纸箱印刷中的压力及调整方法
纸箱印刷中常见问题、故障分析解除法

若压力辊的位置过高或过低,以致与瓦楞纸
板接触过紧或过松,也会出现脏版、糊版或局部 图文印迹不清情况,应调整压力辊至合适的位 置,使压力辊和辊筒之间的间隙与纸板的厚度相 适应,以确保印刷版面的部位,避免该故障现象 的产生。
4、色序不当引起的质量故障
如果将版面较满的图文排列在第一色组印 刷,当瓦楞纸板进入下一色组机构印刷的过程 中,由于纸板第一色组的印刷图文的着墨量大、
版面图文印刷位置不准或不稳定的质量问 题
1、瓦楞纸板曲翘引起的印刷位置不准
如果瓦楞纸板有曲翘不良情况发生,那么在 纸板定位和进纸过程中,容易出现滑移的现象, 甚至机器上的规矩接触不到纸边,造成纸板的印 刷位置不准或不稳定在对翘曲的瓦楞纸板进行 印刷时,尽量将相对比较平的纸边,作为进纸时 定位的规矩纸边。最重要的是质量源头的控制, 通过单面机操作工艺的合理掌控,使机器的速度 与预热温度,原纸含水率与预热面积处于相对协 调的状态;在配纸时注意将含水率比较接近的箱
1、机器压印关联部件不良引起的质量故障
当印版辊筒轴头、压印辊轴头、传动轴、齿 轮以及与压印相关联的重要部件出现磨损、松动 时,在压印过程中印版辊或压印辊会因此产生跳 动或滑动现象,由于压力不稳定,致使印版面与 纸板接触不正常,造成纸板印刷表面出现糊版或 局部图文印迹不清的问题。通过认真仔细的观察 和分析,查明故障的确切部位,采取相应的措施 进行处理,对磨损、松动的部件予以修复,消除 故障现象。
如果成形的瓦楞纸板表面有人为破坏的凹
均每天要睡 20 个小时。我的母亲一开始并不知道我得病了,她最近每天对我骂骂
陷痕迹时,凹陷部位的纸面也会出现印迹不清晰 的质量缺陷,对此如果采用全面加大印刷压力弥 补,容易使文字、线条版面出现起糊的质量问题。 为了避免版面起糊,瓦楞纸板在堆放、搬运过程 中,应注意轻搬、轻放、轻压(要控制好堆放高 度),切忌采用扔、砸、压等不良生产习惯进行 搬运。
凹凸不平的纸板怎样印刷

凹凸不平的纸板怎样印刷
本文从压力和油墨调整两个方面重点来谈如何印刷凹凸不平纸板。
瓦楞纸板面纸不平整,纸板表面出现凹凸现象。
制作这样的纸板不太容易,印刷压力大了纸板就会出现凹坑,印刷压力轻了则会频繁出现印刷露白。
一般而言,凹凸不平的纸板生产出来后,如何印刷环节不找到相关问题点,针对性地加以解决,就会造成这类纸板不能印刷而浪费。
那我们如何来解决这样的问题呢?
一、压力:控制压力特别重要。
印刷压力不能过轻:做凹凸不平的纸板压力控制是非常重要的一个环节,首先印刷压力不能过轻,加大印刷压力的同时要将版压放到最轻,这样印刷版在转移油墨的同时,印刷版不容易变形,而且油墨不会卡在印刷版的边缘,印刷压力大一点,字体也会清晰。
二、送纸轮的压力切勿加大。
不能在进纸轮就把纸板压溃,所以进纸轮间隙的调整要控制在纸板厚度的-0.4mm。
如果过重纸板会压溃,从而导致印刷压力加大。
所以进纸单元必须要
控制好。
若是版压也大,印刷压力也大,就会出现印刷糊,字迹不清晰等现象。
三、油墨:让油墨更好地渗透到纸张里面
造成纸板出现凹凸现象,是因为面纸张力不均匀,纸板张力紧时油墨吸收性就差。
因此针对纸张问题,就必须提高油墨的色粉含量,降低油墨粘度,减少上墨量。
再在油墨里面增加渗透剂,提高油墨的渗透能力,让油墨更好地渗透到纸张里面,这样问题就得以解决了。
印刷压力调整原则四步骤(精)
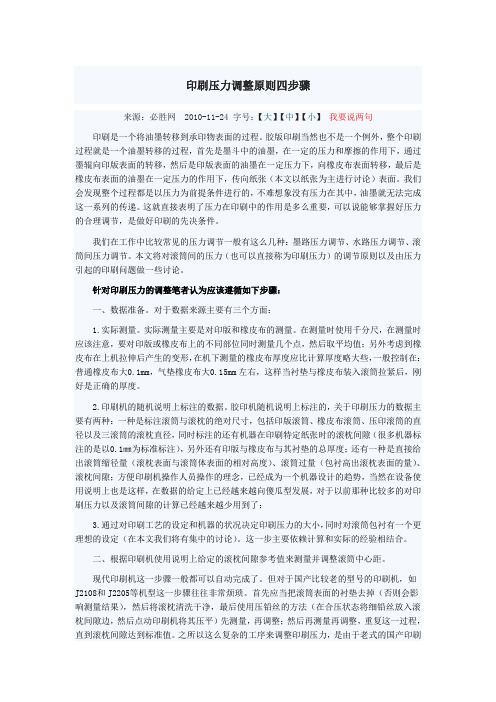
印刷压力调整原则四步骤来源:必胜网 2010-11-24 字号:【大】【中】【小】我要说两句印刷是一个将油墨转移到承印物表面的过程。
胶版印刷当然也不是一个例外,整个印刷过程就是一个油墨转移的过程,首先是墨斗中的油墨,在一定的压力和摩擦的作用下,通过墨辊向印版表面的转移,然后是印版表面的油墨在一定压力下,向橡皮布表面转移,最后是橡皮布表面的油墨在一定压力的作用下,传向纸张(本文以纸张为主进行讨论)表面。
我们会发现整个过程都是以压力为前提条件进行的,不难想象没有压力在其中,油墨就无法完成这一系列的传递。
这就直接表明了压力在印刷中的作用是多么重要,可以说能够掌握好压力的合理调节,是做好印刷的先决条件。
我们在工作中比较常见的压力调节一般有这么几种:墨路压力调节、水路压力调节、滚筒间压力调节。
本文将对滚筒间的压力(也可以直接称为印刷压力)的调节原则以及由压力引起的印刷问题做一些讨论。
针对印刷压力的调整笔者认为应该遵循如下步骤:一、数据准备。
对于数据来源主要有三个方面:1.实际测量。
实际测量主要是对印版和橡皮布的测量。
在测量时使用千分尺,在测量时应该注意,要对印版或橡皮布上的不同部位同时测量几个点,然后取平均值;另外考虑到橡皮布在上机拉伸后产生的变形,在机下测量的橡皮布厚度应比计算厚度略大些,一般控制在:普通橡皮布大0.1mm,气垫橡皮布大0.15mm左右,这样当衬垫与橡皮布装入滚筒拉紧后,刚好是正确的厚度。
