模锻件的机械加工余量和公差
2.3 锻造工艺解析

机械制造工艺基础——锻压工艺
5、平锻机上模锻:
• 平锻机的主要结构与曲柄压力机相同。只因 滑块是作水平运动,故称平锻机。
机械制造工艺基础——锻压工艺
5、平锻机上模锻:
•平锻机上模锻的特点: (1)有两个分模面,可以锻出其他模锻方 法无法锻出的锻件。 (2)生产率高,400-900件/小时。 (3)锻件尺寸精确,表面粗糙度低。 (4)材料利用率达85-95%。 (5)非回转体及中心不对称的锻件较难锻 造。平锻机造价高。 (6)适合于带头部的杆类和有孔零件的模 锻成型。
机械制造工艺基础——锻压工艺
补充: 典型零件模锻工艺过程: (1)零件图纸的分析
(2)选择分模面
(3)确定锻孔
(4)确定模锻工序
(5)绘制锻件图
(6) 锻模设计
机械制造工艺基础——锻压工艺
(1)零件图纸的分析
• 汽车后闸传动杆零件,上下端面、四个大孔、 20.3孔的端面和8孔需机械加工,其余均需模 锻锻出。
机械制造工艺基础——锻压工艺
1、模锻件图的绘制:
4)锻模圆角: •所有两表面交角处都应 有圆角。一般内圆角半 径(R)应大于其外圆半 径(r)。 5)留出冲孔连皮: •锻 件 上 直 径 小 于 25mm 的孔,一般不锻出,或 只压出球形凹穴。
机械制造工艺基础——锻压工艺
1、模锻件图的绘制:
• 大于25mm的通孔,也不能直接模锻出通孔, 而必须在孔内保留一层连皮。 • 冲孔连皮的厚度s与孔径d有关,当d =30~ 80mm时,s =4~8mm。
机械制造工艺基础——锻压工艺
3.摩擦压力机上模锻
④ 摩擦压力机承受偏心载荷能力差,通 常只适用于单膛锻模进行模锻。对于形 状复杂的锻件,需要在自由锻设备或其 它设备上制坯。 •应用: 适合于中小件的小批生产。如铆钉、 螺钉、螺母、气门、齿轮和三通阀体等。
机械制造工艺学毛胚尺寸确定(详解)

确定毛胚类型及制造方法毛胚的种类和制造方法常用的毛胚种类:铸件和锻件。
铸件毛胚,在成批生产条件下,采用砂型铸造,机器造型。
金属模造型。
锻件,可承受冲击载荷、交变载荷,在成批生产条件下,采用锻模。
加工余量的分类1、总余量和工序余量总余量是指某一表面毛胚尺寸与零件设计尺寸之差。
工序余量是指每道工序切除的金属层厚度,即相邻两道工序尺寸之差。
2、单边余量和双边余量工序余量有单边余量和双边余量之分。
对于非对称表面,工序余量是单边的,称单边余量。
对于外圆和内圆这样具有对称结构的对称表面,工序余量是双边的,称双边余量,即指相邻两工序的直径尺寸之差。
3、最大余量和最小余量由于各工序尺寸都有公差,所以各工序实际切除的余量值是变化的,因此工序余量有公称余量、最大余量、最小余量之分。
相邻两工序的基本尺寸之差即是公称余量。
公称余量的变化范围称为余量公差。
工序尺寸公差一般按“入体原则”标注。
即对被包容尺寸(轴径),上偏差为0,其最大尺寸就是基本尺寸;对包容尺寸(孔径、槽宽),下偏差为0,其最小尺寸就是基本尺寸。
一、铸件毛胚的余量铸件的尺寸公差与机械加工余量加工余量RMA:A、B、C、D、E、F、G、H、J、K共十级,其中常用的为C-K。
公差等级:CT1-CT16,常用的为CT4-CT13。
成批生产铸件机械加工余量等级注:第一行为单边余量,第二行为双边余量。
铸件公差及公差带公差带位置:对称标注最小圆角半径(mm)(1)铸件壁部连接处的内转角应有铸造圆角。
计算时热裂性较大的合金取较大值。
(2)算出数值后,应选取与其接近的机械制造业常用的标准尺寸(详见GB2822-81)。
为便于制造,半径应尽可能统一。
例如,对于砂型及金属型铸件,一般统一用R3或R5,对压铸件用R1或R2。
铸造最小孔径表3-19 起模斜度(根据JB/T 5105-91)用二、锻件毛胚的余量选择毛胚该零件材料为45钢。
由于该拨叉在工作过程中要承受冲击载荷,为增强拨叉的强度和冲击韧性,获得纤维组织,以使金属纤维尽量不被切断,毛胚选用锻件。
4204-2004锻件加工余量 TDS.

