水泥搅拌桩检测
水泥搅拌桩检测
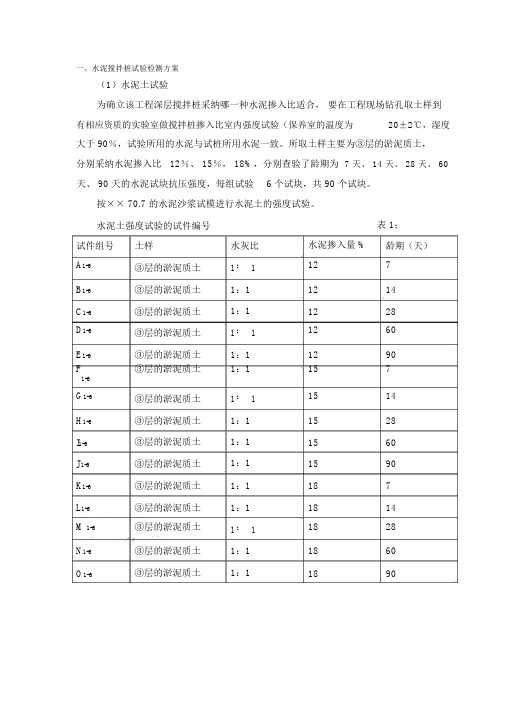
一、水泥搅拌桩试验检测方案(1)水泥土试验为确立该工程深层搅拌桩采纳哪一种水泥掺入比适合,要在工程现场钻孔取土样到有相应资质的实验室做搅拌桩掺入比室内强度试验(保养室的温度为20±2℃,湿度大于 90%,试验所用的水泥与试桩所用水泥一致。
所取土样主要为③层的淤泥质土,分别采纳水泥掺入比12%、 15%, 18%,分别查验了龄期为7 天、 14 天、 28 天、 60 天、 90 天的水泥试块抗压强度,每组试验 6 个试块,共 90 个试块。
按×× 70.7 的水泥沙浆试模进行水泥土的强度试验。
水泥土强度试验的试件编号表 1:试件组号土样水灰比水泥掺入量 % 龄期(天)A1-6 ③层的淤泥质土 1 : 1 12 7B1-6 ③层的淤泥质土1:1 12 14C1-6 ③层的淤泥质土1:1 12 28D1-6 ③层的淤泥质土 1 : 1 12 60E1-6 ③层的淤泥质土1:1 12 90F ③层的淤泥质土1:1 15 71-6G1-6 ③层的淤泥质土 1 : 1 15 14H1-6 ③层的淤泥质土1:1 15 28I1-6 ③层的淤泥质土1:1 15 60J1-6 ③层的淤泥质土1:1 15 90K1-6 ③层的淤泥质土1:1 18 7L1-6 ③层的淤泥质土1:1 18 14M 1-6 ③层的淤泥质土 1 : 1 18 28N1-6 ③层的淤泥质土1:1 18 60O1-6 ③层的淤泥质土1:1 18 90日期试块编号试块强度实验数据记录表实验温度仪器水泥龄期单轴极限抗压强均匀值备注掺量度( kpa)A1A2A3A 组试块12% 7天A4A5A6B组试块C组试块O组试块实验员记录员校核员(2)试桩工艺参数确立试验为了确立深层水泥土搅拌桩的施工工艺,特要求做深层水泥土搅拌变径桩试桩,该桩拥有提高地基承载力、控制地基沉降、降低地基办理花费等长处。
试桩按湿法成桩进行试验。
桩排成 10 行,每行 3 根桩,桩与桩成正方形部署,间距分三组×,××,呈每三个一组;1)水泥土搅拌桩的主桩直径Φ 500,扩大的支盘桩径Φ 1000;水泥掺入比为15%,水泥采纳 32.5R 一般硅酸盐水泥。
水泥搅拌桩质量检测方法

水泥搅拌桩质量检测方法摘要:水泥搅拌桩施工量大、面广,且是隐蔽工程,现有水泥搅拌桩施工机具无法自动、准确地控制水泥搅拌桩施工质量。
因此,如何对水泥搅拌桩施工质量进行检测,实施水泥搅拌桩施工过程中质量有效控制,是软基处理工程没有很好解决而迫切需要解决的问题。
就水泥搅拌桩应用中常见的检测方法及其质量评定进行了浅析,提出了几点建议。
1 水泥搅拌桩的质量检测方法浅析水泥搅拌桩桩身质量至少包括3个方面:桩体强度、搅拌均匀性和桩身长度。
1.1 挖桩检查法挖桩检查法是目前软基设计规范规定的方法,挖桩检查主要查看桩的成型情况,鉴定外观方面:桩体是否圆匀,有无缩颈和回陷现象;搅拌是否均匀,凝体有无松散;群桩桩顶是否平齐,间距是否均匀。
同时可分别在桩顶以下50、150cm等部位砍取足尺桩头,进行无侧限抗压强度试验。
1.2 轻便触探仪触探法使用轻便动力触探法检测粉喷桩时应注意:①探测深度不能超过4 in;②触探点不能在桩中心位置,一般定在距桩中心2/5桩径处,以避开桩中心水泥含量中偏少、强度低的喷灰搅拌盲区,以使触探具有代表性;③触探时触探仪的穿心杆一定要保持垂直。
1.3 静力触探法和标贯法检测已有人采用SPT法结合钻孔取芯对不同龄期、不同的掺入比条件下,对多根水泥搅拌桩进行过对比试验。
根据静力触探比贯入阻力PS和标贯击数N与钻孔取芯无侧限抗压强度QU测试结果,采用数理统计方法提出以下统计关系:静力触探比贯入阻力PS与无侧限抗压强度QU之间关系QU = 39.3+4.17P (7d龄期)标贯击数N与无侧限抗压强度QU之间关系QU =17.85+6.8N 2≤N63.5≤18 (7 d龄期)QU =268.4+10.6N 16≤N63.5≤30 (28d龄期)随着龄期的增长,桩身强度逐渐提高因此静力触探法宜在成桩后近期内进行。
该方法有直、快速的特点,但无论在理论上还是实践上还需要作深入探讨,对测试设备也须作进一步改进和完善。
水泥搅拌桩检测方法
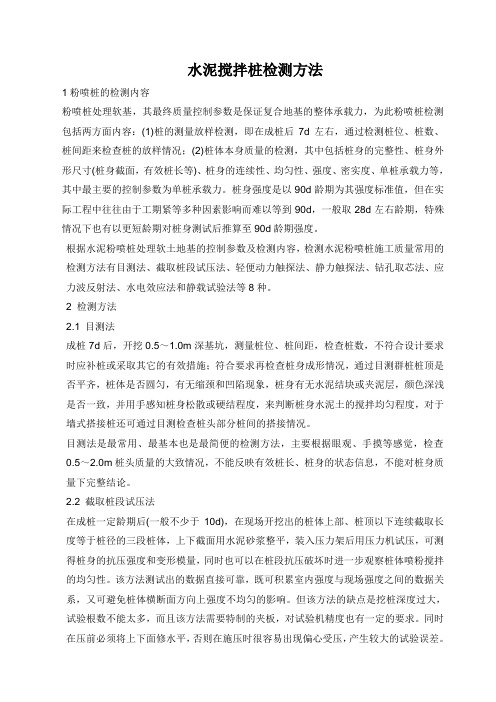
水泥搅拌桩检测方法1粉喷桩的检测内容粉喷桩处理软基,其最终质量控制参数是保证复合地基的整体承载力,为此粉喷桩检测包括两方面内容:(1)桩的测量放样检测,即在成桩后7d左右,通过检测桩位、桩数、桩间距来检查桩的放样情况;(2)桩体本身质量的检测,其中包括桩身的完整性、桩身外形尺寸(桩身截面,有效桩长等)、桩身的连续性、均匀性、强度、密实度、单桩承载力等,其中最主要的控制参数为单桩承载力。
桩身强度是以90d龄期为其强度标准值,但在实际工程中往往由于工期紧等多种因素影响而难以等到90d,一般取28d左右龄期,特殊情况下也有以更短龄期对桩身测试后推算至90d龄期强度。
根据水泥粉喷桩处理软土地基的控制参数及检测内容,检测水泥粉喷桩施工质量常用的检测方法有目测法、截取桩段试压法、轻便动力触探法、静力触探法、钻孔取芯法、应力波反射法、水电效应法和静载试验法等8种。