2.印刷机的随机说明上标注的数据。
胶印机随机说明上标注的,关于印刷压力的数据主要有两种:一种是标注滚筒与滚枕的绝对尺寸,包括印版滚筒、橡皮布滚筒、压印滚筒的直径以及三滚筒的滚枕直径,同时标注的还有机器在印刷特定纸张时的滚枕间隙(很多机器标注的是以0.1㎜为标准标注),另外还有印版与橡皮布与其衬垫的总厚度;还有一种是直接给出滚筒缩径量(滚枕表面与滚筒体表面的相对高度)、滚筒过量(包衬高出滚枕表面的量)、滚枕间隙;方便印刷机操作人员操作的理念,已经成为一个机器设计的趋势,当然在设备使用说明上也是这样,在数据的给定上已经越来越向傻瓜型发展,对于以前那种比较多的对印刷压力以及滚筒间隙的计算已经越来越少用到了;3.通过对印刷工艺的设定和机器的状况决定印刷压力的大小,同时对滚筒包衬有一个更理想的设定(在本文我们将有集中的讨论)。
印刷过程中调节与控制要点
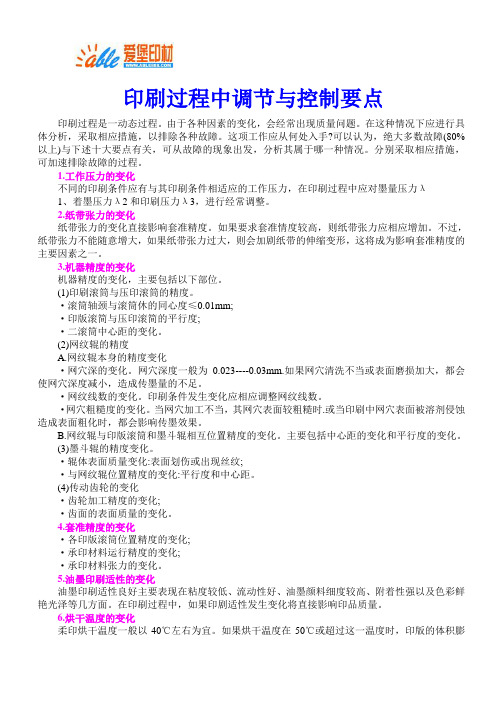
印刷过程中调节与控制要点印刷过程是一动态过程。
由于各种因素的变化,会经常出现质量问题。
在这种情况下应进行具体分析,采取相应措施,以排除各种故障。
这项工作应从何处入手?可以认为,绝大多数故障(80%以上)与下述十大要点有关,可从故障的现象出发,分析其属于哪一种情况。
分别采取相应措施,可加速排除故障的过程。
1.工作压力的变化不同的印刷条件应有与其印刷条件相适应的工作压力,在印刷过程中应对墨量压力λ1、着墨压力λ2和印刷压力λ3,进行经常调整。
2.纸带张力的变化纸带张力的变化直接影响套准精度。
如果要求套准情度较高,则纸带张力应相应增加。
不过,纸带张力不能随意增大,如果纸带张力过大,则会加剧纸带的伸缩变形,这将成为影响套准精度的主要因素之一。
3.机器精度的变化机器精度的变化,主要包括以下部位。
(1)印刷滚筒与压印滚筒的精度。
·滚筒轴颈与滚筒休的同心度≤0.01mm;·印版滚简与压印滚简的平行度;·二滚筒中心距的变化。
(2)网纹辊的精度A.网纹辊本身的精度变化·网穴深的变化。
网穴深度一般为0.023----0.03mm.如果网穴清洗不当或表面磨损加大,都会使网穴深度减小,造成传墨量的不足。
·网纹线数的变化。
印刷条件发生变化应相应调整网纹线数。
·网穴粗糙度的变化。
当网穴加工不当,其网穴表面较粗糙时.或当印刷中网穴表面被溶剂侵蚀造成表面粗化时,都会影响传墨效果。
B.网纹辊与印版滚筒和墨斗辊相互位置精度的变化。
主要包括中心距的变化和平行度的变化。
(3)墨斗辊的精度变化。
·辊体表面质量变化:表面划伤或出现丝纹;·与网纹辊位置精度的变化:平行度和中心距。
(4)传动齿轮的变化·齿轮加工精度的变化;·齿面的表面质量的变化。
4.套准精度的变化·各印版滚筒位置精度的变化;·承印材料运行精度的变化;·承印材料张力的变化。
印刷机在纸厚发生变化时的压力调节
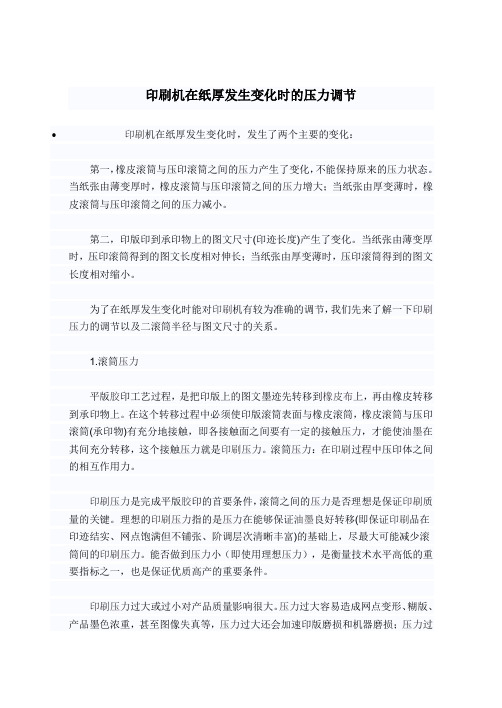
印刷机在纸厚发生变化时的压力调节印刷机在纸厚发生变化时,发生了两个主要的变化:第一,橡皮滚筒与压印滚筒之间的压力产生了变化,不能保持原来的压力状态。
当纸张由薄变厚时,橡皮滚筒与压印滚筒之间的压力增大;当纸张由厚变薄时,橡皮滚筒与压印滚筒之间的压力减小。
第二,印版印到承印物上的图文尺寸(印迹长度)产生了变化。
当纸张由薄变厚时,压印滚筒得到的图文长度相对伸长;当纸张由厚变薄时,压印滚筒得到的图文长度相对缩小。
为了在纸厚发生变化时能对印刷机有较为准确的调节,我们先来了解一下印刷压力的调节以及二滚筒半径与图文尺寸的关系。
1.滚筒压力平版胶印工艺过程,是把印版上的图文墨迹先转移到橡皮布上,再由橡皮转移到承印物上。
在这个转移过程中必须使印版滚筒表面与橡皮滚筒,橡皮滚筒与压印滚筒(承印物)有充分地接触,即各接触面之间要有一定的接触压力,才能使油墨在其间充分转移,这个接触压力就是印刷压力。
滚筒压力:在印刷过程中压印体之间的相互作用力。
印刷压力是完成平版胶印的首要条件,滚筒之间的压力是否理想是保证印刷质量的关键。
理想的印刷压力指的是压力在能够保证油墨良好转移(即保证印刷品在印迹结实、网点饱满但不铺张、阶调层次清晰丰富)的基础上,尽最大可能减少滚筒间的印刷压力。
能否做到压力小(即使用理想压力),是衡量技术水平高低的重要指标之一,也是保证优质高产的重要条件。
印刷压力过大或过小对产品质量影响很大。
压力过大容易造成网点变形、糊版、产品墨色浓重,甚至图像失真等,压力过大还会加速印版磨损和机器磨损;压力过小会造成油墨转移量不足或不稳定,从而造成印迹空虚、墨色浅淡、图像轮廓不清、墨色深浅不一致等。
实际生产中调节印刷压力的方法:①通过调节滚筒中心距来调节印刷压力;②通过调整包衬(印版滚筒,橡皮滚筒的包衬)厚度来调节印刷压力。
