加速渗氮的方法
表面工程习题
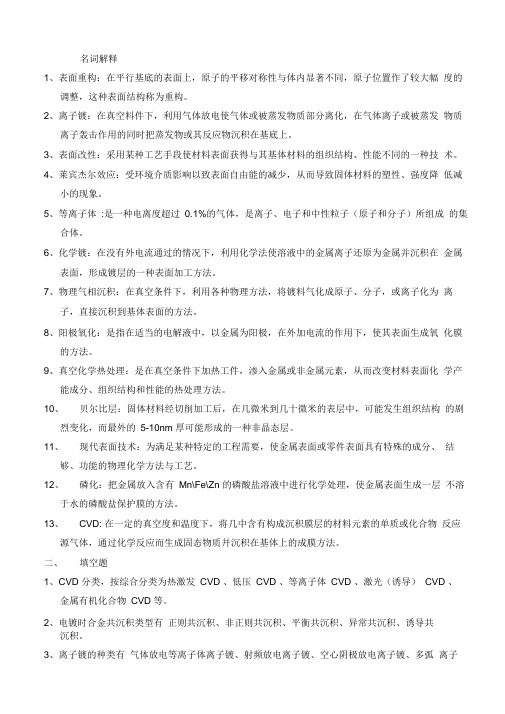
名词解释1、表面重构:在平行基底的表面上,原子的平移对称性与体内显著不同,原子位置作了较大幅度的调整,这种表面结构称为重构。
2、离子镀:在真空料件下,利用气体放电使气体或被蒸发物质部分离化,在气体离子或被蒸发物质离子轰击作用的同时把蒸发物或其反应物沉积在基底上。
3、表面改性:采用某种工艺手段使材料表面获得与其基体材料的组织结构、性能不同的一种技术。
4、莱宾杰尔效应:受环境介质影响以致表面自由能的减少,从而导致固体材料的塑性、强度降低减小的现象。
5、等离子体:是一种电离度超过0.1%的气体,是离子、电子和中性粒子(原子和分子)所组成的集合体。
6、化学镀:在没有外电流通过的情况下,利用化学法使溶液中的金属离子还原为金属并沉积在金属表面,形成镀层的一种表面加工方法。
7、物理气相沉积:在真空条件下,利用各种物理方法,将镀料气化成原子、分子,或离子化为离子,直接沉积到基体表面的方法。
8、阳极氧化:是指在适当的电解液中,以金属为阳极,在外加电流的作用下,使其表面生成氧化膜的方法。
9、真空化学热处理:是在真空条件下加热工件,渗入金属或非金属元素,从而改变材料表面化学产能成分、组织结构和性能的热处理方法。
10、贝尔比层:固体材料经切削加工后,在几微米到几十微米的表层中,可能发生组织结构的剧烈变化,而最外的5-10nm 厚可能形成的一种非晶态层。
11、现代表面技术:为满足某种特定的工程需要,使金属表面或零件表面具有特殊的成分、结够、功能的物理化学方法与工艺。
12、磷化:把金属放入含有Mn\Fe\Zn 的磷酸盐溶液中进行化学处理,使金属表面生成一层不溶于水的磷酸盐保护膜的方法。
13、CVD: 在一定的真空度和温度下,将几中含有构成沉积膜层的材料元素的单质或化合物反应源气体,通过化学反应而生成固态物质幷沉积在基体上的成膜方法。
二、填空题1、CVD 分类,按综合分类为热激发CVD 、低压CVD 、等离子体CVD 、激光(诱导)CVD 、金属有机化合物CVD 等。
渗氮与氮化处理
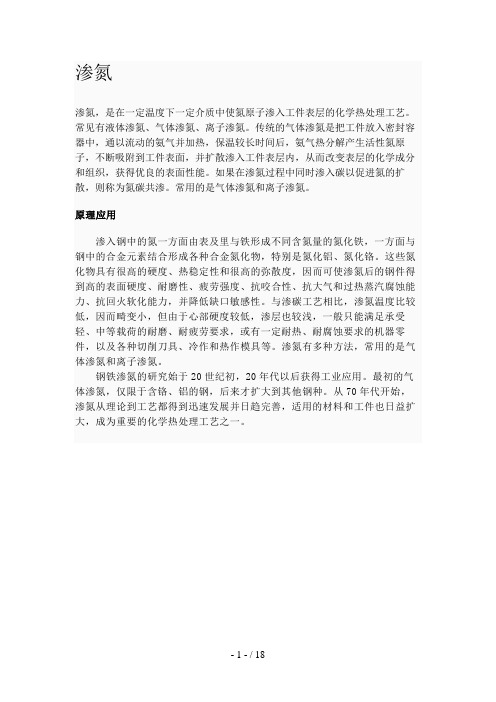
渗氮渗氮,是在一定温度下一定介质中使氮原子渗入工件表层的化学热处理工艺。
常见有液体渗氮、气体渗氮、离子渗氮。
传统的气体渗氮是把工件放入密封容器中,通以流动的氨气并加热,保温较长时间后,氨气热分解产生活性氮原子,不断吸附到工件表面,并扩散渗入工件表层内,从而改变表层的化学成分和组织,获得优良的表面性能。
如果在渗氮过程中同时渗入碳以促进氮的扩散,则称为氮碳共渗。
常用的是气体渗氮和离子渗氮。
原理应用渗入钢中的氮一方面由表及里与铁形成不同含氮量的氮化铁,一方面与钢中的合金元素结合形成各种合金氮化物,特别是氮化铝、氮化铬。
这些氮化物具有很高的硬度、热稳定性和很高的弥散度,因而可使渗氮后的钢件得到高的表面硬度、耐磨性、疲劳强度、抗咬合性、抗大气和过热蒸汽腐蚀能力、抗回火软化能力,并降低缺口敏感性。
与渗碳工艺相比,渗氮温度比较低,因而畸变小,但由于心部硬度较低,渗层也较浅,一般只能满足承受轻、中等载荷的耐磨、耐疲劳要求,或有一定耐热、耐腐蚀要求的机器零件,以及各种切削刀具、冷作和热作模具等。
渗氮有多种方法,常用的是气体渗氮和离子渗氮。
钢铁渗氮的研究始于20世纪初,20年代以后获得工业应用。
最初的气体渗氮,仅限于含铬、铝的钢,后来才扩大到其他钢种。
从70年代开始,渗氮从理论到工艺都得到迅速发展并日趋完善,适用的材料和工件也日益扩大,成为重要的化学热处理工艺之一。
气体渗氮一般以提高金属的耐磨性为主要目的,因此需要获得高的表面硬度。
它适用于38CrMoAl等渗氮钢。
渗氮后工件表面硬度可达HV850~1200。
渗氮温度低,工件畸变小,可用于精度要求高、又有耐磨要求的零件,如镗床镗杆和主轴、磨床主轴、气缸套筒等。
但由于渗氮层较薄,不适于承受重载的耐磨零件。
气体参氮可采用一般渗氮法(即等温渗氮)或多段(二段、三段)渗氮法。
前者是在整个渗氮过程中渗氮温度和氨气分解率保持不变。
温度一般在480~520℃之间,氨气分解率为15~30%,保温时间近80小时。
特殊热处理——可控气氛

4~8
4~15
0.5
30~60
0.1
1~5
0
75
N2 余量 余量
余量 25
露点
-10/+20 -15/+5
-30 -30
.
7
主要保护气的来源及应用
气氛的类型 放热型气体DX
吸热型气体RX
基本燃料 丙烷,丁烷,油,天
然气
丙烷,丁烷,天然气
使用范围
铁基金属光亮退火,浓 有色金属,淡 电机和变压器硅钢片的脱碳 硬钎焊烧结 渗碳 退火,淬火,普通烧结,无脱碳的硬
.
3
基本原理
分解:渗剂中生成能渗入工件表面的活性原 子的反应。
吸附:活性的原子(或离子)于表面金属的 原子产生键合而浸入其表层。
扩散:工件表面吸附活性原子(或离子)后 ,其表面浓度与内部形成浓度梯度,满足扩 散条件,渗入的元素相内部迁移形成一定厚 度的扩散层。
.Hale Waihona Puke 4可控气氛热处理目的
.
5
主要的可控气氛
材料烧结
净化的氨基气体 单组分气体NX
丙烷,丁烷,天然气 黑心可锻铸铁的退火,
油
无脱碳退火,低温退火,
炉子净化
氨基气体AX
氨(利用分解过程) 合金钢的退火和硬钎焊(存在Cr,
.
Al, Si)
8
工业使用率的统计
放热气氛25%
吸热气氛25%
净化的氮基或单组分气体气氛30%
分解氨气氛12%
其他气氛8%
氨分解气氛:
❖ H2 75%,N2 25%.
❖ 不锈钢、硅钢的退火等
.
