塑料模具成型第十章 压模
注塑模具压模技术

模具压模技术在没有做模具保护的情况下,模具被压、撞坏可能会出现下列问题:1、模具因结构较简单,压不坏。
2、模具被压,致使模具精密度下降,使注塑成形条件发生变化,给工艺参数的调试加大难度。
.3、模具被压,致使模具精密度下降,使成形产品的毛边加大、加多,加大了生产工人的工作强度与工作量,加速工人工作的疲劳,产品的产量、质量、效率往下降。
员工对工作的好感下降,员工流动可能会因此而有少许加大。
4、模具被压,致使模具精密度下降,使成形产品的毛边加大、加多。
原定的人员已经无法满足工作对劳动力的需要,需要增加人手,使劳动力密集的注塑行业,劳动力更加密集,增加人工支出,提高了产品生产制造成本。
5、模具被压、撞,致使模具受损害至无法生产的程度,耽误生产,需要时间与费用将模具进行维修。
6、模具型腔面被撞兼压伤,不管如何修补,也无法躲避留下一个补痕,在成形产品上留下一个印记,对于组合成品起来属于在直视面的塑料件的,- -个光滑的产品表面有一个修过的痕迹,这就是一个瑕疵,产品质量与档次将因此受影响。
7、模具被压、撞坏。
对坏模具进行烧焊、驳接、修修补补。
模具的质量与性能加速下降,坏模的发生率,上升,增加模具的运作维护的成本支出。
随着修多、补多以及精密度的逐步下降,模具使用的寿命最终会因在工作中没有得到好好地保护,而受到工作中意外撞压地的推残,最终寿命因此而缩短。
综上所述,这些都对质量、产量、成本、效率、造成不少影响的东西,我们是不是应该为避免其发生而作努力呢?!.在注塑成型过程中对模具保护是一个保证正常生产、产品质量等的重要技术手段。
注塑机模具保护方法主要有以下几种。
1)选择合适的材料或在模具表面喷涂特殊材料。
模具表面经常直接接触到高温胶料的冲击及磨损,长期处于冷热交变的环境下因此对于材料的选择尤为重要。
为了满足工况要求和保证塑料制品成型质量,塑料注塑模具的材料需要满足一定的力学性能和加工工艺性能的要求:①具有可加工性和易抛光性;②优良的耐蚀性和耐磨性;③良好的塑性、韧性匹配;④优良的高温性能;⑤优良的化学性能。
压模要求及培训

成型培训内容一、工艺流程:胶块回温洗模模具上料塑封成型成型烘烤二、各工序操作注意事项:2-1.胶块回温:2-1-1.回温地点的选取:温度:18-35℃,湿度:<70%RH2-1-2.胶块自领出开始必须40小时内使用完毕(含回温时间).2-1-3.室温(回温区)温度在18℃-28℃时,回温16小时以上方可使用。
在28℃以上至35℃时,回温12小时后方可使用. 2-1-4.回温说明:2-1-4-1.室温×16小时以上(25℃左右)2-1-4-2.维持塑胶袋于密封状态:黑胶从冷库处取出温度较低,空气中的水分易附着于温度较低的黑胶上,导致黑胶吸附,影响黑胶的正常使用.2-1-4-3.回温后在24小时内完成2-1-4-4.未用完材料在储存时,将塑胶袋封紧,当材料再次使用时,于室温回温后24小时每必须用完. 避免放置与潮湿环境或阳光直射的地方.2-2.洗模:2-2-1.清洗后模具要干净保证生产时材料质量要求2-2-2.不允许有洗模残渣留于上下模2-2-3.新更换的模具必须用三氯乙烷洗模后使用,使用着的模具每星期必须用三氯乙烷洗模洗一次2-2-4.使用说明:2-2-4-1.洗模剂是一种极易吸潮的物质,吸潮后影响作业性及清洗效果,故开封后,请尽快使用完毕后重新包装好,避免吸潮.2-2-4-2.洗模剂为热硬化性树脂,在高温下影响流动性及清洗效果,预热温度为90-110℃。
2-2-4-3.合适成型条件为:模温175℃,成型时间3-5分钟。
转进压力30-100kgf/cm2,硬化时间适当延长,清洗效果更加.2-2-4-3.洗模剂应存放在清凉干燥、温度不超过30℃之处可保存6个月,10℃以下可保存1年 . 2-3.模具上料:2-3-1.材料上料全部到位,无弯料、断料、混料、上胶不良、空缺、多余材料 2-3-2. CRC涂抹均匀,适量2-3-3. 非酸洗上胶材料严禁摆料,必须用梳条将材料梳到料盘上2-3-4. 空缺处材料填补必须用镊子,严禁裸手补料2-3-5. SKY、GPP、TVS、ZNR等非酸洗类材料由模具上料工序开模,每次开模不能超过5船,防止材料受到污染及碰弯 2-4.塑封成型:2-4-1.除所配定的清模工具外,禁止用任何硬物清模料盘 2-4-2.左右摇晃时,先取下来检查模具是否清好2-4-3.生产线只能使用按工艺回温好的胶块,并优先使用回温早的胶块2-4-4.胶块不得放在成型机台上,必须放在附近的小凳上,已免胶块提前固化变质2-4-5.成型使用的胶块必须放在双层塑料袋中,未使用的胶块及时封好2-4-6.交接班时,卫生清理及洗模完毕,才能把上胶烘烤后的材料(含非酸洗类材料)拉到成型车间进行成型2-4-7.塑封成型之材料要在其“生产流程卡”上注明胶块类型及成型开始和成型完毕时间2-4-8.操作员必须戴手套,前三模做好自检,保证异常情况早发现。
