粉末冶金摩擦材料-培训教材
【培训课件】粉末冶金PPT
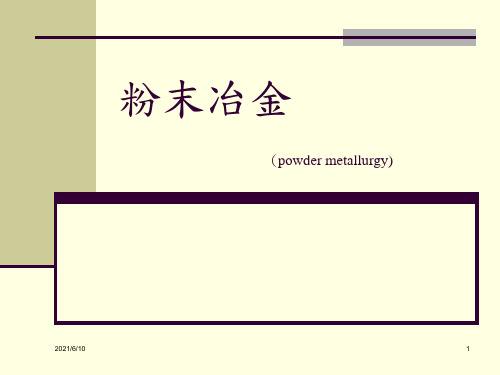
工业生产用的大型HIP的使用温度有1200、 1400、20000C
工作物承受的是各方向均等的成形压力,故其 密度、物理和机械性质均具良好的等方性。
2021/6/10
48
热均压成型示意图
2021/6/10
49
HIP的优点
1、易于维护的管路系统。 2、工作物之装卸方式采底部进出方式。 3、装有微处理机控制系统。 4、保护用的环墙厚壁。
2021/6/10
55
烧结机构示意图
2021/6/10
56
2021/6/10
57
烧结炉的简介
金属网带炉 驼背式炉筛网输送带式炉 滚轮式。
2021/6/10
58
将压粉体加中的润滑剂在烧结前先去除。 脱腊
使烧结炉内的气体不因外在气体(氢、水气…) 侵入而受影响。 气密性
2021/6/10
66
烧结耐热材料
在高温时,具有良好的机械性质、耐氧化性 及耐腐蚀性。
可得较细渡化的粉粒。 优点:资源回收再利用 缺点: 1.无法控制粉末特性 2.生产缓慢
2021/6/10
17
一、机械制造法
球磨
2021/6/10
18
一、机械制造法
球磨 不适用:易生冷焊现象、具延展性的材料 适用:脆性材料
缺点: 1.能量在噪音及摩擦热的消耗大 2.粒度越小所需要的时间和能量相对很大 3.粉末加工硬化、不规则形状、堆积性不良
不规则的粉末在搬运的时候易改变其密度。 圆球状的粉末最安定。
结论:将粉末充分的研磨以减低其形状的影响。
2021/6/10
38
在研磨时受氧化程度及冷作加工的影响。
氧化程度
粉末冶金摩擦材料

粉末冶金摩擦材料
• 用粉末冶金的方法制成的、具有高摩擦系 数和高耐磨性的金属与非金属组成的材料, 也称烧结摩擦材料。 • 粉末冶金摩擦材料的成分是由三部分组成 1.机体组元 其中基体组元保证材料的承受能力、热稳 定性和耐磨性,它占摩擦材料质量的50%-90%。 辅助组元则是用来改善基本组元的性能;
2.润滑组元 一般用石墨和铅,也可用铋代替铅,它一 般占摩擦材料质量的5%-25%,有利于材料的 抗卡性能和抗粘结性能,提高材料的耐磨性; 3.摩擦组元 多用二氧化硅、石绵、碳化硅、三氧化二 铝、氮化硅等,其作用是可以提高摩擦材料 的摩擦系数和耐磨性,防止焊接。
铜基摩擦材料工艺性能好,摩擦系数稳定, 抗粘结抗卡、滞性能好。 铁基的摩擦材料在高温高负荷下能显示出更 良好的摩擦性能,机械强度高,可在4001100度范围内使用。 为了增加粉末冶金摩擦材料的强度,通常将 其粘结在钢背上而成为双金属结构。 其工艺流程如图: 铜基:钢芯板→镀铜→镀锡 原料粉末→混合→压制
1-3摩擦材料讲座2

A鼓式刹车片B卡车刹车片C半锥刹车片 D全锥刹车片E倒角
盘式刹车片部件的名称 A chamfer 倒角
B groove, slot 槽
C frictionmaterial 摩擦 材料
D wear indicator cable 磨损指示器
铜纤维和粉末 copper fibre andpowder10-20 %
碳纤维和其它纤维 arbon and other fibre 10-
30%
有机黏合剂 organic bond4- 8%
无机黏合剂 inorganic ceramic bond10-20 %
摩擦调整剂 friction modified10-30 %
5煅烧氧化铝Fused Alumina (Alundum) 6硫化锑Antimony Trisulphide