锤上钢质自由锻件机械加工余量与公差宝鸡石油机械有限责任公司发布前言本标准代替Q/BS 4204.1~4204.22-88《锤上钢质自由锻件机械加工余量与公差》。
本标准与Q/BS 4204.1~4204.22-88相比主要变化如下:——将原系列标准合并成为一个标准;——原标准中的“台阶和凹挡的锻出条件”、“法兰的最小锻出条件”、“光轴类机械加工余量与公差”、“台阶轴类机械加工余量与公差”、“带孔圆盘类机械加工余量与公差”、“圆环类机械加工余量与公差”、“套筒类机械加工余量与公差”、“黑皮锻件机械加工余量与公差”按GB/T 15826.1~15826.9-1995《锤上钢质自由锻件机械加工余量与公差》中相关规定执行。
本标准由宝鸡石油机械有限责任公司提出。
本标准由技术中心标准室归口。
——本标准主要起草人:李伟阳、郝玉英。
本标准所代替标准的历次版本发布情况为:——Q/BS 4204-78、 Q/BS 4204-88。
锤上钢质自由锻件机械加工余量与公差1 范围本标准规定了锤上钢质自由锻件机械加工余量与公差的一般规定。
本标准适用于锤上锻造含碳量不超过0.9%或其它合金成分总含量不超过4%的碳素钢和合金钢的自由锻件。
凡超越本标准规定的自由锻件,其余量与公差由供需双方另行协商确定。
2 规范性引用文件下列文件中的条款通过本标准的引用而成为本标准的条款。
凡是注日期的引用文件,其随后所有的修改单(不包括勘误的内容)或修订版均不适用于本标准,然而,鼓励根据本标准达成协议的各方研究是否可使用这些文件的最新版本。
凡是不注日期的引用文件,其最新版本适用于本标准。
GB/T 15826.3锤上钢质自由锻件机械加工余量与公差带孔圆盘类、GB/T 15826.4锤上钢质自由锻件机械加工余量与公差圆环类GB/T 15826.5锤上钢质自由锻件机械加工余量与公差套筒类GB/T 15826.6锤上钢质自由锻件机械加工余量与公差光轴类GB/T 15826.7锤上钢质自由锻件机械加工余量与公差台阶轴类GB/T 15826.9锤上钢质自由锻件机械加工余量与公差黑皮锻件3 一般规定3.1 本标准规定的机械加工余量与公差,适用于以钢坯锻造的自由锻件。
铝合金模锻件设计参数

一、防锈铝合金摘自《合金钢与有色金属锻造》郭鸿镇,1999.主要合金元素是锰和镁.不能时效强化,锻造退火后是单相固溶体,抗腐蚀性能高,塑性好。
锰在铝中能通过固溶强化提高铝合金的强度,但其主要的作用是能提高铝合金的抗蚀能力。
A1—Mn系合金中的第二相MnA16与铝的化学性质接近,故含锰合金抗蚀性好。
镁对铝合金的抗蚀性损伤较小,而且有较好的固溶强化效果。
防锈铝承受压力加工的能力很强,可施以冷压力加工使之产生加工强化。
它的可焊性也很好,切削性较差(因太软)。
表1防锈铝合金的化学成分和机械性能二、铝合金可锻性低强度、高塑性合金:LD2,LF2l,LF2,LF3,LF5及工业纯铝等;中等强度和塑性的合金:LD5,LD6,LD7,LD8,LY2,LY6,LY11,LY16,LYl7,LF6等;高强度、低塑性的合金有:LD10,LYl2,LC4,LC6等LF21:锻造温度范围300-500,80%变形量。
变形速度影响不大。
LD5:铸造状态,中等塑性。
300-450,压力机锻造允许变形量大于50%,锤上小于50%。
变形状态,高塑性。
350-500,压力机锻造允许变形量80%,锤上65%。
LC4:塑性较低。
铸态,350-450,压力机,50%,锤上小于40%;变形态,350-450,压力机,65-85%,锤上,30-60%。
表2铝合金的锻造温度和加热规范我车间应用的加热温度:470:LD2 LD7 2618 LF2435: LC4450:L Y12三、铝合金锻造特点注意备料,端面平整,表面无裂纹、斑点、划伤等;不宜采用多膛模锻;注意模具的预热与润滑;模锻后及时切边。
形状复杂、中等大小模锻件宜采用模锻锤。
形状简单、中等大小及不需要制坯采用曲轴压力机。
大型铝合金采用模锻液压机。
锻模预热接近铝合金的锻造温度。
四、锻件图设计余量表3 有色金属锻件的机械加工余量参照HB6077-86标准表4内外表面的加工余量Z1注:表中为单面加工余量,双面加工的余量应加倍。
最新自由锻造工艺规程的编制及举例资料

自由锻造工艺规程的编制及举例制定自由锻工艺规程的过程就是自由锻工艺设计的过程。
主要有以下内容:(一)绘制锻件图自由锻件的锻件图是在零件图的基础上考虑了加工余量、锻造公差、工艺余块等之后绘制的图绘制自由锻件的锻件图可按以下步骤进行:1.简化锻件形状为了简化锻造工艺,零件上的小孔、凹档、台阶等部分,可加上余块而不予锻岀,如图a。
是否加余块要根据零件的形状、尺寸、锻造技术水平和经济效果来确定。
2.确定加工余量和锻件公差(1)机械加工余量【机械加工余量】为使零件具有一定的加工尺寸和表面粗糙度,在零件表面需要加工的部分,锻件上留一层供作机械加工用的金属,称作机械加工余量(见上图a)。
(2)余块【余块】为简化锻件外形及锻造过程,在锻件的某些地方和添一些大于机械加工余量的金属,种加添的金属称作余块(见上图a)。
(3 )锻件公差【锻件公差】锻件实际尺寸与基本尺寸之间所允许的误差。
公差值的大小是根据锻件形状、寸并考虑生产的具体情况而定的。
3.绘制锻件图在锻件图上,规定用粗实线绘出锻件的形状。
为了便于了解零件的形状和检查锻件的实际加工余量,在锻件图上还要用双点划线绘出零件的主要形状,如图10-27b 。
(二)计算坯料质量与尺寸【坯料质量】坯料质量可按下式计算G 坯料=G 锻件+G 烧损+G 料头式中G 坯料——坯料质量G 锻件——锻件质量G 烧损——加热时由于坯料表面氧化而烧损的质量。
第一次加热取被加热金属的2~3%,以后每次加热取1.5~2.0%G 料头——在锻造过程中冲掉或切掉的那部分金属的质量。
如冲孔时坯料中部的料芯,修切端部的料头等。
当锻造大型锻件时,如采用钢锭作坯料,还要考虑应切掉的钢锭头部和尾部的质量。
2.坯料尺寸根据坯料质量即可确定坯料尺寸。
在计算坯料尺寸前,先要考虑锻造比。
【锻造比】是指坯料在锻造前后的断面积的比值。
对于拔长工序来说,其锻造比R d 可按下式计算:R d =A 0 /A 1 或L 1 /L 0式中A 0 、A 1 ——拔长前、后坯料的断面积;L 0 、L 1 ——拔长前、后坯料的长度。
自由锻造水压机锻件机械加工余量和公差标准

