中介机匣加工工艺优化
对机匣零件加工工艺的研究
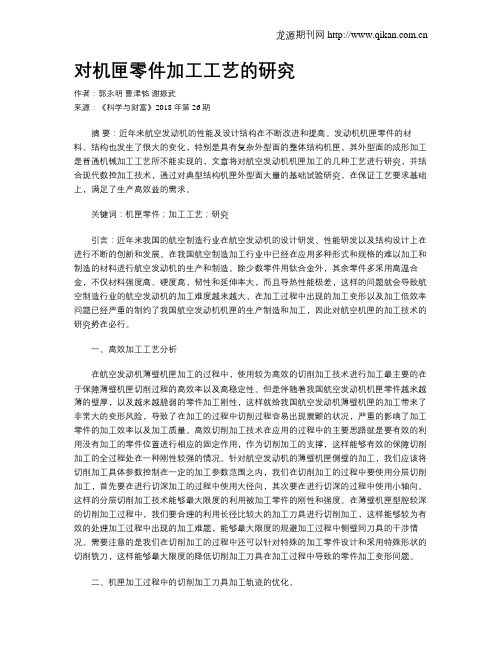
对机匣零件加工工艺的研究作者:郭永明曹津铭谢振武来源:《科学与财富》2018年第26期摘要:近年来航空发动机的性能及设计结构在不断改进和提高。
发动机机匣零件的材料、结构也发生了很大的变化,特别是具有复杂外型面的整体结构机匣,其外型面的成形加工是普通机械加工工艺所不能实现的,文章将对航空发动机机匣加工的几种工艺进行研究,并结合现代数控加工技术,通过对典型结构机匣外型面大量的基础试验研究,在保证工艺要求基础上,满足了生产高效益的需求。
关键词:机匣零件;加工工艺;研究引言:近年来我国的航空制造行业在航空发动机的设计研发、性能研发以及结构设计上在进行不断的创新和发展。
在我国航空制造加工行业中已经在应用多种形式和规格的难以加工和制造的材料进行航空发动机的生产和制造。
除少数零件用钛合金外,其余零件多采用高温合金,不仅材料强度高、硬度高,韧性和延伸率大,而且导热性能极差,这样的问题就会导致航空制造行业的航空发动机的加工难度越来越大,在加工过程中出现的加工变形以及加工低效率问题已经严重的制约了我国航空发动机机匣的生产制造和加工,因此对航空机匣的加工技术的研究势在必行。
一、高效加工工艺分析在航空发动机薄壁机匣加工的过程中,使用较为高效的切削加工技术进行加工最主要的在于保障薄壁机匣切削过程的高效率以及高稳定性。
但是伴随着我国航空发动机机匣零件越来越薄的壁厚,以及越来越脆弱的零件加工刚性,这样就给我国航空发动机薄壁机匣的加工带来了非常大的变形风险,导致了在加工的过程中切削过程容易出现震颤的状况,严重的影响了加工零件的加工效率以及加工质量。
高效切削加工技术在应用的过程中的主要思路就是要有效的利用没有加工的零件位置进行相应的固定作用,作为切削加工的支撑,这样能够有效的保障切削加工的全过程处在一种刚性较强的情况。
针对航空发动机的薄壁机匣侧壁的加工,我们应该将切削加工具体参数控制在一定的加工参数范围之内,我们在切削加工的过程中要使用分层切削加工,首先要在进行切深加工的过程中使用大径向,其次要在进行切深的过程中使用小轴向。
机匣加工工艺

机匣加工工艺机匣一般是一个圆柱形或圆锥形的薄壁筒体,主要起承力和包容作用,而且对不同段机匣的要求不一样。
涡轮机匣通常是带有安装边的圆柱形或截锥形壳体,其前后安装边分别与燃烧室机匣和动力涡轮前的中间机匣连接,涡轮机匣上作用有扭矩、轴向力、惯性力和内环压差力等。
近年来航空发动机的性能及设计结构在不断改进和提高。
随之而来,发动机机匣零件的材料、结构也发生了很大的变化,越来越多的难加工材料,像钛合金、高温合金、不锈钢、硬质合金以及复合材料等被采用。
机匣设计结构也越来越先进,整体结构机匣、单一机匣所具有的功能也越来越多,因此,机匣零件的制造成形难度也越来越大。
特别是具有复杂外型面的整体结构机匣,其外型面的成形加工是普通机械加工工艺所不能实现的,只有应用多轴数控加工技术才能实现复杂外型面的成形加工。
但在加工过程中存在着刀具费用高,加工效率低,设备占用量大。
针对多年来生产中的加工难题,寻求品质的提升、效率的提高、成本降低的途径和方法,运用特种加工技术——电火花加工技术和电解加工技术,同时结合现代数控加工技术,通过对典型结构机匣外型面大量的基础试验研究,取得了良好的加工效果,在保证工艺要求基础上,满足了生产高效益的需求。
多轴数控铣削机匣型面的成形,国内通常是通过在多轴数控铣削设备上加工完成的。
该零件外环形面共分二级,分布有二条环形凸缘,下部有1个纵向小凸缘,两个纵向凸缘对称分布。
由于机匣毛坯是自自锻件,加工余量很大,且零件材料难切削,为了保证尺寸加工精度和表面加工质量,防止加工后零件变形。
其外型面加工分层、分块进行,采取合理的走刀路径,采用对称的切削加工余量。
分几次走刀加工到最后尺寸的方法,以减少加工后的变形。
因此,该机匣加工划分三个主要阶段并附加特征工序热处理,以去除材料内应力,防止零件变形。
火花高效放电铣电火花高效放电铣加工技术原理。
电火花高效放电铣借鉴了数控铣削加工方式,采用简单的超长铜管做工具电极,由导向器导向,在工作中电极作高速旋转,在电极与工件之间施加高效高频脉冲电源,电流高达上百安培,对加工区施以冲、浸工作液进行有效冷却排屑,通过专用数控系统控制工件与电极之间的相对运动轨迹,在电极与工件之间产生高效脉冲放电,加工出所需工件的形状,实现零件复杂型面的高效去余量加工。
航空发电机机匣构件的机械加工技术优化

航空发电机机匣构件的机械加工技术优化作者:邵晓寒来源:《中国新技术新产品》2017年第22期摘要:伴随着我国科学技术的不断发展以及创新,我国在很多的行业中都在享受着我国科学进步带来的福利。
在众多的行业中,作为我国重点行业的航空领域也在很大程度上享受着科技进步带来的福利。
在我国航空领域中,航空发动机非常重要,因此我们要在多个方面保障航空发动机的质量,其中在机械加工的过程中对于发电机机匣的质量保障就是一个非常重要的保障措施。
我国机械加工领域不断提升的一个重要标志就是我国航空发动机机匣的机械加工质量得到了非常大的保障。
在我国机械加工领域,航空发动机机匣也是一个非常重要的难点问题,因此我国的航空领域目前已经针对这一问题进行了针对性的机械加工技术的创新和发展,本文主要针对航空发动机机匣构件的机械加工技术的发展以及创新进行详细的分析以及阐述,希望通过本文的阐述以及分析能够有效提升我国航空机匣的机械加工技术,同时也为我国机械加工领域的进一步提升以及创新贡献一份应尽的责任和力量。
关键词:航空发动机;机匣构件;机械加工技术;机械加工工艺;优化中图分类号:TH16 文献标识码:A在我国航空机械加工的过程中,机匣的机械加工的制约因素非常多,主要的制约因素有两种,首先是在机械加工过程中使用的加工材料,其次是在机械加工过程中采用的加工形位公差等。
这些机械加工影响因素能够在很大程度上影响机匣的加工几何尺寸,同时对加工后的加工公差等也会造成很大的影响,能够在很大程度上影响机匣构件的加工质量以及加工精度,如果质量不过关,会对我国航空领域造成严重的安全隐患。
除此之外,机匣构件的外观情况以及表面损伤,也会影响机匣的使用寿命,同时会机匣构架的强度也会造成严重的影响。
因此为了有效的提升我国航空发电机机匣构件的使用寿命以及使用强度,我们要在机械加工的过程中进行严格的质量控制,只有保障了机匣构架的质量,才能够给我我国航空事业的进一步发展保驾护航。
某延伸机匣机械加工工艺研究

某延伸机匣机械加工工艺研究【摘要】本文研究了某延伸机匣的机械加工工艺,通过分析其工艺特点,探讨加工工艺流程,优化加工工艺参数,制定加工质量控制方法,以及改进工艺提升加工效率和质量。
