发动机曲轴结构设计
曲柄连杆机构设计
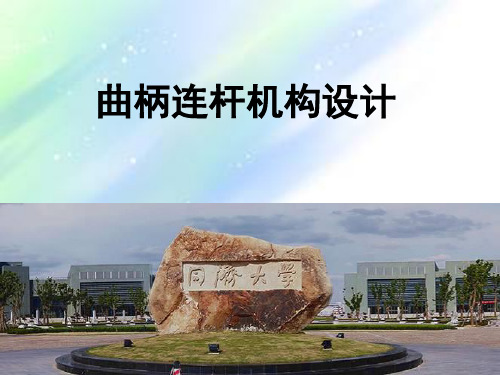
活塞和连杆小头 ➢ 往复直线运动,速度高、不断变化 ➢ 上止点下止点,速度变化规律:
零增大最大(临近中间)减小零 活塞向下运动:
前半行程加速运动,惯性力向上,Fj; 后半行程减速运动,惯性力向下,F’j 活塞向上运动:
前半行程惯性力向下 后半行程惯性力向上
往复惯性力与离心力 Parts inertia and centrifugal force
设在前端。 2. 止推轴承设置在后端则可以避免曲轴各曲拐承受功率消耗者的轴向推
力的作用。 3. 从降低曲轴和机体加工尺寸链精度要求出发,也可设在曲轴中央。
11、曲轴的油封装置
发动机工作时,为了防止曲轴前后端沿着轴向漏油,曲轴应有油封装置。在高 速内燃机上采用的油封结构都是组合式的,常用的有: 1)甩油盘和反油螺纹; 2)甩油盘和填料(石棉绳)油封; 3)甩油盘和橡胶骨架式油封;
螺钉可能承受剪切力,要设计定位凸台或定位齿。
8、油孔的位置和尺寸
将润滑油输送到曲轴油道中去的供油方法有两种: ①集中供油 ②分路供油 ①润滑油一般从机体上的主轴油道通过主轴承的上轴瓦引入。因为上轴瓦仅承受惯性 力的作用,比下轴瓦受力要低一些。 ②从主轴颈向曲柄销供油一般采用斜油道。直的斜油道结构最简单,但有两个主要缺 点:一是油道位于曲拐平面内,油道出口处应力集中现象严重。二是斜油道相对轴承 摩擦面是倾斜的,润滑油中的杂质受离心力的作用总是冲向轴承的一边。
1.、曲轴的工作情况、设计要求 曲轴是内燃机中价格最贵的重要零件。曲轴的成本大致占整机成本的
1/10 。 曲轴承受着不断周期性变化的缸内气体作用力、往复惯性力和旋转惯性
力引起的周期性变化的弯曲和扭转负荷。 曲轴还可能承受扭转振动引起的附加扭转应力 。 曲轴最常见的损坏原因是弯曲疲劳。所以,保证曲轴有足够的疲劳强度
发动机曲轴箱结构形式

发动机曲轴箱结构形式发动机曲轴箱是发动机的关键部件之一,它的结构形式不仅直接关系到整个发动机的性能,还关系到整个车辆的使用寿命和动力性能。
在现代汽车制造业中,发动机曲轴箱结构形式的发展日新月异,当然这肯定是经历了几十年的历史经验积累和不断的技术创新才达到的。
第一步,我们需要了解什么是发动机曲轴箱。
其实,它就是一个实心箱体,位于发动机下部,内部放置着曲轴,它将活塞发出的冲击力转换成旋转动力,从而推动车轮运行。
发动机曲轴箱材料常见的有铸铁、镁合金、铝合金等,不同的工艺制造出来的材料对于曲轴箱的加工精度有着不同的要求。
第二步,是了解发动机曲轴箱的结构形式。
目前发动机曲轴箱的结构形式主要有以下几种。
第一种,是传统式单块式发动机曲轴箱,这种结构适合重型商用车型,因为它可以大大减少车辆在工作中所产生的震动,提高车辆的稳定性。
第二种结构形式是模块化设计的多块式发动机曲轴箱,这种结构可以根据车型定制来拼接不同的模块,能够灵活应对不同乘用车型的需求。
第三种,则是用于高端轿车上的半单块式发动机曲轴箱,在相对较小的空间内,可以达到更好的密封性和减少空气阻力的优势。
第三步,是对发动机曲轴箱的细节要求。
想要发动机曲轴箱有更好的性能,还有很多细节方面需要注意。
首先是对曲轴箱的密封性要求,因为曲轴箱是和发动机密切相关的,容易受到发动机内部高温高压的影响,所以密封性非常重要。
其次是曲轴箱的振动和噪声要求,发动机曲轴箱的制造加工精度非常高,以达到减少车辆振动和噪声的目的。
除此之外,还有一些其他的要求,比如曲轴箱要有足够的刚度,以便对发动机的动力反作用力有一个更好的承载能力,同时为润滑系统、散热系统、进气系统等发动机各要素提供一个平稳牢靠的支撑。
总的来说,发动机曲轴箱的结构形式还有很多值得探讨和研究的方面,从材料、结构到加工工艺,都有重要的影响和作用。
在未来的发展过程中,更高性能、更安全可靠的发动机曲轴箱,将会成为不可避免的趋势。
发动机曲轴结构设计
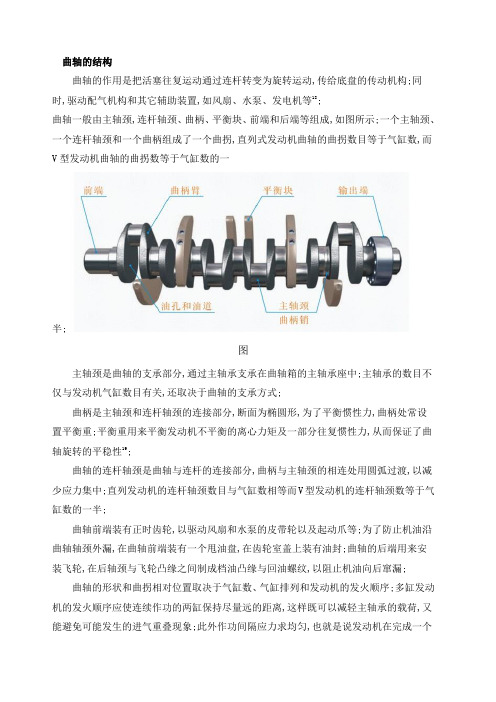
曲轴的结构曲轴的作用是把活塞往复运动通过连杆转变为旋转运动,传给底盘的传动机构;同时,驱动配气机构和其它辅助装置,如风扇、水泵、发电机等18;曲轴一般由主轴颈,连杆轴颈、曲柄、平衡块、前端和后端等组成,如图所示;一个主轴颈、一个连杆轴颈和一个曲柄组成了一个曲拐,直列式发动机曲轴的曲拐数目等于气缸数,而V型发动机曲轴的曲拐数等于气缸数的一半;图主轴颈是曲轴的支承部分,通过主轴承支承在曲轴箱的主轴承座中;主轴承的数目不仅与发动机气缸数目有关,还取决于曲轴的支承方式;曲柄是主轴颈和连杆轴颈的连接部分,断面为椭圆形,为了平衡惯性力,曲柄处常设置平衡重;平衡重用来平衡发动机不平衡的离心力矩及一部分往复惯性力,从而保证了曲轴旋转的平稳性19;曲轴的连杆轴颈是曲轴与连杆的连接部分,曲柄与主轴颈的相连处用圆弧过渡,以减少应力集中;直列发动机的连杆轴颈数目与气缸数相等而V型发动机的连杆轴颈数等于气缸数的一半;曲轴前端装有正时齿轮,以驱动风扇和水泵的皮带轮以及起动爪等;为了防止机油沿曲轴轴颈外漏,在曲轴前端装有一个甩油盘,在齿轮室盖上装有油封;曲轴的后端用来安装飞轮,在后轴颈与飞轮凸缘之间制成档油凸缘与回油螺纹,以阻止机油向后窜漏;曲轴的形状和曲拐相对位置取决于气缸数、气缸排列和发动机的发火顺序;多缸发动机的发火顺序应使连续作功的两缸保持尽量远的距离,这样既可以减轻主轴承的载荷,又能避免可能发生的进气重叠现象;此外作功间隔应力求均匀,也就是说发动机在完成一个工作循环的曲轴