+15
+16
+17
+29
10001~15000
+12
40 − 20 43 − 21
+14
+13
42 − 21 45 − 22
+15
+14
+16
15001~20000
+12
40 − 20
+13
注:⑴有台阶的矩形截面零件,根据最大截面的 A、B 值确定余量和公差; ⑵较短的锻件(L<2500) ,两各加 1a; ⑶宽度大于 1600 的板形锻件的机械加工余量由工艺编制人员自定。 ⑷水压机锻造最小截面厚度为:6000T 水压机为 200,15000T 水压机为 300。
2.4 圆筒形锻件机械加工余量和公差。 2.4.1 加氢大型圆筒型锻件机械加工余量和公差表。
零 件 直 径 D 设备 零件长度 L ≤4500 4501~ 6000 余量及公差 水压机出成品 <4000 90 − 45 80 − 40
+27
+30
≥6001
110 − 55 90 − 45
+30
+37
350/275
495/385
260/220
400/330
注:表中分子为端部法兰用,分母为中间法兰用。
2.2 形状较复杂锻件品种的余量分配 2.2.1 发电机转子的余量分配
2.2.2
汽轮机整体转子的余量分配
A 汽轮发电机转子,汽轮机整体转子长度 lo≤2000 时加 2a。长度 lo≥13000 时加 4a。 B 法兰直径与凹档(相邻小园)直径差大于(或等于)1000 时凹档直径可适当加大余量的 10~20%。 C 凹档下料长度小于窄砧宽度时,可按窄砧宽度计算,加大凹档直径余量。 D 水压机最小砧宽:6000T 水压机最小砧宽 600,15000T 水压机最小砧宽 850 E 凹档直径=√(D1+50mm)×K×6.16÷L 其中 D1:与凹档相邻台阶的直径 K:最小砧宽 L:凹档锻造长度
锻造工艺质量控制规范

锻造工艺质量控制规范1 主题内容与适用范围本标准规定了对锻造工艺进行全过程质量控制的通用原则和要求。
本标准适用于锻造车间的锻造工艺质量控制。
2 引用标准GB 12361 钢质模锻件通用技术条件GB 12362 钢质模锻件公差及机械加工余量GB 13318 锻造车间安全生产通则GB/T 12363 锻件功能分类JB 4249 锤上钢质自由锻件机械加工余量与公差JB 4385 锤上钢质自由锻件通用技术条件JB/T 6052 钢质自由锻件加热通用技术要求JB/T 6055 锻造车间环境保护导则3 锻件分类本标准质量控制所涉及的锻件分类按GB/T 12363 执行。
4 环境的控制锻造厂的工作环境包括厂房地面、天窗、温度、通风、照明、噪声、通道、管道以及坯料、锻件和工夹模具的存放等均应按GB 13318 第3 章和JB/T 6055 第3、4 章的要求和国家的有关法规、法律制订本企业的具体实施要求。
5 设备、仪表与工装的控制5. 1 设备、仪表5. 1. 1 各类设备必须完好,并有操作规程和维修、检定制度。
5. 1. 2 各类在用主要设备必须挂有完好设备标牌,并有检验有效期及下次检定日期。
不合格设备及超过检定合格有效期的设备必须挂“停用”标牌。
5. 1. 3 设备的控制系统及检测显示仪表应定期检查,确保仪表和其精度的显示数值准确。
5. 1. 4 加热设备的温度显示及测点布置应正确反应加热区炉温及炉温均匀性。
5. 1. 5 所用设备都必须建立档案,其具体内容包括:a. 设备使用说明书;b.台时记录;c.故障记录d.修理记录e. 历年检定报告及检定合格证。
5. 2 模具及其他工装5. 2. 1 新模具应按模具图的要求制造,检验合格后进行试模,确认达到设计、制造要求后方可投入生产。
5. 2. 2 在每批锻件生产结束时,应将锻造的尾件上打标记并经检验尺寸合格后,模具方可返库继续使用。
5. 2. 3 锻造所用工具,必须按工艺文件的规定选用,并经检查完好方可使用。
锤上模锻件长宽尺寸公差

