催化裂化柴油加工路线选择及优化
石油化工催化裂化工艺技术优化

2019年06月石油化工催化裂化工艺技术优化赫晓龙(珠海裕珑石化有限公司,广东珠海519050)摘要:催化裂化工艺技术是石油化工企业生产中的主要原油加工技术,经过催化裂化装置可以对原油进行深层加工,把密度较大的重质油转换成密度相对较低的轻质油,从而满足石油化工产品生产需求。
经过炼油催化裂化加工的重质油,可以获得多个优质优良的附加产品,例如汽油等,对于石油化工企业带来了丰富的经济效益。
因此为了进一步增加原油催化裂化效果,从原油中获得更多的产品收益,必须要对现有的催化裂化工艺技术进行必要的优化,从而提升催化裂化工艺技术含量,以此获得更多的经济效益。
文章主要对现有的石油化工催化裂化工艺技术进行分析,并从石油催化裂化工艺的流程、催化剂以及工艺管理等方面进行技术优化。
关键词:石油化工;催化裂化;工艺;技术;优化措施现代国内外石油化工企业获取轻质油石油化工产品的主要工艺技术就是催化裂化工艺技术,提升现有的催化裂化工艺技术含量,可以有效增加重质油的催化裂化效果。
对于重质油进行催化裂化产生的石油化工产品具有显著的顺序性,经过催化裂化工艺反应过程会得到多种优质石油化工产品,并且最终催化裂化装置获剩余的是焦炭。
目前我国各个石油化工企业的原油性质存在着差异性,因此近年来我国的催化裂化工艺技术发展呈现多样化,石油资源属于不可再生资源,因此近年来开采的石油趋向劣质化,再加上国内环保的要求越发严格,重重条件都限制了石油化工催化裂化技术必须要进行优化升级,既要在保证现有催化裂化产品的质量前提下,也要做到生产过程的环保性,只有这样才能满足石油化工企业的发展需要。
1石油化工催化裂化工艺技术简述现代石油化工企业的催化裂化工艺技术发展过程经历了多个时期,从开始的固定床、移动床、流化床以及发展到现在的提升管技术等,每一个发展阶段的,催化裂化技术都表现了各自的工艺技术特征,在实际的重质油催化裂化反应过程中,根据实际生产状况,需要采用最佳的催化裂化工艺技术,可以有效减少原油的催化裂化成本支出,增加催化裂化的效果,让石油化工企业得到更多的经济效益。
石油化工催化裂化装置工艺流程图

炼油生产安全技术-催化裂化的装置简介类型及工艺流程催化裂化技术的发展密切依赖于催化剂的发展。
有了微球催化剂,才出现了流化床催化裂化装置;分子筛催化剂的出现,才发展了提升管催化裂化.选用适宜的催化剂对于催化裂化过程的产品产率、产品质量以及经济效益具有重大影响。
催化裂化装置通常由三大部分组成,即反应¾再生系统、分馏系统和吸收稳定系统。
其中反应––再生系统是全装置的核心,现以高低并列式提升管催化裂化为例,对几大系统分述如下:㈠反应––再生系统新鲜原料(减压馏分油)经过一系列换热后与回炼油混合,进入加热炉预热到370℃左右,由原料油喷嘴以雾化状态喷入提升管反应器下部,油浆不经加热直接进入提升管,与来自再生器的高温(约650℃~700℃)催化剂接触并立即汽化,油气与雾化蒸汽及预提升蒸汽一起携带着催化剂以7米/秒~8米/秒的高线速通过提升管,经快速分离器分离后,大部分催化剂被分出落入沉降器下部,油气携带少量催化剂经两级旋风分离器分出夹带的催化剂后进入分馏系统。
积有焦炭的待生催化剂由沉降器进入其下面的汽提段,用过热蒸气进行汽提以脱除吸附在催化剂表面上的少量油气。
待生催化剂经待生斜管、待生单动滑阀进入再生器,与来自再生器底部的空气(由主风机提供)接触形成流化床层,进行再生反应,同时放出大量燃烧热,以维持再生器足够高的床层温度(密相段温度约650℃~68 0℃)。
再生器维持0.15MPa~0。
25MPa (表)的顶部压力,床层线速约0。
7米/秒~1。
0米/秒。
再生后的催化剂经淹流管,再生斜管及再生单动滑阀返回提升管反应器循环使用。
烧焦产生的再生烟气,经再生器稀相段进入旋风分离器,经两级旋风分离器分出携带的大部分催化剂,烟气经集气室和双动滑阀排入烟囱。
再生烟气温度很高而且含有约5%~10% CO,为了利用其热量,不少装置设有CO 锅炉,利用再生烟气产生水蒸汽。
对于操作压力较高的装置,常设有烟气能量回收系统,利用再生烟气的热能和压力作功,驱动主风机以节约电能。
优化分馏操作 提高柴油收率
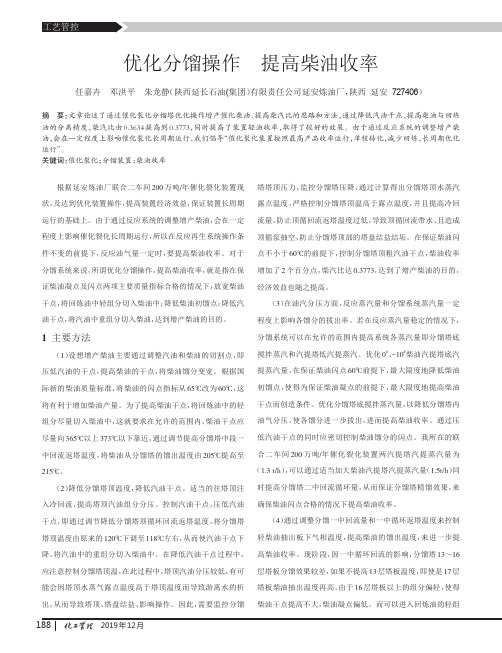
2019年12月优化分馏操作提高柴油收率任嘉卉邓洪平朱龙静(陕西延长石油(集团)有限责任公司延安炼油厂,陕西延安727406)摘要:文章论述了通过催化裂化分馏塔优化操作增产催化柴油、提高柴汽比的思路和方法,通过降低汽油干点、提高柴油与回炼油的分离精度,柴汽比由0.3634提高到0.3773,同时提高了装置轻油收率,取得了较好的效果。
由于通过反应系统的调整增产柴油,会在一定程度上影响催化裂化长周期运行,我们倡导“催化裂化装置按照最高产品收率运行,单程转化,减少回炼,长周期优化运行”。
关键词:催化裂化;分馏装置;柴油收率根据延安炼油厂联合二车间200万吨/年催化裂化装置现状,及达到优化装置操作,提高装置经济效益,保证装置长周期运行的基础上。
由于通过反应系统的调整增产柴油,会在一定程度上影响催化裂化长周期运行,所以在反应再生系统操作条件不变的前提下,反应油气量一定时,要提高柴油收率。
对于分馏系统来说,所谓优化分馏操作,提高柴油收率,就是指在保证柴油凝点及闪点两项主要质量指标合格的情况下,放宽柴油干点,将回炼油中轻组分切入柴油中;降低柴油初馏点;降低汽油干点,将汽油中重组分切入柴油,达到增产柴油的目的。
1主要方法(1)设想增产柴油主要通过调整汽油和柴油的切割点,即压低汽油的干点,提高柴油的干点,将柴油馏分变宽。
根据国际新的柴油质量标准,将柴油的闪点指标从65℃改为60℃,这将有利于增加柴油产量。
为了提高柴油干点,将回炼油中的轻组分尽量切入柴油中,这就要求在允许的范围内,柴油干点应尽量向365℃以上373℃以下靠近,通过调节提高分馏塔中段一中回流返塔温度,将柴油从分馏塔的馏出温度由205℃提高至215℃。