14
特殊气氛
有机液体的滴注式气氛:
氮化工艺在钻杆接头螺纹处理中的应用研究
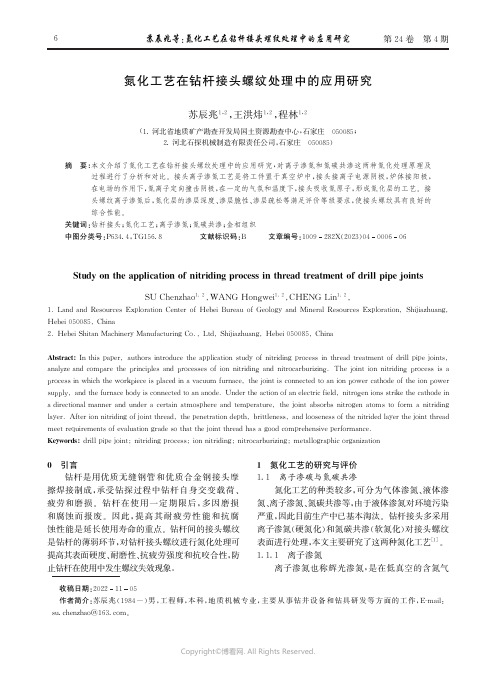
氮化工艺在钻杆接头螺纹处理中的应用研究苏辰兆1,2,王洪炜1,2,程林1,2(1.河北省地质矿产勘查开发局国土资源勘查中心,石家庄 050085;2.河北石探机械制造有限责任公司,石家庄 050085)摘 要:本文介绍了氮化工艺在钻杆接头螺纹处理中的应用研究,对离子渗氮和氮碳共渗这两种氮化处理原理及过程进行了分析和对比㊂接头离子渗氮工艺是将工件置于真空炉中,接头接离子电源阴极,炉体接阳极,在电场的作用下,氮离子定向撞击阴极,在一定的气氛和温度下,接头吸收氮原子,形成氮化层的工艺㊂接头螺纹离子渗氮后,氮化层的渗层深度㊁渗层脆性㊁渗层疏松等满足评价等级要求,使接头螺纹具有良好的综合性能㊂关键词:钻杆接头;氮化工艺;离子渗氮;氮碳共渗;金相组织中图分类号:P 634.4,T G 156.8 文献标识码:B 文章编号:1009282X (2023)04000606S t u d y o n t h e a p p l i c a t i o n o f n i t r i d i n g p r o c e s s i n t h r e a d t r e a t m e n t o f d r i l l p i p e jo i n t s S U C h e n z h a o 1 2W A N G H o n gw e i 1 2C H E N G L i n 1 21 L a n d a n d R e s o u r c e s E x p l o r a t i o n C e n t e r o f H e b e i B u r e a u o f G e o l o g y a n d M i n e r a l R e s o u r c e s E x p l o r a t i o n S h i j i a z h u a n gH e b e i 050085 C h i n a2 H e b e i S h i t a n M a c h i n e r y M a n u f a c t u r i n g C o L t d S h i j i a z h u a n gH e b e i 050085 C h i n a A b s t r a c t I n t h i s p a p e r a u t h o r s i n t r o d u c e t h e a p p l i c a t i o n s t u d y o f n i t r i d i n g p r o c e s s i n t h r e a d t r e a t m e n t o f d r i l l p i p e jo i n t s a n a l y z e a n d c o m p a r e t h e p r i n c i p l e s a n d p r o c e s s e s o f i o n n i t r i d i n g a n d n i t r o c a r b u r i z i n g T h e j o i n t i o n n i t r i d i n g pr o c e s s i s a p r o c e s s i n w h i c h t h e w o r k p i e c e i s p l a c e d i n a v a c u u m f u r n a c e t h e jo i n t i s c o n n e c t e d t o a n i o n p o w e r c a t h o d e o f t h e i o n p o w e r s u p p l y a n d t h e f u r n a c e b o d y i s c o n n e c t e d t o a n a n o d e U n d e r t h e a c t i o n o f a n e l e c t r i c f i e l d n i t r o ge n i o n s s t r i k e t h e c a t h o d e i n a d i r e c t i o n a l m a n n e r a n d u n d e r a c e r t a i n a t m o s p h e r e a n d t e m p e r a t u r e t h e j o i n t a b s o r b s n i t r o g e n a t o m s t of o r m a n i t r i d i ng l a y e r A f t e r i o n n i t r i d i n g o f j o i n t th r e a d t h e p e n e t r a ti o n d e p t h b r i t t l e n e s s a n d l o o s e n e s s o f t h e n i t r i d e d l a y e r t h e jo i n t t h r e a d m e e t r e q u i r e m e n t s o f e v a l u a t i o n g r a d e s o t h a t t h e j o i n t t h r e a d h a s a g o o d c o m pr e h e n s i v e p e r f o r m a n c e K e yw o r d s d r i l l p i p e j o i n t n i t r i d i n g p r o c e s s i o n n i t r i d i n g n i t r o c a r b u r i z i n g m e t a l l o g r a p h i c o r g a n i z a t i o n 收稿日期:20221105作者简介:苏辰兆(1984-)男,工程师,本科,地质机械专业,主要从事钻井设备和钻具研发等方面的工作,E -m a i l:s u .c h e n z h a o @163.c o m ㊂0 引言钻杆是用优质无缝钢管和优质合金钢接头摩擦焊接制成,承受钻探过程中钻杆自身交变载荷㊁疲劳和磨损㊂钻杆在使用一定期限后,多因磨损和腐蚀而报废㊂因此,提高其耐疲劳性能和抗腐蚀性能是延长使用寿命的重点㊂钻杆间的接头螺纹是钻杆的薄弱环节,对钻杆接头螺纹进行氮化处理可提高其表面硬度㊁耐磨性㊁抗疲劳强度和抗咬合性,防止钻杆在使用中发生螺纹失效现象㊂1 氮化工艺的研究与评价1.1 离子渗碳与氮碳共渗氮化工艺的种类较多,可分为气体渗氮㊁液体渗氮㊁离子渗氮㊁氮碳共渗等,由于液体渗氮对环境污染严重,因此目前生产中已基本淘汰㊂钻杆接头多采用离子渗氮(硬氮化)和氮碳共渗(软氮化)对接头螺纹表面进行处理,本文主要研究了这两种氮化工艺[1]㊂1.1.1 离子渗氮离子渗氮也称辉光渗氮,是在低真空的含氮气体中,利用工件(阴极)和阳极间产生的辉光放电现象进行的渗氮工艺㊂可获得高韧性的γ'相或无白亮层的氮化物层,具有良好的耐磨性㊁耐腐蚀性和高抗疲劳强度㊂该工艺是把放入炉内的工件作为阴极,离子渗氮炉体作为阳极,然后将炉内抽成低真空(1.33~ 13.30P a),冲入少量氨气,并继续对炉内抽气㊂当炉内压力达到70P a左右时,在阴阳极之间通以400~800V的直流电压,使炉内稀薄的气体发生电离,氨气在高压电场作用下部分分解成氮和氢的正离子及电子㊂在电场作用下,电子向阳极运动,N+㊁H+向工件(阴极)运动㊂正离子在电场作用下轰击在工件表面形成一层紫色辉光,其厚度为4~ 8m m㊂同时,N+在阴极夺取电子后还原成氮原子被工件表面吸收,并向内层扩散㊂氮离子轰击工件表面还能产生阴极溅射效应,溅射出F e-,这些溅射出来的F e-在等离子区与N+结合成F e N,F e N被吸附到工件表面上㊂在高温及离子轰击下,F e N很快分解为F e2N㊁F