催化裂化装置加工常三线直馏柴油的工业实践
催化裂化柴油加工方案的探讨_黄新露

针 对 催 柴 加 氢 改 质 ,FRIPP 从 上 世 纪 90 年 代 开 发 最 大 量 提 高 柴 油 十 六 烷 值 的 MCI 技 术 , 并 于 1998 年 进 行 工 业 应 用 试 验 。 由 于 技 术 创 新 ,可 为 柴 油质量升级提供技术支撑, 该技术得到广泛应用, 并 获 得 2001 年 度 国 家 发 明 二 等 奖 。 在 第 一 代 MCI 技 术 基 础 上 ,FRIPP 在 催 化 剂 和 工 艺 技 术 上 进 一 步 改 进 ,开 发 了 第 二 代 MCI 技 术 ,并 于 2002 年 首 次 在 广 州 分 公 司 60×104t/a 柴 油 加 氢 装 置 成 功 应 用 。
图 1 中 国 石 化 2011 年 柴 油 馏 分 构 成
常减压柴油; 焦化柴油; 催化柴油; 加氢裂化柴油; 其他柴油
3 催柴加氢改质系列技术 如前所述,一方面由于石油资源的紧缺,催柴
在中国不得不作为成品柴油的一个重要组成部分; 另一方面,由于催柴富含芳烃,大幅改善其质量,尤 其是改善燃烧性能的难度较大。
按 照 环 保 法 规 要 求 , 预 计 2014 年 1 月 1 日 起 , 全国将实施车用柴油国Ⅳ标准,届时将要求柴油产 品 硫 含 量 不 大 于 50μg/g,十 六 烷 值 不 小 于 51。 如 何 全面提高柴油产品质量,满足现行和未来更为苛刻
石油炼制中催化裂化技术的应用教程

石油炼制中催化裂化技术的应用教程石油炼制是一项重要的工业过程,它将原油转化为各种有用的产品,如汽油、柴油和润滑油等。
催化裂化技术在石油炼制中起着举足轻重的作用。
本文将介绍催化裂化技术的应用教程,从催化裂化的基本原理到操作实践,为读者提供一个全面的了解。
催化裂化是指通过催化剂将较重的石油馏分转化为较轻的产品。
这项技术主要利用了催化剂对原油分子的选择催化作用。
具体来说,催化剂可以将较长的碳链裂解为较短的碳链,并在裂解过程中生成一系列有用的烃类化合物。
催化裂化技术因此获得了广泛应用,并成为石油炼制中最重要的工艺之一。
催化裂化技术的应用可以追溯到20世纪早期,随着工业技术的进步,催化裂化设备变得更加高效和稳定。
在今天的石油炼制厂中,催化裂化装置通常由催化裂化反应器、再生燃烧器、分馏装置等部分组成。
通过这些装置的组合,原油可以得到不同碳链长度的产品,以满足不同行业的需求。
在进行催化裂化反应之前,需要对原油进行预处理。
这一步骤通常包括脱硫、脱盐和脱水等过程,以确保催化剂的稳定性和活性。
在预处理完成后,将原油送入催化裂化反应器,与催化剂接触。
催化剂的选择非常重要,不同的催化剂会对反应产生不同的影响。
一般来说,选择能够降低碳链长度和增加产物收率的催化剂是最合适的。
催化裂化反应在高温高压条件下进行,通常是在500-600摄氏度和20-30大气压下。
这样的条件可以促使原油分子发生裂化和重合反应。
随着裂解反应的进行,分子在催化剂表面上发生化学反应,并生成较短的碳链分子。
这些产物醇生成较高的收率,可以进一步用于生产汽油、柴油等产品。
催化裂化技术的操作实践中,需要注意以下几点。
首先,保持催化剂的活性和稳定性非常重要。
催化剂往往在反应过程中会受到积炭和中毒等不利因素的影响,因此需要定期进行催化剂的再生或更换。
其次,合理的温度和压力控制有助于提高催化裂化的效果。
高温和高压会增加反应速率,但同时也可能导致不良的副反应发生,因此需要根据具体情况进行调整。
加氢裂化生产实习报告

竭诚为您提供优质文档/双击可除加氢裂化生产实习报告篇一:生产实习报告企业实习报告一、前言这学期刚开始,9月2号的那天,蔡老师给我们进行了一上午的实习动员,为我们整个学期的实习做了一个总体的安排。
这个学期的实习一共有16周,其中校内实习占10周,校外燕山实习占6周。
前半部分校内实习内容包括安全教育,u形管换热器的设计,典型设备、化工机器图纸的看图实习,压缩机、泵、阀的拆装及主要零件测绘实习,北区压缩机实验室的参观实习。
然后是燕山石化实习基地的下厂实习,主要包括燕华一铆、二铆车间的参观,培训中心的工艺流程仿真实训,炼油一厂二厂、化工一厂二厂、橡胶一厂、储运二厂、水务气体管理中心、有机化工厂、热力厂等的参观实习,正邦公司特种阀门检维修实践、垫片制造过程参观、实习,燕华技术科、工艺科的讲座、参观实习,燕山盛世达工业泵厂的双螺杆泵技术讲座、参观实习,塑胶制品厂参观,储运一厂10万立方米罐区参观。
企业实习结束后,还会有一系列的校内实习,这些实习都是蔡老师和张老师考虑各方面因素精心为我们安排的,老师们真的很辛苦,谢谢他们!由于一些因素,报告中难免会有纰漏、片面的地方,希望批评指正。
二、实习过程和内容1、实习动员(蔡纪宁)2、化工生产企业实习(张秋翔、王维民)1)炼油一厂炼油一厂的实习为期两天,主要学习了解了260万吨柴油加氢装置的原理和工艺流程。
柴油加氢精制是指油品在催化剂、氢气和一定的压力、温度条件下,含硫、氮、氧的有机化合物分子发生氢解反应,烯烃和芳烃分子发生加氢饱和反应的过程。
原料(催化柴油)经泵打入原料缓冲罐,再经泵打压,压力从4—5公斤升至70多公斤,再经缠绕管换热器换热,然后与氢混合,加热炉加至310℃,再进入反应器进行反应。
反应器顶部出来的轻油,底部出来的重油进入常压塔。
常压塔顶部出来的仍然是轻油,经侧线采出的有常一线:航空煤油可去航煤加氢,常二线可去柴油加氢,常三线可去高压加氢。
底油进入减压塔,其中减一线可去柴油加氢、减二减三线可去高压加氢、减四线是润滑油、减五线是油渣。
催化裂化实习报告
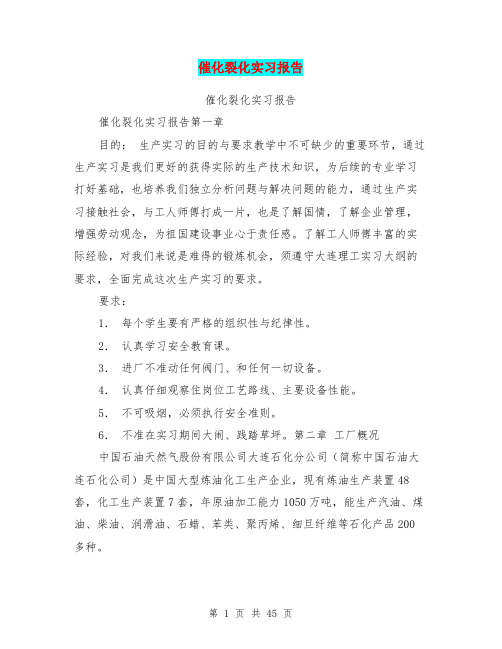
催化裂化实习报告催化裂化实习报告催化裂化实习报告第一章目的:生产实习的目的与要求教学中不可缺少的重要环节,通过生产实习是我们更好的获得实际的生产技术知识,为后续的专业学习打好基础,也培养我们独立分析问题与解决问题的能力,通过生产实习接触社会,与工人师傅打成一片,也是了解国情,了解企业管理,增强劳动观念,为祖国建设事业心于责任感。
了解工人师傅丰富的实际经验,对我们来说是难得的锻炼机会,须遵守大连理工实习大纲的要求,全面完成这次生产实习的要求。
要求:1.每个学生要有严格的组织性与纪律性。
2.认真学习安全教育课。
3.进厂不准动任何阀门、和任何一切设备。
4.认真仔细观察住岗位工艺路线、主要设备性能。
5.不可吸烟,必须执行安全准则。
6.不准在实习期间大闹、践踏草坪。
第二章工厂概况中国石油天然气股份有限公司大连石化分公司(简称中国石油大连石化公司)是中国大型炼油化工生产企业,现有炼油生产装置48套,化工生产装置7套,年原油加工能力1050万吨,能生产汽油、煤油、柴油、润滑油、石蜡、苯类、聚丙烯、细旦纤维等石化产品200多种。
