PLC的自动化生产线供料单元的结构与控制要点
自动化生产线技术教案(YL-335B各单元的控制)

《自动化生产线技术》教案第次课(年月日)教学时数:2 学时课题:供料单元的控制教学目标:1、了解供料单元的结构和工作过程2、了解供料单元的气动控制过程教学重点:1、了解供料单元的气动控制。
2、供料单元的工作过程。
教学难点:供料单元的气动控制教学方法:讲授法(PPT课件)、启发式教学法。
教学内容:1、供料单元的结构和工作过程。
2、供料单元的气动控制过程。
教学过程:供料单元的控制一、供料单元的结构及其工作过程供料单元的主要结构组成为:工件装料管,工件推出装置,支撑架,阀组,端子排组件,PLC,急停按钮和启动/停止按钮,走线槽、底板等.其中,机械部分结构组成如图1所示.图1供料单元的主要结构组成其中,管形料仓和工件推出装置用于储存工件原料,并在需要时将料仓中下层的工件推出到出料台上。
它主要由管形料仓、推料气缸、顶料气缸、磁感应接近开关、漫射式光电传感器组成。
工作原理:工件垂直叠放在料仓中,推料缸处于料仓的底层并且其活塞杆可从料仓的底部通过.当活塞杆在退回位置时,它与下层工件处于同一水平位置,而夹紧气缸则与次下层工件处于同一水平位置。
在需要将工件推出到物料台上时,首先使夹紧气缸的活塞杆推出,压住次下层工件;然后使推料气缸活塞杆推出,从而把下层工件推到物料台上。
在推料气缸返回并从料仓底部抽出后,再使夹紧气缸返回,松开次下层工件.这样,料仓中的工件在重力的作用下,就自动向下移动一个工件,为下一次推出工件做好准备.二、供料单元的气动控制过程①气动控制元件1、标准双作用直线气缸双作用气缸是指活塞的往复运动均由压缩空气来推动。
图 2—3 是标准双作用直线气缸的半剖面图。
图中,气缸的两个端盖上都设有进排气通口,从无杆侧端盖气口进气时,推动活塞向前运动;反之,从杆侧端盖气口进气时,推动活塞向后运动。
双作用气缸具有结构简单,输出力稳定,行程可根据需要选择的优点,但由于是利用压缩空气交替作用于活塞上实现伸缩运动的,回缩时压缩空气的有效作用面积较小,所以产生的力要小于伸出时产生的推力.图2 双作用气缸工作示意图2、单向节流阀单向节流阀是由单向阀和节流阀并联而成的流量控制阀,常用于控制气缸的运动速度,所以也称为速度控制阀。
第三章 供料单元的结构与控制

第三章供料单元的结构与控制3.1 供料单元的结构3.1.1 供料单元的功能供料单元是YL-335A中的起始单元,在整个系统中,起着向系统中的其他单元提供原料的作用。
具体的功能是:按照需要将放置在料仓中待加工工件(原料)自动地推出到物料台上,以便输送单元的机械手将其抓取,输送到其他单元上。
如图3-1所示为供料单元实物的全貌。
3.1.2供料单元的结构组成供料单元的结构组成如图3-2所示。
其主要结构组成为:工件推出与支撑,工件漏斗,阀组,端子排组件,PLC,急停按钮和启动/停止按钮,走线槽、底板等。
1.工件推出与支撑及漏斗部分该部分如图3-3所示。
用于储存工件原料,并在需要时将料仓中最下层的工件推出到物料台上。
它主要由大工件装料管、推料气缸、顶料气缸、磁感应接近开关、漫射式光电传感器组成。
该部分的工作原理是:工件垂直叠放在料仓中,推料缸处于料仓的底层并且其活塞杆可从料仓的底部通过。
当活塞杆在退回位置时,它与最下层工件处于同一水平位置,而夹紧气缸则与次下层工件处于同一水平位置。
在需要将工件推出到物料台上时,首先使夹紧气缸的活塞杆推出,压住次下层工件;然后使推料气缸活塞杆推出,从而把最下层工件推到物料台上。
在推料气缸返回并从料仓底部抽出后,再使夹紧气缸返回,松开次下层工件。
这样,料仓中的工件在重力的作用下,就自动向下移动一个工件,为下一次推出工件做好准备。
为了使气缸的动作平稳可靠,气缸的作用气口都安装了限出型气缸截流阀。
气缸截流阀的作用是调节气缸的动作速度。
截流阀上带有气管的快速接头,只要将合适外径的气管往快速接头上一插就可以将管连接好了,使用时十分方便。
图3-4是安装了带快速接头的限出型气缸截流阀的气缸外观。
图3-5是一个双动气缸装有两个限出型气缸节流阀的连接和调节原理示意图,当调节节流阀A时,是调整气缸的伸出速度,而当调节节流阀B时,是调整气缸的缩回速度。
从图3-4上可以看到,气缸两端分别有缩回限位和伸出限位两个极限位置,这两个极限位置都分别装有一个磁感应接近开关,如图3-6(a)所示。
plc的结构和控制原理及应用实例

PLC的结构和控制原理及应用实例1. PLC的结构PLC(Programmable Logic Controller,可编程逻辑控制器)是一种专门用于工业自动化控制的电子设备。
它由多个模块组成,包括:•CPU(Central Processing Unit,中央处理器):负责处理指令和数据。
•电源模块:提供电力供应。
•输入模块:用于接收来自外部传感器或按钮等输入信号。
•输出模块:用于控制外部执行器或指示灯等输出设备。
•通信模块:实现PLC与其他设备进行数据交换。
•存储器:用于存储程序和数据。
PLC的结构可以根据具体型号和制造商的不同而有所差异,但以上模块通常都会包含在基本的PLC结构中。
2. PLC的控制原理PLC的控制原理主要基于组合逻辑和时序控制。
当输入信号满足特定的逻辑条件时,PLC会执行相应的控制操作。
控制原理可以简述如下:•输入信号检测:PLC的输入模块会不断检测外部传感器或按钮等设备的输入信号状态,并将其转换为数字信号。
•程序执行:PLC的CPU根据预先编写好的程序,按照顺序执行指令。
指令可以包括逻辑运算、数学运算、定时器和计数器等功能。
•输出控制:根据执行指令的结果,PLC的输出模块会控制相应的输出设备(如马达、执行器、指示灯等)完成预定的操作。
3. PLC的应用实例3.1 自动化生产线控制PLC在自动化生产线控制中有广泛应用。
例如,一个汽车组装生产线上使用的PLC系统可以完成以下功能:•检测传感器输入信号:PLC通过检测来自传感器的输入信号,实时监测汽车零部件的位置和状态。
•控制执行器:根据检测结果,PLC可以控制机械手臂、传送带和装配设备等执行器,实现自动化装配操作。
•状态监控:PLC可以记录生产线上的数据,实时监控设备状态,并通过通信模块将数据传输给上位机或监控系统,实现远程监控和异常处理。
3.2 灯光控制系统PLC在灯光控制系统中也有应用。
例如,一个大型展览馆的灯光控制系统可以利用PLC实现以下功能:•输入信号检测:PLC通过检测来自光敏电阻的输入信号,实时感知光线强度。
(精校版)自动生产线物料供给单元的PLC控制
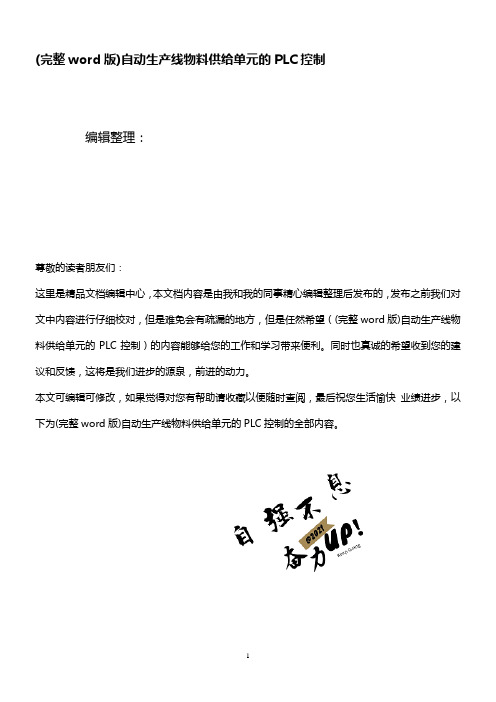
Description
1
I:0/0
STORE2
料仓2到位检测
2
I:0/1
STORE1
料仓1到位检测
3
I:0/2
DETECTION1
料仓1物料检测
4
I:0/3
DETECTION2RETURN
推料气缸回位
6
I:0/5
REACH
推料气缸到位
7
I:0/8
SB1
急停
8
I:0/9
光电传感器CX—411D外观如图2.5所示。投光元件为红色LED,检测距离为70mm。
光电传感器将光的电信号转换为开关信号,使用交流电源,取代接触式行程开关,防止互相干扰.光电传感器是一种小型电子设备,它可以检测出其接收到的光强的变化.