塑料成型工艺与磨具设计课后习题答案

第一章答案1.高分子聚合物链结构有哪些特点?根据链结构的不同,高分子聚合物可以分成哪几类?答:高分子聚合物链结构具有以下结构特点(1)高分子呈现链式结构(2)高分子链具有柔性(3)高聚物的多分散性根据链结构的不同,高分子聚合物可以分为高分子近程结构和高分子远程结构。
2.根据聚集态结构的不同,高分子聚合物可以分成哪几类?试阐述其结构特点和性能特点。
答:根据聚集态结构的不同,高分子聚合物可以分成固体和液体,固体又有晶态和非晶态之分。
(1)聚集态结构的复杂性因为高分子链依靠分子内和分子间的范德华力相互作用堆积在一起,可导致晶态和非晶态结构。
高聚物的比小分子物质的晶态有程序差得多,但高聚物的非晶态结构却比小分子物质液态的有序程度高。
高分子链具有特征的堆方式,分子链的空间形状可以是卷曲的、折叠的和伸直的,还可能形成某种螺旋结构。
如果高分子链由两种以上的不同化学结构的单体组成,则化学结构是决定高分子链段由于相容性的不同,可能形成多种多样的微相结构。
复杂的凝聚态结构是决定高分子材料使用性能的直接因素。
(2)具有交联网络结构某些种类的高分子链能够以化学键相互连接形成高分子网状结构,这种结构是橡胶弹性体和热固性塑料所特有的。
这种高聚物不能被溶剂溶解,也不能通过加热使其熔融。
交联对此类材料的力学性能有重要影。
高聚物长来链大分子堆砌在一起可能导致链的缠结,勾结点可看成为可移的交链点。
3.在线型非晶态(无定形)聚合物的热力学曲线上,可以分为哪三种力学状态的区域?温度点0b、0g、0f、0d表征什么意义?答:在线型非晶体态(无定形)聚合物的热力学曲线上,可以分为玻璃态、高弹态、粘流态。
0b称为脆化温度,它是塑料使用的下限温度。
0g称为玻璃化温度,玻璃态和高弹态之间的转变称为玻璃化转变,对应的转变温度即玻璃态温度。
0f称为粘流温度,高弹态与粘流态之间的转变温度称为粘流温度。
0d称为热分解温度,它是塑料使用的上限温度。
4.绝大多数的聚合物熔体都表现为非牛顿流体,试写出非牛顿流体的指数流动规律,并表述其意义。
模具设计与制造(压缩模)

3.4 压缩模设计压缩成型模具简称压缩模、压模,又称压制模,是塑料压缩成型所采用的模具,主要用于热固性塑料的成型。
其基本成型过程是将塑料粉料或粒料直接加在敞开的模具加料室内,再将模具闭合,通过加热、加压使塑料呈流动状态并充满型腔,然后由于化学或物理变化使塑料固化(或硬化)定型。
压缩成型的特点是塑料直接加入型腔内,压机压力通过凸模直接传递给塑料,模具是在塑料最终成型时才完成闭合。
其优点是无需设置浇注系统,耗料少,使用的设备和模具都比较简单,适用于流动性差的塑料,宜成型大型塑件,塑料的收缩率小,变形小,各向异性比较均匀;其缺点是生产周期长,效率低,不易压制形状复杂、壁厚相差较大、尺寸精度高且带有精细或易碎嵌件的塑件。
3.4.1 压缩模的结构组成及分类1.压缩模的结构组成压缩模的典型结构如图3-96所示。
模具的上模和下模分别安装在压力机的上、下工作台上,上、下模通过导柱导套导向定位。
上工作台下降,使上凸模3进入下模加料室4与装入的塑料接触并对其加热。
当塑料成为熔融状态后,上工作台继续下降,熔料在受热受压的作用下充满型腔。
塑件固化(或硬化)成型后,上工作台上升,模具分型,同时压机下面的辅助液压缸开始工作,脱模机构将塑件脱出。
压缩模按各零部件的功能作用可分为以下几大部分。
(1)成型零件成型零件是直接成型塑件的零件,加料时与加料室一同起装料的作用,模具闭合时形成所要求的型腔。
图3-96中模具型腔由上凸模3、凹模4、型芯8、下凸模9等构成。
(2)加料室图3-96中凹模4的上半部,为凹模截面尺寸扩大的部分。
由于塑料与塑件相比具有较大的比容,塑件成型前单靠型腔往往无法容纳全部原料,因此一般需要在型腔之上设有一段加料腔室。
(3)导向机构导向机构的作用是保证上模和下模两大部分或模具内部其他零部件之间准确对合。
图3-96中,由布置在模具上周边的四根导柱6和导套10组成导向机构,为保证推出机构上下运动平稳,该模具在下模座板15上设有两根推板导柱,在推板上还设有推板导套。
模压成型工艺—模压成型操作(塑料成型加工课件)