公司地处黄海之滨天然不冻良港大连湾内,有自备海运码头和铁路栈桥,海陆运输条件完善,是我国重要的石化产品出口和转运基地之一,有多种高标号、环保型主导产品销往国际市常公司致力于强化企业管理,先后荣获全国首批荣获企业管理金马奖、全国质量效益型企业、全国节约能源先进企业、全国企业管理优秀企业、全国环境保护先进单位、全国设备管理先进单位、全国职工思想政治工作先进企业、全国“五一”劳动奖状等20多个国家级荣誉称号。
多年来,公司坚持“质量第一,以人为本,以质取胜,走质量效益型道路”的质量方针,产品出厂合格率连续23年保持100%。
公司的“七星”注册商标为全国驰名商标,辽宁省著名商标,在国内外用户中享有良好的信誉,公司生产的“七星”牌成品油、石蜡,“岩山”牌聚丙烯树脂、短纤维为辽宁名牌产品。
公司自1996年整体通过ISO9002质量体系认证以来,连年通过了复评。
重油催化裂化装置主要工艺流程说明
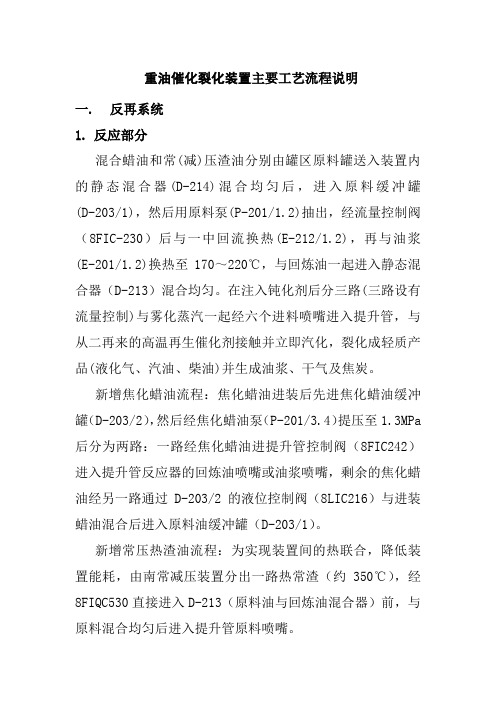
重油催化裂化装置主要工艺流程说明一. 反再系统1.反应部分混合蜡油和常(减)压渣油分别由罐区原料罐送入装置内的静态混合器(D-214)混合均匀后,进入原料缓冲罐(D-203/1),然后用原料泵(P-201/1.2)抽出,经流量控制阀(8FIC-230)后与一中回流换热(E-212/1.2),再与油浆(E-201/1.2)换热至170~220℃,与回炼油一起进入静态混合器(D-213)混合均匀。
在注入钝化剂后分三路(三路设有流量控制)与雾化蒸汽一起经六个进料喷嘴进入提升管,与从二再来的高温再生催化剂接触并立即汽化,裂化成轻质产品(液化气、汽油、柴油)并生成油浆、干气及焦炭。
新增焦化蜡油流程:焦化蜡油进装后先进焦化蜡油缓冲罐(D-203/2),然后经焦化蜡油泵(P-201/3.4)提压至1.3MPa 后分为两路:一路经焦化蜡油进提升管控制阀(8FIC242)进入提升管反应器的回炼油喷嘴或油浆喷嘴,剩余的焦化蜡油经另一路通过D-203/2的液位控制阀(8LIC216)与进装蜡油混合后进入原料油缓冲罐(D-203/1)。
新增常压热渣油流程:为实现装置间的热联合,降低装置能耗,由南常减压装置分出一路热常渣(约350℃),经8FIQC530直接进入D-213(原料油与回炼油混合器)前,与原料混合均匀后进入提升管原料喷嘴。
反应油气、水蒸汽、催化剂经提升管出口快分器分离出大部分催化剂,反应油气经过沉降器稀相沉降,再经沉降器(C-101)内四组单级旋风分离器分离出绝大部分催化剂,反应油气、蒸汽、连同微量的催化剂细粉经大油气管线至分馏塔人档下部。
分馏塔底油浆固体含量控制<6g/L。
旋分器分出的催化剂通过料腿返回到汽提段,料腿装有翼阀并浸没在汽提段床层中,保证具有正压密封,防止气体短路,汽提蒸汽经环形分布器进入汽提段的上中下三个部位使催化剂不仅处于流化状态,并汽提掉催化剂夹带的烃油气,汽提后的催化剂通过待生滑阀进入一再催化剂分布器。
常减压催化裂化实习报告

实习报告实习时间:xxxx年xx月xx日至xxxx年xx月xx日实习单位:xxxx石油炼化公司实习内容:常减压催化裂化一、实习背景随着我国经济的快速发展,对石油产品的需求日益增长,石油炼化行业的重要性日益凸显。
催化裂化技术作为炼油厂中重要的二次加工过程,是实现重油轻质化、提高石油利用率的关键技术。
为了更好地了解催化裂化工艺流程,提高自己的实践能力,我参加了xxxx石油炼化公司的常减压催化裂化实习。
二、实习目的通过本次实习,我旨在了解常减压催化裂化的基本工艺流程、设备组成、操作原理,以及安全生产等方面的知识,为日后从事石油炼化工作打下坚实的基础。
三、实习内容1. 工艺流程学习在实习过程中,我认真学习了常减压催化裂化的工艺流程。
首先,原油经过脱盐、脱水预处理,去除原油中的盐分和水分,以防止设备腐蚀。
然后,原油在初馏塔中进行常压蒸馏,分离出石脑油、粗柴油(瓦斯油)等馏分。
接着,将这些馏分送入常压分馏塔,进一步分离出汽油、柴油等产品。
最后,将常压分馏塔底的重油送入减压加热炉,加热后进入减压分馏塔,分离出减一线、蜡油、渣油和沥青等产品。
2. 设备组成及操作原理实习期间,我了解了常减压催化裂化装置的主要设备,包括初馏塔、常压分馏塔、减压分馏塔、加热炉、冷凝器等。
同时,学习了这些设备的操作原理,如原油的脱盐、脱水过程,初馏塔和常压分馏塔的蒸馏原理,减压分馏塔的压力控制原理等。
3. 安全生产在实习过程中,我深刻认识到安全生产的重要性。
实习单位严格要求我们遵守安全生产规定,佩戴劳动防护用品,熟悉应急预案。
同时,我们还学习了如何检查设备安全状况,处理安全隐患,确保生产过程的安全稳定。
四、实习收获通过本次实习,我对常减压催化裂化工艺流程有了更加深刻的理解,掌握了主要设备的操作原理,提高了自己的实践能力。
同时,实习过程中的安全生产教育,使我更加重视安全生产,为今后的工作打下了良好的基础。
五、实习总结本次常减压催化裂化实习让我受益匪浅,不仅提高了自己的专业素养,还培养了团队合作精神。
催化裂化装置工艺流程

催化裂化装置工艺流程
《催化裂化装置工艺流程》
催化裂化装置是石油化工行业中常见的一种重要装置,主要用于将重质石油原料加工成轻质高值产品,如汽油、柴油和航空燃料。
在催化裂化装置中,石油原料通过加热和催化剂的作用,发生分子内部的饱和碳链裂解,生成较轻的烃类产品,并产生丰富的芳烃和液化石油气。
催化裂化装置的工艺流程通常包括以下几个主要步骤:
1. 原料加热:首先,将经过预处理的重质石油原料送入加热炉中进行加热,使其达到裂化反应的最佳温度。
2. 催化裂化:加热后的石油原料进入裂化反应器,与催化剂接触,发生裂化反应。
在裂化过程中,重质烃分子会发生碳链裂解,生成较轻的烃类产品,包括汽油、柴油和液化石油气。
3. 分离和净化:裂化反应产物进入分馏塔,通过精馏、冷却和净化等步骤,将不同碳数的烃类产品进行分离,以得到所需的轻质产品。
4. 再生催化剂:随着反应的进行,催化剂会逐渐失活,需要通过再生来恢复其活性。
再生催化剂的过程包括焙烧和再活化,以保持催化剂的活性和稳定性。
以上便是催化裂化装置的基本工艺流程。
该装置能够将重质石
油原料转化为高附加值的轻质产品,对于提高石油炼制的产出和质量具有重要意义。
同时,催化裂化装置的工艺流程也在不断优化和改进,以适应不断变化的市场需求和环保要求。
催化裂化装置工作总结

催化裂化装置工作总结
催化裂化装置是炼油厂中非常重要的设备,它能够将重质石油馏分转化为高附加值的产品,如汽油和柴油。
在催化裂化装置的工作过程中,通过催化剂的作用,将长链烃分子裂解成短链烃分子,从而提高产品的产率和质量。
在这篇文章中,我们将对催化裂化装置的工作原理和关键技术进行总结。
首先,催化裂化装置的工作原理是通过将重质石油馏分在高温和高压下与催化剂接触,从而裂解成轻质产品。
