金属或陶瓷粉末注塑成型工艺
金属粉末注射成型件的工艺及特点
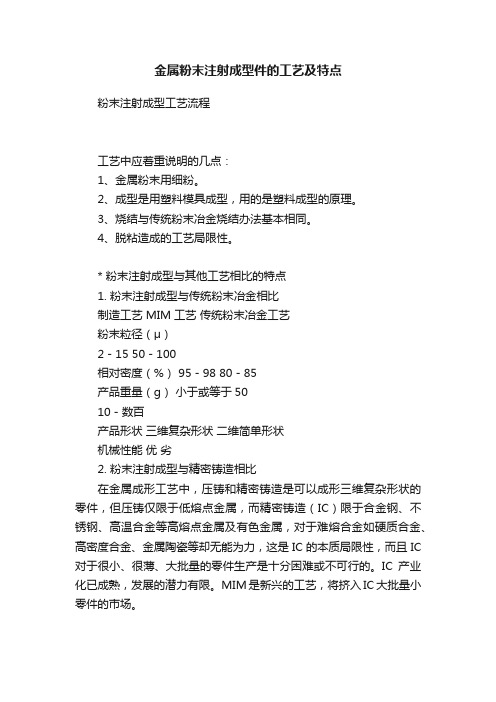
金属粉末注射成型件的工艺及特点粉末注射成型工艺流程工艺中应着重说明的几点:1、金属粉末用细粉。
2、成型是用塑料模具成型,用的是塑料成型的原理。
3、烧结与传统粉末冶金烧结办法基本相同。
4、脱粘造成的工艺局限性。
* 粉末注射成型与其他工艺相比的特点1. 粉末注射成型与传统粉末冶金相比制造工艺 MIM工艺传统粉末冶金工艺粉末粒径(μ)2-15 50-100相对密度(%) 95-98 80-85产品重量(g)小于或等于5010-数百产品形状三维复杂形状二维简单形状机械性能优劣2. 粉末注射成型与精密铸造相比在金属成形工艺中,压铸和精密铸造是可以成形三维复杂形状的零件,但压铸仅限于低熔点金属,而精密铸造(IC)限于合金钢、不锈钢、高温合金等高熔点金属及有色金属,对于难熔合金如硬质合金、高密度合金、金属陶瓷等却无能为力,这是IC的本质局限性,而且IC 对于很小、很薄、大批量的零件生产是十分困难或不可行的。
IC产业化已成熟,发展的潜力有限。
MIM是新兴的工艺,将挤入IC大批量小零件的市场。
3. 粉末注射成型与传统机械加工相比较。
传统机械加工法,近来靠自动化而提升其加工能力,在效率和精度上有极大的进步,但是基本的程序上仍脱不开逐步加工(车削、刨、铣、磨、钻孔、抛光等)完成零件形状的方式。
机械加工方法的加工精度远优于其他加工方法,但是因为材料的有效利用率低,且其形状的完成受限于设备与刀具,有些零件无法用机械加工完成。
相反的,MIM可以有效利用材料,形状自由度不受限制。
对于小型、高难度形状的精密零件的制造,MIM工艺比较机械加工而言,其成本较低且效率高,具有很强的竞争力。
4. 粉末注射成型与其他成型工艺比较总表加工法比较项目 MIM 精密铸造传统粉末冶金冷间锻造机械加工压口形状自由度45 2 2 4 4精度4 3 45 5 3机械强度 4 4 2 5 5 1材质适用自由度 5 4 5 2 3 2模具费 3 4 3 1 5 3量产性 5 2 5 5 3 5产品价格 3 2 4 5 2 4* 粉末注射成型工艺技术的优点MIM的工艺优点可归纳如下:⑴ MIM可以成形三维形状复杂的各种金属材料零件(只要这种材料能被制成细粉)。
pim工艺技术

pim工艺技术PIM工艺技术(Powder Injection Molding)是一种将金属或陶瓷粉末与高分子塑料混合,制成复杂形状零部件的先进制造技术。
PIM技术是在注塑成型和金属粉末冶金的基础上发展起来的,通过粉末的形态设计和后处理工艺的改进,使得材料的性能得到了显著提高。
PIM工艺技术的优势主要体现在以下几个方面:首先,PIM工艺技术可以制造出复杂形状的零部件。
与传统的加工方法相比,PIM技术可以制造出精密度高、耐磨、耐腐蚀等性能优良的复杂形状零部件,满足了工程领域对于复杂形状零部件的需求。
其次,PIM工艺技术可以提高材料的使用效率。
在传统的加工方法中,材料的使用率较低,而PIM技术可以将材料的利用率提高到95%以上。
这一点不仅能够降低生产成本,还能够减少对环境的影响。
再次,PIM工艺技术可以提高生产效率。
PIM技术是一种大规模、连续的生产方式,可以在短时间内生产出大量产品,提高了生产效率。
与传统的注塑成型方法相比,PIM技术的生产效率可以提高2-5倍。
此外,PIM工艺技术还可以制造出高性能的材料。
通过合理调配金属粉末和高分子塑料的配方,可以制造出高强度、高韧性、高耐磨性等性能优良的材料,满足了特定场景下对产品性能的要求。
然而,PIM工艺技术也存在一些挑战和限制。
首先,PIM技术在设计方面存在一定的限制,对零件的形状和结构有一定的要求。
其次,PIM技术对原料的要求较高,需要通过粉末的形态设计和后处理工艺的改进来提高材料的性能。
此外,PIM技术的设备和工艺控制难度较大,对于操作者的要求较高。
总的来说,PIM工艺技术是一种先进的制造技术,具有制造复杂形状零部件、提高材料使用效率、提高生产效率和制造高性能材料的优势。
虽然面临一些挑战和限制,但随着技术的不断发展和改进,相信PIM技术将会在更多领域得到应用,并为制造领域的发展贡献力量。
MIM(金属材料粉末注塑成型)技术介绍

精心整理
MIM(金属粉末注塑成型)技术介绍
?????MIM 是将现代塑料注射成形技术引入粉末冶金领域而形成的一种全新的金属零部件近净成形加工技术,是近年来粉末冶金学科和工业领域中发展十分迅猛的一项高新技术。
MIM 的工艺步骤是:首先选取符合MIM MIM ????1????2~1.6μm ????3度高,工序简单,可实现连续大批量生产;?
????4、产品质量稳定、性能可靠,制品的相对密度可达95%~99%,可进行渗碳、淬火、回火等热处理。
产品强度、硬度、延伸率等力学性能高,耐磨性好,耐疲劳,组织均匀;?
国际上普遍认为MIM技术的发展将会导致零部件成形与加工技术的一场革命,被誉为“21世纪最热门的零部件的成形技术”。
?
MIM技术优势
MIM与传统粉末冶金相对比?
?MIM可以制造复杂形状的产品,避免更多的二次机加工。
?
?MIM产品密度高、耐蚀性好、强度高、延展性好。
?
?MIM可以将2个或更多PM产品组合成一个MIM产品,节省材料和工序。
?
MIM与机械加工相对比?
