催化重柴油加氢后的催化裂解性能
催化裂化技术

催化裂化原料 催化裂化原料分为馏分油和渣油两大类。
1、Distillate Oil(馏分油)
(1)直馏重馏分油(350~500℃)
大多数直馏重馏分含芳烃较少,容易裂化,轻油收率较高, 是理想的催化裂化原料。
(2)热加工产物:焦化蜡油、减粘裂化馏出油等。
其中烯烃、芳烃含量较多,转化率低、生焦率高。不单独
• 5.正碳离子将H+ 还给催化剂,本身变成烯烃,反应中止。
催化裂化催化剂
一、催化裂化剂的种类、组成和结构
工业上使用的裂化催化剂归纳起来有三大类:
1、天然白土催化剂
催化裂化装置最初使用的经处理的天然白土,其主要活性 组分是硅酸铝。
2、无定型硅酸铝催化剂
天然白土被人工合成硅酸铝所取代。
• 无定型硅酸铝催化剂 • 硅酸铝的主要成分是氧化硅和氧化铝,合成硅酸铝依铝含量的不同又分 为低铝(含Al2O310%~13%)和高铝(含Al2O3约25%)二种。其催化剂 按颗粒大小又分为小球状(直径在3~6mm)和微球状(直径在40~80)。 • Al2O3、SiO2及少量水分是必要的活性组分,而其它组分是在催化剂的制 备过程中残留下来的极少量的杂质。合成硅酸铝是由Na2SiO3和Al2(SO4)3 溶液按一定的比例配合而成凝胶,再经水洗、过滤、成型、干燥、活化 而制成的。硅酸铝催化剂的表面具有酸性,并形成许多酸性中心,催化 剂的活性就来源于这些酸性中心,即催化剂的活性中心。
在全世界催化裂化装置的总加工能力中,提升管催化
裂化已占绝大多数。
流程图画面
催化裂化化学反应原理
• 一、单体烃催化裂化的化学反应 • (一)烷烃 • 烷烃主要发生分解反应,分解成较小分子的烷烃和烯烃, 烷烃分解时多从中间的C—C键处断裂,分子越大越容易 断裂
催化裂化原理
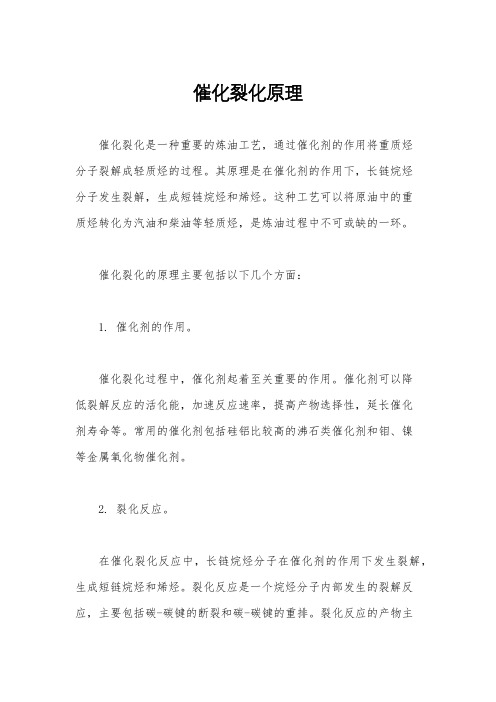
催化裂化原理催化裂化是一种重要的炼油工艺,通过催化剂的作用将重质烃分子裂解成轻质烃的过程。
其原理是在催化剂的作用下,长链烷烃分子发生裂解,生成短链烷烃和烯烃。
这种工艺可以将原油中的重质烃转化为汽油和柴油等轻质烃,是炼油过程中不可或缺的一环。
催化裂化的原理主要包括以下几个方面:1. 催化剂的作用。
催化裂化过程中,催化剂起着至关重要的作用。
催化剂可以降低裂解反应的活化能,加速反应速率,提高产物选择性,延长催化剂寿命等。
常用的催化剂包括硅铝比较高的沸石类催化剂和钼、镍等金属氧化物催化剂。
2. 裂化反应。
在催化裂化反应中,长链烷烃分子在催化剂的作用下发生裂解,生成短链烷烃和烯烃。
裂化反应是一个烷烃分子内部发生的裂解反应,主要包括碳-碳键的断裂和碳-碳键的重排。
裂化反应的产物主要是烷烃、烯烃和芳烃。
3. 反应条件。
催化裂化的反应条件包括温度、压力、催化剂种类和用量等。
通常情况下,催化裂化反应需要在较高的温度下进行,以提高反应速率和产物选择性。
此外,适当的压力和催化剂的选择也对裂化反应的效果有重要影响。
4. 产物分离。
催化裂化反应产生的混合气体需要进行分离和纯化,以得到所需的轻质烃产品。
通常采用的分离技术包括精馏、萃取、吸附等,以获得高纯度的汽油和柴油产品。
5. 催化剂再生。
在催化裂化过程中,催化剂会因受到焦炭和烃类物质的污染而失活,需要进行再生。
催化剂再生是通过热氧化或化学氧化等方法将焦炭烧除,恢复催化剂的活性和选择性,延长催化剂的使用寿命。
总的来说,催化裂化是一种重要的炼油工艺,通过催化剂的作用将重质烃分子裂解成轻质烃,可以提高原油的利用率,生产出更多的汽油和柴油产品。
催化裂化的原理涉及催化剂的作用、裂化反应、反应条件、产物分离和催化剂再生等多个方面,需要综合考虑和控制,以实现高效、稳定的生产过程。
生物柴油的催化裂解技术
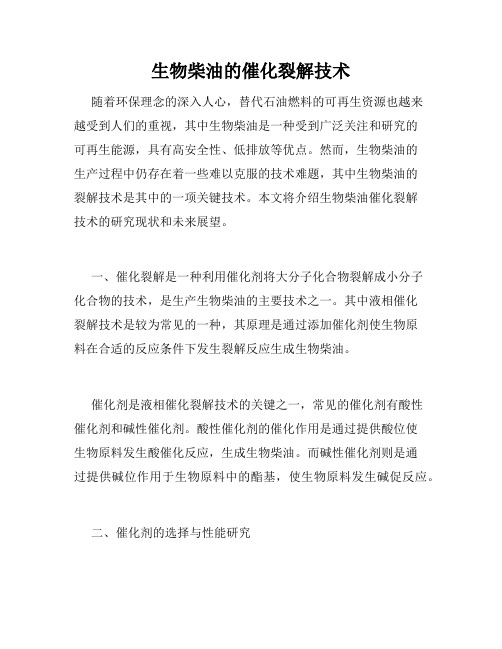
生物柴油的催化裂解技术随着环保理念的深入人心,替代石油燃料的可再生资源也越来越受到人们的重视,其中生物柴油是一种受到广泛关注和研究的可再生能源,具有高安全性、低排放等优点。
然而,生物柴油的生产过程中仍存在着一些难以克服的技术难题,其中生物柴油的裂解技术是其中的一项关键技术。
本文将介绍生物柴油催化裂解技术的研究现状和未来展望。
一、催化裂解是一种利用催化剂将大分子化合物裂解成小分子化合物的技术,是生产生物柴油的主要技术之一。
其中液相催化裂解技术是较为常见的一种,其原理是通过添加催化剂使生物原料在合适的反应条件下发生裂解反应生成生物柴油。
催化剂是液相催化裂解技术的关键之一,常见的催化剂有酸性催化剂和碱性催化剂。
酸性催化剂的催化作用是通过提供酸位使生物原料发生酸催化反应,生成生物柴油。
而碱性催化剂则是通过提供碱位作用于生物原料中的酯基,使生物原料发生碱促反应。
二、催化剂的选择与性能研究不同的催化剂对生物原料的裂解反应产生了不同的影响。
在生物柴油的液相催化裂解中,酸性催化剂更为常见。
研究表明,使用大分子酸性固体催化剂对生物原料进行裂解反应,其产率和选择性会得到较好的控制。
同时,固体酸催化剂具有开发过程简便、操作方便等优点,因此被广泛应用于生物柴油液相催化裂解过程中。
此外,固体酸催化剂的催化效率还与其酸分布特征、酸强度、孔径大小等因素密切相关。
研究表明,催化剂的孔径大小可以影响反应物在催化剂内的分布,从而影响裂解反应的产率和选择性。