e3N等,并放出活性氮原子向工件内部扩散,于是在工件表面形成氮化层㊂随时间的增加,渗氮层逐步加深㊂离子渗氮优势有以下4点:(1)环保节能㊂由于离子氮化是利用辉光放电直接进行加热,通过离子化的含氮气体进行氮化处理,可获得均匀的温度,与间接的加热方式相比效率可提高2倍以上,能源消耗仅为气体氮化的40%~ 70%,耗气量远小于气体氮化工艺,无需配备防止污染的环保设施㊂因此,离子氮化法也称为21世纪的 环保氮化法 ㊂(2)渗速快㊂等离子氮化不仅氮化能力强,而且可使工件表面活化,产生加速吸收和扩散的缺陷,因而离子渗氮可以大大缩短渗氮时间,特别是浅层渗氮时更为突出㊂例如渗氮层深度在0.3~0.5m m 时,离子渗氮的时间仅为普通气体渗氮时间的1/3~1/5㊂(3)变形极小㊂由于离子渗氮是在真空中进行,因此可获得无氧化的加工表面,不会损坏被处理的工件表面,而且在低温下进行处理(380ħ起即可进行氮化处理),被处理的工件变形量极小,能满足高精度零部件的要求,处理后无需再进行机械加工,适合成品件的处理㊂(4)韧性良好㊂经气体氮化和盐浴氮化处理的工件表面通常会出现较厚(>20μm)的化合物层,这是由于ε+γ'两相组成的不均匀混合物层,里层则为扩散层㊂因此,在化合物内产生三相显微应力,若在此方向上再略加外力就会产生微裂纹,此裂纹逐渐扩展而使整个化合物层剥落㊂含铬㊁铝渗氮钢的化合物层很脆,气体氮化后一般都要去除该层后才能使用㊂而离子氮化通过控制气体中氮和碳的含量比,或氮气和氢气的比例,可以获得5~30μm的脆性较小的ε相单相层或0~8μm厚的韧性γ'相单相层,也可以得到韧性更优的无化合物层且仅有扩散层的渗层,这样可以不需要磨削直接装机使用㊂通过调节氮气㊁氢气及其他气体的比例,可以自由调节化合物层的相组成,从而获得预期的机械性能㊂1.1.2氮碳共渗氮碳共渗也称软氮化,是指在工件表层同时渗入氮原子和碳原子,并以渗氮为主的化学热处理工艺㊂氮碳共渗可分为铁素体氮碳共渗和奥氏体氮碳共渗,铁素体氮碳共渗的温度(570ħ)略高于渗氮温度(480~560ħ),使得氮碳共渗速度快于渗氮速度㊂氮碳共渗也可分为液体氮碳共渗和气体氮碳共渗,液体氮碳共渗采用氰盐作为共渗剂,氰盐具有剧毒,使用受限,一般采用气体氮碳共渗㊂气体氮碳共渗常用气体介质一般有尿素热分解气㊁甲酰胺及三乙醇胺等热分解气和氨气+渗碳气3大类㊂尿素在常温下是白色粉末状固体,在不同温度时尿素分解产物不同,在500ħ以下不能直接分解出活性氮㊁碳原子,在500ħ以上,尿素产生热分解反应,产生活性碳㊁氮原子,(N H2)2C OңC O+ 2[N]+2H2,2C Oң[C]+C O2㊂甲酰胺㊁三乙醇胺等有机化合物都是液体,甲酰胺在570ħ产生热分解,产生活性碳㊁氮原子,2H C O N H2ң2H2+ H2O+C O+2[N]+[C],2C OңC O2+[C]㊂渗碳气可采用吸热式气体㊁放热式气体等,采用吸热式气体与氨气的混合气体进行氮碳共渗时,两种气体的体积比为1ʒ1,混合气体的露点为0ħ,在570ħ进行共渗可取得良好的共渗效果㊂氮碳共渗工艺制定与共渗温度㊁共渗保温时间㊁共渗后的冷却息息相关㊂氮碳共渗温度多采用570ħ,低于此温度,氮在α-F e(铁素体)中的溶解度和扩散能力较低,渗速较慢㊂提高共渗温度,氮原子在γ'和ε相中的扩散系数增大,渗速加快,但化合物层(ε相)显著增厚,并且渗层表面易产生疏松层,疏松层厚度和疏松程度随温度提高而增大㊂图1为42C r M o钢不同共渗温度对化合物层深度及疏松层的影响㊂1.白亮层;2.ε相化合物层;3.致密ε相化合物;4.疏松ε相化合物1.t h e w h i t e b r i g h t l a y e r ;2.εi t e m o f t h e c o m p o u n d l a ye r ;3.εi t e m of t h e c o m p a c t c o m p o u n d l a ye r ;4.εi t e m of t h e l o o s e c o m p o u n d l a ye r 图1 42C r M o 钢共渗温度对化合物层深度及疏松层的影响F i g .1 Ef f e c t o f c o -i n f i l t r a t i o n t e m p e r a t u r e o n t h e d e pt h o f c o m p o u n d l a y e r a n d p o r o s i t y l a ye r of 42C r M o s t e e l 以42C r M o 为例,共渗层深度与共渗时间的关系遵循抛物线规律,见图2㊂延长共渗时间,渗层深度增加不明显,而且可能导致表面产生疏松,使渗层容易剥落㊁降低硬度,故氮碳共渗一般控制在4h 以内㊂图2 42C r M o 钢在570ħ氮碳共渗保温时间对渗层深度的影响F i g .2 E f f e c t o f n i t r o c a r b u r i z i n g h o l d i n gt i m e a t 570ħo n t h e d e p t h o f n i t r o c a r b u r i z e d l a ye r of 42C r M o s t e e l 氮碳共渗后的冷却与渗氮后的冷却方式不同,氮碳共渗后通常采用快冷方式,以获得过饱和的固溶体,使表面形成较大残余压应力,提高疲劳强度㊂对于畸变要求高的工件,可炉冷至450ħ左右,再油冷或空冷㊂综上所述,离子渗氮比氮碳共渗工艺所采用的渗氮温度更低,两者的所用温度都应低于回火温度,以保证工件心部性能不在渗氮中发生变化㊂1.2 氮化工艺前的预备热处理为保证工件心部具有良好的综合机械性能,消除加工应力,减小氮化变形以及为氮化处理做好组织准备,在氮化前一般都要进行预备热处理,即调质处理,调质的质量对氮化的质量有很大的影响㊂调质过程中,如淬火保温时间不够或温度太低,都会使铁素体不能完全溶入奥氏体中,调质后有游离铁素体存在㊂由于氮在铁素体中的扩散速度较快,该处在氮化后就会有较高的氮浓度,易形成针状氮化物,使氮化层脆性增大,容易剥落㊂因此调质后,表面层不允许出现游离铁素体,心部游离铁素体量不允许超过5%㊂相反,如果淬火温度过高,淬火后晶粒变粗,氮化物优先沿晶界伸展,氮化后出现波纹状或网状组织,也使氮化层脆性增大㊂调质过程中,回火温度的高低决定了基体中碳化物的弥散度㊂回火温度太高,基体中碳化物弥散度减小,氮化件心部强度㊁硬度不足,不能起支撑硬而脆的氮化层的作用,在外力作用下,尤其在较大接触应力作用下,往往会导致压碎或剥落,使零件过早失效;回火温度过低,会使心部强度㊁硬度过高,零件预备热处理后切削加工较困难,还会降低氮化速度㊂因此,选择适当的回火温度,以调整碳化物的弥散度,使它既能使渗层和心部有较好的性能,又可得到合理的渗速㊂1.3 接头螺纹氮化处理的优势接头螺纹进行表面处理的目的是为了防止钻具在使用过程中产生粘扣㊁表面划伤等影响使用寿命的状况,目前主流的表面处理技术主要包括螺纹表面渗氮和螺纹表面镀铜㊂螺纹表面渗氮可以使螺纹表面具有高的硬度及耐磨性[2-3],经氮化处理的钻杆接头表面硬度可达H R C 47以上,心部硬度为H R C 27~H R C 33,在保证表面高硬度的同时又能保证心部良好的韧性,渗氮层能使螺纹表面具有高的疲劳强度,具备良好的综合性能㊂实践证明,采用渗氮技术后,螺纹拧卸9次之内均可避免发生粘扣问题,同时还能有效减少磨损现象㊂一般渗氮的温度较低,常在480~570ħ,氮化处理后的螺纹表面变形小,可作为最终热处理㊂钻杆接头螺纹采用镀铜的方法可以对钻杆接头螺纹起到防腐减磨防护效果,当镀层的厚度达到5~15μm时,能有效防止螺纹出现粘扣现象㊂但需要注意的是在应用镀铜技术时需要克服镀层均匀性的问题,否则起不到上述的效果㊂2钻杆接头螺纹氮化工艺的技术要求2.1钻杆接头螺纹氮化前工件要求钻杆接头螺纹氮化前必须进行调质处理,原始组织级别1~2级,见表1㊂螺纹表面粗糙度应满足图纸要求的R a1.6μm,应保证螺纹表面无油渍和污物㊂表1渗氮前原始组织级别及说明T a b l e1G r a d e a n d d e s c r i p t i o n o f o r i g i n a l s t r u c t u r e b e f o r e n i t r i d i n