??MIM设计可以节省材料、降低重量。
???MIM可以将注射后的浇口料重复破碎使用,不影响产品性能,材料利用率高。
粉末注塑成型(PIM) - 繁

粘合劑使粉末可用來注塑 對粘合劑最重要的要求是:脫脂過程中的 尺寸穩定性、良好的保存特性、不與粉末 材料發生反應、很高的綠件強度、良好的 脫模特性、熱穩定性和在脫脂過程中易於 去除並可完全去除。
粉末性能
粘合劑與粉末顆粒之間的粘附力還應盡可 能高,以便在注塑過程中增高壓力不會使 兩個組份分離,而導致填充的零件不均 勻。 為了獲得良好的注塑成型特性並以低 收縮率獲得均勻的燒結品質,建議採用球 形粉末。
金屬和陶瓷元件的典型公差:
公稱尺寸 mm
<3 3-6 6-15 15-30 30-60 >60
公差 +/- mm
0.05 0.06 0.075 0.15 0.25 +/-0.5% 的公稱尺寸
在嚴格的公差範圍內的高重複性
設備
葉片攪和機 剪輥式擠出機 雙螺杆擠出機 高速混合器 造粒機 研磨機/顎式粉碎機 注塑成型機
在鎖模裝置中的模具中。 模具保持 閉合,同時成型零件硬化。
開模 3 在綠件冷卻後,噴嘴會通過注塑裝
"標準“注塑週期
置的移動從模具位置移開。 鎖模裝
˙ 填充注塑成型機的料斗
置打開,注塑成型機的頂針系統會
˙ 預塑(原料熔化)
自動頂出成型零件。
˙ 將熔化的材料注入模具中並硬化
˙ 開模和零件脫模
零件脫模 4
操作人員控制的邏輯性和選擇性 顯示幕僅顯示實際可用的功能,即機器上 配置且在週期中啟動的功能。 因此大大減 少了可用參數的數量,使編程更易於進 行。
品質保證 綜合性的品質保證功能和可選的圖形評估 可以確保最佳的生產品質。這方面的控制 可以不斷增強,從而集成 AQC 系統。
10
品質保證 通過故障評估、自動確定參考值、可調節 的過程圖形、監視圖形、壓力信號的集成 監視、隨機取樣功能、擴展監視選項來擴 展基本設備。.
金属注射成型工艺流程
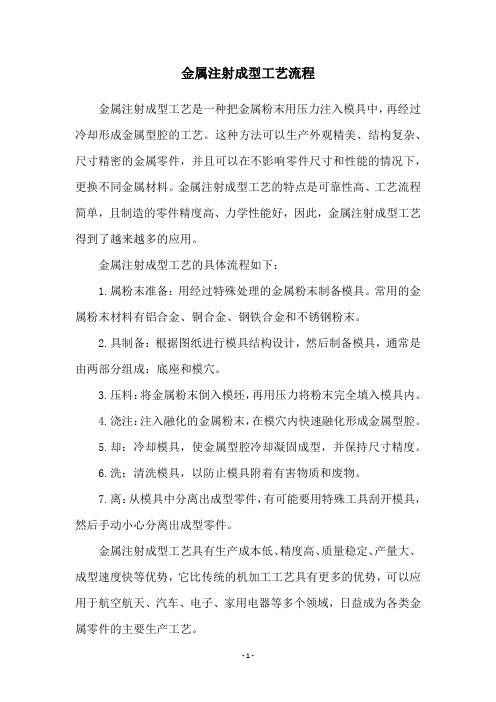
金属注射成型工艺流程金属注射成型工艺是一种把金属粉末用压力注入模具中,再经过冷却形成金属型腔的工艺。
这种方法可以生产外观精美、结构复杂、尺寸精密的金属零件,并且可以在不影响零件尺寸和性能的情况下,更换不同金属材料。
金属注射成型工艺的特点是可靠性高、工艺流程简单,且制造的零件精度高、力学性能好,因此,金属注射成型工艺得到了越来越多的应用。
金属注射成型工艺的具体流程如下:1.属粉末准备:用经过特殊处理的金属粉末制备模具。
常用的金属粉末材料有铝合金、铜合金、钢铁合金和不锈钢粉末。
2.具制备:根据图纸进行模具结构设计,然后制备模具,通常是由两部分组成:底座和模穴。
3.压料:将金属粉末倒入模坯,再用压力将粉末完全填入模具内。
4.浇注:注入融化的金属粉末,在模穴内快速融化形成金属型腔。
5.却:冷却模具,使金属型腔冷却凝固成型,并保持尺寸精度。
6.洗:清洗模具,以防止模具附着有害物质和废物。
7.离:从模具中分离出成型零件,有可能要用特殊工具刮开模具,然后手动小心分离出成型零件。
金属注射成型工艺具有生产成本低、精度高、质量稳定、产量大、成型速度快等优势,它比传统的机加工工艺具有更多的优势,可以应用于航空航天、汽车、电子、家用电器等多个领域,日益成为各类金属零件的主要生产工艺。
但金属注射成型工艺也存在着不足。
其中,模具投资较大,模具设计和制造技术要求也比较高;另外,在产品设计和制造过程中,模具位置及模具结构受到较大的限制,从而影响零件的尺寸、形状及表面精度。
总之,金属注射成型工艺是一种非常重要的金属成型工艺,它具有生产成本低、精度高、质量稳定、产量大、成型速度快等优势,可以大大改善传统的机械加工工艺,为工业生产提供了质量高、工艺简单、成本低的零部件替代方案。
粉末注射成型技术介绍

粉末注射成型技术介绍粉末注射成形概述:粉末注射成形(Powder Injection Molding,PIM)由金属粉末注射成形(Metal Injection Molding,MIM)与陶瓷粉末注射成形(Ceramics Injection Molding,CIM)两部分组成,它是一种新的金属、陶瓷零部件制备技术,它是将塑料注射成形技术引入到粉末冶金领域而形成的一种全新的零部件加工技术。
MIM的基本工艺步骤是:首先选取符合MIM要求的金属粉末和黏结剂,然后在一定温度下采用适当的方法将粉末和黏结剂混合成均匀的喂料,经制粒后再注射成形,获得成形坯(Green Part),再经过脱脂处理后烧结致密化成为最终成品(White Part)。
粉末注射成形技术的特点:粉末注射成形能像生产塑料制品一样,一次成形生产形状复杂的金属、陶瓷零部件。
该工艺技术利用注射方法,保证物料充满模具型腔,也就保证了零件高复杂结构的实现。
以往在传统加工技术中,对于复杂的零件,通常是先分别制作出单个零件,然后再组装;而在使用PIM技术时,可以考虑整合成完整的单一零件,这样大大减少了生产步骤,简化了加工程序。
1、与传统的机械加工、精密铸造相比,制品内部组织结构更均匀;与传统粉末冶金压制∕烧结相比,产品性能更优异,产品尺寸精度高,表面光洁度好,不必进行再加工或只需少量精加工。