转角内,每个气缸都应发火作功一次,以保证发动机运转平稳;曲轴的作用:它与连杆配合将作用在活塞上的气体压力变为旋转的动力,传给底盘的传动机构;同时,驱动配气机构和其它辅助装置,如风扇、水泵、发电机等;工作时,曲轴承受气体压力,惯性力及惯性力矩的作用,受力大而且受力复杂,并且承受交变负荷的冲击作用;同时,曲轴又是高速旋转件,因此,要求曲轴具有足够的刚度和强度,具有良好的承受冲击载荷的能力,耐磨损且润滑良好20;曲轴的疲劳损坏形式曲轴的工作情况十分复杂,它是在周期性变化的燃气作用力、往复运动和旋转运动惯性力及其他力矩作用下工作的,因而承受着扭转和弯曲的复杂应力;曲轴箱主轴承的不同心度会影响到曲轴的受力状况,其次,由于曲轴弯曲与扭转振动而产生的附加应力,再加上曲轴形状复杂,结构变化急剧,产生了严重的应力集中;最后曲轴主轴颈与曲柄销是在比压下进行高速转动,因而产生强烈的磨损;因此柴油机在运转中发生曲轴裂纹和断裂事故不为鲜见,尤其是发电柴油机曲轴疲劳破坏较多;依曲轴产生裂纹的交变应力的性质不同,主要有以下三种疲劳裂纹:弯曲疲劳裂纹、扭转疲劳裂纹和弯曲一扭转疲劳裂纹21,如图所示;图 1-弯曲疲劳裂纹 2-扭转疲劳裂纹弯曲疲劳裂纹曲轴的弯曲疲劳裂纹一般发生在主轴颈或曲柄销颈与曲柄臂连接的过渡圆角处,或逐渐扩展成横断曲柄臂的裂纹,或形成垂直轴线的裂纹;弯曲疲劳试验表明,过渡圆角处的最大应力出现在曲柄臂中心对称线下方;应力沿曲轴长度方向的分布是在中间的和端部的曲柄有较大的弯曲应力峰值;因此,曲轴弯曲疲劳裂纹常发生在曲轴的中间或两端的曲柄上;曲轴弯曲疲劳破坏通常是在柴油机经过较长时间运转之后发生;因为长时间运转后柴油机的各道主轴承磨损不均匀,使曲轴轴线弯曲变形,曲轴回转时产生过大的附加交变弯曲应力;此外,曲轴的曲柄臂、曲柄箱或轴承支座机座等的刚性不足,柴油机短时间运转后,也会使曲轴产生弯曲疲劳破坏;扭转疲劳裂纹曲轴在扭转力矩作用下产生交变的扭转应力,存在扭振时还会产生附加交变扭转应力,严重时会引起曲轴的扭转疲劳破坏;扭转疲劳裂纹一般发生在曲轴上应力集中严重的油孔或过渡圆角处,并在轴颈上沿着与轴线成45°角的两个方向扩展;这是因为轴颈的抗扭截面模数较曲柄臂的小,所以扭转疲劳裂纹多自过渡圆角向轴颈扩展,而很少向曲柄臂扩展;但若同时存在较强的弯曲应力,则裂纹也可自圆角向曲柄臂扩展,造成曲柄臂弯曲断裂;通常扭转疲劳裂纹发生在曲辆扭振节点附近的曲柄上;发生扭砖疲劳裂纹的时间一般是在柴油机运转初期和曲轴的临界转速位于工作转速范围内时;扭转疲劳断裂的断面与轴线相交成45°角,断面上的裂纹线近似螺旋线2223;弯曲--扭转疲劳裂纹曲轴的疲劳破坏还可能是由于弯曲与扭转共同作用造成;常常由于主轴承不均匀磨损造成曲轴上产生弯曲疲劳裂纹,继而在弯曲与扭转的共同作用下使裂纹扩展、断裂,最后断裂面与轴线成45°角;断面上自疲劳源起约2/3的面积为贝纹区,呈暗褐色;剩余l/3的面积为最后断裂区,断面凹凸不平,晶粒明亮;圆形波纹状纹理是弯曲疲劳造成的,放射状纹理是扭转疲劳造成的,两种纹理交织成蛛网状;弯曲一扭转疲劳裂纹有时也呈以弯曲疲劳为主或以扭转疲劳为主的破坏形式;因此,在具体情况下,应根据断面上的纹理、裂纹方向和最后断裂区进行分析判断24;生产中,曲轴的弯曲疲劳破坏远远多于钮转疲劳破坏;其主要原因是由于曲轴弯曲应力集中系数大于扭转应力集中系数,曲轴的弯曲应力难于精确计算和控制;柴油机运转中,曲轴的各道主轴承磨损是很难掌握和计算的,由它所引起的曲轴变形和附加弯曲应力也就难于讨算和控制了;相反,曲轴的扭转应力可以通过计算准确掌握,并可采取有效的减振措施予以平衡,只要避免柴油机在临界转速运转和扭转应力过载,曲轴的扭转疲劳破坏就会得以控制25;曲轴的设计要求根据上述曲轴的损坏形式及其原因,且为避免这些损坏,曲轴在设计过程中应尽量满足以下的要求:1.具有足够的疲劳强度,以保证曲轴工作可靠;尽量减小应力集中,加强薄弱环节;2.具有足够的弯曲和扭转刚度,使曲轴变形不致过大,以免恶化活塞连杆组及轴承的工作条件;3.轴颈就有良好的耐磨性,保证曲轴和轴承有足够的寿命;4.曲柄的排列应合理,以保证柴油机工作均匀,曲轴平衡性良好,以减少振动和主轴承最大负荷;5.材料选择适当,制造方便26;曲轴的结构型式曲轴的支承方式一般有两种,一种是全支承曲轴,其曲轴的主轴颈数比气缸数目多一个,即每一个连杆轴颈两边都有一个主轴颈;这种支承,曲轴的强度和刚度都比较好,并且减轻了主轴承载荷,减小了磨损;柴油机和大部分汽油机多采用这种形式;另一种是非全支承曲轴;其曲轴的主轴颈数比气缸数目少或与气缸数目相等;这种支承方式叫非全支承曲轴,虽然这种支承的主轴承载荷较大,但缩短了曲轴的总长度,使发动机的总体长度有所减小;有些汽油机,承受载荷较小可以采用这种曲轴型式27;鉴于本课题所设计的1015柴油机为四缸,故而动机的总体长度较小;且其常用于重型载重车,曲轴的强度及刚度要求都较高,因此设计采用全支承曲轴;曲轴从结构上可分为整体式和组合式;整体式曲轴的毛胚由整根钢料锻造或铸造方法浇铸出来,具有结构简单、加工方便、重量轻、工作可靠、刚度和强度较高等优点;组合式曲轴是分段制造的,铸造时容易保证质量,降低废品率28;锻造时无需较大的锻压设备,制造方便,热处理和机械加工业较方便,并可缩短生产周期;当生产后使用中某个曲柄发现有缺陷时,可以局部更换而不必报废整个曲轴;一般的说,在选择曲轴结构时,只要生产设备允许应该尽可能采用整体式曲轴;在大型柴油机上由于曲轴尺寸与重量都较大,整体制造极为困难是,往往采用组合式曲轴;对于本课题得设计