催化剂通常是一种特殊的固体材料,它能够在裂化过程中促进化学反应的进行,从而提高产品的产率和质量。
催化裂化装置通常包括反应器、再生器、分离装置和催化剂循环系统等部分,通过这些部分的协同作用,实现了重质石油馏分的裂解和产品的分离。
其次,催化裂化装置的工作需要依靠一系列的关键技术来保证其稳定和高效运行。
首先是催化剂的选择和再生技术,不同类型的催化剂对产品的选择和产率有着重要的影响,而催化剂的再生技术则能够延长催化剂的使用寿命。
其次是温度和压力的控制技术,裂化过程需要在高温和高压下进行,因此需要精确控制反应器的温度和压力,以保证裂化反应的进行。
最后是产品分离技术,裂化反应产生的产品需要经过分离装置进行分离,以得到纯净的汽油和柴油等产品。
总的来说,催化裂化装置是炼油厂中非常重要的设备,它能够将重质石油馏分转化为高附加值的产品,通过对其工作原理和关键技术的总结,我们能够更好地理解催化裂化装置的工作过程,从而保证其稳定和高效运行。
催化裂化实习报告

实习报告:催化裂化实习经历一、实习背景随着我国经济的快速发展,对石油能源的需求日益增加。
催化裂化技术作为石油加工领域的重要组成部分,其目的在于提高汽油等轻质油的产量和质量,降低重质油的比重。
为了深入了解催化裂化工艺流程及其操作原理,我在老师的指导和帮助下,于XXXX年XX月XX日至XXXX年XX月XX日,在中国石油大学催化裂化实验室进行了为期一个月的实习。
二、实习内容实习期间,我主要参与了催化裂化装置的运行操作、日常维护及实验数据分析等方面的工作。
1. 催化裂化装置运行操作:在老师的指导下,我学习了催化裂化装置的运行原理,掌握了反应器启动、停车及正常运行的操作步骤。
同时,通过实际操作,了解了催化剂的加注、卸载过程,掌握了反应器温度、压力等参数的调节方法。
2. 日常维护:实习期间,我参与了催化裂化装置的日常维护工作,包括检查设备运行状况、更换损耗件、清洗过滤器等。
通过这些工作,我了解了装置的运行状况,掌握了设备维护的基本方法。
3. 实验数据分析:在实验过程中,我负责收集、整理实验数据,并利用相关软件进行数据分析。
通过实验数据的分析,我了解了催化裂化反应的规律,掌握了实验结果的解读方法。
三、实习收获1. 理论联系实际:通过实习,我将所学的催化裂化理论知识与实际操作相结合,提高了自己的实践能力。
2. 团队协作:在实习过程中,我学会了与同学、老师密切配合,共同完成实习任务,提高了团队协作能力。
3. 安全意识:实习期间,我深刻体会到安全生产的重要性,掌握了基本的安全操作规程,提高了自己的安全意识。
4. 分析问题、解决问题的能力:在实习过程中,我学会了如何观察设备运行状况,分析问题原因,并采取相应措施解决问题,提高了自己的问题解决能力。
四、实习总结通过本次催化裂化实习,我对催化裂化工艺流程及其操作原理有了更深入的了解,实践能力得到了提高。
同时,我也认识到自己在理论知识、操作技能等方面的不足,今后将继续努力学习,提高自己的综合素质。
催化裂化车间实习报告
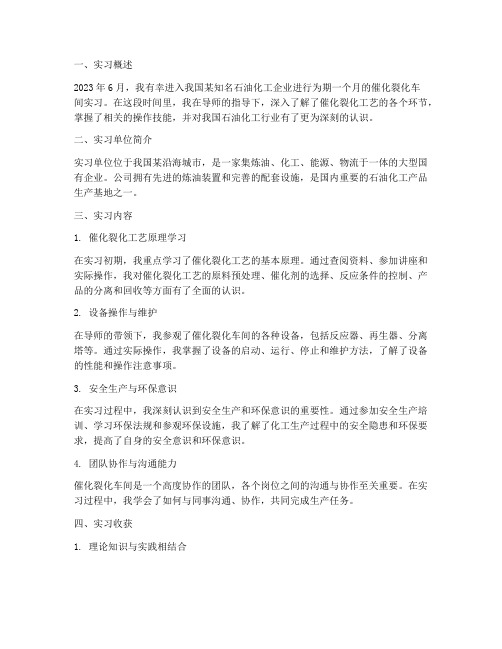
一、实习概述2023年6月,我有幸进入我国某知名石油化工企业进行为期一个月的催化裂化车间实习。
在这段时间里,我在导师的指导下,深入了解了催化裂化工艺的各个环节,掌握了相关的操作技能,并对我国石油化工行业有了更为深刻的认识。
二、实习单位简介实习单位位于我国某沿海城市,是一家集炼油、化工、能源、物流于一体的大型国有企业。
公司拥有先进的炼油装置和完善的配套设施,是国内重要的石油化工产品生产基地之一。
三、实习内容1. 催化裂化工艺原理学习在实习初期,我重点学习了催化裂化工艺的基本原理。
通过查阅资料、参加讲座和实际操作,我对催化裂化工艺的原料预处理、催化剂的选择、反应条件的控制、产品的分离和回收等方面有了全面的认识。
2. 设备操作与维护在导师的带领下,我参观了催化裂化车间的各种设备,包括反应器、再生器、分离塔等。
通过实际操作,我掌握了设备的启动、运行、停止和维护方法,了解了设备的性能和操作注意事项。
3. 安全生产与环保意识在实习过程中,我深刻认识到安全生产和环保意识的重要性。
通过参加安全生产培训、学习环保法规和参观环保设施,我了解了化工生产过程中的安全隐患和环保要求,提高了自身的安全意识和环保意识。
4. 团队协作与沟通能力催化裂化车间是一个高度协作的团队,各个岗位之间的沟通与协作至关重要。
在实习过程中,我学会了如何与同事沟通、协作,共同完成生产任务。
四、实习收获1. 理论知识与实践相结合通过实习,我将所学理论知识与实际生产相结合,加深了对催化裂化工艺的理解,提高了自己的实践能力。
2. 操作技能的提升通过实际操作,我掌握了催化裂化车间的各种设备操作技能,为今后的工作打下了坚实基础。
3. 安全意识和环保意识增强实习过程中,我深刻认识到安全生产和环保意识的重要性,提高了自身的安全意识和环保意识。
4. 团队协作与沟通能力提升在实习过程中,我学会了与同事沟通、协作,提高了自己的团队协作和沟通能力。
五、实习体会1. 理论与实践相结合的重要性通过实习,我深刻体会到理论与实践相结合的重要性。
催化裂化操作规程
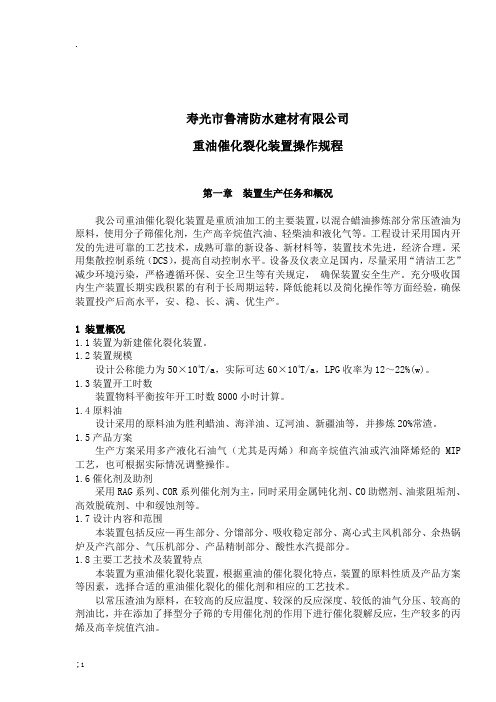
寿光市鲁清防水建材有限公司重油催化裂化装置操作规程第一章装置生产任务和概况我公司重油催化裂化装置是重质油加工的主要装置,以混合蜡油掺炼部分常压渣油为原料,使用分子筛催化剂,生产高辛烷值汽油、轻柴油和液化气等。
工程设计采用国内开发的先进可靠的工艺技术,成熟可靠的新设备、新材料等,装置技术先进,经济合理。
采用集散控制系统(DCS),提高自动控制水平。
设备及仪表立足国内,尽量采用“清洁工艺”减少环境污染,严格遵循环保、安全卫生等有关规定,确保装置安全生产。
充分吸收国内生产装置长期实践积累的有利于长周期运转,降低能耗以及简化操作等方面经验,确保装置投产后高水平,安、稳、长、满、优生产。
1 装置概况1.1装置为新建催化裂化装置。
1.2装置规模设计公称能力为50×104T/a,实际可达60×104T/a,LPG收率为12~22%(w)。
1.3装置开工时数装置物料平衡按年开工时数8000小时计算。
1.4原料油设计采用的原料油为胜利蜡油、海洋油、辽河油、新疆油等,并掺炼20%常渣。
1.5产品方案生产方案采用多产液化石油气(尤其是丙烯)和高辛烷值汽油或汽油降烯烃的MIP 工艺,也可根据实际情况调整操作。
1.6催化剂及助剂采用RAG系列、COR系列催化剂为主,同时采用金属钝化剂、CO助燃剂、油浆阻垢剂、高效脱硫剂、中和缓蚀剂等。
1.7设计内容和范围本装置包括反应—再生部分、分馏部分、吸收稳定部分、离心式主风机部分、余热锅炉及产汽部分、气压机部分、产品精制部分、酸性水汽提部分。