金属注射成形工艺可直接成形薄壁结构件,制品形状已能接近或达到最终产品要求,零件尺寸公差一般保持在±0.10%~±0.30%水平,特别对于降低难以进行机械加工的硬质合金的加工成本、减少贵重金属的加工损失尤其具有重要意义。
2、零部件几何形状的自由度高,制件各部分密度均匀、尺寸精度高,适于制造几何形状复杂、精度密高及具有特殊要求的小型零件(0.2~200g)。
3、合金化灵活性好,对于过硬、过脆、难以切削的材料或原料铸造时有偏析或污染的零件,可降低制造成本。
金属粉末注射成型技术规程
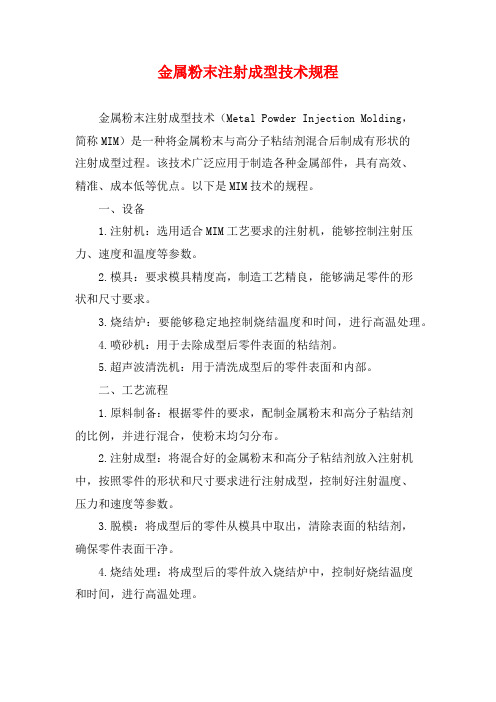
金属粉末注射成型技术规程金属粉末注射成型技术(Metal Powder Injection Molding,简称MIM)是一种将金属粉末与高分子粘结剂混合后制成有形状的注射成型过程。
该技术广泛应用于制造各种金属部件,具有高效、精准、成本低等优点。
以下是MIM技术的规程。
一、设备1.注射机:选用适合MIM工艺要求的注射机,能够控制注射压力、速度和温度等参数。
2.模具:要求模具精度高,制造工艺精良,能够满足零件的形状和尺寸要求。
3.烧结炉:要能够稳定地控制烧结温度和时间,进行高温处理。
4.喷砂机:用于去除成型后零件表面的粘结剂。
5.超声波清洗机:用于清洗成型后的零件表面和内部。
二、工艺流程1.原料制备:根据零件的要求,配制金属粉末和高分子粘结剂的比例,并进行混合,使粉末均匀分布。
2.注射成型:将混合好的金属粉末和高分子粘结剂放入注射机中,按照零件的形状和尺寸要求进行注射成型,控制好注射温度、压力和速度等参数。
3.脱模:将成型后的零件从模具中取出,清除表面的粘结剂,确保零件表面干净。
4.烧结处理:将成型后的零件放入烧结炉中,控制好烧结温度和时间,进行高温处理。
5.机械加工、表面处理:将烧结后的零件进行机械加工和表面处理,使零件达到要求的尺寸和表面粗糙度要求。
6.检验、包装:对成品进行检验,合格后进行包装。
三、质量控制1.原料质量控制:保证金属粉末和高分子粘结剂的质量符合规定要求,严格管控原料供应商。
2.工艺参数控制:精细控制注射温度、压力和速度等参数,保证零件的成型质量。
3.产品检验:对成品进行尺寸、外观等方面的检验,并严格把关。
4.持续改进:根据生产实际情况,不断优化工艺流程,提高生产效率和产品质量。
四、安全生产1.操作人员应接受严格的培训和考核,熟练掌握操作技能和注意安全规定。
2.设备维护保养应按时按方法进行。
3.操作过程中,严格遵守操作规程和安全规定,确保人身和设备安全。
以上就是金属粉末注射成型技术规程,通过规范化的操作流程和严格的品质控制,可以达到生产出高品质、高精度的金属零件的目的。
金属粉末注射成型技术(MIM)工艺原理介绍
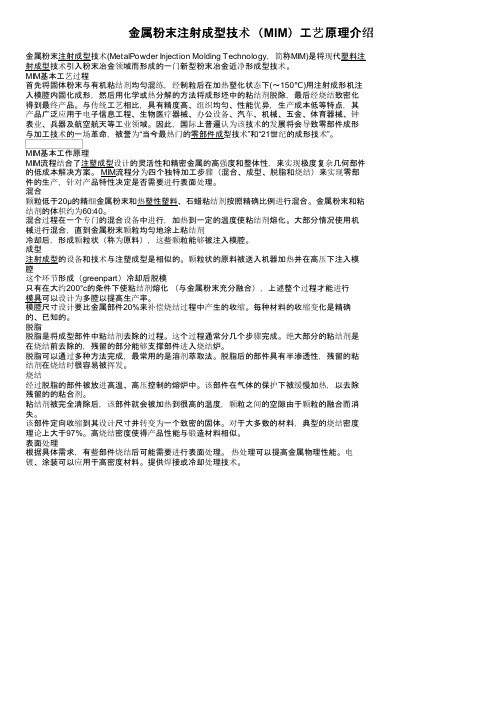
金属粉末注射成型技术(MIM)工艺原理介绍金属粉末注射成型技术(MetalPowder Injection Molding Technology,简称MIM)是将现代塑料注射成型技术引入粉末冶金领域而形成的一门新型粉末冶金近净形成型技术。
MIM基本工艺过程首先将固体粉末与有机粘结剂均匀混练,经制粒后在加热塑化状态下(~150℃)用注射成形机注入模腔内固化成形,然后用化学或热分解的方法将成形坯中的粘结剂脱除,最后经烧结致密化得到最终产品。
与传统工艺相比,具有精度高、组织均匀、性能优异,生产成本低等特点,其产品广泛应用于电子信息工程、生物医疗器械、办公设备、汽车、机械、五金、体育器械、钟表业、兵器及航空航天等工业领域。
因此,国际上普遍认为该技术的发展将会导致零部件成形与加工技术的一场革命,被誉为“当今最热门的零部件成型技术”和“21世纪的成形技术”。
MIM基本工作原理MIM流程结合了注塑成型设计的灵活性和精密金属的高强度和整体性,来实现极度复杂几何部件的低成本解决方案。
MIM流程分为四个独特加工步骤(混合、成型、脱脂和烧结)来实现零部件的生产,针对产品特性决定是否需要进行表面处理。
混合颗粒低于20µ的精细金属粉末和热塑性塑料、石蜡粘结剂按照精确比例进行混合。
金属粉末和粘结剂的体积约为60:40。
混合过程在一个专门的混合设备中进行,加热到一定的温度使粘结剂熔化。
大部分情况使用机械进行混合,直到金属粉末颗粒均匀地涂上粘结剂冷却后,形成颗粒状(称为原料),这些颗粒能够被注入模腔。
成型注射成型的设备和技术与注塑成型是相似的。
颗粒状的原料被送入机器加热并在高压下注入模腔这个环节形成(greenpart)冷却后脱模只有在大约200°c的条件下使粘结剂熔化(与金属粉末充分融合),上述整个过程才能进行模具可以设计为多腔以提高生产率。
模腔尺寸设计要比金属部件20%来补偿烧结过程中产生的收缩。
每种材料的收缩变化是精确的、已知的。
金属粉末注塑成型技术
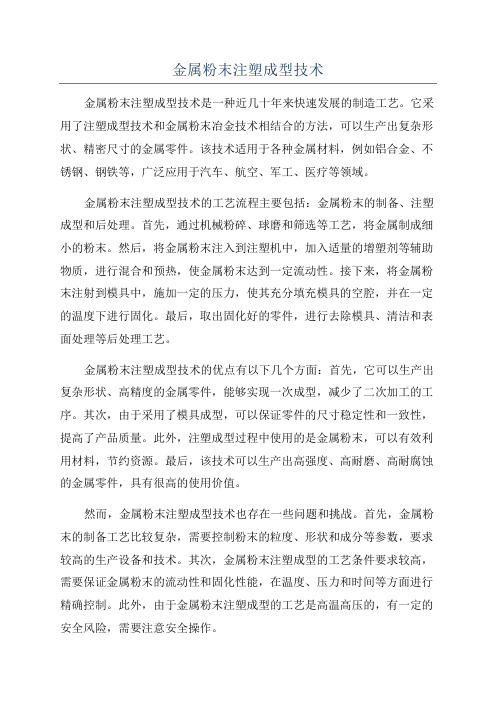
金属粉末注塑成型技术金属粉末注塑成型技术是一种近几十年来快速发展的制造工艺。