在选择催化剂时,应根据反应条件的需要,综合考虑催化剂的比表面积、孔径大小、酸性质等多方面性能。
三、催化裂解技术的影响因素催化裂解技术还受许多其他因素的影响,其中反应温度、反应时间和反应物浓度是导致生物柴油产率和品质变化的重要因素。
1.反应温度反应温度是影响液相催化裂解的重要因素,对产率和品质的影响较大。
在过高的反应温度下,易导致反应物分解或聚合发生,从而影响生物柴油的产率。
另外,过低的反应温度则可能导致反应物未能充分溶解,从而影响反应的进程。
催化裂解原理与机理

催化裂解催化裂解,是在催化剂存在的条件下,对石油烃类进行高温裂解来生产乙烯、丙烯、丁烯等低碳烯烃,并同时兼产轻质芳烃的过程。
由于催化剂的存在,催化裂解可以降低反应温度,增加低碳烯烃产率和轻质芳香烃产率,提高裂解产品分布的灵活性。
一、催化裂解的一般特点1、催化裂解是碳正离子反应机理和自由基反应机理共同作用的结果,其裂解气体产物中乙烯所占的比例要大于催化裂化气体产物中乙烯的比例。
2 、在一定程度上,催化裂解可以看作是高深度的催化裂化,其气体产率远大于催化裂化,液体产物中芳烃含量很高。
3 、催化裂解的反应温度很高,分子量较大的气体产物会发生二次裂解反应,另外,低碳烯烃会发生氢转移反应生成烷烃,也会发生聚合反应或者芳构化反应生成汽柴油。
二、催化裂解的反应机理一般来说,催化裂解过程既发生催化裂化反应,也发生热裂化反应,是碳正离子和自由基两种反应机理共同作用的结果,但是具体的裂解反应机理随催化剂的不同和裂解工艺的不同而有所差别。
在Ca-Al系列催化剂上的高温裂解过程中,自由基反应机理占主导地位;在酸性沸石分子筛裂解催化剂上的低温裂解过程中,碳正离子反应机理占主导地位;而在具有双酸性中心的沸石催化剂上的中温裂解过程中,碳正离子机理和自由基机理均发挥着重要的作用。
三、催化裂解的影响因素同催化裂化类似,影响催化裂解的因素也主要包括以下四个方面:原料组成、催化剂性质、操作条件和反应装置。
3.1 原料油性质的影响一般来说,原料油的H/C比和特性因数K越大,催化裂解法处理焦油方案[1]饱和分含量越高,BMCI值越低,则裂化得到的低碳烯烃(乙烯、丙烯、丁烯等)产率越高;原料的残炭值越大,硫、氮以及重金属含量越高,则低碳烯烃产率越低。
各族烃类作裂解原料时,低碳烯烃产率的大小次序一般是:烷烃>环烷烃>异构烷烃>芳香烃。
3.2催化剂的性质催化裂解催化剂分为金属氧化物型裂解催化剂和沸石分子筛型裂解催化剂两种。
催化剂是影响催化裂解工艺中产品分布的重要因素。
分析柴油加氢改质降凝技术的开发及工业应用

分析柴油加氢改质降凝技术的开发及工业应用【摘要】柴油加氢改质降凝技术是一种在炼油工业中广泛应用的技术,通过加氢处理可以降低柴油的凝固点,提高其流动性和稳定性。
本文首先介绍了柴油加氢改质技术的原理,包括加氢过程中的化学反应机理。
然后探讨了该技术的发展历程,以及在炼油工业中的应用情况。
接着分析了柴油加氢改质降凝技术的优势,如提高产品质量、减少能源消耗等,同时也指出了所面临的挑战,如高成本、技术难度等问题。
最后展望了该技术的未来发展方向,包括提高催化剂的活性和选择性,降低生产成本等。
柴油加氢改质降凝技术具有广阔的发展前景,不仅可以提升经济效益,还对环保方面有重要作用。
【关键词】柴油加氢改质降凝技术、炼油工业、优势、挑战、发展方向、发展前景、经济效益、环保作用1. 引言1.1 柴油加氢改质降凝技术介绍柴油加氢改质降凝技术是一种通过加氢反应对柴油进行改质和降温的技术。
在炼油工业中,柴油的凝点通常较高,这会导致在低温环境下出现结晶和凝固现象,影响燃料流动性和燃烧效率。
柴油加氢改质降凝技术通过在高温高压条件下将柴油与氢气反应,去除其中的硫、氮和氧等杂质,并裂解重分子链,使柴油的凝点降低,提高其流动性和稳定性。
该技术的原理是利用催化剂促进柴油中的重分子链裂解和硫、氮的去除,同时进行氢气的加氢反应,使得柴油的分子结构得到改善,凝点降低。
随着石油品质要求的提高和环保意识的增强,柴油加氢改质降凝技术在炼油工业中得到了广泛应用。
该技术的发展历程经历了不断的技术革新和改进,从最初简单的加氢裂解到现在的高效降凝技术,实现了柴油产品质量和性能的显著提升。
在未来,随着石化工业的发展和技术的进步,柴油加氢改质降凝技术将继续发展壮大,为炼油工业带来更多的机遇和挑战。
2. 正文2.1 柴油加氢改质技术的原理柴油加氢改质技术的原理主要是通过加氢作用将柴油中的不饱和链烃和芳香烃转化为饱和链烃,同时还可以去除硫、氮、氧等杂质,提高柴油的蜡的熔点,从而提高柴油的凝点。
柴油加氢催化剂

柴油加氢催化剂一、介绍柴油加氢催化剂的基本概念柴油加氢催化剂是一种用于柴油加氢反应的催化剂,它可以在较低的温度和压力下将石油馏分转化为高质量的柴油燃料。
这种催化剂通常由铜、锌、铝等金属组成,具有良好的选择性和活性,能够有效地去除硫、氮等杂质,并提高燃料的抗氧化性能。
二、柴油加氢催化剂的工作原理1. 催化反应机理柴油加氢催化剂主要通过两个反应机理来实现对燃料的改良:脱硫和裂解。
其中,脱硫反应是通过将硫元素与氢原子结合形成H2S等无害物质来实现;裂解反应则是将长链烷烃分解为较短链的低碳烷烃和芳香族化合物。
2. 催化剂选择性柴油加氢催化剂具有很强的选择性,在反应过程中只对特定类型的分子进行转换。
例如,它可以将硫化氢转化为无害的水和硫酸盐,但不会对其他分子进行反应。
