莱钢转炉脱磷优化生产工艺措施
转炉炼钢流程中的脱磷工艺
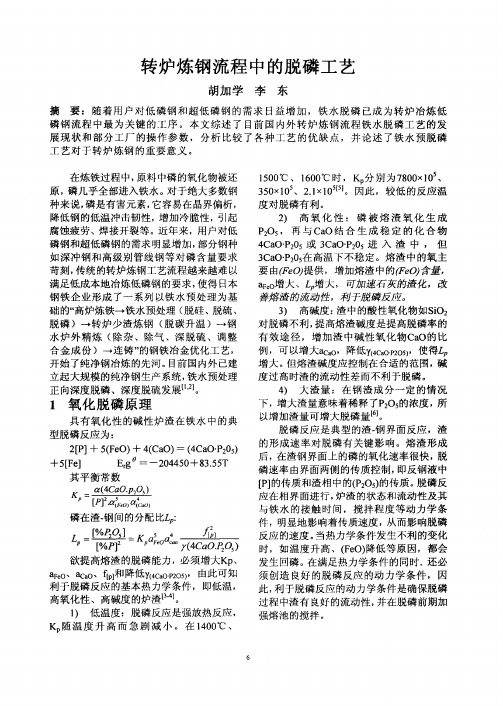
磷 在渣. %P
:
a ̄
7 C . ・ y4 a Q ) ( OP 0 2
欲提 高熔 渣 的脱磷 能力 ,必须增 大K 、 p ae、aa、f]口 F 0 co t 降低1 C .O) 由止 可 失 p , P 5 ( O2 , 4 匕 l J 利 于脱磷 反应 的基 本热 力学 条件 , 即低温 , 高 氧化 性 、高碱度 的炉 渣 【 3 。 1 低温 度 :脱磷 反应 是强 放热 反应 , ) KD 温 度 升 高 而 急 剧 减 小 。 在 10  ̄ 随 4 0C、
3 高碱 度 : 中的酸 性氧化 物如 SO2 ) 渣 i 对脱 磷 不利 , 高熔渣 碱 度是 提 高脱磷 率 的 提 有 效 途 径 ,增 加 渣 中 碱 性氧 化物 C O的 比 a 例 ,可 以增大 a ,降低 丫CO 25 co (a.o) 4 P ,使得三 p 增 大 。 熔渣碱 度 应控 制在 合适 的范 围 , 但 碱 度过 高 时渣 的流 动性差 而 不利 于脱磷 。 4 大 渣 量 :在 钢渣 成 分 一 定 的情 况 ) 下 ,增 大渣 量意 味着稀 释 了P05 2 的浓度 , 所 以增 加渣 量 可增 大脱磷 量 【。 o J 脱 磷 反应 是 典型 的渣 界 面 反应 ,渣 钢 的形 成 速 率对 脱 磷 有 关 键影 响 。熔 渣 形成 后 ,在渣 钢 界面上 的磷 的氧 化速 率很 快 , 脱 磷速 率 由界 面两侧 的传 质控 制 , 即反钢 液 中 【] P 的传 质 和渣相 中 的(2 ) Po5的传质 。 磷反 脱 应 在相 界面 进 行 , 炉渣 的状 态和 流动 性及其 与 铁 水 的接触 时 间 ,搅 拌程 度 等 动 力 学条 件 ,明显地 影响着 传质 速度 , 从而 影 响脱磷 反应 的速度 。 当热 力学条 件 发生 不利 的变化 时 ,如温 度升 高 、(e ) F O 降低 等原 因,都会 发 生 回磷 。在满足 热力 学条 件 的 同时 . 还必 须 创 造 良好 的脱 磷 反 应 的动 力 学 条 件 , 因 此 , 于脱 磷 反应 的动力 学 条件 是确 保脱磷 利 过 程 中渣 有 良好 的流 动性 , 并在 脱磷 前期加 强熔 池 的搅 拌 。
(完整word版)转炉脱磷分析及采取的措施2
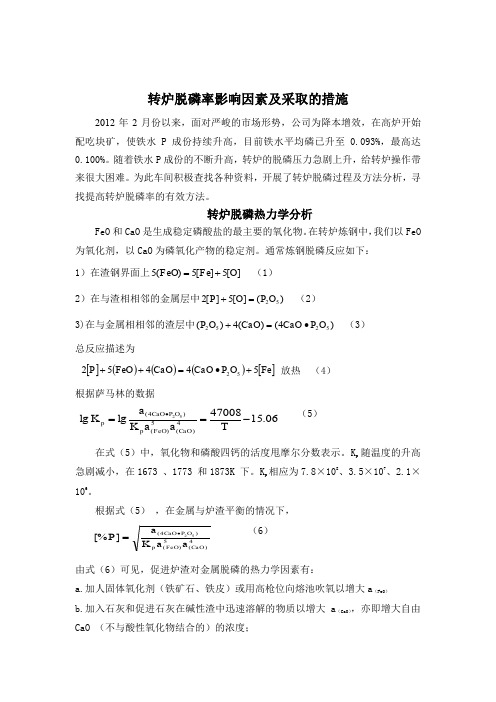
转炉脱磷率影响因素及采取的措施2012年2月份以来,面对严峻的市场形势,公司为降本增效,在高炉开始配吃块矿,使铁水P 成份持续升高,目前铁水平均磷已升至0.093%,最高达0.100%。
随着铁水P 成份的不断升高,转炉的脱磷压力急剧上升,给转炉操作带来很大困难。
为此车间积极查找各种资料,开展了转炉脱磷过程及方法分析,寻找提高转炉脱磷率的有效方法。
转炉脱磷热力学分析FeO 和CaO 是生成稳定磷酸盐的最主要的氧化物。
在转炉炼钢中,我们以FeO 为氧化剂,以CaO 为磷氧化产物的稳定剂。
通常炼钢脱磷反应如下:1)在渣钢界面上][5][5)(5O Fe FeO += (1)2)在与渣相相邻的金属层中)(][5][252O P O P =+ (2)3)在与金属相相邻的渣层中)4()(4)(5252O P CaO CaO O P ∙=+ (3)总反应描述为[]()()()[]Fe O P CaO CaO FeO P 5445252+∙=++ 放热 (4)根据萨马林的数据(5)在式(5)中,氧化物和磷酸四钙的活度甩摩尔分数表示。
K p 随温度的升高急剧减小,在1673 、1773 和1873K 下。
K p 相应为7.8×108、3.5×107、2.1×106。
根据式(5) ,在金属与炉渣平衡的情况下,(6)由式(6)可见,促进炉渣对金属脱磷的热力学因素有:a.加人固体氧化剂(铁矿石、铁皮)或用高枪位向熔池吹氧以增大a (FeO )b.加入石灰和促进石灰在碱性渣中迅速溶解的物质以增大a (CaO ),亦即增大自由CaO (不与酸性氧化物结合的)的浓度;06.1547008lg lg 4)(5)()4(52-==∙T a a K a K CaO FeO p O P CaO p 4)(5)()4(52][%CaO FeO p O P CaO a a K a P ∙=c.用更新与金属接触的渣相的方法,亦即放渣和加入CaO 与FeO 造新渣的方法来减小)4(52O P CaO a ∙d.保持适当的低温,因为温度从1673 增到1873K ,使反应(4)的平衡常数K p 减小到1/370 。
转炉脱磷造渣工艺
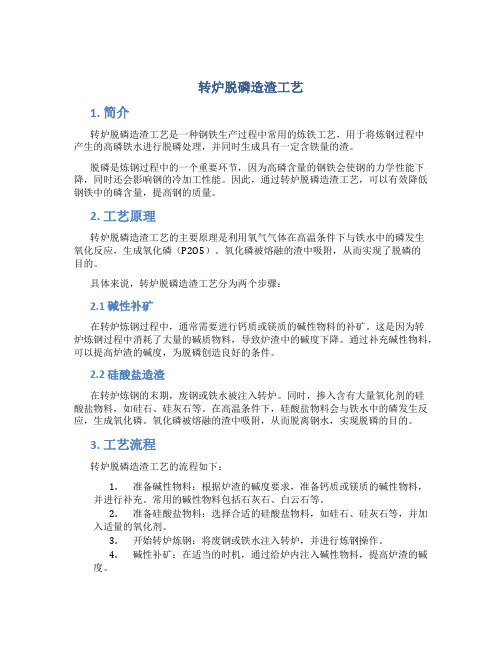
转炉脱磷造渣工艺1. 简介转炉脱磷造渣工艺是一种钢铁生产过程中常用的炼铁工艺,用于将炼钢过程中产生的高磷铁水进行脱磷处理,并同时生成具有一定含铁量的渣。
脱磷是炼钢过程中的一个重要环节,因为高磷含量的钢铁会使钢的力学性能下降,同时还会影响钢的冷加工性能。
因此,通过转炉脱磷造渣工艺,可以有效降低钢铁中的磷含量,提高钢的质量。
2. 工艺原理转炉脱磷造渣工艺的主要原理是利用氧气气体在高温条件下与铁水中的磷发生氧化反应,生成氧化磷(P2O5)。
氧化磷被熔融的渣中吸附,从而实现了脱磷的目的。
