重油催化裂化装置能耗分析及节能降耗措施探讨
浅析催化裂化装置能耗影响因素及应对措施
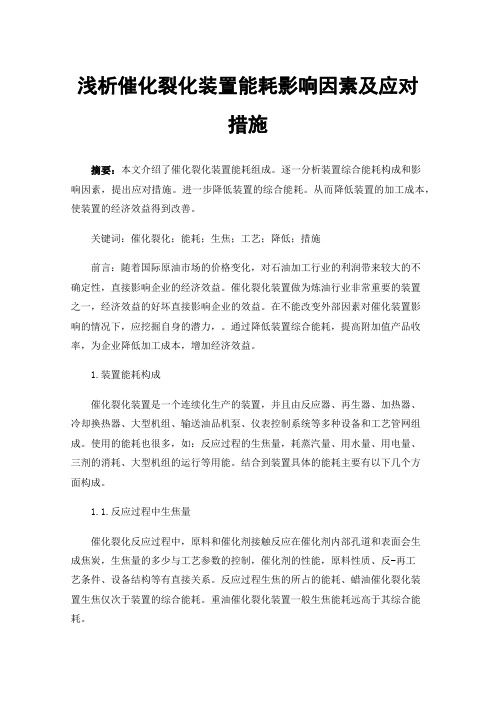
浅析催化裂化装置能耗影响因素及应对措施摘要:本文介绍了催化裂化装置能耗组成。
逐一分析装置综合能耗构成和影响因素,提出应对措施。
进一步降低装置的综合能耗。
从而降低装置的加工成本,使装置的经济效益得到改善。
关键词:催化裂化;能耗;生焦;工艺;降低;措施前言:随着国际原油市场的价格变化,对石油加工行业的利润带来较大的不确定性,直接影响企业的经济效益。
催化裂化装置做为炼油行业非常重要的装置之一,经济效益的好坏直接影响企业的效益。
在不能改变外部因素对催化装置影响的情况下,应挖掘自身的潜力,。
通过降低装置综合能耗,提高附加值产品收率,为企业降低加工成本,增加经济效益。
1.装置能耗构成催化裂化装置是一个连续化生产的装置,并且由反应器、再生器、加热器、冷却换热器、大型机组、输送油品机泵、仪表控制系统等多种设备和工艺管网组成。
使用的能耗也很多,如:反应过程的生焦量,耗蒸汽量、用水量、用电量、三剂的消耗、大型机组的运行等用能。
结合到装置具体的能耗主要有以下几个方面构成。
1.1.反应过程中生焦量催化裂化反应过程中,原料和催化剂接触反应在催化剂内部孔道和表面会生成焦炭,生焦量的多少与工艺参数的控制,催化剂的性能,原料性质、反-再工艺条件、设备结构等有直接关系。
反应过程生焦的所占的能耗、蜡油催化裂化装置生焦仅次于装置的综合能耗。
重油催化裂化装置一般生焦能耗远高于其综合能耗。
1.2.装置消耗蒸汽量催化裂化装置主要用3.5Mpa中压蒸汽、1.0Mpa蒸汽。
中压蒸汽用于大型机组的动力,一般使用背压式汽轮机,主要是主风机组和气体压缩机组的原动机耗汽。
某130万吨加工量的蜡油催化裂化机组是四机组(烟气轮机+主风机+汽轮机+电动/发电机)再生系统烧焦需要1670标准立方米/分钟,烟气轮机满负荷、气压机组是背压式汽轮机的情况下,装置中压蒸汽的使用的能耗排在反应生焦之后。
1.3.装置消耗水量用水主要有循环水、除氧软化水、除盐软化水、新鲜水。
重油催化裂化装置节能优化措施分析

重油催化裂化装置节能优化措施分析重油催化裂化装置是炼油厂的重要设备之一,主要用于将重质石油馏分进行催化裂化,从而生产出高附加值的轻质石油产品。
由于催化裂化过程能耗大、热损失多,因此节能优化一直是炼油企业关注的重点之一。
本文将结合实际案例,对重油催化裂化装置的节能优化措施进行分析,为相关企业提供参考和借鉴。
一、原有装置能耗分析重油催化裂化装置在生产过程中主要消耗能源包括电力、燃料气和冷却水等。
在进行节能优化措施之前,首先需要对原有装置的能耗进行分析,找出能源消耗的主要部分及其原因。
1.电力消耗重油催化裂化装置对电力的需求主要集中在压缩机、泵站、风机、电加热炉、电动阀门等设备上。
在使用过程中,这些设备的运行效率、负荷调节和电力设备的老化都会影响装置的电力消耗。
2.燃料气消耗重油催化裂化装置对燃料气的需求主要集中在燃气锅炉、加热炉等燃烧设备上。
燃气的燃烧效率、热损失、余热利用等都会影响装置的燃料气消耗。
3.冷却水消耗重油催化裂化装置在生产过程中需要大量的冷却水进行冷却和冷凝,然后再循环利用。
冷却水系统的循环水量、水质管理、热损失等因素都会影响冷却水的消耗量。
二、节能优化措施1.提高设备运行效率加强设备的维护和管理,提高设备的运行效率是节能优化的重要措施。
定期对压缩机、泵站、风机等设备进行清洗、润滑、检修和调试,保持设备的运行状态良好,避免因设备运行不稳导致能源浪费。
2.优化工艺控制优化工艺控制是提高生产效率和降低能源消耗的重要手段。
通过优化控制系统的调整参数、优化生产工艺流程,可以减少设备的启停次数,提高设备稳定性和生产效率,降低能源消耗。
3.余热利用重油催化裂化装置在生产过程中会产生大量的余热,合理利用这些余热是节能的重要途径之一。
可以通过余热锅炉、余热蒸汽发生器等设备将废热转化为可用的热能,用于加热蒸汽、供暖等,从而降低对燃料气的需求。
4.替代能源在可行的条件下,可以考虑替代能源,如采用太阳能、风能等清洁能源替代传统能源,减少对传统能源的需求,降低燃料气的消耗。
重油催化裂化装置节能优化措施分析

