模具毕业设计137直三通注塑模设计说明书
注塑模具设计说明书
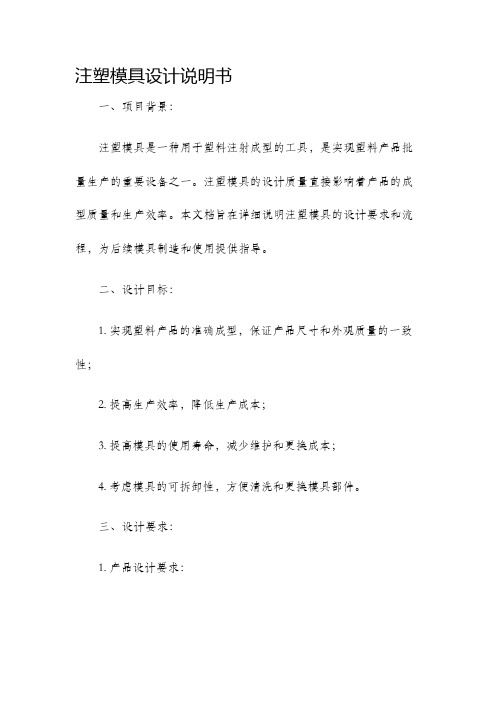
注塑模具设计说明书一、项目背景:注塑模具是一种用于塑料注射成型的工具,是实现塑料产品批量生产的重要设备之一。
注塑模具的设计质量直接影响着产品的成型质量和生产效率。
本文档旨在详细说明注塑模具的设计要求和流程,为后续模具制造和使用提供指导。
二、设计目标:1. 实现塑料产品的准确成型,保证产品尺寸和外观质量的一致性;2. 提高生产效率,降低生产成本;3. 提高模具的使用寿命,减少维护和更换成本;4. 考虑模具的可拆卸性,方便清洗和更换模具部件。
三、设计要求:1. 产品设计要求:a. 确定产品的尺寸和外观要求,提供详细的产品图纸和规格说明;b. 需要考虑产品的材料特性,如塑料的热胀冷缩性,流动性等;c. 确定产品的成型方式和注塑工艺参数。
2. 模具结构设计要求:a. 考虑产品的成型方式,确定模具的结构类型,如单腔模具、多腔模具等;b. 在满足产品尺寸和外观要求的基础上,尽量减小模具的尺寸和重量;c. 考虑模具的使用寿命,采用耐磨、耐腐蚀的材料,优化工艺和热处理;d. 考虑模具的冷却系统,保证注塑过程中材料的快速冷却和成型周期的缩短;e. 考虑模具的导向系统和定位系统,确保模具运动的准确性和稳定性;f. 考虑模具的拆卸性,方便清洗和更换模具部件。
3. 模具零件设计要求:a. 模具芯、模具腔、模具板等零件的尺寸要与产品尺寸要求一致;b. 避免尺寸过小、壁厚过薄等问题,确保零件的强度和刚性;c. 考虑零件的加工工艺,尽量减少加工难度和成本;d. 避免零件之间的干涉和碰撞,确保模具的正常运作;e. 采用标准化零件,方便制造和更换。
四、设计流程:1. 了解产品需求:与产品设计师沟通,收集产品图纸和规格说明;2. 制定模具设计方案:根据产品需求,确定模具的结构类型、尺寸和重量等;3. 进行模具设计:进行模具零件的设计,包括模具芯、模具腔、模具板等;4. 完善模具设计:考虑模具的冷却系统、导向系统、定位系统等;5. 优化模具设计:通过模拟和分析,优化模具结构和零件设计,提高模具的性能;6. 完成模具图纸:根据设计结果,绘制模具图纸,包括三维模型和二维工程图;7. 制造模具:将模具图纸提供给模具制造厂家,开始制造模具;8. 调试模具:完成模具制造后,进行模具调试和试模,保证模具的正常运行;9. 交付使用:完成模具调试后,交付给使用方,并提供模具的维护和保养指南。
注塑模型毕业设计说明书

注塑模型毕业设计说明书
注塑模型毕业设计说明书
设计背景:
注塑模型是一种广泛应用于制造业中的生产工艺,它对于零件原型的制造以及各种产品的批量生产具有重要意义。
本毕业设计的目的就是开发一种高效的注塑模型制造方案,通过对注塑机、注塑模具以及注塑温度等参数的优化设置,实现注塑模型的质量提升和处理效率的提升。
设计方法:
本设计采用了以下几种方法来实现注塑模型的优化制造:
1.优化模具结构。
采用CAD软件进行模具设计,优化模具结构、角度和片数,提高模具运行效率,节约材料成本。
2.优化注塑机设备。
根据注塑模型的特性,选择最适合的注塑机设备,采用高效的注塑技术,确保生产效率。
3.优化注塑温度。
根据不同材料的特性,制定不同的注塑温度方案,减少退火现象,并提高模型质量。
4.生产过程管理。
对于注塑模型的生产过程进行管理,提高生产效率和生产质量,确保模型质量稳定。
设计结果:
通过优化以上设计方法,本毕业设计成功实现了注塑模型的高效制造,提高了生产效率和产品质量。
本设计的成功应用,表明了优化注塑模型生产的重要性和行业应用前景。
同时,本设计也为学术研究和工业生产领域提供了支持和借鉴。
结论:
本毕业设计的目的是通过优化注塑模型制造方案,实现模型质量提升和处理效率的提升,为注塑模型的生产提供优化解决方案。
经过实验验证,本设计成果可以在实际应用中发挥重要作用,具有一定的理论与实践意义,为注塑工艺的研究和优化提供了有价值的参考。
注塑模设计-毕业设计说明书
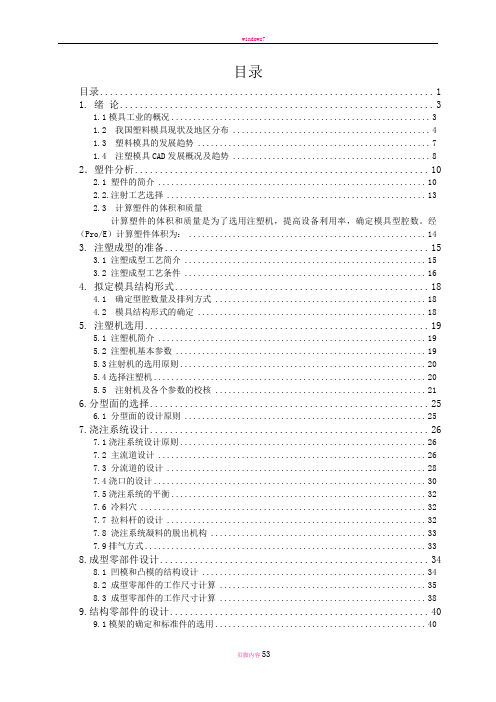
目录目录 (1)1. 绪论 (3)1.1模具工业的概况 (3)1.2 我国塑料模具现状及地区分布 (4)1.3 塑料模具的发展趋势 (7)1.4 注塑模具CAD发展概况及趋势 (8)2.塑件分析 (10)2.1 塑件的简介 (10)2.2.注射工艺选择 (13)2.3 计算塑件的体积和质量计算塑件的体积和质量是为了选用注塑机,提高设备利用率,确定模具型腔数。
经(Pro/E)计算塑件体积为: (14)3. 注塑成型的准备 (15)3.1 注塑成型工艺简介 (15)3.2 注塑成型工艺条件 (16)4. 拟定模具结构形式 (18)4.1 确定型腔数量及排列方式 (18)4.2 模具结构形式的确定 (18)5. 注塑机选用 (19)5.1 注塑机简介 (19)5.2 注塑机基本参数 (19)5.3注射机的选用原则 (20)5.4选择注塑机 (20)5.5 注射机及各个参数的校核 (21)6.分型面的选择 (25)6.1 分型面的设计原则 (25)7.浇注系统设计 (26)7.1浇注系统设计原则 (26)7.2 主流道设计 (26)7.3 分流道的设计 (28)7.4浇口的设计 (30)7.5浇注系统的平衡 (32)7.6 冷料穴 (32)7.7 拉料杆的设计 (32)7.8 浇注系统凝料的脱出机构 (33)7.9排气方式 (33)8.成型零部件设计 (34)8.1 凹模和凸模的结构设计 (34)8.2 成型零部件的工作尺寸计算 (35)8.3 成型零部件的工作尺寸计算 (38)9.结构零部件的设计 (40)9.1模架的确定和标准件的选用 (40)9.2 合模导向机构的设计 (41)10.推出机构的设计 (43)10.1 推出力的计算 (44)10.2 制品推出的基本方式 (44)11.温度调节系统的设计 (45)11.1 冷却回路的尺寸确定 (45)11.2 冷却水回路设置的基本原则 (48)11.3冷却系统的结构 (48)12.模具材料的选择 (49)12.1塑料模零件选材原则 (49)12.2 模具材料的选用 (49)13.结束语 (50)14.致谢 (51)15.参考文献 (52)1. 绪论1.1模具工业的概况模具是机械、汽车、电子、通讯、家电等工业产品的基础工艺装备之一。
注塑模具设计说明书

注塑模具设计说明书一、引言注塑模具是一种用于制造塑料制品的重要工具。