具体来说,转炉脱磷造渣工艺分为两个步骤:2.1 碱性补矿在转炉炼钢过程中,通常需要进行钙质或镁质的碱性物料的补矿。
这是因为转炉炼钢过程中消耗了大量的碱质物料,导致炉渣中的碱度下降。
通过补充碱性物料,可以提高炉渣的碱度,为脱磷创造良好的条件。
2.2 硅酸盐造渣在转炉炼钢的末期,废钢或铁水被注入转炉。
同时,掺入含有大量氧化剂的硅酸盐物料,如硅石、硅灰石等。
在高温条件下,硅酸盐物料会与铁水中的磷发生反应,生成氧化磷。
氧化磷被熔融的渣中吸附,从而脱离钢水,实现脱磷的目的。
3. 工艺流程转炉脱磷造渣工艺的流程如下:1.准备碱性物料:根据炉渣的碱度要求,准备钙质或镁质的碱性物料,并进行补充。
常用的碱性物料包括石灰石、白云石等。
2.准备硅酸盐物料:选择合适的硅酸盐物料,如硅石、硅灰石等,并加入适量的氧化剂。
3.开始转炉炼钢:将废钢或铁水注入转炉,并进行炼钢操作。
4.碱性补矿:在适当的时机,通过给炉内注入碱性物料,提高炉渣的碱度。
5.硅酸盐造渣:当转炉炼钢接近末期时,通过给炉内注入硅酸盐物料,利用氧化剂促进磷的氧化反应。
6.淋渣:根据炉内的渣情况,选择合适的时间进行淋渣操作。
淋渣可以通过人工或机械设备进行。
7.渣铁分离:在脱磷过程中,渣中生成的氧化磷会被吸附在渣中,从而脱离钢水。
通过合适的方法,将渣与钢水分离。
8.尾渣处理:处理分离出来的尾渣,并对其进行资源化利用或安全处理。
转炉炼钢工艺的优化实践

转炉炼钢工艺的优化实践摘要: 目前,我国炼钢行业正在快速发展,同时炼钢技术的进步主要围绕着高效率、高质量、低成本、低能耗、少环境污染等方面。
对于炼钢技术采取优化措施,结合工艺优化和综合降耗,从炉料消耗、氧气消耗、石灰、合金消耗、煤气回收、除尘灰、钢渣综合处理等环节有效控制,明显提高炼钢的经济和质量效益。
在整体上提高炼钢行业的竞争性,创新炼钢工艺,不断优化炼钢工艺等方面,取得了明显的效果。
关键词: 转炉炼钢工艺优化0 前言转炉炼钢工艺的优化大大提高了转炉炼钢的发展,同时增强了炼钢企业的市场竞争力,工艺优化,不但可以降低成本,同时提高炼钢企业的年产量,节省各项资源的消耗,最大限度地提高了企业的经济效益。
各项技术指标的提高,进一步优化炼钢工艺,带动了炼钢业的经济发展。
本文主要通过对炼钢行业现状的分析,结合成功经验,对炼钢工艺优化提出一些既有效又经济的方法,降低成本的同时,提高炼钢产量,节约能源。
笔者分析探讨了炼钢工艺优化的重要性和可实施性。
1总述炼钢行业的现状针对当前钢铁行业所面临的处境,提高市场竞争力、降低炼钢生产成本势在必行。
而在炼钢生产中,金属炉料成本约占炼钢生产总成本的80%以上,因此抓好金属炉料成本是控制炼钢生产成本的关键。
为进一步减少金属炉料消耗,略钢炼钢厂通过探索,优化炉料结构,改进炉前冶炼工艺和优化合金料的使用,采用少渣炼钢工艺、改进吹氧工艺、引用低成本合金等措施,有效地降低金属炉料消耗、氧耗和合金成本,达到降低生产成本的目的,增加了企业经济效益。
近年来炼钢厂通过完善溅渣护炉、低铁水比冶炼、高效转炉、低耐材消耗达到了转炉炼钢厂生产工艺的优化组合。
2炉料结构优化思路目前,常用的转炉金属炉料有高炉铁水、铁块(生铁)、自产废钢、社会废钢( 以中型和小型废钢为主)等。
炉料结构优化应以满足转炉炼钢需要为基础,以提高炉料金属收得率为出发点,找出成本最低的炉料配比为目的。
炉料金属收得率是指某一金属炉料的单位投入量通过冶炼可以产出合格钢水的百分率。
转炉炼钢脱磷工艺理论与实践
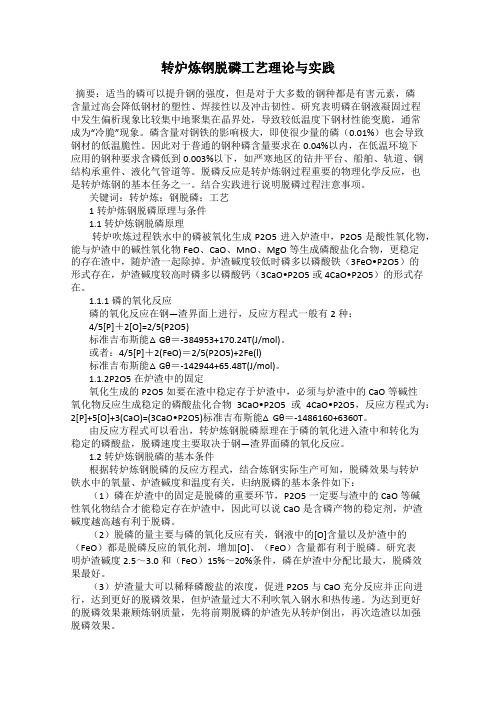
转炉炼钢脱磷工艺理论与实践摘要:适当的磷可以提升钢的强度,但是对于大多数的钢种都是有害元素,磷含量过高会降低钢材的塑性、焊接性以及冲击韧性。
研究表明磷在钢液凝固过程中发生偏析现象比较集中地聚集在晶界处,导致较低温度下钢材性能变脆,通常成为“冷脆”现象。
磷含量对钢铁的影响极大,即使很少量的磷(0.01%)也会导致钢材的低温脆性。
因此对于普通的钢种磷含量要求在0.04%以内,在低温环境下应用的钢种要求含磷低到0.003%以下,如严寒地区的钻井平台、船舶、轨道、钢结构承重件、液化气管道等。
脱磷反应是转炉炼钢过程重要的物理化学反应,也是转炉炼钢的基本任务之一。
结合实践进行说明脱磷过程注意事项。
关键词:转炉炼;钢脱磷;工艺1转炉炼钢脱磷原理与条件1.1转炉炼钢脱磷原理转炉吹炼过程铁水中的磷被氧化生成P2O5进入炉渣中,P2O5是酸性氧化物,能与炉渣中的碱性氧化物FeO、CaO、MnO、MgO等生成磷酸盐化合物,更稳定的存在渣中,随炉渣一起除掉。
炉渣碱度较低时磷多以磷酸铁(3FeO•P2O5)的形式存在,炉渣碱度较高时磷多以磷酸钙(3CaO•P2O5或4CaO•P2O5)的形式存在。
1.1.1磷的氧化反应磷的氧化反应在钢—渣界面上进行,反应方程式一般有2种:4/5[P]+2[O]=2/5(P2O5)标准吉布斯能△Gθ=-384953+170.24T(J/mol)。
或者:4/5[P]+2(FeO)=2/5(P2O5)+2Fe(l)标准吉布斯能△Gθ=-142944+65.48T(J/mol)。
1.1.2P2O5在炉渣中的固定氧化生成的P2O5如要在渣中稳定存于炉渣中,必须与炉渣中的CaO等碱性氧化物反应生成稳定的磷酸盐化合物3CaO•P2O5或4CaO•P2O5,反应方程式为:2[P]+5[O]+3(CaO)=(3CaO•P2O5)标准吉布斯能△Gθ=-1486160+6360T。