重油催化裂化装置节能优化措施分析重油催化裂化装置是炼油行业中较为重要的装置之一,能够将较为低级的重质油制成高级的轻质油,满足市场对于能源的需求。
但是这些装置在运行的过程中,也面临着能源消耗较大、环境污染等问题,为此,需要采取相应的节能优化措施,以达到减少能源消耗、提高生产效率、降低环境污染排放的目的。
1. 升级装置升级装置可以改善重油催化裂化装置的工作效率,提高产品质量,并减少其他不必要的成本。
比如,升级催化剂,使用能够降低反应温度的新型氧化物催化剂,这样有助于提高裂解反应的温度,从而提高生产效率。
同时,还可以增加一些分离设备,提高分离效率,降低生产成本。
2. 优化物料配方优化物料配方可以减少催化剂的使用量,降低成本,同时能够提高催化裂化的效率。
另外,在物料配方中添加一些可再生资源,如生物质或废物催化剂,也能够减少原材料的使用量,并降低污染排放,增加环保性。
3. 热集成技术应用重油催化裂化装置需要大量的热量来维持运作,因此使用热集成技术可以通过高温下的余热来为其他设备供应热能,从而减少能源消耗和排放,提高环保和经济效益。
同时,在装置设计中,也可以加装高效换热器和储热设备,以扩大热集成的范围,进一步降低装置的能耗。
4. 加强运转管理优化运转管理可以精细调节装置操作参数,减少不必要的能源消耗,提高生产效率。
比如,实行节约用水、节约电力、节约氮气等环保型改造,能够降低设备的能耗,同时还可以提高催化剂的使用效率。
此外,对于设备管理,应加强维护和保养工作,及时升级修理设备设施,减少停机维护的次数,提高运转时间和生产效率。
综上所述,在重油催化裂化装置的生产过程中,可以采取多种节能优化措施,如升级装置、优化物料配方、应用热集成技术和加强运转管理等,以实现降低能源消耗,提高生产效率和环保性的目标。
同时也需要加强科学的监控和管理,保障装置的正常运转以及设备压力温度等安全指标的稳定。
重油催化裂化装置降低催化剂消耗的方法

重油催化裂化装置降低催化剂消耗的方法引言重油催化裂化是一种常用的炼油工艺,它可以将重油转化为高价值的轻质石油产品。
然而,在这个过程中,催化剂的消耗量是一个不可忽视的成本因素。
因此,在实际应用中,如何降低催化剂消耗,提高工艺经济效益,成为了炼油厂关注的焦点问题。
本文将介绍重油催化裂化装置降低催化剂消耗的几种方法。
降低装置工艺温度重油催化裂化反应是一种热力学反应,反应温度对反应速率、产品收率和催化剂活性都有着重要的影响。
通过降低反应温度,可以减缓反应速率,延长催化剂寿命,从而降低催化剂消耗。
具体来说,可以采用以下几种方式来降低反应温度:•采用低温催化剂,如超稳定Y型分子筛、ZSM-5等,这些催化剂具有更高的抗热能力和更高的催化活性;•优化反应器物料分布和结构设计,使反应器内部流动状态更加均匀,减少热点的产生,降低反应温度;•采用物料预热技术,如采用废热回收技术,对物料进行预热,减少反应器内的温度梯度,从而降低反应温度。
采用预先硫化的催化剂在重油催化裂化过程中,由于原料中含有大量的硫化合物,会导致催化剂的毒化和失活,从而降低其催化活性和寿命。
因此,采用预先硫化的催化剂可以在一定程度上减少中毒现象的发生。
具体来说,可以在催化剂投入反应器前,将其进行预先硫化处理,使硫化物排在催化剂表面,并形成惰性物质,防止其受到硫化合物的侵蚀,从而延长催化剂的使用寿命。
加强氧化剂的使用氧化剂可以将一些含有碳污染物的组分进行氧化分解,减少碳沉积,从而延长催化剂的使用寿命。
因此,在催化裂化装置中加强氧化剂的使用可以降低催化剂消耗。
具体来说,可以采用以下几种方式来加强氧化剂的使用:•通过改变进料油品的氧含量和空气进料量的比例,调节氧化剂的使用量;•在反应器中加入促氧化剂(如金属氧化物),增加反应器中的活性氧、氢离子等物质的浓度,提高氧化剂的活性,从而降低催化剂消耗。
合理选择催化剂合理选择催化剂不仅可以提高重油催化裂化反应的活性,还可以降低催化剂的消耗。
催化裂化装置降低机组能耗措施分析及实施

催化裂化装置降低机组能耗措施分析及实施摘要:某公司150万吨/年催化裂化装置采用三机组配置,由电/发电机、轴流风机和烟机组成。
三机组配置对装置节能具有重要意义,烟机利用再生高温烟气作为工作介质做功,将能量传递给轴流风机,当烟机功率不够时,则由同步电机补充,反之,烟机多余的功用来发电,根据装置2017~2019年数据统计,夏季三机组电耗约2600~2800kW·h,较冬季电耗约高1000~1200kW·h。
如将夏季三机组电耗大幅度降低,将产生巨大的经济效益。
为此,结合装置生产实际分析降低能耗的措施方法。
关键词:催化裂化装置;机组能耗;措施分析1 问题对策及方案实施1.1 烟机动静叶片及流道改造以原机组运行工况为设计依据,以提高烟气能量回收效率为设计目的,本次改造通过改变动、静叶片的叶片形式,设计弯扭复合叶形,调整根截面、顶截面喉道面积,优化气流速度,减轻内部紊流,使气流流动顺畅,解决气流对叶片和轮盘的冲蚀问题,减轻催化剂结垢;同时,优化进气锥体型线曲率半径,以减少进气损失,减少冲刷。
改造后的烟气轮机输出效率提高约3%左右,实际输出功率可提高约1324kW。
由于齿轮箱在额定输出量的±10%范围内运行不平稳,且电机在1500kW内不能稳定正常输出,为达到节能降耗的目的,选用以下方案:更换新型高效马刀叶形叶片能有效调整等压线的分布形状,抑制根部附面层分离,减少二次流损失,使低能区的流量向主流流动,从而提高叶片的气动效率,增加叶片的做功能力,使烟机的通流效率得到很大的提高,降低改造后烟机的输出功率,使电机输出功率保持在1500kW,且同时满足电机正常工作,齿轮箱平稳输出功率。
1.2 更换低压降辅助燃烧室装置原辅助燃烧室为2002年设计制造,已连续运行17年,受当时技术水平的限制,实际运行压降较高(约6kPa)。
传统的辅助燃烧室在开工期间,为了保证燃烧器的燃烧效果,燃烧空气的压降比较大,燃烧室内筒体火道较长。
浅析重油催化裂化装置能耗构成与节能措施