它具有精密设计和制造的特点,直接影响到注塑成型工艺的质量和效率。
本文档旨在提供一个注塑模具设计的详细说明书,以帮助使用者了解并正确使用注塑模具。
二、设计原则1. 功能性设计:注塑模具设计的首要目标是确保塑料制品的质量和精度。
需要考虑到产品的形状、尺寸、结构等因素,确保模具能够精确地复制产品的形状。
2. 可靠性设计:模具在长时间运行过程中需具有足够的可靠性和稳定性。
设计时应考虑到材料的选择、结构的合理性、工艺性能等因素,以确保模具能够长时间稳定运行。
3. 高效性设计:注塑模具的设计还要考虑到生产效率的提高。
在保证产品质量的前提下,优化流程、减少工序、提高生产速度等都是设计中需要考虑的因素。
三、设计要点1. 产品参数分析:仔细研究产品的形状、尺寸、材料等参数,并根据不同产品的要求进行合理设计。
2. 模具结构设计:根据产品的特点设计合理的模具结构,包括模具的分型面、脱模方式、冷却系统等。
3. 材料选择:根据产品和模具的要求选择合适的材料,考虑材料的韧性、硬度、耐磨性等因素。
4. 流道系统设计:设计合理的流道系统,以保证熔融塑料流动均匀,避免短流、死角等问题,提高注塑成型过程的效率。
5. 冷却系统设计:优化冷却系统的设计,保证塑料在注塑过程中能够迅速冷却固化,提高生产效率并减少翘曲、变形等问题。
6. 模具表面处理:根据产品的表面要求进行合适的模具表面处理,包括抛光、喷涂等,以提高产品的表面质量。
7. 模具装配:模具设计时应考虑装配的便利性和准确性,保证模具能够容易安装和拆卸。
四、注意事项1. 安全操作:在使用注塑模具时,必须严格遵守相关的操作规程和安全要求,保证操作人员的人身安全。
2. 维护保养:定期对模具进行清洁和维护保养,保证模具的正常运行和寿命的延长。
3. 记录维护:对模具的使用情况进行记录,包括使用次数、维修情况等,以便及时调整维修周期和保养计划。
毕业设计(注塑模具设计说明)

重庆信息技术职业学院毕业设计题目放大镜框注塑模具设计选题性质:□设计□报告□其他院系电子工程学院专业计算机辅助设计与制造班级 CAD(3)班学号 0920010314学生姓名王华东指导教师郑宏伟教务处制2011年 9 月 29 日2012 届电子工程学院毕业设计选题审批单年级 3 专业 CAD 班级 3重庆信息技术职业学院毕业设计(论文)任务书院(系)电子工程学院专业: CAD 年级: 3 级班级 3指导老师:毕业设计(论文)工作领导组组长:年月日2012 届电子工程学院毕业设计开题报告及进度要求2012 届电子工程学院毕业设计指导教师指导记录表设计题目:放大镜框注塑模具设计选题性质:□设计□其他年级: 3专业 CAD班级: 3指导教师(签名)学生(签名) 王华东注:此表由教师填写,如指导次数多,可另附纸。
目录一前言 (2)二塑件制品分析 (7)三注塑机的确定 (7)四模具设计的有关计算 (10)五模具结构设计 (10)六注塑机参数较核 (14)七模具凹凸模零件加工工艺 (15)八型腔壁厚;支承板的确定 (17)九模具冷却系统的设计 (18)十设计小结 (19)1 前言1。
1 模具工业在国民经济中的地位模具是制造业的一种基本工艺装备,它的作用是控制和限制材料(固态或液态)的流动,使之形成所需要的形体.用模具制造零件以其效率高,产品质量好,材料消耗低,生产成本低而广泛应用于制造业中。
模具工业是国民经济的基础工业,是国际上公认的关键工业。
模具生产技术水平的高低是衡量一个国家产品制造水平高低的重要标志,它在很大程度上决定着产品的质量,效益和新产品的开发能力。
振兴和发展我国的模具工业,正日益受到人们的关注。
早在1989年3月中国政府颁布的《关于当前产业政策要点的决定》中,将模具列为机械工业技术改造序列的第一位。
模具工业既是高新技术产业的一个组成部分,又是高新技术产业化的重要领域.模具在机械,电子,轻工,汽车,纺织,航空,航天等工业领域里,日益成为使用最广泛的主要工艺装备,它承担了这些工业领域中60%~90%的产品的零件,组件和部件的生产加工。
毕业设计三通管注塑模具设计

三通管注塑模具设计赵大作者李梅指导教师摘要:三通管作为一种连接件在日常生活中应用普遍。
本文主要介绍了三通管注塑模具的设计进程。
本设计通过对塑件的工艺分析,肯定其主要成型工艺参数,设计了三通管注塑模具中的各个系统,如浇注系统、导向与定位机构、侧向分型和抽芯机构、脱模机构、分型面、冷却系统及排气系统等,并对所选用的注塑机参数进行了校核,最后绘制出模具的装配总图,完本钱文的编写。
该注塑模具为双分型面结构,一模一腔,采用滚轮式滑板侧向抽芯机构,利用推杆将塑件脱出,结构合理,运行靠得住。
整个设计进程不仅利用了传统的设计方式,还运用了CAD、PRO/E等技术,大大提高了设计的效率。
本次设计能增强对注塑模具成型原理的理解,同时锻炼了注塑模具设计和制造能力。
关键词:三通管注塑模具侧抽芯Three-way Pipe Injection Mold Design Abstract:The three-way pipe as a connection in daily life is used widely. This paper introduces the process of the three-way pipe injection mold design. Through to the analysis of the technology of plastic parts, determine its main molding process parameters, the design of injection mould three-way pipe each of the system, such as gating system, orientation and the position of the institutions, side parting and core-pulling mechanism, ejection mechanism, the parting surface, cooling systems and exhaust slot. And checked the selected injection molding machine parameters, finally draw mold assembly drawing, completes