由反应方程式可以看出,转炉炼钢脱磷原理在于磷的氧化进入渣中和转化为稳定的磷酸盐,脱磷速度主要取决于钢—渣界面磷的氧化反应。
提高转炉冶炼前期脱磷效率的工艺操作
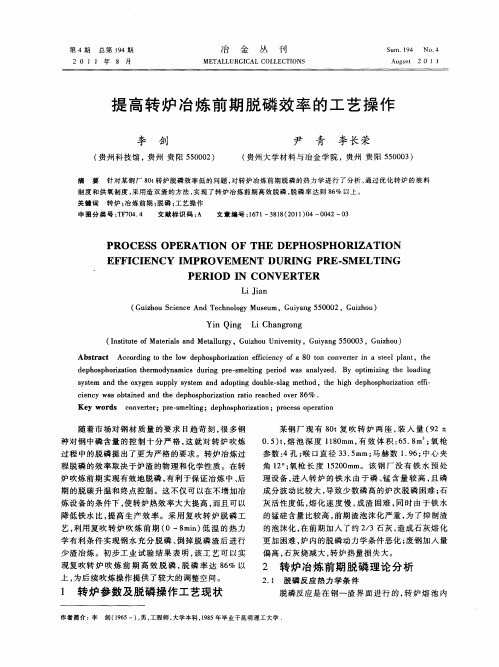
摘 要
尹 青
李 长 荣
( 贵州 大学材 料与 冶金 学院 , 州 贵 阳 5 0 0 ) 贵 5 0 3
针 对某 钢 厂 8 t 炉 脱 磷 效 率 低 的 问 题 , 转 炉 冶 炼 前 期脱 磷 的 热力 学 进 行 了 分 析 , 过 优 化 转 炉 的 装 料 0转 对 通
PRo CES S oPERATI oN F THE o DEPH o S PH o RI ZATI oN EFFI ENCY M PRo VEM ENT CI I DURI NG PRE. M ELTI S NG PERI oD N I CoNVERTER
L in iJa
程脱 磷 的效 率取决 于炉 渣 的物 理 和化学性 质 。在转
炉 吹炼前 期 实现 有效地脱 磷 , 有利 于保证 冶炼 中、 后
理 设备 , 进人 转炉 的 铁 水 由 于磷 、 含 量 较 高 , 磷 锰 且
期 的脱碳 升 温和 终点控 制 。这 不仅 可 以在不 增加 冶
炼设 备 的条 件下 , 使转 炉热效 率大 大提高 , 且可 以 而
极好 的优势 , 同时通 过 加 大前 期 熔 池 搅 拌 强 度 来 获
升高 , 铁水 中的碳 开始 氧化 , 此时 如果 炉 渣 中 的 F O e
钢 水 温度 。
熔 渣 中的 4 a P0 为 固态 , C O・ 其活度系数可近似 看作 1 由于 4 a ・ 与 P0 , CO P0 的摩尔 分数相 同 , 式 () 3 中的 ac .o o P 。 2可代之 以 置c .o或 P P o2 2 。而 当将 o 熔渣 中 口。的活度 系数近似看作 1 , 有 : 。 时 则
转炉炼钢脱磷工艺分析

II
第三章 试验方案的设计.............................................................................................................. 27 3.1 沙钢双渣脱磷的现状........................................................................................................ 27 3.1.1 双渣操作的好处......................................................................................................... 27 3.1.2 沙钢双渣脱磷情况.....................................................................................................27 3.1.3 脱磷的效果及回磷问题............................................................................................ 28 3.2 目前存在的问题................................................................................................................. 29 3.2.1 前期脱磷结果............................................................................................................. 29 3.3 影响前期脱磷的主要因素............................................................................................... 30 3.3.1 钢水中硅的氧化......................................................................................................... 30 3.3.2 前期渣碱度的控制.....................................................................................................30 3.3.3 倒前期渣时间的控制................................................................................................ 31 3.4 180t 转炉冶炼终点脱磷情况.......................................................................................... 