浅析重油催化裂化装置能耗构成与节能措施分析了玉门炼油厂80万吨/年重油催化裂化装置能耗的构成,根据其能耗的特点,从烧焦,电,蒸汽等方面探讨了降低装置能耗可行性办法,使装置生产运行达到最优化。
标签:重油催化裂化;能耗;烧焦;节电;蒸汽玉门炼油厂80万吨/年重油催化裂化装置是2004年9月在原50万吨/年催化裂化装置的基础上改建而成。
改造过程中较多应用了国内外先进重油加工技术,如密闭式旋流快分系统、两段提升管、高效汽提、快速床-湍流床再生、ADV高效浮阀塔盘等,凝缩了国内外多来先进技术成果和设计经验。
装置最大加工量可达到2300t/d(折合年加工量80万吨),在掺渣比25%的情况下,装置能耗基本上在70kg.EO/t左右。
1 重油催化裂化装置能耗的构成对于重油催化裂化装置来说,装置生产过程中所需要的能源较多,但装置在再生过程中产生的自用能量较多,基本上可以达到自给自足。
从中可以看出:①烧焦占比最高,对装置能耗影响最大。
②蒸汽能耗与电能耗占较大比重,直接影响装置能耗。
因此,降低装置能耗着重在减少生焦量,减少用电量,减少蒸汽用量。
2 降低装置能耗的措施2.1 减少生焦量2.1.1 控制原料性质催化裂化装置在生产过程中焦炭的来源主要有:原料焦、催化焦,可汽提焦和污染焦四种,对于重油催化裂化原料焦也已成为重要的焦炭来源。
随着装置掺渣比上升,原料中胶质、重金属等含量上升,焦炭产率也随之上升,优化原料性质可降低原料焦的生成,降低焦炭产率。
发挥原料罐区的调和作用,控制掺渣率在25%左右,控制焦化蜡油掺炼比例在8%~10%之间,优化混合原料密度在900~930 kg/m3,混合原料残炭在4w%以下。
2.1.2 优化工艺操作条件①提高剂油比。
提高剂油比,原料油与尽可能多的催化剂接触,降低碳差,增加有效活性中心,提高转化率,不仅提降低了能耗,还提高了液收。
②降低或停止油浆回炼。
油浆的裂化性能比新鲜原料差得多,但其生焦倾向比新鲜原料高2~4倍。
催化裂化装置能耗因素分析及节能降耗措施

催化裂化装置能耗因素分析及节能降耗措施摘要:近些年,在我国社会经济水平不断提升下,带动了我国科学技术水平的进步,现阶段,为了全面降低催化裂化装置的能耗,文章结合催化裂化装置的基本特点进行研究,首先对催化裂化装置的能耗影响因素进行分析,烧焦、水消耗、电消耗、蒸汽消耗、低温热输出消耗都是催化裂化装置能耗的主要来源,需要从降低反应生焦率、降低电能损耗、优化系统操作、充分利用高温余热和装置间热联合等方面采取节能措施,为推动中国炼油行业节能降耗,科学发展奠定基础。
关键词:催化裂化装置;能耗因素;节能措施引言催化裂化装置(FCCU)可用于生产轻质燃料、化工原料,包括柴油、丙烯、汽油、液化气、醚化原料、烷基原料等,是常见的石油加工装置,具有技术成熟、收率高、适应性强、投资少等特点。
目前,我国的FCCU加工能力>150Mt/a,操作工艺发展方向以大剂油比、高温高压为主,工艺的苛刻度将会不断增加,再加上原料油日趋劣质化与重质化,在反应条件不能达到生产要求或能耗超出标准时可能会恶化产品质量、损失产品收率,并直接影响经济效益。
应重视分析FCCU的能耗因素及寻找节能措施,根据市场需求变化提升FCCU的生产能力。
1催化裂化装置能耗影响因素分析石油加工行业中,应用催化裂化装置产生能耗的主要影响因素有以下几方面:(1)焦炭,在催化裂化装置中形成的生焦率对于装置能耗来说影响最大,因此,降低催化裂化装置的能耗,首先要从焦炭入手,所采用的生产方案和工艺与催化裂化装置离不开关联。
(2)电耗影响因素,电动机所耗费的能量在催化裂化装置中占据比例比较大,很多企业在催化裂化装置中设置了烟气回收机,企图回收烟气给催化裂化装置带来的压力,降低用电量,甚至有的企业使用的烟气回收机还可以用来发电。
(3)蒸汽消耗影响因素,催化裂化装置在运行的过程中需要消耗大量的蒸汽,蒸汽消耗甚至在催化裂化装置中占据三分之一的消耗量,如果按照用途来划分,蒸汽用途主要有工艺用汽、动力用汽和辅助用汽这三种,其中工艺用汽主要有分馏系统,动力用汽主要是气压机或者主风机需要,辅助用汽主要用来采暖与伴热,催化裂化装置中应该在满足当前生产的前提下,尽量降低蒸汽带来的消耗。
催化裂化装置能耗特点分析及节能措施探讨
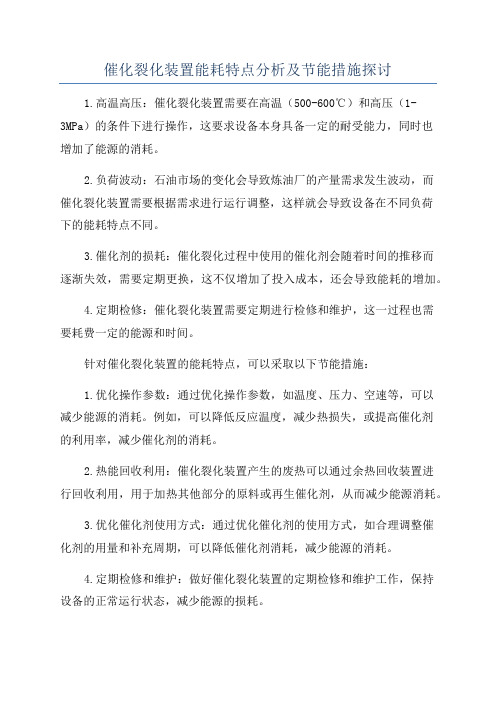
催化裂化装置能耗特点分析及节能措施探讨1.高温高压:催化裂化装置需要在高温(500-600℃)和高压(1-3MPa)的条件下进行操作,这要求设备本身具备一定的耐受能力,同时也增加了能源的消耗。
2.负荷波动:石油市场的变化会导致炼油厂的产量需求发生波动,而催化裂化装置需要根据需求进行运行调整,这样就会导致设备在不同负荷下的能耗特点不同。
3.催化剂的损耗:催化裂化过程中使用的催化剂会随着时间的推移而逐渐失效,需要定期更换,这不仅增加了投入成本,还会导致能耗的增加。
4.定期检修:催化裂化装置需要定期进行检修和维护,这一过程也需要耗费一定的能源和时间。
针对催化裂化装置的能耗特点,可以采取以下节能措施:1.优化操作参数:通过优化操作参数,如温度、压力、空速等,可以减少能源的消耗。
例如,可以降低反应温度,减少热损失,或提高催化剂的利用率,减少催化剂的消耗。
2.热能回收利用:催化裂化装置产生的废热可以通过余热回收装置进行回收利用,用于加热其他部分的原料或再生催化剂,从而减少能源消耗。
3.优化催化剂使用方式:通过优化催化剂的使用方式,如合理调整催化剂的用量和补充周期,可以降低催化剂消耗,减少能源的消耗。
4.定期检修和维护:做好催化裂化装置的定期检修和维护工作,保持设备的正常运行状态,减少能源的损耗。
5.技术改进和创新:通过技术改进和创新,如引入先进的催化剂、改进反应装置结构等,可以提高催化裂化装置的效率,降低能源的消耗。
总之,催化裂化装置的能耗特点是高温高压、负荷波动、催化剂损耗和定期检修等。
针对这些特点,可以通过优化操作参数、热能回收利用、优化催化剂使用方式、定期检修和维护以及技术改进和创新等节能措施来降低能源消耗,提高装置的能效性能。
重油催化裂化装置节能优化措施分析