三、柴油加氢催化剂的优点1. 提高燃料质量柴油加氢催化剂可以有效地去除燃料中的杂质,如硫、氮等元素,从而提高燃料的质量和纯度。
这些杂质不仅会降低燃料的性能,还会对环境造成污染。
2. 减少尾气排放由于柴油加氢催化剂可以去除燃料中的杂质,因此使用经过处理的柴油燃料可以大大减少车辆尾气排放。
这对于改善空气质量和保护环境具有重要意义。
3. 提高发动机效率使用经过处理的柴油燃料可以提高发动机效率,减少能源浪费。
这是因为经过处理后的燃料更加纯净,不含有杂质和污染物,可以更好地与空气混合,从而提高燃烧效率。
四、柴油加氢催化剂的应用领域1. 汽车工业目前,柴油加氢催化剂已经被广泛应用于汽车工业中,可以有效地减少车辆尾气排放,提高燃料质量和发动机效率。
2. 船舶工业柴油加氢催化剂也可以应用于船舶工业中,可以减少船舶尾气排放对海洋环境的污染,同时提高燃料的纯度和效率。
3. 能源工业柴油加氢催化剂还可以应用于能源工业中,可以提高石油馏分的转化率和产量,从而增加石油资源的利用效率。
五、柴油加氢催化剂的发展趋势1. 高性能催化剂的研制随着科技的不断进步和需求的不断增加,人们对柴油加氢催化剂的要求也越来越高。
催化催化裂化技术

催化催化裂化技术催化裂化技术是一种重要的炼油工艺,可以将重质石油馏分转化为高附加值的轻质产品。
本文将从催化裂化技术的原理、应用和发展前景等方面进行探讨,以期为读者提供对该技术的全面了解。
一、催化裂化技术的原理催化裂化技术是通过催化剂的作用将重质石油馏分分解为较轻的产品。
其主要原理是在高温和高压的条件下,将原料油与催化剂接触,使其发生裂化反应。
这种反应可以将长链烃分子裂解成短链烃分子,从而提高汽油和燃料油的产率。
催化裂化反应主要分为两个阶段:热裂化和催化裂化。
在热裂化阶段,原料油在高温下分解成烃气和液体烃。
然后,在催化剂的作用下,烃气和液体烃进一步反应,生成较轻的产品,如汽油、液化气和柴油等。
二、催化裂化技术的应用催化裂化技术在炼油行业中具有广泛的应用。
首先,它可以提高汽油的产率。
由于汽车的普及,对汽油的需求量不断增加。
催化裂化技术可以将重质石油馏分转化为轻质的汽油,从而满足市场需求。
催化裂化技术可以生产出高质量的柴油。
在催化裂化过程中,石油馏分中的硫、氮和金属等杂质可以得到有效去除,从而提高柴油的质量。
这对于减少柴油排放的污染物具有重要意义。
催化裂化技术还可以生产出液化气、石脑油和石化原料等产品。
这些产品在化工、冶金和化肥等行业中具有广泛的应用。
三、催化裂化技术的发展前景随着能源需求的增加和石油资源的日益枯竭,催化裂化技术在未来的发展前景十分广阔。
一方面,随着汽车工业的高速发展,对汽油的需求将持续增加,催化裂化技术将成为满足市场需求的重要手段。
另一方面,随着环境保护意识的提高,对燃料油质量的要求也越来越高。
催化裂化技术可以提高燃料油的质量,减少对环境的污染,因此在未来的发展中具有重要的作用。
随着科技的不断进步,催化剂的研发和改进也将推动催化裂化技术的发展。
新型的催化剂可以提高反应的选择性和活性,从而提高产品的产率和质量。
催化裂化技术作为一种重要的炼油工艺,在提高石油产品产率和质量方面具有重要的作用。
浅谈催化重整的化学反应机理

浅谈催化重整的化学反应机理催化重整是一种制备高质量汽油和柴油的重要过程。
它是利用催化剂对烃类分子进行裂解和重组,形成碳数更高、分子结构更平稳的分子,以提高燃料的辛烷值和抗爆性能。
本文将会讨论催化重整反应机理及其化学过程。
CnHm+ nH2O → (n+m/2)H2 + nCO其中CnHm代表异构体或同分异构体。
这些反应的起始物质包括饱和或不饱和烷烃、环烷烃、芳香烃和气体。
催化重整的主要原理是将碳数较低的烃类分子转化为碳数较高的烃类分子,并降低芳香烃含量和环烷烃含量。
催化重整反应机理涉及三个主要步骤:1. 裂解反应这是一个拆分较大分子的过程,分子内键断裂,产生小分子碳氢化合物和自由基。
在催化重整反应中,烃类和蒸汽从反应器的进料中获得能量,使分子达到裂解所需的能量,然后通过催化剂表面的活性中心,裂解成碳数更低的烃类分子,如甲烷,乙烷,乙烯,丙烷和丙烯等,同时生成一些自由基,如H,OH,CO,C2H5。
这些自由基参与了后续的重组反应。
裂解反应的主要目的是将高分子量的烃类分子分解为较小的分子,以为后续重组反应提供原料。
2. 重组反应在裂解反应以后,多种小分子烃类分子在催化剂表面重新组装成更高分子量的烃类。
通常,一些烷烃与蒸汽重组成更高级别的烷烃,一些氢及其自由基与烯烃和芳烃结合形成烷烃,而一些甲基自由基与芳烃结合形成环烷烃。
重组反应过后形成了更高分子量、更稳定的分子。
3. 转移反应转移反应是指烃类中的某些部分被割裂并传递给其他分子,从而形成长链烃。
而其他一些原子在这个过程中被割裂和释放。
该反应的机理是芳香烃与甲基自由基的反应,分子中的氢离子被气体中的氢雾化,生成甲基芳香烃和 H2。
总的来说,催化重整反应机理的实质就是碳氢化合物的裂解、重排和重组等过程。
通过优化反应条件和催化剂配方,可以获得较高的转化率和选择性,从而获得更高质量的燃料。
通过不断地研究,可以改进制氢和精细化工行业的工艺,使它成为具有极高经济效益的工业领域之一。
加氢裂化催化剂

加氢裂化催化剂(FC系列)FC系列催化剂是抚顺石油化工研究院根据国内加氢裂化技术发展的需要而开发的,具有裂化活性高、加氢性能好、抗氮能力强、稳定性好、对原料适应性强、可再生使用等特点。