(2)降低分馏塔顶温度,降低汽油干点。
适当的往塔顶注入冷回流,提高塔顶汽油组分分压。
控制汽油干点,压低汽油干点,即通过调节降低分馏塔顶循环回流返塔温度,将分馏塔塔顶温度由原来的120℃下调至118℃左右,从而使汽油干点下降,将汽油中的重组分切入柴油中。
石油化工催化裂化工艺技术优化
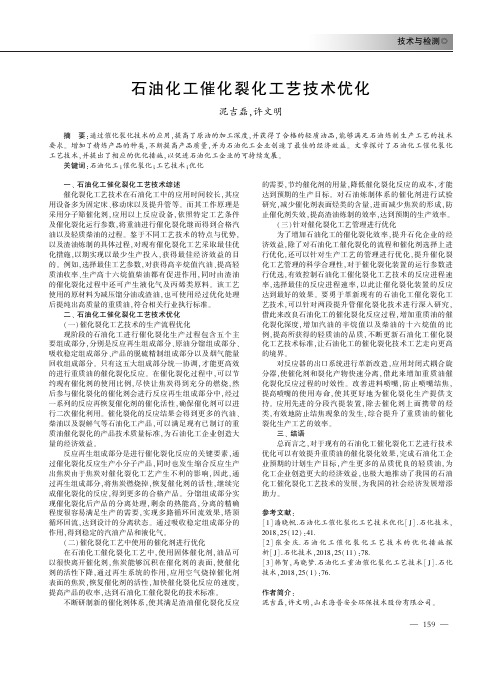
技术与检测Һ㊀石油化工催化裂化工艺技术优化泥吉磊ꎬ许文明摘㊀要:通过催化裂化技术的应用ꎬ提高了原油的加工深度ꎬ并获得了合格的轻质油品ꎬ能够满足石油炼制生产工艺的技术要求ꎮ增加了精炼产品的种类ꎬ不断提高产品质量ꎬ并为石油化工企业创造了最佳的经济效益ꎮ文章探讨了石油化工催化裂化工艺技术ꎬ并提出了相应的优化措施ꎬ以促进石油化工企业的可持续发展ꎮ关键词:石油化工ꎻ催化裂化ꎻ工艺技术ꎻ优化一㊁石油化工催化裂化工艺技术综述催化裂化工艺技术在石油化工中的应用时间较长ꎬ其应用设备多为固定床㊁移动床以及提升管等ꎮ而其工作原理是采用分子筛催化剂ꎬ应用以上反应设备ꎬ依照特定工艺条件及催化裂化运行参数ꎬ将重油进行催化裂化继而得到合格汽油以及轻质柴油的过程ꎮ鉴于不同工艺技术的特点与优势ꎬ以及渣油炼制的具体过程ꎬ对现有催化裂化工艺采取最佳优化措施ꎬ以期实现以最少生产投入ꎬ获得最佳经济效益的目的ꎮ例如ꎬ选择最佳工艺参数ꎬ对获得高辛烷值汽油㊁提高轻质油收率㊁生产高十六烷值柴油都有促进作用ꎬ同时由渣油的催化裂化过程中还可产生液化气及丙烯类原料ꎮ该工艺使用的原材料为减压馏分油或渣油ꎬ也可使用经过优化处理后提纯出高质量的重质油ꎬ符合相关行业执行标准ꎮ二㊁石油化工催化裂化工艺技术优化(一)催化裂化工艺技术的生产流程优化现阶段的石油化工进行催化裂化生产过程包含五个主要组成部分ꎬ分别是反应再生组成部分㊁原油分馏组成部分㊁吸收稳定组成部分㊁产品的脱硫精制组成部分以及烟气能量回收组成部分ꎮ只有这五大组成部分统一协调ꎬ才能更高效的进行重质油的催化裂化反应ꎮ在催化裂化过程中ꎬ可以节约现有催化剂的使用比例ꎬ尽快让焦炭得到充分的燃烧ꎬ然后参与催化裂化的催化剂会进行反应再生组成部分中ꎬ经过一系列的反应再恢复催化剂的催化活性ꎬ确保催化剂可以进行二次催化利用ꎮ催化裂化的反应结果会得到更多的汽油㊁柴油以及裂解气等石油化工产品ꎬ可以满足现有已制订的重质油催化裂化的产品技术质量标准ꎬ为石油化工企业创造大量的经济效益ꎮ反应再生组成部分是进行催化裂化反应的关键要素ꎬ通过催化裂化反应生产小分子产品ꎬ同时也发生缩合反应生产出焦炭由于焦炭对催化裂化工艺产生不利的影响ꎬ因此ꎬ通过再生组成部分ꎬ将焦炭燃烧掉ꎬ恢复催化剂的活性ꎬ继续完成催化裂化的反应ꎬ得到更多的合格产品ꎮ分馏组成部分实现催化裂化后产品的分离处理ꎬ剩余的热能高ꎬ分离的精确程度很容易满足生产的需要ꎬ实现多路循环回流效果ꎬ塔顶循环回流ꎬ达到设计的分离状态ꎮ通过吸收稳定组成部分的作用ꎬ得到稳定的汽油产品和液化气ꎮ(二)催化裂化工艺中使用的催化剂进行优化在石油化工催化裂化工艺中ꎬ使用固体催化剂ꎬ油品可以很快离开催化剂ꎬ焦炭能够沉积在催化剂的表面ꎬ使催化剂的活性下降ꎬ通过再生系统的作用ꎬ应用空气烧掉催化剂表面的焦炭ꎬ恢复催化剂的活性ꎬ加快催化裂化反应的速度ꎬ提高产品的收率ꎬ达到石油化工催化裂化的技术标准ꎮ不断研制新的催化剂体系ꎬ使其满足渣油催化裂化反应的需要ꎬ节约催化剂的用量ꎬ降低催化裂化反应的成本ꎬ才能达到预期的生产目标ꎮ对石油炼制体系的催化剂进行试验研究ꎬ减少催化剂表面烃类的含量ꎬ进而减少焦炭的形成ꎬ防止催化剂失效ꎬ提高渣油炼制的效率ꎬ达到预期的生产效率ꎮ(三)针对催化裂化工艺管理进行优化为了增加石油化工的催化裂化效率ꎬ提升石化企业的经济效益ꎬ除了对石油化工催化裂化的流程和催化剂选择上进行优化ꎬ还可以针对生产工艺的管理进行优化ꎬ提升催化裂化工艺管理的科学合理性ꎬ对于催化裂化装置的运行参数进行优选ꎬ有效控制石油化工催化裂化工艺技术的反应进程速率ꎬ选择最佳的反应进程速率ꎬ以此让催化裂化装置的反应达到最好的效果ꎮ要勇于革新现有的石油化工催化裂化工艺技术ꎬ可以针对两段提升管催化裂化技术进行深入研究ꎬ借此来改良石油化工的催化裂化反应过程ꎬ增加重质油的催化裂化深度ꎬ增加汽油的辛烷值以及柴油的十六烷值的比例ꎬ提高所获得的轻质油的品质ꎬ不断更新石油化工催化裂化工艺技术标准ꎬ让石油化工的催化裂化技术工艺走向更高的境界ꎮ对反应器的出口系统进行革新改造ꎬ应用封闭式耦合旋分器ꎬ使催化剂和裂化产物快速分离ꎬ借此来增加重质油催化裂化反应过程的时效性ꎮ改善进料喷嘴ꎬ防止喷嘴结焦ꎬ提高喷嘴的使用寿命ꎬ使其更好地为催化裂化生产提供支持ꎮ应用先进的分段汽提装置ꎬ除去催化剂上面携带的烃类ꎬ有效地防止结焦现象的发生ꎬ综合提升了重质油的催化裂化生产工艺的效率ꎮ三㊁结语总而言之ꎬ对于现有的石油化工催化裂化工艺进行技术优化可以有效提升重质油的催化裂化效果ꎬ完成石油化工企业预期的计划生产目标ꎬ产生更多的品质优良的轻质油ꎬ为化工企业创造更大的经济效益ꎬ也极大地推动了我国的石油化工催化裂化工艺技术的发展ꎬ为我国的社会经济发展增添助力ꎮ参考文献:[1]潘晓帆.石油化工催化裂化工艺技术优化[J].石化技术ꎬ2018ꎬ25(12):41.[2]张金庆.石油化工催化裂化工艺技术的优化措施探析[J].石化技术ꎬ2018ꎬ25(11):78.[3]韩贺ꎬ马晓梦.石油化工重油催化裂化工艺技术[J].石化技术ꎬ2018ꎬ25(1):76.作者简介:泥吉磊ꎬ许文明ꎬ山东海普安全环保技术股份有限公司ꎮ951。
重油催化裂化装置增产柴油方案论文

重油催化裂化装置增产柴油的方案分析[摘要]本文从生产实际出发,逐个分析提高柴油收率的生产方案以及使用各方案后的实际效果。