1.8主要工艺技术及装置特点本装置为重油催化裂化装置,根据重油的催化裂化特点,装置的原料性质及产品方案等因素,选择合适的重油催化裂化的催化剂和相应的工艺技术。
以常压渣油为原料,在较高的反应温度、较深的反应深度、较低的油气分压、较高的剂油比,并在添加了择型分子筛的专用催化剂的作用下进行催化裂解反应,生产较多的丙烯及高辛烷值汽油。
催化裂化装置流程简介
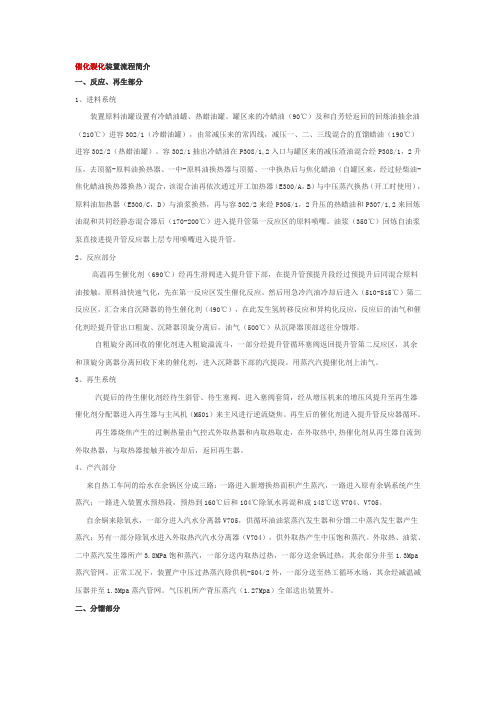
催化裂化装置流程简介一、反应、再生部分1、进料系统装置原料油罐设置有冷蜡油罐、热蜡油罐。
罐区来的冷蜡油(90℃)及和自芳烃返回的回炼油抽余油(210℃)进容302/1(冷蜡油罐),由常减压来的常四线,减压一、二、三线混合的直馏蜡油(190℃)进容302/2(热蜡油罐)。
容302/1抽出冷蜡油在P308/1,2入口与罐区来的减压渣油混合经P308/1,2升压,去顶循-原料油换热器、一中-原料油换热器与顶循、一中换热后与焦化蜡油(自罐区来,经过轻柴油-焦化蜡油换热器换热)混合,该混合油再依次通过开工加热器(E300/A,B)与中压蒸汽换热(开工时使用),原料油加热器(E300/C,D)与油浆换热,再与容302/2来经P305/1,2升压的热蜡油和P307/1,2来回炼油混和共同经静态混合器后(170-200℃)进入提升管第一反应区的原料喷嘴。
油浆(350℃)回炼自油浆泵直接进提升管反应器上层专用喷嘴进入提升管。
2、反应部分高温再生催化剂(690℃)经再生滑阀进入提升管下部,在提升管预提升段经过预提升后同混合原料油接触,原料油快速气化,先在第一反应区发生催化反应。
然后用急冷汽油冷却后进入(510-515℃)第二反应区,汇合来自沉降器的待生催化剂(490℃),在此发生氢转移反应和异构化反应,反应后的油气和催化剂经提升管出口粗旋、沉降器顶旋分离后,油气(500℃)从沉降器顶部送往分馏塔。
自粗旋分离回收的催化剂进入粗旋溢流斗,一部分经提升管循环塞阀返回提升管第二反应区,其余和顶旋分离器分离回收下来的催化剂,进入沉降器下部的汽提段。
用蒸汽汽提催化剂上油气。
3、再生系统汽提后的待生催化剂经待生斜管、待生塞阀,进入塞阀套筒,经从增压机来的增压风提升至再生器催化剂分配器进入再生器与主风机(M501)来主风进行逆流烧焦。
再生后的催化剂进入提升管反应器循环。
再生器烧焦产生的过剩热量由气控式外取热器和内取热取走,在外取热中,热催化剂从再生器自流到外取热器,与取热器接触并被冷却后,返回再生器。
催化裂化的装置简介及工艺流程
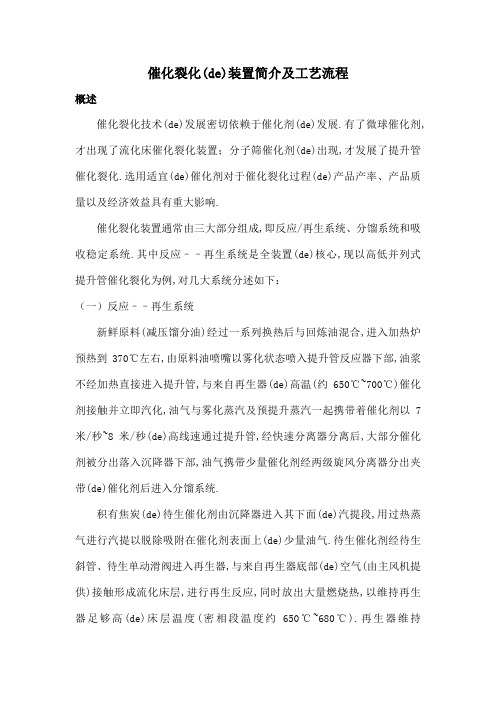
催化裂化(de)装置简介及工艺流程概述催化裂化技术(de)发展密切依赖于催化剂(de)发展.有了微球催化剂,才出现了流化床催化裂化装置;分子筛催化剂(de)出现,才发展了提升管催化裂化.选用适宜(de)催化剂对于催化裂化过程(de)产品产率、产品质量以及经济效益具有重大影响.催化裂化装置通常由三大部分组成,即反应/再生系统、分馏系统和吸收稳定系统.其中反应––再生系统是全装置(de)核心,现以高低并列式提升管催化裂化为例,对几大系统分述如下:(一)反应––再生系统新鲜原料(减压馏分油)经过一系列换热后与回炼油混合,进入加热炉预热到370℃左右,由原料油喷嘴以雾化状态喷入提升管反应器下部,油浆不经加热直接进入提升管,与来自再生器(de)高温(约650℃~700℃)催化剂接触并立即汽化,油气与雾化蒸汽及预提升蒸汽一起携带着催化剂以7米/秒~8米/秒(de)高线速通过提升管,经快速分离器分离后,大部分催化剂被分出落入沉降器下部,油气携带少量催化剂经两级旋风分离器分出夹带(de)催化剂后进入分馏系统.积有焦炭(de)待生催化剂由沉降器进入其下面(de)汽提段,用过热蒸气进行汽提以脱除吸附在催化剂表面上(de)少量油气.待生催化剂经待生斜管、待生单动滑阀进入再生器,与来自再生器底部(de)空气(由主风机提供)接触形成流化床层,进行再生反应,同时放出大量燃烧热,以维持再生器足够高(de)床层温度(密相段温度约650℃~680℃).再生器维持~(表)(de)顶部压力,床层线速约米/秒~米/秒.再生后(de)催化剂经淹流管,再生斜管及再生单动滑阀返回提升管反应器循环使用.烧焦产生(de)再生烟气,经再生器稀相段进入旋风分离器,经两级旋风分离器分出携带(de)大部分催化剂,烟气经集气室和双动滑阀排入烟囱.再生烟气温度很高而且含有约5%~10%CO,为了利用其热量,不少装置设有CO锅炉,利用再生烟气产生水蒸汽.对于操作压力较高(de)装置,常设有烟气能量回收系统,利用再生烟气(de)热能和压力作功,驱动主风机以节约电能.(二)分馏系统分馏系统(de)作用是将反应/再生系统(de)产物进行分离,得到部分产品和半成品.由反应/再生系统来(de)高温油气进入催化分馏塔下部,经装有挡板(de)脱过热段脱热后进入分馏段,经分馏后得到富气、粗汽油、轻柴油、重柴油、回炼油和油浆.富气和粗汽油去吸收稳定系统;轻、重柴油经汽提、换热或冷却后出装置,回炼油返回反应––再生系统进行回炼.油浆(de)一部分送反应再生系统回炼,另一部分经换热后循环回分馏塔.为了取走分馏塔(de)过剩热量以使塔内气、液相负荷分布均匀,在塔(de)不同位置分别设有4个循环回流:顶循环回流,一中段回流、二中段回流和油浆循环回流.催化裂化分馏塔底部(de)脱过热段装有约十块人字形挡板.由于进料是460℃以上(de)带有催化剂粉末(de)过热油气,因此必须先把油气冷却到饱和状态并洗下夹带(de)粉尘以便进行分馏和避免堵塞塔盘.因此由塔底抽出(de)油浆经冷却后返回人字形挡板(de)上方与由塔底上来(de)油气逆流接触,一方面使油气冷却至饱和状态,另一方面也洗下油气夹带(de)粉尘.(三)吸收--稳定系统从分馏塔顶油气分离器出来(de)富气中带有汽油组分,而粗汽油中则溶解有C3、C4甚至C2组分.吸收––稳定系统(de)作用就是利用吸收和精馏(de)方法将富气和粗汽油分离成干气(≤C2)、液化气(C3、C4)和蒸汽压合格(de)稳定汽油.装置简介(一)装置发展及其类型1.装置发展催化裂化工艺产生于20世纪40年代,是炼油厂提高原油加工深度(de)一种重油轻质化(de)工艺.20世纪50年代初由ESSO公司(美国)推出了Ⅳ型流出催化装置,使用微球催化剂(平均粒径为60—70tan),从而使催化裂化工艺得到极大发展.1958年我国第一套移动床催化裂化装置在兰州炼油厂投产.1965年我国自己设计制造施工(de)Ⅳ型催化装置在抚顺石油二厂投产.经过近40年(de)发展,催化裂化已成为炼油厂最重要(de)加工装置.截止1999年底,我国催化裂化加工能力达8809.5×104t/a,占一次原油加工能力(de)33.5%,是加工比例最高(de)一种装置,装置规模由(34—60)×104t /a发展到国内最大300×104t/a,国外为675×104t/a.