图2.5光电传感器CX—411D的外观图2.6气动电磁阀SVK0120的外观
本控制单元由立体框架式及支架、双料井式供料机、MicroLogix1400可编程控制器、各种传感器和控制开关、传送带、推供料仓气缸、推料气缸和气动控制装置等部分组成。
1。2控制要求
物料供给单元应能实现以下控制要求:
(1)料仓上料自动检测。能实时分别检测两个料仓中有料或无料。
(2)当料仓气缸在原点(料仓1在推料位置),且检测传感器检测到料仓1中有料块时,系统自动将料块推出;
电机转动传送带运行锁存开始急停是否按下启动是否按下按下急停按钮动作停止结束手动自动手动自动急停是否按下启动是否按下电机转动传送带运行锁存仓1无料仓1报警灯亮有料仓2有料推仓1到位按下急停按钮所有动作停止到位仓1有料每隔3s推料块推仓2到位仓2无料仓2报警灯亮按下推料按钮推出料块按下推仓1到位按钮按下推仓2到位按钮推仓2到位解锁仓1无料仓1报警灯亮仓2无料仓2报警灯亮图41物料供给单元流程图42梯形图程序物料供给单元主程序用于手动自动切换梯形图如图42所示
自动生产线物料供给单元的PLC控制
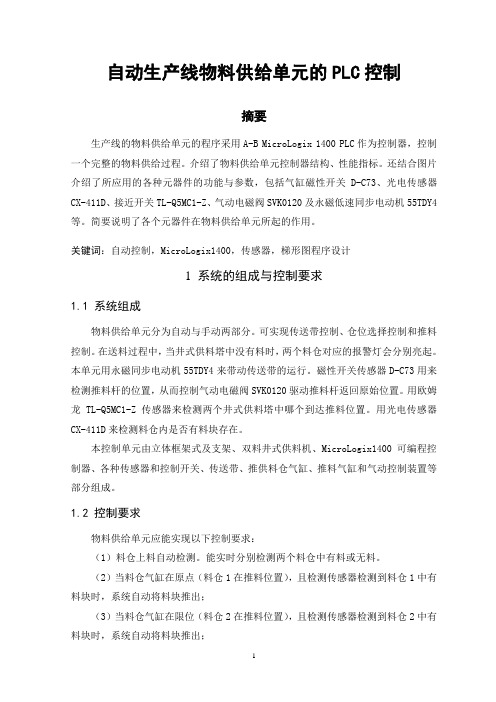
自动生产线物料供给单元的PLC控制摘要生产线的物料供给单元的程序采用A-B MicroLogix 1400 PLC作为控制器,控制一个完整的物料供给过程。
介绍了物料供给单元控制器结构、性能指标。
还结合图片介绍了所应用的各种元器件的功能与参数,包括气缸磁性开关D-C73、光电传感器CX-411D、接近开关TL-Q5MC1-Z、气动电磁阀SVK0120及永磁低速同步电动机55TDY4等。
简要说明了各个元器件在物料供给单元所起的作用。
关键词:自动控制,MicroLogix1400,传感器,梯形图程序设计1 系统的组成与控制要求1.1 系统组成物料供给单元分为自动与手动两部分。
可实现传送带控制、仓位选择控制和推料控制。
在送料过程中,当井式供料塔中没有料时,两个料仓对应的报警灯会分别亮起。
本单元用永磁同步电动机55TDY4来带动传送带的运行。
磁性开关传感器D-C73用来检测推料杆的位置,从而控制气动电磁阀SVK0120驱动推料杆返回原始位置。
用欧姆龙TL-Q5MC1-Z传感器来检测两个井式供料塔中哪个到达推料位置。
用光电传感器CX-411D来检测料仓内是否有料块存在。
本控制单元由立体框架式及支架、双料井式供料机、MicroLogix1400可编程控制器、各种传感器和控制开关、传送带、推供料仓气缸、推料气缸和气动控制装置等部分组成。
1.2 控制要求物料供给单元应能实现以下控制要求:(1)料仓上料自动检测。
能实时分别检测两个料仓中有料或无料。
(2)当料仓气缸在原点(料仓1在推料位置),且检测传感器检测到料仓1中有料块时,系统自动将料块推出;(3)当料仓气缸在限位(料仓2在推料位置),且检测传感器检测到料仓2中有料块时,系统自动将料块推出;(4)当推料气缸在原点时,如果料仓1内检测到没有料块,而料仓2内检测到有料块时,料仓气缸动作,将料仓2移动到推料位置,将料块推出;(5)当推料气缸在限位时,如果料仓2内检测到没有料块,而料仓1内检测到有料块时,料仓气缸动作,将料仓1移动到推料位置,将料块推出;(6)当料块从料仓被推出时,传送带动作,将料块运送到下一个单元。
第三章 供料单元的结构与控制

第三章供料单元的结构与控制3.1 供料单元的结构3.1.1 供料单元的功能供料单元是YL-335A中的起始单元,在整个系统中,起着向系统中的其他单元提供原料的作用。
具体的功能是:按照需要将放置在料仓中待加工工件(原料)自动地推出到物料台上,以便输送单元的机械手将其抓取,输送到其他单元上。
如图3-1所示为供料单元实物的全貌。
3.1.2供料单元的结构组成供料单元的结构组成如图3-2所示。
其主要结构组成为:工件推出与支撑,工件漏斗,阀组,端子排组件,PLC,急停按钮和启动/停止按钮,走线槽、底板等。
1.工件推出与支撑及漏斗部分该部分如图3-3所示。
用于储存工件原料,并在需要时将料仓中最下层的工件推出到物料台上。
它主要由大工件装料管、推料气缸、顶料气缸、磁感应接近开关、漫射式光电传感器组成。
该部分的工作原理是:工件垂直叠放在料仓中,推料缸处于料仓的底层并且其活塞杆可从料仓的底部通过。
当活塞杆在退回位置时,它与最下层工件处于同一水平位置,而夹紧气缸则与次下层工件处于同一水平位置。
在需要将工件推出到物料台上时,首先使夹紧气缸的活塞杆推出,压住次下层工件;然后使推料气缸活塞杆推出,从而把最下层工件推到物料台上。
在推料气缸返回并从料仓底部抽出后,再使夹紧气缸返回,松开次下层工件。
这样,料仓中的工件在重力的作用下,就自动向下移动一个工件,为下一次推出工件做好准备。
为了使气缸的动作平稳可靠,气缸的作用气口都安装了限出型气缸截流阀。
气缸截流阀的作用是调节气缸的动作速度。
截流阀上带有气管的快速接头,只要将合适外径的气管往快速接头上一插就可以将管连接好了,使用时十分方便。
图3-4是安装了带快速接头的限出型气缸截流阀的气缸外观。
图3-5是一个双动气缸装有两个限出型气缸节流阀的连接和调节原理示意图,当A调节节流阀A时,是调整气缸的伸出速度,而当调节节流阀B时,是调整气缸的缩回速度。
从图3-4上可以看到,气缸两端分别有缩回限位和伸出限位两个极限位置,这两个极限位置都分别装有一个磁感应接近开关,如图3-6(a)所示。
自动化生产线供料单元 PLC的自动化生产线__供料单元的结构与控制
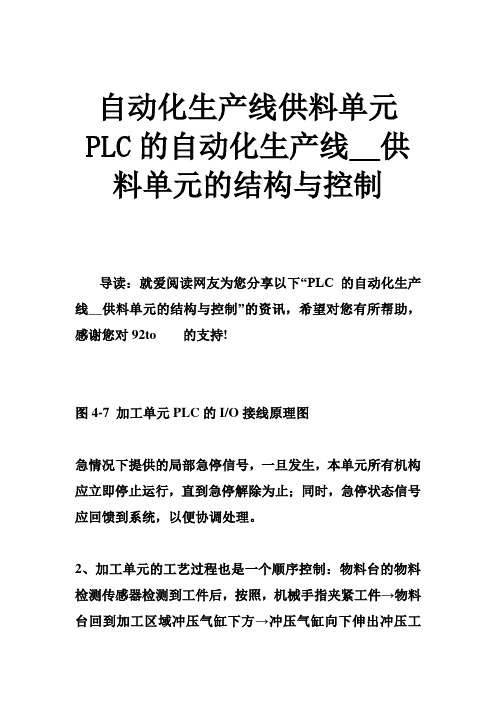