7重晶石Barytes 8玄武岩纤维:Basalt Fibers
9铁黑Iron Oxide (Magnetite) 10黄铜末 brass chip
11青铜粉Bronze Powder 12碳酸钙Calcium Carbonate (Whiting)
三:摩擦材料的原料 B:增强材料
无机纤维:石棉,玻璃纤维,岩石棉,硅酸铝 纤维,海泡石纤维,水镁石纤维,矿棉,硅灰 石
有机纤维:芳伦,炭纤维,炭纤维预氧丝,纤 维素纤维,丙稀氰纤维,尼龙纤维,麻纤维, 纸纤维,粘胶纤维.粉碎型,浆泊型
纤维素纤维图片(浆泊型)
摩擦材料的原料 C润滑剂
含碳润滑剂: 天然石墨(鳞片,土状),人造石墨 焦碳,煤, 其他润滑剂: 硫化物,二硫化钼,有机物,四氟乙烯硬脂酸
三:摩擦材料的原料
教育训练—粉末冶金基础知识培训

如图凸缘另一侧为盲孔.成形困难. 可改为又图设计
制品形状设计参考(模具顶出限制)
不佳设计
良好设计
解说
螺旋齿: 螺旋角大于30度不易成形 正常在25度范围内可以顺利生产
滚花:
钻石滚花无法成形,与加压方向平 行的直齿滚花易于成形
制品形状设计参考(粉末充填限制)
不佳设计
良好设计
解说
孔的位置: 孔的位置尽量避开外缘部,尽量能 在2mm以上
测
温压
渗铜
渗
完成
碳
品
产品应用
直齿零件类型
产品应用
斜齿零件类型
产品应用
家电零件类型
产品应用
家电类型
产品应用
汽车零件类型
产品应用
汽车零件类型
产品应用
汽车零件类型
产品应用
园林工具零件 类型
产品应用
组装零件类型
产品应用
轴承零件类型
粉末冶金原材料
金属粉末 非金属粉末 添加剂
原材料
生产工艺(搅拌)
翼端角,尖角:
避免翼端角,尖角,为保模具安全及 粉末充填均匀,应如图所示加R
制品形状设计参考(粉末充填限制)
不佳设计
良好设计
解说
锲形: 尖端有锲形时粉末不易充填, 平坦过渡形状较佳
栓槽形:
细小形状的栓槽形,不易粉末充填 及加压成形,作成如右圆弧形粉末 充填较好
制品形状设计参考(粉末充填限制)
不佳设计
模具
产品
成形原理方式
成形压制过程
成形压坯的特点
只有一定的强度,还不具备金属的 性能, 稍微外力的撞击会使它发生变形、缺损、 断裂等 现象
所以产品在拿取、搬运过程中必须轻拿 轻放!
粉末冶金培训资料

01
02
03
04
粒度与粒度分布
粉末的粒度大小和粒度分布对 粉末冶金制品的性能有重要影
响。
密度与松装密度
粉末的密度和松装密度决定了 压制和烧结过程中的性能。
流动性与压缩性
粉末的流动性和压缩性对填充 模具和压制坯件的性能有影响
。
化学成分与纯度
粉末的化学成分和纯度对粉末 冶金制品的性能和质量有重要
影响。
粉末的处理与储存
粉末冶金零件的制造过程具有高效、环保等优点,符合电子工业可持续 发展的需求。
其他领域
除了上述领域外,粉末冶金零件还广泛应用于医疗器械、石 油化工、能源等领域。
在这些领域中,粉末冶金零件因其优异的性能和适应性强的 特点而受到广泛应用,为各行业的科技进步和可持续发展做 出了重要贡献。
06
粉末冶金技术发展趋势与挑战
面临的挑战与问题
01
02
03
技术更新换代
随着科技的不断进步,粉 末冶金技术需要不断更新 换代,以适应市场需求的 变化。
环保法规的制约
随着环保法规的日益严格 ,粉末冶金行业需要采取 有效措施降低环境污染。
高成本与低附加值
粉末冶金产品成本较高, 附加值较低,需要加强技 术创新和提高产品质量。
未来发展方向
由于粉末冶金零件具有高强度、 低重量、耐腐蚀等优点,因此在 提高汽车燃油效率和减少排放方