重油催化裂化装置节能优化措施分析重油催化裂化装置是一种将重质石油馏分转化为轻质低碳烯烃和汽油等高附加值产品的装置,其操作能耗较大。
为了提高装置的能源利用效率,降低生产成本,需通过优化措施进行节能。
可以在催化裂化反应器的设计上进行优化。
催化裂化反应器是催化裂化装置的核心设备,在反应器内有效地提高催化剂的利用率,可以减少催化剂的用量。
采用先进的反应器结构,如研磨表面修饰技术和四层嵌套床层结构等,可以提高反应的选择性和温度场分布,减少副反应和热点现象,提高产品质量和产量。
对重油催化裂化装置的动力设备进行优化。
可以采用节能型的压缩机、风机和泵等设备,以减少设备能耗。
可通过改进压缩机的压缩比,降低功率消耗。
使用高效率的机械密封装置,减少泄漏。
对于风机和泵等设备,可采用变频调速技术,根据生产需要调整转速,以减少能耗。
对装置的能源系统进行优化也是节能的重要措施。
可以改进能源循环系统,如利用余热进行发电或供暖等,提高热能的回收利用率。
对于催化裂化装置的蒸汽系统,可采用优化的排污系统,增加换热面积,改进煤气分离系统,提高蒸汽的回收率,降低蒸汽的消耗。
还可以采用先进的自动控制系统,实现装置的优化运行。
通过对反应器温度、压力、流量等参数进行实时监控和调整,可以确保装置在最佳状态下运行,减少能耗。
还需加强管理和培训。
通过建立完善的能源管理制度和监测系统,对装置的能源消耗进行监控和评估。
加强技术培训和员工意识的提高,提高对节能技术和方法的掌握和运用水平,进一步推进节能工作。
重油催化裂化装置的节能优化措施包括优化催化裂化反应器、动力设备和能源系统,建立先进的自动控制系统,加强管理和培训等方面。
通过综合采取以上措施,可以有效降低能耗,提高装置的能源利用效率,降低生产成本,实现可持续发展。
重油催化裂化装置节能优化措施分析

重油催化裂化装置节能优化措施分析催化裂化是炼油厂重要的二次加工工艺,在重质原油轻质化过程中发挥了积极的作用,但在生产轻质燃料的同时也消耗了大量的能源。
国内炼油企业催化裂化装置的能耗平均占炼油企业能耗的35%,通过利用先进的工艺技术和优化操作条件降低装置能耗、缩短国内外企业的差距、提高市场竞争能力,是催化裂化装置亟待解决的问题。
标签:催化裂化装置;重油;经济效益;能降耗问题催化裂化装置是我国炼油行业的主要二次加工装置,也是炼油厂主要的耗能装置,随着原油价格的不断攀升以及催化裂化原料的日益加重,催化裂化装置的节能降耗问题已经成为提高催化裂化装置经济效益的关键问题,其重要性也尤为突出。
降低炼油装置能耗、实现绿色低碳生产已成为当前炼油行业实现可持续发展及提高盈利能力亟待解决的重要课题。
1.装置能耗分析为调整产品结构,增产聚丙烯等高含量满足国家标准要求,后进行多产异构烷烃的催化裂化工艺技术扩能改造。
随着原料日趋变重,产品分布逐步变差,高附加值产品收率下降,装置能耗上升。
催化裂化装置综合能耗的主要权重因素为烧焦能耗、电耗和蒸汽外送量。
其中,烧焦能耗是催化裂化装置中占比最大的能耗,但该装置焦炭产率比设计值低,使得蒸汽外送量下降很多,与设计值相比,电耗增加较多,使得装置能耗仍处于较高水平。
因此,将降低装置电耗作为节能工作的重点,同时采用多种节能手段和措施,降低其他能耗,全面发力,多方着手,降低装置总能耗。
2.节能措施及应用情况2.1节能风机改造空冷风机普遍采用轴流风机输送空气,风机不但能耗高,而且它的状态好坏直接影响整个生产线的稳定。
风机叶轮是唯一对气体做功的部件,叶片的性能好坏直接决定风机的效率和整体性能。
现役空冷风机普遍叶型简单,效率低,能耗高,不符合国家节能减排的趋势;设备长时间运行后,叶片因磨损、腐蚀、老化等因素,强度与性能下降,维护成本高。
为进一步降低风机用电,提高风机稳定性,对车间电机驱动风机的叶片进行改造,由普通叶片改为全三维高效节能轴流风机叶片。
重油催化裂化装置能耗分析及节能措施

- -重油催化裂化装置能耗分析及节能措施牛 驰(中国石化北京燕山分公司,北京102503)摘要 针对中国石化北京燕山分公司Ⅱ套重油催化裂化装置能耗较高的问题,结合装置实际情况,采取改造余热锅炉、循环水系统优化运行、回收利用低温余热、加强实施装置间热联合以及优化操作条件等一系列节能措施,装置能耗从2004 年的3 342.06 MJ/t 下降至2008年的2 103.55 MJ/t ,取得了较为明显的效果。
关键词:催化裂化装置 节能 能耗 技术改造收稿日期:2009-07-20;修改稿收到日期:2009-09-02。
作者简介:牛驰,工程师,2003年毕业于辽宁石油化工大学化学工程与工艺专业,主要从事催化裂化装置生产技术管理工作。
现为北京化工大学化工学院在读工程硕士。
1 前 言催化裂化装置是我国炼油行业的主要二次加工装置,也是炼油厂主要的耗能装置,随着原油价格的不断攀升以及催化裂化原料的日益加重,催化裂化装置的节能降耗问题已经成为提高催化裂化装置经济效益的关键问题,其重要性也尤为突出。
中国石化北京燕山分公司Ⅱ套重油催化裂化装置(简称二催化装置)能耗较高,近年来,为了降低装置能耗,结合装置实际运行情况,通过实施工艺技术改造、设备更新以及优化操作条件等一系列措施,2008年装置能耗降低至历史最好水平。
2 装置能耗情况北京燕山分公司Ⅱ套重油催化裂化装置2004—2008年的能耗见表1。
从表1可以看出,装置能耗主要分为烧焦、水消耗、电消耗、蒸汽消耗、低温热输出等几个主要部分。
其中烧焦能耗是影响装置能耗的最主要因素,如何有效地降低生焦是降低装置能耗的主要课题。
表1 装置能耗统计数据MJ/t影响装置能耗的第二大因素是蒸汽输出量。
重油催化裂化装置原料较重,生焦率较高,焦炭在再生器中燃烧放出的大量热量除提供裂化反应热外,还有大量剩余。
利用装置的高温位余热发生蒸汽,以蒸汽为介质回收热量、提高装置利用热能的能力是降低装置能耗的有效手段。
重油催化裂化装置降低催化剂消耗的方法