热固性塑料在一定的合模压力和模具温度下保 持一段时间,达到一定的交联程度。
在加热加压的状态下,物料快速发生化学交联 反应,交联程度快速提高,树脂分子链由线性结构 变成三维网路结构,物料固化,物理机械性能提高。 有时候,为了提高生产效率,在制品能够不变形脱 模时就暂时结束热压固化过程,然后再通过后处理 完成固化的后期过程。
首先,要检查模具是否有油污、碎屑或异物, 并清理干净,如果需要可适当喷涂脱模剂。然后, 向模具型腔加入物料,尽可能放在模具型腔的中间, 流动阻力大的部位应多放一些料。加料量直接影响 制品的密度和尺寸,加料量过多制品易产生飞边, 厚度尺寸不精确;加料量过少则预压,使树脂充满整个型腔。 在预压过程中应让模具缓慢合紧,使树脂有足 够的时间在模腔内流动,并且避免树脂因合模过快 被空气带出,使制品造成破坏。
模压成型
模压工艺操作
一、模压工艺流程
热固性塑料模压成型的工艺过程包括加料、预压、 排气、固化和脱模等。
二、操作过程
1.开机预热
先接通电源,然后启动模压机开关。将模具放 到加热板上,点击“主缸上”合模;通过控制面板 设置加热板温度,打开加热热开关启动加热,当温 度达到设置值后再恒温一段时间。
2.加料
4.排气
通过适当的卸压松模排除气体,该过程可和预 压配合进行。
热固性塑料在模压时发生化学交联反应,常伴 有水蒸汽和小分子挥发物放出,因此需要短暂的时 间打开模具,使水蒸汽、小分子挥发物和空气排除, 避免对制品造成缺陷影响。排气完成后,应在物料 还处于良好流动状态时迅速闭模,对物料加热加压。
5.固化
6.脱模
固化后让制品和模具分离。脱模速度不能过 快,否则制品容易变形,而速度过慢则会影响生 产效率。当制品脱模后,要认真清理模具,用铜 制工具取出模具上的杂志和附着物,为下一个制 品的生产做准备。
模具设计与制造专业毕业论文--瓶盖注塑模具设计
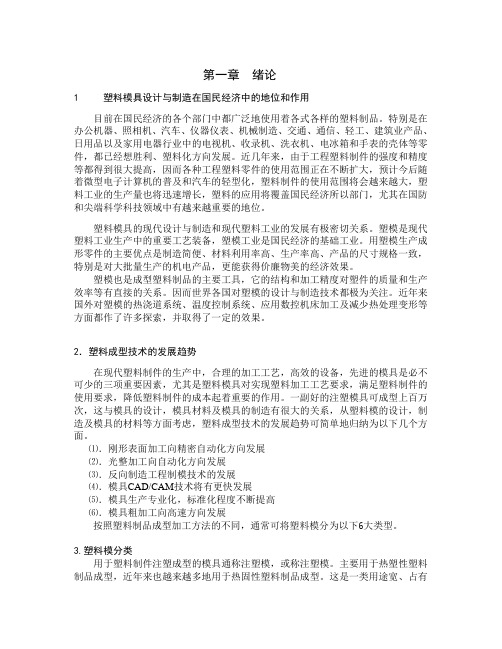
第一章绪论1塑料模具设计与制造在国民经济中的地位和作用目前在国民经济的各个部门中都广泛地使用着各式各样的塑料制品。
特别是在办公机器、照相机、汽车、仪器仪表、机械制造、交通、通信、轻工、建筑业产品、日用品以及家用电器行业中的电视机、收录机、洗衣机、电冰箱和手表的壳体等零件,都已经想胜利、塑料化方向发展。
近几年来,由于工程塑料制件的强度和精度等都得到很大提高,因而各种工程塑料零件的使用范围正在不断扩大,预计今后随着微型电子计算机的普及和汽车的轻型化,塑料制件的使用范围将会越来越大,塑料工业的生产量也将迅速增长,塑料的应用将覆盖国民经济所以部门,尤其在国防和尖端科学科技领域中有越来越重要的地位。
塑料模具的现代设计与制造和现代塑料工业的发展有极密切关系。
塑模是现代塑料工业生产中的重要工艺装备,塑模工业是国民经济的基础工业。
用塑模生产成形零件的主要优点是制造简便、材料利用率高、生产率高、产品的尺寸规格一致,特别是对大批量生产的机电产品,更能获得价廉物美的经济效果。
塑模也是成型塑料制品的主要工具,它的结构和加工精度对塑件的质量和生产效率等有直接的关系。
因而世界各国对塑模的设计与制造技术都极为关注。
近年来国外对塑模的热浇道系统、温度控制系统、应用数控机床加工及减少热处理变形等方面都作了许多探索,并取得了一定的效果。
2.塑料成型技术的发展趋势在现代塑料制件的生产中,合理的加工工艺,高效的设备,先进的模具是必不可少的三项重要因素,尤其是塑料模具对实现塑料加工工艺要求,满足塑料制件的使用要求,降低塑料制件的成本起着重要的作用。
一副好的注塑模具可成型上百万次,这与模具的设计,模具材料及模具的制造有很大的关系,从塑料模的设计,制造及模具的材料等方面考虑,塑料成型技术的发展趋势可简单地归纳为以下几个方面。
⑴.刚形表面加工向精密自动化方向发展⑵.光整加工向自动化方向发展⑶.反向制造工程制模技术的发展⑷.模具CAD/CAM技术将有更快发展⑸.模具生产专业化,标准化程度不断提高⑹.模具粗加工向高速方向发展按照塑料制品成型加工方法的不同,通常可将塑料模分为以下6大类型。
塑料模具课件-压制成型

管材挤出成型机头工艺参数的确定
管材挤出成型机头的工艺参数主要确定口模、芯棒、分
流器和分流器支架的形状和尺寸,
一、口模
口模是成型管材表面的零件,形状如图 5-5 所 示,管材离开口模后,由于压力降低,塑料出现因弹性变
4.2压制模具分类