[关键词]重油催化裂化增产柴油反应温度剂油比回炼比平衡催化剂活性中图分类号:te96 文献标识码:a 文章编号:1009-914x(2013)04-0273-011.前言中国石油大庆石化公司炼油厂现有两套重油催化裂化装置。
其中ⅱ套重油催化装置加工大庆减压渣油、减压蜡油,年加工能力为1.4mt/a,2000年5月建成投产,2008年8月进行mip工艺改造,以达到生产低烯烃、高辛烷值汽油的目的。
为满足市场对柴油的实际需求,装置通过生产调整,增产柴油。
本文将对操作条件变更及实际效果进行逐一讨论。
2.反应部分的操作调整2.1.所用原料性质的影响原则上环烷基和环烷中间基的原料柴油产率高,而直链烃类含较高的石蜡基原料,较容易裂化,提高柴油产率相对较难。
在实际生产中,装置通过提高掺渣比或掺炼其它形式的原料来控制原料中的直链烃类。
但在实际生产过程中,提高掺渣比或掺炼原料会导致生焦量过大,而再生器烧焦负荷是一定的,所以不可以提高幅度过大。
应缓慢提升残渣比和回炼比,同时密切注意再生器烧焦情况,谨防超温。
2.2.反应温度的影响反应温度是催化裂化装置的一个重要操作参数和主要调节手段,反应温度的高低主要取决于原料油的性质、装置结构形式、操作情况以及产品分布的要求。
因此,反应温度的选择应根据装置的实际生产情况,综合考虑各种因素确定。
适当地降低反应温度有利于增产柴油、提高柴油产量。
降低反应温度即减缓了裂化反应速度,从而可以抑制柴油的二次裂化,达到提高柴油产率的目的,但反应温度的降低程度还要视原料油的性质而定。
本装置采用的原料是蜡油和渣油掺炼的形式,掺渣率较高,还有少部分的酮苯蜡膏、加氢尾油、焦化蜡油等,由于原料油较重,难裂化,为了最大限度的获得综合目的产品,通常采用高苛刻度操作。
然而反应温度过高,就会造成部分柴油组分发生裂化,降低了柴油收率,而反应温度过低,又会造成深度不够,即使能够维持较高的回炼比,柴油收率也会受到影响,所以反应温度的高低必须考虑到各种掺炼油和反应深度的影响。
催化裂化柴油的精制

催化裂化柴油的精制重油催化裂化柴油是二次加工产品.由于其中含有大量的烯烃.芳烃和硫,氮,氧化合物.使得催化柴油特别是重油催化柴油的胶质含量比较高这些组分都是氧化.缩合反应的活I生组分从而造成催化裂化柴油的安定『生差其直观表现为颜色很快变深和生成沉淀.为了改善催化裂化柴油的安定性,必须对其进行精制.催化柴油的精制主要分为加氢精制和非加氢精制(化学精制)——加氢精制的优点是精制油收率高,安定性好.无三废排放,非烃化合物脱除率高,但一次性投资大,精制费用高.操作难度大等缺点限制了其应用;化学精制的优点是设备简单,一次性投资少,精制费用低,容易操作等.特别适合中小型炼厂泰州石油化工总厂自行研制了一种柴油化学除胶剂.可有效脱除柴油中的不安定组分.工艺简单,投资少,成本低.是目前非加氢■精制的有效手段.I取自泰州石化总厂催化裂化装置脱胶前馏出口化学除胶剂为自制.以液碱为主要成分.添加聚丙烯酰胺,叔丁醇等化学物质.在催化柴油中加入一定量的除胶剂后.搅拌.沉降.除去黑色胶质.水洗.脱水.2.结果与讨论GB252—2000标准规定柴油的色度不大于35号,氧化总不溶物不大于2.5rag/100mL.分析我厂催化裂化柴油.氧化总不溶物有时大于2.5mg/100mL,避光储存3个月后氧化总不溶物和色度均不合格.因此试验主要是考察氧化总不溶物含量和色度.21除胶剂加入量对精制效果的影响取催化柴油分析当天色度为20号氧化总不溶物为642rag/1OOmL.按一定比例加入除胶剂进行精制.结果显示使用量分别为1‰,3%0.5‰.7‰时,当天色度均为20号.氧化总不溶物分别为1.78rag/1OOmL.1.81rag/1OOmL. 178rag/1OOmL.179mg/1OOmL避光储存3个月后色度分别为30号.25号. 25号,25号氧化总不溶物分别为236rag/1OOmL212rag/1OOmL208rag/1OOmL.21Omg/1OOmL.可以看出,除胶剂能够稳定催化柴油的色度,降低氧化总不溶物.根据试验结果选取加入量为3%0.22精制温度对精制效果的影响取催化柴油+分析当天色度为15号.氧化总不溶物为52mg/1OOmL.分别在室温40.C,50.C,60.C,80.C精制.精制当天色度分别为15号.20号20号25号,25号.氧化总不溶物分别为1.17mg/1OOmL,128mg/1OOmL132mg/1OOmL1.52mg/1OOmL.136mg/ 1OOmL3个月后色度分别为25号.30 号.3.5号,5.0号.70号,氧化总不溶物分别为151mg/1OOmL183mg/1OOmL,192mg/1O0mL.179mg/1OOmL,163mg/1OOmL.根据试验结果.精制温度对催化柴油氧化总不溶物的影响不大.但对色度影响较大综合试验和装置的实际情况,选择精制温度为40.C. 23搅拌时间对精制效果的影响取催化柴油,分析当天色度为15号.氧化总不溶物为52mg/1OOmL.分别考察搅拌时间为05mIn.1rain,2mIn. 4mIn,10mIn时的精制效果,色度均为20号,氧化总不溶物分别为1.32g/1OOmL,129mg/100mL.1.31mg/1OOmL128mg/1OOmL.128mg/1OOmL.可见搅拌时间对精制影响不大.选择搅拌时间为1m-n,可以兼顾到生产的需要.24沉蜂时间对精制效果的影Ⅱ向取催化柴油分析当天色度为15号,氧化总不溶物为52mg/1OOmL分别考察沉降时间为05m[n.1mIn,2mIn, 3m-n.10mln时的精制效果,色度均为2 0号氧化总不溶物分别为179mg/1OOmL165mg/1OOmL.1.48mg/1OOmL.152mg/1OOmL.14gmg/1OOmL.可以看出,随着沉降时间的延长胶质脱除更彻底由于除胶剂本身在柴油中沉降速度较快.总体上对精制效果影响不大.考虑到生产需要.选择沉降1rain为宜.25除姣荆的使用范重分别选取装置平稳运行和装置不正常时的柴油样.用3‰除胶剂进行试验. 结果表明.使用除胶剂处理柴油.对柴油的质量有一定的要求.过差的柴油不能达到很好的精制效果.26精成本测算除胶剂价格以2800元/吨计.添加量为3‰,则催柴精制原料成本为84 元/吨3.结论1自制除胶剂能脱除柴油胶质.改善色度降低氧化总不溶物含量.延长储存时间.2自制除胶剂使用工艺条件为加剂量3%0,40.C搅拌1rain沉降1rain后除胶水洗.3自制除胶剂对催化柴油的质量有一定的要求,不能精制质量较差的柴油. r篓荤囊叶百,'。