,曲轴的尺寸较小及重量较轻,所以选择整体式的;曲轴的材料曲轴的常用材料根据其毛坯制造方法的不同可分为锻造曲轴材料和铸造曲轴材料两大类;锻造游客分为自由锻、模锻和镦锻;自由锻适用于较小设备生产大型曲轴,但效率太低,加工余量也大;模锻需要一套较贵的锻模设备和较大的锻压设备,生产效率价高;镦锻可节约大量金属材料和机械加工工时,且加工出的曲轴能充分发挥材料的强度;锻造曲轴常用材料为普通碳素钢及合金钢;铸造曲轴常用材料为球墨铸QT60-2、可断铸铁KTZ70-2、合金铸铁及铸钢ZG35等;在强化程度要求不高的内燃机中,一般选用普通碳素钢,碳素钢的韧性比合金钢高,可以降低扭转振动振幅;合金钢多用于强化要求高的柴油机曲轴,其疲劳强度高但对应力集中敏感性大,因而对机械加工要求也高;球墨铸铁价格低廉,制造方便,对应力集中不敏感,并可以通过合理的造型降低应力的集中,还可通过加入合金元素、热处理、表面强化等方法提升其性能;因此对于要求高的强度、塑性、韧性、耐磨性、耐严重的热和机械冲击、耐高温或低温、耐腐蚀以及尺寸稳定性的曲轴较适用29;但球墨铸铁延伸率、冲击韧性、弹性模数及疲劳强度较低,在使用其作为曲轴材料时,应该确保轴颈和曲柄臂厚度较粗;曲轴的材料应具有较高的疲劳强度、必要的硬度以及较好的淬透性;在选取材料是不仅要考虑到机械性能,同时也要考虑工艺性、资源性和经济性;在选择材料时,需要根据内燃机类型、用途及生产条件,确定曲轴毛坯的制造方法;并参考同类近似机型所用材料,根据曲轴受力情况和使用习惯,凭经验选取;根据上述各种毛坯制造方法及材料特点,并结合1015柴油机结构、实际受力状况及用途,本设计曲轴毛坯采用铸造方法,曲轴材料选择球墨铸铁QT60-2;曲轴的主要部件设计主轴颈和曲柄销主轴颈和曲柄销是曲轴最重要的两对摩擦副,他们的设计直接影响了内燃机的工作可靠性、外形尺寸及维修;轴颈的尺寸和结构与曲轴的强度、刚度及润滑条件有密切的关系;曲轴的直径越大,曲轴的刚度也越大,但轴颈直径过大会引起表面圆周速度增大,导致摩擦损失和机油温度的增高;曲柄销直径的增大会引起旋转离心力及转动惯量的剧烈增加,并使连杆大头的尺寸增大,这不利于连杆通过气缸取出,因此在保证轴承比压不变的情况下,采用较大的轴颈直径1D ,减小主轴颈长度1L ,这有利于缩短内燃机的长度或者加大曲柄臂的厚度采用短而粗的主轴颈可提高曲轴扭振的自振频率,减小在工作转速范围内产生共振的可能性;一般情况下曲柄销直径2D 总是小于主轴颈直径1D 30;曲柄臂曲柄臂在曲柄平面内的抗弯曲刚度和强度都较差,往往因受交变弯曲应力而引起断裂;因此曲柄臂是整体曲轴上最薄弱的环节,设计时应注意适当的宽度和厚度,并选择合理的形状,以改善应力的分布状况;增大曲柄臂的厚度和宽度都可以增大曲柄臂的强度,而从提高曲柄臂的抗弯强度来说,增加厚度比增加宽度效果要好得多31;曲轴圆角曲轴主轴颈和曲柄臂连接的圆角称为主轴颈圆角,曲柄销和曲柄臂连接的圆角称为曲柄销圆角;这些过渡圆角能够减小应力集中,提高疲劳强度,其半径的增大与其表面光洁程度的提高,是增加曲轴疲劳强度的有效措施32;曲轴圆角半径r 应足够大,但是圆角半径过小会使应力集中严,而圆角半径的增大会使轴颈承压的有效长度减小,因而也会减小轴承承压面积;为增大曲轴圆角半径,且不缩短轴颈的有效工作长度,可采用沉割圆角,但设计沉割圆角时应注意保证曲柄臂有足够厚度;曲轴圆角也可由半径不同的二圆弧和三圆弧组成,当各段圆弧半径选择适当时可提高曲轴疲劳强度;由于沉割圆角和二圆弧以及三圆弧设计工艺十分的复杂,设计要求较高,以我们现阶段的水平难以得出准确结果,故而本设计采用等圆弧圆角;由柴油机设计手册上可知:r/D≈,即r≈;故取曲轴圆角半径r=;润滑油道轴承的工作能力在很大程度上决定于摩擦表面的额润滑品质;因此,为了保证轴承的可靠性,主轴颈和曲柄销通常都采用压力润滑;曲轴上油道和油孔的设计,对于曲轴轴承的润滑及曲轴强度都有重要的影响,因此必须十分慎重的选择油道方案和确定油孔的位置;将润滑油输送到曲轴油道中去的供油方式有两种:一种是集中供油,即将曲轴内部做成中空的连续孔道,作为内燃机的主油道,机油从曲轴的一端输入曲轴,然后经曲轴内孔串联流向各轴承;另一种是分路供油,即机油从曲轴箱上的主油道并联进入各个主轴承,然后通过曲轴的油道再进入相应的连杆轴承;采用集中供油时,因为机油从一端进入曲轴后需要克服很大的离心力和流动阻力,才能供到另一端的轴承,压力损失较大;为了保持最后润滑的轴承仍有一定的油压,进入轴承的油压必须很高,这使得曲轴油腔的密封结构复杂;因而多数内燃机采用分路供油,且本设计也采用分路供油;油道布置主要根据润滑供油充分和对曲轴疲劳强度的影响来决定,主轴颈上的油孔入口应保证像曲柄销供油充分;曲柄销上的油孔出口应设在较低负荷区,以提高轴瓦的供油能力,油孔的位置应参考轴承负荷图和轴心轨迹图来确定;油道的取向对扭转疲劳强度的影响很显着;图曲轴中油道的布置有很多方式,其中斜线油道在结构上是最简单的,如图所示;但其缺点是曲柄臂与轴颈过渡处被削弱,降低了曲轴的强度,油道与轴颈的表面交线呈椭圆形,斜角愈大椭圆度愈大,油孔边缘处的应力集中就愈严重,斜线油孔加工工艺复杂,为避免上述缺点,可从曲柄臂肩部钻一斜孔,贯通曲柄销和主轴颈,再在此两个轴颈上钻直油孔接通,最后将曲柄臂肩部孔堵死;油道也可布置成如图所示的形式,油孔由曲柄臂钻入到主轴颈,再由曲柄臂和主轴颈表面垂直钻通,这样的油道布置,工艺较为复杂,但能够有效的提高曲轴的疲劳强度;图由于本设计曲轴的轴颈及曲柄臂直径都比较粗,重叠度也比较大,再考虑到油道加工的工艺性,因而本设计油道的布置方式选择斜线油道油道加工的工艺性;平衡重平衡块是用来平衡曲轴不平衡的离心惯性力和离心惯性力矩;设计平衡重时,平衡重应尽可能使其重心远离曲轴旋转中心,即用较轻的重量达到较好的效果,以便尽可能减轻曲轴重量,并且应尽量不增加内燃机的尺寸,在满足动平衡的条件下,还能使曲轴的制造比较方便;曲轴上是否需要安装平衡重和怎样决定平衡重的数目,大小及位置等问题,都要根据内燃机的用途,曲轴形状,常用工况的转速和负荷,结构和工艺上的简便程度等因素来定;曲轴的平衡重可以与与曲轴铸成一体,这样可使加工较简单,并且工作可靠;平衡中亦可单独制造,通过螺栓连接在曲轴的曲柄臂上;本设计平衡重采用单独制造的方法,这样的设计过程较为简单,且可以根据实际需求改动平衡重的设置33;。
