东软睿驰-电池系统安全
国内BMS电池管理系统企业一览

国内BMS电池管理系统企业一览随着电动汽车、储能系统和新能源设备的普及,BMS(Battery Management System,电池管理系统)逐渐成为关键技术之一。
BMS是保证电池安全、延长电池寿命、提高电池性能的核心设备,也是电动汽车智能化和可靠性的重要保证。
在国内,BMS电池管理系统企业逐渐壮大,市场需求也不断增加。
本文将为您介绍几家主要的国内BMS电池管理系统企业。
珂兰特克珂兰特克(Contec)成立于1975年,是台湾领先的电子测量仪器制造商。
其BMS电池管理系统主要应用于电动汽车、太阳能储能系统、铁路交通、电力能源等各个领域。
其产品以高集成度、高稳定性、高精度为特点,深受市场认可。
澳度电子澳度电子(Aotuo Electronics)成立于2006年,是一家专业从事电池管理系统的设计、开发、生产的高科技企业。
其BMS电池管理系统已广泛应用于电动汽车、储能系统、船舶、物流车等行业。
澳度电子的BMS电池管理系统以高可靠性、高智能、高成本性为特点,为其用户提供高品质的电池管理系统方案。
香港盛干科技香港盛干科技(Sungan)是一家专业从事电池管理和电源管理控制器的生产企业,其BMS电池管理系统主要应用于储能系统、电动汽车等领域。
盛干科技的BMS电池管理系统以高安全性、稳定性和智能化为特点,能够为用户提供全方位的技术服务和支持。
铃木铃木(Suzuki)是一家世界知名的汽车电子和半导体制造企业。
其BMS电池管理系统广泛应用于电动汽车、储能系统、智能家居等领域。
铃木的BMS电池管理系统以先进的技术、高品质的产品、优质的服务赢得了用户的信赖和赞誉。
重庆赛威电子重庆赛威电子(Sewiton)是一家专业从事电池管理系统、锂电池模组、电池回收业务的企业。
其BMS电池管理系统涵盖了车载、储能、通讯等多个领域。
重庆赛威电子的BMS电池管理系统以精湛的技术、先进的设计和严谨的测试保证高质量的产品和可靠的服务。
电动汽车用电池管理系统功能安全要求及试验方法

电动汽车用电池管理系统功能安全要求及试验方法随着电动汽车的快速发展,电池管理系统的功能安全显得尤为重要。
本文旨在提出电动汽车用电池管理系统的功能安全要求及试验方法,以确保电动汽车的安全性和可靠性。
首先,电动汽车的电池管理系统应具备以下功能安全要求:1. 安全性能要求电池管理系统应具备完善的故障诊断和保护机制,能够在出现故障时快速、准确地诊断和处理问题,确保电池系统的安全性能。
2. 可靠性要求电池管理系统应具备高可靠性,能够在各种复杂环境下稳定运行,并保证电池寿命的长久使用。
3. 兼容性要求电池管理系统应兼容不同型号、不同厂家的电池,并能在不同的车型中实现良好的兼容性。
4. 数据安全要求电池管理系统应具备保护用户数据的能力,防止数据泄露或丢失,确保用户数据的安全性。
其次,针对以上要求,我们提出以下试验方法:1. 安全性能试验通过对电池系统进行各种故障测试,如短路、过流、过压等,检测电池管理系统的故障诊断和保护机制是否能够快速、准确地识别和解决问题。
2. 可靠性试验通过长时间的高温、低温、高湿等环境测试,检测电池管理系统是否能够在不同复杂环境下稳定运行,并保证电池寿命的长久使用。
3. 兼容性试验通过对不同型号、不同厂家的电池进行测试,检测电池管理系统是否能够在不同的车型中实现良好的兼容性。
4. 数据安全试验通过随机破解、数据泄露等测试,检测电池管理系统是否具备保护用户数据的能力,防止数据泄露或丢失,确保用户数据的安全性。