催化柴油生产方案

催化车间柴油生产方案一、多产柴油生产方案催化裂化反应属于平行顺序反应,柴油属于中间产物。
其收率受反应深度影响较大,因此增产柴油的措施首先从降低反应深度入手。
在多产柴油时,要采用较低的反应深度,较低的反应温度,大回炼比,活性稍低的平衡剂,选用多产柴油的催化剂,分馏岗适当降低塔顶温度,降低汽油的干点,提高柴油馏出和二中馏出温度,拓宽柴油的馏程,多产柴油。
A、反应岗位调整措施:1、降低提升管出口温度,减少二次裂化的发生,提高中间馏分的收率。
(单程转化率将会降低)2、加大终止剂流量,使用终止剂下喷嘴。
缩短提升管反应时间,减少中间馏分再次发生裂化反应。
3、提高回炼比,其实也是为降低反应深度。
缺陷:①限制装置的处理量,降低装置的掺渣量。
②增大再生器烧焦负荷,调整不及时导致碳堆。
如果一味调整主风量,导致电耗增加。
最好是提高再生器压力,来改善烧焦效果。
4、控制系统催化剂活性,较低的催化剂活性,可降低反应深度。
这样必须增大剂油比,改善反应的选择性,降低焦炭产率,从而提高柴油的收率。
以上调整有负面影响降低单程转化率,导致回炼比增加,增加装置的能耗。
B、分馏岗位调整措施:二、(在保证柴油闪点质量合格情况下,拓宽柴油流程。
)1、降低分馏塔顶温,降低汽油干点。
目的使汽油的“尾部”组分进入柴油,同时将重汽油分离出来,同时提高汽油的辛烷值。
在调整过程中,适当加大分馏塔冷回流量。
好处有提高分馏塔汽油组分分压(注意沉降器压力,防止反应器憋压,调整气压机入口压力),可以防止顶偱温度过低,导致顶偱泵抽空。
同时防止分馏塔顶部结盐。
(注:保证分馏塔顶偱抽出温度不低于130℃,适当降低顶偱量)2、提高柴油抽出温度和中段抽出温度。
目的减少回炼油中的柴油组分,适当降低中段流量,中段可多走冷路来保证柴油抽出温度。
3、优化柴油汽提蒸汽,在保证最低的柴油闪点要求下。
最大限度的降低柴油初馏点。
石油化工重油催化裂化工艺技术

石油化工重油催化裂化工艺技术石油化工重油催化裂化工艺技术是一种将重油转化为轻质油和化学品的过程。
该过程主要利用催化剂的作用,在高温高压条件下,使重油的大分子裂解成小分子,同时发生异构化、芳构化和氢转移等反应,以获得更多的轻质油和化学品。
催化剂的选择:催化剂是该技术的核心,其选择对产品的质量和产量有着至关重要的影响。
目前,常用的催化剂包括酸性催化剂、金属催化剂和金属氧化物催化剂等。
工艺条件的控制:工艺条件包括反应温度、压力、空速等,这些因素对产品的质量和产量都有着极大的影响。
因此,精确控制这些工艺条件是重油催化裂化工艺技术成功应用的关键。
产品的质量和性能:重油催化裂化工艺技术生产的产品具有高辛烷值、低硫含量等特点,被广泛应用于汽油、柴油、航空煤油等领域。
在应用方面,石油化工重油催化裂化工艺技术适用于不同类型重油,如减压渣油、催化裂化残渣油、脱沥青油等。
对于不同工业应用,可根据实际需求选择合适的工艺技术。
例如,对于生产高质量汽油和柴油的需求,可以选择更为精细的催化剂和严格的工艺条件;对于生产高附加值化学品的需求,则可以通过调整工艺流程和催化剂类型来增加化学品产量。
虽然石油化工重油催化裂化工艺技术在提高石油利用率、生产高质量石油化工产品方面具有重要作用,但也面临着一些挑战。
催化剂的活性、选择性和稳定性是该技术的关键,而目前催化剂的研究与开发尚存在诸多困难。
重油催化裂化过程中产生的固体废物和废气等对环境造成了严重影响,亟需解决。
由于重油资源的有限性,需要进一步探索和研发更为高效、环保的石油化工技术,以适应未来可持续发展的需要。
石油化工重油催化裂化工艺技术在石油化工产业中具有重要地位。
随着经济的发展和科技的进步,该技术将不断完善和优化,提高石油利用率和生产效率,同时注重环保和可持续发展。
未来,需要加强催化剂的研发与优化,减少环境污染,提高技术的绿色性和可持续性。
应积极探索新的石油化工技术,以应对全球能源危机和环境问题的挑战。
燕山石化 催化裂化 炼油三厂 工艺简介

1.概述说明:1.1.装置的地位和作用炼油厂重油催化裂化是在催化剂的作用下将重质油转化为汽油、柴油及液化气等产品的过程,是主要的加工工艺之一。
随着社会的不断发展和进步,能源危机日益成为人们注目的焦点,而催化裂化作为重油深度加工装置,日益显示出其重要作用,我国通过催化裂化工艺生产的汽油约占全国商品汽油的70%,柴油占全国总量的30%,液化气占炼油厂总量的90%以上。
根据中石化总公司’’八五科技进步规则”的精神和炼厂的”九五规划”,为充分利用石油资源,提高二次加工能力,改善产品结构,增加全厂轻质油收率,减少重油产品特拟建此套(200万吨/年)重油催化裂化装置。
本装置是全国最大的重油催化裂化装置之一。
1.2.装置的主要原料、产品和用途1.2.1.本装置所需主要原料为蒸馏装置的常三、常四、减二、减三、减四、减五线、减压渣油以及酮苯蜡膏、糠醛抽余油、和丙烷脱沥青油等。
1.2.2.本装置主要产品为:汽油,柴油,液化气,干气和重油(油浆)。
1.2.2.1.汽油是本装置生产的主要产品之一,其设计牌号为9l号,收率为47.2%。
汽油常用于汽油燃动机,是比较重要的一种动力能源,主要用于轻型汽车,活塞式发动机的飞机,快艇和小型发电机等。
1.2.2.2.柴油也是本装置的主要目标产品,其设计牌号为一10号和0号,收率通常为24.28%,根据季节变化和市场对柴油的使用要求,我们可以通过改变操作条件来生产所需要的目标产品。