g级别渗氮前原始组织级别说明1均匀细针状索氏体,游离铁素体量极少2均匀细针状索氏体,游离铁素体量<5%3细针状索氏体,游离铁素体量<15%4细针状索氏体,游离铁素体量<25%5索氏体(正火),游离铁素体量>25%2.2钻杆接头螺纹氮化后技术要求2.2.1渗氮层脆性渗氮层脆性指渗氮件表面在一定的试验力作用下,维氏硬度压痕边角碎裂的程度㊂检验渗氮层脆性,采用维氏硬度计,试验力规定为98.07N,加载5~10s,然后除去载荷㊂渗氮层脆性级别分为5级,接头螺纹级别1~2级合格,见表2㊂表2渗氮层脆性级别及说明T a b l e2B r i t t l e n e s s g r a d e a n d d e s c r i p t i o n o f n i t r i d e d l a y e r 级别渗氮层脆性级别及说明1压痕边角完整无缺2压痕一边或一角碎裂3压痕二边或二角碎裂4压痕三边或三角碎裂5压痕四边或四角碎裂2.2.2渗氮层疏松渗氮层疏松指渗氮层中表面化合物层(白亮层)微孔的密集程度㊂显微放大500倍检验白亮层的疏松程度,按白亮层内微孔的形状㊁数量㊁密集程度分为5级,接头螺纹级别1~2级合格,见表3㊂表3渗氮层疏松级别及说明T a b l e3G r a d e a n d p o r o s i t y d e s c r i p t i o n o f n i t r i d e d l a y e r级别渗氮层疏松级别及说明1化合物层致密,表面无微孔2化合物层较致密,表面有少量细点状微孔3化合物层微孔密集成点状孔隙,由表及里逐渐减少4微孔占化合物层2/3以上厚度,部分微孔聚集分布5微孔占化合物层3/4以上厚度,部分呈空洞密集分布2.2.3脉状氮化物脉状氮化物指扩散层中与表面平行走向的脉浪状氮化物㊂显微放大500倍检验扩散层中氮化物的形态㊁数量㊁分布情况,分为5级,接头螺纹级别1~ 2级合格,见表4㊂表4氮化物级别及说明T a b l e4N i t r i d e g r a d e a n d d e s c r i p t i o n级别氮化物级别及说明1扩散层中有极少量呈脉状分布的氮化物2扩散层中有少量呈脉状分布的氮化物3扩散层中有较多呈脉状分布的氮化物4扩散层中有较严重脉状和少量断续网状分布的氮化物5扩散层中有连续网状分布的氮化物3钻杆接头氮化的检验分析3.1钻杆接头的化学成分分析采用红外碳硫分析仪N-HW200D和电脑红外多元素分析仪N-HW300D,对接头试样进行取屑化验,分析结果如表5所示㊂表54137H(37C r M n M o)化学成分T a b l e5C h e m i c a l c o m p o s i t i o n o f137H(37C r M n M o)元素含量/%C0.370S i0.240M n0.930C r1.120M o0.310A l0.015P0.013S0.0043.2钻杆接头氮化后微观组织分析利用铁氮平衡图(图3)可以分析钻杆接头在不同温度下渗氮层各相的组成,由表及里依次为α㊁ε+γ'㊁γ'+α㊁α㊂从图中可得出在不同温度下各渗氮相形成顺序及组成物[4]㊂表6给出渗氮相形成顺序及相组成物,从表6可知,为减少螺纹表面变形,尽量选择<590ħ进行渗氮处理㊂3.3 钻杆接头渗氮前的原始组织使用H V S -1000数显显微硬度计,抛光后在4%的硝酸酒精腐蚀的状态下,放大500倍对接头螺纹进行钻杆接头的原始组织检验㊂检验结果如图4所示,原始组织为调质后的索氏体+少量游离铁素体,评定为2级㊂图3 铁氮平衡图F i g .3 I r o n -n i t r o g e n e q u i l i b r i u m d i a gr a m 表6 渗氮相形成顺序及相组成物T a b l e 6 N i t r i d i n g p h a s e f o r m a t i o n s e qu e n c e a n d p h a s e c o m -po s i t i o n 渗氮温度/ħ相形成顺序由表及里的相组成物<590αңγ'ңεεңγ'+εңγ'ңα+γ'ңα590~680αңγңγ'ңεεңγ'+εңγ'ңγ+γ'ңγңα+γңα>680αңγңεεңγ+εңγңα+γңα图4 原始组织F i g .4 T h e o r i g i n a l o r ga n i z a t i o n 3.4 钻杆接头螺纹渗层深度测定使用H V S -1000数显显微硬度计,采用硬度法对接头螺纹进行渗氮深度的测定,分析结果如图5所示㊂由图6可知,试验力采用2.94N ,渗层深度图5 渗氮层深度检验F i g .5 D e p t h i n s p e c t i o n o f n i t r i d e d l a ye r D N =0.46m m ,渗层硬度>350H V (基体硬度+50H V ),可表示为0.46D N (350H V 0.3)㊂其中,基体硬度是在距表面3倍渗层深度处测3点硬度,并求平均值作为基体硬度值,此样约为300H V ㊂3.5 钻杆接头螺纹金相组织检验3.5.1 接头螺纹渗氮层脆性检验使用H V S -1000数显显微硬度计,在抛光未腐蚀的状态下,试验力采用98.07N ㊂对接头螺纹进行渗氮层脆性检验,如图6所示,渗氮层脆性为1级㊂图6 渗氮层脆性检验F i g .6 B r i t t l e n e s s i n s p e c t i o n o f n i t r i d e d l a ye r 3.5.2 接头螺纹渗氮层疏松检验使用H V S -1000数显显微硬度计,抛光后在4%的硝酸酒精腐蚀的状态下,放大500倍对接头螺纹进行渗氮层疏松检验㊂如图7所示,渗氮层中化合物层(白亮层)的疏松为2级㊂3.5.3 接头螺纹渗氮层氮化物检验使用H V S -1000数显显微硬度计,抛光后在4%的硝酸酒精腐蚀的状态下,放大500倍对接头螺纹进行渗氮层氮化物检验㊂如图8所示,渗氮层中扩散层的氮化物为2级㊂图7 渗氮层疏松检验F i g .7 P o r o s i t y i n s p e c t i o n o f n i t r i d e d l a yer 图8 渗氮层氮化物检验F i g .8 N i t r i d e i n s p e c t i o n o f n i t r i d e d l a ye r 4 结语钻杆接头螺纹经过表面氮化处理后,渗层深度为0.46m m ,渗层硬度>350H V ;渗氮层脆性等级为1级,压痕边角完整无缺;渗氮层疏松等级为2级,化合物层较致密,表面有少量细点状微孔;渗氮层氮化物等级为2级,扩散层中有较少量呈脉状分布的氮化物㊂钻杆接头渗氮层符合G B /T 113542005中规定的技术要求,满足了客户的需求,使离子渗氮技术得到推广和应用㊂参考文献(R e f e r e n c e s):[1] 侯旭明.热处理原理与工艺[M ].机械工业出版社,2011.H O U X u m i n g .H e a t t r e a t m e n t p r i n c i pl e a n d p r o c e s s [M ].C h i n a M a c h i n e P r e s s ,2011.[2] 付现桥,刘志田,张文浩,等.钻杆接头离子渗氮处理组织和性能研究[J ].当代化工,2014(6):925927.F U X i a n qi a o ,L I U Z h i t i a n ,Z H A N G W e n h a o ,e t a l .M i c r o s t r u c t u r e a n d p r o p e r t i e s o f n i t r i d e d l a ye r o b t a i n e d b y i o n n i t r i d i n g o n d r i l l p i pe j o i n t s [J ].C o n t e m p o r a r y C h e m i c a l I n d u s t r y ,2014(6):925927.[3] 葛鹏飞.激光淬火技术在钻杆接头螺纹表面硬化处理的应用[J ].内蒙古石油化工,2015(1):119120.G E P e n g f e i .A p p l i c a t i o n o f l a s e r t e c h n o l o g yi n s u r f a c e h a r d e n i n g t r e a t m e n t o f d r i l l p i pe j o i n t t h r e a d [J ].I n n e r M o n g o l i a P e t r o c h e m i c a l I n d u s t r y,2015(1):119120.[4] 阎利民.气体氮化工艺探究[J ].金属加工(热加工),2009(19):4042.Y A N L i m i n .R e s e a r c h o n g a s n i t r i d i n g t e c h n o l o g y[J ].M e t a l W o r k i n g,2009(19):4042.。