32 3.4.1 增碳剂加入量的控制................................................................................................ 32 3.4.2 冶炼终点脱磷情况.....................................................................................................32 3.5 180t 转炉冶炼工艺改进方案.......................................................................................... 32 3.5.1 冶炼前期控制............................................................................................................. 33 3.5.2 冶炼终点控制............................................................................................................. 33 结论..............................................................................................................................................35 参考文献..................................................................................................................................... 36 致 谢....................................................................................................................................... 37
莱钢转炉炼钢生产工艺流程系统优化
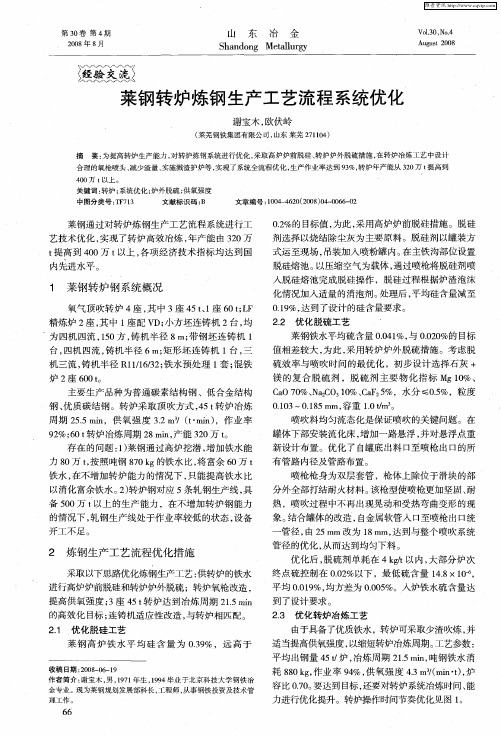
脱硅熔池 。 以压缩 空气 为载体 , 过喷枪 将脱硅剂 喷 通 入脱硅 熔池 完成脱 硅操作 ,脱 硅过程 根据 炉渣泡 沫
化情况 加入适 量 的消泡剂 。 处理 后 , 均硅含量减 至 平
1 莱钢转炉钢 系统 概况
氧气 顶 吹转 炉 4座 , 中 3座 4 1 6 L 其 5t 座 0t F 、 ;
到 了设计 要求 。 23 优 化转炉 冶炼 工艺 . 由于具备 了优质铁 水 ,转炉可采取 少渣 吹炼 , 并
进行高炉炉前 脱硅和转炉炉外脱 硫 ;转 炉氧枪 改造 , 提 高供氧强 度 ; 4 转 炉 达到 冶炼 周期 2.mi 3座 5 t 1 n 5
的高效化 目标 ; 连铸 机适应性 改造 , 与转炉 相匹配 。
一
以消化富余铁水。 ) 2转炉钢对应 5 条轧钢生产线 , 具
备 50万 t 0 以上 的生产 能力 ,在不 增加 转 炉钢 能力 的情 况下 , 轧钢 生产线 处于作 业 率较低 的状态 , 设备
开 工 不 足
管径 , 2 m改 为 1 达 到与整 个喷 吹系统 由 5m 8 mm,
01%, 到 了设计 的硅 含量要求 。 .9 达
22 优化 脱硫工 艺 -
精炼炉 2 , 座 其中 1 座配 V ; D 小方坯连铸机 2台, 均
为 四机 四流 ,5 10方 , 机半 径 8m; 铸 带钢 坯 连铸 机 1
莱 钢铁水平 均硫含 量 00 1 与 000 . %, . %的 目标 4 2 值 相差较 大 , 为此 , 采用转 炉炉外 脱硫 措施 。考虑 脱 硫 效 率与 喷 吹时 间的最 优化 ,初 步设计 选择 石灰 + 镁 的 复 合脱 硫 剂 ,脱 硫剂 主 要 物 化 指标 Mg1%、 0
莱钢50t转炉高效脱磷技术的应用
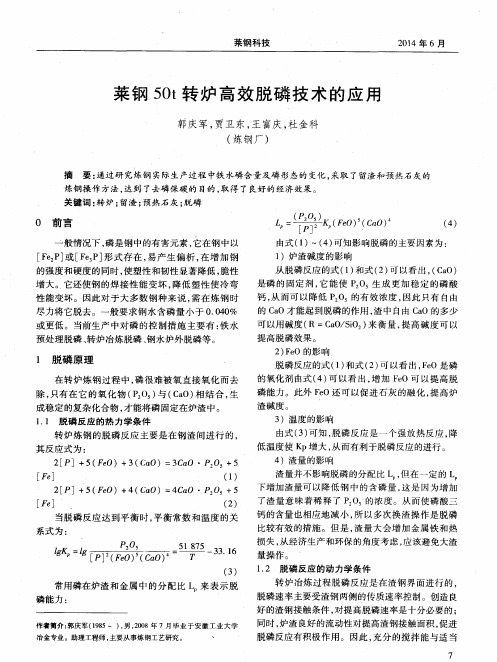
郭庆 军 , 等: 莱钢 5 0 t 转 炉高效 脱磷 技术 的应 用
的熔 池温度 , 推 动钢渣 接触 , 是 促进 脱磷 反应 的动 力
学条件 。
第 3期 ( 总第 1 7 1 期) 和 氧化锰 含量 , 而且 是现成 的熔 体 , 这 些特点 恰好 是
前期 渣需 要 的。为此 遵循 “ 前 期 早化 渣 , 多 去磷 ” 的 原则 , 充分 利用 上一 炉次终 点渣 , 采取 全 留渣 +石灰
脱磷速率主要受渣钢两侧的传质速率控制。创造良
好 的渣钢 接触条 件 , 对提 高脱磷 速率 是 十分必要 的 ; 同时 , 炉渣 良好 的流 动性对 提 高渣钢 接触 面积 , 促 进
冶金专业。助理工程师 , 主要从事炼钢工艺研究。
・
脱磷反应有积极作用 。因此 , 充分 的搅拌能与适 当
关 键词 : 转炉; 留渣 ; 预 热石灰 ; 脱 磷
0 前 言
L1 J
一