柴油的用途相当广泛,主要用于大马力的运输机械,现已广泛用于载重汽车,拖拉机,曳引机,机车,船舶及各种农业,矿山,车用机械作为动力设备,其功率从几十马力到四万马力左右。
1.2.2.3.液化气也是本装置的重要产品,其设计收率为10.736%。
它通常用作民用燃料,但随着科学技术的日新月异,液化气的用途也有了新的变化,比如:由于世界环卫组织宣布氟利昂严重影响生态环境,造成臭氧层破坏,故研究氟利昂的替代产品显得尤其重要,而液化气正是理想的原材料之一。
石油化工催化裂化技术的工艺优化分析

石油化工催化裂化技术的工艺优化分析发布时间:2023-03-03T08:56:47.868Z 来源:《科技新时代》2022年第20期作者:王中亮杨立志[导读] “三油并轨”政策的实施和车用柴油标准的升级将进一步减少污染物的排放王中亮杨立志中国石油哈尔滨石化公司第二联合车间 150056摘要:“三油并轨”政策的实施和车用柴油标准的升级将进一步减少污染物的排放,保护环境,并推动发动机企业技术进步和炼油企业转型升级。
例如,车用柴油国Ⅵ质量标准要求大幅降低柴油的硫含量和多环芳烃含量,这将使催化裂化柴油(LCO)占比较高的炼油企业面临巨大技术经济挑战。
这是因为LCO的总芳烃质量分数为50%~70%,且双环芳烃占比很大,为总芳烃的40%~60%;同时LCO的硫、氮等杂质含量高、十六烷值低,难以直接作为柴油馏分,必须进一步深入加工才能满足国Ⅵ柴油质量标准的要求。
LCO深加工技术主要有加氢精制、加氢改质等技术。
通过加氢,可以脱除LCO中的硫和氮元素,但LCO加氢过程需要高苛刻度的工况条件,氢耗高、操作成本高、经济效益差。
同时,随着消费柴汽比的不断下降,炼油企业间的竞争不断加剧,为LCO加工路线的选择带来巨大挑战。
因此,探寻最优LCO加工路径,实现低成本提升LCO经济价值成为研究热点。
关键词:催化裂化;低辛烷值汽油;辛烷值引言我国FCC汽油为商品汽油的主要组分,其在商品汽油中的比例达70%以上,无论目前还是可预见的未来,FCC汽油在炼油厂中的重要地位不容置疑。
FCC汽油性质明显优于热裂化汽油,而且,稳定性要比热裂化汽油高得多,各种烃类在FCC汽油中大致分为正构烷烃约5%,异构烷烃在25%~33%之间,环烷烃在6%~12%之间,烯烃在33%~46之间,芳烃在16%~22%之间。
高辛烷值汽油能够提高发动机的功率和热效率,提高汽油辛烷值已经成为各汽油生产单位的主要努力方向。
粗汽油作为终止剂在催化裂化装置上进行工业应用已经取得了不错的效果,能够抑制氢转移二次反应和减少热裂化反应,提高重油催化裂化的轻质油和液化气收率,降低干气和焦炭产率。
石油炼化常用的七种工艺流程

石油炼化七种工艺流程从原油到石油要经过多种工艺流程,不同的工艺流程会将同样的原料生产出不同的产品。
从原油到石油的基本途径一般为:①将原油先按不同产品的沸点要求,分割成不同的直馏馏分油,然后按照产品的质量标准要求,除去这些馏分油中的非理想组分;②通过化学反应转化,生成所需要的组分,进而得到一系列合格的石油产品。
石油炼化常用的工艺流程为常减压蒸馏、催化裂化、延迟焦化、加氢裂化、溶剂脱沥青、加氢精制、催化重整.(一)常减压蒸馏1。
原料:原油等.2。
产品:2.石脑油、粗柴油(瓦斯油)、渣油、沥青、减一线。
3。
基本概念:常减压蒸馏是常压蒸馏和减压蒸馏的合称,基本属物理过程:原料油在蒸馏塔里按蒸发能力分成沸点范围不同的油品(称为馏分),这些油有的经调合、加添加剂后以产品形式出厂,相当大的部分是后续加工装置的原料。
常减压蒸馏是炼油厂石油加工的第一道工序,称为原油的一次加工,包括三个工序:a。
原油的脱盐、脱水;b.常压蒸馏;c.减压蒸馏。
4。
生产工艺:原油一般是带有盐份和水,能导致设备的腐蚀,因此原油在进入常减压之前首先进行脱盐脱水预处理,通常是加入破乳剂和水.原油经过流量计、换热部分、沏馏塔形成两部分,一部分形成塔顶油,经过冷却器、流量计,最后进入罐区,这一部分是化工轻油(即所谓的石脑油);一部分形成塔底油,再经过换热部分,进入常压炉、常压塔,形成三部分,一部分柴油,一部分蜡油,一部分塔底油;剩余的塔底油在经过减压炉,减压塔,进一步加工,生成减一线、蜡油、渣油和沥青。
各自的收率:石脑油(轻汽油或化工轻油)占1%左右,柴油占20%左右,蜡油占30%左右,渣油和沥青约占42%左右,减一线约占5%左右。
常减压工序是不生产汽油产品的,其中蜡油和渣油进入催化裂化环节,生产汽油、柴油、煤油等成品油;石脑油直接出售由其他小企业生产溶剂油或者进入下一步的深加工,一般是催化重整生产溶剂油或提取萃类化合物;减一线可以直接进行调剂润滑油。
催化裂化油浆进焦化掺炼流向优化及经济效益分析
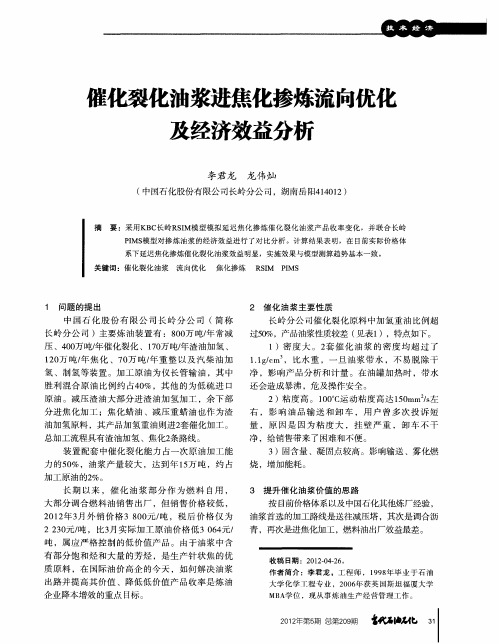
系下延迟焦化掺炼催化裂化油浆效益 明显 ,实施效果与模型测算趋势基本一致 。 关键词 :催化裂化油浆 流 向优 化 焦化掺炼 R I SM PMS I
1 问题 的提 出
2 催 化油 浆主 要性质
中 国 石 化 股 份 有 限 公 司 长 岭 分 公 司 ( 称 简 长 岭分 公 司 )主 要炼 油 装 置 有 :8 0 吨/ 常 减 0万 年
催化裂化油浆进焦化掺炼流 向优化
李君龙
龙伟灿
( 国石 化股份 有 限公 司长岭分 公 司 ,湖 南岳  ̄44 1 中 102)
摘 要 :采 用K 长 岭RSM模型模拟 延迟焦化 掺炼催化 裂化油浆 产品收率变 化 ,并联 合长岭 BC I
PMS 型 对 掺 炼 油浆 的 经 济 效 益 进 行 了对 比分 析 。计 算 结 果 表 明 , 在 目前 实 际 价 格 体 I 模
密 度 ( 0 ) (/m 2℃ gc )
运动粘度 (0 。 10C) ( n/) mr2 s