在中压及高压条件下均有优异的加氢裂化性能,可按中油型或轻油型方案灵活进行生产,适用于减压馏分油中压或高压加氢裂化以及劣质柴油中压加氢改质,生产优质石油产品和化工原料,能满足用户的不同需求。
FC系列加氢裂化催化剂性能达到国际同类催化剂先进水平。
柴油加氢脱硫催化剂柴油加氢脱硫催化剂是抚顺石油化工研究院研制开发的,以新型改性氧化铝为载体,以非贵金属为活性组分,制备岀具有孔容大、比表面积高、活性组分匹配合理、活性金属高度分散、加氢脱硫和加氢脱氮活性好、对原料适应性强等特点的催化剂。
不仅其低压加氢脱硫活性比同类催化剂好,而且其加氢脱氮、芳烃饱和及深度加氢脱硫活性也比同类催化剂高许多。
催化剂性能属柴油领域国际领先水平。
工业应用结果表明:处理高硫柴油,FH-UDS催化剂可以满足生产硫含量<15mg/g低硫柴油的要求。
汽油选择性加氢脱硫剂(FGH系列)抚顺石油化工研究院研制开发的OCT-M FCC汽油选择性加氢脱硫技术,主要用于降低FCC汽油的硫含量和烯烃含量。
针对FCC汽油的硫化物集中在重馏分、烯烃集中在轻馏分中的分布特点,OCT-M技术将全馏分FCC汽油预分馏为重馏分和轻馏分,加氢脱硫后的重馏分与轻馏分混合进行无碱脱臭处理,在辛烷值损失较小的情况下可生产低硫含量清洁汽油。
本技术2004年通过了中国石油化工股份有限公司科技开发部组织的技术鉴定,认为本技术属国外同类技术先进水平。
FGH系列加氢脱硫催化剂是OCT-M技术所用组合催化剂。
石蜡加氢催化剂(FV系列)FV系列石蜡加氢催化剂具有孔容大、比表面积高、孔结构集中等特点,用于石蜡加氢精制具有较好的活性、选择性和稳定性,机械强度高,尤其是稠环芳烃饱和能力强。
催化剂的重复性和再现性良好。
催化裂化的工艺特点及基本原理
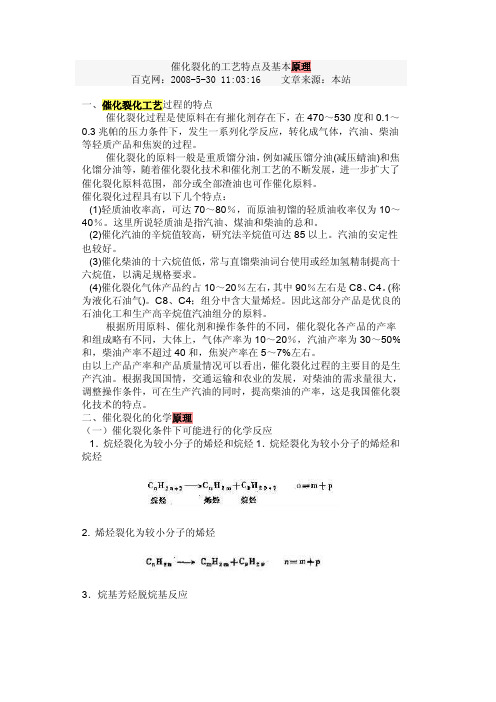
催化裂化的工艺特点及基本原理百克网:2008-5-30 11:03:16 文章来源:本站一、催化裂化工艺过程的特点催化裂化过程是使原料在有摧化剂存在下,在470~530度和0.1~0.3兆帕的压力条件下,发生一系列化学反应,转化成气体,汽油、柴油等轻质产品和焦炭的过程。
催化裂化的原料一般是重质馏分油,例如减压馏分油(减压蜻油)和焦化馏分油等,随着催化裂化技术和催化剂工艺的不断发展,进一步扩大了催化裂化原料范围,部分或全部渣油也可作催化原料。
催化裂化过程具有以下几个特点:(1)轻质油收率高,可达70~80%,而原油初馏的轻质油收率仅为10~40%。
这里所说轻质油是指汽油、煤油和柴油的总和。
(2)催化汽油的辛烷值较高,研究法辛烷值可达85以上。
汽油的安定性也较好。
(3)催化柴油的十六烷值低,常与直馏柴油词台使用或经加氢精制提高十六烷值,以满足规格要求。
(4)催化裂化气体产品约占10~20%左右,其中90%左右是C8、C4。
(称为液化石油气)。
C8、C4;组分中含大量烯烃。
因此这部分产品是优良的石油化工和生产高辛烷值汽油组分的原料。
根据所用原料、催化剂和操作条件的不同,催化裂化各产品的产率和组成略有不同,大体上,气体产率为10~20%,汽油产率为30~50%和,柴油产率不超过40和,焦炭产率在5~7%左右。
由以上产品产率和产品质量情况可以看出,催化裂化过程的主要目的是生产汽油。
根据我国国情,交通运输和农业的发展,对柴油的需求量很大,调整操作条件,可在生产汽油的同时,提高柴油的产率,这是我国催化裂化技术的特点。
二、催化裂化的化学原理(一)催化裂化条件下可能进行的化学反应1.烷烃裂化为较小分子的烯烃和烷烃1.烷烃裂化为较小分子的烯烃和烷烃2. 烯烃裂化为较小分子的烯烃3.烷基芳烃脱烷基反应4.烷基芳烃侧链断裂5.环烷烃裂化为烯烃假如环烷烃中仅有单环,则环不打开:6.氢转移反应如:环烷烃+烯烃→芳香烃+烷烃7.异构化反应:烷烃→异构烷烃烯烃→异构烯烃8.芳构化反应烯烃环化脱氢生成芳香烃,如:9.缩合反应单环芳烃可缩台成稠环芳烃,最后可缩合成焦炭,并放出氢气,使烯烃饱和。
重油催化裂解技术

重油催化裂解技术重油催化裂解技术是一种能够将重质石油原料转化为高附加值产品的重要技术。
本文将介绍重油催化裂解技术的原理、工艺流程和应用前景。
一、原理重油催化裂解技术利用催化剂将重质石油原料中的大分子化合物分解为较小分子量的产物。
催化剂可以提供活性位点,降低反应活化能,加速反应速率。
同时,催化剂还能选择性地促进某些反应路径,提高目标产物的产率和选择性。
重油催化裂解反应主要发生在催化剂和重质石油原料之间的接触界面上。
二、工艺流程重油催化裂解技术的工艺流程一般包括预热、催化裂解反应、分离和处理四个步骤。
1. 预热:将重质石油原料提前加热到适宜的反应温度,以提高反应速率和转化率。
2. 催化裂解反应:将预热后的重质石油原料与催化剂混合,通过加热和压力控制,使其在催化剂的作用下进行裂解反应。
在反应过程中,大分子量的重质石油原料会被分解为较小分子量的产物,如汽油、柴油和液化石油气等。
3. 分离:将催化裂解反应产生的混合物进行分离,根据不同组分的沸点差异,通过蒸馏、萃取等分离技术将产物分离出来。
这样可以得到纯净的目标产物,同时将未反应的原料和副产物进行回收利用。
4. 处理:对分离后的产物进行进一步处理,如脱硫、脱氮、裂解汽油脱烯和脱芳等,以提高产物的质量和降低环境污染。
三、应用前景重油催化裂解技术具有广阔的应用前景。
