同系列铆钉可以通过Magazine Fill系统,使用不同的枪铆接 换枪盘上装不同规格送钉管,不同送钉器
设备应用柔性、互换性
不同铆接枪之间的互换:最多3枪互换 Tool Changer品牌:Walther,Staubli SPR跟其他应用互换:Gripper,FDS
2. 底层材料(die侧)可以是钢板或者铝板,如果是铝 型材或铸铝其延伸率必须大于12%
3. 不同材质铆接原则: 薄板铆向厚板,硬材质铆向软材质(steel->Al) 底层板材的厚度必须大于铆点总厚度的1/3
工艺要求MR接头设计要求
工艺要求MR铆接翻边设计要求
汽车车身铝合金焊接与连接技术
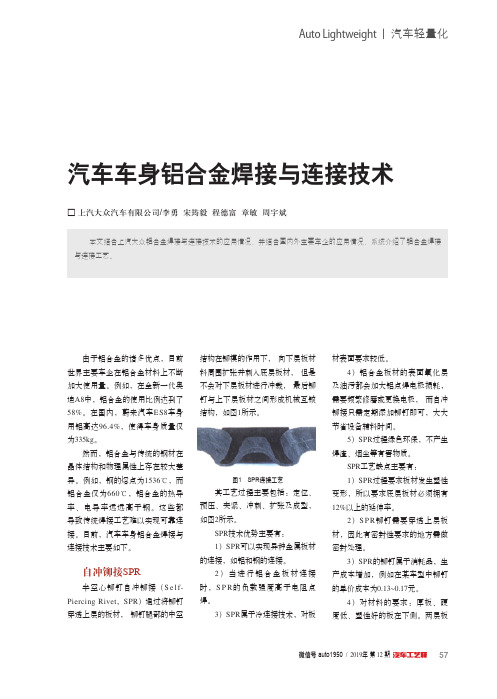
摩擦塞铆焊 EJOWELD
摩擦塞铆焊EJOWELD是一 种新型连接技术,利用“钉子” 的高速旋转穿透上板板料(如铝合 金),并利用钉子和下层板的旋转 摩擦生热熔化下层板料(如22MnB5 硼钢),并在压力的作用下,完成 “钉子”(钢质)与下层板料的焊 接,从而形成稳固结合。如图4所 示。
结构在铆模的作用下, 向下层板材 料周围扩张并刺入底层板材, 但是 不会对下层板材进行冲裁, 最后铆 钉与上下层板材之间形成机械互锁 结构,如图1所示。
图1 SPR连接工艺
其工艺过程主要包括:定位、 预压、夹紧、冲刺、扩张及成型, 如图2所示。
SPR技术优势主要有: 1)SPR可以实现异种金属板材 的连接,如铝和钢的连接。 2)当进行铝合金板材连接 时,SPR的负载强度高于电阻点 焊。 3)SPR属于冷连接技术,对板
激光焊Laser Beam Welding
常用的激光焊接方法主要分为 3类:
1)激光焊接,即单纯使用激 光作为单一热源进行焊接的方法。 目前,在汽车工艺中应用最多的是 激光飞行焊接技术。
2)激光填丝焊接,这类焊接 方法是在焊接过程中,通过自动送 丝装置往金属熔池中添加焊丝,并 利用激光束的热能使其熔化。
其原因是多方面的,一是因为 铝合金的电阻远小于钢,需要4倍 于钢的焊接能量;二是因为电极 极易被污染,30个左右的点焊就需 要修磨电极,生产的连续性受到影 响;三是因为焊接一致性较差。
一般来说,普通铝电阻点焊需 要高压力(如5000~7000N)、高电 流(如32~45kA)、焊接周波少(2 层板5周波,3层板10周波)且电极 头会黏连氧化物,必须要提供适当 的清洁与维护,相对与钢材焊接, 冷却水流量需求至少增加2倍,电 极端面一般建议在10~16mm。