一、表7-1 锤上模锻件长宽尺寸公差(mm)二、表7-2 按锻锤吨位确定锻件余量及公差(mm)三、出模斜度,系列化:30′、1°、1°30′、2°、3°、5°、7°、10°、12°、15°。
四、锻件圆角半径的确定外圆角半径r:r=B+a式中r——外圆角半径(mm);B——机械加工余量(mm);a——产品零件圆角半径或倒角(mm)。
内圆角半径R:R=(2~3)r式中r——外圆角半径。
圆角半径,系列化:1、1.5、2、2.5、3、5、8、10、12、15、20(mm)。
一般情况下,同一锻模的内、外圆角半径应统一。
五、模锻锤所需的吨位1、双动模锻锤的吨位G=1/1000K·F式中G——所需双动模锻锤的吨位(kN);F——包括飞边及冲孔连皮在内的锻件水平投影面积(cm2);K——钢种系数,见表8-8。
2、单动模锻锤的吨位G单=(1.5~1.8)G式中G单——单动模锻锤吨位(kN);G——双动模锻锤吨位(kN)。
六、所需自由锻锤的吨位自由锻锤用于胎模锻。
钢锻件在有飞边的合模中锻造时,所需吨位可按下式计算:G=K·F·1/1000式中G——所需吨位(kN);K——系数,通常K=5~10。
形状简单、制坯较好的锻件取5~6;较复杂的形状取6~7;直接终锻小型锻件取7~9;扁薄锻件取8~10;F——锻件锻造部分的投影面积(cm2),计算时可不计飞边面积。
七、摩擦压力机的吨位P=(3.5~5.5)K·F式中P——摩擦压力机吨位(kN);F——锻件投影面积,包括飞边及连皮(cm2);K——钢种系数,对于10、20、Q235号钢K=0.9;45、20Cr钢K=1;45Cr、45CrNi钢K=1.1;GCr15、45CrNiMo钢K=1.25。
上述公式适用于一次打击成形。
若采用2~3次打击成形,可按上述P值折半选用。
平锻机模锻平锻机模锻特点及应用范围

带入得 1 = ( 2+ 2+ ) 3
解得
=
3
3 3 3 - 2- 或= - 2- 4 2 - 4 2
ε 是一个关于、 函数。下图是锥形型槽内聚集的限制曲线,设 计时采用abc曲线以下的系数,可获得合格的产品。由长径比数值 与曲线的交点确定系数、,求出聚集工步尺寸Dm= d,dm= d0。
2 2 d 计= D锻 -d 锻
带孔锻件坯料直径计算: 当(1)d计/ d锻=1.0~1.2时,取d坯=(0.82~1.0)d计; (2) d计/ d锻> 1.2时,取d坯> d锻 (3)d计/ d锻< 1.2时,取d坯< d锻 坯料长度的计算: L坯=1.27V坯/d2坯 其中 V坯=(V锻+V芯+M毛)(1+δ )
6-4 顶镦规则及聚集工步计算
一、顶镦规则 顶镦:坯料端部的局部墩粗为顶镦或聚集,是平锻机的基本工步。 1)顶镦第一规则:当长径比 ≤ 3,端部较平时,可在平锻机中自 由墩粗到任意大的直径而不弯曲。即:不弯曲的工艺条件 ≤ 3。
长径比过大造成弯曲
端面不平,长径比过大造成弯曲
允许长径比允
2)顶镦第二规则:在凹模内顶镦时,若:Dm ≤1.5d0时,f ≤ d0 或 Dm ≤ 1.25d0时,f ≤ 1.5d0, > 允,可进行正常的局部墩粗而不 产生折叠。如图(b),用于 <10锻件。即:细长杆镦粗时,产 生纵向弯曲,但不致于引起折叠的工艺条件。
模锻过程原理图
2.平锻机模锻工艺、设备特点及其应用 工艺特点: (1)设有两个相互垂直的分模面,能锻出两个不同方向具有凹档和凹 孔的锻件。
(2)坯料水平放料,锻件长度不受设备空间限制,能进行长杆类 锻件和长杆空心类锻件的模锻,进行深穿孔或深冲孔工作。
平锻机模锻平锻机模锻特点及应用范围

6-5 通孔锻件和盲孔锻件的工步计算 通孔锻件和盲孔锻件锻造特点:模锻工艺需要聚集、冲孔和切断。 一、通孔锻件热锻件图设计 设计依据:冷锻件图,在冷锻件图基础上加收缩量获得。设计要点如下图。
二、冲孔次数的确定和冲孔工步设计 冲孔次数设计依据:冲孔深度 lnp和冲孔直径dc`之比。由下图确定。
设备特点 (1)设备是模锻设备中结构最复杂,价格最贵锻造设备。 (2)锻件表面尺寸要求精度高,否则夹不紧或产生纵向毛刺。 (3)锻件加热质量高,平锻机工艺适应性差,不适应非对称件。 (4)锻造同类大小的锻件,平锻机生产效率比热模锻压机低。 应用特点 (1)各种螺栓、铆钉类锻件; (2)汽车锻件如气门、半轴,环形类锻件; (3)长杆件的局部镦粗,如抽油杆类的镦粗。
6-2 平锻机工步及锻件分类 一、平锻机基本工步 平锻机常用的基本工步有: (1)局部墩粗;(2)冲孔;(3)成形;(4)切边(5)穿孔(6)切断
集聚-压扁-成形-切边
集聚-成形穿孔、切芯料
二、平锻机模锻锻件的分类:五类 第一类:具有粗大部分的杆件类,锻造工步:集聚、预锻、终锻
6-4 顶镦规则及聚集工步计算 一、顶镦规则 顶镦:坯料端部的局部墩粗为顶镦或聚集,是平锻机的基本工步。 1)顶镦第一规则:当长径比 ≤ 3,端部较平时,可在平锻机中自 由墩粗到任意大的直径而不弯曲。即:不弯曲的工艺条件 ≤ 3。
长径比过大造成弯曲
端面不平,长径比过大造成弯曲
允许长径比允
2)顶镦第二规则:在凹模内顶镦时,若:Dm ≤1.5d0时,f ≤ d0 或 Dm ≤ 1.25d0时,f ≤ 1.5d0, > 允,可 进行正常的局部墩粗而不产生折叠。如图(b),用于 <10锻件。即:细长杆镦粗时,产生纵向弯曲,但 不致于引起折叠的工艺条件。
锻造工艺学及模具设计复习思考题