它采用了注塑成型技术和金属粉末冶金技术相结合的方法,可以生产出复杂形状、精密尺寸的金属零件。
该技术适用于各种金属材料,例如铝合金、不锈钢、钢铁等,广泛应用于汽车、航空、军工、医疗等领域。
金属粉末注塑成型技术的工艺流程主要包括:金属粉末的制备、注塑成型和后处理。
首先,通过机械粉碎、球磨和筛选等工艺,将金属制成细小的粉末。
然后,将金属粉末注入到注塑机中,加入适量的增塑剂等辅助物质,进行混合和预热,使金属粉末达到一定流动性。
接下来,将金属粉末注射到模具中,施加一定的压力,使其充分填充模具的空腔,并在一定的温度下进行固化。
最后,取出固化好的零件,进行去除模具、清洁和表面处理等后处理工艺。
金属粉末注塑成型技术的优点有以下几个方面:首先,它可以生产出复杂形状、高精度的金属零件,能够实现一次成型,减少了二次加工的工序。
其次,由于采用了模具成型,可以保证零件的尺寸稳定性和一致性,提高了产品质量。
此外,注塑成型过程中使用的是金属粉末,可以有效利用材料,节约资源。
最后,该技术可以生产出高强度、高耐磨、高耐腐蚀的金属零件,具有很高的使用价值。
然而,金属粉末注塑成型技术也存在一些问题和挑战。
首先,金属粉末的制备工艺比较复杂,需要控制粉末的粒度、形状和成分等参数,要求较高的生产设备和技术。
其次,金属粉末注塑成型的工艺条件要求较高,需要保证金属粉末的流动性和固化性能,在温度、压力和时间等方面进行精确控制。
此外,由于金属粉末注塑成型的工艺是高温高压的,有一定的安全风险,需要注意安全操作。
对于金属粉末注塑成型技术的研究和发展,目前存在一些热点和趋势。
首先,随着3D打印技术的发展,金属粉末注塑成型技术与3D打印技术的结合成为研究的热点之一、其次,注塑成型工艺参数和模具设计对产品质量和性能的影响也是研究的重点。
此外,新型材料和合金的研发,以及注塑成型技术在新兴领域的应用也是未来的研究方向。
MIM金属粉末注塑成型技术介绍
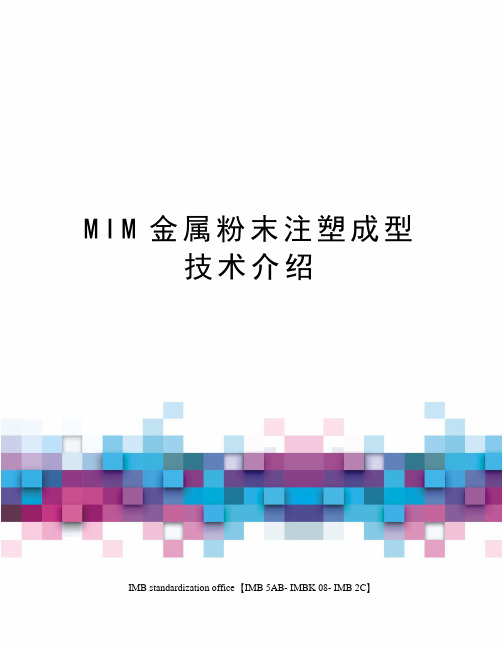
M I M金属粉末注塑成型技术介绍IMB standardization office【IMB 5AB- IMBK 08- IMB 2C】M I M(金属粉末注塑成型)技术介绍MIM是将现代塑料注射成形技术引入粉末冶金领域而形成的一种全新的金属零部件近净成形加工技术,是近年来粉末冶金学科和工业领域中发展十分迅猛的一项高新技术。
MIM的工艺步骤是:首先选取符合MIM要求的金属粉末与有机粘结剂在一定温度条件下采用适当的方法混合成均匀的喂料,然后经制粒后在加热塑化状态下用注射成形机注入模具型腔内获得成形坯,再经过化学或溶剂萃取的方法脱脂处理,最后经烧结致密化得到最终产品。
MIM产品的特点:1、零部件几何形状的自由度高,能像生产塑料制品一样,一次成形生产形状复杂的金属零部件;2、MIM产品密度均匀、光洁度好,表面粗糙度可达到~μm,重量范围在~200g。
尺寸精度高(±%~±%),一般无需后续加工;3、适用材料范围宽,应用领域广,原材料利用率高,生产自动化程度高,工序简单,可实现连续大批量生产;4、产品质量稳定、性能可靠,制品的相对密度可达95%~99%,可进行渗碳、淬火、回火等热处理。
产品强度、硬度、延伸率等力学性能高,耐磨性好,耐疲劳,组织均匀;国际上普遍认为MIM技术的发展将会导致零部件成形与加工技术的一场革命,被誉为“21世纪最热门的零部件的成形技术”。
MIM可以制造复杂形状的产品,避免更多的二次机加工。
MIM产品密度高、耐蚀性好、强度高、延展性好。
MIM可以将2个或更多PM产品组合成一个MIM产品,节省材料和工序。
MIM设计可以节省材料、降低重量。
MIM可以将注射后的浇口料重复破碎使用,不影响产品性能,材料利用率高。
MIM通过模具一次成形复杂产品,避免多道加工工序。
MIM可以制造难以机械加工材料的复杂形状零件。
MIM可以制造薄壁产品,最薄可以做到。
MIM产品表面粗糙度更好。
MIM更适宜制细盲孔和通孔。
金属粉末注射成形工艺

金属粉末注射成形工艺金属粉末注射成形,又被称为金属三维打印,是一种先进的制造技术,可以快速、高效地制造出复杂形状的金属零部件。
该工艺使用金属粉末作为原料,通过注射成形技术将粉末逐层堆积并熔化,最终形成所需的零部件。
金属粉末注射成形工艺主要包括以下几个步骤:1. 材料准备:首先需要选择适合的金属粉末作为原料,常用的金属粉末包括不锈钢、铝合金、钛合金等。
这些粉末需要经过筛分、分类和预处理等工艺,以保证其质量和性能。
2. 粉末注射:将经过处理的金属粉末注入注射成形机中,通过气压或机械力推动粉末向成型腔体注入,并形成具有预定形状的初模。
3. 粉末固化:在注射成形过程中,粉末通过高温或加热装置进行固化,使其达到一定的强度和硬度。
固化后的金属粉末形成一层层的堆积。
4. 层层熔化:通过高能激光束或电子束熔化技术,对已固化的粉末进行局部加热,使其熔化并与下一层的金属粉末融合在一起。
重复这个过程,直到完成整个零件的制造。
5. 后处理:完成熔化过程后,金属零件需要经过去渣、退火、热处理等后续工艺,以进一步提高零件的性能,去除残留的应力和瑕疵。