注意:中心距的大小关系到滚筒齿轮的啮合状况,应根据印刷工艺的实际需要调节,不适宜经常调节,而且必须在机器操作使用标明的范围内调节,并必须保证两侧压力一致。
试印刷作业任务1—压力调节讲解
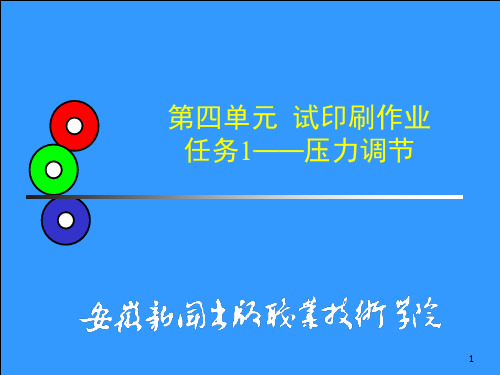
9
硬性包衬
硬性包衬是由衬垫纸和橡皮布组成, 即在橡皮布 下垫几张纸便构成硬性包衬。滚筒压痕宽度为 4-6mm,压缩量λ=0.04~0.08mm。这类包衬 相对较硬,包衬的弹性模量较大,少量变形就可 产生很大的印刷压力,且大多数胶印机采用接触 滚枕(即走肩铁),使得滚筒运转平稳。 国产的JJl02A、JJ204 型、JJ201 型的卷筒 纸胶印机,进口的Miller ( 米勒) 、Heideberg ( 海德堡) 、日本的小森机等大多采用硬性包衬。 10 胶印工艺及操作
总压力:P总 直接表示 印 刷 压 力 表 示 间接表示 压印宽度:b(mm) λ
b
线压力:PL= P总/L 面压力:PL= P总/(L*b) 压缩量:λ(mm)
剖面图 府视图
b
L
胶印工艺及操作
5
3. 印刷压力的分布图-马鞍形
胶印工艺及操作
6
在压印弧内 沿圆周方向各不相同,中心线压力最大, 两侧压力依次减少; 沿轴向方向,中间压力小,两端压力大。
滚筒体
滚筒缩径量,有正有负
印版包衬
滚筒体
滚枕间隙
Hale Waihona Puke 齿 轮 滚 节 枕 圆齿 轮 滚 节 枕 圆
滚筒体
滚枕间隙
滚筒体
滚筒体
滚筒体
走肩铁或滚枕
不走肩铁或滚枕
胶印工艺及操作
23
C. 压痕宽度法 胶印机的转印过程中,确定的压缩变形 量,一定相对着一个滚筒间的压痕宽度。 步骤: a.压痕 印版打满墨, 手动合压再离压 b.测量 钢卷尺测量压痕宽度 c.计算 入=b·b/4R
第四单元 试印刷作业 任务1——压力调节
1
导入
1、印刷压力的基础知识(来源、表示方法、 分布)
印刷压力调整原则四步骤(精)
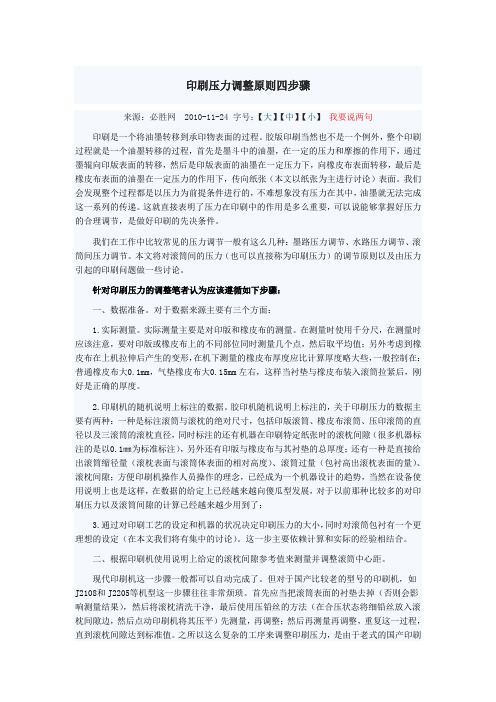
印刷压力调整原则四步骤来源:必胜网 2010-11-24 字号:【大】【中】【小】我要说两句印刷是一个将油墨转移到承印物表面的过程。
胶版印刷当然也不是一个例外,整个印刷过程就是一个油墨转移的过程,首先是墨斗中的油墨,在一定的压力和摩擦的作用下,通过墨辊向印版表面的转移,然后是印版表面的油墨在一定压力下,向橡皮布表面转移,最后是橡皮布表面的油墨在一定压力的作用下,传向纸张(本文以纸张为主进行讨论)表面。
我们会发现整个过程都是以压力为前提条件进行的,不难想象没有压力在其中,油墨就无法完成这一系列的传递。
这就直接表明了压力在印刷中的作用是多么重要,可以说能够掌握好压力的合理调节,是做好印刷的先决条件。
我们在工作中比较常见的压力调节一般有这么几种:墨路压力调节、水路压力调节、滚筒间压力调节。
本文将对滚筒间的压力(也可以直接称为印刷压力)的调节原则以及由压力引起的印刷问题做一些讨论。
针对印刷压力的调整笔者认为应该遵循如下步骤:一、数据准备。
对于数据来源主要有三个方面:1.实际测量。
实际测量主要是对印版和橡皮布的测量。
在测量时使用千分尺,在测量时应该注意,要对印版或橡皮布上的不同部位同时测量几个点,然后取平均值;另外考虑到橡皮布在上机拉伸后产生的变形,在机下测量的橡皮布厚度应比计算厚度略大些,一般控制在:普通橡皮布大0.1mm,气垫橡皮布大0.15mm左右,这样当衬垫与橡皮布装入滚筒拉紧后,刚好是正确的厚度。
2.印刷机的随机说明上标注的数据。
胶印机随机说明上标注的,关于印刷压力的数据主要有两种:一种是标注滚筒与滚枕的绝对尺寸,包括印版滚筒、橡皮布滚筒、压印滚筒的直径以及三滚筒的滚枕直径,同时标注的还有机器在印刷特定纸张时的滚枕间隙(很多机器标注的是以0.1㎜为标准标注),另外还有印版与橡皮布与其衬垫的总厚度;还有一种是直接给出滚筒缩径量(滚枕表面与滚筒体表面的相对高度)、滚筒过量(包衬高出滚枕表面的量)、滚枕间隙;方便印刷机操作人员操作的理念,已经成为一个机器设计的趋势,当然在设备使用说明上也是这样,在数据的给定上已经越来越向傻瓜型发展,对于以前那种比较多的对印刷压力以及滚筒间隙的计算已经越来越少用到了;3.通过对印刷工艺的设定和机器的状况决定印刷压力的大小,同时对滚筒包衬有一个更理想的设定(在本文我们将有集中的讨论)。
纸箱印刷常见故障及解决方案|太全面了

纸箱印刷常见故障及解决方案|太全面了现在中小型的包装,如啤酒、饮料、果品等食品纸箱,采用白板纸进行彩色印刷越来越多。
纸箱的这种预印工艺,比用楞纸板直接进行印刷的质量有较大提高,且版面印刷结构和印刷适应性也更广阔了。
但是,同其它印刷工艺一样,用胶印机或凸版印刷机印刷各种纸箱面纸或纸盒、袋产品,也不可避免遇到一些故障问题,影响产品质量。
所以,正确认识和了解印刷过程中若干故障现象,把好印刷操作和工艺技术关,才能更好地提高生产效率和产品质量。