结合实际案例和数据分析,展望了某延伸机匣机械加工工艺的应用前景,并总结了研究的创新点和不足之处。
通过本研究,可以为相关行业提供参考和借鉴,推动该领域的发展和提升。
【关键词】某延伸机匣,机械加工,工艺特点,工艺流程,工艺参数,质量控制,工艺改进,应用前景,创新点,不足之处。
1. 引言1.1 研究背景某延伸机匣是一种常用于工业生产中的机械零部件,其加工工艺对于提高产品质量和生产效率具有重要意义。
由于某延伸机匣的复杂结构和精密要求,其加工工艺需要经过深入研究和优化,才能实现最佳加工效果。
对某延伸机匣机械加工工艺的研究具有重要意义。
过去,针对某延伸机匣加工工艺的研究主要集中在传统加工方法的改进和优化上,缺乏针对性的探讨和实践。
随着现代加工技术的不断发展和提升,对某延伸机匣机械加工工艺的研究也日益受到重视。
为了提高某延伸机匣的加工质量和效率,开展针对性的研究是非常必要的。
本研究将针对某延伸机匣机械加工工艺进行深入探讨,分析其工艺特点、优化参数,探讨加工质量控制方法,并提出工艺改进与提升的方向。
通过本研究,旨在为某延伸机匣的加工工艺提供可靠的理论依据和实践指导,促进相关领域的发展和进步。
1.2 研究意义某延伸机匣机械加工工艺的研究对于提高生产效率、降低生产成本、提升产品质量具有重要意义。
随着社会的发展和科技的进步,机械加工行业也在不断发展壮大。
某延伸机匣是机械行业中常见的零部件之一,其加工工艺和质量直接影响着整个产品的性能和稳定性。
通过深入研究某延伸机匣的加工工艺,可以更好地理解其工艺特点,探讨加工流程和参数的优化,并提出相应的质量控制方法。
这不仅可以提高生产效率,减少生产中的浪费,还可以提升产品质量,增强产品的市场竞争力。
研究某延伸机匣的加工工艺还可以为工艺改进和提升提供重要参考。
航空发动机机匣构件机械加工工艺优化 姜志龙

航空发动机机匣构件机械加工工艺优化姜志龙摘要:在飞机当中,发动机是最为重要的组成部分之一,也是当前国家非常重视的一项技术。
而在航空发电机部件机械加工过程之中,其机匣构件是机械加工的一个难点和重点。
航空发电机机匣构件在进行机械加工时由于其材料、尺寸、形状等因素,往往导致其加工完成之后出现超差情况,从而影响到整个航空发电机质量。
基于此,文章针对航空发电机机匣构件机械加工工艺展开了分析,并就如何进行优化进行了探究。
关键词:航空发动机;机匣构件;机械加工;优化1.引言航空发动机机匣构件作为飞机中非常重要的一部分,其机械加工质量至关重要。
航空发电机机匣构件多是高强度合金材质,例如高温合金、钛合金等等。
这类材质大都具有良好的耐高温性、高负荷性,不过这种材质在机械加工过程之中难度相对较大,如若采取的加工工艺不当,很有可能导致出现超差情况,从而严重影响到整个航空发动机的使用寿命。
因此,必须对航空发电机机匣构件加工中所采用的机械加工工艺进行科学合理的优化,提高机匣构件加工质量,促进航空发动机质量的提升。
2.影响机匣构件机械加工质量的因素在航空发动机机匣构件加工中,影响其加工质量的因素比较多,而在众多影响因素当中,最为主要的影响因素有两种,分别为:第一种因素是加工过程中所选择刀具材质等影响,第二种则是加工过程中各种参数等影响。
这些因素在很大程度上影响着航空发动机机匣构件加工几何尺寸,对机械加工之后的加工精度有着较大的影响。
若是航空发动机机匣构件加工质量达不到足够要求,那么必将严重影响到航空事业的安全性。
除此之外,由于机匣构件质量直接关系到整个航空发电机的使用寿命,为了保证机匣构件具体足够的强度,则应该避免机匣构件外表面出现机械加工损伤。
由此可见,若想在一定程度上提高航空发电机使用寿命,那么就必须对其机械加工质量加以控制,进而保证机匣构件质量达到相关要求,只有这样才能够进一步推动我国航空事业的发展与进步。
3.机匣构件受力分析在航空发电机中,应对其机匣构件的轴承支点位置加以重视,该位置属于航空发动机主要的支撑点,所受到的应力相对较为集中,并且该位置在航空发动机涡轮的后壳之下,该位置直接与轴承表面接触,是保证轴承部位的重要结构。
航空发动机机匣数控加工工艺探究
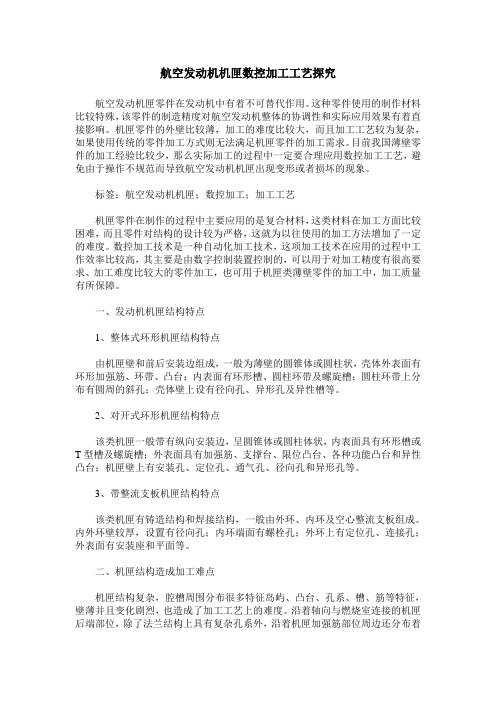
航空发动机机匣数控加工工艺探究航空发动机匣零件在发动机中有着不可替代作用。
这种零件使用的制作材料比较特殊,该零件的制造精度对航空发动机整体的协调性和实际应用效果有着直接影响。
机匣零件的外壁比较薄,加工的难度比较大,而且加工工艺较为复杂,如果使用传统的零件加工方式则无法满足机匣零件的加工需求。
目前我国薄壁零件的加工经验比较少,那么实际加工的过程中一定要合理应用数控加工工艺,避免由于操作不规范而导致航空发动机机匣出现变形或者损坏的现象。
标签:航空发动机机匣;数控加工;加工工艺机匣零件在制作的过程中主要应用的是复合材料,这类材料在加工方面比较困难,而且零件对结构的设计较为严格,这就为以往使用的加工方法增加了一定的难度。
数控加工技术是一种自动化加工技术,这项加工技术在应用的过程中工作效率比较高,其主要是由数字控制装置控制的,可以用于对加工精度有很高要求、加工难度比较大的零件加工,也可用于机匣类薄壁零件的加工中,加工质量有所保障。
一、发动机机匣结构特点1、整体式环形机匣结构特点由机匣壁和前后安装边组成,一般为薄壁的圆锥体或圆柱状,壳体外表面有环形加强筋、环带、凸台;内表面有环形槽、圆柱环带及螺旋槽;圆柱环带上分布有圆周的斜孔;壳体壁上设有径向孔、异形孔及异性槽等。
2、对开式环形机匣结构特点该类机匣一般带有纵向安装边,呈圆锥体或圆柱体状,内表面具有环形槽或T型槽及螺旋槽;外表面具有加强筋、支撑台、限位凸台、各种功能凸台和异性凸台;机匣壁上有安装孔、定位孔、通气孔、径向孔和异形孔等。
3、带整流支板机匣结构特点该类机匣有铸造结构和焊接结构,一般由外环、内环及空心整流支板组成。
内外环壁较厚,设置有径向孔;内环端面有螺栓孔;外环上有定位孔、连接孔;外表面有安装座和平面等。
二、机匣结构造成加工难点机匣结构复杂,腔槽周围分布很多特征岛屿、凸台、孔系、槽、筋等特征,壁薄并且变化剧烈,也造成了加工工艺上的难度。
沿着轴向与燃烧室连接的机匣后端部位,除了法兰结构上具有复杂孔系外,沿着机匣加强筋部位周边还分布着放气孔,该类孔一般与发动机轴线成一定角度,这些特殊结构的异型孔加工难度很大。
航空发动机机匣高效加工方法研究
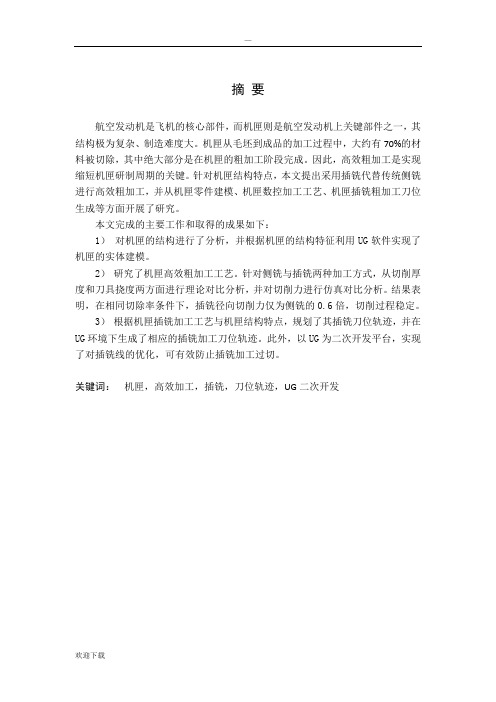
摘要航空发动机是飞机的核心部件,而机匣则是航空发动机上关键部件之一,其结构极为复杂、制造难度大。