2 检测方法2.1 目测法成桩7d后,开挖0.5~1.0m深基坑,测量桩位、桩间距,检查桩数,不符合设计要求时应补桩或采取其它的有效措施;符合要求再检查桩身成形情况,通过目测群桩桩顶是否平齐,桩体是否圆匀,有无缩颈和凹陷现象,桩身有无水泥结块或夹泥层,颜色深浅是否一致,并用手感知桩身松散或硬结程度,来判断桩身水泥土的搅拌均匀程度,对于墙式搭接桩还可通过目测检查桩头部分桩间的搭接情况。
目测法是最常用、最基本也是最简便的检测方法,主要根据眼观、手摸等感觉,检查0.5~2.0m桩头质量的大致情况,不能反映有效桩长、桩身的状态信息,不能对桩身质量下完整结论。
2.2 截取桩段试压法在成桩一定龄期后(一般不少于10d),在现场开挖出的桩体上部、桩顶以下连续截取长度等于桩径的三段桩体,上下截面用水泥砂浆整平,装入压力架后用压力机试压,可测得桩身的抗压强度和变形模量,同时也可以在桩段抗压破坏时进一步观察桩体喷粉搅拌的均匀性。
该方法测试出的数据直接可靠,既可积累室内强度与现场强度之间的数据关系,又可避免桩体横断面方向上强度不均匀的影响。
水利工程水泥搅拌桩检测要求和费用

水利工程水泥搅拌桩检测要求和费用文稿归稿存档编号:[KKUY-KKIO69-OTM243-OLUI129-G00I-FDQS58-水利工程水泥搅拌桩检测要求一、检测的依据①设计图纸要求②《建筑地基处理技术规范》(JGJ 79-2002 J 220-2002)③《建筑基桩检测技术规范》(JGJ 106-2003 J256-2003)④地基处理手册二、检测方法及工作量查明水泥土搅拌桩的质量,需采用多种方法和手段相互结合,相互补充,相互验证,一般包括如下几个方面:)检查桩身每米的均匀性;检验数量为施①成桩后3天内,采用轻型动力触探(N10工总桩数的1%,且不少于3根。
②成桩7天后,采用浅部开挖桩头(深度宜超过停浆面以下0.5m),目测检查搅拌的均匀性,量测成桩直径。
检查量为总桩数的5%。
③对防渗墙,成桩15-21天后,采用地质雷达全段检测水泥土搅拌桩的连续性。
成桩28天后进行钻芯法采取芯样进行单轴抗压强度和渗透性试验检测。
检验数量为施工总桩数的0.5%,且不少于3根。
试验样数量一般每孔上、中、下三段各不少于2组。
④竖向承载水泥土搅拌桩地基,承载力检验应采用复合地基载荷试验和单桩载荷试验。
载荷试验必须在桩身强度满足试验荷载要求时,并宜在成桩28天后进行。
检验数量为桩总数的1%,且每项单体各不少于3点。
三、收费标准主要依据《工程勘察设计收费标准》(2002修订本),部分参照市场实际价格。
①轻型动力触探:每组日1320元,(设备进出场地视情况200~500元/次另计)②浅部桩头均匀性目测及桩径测量:每组日1320元③地质雷达: 16000元/km,(最低10000元/次)④钻芯法:a) 钻探取芯: 253元/m(设备进出场地视情况500~1000元/次另计)b) 试样采取及运输: 310元/件c) 试验费:单轴抗压强度(含试样切割、打磨):161元/组渗透试验(含试样切割、打磨): 242元/件⑤b) 试坑开挖、桩头处理由施工单位配合c) 加荷体吊装运输:50元/吨.百公里,且不少于3000元/场次。
水泥搅拌桩质量检验记录

水泥搅拌桩质量检验记录一、引言水泥搅拌桩广泛应用于土木工程中,为确保工程的质量和安全,对水泥搅拌桩的质量进行检验是非常重要的。
本文记录了水泥搅拌桩的质量检验过程和结果,以供工程监理和有关人员参考。
二、检验项目及方法1. 桩型和尺寸检验:通过与设计图纸和规范进行对比,检查水泥搅拌桩的型号、直径和长度是否符合要求。
2. 混凝土材料检验:采集水泥、砂、石的样品进行实验室检测,检查水泥搅拌桩所使用的混凝土材料的配合比是否合理,强度是否达标。
3. 钢筋检验:对水泥搅拌桩的钢筋进行抽检,检查钢筋的规格、数量和布置是否符合设计要求。
4. 现场浇筑质量检验:监测现场浇筑过程中混凝土的坍落度、骨料分布和浇筑厚度等参数,确保混凝土均匀且密实。
5. 强度试验:采集所浇筑的混凝土样品,进行强度试验,确保水泥搅拌桩的强度满足设计要求。
三、检验记录1. 检验项目:桩型和尺寸检验检验结果:水泥搅拌桩的型号为XX型,直径为XXmm,长度为XXm,与设计图纸和规范要求一致。
2. 检验项目:混凝土材料检验检验结果:经实验室检测,混凝土采用的水泥配合比为1:3:5,强度达到设计要求。
3. 检验项目:钢筋检验检验结果:共抽检XX根钢筋,规格为XX,布置符合设计要求,钢筋数量满足工程需要。
4. 检验项目:现场浇筑质量检验检验结果:浇筑过程中混凝土坍落度为XXmm,骨料分布均匀,浇筑厚度达到要求,浇筑过程具备密实性。
5. 检验项目:强度试验检验结果:经强度试验,水泥搅拌桩的强度达到设计要求,满足工程使用要求。
四、结论根据以上检验结果,水泥搅拌桩的质量检验通过,各项参数均满足设计要求。
经过严格控制和检查,水泥搅拌桩的质量问题得到有效解决,能够确保工程的质量和安全。
五、建议为了进一步提高水泥搅拌桩的质量,建议在施工过程中加强对混凝土原材料的检验和控制,保证材料的质量。