自动化生产线供料单元PLC的自动化生产线__供料单元的结构与控制导读:就爱阅读网友为您分享以下“PLC的自动化生产线__供料单元的结构与控制”的资讯,希望对您有所帮助,感谢您对92to 的支持!图4-7 加工单元PLC的I/O接线原理图急情况下提供的局部急停信号,一旦发生,本单元所有机构应立即停止运行,直到急停解除为止;同时,急停状态信号应回馈到系统,以便协调处理。
2、加工单元的工艺过程也是一个顺序控制:物料台的物料检测传感器检测到工件后,按照,机械手指夹紧工件→物料台回到加工区域冲压气缸下方→冲压气缸向下伸出冲压工件→完成冲压动作后向上缩回→物料台重新伸出→到位后机械手指松开的顺序完成工件加工工序,并向系统发出加工完成信号。
下面给出YL-335A出厂例程中加工单元程序清单供读者在实训时参考。
主程序如图4-9 所示,它只是在每一扫描周期(SM0.0 ON)调用2个子程序,一个是启动/停止子程序,其功能是在读取主站发送来的控制命令以及把本站状态信号写到通信数据存储区。
另一个子程序则是完成加工工艺控制功能。
图4-9 加工站主程序梯形图启动/停止子程序如图4-10所示图4-10 启动/停止子程序梯形图第六章分拣单元的结构与控制分拣单元的结构组成如图6-2所示。
其主要结构组成为:传送和分拣机构,传动机构,变频器模块,电磁阀组,接线端口,PLC模块,底板等。
传送和分拣机构如图6-3所示。
传送已经加工、装配好的工件,在光纤传感器检测到并进行分拣。
它主要由传送带、物料槽、推料(分拣)气缸、漫射式光电传感器、光纤传感器、磁感应接近式传感器组成。
传送带是把机械手输送过来加工好的工件进行传输,输送至分拣区。
导向件是用纠偏机械手输送过来的工件。
两条物料槽分别用于存放加工好的黑色工件和白色工件。
传送和分拣的工作原理:本站的功能是完成从装配站送来的装配好的工件进行分拣。
当输送站送来工件放到传送带上并为入料口漫射式光电传感器检测到时,将信号传输给PLC,通过PLC的程序启动变频器,电机运转驱动传送带工作,把工件带进分拣区,如果进入分拣区工件为白色,则检测白色物料的光纤传感器动作,作为1号槽推料气缸启动信号,将白色料推到1号槽里,如果进入分拣区工件为黑色,检测黑色的光纤传感器作为2号槽推料气缸启动信号,将黑色料推到2号槽里。
plc的结构和控制原理及应用

PLC的结构和控制原理及应用1. PLC的结构PLC(Programmable Logic Controller,可编程逻辑控制器)是一种专门用于工业自动化控制的电子装置。
它由中央处理器、输入/输出模块、存储器和外围设备组成。
1.1 中央处理器PLC的中央处理器是控制系统的核心部分,它负责执行控制程序并进行数据处理。
中央处理器通常由一个微处理器芯片组成,具有高速计算和响应能力。
1.2 输入/输出模块输入/输出模块是PLC与外部设备之间的接口。
它负责处理输入量(如传感器信号)和输出量(如执行器控制信号)。
1.3 存储器存储器用于存储PLC的控制程序、数据表和其他数据。
存储器分为程序存储器和数据存储器,可以保证数据和程序的可靠性和稳定性。
1.4 外围设备外围设备包括显示器、键盘、通信接口等,用于与PLC进行交互和监控。
2. PLC的控制原理PLC的控制原理是通过对输入信号的检测和处理,根据已编写好的控制程序,控制输出信号,从而实现对机器或过程的控制。
2.1 输入信号检测和处理PLC通过输入模块接收来自外部设备的信号,如开关、传感器等。
输入信号经过处理后,将信号转化为PLC能够识别的电平或值。
2.2 控制程序执行PLC的控制程序是由用户编写的程序,通常采用图形化编程软件。
控制程序根据输入信号的状态和用户定义的逻辑关系,通过中央处理器执行相应的操作。
2.3 输出信号控制控制程序执行后,根据逻辑关系,PLC将通过输出模块产生相应的输出信号,控制执行器、接触器等外部设备的开关状态。
3. PLC的应用PLC在工业自动化领域有着广泛的应用,以下是几个常见的应用领域:3.1 自动化生产线PLC能够实现生产线的自动化控制,通过编写控制程序,对生产线上的各个设备进行精确的控制和调度,提高生产效率和产品质量。
3.2 智能建筑PLC可以用于智能建筑中的控制系统,如楼宇自动化控制、安防系统等。
通过PLC的控制,实现对各个系统的精确控制和能耗管理。
实训五、供料单元的结构与控制
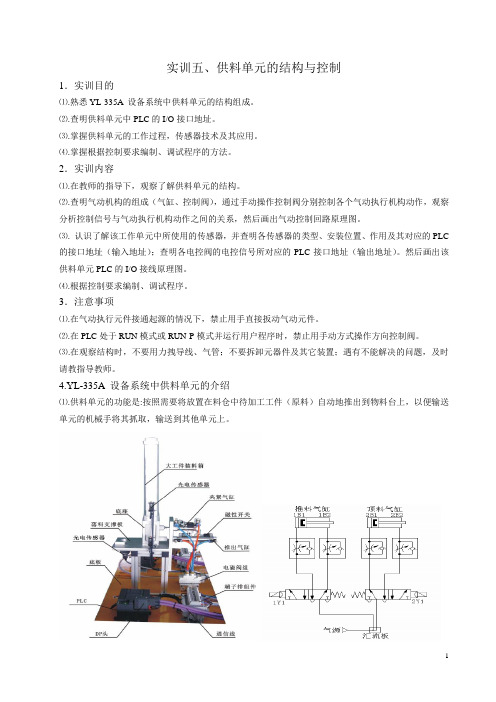
实训五、供料单元的结构与控制1.实训目的⑴.熟悉YL-335A 设备系统中供料单元的结构组成。
⑵.查明供料单元中PLC的I/O接口地址。
⑶.掌握供料单元的工作过程,传感器技术及其应用。
⑷.掌握根据控制要求编制、调试程序的方法。
2.实训内容⑴.在教师的指导下,观察了解供料单元的结构。
⑵.查明气动机构的组成(气缸、控制阀),通过手动操作控制阀分别控制各个气动执行机构动作,观察分析控制信号与气动执行机构动作之间的关系,然后画出气动控制回路原理图。
⑶. 认识了解该工作单元中所使用的传感器,并查明各传感器的类型、安装位置、作用及其对应的PLC 的接口地址(输入地址);查明各电控阀的电控信号所对应的PLC接口地址(输出地址)。
然后画出该供料单元PLC的I/O接线原理图。
⑷.根据控制要求编制、调试程序。
3.注意事项⑴.在气动执行元件接通起源的情况下,禁止用手直接扳动气动元件。
⑵.在PLC处于RUN模式或RUN-P模式并运行用户程序时,禁止用手动方式操作方向控制阀。
⑶.在观察结构时,不要用力拽导线、气管;不要拆卸元器件及其它装置;遇有不能解决的问题,及时请教指导教师。
4.YL-335A 设备系统中供料单元的介绍⑴.供料单元的功能是:按照需要将放置在料仓中待加工工件(原料)自动地推出到物料台上,以便输送单元的机械手将其抓取,输送到其他单元上。