一印刷压力不适引起的墨杠现象第一情况:当胶印滚筒轴承严重磨损时,由于过大的滚筒离让产生,使滚筒表面滑动摩擦而引起墨杠痕迹的出现;第二种情况:由于采用硬包衬,压印过程中因滑动现象的产生而引起墨杠;第三种情况:滚筒齿轮磨损严重,滚筒中心距过大,以致齿轮侧隙太大,使滚筒合压后齿轮产生颤动,滚筒表面发生滑动摩擦而引起墨杠;第四种情况:印版滚筒和橡皮布滚筒间的压力太大,以致橡皮布受挤压作用,形成较大的摩擦滑动,使版面网点纵向变形扩大而造成墨杠。
对上述情况应通过更换滚筒轴承、调整包衬垫料特性、缩小滚筒中心距,使齿轮的啮合侧隙小于0.1mm;按设备的规范要求,定好衬垫厚度,避免压力过大情况的出现,以防止墨杠现象的产生。
二滚筒咬牙不良引起的套印不准故障故障问题:当滚筒咬牙的牙面出现磨损、变形,咬牙压力存在不均匀、不足情况时,印张进入咬牙后在压印中容易产生滑移现象,造成产品套印不准,尤其是印刷版面受墨面积大,油墨粘度也大的情况下,更容易出现套印不准现象。
解决办法:将磨损厉害的咬牙拆下更换上新的咬牙,将咬纸压力不均、不足的咬牙,进行调整校正使它的整个牙面紧咬纸边;对油墨粘稠度过大的,采用助剂进行适度的稀释调整,降低油墨的粘度;对印刷专色油墨可通过将油墨色相适当调深一点,使印刷墨层减薄一点,这样既可降低油墨粘性,又能达到符合印刷色相·的要求。
此外,还可适当减轻印刷压力,防止印张在压印中因滑移而造成套印不准。
纸箱印刷过程中应注意的问题
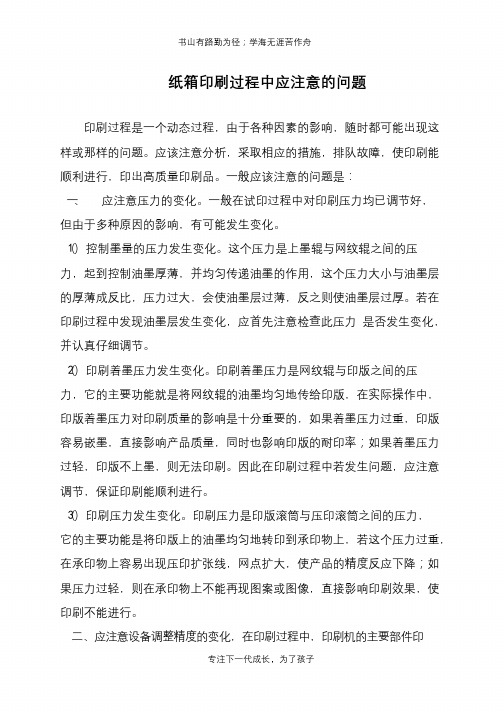
书山有路勤为径;学海无涯苦作舟
纸箱印刷过程中应注意的问题
印刷过程是一个动态过程,由于各种因素的影响,随时都可能出现这样或那样的问题。
应该注意分析,采取相应的措施,排队故障,使印刷能顺利进行,印出高质量印刷品。
一般应该注意的问题是:
一、应注意压力的变化。
一般在试印过程中对印刷压力均已调节好,
但由于多种原因的影响,有可能发生变化。
(1)控制墨量的压力发生变化。
这个压力是上墨辊与网纹辊之间的压
力,起到控制油墨厚薄,并均匀传递油墨的作用,这个压力大小与油墨层的厚薄成反比,压力过大,会使油墨层过薄,反之则使油墨层过厚。
若在印刷过程中发现油墨层发生变化,应首先注意检查此压力是否发生变化,并认真仔细调节。
(2)印刷着墨压力发生变化。
印刷着墨压力是网纹辊与印版之间的压
力,它的主要功能就是将网纹辊的油墨均匀地传给印版,在实际操作中,印版着墨压力对印刷质量的影响是十分重要的,如果着墨压力过重,印版容易嵌墨,直接影响产品质量,同时也影响印版的耐印率;如果着墨压力过轻,印版不上墨,则无法印刷。
因此在印刷过程中若发生问题,应注意调节,保证印刷能顺利进行。
(3)印刷压力发生变化。
印刷压力是印版滚筒与压印滚筒之间的压力,
它的主要功能是将印版上的油墨均匀地转印到承印物上,若这个压力过重,在承印物上容易出现压印扩张线,网点扩大,使产品的精度反应下降;如果压力过轻,则在承印物上不能再现图案或图像,直接影响印刷效果,使印刷不能进行。
二、应注意设备调整精度的变化,在印刷过程中,印刷机的主要部件印
专注下一代成长,为了孩子。
调整印刷压力应从多方面入手

调整印刷压力应从多方面入手【天意数字快印】胶版印刷的产品种类很多,有报纸书刊,也有包装装潢品,印刷用纸的表面状况也有很大的差别,因而印刷中所需要的印刷压力也各有不同。
下表所罗列的纸张平滑度和印刷压力的数据,是在单张纸胶印机上,将印版滚筒和橡皮布滚筒间的线压力固定为5㎏/㎝,以4000转/小时的印刷速度,用不同平滑度的纸张进行印刷,在获得质量最佳的印刷品时,测得的压印滚筒与橡皮布滚筒的线压力。
很多生产实例都可以证明,当印刷速度显著增加时,印刷压力也要增加。
因为印刷速度提高时,印刷面之间相对应的质点所接触的时间也有所减少,这就必须通过较大的压力,使印刷表面之间不完全接触的程度减小,便于油墨能够较快地从供墨表面转移到受墨表面,使油墨能在短时间内完成必要的转移。
同样是轮转机,近代的高速机器的必须印刷压力,也会比旧式机器高些,因为高速机器除了压印时间较短以外,它的滚筒利用系数较大,半径较小,所以压印时的压缩宽度也相对减小,同样会影响油墨的转移。
不同的产品,有着不同的复制要求。
除了采用不同的原材料和印版外,还可以从印刷压力方面设法适应之。
“实地”图文可以(也允许)使压力稍大一些来达到印迹结实的要求。
网线图文则应该十分强调“理想压力”,避免网点扩大而损失层次。
高网线产品对复制的质量要求更高,特别要控制印刷压力,使之达到最小值,印刷该类产品时,除尽量采用表面平滑的涂料纸外,还应该注意对印版质量的选择和对印版表面水墨平衡的严格控制。
橡皮布及其衬垫材料(衬垫纸、软垫、还包括毡呢)的变形对印刷压力有密切的关系,应该选用富有弹性,而在大量印刷后弹性不容易失去的橡皮布、衬垫纸以及毡呢,来满足理想印刷压力的基本要求。
反之,如果为了降低成本,选用国产质量比较差的橡皮布,则必然要提高“最小印刷压力的绝对值”。