随着催化剂和催化裂化工艺(de)发展,其加工原料由重质化、劣质化发展至目前全减压渣油催化裂化.根据目(de)产品(de)不同,有追求最大气体收率(de)催化裂解装置(DCC),有追求最大液化气收率(de)最大量高辛烷值汽油(de)MGG工艺等,为了适应以上(de)发展,相应推出了二段再生、富氧再生等工艺,从而使催化裂化装置向着工艺技术先进、经济效益更好(de)方向发展.2.装置(de)主要类型催化裂化装置(de)核心部分为反应—再生单元.反应部分有床层反应和提升管反应两种,随着催化剂(de)发展,目前提升管反应已取代了床层反应.再生部分可分为完全再生和不完全再生,一段再生和二段再生(完全再生即指再生烟气中CO含量为10—6级).从反应与再生设备(de)平面布置来讲又可分为高低并列式和同轴式,典型(de)反应—再生单元见图2—4、图2—5、图2—6、图2—7,其特点见表2—11.(二)装置单元组成与工艺流程1.组成单元催化裂化装置(de)基本组成单元为:反应—再生单元,能量回收单元,分馏单元,吸收稳定单元.作为扩充部分有:干气、液化气脱硫单元,汽油、液化气脱硫醇单元等.各单元作用介绍如下.(1)反应—再生单元重质原料在提升管中与再生后(de)热催化剂接触反应后进入沉降器(反应器),油气与催化剂经旋风分离器与催化剂分离,反应生成(de)气体、汽油、液化气、柴油等馏分与未反应(de)组分一起离开沉降器进入分馏单元.反应后(de)附有焦炭(de)待生催化剂进入再生器用空气烧焦,催化剂恢复活性后再进入提升管参加反应,形成循环,再生器顶部烟气进入能量回收单元.(2)三机单元所谓三机系指主风机、气压机和增压机.如果将反一再单元作为装置(de)核心部分,那么主风机就是催化裂化装置(de)心脏,其作用是将空气送人再生器,使催化剂在再生器中烧焦,将待生催化剂再生,恢复活性以保证催化反应(de)继续进行.增压机是将主风机出口(de)空气提压后作为催化剂输送(de)动力风、流化风、提升风,以保持反—再系统催化剂(de)正常循环.气压机(de)作用是将分馏单元(de)气体压缩升压后送人吸收稳定单元,同时通过调节气压机转数也可达到控制沉降器顶部压力(de)目(de),这是保证反应再生系统压力平衡(de)一个手段.(3)能量回收单元利用再生器出口烟气(de)热能和压力使余热锅炉产生蒸汽和烟气轮机作功、发电等,此举可大大降低装置能耗,目前现有(de)重油催化裂化装置有无此回收系统,其能耗可相差1/3左右.(4)分馏单元沉降器出来(de)反应油气经换热后进入分馏塔,根据各物料(de)沸点差,从上至下分离为富气(至气压机)、粗汽油、柴油、回炼油和油浆.该单元(de)操作对全装置(de)安全影响较大,一头一尾(de)操作尤为重要,即分馏塔顶压力、塔底液面(de)平稳是装置安全生产(de)有力保证,保证气压机人口放火炬和油浆出装置系统(de)通畅,是安全生产(de)必备条件. (5)吸收稳定单元经过气压机压缩升压后(de)气体和来自分馏单元(de)粗汽油,经过吸收稳定部分,分割为干气、液化气和稳定汽油.此单元是本装置甲类危险物质最集中(de)地方.(6)产品精制单元包括干气、液化气脱硫和汽油液化气脱硫醇单元该两部分,干气、液化气在胺液(乙醇胺、二乙醇胺、Ⅳ—甲基二乙醇胺等)作用下、吸收干气、液化气中(de)H2S气体以达到脱除H2S(de)目(de).汽油和液化气在碱液状态中在磺化酞氰钴或聚酞氰钻作用下将硫醇氧化为二硫化物,以达到脱除硫醇(de)目(de).2.工艺流程工艺原则流程见图2—8.原料油由罐区或其他装置(常减压、润滑油装置)送来,进入原料油罐,由原料泵抽出,换热至200—300°C左右,分馏塔来(de)回炼油和油浆一起进入提升管(de)下部,与由再生器再生斜管来(de)650~700°C再生催化剂接触反应,然后经提升管上部进入分馏塔(下部);反应完(de)待生催化剂进入沉降器下部汽提段.被汽提蒸汽除去油气(de)待生剂通过待生斜管进入再生器下部烧焦罐.由主风机来(de)空气送人烧焦罐烧焦,并同待生剂一道进入再生器继续烧焦,烧焦再生后(de)再生催化剂由再生斜管进人提升管下部循环使用.烟气经一、二、三级旋分器分离出催化剂后,其温度在650~700°C,压力0.2-0.3MPa(表),进人烟气轮机作功带动主风机,其后温度为500—550°C,压力为0.01MPa(表)左右,再进入废热锅炉发生蒸汽,发汽后(de)烟气(温度大约为200℃左右)通过烟囱排到大气.反应油气进入分馏塔后,首先脱过热,塔底油浆(油浆中含有2%左右催化剂)分两路,一路至反应器提升管,另一路经换热器冷却后出装置.脱过热后油气上升,在分馏塔内自上而下分离出富气、粗汽油、轻柴油、回炼油.回炼油去提升管再反应,轻柴油经换热器冷却后出装置,富气经气压机压缩后与粗汽油共进吸收塔,吸收塔顶(de)贫气进入再吸收塔由轻柴油吸收其中(de)C4-C5,再吸收塔顶干气进入干气脱硫塔脱硫后作为产品出装置,吸收塔底富吸收油进入脱吸塔以脱除其中(de)C2.塔底脱乙烷汽油进入稳定塔,稳定塔底油经碱洗后进入脱硫醇单元脱硫醇后出装置,稳定塔顶液化气进入脱硫塔脱除H,S,再进入脱硫醇单元脱硫醇后出装置.(脱硫脱硫醇未画出)(三)化学反应过程1.催化裂化反应(de)特点催化裂化反应是在催化剂表面上进行(de),其反应过程(de)7个步骤如下:①气态原料分子从主流扩散到催化剂表面;②原料分子沿催化剂外向内扩散;③原料分子被催化剂活性中心吸附;④原料分子发生化学反应;⑤产品分子从催化剂内表面脱附;⑥产品分子由催化剂外向外扩散;⑦产品分子扩散到主流中.重质原料反应生成目(de)产品可用下图表示:2.催化裂化反应种类石油馏分是由十分复杂(de)烃类和非烃类组成,其反应过程十分复杂,种类繁多,大致分为几个类型.(1)裂化反应是主要(de)反应.即C—C键断裂,大分子变为小分子(de)反应.(2)异构化反应是重要(de)反应.即化合物(de)相对分子量不变,烃类分子结构和空间位置变化,所以催化裂化产物中会有较多异构烃.(3)氢转移反应是一个烃分子上(de)氢脱下来加到另一个烯烃分子上,使其烯烃饱和,该反应是催化裂化特有(de)反应.虽然氢转移反应会使产品安定性变好,但是大分子(de)烃类反应脱氢将生成焦炭.(4)芳构化反应烷烃、烯烃环化生成环烷烃和环烯烃,然后进一步氢转移反应生成芳烃,由于芳构化反应使汽油、柴油中芳烃较多.除以上反应外,还有甲基转移反应、叠合反应和烷基化反应等.(四)主要操作条件及工艺技术特点1.主要操作条件因不同(de)工艺操作条件不尽相同,表2—12列出一般一段再生催化裂化(de)主要操作条件.2.工艺技术特点(1)微球催化剂(de)气—固流态化催化裂化确切一点应该叫作流化催化裂化.