锻造工艺学及模具设计复习思考题1)试阐述镇静钢锭的结构及其主要缺陷的产生部位。
2)钢锭常见缺陷有哪些它们产生的原因和危害性是什么3)常见的型材缺陷有哪些它们产生的原因和危害性是什么4)锻造用型材常采用哪些方法下料各自有何特点5)铸锭作为锻造坯料时如何下料6)试说明锻前加热的目的和方法。
7)氧化和脱碳有哪些共性和异性8)氧化和脱碳可产生哪些危害如何防止9)过烧和过热有哪些危害如何防止10)导致裂纹产生的内应力有几种清阐述它们相应的应力状态。
11)通常圆柱形坯料产生加热裂纹的危险位置在何处原因何在如何防止12)锻造温度范围的确定原则和基本方法是什么13)怎样确定碳钢的始锻和终锻温度它们受到哪些因素的影响14)为什么要制定合理的加热规范加热规范包括哪些内容其核心问题是什么15)两种不同概念的加热速度实质上反映了什么因素的影响16)选择加热速度的原则是什么提高加热速度的措施有哪些17)均热保温的目的是什么18)冷锭和热锭的加热规范各有什么特点为什么、19)少无氧化加热主要有哪几种方法其中火焰加热法的基本工作原理是什么20)金属断后冷却常见缺陷有哪些各自产生原因是什么21)为什么硬钢锻后冷却易产生表面纵向裂纹22)金属锻后冷却规范一般包括哪些内容23)锻件热处理的目的是什么24)中小锻件通常采用哪些热处理各自作用是什么25)通常大锻件采用哪些热处理各自作用是什么26)导致金属塑性变形不均匀性的原因是什么27)镦粗和拔长各有哪些用途28)镦粗工序主要存在哪些质量问题试分析它们产生的原因及其预防措施。
29)拔长工序主要存在哪些质量问题试分析它们产生的原因及其预防措施。
30)为什么采用平砧小压缩量拔长圆截面坯料时效率低且质量差应怎样解决31)空心件拔长时孔内壁和端面裂纹产生的原因是什么应采取哪些措施加以解决32)试阐述开式冲孔时金属变形和流动特点并画出相应的应力、应变图。
33)冲孔时易出现哪些质量问题应采取什么措施解决34)试阐述冲子扩孔时金属变形和流动特点并画出相应的应力、应变图。
锻件余量和材料消耗计算基本原则
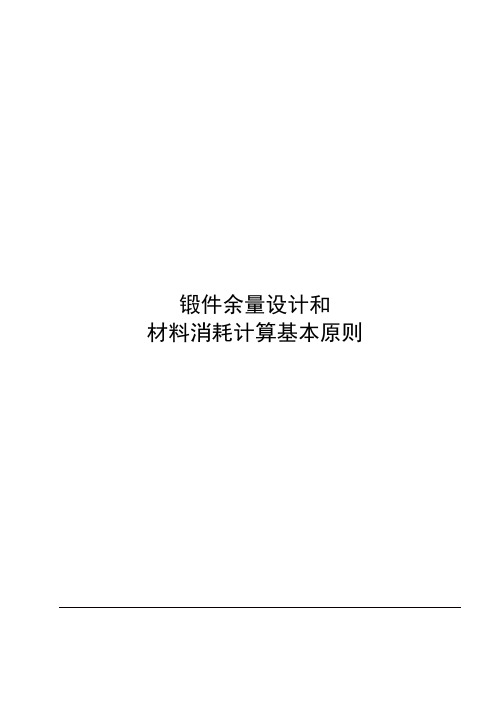
锻件余量设计和材料消耗计算基本原则锻件余量设计和材料消耗计算基本原则1 范围本标准规定了滚动轴承(包括轮毂单元、凸缘等)套圈所有热锻锻件的设计基本方法,锻件重量、飞边重量、料芯重量、火耗重量、下料重量、材料消耗重量的基本计算方法。
本标准适用于滚动轴承(包括轮毂单元、凸缘等)套圈所有热锻锻件。
2 规范性引用文件下列文件中的条款通过本标准的引用而成为本标准的条款。
凡是注日期的引用文件,其随后所有的修改单(不包括勘误的内容)或修订版均不适用于本标准,然而,鼓励根据本标准达成协议的各方研究是否可使用这些文件的最新版本。
凡是不注日期的引用文件,其最新版本适用于本标准。
GB/T 12361 钢质模锻件通用技术条件GB/T 12362 钢质模锻件公差及机械加工余量CSBTS TC98.25 滚动轴承套圈锻件技术条件3 术语和定义锻件重量:锻件毛坯的实际重量飞边重量:锻造过程中外轮廓分模面处多余的材料料芯重量:锻造过程中内孔多余的材料火耗重量:锻件在锻打过程中的热损耗下料重量(切料重量):锻打一件锻件所需要的钢坯重量材料消耗定额:锻打一件锻件所需要的钢材消耗总重量4 锻件设计基本原则4.1 锻件余量设计基本原则4.1.1 法兰盘/单元外圈/轴承座/凸缘等锻件余量设计基本原则径向余量2.2mm,外径公差+1.0mm,内径公差-1.0mm;当直径超过φ100mm时,径向余量2.5 mm,外径公差+1.2mm,内径公差-1.2mm。
(注:在保证法兰盘两端厚度C1、C2最小壁厚不小于5mm的前提下)法兰大外径D径向余量2.5mm,外径公差+1.2mm。
轴向余量2.5mm, 两端轴向余量每端各2mm,一般外轮廓公差+1.0mm,内轮廓公差-1.0mm。
法兰内孔深度一般为h1小于等于10mm,h2小于等于18mm,具体可视产品情况而定。
料芯厚度:单元外圈料芯厚度一般按8mm设计。
图一4.1.2 挡环余量设计基本原则径向余量2.5mm。
1模锻方法与工艺解析