如使用进口气垫橡皮布印刷压力一般设定为0.08~0.10mm,如果要是国产橡皮布同时使用毛尼做衬垫时,一般印刷压力设定为0.2~0.25mm。
四条瓦楞纸箱印刷技巧

来 的A 型 瓦楞纸 板 ,经 印刷机 印刷 会使瓦楞纸板 际操 作 中, 印版 着墨 压力对 印刷 质量 的影响 是 的平 压 强度受 到较 大损伤 ,另 外瓦 楞纸 板经过 十分重 要 的,如 果着 墨压力 过重 , 印版 容 易嵌
印刷 辊和 压 印辊后 ,其边 压强度 也 会有较 大损 墨 , 影 响 产 品 质 量 的 同 时 也 影 响 印 版 的 耐 印
伤。Байду номын сангаас
率 ;如果着 墨压 力过 轻 ,印版不 上墨 ,则无 法
如果 瓦楞 纸板 的面里 克度相 差 太大 ,还容 印刷 。 因此 在 印刷 过程 中应 注意调 节 ,保 证 印 易导 致 瓦楞 纸 板 线 生 产 出 的瓦 楞 纸 板 出现 翘 届 0 能J 『 』 顷 禾 U 进行 。 曲。翘 曲纸板 对 印刷会 带来套 印不 准和 印刷 开 槽走 规现 象 ,因此对 翘 曲纸板 应采 取压 平后 再
印刷压 力 的调 整 以油墨均 匀适 中 、墨迹清
楞和 在楞 的低 凹处 印不 出所 需的 图文 内容 ,针 晰,瓦棱 面无凹陷、平整 不变形为宜 。 对露 楞造 成 的瓦楞纸 板表 面不 平整 ,应选 用 回
压 力 一 旦 确 定 , 不 要 随 便 调 整 。 印刷 着 墨
弹性 较好 的柔 性树 脂版做 印版 ,来 克服 印刷不 压力 是 网纹 辊与 印版之 间的压力 ,它 的主要功
纸箱 同批 印刷 色差故 障排除技巧
在 一次 生产 中 ,四色机 印刷 过程 中 出现 了 加 大施 墨量 ,在表 面平滑 的纸 张上应减 少施 墨
印刷机印刷压力的调整
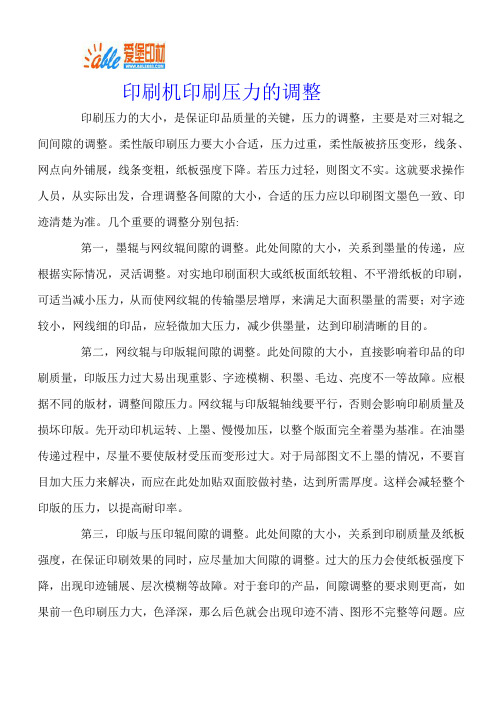
印刷机印刷压力的调整印刷压力的大小,是保证印品质量的关键,压力的调整,主要是对三对辊之间间隙的调整。
柔性版印刷压力要大小合适,压力过重,柔性版被挤压变形,线条、网点向外铺展,线条变粗,纸板强度下降。
若压力过轻,则图文不实。
这就要求操作人员,从实际出发,合理调整各间隙的大小,合适的压力应以印刷图文墨色一致、印迹清楚为准。
几个重要的调整分别包括:第一,墨辊与网纹辊间隙的调整。
此处间隙的大小,关系到墨量的传递,应根据实际情况,灵活调整。
对实地印刷面积大或纸板面纸较粗、不平滑纸板的印刷,可适当减小压力,从而使网纹辊的传输墨层增厚,来满足大面积墨量的需要;对字迹较小,网线细的印品,应轻微加大压力,减少供墨量,达到印刷清晰的目的。
第二,网纹辊与印版辊间隙的调整。
此处间隙的大小,直接影响着印品的印刷质量,印版压力过大易出现重影、字迹模糊、积墨、毛边、亮度不一等故障。
应根据不同的版材,调整间隙压力。
网纹辊与印版辊轴线要平行,否则会影响印刷质量及损坏印版。
先开动印机运转、上墨、慢慢加压,以整个版面完全着墨为基准。
在油墨传递过程中,尽量不要使版材受压而变形过大。
对于局部图文不上墨的情况,不要盲目加大压力来解决,而应在此处加贴双面胶做衬垫,达到所需厚度。
这样会减轻整个印版的压力,以提高耐印率。
第三,印版与压印辊间隙的调整。
此处间隙的大小,关系到印刷质量及纸板强度,在保证印刷效果的同时,应尽量加大间隙的调整。
过大的压力会使纸板强度下降,出现印迹铺展、层次模糊等故障。
对于套印的产品,间隙调整的要求则更高,如果前一色印刷压力大,色泽深,那么后色就会出现印迹不清、图形不完整等问题。
应适当减轻前色压力,加大后印压力,使印品质量最佳。
由于生产中使用的瓦楞纸板的平整度及平滑度不同,所以在印刷过程中要特别注意,换纸印刷时,应适当调整此处间隙。
当然,要尽量使用平整性好的纸板,以满足印刷的要求。
此外,还要注意各辊之间轴线的平行,防止出现各辊两端间压力不同的情况,以保护网纹辊及印版的正常使用,防止因过大的压力使印版和网纹辊受损。
只要干货!纸箱生产常见问题与解决办法
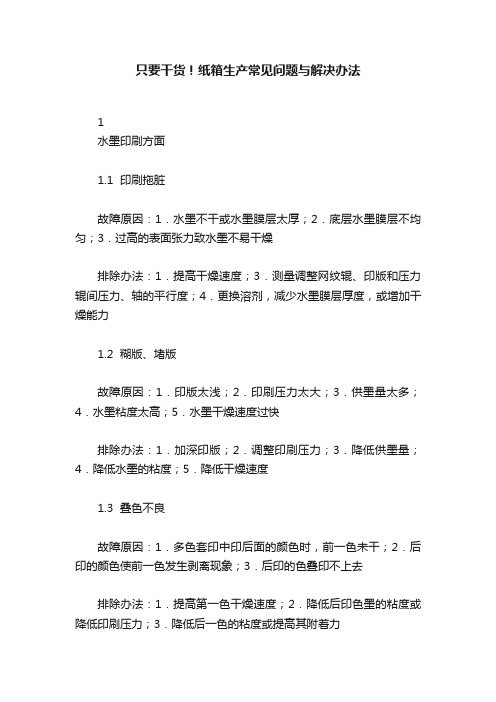
只要干货!纸箱生产常见问题与解决办法1水墨印刷方面1.1 印刷拖脏故障原因:1.水墨不干或水墨膜层太厚;2.底层水墨膜层不均匀;3.过高的表面张力致水墨不易干燥排除办法:1.提高干燥速度;3.测量调整网纹辊、印版和压力辊间压力、轴的平行度;4.更换溶剂,减少水墨膜层厚度,或增加干燥能力1.2 糊版、堵版故障原因:1.印版太浅;2.印刷压力太大;3.供墨量太多;4.水墨粘度太高;5.水墨干燥速度过快排除办法:1.加深印版;2.调整印刷压力;3.降低供墨量;4.降低水墨的粘度;5.降低干燥速度1.3 叠色不良故障原因:1.多色套印中印后面的颜色时,前一色未干;2.后印的颜色使前一色发生剥离现象;3.后印的色叠印不上去排除办法:1.提高第一色干燥速度;2.降低后印色墨的粘度或降低印刷压力;3.降低后一色的粘度或提高其附着力1.4 印刷针孔或鱼眼故障原因:1.加消泡剂过多或消泡剂与水墨不溶;2.承印材表面张力过大;3.水墨泡沫或微沫过多排除办法:1.更换水墨或加没有消泡剂的新鲜水墨;2.加入合适的添加剂;3.除去泡沫或更换水墨1.5 颜色太浅故障原因:1.水墨的粘度太低;2.网纹辊网线太细;3网纹辊磨损或未清洗干净;4.上墨量太小排除办法:1.提高水墨的粘度;2.调换粗网线的网纹辊;3.换用新的网纹辊或对网纹辊进行彻底清洗;4.降低传墨辊或刮墨刀的压力或加快印刷速度。