机匣从毛坯到成品的加工过程中,大约有70%的材料被切除,其中绝大部分是在机匣的粗加工阶段完成。
因此,高效粗加工是实现缩短机匣研制周期的关键。
针对机匣结构特点,本文提出采用插铣代替传统侧铣进行高效粗加工,并从机匣零件建模、机匣数控加工工艺、机匣插铣粗加工刀位生成等方面开展了研究。
本文完成的主要工作和取得的成果如下:1)对机匣的结构进行了分析,并根据机匣的结构特征利用UG软件实现了机匣的实体建模。
2)研究了机匣高效粗加工工艺。
针对侧铣与插铣两种加工方式,从切削厚度和刀具挠度两方面进行理论对比分析,并对切削力进行仿真对比分析。
结果表明,在相同切除率条件下,插铣径向切削力仅为侧铣的0.6倍,切削过程稳定。
3)根据机匣插铣加工工艺与机匣结构特点,规划了其插铣刀位轨迹,并在UG环境下生成了相应的插铣加工刀位轨迹。
此外,以UG为二次开发平台,实现了对插铣线的优化,可有效防止插铣加工过切。
关键词:机匣,高效加工,插铣,刀位轨迹,UG二次开发ABSTRACTAero-engine is the core component of the aircraft, and the casing which is a key part of the engine is difficult to manufacture because its extremely complicate structure. About 70% of the material is removed from blank to finished product, while the most material is removed in rough milling of casing. Therefore, high efficiency roughing of the casing is a key technology to realizing higher efficiency manufacturing and shorter developing cycle. Based on characteristics of casing, plunge milling was proposed to instead of traditional layered flank milling in this paper. And the part modeling, the CNC machining process modeling, the cut-location generation of the plunge milling in rough machining were studied.The main work and achievements of this thesis are as follows:1) The casing structure is analyzed, and on this basis, the entity model of casing is established using UG.2) The efficient rough machining of casing is studied for process planning. Between the side milling and plunge milling methods, cutting thickness and tools deflection were contrasted in theory and the cutting force were contrasted in simulation. The results show that, under the same resection rate, the radial cutting force of the plunge is only 0.6 times than the side milling, and the process is stable.3) According to the Plunge milling process and the structure characteristics of casing, the plunge milling cutter path was planned, which is then generated in UG. Additionally, aiming at overcut in plunge milling process, the optimization of the plunge milling line has been implemented using UG secondary development.Key words: Casing, Efficient processing, Plunge milling, tool path, UG Secondary development目录摘要 (I)ABSTRACT........................................................ I I第一章绪论 (1)1.1研究背景 (1)1.2国内外研究现状 (2)1.2.1 复杂结构类零件粗加工技术 (2)1.2.2 插铣工艺技术 (3)1.3 论文主要内容及章节安排 (5)第二章机匣造型 (7)2.1基于特征的建模方法 (7)2.2建模平台选择 (8)2.3机匣造型 (9)2.3.1 机匣模型分析 (9)2.3.2 机匣实体建模 (10)第三章机匣数控加工工艺 (15)3.1工艺规程编制原则 (15)3.2机匣零件的工艺特征 (15)3.3机匣加工工艺阶段的划分 (16)3.4机匣加工工艺路线制定 (16)3.5机匣粗加工工艺方案分析 (18)第四章机匣插铣粗加工刀具轨迹 (25)4.1 UG数控加工 (25)4.2刀具轨迹规划原则 (25)4.3刀具轨迹生成 (27)4.3.1 加工环境设定 (27)4.3.2 刀具轨迹生成 (27)4.3.3 程序后置处理 (33)4.4基于UG的插铣线优化 (35)总结 (38)致谢 (39)参考文献 (40)第一章绪论1.1研究背景航空发动机是飞机的“心脏”,其内部温度高,转速高,压力大,使用寿命长,构件的机械负荷和热负荷大,工作条件十分苛刻和复杂,其研究和发展工作的技术难度大,耗资多,周期长,是一个世界公认的、复杂的多学科综合性系统工程[1]。
航空发动机机匣典型件工艺优化方案研究