重油催化裂化装置降低催化剂消耗的方法背景与意义重油催化裂化是一种能够转化重质石油成为高附加值产品的技术,被广泛应用于炼油厂。
然而,重油催化裂化生产中,催化剂的消耗量占到了总投入的重要地位,而且催化剂的成本较高,因此如何降低催化剂消耗量,成为优化生产的一个重要课题。
主要方法1. 催化剂再生技术催化剂再生技术是一种将已经失去活性的催化剂通过化学和物理手段再次活化的方法。
通过催化剂再生技术,可以减少催化剂的消耗量,提高催化剂的利用率,从而降低生产成本。
具体的,催化剂再生技术包括溶剂吸附再生法、高温气氛还原法、气氛热脱附法、酸洗法等多种方法,根据不同的催化剂类型和工艺要求,选择合适的再生方法。
2. 精细化催化剂技术精细化催化剂技术是一种利用微纳米材料形成的特殊结构,通过催化剂表面的高效反应,提高催化剂性能,从而减少催化剂的消耗量的方法。
具体的,精细化催化剂技术基于相变和群集效应,通过调节催化剂分散度、粒径等因素,实现催化剂表面结构的优化,从而提高催化剂的利用效率。
3. 中间升温技术中间升温技术是一种在裂化反应过程中分别在反应器的上下部位升高温度的方法。
通过中间升温技术,可以使裂化过程的反应效率提高,从而减小催化剂的用量。
具体的,中间升温技术是通过调节反应器的反应筒和催化剂分层布置的方式,使裂化反应在不同温度下进行,从而使烃分子分别在不同阶段裂解,提高反应效率。
结论与展望重油催化裂化装置降低催化剂消耗的方法多种多样,其中包括催化剂再生技术、精细化催化剂技术、中间升温技术等多种方法。
通过这些技术的应用,可以减少催化剂的消耗量,提高催化剂的利用率,从而降低生产成本。
通过不断的研究和应用,未来将会出现更多更先进的催化技术,推动重油催化裂化装置的发展,为能源化工产业的发展做出更大贡献。
重油催化裂化装置节能措施与效果分析

科 技 论坛 l l l
徐 仕 光
重油 催化 裂化 装置 节 能措施 与效 果分析
( 中国石油哈 尔滨石化公 司 , 黑龙江 哈 尔滨 10 0 ) 5 0 0
摘 要: 重油催化 裂化装 置的能耗 问题对节能工作具有十分重要的意义 , 本文主要针对 目 前催化裂化装 置节能方面存在的 问题进行简要 阐述 , 同时分别就工艺、 设备 以及操作 三个方 面的节能措施和相应的效果进行分析论述。 关键词 : 油催化裂化 ; 重 节能 ; 存在问题 ; ; 措施 效果 . W,同时还增 温度下降 , 4 0 影响余热锅炉过热蒸汽质量 , 为此必 目前 , 重油催化裂化装置 的能耗问题对我 剂脱 沥青装 置损失 能量 达 1 M 国石油化工企业 的发展有着至 关重要 的作用 。 加 了循环水 的耗量 ; 油催化裂化装置为提高 须增加燃料气用 量, 重 因而造 成装置能耗增加 ;. d 催化裂化是我 国主要的重 油二 次加工装 置 , 同 脱沥青油温度 , 至少需提供 1 M 热量 , . W 4 0 即造 由于烟气温度低 , 省煤器的低温腐蚀加重 , 余热 时也是最主要 的耗能装置 ,强吸热催化裂化反 成油浆热量损失。 锅炉的故障率加大 , 安全运行周期缩短。 2节能措施及效果 20 年 5 , 02 月 将原余热锅炉更 换为新型模 应所需要 的全部热量都是 由催化剂再生烧焦的 过程提供 , 如何降低反应过程 的能耗 , 提高其节 21生产工艺 的优化 . 块 式余热 锅炉 , 使重油催化裂化装置所产的饱 第一 , 改善原料性质 。由于原油变重 , 常压 和蒸汽全 部过热 , 停掉了减温减压器 , 避免了高 能水平是我们研究 的重要课题 。 1节能方面存在的主要问题 渣油残炭一般 为 7 8 催化裂化焦炭产率高 品位 能量损失 ,同时提高 了余热锅炉 自
重油催化裂化装置能耗分析及节能降耗措施探讨

重油催化裂化装置能耗分析及节能降耗措施探讨发布时间:2021-11-16T09:17:52.387Z 来源:《科学与技术》2021年第8月23期作者:李玥[导读] 催化裂化装置是炼油厂重要的二次加工设备,其能耗在炼油厂能耗结构中占比较大。
李玥大庆职业学院石油化学工程系摘要:催化裂化装置是炼油厂重要的二次加工设备,其能耗在炼油厂能耗结构中占比较大。
针对催化裂化装置能耗的特点,制定相应技术措施,降低催化裂化过程中能耗,并且加强对能量的回收利用,对于企业节能减排、降本增效具有重要意义。
关键词:重油催化裂化装置;能耗影响因素;节能措施1 前言催化裂化装置是炼油厂重要的二次加工设备,油田大部分汽油和柴油都由催化裂化装置加工而来,催化裂化装置消耗的能源占炼油厂能耗的很大一部分,是炼油化工厂的能耗大户,也是炼油化工厂的主要生产设备之一。
随着我国倡导绿色发展、低碳发展的新发展路线,以及2060年代碳中和目标的确定,对企业生产提出了更高的要求。
炼油化工企业作为高污染、高能耗的企业,需要不断推动技术发展,降低生产能耗,提升企业经济效益,符合国家绿色发展的路线。
催化裂化装置作为高能耗设备,其能耗特点具有总输入能高、能量自给率低、蒸汽用量多且分散、低温低热的特点,并且能量可回收利用量大,针对催化裂化装置能耗的特点,制定相应技术措施,降低催化裂化过程中能耗,并且加强对能量的回收利用,提升能量的外输量,综合多方面降低催化裂化装置生产能耗,对于降低企业生产成本,提升化工企业经济效益具有重要意义。
2 催化裂化装置能耗影响因素分析(1)焦炭产率对能耗的影响。
催化裂化的产物焦炭主要有催化焦、污染焦、附加焦、剂油比焦,这四种焦炭附着在催化剂表面上,焦炭对催化裂化装置能耗影响较大,研究表面,焦炭产率下降一个百分点,能够减少催化裂化过程能耗4000MJ/t,特别是在重油催化过程中,由于掺渣比例较高,生焦比例大,控制生焦率是控制能耗的关键,降低重油催化过程中生焦率对于降低催化裂化装置能耗意义重大。
重油催化裂化装置节能优化措施分析