渗氮

渗氮求助编辑渗氮,是在一定温度下一定介质中使氮原子渗入工件表层的化学热处理工艺。
常见有液体渗氮、气体渗氮、离子渗氮。
传统的气体渗氮是把工件放入密封容器中,通以流动的氨气并加热,保温较长时间后,氨气热分解产生活性氮原子,不断吸附到工件表面,并扩散渗入工件表层内,从而改变表层的化学成分和组织,获得优良的表面性能。
如果在渗氮过程中同时渗入碳以促进氮的扩散,则称为氮碳共渗。
常用的是气体渗氮和离子渗氮。
目录编辑本段一般以提高金属的耐磨性为主要目的,因此需要获得高的表面硬度。
它适用于38CrMoAl等渗氮钢。
渗氮后工件表面硬度可达HV850~1200。
渗氮温度低,工件畸变小,可用于精度要求高、又有耐磨要求的零件,如镗床镗杆和主轴、磨床主轴、气缸套筒等。
但由于渗氮层较薄,不适于承受重载的耐磨零件。
气体参氮可采用一般渗氮法(即等温渗氮)或多段(二段、三段)渗氮法。
前者是在整个渗氮过程中渗氮温度和氨气分解率保持不变。
温度一般在480~520℃之间,氨气分解率为15~30%,保温时间近80小时。
这种工艺适用于渗层浅、畸变要求严、硬度要求高的零件,但处理时间过长。
多段渗氮是在整个渗氮过程中按不同阶段分别采用不同温度、不同氨分解率、不同时间进行渗氮和扩散。
整个渗氮时间可以缩短到近50小时,能获得较深的渗层,但这样渗氮温度较高,畸变较大。
还有以抗蚀为目的的气体渗氮,渗氮温度在 550~700℃之间,保温0.5~3小时,氨分解率为35~70%,工件表层可获得化学稳定性高的化合物层,防止工件受湿空气、过热蒸汽、气体燃烧产物等的腐蚀。
正常的气体渗氮工件,表面呈银灰色。
有时,由于氧化也可能呈蓝色或黄色,但一般不影响使用。
编辑本段离子渗氮又称辉光渗氮,是利用辉光放电原理进行的。
把金属工件作为阴极放入通有含氮介质的负压容器中,通电后介质中的氮氢原子被电离,在阴阳极之间形成等离子区。
在等离子区强电场作用下,氮和氢的正离子以高速向工件表面轰击。
金属热处理渗氮加工的工艺方法
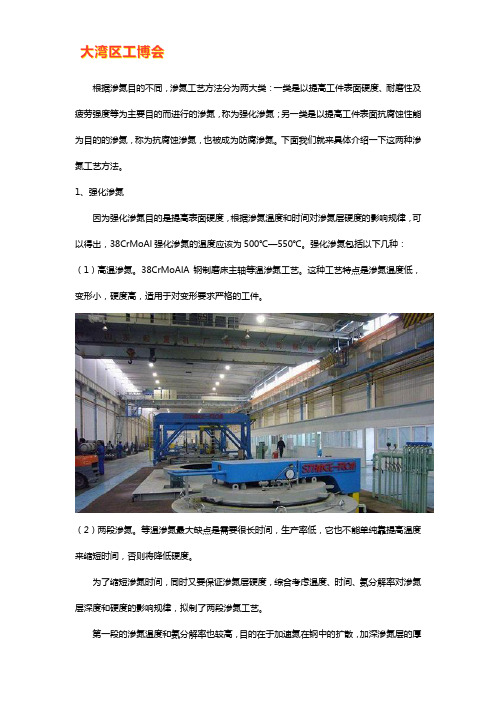
根据渗氮目的不同,渗氮工艺方法分为两大类:一类是以提高工件表面硬度、耐磨性及疲劳强度等为主要目的而进行的渗氮,称为强化渗氮;另一类是以提高工件表面抗腐蚀性能为目的的渗氮,称为抗腐蚀渗氮,也被成为防腐渗氮。
下面我们就来具体介绍一下这两种渗氮工艺方法。
1、强化渗氮因为强化渗氮目的是提高表面硬度,根据渗氮温度和时间对渗氮层硬度的影响规律,可以得出,38CrMoAl强化渗氮的温度应该为500℃—550℃。
强化渗氮包括以下几种:(1)高温渗氮。
38CrMoAlA钢制磨床主轴等温渗氮工艺。
这种工艺特点是渗氮温度低,变形小,硬度高,适用于对变形要求严格的工件。
(2)两段渗氮。
等温渗氮最大缺点是需要很长时间,生产率低,它也不能单纯靠提高温度来缩短时间,否则将降低硬度。
为了缩短渗氮时间,同时又要保证渗氮层硬度,综合考虑温度、时间、氨分解率对渗氮层深度和硬度的影响规律,拟制了两段渗氮工艺。
第一段的渗氮温度和氨分解率也较高,目的在于加速氮在钢中的扩散,加深渗氮层的厚度,从而缩短总的渗氮时间,并使渗氮层的硬度分布曲线趋于平缓。
第二段温度的升高,虽要发生氮化物的集聚、长大,但它与一次较高温度渗氮不同,因为在第一段渗氮时首先形成的高度弥散细小的氮化物,其集聚涨大要比直接再高温时涨大的氮化物的粗化过程慢得多,因而其硬度下降不显著。
(3)三段渗氮。
为了使两段渗氮后表面氮浓度有所提高,以提高其表面硬度,在两端渗氮后期再次降低渗氮温度和氨分解率而出现了三段渗氮法。
2、抗腐蚀渗氮经过抗腐蚀渗氮的碳钢、低合金钢及铸铁零件,在自来水、湿空气、过热蒸汽以及弱碱液中,具有良好的抗腐蚀性能。
因此已用来制造自来水龙头、锅炉汽管、水管阀门及门把手等,代替铜件和镀铬件,但是,渗氮层在酸溶液中没有抗腐蚀性。
抗腐蚀渗氮过程与强化渗氮过程基本相同,只有渗氮温度较高,有利于缩短渗氮时间。
但是温度过高,表面含氮量降低,孔隙度增大,因而抗腐蚀性降低。
渗氮、渗碳工艺与操作过程

一渗碳工艺(气体渗碳——煤油):渗碳钢的碳含量一般在0.12%~0.25%之间,其所含主要合金元素一般是铬、锰、镍、钼、钨、钛等。
○1把炉温升到800℃左右,断开电源打开炉盖,放入装好工件的工装,关闭炉盖升温到930℃左右。
在升温过程中,打开风扇及煤油阀门,以每分钟160滴的速度滴入炉内,进行排气,同时打开试样孔和排气管并点燃排气火焰。
排气时间一般为60~80分钟(保证温度到渗碳温度还要排气30分钟左右);○2当火焰为鸡蛋黄颜色时开始强渗了,此时要加大煤油的滴量,按每分钟180~200滴。
在强渗时就可用放入试棒(含碳量少的材料,尺寸Ф8×100mm),关闭试样孔,炉压保持在6~10格——渗层深炉压取高值。
渗碳速度一般按0.15~0.2mm/h来计算,如要渗层深度为0.8~1.2mm,则强渗时间为6小时,提前在强渗设定时间结束前半小时,取出试棒,观察渗层深度(试棒渗层深度一般为工件的一半,这边渗层深度靠操作工的肉眼加经验判断),深度够在强渗结束就可以开始扩散,否则增加强渗时间;○3扩散期温度不变,减少煤油滴量,按每分钟100滴,一般扩散时间为60~90分钟,作用是均匀工件表层的碳溶度;○4扩散期结束开始降温,此时断开加热器,降温到810℃左右,并在此温度保温10~20分钟。
降温期减少煤油滴量,按每分钟60滴。
保温结束时断开加热器,关闭风扇,打开炉盖,用行车吊起工装,垂直进入温度为50~70℃的油中冷却,冷却时上下左右轻轻摇动工装,一般冷却时间为10~20分钟左右,吊起工装时也要注意工件出油的温度。
○5冷却好的工件要在半个小时之内(防止工件开裂)进行低温回火,温度一般在160~190℃(由硬度要求而定),保温时间2小时左右出炉空冷。
在渗碳过程中要随时注意火焰形状,正常的火焰是:火焰呈金黄色,无力不熄灭(断续熄灭,说明水气高了),火苗无黑焰和火星,火苗长100~150mm;若火苗出现火星,说明炉内炭黑过度;火苗过长、尖端外缘呈亮白色,说明渗碳剂供量过多;火苗短、外缘呈浅蓝色并有透明,说明渗碳剂供量不足或炉子漏气。
合金钢表面渗氮处理

合金钢表面渗氮处理合金钢表面渗氮处理是一种常见的表面改性技术,通过将氮元素引入合金钢的表层,改善了其硬度、耐磨性和耐蚀性,提高了材料的综合性能。
本文将从渗氮的原理、渗氮方法和渗氮处理的效果等方面进行详细介绍。
一、渗氮原理合金钢表面渗氮处理是利用氮在高温下与钢的表面发生化学反应的特性,将氮原子引入钢材表层。
这种处理方法可以通过多种方式实现,包括气体渗氮、盐浴渗氮、浆料渗氮和离子渗氮等。
其中,离子渗氮是一种较为常用的方法。
在渗氮过程中,渗氮源通常是氨气,通过将氨气电离成氮离子,然后在高温下将氮离子引入合金钢表面,实现渗氮。
二、渗氮方法1. 气体渗氮:将氨气或氮气通入渗氮炉中,在高温下使氨气或氮气分解产生游离的氮原子,然后通过扩散作用将氮原子渗透到合金钢表面。
这种方法操作简单,成本较低,但渗层深度较浅,一般不超过0.5mm。
2. 盐浴渗氮:将含有氮化物的盐浴加热至高温,然后将合金钢浸入盐浴中进行渗氮处理。
这种方法渗层深度较大,一般可达1-2mm,但温度较高,对钢材的变形和热应力有一定影响。
3. 浆料渗氮:将氮化物粉末与助剂混合成浆料,然后将浆料涂覆在合金钢表面,在高温下使氮化物分解,将氮原子渗透到钢材表层。
这种方法对钢材的变形和热应力影响较小,但渗层深度较浅。
4. 离子渗氮:在真空或氮气气氛中,通过电离氨气产生氮离子,然后加速氮离子并引入合金钢表面,实现渗氮。
这种方法操作灵活,渗层深度可控制,且渗层均匀。
三、渗氮处理的效果合金钢表面渗氮处理后,可以显著提高钢材的硬度和耐磨性,使其具有较好的耐磨性能。