航空发动机机匣典型件工艺优化方案研究在现代工业的心脏——航空发动机领域,机匣作为其关键组成部分,承担着保护内部精密零件、维持气流顺畅等重要职责。
然而,随着航空技术的飞速发展,传统的制造工艺已难以满足日益严苛的性能要求。
因此,对航空发动机机匣典型件的工艺进行优化,不仅是提升整体性能的关键一环,更是推动航空工业进步的必由之路。
首先,我们要认识到,机匣的加工精度直接关系到发动机的性能表现。
如同一位舞者在舞台上的每一个动作都影响着观众的观感,机匣的每一次加工都必须精确无误。
因此,采用先进的数控技术和精密测量手段,确保加工过程的高精度和高稳定性,是优化工艺的首要步骤。
其次,材料的选择和处理也至关重要。
机匣需要具备轻质、高强度、耐高温等特性,这就要求我们在选材时如同挑选珍珠般谨慎。
同时,通过热处理等工艺改善材料的微观结构,使其更加坚韧耐用,是提升机匣性能的有效途径。
再者,工艺流程的优化不可忽视。
传统的串行式生产模式效率低下,且容易产生误差累积。
而采用并行工程和模块化设计思想,不仅能缩短生产周期,还能提高产品质量。
这就像是将一条狭窄的山路改造成宽阔的高速公路,使得生产流程更加顺畅高效。
此外,我们还应该关注环保和可持续发展问题。
在优化工艺的同时,减少能源消耗和废弃物排放,是企业社会责任的体现,也是长远发展的保障。
这就如同在绿洲中种下一棵树,既美化了环境,又为未来留下了宝贵的资源。
最后,创新是永恒的主题。
在优化工艺的过程中,我们应该鼓励工程师们发挥创造力,探索新的加工方法和设计理念。
正如在茫茫沙漠中寻找水源一样,只有不断探索和尝试,才能发现更多的可能性。
综上所述,航空发动机机匣典型件的工艺优化是一个系统工程,需要我们从多个角度出发,综合考虑各种因素。
通过提高加工精度、选择合适的材料、优化工艺流程、关注环保和鼓励创新等措施,我们一定能打造出性能更优、质量更高的机匣产品,为航空工业的发展注入新的活力。
航空机匣数控程序路径优化方法
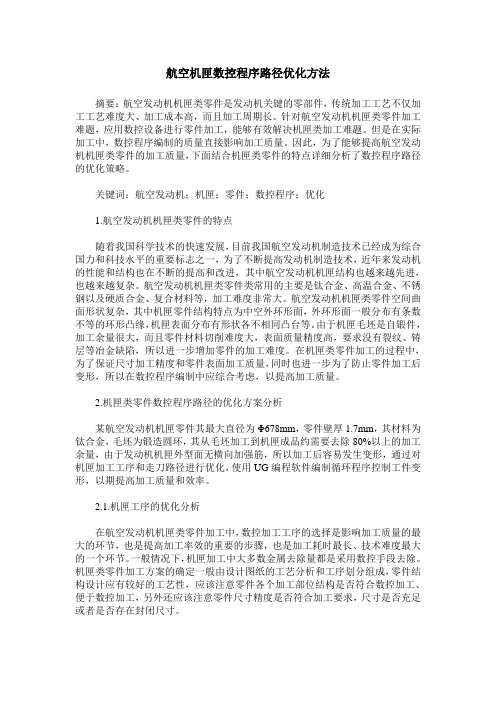
航空机匣数控程序路径优化方法摘要:航空发动机机匣类零件是发动机关键的零部件,传统加工工艺不仅加工工艺难度大、加工成本高,而且加工周期长。
针对航空发动机机匣类零件加工难题,应用数控设备进行零件加工,能够有效解决机匣类加工难题。
但是在实际加工中,数控程序编制的质量直接影响加工质量。
因此,为了能够提高航空发动机机匣类零件的加工质量,下面结合机匣类零件的特点详细分析了数控程序路径的优化策略。
关键词:航空发动机;机匣;零件;数控程序;优化1.航空发动机机匣类零件的特点随着我国科学技术的快速发展,目前我国航空发动机制造技术已经成为综合国力和科技水平的重要标志之一,为了不断提高发动机制造技术,近年来发动机的性能和结构也在不断的提高和改进,其中航空发动机机匣结构也越来越先进,也越来越复杂。
航空发动机机匣类零件类常用的主要是钛合金、高温合金、不锈钢以及硬质合金、复合材料等,加工难度非常大。
航空发动机机匣类零件空间曲面形状复杂,其中机匣零件结构特点为中空外环形面,外环形面一般分布有条数不等的环形凸缘,机匣表面分布有形状各不相同凸台等。
由于机匣毛坯是自锻件,加工余量很大,而且零件材料切削难度大,表面质量精度高,要求没有裂纹、铸层等冶金缺陷,所以进一步增加零件的加工难度。
在机匣类零件加工的过程中,为了保证尺寸加工精度和零件表面加工质量,同时也进一步为了防止零件加工后变形,所以在数控程序编制中应综合考虑,以提高加工质量。
2.机匣类零件数控程序路径的优化方案分析某航空发动机机匣零件其最大直径为Φ678mm,零件壁厚1.7mm,其材料为钛合金,毛坯为锻造圆环,其从毛坯加工到机匣成品约需要去除80%以上的加工余量,由于发动机机匣外型面无横向加强筋,所以加工后容易发生变形,通过对机匣加工工序和走刀路径进行优化,使用UG编程软件编制循环程序控制工件变形,以期提高加工质量和效率。
2.1.机匣工序的优化分析在航空发动机机匣类零件加工中,数控加工工序的选择是影响加工质量的最大的环节,也是提高加工率效的重要的步骤,也是加工耗时最长、技术难度最大的一个环节。
浅谈机匣凸台加工技术改进

浅谈机匣凸台加工技术改进涡轮机匣的凸台在五轴加工中心的加工一直是整个涡轮机匣机械加工的最难点,由于涡轮机匣机匣壁薄,凸台材料硬,切削余量多,所以加工极易引起零件变形,再而造成零件加工不合格,本文论述的就是如何改进加工方法和调整加工参数,从而减少零件的变形,确保零件的工艺技术要求。
标签:涡轮机匣;高温合金;薄壁件;加工路线;加工变形0 前言涡轮机匣是航空发动机上的重要部件之一,它的特点是机匣壁薄,最少厚度厚仅0.8mm,零件位置度、平面度、平行度等型位公差要求高,但是它的凸台是高温镍基合金,材料硬度高,韧性好,壁厚薄,零件易变形,位置度倾斜度等达不到工艺要求。
如何优质高效的加工凸台是涡轮机匣顺利交付与否的源头所在点,在实际的加工中,通过对所加工零件的夹具改进,刀具选择和加工路线的优化等各方面的改进改善,终于使这个加工的技术难点获得突破性的进展。
下文就这一论点做详细的论述。
1 夹具的改善夹具改善前,夹具支靠零件的面的平面度有0.2 mm~0.3 mm,定位圆与零件需支靠的面也未清根,这就造成零件放到夹具里面之后,零件翘起,压紧零件之后可能造成零件产生塑性变形,从而影响零件的加工精度,为了避免此种问题的发生,我们做了如下改进:(1)将夹具定位圆与支靠面底部清根。
(2)磨制夹具支靠零件面,平面度控制在0.005 mm以内,从而保证零件加工时所需的“A”基准(图1)。
2 刀具及加工参数的优化涡轮机匣凸台的面加工在最开始加工时用的是国产饟合金杆铣刀,切削量大,刀具磨损也很严重,刀具经常磞刀,断刃,加工精度自然也很难保证。
经过多次尝试和改进后,我们选择装刀片式的盘铣刀,粗加工选择φ32的SECO盘铣刀盘,刀片选择型号为XCKX 13T316R-ME10(经试验此刀片做粗加工用性价比较好);精加工我们选择φ80的肯纳合金盘铣刀,刀片型号为W1D1A XPHT160408。
同时,对刀片的寿命做了详细的规定,粗加工每加工两个零件换一次刀刃,精加工每个零件换一次刀刃,这样保证了即解决了我们刀具的问题,同时也保证了凸台间的加工精度。
关于航空发动机机匣构件机械加工工艺优化研究

关于航空发动机机匣构件机械加工工艺优化研究发布时间:2022-09-13T09:58:56.777Z 来源:《中国科技信息》2022年第5月9期作者:刘楚煜[导读] 在我国科技不断发展的过程中刘楚煜中国航发长江动力有限公司(湖南岳阳 414000)摘要:在我国科技不断发展的过程中,促进了多个行业的进一步发展,也为航空领域提供了技术支持。