汽车发动机的曲轴材料的选择及工艺设计
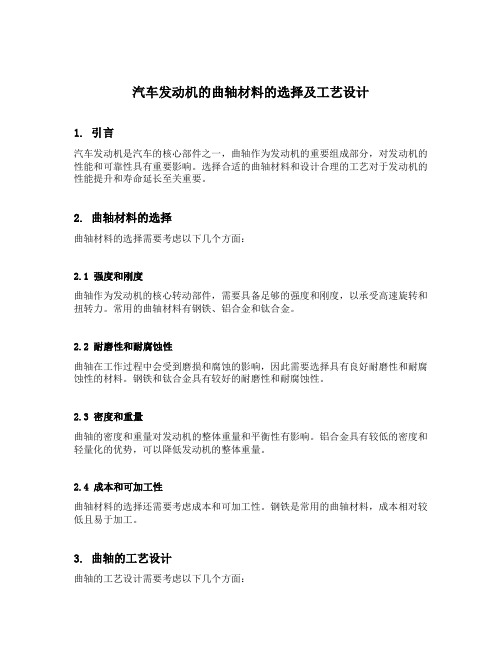
汽车发动机的曲轴材料的选择及工艺设计1. 引言汽车发动机是汽车的核心部件之一,曲轴作为发动机的重要组成部分,对发动机的性能和可靠性具有重要影响。
选择合适的曲轴材料和设计合理的工艺对于发动机的性能提升和寿命延长至关重要。
2. 曲轴材料的选择曲轴材料的选择需要考虑以下几个方面:2.1 强度和刚度曲轴作为发动机的核心转动部件,需要具备足够的强度和刚度,以承受高速旋转和扭转力。
常用的曲轴材料有钢铁、铝合金和钛合金。
2.2 耐磨性和耐腐蚀性曲轴在工作过程中会受到磨损和腐蚀的影响,因此需要选择具有良好耐磨性和耐腐蚀性的材料。
钢铁和钛合金具有较好的耐磨性和耐腐蚀性。
2.3 密度和重量曲轴的密度和重量对发动机的整体重量和平衡性有影响。
铝合金具有较低的密度和轻量化的优势,可以降低发动机的整体重量。
2.4 成本和可加工性曲轴材料的选择还需要考虑成本和可加工性。
钢铁是常用的曲轴材料,成本相对较低且易于加工。
3. 曲轴的工艺设计曲轴的工艺设计需要考虑以下几个方面:3.1 曲轴的结构设计曲轴的结构设计需要满足发动机的工作要求和空间限制。
曲轴的结构包括曲柄、连杆和偏心轴等部分,需要合理设计以实现发动机的正常工作和高效能。
3.2 曲轴的热处理曲轴的热处理是提高曲轴强度和耐磨性的重要工艺步骤。
常用的热处理方法包括淬火、回火和表面渗碳等,可以提高曲轴的硬度和耐磨性。
3.3 曲轴的加工工艺曲轴的加工工艺需要考虑到曲轴的复杂形状和高精度要求。
常用的加工工艺包括车削、磨削和磨齿等,可以实现曲轴的精确加工和高质量要求。
3.4 曲轴的平衡设计曲轴的平衡设计是提高发动机平稳性和减少振动的重要环节。
通过合理的平衡设计,可以降低曲轴和发动机的振动和噪音,提高发动机的工作效率和舒适性。
4. 总结汽车发动机的曲轴材料的选择及工艺设计对于发动机的性能和可靠性具有重要影响。
合理选择曲轴材料,结合适当的工艺设计,可以提高曲轴的强度、耐磨性和耐腐蚀性,同时降低发动机的重量和振动,实现发动机的高效能和长寿命。
毕业设计发动机曲轴加工工艺分析与设计

毕业设计发动机曲轴加工工艺分析与设计引言发动机曲轴作为发动机的重要部件之一,在发动机工作过程中起到连接活塞和驱动传动机构的作用。
曲轴的质量和加工工艺直接影响发动机的性能和可靠性。
因此,针对毕业设计课题,本文将对发动机曲轴的加工工艺进行分析与设计。
1. 毕业设计课题背景随着汽车行业的不断发展,对发动机的要求越来越高。
而曲轴作为发动机的核心部件之一,具有复杂的形状结构和精密的加工要求。
因此,对发动机曲轴的加工工艺进行分析与设计,能够提高发动机的性能和可靠性。
2. 发动机曲轴的加工工艺分析2.1 曲轴的材料选择曲轴通常采用高强度合金钢材料,如40Cr、42CrMo等。
选择合适的材料可以保证曲轴具有足够的强度和硬度,以及良好的耐磨性。
2.2 曲轴的加工工艺流程曲轴的加工主要包括以下几个环节: 1. 初加工:包括锻造成型、粗车、粗磨等工艺,将原材料初步加工成近似形状的曲轴毛坯。
2. 精加工:包括细车、细磨、细磨光等工艺,对曲轴进行精细加工,使其达到设计要求的尺寸和表面质量。
3.热处理:通过热处理工艺对曲轴进行淬火或回火,提高曲轴的强度和硬度,以及更好的耐磨性。
4. 零件组装:将曲轴和其他相关部件进行组装,组成完整的发动机曲轴系统。
2.3 曲轴加工工艺中的关键技术在曲轴的加工过程中,有几个关键技术需要特别注意: 1. 切削力控制:控制切削力的大小和方向,避免过大的切削力对刀具和工件产生损伤。
2. 加工精度控制:控制加工精度的达到设计要求,特别是曲轴主轴段的圆度、圆柱度和轴向偏差等指标。
3. 表面质量控制:通过抛光等工艺控制曲轴表面的光洁度和平整度,以减小曲轴在工作过程中的摩擦损失和功耗。
3. 发动机曲轴加工工艺设计基于对发动机曲轴加工工艺的分析,可以进行如下的工艺设计: 1. 确定合适的材料:根据曲轴的设计要求,选择合适的高强度合金钢材料作为毛坯材料。
2. 设计加工工艺流程:根据曲轴的形状和尺寸要求,设计合理的加工工艺流程,包括初加工、精加工、热处理和零件组装等环节。
MSC柴油发动机曲轴疲劳分析示例
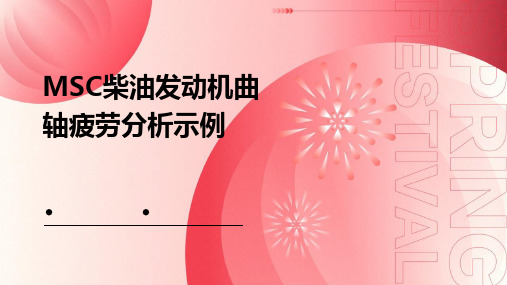
曲轴疲劳寿命预测
01
应力-寿命法(S-N法)
通过测试不同应力和循环次数下材料的断裂寿命,建立应力与寿命的关
系曲线,用于预测曲轴的疲劳寿命。
02
局部应变法(ε-N法)
通过测量曲轴局部区域的应变和循环次数,计算材料的疲劳寿命。该方
法考虑了应力集中的影响,更适用于预测曲轴的疲劳寿命。
03
有限元分析(FEA)