同时,应加强对施工现场的监管,确保浇筑过程的操作规范。
六、参考文献无七、附录无八、致谢感谢所有参与水泥搅拌桩质量检验工作的人员,为工程质量提供了有力保障。
水泥搅拌桩检测
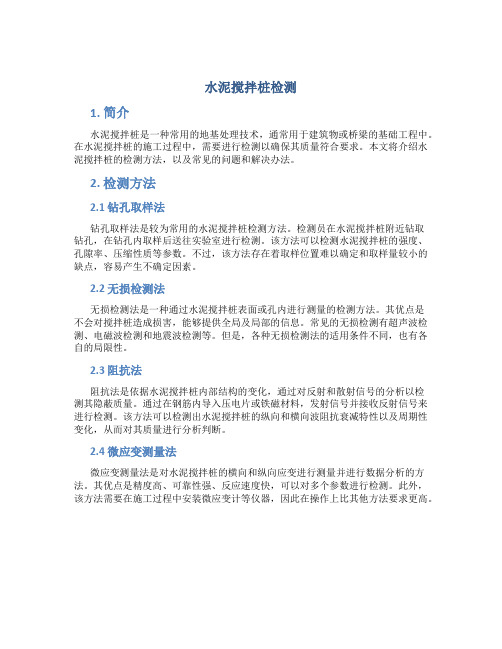
水泥搅拌桩检测1. 简介水泥搅拌桩是一种常用的地基处理技术,通常用于建筑物或桥梁的基础工程中。
在水泥搅拌桩的施工过程中,需要进行检测以确保其质量符合要求。
本文将介绍水泥搅拌桩的检测方法,以及常见的问题和解决办法。
2. 检测方法2.1 钻孔取样法钻孔取样法是较为常用的水泥搅拌桩检测方法。
检测员在水泥搅拌桩附近钻取钻孔,在钻孔内取样后送往实验室进行检测。
该方法可以检测水泥搅拌桩的强度、孔隙率、压缩性质等参数。
不过,该方法存在着取样位置难以确定和取样量较小的缺点,容易产生不确定因素。
2.2 无损检测法无损检测法是一种通过水泥搅拌桩表面或孔内进行测量的检测方法。
其优点是不会对搅拌桩造成损害,能够提供全局及局部的信息。
常见的无损检测有超声波检测、电磁波检测和地震波检测等。
但是,各种无损检测法的适用条件不同,也有各自的局限性。
2.3 阻抗法阻抗法是依据水泥搅拌桩内部结构的变化,通过对反射和散射信号的分析以检测其隐蔽质量。
通过在钢筋内导入压电片或铁磁材料,发射信号并接收反射信号来进行检测。
该方法可以检测出水泥搅拌桩的纵向和横向波阻抗衰减特性以及周期性变化,从而对其质量进行分析判断。
2.4 微应变测量法微应变测量法是对水泥搅拌桩的横向和纵向应变进行测量并进行数据分析的方法。
其优点是精度高、可靠性强、反应速度快,可以对多个参数进行检测。
此外,该方法需要在施工过程中安装微应变计等仪器,因此在操作上比其他方法要求更高。
3. 常见问题和解决办法3.1 检测结果出现误差检测结果出现误差通常是由于测量仪器的准确性和施工过程中的操作不当所引起的。
在使用测量仪器时需要确保其准确性,而在施工过程中需要严格遵守操作规程,避免操作不当所导致的质量问题。
3.2 检测数据不一致如果从不同的检测方法中获得的数据存在差异,需要进行进一步分析和比较,找出其差异的原因。
在分析差异时需要注意测量的条件、采样的位置、取样的数量等因素,以找出差异的根源并对其进行改善。
水泥搅拌桩检测规范

水泥搅拌桩检测规范水泥搅拌桩是一种常见的地基处理工艺,其质量直接影响到工程的安全性和可靠性。
为了保证水泥搅拌桩的质量,需要进行严格的检测。
下面就水泥搅拌桩的检测规范进行详细介绍。
1. 检测前准备在进行水泥搅拌桩检测之前,需要进行一些准备工作。
首先,要对检测设备进行校准和检查,确保其准确性和可靠性。
同时,要清理桩顶,将堆积在桩顶上的泥土和杂物清除干净,以便于检测。
2. 检测方法水泥搅拌桩的检测方法主要包括静载试验、动载试验和质量检验。
其中,静载试验是最常用的检测方法,可以通过加载一定的荷载,观察桩的沉降变形和抗力变化情况来评估桩的质量。
动载试验是在桩上施加动态荷载,通过振动传感器记录下振动响应来评估桩的质量。
质量检验主要针对桩身的成型质量和质量控制情况进行检查。
3. 检测参数和标准水泥搅拌桩的检测参数和标准包括桩直径、桩长、桩身强度、桩身的垂直度和偏斜度等。
桩直径和桩长是水泥搅拌桩设计的重要参数,需要在施工过程中进行实测,并与设计要求进行对比。
桩身强度可以通过静载试验和动载试验来评估,其强度要符合相关规范要求。
桩身的垂直度和偏斜度是评估桩的成型质量的重要指标,其偏差要符合相关规范要求。
4. 检测频率水泥搅拌桩的检测频率决定了检测结果的准确性和可靠性。
一般情况下,对于水泥搅拌桩的每批次,应当进行全批次的质量检测,确保每个桩的质量符合要求。
对于桩的强度和垂直度等参数的检测,可以按照设计要求和施工规范定期进行。
5. 检测结果的评估与记录在进行水泥搅拌桩检测后,需要及时对检测结果进行评估和记录。
评估结果应与设计要求和施工规范进行对比,判断桩的质量是否合格。
同时,要将检测结果详细记录,包括桩号、检测日期、检测人员和检测设备等信息,以备后期使用。
综上所述,水泥搅拌桩的检测规范主要包括检测前的准备工作、检测方法、检测参数和标准、检测频率以及检测结果的评估与记录等内容。
只有通过严格按照规范进行检测,才能保证水泥搅拌桩的质量,确保工程的安全性和可靠性。
水泥搅拌桩质量检验

水泥搅拌桩质量检验
(2)质量检验
①成桩后3天内,可用轻型动力触探(10N)检查每米桩身的均匀性。
检查数量为施工总桩数的1%,且不少于3根;成桩7天后要求承包人采用浅部开挖检测,用目测法检查桩体成型情况、搅拌均匀程度,量测成桩直径,如实做好记录。
开挖深度为0.5m~1.0m,如发现凝体不良等情况,应报废补桩。
检查数量为总桩数的5%。
②成桩28天后,用钻控取芯的办法,检测桩身的完整性、桩土搅拌均匀程度及桩的施工长度。
桩体的设计强度(90天无侧限)为1.2Mpa,28天强度> Mpa。
对每桩取出的芯样监理工程师应现场指定相对弱的地方截取一段,送检测中心做一组(三个)一个月龄期的无侧限抗压试验,以测定桩身强度。
③在特大桥桥台或软土较厚的地方,或对施工质量有怀疑时,监理工程师可在成桩28天后,进行随机和抽检单桩或复合地基承载力。