图2-1 供料单元实物图图2-2 供料单元气动控制回路工作原理图⑵.供料单元的结构组成供料单元的结构组成如图2-1所示。
主要结构为:进料模块和物料台,电磁阀组,接线端口,PLC 模块,急停按钮和启动/停止按钮,走线槽、底板等。
⑶. 供料单元的工作过程是:工件垂直叠放在料仓中,推料缸处于料仓的底层并且其活塞杆可从料仓的底部通过。
当活塞杆在退回位置时,它与最下层工件处于同一水平位置,而夹紧气缸则与次下层工件处于同一水平位置。
在需要将工件推出到物料台上时,首先使夹紧气缸的活塞杆推出,压住次下层工件;然后使推料气缸活塞杆推出,从而把最下层工件推到物料台上。
自动化生产线的单元组成

自动化生产线是一种应用自动化技术和设备来实现产品生产的生产系统。
它由多个单元组成,每个单元负责完成特定的生产任务,通过自动化控制和协调,实现产品的连续生产。
自动化生产线的单元组成通常包括以下几个方面:传送系统:传送系统是生产线上的基础设施,用于将原材料、零部件和成品在不同单元之间传送。
传送系统可以是传送带、输送线、搬运机器人等,它们确保生产流程的连续性和高效性。
加工单元:加工单元是完成产品加工和制造的核心部分。
它们根据产品的不同要求,进行切割、成型、焊接、组装、喷涂等生产工序。
加工单元通常由机械设备、机器人和自动化控制系统组成。
检测与质检单元:这些单元用于对产品进行检测和质量检验,确保产品符合规定的质量标准。
检测与质检单元可以使用传感器、视觉系统和自动化检测设备。
自动化控制系统:自动化生产线的关键是自动化控制系统,它负责对生产线上的各个单元进行协调和控制。
自动化控制系统可以是PLC(可编程逻辑控制器)、SCADA(监控与数据采集系统)、DCS(分布式控制系统)等。
输送与存储系统:输送与存储系统用于将生产好的产品从生产线送至仓库或运输出去。
它可以包括物料输送带、自动化堆垛机、自动化包装设备等。
数据采集与分析系统:这些系统用于实时采集生产线上的数据,并对数据进行分析和处理,以优化生产过程和提高生产效率。
人机界面(HMI):人机界面是操作员与生产线交互的界面,通过触摸屏或计算机界面,操作员可以对生产线进行监控、调整和控制。
以上是自动化生产线的一些常见单元组成,不同类型的生产线可能会根据产品和生产工艺的不同而有所调整和变化。
这些单元共同协作,实现产品的高效、精确和连续生产。
PLC的自动化生产线供料单元的结构与控制要点

PLC的自动化生产线供料单元的结构与控制要点PLC(可编程逻辑控制器)的自动化生产线供料单元是指通过PLC控制的系统,主要用于对生产线上的原料或零部件进行供料和控制。
供料单元的结构和控制要点可以从以下几个方面来讨论:1.结构组成:供料单元的结构通常包括以下几个部分:-上料部分:用于将原料或零部件从存储位置(如货架、仓库等)运送到供料位置,通常使用输送带、机器臂、振动盘等设备进行物料传送。
-供料位置:原料或零部件被放置的位置,通常是供给生产线机械手或机器进行下一步处理的地方。
-控制系统:包括PLC、传感器、执行元件等设备,用于实现对供料过程的控制和监控。
2.供料单元的控制要点:-传感器的选择和布置:传感器用于检测物料的状态和位置,例如光电传感器、接近传感器等,应根据具体物料的特点来选择合适的传感器,并合理布置在供料单元的关键位置,确保传感器能够准确地感知物料的状态和位置。
-机械手或机器的控制:机械手或机器用于将原料或零部件从供料位置取出,并放置到生产线上进行下一步处理。
PLC控制器需要编写相应的程序,通过控制机械手或机器的动作来实现物料的取放。
同时,还需考虑机械手或机器的速度、精度等参数,以及与传感器的配合,确保供料过程的稳定性和准确性。
-异常处理:供料过程中可能会出现一些异常情况,例如物料堵塞、物料缺失等。
在PLC控制程序中,需要提前设置相应的异常处理逻辑,并通过监控传感器状态来及时发现和处理异常情况,以避免对生产线的影响。
-安全保护:供料单元通常与人员密切接触,因此,安全保护也是供料单元设计的重要考虑因素之一、在PLC控制程序中,需要设置相应的安全保护逻辑,如急停按钮、安全门等,以确保操作人员的安全。
此外,在设计和控制供料单元时,还需考虑以下几个方面:-物料的特性:不同的物料对于供料单元的要求是不同的,例如粉体物料需要防止堵塞,易碎物料需要防止破损等。
在设计和控制过程中,需要充分考虑物料的特性,并选择合适的设备和控制措施。
自动化生产线中的PLC编程与控制策略

自动化生产线中的PLC编程与控制策略自动化生产线在现代工业领域中扮演着至关重要的角色。
为了实现高效、安全和可靠的生产,PLC(可编程逻辑控制器)编程和控制策略的设计变得尤为关键。
本文将探讨在自动化生产线中的PLC编程与控制策略,并介绍其应用和优势。
一、PLC编程的基础PLC作为自动化生产线控制的关键设备,具有高度灵活性和可编程性。
PLC编程的基础是使用类似于传统电气电路的逻辑元件定义控制程序。
这些逻辑元件包括输入、输出、中继、定时器和计数器等。
通过逻辑元件及其相互之间的逻辑关系,我们可以实现对生产线各个部分的控制。
在PLC编程中,使用一种称为“梯形图”的图形化编程语言是常见的。
梯形图是以梯子形状进行表示的,每一横栏表示一个逻辑元件的状态。
通过将逻辑元件的输入和输出进行连接,我们可以构建复杂的控制程序。
二、PLC控制策略的设计在自动化生产线中,PLC的控制策略非常重要。
有效的控制策略可以提高生产线的吞吐量、减少故障率并降低人员的操作负担。
以下是几种常见的PLC控制策略:1. 顺序控制策略顺序控制是在自动化生产线中最基本的控制策略之一。
通过设定不同的工序顺序和间隔时间,PLC可以按照设定的步骤自动控制机器和设备的操作。