曲轴疲劳损伤机制
弯曲疲劳
由于周期性的弯矩作用,曲轴在 应力集中的位置(如轴颈和曲拐 的过渡区域)容易发生弯曲疲劳
断裂。
扭转疲劳
周期性的扭矩作用使曲轴在轴颈和 曲拐的过渡区域产生剪切应力,可 能导致扭转疲劳断裂。
热疲劳
由于温度变化引起的热应力,可能 导致曲轴材料内部产生微裂纹,进 而扩展形成疲劳裂纹。
详细描述
该案例针对曲轴的结构和工艺参数进行了优化设计,如改变曲轴的形状、增加 加强筋等。通过有限元分析和疲劳试验验证了优化设计的有效性,发现这些改 进能够显著提高曲轴的抗疲劳性能和疲劳寿命。
05
结论与展望
疲劳分析在MSC柴油发动机曲轴设计中的重要性
疲劳分析是评估曲轴结构强度和寿命 的关键手段,通过分析可以预测曲轴 在不同工况下的疲劳损伤和断裂风险。
在船舶领域,柴油发动机曲轴作为船 舶推进系统的关键部件,需承受高负 荷和极端环境条件下的运转。
在发电机组领域,柴油发动机曲轴用 于驱动发电机,要求具有高效率和可 靠性。
02
疲劳分析基本原理
疲劳定义与分类
疲劳定义
疲劳是由于材料或结构在循环应力或 应变下逐渐损伤和失效的现象。
疲劳分类
根据应力类型和循环特性,疲劳可分 为高周疲劳和低周疲劳,其中高周疲 劳是指循环次数大于10^4的疲劳,低 周疲劳是指循环次数小于10^4的疲劳 。
发动机曲轴加工工艺及其夹具设计
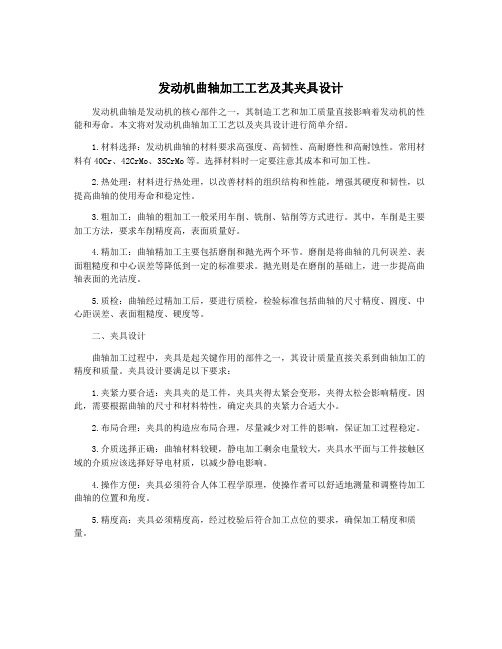
发动机曲轴加工工艺及其夹具设计发动机曲轴是发动机的核心部件之一,其制造工艺和加工质量直接影响着发动机的性能和寿命。
本文将对发动机曲轴加工工艺以及夹具设计进行简单介绍。
1.材料选择:发动机曲轴的材料要求高强度、高韧性、高耐磨性和高耐蚀性。
常用材料有40Cr、42CrMo、35CrMo等。
选择材料时一定要注意其成本和可加工性。
2.热处理:材料进行热处理,以改善材料的组织结构和性能,增强其硬度和韧性,以提高曲轴的使用寿命和稳定性。
3.粗加工:曲轴的粗加工一般采用车削、铣削、钻削等方式进行。
其中,车削是主要加工方法,要求车削精度高,表面质量好。
4.精加工:曲轴精加工主要包括磨削和抛光两个环节。
磨削是将曲轴的几何误差、表面粗糙度和中心误差等降低到一定的标准要求。
抛光则是在磨削的基础上,进一步提高曲轴表面的光洁度。
5.质检:曲轴经过精加工后,要进行质检,检验标准包括曲轴的尺寸精度、圆度、中心距误差、表面粗糙度、硬度等。
二、夹具设计曲轴加工过程中,夹具是起关键作用的部件之一,其设计质量直接关系到曲轴加工的精度和质量。
夹具设计要满足以下要求:1.夹紧力要合适:夹具夹的是工件,夹具夹得太紧会变形,夹得太松会影响精度。
因此,需要根据曲轴的尺寸和材料特性,确定夹具的夹紧力合适大小。
2.布局合理:夹具的构造应布局合理,尽量减少对工件的影响,保证加工过程稳定。
3.介质选择正确:曲轴材料较硬,静电加工剩余电量较大,夹具水平面与工件接触区域的介质应该选择好导电材质,以减少静电影响。
4.操作方便:夹具必须符合人体工程学原理,使操作者可以舒适地测量和调整待加工曲轴的位置和角度。
5.精度高:夹具必须精度高,经过校验后符合加工点位的要求,确保加工精度和质量。
发动机曲轴毕业论文

成都工业学院毕业设计(论文)设计(论文)题目:发动机曲轴工艺设计及钻中心孔夹具和钻斜油孔夹具设计系部名称:机电工程系专业:数控技术专业班级:09423学生姓名:学号:指导教师:二O一二年五月摘要曲轴是发动机上的一个重要的旋转机件,装上连杆后,可承接活塞的上下(往复)运动变成循环运动。
曲轴主要有两个重要加工部位:主轴颈和连杆颈。
主轴颈被安装在缸体上,连杆颈与连杆大头孔连接,连杆小头孔与汽缸活塞连接,是一个典型的曲柄滑块机构。
发动机工作过程就是:活塞经过混合压缩气的燃爆,推动活塞做直线运动,并通过连杆将力传给曲轴,由曲轴将直线运动转变为旋转运动。
而曲轴加工的好坏将直接影响着发动机整体性能的表现。
曲轴的材料一般为35、40、45钢或球墨铸铁QT600-2,曲轴有两个重要部位:主轴颈,连杆颈。
本次采用45钢,设计的主要就是这两方面的在数控机床的加工。
集合多种的曲轴加工后,深入分析了曲轴的加工工艺。
关键词:曲轴主轴劲夹具连杆劲数控加工AbstractThe crankshaft is an important engine rotating parts, fitted with linking, you can undertake up and down the piston (reciprocating) motion into circular motion. The crankshaft main two important processing areas: the main journal and rod neck. Spindle neck to be installed on the cylinder block, connecting rod journal and connecting rod hole connection, connect the connecting rod small end hole and the cylinder piston, is a typical slider-crank mechanism. Engine working process: the piston after the blasting of the mixed compressed gas pushes