渗氮处理后的合金钢表面形成了一层硬度较高的氮化物,这种氮化物可以在摩擦和磨损过程中起到保护作用。
同时,渗氮处理还可以显著提高合金钢的耐蚀性能,使其在恶劣环境下具有更好的抗腐蚀能力。
此外,渗氮处理还可以提高合金钢的疲劳强度和抗氢脆性能,延长材料的使用寿命。
合金钢表面渗氮处理是一种有效的表面改性技术,通过引入氮元素,可以显著改善合金钢的硬度、耐磨性和耐蚀性,提高材料的综合性能。
渗氮处理
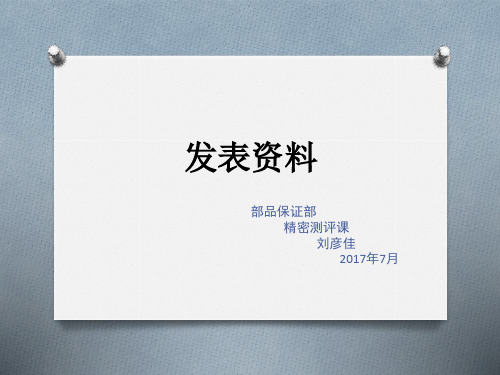
单体内
600以下
600以上
45
60
同一批次
600以下
600以上
70
100
窒化处理后的化合物层厚度(均匀性)一般满足以下要求: 单位:um
化合物层深度
单体内
深度偏差
同一批次
5以下
2
3
5-10 10-20 20以上
4
5
6
7
8
10
参考JIS B 6915:1998
谢谢!Leabharlann 铜箔 氮化层芯材膜厚块
金相分析仪
化合物层厚度
主要是Fe3N及少量Fe4C
S45C系列用3%硝酸(HNO3)+97%乙醇(C2H6O)溶液腐蚀 SUM系列用五水硫酸铜(CuSO4.5H2O)+盐酸(HCl)溶液腐蚀
窒化处理后的样品硬度(均匀性)一般满足以下要求: 单位:um
HV 实际值
HV(max-min)
气体渗氮技术流程
表面清 洗
气体去油,氧 化铝粉将表面 作喷砂处理
二选一
表面加以磷 酸皮膜处理
加热
同时进行
排除空 气
渗氮炉
渗氮处理
(520C。左右, 4-10h)
氮化处理 冷却
热交换机 启动
气体渗氮的三种方法
一段式渗氮法
等温渗氮也称一段式渗氮法。 它是在恒温下进行长时间保温的 渗氮工艺,渗氮温度510~530℃, 其渗氮工艺曲线如图所示。
特点:三段式渗氮能进一步提高渗氮速度,但硬度比一般渗氮工艺 低,脆性、变形等比一般渗氮工艺略大。
渗氮注意事项
(1)渗氮前的预备热处理调质--渗氮工件在渗氮前应进行调质处理,以 获得回火索氏体组织.调质处理回火温度一般高于渗氮温度. (2)渗氮前的预备热处理去应力处理--渗氮前应尽量消除机械加工过 程中产生的内应力以稳定零件尺寸.消除应力的温度均应低于回火温 度,保温时间比回火时间要长些,再缓慢冷却到室温.断面尺寸较大的 零件不宜用正火.工模具钢必须采用淬火回火,不得用退火. (3)渗氮零件的表面粗糙度Ra应小于1.6um,表面不得有拉毛、碰伤及 生锈等缺陷.不能及 时处理的零件须涂油保护,以免生锈.吊装入炉时 再用清洁汽油擦净以保证清洁度. (4)含有尖角和锐边的工件,不宜进行氮化处理. (5)局部不氮化部位的保护,不宜用留加工余量的方法. (6)表面未经磨削处理的工件,不得进行氮化
渗氮知识
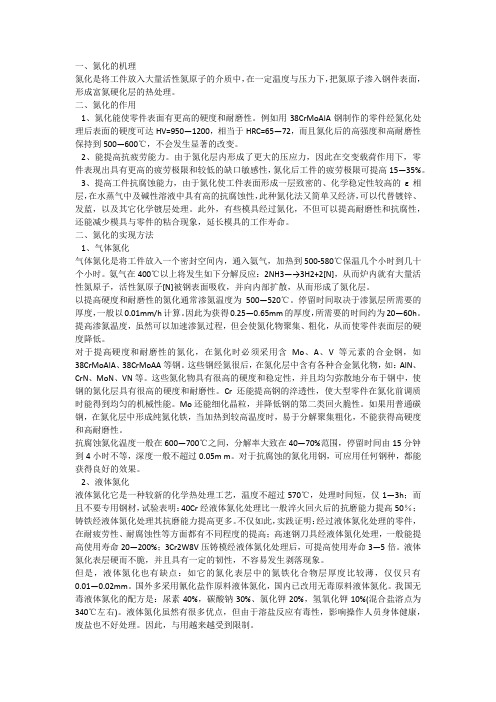
一、氮化的机理氮化是将工件放入大量活性氮原子的介质中,在一定温度与压力下,把氮原子渗入钢件表面,形成富氮硬化层的热处理。
二、氮化的作用1、氮化能使零件表面有更高的硬度和耐磨性。
例如用38CrMoAlA钢制作的零件经氮化处理后表面的硬度可达HV=950—1200,相当于HRC=65—72,而且氮化后的高强度和高耐磨性保持到500—600℃,不会发生显著的改变。
2、能提高抗疲劳能力。
由于氮化层内形成了更大的压应力,因此在交变载荷作用下,零件表现出具有更高的疲劳极限和较低的缺口敏感性,氮化后工件的疲劳极限可提高15—35%。
3、提高工件抗腐蚀能力,由于氮化使工件表面形成一层致密的、化学稳定性较高的ε相层,在水蒸气中及碱性溶液中具有高的抗腐蚀性,此种氮化法又简单又经济,可以代替镀锌、发蓝,以及其它化学镀层处理。
此外,有些模具经过氮化,不但可以提高耐磨性和抗腐性,还能减少模具与零件的粘合现象,延长模具的工作寿命。
二、氮化的实现方法1、气体氮化气体氮化是将工件放入一个密封空间内,通入氨气,加热到500-580℃保温几个小时到几十个小时。
氨气在400℃以上将发生如下分解反应:2NH3—→3H2+2[N],从而炉内就有大量活性氮原子,活性氮原子[N]被钢表面吸收,并向内部扩散,从而形成了氮化层。
以提高硬度和耐磨性的氮化通常渗氮温度为500—520℃。
停留时间取决于渗氮层所需要的厚度,一般以0.01mm/h计算。
因此为获得0.25—0.65mm的厚度,所需要的时间约为20—60h。
提高渗氮温度,虽然可以加速渗氮过程,但会使氮化物聚集、粗化,从而使零件表面层的硬度降低。
对于提高硬度和耐磨性的氮化,在氮化时必须采用含Mo、A、V等元素的合金钢,如38CrMoAlA、38CrMoAA等钢。
这些钢经氮很后,在氮化层中含有各种合金氮化物,如:AlN、CrN、MoN、VN等。
这些氮化物具有很高的硬度和稳定性,并且均匀弥散地分布于钢中,使钢的氮化层具有很高的硬度和耐磨性。
模具钢渗氮层金相分析
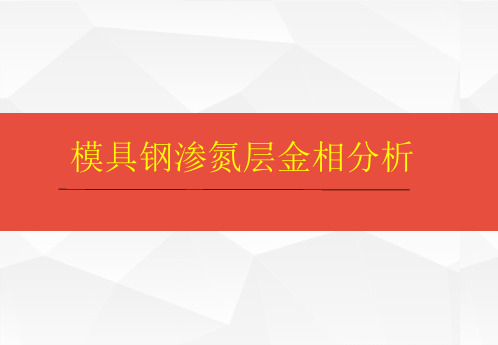
造成硬度偏低的原因通常有: 设备方面:如系统漏气造成氧化。 材料方面:如材料选择不合理。 前期热处理:如基体硬度太低,表面脱碳严重等。 工件预处理不彻底:如进炉前的清洁方式及清洁度。 工艺方面:如渗氮温度过高或过低,时间短或氮浓度不足等等。
6)外观颜色有差别 不同材质的零件经渗氮处理后表面颜色是略有区别的,零件出炉后首先用肉 眼检查外观质量,钢件经渗氮处理后表面通常呈银灰(蓝黑色)色或暗灰色 (蓝黑色),钛及钛合金件表面应呈金黄色。
模具钢渗氮工艺基础知识
模具钢渗氮层的金相分析
3、气体渗氮工艺
工艺路线:锻造→正(退)火→粗加工→调质→精加工→去应力退火→粗磨 →氮化(→精磨)。 气体渗氮分为三种:等温渗氮(一段氮化)、二段氮化、三段氮化。
1)等温氮化:
前20h是表面形成氮化物阶段,采用低 氨分解率使表面迅速吸收大量氮原子并使 表面形成弥散度大的氮化物提高表面硬度。 第二阶段是表层氮原子向内扩散,增 加渗层厚度.为了降低氮化层脆性,在氮化 结束前2h进行退氮处理,使氮继续向内层扩 散,以降低表面的氮浓度。 等温氮化操作简单、变形小,但氮化 时间长,生产效率低,且氮化后表面往往 有“白亮层”产出,有时还有疏松层。
模具钢渗氮层金相分析 我们毕业啦
其实是答辩的标题地方
第一部分 模具钢渗氮工艺基础知识
第二部分 模具钢渗氮层的金相分析 CONTANTS
第一部分
渗氮工艺基础知识
模具钢渗氮工艺基础知识
模具钢渗氮层的金相分析
1、定义
渗氮:是在一定温度下一定介质中使氮原子渗入工件表层的化学热处理工 艺。常见的渗氮方式有:液体渗氮、离子渗氮、气体渗氮。 气体渗氮:是把工件放入密封容器中,通以流动的氨气并加热,保温较长 时间后,氨气热分解产生活性氮原子,不断吸附到工件表面,并扩散渗入 工件表层内,从而改变表层的化学成分和组织,获得优良的表面性能。
金属热处理工艺学

1.碳势:纯铁在一定温度下于加热炉气中加热时达到既部增碳也不脱碳并与炉气保持平衡时表面的含碳量.2.脱碳:钢中的碳也会和气氛作用,使钢的表面失去一部分碳,含碳量降低,这种现象成为脱碳。
3.过烧:加热温度过高,出现晶界氧化,甚至晶界局部熔化,造成工件报废。
4.放热式气体:原料气与较充足的空气混合,仅靠其本身的不完全燃烧所放出的热量就能维持其反应时,所制成的气体。
5.光亮热处理:是指在热处理过程中(主要是淬火和退火),采用气体保护或者是真空状态,避免或减少被热处理的工件表面与氧气接触而发生氧化,从而达到工件表面的光亮或相对光亮。
6.淬火烈度:淬火介质的冷却能力。
7.淬透性:钢材淬火时获得马氏体的能力的特性.8.淬硬性:淬硬性是指钢在淬火时的硬化能力,用淬火后马氏体所能达到的最高硬度表示,它主要取决于马氏体中的含碳量。
9.自回火:当淬火后尚未完全冷却,利用在工件内残留的热量进行回火。
10.退火:将组织偏离平衡状态的金属或合金加热到适当的温度,保持一定时间,然后缓慢冷却以达到接近平衡状态组织的热处理工艺。
11.表面淬火:被处理工件在表面有限深度范围内加热至相变点以上,然后迅速冷却,在工件表面一定深度范围内达到淬火目的的热处理工艺。
12.连续加热法:对工件需淬火部位中的一部分同时加热,通过感应器与工件之间的相对运动,把已加热部位逐渐移到冷却位置冷却,待加热部位移至感应器中加热,如此连续进行,直至需硬化的全部部位淬火完毕。