压制模具的分类方法很多,可按模具在压机上固定 方式分类:可按上下模闭合形式分类,按分型面特征 分类,按型腔数目分类以及按制品顶出方式分类等。 本书按压制模具的上下模配合结构特征进行分类。 1.溢式压模如图 4-2 2.不溢式压模如图 4-3 3.半溢式压模 4-4 4.带加料板的压模 4-7 5.半不溢式压模 4-5 6.多型腔压模如图 4-6 4-8 压铸模具的典型结构如图 4-9
移动式压缩模脱模机构——撬棒
移动式压缩模脱模机构——撞击 架脱模
移动式压缩模脱模机构——卸模架脱模
5.热塑性塑料挤出成型机头
5.1挤出成型机头概述 塑料挤出成型是用加热或其它方法使塑料成为流动
状态,然后在一定压力作用下使它通过塑料模具而制 得连续得型材。挤出法几乎可加工所有得热塑性塑料 和部分热固性塑料。挤出加工的制品种类很多如管材、 薄膜、棒材、板材、电缆包层,单丝以及其它型材等。 挤出成型在塑料成型加工工业中占有重要地位。
压制模具结构
典型的压制模具结构如图 4-1 所示,它可分为装于压机 上模板的上模和装于下模板的下模两大部件。上下模闭合使 装于加料室和型腔中的塑料受热受压,成为熔融态充满整个 型腔,当制件固化成型后,上下模打开利用顶出装置顶出制 件,压制模具可进一步分为以下几大部分: 1.型腔 2.加料室 3.导向机构 4.侧向分型抽芯机构 5.脱模机构 6.加热系统
知识点十 模压、烧结成型

生产过程复杂,实际生产中一般不进行预压。
高分子材料专业 高分子成型加工技术Ⅰ(塑料)
三、工艺
1.模压前的准备
③对压塑粉的要求:
颗粒最好大小相间 压缩率(塑料/锭料)宜为3.0左右
含有润滑剂
④预压条件: 温度:室温或50~90℃预压 压力:压力范围40~200MPa 原则:锭料的密度达到塑件最大密度的80%
高分子材料专业 高分子成型加工技术Ⅰ(塑料)
三、工艺
2.模压过程
⑵ 合模
加料后即可合模,合模时间一般从几秒到几十秒不等。 合模过程分为两个部分:
①凸模触及塑料之前:尽量加快合模速度(缩短周期, 避免塑料过早固化) ②凸模触及塑料之后:减慢合模速度(利于排气)
高分子材料专业 高分子成型加工技术Ⅰ(塑料)
一模多腔
高分子材料专业 高分子成型加工技术Ⅰ(塑料)
二、模压设备
1.模压设备作用
合模 开模 顶件
提供所需的压力
某些情况下也传递压缩过程中所需的热量
2.模压设备的种类
机械式压机:螺旋式压力机
按传动方式分
液压机:水压机和油压机
高分子材料专业 高分子成型加工技术Ⅰ(塑料)
二、模压设备
2.模压设备的种类
五、容易产生废品的类型、原因及其处理方法
• 制品必须通过检验方可认为成品。检验项目的多少须看 对成品性能的要求而定,其类型大体可分为: • (1)外观质量; • (2)内应力的有无; • (3)尺寸和相对位置的准确比;
• (4)与成品有关的物理机械性能、电性能和化学性能等。
高分子材料专业 高分子成型加工技术Ⅰ(塑料)
四、工艺条件
2.成型温度
成型温度 —— 指压缩时所需的模具温度,对塑件质量、 模压时间影响很大
压缩模与压注模
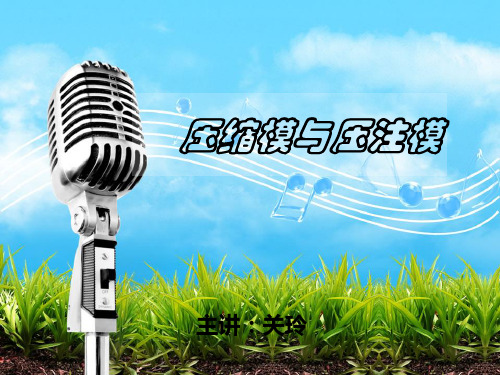
• 把预热的原料加到加料腔内,塑料经过
加热塑化,在压力机柱塞的压力下经过模 具的浇注系统挤入型腔,型腔内的塑料 在 一定压力和温度下保持一定时间充分固化, 得到所需的塑件。在挤塑的时候加料腔的 底部必须留有一定厚度的塑料垫,以供压 力传递。 • 熔料经过浇注系统才进入型腔,会有一 定的压力损失;而熔料经过浇注系统时, 会产生摩擦热,从而使塑料的流动性增大, 有利于填充型腔,又有利于提高塑料的固 化速度。
压缩模结构及分类
一、压缩模具的 结构组成
1、组成
型腔 加料室 导向机构 侧向分型抽芯机构推
出机构 加热系统 排气系统
压缩模结构及分类
2、压缩模的分类
按模具加料室的形式分
溢式压缩模 不溢式压缩模 半溢式压缩模
按模具在压机上的固定方式分: 固定式压缩模 移动式压缩模 半固定式压缩模
热固性塑料的压缩、压注、注射成型各有其优缺点及其
适用范围,现比较如下:
(1)就成型效率来看,以注射成型为高,压注成型次之,压缩成型较低。 (2)就塑件质量来看,由于注射和压注成型能使塑料受到均匀地加热,故
而获得的制品在其整个断面上固化程度比较均匀,有较良的电气性能和 较高的机械强度。 (3)注射和压注成型时,塑料注入闭合的型腔内,因此制品在分型面处产 生的飞边很薄,容易修除,或无飞边,塑件高度能达到较高的尺寸精度, 而压缩成型则不能。 (4)注射和压注成型可用于成型带有精细孔、细小嵌件的塑件,而压缩成 型则不能。 (5)注射成型比压缩、压注成型都更容易实现机械化和自动化,工人劳动 强度可得到大大地改善。 (6)压缩模适用于流动性较好的塑料和形状较复杂的带小嵌件的塑件。