1. 产物丰富多样:通过重油催化裂解技术可以得到多种高附加值产物,如高辛烷值汽油、超低硫柴油、纯净的液化石油气等。
这些产物在石油化工、交通运输和燃料供应等领域具有重要应用价值。
2. 降低能源消耗:重油催化裂解技术可以将重质石油原料转化为较轻质的产物,提高能源利用效率。
同时,该技术还可以将低价的重质石油原料转化为高价值的产物,实现资源的有效利用。
3. 减少环境污染:重油催化裂解技术可以降低石油产品中硫、氮等有害元素的含量,减少燃料燃烧过程中的环境污染物排放。
同时,通过对催化剂的研发和改进,还可以降低催化剂的用量和再生成本,减少对环境的影响。
重油催化裂解技术

重油催化裂解技术重油催化裂解技术是一种将重质石油馏分转化为轻质石油产品的方法。
它是通过在高温和催化剂的作用下,将重油分子链断裂为较小的分子,从而提高其燃烧性能和降低粘度。
本文将介绍重油催化裂解技术的原理和应用。
重油是石油加工过程中产生的一种质量较重、粘度较高的石油产品。
由于其燃烧性能较差,使用范围受限。
为了提高重油的利用价值,重油催化裂解技术应运而生。
该技术通过将重油加热至高温,并在催化剂的作用下进行分子链断裂,生成较轻质的石油产品,如汽油、柴油和润滑油等。
重油催化裂解技术有效地提高了重油的利用率,并减少了对传统石油产品的需求。
重油催化裂解技术的核心是催化剂的选择和反应条件的控制。
常用的催化剂有氧化铝、硅铝酸盐等。
它们能够加速重油分子链的断裂,并促使生成较轻质的石油产品。
在反应过程中,需要控制适当的温度和压力,以确保反应的进行和产物的质量。
此外,还可以通过添加一些助剂,如金属元素和添加剂,来进一步改善重油的裂解效果。
重油催化裂解技术具有许多优点。
首先,它可以将重油转化为更有价值的轻质石油产品,提高了能源资源的利用效率。
其次,重油催化裂解技术可以降低石油产品的粘度,改善其流动性,提高燃烧效率。
此外,该技术还可以减少环境污染物的排放,对环境友好。
重油催化裂解技术在石油加工和能源产业中具有广泛的应用。
它可以用于炼油厂的重油加工,将重油转化为更高价值的石油产品,如汽油和柴油。
此外,重油催化裂解技术还可以用于发电厂和工业锅炉等能源设备的燃料改造,提高燃烧效率和环境友好性。
此外,重油催化裂解技术还可用于生产润滑油和化工原料等领域。
然而,重油催化裂解技术也存在一些挑战和限制。
首先,该技术需要高温高压条件下进行反应,能耗较高。
其次,催化剂的选择和优化需要大量的实验研究和经验积累。
此外,重油催化裂解技术还面临着催化剂中毒、产物选择性和废水处理等问题。
重油催化裂解技术是一种将重油转化为轻质石油产品的有效方法。
它通过在高温和催化剂的作用下,将重油分子链断裂,生成较轻质的石油产品。
柴油加氢改质装置增产石脑油技术分析

柴油加氢改质装置增产石脑油技术分析甘肃省庆阳市745000摘要:随着双碳目标的实施,炼油厂汽油、柴油产品将减少,石脑油、尾油等化工原料将逐渐成为主要炼油产品。
加氢裂化重石脑油馏分可作为催化重整制低碳芳烃的原料。
加氢裂化反应遵循正碳离子β裂解机理,当裂化反应作用较强时会促进在酸性中心上发生二次裂化,生成低碳数的重石脑油馏分。
目前全转化模式下重石脑油收率可以达到71%~73%,副产干气、液化气和轻石脑油价格低,耗氢高,这使得提高加氢裂化重石脑油选择性成为此类技术的关键指标。
氢气在柴油中的溶解度很小,传质过程受液膜控制,这使得柴油加氢精制的总反应过程成为了受传质控制的慢反应体系。
采用微界面强化传质技术后可以通过界面处微观的相互作用进行调控,实现过程传质和反应强化。
基于此,本篇文章对柴油加氢改质装置增产石脑油技术进行研究,以供参考。
关键词:柴油加氢;改质装置;增产;石脑油技术引言近年来,由于环保排放法规日趋严格,成品油质量升级步伐加快。
2016年12月23日,国家发布了最新的柴油国家标准GB19147—2016《车用柴油强制性国家标准》。
标准规定了最新的国Ⅵ阶段车用柴油的主要指标;与国Ⅴ标准相比较,国Ⅵ标准在油品烯烃、芳烃和苯含量以及挥发等的指标更加严苛,在继续限制硫含量的同时,其油品组分和烃类组成更是公认的优化后的标准。
受经济增速放缓及清洁能源发展影响,国际国内市场柴油需求量进一步降低,预计2030年柴汽比将降至1.28。
因此,当前环境下调整改造炼厂炼油结构,更适应汽油质量升级,降低柴汽比,是提高炼厂经济效益的重要手段,也是炼油企业转型升级的必然结果。
1柴油加氢精制工艺技术简介加氢精制具体就是促使温度、压力以及氢油比处于某种条件下,促使原料油、氢气通过反应器内部的催化剂床层,之后在催化剂的作用之下,实现对油品之中含有的一些非烃类化合物的转化,将这些非烃类化合物转化成为比较容易剔除的化合物,从而促使油品的品质得到提升的过程。
催化裂化文献综述

文献综述催化裂化是重质油在酸性催化剂存在下,在五百摄氏度左右、一万到三万帕下发生以裂化反应为主的一系列化学反应,生产轻质油、气体和焦炭的过程。
由于催化裂化投资和操作费用低、原料适应性强、转化率高,自1942年第一套工业化流化催化裂化装置运转以来,它已发展成为炼油厂中的核心加工工艺,是重油轻质化的主要手段之一。
催化裂化产品是主要的运输燃料调合组分。
在世界范围内,FCC汽油占总汽油产量的25%~80%,FCC柴油占总柴油量的,10%~30%,而且是仅次于蒸汽裂解制取丙烯的又一大生产装置。
面对日益严格的环保法规的要求,通过装置改造和与其它上下游工艺结合(如进料加氢,产品后处理等),催化裂化能以合适的费用生产合适的产品。