综上,电动汽车用电池管理系统的功能安全是电动汽车安全性和可靠性的重要保障。
通过对电池管理系统的功能安全要求和试验方法的探讨,可以为电动汽车的安全发展提供有力的保障。
电动汽车动力电池系统安全方法
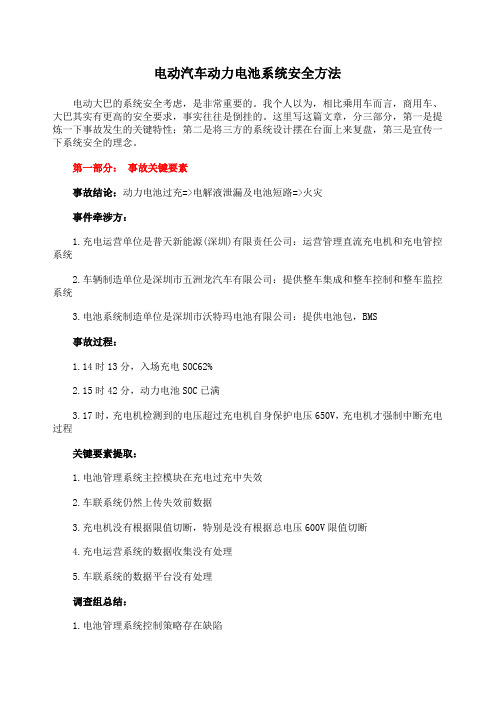
电动汽车动力电池系统安全方法电动大巴的系统安全考虑,是非常重要的。
我个人以为,相比乘用车而言,商用车、大巴其实有更高的安全要求,事实往往是倒挂的。
这里写这篇文章,分三部分,第一是提炼一下事故发生的关键特性;第二是将三方的系统设计摆在台面上来复盘,第三是宣传一下系统安全的理念。
第一部分:事故关键要素事故结论:动力电池过充=>电解液泄漏及电池短路=>火灾事件牵涉方:1.充电运营单位是普天新能源(深圳)有限责任公司:运营管理直流充电机和充电管控系统2.车辆制造单位是深圳市五洲龙汽车有限公司:提供整车集成和整车控制和整车监控系统3.电池系统制造单位是深圳市沃特玛电池有限公司:提供电池包,BMS事故过程:1.14时13分,入场充电SOC62%2.15时42分,动力电池SOC已满3.17时,充电机检测到的电压超过充电机自身保护电压650V,充电机才强制中断充电过程关键要素提取:1.电池管理系统主控模块在充电过充中失效2.车联系统仍然上传失效前数据3.充电机没有根据限值切断,特别是没有根据总电压600V限值切断4.充电运营系统的数据收集没有处理5.车联系统的数据平台没有处理调查组总结:1.电池管理系统控制策略存在缺陷2.充电系统功能不完善3.监控数据不被重视4.车--充电机--后台监控等缺乏系统的安全保护设计调查组提议的改进措施:1.电池企业:改进BMS设计2.充电企业:充电设施增设限制过充的措施3.整车企业a.布置改进:对结构、内饰材料、高低压电缆进行改进设计b.布置改进:控制电池箱相对集中的车辆尾部电池舱的环境温度第二部分:相关的系统设计要素大巴的结构布置示意图,可以如图1所示。
根据参考文献1,沃特玛基于客车的系统是BMS整套电池管理系统,包括主机模块、采集模块、显示屏模块、绝缘检测模块、CAN盒等电池管理主机模块(BMS):BMS主模块可接收BMU(电池单体信息采集模块)部件上传的电池组信息,计算电池容量,健康状态等,能随时给出电池组整个系统的剩余容量。
新能源汽车电池管理系统的可靠性与安全性研究
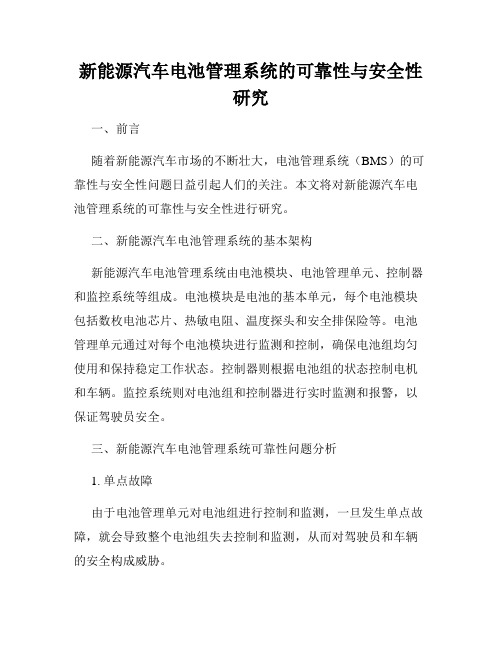
新能源汽车电池管理系统的可靠性与安全性研究一、前言随着新能源汽车市场的不断壮大,电池管理系统(BMS)的可靠性与安全性问题日益引起人们的关注。
本文将对新能源汽车电池管理系统的可靠性与安全性进行研究。
二、新能源汽车电池管理系统的基本架构新能源汽车电池管理系统由电池模块、电池管理单元、控制器和监控系统等组成。
电池模块是电池的基本单元,每个电池模块包括数枚电池芯片、热敏电阻、温度探头和安全排保险等。
电池管理单元通过对每个电池模块进行监测和控制,确保电池组均匀使用和保持稳定工作状态。
控制器则根据电池组的状态控制电机和车辆。
监控系统则对电池组和控制器进行实时监测和报警,以保证驾驶员安全。
三、新能源汽车电池管理系统可靠性问题分析1. 单点故障由于电池管理单元对电池组进行控制和监测,一旦发生单点故障,就会导致整个电池组失去控制和监测,从而对驾驶员和车辆的安全构成威胁。