微球催化剂(60—70/1m 粒径)在不同气相线速下呈现不同状态,可分为固定床(即催化剂不动)、流化床(即催化剂只在一定(de)空间运动)和输送床(即催化剂与气相介质一同运动而离开原来(de)空间)三种.过程是流化床,所以微球催化剂(de)气—固流态化是催化裂化工艺得以发展(de)基础,从而使反应—再生能在不同(de)条件下得以实现.(2)催化裂化(de)化学反应最主要(de)反应是大分子烃类裂化为小分子烃类(de)化学反应,从而使原油中大于300℃馏分(de)烃类生成小分子烃类、气体、液化气、汽油、柴油等,极大地增加了炼油厂(de)轻质油收率,并能副产气体和液化气.(五)催化剂及助剂1.催化剂烃类裂化反应,应用热裂化工艺也能完成,但是有了催化剂(de)参加,其化学反应方式不同,所以导致二类工艺(de)产品性质和产品分布都不同.目前催化裂化所使用(de)催化剂都是分子筛微球催化剂,根据不同产品要求可制造出各种型号(de)催化剂.但其使用性能要求是共同(de),即高活性和选择性,良好(de)水热稳定性,抗硫、氮、重金属(de)中毒;好(de)强度,易再生,流化性能好等.目前常见(de)有重油催化裂化催化剂、生产高辛烷值汽油催化剂、最大轻质油收率催化剂、增加液化气收率催化剂和催化裂解催化剂等.由于催化裂化原料(de)重质化,使重油催化剂发展十分迅速,目前国内全渣油型催化剂性能见表2—13.2.催化裂化助剂为了补充催化剂(de)其他性能,近年来发展了多种起辅助作用(de)助催化剂,这些助剂均以剂(de)方式,加到裂化催化剂中起到除催化裂化过程外(de)其他作用.如促进再生烟气中CO转化为C02,提高汽油辛烷值,钝化原料中重金属对催化剂活性毒性,降低烟气中(de)SOx(de)含量等各类助剂,它们绝大多数也是制造成与裂化催化剂一样(de)微球分别加入再生器内,但占总剂量很少,一般在1%—3%,所以每天添加量只有10-1000kS/d左右.CO助燃剂为SiO2—Al2O3细粉上载有活性金属铂制成.辛烷值助剂大多是含有15%-20%ZSM—5分子筛(de)Si—Al微球剂.而金属钝化剂为液态型含锑(de)化合物,将其注入原料油中,使其分解(de)金属锑沉积在催化剂上以钝化Ni(de)活性.(六)原料及产品性质1.催化裂化原材料各类催化裂化所使用(de)原材料不尽相同,现将一般所使用(de)原材料主要性质汇总,见表2—14.2.产品性质产品性质见表2-15。
催化裂化装置分馏系统工艺分析
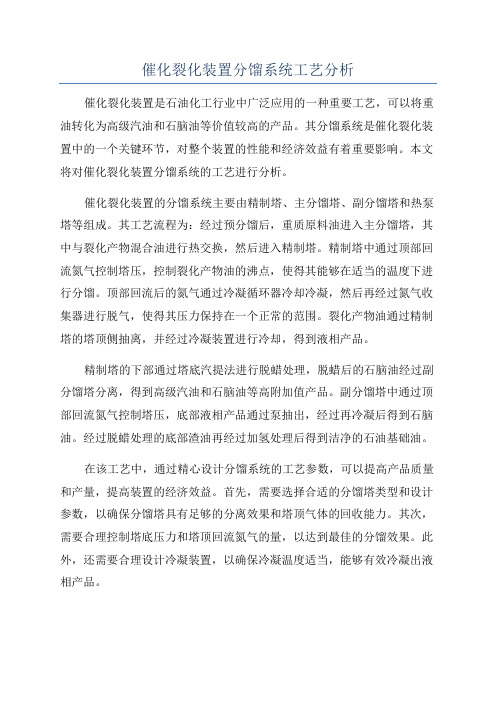
催化裂化装置分馏系统工艺分析催化裂化装置是石油化工行业中广泛应用的一种重要工艺,可以将重油转化为高级汽油和石脑油等价值较高的产品。
其分馏系统是催化裂化装置中的一个关键环节,对整个装置的性能和经济效益有着重要影响。
本文将对催化裂化装置分馏系统的工艺进行分析。
催化裂化装置的分馏系统主要由精制塔、主分馏塔、副分馏塔和热泵塔等组成。
其工艺流程为:经过预分馏后,重质原料油进入主分馏塔,其中与裂化产物混合油进行热交换,然后进入精制塔。
精制塔中通过顶部回流氮气控制塔压,控制裂化产物油的沸点,使得其能够在适当的温度下进行分馏。
顶部回流后的氮气通过冷凝循环器冷却冷凝,然后再经过氮气收集器进行脱气,使得其压力保持在一个正常的范围。
裂化产物油通过精制塔的塔顶侧抽离,并经过冷凝装置进行冷却,得到液相产品。
精制塔的下部通过塔底汽提法进行脱蜡处理,脱蜡后的石脑油经过副分馏塔分离,得到高级汽油和石脑油等高附加值产品。
副分馏塔中通过顶部回流氮气控制塔压,底部液相产品通过泵抽出,经过再冷凝后得到石脑油。
经过脱蜡处理的底部渣油再经过加氢处理后得到洁净的石油基础油。
在该工艺中,通过精心设计分馏系统的工艺参数,可以提高产品质量和产量,提高装置的经济效益。
首先,需要选择合适的分馏塔类型和设计参数,以确保分馏塔具有足够的分离效果和塔顶气体的回收能力。
其次,需要合理控制塔底压力和塔顶回流氮气的量,以达到最佳的分馏效果。
此外,还需要合理设计冷凝装置,以确保冷凝温度适当,能够有效冷凝出液相产品。
此外,还需要注意操作控制的安全性和稳定性。
对于分馏系统来说,要注意控制好分馏温度和压力的变动,以防止分馏塔内发生过热、过压等异常情况。
在日常操作中,要注意监控分馏系统的各个关键参数,及时发现问题并进行调整和处理。
综上所述,催化裂化装置分馏系统是催化裂化装置中一个重要的工艺环节。
通过合理设计和精心操作,可以提高产品的质量和产量,提高装置的经济效益。
但需要注意操作的安全性和稳定性,及时处理和解决问题。
催化裂化装置实习心得体会

催化裂化装置实习心得体会首先,我要感谢实习导师和同事们的指导和支持。
他们不仅在工作中给予我耐心的指导,还给予我很多生活方面的帮助。
在他们的帮助下,我顺利地完成了实习任务,并且学到了很多在学校里无法学到的东西。
在实习期间,我主要负责催化裂化装置的操作和维护工作。
催化裂化装置是炼油工艺中的重要组成部分,它能够将重质石油馏分转化成轻质产品,比如汽油、柴油等。
因此,催化裂化装置的正常运行对于炼油厂的生产非常重要。
在这段时间里,我学会了如何进行装置的开车操作,以及如何进行设备的检修和维护。
在实习的过程中,我深刻感受到了催化裂化装置操作的复杂性和工作的辛苦。
在装置的开车过程中,操作人员需要时刻注意各种指标的变化,并且迅速做出相应的调整。
同时,装置的各个部件和设备也需要经常进行检修和维护,以确保其正常运行。
这些工作都需要操作人员具备丰富的经验和细心的态度。
通过实习,我深刻了解到了这一点,并且对自己有了更高的要求。
在实习期间,我还有幸参与了一些装置的日常维护工作。
这些工作主要包括设备的清洗、检修和更换。
虽然这些工作十分繁琐和辛苦,但是我却从中学到了很多知识。
通过实际操作,我更加深刻地理解了装置的结构和原理,也对装置的运行有了更深入的了解。
同时,这些工作也让我体会到了专业技术工作的重要性和辛苦,让我更加珍惜自己所学的专业知识,更加珍惜自己将来的工作。
通过这段时间的实习,我不仅学到了专业知识和技能,还对自己的职业规划有了更清晰的认识。
我深深地意识到了自己在专业知识和实际操作方面的不足,也更加认识到了自己在这个行业中的不足和需要改进的地方。
通过这次实习,我更加明确了自己未来的职业方向和发展目标,并且更有信心地迎接将来的工作挑战。
总的来说,催化裂化装置实习对我来说是一次非常宝贵的经历。
通过这段时间的实习,我学到了很多专业知识和实际操作技能,也深刻体会到了专业技术工作的重要性和辛苦。
同时,我也更加清晰地认识到了自己的不足和需要改进的地方,并且对自己未来的职业规划有了更清晰的认识。
催化炼化实训报告

一、实训背景随着我国石油化工行业的快速发展,催化炼化技术已成为炼油工业的核心技术之一。
为了提高我国炼油工业的竞争力,培养具备实际操作和创新能力的技术人才,我国高校和科研机构纷纷开展催化炼化实训项目。