2锻造种类
(三)按行业应用 ■飞机锻件 按重量计算,飞机上有85%左右的的构件是锻件。飞机发动机 的涡轮盘、后轴颈(空心轴)、叶片、机翼的翼梁, 机身的肋筋 板、轮支架、起落架的内外筒体等都是涉及飞机安全的重要锻件。 飞机锻件多用高强度耐磨、耐蚀的铝合金、钛合金、镍基合金等 贵重材料制造。为了节约材料和节约能源,飞机用锻件大都采用 模锻或多向模锻压力机来生产。 ■汽车锻件 按重量计算,汽车上约有58%的锻件。一般的汽车由车身、车 箱、发动机、前桥、后桥、车架、变速箱、传动轴、转向系统等 15个部件构成汽车锻件的特点是外形复杂、重量轻、工况条件差、 安全度要求高。如汽车发动机所使用的曲轴、连杆、凸轮轴、前 桥所需的前梁、转向节、后桥使用的半轴、半轴套管、桥箱内的 传动齿轮等等,无一不是有关汽车安全运行的保安关键锻件。
液压机的最大缺点是生产效率低,占地面积较大。
5. 胎 模 锻
胎模锻是自由锻设备上使用可移动模具生 产模锻件的一种锻造方法. 介于自由锻和模锻之间的锻造方法。 胎膜锻特点: 胎模图示
(1)胎模不固定。 (2)不需要模锻设备,锻模简单,加工成本低; (3)工艺灵活,适应性强等优点。 (4)劳动强度大,效率低。
对复杂件预先的部分变形加工。有:
1)拔长模膛;
2)滚压模膛;
3)弯曲模膛;
4)切断模膛;
2.曲柄压力机上模锻 曲柄压力机传动示意 曲柄压力机上模锻特点: (1)产生静压力; (2)压力机行程固定;
(3)导向严细,自动顶件;
(4)锻模镶块组合简又省;
(5)清除氧化皮困难;
(6)效率高,锻件精,设备贵,宜大量生产。
锻造液压机有自由锻液压机、模锻液压机和切边
液压机之分。锻造生产常用的模锻液压机,又有 通用模锻液压机和专用模锻液压机两大类。
锻件毛坯计算

锻件毛坯计算如图,根据零件图绘制锻件图。
在1吨模锻锤上模锻,生产批量为成批生产,材料45钢。
解:计算过程如下 1、确定机械加工余量和公差(1)计算锻件质量m()2223313290463610036100107.8510222m kg πππ--⎡⎤⎛⎫⎛⎫⎛⎫=⨯⨯+⨯⨯--⨯⨯⨯⨯⨯⎢⎥ ⎪ ⎪ ⎪⎝⎭⎝⎭⎝⎭⎢⎥⎣⎦5.76kg = (2)计算锻件复杂系数S()2222132904636100361002220.5361321002S ππππ⎡⎤⎛⎫⎛⎫⎛⎫⨯⨯+⨯⨯--⨯⨯⎢⎥ ⎪ ⎪ ⎪⎝⎭⎝⎭⎝⎭⎢⎥⎣⎦==⎛⎫⨯⨯⎪⎝⎭S 在0.32~0.63G C =范围内,所以复杂系数为2S 级。
(3)材质系数M45钢含碳量c%=0.42~0.50%<0.65%所以材质系数为1M 级。
(4)由表2-2、表2-3查得零件加工余量锻件厚度尺寸100mm ,余量2.0~2.5mm ,取2.5mm 。
锻件长度尺寸132mm ,余量2.0~2.5mm ,取2.5mm 。
内孔直径尺寸46mm ,余量2.6mm 。
(5)根据锻件质量m 、复杂系数S 、材质系数M ,由表2-4、2-6查公差锻件尺寸132mm ,公差 2.11.13.2mm +-;锻件尺寸90mm ,公差 1.90.92.8mm +-;厚度尺寸100mm ,公差 2.70.93.6mm +-;厚度尺寸36mm ,公差 1.90.62.5mm +-;内孔直径46mm ,公差0.81.72.5mm +-;错差1.2mm ;残留飞边公差1.2mm ;表面缺陷,不允许超过1.2mm 。
2、确定模锻斜度由零件尺寸,查得,内表面拔模斜度10,外表面拔模斜度7。
3、圆角半径外圆角半径r=余量+a=2.5+2=4.5mm ,取r=5mm 。
内圆角半径R=(2~3)r ,根据需要,取R=8mm 。
4、冲孔连皮(当孔径为25~80mm 时,冲孔连皮厚度取4~8mm)冲孔连皮:对于有内孔的模锻件,锤上模锻不能直接锻出通孔,必须在所锻成的盲孔内保留一层具有一定厚度的金属层。
《铝及铝合金模锻件的尺寸偏差及加工余量》