重油催化裂化装置节能优化措施分析重油催化裂化装置是炼油厂的重要装置之一,它能够将粘度大、密度大的重质石油加工成轻质石油产品,提高能源利用效率。
为了实现良好的经济效益和环保效益,需要对重油催化裂化装置进行节能优化。
在此基础上,本文将对重油催化裂化装置的节能优化措施进行分析,以期为炼油厂的生产带来更多的利益。
一、提高反应器的加热效率反应器是催化裂化过程中最为关键的设备之一,它的加热效率直接影响到整个裂化过程的效率。
为了提高反应器的加热效率,建议从以下几个方面进行改进:1.改善燃烧质量。
在重油催化裂化过程中,燃料直接影响到反应器的加热效率,因此需要注意选择合适的燃料。
此外,可以通过控制燃烧的氧气浓度和燃料进料速率等方式来改善燃烧质量,提高燃烧效率。
2.增加换热面积。
在反应器周围增加一定的换热面积,增加热量的输入,提高反应器的加热效率。
此外,在换热过程中还可以利用余热再次产生热能,进一步提高反应器的加热效率。
二、提高催化剂的利用效率1.选择合适的催化剂。
合适的催化剂可以提高炼油厂的能源利用效率和生产效率。
在选择催化剂时,需要考虑重油中各组分的含量和成分,合理选择不同组分的催化剂,以提高其活性和利用效率。
2.增加催化剂的存留时间。
催化者在反应器中的停留时间较长或反应过程中催化剂温度变化较小有利于提高催化剂的利用效率。
因此,可以通过增加催化剂的存留时间,提高催化剂的利用效率。
三、加强废气处理废气处理是催化裂化过程中的关键环节,它能够将催化裂化过程中产生的污染物去除掉,降低对环境的污染程度。
为了加强废气处理,我们建议从以下几个方面进行改进:1.合理选择废气处理设备和工艺。
不同的工艺和设备可以对不同的废气产生不同的效果,因此需要根据废气特点、目标排放标准等要求选择合适的废气处理设备和工艺,以提高废气处理效率。
2.优化系统配套。
废气处理系统需要与催化裂化系统相配套,优化系统配套能够提高系统的整体效率。
例如,在催化裂化过程中选择高效的催化剂,能够降低废气中的排放物质含量,进一步降低废气处理的难度和成本。
重油催化裂化装置节能优化措施分析

重油催化裂化装置节能优化措施分析重油催化裂化装置是炼油厂中常用的一种加工设备,其主要作用是将高沸点的重油转化为低沸点的轻质产品。
在实际运行过程中,为了提高设备的能效,减少能源消耗,可以采取以下优化措施:1. 优化反应装置结构:适当增加催化剂层数,增加反应装置的有效催化面积,提高催化剂利用率和反应效果。
还可以采用异型催化剂加入物理混合层的方式,优化反应装置内部流体分布,减少局部温度过高或过低的情况发生,提高裂解反应的效率。
2. 改进催化剂性能:选择良好的催化剂,具有较高的活性和选择性,可以提高重油裂化的反应效果。
针对催化剂的失活问题,可以采用再生和添加剂的方式进行修复和改善,延长催化剂的使用寿命,减少设备停产频率,提高装置运行的连续性和稳定性。
3. 优化冷却系统:在重油裂化过程中,由于反应产热较高,需要通过冷却系统将其以及生成的轻质产品冷却至适宜的温度。
合理设计和优化冷却器的结构、冷却介质的选择以及冷却系统的工艺参数,可以提高冷却效果,降低能耗。
4. 合理调整裂解温度和压力:裂解温度和压力是影响重油裂化反应效果以及轻质产物分布的重要因素。
通过合理调整温度和压力参数,可以提高裂解的效果和产品质量,并降低能耗。
5. 优化废热回收系统:在重油裂解过程中产生了大量的废热,合理利用这部分废热可以减少能源消耗。
可以采用余热锅炉、热交换器等设备进行废热回收,将废热转化为热水或蒸汽,用于生产和供暖等其他用途。
6. 引进先进的自动控制系统:通过引进先进的自动控制系统,可以实现对重油裂化装置的各个环节进行精确的监控和控制,提高设备的运行效率和稳定性。
还可以采用先进的模型预测和优化算法,进行工艺参数的优化调整,实现最佳化运行。
在重油催化裂化装置的节能优化中,需要综合考虑设备结构、催化剂性能、工艺参数以及自动控制等多个方面的因素。
通过合理的优化措施,可以提高设备的能效,降低能源消耗,实现经济效益和环境效益的双重收益。
催化裂化装置节能降耗途径
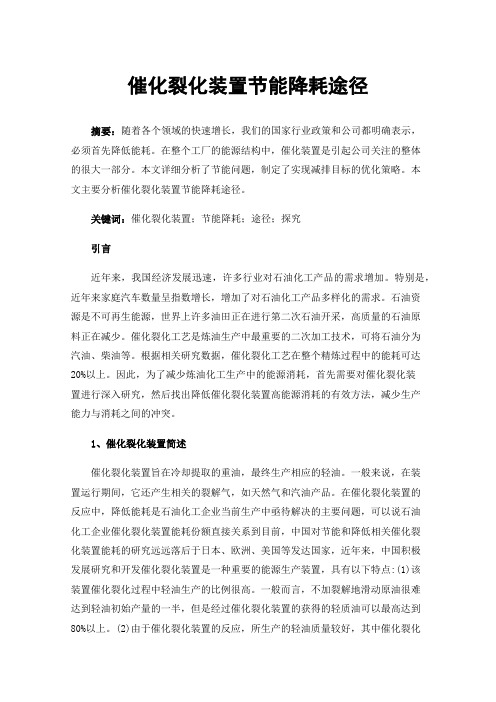
催化裂化装置节能降耗途径摘要:随着各个领域的快速增长,我们的国家行业政策和公司都明确表示,必须首先降低能耗。
在整个工厂的能源结构中,催化装置是引起公司关注的整体的很大一部分。
本文详细分析了节能问题,制定了实现减排目标的优化策略。
本文主要分析催化裂化装置节能降耗途径。
关键词:催化裂化装置;节能降耗;途径;探究引言近年来,我国经济发展迅速,许多行业对石油化工产品的需求增加。
特别是,近年来家庭汽车数量呈指数增长,增加了对石油化工产品多样化的需求。
石油资源是不可再生能源,世界上许多油田正在进行第二次石油开采,高质量的石油原料正在减少。
催化裂化工艺是炼油生产中最重要的二次加工技术,可将石油分为汽油、柴油等。
根据相关研究数据,催化裂化工艺在整个精炼过程中的能耗可达20%以上。
因此,为了减少炼油化工生产中的能源消耗,首先需要对催化裂化装置进行深入研究,然后找出降低催化裂化装置高能源消耗的有效方法,减少生产能力与消耗之间的冲突。
1、催化裂化装置简述催化裂化装置旨在冷却提取的重油,最终生产相应的轻油。
一般来说,在装置运行期间,它还产生相关的裂解气,如天然气和汽油产品。
在催化裂化装置的反应中,降低能耗是石油化工企业当前生产中亟待解决的主要问题,可以说石油化工企业催化裂化装置能耗份额直接关系到目前,中国对节能和降低相关催化裂化装置能耗的研究远远落后于日本、欧洲、美国等发达国家,近年来,中国积极发展研究和开发催化裂化装置是一种重要的能源生产装置,具有以下特点:(1)该装置催化裂化过程中轻油生产的比例很高。
一般而言,不加裂解地滑动原油很难达到轻油初始产量的一半,但是经过催化裂化装置的获得的轻质油可以最高达到80%以上。
(2)由于催化裂化装置的反应,所生产的轻油质量较好,其中催化裂化所生产的汽油含有较多的辛烷,燃烧所产生的能量较高,催化裂化所生产的汽油较安全。
(3)催化裂化装置反应过程中的气体生产率约为15%,所生产的气体大部分是含乙烯燃料较多的液化石油气(GPL)。
重油催化裂化装置节能优化措施分析