航空发动机的质量对航空领域有着至关重要的影响,而发动机机匣直接关系着航空发动机的质量,因此,必须要采取有效措施,不断优化改进航空发动机机匣的机械加工技术,保障航空领域的安全稳定发展。
因此,本文主要针对航空发动机机匣构件机械加工工艺的优化措施进行探讨分析,旨在提升其加工质量。
关键词:航空发动机;机匣构件;机械加工;工艺优化引言:在制造飞机发动机的过程中,机匣构件是其中非常关键的一个构件,不仅需要承载较大的负荷,还需要承受较高的温度,所以其主要材料为高强度的合金。
在当前的机械加工过程中,经常会出现零件受损或表面不平整等质量问题,严重影响了航空发动机机匣的使用年限。
因此,应严格控制机械加工质量,优化加工工艺,进而保障机匣构件质量,确保航空事业的稳定发展。
一、机匣构件机械加工的重要意义机匣构件机械加工时航空发动机制作中的重要内容,主要由于其需要承担较大的负载和高温的影响。
因此,在实际进行加工的过程中,需要选择具有较高强度的金属材料,并且能够具有抗高温。
现阶段,我国的机匣构件加工质量得到了优化完善,但还存在一些质量问题,如表面受损问题,会导致机匣使用寿命减少。
因此,需要进一步优化机匣机械加工工艺,保障其构件的整体性,提升其机械性能和抗疲劳性能。
同时,需要制定相应的分析流程,如图1所示。
对机匣进行工艺分析是进一步优化其工艺的前提。
即对其构件的加工的工艺性进行分析。
因为航空发动机的结构具有较强的复杂性,所以在机匣制造的过程中,很容易出现结构性问题,增强了其工艺问题的复杂性。
在制作机匣构件的过程中,要想保障其质量合格,需要采用机械加工的方式对其表面质量和形状等进行调整,是技巧和方法的结合[1]。
某延伸机匣机械加工工艺研究
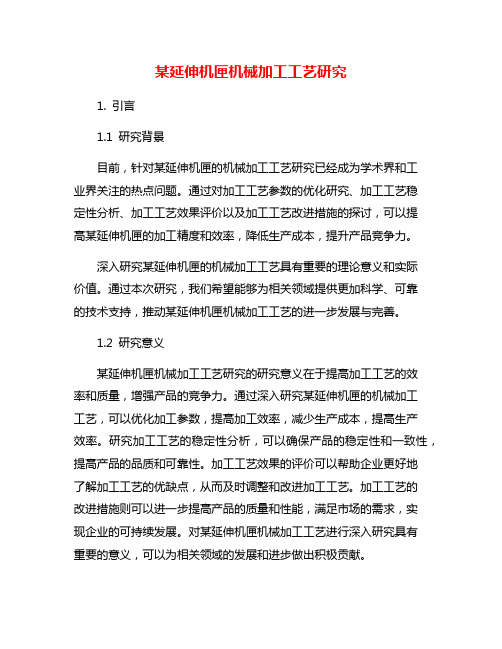
某延伸机匣机械加工工艺研究1. 引言1.1 研究背景目前,针对某延伸机匣的机械加工工艺研究已经成为学术界和工业界关注的热点问题。
通过对加工工艺参数的优化研究、加工工艺稳定性分析、加工工艺效果评价以及加工工艺改进措施的探讨,可以提高某延伸机匣的加工精度和效率,降低生产成本,提升产品竞争力。
深入研究某延伸机匣的机械加工工艺具有重要的理论意义和实际价值。
通过本次研究,我们希望能够为相关领域提供更加科学、可靠的技术支持,推动某延伸机匣机械加工工艺的进一步发展与完善。
1.2 研究意义某延伸机匣机械加工工艺研究的研究意义在于提高加工工艺的效率和质量,增强产品的竞争力。
通过深入研究某延伸机匣的机械加工工艺,可以优化加工参数,提高加工效率,减少生产成本,提高生产效率。
研究加工工艺的稳定性分析,可以确保产品的稳定性和一致性,提高产品的品质和可靠性。
加工工艺效果的评价可以帮助企业更好地了解加工工艺的优缺点,从而及时调整和改进加工工艺。
加工工艺的改进措施则可以进一步提高产品的质量和性能,满足市场的需求,实现企业的可持续发展。
对某延伸机匣机械加工工艺进行深入研究具有重要的意义,可以为相关领域的发展和进步做出积极贡献。
1.3 研究目的本文旨在探究某延伸机匣机械加工工艺的特点和优化方向,从而提高加工效率和产品质量。
具体目的包括以下几个方面:1. 分析某延伸机匣机械加工工艺的优缺点,找出存在的问题和改进空间;2. 研究加工工艺参数的优化方法,以实现加工过程的高效稳定;3. 分析加工工艺的稳定性,探讨可能影响加工效果的因素;4. 对某延伸机匣机械加工工艺进行效果评价,验证改进措施的有效性;5. 提出针对加工工艺改进的具体措施和建议,为相关领域的实践提供参考和借鉴。
通过对上述目的进行研究和探讨,旨在为某延伸机匣机械加工工艺的优化提供理论支持和实践指导,推动相关领域的发展和提升。
2. 正文2.1 某延伸机匣机械加工工艺概述某延伸机匣(Extension Box)是一种常用于机械设备中的零部件,其加工工艺对产品质量和性能具有重要影响。
机械加工工艺优化方法及其应用
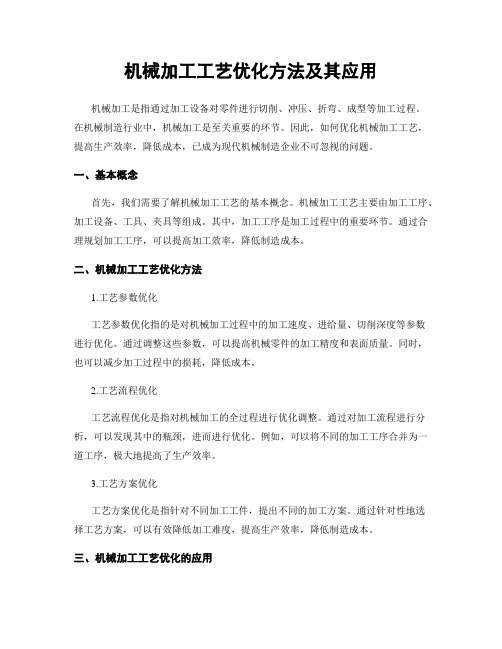
机械加工工艺优化方法及其应用机械加工是指通过加工设备对零件进行切削、冲压、折弯、成型等加工过程。
在机械制造行业中,机械加工是至关重要的环节。
因此,如何优化机械加工工艺,提高生产效率,降低成本,已成为现代机械制造企业不可忽视的问题。
一、基本概念首先,我们需要了解机械加工工艺的基本概念。
机械加工工艺主要由加工工序、加工设备、工具、夹具等组成。
其中,加工工序是加工过程中的重要环节。
通过合理规划加工工序,可以提高加工效率,降低制造成本。
二、机械加工工艺优化方法1.工艺参数优化工艺参数优化指的是对机械加工过程中的加工速度、进给量、切削深度等参数进行优化。
通过调整这些参数,可以提高机械零件的加工精度和表面质量。
同时,也可以减少加工过程中的损耗,降低成本。
2.工艺流程优化工艺流程优化是指对机械加工的全过程进行优化调整。
通过对加工流程进行分析,可以发现其中的瓶颈,进而进行优化。
例如,可以将不同的加工工序合并为一道工序,极大地提高了生产效率。
3.工艺方案优化工艺方案优化是指针对不同加工工件,提出不同的加工方案。
通过针对性地选择工艺方案,可以有效降低加工难度,提高生产效率,降低制造成本。
三、机械加工工艺优化的应用机械加工工艺优化方法在实际生产中具有广泛的应用。
例如,某机械制造企业通过对机械加工工艺进行优化,成功实现了生产效率的提高,降低了生产成本。
另外,一些新型材料的加工也需要采用机械加工工艺优化方法。
例如,在高速钢加工中,通过对加工参数进行调整,可以有效降低工件表面的残余应力,从而提高加工精度和表面质量。
结论总之,机械加工工艺的优化是实现机械制造企业高效、低成本的重要手段。
在实际应用中,需要根据不同的加工工件和材料选择合适的优化方法。
加强机械加工工艺的研究和应用,将有助于提高机械制造的技术含量,推进机械制造行业的发展。
中介机匣加工工艺优化

中介机匣加工工艺优化摘要:本文根据中介机匣的结构特点和工艺难点,结合对实际生产过程产生的问题进行分析,通过对加工工艺进行优化,有效解决加工过程的难题,提高了产品的生产效率和合格率。
主题词:中介机匣变形工艺优化1引言某型中介机匣(以下简称中介机匣)是贵州航天风华精密设备有限公司承担的某所外协配套产品,是某型号产品涡轮风扇发动机的重要部件。
中介机匣属于典型的薄壁焊接、精密加工结构类零件,焊接变形控制困难,而且组件结构复杂,对装配、焊接和机械加工顺序要求较高。
大部分零件为典型的薄壁结构件,结构刚性差,装夹困难。