与模具型腔有关,因此原标准中的尺寸名称不妥。
2.2.2.3 本标准的B级指标不变,与原标准相一致。
2.2.2.4 本标准的A级指标对照欧洲EN586.3-3:2001制订,原指标高于欧洲标准的不变,原指标低于欧洲标准的,修改等同或高于欧洲标准。其原A级指标与欧洲标准对照如表1所示。
表1 非跨模尺寸的原A级允许偏差与欧洲欧洲标准对比
-1.3 +2.0
-1.4 +2.0
-1.5 +2.1
-1.5 +2.1
-1.6 +2.2
-1.6 >120
~180 +1.3
-0.9 +1.4
-1.0 +1.6(1.5)
-1.0 +1.6
-1.1 +1.7
-1.2 +1.9
-1.2 +1.9
-1.3 +2.1
-1.4 +2.2
-1.6 +2.5
-1.7 +2.5
-1.7 +2.5
-1.8 +2.5
-1.9 +2.6
-2.0 +2.7
-2.1 >630
~800 +2.5(-)
-1.7(-) +2.5(-)
-1.7(-) +2.5(-)
金属模锻工艺
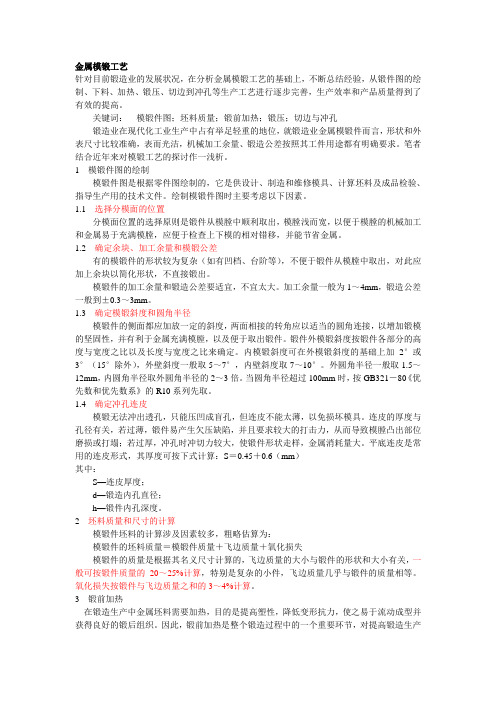
金属模锻工艺针对目前锻造业的发展状况,在分析金属模锻工艺的基础上,不断总结经验,从锻件图的绘制、下料、加热、锻压、切边到冲孔等生产工艺进行逐步完善,生产效率和产品质量得到了有效的提高。
关键词:模锻件图;坯料质量;锻前加热;锻压;切边与冲孔锻造业在现代化工业生产中占有举足轻重的地位,就锻造业金属模锻件而言,形状和外表尺寸比较准确,表而光洁,机械加工余量、锻造公差按照其工件用途都有明确要求。
笔者结合近年来对模锻工艺的探讨作一浅析。
1模锻件图的绘制模锻件图是根据零件图绘制的,它是供设计、制造和维修模具、计算坯料及成品检验、指导生产用的技术文件。
绘制模锻件图时主要考虑以下因素。
1.1选择分模面的位置分模面位置的选择原则是锻件从模膛中顺利取出,模膛浅而宽,以便于模膛的机械加工和金属易于充满模膛,应便于检查上下模的相对错移,并能节省金属。
1.2确定余块、加工余量和模锻公差有的模锻件的形状较为复杂(如有凹档、台阶等),不便于锻件从模膛中取出,对此应加上余块以简化形状,不直接锻出。
模锻件的加工余量和锻造公差要适宜,不宜太大。
加工余量一般为1~4mm,锻造公差一般到±0.3~3mm。
1.3确定模锻斜度和圆角半径模锻件的侧面都应加放一定的斜度,两面相接的转角应以适当的圆角连接,以增加锻模的坚固性,并有利于金属充满模膛,以及便于取出锻件。
锻件外模锻斜度按锻件各部分的高度与宽度之比以及长度与宽度之比来确定。
内模锻斜度可在外模锻斜度的基础上加2°或3°(15°除外),外壁斜度一般取5~7°,内壁斜度取7~10°。
外圆角半径一般取1.5~12mm,内圆角半径取外圆角半径的2~3倍。
当圆角半径超过100mm时,按GB321-80《优先数和优先数系》的R10系列先取。
1.4确定冲孔连皮模锻无法冲出透孔,只能压凹成盲孔,但连皮不能太薄,以免损坏模具。
连皮的厚度与孔径有关,若过薄,锻件易产生欠压缺陷,并且要求较大的打击力,从而导致模膛凸出部位磨损或打塌;若过厚,冲孔时冲切力较大,使锻件形状走样,金属消耗量大。
钢质模锻件通用技术条件