the preparation. This injection mold is two joint surfaces structure,dying structure adopted one module one cavity, used the side core-pulling mechanism of a slide,using the push rod plastic parts prolapse, it is a reasonable structure, reliable operation. The whole design process not only using traditional design method, still use of the CAD, PRO / E and other technology greatly improving the design efficiency. The design of injection mould can strengthen the understanding of forming principle, while exercising the injection moldingmould design and manufacturing ability.Key words:The three-way pipe injection mold side core-pulling目录第1 章 ............................................................................................................................................................... 绪论 11.1............................................................................................................................... 塑料成型在塑料工业中的地位 11.2............................................................................................................................................ 塑料成型模具的重要性 11.3........................................................................................................................................ 塑料成型技术的进展方向 1第2 章................................................................................................................................................. 塑件工艺分析 32.1......................................................................................................................................................................... 塑件图 32.2........................................................................................................................................................ 塑件原材料分析 32.3............................................................................................................................................................. 塑件形状分析 3第3 章................................................................................................................................................. 注塑工艺设计 43.1........................................................................................................................................................ 工艺参数的计算 43.1.1................................................................................................................................ 塑件的体积和质量的计算 43.1.2注塑机的选择 (4)3.2塑件注塑成型工艺参数 (5)第 4 章注塑模具整体设计 (6)4.1注射模浇注系统设计 (6)4.1.1主流道的设计 (6)4.1.2分流道的设计 (7)4.1.3冷料穴的设计 (8)4.1.4浇口的设计 (8)4.2分型面的设计 (9)4.3排气系统的设计 (9)4.4成型零部件设计 (9)4.4.1成型零部件的结构设计 (10)4.4.2成型零部件工作尺寸的计算 (11)4.4.3模具型腔侧壁和底板厚度的计算 (13)4.5模架的选择 (13)4.6导向及脱模机构设计 (13)4.6.1导向机构设计 (13)4.6.2脱模机构设计 (15)第 5 章模具侧向分型与抽芯机构设计 (18)5.1侧向分型与抽芯机构的分类 (18)5.2侧向分型与抽芯机构的肯定 (18)5.3抽芯距和抽芯力的计算 (18)第 6 章温度调节系统的设计 (19)6.1温度调节系统的重要性 (19)6.2温度调节系统的设计计算 (19)6.3模具加热装置设计 (20)第7 章注塑机的校核 (21)7.1注射量校核 (21)7.2锁模力的校核 (21)7.3开模行程的校核 (22)7.4模具厚度的校核 (22)第8 章模具装配总图 (23)致谢 (25)参考文献: (26)第 1 章绪论1.1塑料成型在塑料工业中的地位塑料工业包括塑料生产和塑料制品生产两大部份。