13.化学热处理:将工件放置于某种渗入元素的活性介质中,通过加热、保温和冷却,使渗入元素被吸附并扩散渗入工件表面层,以改变表面层化学成分和组织,从而使其表面具有与心部不同的特殊性能的一种工艺。
14.淬火:把钢加热到临界点Ac1或Ac3以上,保温并随之以大于临界冷却速度(Vc)冷却,以得到介稳状的M或B下组织的热处理工艺。
15.反应扩散:由溶解度较低的固溶体转变成浓度更高的化合物,这种扩散称为反应扩散。
渗氮氧处理处理工艺

[知识园地]渗氮+氧处理处理工艺渗氮过程中氧的加入大致有三种方式:渗氮前预氧化、渗氮后氧化、氧化渗氮同时进行(氧氮共渗、氮氧共渗)。
1 预氧化渗氮(预氧化催渗气体渗氮)气体渗氮在工业上应用广泛,但周期太长,人们不断努力探索新工艺,以缩短周期,预氧化就是其中的一例。
预氧化渗氮就是在气体渗氮前进行一次规范的预氧化处理,使工件表面形成一层致密的Fe3O4氧化物薄膜,这层薄膜对随后氮的渗入起着加速作用,在保证渗氮效果的前提下,可缩短周期15%~30%(也有报道采用预氧化两段快速渗氮处理38CrMoAl钢或经预氧化多段变温快速气体渗氮,渗氮周期缩短50%以上),从而显著提高生产率,降低能耗和气耗。
预氧化渗氮也能起到改善渗氮表面的抗初期磨损能力、抗咬合能力和疲劳强度等。
采用预氧化催渗气体渗氮技术无需添加额外设备,工艺简单,适合于生产中推广应用。
采用预氧化气体渗氮工艺:200℃进炉,350~450℃×1.5h预氧化,520℃×(8~12)h,氨分解率为18%~22%;然后560℃×(10~12)h,氨分解率为40%~60%,炉冷至160℃出炉。
经此工艺处理后:38CrMoAl渗层深度为0.4~0.6mm,硬度为840~1028HV10;40Cr渗层深度为0.5~0.7mm,硬度为500~580HV10;42CrMo钢渗层深度为0.4~0.6mm,硬度为580~600HV10。
与传统工艺比较,可缩短一半时间。
球墨铸铁气体渗氮工艺:预氧化300℃×1h,然后升温至480℃开始通氨气和氮气,尽快排除炉内空气;然后520℃×2h强渗(氨分解率30%~40%),570℃×3h扩散(氨分解率40%~60%)。
经此工艺处理后:试样渗氮层深度为0.19mm,表面硬度为405HV。
预氧化温度一般350~450℃,时间为1~2h。
预硬化催渗机理,基本上有两种观点:一种认为表面获得结构致密的Fe3O4氧化膜,在渗氮初期被氨气分解产生的氢还原(Fe3O4+4H2=3Fe+4H2O),生成洁净的表面,产生大量能够吸附氮原子的活性位置,使得氮原子被吸附的几率和吸附量增加,因此,增强了工件表面的吸氮能力;另一种观点认为预氧化表面和预氧化层内部本身的多孔结构增加了氨气与工件表面反应的有效面积,同时,炉气中的NH3与Fe3O4反应(4Fe3O4+4NH3=4Fe3N+6H2O+5O2),使孔隙进一步增加,大量吸附氨,并使之在表面或疏松面分解,释放出氮原子,另外NH3与Fe3O4反应生成O2,氧也能被吸附进入工件,形成氧氮共渗,而氧的渗入对渗氮有催化作用。
离子渗氮工艺原理

离子渗氮工艺原理【2009-1-8】﹝一﹞钢的渗氮渗氮是把氮渗入钢件的表面,形成富氮硬化层的化学热处理过程。
在工业生产中,常用的工艺方法有:气体渗氮、盐浴渗氮和离子渗氮。
1.渗氮工艺的特点﹝1﹞渗氮后的零件表面具有高的硬度、耐磨性、疲劳强度和低的缺口敏感性。
﹝2﹞渗氮温度较低,一般在500-600℃,而且,渗氮层的高硬度可以由渗氮直接得到,不需要经过较高温度的加热和淬火。
所以,渗氮工艺的变形是最小的,常常作为零件的最后一道工序。
﹝3﹞渗氮层有较高的抗腐蚀性能。
2.渗氮工艺的化学过程渗氮和其他化学热处理工艺一样,也是由分解、吸收、扩散三个基本过程组成的。
﹝1﹞分解渗氮介质﹝通常为氨气﹞通过热分解或其他方法,生成活性氮原子。
﹝2﹞吸收钢表面吸收氮原子,形成氮在铁中的固溶体和氮化物。
﹝3﹞扩散氮从表面高浓度的饱和层向钢内层深处进行扩散,形成一定深度的渗氮层。
3.渗氮层的组织根据Fe-N状态图,渗氮层主要由α、γ、γ,、ε四个相组成。
﹝1﹞α相氮在α-Fe中的间隙固溶体。
最大溶解度为0.1%。
﹝2﹞γ相氮在γ-Fe中的间隙固溶体。
﹝3﹞γ,相为一可变成分的间隙相化合物,含氮量在5.7-6.1%之间,成分符合Fe4-N。
﹝4﹞ε相是含氮量变化范围相当宽的化合物,成分在8.25-11.0%之间变化。
ε相硬度高,脆性大。
4.合金元素的作用碳钢和合金钢中由于碳和合金元素的作用,也影响渗氮层的形成。
碳的存在会使氮的扩散受阻,减小渗氮层的厚度。
钢中大部分合金元素都能形成氮化物,按氮化物的稳定性﹝稳定性越高,硬度也越高﹞次序排列依次为:Ti、Al、V、W、Mo、Cr、Mn、Fe。
所以,为了在表面得到高的硬度和耐磨性,必须向钢中加入能与氮形成稳定氮化物的合金元素。
同时,V、W、Mo、Cr等合金元素还能改善钢的组织,提高心部的强韧性。
合金元素也会使氮的扩散受阻,减小渗氮层的厚度。
﹝二﹞离子渗氮工艺原理离子渗氮渗氮层的形成也是由分解、吸收、扩散三个基本过程组成的。
渗氮工艺及材料的选择

渗氮(nitriding)在低于钢铁材料临界点A c1基体不发生相变的前提下,将活性氮原子渗入制件表层的化学热处理工艺.以提高耐磨性、抗疲劳性能为目的的渗氮通常在500~570℃进行;以提高耐蚀性为目的的渗氮温度也不高于650℃。
本法的优点是表面改性显著,且处理前后尺寸变化小,能保持制件的精度。
除钢之外,球墨铸铁和钛合金制件亦可通过渗氮提高耐磨性和使用寿命。
分类应用最广泛的是气体渗氮,其次为离子渗氮,盐浴渗氮(不包括兼有渗碳作用的氮碳共渗)和固体渗氮用户极少。
气体渗氮常用的渗氮介质有氨、氨与氮、氨与氢、氨与预先在炉外分解的氨分解气的混合气。
氨在300℃以上即发生显著的分解,故上述各种气体都是氨、氮与氢的混合气。
混合气在钢件表面的催化作用下分解出活性氮原子,吸附并渗入钢件表层.介质的渗氮能力与氨分解程度有关。
图1示出氨分解率对38CrMoAlA钢渗氮处理(24h)后渗层深度和硬度的影响.气体掺氮常用设备为RJJ系列井式电炉.密封加热罐常用1Cr18Ni9Ti不锈钢制造。
此种密封罐的缺点是内壁对氨分解有触媒作用,使用过程中使氨分解率失去控制,影响渗氮质量.懈决这一问题的方法是在新罐使用前空载通入含硫气体(H2S或SO2),或滴注CS2,于500~600C保持2~4h,或在800~860℃空载保温2~4h,可使罐内壁的催化作用大幅度下降.采用搪瓷渗氮罐代替不锈钢罐已进入工业实用阶段,后者色完全消除了罐壁的催化作用.气体渗氮温度因钢种、渗层深度、硬度和性能指标的不同要求在480~650℃之间选择.大多数钢种的渗氮件在520~560℃处理,保温时间主要取决于要求的渗层深度.离子渗氮以钟罩式炉壳为阳极,欲渗零件为阴极,置于真空度为130~1300Pa的含氮气氛中,在电场作用下两极问激发辉光放电,并将气体电离产生氮离子,由电场加速向阴极迁移、轰击,使之加热到480~560℃渗氮温度,将吸附的氮渗入工件。
用作渗氮气氛的有氨、氮或氮与氢的混合气。
不锈钢气体渗氮过程中难点与解决方案
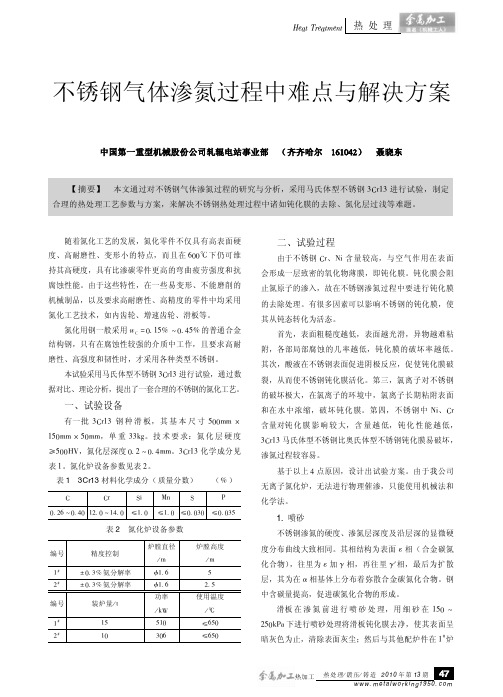
$& ()’ *+ 催渗
以上两种方法从试验结果分析,氮化效果不明显, 无法满足设计要求,而且在实际操作中难度较大。下面 我们采用卤化物催渗法。即在氮化过程中加入氟、氯等 化合物。卤化物能使工件表面活化,氮原子被工件表面 有效地吸附和吸收,促进渗入过程。我们采用卤化 物 ;(+ ,5 催渗( 国内称之为洁净渗氮法) ,在渗氮过程中 加入 ;(+ ,5,能分解出氯化氢或氯气,破坏工件表面的 氧化膜。分解出来的气体,化学性很强,当有微量水蒸 汽存在的条件下,它就能与几乎所有的金属和金属氧化
!& 酸洗
经过喷砂后总结,不锈钢去除钝化膜后,滞留时间 过久,会在空气中重新形成氧化膜,阻止了氮原子的渗 入。为解决此问题,我们在现场用 0%8 ( 体积) 盐酸 进行酸洗,将氧化膜破坏。由于需要配炉生产,酸洗后 迅速入炉执行图 # 工艺。检测结果如表 + 所示。
表 ’% 酸洗后氮化性能结果
材料 +$,-./ ’2,-./45 ’,-#’ 氮化后表面硬度 ()’ +7% 、0%0 29% 、22% ’70 、+#% 渗氮层深 " ** %1 +% 3 %1 +$ %1 +$ 3 %1 ++ %1 #% 3 %1 #0
一、试验设备