金属粉末注射成形工艺具有以下优点:1. 快速高效:相比传统的制造工艺,金属粉末注射成形工艺可以大大缩短制造周期,节约人力和时间成本。
2. 复杂形状:金属粉末注射成形技术可以制造出具有复杂形状的零部件,包括中空结构、内腔结构等。
3. 材料选择多样:金属粉末注射成形工艺可以使用多种金属粉末作为原料,满足不同材料性能和需求。
4. 资源节约:由于金属粉末注射成形工艺是按需制造,不需要额外加工或切割,可以最大限度地节约材料,减少废料产生。
然而,金属粉末注射成形工艺也存在一些挑战,如技术难度高、成本较高等。
随着技术的不断进步和成熟,相信金属粉末注射成形工艺将在未来得到更广泛的应用,成为制造业领域的新宠。
金属粉末注射成形工艺是一项颇具潜力的新兴制造技术,它在汽车、航空航天、医疗器械等许多行业都有广泛应用的前景。
粉末冶金与陶瓷材料成型工艺流程讲义
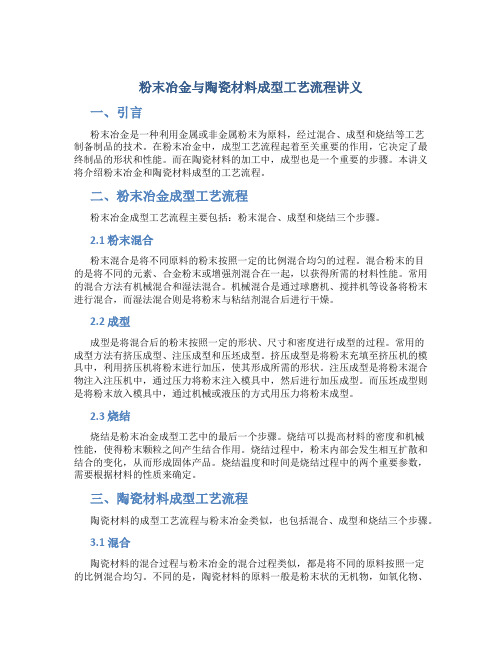
粉末冶金与陶瓷材料成型工艺流程讲义一、引言粉末冶金是一种利用金属或非金属粉末为原料,经过混合、成型和烧结等工艺制备制品的技术。
在粉末冶金中,成型工艺流程起着至关重要的作用,它决定了最终制品的形状和性能。
而在陶瓷材料的加工中,成型也是一个重要的步骤。
本讲义将介绍粉末冶金和陶瓷材料成型的工艺流程。
二、粉末冶金成型工艺流程粉末冶金成型工艺流程主要包括:粉末混合、成型和烧结三个步骤。
2.1 粉末混合粉末混合是将不同原料的粉末按照一定的比例混合均匀的过程。
混合粉末的目的是将不同的元素、合金粉末或增强剂混合在一起,以获得所需的材料性能。
常用的混合方法有机械混合和湿法混合。
机械混合是通过球磨机、搅拌机等设备将粉末进行混合,而湿法混合则是将粉末与粘结剂混合后进行干燥。
2.2 成型成型是将混合后的粉末按照一定的形状、尺寸和密度进行成型的过程。
常用的成型方法有挤压成型、注压成型和压坯成型。
挤压成型是将粉末充填至挤压机的模具中,利用挤压机将粉末进行加压,使其形成所需的形状。
注压成型是将粉末混合物注入注压机中,通过压力将粉末注入模具中,然后进行加压成型。
而压坯成型则是将粉末放入模具中,通过机械或液压的方式用压力将粉末成型。
2.3 烧结烧结是粉末冶金成型工艺中的最后一个步骤。
烧结可以提高材料的密度和机械性能,使得粉末颗粒之间产生结合作用。
烧结过程中,粉末内部会发生相互扩散和结合的变化,从而形成固体产品。
烧结温度和时间是烧结过程中的两个重要参数,需要根据材料的性质来确定。
三、陶瓷材料成型工艺流程陶瓷材料的成型工艺流程与粉末冶金类似,也包括混合、成型和烧结三个步骤。
3.1 混合陶瓷材料的混合过程与粉末冶金的混合过程类似,都是将不同的原料按照一定的比例混合均匀。
不同的是,陶瓷材料的原料一般是粉末状的无机物,如氧化物、碳化物和氮化物等。
混合的目的是将不同的材料混合在一起,以获得所需的陶瓷组分。
3.2 成型陶瓷材料的成型方法有很多种,常见的有干压成型、注塑成型和注浆成型等。
金属粉末注射成型工艺技术
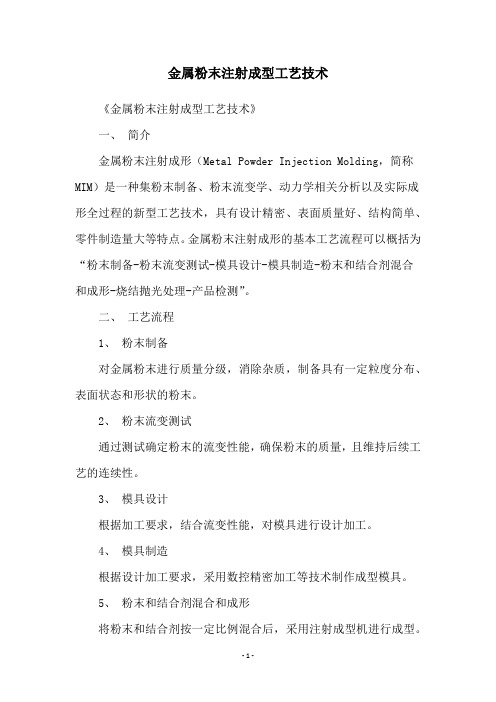
金属粉末注射成型工艺技术
《金属粉末注射成型工艺技术》
一、简介
金属粉末注射成形(Metal Powder Injection Molding,简称MIM)是一种集粉末制备、粉末流变学、动力学相关分析以及实际成形全过程的新型工艺技术,具有设计精密、表面质量好、结构简单、零件制造量大等特点。
金属粉末注射成形的基本工艺流程可以概括为“粉末制备-粉末流变测试-模具设计-模具制造-粉末和结合剂混合
和成形-烧结抛光处理-产品检测”。
二、工艺流程
1、粉末制备
对金属粉末进行质量分级,消除杂质,制备具有一定粒度分布、表面状态和形状的粉末。
2、粉末流变测试
通过测试确定粉末的流变性能,确保粉末的质量,且维持后续工艺的连续性。
3、模具设计
根据加工要求,结合流变性能,对模具进行设计加工。
4、模具制造
根据设计加工要求,采用数控精密加工等技术制作成型模具。
5、粉末和结合剂混合和成形
将粉末和结合剂按一定比例混合后,采用注射成型机进行成型。
6、烧结抛光处理
根据加工要求,对模具内产品进行烧结,最后经过抛光处理。
7、产品检测
根据加工要求,对产品进行检测,确保产品的质量。
三、应用
金属粉末注射成型工艺技术目前主要应用于制造精密复杂零件,如电子行业的传感器、电子及工具手柄、锁扣件、电动机转子及维修重要零件、汽车行业的汽车零部件等。
金属的粉末注射成型技术
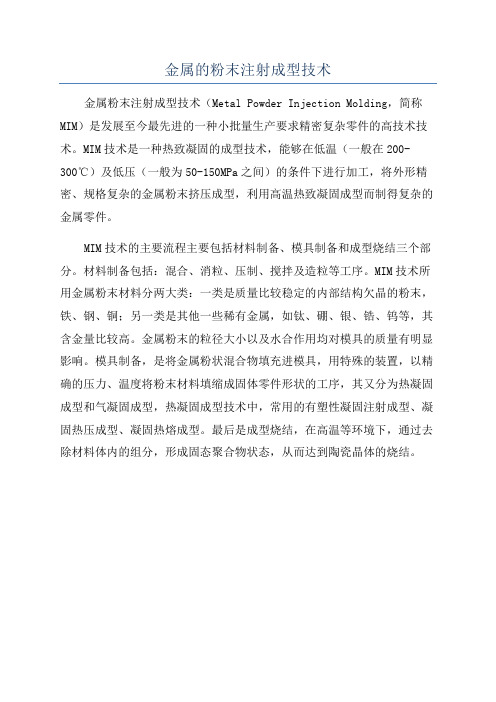
金属的粉末注射成型技术
金属粉末注射成型技术(Metal Powder Injection Molding,简称MIM)是发展至今最先进的一种小批量生产要求精密复杂零件的高技术技术。
MIM技术是一种热致凝固的成型技术,能够在低温(一般在200-300℃)及低压(一般为50-150MPa之间)的条件下进行加工,将外形精密、规格复杂的金属粉末挤压成型,利用高温热致凝固成型而制得复杂的金属零件。