面具有显著优势。
粉末冶金零件的生产效率高,可 以大幅度降低生产成本,提高汽
车的整体性能和竞争力。
航空航天
在航空航天领域,粉末冶金零件因其 具有优异的力学性能、高温性能和可 靠性而被广泛应用于飞机和火箭的结 构件和功能件。
03
粉末冶金工艺流程
摩擦材料技术培训
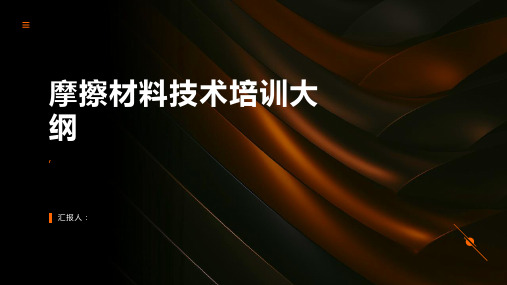
质量控制和可靠性评估
质量控制:制定严 格的生产标准和检 测流程确保产品质 量
可靠性评估:通过 模拟实际使用环境 进行测试评估产品 的使用寿命和性能 稳定性
检测方法:采用先 进的检测技术和设 备确保检测结果的 准确性和可靠性
标准制定:根据行 业标准和客户需求 制定符合实际需求 的技术标准和检测 方法
采用智能化技术提 高摩擦材料的性能 和寿命
开发多功能摩擦材 料满足不同领域的 需求
未来发展前景和市场预测
市场需求:随 着汽车、机械、 电子等行业的 发展摩擦材料 的市场需求将
持续增长
技术发展趋势: 环保、节能、 高效、长寿命 等将成为摩擦 材料技术的发
展方向
市场竞争:国 内外企业竞争 激烈需要不断 提高产品质量
热处理和表面处理
热处理:通过加热和冷却改变材料性能如淬火、退火等 表面处理:通过化学或物理方法改变材料表面性能如电镀、喷涂等 热处理和表面处理的目的:提高摩擦材料的耐磨性、耐腐蚀性和抗疲劳性 热处理和表面处理的应用:广泛应用于汽车、机械、航空航天等领域
05 摩擦材料的应用实例
汽车制动器摩擦片
应用领域:汽车制动系统 作用:提高制动性能保障行车安全 材料类型:陶瓷、金属、有机材料等 设计要求:耐磨、耐高温、耐腐蚀、抗冲击等 制造工艺:压制、烧结、涂装等 性能测试:制动力、磨损、噪音等
07
摩擦材料的市场分析和 未来发展前景
国内外市场现状和趋势分析
国内市场:需求 量逐年增长市场 竞争激烈
国外市场:需求 量稳定市场竞争 相对较小
发展趋势:环保、 节能、高性能、 智能化
技术研发:加强 技术创新提高产 品质量和性能
技术创新和产品升级方向
研发新型摩擦材料 提高耐磨性和耐热 性
摩擦材料技术培训

损伤制动盘或鼓。主要市场: 北美和亚洲低金属:。在实际应用中会降低摩擦力,从而降低了制动作用。 谢谢
Image
第二十五页,共二十五页。
背板的前处理
混合
背板
清洗
喷丸
涂胶
第七页,共二十五页。
背板 底料 摩擦材料
冷压或热压
摩擦(mócā)材料的生产流程 2
热处理
磨削
烧蚀
喷漆
粘消音片
印码
装附件
包装
•铆消音片 •磨损指示器 •保持弹簧
第八页,共二十五页。
摩擦(mócā)材料的 分类
半金属:
– 较高的金属含量,有30%~50%左右的铁质金属物(如钢纤维、还原铁粉、泡沫铁粉)。
➢ 良好的耐磨性。 ➢ 制动(zhì dònɡ)噪音低。
➢ 对偶面磨损较小。 ➢ 具有良好的机械强度和物理性能。
第十一页,共二十五页。
摩擦(mócā)材料的技术要求
适宜(shìyí)而稳定的摩擦系 数
摩擦系数过高:噪音、磨损过快、伤对偶件
过低 :不能满足整车使用要求
摩擦(mócā)系数是评价任何一种摩擦(mócā)材料的一个最重要的性能指 标,关系着摩擦(mócā)片制动功能的好坏。它不是一个常数,而是受温度、压 力、摩擦(mócā)速度或表面状态及周围介质因素等影响而发生变化的一个数。
粉末冶金培训资料
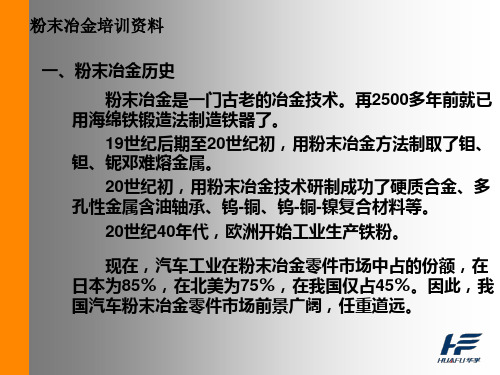
三、粉末冶金工艺过程介绍
1、制粉 制粉工艺过程较复杂,主要的方法有 氧化还原法、水雾化法、气雾化法、电解 法等。