2. 维护成本高由于电池管理单元对电池模块进行实时监测和控制,一旦电池管理单元发生故障,往往需要更换整个电池模块,维修成本高,维护难度大。
3. 电池容量衰减电池的容量随着使用次数的增加会逐渐下降,这就需要BMS 能够及时检测电池的容量,并对电池进行均衡充放电,以延长电池使用寿命。
但是,由于电池的容量衰减是随机的,而且受多种因素影响,所以BMS的算法难以完全准确。
四、新能源汽车电池管理系统安全性问题分析1. 温度过高电池的温度过高会导致电池损坏,从而威胁驾驶员和车辆的安全。
因此,BMS需要能够及时检测电池的温度,并通过防爆、降温等措施避免温度过高的情况发生。
2. 电池短路电池短路会引起电流过大,从而威胁驾驶员和车辆的安全。
因此,BMS需要能够及时检测电池的电流,一旦出现电流过大的状况,就需要及时停止使用电池组。
3. 输电线束寿命输电线束是连接电池组和控制器的关键组件,一旦输电线束老化或损坏,就会引起电池组故障或控制器失效,从而威胁驾驶员和车辆的安全。
电池包自动测试系统安全操作及保养规程

电池包自动测试系统安全操作及保养规程前言电池包自动测试系统是一种用于自动化测试电池组的设备。
为了保障工作人员和设备的安全,特制订了本规程,以规范电池包自动测试系统的使用、操作和保养。
请严格遵守规程中的各项要求。
一、安全操作1. 设备启动1.1 在启动设备前,先检查设备及其附属设备是否连接良好,检查各线缆是否损伤或老化。
1.2 先接好电源线,然后再接好数据线。
启动设备过程中,应按操作流程依次进行。
1.3 启动设备时,请将其放置在平稳的表面上,不要将它放在可移动或不稳定的物品上,或者不易固定的表面。
2. 使用设备2.1 请不要将潮湿的手靠近或触摸设备,这可能会导致电击或设备短路。
2.2 使用设备前,应按照技术手册指引进行调试和操作,不要随意更改参数。
如果不熟悉设备的操作,请先咨询相关技术人员。
2.3 操作人员在使用设备时应戴防静电手套,并在操作前及操作中进行静电排除。
2.4 必须使用适合的测量设备或工具,使用不当的工具或设备可能会损坏设备或导致不安全的操作。
2.5 操作人员在使用设备时,应始终关注设备的运行情况,以及传送带和其他部件是否正常工作。
如发现异常,应立即停止设备,并通知负责人员处理。
2.6 操作人员在使用设备时,应根据需要进行适当的维护和保养,如手动清洁、润滑等操作。
3. 维护和保养3.1 操作人员应定期清理设备、传送带、传感器和其他组件,以保证设备在正常运行中的清洁、干燥和无尘。
3.2 定期进行设备维护和保养,如钳紧螺丝、润滑传送带等,以确保设备始终处于最佳状态。
3.3 操作人员应时常检测设备各部件的运转情况,如传送带是否有松动、损坏等情况,及时进行维护和更换。
4. 安全环境4.1 在使用设备时,请保证环境温度适宜,不要让设备过热或过冷。
4.2 在使用设备时,请保证设备周围通风良好,避免积尘和异味损害设备。
4.3 操作人员在使用设备时,请注意通道的宽度、高度和安全距离,确保人员不会受到伤害或困了。
电动汽车动力电池热失控过程分析及预警机制设计
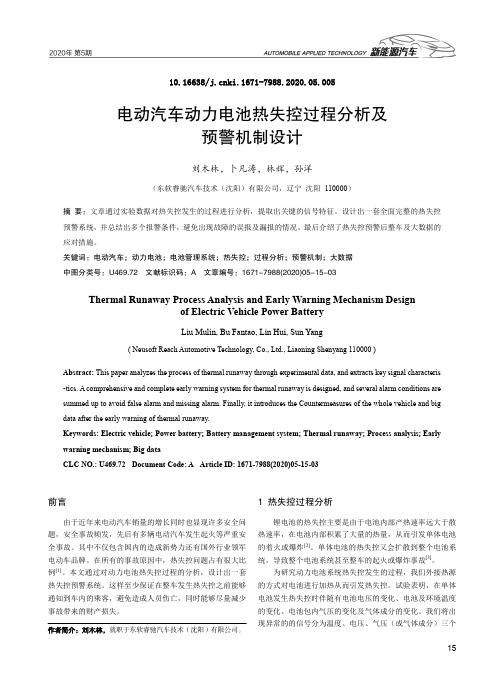
10.16638/ki.1671-7988.2020.05.005电动汽车动力电池热失控过程分析及预警机制设计刘木林,卜凡涛,林辉,孙洋(东软睿驰汽车技术(沈阳)有限公司,辽宁沈阳110000)摘要:文章通过实验数据对热失控发生的过程进行分析,提取出关键的信号特征。