由单桩或复合地基载荷试验测试其承载力,检验桩身质量。
随机抽检的桩数不宜少于总桩数的0.2%,并不得少于3根。
试验用最大载荷为单桩或复合地基设计荷载的两倍。
水泥搅拌桩试验检测方案

水泥搅拌桩试验检测方案(1)水泥土试验为确定该工程深层搅拌桩采用哪种水泥掺入比合适,要在工程现场钻孔取土样到有相应资质的实验室做搅拌桩掺入比室内强度试验(养护室的温度为20±2℃,湿度大于90%,试验所用的水泥与试桩所用水泥一致。
所取土样主要为③层的淤泥质土,分别采用水泥掺入比12%、15%,18%,分别检验了龄期为7天、14天、28天、60天、90天的水泥试块抗压强度,每组试验6个试块,共90个试块。
按70.7×70.7×70.7的水泥砂浆试模进行水泥土的强度试验。
水泥土强度试验的试件编号表1:试件组号土样水灰比水泥掺入量% 龄期(天)A1-6③层的淤泥质土1:1 12 7B1-6③层的淤泥质土1:1 12 14C1-6③层的淤泥质土1:1 12 28D1-6③层的淤泥质土1:1 12 60E1-6③层的淤泥质土1:1 12 90F1-6③层的淤泥质土1:1 15 7G1-6③层的淤泥质土1:1 15 14H1-6③层的淤泥质土1:1 15 28I1-6③层的淤泥质土1:1 15 60J1-6③层的淤泥质土1:1 15 90K1-6③层的淤泥质土1:1 18 7L1-6③层的淤泥质土1:1 18 14M1-6③层的淤泥质土1:1 18 28N1-6③层的淤泥质土1:1 18 60O1-6③层的淤泥质土1:1 18 90试块强度实验数据记录表日期实验温度仪器实验员记录员校核员(2)试桩工艺参数确定试验为了确定深层水泥土搅拌桩的施工工艺,特要求做深层水泥土搅拌变径桩试桩,该桩具有提高地基承载力、控制地基沉降、降低地基处理费用等优点。
试桩按湿法成桩进行试验。
桩排成10行,每行3根桩,桩与桩成正方形布置,间距分三组1.5×1.5m,2.0×2.0m, 2.5×2.5m,呈每三个一组;1)水泥土搅拌桩的主桩直径Φ500,扩大的支盘桩径Φ1000;水泥掺入比为15%,水泥采用32.5R普通硅酸盐水泥。
水泥土搅拌桩地基工程质量标准及检验方法

桩底标回偏差
±200
mm
测机头深度
3
桩顶标同偏差
-50〜+100
mm
水准仪检查(最上 部500mni不计入)
4
桩位偏差
<50
mm
钢尺检查
5
桩径偏差
<0.04〃
钢尺检查
6
垂直度
W1.5
%
经纬仪检查
7
搭接
>200
mm
钢尺检查
注:D为桩径。
一般工程按桩数至少抽查20%o
2
水泥土搅拌桩地基工程质量标准和检验方法
类别
序号
检查工程
质量标准
单位
检验方法及器具
主控 工程
1
地基承载力
必须符合GB50202的规定
按规定方法检查检测报告
2
水泥及外掺剂质量
水泥进场时应对其品种、级别、 包 装或散装仓号、出厂日期等进行 检查,并应对其强度、安定性及 其他必要的性能指标进行复验, 其质量必须符合GB175等的规 定。混凝土中掺用外加剂的质量及
应用技术应符合GB8076、GB50119和有关环境保护等的规定
检查产品合格证或抽样 送检
3
水泥用量
应符合参数指标
查看流量计
4
桩体强度
应符合设计要求
按规定方法对承重水泥 土搅拌桩应取90天后的 试件;对支护水泥土搅拌
桩应取28天后的试件
一般 工程
1
机头提升速度偏差
W0.5
m/min
测机头上升距离及时间
水泥土搅拌桩地基工程质量标准及检验来自法1主控工程1)承载力、桩体强度检验:应按现行有关标准或按经专项论证的检验方 案抽样检测。
水泥土搅拌桩桩长检测方法
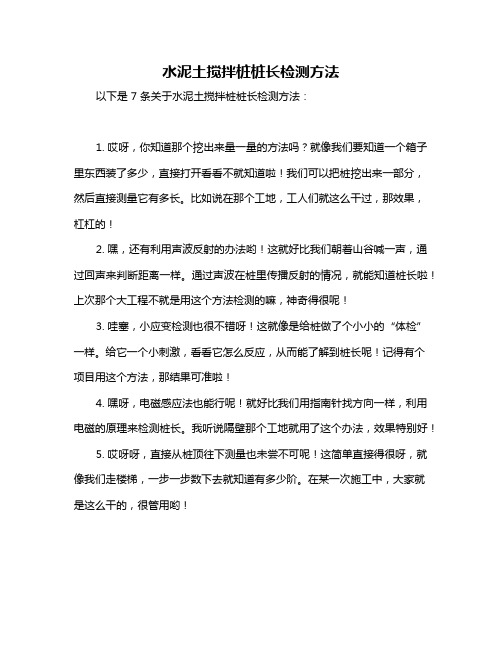
水泥土搅拌桩桩长检测方法
以下是 7 条关于水泥土搅拌桩桩长检测方法:
1. 哎呀,你知道那个挖出来量一量的方法吗?就像我们要知道一个箱子里东西装了多少,直接打开看看不就知道啦!我们可以把桩挖出来一部分,然后直接测量它有多长。
比如说在那个工地,工人们就这么干过,那效果,杠杠的!
2. 嘿,还有利用声波反射的办法哟!这就好比我们朝着山谷喊一声,通过回声来判断距离一样。
通过声波在桩里传播反射的情况,就能知道桩长啦!上次那个大工程不就是用这个方法检测的嘛,神奇得很呢!
3. 哇塞,小应变检测也很不错呀!这就像是给桩做了个小小的“体检”一样。
给它一个小刺激,看看它怎么反应,从而能了解到桩长呢!记得有个项目用这个方法,那结果可准啦!
4. 嘿呀,电磁感应法也能行呢!就好比我们用指南针找方向一样,利用电磁的原理来检测桩长。
我听说隔壁那个工地就用了这个办法,效果特别好!
5. 哎呀呀,直接从桩顶往下测量也未尝不可呢!这简单直接得很呀,就像我们走楼梯,一步一步数下去就知道有多少阶。
在某一次施工中,大家就是这么干的,很管用哟!
6. 哇哦,通过分析施工数据来推断桩长也蛮有意思的嘛!就好像通过一个人的行为来猜他的心思一样。
上次那个大项目,技术人员就这么厉害地推断出来了,真牛啊!
7. 哈哈,用探地雷达检测桩长简直太酷啦!就像我们有了一双能看透地下的眼睛。
有个大型建筑场地就是靠这个方法检测的,那结果,让人特别放心呢!