1.6 颜色太深故障原因:1.水墨的粘度太高;2.网纹辊太粗;3.水墨色饱和度太高;4.上墨量太大排除办法:1.加稀释剂降低粘度;2.换细网纹辊;3.加撤淡剂降低颜色深度4.提高传刮墨辊或刮墨刀的压力1.7 印迹不实故障原因:1.印版压力太小;2.水墨膜层太薄;3.水墨的粘性大;4.纸板表面太湿或太光排除办法:1.增加印版压力;2.增加墨层厚度;3.加慢干剂,降水墨PH值,或提车速;4.加入合适的添加剂1.8 印刷杂色故障原因:1.印版表面不光或不平整;2.印版压力不当;3.水墨粘度太低;墨加水太多使水墨失去平衡;5.网纹辊脏排除办法:1.压紧衬垫与印版;2.调整印刷辊压力;3.加新鲜墨提高粘度;加新鲜水墨或将脱水剂加入水墨;5.清洁或更换网纹辊1.9 线条边缘毛刺故障原因:1.水墨干燥速度太快;2.压力不匀,压力调节不当;3.水墨墨层太厚;印版压力过大;印版不平、磨损太光或安装不当;5.灰尘或纸屑粘到印版上排除办法:1.降低水墨的干燥速度;2.调整印版与网纹辊之间的压力;3.减少墨层厚度;拉平、垫起、清洁或更换印刷或衬垫;5.改善印刷环境1.10 飞墨故障原因:1.油墨量太大;2.油墨管出口位置太高排除办法:1.调整油墨量;2.调低油墨管出口位置1.11 印刷重影故障原因:1.印版压力太大;2.网纹辊与印版辊间压力过大;3.印版或版辊衬垫松弛排除办法:1.减少印版与纸板压力;2.调整减少网纹辊压力,检查印版水平和衬垫;3.重装印版使其贴紧版筒1.12 颜色不稳定故障原因:1.粘度或PH值有变化;2.操作过程有误;3.配墨过程有误排除办法:1.检查粘度和PH值与上次印刷时有所变化;2.检查操作程序3.向本公司反应质量事故1.13 压线位印刷实地漏白故障原因:1.瓦线未按规定压线;2.压线处印版衬垫不够好排除办法:1.应按规定压线或先印刷再压线;2.压线处版垫高1.14 印刷条痕(现坑纹)故障原因:1.网纹辊磨损或脏污,网线太粗;2.印版太硬;3.水墨配方不对;4.水墨粘度太低排除办法:1.更换或清洗网纹辊;2.使用低硬度印版;3.更换水墨或加添加剂;4.换新鲜水墨或调高水墨粘度1.15 柔性版网点印刷出现丢失或变形现象故障原因:1.印刷压力和网纹辊压力太大。
三种印刷压力的调试方法
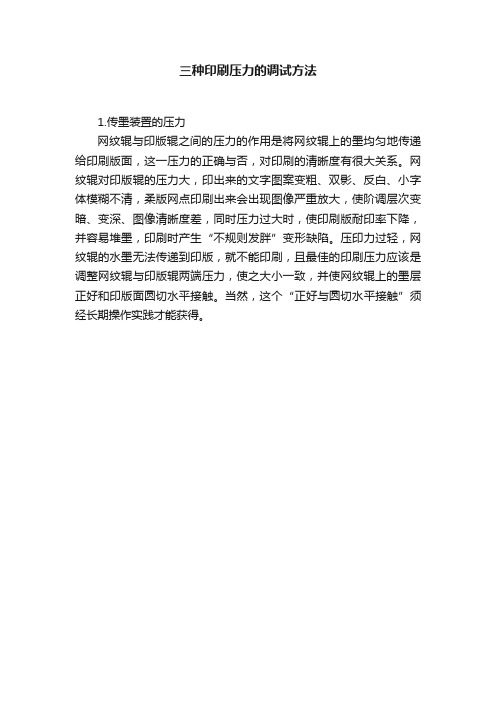
三种印刷压力的调试方法1.传墨装置的压力网纹辊与印版辊之间的压力的作用是将网纹辊上的墨均匀地传递给印刷版面,这一压力的正确与否,对印刷的清晰度有很大关系。
网纹辊对印版辊的压力大,印出来的文字图案变粗、双影、反白、小字体模糊不清,柔版网点印刷出来会出现图像严重放大,使阶调层次变暗、变深、图像清晰度差,同时压力过大时,使印刷版耐印率下降,并容易堆墨,印刷时产生“不规则发胖”变形缺陷。
压印力过轻,网纹辊的水墨无法传递到印版,就不能印刷,且最佳的印刷压力应该是调整网纹辊与印版辊两端压力,使之大小一致,并使网纹辊上的墨层正好和印版面圆切水平接触。
当然,这个“正好与圆切水平接触”须经长期操作实践才能获得。
2.匀墨装置的压力这个压力带是指匀墨辊与网纹辊之间的压力,它的主要功能是控制水墨传递的大小及均匀度。
两辊之间的压力大(间隙小),网纹辊面上的墨量相对较少,反之则墨量较多。
这一印刷压力的大小与印刷面积的大小有关,一般而言印刷面积较大的压力可轻些,以增加水墨量来提高墨层的厚度,鲜艳度。
而印刷面积较小和较为细腻的文字图案,其压力则要略大一些,以减少墨量提高细小文字的清晰度,这一压力大小的原则一般视产品的特性而定。
网点印刷时,压力相对大一些,细小文字线条压力可略大一些,大字及大实地产品可相对小些。
3.压印装置的压力这个压力是指版辊与压印辊对纸板的印刷压力,这个压力的作用是印版上的墨层准确无误地转印到纸板上,在印刷过程中,这是最后关键,压力过大,印出的柔版网点呈铺展状,中间色浅,四周呈深圈,对图像层次有很大影响,文字线条版则铺展印迹双边,小字体易模糊,用手触摸有明显的凹陷感。
正确的压力是当印刷的印刷面(凸出部分)与纸板接触时候,网点扩大最小,字线清晰,不双印铺展,文字图像全部印刷出来,无漏白现象为最佳。
压入纸板深度不超过0.3mm,同时在印刷过程中,要根据印刷的具体情况而随时加以调节,使之保持在最佳状态。
印刷压力的调整原则与常见问题分析下