三、压注模的典型结构
1、组成
塑料模具课件-压制模具图

图5-2 直管机头
1-芯棒 2-导柱 33-调节螺钉 4-加热器 5-分流器 6-机头体 7、9-温度计插孔 8-空气
图5-3 弯机头
1-接管 2-机头体 3、9-温度计插孔 4-芯棒加热器 5-芯棒 6、
图5-4 旁侧机头
1、12-温度计插孔 2-口模 3-芯棒 4、7-加热器 5-调节螺钉 6-机 头体 8-熔融塑料测温孔 9-机头 10-高温计插孔 11-芯棒加热器
图5-18口模内外圈都能旋转的机头
图5-19 挤压式包覆机头
1-包覆制品 2-电热圈 3-调节螺钉 4-机头体 5-导向棒
图5-20口模处放大图
1-芯线 2-口模 3-导向棒
图5-21套管式包覆机头
1-螺旋面 2-芯线 3-挤出机 4-多孔板 5-电热圈 6-口模
图5-224-4半溢式压模
图4-5半不溢式压模
图4-6多腔模加料板
1-滑块 2-定位块
图4-7带加料板压模
图4-8多腔压制模
具结 构
图4-9压铸模具
1-加料室 2-压柱 3-浇口套 4-拉杆 5-加热元件 6-锁钩 7-螺栓杆 8-顶板
图5-1管材挤出机头
1-口模 2-芯棒 3-分流器 4-分流器支架 5-多孔板
机头内部空腔 大,存料多,不易 加工PVC
图5-12旋转式机头
优点: 出料均匀,厚
度易于控制 缺点:
结构复杂,拐 角多,适于PE、 PP。不适于PVC
图5-13双层吹塑薄膜机头
图5-14内结合双层吹膜机头
图5-15外结合双层吹膜机头
图5-16三层吹膜机头
图5-17三层吹膜机头
1-调节组件 2-料流环槽
图5-5口模
图5-6分流器、分流器支架与芯
注塑模具“压模”的原因和预防措施

注塑模具“压模”的原因和预防措施在注塑机生产的过程中,模具合模时如果模腔中存在异物,没有及时取出,而导致的二次合模压坏模具或者挤伤模具,这种现象称之为“压模”。
在工厂中,模具就是我们吃饭的饭碗,因压模需要很长的时间维修模具而停止生产,从而会导致生产计划延误,不能按时交货。
修理后的模具,故障频频出现,无法达到之前的生产状态,是注塑加工行业中最不愿意看到的事情,其重要程度不言而喻。
所以工厂不仅仅会制定一套防止注塑压模的预防措施,也会制定一套模具压坏的奖罚考核制度。
一、注塑模具压伤的主要原因1、当注塑机使用半自动拉门生产,开模顶出产品后,由于员工操作失误和注意力不集中;在取出产品的时候(产品拔模角度不够而黏前模),没有将产品和水口全部取出来,粘在模具型腔中,二次合模压坏模具。
(操作方面)2、注塑机全自动生产的时候,机械手在使用吸盘取出产品的过程,吸取信号短接,没有将产品全部取出;在使用机械手夹取(抱取)水口,还留有一部分在模具型腔中或者掉落在导柱上。
(操作方面)3、根据产品设计要求,需要嵌入金属镶件,在安装镶件的过程中员工操作失误,没有将镶件按照要求摆正;注塑机在合模的时候震动导致位移或者重复安装两个镶件,而导致压伤模具。
(操作方面)4、在注塑机调试工艺的过程中,参数设置错误或者(操作步骤)按键错误。
应使用半自动生产操作时,却错误使用全自动生产;机械手在没有运行的情况下使用全自动生产;产品在还没有充满(缺胶)的情况下,人员离开机台,导致产品压伤模具。
(操作方面)5、模具长时间使用,没有下机对其进行维修保养。
模具运动部件缺少润滑油,顶针和滑块“烧死”和断裂;顶针和滑块未复位,在模具合模的时候撞上前模。
(模具方面)6、注塑机在使用全自动定(多)次顶出产品时,因为顶针前后惯性作用,又将产品带回动模,没有将产品离型掉落至模具外。
(模具方面)7、对于大中型汽车模具,滑块部位都单独设计一组冷却水路。
在模具装模接水的时候,使滑块发生位移;在模具需要抛光的时候滑块发生位移,在生产的时候没有将滑块拉至指定位置,合模时导致导柱断裂。
挤压模具工作原理

挤压模具工作原理
挤压模具是一种常见的塑料加工设备,主要用于将熔融的塑料材料通过挤出机挤压成特定形状的产品。
挤压模具的工作原理可以简述为以下几个步骤:
1. 原料进料:将塑料颗粒或粉末料通过料斗等设备输送到挤出机中,同时加热使其熔化成熔融状态。
2. 挤出机挤压:熔融的塑料被挤出机内的螺杆推进,同时受到螺杆回转和螺杆筒的加热作用,使其形成连续的熔融塑料流。
3. 模具挤压:挤出机的熔融塑料流经过挤压模具,通过模具的流道和出口,塑料受到模具的约束和形状限制,逐渐冷却固化成为产品的形状。