顺序控制可以提高生产效率,降低故障风险,实现产品的高质量和稳定输出。
2. 工艺控制策略工艺控制涉及到对生产过程中各种参数的控制和监测。
通过PLC编程,在生产线中可以实现温度、压力、速度等参数的自动调节和监控。
这种控制策略可以提高产品的一致性和质量稳定性,减少人为因素对生产过程的影响。
3. 故障检测与报警策略PLC编程还可以设计故障检测和报警策略,提前发现和诊断生产线中的故障,并及时报警。
通过监测各个设备的状态和特定的故障标识,PLC可以在出现故障时迅速停止相关操作,并发送报警信息给操作人员,以便及时处理。
三、PLC编程与控制策略的应用PLC编程和控制策略的应用非常广泛,几乎涵盖了所有需要自动化控制的工业领域。
PLC的自动化生产线__供料单元的结构与控制
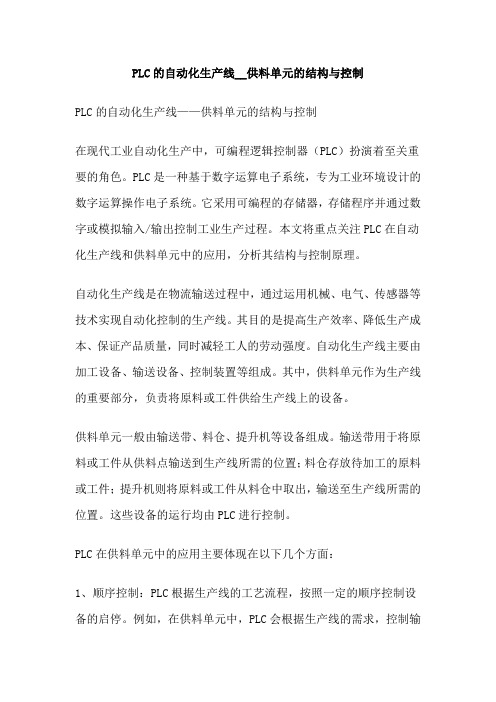
PLC的自动化生产线__供料单元的结构与控制PLC的自动化生产线——供料单元的结构与控制在现代工业自动化生产中,可编程逻辑控制器(PLC)扮演着至关重要的角色。
PLC是一种基于数字运算电子系统,专为工业环境设计的数字运算操作电子系统。
它采用可编程的存储器,存储程序并通过数字或模拟输入/输出控制工业生产过程。
本文将重点关注PLC在自动化生产线和供料单元中的应用,分析其结构与控制原理。
自动化生产线是在物流输送过程中,通过运用机械、电气、传感器等技术实现自动化控制的生产线。
其目的是提高生产效率、降低生产成本、保证产品质量,同时减轻工人的劳动强度。
自动化生产线主要由加工设备、输送设备、控制装置等组成。
其中,供料单元作为生产线的重要部分,负责将原料或工件供给生产线上的设备。
供料单元一般由输送带、料仓、提升机等设备组成。
输送带用于将原料或工件从供料点输送到生产线所需的位置;料仓存放待加工的原料或工件;提升机则将原料或工件从料仓中取出,输送至生产线所需的位置。
这些设备的运行均由PLC进行控制。
PLC在供料单元中的应用主要体现在以下几个方面:1、顺序控制:PLC根据生产线的工艺流程,按照一定的顺序控制设备的启停。
例如,在供料单元中,PLC会根据生产线的需求,控制输送带、料仓、提升机的运行顺序。
2、实时监控:PLC能够实时监测设备的运行状态,如输送带是否正常运行、料仓是否有足够的原料等。
当出现异常情况时,PLC会及时发出警报,以便工作人员进行处理。
3、运动控制:PLC能够对设备的运动轨迹进行精确控制,如控制提升机的升降速度、位置等,以确保原料或工件能够准确无误地输送至生产线所需的位置。
通过以上应用,PLC在供料单元中实现了对设备的自动化控制,大大提高了生产线的生产效率,降低了生产成本。
PLC的可靠性和稳定性也保证了生产线的正常运行,减少了人为错误和设备故障的发生。
总结起来,PLC在自动化生产线和供料单元中的应用显著提高了生产效率和质量,减轻了工人的劳动强度。
基于PLC的自动化生产线控制系统分析

• 65•自动化的生产线具备着组装灵活、安全性高以及构造较为简单等多种优点,可以根据实际需求和车间的大小来增减设备,这也使其成为了现代化企业中建造生产线的重要选择。
因此,本文首先对自动化生产线控制系统的整体架构加以明确,然后对自动化生产线控制系统的内部硬件构成展开分析,在此基础上提出基于PLC 的自动化生产线控制系统的设计措施。
1 自动化生产线控制系统的整体架构如图1所示,自动化生产线内部的控制系统主要是由PLC 、位置传感器、工业计算机、电机驱动器以及工业摄像头等所构成。
在整体控制系统当中,三自由度的滑台是其内部的核心部件,其是由X 、Y 、Z 三个不同方向的线性模组以及与之对应的步进电机组成,完全能够通过PLC 来为驱动器发送准确的控制信号,有效控制滑台当中的三个分支,使其能够按照规定中的坐标来进行移动。
通常情况下,X 轴方向应当尽量与流水线内部的传输带维持一种平行的状态,可以利用齿轮带动皮带这一简单的驱动方式使得X 轴对应的步进电机能够更好的发挥出自身的驱动作用,实现高速运转的直线行驶,保证定位的准确性、平稳性。
而其中的横向机构就可以由Y 轴步进电机进行驱动,其整体驱动方式与X 方向基本一致,主要目的就在于能够更好的配合X 方向来完成坐标的定位工作。
升降机则是由Z 轴的步进电机进行驱动,在驱动方式上与前两者并无太大差异,在实际工作中主要就是顺着垂直的方向来上下运转,实现对各种工件的放置和抓取。
这一控制系统的主要功能有以下几个方面:一是能够实现自动操作与手动操作之间的选择;二是可以实现更加精准的控制;三是能够对工件图像进行更加准确的捕获,及时计算出与之对应的坐标;四是具备良好的安全保护功能。
图1 系统的总体设计2 自动化生产线控制系统内部的硬件构成自动生产线控制系统内部的硬件,主要是由传感器、执行部件、网络通信系统以及PLC 等所组成的。
PLC 的型号相对较多,但其内部的工作原理以及主要结构却基本一致,都是由电源、主机、外部设备接口以及拓展器接口组成的,其拥有抗干扰能力强、可靠性高以及使用较为方便等优点。
配料生产线控制系统的PLC自动控制

工业控制
配料生产线控制系统的 PLC 自动控制
罗及红
(湖南商务职业技术学院电控系, 湖南长沙 410205)
摘要: 为 了 实 现 典 型 配 料 生 产 线 系 统 的 实 际 控 制 要 求 , 运 用 三 菱 PLC 技 术 中 的 顺 序 控 制 步 进 STL 指 令 和 PLC 置 位 、 复 位 基 本 指
[7] 宋清, 邓捷, 邱润才. 配方奶粉生产线全自动程序化控制系
统的研发 [J] . 中国乳业, 2006 (7): 43-43. [8] 赵迎春. 基于 PLC 的自动化电镀生产线控制 系 统 [J] . 中 国
高新技术企业, 2009 (5): 9-10.