残 炭 ,% 凝 固点 , o c 元 素 组 成 ,w%
C H
146 2.
2 .1 79 4 6
8. 19
2 .1 72
产 品 收率 变 化 。根 据 模 型计 算 ,得 到 以下 结 果 ,
压 、4 0 吨/ 0万 年催 化 裂化 、1 0 吨/ 渣油加 氢 、 7万 年
长岭 分 公 司催 化 裂 化 原料 中加氢 重 油 比例超 过5%,产品油浆性质较差 ( 0 见表 1 ),特点如下 。
1)密 度 大 。2 催 化 油 浆 的 密 度 均 超 过 了 套 11/m .ge ,比水 重 ,一 旦 油 浆 带 水 ,不 易脱 除干 净 ,影 响产 品分 析 和计 量 。在 油罐 加 热 时 ,带水 还会 造成 暴沸 ,危及 操作 安全 。 2)粘度 高 。 10C 动 粘 度 高达 10 m/左 0 。运 5 r s a 右 ,影2 .4 26 .3 1.8 22 3 .1 4O 1.O 28 49 .1 20 .7 2. 70 6
柴油精制工艺流程设计与设备选型

柴油精制工艺流程设计与设备选型精制柴油是一种重要的石油产品,在现代社会的交通运输和工业领域具有广泛应用。
为了生产高质量的柴油,必须设计合理的工艺流程并选择适用的设备。
本文将针对柴油精制的工艺流程设计和设备选型进行探讨。
一、前处理阶段在柴油精制的工艺流程中,前处理阶段是必不可少的一步。
前处理的目的是去除原油中的杂质和硫化物等不纯物质,以便在后续的精制过程中得到更高品质的柴油产品。
1. 原油加热通过加热原油可以使其黏度降低,有利于后续处理工艺的进行。
加热温度应根据原油品质和工艺要求来确定。
2. 分离原油经过加热后,通过分离器进行初步分离。
在该阶段,可以去除油中的水分、机械杂质和一些轻质烃类。
3. 硫化物去除硫化物是柴油中的一个主要污染物,会降低柴油的品质并产生有害物质。
采用加氢脱硫工艺可以有效降低硫化物的含量。
二、精制阶段在前处理后,原油进入精制阶段进行深度加工,以提高柴油的质量和性能。
1. 催化裂化催化裂化是一种常用的柴油精制工艺,通过将重质石油馏分转化为轻质烃类,提高柴油的脱硫、脱氮、脱蜡性能。
2. 加氢处理通过加氢处理可以降低柴油中的芳烃和不饱和烃含量,提高柴油的稳定性和抗氧化性能。
3. 深度脱硫通过深度脱硫工艺可以将柴油中的硫化物含量进一步降低,使柴油达到国家标准。
4. 加油剂添加在柴油精制的最后阶段,可以通过加油剂的添加来改善柴油的性能,如增加助燃剂、增加润滑剂等。
三、设备选型在柴油精制工艺中,设备的选型是关键的一环。
合理选择设备不仅可以提高生产效率,还能降低能耗和运行成本。
1. 加热设备对于原油的加热,在工艺流程中可以选择采用炉膛加热、换热器加热等方式,具体的设备选型应结合生产规模和工艺要求来确定。
2. 分离设备分离器在前处理阶段起着重要作用,常用的设备有旋流分离器、离心分离器等。
根据处理量和分离效果,选择合适的设备进行分离。
3. 催化裂化设备催化裂化是柴油精制过程中的重要环节,常用的设备有流化催化裂化装置、固定床催化裂化装置等。
催化裂化工艺流程及主要设备课件

加热炉通常采用燃油、燃气或电加热方式,根据不同的 工艺需求选择合适的加热方式。
加热炉的操作需根据工艺要求控制温度、压力和流量等 参数,以确保原料油和催化剂得到均匀加热。
分馏塔
分馏塔是催化裂化工艺流程中 用于分离不同沸点的烃类的设 备。
反应器内部通常装有高效催化剂,以 促进原料油裂化成小分子烃类,同时 降低生焦率。
反应器通常采用固定床、流化床或移 动床的情势,根据不同的原料和产品 需求选择合适的反应器类型。
反应器的设计需考虑温度、压力、原 料油性质和流量等工艺参数,以确保 较高的转化率和选择性。
再生器
再生器是催化裂化工艺流程中 用于烧焦和再生催化剂的设备
气体净化
分离出的气体中可能含有 硫化氢、一氧化碳等杂质 ,需要进行脱硫、脱碳等 处理,以满足环保要求。
液体产品精制
经过油气分离后的液体产 品需要进行精制,如加氢 处理、脱蜡等,以提高产 品的质量和稳定性。
03
主要设备介绍
反应器
反应器是催化裂化工艺流程中的核心 设备,用于实现原料油在催化剂的作 用下的裂化反应。
活性和寿命。
预热和注水
预处理过程中,原料油需要经过 加热和注水处理,以提高油品的 流动性和降低粘度,有利于油品
的快速加热和反应。
原料的雾化
为了使原料油与催化剂充分接触 和混合,需要对原料油进行雾化 处理,使其形成微小的液滴,增 加油滴在反应器内的停留时间。
反应过程
反应温度与压力
催化裂化反应需要在一定的温度和压力下进行,通常温度在450550℃之间,压力在0.5-1.0 MPa之间。
催化裂化工艺流程及主要设备课 件
重油催化裂化装置增产柴油的方案分析

率。 但是 , 反应时间在实际装置中是不可以任意调节的, 它主要取决于提升管的
内径大 小和进 料 喷嘴与 提升 管 出 口之 间的长 度。 在装置 负荷 较低 时 , 增 大提 升 管 蒸汽量 或 干气量 来维 持较短 的反 应时 间 。 另外 , 可 以在提升 管 末端采 用终 止
剂 技术 。
2 . 1 . 所 用原 料性 质的 影响
催化 裂化 主反 应是 平行顺序 反应 , 馏分油和 渣油 的大 分子与 催化剂接触 时 首先 裂化 为柴 油等 中间馏分 , 随着反 应 时间 的延长 , 中间馏分 将进一 步裂 化为 汽油 和气 体 。 因此 , 适 当缩短 反 应时 间可 以 防止柴 油 的再 次裂化 , 提高 柴油 产
不 可 以提高 幅度 过大 。 应缓 慢提 升残 渣 比和 回炼 比 , 同时密切 注意 再生器 烧 焦 情况, 谨 防超 温 。
2 . 2 . 反 应 温度 的影 响
采取 回炼操作 有 利于柴 油收率 的增 加 。 增加 回炼 比, 提升 管 内新鲜进 料 的