设计出一套全面完整的热失控预警系统,并总结出多个报警条件,避免出现故障的误报及漏报的情况。
最后介绍了热失控预警后整车及大数据的应对措施。
关键词:电动汽车;动力电池;电池管理系统;热失控;过程分析;预警机制;大数据中图分类号:U469.72 文献标识码:A 文章编号:1671-7988(2020)05-15-03Thermal Runaway Process Analysis and Early Warning Mechanism Designof Electric Vehicle Power BatteryLiu Mulin, Bu Fantao, Lin Hui, Sun Yang( Neusoft Reach Automotive Technology, Co., Ltd., Liaoning Shenyang 110000 )Abstract: This paper analyzes the process of thermal runaway through experimental data, and extracts key signal characteris -tics. A comprehensive and complete early warning system for thermal runaway is designed, and several alarm conditions are summed up to avoid false alarm and missing alarm. Finally, it introduces the Countermeasures of the whole vehicle and big data after the early warning of thermal runaway.Keywords: Electric vehicle; Power battery; Battery management system; Thermal runaway; Process analysis; Early warning mechanism; Big dataCLC NO.: U469.72 Document Code: A Article ID: 1671-7988(2020)05-15-03前言由于近年来电动汽车销量的增长同时也显现许多安全问题,安全事故频发,先后有多辆电动汽车发生起火等严重安全事故。
车辆部件级分割方法、装置以及电子设备[发明专利]
![车辆部件级分割方法、装置以及电子设备[发明专利]](https://img.taocdn.com/s3/m/1f7b43f4a300a6c30c229ffe.png)
专利名称:车辆部件级分割方法、装置以及电子设备专利类型:发明专利
发明人:胡骏,李根,田欢,刘威,袁淮
申请号:CN202011644516.1
申请日:20201231
公开号:CN112767412A
公开日:
20210507
专利内容由知识产权出版社提供
摘要:本申请提供了一种车辆部件级分割方法、装置以及电子设备,涉及图像处理技术领域,缓解了对车辆图像的分割处理精细度较低技术问题。
该方法包括:获取待处理2D图像、待处理2D图像中的目标车辆上的关键点的2D坐标、目标车辆的3D模型以及关键点在3D模型上对应的3D坐标;其中,关键点是预先设定的车辆特定位置,如车前窗左上角点、左前车轮中心点等,车辆特定位置用于表示车辆部件信息;根据2D坐标、3D坐标以及预设相机内参通过PnP算法进行计算,得到目标车辆的姿态信息;基于目标车辆的姿态信息,将含有车辆部件信息的3D模型投影至待处理2D图像上,得到目标车辆的部件级分割2D图像。