我觉得这些水泥土搅拌桩桩长检测方法都各有优势,我们要根据具体情况选择最合适的那个呀!。
水泥搅拌桩怎么送样检测
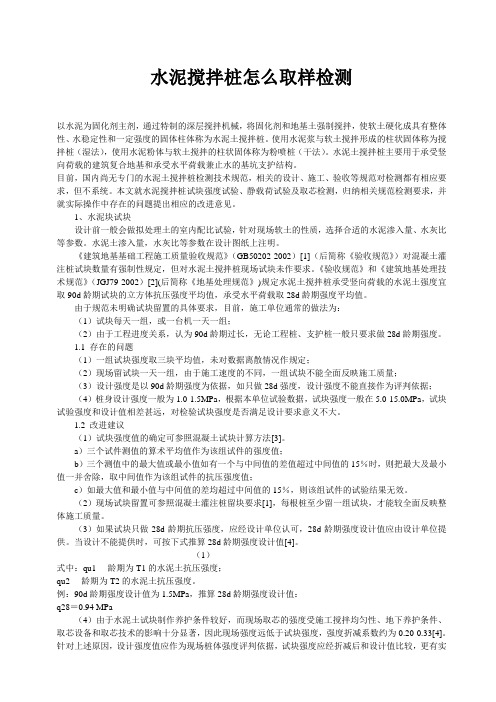
水泥搅拌桩怎么取样检测以水泥为固化剂主剂,通过特制的深层搅拌机械,将固化剂和地基土强制搅拌,使软土硬化成具有整体性、水稳定性和一定强度的固体柱体称为水泥土搅拌桩。
使用水泥浆与软土搅拌形成的柱状固体称为搅拌桩(湿法),使用水泥粉体与软土搅拌的柱状固体称为粉喷桩(干法)。
水泥土搅拌桩主要用于承受竖向荷载的建筑复合地基和承受水平荷载兼止水的基坑支护结构。
目前,国内尚无专门的水泥土搅拌桩检测技术规范,相关的设计、施工、验收等规范对检测都有相应要求,但不系统。
本文就水泥搅拌桩试块强度试验、静载荷试验及取芯检测,归纳相关规范检测要求,并就实际操作中存在的问题提出相应的改进意见。
1、水泥块试块设计前一般会做拟处理土的室内配比试验,针对现场软土的性质,选择合适的水泥渗入量、水灰比等参数。
水泥土渗入量,水灰比等参数在设计图纸上注明。
《建筑地基基础工程施工质量验收规范》(GB50202-2002)[1](后简称《验收规范》)对混凝土灌注桩试块数量有强制性规定,但对水泥土搅拌桩现场试块未作要求。
《验收规范》和《建筑地基处理技术规范》(JGJ79-2002)[2](后简称《地基处理规范》)规定水泥土搅拌桩承受竖向荷载的水泥土强度宜取90d龄期试块的立方体抗压强度平均值,承受水平荷载取28d龄期强度平均值。
由于规范未明确试块留置的具体要求,目前,施工单位通常的做法为:(1)试块每天一组,或一台机一天一组;(2)由于工程进度关系,认为90d龄期过长,无论工程桩、支护桩一般只要求做28d龄期强度。
1.1 存在的问题(1)一组试块强度取三块平均值,未对数据离散情况作规定;(2)现场留试块一天一组,由于施工速度的不同,一组试块不能全面反映施工质量;(3)设计强度是以90d龄期强度为依据,如只做28d强度,设计强度不能直接作为评判依据;(4)桩身设计强度一般为1.0-1.5MPa,根据本单位试验数据,试块强度一般在5.0-15.0MPa,试块试验强度和设计值相差甚远,对检验试块强度是否满足设计要求意义不大。
水泥土搅拌桩检测规范
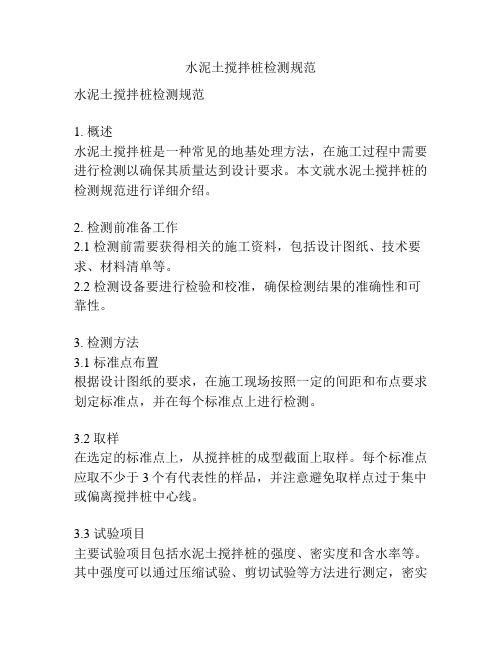
水泥土搅拌桩检测规范水泥土搅拌桩检测规范1. 概述水泥土搅拌桩是一种常见的地基处理方法,在施工过程中需要进行检测以确保其质量达到设计要求。
本文就水泥土搅拌桩的检测规范进行详细介绍。
2. 检测前准备工作2.1 检测前需要获得相关的施工资料,包括设计图纸、技术要求、材料清单等。
2.2 检测设备要进行检验和校准,确保检测结果的准确性和可靠性。
3. 检测方法3.1 标准点布置根据设计图纸的要求,在施工现场按照一定的间距和布点要求划定标准点,并在每个标准点上进行检测。
3.2 取样在选定的标准点上,从搅拌桩的成型截面上取样。
每个标准点应取不少于3个有代表性的样品,并注意避免取样点过于集中或偏离搅拌桩中心线。
3.3 试验项目主要试验项目包括水泥土搅拌桩的强度、密实度和含水率等。
其中强度可以通过压缩试验、剪切试验等方法进行测定,密实度可以通过标准贯入试验等方法进行测定,含水率可以通过重量法、干燥法等方法进行测定。
4. 检测结果评定4.1 强度评定根据设计要求和相关规范,对搅拌桩的强度进行评定。
强度评定可以根据试验结果进行,也可以通过现场观察和经验判断。
4.2 密实度评定参照相关规范,对搅拌桩的密实度进行评定。
密实度评定可以根据试验结果进行,也可以通过现场观察和经验判断。
4.3 含水率评定根据设计要求和相关规范,对搅拌桩的含水率进行评定。
含水率评定可以根据试验结果进行,也可以通过现场观察和经验判断。
5. 检测报告5.1 检测结果要详细记录并形成检测报告。
5.2 检测报告应包括检测日期、检测地点、检测项目、检测结果、评定结论等内容。
5.3 检测报告应及时提交给相关单位和项目经理,并妥善保管。
6. 处理不合格情况6.1 对于检测结果不合格的搅拌桩,应及时采取措施予以整改。
6.2 不合格的搅拌桩需要重新进行检测,直到达到设计要求为止。
7. 检测责任7.1 检测工作由具备相应资质和专业技术的检测人员负责。
7.2 施工单位和监理单位要对检测工作进行监督和指导,确保检测结果的准确性和可靠性。
水泥深层搅拌桩质量检验报告单

水泥深层搅拌桩质量检验报告单一、试验目的和依据本次试验的目的是对水泥深层搅拌桩的质量进行检验,以保证其符合设计要求和相关规范的技术要求。
试验依据包括《水泥深层搅拌桩施工及验收规范》等相关标准和规范。
二、试验内容和方法1.搅拌桩强度试验:采用抽样试块的方法,从搅拌桩体中取得样品,进行强度试验。
试验方法应符合相关标准的规定。
2.搅拌桩竖向位移试验:通过测量搅拌桩在不同荷载作用下的竖向位移,评估搅拌桩的稳定性。
试验方法可采用沉降钢尺法或其他适用方法。
3.搅拌桩尺寸检测:测量搅拌桩的直径、长度、孔距等尺寸参数,以检查其是否符合设计要求。
4.搅拌桩灌注质量检验:检测搅拌桩内部混凝土质量,是否存在空洞和杂质等问题。
三、试验结果和评价1.强度试验结果:通过对搅拌桩样品进行强度试验,得出其抗压强度和抗折强度。
试验结果符合设计要求,均达到或超出相关标准的要求。
2.竖向位移试验结果:通过测量搅拌桩在荷载作用下的变形情况,得出其竖向位移。
试验结果表明搅拌桩在不同荷载下具有良好的稳定性和变形能力。
3.尺寸检测结果:根据测量数据,得出搅拌桩的直径、长度、孔距等尺寸参数。
结果表明搅拌桩的实际尺寸与设计要求基本一致。
4.灌注质量检验结果:通过检测搅拌桩内部混凝土质量,确定其存在空洞和杂质的情况。
试验结果表明搅拌桩的灌注质量良好,无空洞和杂质。
四、试验结论本次水泥深层搅拌桩质量检验结果显示,搅拌桩在强度、稳定性、尺寸和灌注质量等方面均符合设计要求和相关规范的要求。
经过检验,水泥深层搅拌桩的质量可被确认为合格。
五、质量问题和建议在本次试验中,水泥深层搅拌桩的质量检验均未发现问题,符合设计要求和相关规范。