三、粉末冶金工艺过程介绍
现在汽车工业主要用粉 80目、100目还原铁粉 100目200目雾化铁粉 各种合金粉 备注:目数越大、粉越细,即100目 粉比80目粉细
三、粉末冶金工艺过程介绍
1、真空烧结炉;
2、常压烧结炉; 3、高压烧结炉。
三、粉末冶金工艺过程介绍
烧结炉分类:
按加热方式不同分为: 按保护气氛气体不同分为: 1、还原气氛烧结炉; 2、真空或惰性气氛烧结炉; 3、氧化气氛烧结炉; 4、其它气氛烧结炉。
1、电加热式烧结炉;
2、燃料加热式烧结炉; 烧结炉。
三、粉末冶金工艺过程介绍
5、整形 整形的目的是纠正烧结过程中的变形 ,提高产品精度。 备注:通常情况下,整形压力为成形所 需压力的近2倍。重点关注高度、装配 尺寸的变化。
三、粉末冶金工艺过程介绍
6、蒸汽处理:
蒸汽处理原理: 4H2O(气)+3Fe→Fe3O4+4H2 (气) 主要作用:
1、防锈; 2、提高硬度;
3、提高产品耐磨性
4、烧结 将压制好的坯件在1120℃左右烧结30 分钟左右,各合金元素发生作用,使坯件 形成有强度的半成品。
备注:主要关注产品硬度、密度、金相 组织等性能方面的参数
三、粉末冶金工艺过程介绍
烧结炉分类:
按炉内压力不同分为: 按制品移动方式不同分为: 1、连续式烧结炉; 2、间歇式烧结炉; 3、半连续式烧结炉。
2、混粉 即:将不同的合金元素、润滑剂按一 定的比例混合均匀。
备注:该工序主要控制化学成分含量、 松装密度、流动性
三、粉末冶金工艺过程介绍
粉末冶金培训资料

汇报人: xx年xx月xx日
目 录
• 粉末冶金基本概念 • 粉末冶金的制备技术 • 粉末冶金材料的性能与特点 • 粉末冶金材料的制造工艺 • 粉末冶金材料的应用 • 粉末冶金的未来发展
01
粉末冶金基本概念
粉末冶金的定义和历史
粉末冶金的定义
粉末冶金是一种制粉、成形和烧结工艺,通过使用金属或非 金属粉末,以压制、烧结、熔渗等方法制造材料、零件或组 件。
粉末冶金材料的加工性能优良 ,可以通过压制成形、烧结、 热等静压等工艺方法加工成各 种复杂形状,提高其使用性能
和应用范围。
04
粉末冶金材料的制造工艺
制造工艺流程
粉末制备
包括原材料的选择、粉体材料的合 成和加工等。
压制成型
将粉末装入模具中,通过压制成型 机施加压力,制成具有一定形状和 密度的胚体。
机械法
通过机械研磨、破碎、雾化等 方法将金属或合金制成粉末,
如球磨、喷雾塔等。
热分解法
通过加热分解含金属离子的盐 类或氧化物,获得金属粉末,
如还原焙烧、热分解等。
粉末成形技术
01
02
03
模压成形
将金属粉末放入模具中, 施加压力使其成形,适用 于形状简单的制品。
注射成形
将金属粉末与粘结剂混合 后注入模具,脱模后进行 烧结,适用于形状复杂的 制品。
随着3D打印技术的不断发展 ,粉末冶金将与3D打印技术 相结合,实现快速原型制造和 生产个性化产品。
粉末冶金材料的循环利用也将 得到更广泛的应用,有利于资 源的节约和环境的保护。
粉末冶金材料的市场前景
随着粉末冶金技术的不断进步和 应用的扩大,粉末冶金材料的市
场需求将继续增长。
粉末冶金培训资料

自蔓延高温合成
总结词
自蔓延高温合成是一种利用化学反应产生的高温实现材 料合成和致密化的技术。
详细描述
自蔓延高温合成的原理是通过引发化学反应产生高温, 使反应体系内的物质发生熔融、蒸发、凝聚等物理化学 变化,从而实现材料的合成和致密化。这种技术具有反 应速度快、节能环保等优点,广泛应用于陶瓷、金属等 材料的合成和致密化。
详细描述