作 者 简 介 : 罗 及 红 , 男 , 1970 年 生 , 湖 南 长 沙 人 , 硕 士 , 讲 师 。 研究领域: 电气自动化。
[J] . 华中科技大学学报 (自然科学版), 2002 (4): 20-22. [2] 董秀洁, 苗凤君. 提高 PLC 控制系统可靠性 的 措 施 [J] . 郑
州纺织工学院学报, 1998, 9 (3): 80-82, 94. [3] 高 钦 和. PLC 控 制 系 统 故 障 检 测 与 处 理 功 能 的 实 现 [J] . 计
(3) Modbus 和 Modbus Plus 口地址 的 自 动 切 换 可 实 现 主机的透明通讯, 不需要专门的驱动设备。
(4) 所有的 I / O 模块均可在不影响控制系统正常操作 的情况下带电插拔。
(5) 在通讯失败的情况下, 所有离散量和模拟量 I / O 的输出均可设置为下述 3 种状态之一: 所有输出关断、 保 持最后的输出值或预定义的输出状态。 这种的选择能够保 证在通讯中断的情况下, 整个系统有计划地运行。
供料单元的PLC控制

1个,如果需要有启动和停止 2种主令信号,只能由软件编程实现。
(2)推出工件的操作过程,是一步进顺序控制 过程。编程时,应注意供料不足时对顶料操作 的影响,以及缺料状态和停止信号对顺控流程 的影响。
(或32MR)
供料单元的电气接线采用双层接线端子排,集中连接本工作 单元所有电磁阀、传感器等器件的电气连接线、PLC的I/O 端口及直流电源。上层端子用作连接公共电源正、负极(Vcc 和OV),下层端子用作信号线的连接。端子排上的每一个端 子旁都有数字标号,以说明端子的位地址。接线端口通过导 轨固定在底板10上
要求完成如下任务。 1、规划PLC的I/O分配及接线端
子分配。 2、进行系统安装接线。 3、按控制要求编制PLC程序。 4、进行调试与运行。
PLC的I/O分配及系统安装接线
本单元中,传感器信号占用7个输入点, 留出1个点提供给启/停按钮作本站主 令信号,则所需的PLC I/O点数为8点输 入12点输出。选用三菱FX2N-16MR (32MR)主单元,共8点输入和8点继 电器输出,供料单元的I/O接线原理图 如图
本项目只考虑供料单元作为独立设备运行时的情况。 具体的控制要求为:
(1)项料气缸和推料气缸的初始位置均设定在缩回状态。 启动前,料仓内有足够的工件,否则不能启动。
(2)只用一个按钮产生启动/停止信号。 (3)启动后,如果物料台上没有工件,则应把工件推到物 料台上。在工作过程中,若料仓内工件不足,单元继续工 作,但应发出预警信号;若料仓内没有工件,则单元停止 工作并发出报警信号。物料台上的工件被取出后,若系统 启动信号仍然为ON,则进行下一次推出工件操作。 (4)停止信号发出后,若尚未进行推出工件的操作,则立 即停止工作;否则在完成本次推出操作后停止工作。
PLC的自动化生产线供料单元的结构与控制要点

第三章供料单元的结构与控制3.1 供料单元的结构3.1。
1 供料单元的功能供料单元是YL-335A中的起始单元,在整个系统中,起着向系统中的其他单元提供原料的作用。
具体的功能是:按照需要将放置在料仓中待加工工件(原料)自动地推出到物料台上,以便输送单元的机械手将其抓取,输送到其他单元上。
如图3—1所示为供料单元实物的全貌。
3.1.2供料单元的结构组成供料单元的结构组成如图3—2所示。
其主要结构组成为:工件推出与支撑,工件漏斗,阀组,端子排组件,PLC,急停按钮和启动/停止按钮,走线槽、底板等.1.工件推出与支撑及漏斗部分该部分如图3—3所示。
用于储存工件原料,并在需要时将料仓中最下层的工件推出到物料台上.它主要由大工件装料管、推料气缸、顶料气缸、磁感应接近开关、漫射式光电传感器组成。
该部分的工作原理是:工件垂直叠放在料仓中,推料缸处于料仓的底层并且其活塞杆可从料仓的底部通过。
当活塞杆在退回位置时,它与最下层工件处于同一水平位置,而夹紧气缸则与次下层工件处于同一水平位置.在需要将工件推出到物料台上时,首先使夹紧气缸的活塞杆推出,压住次下层工件;然后使推料气缸活塞杆推出,从而把最下层工件推到物料台上。
在推料气缸返回并从料仓底部抽出后,再使夹紧气缸返回,松开次下层工件。
这样,料仓中的工件在重力的作用下,就自动向下移动一个工件,为下一次推出工件做好准备。
为了使气缸的动作平稳可靠,气缸的作用气口都安装了限出型气缸截流阀.气缸截流阀的作用是调节气缸的动作速度.截流阀上带有气管的快速接头,只要将合适外径的气管往快速接头上一插就可以将管连接好了,使用时十分方便。
图3-4是安装了带快速接头的限出型气缸截流阀的气缸外观。
图3—5是一个双动气缸装有两个限出型气缸节流阀的连接和调节原理示意图,当调节节流阀A时,是调整气缸的伸出速度,而当调节节流阀B时,是调整气缸的缩回速度。
从图3-4上可以看到,气缸两端分别有缩回限位和伸出限位两个极限位置,这两个极限位置都分别装有一个磁感应接近开关,如图3—6(a)所示。
第三章 供料单元的结构与控制
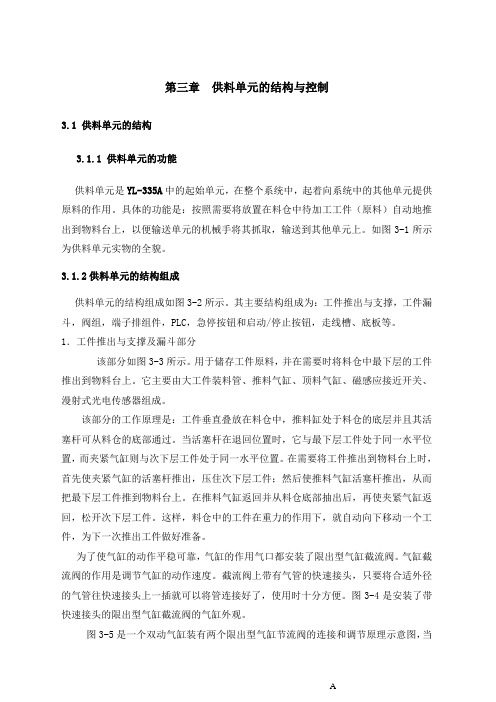
第三章供料单元的结构与控制3.1 供料单元的结构3.1.1 供料单元的功能供料单元是YL-335A中的起始单元,在整个系统中,起着向系统中的其他单元提供原料的作用。
具体的功能是:按照需要将放置在料仓中待加工工件(原料)自动地推出到物料台上,以便输送单元的机械手将其抓取,输送到其他单元上。
如图3-1所示为供料单元实物的全貌。
3.1.2供料单元的结构组成供料单元的结构组成如图3-2所示。
其主要结构组成为:工件推出与支撑,工件漏斗,阀组,端子排组件,PLC,急停按钮和启动/停止按钮,走线槽、底板等。
1.工件推出与支撑及漏斗部分该部分如图3-3所示。
用于储存工件原料,并在需要时将料仓中最下层的工件推出到物料台上。
它主要由大工件装料管、推料气缸、顶料气缸、磁感应接近开关、漫射式光电传感器组成。
该部分的工作原理是:工件垂直叠放在料仓中,推料缸处于料仓的底层并且其活塞杆可从料仓的底部通过。
当活塞杆在退回位置时,它与最下层工件处于同一水平位置,而夹紧气缸则与次下层工件处于同一水平位置。