建议在后续施工过程中,加强施工管理,确保施工工艺的正确执行,以提高水泥深层搅拌桩的质量。
六、检验人员及日期检验人员:XXX检验日期:XXXX年XX月XX日。
水泥搅拌桩地基质量检验的主控项目

水泥搅拌桩地基质量检验的主控项目包括以下几个方面:
1. 原材料质量检验:对水泥、砂、石等原材料进行检验,确保其符合使用要求。
包括水泥强度检验、砂粒级配检验、石料质量检验等。
2. 现场施工检验:对搅拌桩施工现场进行检查,确保施工符合相关规范和要求。
包括搅拌机设备的检验,保证其正常运行和混合质量;对混合后的浆液进行取样检验,包括浆液的含水率、坍落度、固化时间等。
3. 桩身成型检验:对搅拌桩的成型情况进行检验,确保桩身的质量符合设计要求。
包括对桩身的直径、长度、竖直度、平顺度等进行测量和记录,以及对钢筋试验桩进行抽取和检验。
4. 桩基承载力检验:对搅拌桩的承载力进行检验,确保桩基的稳定性和承载力满足设计要求。
包括进行静载试验或动力触探等方法,对搅拌桩的承载力进行计算和评估。
5. 桩身质量检验:对搅拌桩的质量进行检验,确保桩身的强度和密实度满足要求。
包括进行抗压试验、抗拉试验等,检验桩身的强度指标;采用钻孔取芯或动力触探等方法,检测桩身的密实度和质地。
以上是水泥搅拌桩地基质量检验的主控项目,每个项目都有相应的检验方法和标准。
在实际操作中,需要依据工程设计文件、相关规范和技术要求,制定具体的检验方案,并由专业的检验机构或技术人员进行检验和评估。
水泥搅拌桩检测

水泥搅拌桩检测⑴桩的测量放样检测,即在成桩后7d左右,通过检测桩位、桩数、桩间距来检查桩的放样情况;(2)桩体本身质量的检测,其中包括桩身的完整性、桩身外形尺寸(桩身截面,有效桩长等)、桩身的连续性、均匀性、强度、密实度、单桩承载力等,其中最主要的控制参数为单桩承载力。
桩身强度是以90d龄期为其强度标准值,但在实际工程中往往由于工期紧等多种因素影响而难以等到90d,一般取28d左右龄期,特殊情况下也有以更短龄期对桩身测试后推算至90d龄期强度。
根据水泥粉喷桩处理软土地基的控制参数及检测内容,检测水泥粉喷桩施工质量常用的检测方法有目测法、截取桩段试压法、轻便动力触探法、静力触探法、钻孔取芯法、应力波反射法、水电效应法和静载试验法等8种。
目测法成桩7d后,开挖0.5〜1.0m深基坑,测量桩位、桩间距,检查桩数,不符合设计要求时应补桩或采取其它的有效措施;符合要求再检查桩身成形情况,通过目测群桩桩顶是否平齐,桩体是否圆匀,有无缩颈和凹陷现象,桩身有无水泥结块或夹泥层,颜色深浅是否一致,并用手感知桩身松散或硬结程度,来判断桩身水泥土的搅拌均匀程度,对于墙式搭接桩还可通过目测检查桩头部分桩间的搭接情况。
目测法是最常用、最基本也是最简便的检测方法,主要根据眼观、手摸等感觉,检查0.5〜2.0m桩头质量的大致情况,不能反映有效桩长、桩身的状态信息,不能对桩身质量下完整结论。
截取桩段试压法在成桩一定龄期后(一般不少于10d),在现场开挖出的桩体上部、桩顶以下连续截取长度等于桩径的三段桩体,上下截面用水泥砂浆整平,装入压力架后用压力机试压,可测得桩身的抗压强度和变形模量,同时也可以在桩段抗压破坏时进一步观察桩体喷粉搅拌的均匀性。
该方法测试出的数据直接可靠,既可积累室内强度与现场强度之间的数据关系,又可避免桩体横断面方向上强度不均匀的影响。
但该方法的缺点是挖桩深度过大,试验根数不能太多,而且该方法需要特制的夹板,对试验机精度也有一定的要求。
水泥土搅拌桩检测项目
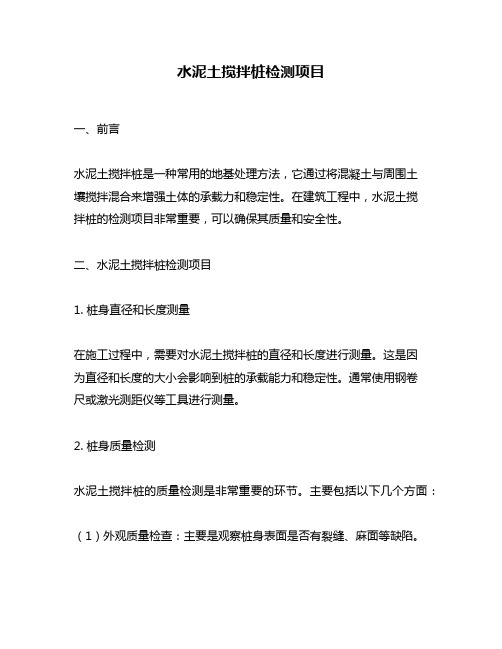
水泥土搅拌桩检测项目一、前言水泥土搅拌桩是一种常用的地基处理方法,它通过将混凝土与周围土壤搅拌混合来增强土体的承载力和稳定性。
在建筑工程中,水泥土搅拌桩的检测项目非常重要,可以确保其质量和安全性。
二、水泥土搅拌桩检测项目1. 桩身直径和长度测量在施工过程中,需要对水泥土搅拌桩的直径和长度进行测量。
这是因为直径和长度的大小会影响到桩的承载能力和稳定性。
通常使用钢卷尺或激光测距仪等工具进行测量。
2. 桩身质量检测水泥土搅拌桩的质量检测是非常重要的环节。
主要包括以下几个方面:(1)外观质量检查:主要是观察桩身表面是否有裂缝、麻面等缺陷。
(2)声音检查:使用锤敲击桩身,听其声音是否均匀清脆。
(3)取样试验:取样后进行强度试验、抗渗试验等。
3. 桩身竖向位移测量水泥土搅拌桩在施工过程中,需要进行竖向位移的测量,以便控制其沉降和变形。
通常使用自动水准仪或激光测距仪等工具进行测量。
4. 桩身水平位移测量在施工过程中,需要对水泥土搅拌桩的水平位移进行监测。
这是因为水平位移会影响到桩的承载能力和稳定性。
通常使用全站仪或激光测距仪等工具进行测量。
5. 桩身荷载试验为了保证水泥土搅拌桩的承载能力和稳定性,需要进行荷载试验。
主要包括静载试验和动载试验两种方式。
静载试验是通过施加静态荷载来测试桩的承载能力;动载试验则是通过施加冲击荷载来测试桩的抗震性能。
6. 桩身超声波检测超声波检测是一种非破坏性检测方法,可以用于检查水泥土搅拌桩内部质量情况。
通过超声波探头对桩身进行扫描,可以检测到裂缝、空洞等缺陷。
7. 桩身电阻率测试水泥土搅拌桩的电阻率测试是一种常用的检测方法。
通过对桩身进行电极接触,测量其电阻率大小,可以判断桩体内部的质量情况。
三、总结水泥土搅拌桩是一种常用的地基处理方法,在施工过程中需要进行多项检测项目来确保其质量和安全性。
主要包括桩身直径和长度测量、桩身质量检测、桩身竖向位移测量、桩身水平位移测量、桩身荷载试验、桩身超声波检测和桩身电阻率测试等。
水泥搅拌桩取芯检测要求

水泥搅拌桩取芯检测要求水泥搅拌桩取芯检测是对水泥搅拌桩施工中的砼样品进行取芯、检测和分析的过程。
水泥搅拌桩的取芯检测是施工质量控制的重要环节,有效的取芯检测可以确保水泥搅拌桩施工的质量和安全性。
以下是对水泥搅拌桩取芯检测要求的详细介绍。
一、取芯的方法和原则1.水泥搅拌桩取芯必须在桩周混凝土到达强度设计要求后进行,一般为7天龄或28天龄样品。
2.取样点应该选择在桩体上三分之二高度的上部,并且要求在同一截面上选择多个取样点,以保证取样的代表性。