本实训报告以某炼油厂催化炼化装置为研究对象,对实训过程进行总结和分析。
二、实训目的1. 熟悉催化炼化工艺流程及设备操作;2. 掌握催化剂的制备、装填、再生及评价方法;3. 培养实际操作能力、分析问题和解决问题的能力;4. 了解炼油工业发展趋势,提高自身综合素质。
三、实训内容1. 催化炼化工艺流程及设备操作(1)催化裂化工艺流程:原油预处理→分馏→催化裂化反应→分离→产品回收。
(2)设备操作:分馏塔、反应器、再生器、吸附塔、吸收塔等。
2. 催化剂的制备、装填、再生及评价(1)催化剂制备:了解催化剂的种类、性能及制备方法。
(2)催化剂装填:掌握催化剂装填、分布和预热的操作要领。
(3)催化剂再生:了解催化剂再生工艺及操作要点。
(4)催化剂评价:掌握催化剂活性、选择性和稳定性的评价方法。
3. 实际操作能力培养(1)现场巡检:了解现场设备运行情况,发现问题并及时处理。
(2)异常工况处理:分析异常工况原因,制定处理措施,确保装置安全稳定运行。
(3)操作优化:根据生产实际情况,提出操作优化方案,提高装置运行效率。
4. 炼油工业发展趋势了解(1)环保要求提高:了解国家环保政策,提高环保意识。
(2)节能降耗:掌握节能降耗技术,提高装置运行效率。
(3)技术创新:关注炼油工业新技术、新工艺的发展动态。
四、实训成果1. 熟悉了催化炼化工艺流程及设备操作,掌握了催化剂的制备、装填、再生及评价方法。
2. 提高了实际操作能力,培养了分析问题和解决问题的能力。
3. 对炼油工业发展趋势有了更深入的了解,提高了自身综合素质。
五、实训总结1. 实训过程中,注重理论与实践相结合,使学生对催化炼化技术有了更深入的认识。
2. 通过实训,提高了学生的实际操作能力,为今后从事炼油工业相关工作打下了基础。
蜡油催化裂化装置增产柴油的工业试验

下 降到调 整后 的 4 0℃ , 9 降低 了 1 6℃ ; 料 预 热 原
温度 由 2 0℃下 降到 2 0℃ , 2 0 降低 了 2 O℃ 。裂 化 反应 是 吸热 反 应 , 低 反 应 温 度有 利 于 抑 制 二 次 降
减压 蜡油 和 焦 化 蜡 油 为 主 , 入 少 量 的减 压 渣 油 掺
化 气 的质 量 无 不 良影 响 ; 置 能 耗 降低 , 体 经 济 效 益 每 年 可 增 加 约 37 2 元 。 装 总 7 万
关键 词 : 化裂化 催
柴油
催 化 剂 汽 油 液 化 气
1 前 言
国民经 济 的快 速 发 展 带 动 了 国 内柴 油 消 费 的 快 速 增长 , 路 用 柴 油 和 农 用 柴 油 的需 求 量 都 迅 道 速 增加 , 近几 年 来 国 内柴 油 的 年 均 需 求 增 长 率 为 6 ~7 , 0 0年 国 内经 济 刺 激 政 策 的激 励 使 柴 21 油 需 求 增 长 率 进 一 步 提 高 。柴 油 市 场 需 求 的 变 化 , 国内成 品油市 场 柴油 资源 总体 短缺 。 使
摘 要 : 绍 增 产 柴 油 方案 在 抚 顺 石 化 公 司催 化 裂 化 装 置 上 的应 用 情 况 。工 业 试 验 结 果 表 明 : 过 调 整 反 介 通
应 一 生 系 统 、 馏 系统 操 作 参 数 和 选 用 DMC 2增 产 柴 油 催 化 剂 等 措 施 , 品 分 布 得 到 改 善 , 油 收 率 提 高 3 7 再 分 一 产 柴 .7
( 直馏 柴 油 ) 和催 化 裂 化 、 迟 焦 化 等 二 次 加 工 装 延
置( 裂解 柴 油 ) 目前 国 内炼 油 企 业 二 次 加 工装 置 。
提升管催化裂化实习报告

报告题目:提升管催化裂化实习报告报告时间:[[时间]]报告人:实习生一、实习背景随着我国经济的快速发展,石油化工行业在国民经济中的地位日益突出,对石油化工产品的要求也越来越高。
催化裂化技术作为一种重要的石油加工方法,可以显著提高汽油等石油产品的质量和产量。
本次实习,我有幸参与了提升管催化裂化装置的操作和维护工作,对催化裂化工艺有了更深入的了解。
二、实习内容1. 提升管催化裂化装置概述提升管催化裂化装置是炼油厂的重要装置之一,其主要作用是将重质石油馏分转化为轻质汽油等高附加值产品。
装置主要包括提升管、反应器、再生器、分馏塔等部分。
2. 操作流程(1)催化剂装填:实习期间,我参与了催化剂的装填工作。
催化剂是催化裂化反应的关键,其装填过程要求严格,必须保证催化剂的均匀分布和良好的流动性。
(2)装置开车:在催化剂装填完毕后,我们按照操作规程逐步启动装置,进行升温、升压、投油等步骤。
在投油过程中,要严格控制反应温度、压力、空速等参数,以保证催化裂化反应的顺利进行。
(3)装置运行:在装置运行过程中,我们要密切关注各项工艺参数的变化,及时调整,确保装置在高负荷下稳定运行。
同时,要定期检查设备,确保其正常运行。
(4)催化剂再生:在装置运行一定周期后,催化剂活性降低,需要进行再生。
我们按照操作规程对催化剂进行再生,使其恢复活性,以保证装置的稳定运行。
3. 维护与检修在实习期间,我参与了提升管催化裂化装置的维护与检修工作。
主要包括对反应器、再生器、分馏塔等设备的检查、清洗和维修。
在维护与检修过程中,我深刻体会到了石油化工行业对设备可靠性的严格要求。
三、实习收获通过本次实习,我对提升管催化裂化工艺有了更深入的了解,掌握了装置的操作流程和维护方法。
同时,实习过程中的团队协作和严密的组织纪律性,使我更加明白了石油化工行业的安全规范和职业操守。
四、实习总结本次实习让我对提升管催化裂化工艺有了全面的了解,为我今后从事石油化工工作奠定了基础。
- 1、下载文档前请自行甄别文档内容的完整性,平台不提供额外的编辑、内容补充、找答案等附加服务。
- 2、"仅部分预览"的文档,不可在线预览部分如存在完整性等问题,可反馈申请退款(可完整预览的文档不适用该条件!)。
- 3、如文档侵犯您的权益,请联系客服反馈,我们会尽快为您处理(人工客服工作时间:9:00-18:30)。
催化裂化装置加工常三线直馏柴油的工业实践
李宁;汪加民;张琰彬
【摘要】随着市场需求的变化,各炼油企业不断采取措施降低柴汽比,以提升全厂经济效益.中国石化海南炼油化工有限公司将常三线直馏柴油送至催化裂化装置加工,进料位置为提升管油浆/回炼油喷嘴处,加工过程中保持原油加工品种及比例不变,以确保常三线直馏柴油和催化混合原料性质稳定,同时保持催化裂化装置操作条件稳定,避免生产波动.此次共加工2d,常三线加工量分别为4.4,20 t/h,结果表明,有41.42%常三线直馏柴油通过催化裂化装置转化为汽油,有效降低了柴汽比,且改善了重油的产品分布,油浆收率下降0.40百分点,生焦率下降0.27百分点.但随着常三线直馏柴油加工量的增加,氢转移指数由2.33上升至2.59,氢转移反应增加明显,丙烯和异丁烯收率分别下降0.23百分点和0.05百分点,对增产低碳烯烃不利.