溶胶-凝胶法是一种制备金属粉末的方法,通过将金属盐溶液进行水解、聚合和缩聚反应,形成溶胶或凝胶,然 后进行热处理得到金属氧化物或氮化物粉末。这种方法可以制备出具有优异性能的金属粉末,广泛应用于粉末冶 金领域。
03
粉末成型技术
压制成型
总结词
压制成型是粉末冶金中最常用的成型技术,通过施加压力将粉末压制成一定形状和密度的坯块。
磁导率
一些粉末冶金材料具有较好的磁导率, 可以用于制造磁性元件和磁性材料。
电导率
某些粉末冶金材料具有较高的电导率, 可以用于制造电子元件和导电材料。
化学性能
耐腐蚀性
粉末冶金材料具有较好的 耐腐蚀性,不易受酸、碱、 盐等化学物质的侵蚀。
抗氧化性
粉末冶金材料经过特殊处 理后,能够形成致密的氧 化膜,具有良好的抗氧化 性。
总结词
热压烧结是一种在加压和加热的条件下进行的烧结技 术,通过加压和加热的联合作用,促进粉末颗粒之间 的扩散和粘结。
详细描述
热压烧结的原理是将粉末或预压坯置于模具中,通过 施加压力和加热的方式,使粉末颗粒之间发生粘结和 扩散,从而实现材料的致密化和强化。这种技术广泛 应用于陶瓷、金属粉末等材料的烧结。
成发具有优异性能的新型粉末冶金材料,满足不 同领域的需求。
新工艺研发
探索新的粉末冶金工艺和技术,提高产品质量和 性能,降低生产成本。
粉磨站培训教材中文

粉磨站培训教材中文随着经济的发展,我国的科技水平也在稳步提高。
作为主要国家之一,我国的工业化进程也日益加快,其中特别是钢铁行业的发展。
粉磨站是钢铁生产中重要的工艺链之一,对钢铁的品质和产量具有至关重要的作用。
为了提高国内粉磨站的工作效率和生产质量,研发一份完善的培训教材显得尤为重要。
粉磨站的生产流程十分繁琐,其中包括物料输送、粉磨筛分、环保处理、设备维护等多个环节。
这些工作环节的重要性不言而喻,既需要工作人员对于各项设备的操作和维护十分熟悉,也需要他们深入了解每一个工序的性质和相互之间的关系以及可能出现的问题和应对方法。
然而目前的状况是,很多粉磨站的工作人员,大都是通过熟悉上岗逐渐积累而成的,而缺乏较为系统、全面的培训和入门指导。
因此,为了提高生产效率和提高产品质量,粉磨站培训教材中文的编制势在必行。
针对这一需求,我们要针对作业环节进行评估和分拣。
比如物料输送,评估需要知道是否有足够的一级输送机和二级输送机。
对于粉磨筛分的评估,则需要知道筛齿是否是平面的,筛框是否严密以及网目是否符合要求等等。
这就要求教材要全面、详尽的介绍一个生产流程中的每个环节,以及每个环节的具体操作流程和注意事项。
另外,教材中还应该包含一些常见的故障及其处理方法,同时还要详细介绍各个设备的结构和构造、维修保养及检测方法,以及与之相关的专业术语等等。
教材编写者可以根据实践和理论知识进行编写,建立起可操作、可呈现、可参考的内容。
为了满足工作实际,我们可以采取以下策略进行理论教育:首先应从实际出发降低技术门槛;其次,必须提高学习效果,落实学后效果如何;同样重要的是要使学员彻底理解电气处理、环保、设备维护、设备检修、服务等方面的基本知识。
从这些基本方面入手,通过问题的发掘,理论结合实践,具体问题和实例的呈现等方式,进而增加学员对培训教材的好奇心和兴趣,提高学习效果,还需要合理的考评体系,促进学员的进步和逐次的达成教育目标。
在教材编写方面,需要注意的是,尽可能的减少专业术语的使用,使其更通俗易懂。
- 1、下载文档前请自行甄别文档内容的完整性,平台不提供额外的编辑、内容补充、找答案等附加服务。
- 2、"仅部分预览"的文档,不可在线预览部分如存在完整性等问题,可反馈申请退款(可完整预览的文档不适用该条件!)。