3.取芯时,应在桩体截面中央位置,避开可能存在的预埋件和抗浮垫。
取样点的选择应符合设计要求和规范的限制要求。
4.取芯钻头应选择合适的直径和长度。
取芯钻头应无缺口、无絮凝物、无泥土和其它杂质附着。
每次取芯所需碳钎杆直径不宜超过钻孔内径的1/4。
5.取芯钻头下穿过预埋钢筋时,应注意避开钢筋,以免损坏钻头和钻杆。
6.取芯时应注意均匀施力,控制速度。
不得在取芯过程中使芯全断裂、全丢失。
7.取芯样品应符合国家相关规范的取样要求。
每个取芯样品应称重并记录其质量。
二、取芯样品的保存和打包1.取芯样品应在取样后立即进行标识,并按取样点、混凝土类型、取样日期等信息进行记录。
2.标识后的芯样应进行有效保护,避免受潮、破碎和污染。
3.取芯样品要尽快送到实验室进行检测分析,不得长时间滞留于野外或施工现场。
4.取芯样品在运输过程中要注意防止震动和碰撞,保证芯样完整。
5.取芯样品的打包应采用防震、防水等措施,确保芯样的完整性和安全性。
三、取芯样品的检测和分析1.取芯样品进入实验室后,应首先进行取芯样品的制备工作,包括样品表面的处理、裁剪和修整。
2.检测和分析主要包括对芯样强度、密度、孔隙率、抗渗性、抗冻性、抗压强度等性能的检测。
3.取芯样品的检测要依据国家相关规范和设计要求,采用合适的仪器设备进行。
4.检测结果应及时记录、整理和分析,并进行必要的报告编制。
5.对取芯样品的检测结果进行评价和比较,以确定水泥搅拌桩的施工质量。
- 1、下载文档前请自行甄别文档内容的完整性,平台不提供额外的编辑、内容补充、找答案等附加服务。
- 2、"仅部分预览"的文档,不可在线预览部分如存在完整性等问题,可反馈申请退款(可完整预览的文档不适用该条件!)。
- 3、如文档侵犯您的权益,请联系客服反馈,我们会尽快为您处理(人工客服工作时间:9:00-18:30)。
一、水泥搅拌桩试验检测方案(1)水泥土试验为确定该工程深层搅拌桩采用哪种水泥掺入比合适,要在工程现场钻孔取土样到有相应资质的实验室做搅拌桩掺入比室内强度试验(养护室的温度为20±2℃,湿度大于90%,试验所用的水泥与试桩所用水泥一致。
所取土样主要为③层的淤泥质土,分别采用水泥掺入比12%、15%,18%,分别检验了龄期为7 天、14天、28 天、60天、90 天的水泥试块抗压强度,每组试验 6 个试块,共90 个试块。
按70.7×70.7×70.7 的水泥砂浆试模进行水泥土的强度试验。
水泥土强度试验的试件编号表1:试块强度实验数据记录表日期实验温度仪器实验员记录员校核员2)试桩工艺参数确定试验为了确定深层水泥土搅拌桩的施工工艺,特要求做深层水泥土搅拌变径桩试桩,该桩具有提高地基承载力、控制地基沉降、降低地基处理费用等优点。
试桩按湿法成桩进行试验。
桩排成10 行,每行 3 根桩,桩与桩成正方形布置,间距分三组 1.5×1.5m,2.0 × 2.0m, 2.5×2.5m,呈每三个一组;1)水泥土搅拌桩的主桩直径Φ 500,扩大的支盘桩径Φ 1000;水泥掺入比为15%,水泥采用32.5R普通硅酸盐水泥。
如图 1 所示:图 1 试验桩的剖面图2)水泥土搅拌桩支承于第四层(细砂),要求进入该层1.0 米,预计桩长约12.0 米。
3)施工过程中,应认真记录施工中的各种操作参数,下钻及提升的阻力情况等。
以便根据试验结果,确定正式施工参数。
浆液配制。
按照水泥浆的水灰比和水泥质量要求称取用水量。
先将水泥加入自动计量灰浆搅拌机中,再将水加入,搅拌时间≥ 3 min。
制备好的水泥浆停置时间应≤45 min,使用前浆液在灰浆搅拌机中应不断搅拌。
设备安装搭置起吊塔架、安装起吊装置、导向架及搅拌轴、输浆管。
电器系统必须安装漏电保护装置,供浆系统应布置在离深层搅拌桩机50 m的范围内。
桩机定位用起重机将深层搅拌桩机吊至指定桩位。
对正桩位,调平桩机机身,保证钻杆的垂直度;桩位对中误差≤50 mm,搅拌轴和导向架的垂直度偏差应≤ 1.5 %。
启动主电机下钻,待搅拌钻头接近地面时,启动空压机送气,继续钻进。
预搅下沉待深层搅拌桩机的冷却水循环正常后,启动深层搅拌桩机的电机,钻机正转给进状态,放松起重机钢兹绳,同时启动空压机喷射压缩空气,使深层搅拌桩机导向架搅拌下沉。
一般情况下不宜冲水,当遇到较硬土层下沉太慢(>30 min/m)时,可适当冲水下沉。
钻进速度应严格控制,使土体能完全破碎,以利于灰土拌和均匀,一般采用1V~V 挡钻进。
钻进实际工作中钻进深度 D 由深度尺盘按D= H+ a1+ a2确定,其中H 为设计加固深度,a1为搅拌钻头喷射口与地面平行时深度尺盘的读数,可事先调整为a1 = 0, a2 为停灰面深度。
钻到设计孔深时,停止钻进,钻头反转,但不提升。
提升喷浆搅拌当确认深层搅拌桩机钻头下沉到设计桩底标高以下0. 6 m后开动灰浆泵,关闭送气阀门,估计浆液从喷嘴喷出后,搅拌头自桩底反转,边喷浆边旋转,同时匀速提升搅拌轴。
每米喷灰量控制在50kg 左右,并保证瞬时喷灰的均匀性,提升至桩顶设计标高时停止供料。
重复搅拌当搅拌轴提升到试验加固深度的顶面标高时,喷浆量应达到设计要求,为使水泥浆与土拌和均匀,对桩体按设计要求进行重复搅拌一次,搅拌头下沉、再重复上下搅拌一次,形成桩体,复搅时停止喷水泥。
复搅完毕后继续提升钻头直至离开地面,移动钻机到下一个桩位。
清洗注浆管每个工班应清洗一次注浆管。
清洗时,向贮浆桶中注入适量清水,开启灰浆泵,清洗全部管道中残存的水泥浆,直至无残留水泥浆液。
施工要点1)施工前应平整场地,清除桩位处障碍物。
场地低洼时应回填黏土料,不得回填杂填土。
基础底面以上宜预留厚500 mm 的土层,搅拌桩施工时,桩顶应比设计标高高出50cm。
2)在施工前应画好施工桩位图,对每一个桩进行编号,然后根据桩位图进行施工现场定位并挂上明显的标志牌,防止施工时漏桩。
3)机身调平以钻杆是否垂直为依据,操作时以钻锤吊线进行控制。
4)水泥浆从砂浆搅拌机倒入贮浆桶前,须将水泥块等杂物滤掉,水泥浆体最大粒径≤0. 5 cm 时,以防喷粉时堵管。
贮浆桶容量应适中,要保证有一定余量,当储灰量不足时,不得对下一根桩施工,否则会造成因浆液不足而断桩。