( F e O) s ( C a O)
( 4 )
般 情况 下 , 磷 是 钢 中的有 害元 素 , 它在 钢 中 以
由式 ( 1 )~( 4 ) 可知 影 响脱磷 的主要 因素 为 :
[ F e P ] 或[ F e P ] 形式存在 , 易产生偏析 , 在增 加钢 的强度 和 硬度 的 同时 , 使塑性 和韧性 显著 降低 , 脆 性
提 高脱磷 效果 。
2 ) F e O的影 响
1 脱 磷 原 理
在 转 炉 炼 钢 过程 中 , 磷 很 难 被 氧 直接 氧 化 而 去 除, 只有在 它 的氧 化 物 ( P 0 ) 与( C a O) 相 结合 , 生
脱磷 反应 的式 ( 1 ) 和式 ( 2 ) 可 以看 出 , F e O是磷 的氧化 剂 由式 ( 4 ) 可 以看 出 , 增加 F e O可 以提 高脱 磷 能力 。此外 F e O还 可 以促进 石 灰 的融 化 , 提 高 炉
转炉炼钢脱磷工艺的探讨

转炉炼钢脱磷工艺的探讨【摘要】本文从脱磷的热力学分析入手,对冶炼过程中温度、炉渣碱度、渣中(FeO),等对磷含量的影响进行了探讨。
同时探讨了回磷的原因、影响的因素和防止的措施。
【关键词】转炉炼钢;脱磷工艺;探讨磷在钢中是以【Fe3P】或【Fe2P】形式存在,一般以【P】表示。
磷含量高时,会使钢的朔性和韧性降低,即使钢的脆性增加,这种现象低温时更严重,通常把它称为“冷脆”。
且这种影响常常随着氧,氮含量的增加而加剧。
磷在连铸坯中的偏析仅次于硫,同时它在铁固溶体中扩散速度又很小。
不容易均匀化,因而磷的偏析和难消除。
由于炼铁过程为还原性气氛,脱磷能力较差。
因此脱磷是炼钢过程的重要任务之一。
在20世纪90年代中后期,为解决超低磷钢的生产难题,世界上各大钢厂都曾经进行过转炉铁水脱磷实验研究。
1、铁水预处理方法1.1喷吹苏打粉处理日本住友公司鹿岛厂开发的“住友碱精炼法”是成功用于工业生产的苏打精炼法。
工艺流程:从高炉流出的铁水先经脱硅处理,即将高炉铁水注入混铁车内,用氮气输送和喷吹烧结矿粉,喷入量为每吨铁水40公斤,最大供粉速度为每分钟400公斤,最大吹氧量为每分钟50立方米,脱硅量约为0.4%。
脱硅处理后的铁水硅含量可降到0.1%以下。
然后用真空吸渣器吸出脱硅渣,进行脱磷处理,以氮气为载气向铁水中喷入苏打粉,苏打粉用量为每吨18公斤,最大供粉量为每分钟250公斤,最大吹氧量为每分钟50立方米,处理后铁水中【P】≤0.001%,【S】≤0.003%,再用真空吸渣器吸出脱磷渣,并将其送到苏打回收车间,经水浸后可回收约80%的Na2O,最后将处理过的铁水倒入转炉冶炼。
1.2喷吹石灰系熔剂处理由于石灰系熔剂具有成本低,对环境污染小的优点,因此受到重视,并不断对其深入研究,以使其满足精炼铁水的需要。
工艺流程:向高炉铁沟中加入铁磷进行脱硅处理,加入量为每吨铁水27公斤,处理后铁水含硅量由0.5%降到0.15%,氧的利用率为80%-90%。
莱钢转炉脱磷优化生产工艺措施

莱钢转炉脱磷优化生产工艺措施摘要:通过对现有装备和工艺技术能力进行系统分析,莱钢炼钢厂通过完善与优化转炉护炉技术、推广应用连铸新技术和新工艺、在铁水预处理、转炉、二次精炼、等方面的先进工艺技术,保证了炼钢生产的稳定运行。
关键词:转炉品种结构工艺优化1、前言高效转炉工艺技术主要以保证质量为前提,以高作业率为基本手段来实现高质量、低成本。
实现转炉的高效生产不仅需要科学管理,更重要的是持续不断的技术改造创新,采用优质耐材和先进工艺、生产设备技术,以不断提高转炉脱磷工艺技术装备水平。
莱钢炼钢转炉系统经过近年来改革和发展,坚持走引进、消化、吸收、再创新的道路,在品种、质量等方面有了质的飞跃,而且自主开发集成了多项关键技术。
目前,莱钢炼钢系统主要包括转炉炼钢和电炉炼钢,转炉炼钢现有3座50t转炉、1座60t转炉,5座120t转炉,相应配套小方坯连铸机、带钢坯连铸机、矩形坯连铸机、异型坯连铸机、板坯连铸机,生产能力为1 000万t/a。
莱钢炼钢厂针对实际生产中存在的薄弱工艺环节,对现有设备工艺进一步优化改造,提高了生产装备水平,完善炼钢新工艺、新技术,进一步发挥了转炉的潜能,提高了质量,降低了成本。
2、依靠技术创新,提升工艺水平自金融危机以来。
全球钢铁消费需求不断下滑,国内钢企面临日益严峻的增支减利和结构优化调整压力。
为了更好地生存与发展,坚持以效益为中心,以技术创新为手段,立足于自主开发,加快新技术和新工艺的集成应用,大力发展循环经济,挖掘节能降耗潜力;同时加大高端新产品开发力度,提高产品质量,改善品种结构,积极应对市场变化。
莱钢炼钢系统充分发挥广大工程技术人员的聪明才智,大力开展技术攻关,提升工艺技术水平,促进了生产顺行,改善了产品质量,降低了生产成本。
特别是在炼钢系统,不断开发和应用新技术、新工艺,依靠技术进步和创新,工艺降本增效和新产品开发工作取得了显著成效。
3、转炉炼钢工艺过程在转炉炼钢过程中,通过氧枪向熔池内吹入氧气,与铁水中的碳、硅、磷、硫等元素反应生成炉渣、废气等,同时释放热量使熔液的温度升高,进而得到所需的钢种。
提高转炉炼钢终点磷命中率优化控制措施

提高转炉炼钢终点磷命中率优化控制措施摘要:磷在钢中作为一种有害元素会危害钢材的塑性、韧性和可焊性等性能,如何高效地降低钢中的磷含量一直成为国内外钢铁企业的研究重点。
基于此,本文就提高转炉炼钢终点磷命中率优化控制措施进行了探讨。