4. 切割和收集:经过模具挤压后,形成的连续的塑料制品通过切割装置进行切断,然后通过传送带或收集装置进行收集或包装。
在挤压模具的工作过程中,模具的设计和制造对最终产品的质量和外观有着重要的影响。
模具内部的流道和出口形状决定了产品的横截面形状,模具的材料和加工精度也会影响产品的表面质量和尺寸精度。
因此,在挤压生产中,通常需要根据产品的要求设计和制造适合的模具,以获得理想的成品。
总结起来,挤压模具是通过挤出机将熔融的塑料材料挤出,并通过模具的约束和形状限制,使其冷却固化成为特定形状的产
品。
模具的设计和制造对产品质量具有重要影响,需要根据产品要求来选择合适的模具。
压模具原理

压模具原理压模具是一种用于加工成型金属材料的工具,它通过对金属材料施加一定的压力,使其产生塑性变形,从而得到所需的形状和尺寸。
压模具在工业生产中起着至关重要的作用,它不仅可以提高生产效率,还可以保证产品的质量和精度。
本文将介绍压模具的原理及其相关知识。
首先,压模具的原理是基于金属材料的塑性变形特性。
当金属材料受到外力作用时,其内部分子结构会发生变化,从而产生塑性变形。
而压模具正是利用这一原理,通过对金属材料施加压力,使其产生塑性变形,从而得到所需的形状和尺寸。
在压模具加工过程中,金属材料会在模具的作用下发生流动,经过一系列的变形和成形,最终得到成型零件。
其次,压模具的原理还涉及到金属材料的应力和应变关系。
在压模具加工过程中,金属材料受到的压力会引起其内部产生应力,从而使其产生应变。
这种应力和应变的作用下,金属材料会产生塑性变形,从而得到所需的形状和尺寸。
因此,在设计和制造压模具时,需要充分考虑金属材料的力学性能,以确保加工过程中金属材料能够得到合理的塑性变形,从而得到高质量的成型零件。
此外,压模具的原理还涉及到模具的结构和工作原理。
模具通常由上模和下模组成,上模和下模之间通过导柱和导套进行定位,同时通过压紧装置进行固定。
在压模过程中,上模和下模会对金属材料施加一定的压力,使其产生塑性变形。
同时,模具还会通过一系列的动作,如顶出、退料、喷气等,来完成成型零件的脱模和后续处理。
综上所述,压模具是利用金属材料的塑性变形特性,通过对金属材料施加一定的压力,使其产生塑性变形,从而得到所需的形状和尺寸。
在压模具加工过程中,需要充分考虑金属材料的力学性能,同时合理设计和制造模具结构,以确保得到高质量的成型零件。
压模具在工业生产中具有重要的应用价值,它不仅可以提高生产效率,还可以保证产品的质量和精度,因此在现代制造业中得到了广泛的应用。
塑料模具成型第十章 压模

第十章塑料压塑成型模具第一节概述第二节压模成型零件设计原则一、压制成型及压制模结构特点压制成型是高分子材料成型加工技术中历史最悠久,也是最为重要的一种工艺。
几乎所有的高分子材料都可用此方法来成型制品。
考虑到生产效率、制品尺寸、产品使用的特点,目前主要用于:热固性塑料、橡胶制品、复合材料的成型。
热固性塑料的模压成型将压塑料置于金属模具中的型腔内,然后闭模在加热加压的情况下,使塑料熔融、流动,充满型腔,经适当的放气、保压后,塑料就充分交联固化为制品。
因为热固性塑料经交联固化后,其分子结果变形三维交联的体型结构,所以制品可以趁热脱模。
工艺特点:成型工艺及设备成熟,是较老的成型工艺,设备和模具比注射简单。
间歇,生产周期长,生产效率低,劳动强度大,难自动化。
制品质量好,不会产生内应力或分子取向。
能压制较大面积制品,但不能压制形状复杂及厚度较大的制品。
制品成型后,可趁热脱模。
热塑性塑料:受热后软化,冷却后变硬,这种软化和变硬可以重复循环,所以可以反复成型。
70%PVC、PE、PP热固性塑料:由单体直接形成网状聚合物或通过交联线型预聚体而形成,一旦形成交联聚合物,受热后不能再回到可塑状态。
所以热固性塑料来说,聚合过程和成型过程是同时进行的,所得制品是不溶不熔的。
压制成型:又叫压塑成型,成型方法是将粉状或纤维状等塑料放入成型温度下的模具型腔中,后闭模加压而使其成型并固化的作业。
压模可以兼用于热固性塑料和热塑性塑料。
模压热固性塑料时,塑料一直处于高温,置于型腔中的热固性塑料在压力的作用下,先由固体变为半液体,并在这种状态下流满型腔而取得型腔所赋予的形状;随交联反应的深化,半液体的粘度逐渐增加以至变为固体,最后脱模成为制品。
热塑性塑料的模压,在前一阶段的情况与热固性塑料相同,但是由于没有交联反应,所以在流满型腔后,将模具冷却使其固化才能脱模成为制品。
由于热塑性塑料模压时,模具需要交替的加热和冷却,生产周期长,所以热塑性塑料制品的成型用注射成型等方法更为经济,只有在模压较大平面的塑料制品时,才采用模压成型,如透明板材等。