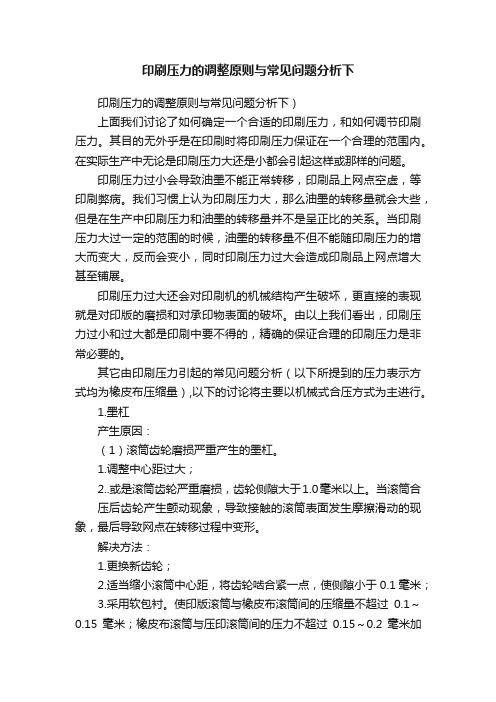
印刷压力的调整原则与常见问题分析下印刷压力的调整原则与常见问题分析下)上面我们讨论了如何确定一个合适的印刷压力,和如何调节印刷压力。
其目的无外乎是在印刷时将印刷压力保证在一个合理的范围内。
在实际生产中无论是印刷压力大还是小都会引起这样或那样的问题。
印刷压力过小会导致油墨不能正常转移,印刷品上网点空虚,等印刷弊病。
我们习惯上认为印刷压力大,那么油墨的转移量就会大些,但是在生产中印刷压力和油墨的转移量并不是呈正比的关系。
当印刷压力大过一定的范围的时候,油墨的转移量不但不能随印刷压力的增大而变大,反而会变小,同时印刷压力过大会造成印刷品上网点增大甚至铺展。
印刷压力过大还会对印刷机的机械结构产生破坏,更直接的表现就是对印版的磨损和对承印物表面的破坏。
由以上我们看出,印刷压力过小和过大都是印刷中要不得的,精确的保证合理的印刷压力是非常必要的。
其它由印刷压力引起的常见问题分析(以下所提到的压力表示方式均为橡皮布压缩量),以下的讨论将主要以机械式合压方式为主进行。
1.墨杠产生原因:(1)滚筒齿轮磨损严重产生的墨杠。
1.调整中心距过大;2..或是滚筒齿轮严重磨损,齿轮侧隙大于1.0毫米以上。
当滚筒合压后齿轮产生颤动现象,导致接触的滚筒表面发生摩擦滑动的现象,最后导致网点在转移过程中变形。
解决方法:1.更换新齿轮;2.适当缩小滚筒中心距,将齿轮啮合紧一点,使侧隙小于0.1毫米;3.采用软包衬。
使印版滚筒与橡皮布滚筒间的压缩量不超过0.1~0.15毫米;橡皮布滚筒与压印滚筒间的压力不超过0.15~0.2毫米加上一张纸的厚度。
(2)滚筒轴承齿轮磨损严重产生的墨杠。
当轴头和轴套磨损严重时,叼口受压后立即产生离让,引起滑动摩擦而产生深墨杠。
解决方法:①更换新轴套;②如果要是老式低速胶印机可以将印版轴头上的刚带收紧些。
(3)印版滚筒和橡皮滚筒之间的压力过大。
墨杠特征是固定区域的墨杠。
印版和橡皮滚筒之间的压力过大,橡皮布在挤压作用下,产生较大的摩擦滑动,从而造成网点变形而形成墨杠。
纸箱印刷中压力及调整方法
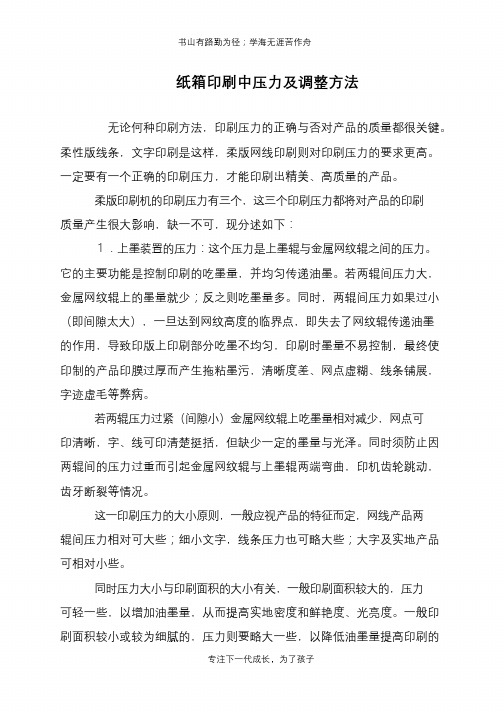
书山有路勤为径;学海无涯苦作舟
纸箱印刷中压力及调整方法
无论何种印刷方法,印刷压力的正确与否对产品的质量都很关键。
柔性版线条,文字印刷是这样,柔版网线印刷则对印刷压力的要求更高。
一定要有一个正确的印刷压力,才能印刷出精美、高质量的产品。
柔版印刷机的印刷压力有三个,这三个印刷压力都将对产品的印刷
质量产生很大影响,缺一不可,现分述如下:
1.上墨装置的压力:这个压力是上墨辊与金属网纹辊之间的压力。
它的主要功能是控制印刷的吃墨量,并均匀传递油墨。
若两辊间压力大,金属网纹辊上的墨量就少;反之则吃墨量多。
同时,两辊间压力如果过小(即间隙太大),一旦达到网纹高度的临界点,即失去了网纹辊传递油墨
的作用,导致印版上印刷部分吃墨不均匀,印刷时墨量不易控制,最终使印制的产品印膜过厚而产生拖粘墨污,清晰度差、网点虚糊、线条铺展,字迹虚毛等弊病。
若两辊压力过紧(间隙小)金属网纹辊上吃墨量相对减少,网点可
印清晰,字、线可印清楚挺括,但缺少一定的墨量与光泽。
同时须防止因两辊间的压力过重而引起金属网纹辊与上墨辊两端弯曲,印机齿轮跳动,齿牙断裂等情况。
这一印刷压力的大小原则,一般应视产品的特征而定,网线产品两
辊间压力相对可大些;细小文字,线条压力也可略大些;大字及实地产品可相对小些。
同时压力大小与印刷面积的大小有关,一般印刷面积较大的,压力
可轻一些,以增加油墨量,从而提高实地密度和鲜艳度、光亮度。
一般印刷面积较小或较为细腻的,压力则要略大一些,以降低油墨量提高印刷的
专注下一代成长,为了孩子。
瓦楞纸箱印刷中常见的几个问题分析

瓦楞纸箱印刷中常见的几个问题分析瓦楞纸箱作为一种常见的包装材料,其图案的印刷质量对于产品的外观和质量都具有重要的影响。
然而,在瓦楞纸箱印刷过程中,常常会遇到一些问题,影响印刷质量和产量。
本文将对瓦楞纸箱印刷中常见的几个问题进行分析,并提出相应的解决方案。
1. 印刷颜色不真实在瓦楞纸箱印刷中,有时会出现印刷颜色不够真实的情况。
这种问题的主要原因是印刷机的墨路设置不当。
当墨路不均衡或者墨量不适当时,就会导致印刷颜色变淡或者色差过大的情况。
解决方案:(1)调整墨路:对于印刷颜色不真实的情况,可以考虑调整墨路。
首先需要使用专业的测试仪器来测试各个墨路的墨量,找出墨量不均衡的原因。
然后可以通过调整辊道压力或者调整墨槽和刮刀的间距来解决问题。
(2)调整墨量:对于印刷颜色过淡或者过浓的情况,可以通过调整墨量来解决。
可以尝试减少或者增加墨量,或者调整墨盘的转速来改变墨量。
2. 印刷墨层不均匀瓦楞纸箱的印刷墨层不均匀是另一个常见的问题。
这种问题的主要原因是印刷机的墨路设置不当、印刷机的辊子表面磨损或者印版的质量不好。