铝合金车身设计中的铆接技术
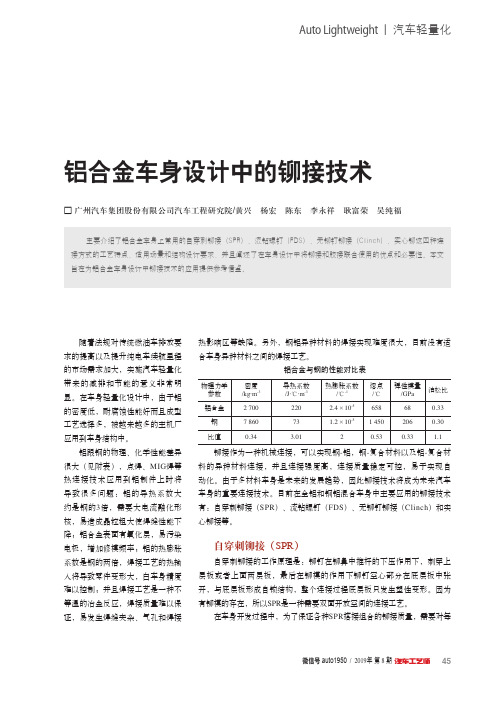
图1 SPR断面扫描
为了保证SPR铆接点的质量,图3 带拔模角铸件法兰边SPR铆接点图5 优化后状态
为了节约成本和提高生产节
拍,工厂在合枪设计时会尽量将多
图2 连接板之间拱起图4 优化前状态
图6 FDS工作原理
图7 FDS断面扫描
FDS区域的刚度需有一定要求,否
图8 无铆钉铆接工作原理示意
无铆钉铆接的优点有:
(1)不需要铆钉,连接点的
质量无增加,有利于轻量化。
图10 铆钉长度的影响
结构胶与铆接
目前车身所有的铆接都是与结构胶联合使用的,其主要原因除了结构胶
能提高连接点的剪切强度、隔绝异种材料之间的电化学腐蚀外,另外一个重
要的作用就是提升铆接点的刚度,增强铆接点的疲劳强度。
铆接工艺的一个图9 实心铆接工作原理图示意。
新能源全铝车身铆接技术解决方案

编号
1
2
图片
编号
6
7
图片
图 1 高温烘烤设置
图 2 低温冷冻设置
编号
11
12
图片
编号
16
17
图片
图 3 60 次拆卸试验
图 4 防水测试
编号
21
22
图片
高低温实验温度:-40~150° 反复拆卸次数:60次
第一组 (拉铆后)
测试数量
30
合格数量
30
合格率
100%
编号
26
27
图片
第二组 (高低温后)
30 30 100%
防电化学腐蚀原理:
铝钉壳与铝基材为第一腐蚀通道,因同种材料,几乎不存在电位差,故而几乎不会发生电化学腐蚀
碳钢镀锌镍钉杆与铝钉壳为第二腐蚀通道,由于钉壳铝材将挤入钉杆沟槽中,加上较长的过盈连接面,形
成气密级的密封效果,腐蚀性介质难以进入,可以很好的防电化学腐蚀
11
<>
01 乘用车铝车身连接技术
铝框架车身铆钉应用实例:
BOM铆钉安装方法
<19>
02 铝合金大巴车身连接技术
关键焊接部位局部加强
挤
压
密
封
区
铝型材刚度加强
✓ 具有高紧固力,很强的抗剪、抗拉、抗震性
能;
✓ 适用于高强度连接,抗震防松要求高的钣
材铆接。
<
2 0
>
02 铝合金大巴车身连接技术
高强度钣材连接抗拉强度
80000
60000
40000
20000
0 5
新能源汽车全铝车身和铝合金电池包 连接解决方案
SPR-工艺介绍只是分享
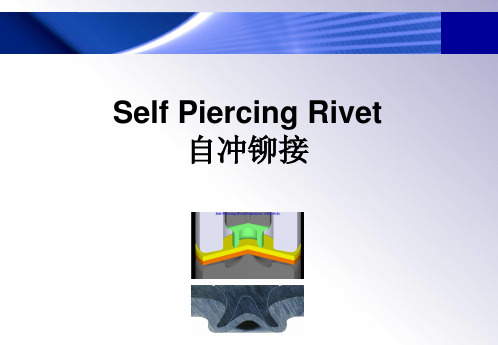
✓返修方法
结束!