MIM技术的主要流程主要包括材料制备、模具制备和成型烧结三个部分。
材料制备包括:混合、消粒、压制、搅拌及造粒等工序。
MIM技术所用金属粉末材料分两大类:一类是质量比较稳定的内部结构欠晶的粉末,铁、钢、铜;另一类是其他一些稀有金属,如钛、硼、银、锆、钨等,其含金量比较高。
金属粉末的粒径大小以及水合作用均对模具的质量有明显影响。
模具制备,是将金属粉状混合物填充进模具,用特殊的装置,以精确的压力、温度将粉末材料填缩成固体零件形状的工序,其又分为热凝固成型和气凝固成型,热凝固成型技术中,常用的有塑性凝固注射成型、凝固热压成型、凝固热熔成型。
最后是成型烧结,在高温等环境下,通过去除材料体内的组分,形成固态聚合物状态,从而达到陶瓷晶体的烧结。
金属粉末注射成型工艺流程
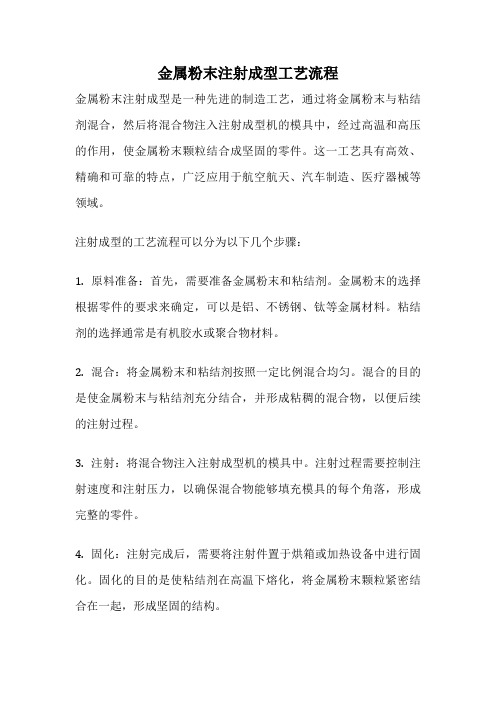
金属粉末注射成型工艺流程金属粉末注射成型是一种先进的制造工艺,通过将金属粉末与粘结剂混合,然后将混合物注入注射成型机的模具中,经过高温和高压的作用,使金属粉末颗粒结合成坚固的零件。
这一工艺具有高效、精确和可靠的特点,广泛应用于航空航天、汽车制造、医疗器械等领域。
注射成型的工艺流程可以分为以下几个步骤:1. 原料准备:首先,需要准备金属粉末和粘结剂。
金属粉末的选择根据零件的要求来确定,可以是铝、不锈钢、钛等金属材料。
粘结剂的选择通常是有机胶水或聚合物材料。
2. 混合:将金属粉末和粘结剂按照一定比例混合均匀。
混合的目的是使金属粉末与粘结剂充分结合,并形成粘稠的混合物,以便后续的注射过程。
3. 注射:将混合物注入注射成型机的模具中。
注射过程需要控制注射速度和注射压力,以确保混合物能够填充模具的每个角落,形成完整的零件。
4. 固化:注射完成后,需要将注射件置于烘箱或加热设备中进行固化。
固化的目的是使粘结剂在高温下熔化,将金属粉末颗粒紧密结合在一起,形成坚固的结构。
5. 后处理:固化后的零件需要进行后处理,包括除去粘结剂残留物、去除表面缺陷、热处理等。
后处理的目的是提高零件的密度和强度,并使其达到设计要求。
金属粉末注射成型工艺流程简单而有效,能够生产出复杂形状的零件,具有较高的精度和良好的表面质量。
与传统的金属加工方法相比,注射成型工艺无需进行复杂的切削和加工过程,节约了原材料和能源,降低了生产成本。
同时,注射成型还能够实现零件的批量生产,提高生产效率。
然而,金属粉末注射成型工艺也存在一些挑战。
首先,注射成型过程中需要控制好粉末颗粒的分布和流动性,以确保零件的均匀性和一致性。
其次,粘结剂的选择和控制对零件的质量和性能有重要影响,需要进行细致的调整和优化。
此外,注射成型工艺还存在一定的限制,对于形状复杂、壁厚较大的零件难以实现。
随着科学技术的不断发展,金属粉末注射成型工艺将得到进一步改进和应用。
未来,注射成型工艺有望实现更高的精度和更广泛的应用领域,为制造业的发展带来新的机遇和挑战。
金属粉末注射成型技术
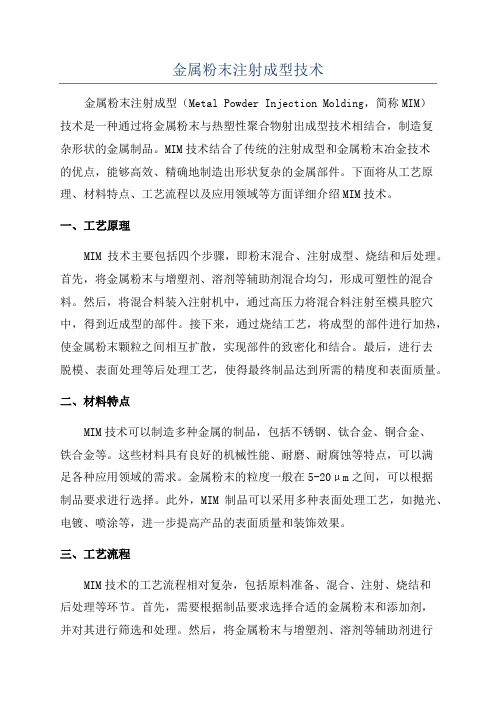
金属粉末注射成型技术金属粉末注射成型(Metal Powder Injection Molding,简称MIM)技术是一种通过将金属粉末与热塑性聚合物射出成型技术相结合,制造复杂形状的金属制品。
MIM技术结合了传统的注射成型和金属粉末冶金技术的优点,能够高效、精确地制造出形状复杂的金属部件。
下面将从工艺原理、材料特点、工艺流程以及应用领域等方面详细介绍MIM技术。
一、工艺原理MIM技术主要包括四个步骤,即粉末混合、注射成型、烧结和后处理。
首先,将金属粉末与增塑剂、溶剂等辅助剂混合均匀,形成可塑性的混合料。
然后,将混合料装入注射机中,通过高压力将混合料注射至模具腔穴中,得到近成型的部件。
接下来,通过烧结工艺,将成型的部件进行加热,使金属粉末颗粒之间相互扩散,实现部件的致密化和结合。
最后,进行去脱模、表面处理等后处理工艺,使得最终制品达到所需的精度和表面质量。
二、材料特点MIM技术可以制造多种金属的制品,包括不锈钢、钛合金、铜合金、铁合金等。
这些材料具有良好的机械性能、耐磨、耐腐蚀等特点,可以满足各种应用领域的需求。
金属粉末的粒度一般在5-20μm之间,可以根据制品要求进行选择。
此外,MIM制品可以采用多种表面处理工艺,如抛光、电镀、喷涂等,进一步提高产品的表面质量和装饰效果。
三、工艺流程MIM技术的工艺流程相对复杂,包括原料准备、混合、注射、烧结和后处理等环节。
首先,需要根据制品要求选择合适的金属粉末和添加剂,并对其进行筛选和处理。
然后,将金属粉末与增塑剂、溶剂等辅助剂进行混合,形成可塑性的混合料。
接下来,将混合料装入注射机中,通过高压力将混合料注射至模具腔穴中。
然后,将近成型的部件进行烧结,使其实现致密化和结合。
最后,通过去脱模、除渣、表面处理等后处理工艺,得到最终的金属部件。
四、应用领域MIM技术的应用领域非常广泛,包括电子通讯、汽车工业、医疗器械、军工等领域。
在电子通讯领域,MIM技术可以制造小型高精度的连接器、插件等零部件,满足电子设备不断减小体积和提高性能的需求。
金属(陶瓷)粉末注射成型技术(MIM).