在组件状态的加工要素多,尺寸精度要求高,多处加工要素间有较高的形位公差要求,零件尺寸和位置精度较难保证。
在前期研制试生产过程中,由于焊接和机械加工的变形控制不稳定,致使生产过程中质量问题屡屡发生,严重影响了产品的质量和生产进度。
为全面提升中介机匣加工工艺技术保障能力,控制好焊接和机械加工过程的变形量,深入开展中介机匣的工艺优化工作,在确保产品质量的前提下,使生产效率上到了一个新的台阶。
2实施方案2.1 焊接变形控制的工艺优化2.1.1在研制试生产过程中,发现支座与腹板焊接和支座组件与外环焊接时易产生质量问题。
经研究分析,主要原因是由于支座为铸件毛坯,外形尺寸不规范,焊接装配时尺寸难以兼顾,致使后续加工中出现腹板尺寸超差和支座组件与外环焊接错位的现象。
针对该问题,经过认真分析,决定进一步优化工艺,对支座铸件毛坯进行补充加工,在支座毛坯上光出一基准面,同时光出腹板的焊接装配平面。
经后续研制生产的验证,达到了预期效果。
2.1.2 小批量生产过程中,零件存在焊接后变形过大,焊后加工找正难度大,找正耗费时间长的弊端。
通过逐项分析原因,发现在前期生产过程中,零件焊前已经存在变形较大的情况,部分零件自由状态下变形量可达0.3mm~0.4mm,零部件的变形过大直接加剧了后续焊接工序中变形量,导致了产品的加工质量下降及加工周期延长。
航空发动机机匣构件机械加工工艺优化
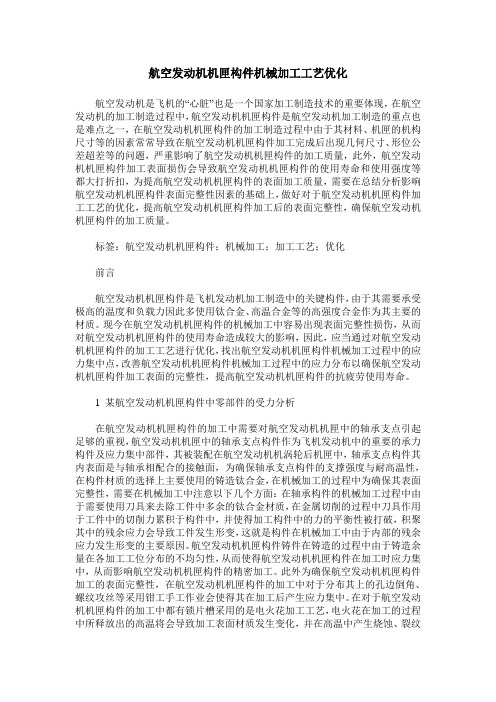
航空发动机机匣构件机械加工工艺优化航空发动机是飞机的“心脏”也是一个国家加工制造技术的重要体现,在航空发动机的加工制造过程中,航空发动机机匣构件是航空发动机加工制造的重点也是难点之一,在航空发动机机匣构件的加工制造过程中由于其材料、机匣的机构尺寸等的因素常常导致在航空发动机机匣构件加工完成后出现几何尺寸、形位公差超差等的问题,严重影响了航空发动机机匣构件的加工质量,此外,航空发动机机匣构件加工表面损伤会导致航空发动机机匣构件的使用寿命和使用强度等都大打折扣,为提高航空发动机机匣构件的表面加工质量,需要在总结分析影响航空发动机机匣构件表面完整性因素的基础上,做好对于航空发动机机匣构件加工工艺的优化,提高航空发动机机匣构件加工后的表面完整性,确保航空发动机机匣构件的加工质量。
标签:航空发动机机匣构件;机械加工;加工工艺;优化前言航空发动机机匣构件是飞机发动机加工制造中的关键构件,由于其需要承受极高的温度和负载力因此多使用钛合金、高温合金等的高强度合金作为其主要的材质。
现今在航空发动机机匣构件的机械加工中容易出现表面完整性损伤,从而对航空发动机机匣构件的使用寿命造成较大的影响,因此,应当通过对航空发动机机匣构件的加工工艺进行优化,找出航空发动机机匣构件机械加工过程中的应力集中点,改善航空发动机机匣构件机械加工过程中的应力分布以确保航空发动机机匣构件加工表面的完整性,提高航空发动机机匣构件的抗疲劳使用寿命。
1 某航空发动机机匣构件中零部件的受力分析在航空发动机机匣构件的加工中需要对航空发动机机匣中的轴承支点引起足够的重视,航空发动机机匣中的轴承支点构件作为飞机发动机中的重要的承力构件及应力集中部件,其被装配在航空发动机机涡轮后机匣中,轴承支点构件其内表面是与轴承相配合的接触面,为确保轴承支点构件的支撑强度与耐高温性,在构件材质的选择上主要使用的铸造钛合金,在机械加工的过程中为确保其表面完整性,需要在机械加工中注意以下几个方面:在轴承构件的机械加工过程中由于需要使用刀具来去除工件中多余的钛合金材质,在金属切削的过程中刀具作用于工件中的切削力累积于构件中,并使得加工构件中的力的平衡性被打破,积聚其中的残余应力会导致工件发生形变,这就是构件在机械加工中由于内部的残余应力发生形变的主要原因。
某延伸机匣机械加工工艺研究

DOI:10.19392/j.cnki.1671 7341.202007153某延伸机匣机械加工工艺研究林东玲辽宁装备制造职业技术学院 辽宁沈阳 110164摘 要:文章阐述了机匣类零件的结构特点,对机匣加工工艺进行了分析,并对某延伸机匣进行了生产工艺的制定。
在制定生产工艺的过程中,发现了工艺路线较长、零件易变形、零件圆度和平面度差的问题。
针对这些问题,提出了缩短工艺路线,改变走刀路线,控制轴向变形等办法,以提高零件的加工效率和加工质量。
关键词:工艺优化;变形控制;薄壁机匣 近年来,随着机匣设计生产技术的发展,机匣零件的材料及结构发生了很大的变化,越来越多的材料被用于机匣零件的生产,与此同时,机匣的功能也变得更加的丰富。
但是在机匣的生产过程中,各种各样的问题也是层出不穷,为了解决这些问题,就需要对机匣机械的加工工艺进行研究和优化,以提高零件的质量,从而满足相关领域的生产需要。
一、机匣类零件结构特点分析当前阶段,机匣类部件成为了航空发动机部件的主要组成部分,在航空发动机领域得到了广泛应用。
机匣类部件种类较多,因此,不同的机匣部件功能各异,不同位置的机匣部件在航空发动机的运转过程中发挥着不同的作用。
根据机匣部件的结构,可以将其分为环形、箱型两类,而环形机匣又可以分为带整流只板环形机匣、对开环环形机匣、整体环形机匣三种。
大多数发动机的环形机匣都属于薄壁类机匣,结构复杂。
因此,在加工机匣部件时需要通过多个环节的加工才能完成,加工环节主要分为粗、半精、精加工。
第一个环节的任务是去除部件的余量,该环节对部件加工的精细度要求较低。
而半精加工环节主要是为后续的加工提供便利,通过半精加工消除形变、去除余量,使部件更加均匀。
精加工作为最后一个环节,加工余量小,但是对加工的精细度要求较高,这一环节的目标是使零部件符合设计要求。
二、机匣加工工艺(一)加工工艺特点航空发动机的机匣结构比较复杂,壁厚变化大,需要极高的加工工艺才能使部件符合设计要求。
精密机械加工中的加工工艺优化和模拟

精密机械加工中的加工工艺优化和模拟一、引言精密机械加工是工业生产中的重要环节之一。
在这些加工过程中,通过优化加工工艺和模拟技术,我们可以提高加工效率,降低成本,同时保持高质量的加工结果。
本文将重点讨论如何在精密机械加工中进行加工工艺的优化和模拟。
二、加工工艺的优化1. 设计优化在进行加工之前,我们需要进行设计优化。
这里的设计优化包括机械结构设计、模块化设计和选材等。
机械结构设计应该考虑到机器的稳定性和刚性;模块化设计则可以提高生产效率,降低成本;选材应该考虑到机器所需的材料的强度、耐腐蚀性等。
2. 选择合适的加工方式和工具根据不同的工件,我们需要选择不同的加工方式和工具。
一般来说,对于较粗的表面加工,应使用粗大的刀具和高效率的加工方式,以提高加工速度;对于需要高精度加工的表面,应选择更小的刀具和加工方式,以提高加工质量。