- 3、如文档侵犯您的权益,请联系客服反馈,我们会尽快为您处理(人工客服工作时间:9:00-18:30)。
粉末冶金摩擦材料(培训教材)中国粉末冶金实验基地目录1.概述2.粉末冶金摩擦材料的特点3.我国生产的粉末冶金摩擦材料4.粉末冶金摩擦材料的装配5.粉末冶金摩擦材料的组成6.粉末冶金摩擦材料的生产7.对摩材料1.概述摩擦材料是制动器(刹车制动)、离合器(传递扭矩)使用的一种功能性材料,它对制动器、离合器的工作起着重要的作用。
例如,飞机的刹车片、汽车的刹车带、火车的制动闸瓦(闸片)等,是用做制动器中的摩擦材料。
离合器片则是用在离合器中的摩擦材料。
与摩擦材料一起摩擦进行工作的材料在飞机上称为对偶,或者叫作对摩材料;而在火车和汽车上则称为制动盘材料。
摩擦材料和对摩材料构成一组摩擦副。
尽管摩擦副的工作是由摩擦材料和对摩材料的共同性质所决定的,但是在其中起主要作用的、决定性作用的仍然是摩擦材料。
制动就是强制运转的机器或机械减速和停止的过程。
在制动器中,摩擦副吸收机器或机械的动能,并把它转化为热能。
一部分热量发散到周围的环境中去,而另一部分为摩擦副所吸收,使摩擦副本身的温度升高。
传递扭矩摩擦副的工作和制动摩擦副的工作没有什么本质的区别,同样都是摩擦副中摩擦材料和对摩材料的相对速度发生变化。
工作开始时相对速度最大,而后逐渐减小到零的过程。
区别是工作时间的长短(制动时间一般是从几秒到十几秒,传递扭矩的时间一般是十分之几秒到几秒)不同,吸收能量的大小不同,摩擦因数不同,因而摩擦副的工作温度也不同。
摩擦副在工作过程中总是要吸收能量,使本身的温度升高。
因此,摩擦材料不是在室温,而是在较高的温度下工作的。
摩擦材料工作时的温度和升温速度,在结构一定的情况下,主要和摩擦副工作时必须吸收的能量大小、吸收这些能量的时间间隔有关。
吸收的能量越大、时间间隔越短,那么摩擦材料的温度越高,升温速度也越大。
在某些情况下,发生热冲击,也就是在很短的时间间隔之内,摩擦表面产生极高的温度。
例如,飞机在着陆制动时,在3~5秒种之内,摩擦材料工作表面温度可达到1000℃以上,体积温度高达400℃~600℃。
在油中工作的离合器摩擦副(称为湿式工作条件下),尽管工作时吸收的能量也很大,但由于有油的存在,一般工作表面的温度和整个摩擦材料的体积温度不超过200℃。
摩擦材料是靠表面工作的。
在工作中,摩擦材料的工作表面温度很快升高,而后靠传导作用,使整个摩擦材料的温度升高。
因此,摩擦材料的工作表面温度和整个体积的温度相差很大。
一般讲摩擦材料的温度特性,是指摩擦材料表面工作温度和体积温度。
摩擦材料的摩擦—磨损性能、物理—力学性能,受温度的影响很大。
任何摩擦材料都存在一个最高的工作温度,超过了这个温度,摩擦材料的摩擦—磨损性能急剧下降,也就是摩擦因数变得很低,磨损很快。
这个温度一般叫做摩擦材料的极限工作温度。
随着现代科学技术和工业生产的发展,飞机、汽车、工程机械等,机械运转的速度、负荷大幅度提高,要求摩擦副吸收的能量响应的增加很多,因而提高了对摩擦材料的要求。
1.1对摩擦材料的主要要求是:1、足够的摩擦因数及较高的热稳定性。
2、耐磨性好,使用寿命长。
3、良好的磨合性。
4、良好的抗卡滞性能,平稳的传递扭矩和制动。
5、足够的强度,能够承受较高的工作压力及速度。
6、其他一些特殊的要求,如耐腐蚀性能等。
随着交通工具的不断发展和制动器结构的变化,摩擦材料由最早的天然材料发展到了下述五种类型,分别适应于不同的工作情况和热负荷的材料:1、聚合物基摩擦材料(石棉树脂);2、半金属有机摩擦材料;3、粉末冶金(金属陶瓷)摩擦材料;4、炭/炭复合摩擦材料;5、陶瓷基摩擦材料。