分压 和停 留时间相对 降 低 , 从而 降低 了新鲜原 料 的裂化苛 刻度 和转 化率 , 柴 油 收率 增加 。 但是 , 采用 回炼和 大回炼操 作会导 致焦炭产 率增 加 , 将 影响到装 置处
理量 , 因此 回炼 比的 选择 应适 当 。
本装置 的 回炼 介质 主要 是回炼 油 , 提高 回炼 比主要参 考 回炼 油 的密度 , 如 密度 过大 , 则 对增 产 柴油 的效 果不大 。
2 . 5 . 剂 油 比的影响
反 应温度是 催化裂 化装置 的一个重 要操作参 数和主 要调节手 段 , 反 应温度 的高低 主要 取决 于原料 油 的性质 、 装 置结 构形 式 、 ቤተ መጻሕፍቲ ባይዱ作情 况 以及产 品分布 的要 求。 因此 , 反 应 温度 的选 择应 根据 装 置的 实 际生产 情 况 , 综合 考虑 各 种 因素确
- 1、下载文档前请自行甄别文档内容的完整性,平台不提供额外的编辑、内容补充、找答案等附加服务。
- 2、"仅部分预览"的文档,不可在线预览部分如存在完整性等问题,可反馈申请退款(可完整预览的文档不适用该条件!)。
- 3、如文档侵犯您的权益,请联系客服反馈,我们会尽快为您处理(人工客服工作时间:9:00-18:30)。
催化裂化柴油加工路线选择及优化高磊【摘要】The comparisons of the processing results of LCO hydrofining,hydrocracking of VGO mixed with LCO,hydrotreating VGO mixed with LCO and LTAG in SINOPEC Wuhan Company were introduced.The results show that LCO hydrofining can only achieve desulfurization,and the hydrocracking of VGO blended with LCO is favorable for the production of petrochemicals and the improvement of diesel cetane number,while LTAG process can produce much more gasoline than that of the hydrotreating VGO mixed with LCO process and is the most economical processing route,but needs severer hydrotreating operation.It is recognized that the LTAG process combined with optimal LCO hydrotreating process is the primary economical choice for LCO processing in Wuhan Company.%介绍了中国石化武汉分公司催化裂化柴油(LCO)的加工路线,对LCO进柴油加氢装置精制、进加氢裂化装置掺炼、与蜡油加氢混炼及LTAG工艺进行对比.结果表明:LCO进柴油加氢装置精制仅能实现柴油的脱硫精制,进加氢裂化装置掺炼有利于化工料的增产及柴油十六烷值的提升;LTAG 工艺增产汽油的效果好于LCO与蜡油加氢混炼工艺,也是经济效益最优的工艺路线,但加氢深度要求较高.因此,优化加氢效果,投用LTAG工艺是武汉分公司催化裂化柴油加工首选的经济性途径.【期刊名称】《石油炼制与化工》【年(卷),期】2017(048)007【总页数】6页(P64-69)【关键词】催化裂化柴油;LTAG;蜡油加氢混炼工艺;加氢裂化掺炼【作者】高磊【作者单位】中国石化武汉分公司,武汉 430082【正文语种】中文催化裂化技术在我国普遍应用,导致炼油厂柴油池中催化裂化柴油的比例达25%以上[1]。
催化裂化柴油(简称LCO)的特点是密度大,硫、氮等杂质含量高,芳烃含量高,十六烷值低,不适合作为车用柴油调合组分。
由于以汽油为燃料的私家车越来越多,且高辛烷值汽油需求量上升,以及经济减缓导致柴油结构性过剩,需要炼油厂降低柴汽比。
在以上背景下,许多炼油企业都为催化裂化柴油寻找出路。
中国石化武汉分公司(简称武汉分公司)根据市场需求,灵活采用各种加工路线消化LCO,以提高柴油品质及增产汽油。
1.1 柴油加氢精制工艺柴油加氢精制主要适用于直馏柴油十六烷值较高且催化裂化柴油占比较小的企业。
一般将LCO直接与其它柴油组分混合加氢,使柴油硫含量满足环保要求,同时可使十六烷值提高2~5 个单位,精制柴油收率可达98%以上,氢耗一般在1%(质量分数)以下[2]。
1.2 加氢裂化掺炼催化裂化柴油工艺加氢裂化技术具有产品质量好、产品方案灵活的特点,劣质的LCO进入高压的加氢裂化装置后,通过芳烃饱和、环烷烃裂化,可以实现劣质柴油的优质化,同时增产石脑油、喷气燃料等。
但加氢裂化装置的反应器温升、冷氢裕量、尾油芳烃指数(BMCI值)、喷气燃料烟点、二次原料的最大掺炼比例等都是LCO掺炼的限制因素[3-4]。
通常加氢裂化装置掺炼LCO占原料的比例在10%以下,选用加氢饱和与开环能力较强的催化剂确保喷气燃料质量,氢分压大于13 MPa。
若需生产用作蒸汽裂解制乙烯原料的尾油,还要严格控制LCO的95%馏出温度在320~350 ℃之间。
1.3 LCO与蜡油加氢混炼技术LCO与蜡油加氢混炼技术主要是将LCO与VGO一起送入加氢单元进行加氢处理,然后精制柴油与加氢重油混合,再送至催化裂化单元与原料混合进入提升管发生开环裂化反应,进而实现柴油转化为高辛烷值汽油组分或轻芳烃。
研究表明,在氢分压5.5 MPa、体积空速2.0 h-1的条件下,萘系的双环芳烃转化为四氢萘的比例可达到50%左右,随着压力的提高和空速的进一步降低,十氢萘的产率将逐步上升。