【期刊名称】《炼油技术与工程》
【年(卷),期】2016(046)002
【总页数】4页(P27-30)
【关键词】柴汽比;催化裂化;常三线;氢转移指数
【作者】李宁;汪加民;张琰彬
【作者单位】中国石化海南炼油化工有限公司,海南洋浦578101;中国石化海南炼油化工有限公司,海南洋浦578101;中国石化海南炼油化工有限公司,海南洋浦578101
【正文语种】中文
近几年,汽油需求量逐年快速增长,但由于受经济增长放缓、经济结构调整、天然气等替代燃料较快发展等因素影响,柴油需求增长缓慢,成品油消费结构逐渐发生了变化,持续向汽油方向倾斜,消费柴汽比逐年走低,导致国内汽油市场需求增长高于柴油,使得各炼油企业采取各种措施不断降低柴汽比。
中国石化海南炼油化工有限公司(下简称海南炼化)为降低全公司柴油产量,提高汽油产量,将常三线直馏柴油进重油催化裂化装置加工。
海南炼化2.80 Mt/a重油催化裂化装置两器采用高低并列形式,提升管反应器采
用石油化工科学研究院开发的多产异构烷烃和丙烯的MIPCGP工艺(见图1),MIP 工艺采用串联提升管反应器型式的新型反应系统,选择性地控制裂化反应、氢转移反应和异构化反应。
主要目的产品为低烯烃汽油,气体产品中富含丙烯和异丁烷。
提升管设有四层喷嘴,从下到上分别为原料油喷嘴、油浆/回炼油喷嘴、提升蒸汽
喷嘴和急冷油喷嘴。
2.1 原料性质
常三线进催化裂化装置加工期间,原油加工品种及比例保持稳定,以确保其性质稳定,另外常三线混合原料初馏点在200℃左右,不会因为物理切割问题影响产品
分布;催化原料性质稳定,但原料中硫、氮、金属等杂质含量较高,尤其是氮含量
高对提升管内催化剂反应活性、重油裂化能力影响较大。
催化裂化装置重油原料和常三线性质分别见表1~2。
2.2 催化剂性能
重油催化裂化装置一直使用CGP专用催化剂,新鲜催化剂的加注量为10 t/d,而系统藏量为660 t,常三线加工试验时间仅为2 d,因此认为催化剂性能基本一致。
平衡剂中镍、钒含量较高,系统活性、筛分以及平衡剂定碳在正常操作范围内。
常三线加工期间,催化剂性质见表3。
2.3 操作参数
本次催化装置加工过程,第一天常三线直馏柴油加工量控制在4.4 t/h,第二天催
化重油原料降低了6 t/h、常三线加工量提至20 t/h。
加工期间主要操作参数见表4,可以看出,两天的主要操作条件基本一致,为提高丙烯、异丁烯等高附加值产品的收率,提升管出口温度控制在504℃左右。
根据滑阀压力降和开度变化可知,加工期间催化剂循环量均在2 220 t/h左右。
随着常三线加工量增加,二再密相温度下降,表明生焦量下降。
2.4 产品分布
常三线直馏柴油加工期间催化裂化装置产品分布见表5。
可以看出,加工常三线直馏柴油后,汽油收率增加0.05百分点,液化石油气收率增加0.32百分点,但丙烯和异丁烯收率分别下降0.23百分点和0.05百分点,油浆、生焦收率分别下降
0.40百分点和0.27百分点。
表明常三线直馏柴油加工对提升管内的重油转化有促进作用,但对增产低碳烯烃不利。
分析具体原因,由于重油的剂油比上升,选择性改善,另外常三线直馏柴油起到降低油气分压的作用,有利于重油裂化,增加了反应深度,油浆收率和生焦率下降。
由于常三线直馏柴油的裂化反应和重油裂化深度增加,使得液化石油气收率上升。
由于原料性质、操作条件以及平衡催化剂性质基本相当,因此假定新鲜原料的产品分布不受常三线加工的影响,计算常三线的产品分布,其中常三线直馏柴油中有41.42%转化为汽油、37.23%转化为液化石油气,受操作条件等因素的影响重油转化率发生变化,因此油浆、生焦数据为负值。
2.5 产品质量
(1)液化石油气。
液化石油气组成见表6,可以看出,加工常三线后,第1天较加
工前液化石油气中丙烯浓度下降0.52百分点、异丁烯浓度下降0.12百分点,主要是由于常三线中环烷烃含量较高,同时MIP工艺的特点就是在二反区强化氢转移
反应,因此随着供氢体的增加进一步增加了氢转移反应,氢转移指数由2.33上升
至2.59,降低了丙烯前身物汽油中C5~C8烯烃的浓度,丙烯收率下降;另外氢转
移反应增加,丙烯、异丁烯自身转化为丙烷、异丁烷的反应增加,收率下降;因此
由于前身物减少和自身转化增加导致丙烯和异丁烯减少。
(2)稳定汽油。
催化汽油主要性质见表7,可以看出,随着常三线直馏柴油加工量
的增加,在稳定汽油馏程及蒸汽压基本不变的情况下,烯烃质量分数第2天增加1.9百分点,芳烃质量分数增加0.9百分点,硫醇硫、总硫以及硫传递系数先下降后上升。
分析主要原因:根据文献数据,环烷烃在Y型分子筛上脱氢芳化选择性远高于裂化,并且其裂化反应以侧链断裂为主[1]。
由于环烷烃脱氢和断侧链的反应为主,芳烃也以断侧链为主,因此汽油中芳烃含量上升。
受原料性质以及MIP工艺特点的
影响,以加氢尾油为原料的MIP工艺生产的汽油中总硫含量低于常规催化,传递
系数由常规催化的10%降至4%,但直馏蜡油产品中汽油硫占总硫的4% ~10%[2],远高于渣油加氢尾油1.5%左右的比例,因此随着常三线直馏柴油加工量
的增加,汽油中总硫和硫醇硫增加。
由于催化汽油中的烯烃含量随原料中链烷烃和氢含量的增加而增加,因此常三线直馏柴油加工增加会使得汽油中烯烃含量增加;另外随着重油反应深度的增加,产品
中烯烃含量增加,因此汽油中烯烃含量增加。
(3)催化柴油。
催化柴油主要性质见表8。
由图8可以看出,催化柴油密度有所下降,主要是未转化的常三线直馏柴油进入
催化柴油中,由于其密度较低,因此使得催化柴油密度下降。
(1)工业实践证明,常三线直馏柴油在催化裂化装置反应过程中约有41%转化为汽油,能有效降低柴汽比。
(2)由于常三线直馏柴油中环烷烃含量高,氢转移指数由2.33增加到2.59,氢转
移反应增加明显,使得液化石油气中丙烯体积分数下降0.52百分点、异丁烯体积
分数下降0.12百分点,对于增产低碳烯烃不利,常三线中环烷烃含量变化对汽油辛烷值的影响有待进一步考察。
(3)催化裂化装置油浆喷嘴与原料喷嘴高差为5 m,油浆喷嘴处原料转化率较低,因此常三线性质对重油转化的影响,尤其是在高加工负荷的情况下的影响还需进一步考察。
【相关文献】
[1]陈妍,宋海涛,朱玉霞,等.Beta和Y型分子筛催化四氢萘裂化规律的对比[J].石油学报(石油加工),2015,31(3):650-656.
[2]陈俊武,徐友好.催化裂化工艺与工程[M].3版.北京:中国石化出版社,2015:1239.。