3. 加工过程控制在加工过程中,我们需要控制加工速度、进给量、切削深度等参数,以保证加工的质量。
同时,在加工过程中我们也需要仔细观察机器的运转状况,及时发现问题。
4. 加工润滑和清洗在加工过程中,我们需要给机器润滑和清洗。
润滑可以减少机器的摩擦,从而提高加工速度和效率;清洗可以保持机器的良好状态,避免机器出现故障。
三、加工模拟技术1. 数值模拟现代数值模拟技术可以通过建立数值模型,对机器的运行状态进行预测和分析。
数值模拟可以帮助我们更好地理解机器的加工过程,预测机器的加工效果,优化加工工艺,并提高精密机械加工的效率和质量。
2. 运动模拟运动模拟技术可以帮助我们模拟机器在运行时的状态。
这种技术可以帮助我们更好地理解机器的运行状况,发现机器运行中的问题,并加以解决。
运动模拟也可以用来优化加工工艺,提高加工效率和质量。
3. 光学模拟光学模拟技术可以帮助我们模拟机器加工中的光学效应。
通过光学模拟,我们可以更好地理解机器在光学加工方面的性能,并通过优化加工工艺,提高加工效率和质量。
四、结论通过优化加工工艺和模拟技术,我们可以提高精密机械加工的效率和质量。
某延伸机匣机械加工工艺研究

某延伸机匣机械加工工艺研究一、引言随着工业技术的进步和数字化制造技术的不断成熟,机械加工工艺也在快速发展和完善。
延伸机匣作为机械产品的重要组成部分,对加工工艺的要求也越来越高。
本文将对某延伸机匣的机械加工工艺进行研究,探讨其加工过程中可能出现的问题及解决方法。
二、某延伸机匣机械加工工艺研究1. 延伸机匣的加工工艺概述延伸机匣是一种重要的机械零部件,广泛应用于各种机械设备中。
其主要功能是在机械运转过程中传递动力和减速。
由于其结构复杂,加工工艺要求严格。
常见的加工工艺包括车削、铣削、钻削、磨削等。
由于其要求精度高,还需要进行热处理、表面处理等工艺。
2. 加工过程中可能出现的问题(1)尺寸精度不足在加工延伸机匣的过程中,由于受到工艺、设备、刀具等因素的影响,很容易导致加工零件的尺寸精度不足。
这将影响整个机械产品的质量和性能。
(2)表面粗糙度不符合要求延伸机匣作为机械零部件的重要组成部分,其表面粗糙度对整个机械产品的性能有着重要影响。
如果加工过程中出现表面粗糙度不符合要求,将会直接影响机械产品的使用寿命和性能。
(3)易变形由于延伸机匣的结构复杂,加工时如果受力不均匀,很容易导致变形,影响其使用效果。
3. 加工工艺改进方法(1)优化工艺参数通过对加工工艺参数的优化,可以有效提高加工质量和效率。
比如合理选择刀具材料、切削速度和进给量,以及加工过程中的冷却润滑等措施,可以减小尺寸精度和表面粗糙度方面的问题。
(2)加强设备维护定期对加工设备进行检查、维护和保养,确保设备正常运转,对延伸机匣进行高效、高质量的加工。
(3)精良刀具的选择选择质量好的刀具进行加工,可以有效减小切削力、提高切削效率,并减小变形的风险。
(4)制定严格的工艺控制和质量检验标准严格执行加工工艺控制和质量检验标准,确保每一道工序都符合要求,及时发现和解决问题。
4. 机械加工工艺未来发展趋势随着数字化制造技术的不断发展和成熟,机械加工工艺也将朝着智能化、精密化、高效化的方向发展。
中机匣产能提升方案分析与实施

中机匣产能提升方案分析与实施基于中机匣的产能提升需求,从产品结构和加工内容等角度进行分析,借助工序内容分解、工位平衡分析等方法进行加工内容转移,针对避让槽的加工难点制定新的工艺方案,并通过自主设计夹具实现独立加工,最终提高了中机匣的产能。
1序言T29R中机匣为我公司机匣工段加工的新产品,原加工节拍为189s/件,日产能为428件,由于需求量不断提高,急需提高其产能,而中机匣所有产品特性中,避让槽为加工最难点,且加工节拍最长,因此工艺优化是产能提升的关键。
2中机匣加工工艺流程及节拍T29R中机匣的加工工艺流程:毛坯→OP10打号→OP20数控加工→OP30数控加工→OP40数控加工→OP50数控加工→OP60数控加工→OP70洗涤→OP80检验→成品。
其中OP20~OP60为数控加工工序,节拍较长,为限制产能提高的主要原因。
对中机匣OP20~OP60的加工内容与加工时间进行分解,分解后各工序加工步骤及节拍见表1。
表1中机匣各工序加工步骤及节拍(单位:s)利用工位平衡分析工具对表1内容进行分析对比,得出如下结论。
1)节拍最慢的瓶颈工序为OP20、OP60,其次为OP30。
2)各工序加工步骤中,节拍最长的步骤为OP20中的步骤7:铣避让槽;OP40节拍最短,为加工内容转移重点。
3工艺优化方案从产品加工的角度和加工精度等方面,对OP20、OP60和OP30加工内容转移的可行性进行分析,结果如下。
3.1 OP20工序从加工角度分析:对OP20的加工内容和加工节拍进行分解,其加工内容均为大面系角度加工,整个生产线中只有OP60工序可加工大面系角度的部分内容,故OP20步骤2、4的7个M8螺纹孔中,2处M8螺纹孔可在OP60加工,但另2处M8螺纹孔加工内容只能调整到OP60后,其加工节怕更慢。
所以此方案不可行。
3.2 OP60工序对OP60的加工内容和加工节拍进行分析,OP60加工内容为大面系、小面系及侧面系3种角度加工。
机匣机加工艺

机匣机加工艺术是一种制造机械零件的方法,它是通过将金属材料切削、钻孔、铣削等方式来加工出所需形状和尺寸的零件。
机匣机是机械加工中的一种重要设备,主要用于加工大型或复杂的工件。
机匣机加工技术的发展历史可以追溯到19世纪初期。
当时,人们开始使用手动操作的旋床和铣床来制造各种零件。
随着科学技术的不断发展,自动化生产设备得到了广泛应用,并逐渐取代了手动操作。
在现代机匣机加工中,数控技术已经成为主流。
数控机匣机具有高精度、高效率、高可靠性等优点,在航空航天、汽车制造、电子设备等领域得到了广泛应用。
数控机匣机加工过程包括以下几个步骤:1.设计:首先需要进行产品设计,确定所需零件的形状和尺寸。
2.编程:根据设计图纸进行编程,将所需零件的形状和尺寸转化为数控程序。
3.夹紧:将待加工的材料夹在机匣机的工作台上,以便进行加工。
4.加工:通过控制数控机匣机的刀具移动,切削、钻孔、铣削等方式来加工出所需形状和尺寸的零件。
5.检测:将加工出来的零件进行检测,确保其符合设计要求。
在机匣机加工中,刀具是非常重要的一环。
不同类型的刀具适用于不同的材料和加工方式。
常见的刀具有铣刀、钻头、车刀等。
另外,在机匣机加工中还需要注意以下几点:1.保持设备清洁:定期清理机匣机内部和外部的杂物和灰尘,以确保设备正常运转。
2.调整参数:根据不同材料和加工方式调整数控程序中的参数,以达到最佳效果。