即使从更长远的目标看,催化裂化装置所产汽油经加氢饱和后也应能成为燃料电池的一种燃料组分【1】。
催化裂化的原料和产品【2】一原料催化裂化的原料范围广泛,可分为馏分油和渣油两大类。
馏分油主要是直馏减压馏分油,也包括少量的二次加工重馏分油如焦化蜡油、脱沥青油等;渣油主要是减压渣油、加氢处理渣油等。
渣油都是以一定的比例掺入到减压馏分油中进行加工,其掺入的比例主要受制于原料的金属含量和残炭值。
对于一些金属含量很低的石蜡基原油也可以直接用常压重油作为原料。
当减压馏分油中掺入渣油时则通称为重油催化裂化,1995年之后我国新建的装置均为掺炼渣油RFCC【2】。
二产品催化裂化的产品包括气体、液体和焦炭。
其中气体主要是干气和液化气。
液体产物分为:汽油、柴油、重柴油(回炼油)和油浆。
中国石油石油化工研究院开发的国Ⅳ汽油生产技术集成催化剂、催化剂级配、工艺及开工操作等多项核心技术,有效破解了高烯烃含量的催化汽油脱硫和辛烷值降低的技术难题,形成了具有自主知识产权的满足国Ⅳ标准的催化裂化汽油加氢改质技术。
该技术作为中国石油具有自主知识产权的清洁汽油生产技术,填补了中国石油生产国Ⅳ清洁汽油的技术空白,可为企业汽油质量升级提供自主技术支持,具有巨大的社会效益和经济效益,工业应用前景广阔【7】。
催化裂化与催化裂解(李春义)
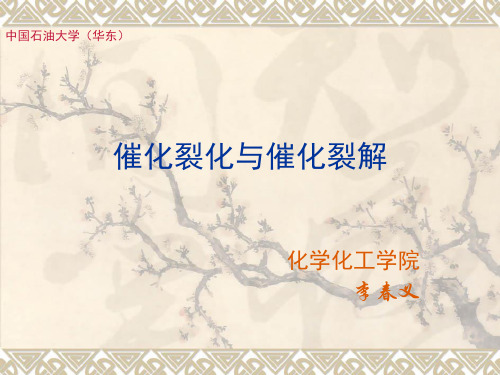
1.前言--流化催化裂化(FCC)发展概况
FCC的优点
烟气 再生器 再生剂 料斗 待生剂 料斗 分馏塔 汽油 加热油 重瓦斯油 原料 油气 塔底油 鼓风机
可以用小颗粒催化剂,消除了 内扩散的影响; 固体催化剂循环速率可以在较 宽的范围内调节,操作灵活; 流体与固体可以迅速混合,并 且固体的快速运动极大地改善 了传热效果。
1.前言--发展方向
加工重质原料。直接加工AR、脱沥青油甚至VR,经济效益显著。焦炭产率高、重 金属污染严重等是亟待解决的问题。
降低能耗。催化裂化装置的能耗较大,降低能耗的潜力也较大。降低能耗的主要 方向是降低焦炭产率、充分利用再生烟气中CO的燃烧热以及发展再生烟气热能利 用技术等。
减少污染物排放。催化裂化装置的主要污染物排放是再生烟气中的粉尘、CO、 SOX和NOX。随着环境保护立法日趋严格,减少污染的问题也日益显得重要。 适应多种生产需要的催化剂和工艺。例如,结合我国国情多产柴油,又如多产丙 烯、丁烯,甚至是多产乙烯的新催化剂和工艺技术。 过程模拟和系统集成优化。正确的设计、预测及优化控制都需要准确的催化裂化 过程数学模型。由于催化裂化过程的复杂性,仅依靠某一局部单项技术的开发和 实施是不能从根本上解决问题的,必须针对重要科学问题和关键技术问题,对催 化裂化过程进行系统集成优化,开发新型工艺技术及配套专用装备,从根本上优 化工业提升管反应系统的操作。
1.前言--原料与产品
不同原料的催化裂化产物分布
项 目 催化裂化原料:VGO、AR、 VR、CGO、溶剂脱沥青油 原料油 和加氢处理的重油。 原料、催化剂和操作条件 干 气 对催化裂化产物分布和产 品质量都有明显的影响。 液化气 以多产丙烯或多产乙烯和 汽 油 丙烯为目的的催化裂解, 产品 轻柴油 理想的原料是石蜡基的重 产率 wt% 重柴油 油或渣油。 油 浆 对劣质原料进行加氢处理, 为大势所趋。 焦 炭
加氢裂化
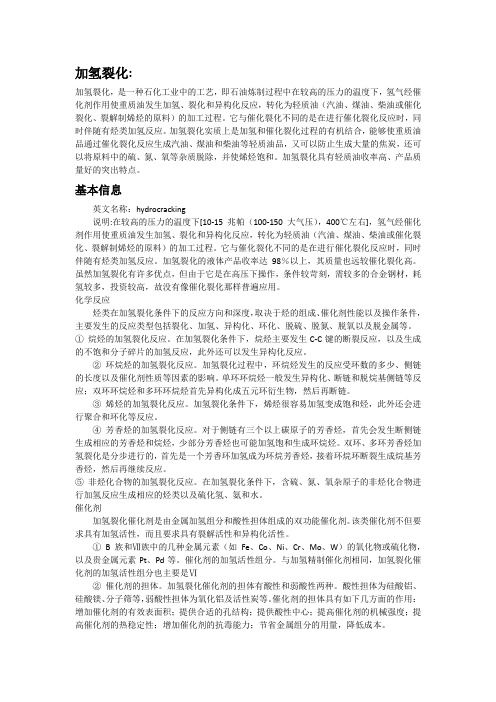
加氢裂化:加氢裂化,是一种石化工业中的工艺,即石油炼制过程中在较高的压力的温度下,氢气经催化剂作用使重质油发生加氢、裂化和异构化反应,转化为轻质油(汽油、煤油、柴油或催化裂化、裂解制烯烃的原料)的加工过程。
它与催化裂化不同的是在进行催化裂化反应时,同时伴随有烃类加氢反应。
加氢裂化实质上是加氢和催化裂化过程的有机结合,能够使重质油品通过催化裂化反应生成汽油、煤油和柴油等轻质油品,又可以防止生成大量的焦炭,还可以将原料中的硫、氮、氧等杂质脱除,并使烯烃饱和。
加氢裂化具有轻质油收率高、产品质量好的突出特点。
基本信息英文名称:hydrocracking说明:在较高的压力的温度下[10-15兆帕(100-150大气压),400℃左右],氢气经催化剂作用使重质油发生加氢、裂化和异构化反应,转化为轻质油(汽油、煤油、柴油或催化裂化、裂解制烯烃的原料)的加工过程。
它与催化裂化不同的是在进行催化裂化反应时,同时伴随有烃类加氢反应。
加氢裂化的液体产品收率达98%以上,其质量也远较催化裂化高。
虽然加氢裂化有许多优点,但由于它是在高压下操作,条件较苛刻,需较多的合金钢材,耗氢较多,投资较高,故没有像催化裂化那样普遍应用。
化学反应烃类在加氢裂化条件下的反应方向和深度,取决于烃的组成、催化剂性能以及操作条件,主要发生的反应类型包括裂化、加氢、异构化、环化、脱硫、脱氮、脱氧以及脱金属等。
①烷烃的加氢裂化反应。
在加氢裂化条件下,烷烃主要发生C-C键的断裂反应,以及生成的不饱和分子碎片的加氢反应,此外还可以发生异构化反应。
②环烷烃的加氢裂化反应。
加氢裂化过程中,环烷烃发生的反应受环数的多少、侧链的长度以及催化剂性质等因素的影响。
单环环烷烃一般发生异构化、断链和脱烷基侧链等反应;双环环烷烃和多环环烷烃首先异构化成五元环衍生物,然后再断链。
③烯烃的加氢裂化反应。
加氢裂化条件下,烯烃很容易加氢变成饱和烃,此外还会进行聚合和环化等反应。