在需要将工件推出到物料台上时,首先使夹紧气缸的活塞杆推出,压住次下层工件;然后使推料气缸活塞杆推出,从而把最下层工件推到物料台上。
在推料气缸返回并从料仓底部抽出后,再使夹紧气缸返回,松开次下层工件。
这样,料仓中的工件在重力的作用下,就自动向下移动一个工件,为下一次推出工件做好准备。
为了使气缸的动作平稳可靠,气缸的作用气口都安装了限出型气缸截流阀。
气缸截流阀的作用是调节气缸的动作速度。
截流阀上带有气管的快速接头,只要将合适外径的气管往快速接头上一插就可以将管连接好了,使用时十分方便。
图3-4是安装了带快速接头的限出型气缸截流阀的气缸外观。
图3-5是一个双动气缸装有两个限出型气缸节流阀的连接和调节原理示意图,当A调节节流阀A时,是调整气缸的伸出速度,而当调节节流阀B时,是调整气缸的缩回速度。
从图3-4上可以看到,气缸两端分别有缩回限位和伸出限位两个极限位置,这两个极限位置都分别装有一个磁感应接近开关,如图3-6(a)所示。
- 1、下载文档前请自行甄别文档内容的完整性,平台不提供额外的编辑、内容补充、找答案等附加服务。
- 2、"仅部分预览"的文档,不可在线预览部分如存在完整性等问题,可反馈申请退款(可完整预览的文档不适用该条件!)。
- 3、如文档侵犯您的权益,请联系客服反馈,我们会尽快为您处理(人工客服工作时间:9:00-18:30)。
第三章供料单元的结构与控制3.1 供料单元的结构3.1.1 供料单元的功能供料单元是YL-335A中的起始单元,在整个系统中,起着向系统中的其他单元提供原料的作用。
具体的功能是:按照需要将放置在料仓中待加工工件(原料)自动地推出到物料台上,以便输送单元的机械手将其抓取,输送到其他单元上。
如图3-1所示为供料单元实物的全貌。
3.1.2供料单元的结构组成供料单元的结构组成如图3-2所示。
其主要结构组成为:工件推出与支撑,工件漏斗,阀组,端子排组件,PLC,急停按钮和启动/停止按钮,走线槽、底板等。
1.工件推出与支撑及漏斗部分该部分如图3-3所示。
用于储存工件原料,并在需要时将料仓中最下层的工件推出到物料台上。
它主要由大工件装料管、推料气缸、顶料气缸、磁感应接近开关、漫射式光电传感器组成。
该部分的工作原理是:工件垂直叠放在料仓中,推料缸处于料仓的底层并且其活塞杆可从料仓的底部通过。
当活塞杆在退回位置时,它与最下层工件处于同一水平位置,而夹紧气缸则与次下层工件处于同一水平位置。
在需要将工件推出到物料台上时,首先使夹紧气缸的活塞杆推出,压住次下层工件;然后使推料气缸活塞杆推出,从而把最下层工件推到物料台上。
在推料气缸返回并从料仓底部抽出后,再使夹紧气缸返回,松开次下层工件。
这样,料仓中的工件在重力的作用下,就自动向下移动一个工件,为下一次推出工件做好准备。
为了使气缸的动作平稳可靠,气缸的作用气口都安装了限出型气缸截流阀。
气缸截流阀的作用是调节气缸的动作速度。
截流阀上带有气管的快速接头,只要将合适外径的气管往快速接头上一插就可以将管连接好了,使用时十分方便。
图3-4是安装了带快速接头的限出型气缸截流阀的气缸外观。
图3-5是一个双动气缸装有两个限出型气缸节流阀的连接和调节原理示意图,当调节节流阀A时,是调整气缸的伸出速度,而当调节节流阀B时,是调整气缸的缩回速度。
A从图3-4上可以看到,气缸两端分别有缩回限位和伸出限位两个极限位置,这两个极限位置都分别装有一个磁感应接近开关,如图3-6(a)所示。
磁感应接近开关的基本工作原理是:当磁性物质接近传感器时,传感器便会动作,并输出传感器信号。
若在气缸的活塞(或活塞杆)上安装上磁性物质,在气缸缸筒外面的两端位置各安装一个磁感应式接近开关,就可以用这两个传感器分别标识气缸运动的两个极限位置。
当气缸的活塞杆运动到哪一端时,哪一端的磁感应式接近开关就动作并发出电信号。
在PLC 的自动控制中,可以利用该信号判断推料及顶料缸的运动状态或所处的位置,以确定工件是否被推出或气缸是否返回。
在传感器上设置有LED显示用于显示传感器的信号状态,供调试时使用。
传感器动作时,输出信号“1”,LED亮;传感器不动作时,输出信号“0”,LED不亮。
传感器(也叫做磁性开关)的安装位置可以调整,调整方法是松开磁性开关的紧定螺栓,让磁性开关顺着气缸滑动,到达指定位置后,再旋紧紧定螺栓。
磁性开关有蓝色和棕色2根引出线,使用时蓝色引出线应连接到PLC输入公共端,棕色引出线应连接到PLC输入端子。
磁性开关的内部电路如图3-6虚线框内所示,为了防止实训时错误接线损坏磁性开关,YL-335A上所有磁性开关的棕色引出线都串联了电阻和二极管支路。
因此,使用时若引出线极性接反,该磁性开关不能正常工作。
图3-6 磁性开关内部电路在底座和装料管第4层工件位置,分别安装一个漫射式光电开关。
漫射式光电接近开关是利用光照射到被测物体上后反射回来的光线而工作的,由于物体反射的光线为漫射光,故称为漫射式光电接近开关。
它的光发射器与光接收器处于同一侧位置,且为一体化结构。
在工作时,光发射器始终发射检测光,若接近开关前方一定距离内没有物体,则没有光被反射到接收器,接近开关处于常态而不动作;反之若接近开关的前方一定距离内出现物体,只要反射回来的光强度足够,则接收器接收到足够的漫射光就会使接近开关动作而改变输出的状态。
图3-7为漫射式光电接近开关的工作原理示意图。
图3-7 漫射式接近开关的工作原理由此可见,若该部分机构内没有工件,则处于底层和第4层位置的两个漫射式光电接近开关均处于常态;若仅在底层起有3个工件,则底层处光电接近开关动作而第4层处光电接近开关常态,表明工件已经快用完了。
这样,料仓中有无储料或储料是否足够,就可用这两个光电接近开关的信号状态反映出来。
在控制程序中,就可以利用该信号状态来判断底座和装料管中储料的情况,为实现自动控制奠定了硬件基础。
供料单元中,用来检测工件不足或工件有无的漫射式光电接近开关选用OMRON公司的E3Z-L型放大器内置型光电开关(细小光束型)。
该光电开关的外形和顶端面上的调节旋钮和显示灯如图3-8所示。
图3-9给出该光电开关的内部电路原理框图。