申请人:东软睿驰汽车技术(沈阳)有限公司
地址:110000 辽宁省沈阳市沈抚新区金枫街75-1号
国籍:CN
代理机构:北京超成律师事务所
代理人:孔默
更多信息请下载全文后查看。
东软睿驰汽车技术(沈阳)有限公司与国家知识产权局其他二审行政判决书
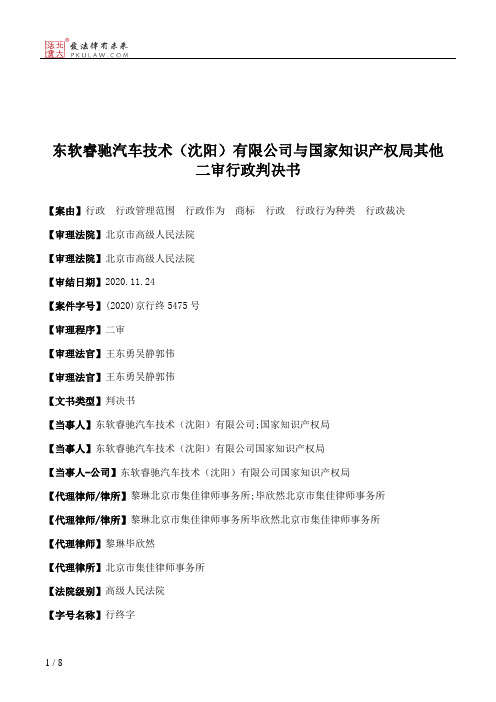
东软睿驰汽车技术(沈阳)有限公司与国家知识产权局其他二审行政判决书【案由】行政行政管理范围行政作为商标行政行政行为种类行政裁决【审理法院】北京市高级人民法院【审理法院】北京市高级人民法院【审结日期】2020.11.24【案件字号】(2020)京行终5475号【审理程序】二审【审理法官】王东勇吴静郭伟【审理法官】王东勇吴静郭伟【文书类型】判决书【当事人】东软睿驰汽车技术(沈阳)有限公司;国家知识产权局【当事人】东软睿驰汽车技术(沈阳)有限公司国家知识产权局【当事人-公司】东软睿驰汽车技术(沈阳)有限公司国家知识产权局【代理律师/律所】黎琳北京市集佳律师事务所;毕欣然北京市集佳律师事务所【代理律师/律所】黎琳北京市集佳律师事务所毕欣然北京市集佳律师事务所【代理律师】黎琳毕欣然【代理律所】北京市集佳律师事务所【法院级别】高级人民法院【字号名称】行终字【原告】东软睿驰汽车技术(沈阳)有限公司【被告】国家知识产权局【权责关键词】证据【指导案例标记】0【指导案例排序】0【本院查明】经审理查明:原审法院查明的事实属实,证据采信得当,且有被诉决定、诉争商标档案、引证商标档案、双方当事人在行政程序和诉讼程序中提交的证据,以及当事人陈述等在案佐证,本院予以确认。
另查,2020年8月13日,引证商标一的注册商标撤销公告刊登于第1707期《商标公告》上,引证商标一在全部服务上的注册被撤销。
该事实有《商标公告》等在案佐证。
【本院认为】本院认为:2019年商标法第三十条规定,申请注册的商标,凡不符合本法有关规定或者同他人在同一种商品或类似商品上已经注册的或者初步审定的商标相同或者近似的,由商标局驳回申请,不予公告。
《最高人民法院关于审理商标授权确权行政案件若干问题的规定》第二十八条规定,人民法院审理商标授权确权行政案件的过程中,商标评审委员会对诉争商标予以驳回、不予核准注册或者予以无效宣告的事由不复存在的,人民法院可以依据新的事实撤销商标评审委员会相关裁决,并判令其根据变更后的事实重新作出裁决。
解析动力电池包集成与系统安全
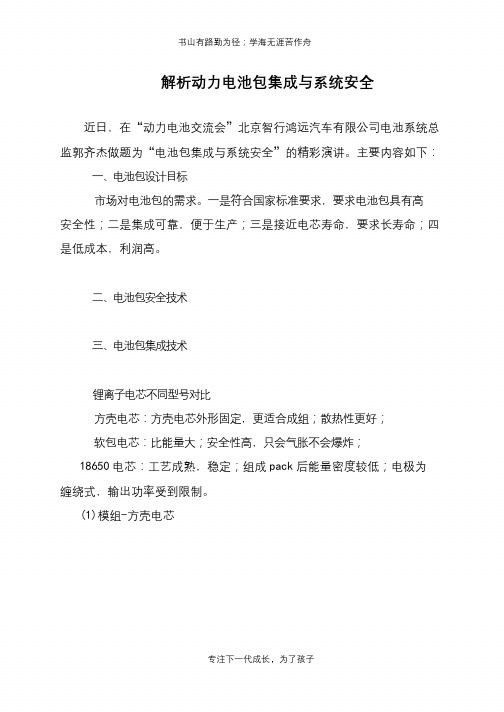
书山有路勤为径;学海无涯苦作舟
解析动力电池包集成与系统安全
近日,在“动力电池交流会”北京智行鸿远汽车有限公司电池系统总
监郭齐杰做题为“电池包集成与系统安全”的精彩演讲。
主要内容如下:
一、电池包设计目标
市场对电池包的需求。
一是符合国家标准要求,要求电池包具有高
安全性;二是集成可靠,便于生产;三是接近电芯寿命,要求长寿命;四是低成本,利润高。
二、电池包安全技术
三、电池包集成技术
锂离子电芯不同型号对比
方壳电芯:方壳电芯外形固定,更适合成组;散热性更好;
软包电芯:比能量大;安全性高,只会气胀不会爆炸;
18650电芯:工艺成熟,稳定;组成pack后能量密度较低;电极为缠绕式,输出功率受到限制。
(1)模组-方壳电芯