注塑模具设计说明书

注塑模具设计说明书注塑模具设计说明书1.引言本文档旨在为注塑模具的设计提供详细指导和说明。
注塑模具是在注塑成型过程中必备的工具,准确的设计和制造对于生产高质量的注塑制品至关重要。
2.模具设计概述2.1 模具类型及用途2.2 模具材料选择2.3 模具尺寸和形状设定2.4 模具结构设计2.5 模具配件选择与设计3.模具主要零部件设计3.1 模具基板设计3.2 模具腔体与芯腔设计3.3 模具导向系统设计3.4 模具冷却系统设计3.5 模具强度校核3.6 模具表面处理4.注塑模具设计考虑因素4.1 塑料材料特性4.2 注塑工艺要求4.3 产品设计要求4.4 模具制造成本和周期5.模具设计流程5.1 需求分析与规划5.2 初始设计与草图5.3 详细设计与模拟分析5.4 模具制造与加工5.5 模具调试与试模5.6 模具验收和交付6.模具设计的注意事项6.1 常见设计错误与避免方法6.2 模具装配和拆卸注意事项6.3 模具维护与保养7.附件本文档涉及以下附件:- 附件1:注塑模具设计草图- 附件2:注塑模具3D模型文件- 附件3:模具设计分析报告8.法律名词及注释本文所涉及的法律名词及其相应注释如下:- 法律名词1:注塑成型工艺注释:指利用注塑设备将塑料加热并溶化,然后将熔融塑料注入模具腔中,并通过冷却固化成型的工艺。
- 法律名词2:模具基板注释:指注塑模具的基础组件,用于固定和支撑模具的其他部件,具有足够的强度和稳定性。
- 法律名词3:模具腔体与芯腔注释:模具腔体为模具中用于成型制品外形的部分,芯腔为模具中用于成型制品内部结构的部分。
9.结束语本文档详细介绍了注塑模具设计的各个方面。
通过遵循本文档中的指导和说明,设计师可以制定出高质量的注塑模具并实现优秀的注塑成型工艺。
注塑模具设计说明书
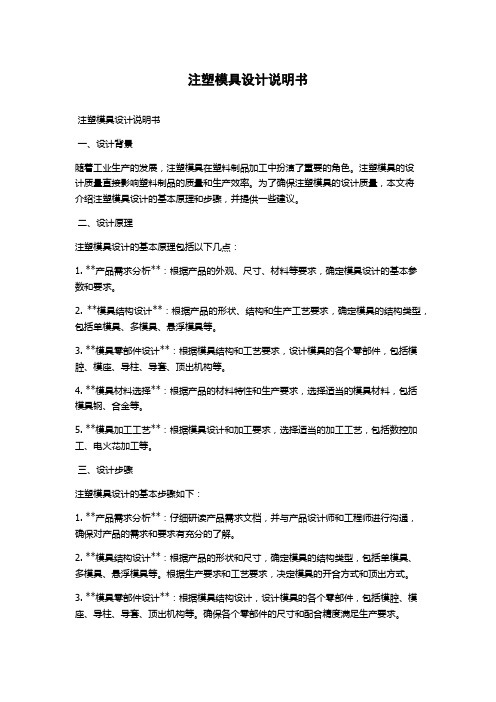
注塑模具设计说明书注塑模具设计说明书一、设计背景随着工业生产的发展,注塑模具在塑料制品加工中扮演了重要的角色。
注塑模具的设计质量直接影响塑料制品的质量和生产效率。
为了确保注塑模具的设计质量,本文将介绍注塑模具设计的基本原理和步骤,并提供一些建议。
二、设计原理注塑模具设计的基本原理包括以下几点:1. **产品需求分析**:根据产品的外观、尺寸、材料等要求,确定模具设计的基本参数和要求。
2. **模具结构设计**:根据产品的形状、结构和生产工艺要求,确定模具的结构类型,包括单模具、多模具、悬浮模具等。
3. **模具零部件设计**:根据模具结构和工艺要求,设计模具的各个零部件,包括模腔、模座、导柱、导套、顶出机构等。
4. **模具材料选择**:根据产品的材料特性和生产要求,选择适当的模具材料,包括模具钢、合金等。
5. **模具加工工艺**:根据模具设计和加工要求,选择适当的加工工艺,包括数控加工、电火花加工等。
三、设计步骤注塑模具设计的基本步骤如下:1. **产品需求分析**:仔细研读产品需求文档,并与产品设计师和工程师进行沟通,确保对产品的需求和要求有充分的了解。
2. **模具结构设计**:根据产品的形状和尺寸,确定模具的结构类型,包括单模具、多模具、悬浮模具等。
根据生产要求和工艺要求,决定模具的开合方式和顶出方式。
3. **模具零部件设计**:根据模具结构设计,设计模具的各个零部件,包括模腔、模座、导柱、导套、顶出机构等。
确保各个零部件的尺寸和配合精度满足生产要求。
4. **模具材料选择**:根据产品的材料特性和生产要求,选择适当的模具材料,包括模具钢、合金等。
考虑模具材料的硬度、强度、耐磨性和耐腐蚀性等因素。
5. **模具加工工艺**:根据模具设计和加工要求,选择适当的加工工艺,包括数控加工、电火花加工等。
确保模具的加工精度和表面质量符合要求。
四、设计要点在注塑模具设计过程中,需要注意以下要点:- **结构合理性**:模具的设计结构应合理、紧凑,尽量减少杂散空间和无效运动。
塑料三通模具设计说明书

塑料三通模具设计说明书厦门工学院毕业设计(论文)厦门工学院本科生毕业设计(论文)题目:三通管注塑模具设计姓名:钟磊学号: 1202104042系别:机械系专业:机械工程及自动化年级:机械4班指导教师:郑清娟年月日IV厦门工学院毕业设计(论文)独创性声明本毕业设计(论文)是我个人在导师指导下完成的。
文中引用他人研究成果的部分已在标注中说明;其他同志对本设计(论文)的启发和贡献均已在谢辞中体现;其它内容及成果为本人独立完成。
特此声明。
论文作者签名:日期:关于论文使用授权的说明本人完全了解厦门工学院有关保留、使用学位论文的规定,即:学院有权保留送交论文的印刷本、复印件和电子版本,允许论文被查阅和借阅;学院可以公布论文的全部或部分内容,可以采用影印、缩印、数字化或其他复制手段保存论文。
保密的论文在解密后应遵守此规定。
论文作者签名:指导教师签名:日期IV厦门工学院毕业设计(论文)三通管注塑模具设计摘要根据塑料制品的性能要求,了解自然和塑料部件,分析过程中,尺寸精度表面粗糙度等技术要求的塑料件的目的,选择塑料零件的大小。
附上说明书,系统使用简短的文字公式和计算,以及其他的图表和简明的分析和形状与塑件的性能的计算,以做出合理的模具设计。
模具的发展也是比较快速的,很多领域都应用广泛,特别是一些生活家用品几乎都是由模具做出来生产的,而塑料制品也是越来越广泛的应用于生活中。