1.2下面着重介绍粉末冶金摩擦材料:粉末冶金摩擦材料是伴随着工业发展而发展起来的一种新型摩擦材料。
应该承认,目前实际应用的摩擦材料中,粉末冶金摩擦材料是很有前途的。
特别是由于科学技术的进步,高速、重载机械的出现,给其他摩擦材料带来困难,而粉末冶金摩擦材料正是适应这种情况而发展起来的,因此它具有广泛使用的可能性。
早在20世纪二十年代末期,由于机械能量的增大,摩擦材料工作温度的提高,使传统的摩擦材料在工作中发生热衰退,寿命很短,这就促使研制性能更好的摩擦材料,于是粉末冶金摩擦材料诞生了。
开始形成了以铜为主要成分的铜基粉末冶金摩擦材料和以铁为主要成分的铁基粉末冶金摩擦材料两大类。
从工作条件来讲,把粉末冶金摩擦材料又分成了在空气中工作的干式和在油中工作的湿式两种摩擦材料。
到六十年代,飞速发展的现代技术对摩擦材料的要求越来越高,特别是对航空用摩擦材料的工作温度要求提高了很多。
这样,各国在寻找新型材料的组成方面进行了大量的工作,而且超出了铜基和铁基的概念,研究制造了其他金属或合金为基体的材料,特点是向多组元、复杂成分合金化的方向发展,以适应对摩擦材料多方面的要求。
早在20世纪五十年代,我国就已经开始研究和生产粉末冶金摩擦材料。
经过了多年的努力,取得了显著的成绩,无论是铜基材料还是铁基材料都已达到了相当高的水平。
不仅能生产各类航空、汽车、拖拉机、坦克、船舶、工程机械以及一般机械用的粉末冶金摩擦材料,还研究成功了湿式铁基粉末冶金摩擦材料,并在实际中得到应用。
湿式铜、铁基粉末冶金摩擦材料具有使用性能好,摩擦因数高、机械强度好、不易产生翘曲及节约有色金属等优点,为我国粉末冶金摩擦材料的发展开辟了一条新路。
在摩擦材料的摩擦性能测试方面,我国自行设计和制造了摩擦试验机及各类台架试验设备,为我国粉末冶金摩擦材料的发展打下了良好的基础。
2.粉末冶金摩擦材料的特点粉末冶金摩擦材料已经成功应用在飞机的制动,汽车、坦克、拖拉机、船舶、工程机械和一般机械的制动和离合器上,经过长期的使用,证明粉末冶金摩擦材料具有以下的特点:2.1摩擦因数高粉末冶金摩擦材料具有足够高的摩擦因数,耐高温,在不同的使用条件下比较稳定。
摩擦副在制动中的制动力矩和在离合器中传递的扭矩大小,以下式表示:M = μ·n·P·R上式中:M ——力矩μ——摩擦因数n ——摩擦副摩擦面数(一个动盘两个面)P ——作用在摩擦副上的垂直压力;R ——摩擦副的作用半径;由上面的公式可以清楚地看出,在设计结构一定的情况下,也就是n、P、R一定的情况下,只有摩擦材料的摩擦因数μ足够高,才能刹车灵敏,传递扭矩迅速,不打滑。
反过来讲,如果材料的摩擦因数足够高,就可以减小n、P、R中的任何一个指标,或者都可以减小一些,使摩擦机构的尺寸减小。
当然当摩擦机构一定时,对摩擦因数就有了一定的要求,低了不行,高了也不好。
摩擦因数太高,会造成机械零件的破坏,而且摩擦副也不能平稳地工作。
2.2耐高温在比较广泛的温度范围内,粉末冶金摩擦材料有比较平稳的摩擦因数;或者说在很高的温度下,摩擦因数仍然能够满足要求。
表1 材料性能对比试验结果注:⑴、试验是按照JG129-66部颁标准进行的。
⑵、高温指250℃,常温指120℃。
⑶、磨损指半小时的磨损。
从表1不难看出,粉末冶金摩擦材料在很高的工作温度下,仍有比较稳定的摩擦因数。
树脂基材料,到300℃时就开始发生摩擦因数的衰退现象,温度再升高,出现一个摩擦因数较低但比较稳定的阶段。