压缩模与压注模
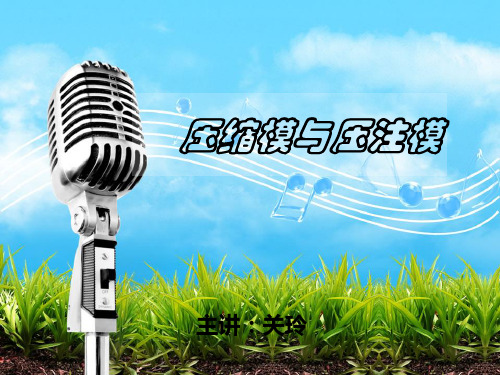
• 把预热的原料加到加料腔内,塑料经过
加热塑化,在压力机柱塞的压力下经过模 具的浇注系统挤入型腔,型腔内的塑料 在 一定压力和温度下保持一定时间充分固化, 得到所需的塑件。在挤塑的时候加料腔的 底部必须留有一定厚度的塑料垫,以供压 力传递。 • 熔料经过浇注系统才进入型腔,会有一 定的压力损失;而熔料经过浇注系统时, 会产生摩擦热,从而使塑料的流动性增大, 有利于填充型腔,又有利于提高塑料的固 化速度。
三、压注模的典型结构
1、组成
型腔 加料室 浇注系统 导向机构 侧分型与抽芯机构 脱模机构 加热系统
压注模结构及分类
定式
上加料室柱塞式压注模 柱塞式压注模
下加料室柱塞式压注模
压注模结构及分类
1)罐式压注模
压注模结构及分类
2)柱塞式压注模
压注模结构及分类
柱塞式压注模
适用范围:
小批量或试制、低精度和强度无严格要求的的扁 平塑件。
压缩模结构及分类
2)不溢式压缩模
结构特点:
❖ 加料腔是型腔上侧的延续部分 ❖ 无挤压面 ❖ 凸模与加料腔有小间隙的配合
优点:
❖ 塑件密度大、质量高 ❖ 对塑料要求不严(以棉布、玻璃 布或长纤维填料的塑料均可) ❖ 塑件飞边薄且呈垂直状易于去除
压缩模结构及分类
一、压缩模具的 结构组成
1、组成
型腔 加料室 导向机构 侧向分型抽芯机构推
出机构 加热系统 排气系统
压缩模结构及分类
2、压缩模的分类
按模具加料室的形式分
溢式压缩模 不溢式压缩模 半溢式压缩模
按模具在压机上的固定方式分: 固定式压缩模 移动式压缩模 半固定式压缩模
根据成型型腔数分类: 单型腔压缩模 多型腔压缩模
- 1、下载文档前请自行甄别文档内容的完整性,平台不提供额外的编辑、内容补充、找答案等附加服务。
- 2、"仅部分预览"的文档,不可在线预览部分如存在完整性等问题,可反馈申请退款(可完整预览的文档不适用该条件!)。
- 3、如文档侵犯您的权益,请联系客服反馈,我们会尽快为您处理(人工客服工作时间:9:00-18:30)。
第十章
塑料压塑成型模具第一节
概述第二节压模成型零件设计原则
一、压制成型及压制模结构特点
压制成型是高分子材料成型加工技术中历史最悠久,也是最为重要的一种工艺。
几乎所有的高分子材料都可用此方法来成型制品。
考虑到生产效率、制品尺寸、产品使用的特点,目前主要用于:
热固性塑料、橡胶制品、复合材料的成型。
热固性塑料的模压成型
将压塑料置于金属模具中的型腔内,然后闭模在加热加压的情况下,使塑料熔融、流动,充满型腔,经适当的放气、保压后,塑料就充分交联固化为制品。
因为热固性塑料经交联固化后,其分子结果变形三维交联的体型结构,所以制品可以趁热脱模。
工艺特点:
成型工艺及设备成熟,是较老的成型工艺,设备和模具比注射简单。
间歇,生产周期长,生产效率低,劳动强度大,难自动化。
制品质量好,不会产生内应力或分子取向。
能压制较大面积制品,但不能压制形状复杂及厚度较大的制品。
制品成型后,可趁热脱模。
热塑性塑料:受热后软化,冷却后变硬,这种软化和变硬可以重复循环,所以可以反复成型。
70%PVC、PE、PP
热固性塑料:由单体直接形成网状聚合物或通
过交联线型预聚体而形成,一旦形成交联聚合物,受热后不能再回到可塑状态。
所以热固性
塑料来说,聚合过程和成型过程是同时进行
的,所得制品是不溶不熔的。
压制成型:又叫压塑成型,成型方法是将粉状或纤维状等塑料放入成型温度下的模具型腔
中,后闭模加压而使其成型并固化的作业。
压模可以兼用于热固性塑料和热塑性塑料。
模压热固性塑料时,塑料一直处于高温,置于型腔中的热固性塑料在压力的作用下,先由固体变为半液体,并在这种状态下流满型腔而取得型腔所赋予的形状;随交联反应的深化,半液体的粘度逐渐增加以至变为固体,最后脱模成为制品。
热塑性塑料的模压,在前一阶段的情况与热固性塑料相同,但是由于没有交联反应,所以在流满型腔后,将模具冷却使其固化才能脱模成为制品。
由于热塑性塑料模压时,模具需要交替的加热和冷却,生产周期长,所以热塑性塑料制品的成型用注射成型等方法更为经济,只有在模压较大平面的塑料制品时,才采用模压成型,如透明板材等。
本章主要介绍热固性塑料的压制成型。
与注射成型比较,压模有其特殊的地方:(一)优缺点P316(二)压模结构分为装于压机上压板得上模和装于下压板得下模两个部分。
上下两模闭合使装于加料室和型腔中的塑料受热受压,成为熔融态充满整个型腔,当制件固化成型后,上下模打开利用顶出装置顶出制件,压模可以分为以下几个部分:1、型腔