专注下一代成长,为了孩子。
电动汽车单体电池采集电路故障分析与对策
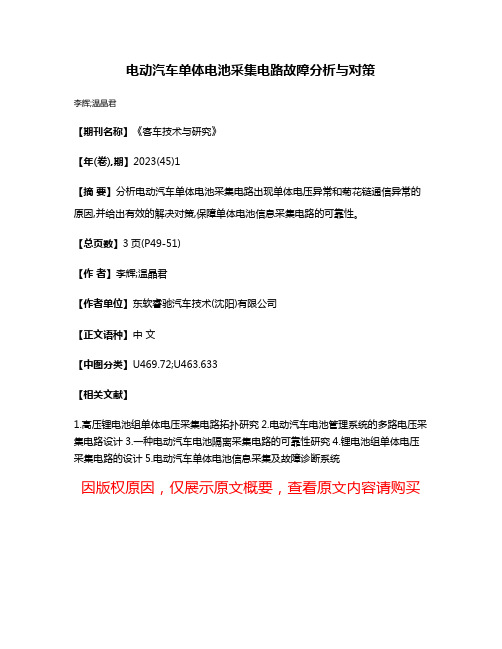
电动汽车单体电池采集电路故障分析与对策
李辉;温晶君
【期刊名称】《客车技术与研究》
【年(卷),期】2023(45)1
【摘要】分析电动汽车单体电池采集电路出现单体电压异常和菊花链通信异常的原因,并给出有效的解决对策,保障单体电池信息采集电路的可靠性。
【总页数】3页(P49-51)
【作者】李辉;温晶君
【作者单位】东软睿驰汽车技术(沈阳)有限公司
【正文语种】中文
【中图分类】U469.72;U463.633
【相关文献】
1.高压锂电池组单体电压采集电路拓扑研究
2.电动汽车电池管理系统的多路电压采集电路设计
3.一种电动汽车电池隔离采集电路的可靠性研究
4.锂电池组单体电压采集电路的设计
5.电动汽车单体电池信息采集及故障诊断系统
因版权原因,仅展示原文概要,查看原文内容请购买。
- 1、下载文档前请自行甄别文档内容的完整性,平台不提供额外的编辑、内容补充、找答案等附加服务。
- 2、"仅部分预览"的文档,不可在线预览部分如存在完整性等问题,可反馈申请退款(可完整预览的文档不适用该条件!)。
- 3、如文档侵犯您的权益,请联系客服反馈,我们会尽快为您处理(人工客服工作时间:9:00-18:30)。
02 机械安全
4.2.1机械安全
电池系统应具备足够的机械强度, 保证在整车正常使用的生命周期内不会因振动、机械冲击等工况引发安全风 险。
机械安全
基于正碰、侧碰、侧柱 碰、底碰、石击的电池及
1、环境条件:0℃以上,风速不大于2.5km/h; 2、增加:对电池包或系统起到保护作用的车身结构,可参与火烧实验; 3、补充耐火隔板要求; 4、安全要求:删除2min自熄灭,保留不爆炸
1、按照GB/T 2423.18严酷等级5;
1、按照GB/T 28046.4(5.2.2);
6
盐雾
2、试验周期28天{(2h喷雾+22h湿热存储)
系统级
1. 电池壳体,包括上盖、底板以 及密封条等附件,应采用阻燃 材料,以避免明火引燃整车
2. 电池包内部高压线束,包括主 回路高压线束、 电池电压采集 线束等,建议具有熔断保护, 防止在热失控期间因线束受损 短路引起的二次伤害
4.2.2.3阻燃设计
概述
为延缓热失控扩散,延长乘员逃生时间,电池系统的零部件应尽量选用阻燃等级较高或者不燃烧的材料,这样即使在热失控的极端环境 下,这些零部件至少不会进一步加剧反应。 1. 电池系统内部有机材料(如结构胶、导热胶等)应采用阻燃等级较高的材料 2. 应重点评估电池包内薄片非金属材料的阻燃等级 3. 其他与电芯直接接触材料,以及电气件、热管理部件等应选用阻燃等级较高或者不燃烧的材料 4. 在电芯热失控以后,建议评估喷发物对模组周围带来的绝缘下降引起的短路造成的二次加热
整车安全设计
振动可靠性安全设计
全生命周期高防护等级安 全设计
4.2.1.1 基于正碰、侧碰、侧柱碰、底碰、石击的电池及整车安全设计
针对于整车碰撞衍生出电池系统碰撞、挤压工况,需要结合整车设计及电池系统安装位置有针对性的进行结 构设计保证电池系统的机械安全。 电池系统的结构强度应至少满足《GB/T 31467.3-2015 电动汽车用锂离子动力蓄电池包和系统第 3 部分: 安全性要求与测试方法》中电池系统模拟碰撞的标准要求或整车企业的标准要求。
4.2.1.3 全生命周期高防护等级安全设计