关键词:转炉炼钢;终点磷;命中率;优化控制;措施脱磷有利条件为“三高一低一良好”,“三高”分别指适度的高碱度R、高FeO、大渣量;“一低”指适当的低温,这两项为热力学因素;“一良好”指良好的炉渣熔化性及流动性、钢渣界面传质速度等,而“一良好”为动力学条件,但常常被忽略,确是最为重要因素。
转炉脱磷是受到热力学及动力学因素的综合影响,在生产中采用吹炼前期渣早化、吹炼中期渣化好、吹炼后期渣化透的方法,达到良好、稳定、高效的脱磷效果,确保终点磷的命中率。
1脱磷关键影响因素简析1.1适度高FeOFeO在脱P过程中起双重作用,一方面作为P的氧化剂使P氧化P2O5,另一方面把P2O5结合成(3FeO·P2O5)基础化合物,所以炉渣中存在FeO是脱磷的必要条件与前提。
但由于(3FeO·P2O5)高温稳定性差,必须生成稳定(3FeO·P2O5)或(4FeO·P2O5)才能彻底脱磷。
当FeO含量很低时,石灰不能很好熔化,既不能氧化脱磷,也不能生成稳定的磷酸盐化合物,特别是中期脱碳剧烈反应期,FeO含量降低,炉渣极易返干,钢水易回P,导致脱P异常。
但FeO含量过高,将稀释渣中CaO含量,使碱度降低,也降低脱P效果。
1.2适度高的R为了从钢液中脱磷并把脱磷产物固化在渣中,必须降低P2O5活度,需通过CaO 实现,形成(3FeO·P2O5)或(4FeO·P2O5)固留渣中,以确保脱磷效果,因此需确保高效稳定的化渣效果并适当提高渣中CaO含量。
但如果石灰加入量过大,导致石灰无法完全熔化,炉渣中固相比例增加,增大了炉渣的粘度,使炉渣流动性减弱,脱磷反应动力学条件变差,最终使脱磷率降低。
转炉冶炼高磷高带渣量铁液脱磷工艺研究

转炉冶炼高磷高带渣量铁液脱磷工艺研究铁液冶炼是一门细致、复杂的工艺,是冶炼业发展壮大的方面之一,也是当今冶炼行业最具活力的领域之一。
转炉冶炼作为一种节能环保的高效率冶炼技术,在国家能源节约和环境保护方面发挥了重要作用,受到有关部门的极大重视。
然而,随着转炉冶炼技术的发展,转炉冶炼高磷高带渣量铁液脱磷也成为一个热门话题。
转炉冶炼高磷高带渣量铁液脱磷是一种复杂的工艺,主要是把冶炼后的铁液中的过量磷去除,使其中的磷含量达到规定的标准。
在这一过程中,合规的冶金设备、精确的操作技术以及优质的带渣料等都起着关键的作用。
首先,转炉冶炼高磷高带渣量铁液脱磷的关键是选择合适的设备和工艺。
其中,选择一台性能稳定、节能节水、结构紧凑、操作便捷的高效脱磷炉,可以有效地提高脱磷效率;此外,还要选择具有良好的热稳定性的带渣料,以保证脱磷的稳定性,以及确保炉内的温度能够保持稳定。
紧接着,在转炉冶炼高磷高带渣量铁液脱磷的工艺操作上,应以铁液的机械化、控制化为基础,在保持安全的前提下,提高铁液的精炼度、活性度和质量,以便提高脱磷效果。
此外,在操作过程中,应该注意炉内各种物料的使用量及物料的运行状况,以及把安全程度放在第一位,确保铁液冶炼的质量和效率。
同时,在脱磷的过程中,应该根据不同的铁液品质,选择合理的工艺参数,如温度、时间、PH值等,并结合不断完善的新技术,如气浮技术、电解技术等,使脱磷效果取得最佳,以提高铁液质量。
最后,转炉冶炼高磷高带渣量铁液脱磷也需要多种技术手段和技术来完成。
其中包括有机还原脱磷、氧化脱磷等脱磷技术,还有各种机械设备、测试设备以及气体如氧气的使用,以保证冶炼的顺利进行及最终的成功。
转炉冶炼高磷高带渣量铁液脱磷是一种复杂的工艺,需要综合运用多种技术手段,充分发挥仪器的性能,确保冶炼的顺利进行及最终的成功。
随着社会发展,中国政府将继续加强和完善当前转炉冶炼技术,注重开发新动力,以促进我国冶炼行业进步和社会经济发展。
钢铁生产中的脱磷工艺
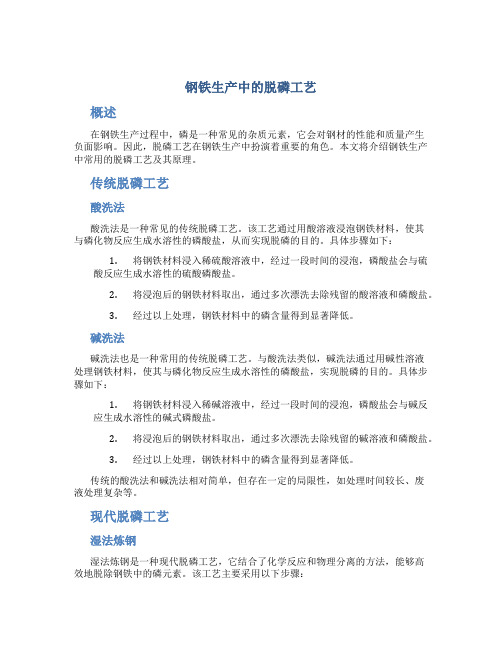
钢铁生产中的脱磷工艺概述在钢铁生产过程中,磷是一种常见的杂质元素,它会对钢材的性能和质量产生负面影响。
因此,脱磷工艺在钢铁生产中扮演着重要的角色。
本文将介绍钢铁生产中常用的脱磷工艺及其原理。
传统脱磷工艺酸洗法酸洗法是一种常见的传统脱磷工艺。
该工艺通过用酸溶液浸泡钢铁材料,使其与磷化物反应生成水溶性的磷酸盐,从而实现脱磷的目的。
具体步骤如下:1.将钢铁材料浸入稀硫酸溶液中,经过一段时间的浸泡,磷酸盐会与硫酸反应生成水溶性的硫酸磷酸盐。
2.将浸泡后的钢铁材料取出,通过多次漂洗去除残留的酸溶液和磷酸盐。
3.经过以上处理,钢铁材料中的磷含量得到显著降低。
碱洗法碱洗法也是一种常用的传统脱磷工艺。
与酸洗法类似,碱洗法通过用碱性溶液处理钢铁材料,使其与磷化物反应生成水溶性的磷酸盐,实现脱磷的目的。
具体步骤如下:1.将钢铁材料浸入稀碱溶液中,经过一段时间的浸泡,磷酸盐会与碱反应生成水溶性的碱式磷酸盐。
2.将浸泡后的钢铁材料取出,通过多次漂洗去除残留的碱溶液和磷酸盐。
3.经过以上处理,钢铁材料中的磷含量得到显著降低。
传统的酸洗法和碱洗法相对简单,但存在一定的局限性,如处理时间较长、废液处理复杂等。
现代脱磷工艺湿法炼钢湿法炼钢是一种现代脱磷工艺,它结合了化学反应和物理分离的方法,能够高效地脱除钢铁中的磷元素。
该工艺主要采用以下步骤:1.将含有磷的钢铁熔炼成液态,在熔炉中添加适量的石灰石、氧化铁等脱磷剂。
2.通过控制温度和反应时间,使磷与脱磷剂发生反应,生成不溶于钢液中的磷酸盐。
3.通过过滤或离心等物理分离的方法,将含有磷酸盐的渣滓与钢液分离。