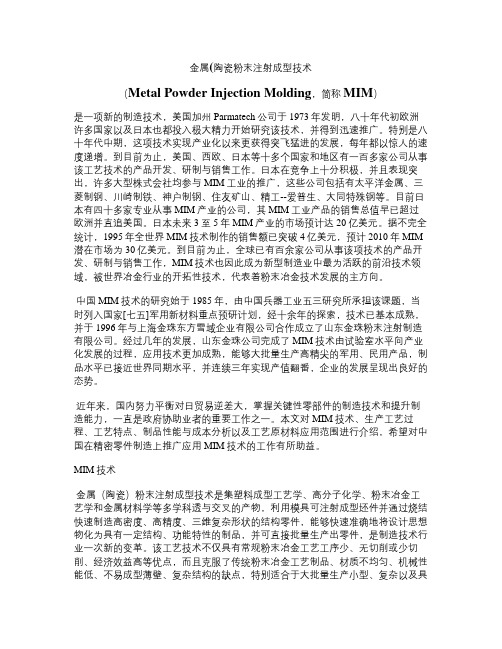
金属(陶瓷粉末注射成型技术(Metal Powder Injection Molding,简称MIM)是一项新的制造技术,美国加州Parmatech公司于1973年发明,八十年代初欧洲许多国家以及日本也都投入极大精力开始研究该技术,并得到迅速推广。
特别是八十年代中期,这项技术实现产业化以来更获得突飞猛进的发展,每年都以惊人的速度递增。
到目前为止,美国、西欧、日本等十多个国家和地区有一百多家公司从事该工艺技术的产品开发、研制与销售工作。
日本在竞争上十分积极,并且表现突出,许多大型株式会社均参与MIM工业的推广,这些公司包括有太平洋金属、三菱制钢、川崎制铁、神户制钢、住友矿山、精工--爱普生、大同特殊钢等。
目前日本有四十多家专业从事MIM产业的公司,其MIM工业产品的销售总值早已超过欧洲并直追美国。
日本未来3至5年MIM产业的市场预计达20亿美元。
据不完全统计,1995年全世界MIM技术制作的销售额已突破4亿美元,预计2010年MIM 潜在市场为30亿美元。
到目前为止,全球已有百余家公司从事该项技术的产品开发、研制与销售工作,MIM技术也因此成为新型制造业中最为活跃的前沿技术领域,被世界冶金行业的开拓性技术,代表着粉末冶金技术发展的主方向。
中国MIM技术的研究始于1985年,由中国兵器工业五三研究所承担该课题,当时列入国家[七五]军用新材料重点预研计划,经十余年的探索,技术已基本成熟,并于1996年与上海金珠东方雪域企业有限公司合作成立了山东金珠粉末注射制造有限公司。
经过几年的发展,山东金珠公司完成了MIM技术由试验室水平向产业化发展的过程,应用技术更加成熟,能够大批量生产高精尖的军用、民用产品,制品水平已接近世界同期水平,并连续三年实现产值翻番,企业的发展呈现出良好的态势。
近年来,国内努力平衡对日贸易逆差大,掌握关键性零部件的制造技术和提升制造能力,一直是政府协助业者的重要工作之一。
本文对MIM技术、生产工艺过程、工艺特点、制品性能与成本分析以及工艺原材料应用范围进行介绍,希望对中国在精密零件制造上推广应用MIM技术的工作有所助益。
金属粉末注射成型工艺技术
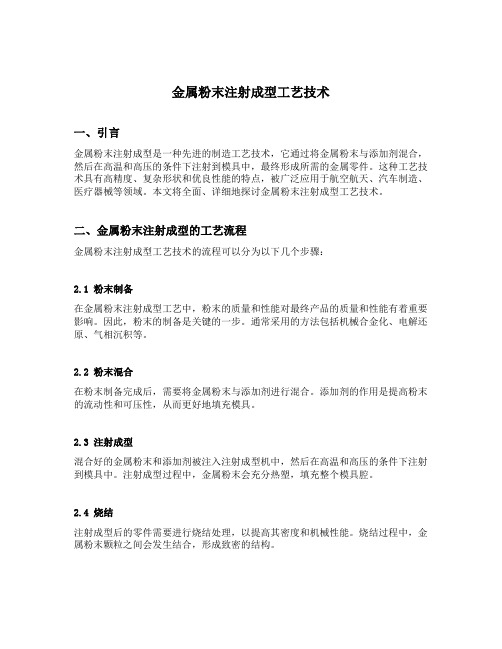
金属粉末注射成型工艺技术一、引言金属粉末注射成型是一种先进的制造工艺技术,它通过将金属粉末与添加剂混合,然后在高温和高压的条件下注射到模具中,最终形成所需的金属零件。
这种工艺技术具有高精度、复杂形状和优良性能的特点,被广泛应用于航空航天、汽车制造、医疗器械等领域。
本文将全面、详细地探讨金属粉末注射成型工艺技术。
二、金属粉末注射成型的工艺流程金属粉末注射成型工艺技术的流程可以分为以下几个步骤:2.1 粉末制备在金属粉末注射成型工艺中,粉末的质量和性能对最终产品的质量和性能有着重要影响。
因此,粉末的制备是关键的一步。
通常采用的方法包括机械合金化、电解还原、气相沉积等。
2.2 粉末混合在粉末制备完成后,需要将金属粉末与添加剂进行混合。
添加剂的作用是提高粉末的流动性和可压性,从而更好地填充模具。
2.3 注射成型混合好的金属粉末和添加剂被注入注射成型机中,然后在高温和高压的条件下注射到模具中。
注射成型过程中,金属粉末会充分热塑,填充整个模具腔。
2.4 烧结注射成型后的零件需要进行烧结处理,以提高其密度和机械性能。
烧结过程中,金属粉末颗粒之间会发生结合,形成致密的结构。
2.5 后处理经过烧结处理后的零件可能需要进行后处理,如去除表面氧化层、研磨抛光等,以提高表面质量和精度。
三、金属粉末注射成型的优势和应用金属粉末注射成型工艺技术具有以下优势:3.1 高精度金属粉末注射成型可以制造出复杂形状的零件,并且具有较高的尺寸精度和表面质量。
3.2 材料利用率高金属粉末注射成型可以有效利用原材料,减少材料浪费。
3.3 机械性能优良经过烧结处理的金属粉末注射成型零件具有较高的密度和机械性能,可以满足各种工程应用的需求。
金属粉末注射成型工艺技术在许多领域得到了广泛应用:3.4 航空航天领域金属粉末注射成型可以制造出轻量化、高强度的零件,满足航空航天领域对材料性能和质量的要求。
3.5 汽车制造领域金属粉末注射成型可以制造出复杂形状的汽车零件,提高汽车的性能和安全性。
金属、陶瓷粉末注射成型工艺简介

金属、陶瓷粉末注射成型工艺简介:金属、陶瓷粉末注射成型工艺技术是一种将粉末冶金工艺、粉末陶瓷工艺与塑料注射成型工艺相结合的新型制造工艺技术。
该工艺技术适合大批量生产小型、精密、复杂及具有特殊性能要求的金属陶瓷零件的制造。
该工艺的基本过程是:将微细的金属或陶瓷粉末与有机粘结剂均匀混合成为具有流变性的物料,采用先进的注射机注入具有零件形状的模腔形成坯件,新技术脱除粘结剂并经烧结,使其高度致密成为制品,必要时还可以进行后处理。
金属、陶瓷粉末注射成型工艺技术是近年来世界粉末冶金领域发展最快的高新技术。