重油催化裂化装置节能优化措施分析重油催化裂化装置是炼油厂中的重要设备,用于将重油进行裂化反应,产生更多的轻质油品,如汽油和柴油。
由于裂化反应所需能量较大,重油催化裂化装置的能耗一直是炼油企业关注的焦点。
为了降低能耗、提高生产效率和降低成本,需要对重油催化裂化装置的节能优化措施进行分析和研究。
一、工艺参数优化在重油催化裂化装置的运行过程中,对工艺参数的优化是降低能耗的关键。
需要对裂化反应的温度、压力、催化剂种类和比表面积等参数进行综合优化,以确保裂化反应的高效进行。
需要对裂化反应器的结构和材料进行改进,提高传热效率和防腐蚀性能,减少能量损耗和设备维护成本。
还需要对产品分离和精馏过程进行优化,提高产品收率和质量,减少能源消耗和环境污染。
二、节能设备应用为了降低重油催化裂化装置的能耗,可以采用一些节能设备进行辅助。
在裂化反应器的传热装置中使用高效换热器和隔沉器,提高传热效率和分离效果,减少能量损耗和产品损失。
在产品分离和精馏过程中使用节能离心机、蒸馏塔和冷凝器等设备,提高产品收率和质量,降低热能消耗和材料损耗。
三、能源优化管理重油催化裂化装置的能源优化管理是节能工作的重点内容。
通过建立全面的能源消耗监测系统,对设备、管道和工艺进行实时监测和分析,及时发现和处理能源浪费和泄漏问题,提高能源利用率和设备运行稳定性。
还可以实施能源管理制度和标准化作业流程,加强员工能源节约意识和技能培训,减少人为因素对能源消耗的影响。
四、技术改进创新五、环境保护措施在重油催化裂化装置的节能优化过程中,需要注重环境保护措施的实施。
可以通过改进废热利用装置和环保设施,将裂化反应产生的废热和废气进行深度利用和处理,减少能源浪费和环境污染。
还可以加强废水处理和垃圾回收利用工作,降低生产过程对水资源和土地资源的消耗,实现循环经济和可持续发展。
重油催化裂化装置的节能优化是炼油企业提高竞争力和可持续发展的重要举措。
通过工艺参数优化、节能设备应用、能源优化管理、技术改进创新和环境保护措施的综合实施,可以实现能耗降低、生产效率提高和环境质量改善的良好效果,为炼油企业的长期发展奠定坚实的基础。
- 1、下载文档前请自行甄别文档内容的完整性,平台不提供额外的编辑、内容补充、找答案等附加服务。
- 2、"仅部分预览"的文档,不可在线预览部分如存在完整性等问题,可反馈申请退款(可完整预览的文档不适用该条件!)。
- 3、如文档侵犯您的权益,请联系客服反馈,我们会尽快为您处理(人工客服工作时间:9:00-18:30)。
重油催化裂化装置能耗分析及节能降耗
措施探讨
摘要:催化裂化装置是炼油厂重要的二次加工设备,其能耗在炼油厂能耗结构中占比较大。
针对催化裂化装置能耗的特点,制定相应技术措施,降低催化裂化过程中能耗,并且加强对能量的回收利用,对于企业节能减排、降本增效具有重要意义。
关键词:重油催化裂化装置;能耗影响因素;节能措施
1 前言
催化裂化装置是炼油厂重要的二次加工设备,油田大部分汽油和柴油都由催化裂化装置加工而来,催化裂化装置消耗的能源占炼油厂能耗的很大一部分,是炼油化工厂的能耗大户,也是炼油化工厂的主要生产设备之一。
随着我国倡导绿色发展、低碳发展的新发展路线,以及2060年代碳中和目标的确定,对企业生产提出了更高的要求。
炼油化工企业作为高污染、高能耗的企业,需要不断推动技术发展,降低生产能耗,提升企业经济效益,符合国家绿色发展的路线。
催化裂化装置作为高能耗设备,其能耗特点具有总输入能高、能量自给率低、蒸汽用量多且分散、低温低热的特点,并且能量可回收利用量大,针对催化裂化装置能耗的特点,制定相应技术措施,降低催化裂化过程中能耗,并且加强对能量的回收利用,提升能量的外输量,综合多方面降低催化裂化装置生产能耗,对于降低企业生产成本,提升化工企业经济效益具有重要意义。
2 催化裂化装置能耗影响因素分析
(1)焦炭产率对能耗的影响。
催化裂化的产物焦炭主要有催化焦、污染焦、附加焦、剂油比焦,这四种焦炭附着在催化剂表面上,焦炭对催化裂化装置能耗影响较大,研究表面,焦炭产率下降一个百分点,能够减少催化裂化过程能耗4000MJ/t,特别是在重油催化过程中,由于掺渣比例较高,生焦比例大,控制生
焦率是控制能耗的关键,降低重油催化过程中生焦率对于降低催化裂化装置能耗意义重大。
(2)烟气系统能量回收率低造成能耗偏高。
催化裂化装置不仅产能高,能耗也高,在反应过程中,做好能量的回收利用对于降低能耗意义重大。
在重油催化裂化过程中,再生烟气余热能量大,加强对余热的回收利用具有重要意义。
研究表明,馏分油装置的可利用余热换算成能耗为300MJ/t左右,重油装置能耗能够达到800MJ/t。
经过统计,我国炼油化工企业重油催化剂裂化装置能量回收利用只有60%左右,剩余的能量白白浪费掉了,导致催化裂化装置能量利用率偏低,排出的烟气温度较高,携带走了大量热量,导致这部分热量无法利用。
(3)热工系统积灰对能耗的影响。
在催化裂化装置长期运行过程中,锅炉内管束内容易积灰,当积灰严重时,会导致余锅排烟温度太高,同时蒸汽温度较低,为了保证蒸汽温度达到要求,必须多燃烧燃料。