Self Piercing Rivet 自冲铆接
✓简介:自冲铆接工艺是一个在铆钉与板料之间形成牢固互锁的冷成型工艺。
Cycle Initiation
Nose Contact
Rivet Inserting Setting Flush
Tool Retract
✓铆钉:车身通常的铆钉有3mm,5mm两个系列
✓质量标准GMN11010
在线依靠自动监控系统0%反馈质量,并外观检查 破检 金相检查,拉伸试验
1. An even gap free set-down of the rivet 2. Crack free button 3. Fill inside rivet, minimum of 2/3 of formed length 4. Sf min minimum sheet thickness of 0.2 mm at foot of rivet 5. A closed joint between rivet and sheets, no gaps SH Degree of interlocking into bottom sheet XT Rivet compression, no gaps permitted
2. 通常不同的材质、厚度、硬度的接头组合需 要不同的铆钉、冲头冲模
3. 铆钉成本的piece cost 0.08Euro/Rivet
4. 设备系统成本远高于电阻点焊 800K人民 币/system
5. 铆接点凸起约2-3mm
6. 只能使用C型铆接枪
✓工艺要求MR材料、厚度匹配要求
1. 接头不能含脆性材料(如玻璃、脆性塑料)
Rivets are made from heat-treated carbon steel, with a complex mechanically applied alloy coating to prevent corrosion when used in Al structure.
上层板对钢铝SPR接头性能影响的试验研究

上层板对钢铝SPR接头性能影响的试验研究作者:刘洋李献龙黄涛来源:《企业科技与发展》2021年第07期【关键词】SPR;自冲铆接;钢铝接头;“十”字拉伸强度;剪切强度;自锁量【中图分类号】TG938 【文献标识码】A 【文章编号】1674-0688(2021)07-0037-030 引言以铝代钢是车身轻量化发展的趋势,但铝合金焊接存在局部应力集中、金属变脆、微裂纹、热变形等缺陷,传统车身点焊难以直接移植到铝合金零件的连接,因此铝合金薄板的连接问题一直是制约其大批量应用的重要因素。
汽车行业铝车身的连接技术一般采用自冲铆接(SPR)、流钻螺钉(FDS)、无铆铆接(TOX)、胶接、磁脉冲焊接等,其中SPR具有连接强度高、速度快、无污染、无预冲孔、成本低的优点,被大量应用于“奥迪”A8、“宝马”5系、“特斯拉”Model S&X、“蔚来”ES8、“奇瑞”蚂蚁eQ5等铝合金车身的连接。
目前,SPR研究主要集中在成型过程和仿真技术方面。
例如,文献[1]以铝合金AA6111-T4和高强钢HSLA340的SPR连接为研究对象,建立了考虑铆钉穿刺、机械回弹、冷却回弹的铆接仿真方法。
文献[2]研究了两层AA5052铝合金SPR接头铆接材料变形和应力应变分布情况,给出了成型过程中的危险部位。
文献[3]通过试验研究了不同铆接压力对接头成型的影响。
文献[4]研究不同长度铆钉,不同厚度板材对高强钢与A5052铝合金SPR接头质量和“十”字拉伸强度的影响。
实际上,不同材料会对接头的连接强度产生影响,车身开发过程中不仅要考虑成型工艺控制,还要考虑连接强度是否满足整车耐久、碰撞要求,并确定是否需要更换材料,而不同的材料对SPR接头强度性能的影响研究鲜见报道。