the piston linear motion and force to the crankshaft through the connecting rod, the linear motion into rotary motion by the crankshaft. The crankshaft processing will directly affect the overall performance of the engine performance. The material of the crankshaft is made of carbon structural steel or ductile iron, there are two important areas: the main journal rod neck. This paper introduces the fixture design of the engine crankshaft process design of the two processes. Ensure product quality, increase productivity, reduce costs, make full use of the existing production conditions to ensure workers have designed under the premise of a good and safe working conditions. In process design, the author combines practical theory of design, traditional crankshaft production process improvements, optimizing processes and process equipment, production and processing more economical and reasonable so that the crankshaft. Fixture design part of the collection of processing machine tools, cutting tools and auxiliary tools and other relevant information used based on the workpiece material, structural features, technical requirements and process analysis, in accordance with the fixture design steps to design a line with the crankshaft production process and fixture manufacturing requirements of the fixture.目录摘要 (I)Abstract (II)目录..................................................................................................................................................... 第1章绪论.. (1)1.1 课题研究的意义及现状 (1)1.2 论文主要研究内容 (2)第2章发动机曲轴零件图分析 (3)2.1曲轴的作用分析 (3)2.2曲轴的结构及其特点 (3)2.3曲轴的主要技术要求分析 (4)2.4曲轴的材料和毛坯的确定 (4)第3章工艺规程设计 (5)3.1 计算生产纲领,确定生产类型 (5)3.2 选择毛坯 (5)3.3 工艺过程设计 (5)3.3.1定位基准的选择 (5)3.3.2加工阶段的划分与工序顺序的安排 (6)3.3.3制定工艺路线 (7)3.4 确定加工余量 (10)3.4.1确定机械加工余量 (11)3.4.2设计毛坯图(一)确定毛坯尺寸公差 (12)3.5重要工序设计 (15)3.5.1选择加工设备和工艺装备 (15)3.6 确定切削用量及基本工时 (17)3.6.1曲轴主要加工表面的工序安排 (17)3.6.2确定工时定额 (17)3.6.3粗磨第一主轴颈和齿轮轴颈 (19)3.6.4精车二、三、五、主轴颈、油封轴颈、法兰 (19)3.6.5切槽 (20)3.6.6精车第三主轴颈及过渡圆角 (20)第4章夹具设计 (24)4.1 机床夹具的分类、基本组成和功用 (24)4.2发动机曲轴夹具的设计思路 (24)4.2.1形状复杂 (24)4.2.2刚性差 (24)4.2.3技术要求高 (25)4.3铣曲轴两端面打中心孔夹具 (25)4.3.1零件的工艺性分析: (25)4.3.2零件机械加工工艺路线制定: (25)4.3.3夹具结构方案确定 (27)4.3.4其它装置和夹具体确定 (29)4.3.5定位误差分析计算 (31)4.3.6夹具结构及操作介绍 (33)4.3.7本设计的主要优缺点 (34)总结....................................................................................................................错误!未定义书签。