4.经过以上处理,钢液中的磷含量得到显著降低。
湿法炼钢脱磷工艺快速、高效,并能得到较高质量的钢材。
然而,它的设备和操作成本相对较高,需要进行废液处理等附加工作。
精炼炉脱磷法精炼炉脱磷法是一种在炼钢过程中进行脱磷的方法。
该工艺主要包括以下步骤:1.将含有磷的钢铁在精炼炉中进行加热和搅拌。
转炉冶炼高磷高带渣量铁液脱磷工艺研究

转炉冶炼高磷高带渣量铁液脱磷工艺研究转炉冶炼是当今冶金行业中最常用的冶炼方法,由于高磷高带渣量铁液的特殊性,传统冶炼过程使用的工艺参数受到了较大的限制。
因此,研究如何利用转炉冶炼技术脱除高磷高带渣量铁液中的磷,对提高铁液质量和提高冶金生产效率具有重要意义和指导意义。
首先,要明确脱磷对转炉冶炼影响。
转炉冶炼高磷高带渣量铁液最主要的影响有:(1)由于磷是一种非金属元素,其溶解度非常低,当磷溶解度过高时,其在熔炼、坩埚和下砂过程中形成砂渣,阻碍清除砂渣,从而影响转炉冶炼的效率,导致杂质含量过高;(2)当磷含量过高时,会影响转炉冶炼的熔强度,从而降低冶炼质量;(3)磷本身是易焊性金属,磷在铁液中高度溶解,会影响转炉冶炼过程中生成的熔铸,从而降低铸件的质量。
其次,要考虑脱磷工艺的技术参数设置。
针对高磷高带渣量铁液的脱磷,应该从技术参数的设置入手。
建议采用相应的冶炼参数,例如增加转炉温度,调整转炉的转矩、转速、温度梯度等。
在实际冶炼过程中,要注意控制转炉内部熔炼温度和溶解度,加速磷的溶解过程,使磷容易脱除,从而提高冶炼效率和质量。
此外,可以使用辅助剂催化脱磷。
有些辅助剂可以促进铁液中磷的溶解,增加转炉冶炼过程中磷的溶解度,因此可以有效催化脱磷,提高转炉冶炼效果。
最后,如何选择脱磷剂也是值得考虑的一个因素,目前已经开发的脱磷剂包括磷酸根和硫酸、氯化物等。
在选择脱磷剂时,还需考虑
其磷溶解度、操作成本、环境危害等因素。
总之,研究转炉冶炼高磷高带渣量铁液的脱磷工艺具有重要的指导意义。
在实际应用中,应该分析影响高磷高带渣量铁液脱磷工艺的各种因素,科学设置冶炼参数,合理选择脱磷剂,以确保冶炼质量和效率,满足生产需求。
转炉脱磷造渣工艺
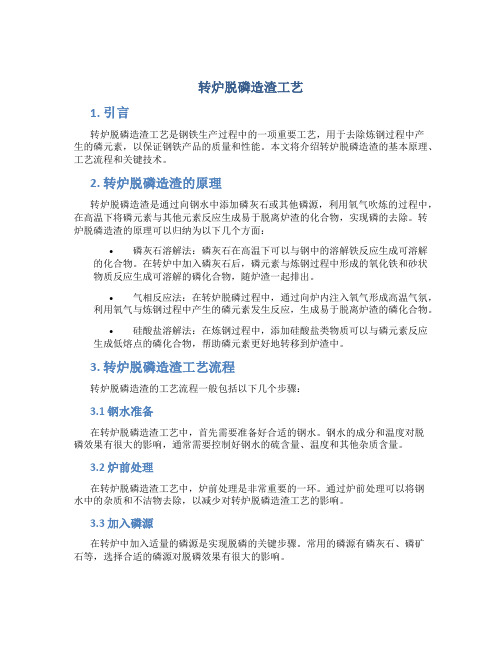
转炉脱磷造渣工艺1. 引言转炉脱磷造渣工艺是钢铁生产过程中的一项重要工艺,用于去除炼钢过程中产生的磷元素,以保证钢铁产品的质量和性能。
本文将介绍转炉脱磷造渣的基本原理、工艺流程和关键技术。
2. 转炉脱磷造渣的原理转炉脱磷造渣是通过向钢水中添加磷灰石或其他磷源,利用氧气吹炼的过程中,在高温下将磷元素与其他元素反应生成易于脱离炉渣的化合物,实现磷的去除。
转炉脱磷造渣的原理可以归纳为以下几个方面:•磷灰石溶解法:磷灰石在高温下可以与钢中的溶解铁反应生成可溶解的化合物。
在转炉中加入磷灰石后,磷元素与炼钢过程中形成的氧化铁和砂状物质反应生成可溶解的磷化合物,随炉渣一起排出。
•气相反应法:在转炉脱磷过程中,通过向炉内注入氧气形成高温气氛,利用氧气与炼钢过程中产生的磷元素发生反应,生成易于脱离炉渣的磷化合物。
•硅酸盐溶解法:在炼钢过程中,添加硅酸盐类物质可以与磷元素反应生成低熔点的磷化合物,帮助磷元素更好地转移到炉渣中。
3. 转炉脱磷造渣工艺流程转炉脱磷造渣的工艺流程一般包括以下几个步骤:3.1 钢水准备在转炉脱磷造渣工艺中,首先需要准备好合适的钢水。
钢水的成分和温度对脱磷效果有很大的影响,通常需要控制好钢水的硫含量、温度和其他杂质含量。
3.2 炉前处理在转炉脱磷造渣工艺中,炉前处理是非常重要的一环。
通过炉前处理可以将钢水中的杂质和不洁物去除,以减少对转炉脱磷造渣工艺的影响。
3.3 加入磷源在转炉中加入适量的磷源是实现脱磷的关键步骤。
常用的磷源有磷灰石、磷矿石等,选择合适的磷源对脱磷效果有很大的影响。
3.4 氧气吹炼在加入磷源后,转炉中开始进行氧气吹炼处理。
氧气的注入可以改变钢水中的气氛,促进磷元素与其他元素的反应,生成易于脱离炉渣的化合物。
3.5 炉渣处理转炉脱磷造渣过程中产生的炉渣需要进行处理。
一般情况下,炉渣会经过冷却、处理、分离等步骤,将渣中的磷元素尽可能去除,以保证炉渣的质量和性能。
4. 转炉脱磷造渣的关键技术转炉脱磷造渣的关键技术包括以下几个方面:4.1 磷源选择选择合适的磷源对于脱磷工艺的效果至关重要。
- 1、下载文档前请自行甄别文档内容的完整性,平台不提供额外的编辑、内容补充、找答案等附加服务。
- 2、"仅部分预览"的文档,不可在线预览部分如存在完整性等问题,可反馈申请退款(可完整预览的文档不适用该条件!)。
- 3、如文档侵犯您的权益,请联系客服反馈,我们会尽快为您处理(人工客服工作时间:9:00-18:30)。
莱钢转炉脱磷优化生产工艺措施
摘要:通过对现有装备和工艺技术能力进行系统分析,莱钢炼钢厂通过完善与优化转炉护炉技术、推广应用连铸新技术和新工艺、在铁水预处理、转炉、二次精炼、等方面的先进工艺技术,保证了炼钢生产的稳定运行。
关键词:转炉品种结构工艺优化
1、前言
高效转炉工艺技术主要以保证质量为前提,以高作业率为基本手段来实现高质量、低成本。
实现转炉的高效生产不仅需要科学管理,更重要的是持续不断的技术改造创新,采用优质耐材和先进工艺、生产设备技术,以不断提高转炉脱磷工艺技术装备水平。
莱钢炼钢转炉系统经过近年来改革和发展,坚持走引进、消化、吸收、再创新的道路,在品种、质量等方面有了质的飞跃,而且自主开发集成了多项关键技术。