四氢萘和十氢萘的催化裂化反应产物分布明显不同,四氢萘更容易发生氢转移反应生成萘,十氢萘和八氢菲较多发生开环反应,同时发生氢转移反应。
加氢柴油和蜡油混炼容易强化氢转移反应,氢转移反应造成部分柴油组分(萘、菲)在催化裂化和加氢装置之间循环,还有部分缩合生焦[5]。
1.4 LTAG工艺LTAG(LCO To Aromatics and Gasoline)是利用选择性加氢饱和单元和选择性催化裂化单元优化组合,将LCO馏分中的多环芳烃先选择性加氢饱和成单环芳烃再进行选择性催化裂化,实现最大化生产高辛烷值汽油或C6~C8芳烃的技术。
工业试验结果表明,加氢后柴油与催化裂化原料分开进提升管独立喷嘴,并且加氢柴油进料位置在原料喷嘴之下,有利于降低氢转移反应,改善催化裂化的产品分布[6]。
LCO加氢过程,主要是LCO中芳烃的选择性加氢饱和。
以甲基乙基萘为厚料,加氢过程生成四氢萘型(目标产物)时,氢耗为2.12%,相对较低。
生成十氢萘型(非目标产物)时,氢耗为5.12%,相对较高,产物辛烷值低。
加氢过程的两个关键控制指标:加氢后柴油密度需低于910 kgm3,多环芳烃质量分数低于15%。
LTAG 技术中的反应途径如图1所示,在加氢后LCO催化裂化过程中,四氢萘类催化裂化与不希望发生的氢转移反应之间存在竞争,但氢转移反应能垒低,更容易发生,所以高反应温度、高剂油比、短反应时间有利于四氢萘型单环芳烃发生裂化反应,而抑制氢转移反应发生[7]。
1.5 炼油厂其它工艺柴油加氢改质工艺是在脱除硫、氮等杂质的基础上,经过芳烃加氢饱和、环烷烃选择性开环等过程,进而大幅提高十六烷值。
该类技术十六烷值提高幅度较大,一般在8~25个单位[8]。
典型技术如:催化裂化柴油深度加氢处理(RICH)、高选择性灵活加氢改质(MHUG)等劣质柴油中压加氢改质技术。
加氢转化工艺是以催化裂化柴油为原料,在脱除硫、氮等杂质的基础上,控制芳烃的适度加氢饱和,通过四氢萘等单环芳烃的异构、开环,以及烷基苯等单环芳烃的烷基侧链断裂,将单环、双环以上芳烃转化为碳数小于10的高辛烷值汽油或轻芳烃,同时大幅提高未转化柴油组分的十六烷值[9-10]。
典型技术如:采用催化裂化柴油加氢裂化生产高辛烷值汽油或BTX的RLG技术、中国石化抚顺石油化工研究院开发的FD2G技术、UOP公司开发的LCO UnicrackingTM技术、LCO-X组合工艺等。
武汉分公司LCO加工路线如图2所示,实线是实际运行加工路线,虚线是可选加工路线。
2.1 武汉分公司LCO加工路线现状分析表观收率是为了更直观地显示催化裂化柴油的转化效果,其计算方法如下:由表2可以看出,加氢LCO有48.04%未实现转化,36.94%生成汽油。
当柴油出厂计划富裕时,蜡油加氢开分馏炉,抽出15 th柴油进普通柴油,其余并入精制蜡油作为催化裂化原料。
对于该组合而言,建议LCO掺炼比例小于30%,LCO部分进蜡油加氢,蜡油加氢出部分柴油,不建议柴油全回炼,否则氢转移反应过强,生焦增加,同时异丁烯和丙烯减产。
武汉分公司曾尝试将蜡油加氢装置氢分压提高至10.0 MPa,反应温度由335 ℃提高至340 ℃,精制柴油密度由910 kgm3降低至895 kgm3,十六烷值由29提高至31,柴油产品质量得到进一步改善,但补充氢气量增大600 m3h(标准状态),瓦斯耗量增大100 m3h(标准状态)。
2.2 武汉分公司LTAG工艺试运行分析及结果武汉分公司LTAG工艺的基本运行模式有两个:一个是2号(或1号)催化裂化装置LCO全部进蜡油加氢装置处理,加氢后柴油返回2号(或1号)催化裂化单独进提升管,LCO处理能力200 kta;另一个是两套装置的LCO全部去1号加氢装置,加氢后柴油分别返回两套催化裂化装置单独进提升管,LCO处理能力400 kta。
武汉分公司2016年8月对两套催化裂化装置与1号加氢装置联合的LTAG工艺进行了试运行及标定,2016年9月对2号催化裂化装置与蜡油加氢处理装置联合的LTAG工艺进行了试运行及标定。
对于蜡油加氢处理装置而言,外送LTAG柴油保持20 th,LCO进入蜡油加氢装置时,LCO的烃族组成中多环芳烃质量分数为68.8%,总芳烃质量分数为88.8%。
经蜡油加氢装置处理后,加氢LCO密度(20 ℃)为902 kgm3,多环芳烃质量分数为18.9%(略高于设计值15%),总芳烃质量分数为68.4%。
装置总氢气耗量为1.21%,比设计值高0.03%。
一是由于催化裂化柴油加氢氢耗较大,二是为了保证加氢的深度,装置维持足够的氢分压,循环氢的纯度提高到88%。
投用2号催化裂化与1号加氢装置联合的LTAG工艺后,汽油辛烷值由投用前的91.6提高至92.3,汽油收率56.42%,低于设计值(57.18%)。
随着掺炼,LCO导致分馏塔冷却负荷不够,柴油抽出温度为229 ℃,柴油干点偏高(95%点馏出温度370 ℃),且顶回流冷却负荷不足,主风量不足。
每回炼1 th加氢LCO,影响2号催化裂化新鲜进料量0.85 th。
投用两套催化裂化装置与1号加氢装置随着合的LTAG工艺后,汽油产量均有上升,汽油辛烷值提高明显。
但由于1号加氢装置并未达到LTAG工艺最优选的加氢深度,加氢LCO密度较高,多环芳烃质量分数较高。
多环芳烃进入催化裂化后,在提升管底部高温大剂油比的反应条件下,多环芳烃裂解反应与缩合反应都有发生,且LTAG工艺的优化反应——四氢萘开环裂化生成单环芳烃的比例低于预期值,导致汽油产率都远低于LTAG工艺设计值。
投用2号催化裂化与蜡油加氢处理装置联合的LTAG工艺后,由于加氢深度提高,稳定汽油产量较投用1号加氢LTAG工艺提高了1.91 th,汽油收率与1号加氢投用LTAG工艺相近,约为56%,仍低于设计值。
同时2号催化裂化装置通过调节塔底油浆返回量和温度、一中换热器投用等分馏塔优化提高装置处理量,降低了回炼LCO对新鲜进料量的影响,每回炼1 th加氢LCO,影响2号催化裂化新鲜进料量0.78 th。