- 1、下载文档前请自行甄别文档内容的完整性,平台不提供额外的编辑、内容补充、找答案等附加服务。
- 2、"仅部分预览"的文档,不可在线预览部分如存在完整性等问题,可反馈申请退款(可完整预览的文档不适用该条件!)。
- 3、如文档侵犯您的权益,请联系客服反馈,我们会尽快为您处理(人工客服工作时间:9:00-18:30)。
催化重柴油加氢后的催化裂解性能张海娜;陈晓成;祝晓琳;王斌;许乃文;李春义【摘要】The catalytic diesel cannot be used as diesel blending fraction even after hydrogenation due to its high aromatic content. In this work,thecatalytic cracking performance of FCC heavy diesel (density of 934.0 kg/m3,aromatic content of 72.06% and 2-ring aromatics content of 35.86%) before and after hydrogenation were investigated.The main aromatics in FCC heavy diesel are the 2-ring aromatics,which can be selectively transformed to naphthenoaromaticsvia hydrogenation and further cracked into aromatics in gasoline fraction and olefins in LPG through catalytic cracking. The results indicate that the cracking performance of hydro-treated diesel is substantially improved. The polycyclic aromatics are transformed to naphthen-ic hydrocarbons that can be easily cracking, and the conversion is 19.09% higher than the untreated diesel fraction. The gasoline yield is increased by 16.60% with high aromatic content (about 47.29%) and low olefin concentration (about 12.50%), which is a good high-octane gasoline blending component. Meanwhile, the LPG yield is increased up to 16.58%,in which the content of propylene and iso-butylene is 42.70% and 10.80%,respectively.%催化重柴油芳烃含量高,加氢后仍难以作为车用柴油调和组分.对密度为934.0 kg/m3、芳烃质量分数为72.06%(其中双环芳烃质量分数为35.86%)的催化重柴油加氢前后的催化裂解性能进行研究.催化重柴油芳烃中以双环芳烃为主,通过加氢将其部分饱和得到环烷芳香烃,然后进行催化裂解,转化成汽油馏分芳烃和以烯烃为主的液化气.结果表明:加氢处理后的催化重柴油具有较好的裂解性能,柴油中的多环芳烃经加氢成为更易裂解的环烷芳香烃,有效减少了多环芳烃的含量,其裂解能力得到明显改善,转化率较催化重柴油直接裂解提高了19.09个百分点;产物中汽油收率增加16.60个百分点,且汽油中芳烃含量高(47.29%)、烯烃含量低(12.50%),是较好的高辛烷值汽油调和组分;液化气收率达到16.58%,其中丙烯、异丁烯在液化气中含量分别达到了42.70%和10.80%.【期刊名称】《中国石油大学学报(自然科学版)》【年(卷),期】2018(042)001【总页数】6页(P165-170)【关键词】催化重柴油;加氢;催化裂解;产物分布【作者】张海娜;陈晓成;祝晓琳;王斌;许乃文;李春义【作者单位】中国石油大学重质油国家重点实验室,山东青岛266580;中国石油大学重质油国家重点实验室,山东青岛266580;中国石油大学重质油国家重点实验室,山东青岛266580;中国石油大学重质油国家重点实验室,山东青岛266580;中国石油大学重质油国家重点实验室,山东青岛266580;中国石油大学重质油国家重点实验室,山东青岛266580【正文语种】中文【中图分类】TE624.41催化裂化导致催化柴油在成品柴油中所占比例逐步增大,但柴油的需求量呈现逐年递减趋势[1];催化裂化装置所加工的原料日趋重质化和劣质化,导致催化柴油质量恶化。
通过深度加氢处理[2]、加氢芳环饱和[3]、加氢裂化[4]和加氢选择性开环[5-6]等方法可改善催化柴油质量。
朱长健等[7]将蜡油加氢后进催化裂解装置进行裂解,得到的催化柴油中S、N含量明显减少,实际胶质降低,十六烷值得到提高;加氢催化剂在改善柴油产品性质方面也取得了较为理想的效果[8-9]。