关键词:UG绘制3D图:注射机的选择:机械设计:模具设计:CAD绘制二维图:三通管IV厦门工学院毕业设计(论文) English the moldTake toAccording to the plastic products requirements, understand the use of plastic parts, plastic parts of the process analysis, dimensional accuracy and other technical requirements, selection of plastic parts size. The use of a mold of a mold two, a side gate feed, injection machine uses the Haitian 80X1A models, cooling system, CAD and PROE mapping of2D assembly drawing and parts drawing, mold reasonable processing method. Enclose brochures, the systematic use of a brief text, concise schematic diagram and calculation analysis of plastic parts, so as to makereasonable mold design.Key words: mechanical design; mold design; CAD drawing two-dimensionalmap; PROE rendering3D map, the choice of injection machineIV厦门工学院毕业设计(论文)目录摘要 .......................................................... III 第1章绪论 . (1)1.1 1.2塑料简介 ................................................. 1 注塑成型及注塑模 .. (1)第2章塑料材料分析 (3)2.1 塑料材料的基本特性 ........................................ 3 2.2. PVC的性能指标 ............................................ 3 2.3. 塑件材料成型性能 .......................................... 3 2.4. 塑件材料主要用途 .......................................... 3 第3章塑件的工艺分析 (4)3.1 塑件的结构设计 ............................................ 4 3.2 塑件尺寸及精度 ............................................ 5 3.3 塑件表面粗糙度 ............................................ 6 3.4 塑件的体积和质量 .......................................... 6 第4章注射成型工艺方案及模具结构的分析和确定 (7)4.1、注射成型工艺过程分析[5] .................................... 9 4.2 浇口种类的确定 ........................................... 7 4.3 型腔数目的确定 ............................................ 8 4.4 注射机的选择和校核 (8)4.4.1 注射量的校核 (9)第5章注射模具结构设计 (11)5.1 分型面的设计 ............................................. 11 5.2 型腔的布局 ............................................... 13 5.3 浇注系统的设计 . (14)5.3.1 浇注系统组成 ...................................... 14 5.3.2确定浇注系统的原则 ................................ 14 5.3.3 主流道的设计 ...................................... 15 5.3.4 分流道的设计 ...................................... 16 5.3.5 浇口的设计 (16)IV感谢您的阅读,祝您生活愉快。
直三通设计说明书

塑件分析三通头塑件结构如图1-1所示。
图1-1 注塑零件图该零件尺寸中等大小,平均厚度1.8mm,最大厚度2mm,最小厚度1mm。
根据各材料的注塑性能及加工使用性能,选择材料为PVC。
塑件的成型工艺分析成型工艺分析精度等级:采用一般精度5级。
脱模斜度:该注塑零件壁厚约为1.8mm,其脱模斜度查表有塑件内表面35′~1°,塑件外表面40′~1°20′。
由于该塑件没有特殊狭窄细小部位,所用塑料为PVC,流动性较好,而且,主要部分有较好的弧度,可顺势脱模,所以塑件外表面没有放脱模斜度。
同时,侧面采用滑块机构,脱模时,滑块抽去,两壁处脱模没有困难,所有也不放脱模斜度。
1分型面位置的确定分型面的选择原则(1)有利于保证塑件的外观质量;(2)分型面应选择在塑件的最大截面处;(3)尽可能使塑件留在动模一侧;(4)有利于保证塑件的尺寸精度;(5)尽可能满足塑件的使用要求;(6)尽量减少塑件在合模方向上的投影面积;(7)长型芯应置于开模方向;(8)有利于排气;(9)有利于简化模具结构。
确定型腔数量及排列方式当分型面确定之后,就需要考虑是采用单型腔模还是多型腔模。
一般来说,大中型塑件和精度要求高的小型塑件优先采用一模2腔的结构,但对于精度要求不高的小型塑件(没有配合精度要求),形状简单,又是大批量生产时,若采用多型腔模具可提供独特的优越条件,使生产效率大为提高。
故由此初步拟定采用一模2腔。
注射机型号的确定注射机规格的确定主要是根据塑件的大小及型腔的数目和排列方式,在确定模具结构形式及初步估算外形尺寸的前提下,设计人员应该对模具所需的注射量、锁模力、注射压力、拉杆间距、最大和最小模厚、推出形式、推出位置、推出行程、开模距离等进行计算。
根据这些参数,选择一台和模具匹配的注射机,对其进行校核。
21.所需注射量的计算(1)塑件质量、体积计算:对于该设计,建立塑件模型,并用软件对此模型分析得:塑料制件体积V1=44.2713cm;塑料制件质量M1=46.5g。