这主要是由于材料表面形成了一层比较稳定的薄膜,膜层主要由氧化物、硫化物、磨损产物以及材料中粘结剂组织破坏产物等组成。
这种薄膜能起较稳定的润滑作用,所以摩擦因数是较低的。
当温度再继续升高时,由于材料表面的炭化作用而形成焦化层,使摩擦因数增高。
而材料的剧烈分解和燃烧,使材料的磨损急剧增加,甚至造成彻底损坏。
粉末冶金摩擦材料的摩擦因数,对于不同的速度和工作压力的变化,也同样是比较稳定的。
2.3耐磨性高,使用寿命长对于摩擦材料来讲,耐磨性也是十分重要的。
材料的耐磨性高,使用寿命就长。
如果使用期限一定,就可以将摩擦材料的厚度减小,减小摩擦副的尺寸。
粉末冶金摩擦材料的寿命,一般比树脂基摩擦材料高5~10倍。
汽车离合器片(7吨汽车、单片干式)用粉末冶金摩擦材料代替树脂基材料,尽管粉末冶金摩擦材料的总面积只有树脂基材料总面积的57%,但其使用寿命仍比树脂基材料高约10倍以上。
在山西、四川使用的解放牌汽车(4吨),刹车采用粉末冶金摩擦材料后,使用寿命比原用树脂基材料高(5倍以上)。
在油中工作的铜基粉末冶金摩擦材料,寿命很长,磨损很小,一般一次离合磨损为10-6毫米。
2.4良好的磨合性磨合性一般是指摩擦副工作时,摩擦材料表面在压力和速度的作用下,以塑性变形和磨损的方式,增加摩擦副实际接触面积的特性。
对于摩擦机构来讲,摩擦副获得最大可能的实际接触表面是很重要的。
材料的磨合性好,便可以比较快的达到这种情况,也就是说比较快的达到最好达到工作状态。
评价磨合性,最主要的是以实际接触面积与名义工作面积之比的大小,或者以制动力矩,传递扭矩达到平稳来估计。
在实际应用中,摩擦副在进入实际运行之前,一般都需要进行磨合或者称为跑合。
跑合时间的长短,就取决于材料的磨合性。
磨合性好,跑合的时间就可以缩短,实际上提高了机器或机械的效率。
2.5良好的导热性铁基粉末冶金摩擦材料的导热因数约为10-1卡/厘米·秒·度的数量级(铜基材料还要高一些)。
树脂基材料大约为10-3卡/厘米·秒·度,相差100倍之多。
导热性能好,非常有利于散热,因而摩擦副的工作温度就比较低。
这一特点对重负荷工作的摩擦副,将是非常有利的。
由于摩擦副工作温度比较低,从而保护了对摩材料,使对摩材料不致由于过热而造成金相组织的改变,发生碎裂或翘曲等。
试验指出:在相同的条件下,与树脂基材料相配对的铸铁对摩材料,发生了马氏体相变,相变深度为0.18mm,表面产生了热裂纹。
而与粉末冶金摩擦材料相配的同样对摩材料,表面光亮,没有发生相边和产生裂纹。
摩擦材料的摩擦因数随温度的升高而下降,摩擦副工作温度比较低,那么摩擦因数就可以比较高,这对摩擦副的工作也是有利的。
由于粉末冶金摩擦材料的导热性能好,在汽车点盘式制动器中,摩擦材料靠近刹车油压活塞,容易造成油温过高而影响刹车,因此在设计时要考虑隔热的问题。
2.6使用负荷高粉末冶金摩擦材料比树脂基材料具有更高的物理——机械性能,因此可以在更高的速度、更高的压力下工作。
在比较高的冲击负荷下工作不碎裂、不破坏。
粉末冶金摩擦材料允许使用的负荷高;还由于粉末冶金摩擦材料的摩擦因数随温度和工作压力的增加变化很小。
从摩擦副传递扭矩和制动力矩的公式上还可以看出,总的压力提高,就可以减少n、R,使摩擦机构的尺寸更为紧凑。
如果是结构设计一定的摩擦副,便可以减少粉末冶金摩擦材料的铺面,这对提高材料的磨合性也是有利的。
一般树脂基材料允许的使用压力为1.5~8kg/cm2,最高允许为11~26kg/cm2。
而粉末冶金摩擦材料允许的使用压力为28~40kg/cm2,最高可以允许达到100kg/cm2以上。