还要防止浆液在贮浆桶内沉淀离析。
拌制浆液的罐数、固化剂和外掺剂的用量以及泵送浆液的时间等应有专人记录。
5)施工前应进行工艺试验,确定灰浆泵压力、送浆速度灰浆经灰浆管到达喷浆口的时间和搅拌轴提升速度等参数。
采用流量泵控制输浆量时,一般输浆速度为30L/min,喷日压力保持在0. 4~ 0. 6 MPa,并应使搅拌提升速度与输浆速度相适应。
6)专人记录搅拌轴每米下沉或提升时间,深度记录误差应≤50 mm,时间记录误差≤5s。
记录水泥的瞬时喷入量,以保证桩各段的均匀性,目提升至设计高度时,正好将设计的水泥用量喷完并记录水泥的累计喷入量。
尽量一次喷足,提升时为便于控制成桩质量,一般不得使用1V 挡提升。
为保证桩端施工质量,当浆液达到出浆口后,原地喷浆30s,使浆液完全到达桩端。
7)为保证桩端施工质量,当浆液达到出浆日后,原地喷浆30 s,使浆液完全到达桩端。
8)在成桩过程中,由于电压过低或其它原因造成停机,使成桩工艺中断时,为防止断桩,当桩机重新起动时。
均应将水泥搅拌机钻杆下沉0.5m 再继续往下制桩。
当停机>3h 时,为防止浆液硬结堵管,应拆卸输浆管彻底清洗管路。
9)搅拌轴提升变为搅拌时必须反转,否则正转提升易将土带起造成空洞。
10)根据现场实践表明,进行基坑开挖时,在基底标高以上1m 宜采用人工开挖,以保护桩头质量。
11)钻头直径的磨损应≤1cm,磨损>lcm 时必须换钻头。
施工中注意的问题施工中常见质量问题有:①水泥浆稠度控制不准;②水泥浆发生沉淀;③喷浆系统密封性不好;④桩体倾斜;⑤断桩;⑥偏桩;⑦桩体强度不均。
为保证桩的施工质量,针对施工中的常见问题,采用了以下质量控制措施:①采用自动计量装置,严格控制水灰比;②水泥未受潮无结块,喷浆前水泥浆应不断搅拌,其滞用时间不得超过水泥初凝时间;③施工前检查,保证在高压作用下正常施工;④施工前将钻机定位,安放平稳,施工中,随时检查钻机垂直度;⑤保持连续供浆,法兰连结处要拧紧螺帽,地层分界处增加水泥浆量;⑥准确放桩位,桩机准确就位,若偏差过大,应补桩施工;⑦控制提钻速度,确保均匀提升,均匀喷灰,均匀搅拌。
施工安全措施安全措施为解决好施工与安全之间的矛盾,严格贯彻“安全第一,预防为主”的方针,针对工程特点,制订具体措施。
认真贯彻执行,以减少各类事故的发生。
①建立健全安全生产保障体系,实行安全岗位责任制,签订安全承包责任状,明确分工,责任到人,使安全工作真正落到实处。
②实行保证安全的奖惩制度,做到奖惩严明,把安全生产纳入竞争机制。
③加强安全生产教育,通过安全法制教育和安全技术教育提高全体施工人员的安全生产意识;严格执行安全操作规程,加强安全教育和检查,杜绝不合要求的施工操作。
④建立机械设备的定期检查、保养制度。
⑤机械操作人员必须严格培训,持证上岗,按照安全操作规程作业。
作业前应对机械设备进行详细检查;机械设备运行时,特别是在制桩过程中,必须坚守岗位,夜间作业应充分照明,登高作业必须系安全带。
⑥及时排除空气储气罐内的积水,注意控制粉尘的弥漫和扩散。
⑦加强安全检查工作,设专职安全检查人员,负责施工过程中的安全管理和检查。
试桩施工工艺要求:试桩施工中,严格控制机头的钻进速度(1.8m/min)及提升速度(0.9m/min),通过正搅拌头的正、反转实现变径,注意保证反转时成扩大支盘的质量(采用停留喷浆30 秒和取得的降低提升与钻井速度的方法),用电子秤或电子自动记录仪来记录每米水泥的渗入量(要求自动记录总喷浆量及平均喷浆量)。
通过揭示(主要检验桩的垂直度和整齐度、桩体裂缝、缺损和漏桩、桩体强度和均匀性。
)成桩效果来确定最终的施工工艺参数。
对深层搅拌水泥土桩成型工艺的确定试验(主径500、扩径1000,桩长12000)(3)水泥搅拌桩单桩静载试验根据成桩工艺试验确定的工艺参数,施工单桩静力载荷试验用桩。
施工28 天后,做单桩静力载荷试验。
本工程单桩承载力要求大于70kN。
本次试验做 3 根桩。
单桩静力载荷试验的深度为现有地面下0.6 米。
试验方法:慢速维持荷载法。
加裁、卸载方法1)加荷等级可分为8~12级,总加载量不宜少于设计要求值的2 倍。
2)每加1级荷载,在加荷前后应各读记压板沉降、1次,以后每0.5h读记1次。
当1h 内沉降增量小于0.1mm 时即可加下一级荷载;对饱和粘性土地基中的振冲桩或砂石桩,1h内沉降增量小于0. 25 mm时即可加下一级荷载。
3)当出现下列现象之一时,可终止试验:①沉降急骤增大、土被挤出或压板周围出现明显的裂缝;②累计的沉降量己大于压板宽度或直径的10%;③总加载量己为设计要求值的2 倍以上4)卸荷可分3 级等量进行,每卸1 级,读记回弹量,直至变形稳定。
5)压板面积为0.79 × 0.79 m2检测数据记录表:数据处理样版(4)水泥搅拌桩复合地基静载试验:I. 根据成桩工艺试验确定的工艺参数,施工复合地基静力载荷试验用桩II. 复合地基载荷试验:施工28 天后,做复合地基载荷试验。
本工程复合地基承载力要求大于100kPa。
本次试验按三个不同桩距,每种桩距做1组,每3根桩为一组。
III. 复合地基载荷试验的深度为现有地面下0.5 米。
IV. 试验方法:慢速维持荷载法。
对复合地基,桩距 1.5 m×1.5 m,正方形布桩,荷载板采用 2.05 m×2.05 m 的正方形型钢加压板;对复合地基,桩距 2.0 m×2.0 m,正方形布桩,荷载板采用 2.50 m×2.50 m 的正方形型钢加压板;对复合地基,桩距 2.5 m×2.5 m,正方形布桩,荷载板采用 3.0 m×3.0 m的正方形型钢加压板。
检测数据记录表:(5)试验检测要求为分析深层搅拌桩相关设计参数,进行了静载单桩竖向抗压极限值试验。
作静载试验由堆砂压重平台作为反力装置,试验静荷载由安装在桩顶的油压千斤顶进行逐级加荷,桩顶沉降由对称方向安装的大量程百分表进行测读。
试验加荷方式为慢速维持荷载法,按预估极限承载力,共分10 级加荷。
在每级荷载作用下,当桩顶沉降量<0.1 mm,并在 1 h 内连续出现两次,则认为已趋稳定,再加下一级荷载,直至某一荷载下沉降急骤增大,S-Q 曲线出现明显陡降段时才终止加荷。