3.安全操作:在操作过程中要注意安全,戴好防护眼镜和手套,避免意外伤害。
总之,机匣机加工技术是一种先进而高效率的制造方法,在现代制造业中得到了广泛应用。
随着科学技术不断发展,在未来也将继续发挥重要作用。
- 1、下载文档前请自行甄别文档内容的完整性,平台不提供额外的编辑、内容补充、找答案等附加服务。
- 2、"仅部分预览"的文档,不可在线预览部分如存在完整性等问题,可反馈申请退款(可完整预览的文档不适用该条件!)。
- 3、如文档侵犯您的权益,请联系客服反馈,我们会尽快为您处理(人工客服工作时间:9:00-18:30)。
中介机匣加工工艺优化
发表时间:2019-04-12T08:16:55.483Z 来源:《防护工程》2018年第36期作者:程志凯[导读] 通过对加工工艺进行优化,有效解决加工过程的难题,提高了产品的生产效率和合格率。
贵州航天风华精密设备有限公司
摘要:本文根据中介机匣的结构特点和工艺难点,结合对实际生产过程产生的问题进行分析,通过对加工工艺进行优化,有效解决加工过程的难题,提高了产品的生产效率和合格率。
主题词:中介机匣变形工艺优化
1引言
某型中介机匣(以下简称中介机匣)是贵州航天风华精密设备有限公司承担的某所外协配套产品,是某型号产品涡轮风扇发动机的重要部件。
中介机匣属于典型的薄壁焊接、精密加工结构类零件,焊接变形控制困难,而且组件结构复杂,对装配、焊接和机械加工顺序要求较高。
大部分零件为典型的薄壁结构件,结构刚性差,装夹困难。
在组件状态的加工要素多,尺寸精度要求高,多处加工要素间有较高的形位公差要求,零件尺寸和位置精度较难保证。
在前期研制试生产过程中,由于焊接和机械加工的变形控制不稳定,致使生产过程中质量问题屡屡发生,严重影响了产品的质量和生产进度。
为全面提升中介机匣加工工艺技术保障能力,控制好焊接和机械加工过程的变形量,深入开展中介机匣的工艺优化工作,在确保产品质量的前提下,使生产效率上到了一个新的台阶。
2实施方案
2.1 焊接变形控制的工艺优化
2.1.1在研制试生产过程中,发现支座与腹板焊接和支座组件与外环焊接时易产生质量问题。
经研究分析,主要原因是由于支座为铸件毛坯,外形尺寸不规范,焊接装配时尺寸难以兼顾,致使后续加工中出现腹板尺寸超差和支座组件与外环焊接错位的现象。
针对该问题,经过认真分析,决定进一步优化工艺,对支座铸件毛坯进行补充加工,在支座毛坯上光出一基准面,同时光出腹板的焊接装配平面。
经后续研制生产的验证,达到了预期效果。
2.1.2 小批量生产过程中,零件存在焊接后变形过大,焊后加工找正难度大,找正耗费时间长的弊端。
通过逐项分析原因,发现在前期生产过程中,零件焊前已经存在变形较大的情况,部分零件自由状态下变形量可达0.3mm~0.4mm,零部件的变形过大直接加剧了后续焊接工序中变形量,导致了产品的加工质量下降及加工周期延长。
为降低零件在自由状态下的变形量,为后续焊接变形的控制奠定好的基础,对结构刚性差的分流前环、分流后环进行工艺方案优化,通过增加人工去应力的方式,有效的控制零件的变形。
在增加去应力措施的同时,优化零件加工装夹方式,由于零件为薄壁零件,若采用传统车削加工装夹方式,采用三爪或四爪进行夹或撑的方式会产生装夹变形。
经优化装夹方式后,零件的装夹方式改为留取工艺法兰边,采用基础板、压板压紧方式装夹,在每次加工前,均对装夹面进行修平加工,保证装夹面平面控制在0.05mm以内,使夹紧力尽量作用于工艺法兰上,有效的控制了零件的变形。
2.1.3 在核心组件“三件套”的焊接过程中,发现有错位的现象。
经分析,主要原因是由于空心支板与外环、分流前环和内机匣上的支板安装孔间隙过大,装配焊接时易发生位移。
由于空心支板为钣金冲压件,零件外形受冲压模具的影响,难以保持一致性,尺寸偏差有较大的波动,往往装配过程中要对空心支板安装孔进行修配。
为控制空心支板的装配间隙,经与设计师沟通协调,将空心支板更改为用棒材整体线切割成型,将装配间隙尺寸由原先0.1mm~0.2mm提升到在0.1mm以内,避免了“三件套”焊接过程中错位现象的发生。
2.2内衬套与分流后环同轴度要求的优化
中介机匣加工中另一个难点为内衬套中φ68H7孔与分流后环φ260H6孔同轴度0.05mm的要求。
因零件结构的特点,两处孔不能实现一次装夹加工保证,需进行二次装夹,而二次装夹保证同轴度0.05mm的要求难度较大。
在前期加工中,采用的是先加工φ260H6孔,再根据φ260H6孔配车堵头定位的方式进行装夹,这种装夹方式从理论可以保证同轴度要求,但在实际生产过程中,因堵头磨损、配车堵头精度等因素的限制,保证同轴度0.05mm要求是很困难的。
在前期生产的20台产品中,就有多台产品因堵头磨损过大而造成同轴度尺寸超差的情况出现,其余未出现超差的产品,实际同轴度尺寸也介于0.03mm~0.05mm之间,产品存在较大的超差风险。
为彻底解决同轴度尺寸精度难以保证的问题,通过认真分析,决定调整工艺方案,在车削加工中以长吊耳及腹板表面为定位装夹基准(见图1),调整加工顺序,先加工φ68H7孔,再打表φ68H7孔表跳动不大于0.01mm,再加工φ260H6孔,经过批生产的前5件产品验证,同轴度尺寸均控制在0.03mm以内,加工精度稳定,说明该工艺方法有效可行。
图2 外环补充加工示意图
3工艺优化成果分析
通过开展中介机匣工艺优化工作,提高了产品整体的工艺性能,提升了产品的质量和生产效率,降低了产品的生产成本。
具体如下:a)通过对分流前环、分流后环的工艺优化,降低了零件变形情况,变形量由原来的0.3mm左右控制在0.05mm以内,为后续焊接变形的控制提供了好的基础;
b)通过对支座零件的工艺改进,降低了焊接对接面的间隙,将原焊接变形1.5mm控制为0.5mm左右,同时减少后续数铣加工工作量,降低了加工成本;
c)通过对空心支板的工艺优化,控制了空心支板与异形孔的间隙,有效的控制了三层结构的变形,降低了修配支板及后续加工找正的时间,提高了加工效率;
d)通过对长吊耳、腹板的工艺优化,在保证质量的情况下,大幅度提升了加工效率,加工时间由原来的24h下降为16h; e)通过优化工艺方法,提高了φ68H7孔与φ260H6的同轴度尺寸,进而避免因返修所造成了花费。
4结论
综上所述,经深入开展中介机匣加工工艺优化工作,通过改进工装、夹具和加工装夹方式,优化加工工艺参数、加工工艺流程和加工方法,提升了产品质量的稳定性和可靠度,提高了产品的生产效率,降低了产品制造成本。
参考文献:
[1] 机械设计师手册.王少怀.1989.机械工业出版社
[2] 工程机械构造.曹寅昌.1981.机械工业出版社。