目前,莱钢炼钢系统主要包括转炉炼钢和电炉炼钢,转炉炼钢现有3座50t转炉、1座60t转炉,5座120t转炉,相应配套小方坯连铸机、带钢坯连铸机、矩形坯连铸机、异型坯连铸机、板坯连铸机,生产能力为1 000万t/a。
莱钢炼钢厂针对实际生产中存在的薄弱工艺环节,对现有设备工艺进一步优化改造,提高了生产装备水平,完善炼钢新工艺、新技术,进一步发挥了转炉的潜能,提高了质量,降低了成本。
2、依靠技术创新,提升工艺水平
自金融危机以来。
全球钢铁消费需求不断下滑,国内钢企面临日益严峻的增支减利和结构优化调整压力。
为了更好地生存与发展,坚持以效益为中心,以技术创新为手段,立足于自主开发,加快新技术和新工艺的集成应用,大力发展循环经济,挖掘节能降耗潜力;同时加大高端新产品开发力度,提高产品质量,改善品种结构,积极应对市场变化。
莱钢炼钢系统充分发挥广大工程技术人员的聪明才智,大力开展技术攻关,提升工艺技术水平,促进了生产顺行,改善了产品质量,降低了生产成本。
特别是在炼钢系统,不断开发和应用新技术、新工艺,依靠技术进步和创新,工艺降本增效和新产品开发工作取得了显著成效。
3、转炉炼钢工艺过程
在转炉炼钢过程中,通过氧枪向熔池内吹入氧气,与铁水中的碳、硅、磷、硫等元素反应生成炉渣、废气等,同时释放热量使熔液的温度升高,进而得到所需的钢种。
该过程的原料包括:主原料(废钢和铁水)和辅原料(氧气、石灰、铁矿石、白云石等),最后的温度和成分(主要指熔池碳含量)要求合格的钢水。
在吹炼之前,由静态模型对整个炼钢过程需要的氧气量做出估算,吹炼进行到该值的86%左右时,进行第一次副枪检测,然后将检测到的熔池碳含量、熔池温度与本
炉的冶炼目标值相比较,确定出本炉需要的补吹氧气量和补加冷却剂量,继续吹炼,直至得到合格的钢水,转炉冶炼一炉钢的操作过程由装料、吹炼、测温、取样、出钢、除渣构成。
4、转炉脱磷工艺优化
脱磷是炼钢工艺的核心问题之一,贯穿于炼钢工艺发展的始终,随着钢铁工业的不断发展,高效化、洁净化已成转炉发展的主要方向。
国外先进钢铁企业已建立起以转炉脱磷预处理和少渣冶炼为技术平台的洁净钢生产体系,其突出的优点已被人们所认识,已成为我国钢铁企业发展的一个重要方向。
转炉脱磷预处理工艺的技术是转炉高效洁净钢生产工艺的关键技术之一,炉渣的脱磷能力决定了脱磷预处理工艺能够达到的处理极限,是转炉脱磷预处理制定造渣工艺和供氧工艺的基础,同时也为脱碳精炼工艺的制定提供了理论依据,实现快速脱磷的工艺措施应从以下几个方面入手:
4.1 溅渣工艺
溅渣的主要作用是通过溅渣形成的溅渣层耐腐蚀性较好,可抑制炉衬砖表面的氧化脱碳,又能减轻高温熔渣对炉衬砖的侵蚀冲刷,从而保护炉衬砖,提高炉衬的使用寿命。
转炉溅渣工艺参数的优化? 包括留渣量、终渣成分、分阶段溅渣枪位、溅渣时间、氮气工作压力、主要溅渣区域等。
溅渣护炉的技术是:利用MgO含量达到饱和或过饱和的炼钢终点渣,通过高压氮气的吹溅,是其在炉衬表面形成一层高熔点的熔渣层,并与炉衬很好地黏结附着。
炉渣脱磷能力是实现快速脱磷的热力学基础条件之一,铁水脱磷预处理过程,造渣工艺的核心问题是如何提高石灰成渣速度,低温石灰成渣问题必须通过配加一定的熔剂实现,因此研究熔剂对石灰成渣速度的影响是实现快速成渣的关键。
4.2 供氧优化工艺
转炉作为高效化冶炼设备,其高效在于供氧的高效,当造渣工艺确定后,如何确定供氧强度是实现高效脱磷的关键。
莱钢自转炉扩容改造后,进行了大幅度提高供氧流量的研究,供氧强度提高到 4.5(m3/min·t),每炉平均吹炼时间降低到10min,缩短了冶炼周期,提高了转炉的生产效率。
此外,通过不断优化冶炼工艺,加强化渣操作,减少喷溅,提高了终点成分的保障能力,降低了再吹率,缩短了镇静时间,从而达到了转炉不等成分直接出钢,转炉冶炼周期缩短到18min以下,二次拉碳率也降低到1.5%。
4.3 顶底复吹工艺技术
复吹转炉具有较强的底搅能力,能够为脱磷反应提供良好动力学条件,对于莱钢120t转炉,投产初期就采用顶底复吹技术,底吹气体为氮气,目前底吹供气强度为0.03~0.1(m3/min·t)。
通过对该技术的引进消化和改进创新,对底吹风口的选择、风口布置结构进行了优化,注重提高底吹风口寿命和复吹比例,强调底吹风口裸露,提高了底吹效果。
由于复吹转炉底搅气体可调范围较大,对于
不同吨位的转炉,实际生产中采用的底搅气体强度存在一定差异,合理制定转炉脱磷预处理底搅工艺具有重要意义。
转炉复吹技术不仅创造了良好的经济效益,而且为提高产品的质量创造了条件,特别是为开发高难度、高附加值的新钢种提供了良好的条件。
5、结语
通过完善优化转炉脱磷工艺技术,稳定脱磷效果;优化转炉复吹技术,提高复吹比例和底吹效果;优化转炉挡渣技术,减少钢包渣量;进一步完善钢水快速精炼技术和低碳钢生产技术,实现了产能大幅度提高,创造了可观的经济效益。
参考文献
[1]杜松林.转炉两步脱氧工艺研究[J].钢铁,2005年04期.
[2]陈爱梅,张晓光,李炯伟.转炉高效供氧技术的开发与应用[J].包钢科技;2008年04期.
[3]王荣,李伟东,孙群.转炉炼钢脱氧工艺的优化[A].2010年全国炼钢—连铸生产技术会议文集[C],2010年.
[4]孟劲松.LF合成精炼渣优化与深脱硫工艺研究[D].东北大学,2006年.
[5]原丽君,田勇,马勇,王德绪,张守东.转炉合金优化控制系统的开发与应用[J].鞍钢技术,2010年01期.。