直接成型制品的部位,加料时与加料室一起装料作用,由上凸模、下凸模、凹模构成,对制件成型有很大的影响。
2、加料室凹模的上半部分,为凹模断面尺寸的扩大部分。
由于塑料与制品相比有较大的比容,成型前单靠型腔往往无法容纳全部原料,所以在型腔上设有一段加料室。
3、导向机构
布置在模具上模周边的四根导柱和装有导向套的导柱孔组成。
导向机构用来保证上下模合模的对中性。
为保证顶出机构水平运动,该模具在底板上还设有二根导柱,在顶出板上有带导向套的导向孔。
4、侧向分型抽芯机构
与注射模具一样,模制带有侧孔和侧凹的制件,模具必须设有各种侧向分型抽芯机构,制件方能脱出。
5、脱模机构压制件脱模机构与注射模具相似,脱模机构具有顶出版、顶出杆等零件。
6、加热系统热固性塑料压制成型需要在较高的温度下进行,所以模具必须加热。
常见的加热方法有:电加热、蒸汽加热、煤气加热、天然气加热等。
压制热塑性塑料时,在型腔周围开设温度控制通道,在塑化和定型阶段,分别通入蒸汽进行加热或者通入冷水进行冷却。
二、压模分类分类方法很多,可以按模具在压机上的固定方式分类、上下模闭合形式分、分型面特征分、型腔数目分、制品的顶出方式分等。
一般按压制模具的上下模配合结构特征进行分类。
(一)溢式模具(敞开式压模)6-2-1
1、无加料室;
2、模腔总高A ;基本就是制件高度,凸模和凹模无配合部分,故压制时过剩的物料极易溢出。
3、环形面积B 是挤压面较窄,以降低制件的毛边;
优点:结构简单,造价低廉,耐用。
(二)不溢式模具(密闭式模具、正压模、全压式模具)1、加料室:型腔上部断面延续,无挤压面,压力全在制件上,塑料溢出量少。
2、0.025-0.75mm
的间隙(压模与型腔),配合高度不宜过大(凸模降低,凹模声高)。
3、必须设置顶出装置,否则制品难以取出。
4、不应该设计多型腔。
因为加料稍有不均衡,各压力不等。
5、优点:承受力大(密实性好),机械强度高,形状复杂,薄、长流程、深形制品。
6、缺点:溢出量少,加料量多少直接影响制件的高度尺寸,每模必须准确称量,凸模与加料室的摩擦会损伤之间的表面。
(三)半溢式模具(半密闭式压模)1、特点:在型腔上方设有一断面尺寸大于制件尺寸的加料室,凸模与加料室为动配合接触,并且在分界处有一环形挤压面,其宽度约为4-5mm ,压到挤压面为止。
2、物料料稍有过量,通过配合间隙或在凸模上开设专门的溢料槽排出,其速度可以由溢料数目和间隙大小调节。
制品紧密程度比溢式模具好。
3、操作方便,加料时,按体积计量。
制品的高度由型腔高度A 决定。
可达到每模基本一致,应用广泛。
4、优点:不划伤型腔壁,而不损伤制件的表面。
5、易于成型制件外缘形状复杂的制品。
第二节压模成型零件设计原则成型零件包括凹模、凸模、型芯、成型杆等。
还有加料室的结构尺寸。
一、型腔总体尺寸设计模具内加压方向的选择,凸模和凹模的配合
结构选择,分型面的位置选择。
(一)塑件在模具内施压方向的选择施压方向:是凸模施压作用力的方向一般都是其轴线方向。
1、有利于压力的传递避免压力传递距离太长(压力损失太大),压力不易均匀作用在全长范围内。
2、便于加料便于加料,加料室直径大,深度浅;
不易加料,加料室直径小,深度大;3、便于安装和固定嵌件考虑将嵌件安装在下模。
如果装在上模时不慎落下,会压坏模具。
4、保证凸模的强度上凸模越简单越好。
5、长型芯位于施压方向对于侧型芯来说,把抽拔距长的放在施压方向(开模方向),而把抽拔距短的放在侧面,作为侧向分型抽芯。
6、保证重要的尺寸精度精度要求高的尺寸不宜设计在施压方向上,受溢边厚度和加料量不同而变化。
(二)分型面位置和形状的选择与注射模具分型面的选择相似。
1、轮廓最大的地方;
2、避免侧型芯;
3、溢料痕迹应该在制件易修易隐蔽的地方;
4、要求同心的尺寸同设计在压模的同一侧;
5、顶出机构在下模。
6、压模的挤压边缘和分型面多为水平面。
二、压模型腔配合结构和尺寸
1、溢式压模配合形式
密合面(溢料面或挤压面)光滑平整,面积不易过大,多设计成紧紧围绕在制品周边的环形,其宽度为3-5mm 。
增设承压面
2、不溢式压模配合形式
加料室断面尺寸与型腔尺寸相同;
配合间隙:过小,难排气,易咬死、擦伤。
过大,溢料,影响质量。
一般为:0.025-0.075mm 。
3、半溢式压模凸模与凹模配合形式
特点:带有水平挤压面B ,凸模与加料室间的配合间隙或溢料槽有溢料和排气的作用。
尺寸:0.025-0.075mm 。
引导部分高:1mm 。