三通管注塑模具设计说明书

三通管注塑模具设计说明书:三通管注塑模具设计说明书1. 引言本文档为三通管注塑模具的设计说明书,旨在详细介绍模具设计的要求和流程。
通过该说明书,设计人员能够了解模具设计的具体步骤和相关要素,确保模具设计满足产品生产的需求。
2. 模具设计概述2.1 产品概述介绍三通管产品的基本信息,包括外观、尺寸、材料等。
2.2 模具设计目标明确模具设计的目标,如生产效率、质量要求、成本控制等。
2.3 模具设计流程详细描述模具设计的流程,包括产品分析、结构设计、零件设计、装配设计、模具材料选择等。
3. 产品分析3.1 产品功能描述三通管产品的功能和用途。
3.2 工艺要求介绍三通管产品的生产工艺要求,包括注塑工艺参数、模具使用寿命等。
3.3 市场需求分析目标市场对三通管产品的需求,为模具设计提供参考。
4. 结构设计4.1 结构设计原则三通管模具设计的基本原则,如结构合理性、易于制造等。
4.2 模具结构图提供三通管模具的结构图,包括模具整体结构、分模结构等。
4.3 模腔设计根据产品要求,设计三通管模腔的形状和尺寸。
5. 零件设计5.1 模具主要零件三通管模具的主要零件,如模架、模腔、导柱等。
5.2 零件制造工艺描述三通管模具零件的制造工艺,如加工方式、检测要求等。
6. 装配设计6.1 模具装配方案根据模具结构和零件设计,设计三通管模具的装配方案。
6.2 模具装配图提供三通管模具装配图,包括零件的安装位置和顺序。
7. 模具材料选择根据产品要求和工艺要求,选择适合的模具材料。
8. 附件列出本文档所涉及的附件清单,如结构图、装配图等。
9. 法律名词及注释列出文档中涉及的法律名词,并提供相应的注释说明。
10. 结束语本文档详细介绍了三通管注塑模具的设计说明,旨在确保模具设计满足产品生产的需求。
通过遵循本文档的设计要求,可以提高模具的生产效率和质量。
《注塑模设计》毕业设计指导书
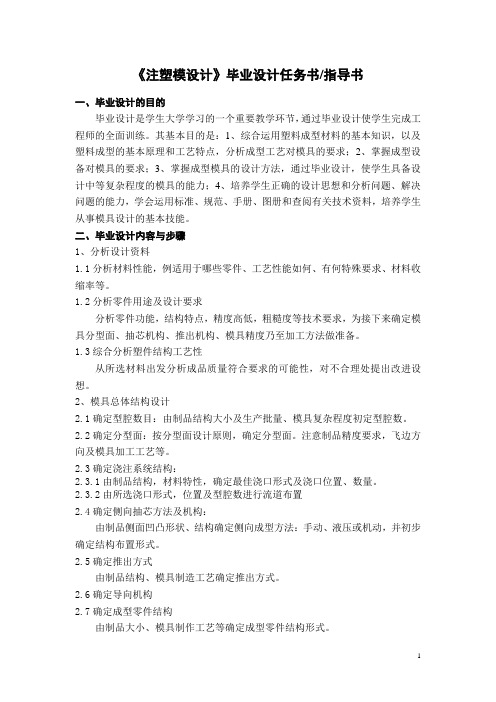
《注塑模设计》毕业设计任务书/指导书一、毕业设计的目的毕业设计是学生大学学习的一个重要教学环节,通过毕业设计使学生完成工程师的全面训练。
其基本目的是:1、综合运用塑料成型材料的基本知识,以及塑料成型的基本原理和工艺特点,分析成型工艺对模具的要求;2、掌握成型设备对模具的要求;3、掌握成型模具的设计方法,通过毕业设计,使学生具备设计中等复杂程度的模具的能力;4、培养学生正确的设计思想和分析问题、解决问题的能力,学会运用标准、规范、手册、图册和查阅有关技术资料,培养学生从事模具设计的基本技能。
二、毕业设计内容与步骤1、分析设计资料1.1分析材料性能,例适用于哪些零件、工艺性能如何、有何特殊要求、材料收缩率等。
1.2分析零件用途及设计要求分析零件功能,结构特点,精度高低,粗糙度等技术要求,为接下来确定模具分型面、抽芯机构、推出机构、模具精度乃至加工方法做准备。
1.3综合分析塑件结构工艺性从所选材料出发分析成品质量符合要求的可能性,对不合理处提出改进设想。
2、模具总体结构设计2.1确定型腔数目:由制品结构大小及生产批量、模具复杂程度初定型腔数。
2.2确定分型面:按分型面设计原则,确定分型面。
注意制品精度要求,飞边方向及模具加工工艺等。
2.3确定浇注系统结构:2.3.1由制品结构,材料特性,确定最佳浇口形式及浇口位置、数量。
2.3.2由所选浇口形式,位置及型腔数进行流道布置2.4确定侧向抽芯方法及机构:由制品侧面凹凸形状、结构确定侧向成型方法:手动、液压或机动,并初步确定结构布置形式。
2.5确定推出方式由制品结构、模具制造工艺确定推出方式。
2.6确定导向机构2.7确定成型零件结构由制品大小、模具制作工艺等确定成型零件结构形式。
2.8确定温度调节系统由材料工艺特性确定温度调节方法,若需加热,确定加热方法及加热装置大致安装位置。
若需冷却,确定冷却方式及大致位置。
2.9确定模具支撑零件结构2.10绘制模具总体结构草图3、模具零件结构尺寸设计3.1初选设备3.1.1计算制品体积及重量3.1.2结合型腔及浇注系统初定注射容量3.1.3根据容量初选注射机3.1.4纪录所选注射机主要参数额定注射量、注射行程、合模力、最大成型面积、最大开模行程、模具最大厚度、模具最小厚度、拉杆空间、动、定模固定板尺寸、推出方式及有关尺寸、喷嘴有关尺寸、定位圈尺寸等。
三通管注塑模模具设计说明书样本

三通管注塑模模具设计目录第1章塑件的工艺分析.................... 错误!未定义书签。
2 -1.1塑件分析............................. 错误!未定义书签。
1.2塑料件的原材料分析................... 错误!未定义书签。
1.3 塑料件的结构、尺寸精度、及表面质量分析错误!未定义书签。
第2章注射机的选择......................... 错误!未定义书签。
2.1 制件体积的计算....................... 错误!未定义书签。
2.2 注射机的选择......................... 错误!未定义书签。
2.3 注射机的校核......................... 错误!未定义书签。
2.3.1最大注射量的校核................ 错误!未定义书签。
2.3.2最大注射压力的校核.............. 错误!未定义书签。
2.3.3锁模力的校核.................... 错误!未定义书签。
第3章模具结构方案的确定.................... 错误!未定义书签。
3.1 分型面的选择......................... 错误!未定义书签。
3.2 型腔的排列方式....................... 错误!未定义书签。
3.3 浇注系统的设计....................... 错误!未定义书签。
3.3.1 主流道的设计.................... 错误!未定义书签。
3.3.2 分流道的设计.................... 错误!未定义书签。
3.3.3 浇口设计........................ 错误!未定义书签。
3.4 推出机构的设计....................... 错误!未定义书签。
注塑模毕业设计说明书