钢质模锻件通用技术条件一、总则1.1锻件的技术条件是锻件质量的检验依据。
锻件的主要技术条件一般都标在锻件工艺卡片上,而对于工艺卡上没有注明的、技术协议书上或合同上没有规定的技术问题,在检验锻件时应该执行锻件通用技术条件中的相应规定。
1.2本技术条件适用于在模锻锤、模锻压力机、螺旋压力机或平锻机等锻压设备上进行成批、大批生产成形的钢质热模锻件(以下简称锻件)。
二、锻件的外观质量和交货重量2.1内外拔模角及其数值:锻件在冷缩时,趋向离开模壁内部分为外拔模角,用α表示。
反之为外拔模角,用β表示。
如图所示。
为了便于制造模具时采用标准刀具,拔模角应选用:0°15'、0°30'、1°00'、1°30'、3°00'、5°00'、7°00'、10°00'、12°00'、15°00'。
2.2圆角半径内、外圆角半径及数值:锻件上的凸角圆角半径为外圆半径r,凹圆角半径为内圆角半径R。
为保证锻件凸角处的最小余量,则V1=余量+零件的倒角值。
为了便于制造模具所用刀具的标准化,圆角半径数值应选用:1.0mm、1.5mm、2.0mm、2.5mm、3.0mm、4.0mm、5.0mm、6.0mm、8.0mm、10.0mm、12.0mm、15.0mm……。
圆角半径大于15mm时,逢5递增。
2.3尺寸公差:锻件图未注明的长度、宽度、高度和深度公差、直线度、平面度、错模,可按GB/T12362-1990《钢质模锻件公差及机械加工余量》所列数值确定。
2.4表面缺陷深度:锻件的表面缺陷包括凹坑、麻点、碰伤、凹凸不平、折叠和裂纹等。
锻件的表面缺陷深度是指从锻件实际表面测量所得的局部凹陷或凸起的尺寸数值,该数值不计入锻件的实测尺寸。
(1)加工面的缺陷深度:若锻件的实际尺寸恰等于其基本尺寸,则缺陷之深度不得大于锻件的名义加工余量的一半。
若锻件的实际尺寸大于或小于其基本尺寸,则缺陷的深度不得大于锻件名义加工余量之半,加上或减去单边的实际偏差值。
- 1、下载文档前请自行甄别文档内容的完整性,平台不提供额外的编辑、内容补充、找答案等附加服务。
- 2、"仅部分预览"的文档,不可在线预览部分如存在完整性等问题,可反馈申请退款(可完整预览的文档不适用该条件!)。
- 3、如文档侵犯您的权益,请联系客服反馈,我们会尽快为您处理(人工客服工作时间:9:00-18:30)。
模锻件的机械加工余量和公差
1.机械加工余量
锻造过程中由于锻模磨损、上下模具错移、模具的斜度及其毛坯体积的变化、加热过程产生氧化、脱碳及终锻温度的波动等,使得锻件的形状和尺寸发生变化,尺寸在一定范围波动。
在锻后锻件的全部或局部表面,还需要机械加工,因此这些表面在设计时留有供机械加工用的金属层,称为机械加工余量。
机械加工余量设计目的是为提高表面质量及保证尺寸,锻件图上凡是需要机械加工的表面,都留有余量。
加工余量的大小与锻件的形状复杂程度、尺寸精度、表面光洁度、锻件材料和模锻设备等有关。
2.锻件公差
锻造过程中,由于欠压、金属不充满型槽、模具磨损或变形、模具设计时锻件收缩率选取不准确、终锻型槽制造公差、锻造设备精度变化、模具错移、人工操作误差等原因,锻件的实际尺寸不可能准确无误地达到锻件的公称尺寸,应该留有一定的尺寸误差,称为锻件公差。
锻件上无论是否进行机械加工,都应设计和注明锻件的公差。
锻件的公差主要包括长度、高度、宽度方向的公差、厚度公差、直线度和平面度公差、中心距尺寸公差、同轴度公差、残留横向毛边公差及切入锻件深度公差、纵向毛刺及冲孔变形量公差等。
模锻工艺设计过程中,对于零件图上较小的小孔、狭窄的沟槽、直径差较小的台阶等难以锻造的部位,可以设计锻造余块。
锻造余块设计可以简化锻件形状,减少模锻难度,但会增加机械加工量和金属消耗。
余块的设计要根据零件形状、模锻水平、加工难易程度等综合考虑,对于有些要求组织和力学性能检测的锻件,需要设计试样余块,以便用来进行锻件组织和力学性能检测,对于热处
理和机械加工时有特殊要求的锻件,需要设计夹头余块。
确定加工余量和公差的方法主要有两种:一种是按照锻件形状和尺寸大小査表确定,一种是根据模锻锤吨位大小确定,具体加工余量和公差确定可査阅GB/T12362—2003“钢质模锻件公差及其机械加工余量”。
锻件的公差可分为尺寸公差、形状位置公差和表面技术要求公差。
尺寸公差主要包括长度、厚度、宽度、中心距、角度、锻模斜度、圆角半径和圆弧半径等公差。
形状位置公差包括直线度、平面度、同轴度、错移量、剪切端变形量和杆部变形量等。
表面技术公差包括剪毛刺的尺寸、顶杆压痕深度和表面粗糙度等。
影响锻件加工余量和公差的因素主要有以下几类。
(1)锻件的质董锻件质量可按下列程序进行估算:零件图基本尺寸→估计机械加工余量→绘制锻件图→估算锻件质量。
并按此质量查表确定公差和机械加工余量。
(2)锻件的形状复杂系数,锻件的形状复杂系数是锻件质量或体积与其外廓包容体的质量或体积的比值。
锻件形状复杂系数分为4级。
(4)锻件分模面形状和锻模状况锻件分模线形状分为平直分模线或对称弯曲分模线及其不对称弯曲分模线等,公差和余量设计时应考虑分模面形状。
模具材质不同、强度不同,磨损情况不同,设计时应考虑余量和公差有差别。
(5)模锻件精度等级模锻件的公差等级一般分普通级和精密级。
精度等级不同,加工余量和公差不同。
(6)锻件加热方式和锻造设备类型锻件加热方法不同,公差和加工余量不同。
各类锻造设备因导向精度和运动特性不同,导致余量和
公差不同。
余量和公差确定,可参考相关手册和国家及其行业标准。
公差确定的步骤如下:根据同轴度要求→毛边大小→分模线形状→锻件质量→材质系数→形状复杂系数→锻件轮廓尺寸→确定公差。
加工余量步骤如下:锻件重量→加工精度等级→形状复杂系数→厚度和长度方向尺寸→确定加工余量。