安装在车身外部的电池系统应具备 IP67 或以上的防护等级,并应定期维护检测以避免整个生命周期内防护 等级在使用过程造成降低。
电池系统接触防护
1. 集成式 BDU,并具备外壳防护设计; 2. 模组级别正负极位置防护设计; 3. 高压连接器防护:
电池系统防水防尘
4.2.2.2热扩散防护
电池级
1. 相邻电池间建议具备一定的隔 热设计,如增加绝热毡、气凝 胶、云母等隔热阻燃材料,延 缓热蔓延。
2. 电芯防爆设计(如防爆阀等) 指向建议避免直接朝向相邻电 芯,防止产生链式反应。电芯 的开阀保护时间,需要在单电 芯、模组中保持一致性,开阀 的条件应在一定的偏差范围内。
热安全设计案例
壳体隔热防护
壳体采用5mm气凝胶隔热毡,在火焰温度不超过400℃时(铁 锂电芯热失控时最高温度),隔热毡背温100℃左右。
黄色部分为 隔热毡材料
电芯间 隔热毡
电 芯
气凝胶隔热材料——平板加热模拟实际热失控实验
测试项目:铝板加热模拟实际热失控 测试平台:平板加热器 测试参数:温度 400℃(LFP热失控时最高温度) 测试材料:气凝胶隔热毡(PI膜包边处理) 测试尺寸:148*97*1.5mm
《电动汽车安全指南(2019版)》宣贯会
电池系统安全
单位名称:东软睿驰汽车技术(沈阳)有限公司 2020年6月12日
目录
1 电池系统安全 2 机械安全 3 热安全 4 后续建议
01 电池系统安全
4.2电池系统安全
4.2 电池系统安全
基于市场上出现的电动汽车泡水、碰撞、底盘划伤后的起火事件,电池系统安全从 系统设计(机械安全、热安全、电气安全)、安全测试、生产三阶段展开,保证电 池系统的安全。
压力释放装置有效性 无
压力释放装置
压力
出现
时间
有无隔热装置的热趋势
有 无
隔热装置
温度
出现
有
时间
04 后续建议
后续建议
序 号
测试项目
GBT-31467.3
GB 38031-2020
采用正弦波扫频,7-18Hz:10m/s²;18-30Hz: 不低于制造商规定的正常SOC工作范围的50%;
1
振动
10m/s²逐渐减少到2m/s²;30-50Hz:2m/s²。 分三个轴进行,分别施加随机和定频振动载荷;
1. 电池系统箱体防护要求: 2. 防水透气阀:与箱体配合处防护在全生命周期等级达到 IP67 等级; 3. 电气接口防护要求:
电池系统防爆防护
1. 电池系统应具备有效的泄压装置,可以快速平衡内外部气压变化,防止因内部气压过高造成壳体变形引 起的防护等级降低或失效。 泄压装置安装的位置和方向应避免对乘员舱或车辆周边人员造成人身伤害, 且应避免引燃整车。
4
挤压
1、挤压板形式:R75半圆柱体,长度大于测试 对象高度,但不超过1m;2、挤压截止力: 200kN;3.挤压速度:无
1、挤压板形式:二选一,增加UN GTR No.20三拱挤压头作为可选; 2、挤压截止力:100kN,同1号修改单;3、挤压速度:增加,同单体
5
外部火烧
1、环境条件:试验环境温度,未规定风速; 2、汽油液面与测试对象距离可由双方商定; 3、间接燃烧阶段隔板未定义; 4、安全要求:无爆炸,若有火苗,应在火源移 开后2min内熄灭
碰撞安全设计
挤压安全设计
防石击安全设计
1. 应分析碰撞过程中电池箱体及其内部结 构(电池模组、高低压线束)产生的最 大变形情况,并结合电池模组允许的最 大变形量来判断碰撞过程中的安全风险;
2. 应具有吸能效果的结构设计,设计时应 考虑相应材料的塑性要求;
3. 应具有合理的内部加强筋设计,提高整 体结构强度;