该工艺技术的研究起始于70年代末,由于它适用性强、市场广阔,而且潜力巨大,所以一出现,便受到普遍重视,发展非常迅速。
美国、日本和西欧等发达国家率先形成产业规模。
1、粉末注射成型工艺特点:1)零部件几何形状的自由度高,制件各部分密度均匀、尺寸精度高,适于制造几何形状复杂、精密及具有特殊要求的小型零件(0.05g-200g);2)合金化灵活性好,对于过硬、过脆、难以切削的材料或原料铸造时有偏析或污染的零件,可降低制造成本;3)产品质量稳定、性能可靠,制品的相对密宽可达92-98%,可进行渗碳、淬火、回火等处理;4)加工零件的典型公差为±0.05mm;5)工艺流程短、生产效率高,易于实现大批量、规模化生产;2、粉末注射成型适用的材料:主要有Fe合金、Fe-Ni合金、不锈钢、Kovar合金、W合金、钛合金、Stellite Si-Fe合金、Hastelloy 合金、硬质合金、永磁合金及氧化铝、氮化硅、氧化锆等陶瓷材料。
3、粉末注射成型技术的应用领域:计算机及其辅助设施:如打印机零件、磁头、磁芯、撞针轴销、驱动零件;工具:如钻头、刀头、喷丸咀、枪钻、螺旋铣刀、冲头、套筒、扳手、电工工具、手工工具等;家用器具:如表壳、表链、电动牙刷、剪刀、风扇、高尔夫球头、珠宝链环、圆珠笔卡箍、照相机用等零件;医疗机械用零件:如牙矫形架、剪刀、镊子;军用零件:导弹尾翼、枪支零件、弹头、药型罩、引信用零件;电气用零件:微型马达、电子零件、传感器件;机械用零件:如松棉机、纺织机、卷边机、办公机械等;。
- 1、下载文档前请自行甄别文档内容的完整性,平台不提供额外的编辑、内容补充、找答案等附加服务。
- 2、"仅部分预览"的文档,不可在线预览部分如存在完整性等问题,可反馈申请退款(可完整预览的文档不适用该条件!)。
- 3、如文档侵犯您的权益,请联系客服反馈,我们会尽快为您处理(人工客服工作时间:9:00-18:30)。
来源于:注塑塑胶网
金属或陶瓷粉末注塑成型工艺
使用金属或陶瓷粉末通过注塑成型工艺生产复杂零件
如今,使用粉末材料的注塑成型技术主要用于制造工业用复杂组件。
粉末注塑成型是除了其它成型工艺(精密铸造和轴向或均衡压制)外的另一种可供选择的工艺。
近年来,用陶瓷或金属粉末来制造注塑成型零件的应用领域主要包括汽车工业、刀具工业、磁体生产、纺织工业、钟表工业、家居用品、精密工程、医疗和牙科技术以及陶瓷工业。
在 ARBURG PIM 实验室,客户可以通过实际观看样品生产来了解粉末注塑的优点。
表1: 金属和陶瓷组件的典型公差
粉末注塑成型技术使组件的批量生产成为可能,因为采用机械加工或压制技术进行批量生产已经不再是一种经济有效的方式。
注塑成型技术使组件的设计和制造过程具有几乎无限的自由度。
粉末注塑成型制造过程包括成型零件的初始注塑成型、脱脂和烧结。
组件公差由以下重要因素确定:
● 粘合剂含量
● 粉末特性
● 混合过程
● 注塑成型参数
● 重力变形
● 在烧结托盘上的滑动性能
可用材料范围广泛
原则上,所有细颗粒、可烧结的粉末都可以和相应的粘合剂混合并在注塑机上加工。
包括氧化陶瓷、金属、碳化物及氮化物。
由于混合和注塑设备在处理粉末材料的过程中会受到较强磨损,因此建议选择粒度尽可能小的粉末。
较细的粉末可降低表面粗糙度,从而在加工过程中降低磨损并提高生坯强度。
各种粉末材料的性能范围如表3中所示。
表2: 在严格的公差范围内的高重复性
粘合剂使粉末可用来注塑
对粘合剂最重要的要求是:脱脂过程中的尺寸稳定性、良好的保存特性、不与粉末材料发生反应、很高的零件强度、良好的脱模特性、热稳定性和在脱脂过程中易于去除并可完全去除。
粘合剂与粉末颗粒之间的粘附力还应尽可能高,以便在注塑过程中增高压力不会使两个组份分离,而导致填充的零件不均匀。
为了获得良好的注塑成型特性并以低收缩率获得均匀的烧结质量,建议采用球形粉末。
具有最佳配比的粘合剂与粉末
在混合过程中,粘合剂和粉末混合成一种匀质的混合物,即原料。
市场上有出售金属粉末和陶瓷粉末的原料供货商。
他们供应的材料品种繁多,并不断推出新品。
因此,MIM(金属注塑成型)或 CIM(陶瓷注塑成型)所需的原料都是现成的,可立即用于注塑,而不再需要内部制作。
如果可用材料的性能不能充分满足所需的用途,专业化的材料供货商可以开发并生产客户需要的特定原料。
注塑成型过程中的加工步骤
用原料(粉末/粘合剂的混合物)制造成型零件的过程与塑料的注塑成型过程相似。
▲ 预塑
在塑化单元中,原料的粘合剂部分会在温度的作用下熔化。
▲ 注塑
塑料混合物在高压下被注塑到固定在锁模装置中的模具中。
模具保持闭合,同时成型零件硬化。
▲ 开模
在零件冷却后,喷嘴会通过注塑装置的移动从模具位置移开。
锁模装置打开,注塑成型机的顶针系统会自动顶出成型零件。
▲ 零件脱模
使用机械手系统从模具中脱出易碎的零件而不造成损坏。
在粉末材料的注塑成型时,推荐使用此工艺来保护绿件免受震动或冲击,从而避免损害成型零件的质量。