- 1、下载文档前请自行甄别文档内容的完整性,平台不提供额外的编辑、内容补充、找答案等附加服务。
- 2、"仅部分预览"的文档,不可在线预览部分如存在完整性等问题,可反馈申请退款(可完整预览的文档不适用该条件!)。
- 3、如文档侵犯您的权益,请联系客服反馈,我们会尽快为您处理(人工客服工作时间:9:00-18:30)。
发动机曲轴结构设计 Document number:PBGCG-0857-BTDO-0089-PTT1998曲轴的结构曲轴的作用是把活塞往复运动通过连杆转变为旋转运动,传给底盘的传动机构。
同时,驱动配气机构和其它辅助装置,如风扇、水泵、发电机等【18】。
曲轴一般由主轴颈,连杆轴颈、曲柄、平衡块、前端和后端等组成,如图所示。
一个主轴颈、一个连杆轴颈和一个曲柄组成了一个曲拐,直列式发动机曲轴的曲拐数目等于气缸数,而V型发动机曲轴的曲拐数等于气缸数的一半。
图主轴颈是曲轴的支承部分,通过主轴承支承在曲轴箱的主轴承座中。
主轴承的数目不仅与发动机气缸数目有关,还取决于曲轴的支承方式。
曲柄是主轴颈和连杆轴颈的连接部分,断面为椭圆形,为了平衡惯性力,曲柄处常设置平衡重。
平衡重用来平衡发动机不平衡的离心力矩及一部分往复惯性力,从而保证了曲轴旋转的平稳性【19】。
曲轴的连杆轴颈是曲轴与连杆的连接部分,曲柄与主轴颈的相连处用圆弧过渡,以减少应力集中。
直列发动机的连杆轴颈数目与气缸数相等而V型发动机的连杆轴颈数等于气缸数的一半。
曲轴前端装有正时齿轮,以驱动风扇和水泵的皮带轮以及起动爪等。
为了防止机油沿曲轴轴颈外漏,在曲轴前端装有一个甩油盘,在齿轮室盖上装有油封。
曲轴的后端用来安装飞轮,在后轴颈与飞轮凸缘之间制成档油凸缘与回油螺纹,以阻止机油向后窜漏。
曲轴的形状和曲拐相对位置取决于气缸数、气缸排列和发动机的发火顺序。
多缸发动机的发火顺序应使连续作功的两缸保持尽量远的距离,这样既可以减轻主轴承的载荷,又能避免可能发生的进气重叠现象。
此外作功间隔应力求均匀,也就是说发动机在完成一个工作循环的曲轴转角内,每个气缸都应发火作功一次,以保证发动机运转平稳。
曲轴的作用:它与连杆配合将作用在活塞上的气体压力变为旋转的动力,传给底盘的传动机构。
同时,驱动配气机构和其它辅助装置,如风扇、水泵、发电机等。
工作时,曲轴承受气体压力,惯性力及惯性力矩的作用,受力大而且受力复杂,并且承受交变负荷的冲击作用。
同时,曲轴又是高速旋转件,因此,要求曲轴具有足够的刚度和强度,具有良好的承受冲击载荷的能力,耐磨损且润滑良好【20】。
曲轴的疲劳损坏形式曲轴的工作情况十分复杂,它是在周期性变化的燃气作用力、往复运动和旋转运动惯性力及其他力矩作用下工作的,因而承受着扭转和弯曲的复杂应力。
曲轴箱主轴承的不同心度会影响到曲轴的受力状况,其次,由于曲轴弯曲与扭转振动而产生的附加应力,再加上曲轴形状复杂,结构变化急剧,产生了严重的应力集中。
最后曲轴主轴颈与曲柄销是在比压下进行高速转动,因而产生强烈的磨损。
因此柴油机在运转中发生曲轴裂纹和断裂事故不为鲜见,尤其是发电柴油机曲轴疲劳破坏较多。
依曲轴产生裂纹的交变应力的性质不同,主要有以下三种疲劳裂纹:弯曲疲劳裂纹、扭转疲劳裂纹和弯曲一扭转疲劳裂纹【21】,如图所示。
图 1-弯曲疲劳裂纹 2-扭转疲劳裂纹弯曲疲劳裂纹曲轴的弯曲疲劳裂纹一般发生在主轴颈或曲柄销颈与曲柄臂连接的过渡圆角处,或逐渐扩展成横断曲柄臂的裂纹,或形成垂直轴线的裂纹。
弯曲疲劳试验表明,过渡圆角处的最大应力出现在曲柄臂中心对称线下方。
应力沿曲轴长度方向的分布是在中间的和端部的曲柄有较大的弯曲应力峰值。
因此,曲轴弯曲疲劳裂纹常发生在曲轴的中间或两端的曲柄上。
曲轴弯曲疲劳破坏通常是在柴油机经过较长时间运转之后发生。
因为长时间运转后柴油机的各道主轴承磨损不均匀,使曲轴轴线弯曲变形,曲轴回转时产生过大的附加交变弯曲应力。
此外,曲轴的曲柄臂、曲柄箱或轴承支座(机座)等的刚性不足,柴油机短时间运转后,也会使曲轴产生弯曲疲劳破坏。
扭转疲劳裂纹曲轴在扭转力矩作用下产生交变的扭转应力,存在扭振时还会产生附加交变扭转应力,严重时会引起曲轴的扭转疲劳破坏。
扭转疲劳裂纹一般发生在曲轴上应力集中严重的油孔或过渡圆角处,并在轴颈上沿着与轴线成45°角的两个方向扩展。
这是因为轴颈的抗扭截面模数较曲柄臂的小,所以扭转疲劳裂纹多自过渡圆角向轴颈扩展,而很少向曲柄臂扩展。
但若同时存在较强的弯曲应力,则裂纹也可自圆角向曲柄臂扩展,造成曲柄臂弯曲断裂。
通常扭转疲劳裂纹发生在曲辆扭振节点附近的曲柄上。
发生扭砖疲劳裂纹的时间一般是在柴油机运转初期和曲轴的临界转速位于工作转速范围内时。
扭转疲劳断裂的断面与轴线相交成45°角,断面上的裂纹线近似螺旋线【22】【23】。
弯曲--扭转疲劳裂纹曲轴的疲劳破坏还可能是由于弯曲与扭转共同作用造成。
常常由于主轴承不均匀磨损造成曲轴上产生弯曲疲劳裂纹,继而在弯曲与扭转的共同作用下使裂纹扩展、断裂,最后断裂面与轴线成45°角。
断面上自疲劳源起约2/3的面积为贝纹区,呈暗褐色;剩余l/3的面积为最后断裂区,断面凹凸不平,晶粒明亮。
圆形波纹状纹理是弯曲疲劳造成的,放射状纹理是扭转疲劳造成的,两种纹理交织成蛛网状。
弯曲一扭转疲劳裂纹有时也呈以弯曲疲劳为主或以扭转疲劳为主的破坏形式。
因此,在具体情况下,应根据断面上的纹理、裂纹方向和最后断裂区进行分析判断【24】。
生产中,曲轴的弯曲疲劳破坏远远多于钮转疲劳破坏。
其主要原因是由于曲轴弯曲应力集中系数大于扭转应力集中系数,曲轴的弯曲应力难于精确计算和控制。