催化柴油的利用主要是通过加氢方法生产二甲苯(BTX)和低碳烯烃[10-12],以芳烃含量达到70%~90%的催化重柴油(其馏程介于普通柴油和回炼油)作为研究对象,既能减少回炼油在回炼过程中生成的油浆及焦炭,又可将其转化成小分子烯烃(液化气组成)和带短侧链的单环芳烃(汽油组分)。
笔者以催化重柴油为原料,经加氢得到加氢柴油;利用提升管中试装置,在相近操作条件下进行催化重柴油加氢前后催化裂解反应,研究产物分布以及各产品组成分布。
1 实验1.1 实验原料及催化剂以催化裂化装置得到的催化重柴油为原料,该柴油密度较高(934.0 kg/m3)、终馏点较高(425 ℃),多环芳烃含量较高(54.32%,即双环芳烃和三环芳烃之和);在重油加氢精制实验装置上经加氢处理使多环芳烃适当加氢饱和得到加氢柴油,催化重柴油加氢前后主要性质列于表1。
原料加氢处理所用催化剂为FDS-1和TK-951。
FDS-1为柴油深度加氢脱硫催化剂[13],以γ-Al2O3为载体,Ni-Mo为活性组分,外观为三叶草条形,堆密度0.810~0.820 g/cm3,直径1.51~1.53 mm,长度3.00~10.00 mm;TK-951为含微量分子筛型加氢裂化催化剂[14],外观为圆柱形,堆密度0.880~0.890 g/cm3,直径0.40~0.50 mm,长度0.80~8.00 mm。
催化裂解催化剂为ARGG工业平衡催化剂,其主活性组分为按一定比例混合的ZSM-5分子筛和USY 型分子筛[15],常用于多产液化气和汽油;催化剂的堆密度为0.918 g/cm3,比表面积139 m2/g,孔容0.17 cm3/g,平均粒径70 μm,微反活性66。
表1 催化重柴油和加氢柴油的基本性质Table 1 Properties of FCC heavy dieseland hydrogenated diesel oil原料密度(20°C)ρ/(kg·m-3)残炭质量分数/%元素质量分数/%CH黏度/(mm2·s-1)20℃50℃烃类质量分数/%链烷烃+环烷烃芳烃单环芳烃双环芳烃三环芳烃凝点/℃闭口闪点/℃催化重柴油934.00.3488.7810.689.463.7927.9417.7435.8618.461178加氢柴油902.1<0.0286.8211.898.163.2535.1354.477.662.747741.2 实验装置和产物分析方法催化重柴油加氢处理实验是在重油加氢精制实验装置上进行(图1)。
该装置有2个反应器,分别装有不同性能的催化剂。
采用2个反应器串联模式,在第一个反应器内装填FDS-1催化剂;第二个反应器内装填TK-951催化剂。
在压力为8.7 MPa、氢油比为1 000∶1、空速为1.2 h-1、精制反应器温度为345 ℃、改质反应器温度为365 ℃条件下,对原料进行加氢处理,进料量为244 g/h。
每间隔6 h取液体进行馏程分析,连取3次。
催化裂解实验在ZDT-1中型多功能提升管催化裂化实验装置上进行(图2)。
该装置为高低并列式提升管催化裂化试验装置,能够模拟工业提升管装置进行反应再生连续运转,试验数据与工业生产数据具有较好的可比性,其主要由反应-再生系统、进料及蒸汽发生系统、油气接收计量系统、气路控制系统和计算机控制系统5部分组成。
利用该装置已经成功研究了两段提升管催化裂解多产丙烯[16]、焦化蜡油和焦化汽油的催化裂解反应[17]等实验。
催化重柴油和加氢柴油进行催化裂解所采用工艺条件为:反应温度为510 ℃,油剂混合温度为580 ℃,剂油比为8,停留时间为1.4 s。
为保证实验数据的可靠性,实验数据均进行重复实验,每个实验数据均是选取2组实验结果相近、物平均在95%以上的数据进行平均,然后再进行归一化处理得到。
图1 重油加氢精制实验装置流程Fig.1 Schematic of hydrogenation unit催化裂解反应生成的气体通过Bruker 450-GC型气相色谱分析其组成。
液体产物则同样采用气相色谱仪进行馏程分析,以确定汽油(小于204 ℃)、柴油(204~350 ℃)、重油(大于350 ℃)的比例。
同时,将液体产物进行实沸点蒸馏切割得到各馏分油,进而分析汽油和柴油性质和组成;其中,汽油馏分通过Perkin Elmer Clarus 580型气相色谱进行单体烃组成分析,柴油馏分则通过美国LECO公司全二维气相色谱-飞行时间质谱仪(GC×GC/TOF MS)分析其烃类组成。
加氢前后催化重柴油、裂解产物柴油以及重油的物化性质,如密度、残炭、C、H元素分析、黏度、凝点、闭口闪点、折光指数、四组分组成以及馏程等分别依据GB/T1884、GB/T265、Q/SY DH0402-2006、GB/T265、GB/T510、GB/T261、SH/T 0724-2002、NB/SH/T0509-2010、ASTM 6352等方法标准进行分析。
图2 ZDT-1型提升管催化裂化实验装置流程Fig.2 Schematic of pilot-scale riser FCC unit2 结果分析2.1 催化重柴油加氢后的性质催化重柴油和经加氢处理得到的加氢柴油的性质见表1。
由表1可知,原料催化重柴油密度较高,超过930 kg/m3,氢质量分数为10.68%。
烃类组成中芳烃含量最高,达到72.06%,其中双环芳烃质量分数为35.86%,约占总芳烃的50%。
芳烃含量高、氢含量低,导致柴油的十六烷值不会很高[18]。