壳体隔热毡布置示意图
平板加热器
温度记录仪
600
400℃加热温度变化
400
背面
正面
温度/℃
200
气凝胶隔热毡
0
0
200
400
600
800
时间/s
通过增加隔热毡厚度,如5mm可在400℃温度时正面温度15min控制在100℃左右。
热安全设计案例
某电池包使用了电池包减压阀和耐热盖,针对热蔓延设计了对策。
外梁设计 内梁设计
03 热安全
4.2.2 热安全
通过热管理系统对电池系统进行加热、散热、均衡、保温;电池系统内部要有防止热扩散的结构设计;关键部件 的阻燃设计,来确保电池系统的热安全。
热管理系统
冷却 加热 均衡 保温
防止热扩散
阻燃
热安全
4.2.2.1可靠的热管理系统
概述
无论在高温或是低温,都有引发电池热失控的风险,而电池热管理系统的设计目标就是结合BMS控制策略和调整功能,控制电池工作在 舒适温度范围内、并降低电池之间的温差实现性能均衡,保证系统热安全并延长系统寿命。要实现以上目标,需从冷却、加热、保温三 个方面进行设计,同时还需保证整个系统的气密安全,不允许发生冷却液泄露。需关注低温冷却管路可能引发的冷凝水,避免因此而导 致的绝缘、短路安全隐患。
3. 为适应不同工况,散热系统可按有无chiller以及风扇挡位分为多种回路: ①风冷散热系统中,能够对风扇状态进行检测并判定是否工作正常;当风扇或冷却系统其它部件出
现故障时能及时报警并采取保护措施(如限制充放电功率等); ②液冷系统中,能够对压缩机、水泵等部件进行检测并判定是否工作正常;当冷却系统出现故障时能及时报
模组级
1. 模组间建议考虑合适的间距, 具备一定的防止热蔓延的能力; 建议采用隔热设计(如隔热罩 等),抑制热量在相邻模组间 的蔓延。
2. 设计合理的电连接孔、泄气孔 及火焰导向孔,防止蔓延
3. 对于不具备单体熔断功能的电 芯,模组建议采用可熔断连接 设计,防止电芯内短路时其他 并联电池产生电流倒灌,引发 热失控
1. 提高电池系统整体固有频率:
•
提高电池系统刚度:如增加车体安装点,优化固定梁结构设计;
•
减少电池系统的重量:轻量化的结构设计及材料选择;
2. 疲劳强度高的材料选择;
3. 提高电池系统强度:避免质量过度集中,在质量集中位置增强结构设计;固定梁焊接要求、结构紧固 件的选型及固定扭矩设计均应符合设计规范要求。
3、安全要求:无起火或爆炸现象
1、试验名:浸水;2、测试方法:样品连接好线束、接插件等部件,以下方法 二选一:1)同海水浸泡;2)新增IPX7;3、安全要求:1)方式一:无不小于100Ω/V,振动试 验后进行
单次扫频15min,共12次,3h。
区分装载在M1、N1类车和其他车辆,具体振动参数见标准
2 机械冲击 25g,15ms,半正弦冲击波形,z方向,3次
7g,6ms的半正弦波形,±z方向各6次 相邻两次冲击的间隔时间不小于5倍冲击脉冲持续时间
3 模拟碰撞 台车实验,实验方向:x和y方向
增加:存在多个安装方向,按照加速度大的安装方向进行试验
1. 根据指定的严苛工况下的系统发热量确定电池包散热形式及控制边界,保证电池最高温度不超过允许使用温度,且大多数时间能在舒适温度范围工作。
冷却 2. 建议正常工况下电池系统内部采集的温度点之间的最大温差不超过5℃,极限工况下最大温差不超过10℃,且能满足极限工况的连续运行(例如持续高速工况加快充)。
电池系统防腐防护
1. 在全生命周期内防腐的要求,要根据电池系统使用寿命要求和使用区域环境要求来确定电池系统的防腐 等级。