注塑模毕业设计说明书本文是一份有关注塑模的毕业设计说明书,主要包括以下几个方面:背景介绍、问题陈述、研究目的、研究内容、研究方法、预期成果、研究意义和可行性分析等。
一、背景介绍注塑模是工业生产中常用的一种生产工艺,包括各类塑料、橡胶、金属以及陶瓷等材料的注塑成型加工技术。
随着我国制造业的发展,注塑模产业也在逐步壮大,成为一个重要的支柱产业。
然而,由于注塑模的特殊性,其制造周期较长、成本较高,导致许多企业难以满足其快速发展的需求。
目前,注塑模的生产制造仍存在许多问题,主要包括:制造周期长、成本高、生产效率低、精度不高等。
因此,研究如何提高注塑模的生产效率和精度,并降低成本,已成为当前注塑模产业的瓶颈问题。
二、问题陈述注塑模的生产制造存在多方面的问题,主要包括:1、生产周期长:注塑模的制造周期长,需要经过多次设计、加工、检测、调整等步骤,生产过程中容易出现各种问题,从而导致生产周期延长。
2、成本高:注塑模的制造成本较高,主要由于材料、加工工艺和设备等方面的原因。
3、生产效率低:注塑模生产效率低下,以及部分企业没有建立完善的生产管理体系,导致生产效率低下。
4、精度不高:注塑模的加工精度不高,存在的问题主要是加工精度低,产品的精度也无法保证。
三、研究目的为了解决注塑模生产制造存在的问题,研究如何提高注塑模的生产效率和精度,降低成本,本研究的目的是:1、分析注塑模生产制造中存在的问题及原因,确定改进措施。
2、研究注塑模加工精度的影响因素,探索如何提高注塑模加工精度。
3、通过调查与分析,寻找比较成熟、适应企业实际情况的注塑模生产和管理模式。
四、研究内容1、注塑模生产制造问题的分析和研究:对注塑模的生产制造过程进行分析,找出其中存在的问题与原因,并提出改进措施。
2、注塑模加工精度的影响因素研究:通过模具结构设计、制作CAD模型、数字化加工等手段,研究注塑模加工精度的影响因素。
3、注塑模生产和管理模式的研究:对注塑模的生产和管理模式进行调查与研究,寻找适合企业的管理模式,并提出改进建议。
- 1、下载文档前请自行甄别文档内容的完整性,平台不提供额外的编辑、内容补充、找答案等附加服务。
- 2、"仅部分预览"的文档,不可在线预览部分如存在完整性等问题,可反馈申请退款(可完整预览的文档不适用该条件!)。
- 3、如文档侵犯您的权益,请联系客服反馈,我们会尽快为您处理(人工客服工作时间:9:00-18:30)。
届毕业设计说明书直三通注塑模设计系、部:机械工程系学生姓名:指导教师:颜家福/唐田秋职称讲师/副教授专业:材料成型及控制工程班级:完成时间:摘要三通管作为一种连接件在日常生活中应用广泛,本文对塑料模具的设计方法及过程进行了阐述。
包括了塑件结构的分析和材料的选择,拟定模具结构形式、注塑机型号的选择,浇注系统的形式和浇口的设计、成型零件的设计、模架的确定和标准件的选用。
合模导向机构的确定、脱模推出机构的确定,侧向分型与抽芯机构的设计、排气系统的设计、模具温度调节系统的设计、典型零件制造工艺、模具材料的选用等。
关键词三通管;注塑模;导向;分型;脱模ABSTRACTThe Three Links Pipeline as a kind of attachment is widely used in daily life. In the paper, the design method and processes of the plastics mould have been described. including the structural analysis and material selection of the plastic, drawing up the mold structural style, selection of the injection molding machine, the form of feed system and the design of the runner, the design of shaped parts, mold-determination and selection of standards, the oriented institutions to identify for mold clamping, the determination of ejector organization for de-molding, the design of lateral core-pulling organization, the design of the mold pumping system, the design of the system for controlling the mold temperature, the manufacturing processes of typical components, selection of the mold material and so on.Keywords Three links pipeline; Injection mould; director; joint face; stripping目录1 前言 (1)1.1 我国塑料模具工业的发展现状 (1)1.2 国际塑料模具工业的发展现状 (1)1.2.1 网络的CAD/CAE/CAM一体化系统结构初见端倪 (2)1.2.2 AM软件日益深人人心并发挥越来越重要的作用 (2)1.2.3 AM软件的智能化程度正在逐渐提高 (2)1.2.4 设计与3D分析的重要性更加明确 (2)1.3 我国塑料模具工业和技术今后的主要发展方向 (3)1.4 本次设计的目的 (4)2塑件成型工艺性分析 (5)2.1 塑件(直三通)分析 (5)2.1.1 塑件图(因使用需要对原式样有所改进 (5)2.1.2 塑件分析 (5)2.1.3 成型工艺分析如下 (5)2.2 ABS的注射成型过程及工艺参数 (6)2.2.1 注射成型过程 (6)2.2.2 ABS的注射工艺参数 (6)2.2.3 ABS化学和物理特性 (7)2.2.4 ABS塑料的主要技术指标 (8)3 拟定模具结构形式 (9)3.1 分型面的选择 (9)3.1.1 分型面的选择原则 (9)3.1.2 分型面的确定 (9)3.2 型腔数目的确定 (10)4注塑机型号的确定 (11)4.1 所需注射量的计算 (11)4.2 塑件和流道凝料在分型面上的投影面积及所需锁模力的计算 (11)4.3 选择注射机 (12)4.4 注射机有关参数的校核 (13)4.4.1 型腔数量的校核 (13)4.4.2 注射机工艺参数的校核 (13)4.4.3 安装尺寸 (14)4.4.4 开模行程的校核 (14)4.4.5 模架尺寸与注射机拉杆内间距校核 (14)5浇注系统的形式和浇口的设计 (15)5.1 主流道的设计 (15)5.1.1 主流道设计要点 (15)5.1.2 主流道尺寸 (15)5.1.3 主流道衬套的形式 (16)5.1.4 主流道衬套的固定 (17)5.2 冷料穴的设计 (17)5.3 分流道的设计 (19)5.3.1 分流道的布置形式 (19)5.3.2 分流道的长度 (19)5.3.3 分流道的形状及尺寸 (19)5.3.4 分流道的表面粗糙度 (20)5.4 浇口的设计 (20)5.4.1 浇口的形式 (21)5.4.2 浇口类型的选择 (21)5.4.3 浇口位置的选择 (22)5.4.4 浇口的尺寸的确定 (22)5.5 浇注系统的平衡 (22)5.6 浇注系统凝料体积计算 (22)5.7 浇注系统各截面流过熔体的体积计算 (23)5.8 普通浇注系统截面尺寸的计算与校核 (23)5.8.1 确定适当的剪切速率 (23)5.8.2 确定主流道体积流率 (23)5.8.3 注射时间(充模时间)的计算 (24)5.8.4 校核各处剪切速率 (24)6 成型零件的结构设计和计算 (26)6.1 成型零件的结构设计 (26)6.2 成型零件工作尺寸的计算 (26)6.3 型腔零件强度、刚度的校核 (30)6.3.1 根据侧壁厚度校核强度、刚度 (30)6.3.2 根据底板厚度校核强度、刚度 (31)7 模架的确定和标准件的选用 (33)8 合模导向机构的设计 (35)8.1 导向结构的总体设计 (35)8.2 导柱设计 (35)8.3 导套设计 (36)9 脱模推出机构的设计 (37)9.1 脱模力的计算 (37)9.2 脱模机构的结构设计 (38)10 侧向抽芯机构的设计 (39)10.1 抽芯距与抽芯力的计算 (39)10.2 斜导柱截面尺寸的确定 (40)10.3 楔紧块的设计 (41)11 排气系统的设计 (43)12 温度调节系统设计 (44)12.1 冷却时间的计算 (44)12.2 冷却管道传热面积及管道数目的简易计算 (45)13 典型零件的制造加工工艺 (48)13.1 带头导柱的制造工艺 (48)13.2 编程零件及刀具选择 (49)13.3 切削用量确定 (49)13.4 编制加工程序 (49)14 设计小结 (51)参考文献 (52)致谢词 (53)附录 (54)1 前言1.1我国塑料模具工业的发展现状80年代以来,在国家产业政策和与之配套的一系列国家经济政策的支持和引导下,我国模具工业发展迅速,年均增速均为13%,1999年我国模具工业产值为245亿, 2003年模具进出口统计中,我国模具的出口总额为2.52亿美元,我国模具的出口总额3亿美元,进口额则达到13亿多美元,在进口模具中的塑料模具占到50%左右。
可以看出,在塑料模具方面,我国与国外产品还存在较大差距。
在引进的塑料模具中,以科技含量较高的模具居多,如高精度模具、大型模具。
热流道模具、气辅及高压注射成型模具等。
现代塑料制品对表面光洁度、成型时间都提高了更高的要求,因而也推动了塑料模具的发展。
以电视机塑料外壳模具为例。
其精度已由以前的0.05~0.1mm提高到0.005~0.01mm ,制造周期也由8个月缩短到了2个月,并且使用寿命也由过去可制10万~20万件制品延长到了可60万件制品。
从电视机外壳塑料模具的发展可以看到,高精密、长寿命、短周期、低成本是模具的发展方向。
目前我国使用覆盖率和使用量最大的模具标准件为冷冲模架、注塑模架和推杆管这三类产品。
以注塑模架为例,目前全国总产值有20多亿元,按照需求,国内约需注塑模架30多亿元,而实际上国内市场并未达到这个规模,其中主要一个原因就是模具厂家观念旧,注塑模架自产配比例较高,外购很少。
这样做厂家不仅重复制造本应标准化的购件,延长了模具生产周期,又不利于维修。
很多相关的模具标准件并没有相关的国家标准,因此制定模具构件的标准规范工作也是当务之急。
1.2 国际塑料模具工业的发展现状美国1991年发表的“国家关键技术报告”认为:材料领域的进展几乎可以显著改进国民经济所有部门的产品性能,提高它们的竞争能力;因此把材料列为六大关键技术的首位。
这是由于先进材料与制造技术是未来国民经济与国防力量发展的基础,是各种高、新技术成果转化为实用产品与商品的关键。
当前各种新材料市场规模超过1000亿美元,预计到2000年将达4 000亿美元。
由新材料带动而产生的新产品新技术则是一个更大的市场。
以上参展项目基本上代表了当前国际和国内的先进水平和发展趋势,具体表现在如下五个方面。
1.2.1网络的 CAD/CAE/CAM一体化系统结构初见端倪。
随着计算机硬件与软件的进步以及工业部门的实际需求,国外许多著名计算机软件开发商已能按实际生产过程中的功能要求划分产品系列,在网络系统下实现了CAD/CAM 的一体化。
解决了传统混合型CAD/CAM系统无法满足实际生产过程分工协作要求的问题,以便更能符合实际应用的自然过程。
例如英国达尔康公司在原有软件DUCT5的基础上,为适应最新软件发展及工业生产实际而在最近推出的CAD/CAM集成化系统Delcam's Power Solution,该系统覆盖了几何建模、逆问工程、工业设计、工程制图、仿真分析、快速原型、数控编程、测量分析等领域。
1.2.2 AM软件日益深人人心并发挥越来越重要的作用在90年代,能进行复杂形体几何造型和NC加工的CAD/CAM系统主要是在工作站上采用UNIX操作系统开发和应用的,如美国的Pro-E、UGⅡ、CADDS 5软件,法国的 CATIA、EUCLID软件和英国的DUCT5软件等。
随着微机技术的突飞猛进、在90年代后期,新一代的微机CAD/CAM软件,如Solidworks、Solid adae崭露头角,深得用户的好评。
这些微机软件不仅在采用诸如NURBS曲面、三维参数化特征造型等先进技术方面继承了工作站级CAD/CAM软件的优点,而且在Windows风格、动态导航、特征树、面向对象等方面具有工作站级软件所不能比拟的优点。
1.2.3 AM软件的智能化程度正在逐渐提高由于在现阶段,模具设计和制造在很大程度上仍然依靠着模具设计与制造工程师的经验。