本文以两层钢铝SPR接頭为研究对象,上层板采用不同钢板材料,通过试验获得上层板料厚度和抗拉强度对SPR自锁量、“十”字拉伸强度、剪切强度的影响。
1 试验方案仅考虑两层板的SPR连接(如图1所示)。
FDS连接工艺在车身轻量化中的应用研究
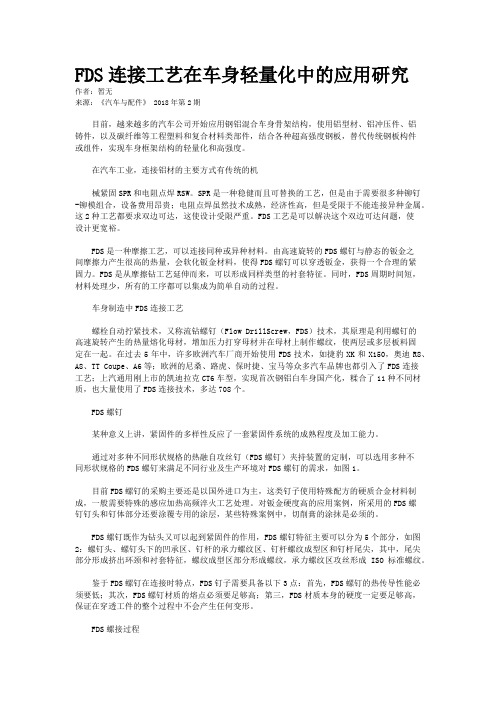
FDS连接工艺在车身轻量化中的应用研究作者:暂无来源:《汽车与配件》 2018年第2期目前,越来越多的汽车公司开始应用钢铝混合车身骨架结构,使用铝型材、铝冲压件、铝铸件,以及碳纤维等工程塑料和复合材料类部件,结合各种超高强度钢板,替代传统钢板构件或组件,实现车身框架结构的轻量化和高强度。
在汽车工业,连接铝材的主要方式有传统的机械紧固SPR和电阻点焊RSW。
SPR是一种稳健而且可替换的工艺,但是由于需要很多种铆钉-铆模组合,设备费用昂贵;电阻点焊虽然技术成熟,经济性高,但是受限于不能连接异种金属。
这2种工艺都要求双边可达,这使设计受限严重。
FDS工艺是可以解决这个双边可达问题,使设计更宽裕。
FDS是一种摩擦工艺,可以连接同种或异种材料。
由高速旋转的FDS螺钉与静态的钣金之间摩擦力产生很高的热量,会软化钣金材料,使得FDS螺钉可以穿透钣金,获得一个合理的紧固力。
FDS是从摩擦钻工艺延伸而来,可以形成同样类型的衬套特征。
同时,FDS周期时间短,材料处理少,所有的工序都可以集成为简单自动的过程。
车身制造中FDS连接工艺螺栓自动拧紧技术,又称流钻螺钉(Flow DrillScrew,FDS)技术,其原理是利用螺钉的高速旋转产生的热量熔化母材,增加压力打穿母材并在母材上制作螺纹,使两层或多层板料固定在一起。
在过去5年中,许多欧洲汽车厂商开始使用FDS技术,如捷豹XK和X150,奥迪R8、A8、TT Coupe、A6等;欧洲的尼桑、路虎、保时捷、宝马等众多汽车品牌也都引入了FDS连接工艺;上汽通用刚上市的凯迪拉克CT6车型,实现首次钢铝白车身国产化,糅合了11种不同材质,也大量使用了FDS连接技术,多达708个。
FDS螺钉某种意义上讲,紧固件的多样性反应了一套紧固件系统的成熟程度及加工能力。
通过对多种不同形状规格的热融自攻丝钉(FDS螺钉)夹持装置的定制,可以选用多种不同形状规格的FDS螺钉来满足不同行业及生产环境对FDS螺钉的需求,如图1。
- 1、下载文档前请自行甄别文档内容的完整性,平台不提供额外的编辑、内容补充、找答案等附加服务。
- 2、"仅部分预览"的文档,不可在线预览部分如存在完整性等问题,可反馈申请退款(可完整预览的文档不适用该条件!)。
- 3、如文档侵犯您的权益,请联系客服反馈,我们会尽快为您处理(人工客服工作时间:9:00-18:30)。
车身材料铆接工艺(SPR&FDS)
成本
201520252030汽车车身板材应用整体趋势预测2015-2030
凯迪拉克CT6 车身先进连接工艺应用概括
工艺SPR FDS铝电焊铝螺柱焊铝弧焊铝激光钎焊结构胶单位个个个个mm mm mm
工艺要求双面可达单面可达双面可达单面可达单面可达单面可达单面可达
对应材料铝-铝
铝-铁铝-铝
铝-铁
铝-铝铝-铝铝-铝铝-铝铝-铝
铝-铁
铁-铁
车身用量合计373726193314499053046311547
3施压
6完成
4刺穿
SPR特性:
可以连接金属和非金属材料,可以连接不同厚度的材料;动态疲劳强度高;碰撞能量吸收性能好;
可无损检测连接性能质量;
其质量由设备决定。
工艺难点:
1.铝薄板连接处易变形
2.铸件连接容易开裂
3.铆钉种类和数量多前期选择难度大
4.材料时效影响连接点质量稳定性
FDS特性:
单面连接工艺;
可以连接不同材料;很高的松开扭矩;气密性和水密性好;动态承载性好。