柴油机运转中,曲轴的各道主轴承磨损是很难掌握和计算的,由它所引起的曲轴变形和附加弯曲应力也就难于讨算和控制了。
相反,曲轴的扭转应力可以通过计算准确掌握,并可采取有效的减振措施予以平衡,只要避免柴油机在临界转速运转和扭转应力过载,曲轴的扭转疲劳破坏就会得以控制【25】。
曲轴的设计要求根据上述曲轴的损坏形式及其原因,且为避免这些损坏,曲轴在设计过程中应尽量满足以下的要求:1.具有足够的疲劳强度,以保证曲轴工作可靠。
尽量减小应力集中,加强薄弱环节;2.具有足够的弯曲和扭转刚度,使曲轴变形不致过大,以免恶化活塞连杆组及轴承的工作条件;3.轴颈就有良好的耐磨性,保证曲轴和轴承有足够的寿命;4.曲柄的排列应合理,以保证柴油机工作均匀,曲轴平衡性良好,以减少振动和主轴承最大负荷;5.材料选择适当,制造方便【26】。
曲轴的结构型式曲轴的支承方式一般有两种,一种是全支承曲轴,其曲轴的主轴颈数比气缸数目多一个,即每一个连杆轴颈两边都有一个主轴颈。
这种支承,曲轴的强度和刚度都比较好,并且减轻了主轴承载荷,减小了磨损。
柴油机和大部分汽油机多采用这种形式。
另一种是非全支承曲轴。
其曲轴的主轴颈数比气缸数目少或与气缸数目相等。
这种支承方式叫非全支承曲轴,虽然这种支承的主轴承载荷较大,但缩短了曲轴的总长度,使发动机的总体长度有所减小。
有些汽油机,承受载荷较小可以采用这种曲轴型式【27】。
鉴于本课题所设计的1015柴油机为四缸,故而动机的总体长度较小。
且其常用于重型载重车,曲轴的强度及刚度要求都较高,因此设计采用全支承曲轴。
曲轴从结构上可分为整体式和组合式。
整体式曲轴的毛胚由整根钢料锻造或铸造方法浇铸出来,具有结构简单、加工方便、重量轻、工作可靠、刚度和强度较高等优点。
组合式曲轴是分段制造的,铸造时容易保证质量,降低废品率【28】;锻造时无需较大的锻压设备,制造方便,热处理和机械加工业较方便,并可缩短生产周期。
当生产后使用中某个曲柄发现有缺陷时,可以局部更换而不必报废整个曲轴。
一般的说,在选择曲轴结构时,只要生产设备允许应该尽可能采用整体式曲轴。
在大型柴油机上由于曲轴尺寸与重量都较大,整体制造极为困难是,往往采用组合式曲轴。
对于本课题得设计,曲轴的尺寸较小及重量较轻,所以选择整体式的。
曲轴的材料曲轴的常用材料根据其毛坯制造方法的不同可分为锻造曲轴材料和铸造曲轴材料两大类。
锻造游客分为自由锻、模锻和镦锻。
自由锻适用于较小设备生产大型曲轴,但效率太低,加工余量也大。
模锻需要一套较贵的锻模设备和较大的锻压设备,生产效率价高。
镦锻可节约大量金属材料和机械加工工时,且加工出的曲轴能充分发挥材料的强度。
锻造曲轴常用材料为普通碳素钢及合金钢。
铸造曲轴常用材料为球墨铸QT60-2、可断铸铁KTZ70-2、合金铸铁及铸钢ZG35等。
在强化程度要求不高的内燃机中,一般选用普通碳素钢,碳素钢的韧性比合金钢高,可以降低扭转振动振幅。
合金钢多用于强化要求高的柴油机曲轴,其疲劳强度高但对应力集中敏感性大,因而对机械加工要求也高。
球墨铸铁价格低廉,制造方便,对应力集中不敏感,并可以通过合理的造型降低应力的集中,还可通过加入合金元素、热处理、表面强化等方法提升其性能。
因此对于要求高的强度、塑性、韧性、耐磨性、耐严重的热和机械冲击、耐高温或低温、耐腐蚀以及尺寸稳定性的曲轴较适用【29】。
但球墨铸铁延伸率、冲击韧性、弹性模数及疲劳强度较低,在使用其作为曲轴材料时,应该确保轴颈和曲柄臂厚度较粗。
曲轴的材料应具有较高的疲劳强度、必要的硬度以及较好的淬透性。
在选取材料是不仅要考虑到机械性能,同时也要考虑工艺性、资源性和经济性。
在选择材料时,需要根据内燃机类型、用途及生产条件,确定曲轴毛坯的制造方法。
并参考同类近似机型所用材料,根据曲轴受力情况和使用习惯,凭经验选取。
根据上述各种毛坯制造方法及材料特点,并结合1015柴油机结构、实际受力状况及用途,本设计曲轴毛坯采用铸造方法,曲轴材料选择球墨铸铁QT60-2。
曲轴的主要部件设计主轴颈和曲柄销主轴颈和曲柄销是曲轴最重要的两对摩擦副,他们的设计直接影响了内燃机的工作可靠性、外形尺寸及维修。
轴颈的尺寸和结构与曲轴的强度、刚度及润滑条件有密切的关系。
曲轴的直径越大,曲轴的刚度也越大,但轴颈直径过大会引起表面圆周速度增大,导致摩擦损失和机油温度的增高。
曲柄销直径的增大会引起旋转离心力及转动惯量的剧烈增加,并使连杆大头的尺寸增大,这不利于连杆通过气缸取出,因此在保证轴承比压不变的情况下,采用较大的轴颈直径1D ,减小主轴颈长度1L ,这有利于缩短内燃机的长度或者加大曲柄臂的厚度采用短而粗的主轴颈可提高曲轴扭振的自振频率,减小在工作转速范围内产生共振的可能性。
一般情况下曲柄销直径2D 总是小于主轴颈直径1D 【30】。
曲柄臂曲柄臂在曲柄平面内的抗弯曲刚度和强度都较差,往往因受交变弯曲应力而引起断裂。
因此曲柄臂是整体曲轴上最薄弱的环节,设计时应注意适当的宽度和厚度,并选择合理的形状,以改善应力的分布状况。
增大曲柄臂的厚度和宽度都可以增大曲柄臂的强度,而从提高曲柄臂的抗弯强度来说,增加厚度比增加宽度效果要好得多【31】。
曲轴圆角曲轴主轴颈和曲柄臂连接的圆角称为主轴颈圆角,曲柄销和曲柄臂连接的圆角称为曲柄销圆角。
这些过渡圆角能够减小应力集中,提高疲劳强度,其半径的增大与其表面光洁程度的提高,是增加曲轴疲劳强度的有效措施【32】。
曲轴圆角半径r应足够大,但是圆角半径过小会使应力集中严,而圆角半径的增大会使轴颈承压的有效长度减小,因而也会减小轴承承压面积。