有一 批 #$%&# 钢 种 滑 板, 其 基 本 尺 寸 ,((00 1 &,(00 1 ,(00, 单 重 ##23。 技 术 要 求: 氮 化 层 硬 度 #,((45,氮化层深度 (+ 6 . (+ /00。#$%&# 化学成分见 表 & 。氮化炉设备参数见表 6 。
! 表 $! %&’$% 材料化学成分( 质量分数)
- 1、下载文档前请自行甄别文档内容的完整性,平台不提供额外的编辑、内容补充、找答案等附加服务。
- 2、"仅部分预览"的文档,不可在线预览部分如存在完整性等问题,可反馈申请退款(可完整预览的文档不适用该条件!)。
- 3、如文档侵犯您的权益,请联系客服反馈,我们会尽快为您处理(人工客服工作时间:9:00-18:30)。
加速渗氮的方法
摘要:从优化渗氮钢成分、在渗剂中添加催渗介质、优化渗氮工艺三个方面对加快渗氮的方法做了概括和归纳分析,并提出了几种快速渗氮新技术。
关键词:快速渗氮;工艺;分析
1 前言
渗氮不仅能提高零件的硬度、耐磨性和疲劳强度, 同时还使零件具有良好的红硬性、抗擦伤能力、变形小、尺寸稳定和工件表面呈压应力状态等优点。
但是它有生产周期长( 几十至上百小时)这一较大缺点。
因此, 热处理工作者一直在不断探索新方法, 以缩短渗氮生产周期。
近年来,热处理工作者在缩短渗氮周期方面开展了广泛的研究。
2 快速渗氮的研究思路
钢的渗氮过程和其他化学热处理过程一样,包括渗剂中活性氮的形成反应,渗剂中氮的扩一散,渗氮气氛/钢件相界面的反应,钢中氮的扩散及扩散过程中氮化物的形成等步骤。
提高渗氮速度主要是加速渗氮过程的一个或几个步骤。
为此可以从优化渗氮钢成分、在渗剂中添加催渗介质、优化渗氮工艺等方面进行。
3 优化渗氮钢成分
研究发现,金属氮化物的稳定性按如下顺序递增(以金属元素为主):Ni→Co→Fe→Mn→Cr→Mo→V →Nb→Ti→Zr。
Ti、V、Mo、Nb和Cr等合金元素能显著提高氮在α- Fe中的溶解度,起强化渗氮层的作用。
特别是Ti和V的效果最佳,它们可形成氮化物,改善氮沿渗层分布的均匀性,加速渗氮过程并提高渗层耐磨性。
因此,采用这些含形成稳定氮化物的合金元素的快速渗氮钢能成倍缩短工艺周期。
[1]
4 在渗剂中添加催渗介质
为了缩短渗氮的时间,我们在渗氮介质中添加一种或几种起催渗作用的物质,即催渗渗氮。
稀土催渗是催渗渗氮的有效方法之一。
其优点在于渗氮过程中稀土不仅加速氨的分解及[N]的渗入,同时稀土本身也渗入钢中,并使所形成的氮化物形态由片状变为高度弥散的球状,弥散的程度越高,渗氮层的硬度越高,并且硬而不脆。
这是因为常规渗氮的渗层中很容易产生脉状组织,氮化物容易沿晶界聚集,尽管渗层表面硬度提高,往往同时使脆性增大。
此外,正因为稀土渗氮较常规渗氮硬度高,渗氮温度也可以相应地提高,渗氮速度也自然随之提高了。
[2]
5 优化渗氮工艺
5.1 等温渗氮法、二段渗氮法、三段渗氮法、循环两段渗氮法[1]
等温渗氮是最初的渗氮方法,但此工艺时间过长、渗层浅,易产生脆性层。
因此发展了二段渗氮法、三段渗氮法来代替等温渗氮。
最近有人研究了一种循环两段渗氮新工艺,所谓“循环两段”渗氮是指进行2~4个周期较短的二段渗氮循环,这一新工艺已用于生产。
这种工艺渗氮初期采用较低的氨分解率和较低的渗氮温度,使零件表面氮含量提高,气氛与零件表面逐渐达到吸收与扩散的亚稳定平衡。
升高温度、加大氨分解率,目的是提高氮的扩散速度,强化氮在渗层中的扩散。
持续6 h后,零件表面氮含量降低。
此时渗层增长速度极小,不宜再延长保温时间,于是进入第2循环的第1段,即降低温度及氨分解率,恢复气氛的高氮势,并逐渐达到新的亚稳平衡。
随后又适时提高温度与氨分解率。
如此循环,就能充分利用强渗与扩散的高效率阶段。
5.2 预氧化多段变温快速渗氮[3]
预氧化多段变温快速渗氮工艺是在预氧化催渗和两段循环渗氮工艺基础上发展起来的。
渗氮速度主要取决于气氛的氮势、工件表面的吸氮能力和氮在工件内的扩散速度。
新工艺利用钢在570℃以下获得致密结构的氧化薄膜,在渗氮初期被还原,生成洁净的新生表面,呈现出很高的化学活性,产生大量能够吸附渗剂的活性位置,同时工件表面还可提供位错露头、台阶和各种表面缺陷的悬键,形成具有较低“势垒”的活性中心,使渗剂的被吸附几率和吸附量增加,促使其分子断键,在渗氮过程中起到了触媒的作用,从而使活性氮原子渗入过程加快。
5.3 离子渗氮
在全球,运用最广泛的这类处理是离子渗氮,它能大大缩短渗氮周期并能较充分地控制渗氮过程。
离子渗氮时,工件置于阴极盘上,炉壁为阳极,在阴阳极之间加以数百伏直流/ 脉冲偏压,炉内低压氮氢气体被电离,在电场的作用下以较大的能量轰击工件表面,产生大量的热量把工件加热到一定的温度,同时放电产生的活性氮在工件表面发生吸附、化合、扩散的物理化学反应,获得一定深度的改性层。
离子渗氮在批量处理形状简单的工件时是非常有效的,但其固有的缺点,如保持形状复杂工件处理时的温度均匀性,由于等离子体直接产生在工件上而引起的打弧、边缘效应、空心阴极效应、电场效应、温度测量和电源保护等,阻碍了离子渗氮技术的推广应用。
近年来出现了一些新的离子渗氮技术,如活性屏离子渗氮、等离子体源离子渗氮、离子注入离子渗氮等可以解决这一问题。
[4]
5.4 高温渗氮
以提高表面硬度和强度为目的的常规气体渗氮工艺温度一般在520℃左右,高温渗氮是指采用更高的工艺温度(一般在540~580℃),在相同的氨分解率下,提高钢件表面的吸氮能力和氮原子在γ′相和γ相中的扩散速度,大幅缩短渗氮时间,提高渗氮效率。
[5]
5.5 一些渗氮新工艺[6]
a、电接触加热渗氮
电接触加热渗氮是直接向工件通电加热,可使工件迅速达到渗氮温度,周围氨的温度仍低于分解温度,只有氨与工件表面接触时才能分解产生活性氮原子,这就减少了氨的分解,减轻了氨分解气体的阻碍作用,使活性氮原子保持高浓度和迅速被金属吸收并向内扩散。
渗氮工艺时间可缩短到一般炉内渗氮的1/5~1/8。
b、在磁场中渗氮
在磁场中渗氮也可加速渗氮过程,实验表明,在电磁强度为(25~30)×(1000/4π)A/m工频激磁磁场中进行渗氮,比一般纯氨氮化快2~3倍,且可有效地消除钢的脆性,显著提高其疲劳强度和耐磨性,磁场加速氮的原理,被认为是磁场作用,使钢的组织变得具有一定方向性,加速氮在钢中的扩散。
c、高频渗氮
高频渗氮兼有上述两种渗氮方法的优点,而且,工件在高频磁场中还产生磁致伸缩效应,有利于进一步促进氮原子的扩散。
这种工艺比较成熟,已成功地应用于小型零件的生产。
通常以石英管作渗氮容器,外绕感应圈,渗氮温度通常在500~550℃范围,温度再高,工件硬度下降,氮化时间一般为0.5~3h,继续延长时间,渗层增厚并不明显。
此外还有超声波渗氮、表面预变形渗氮、表面纳米化预处理、激光表面氮化渗氮、微波等离子体渗氮、离子注入渗氮等方法均能有效提高渗氮速度。
[7]
参考文献
[1] 高美兰, 白树全. 渗氮技术的现状及发展方向[J]. 《新技术新工艺》·热加工工艺技术与材料研究, 2011, (4): 68-68
[2] 田君, 张奇志, 高军. 催渗技术提高渗氮效率[J]. 热处理, 2011, 26(4): 81-82[3] 危丽琼. 硅烷技术带来涂装工艺突破
[J]. 中国化工报-涂料工业, 2007, 12(25): 007.
[3] 代立新, 马占坡, 王焕琴. 预氧化快速气体渗氮新工艺[J]. 金属热处理, 1997, (9): 30-31
[4] 龙发进, 周, 祎. 离子渗氮新技术的研究现状[J]. 热加工工艺, 2007, 36(6): 61-64
[5] 陈贺, 叶小飞, 刘臻. 快速气体渗氮工艺:高温渗氮和稀土催渗[J]. 金属加工, 2012, (7): 9-10
[6] 闫洪. 钢的渗氮新技术[J]. 四川冶金, 1999, (6): 37-38
[7] 陈玮, 王蕾, 周磊, 王君. 钢的快速渗氮技术研究现状[J]. 武汉科技大学学报(自然科学版) , 2006, 29(3): 227-228
[8] 胡月娣, 赵增爵, 沈介国. 离子渗氮技术及其应用[J]. 热处理, 2009, 24(1): 53-56
[9] 陈方生, 刘玉先. 稀土催渗离子渗氮机理的研究[J]. 金属热处理, 1999, (2): 7-9
[10] 谢飞, 马宝钿, 何家文. 钢的快速深层渗氮研究进展[J]. 材料导报, 1998, 12(5): 19-22。