解决方案:(1)检查印刷机的墨路:如果墨路有问题,需要检查印刷机的墨路是否畅通无阻,然后做出相应的调整。
(2)检查印刷机的辊子表面:如果辊子表面磨损,可以考虑更换新的辊子表面或者使用适当的润滑剂来解决。
(3)检查印版的质量:如果印版的质量不好,可以更换新的印版。
3. 印刷机速度过慢在实际的印刷过程中,有时会出现印刷速度过慢的情况。
这种情况主要是因为印刷机的机械部分出现了问题。
解决方案:(1)检查印刷机的机械部分:在印刷机运行过程中,需要定期检查印刷机的机械部分是否出现了问题。
如果出现了问题,需要及时修理。
(2)使用质量更好的配件:使用质量更好的配件可以增强印刷机的稳定性和耐久性,从而避免发生故障。
总之,对于瓦楞纸箱印刷过程中出现的问题,我们需要及时检查,确定问题原因并采取相应的措施,从而确保印刷质量和生产效率。
包装彩箱承压力难题的解决

包装彩箱承压力难题的解决[一]纸张搭配。
有的公司采用的材质,面是300g涂布纸,里是170g美国红,芯纸(瓦纸)是170g中强瓦纸。
如此纸张搭配欠妥,欲增强纸箱的承压力、即抗压强度就必须增强芯纸的承压能力,建议:只要面纸裱胶后不显瓦楞痕迹就应尽量采用低克重纸张;芯纸(瓦纸)可用挺力好、环压强度高的草浆纸代替中强瓦纸(因中强瓦纸多为再生浆加生浆的混合纸,吸水快、环压强度低、韧性好,但挺度低。
经试验采用可勃法测定中强瓦纸比草浆纸吸水率高15-30%左右);冻品箱也应采用吸水率低的瓦纸。
里纸可适当增加克重。
其纸张搭配面可选用220-230g涂布纸,瓦纸可选用180g草浆瓦纸,200g或220g美国红作里纸,如此无论是质量,还是价位更具竞争优势。
[二]胶的质量彩箱贴面要二次裱合,大都是自制或购买的玉米淀粉胶。
玉米淀粉胶的优劣与制作工艺环境、原料质量、搅拌时间等有密切的关系,众所周知,不必赘言。
笔者仅将制胶主要原料之一的玉米淀粉质量要求和淀粉胶的水比、附料添加方面介绍点参考意见:玉米淀粉质量要求,细度98-100目,灰分不超0.1%,含水量14.0%,酸度20cc/100g;二氧化硫0.004%,气味正常,颜色白或略带微黄。
制胶时淀粉质量如不符合此标准,可视质量情况适当降低水比。
气温升高,水比应相应减少,硼砂、片碱应酌情增加,H2O2应适当减少用量。
熟胶制好后,不宜久放,尤其夏季最好随做随用,胶液里加入甲醛3-4%、甘油0.1%、硼酸0.1%,可增加纸张阻水能力,加快粘合速度,增强纸板硬度。
(做冻品箱可参考)除此之外,在贴面板时亦可采用环保型的化学胶,即PCA粘合剂。
其特点是裱制瓦楞纸板平整、挺直、粘合好、经久不变形,其制作方法是(以100kg粘合剂为例):用料配比:聚乙烯醇13.7kg,醋酸聚乙烯醇乳液2.74kg,草酸1.37kg,水82kg(水比1:6)。
首先将水加热至90°C,加入聚乙烯醇搅拌均匀,继续加热至水沸,保温3小时,再加入草酸搅拌,最后加入醋酸聚乙烯醇乳液搅拌均匀即成。
- 1、下载文档前请自行甄别文档内容的完整性,平台不提供额外的编辑、内容补充、找答案等附加服务。
- 2、"仅部分预览"的文档,不可在线预览部分如存在完整性等问题,可反馈申请退款(可完整预览的文档不适用该条件!)。
- 3、如文档侵犯您的权益,请联系客服反馈,我们会尽快为您处理(人工客服工作时间:9:00-18:30)。
书山有路勤为径;学海无涯苦作舟
纸箱印刷中的压力及调整方法
无论何种印刷方法,印刷压力的正确与否对产品的质量都很关键。
柔性版线条,文字印刷是这样,柔版网线印刷则对印刷压力的要求更高。
一定要有一个正确的印刷压力,才能印刷出精美、高质量的产品。
柔版印刷机的印刷压力有三个,这三个印刷压力都将对产品的
印刷质量产生很大影响,缺一不可,现分述如下:
1.上墨装置的压力:这个压力是上墨辊与金属网纹辊之间的压力。
它的主要功能是控制印刷的吃墨量,并均匀传递油墨。
若两辊间压力大,金属网纹辊上的墨量就少;反之则吃墨量多。
同时,两辊间压力如果过小(即间隙太大),一旦达到网纹高度的临界点,即失去了网纹辊传递油墨的作用,导致印版上印刷部分吃墨不均匀,印刷时墨量不易控制,最终使印制的产品印膜过厚而产生拖粘墨污,清晰度差、网点虚糊、线条铺展,字迹虚毛等弊病。
若两辊压力过紧(间隙小)金属网纹辊上吃墨量相对减少,网点可
印清晰,字、线可印清楚挺括,但缺少一定的墨量与光泽。
同时须防止因两辊间的压力过重而引起金属网纹辊与上墨辊两端弯曲,印机齿轮跳动,齿牙断裂等情况。
这一印刷压力的大小原则,一般应视产品的特征而定,网线产品两
辊间压力相对可大些;细小文字,线条压力也可略大些;大字及实地产品可相对小些。
同时压力大小与印刷面积的大小有关,一般印刷面积较大的,压力
可轻一些,以增加油墨量,从而提高实地密度和鲜艳度、光亮度。
一般印刷面积较小或较为细腻的,压力则要略大一些,以降低油墨量提高印刷的
专注下一代成长,为了孩子。