图3-9 E3Z-L光电开关电路原理图被推料缸推出的工件将落到物料台上。
物料台面开有小孔,物料台下面设有一个园柱形漫射式光电接近开关,工作时向上发出光线,从而透过小孔检测是否有工件存在,以便向系统提供本单元物料台有无工件的信号。
在输送单元的控制程序中,就可以利用该信号状态来判断是否需要驱动机械手装置来抓取此工件。
该光电开关选用OTS41型。
2、电磁阀组阀组,就是将多个阀与消声器、汇流板等集中在一起构成的一组控制阀的集成,而每个阀的功能是彼此独立的。
供料单元的阀组只使用两个由二位五通的带手控开关的单电控电磁阀,两个阀集中安装在汇流板上,汇流板中两个排气口末端均连接了消声器,消声器的作用是减少压缩空气在向大气排放时的噪声。
阀组的结构如图3-10所示。
本单元的两个阀分别对顶料气缸和推料气缸进行控制,以改变各自的动作状态。
本单元所采用的电磁阀,带手动换向、加锁钮,有锁定(LOCK)和开启(PUSH)2个位置。
用小螺丝刀把加锁钮旋到在LOCK位置时,手控开关向下凹进去,不能进行手控操作。
只有在PUSH位置,可用工具向下按,信号为“1”,等同于该侧的电磁信号为“1”;常态时,手控开关的信号为“0”。
在进行设备调试时,可以使用手控开关对阀进行控制,从而实现对相应气路的控制,以改变推料缸等执行机构的控制,达到调试的目的。
3.1.3 气动控制回路气动控制回路是本工作单元的执行机构,该执行机构的控制逻辑控制功能是由PLC 实现的。
气动控制回路的工作原理如图3-11所示。
图中1A和2A分别为推料气缸和顶料气缸。
1B1和1B2为安装在推料缸的两个极限工作位置的磁感应接近开关,2B1和2B2为安装在推料缸的两个极限工作位置的磁感应接近开关。
1Y1和2Y1分别为控制推料缸和顶料缸的电磁阀的电磁控制端。
图3-11 供料单元气动控制回路工作原理图3.2 供料单元的PLC控制及编程3.2.1 PLC的I/O 接线本单元中,传感器信号占用7个输入点,留出1个点提供给启/停按钮作本地主令信号,则所需的PLC I/O点数为8点输入/2点输出。
选用西门子S7-222主单元,共8点输入和6点继电器输出,供料单元的I/O接线原理图如图3-12所示。
图3-12 供料单元PLC的I/O接线原理图供料单元PLC的I/O接线是采用双层接线端子排连接的,端子排集中连接本工作单元所有电磁阀、传感器等器件的电气连接线、PLC的I/O端口及直流电源。
上层端子用作连接公共电源正、负极(Vcc和0V),连接片的作用是将各分散端子片上层端子排进行电气短接,下层端子用作信号线的连接,固定端板是将各分散的组成部分进行横向固定,保险座内插装有2A的保险管。
接线端口上的每一个端子旁都有数字标号,以说明端子的位地址。
接线端口通过导轨固定在底板上。
图3-13和图3-14分别是本单元的接线端口外观和端子接线图。
3.2.2供料单元的本地控制和网络控制1、本地控制YL-335A允许各工作单元作为独立设备运行,但在供料单元中,主令信号输入点被限制为1个,如果需要有启动和停止2种主令信号,只能由软件编程实现。
图3-15是软件实现用一个按钮产生启动/停止信号的一个方法。
图3-15 用一个按钮产生启动/停止信号程序2、网络控制YL-335A着重考虑采用RS485串行通信实现的网络控制方案,系统的主令信号均从连接到输送站PLC(主站)的按钮/指示灯模块发出,经输送站PLC程序处理后,把控制要求存储到其发送缓冲区,通过调用NET_EXE子程序,向各从站发送控制要求,以实现各站的复位、启动、停止等等操作。
供料、加工、装配、分拣各从站单元在运行过程中的状态信号,应存储到该单元PLC规划好的数据缓冲区,等待主站单元的读取而回馈到系统,以实现整个系统的协调运行。
以第二章所举的例子为例,按表2-2的规划,主站单元发送的控制要求,存放在供料单元VB1000处,而供料单元运行过程中需要回馈到系统的状态信号则应写入到VB1010处。
VB1000和VB1010的具体内容以及控制程序如何编制,取决于系统工艺过程的要求,下面以YL-335A出厂例程为实例说明。
例:在网络控制方式下供料单元的控制要求如下:系统启动后,供料站把待加工工件推到物料台上,向系统发出物料台有物料信号,并且推料气缸缩回,准备下一次推料。
若供料站的料仓和料槽内没有工件或工件不足,则向系统发出报警或预警信号。
物料台上的工件被输送站机械手取出后,须等待系统本工作周期结束,输送站机械手装置返回原点位置,才进行下一次推出工件操作。
如果在工作过程中,系统曾发出停止信号,则不再进行下一次推料操作。
由控制要求可知,程序应包括两部分,一是如何响应系统的启动、停止指令和状态信息的返回,二是送料过程的控制。
可以编写实现这二个功能的子程序,在主程序中调用。
1)主程序如图3-16所示。
图3-16 主程序梯形图2)启动/停止子程序图3-17启动/停止子程序梯形图3)送料子程序图3-18 送料子程序梯形图主站在读取供料站回馈信息后如何处理,将在第八章中说明。
第四章加工单元的结构与控制4.1 加工单元的结构4.1.1 加工单元的功能加工单元的功能是完成把待加工工件从物料台移送到加工区域冲压气缸的正下方;完成对工件的冲压加工,然后把加工好的工件重新送回物料台的过程。
如图4-1所示为加工单元实物的全貌4.1.2加工单元的结构组成加工单元主要结构组成为:物料台及滑动机构,加工(冲压)机构,电磁阀组,接线端口,PLC模块,急停按钮和启动/停止按钮,底板等,加工机构的总成如图4-2所1.物料台及滑动机构物料台及滑动机构如图4-3所示。
物料台用于固定被加工件,并把工件移到加工(冲压)机构正下方进行冲压加工。
它主要由手爪气动、手指、物料台伸缩气缸、线性导轨及滑块、磁感应接近开关、漫射式光电传感器组成。
滑动物料台的工作原理:滑动物料台在系统正常工作后的初始状态为伸缩气缸伸出,物料台气动手爪张开的状态,当输送机构把物料送到料台上,物料检测传感器检测到工件后,PLC控制程序驱动气动手指将工件夹紧→物料台回到加工区域冲压气缸下方→冲压气缸活塞杆向下伸出冲压工件→完成冲压动作后向上缩回→物料台重新伸出→到位后气动手指松开的顺序完成工件加工工序,并向系统发出加工完成信号。