为了保证余锅能耗不至于太高,必须过一段时间就清理一次锅炉,在清理期间,需要停产,锅炉检修周期通常在两周左右,检修期间装置处于停产或半停产状态,大量高温烟气会直接排放到大气中,同时,为了平衡其它部分的蒸汽,必须加大燃料用量,造成能耗的浪费,同时给环境造成较大污染。
3 降低重油催化裂化装置能耗的对策
3.1降低焦炭产率
降低焦炭产率对于催化裂化装置能耗影响较大,为了有效降低能耗,可以从以下几个方面来降低焦炭产率:
(1)优化干气预提升量,在保证气压机负荷的情况下,既钝化了催化剂上的重金属,又有利于增大油气分压,减少生焦。
在满足汽油烯烃指标的情况下,严格控制平衡剂活性,避免加注催化剂过多,导致催化剂活性太高,反应深度大,而导致总生焦量上升。
增加了催化剂消耗得同时也不利于降低生焦。
(2)在适当提高汽提段的催化剂藏量的同时优化汽提蒸汽量。
延长了汽提段催化剂的停留时间,尽量降低可汽提焦,控制沉降器料位在65%~70%。
而蒸汽耗量却减少了,这也有利于降低分馏塔顶的冷却负荷,降低循环水用量。
(3)根据原料性质的变化,及时调整反应深度,使提升管出口温度控制在一个合理的范围,降低焦炭和干气产率。
(4)应用降低焦炭产率的工艺设备。
降低焦炭产率的工艺设备,主要集中在预提升段、原料喷嘴、提升管出口快分、汽提段等部位。
目前新型工艺设备较多,其降低焦炭产率的出发点都是改善提升管催化剂流化状态,改善原料、尤其是重质原料的雾化状态,减少反应生成油气与催化剂的接触时间,减少油气在沉降器的停留时间,强化汽提段汽提效果,尽量减少催化剂表面的可汽提焦。
这些措施可以根据装置的原料性质、生产方案、装置特性甄别选用。
3.2 改进优化烟机,提高烟机回收功率
烟气轮机是催化裂化装置最重要的能量回收设备,其运行好坏对装置电耗具有决定性作用。
目前困扰烟气能量回收系统的关键是烟机随着装置的运行,运行工况逐渐变差、烟机逐渐下降。
在停机检修前,在保证烟机操作水平的同时,通过注意以下问题来保证烟机的平稳运行。
降低主风机出口至烟机入口压降要逐段分析主风机出口至烟气轮机管路压降,对压降大的部位采取适当措施。
注意辅助设备上的问题,如油站、阀门及控制系统等的问题。
控制烟机入口催化剂浓度和粒度,减少一次和二次磨损。
控制好轮盘冷却蒸汽的品质。
保持较高的再生压力以保证烟机的入口压力。
3.3 定期清理烟气轮机,确保烟气轮机运转正常
烟气轮机的平稳、高效、长周期运行,对装置节能意义重大。
影响烟机长周期运行的因素主要是烟机结垢。
针对烟气轮机结垢问题,需要从以下几个方面进行清理:首先对一、二再旋风分离器进行内部衬里修复;其次将三旋内部损坏或磨损严重的分离单管进行更换或修复,提高分离效率;然后控制烟机入口温度,避开催化剂易结垢的温度区域;最后提高烟气轮机使用蒸汽温度,防止随烟气进
入烟气轮机内部叶片间的催化剂细粉和泥结垢;还可以提高常压电脱盐的合格率,减少原料和催化剂的重金属含量。
3.4 增加蒸汽量,降低蒸汽消耗
由于催化裂化装置热量较大,导致产生的蒸汽多,这些分蒸汽除一部分自用外,其余蒸汽外输出去供后续流程使用。
如果能够降低催化裂化蒸汽用量,就能增加外输蒸汽量,能够抵消一部分催化裂化装置能耗。
可以从以下几个方面来减少蒸汽消耗:一是提高富气压缩机压力,减少汽轮机的蒸汽消耗量;二是减少或者停用分馏塔冷回流量,使得分馏塔压降减小,减少冷回流量;二是优化余热锅炉运行,避免出现排烟温度高、过热能力差、吹灰器效果差等问题;三是提高低压蒸汽利用率。
优化能源调度方式,加强对低温位蒸汽的使用管理,同时可以开发低压蒸汽发电技术,提高能量回收利用。
3.5 优化催化裂化装置间热联合,增加低温热输出
催化裂化装置间可以通过强化热联合,优化上下游装置间的配合,使得整体能耗降低。
可以从以下几个方面加强热联合:一是催化裂化装置与常减压蒸馏装置之间的热联合。
常减压蒸馏装置是催化裂化装置原料的提供方,可以加强上下游结合,例如渣油和蜡油经过常减压装置换热后输送到催化裂化装置,然后进行加热到所需温度。
同时可以将催化裂化装置的油浆送到常减压装置加热,从常减压装置返回后能够产生蒸汽;二是催化裂化装置与柴油加氢装置联合。
改变过去柴油换热后冷却的做法,无需冷却,直接以热出料的方式为催化加氢装提供原料。
4 结束语
随着我国环境保护政策越来越严格,绿色发展、低碳经济已成为大趋势,石油化工企业作业高污染、高能耗企业,必须把握国家产业政策,将节能减排工作提上日程。
催化裂化装置作为石油化工企业能耗大户,其能量利用效率直接关系到企业能耗,必须针对装置特征、用料情况、催化剂情况等,进行认真研究论证,采取针对性对策,降低催化裂化装置能耗,为企业节能减排做出贡献。
参考文献:
[1] 童三和.重油催化裂化装置能耗分析与节能措施[J].江西能源,
2004(4):35-38.
[2] 尤克伟.1.4Mt/a重油催化裂化装置能耗分析与措施[J].中外能源,2010,15(11):88-91.。